精密和超精密加工技术-第一章
精密和超精密加工技术

第一章精密和超精密加工技术及其发展展望精密和超精密加工代表了加工精度发展的不同阶段,通常,按加工精度划分,可将机械加工分为一般加工、精密加工、超精密加工三个阶段。
什么叫精密加工?加工精度在0.1~1µm,加工表面粗糙度在Ra0.02~0.1µm之间的加工方法称为精密加工。
什么叫超精密加工?加工精度高于0.1µm,加工表面粗糙度小于Ra0.01µm之间的加工方法称为超精密加工。
以下哪些是精密和超精密加工的分类?A.去除加工;B.结合加工;C.变形加工;D.切削加工;E.磨粒加工;F.特种加工;G.复合加工;影响精密与超精密加工的因素有哪些?加工机理、被加工材料、加工设备及其基础元部件、加工工具、检测与误差补偿、工作环境等。
我国今后发展精密与超精密加工技术的重点研究内容包括什么?(1)超精密加工的加工机理;(2)超精密加工设备制造技术;(3)超精密加工刀具、磨具及刃磨技术;(4)精密测量技术及误差补偿技术;(5)超精密加工工作环境条件。
第二章超精密切削与金刚石刀具举例说明超精密切削的应用范围有哪些?陀螺仪、激光反射镜、天文望远镜的反射镜、红外反射镜和红外透镜、雷达的波导管内腔、计算机磁盘、激光打印机的多面棱镜、录像机的磁头、复印机的硒鼓、菲尼尔透镜等由有色金属和非金属材料制成的零件。
超精密切削速度是如何选择的?超精密切削实际速度的选择根据所使用的超精密机床的动特性和切削系统的动特性选取,即选择振动最小的转速。
金刚石刀具的尺寸寿命甚高,高速切削时刀具磨损亦甚慢,因此刀具是否磨损以加工表面质量是否下降超差为依据,切削速度并不受刀具寿命的制约。
第二章超精密切削与金刚石刀具•举例说明超精密切削的应用范围有哪些?陀螺仪、激光反射镜、天文望远镜的反射镜、红外反射镜和红外透镜、雷达的波导管内腔、计算机磁盘、激光打印机的多面棱镜、录像机的磁头、复印机的硒鼓、菲尼尔透镜等由有色金属和非金属材料制成的零件。
超精密加工技术在航天器制造中的应用

超精密加工技术在航天器制造中的应用引言随着航天事业的不断发展,航天器的制造技术也在不断地提高和改进,其中超精密加工技术是一种非常重要的技术之一。
超精密加工技术是指在非常高精度和高效率的情况下,对工件进行精密加工的一种加工技术,具有高质量、高精度、高效率、高耐磨性等优点。
在航天器制造中,超精密加工技术可以被广泛地应用,可以大大提高航天器的制造精度和质量,从而提高整个航天工程的成功率和效益。
第一章超精密加工技术的基本概念超精密加工技术是一种高度精密和高效率的加工技术,它可以在非常高的精度和效率下对工件进行加工,从而保证加工后的工件具有高质量、高精度、高效率以及高耐磨性等优良性质。
超精密加工技术可以分为机械加工、电子加工、化学加工等多种加工方式,其中机械加工是最为常见的一种。
机械加工的超精密加工技术主要包括铣削、车削、磨削等方式,其加工精度可以达到微米乃至纳米级别。
这种加工方式不仅可以对各种材料进行加工,而且加工过程中对环境污染也非常小,因此被广泛地应用于各种高精度的加工领域中。
第二章超精密加工技术在航天器制造中的应用在航天器制造中,超精密加工技术得到了广泛的应用,可以大大提高航天器的制造精度和质量,从而保证整个航天工程的成功率和效益。
具体应用如下:2.1 航天器壳体制造航天器的壳体是一个非常关键的零部件,它要求具有高精度、高强度、耐热、防辐射等特点。
超精密加工技术可以在满足这些要求的基础上,对航天器的壳体进行加工,从而保证壳体的精度和质量,从而提高航天器的安全性和稳定性。
2.2 航天器零部件制造除壳体外,航天器的其他零部件也需要采用超精密加工技术进行制造,例如导弹喷雾板、电机减速装置等。
这些零部件要求具有精度高、耐热、耐磨等特点,超精密加工技术可以满足这些要求,从而提高航天器的质量和效率。
2.3 航天器加工技术研究超精密加工技术的应用还可以促进航天器制造技术的发展和研究。
例如,通过对航天器加工技术的研究和改进,可以提高航天器的制造精度和质量,从而保证整个航天工程的成功率和效益。
精密和超精密加工技术

本章内容
I. 特种加工技术概述 II. 电火花加工 III.电解加工 IV. 高能束加工
特种加工技术概述
➢ 非传统加工又称特种加工,通常被理解为别于传统切 削与磨削加工方法的总称。
➢非传统加工方法 产生于二次大战后。两方面问题传统 机械加工方法难于解决:
1)难加工材料的加工问题。宇航工业等对材料高强度、 高硬度、高韧性、耐高温、耐高压、耐低温等的要求,使 新材料不断涌现。
电火花加工工作要素
➢脉冲宽度与间隔——影响加工速度、表面粗糙 度、电极消耗和表面组织等。脉冲频率高、持 续时间短,则每个脉冲去除金属量少,表面粗 糙度值小,但加工速度低。通常放电持续时间 在2μs至2ms范围内,各个脉冲的能量2mJ到20J (电流为400A时)之间。
电火花加工类型
➢电火花成形加工:主要指孔加工,型腔加工等 ➢电火花线切割
➢ 拓宽现有非传统加工方法的应用领域。
➢ 探索新的加工方法,研究和开发新的元器件。
➢ 优化工艺参数,完善现有的加工工艺。
➢ 向微型化、精密化发展。 ➢ 采用数控、自适应控 2084 制、CAD/CAM、专家系统
等 技 术 , 提 高 加 工 过 程1104
70年代 80年代 90年代
自动化、柔性化程度。
232
424 244 142
441 321 214
353 252 316
激光加工 电火花加工 超声加工 电化学加工 EI 收录文章数比较
几种代表性特种加 工方法
电火花加工的原理示意 图
电火花加工
原理:利用工具电极与工件电极之间脉冲性火花放电, 产生瞬时高温,工件材料被熔化和气化。同时,该处绝 缘液体也被局部加热,急速气化,体积发生膨胀,随之 产生很高的压力。在这种高压作用下,已经熔化、气化 的材料就从工件的表面迅速被除去
精密和超精密加工技术

1、通常将加工精度在0.1-1um、加工表面粗糙度R在0.02-0.1um之间的加工方法称为精密加工。
而将加工精度高于0.1um、加工表面粗糙度R小于0.01um的加工方法称为超精密加工。
2、提高加工精度的原因:提高制造精度后可提高产品的性能和质量,提高其稳定性和可靠性;促进产品的小型化;增强零件的互换性,提高装配生产率,并促进自动化装配。
3、精密和超精密加工目前包含三个领域:超精密切削;精密和超精密磨削研磨‘精密特种加工。
4、金刚石刀具的超精密切削加工技术,主要应用于两个方面:单件的大型超精密零件的切削加工和大量生产的中小型零件的超精密切削加工技术。
5、金刚石刀具有两个比较重要的问题:晶面的选择;切削刃钝圆半径。
6、超稳定环境条件主要是指恒温、防振、超净和恒湿五个方面的条件。
7、我国应开展超精密加工技术基础的研究,其主要内容包括以下四个方面:1)超精密切削、磨削的基本理论和工艺。
2)超精密设备的关键技术、精度、动特性和热稳定性。
3)超精密加工的精度检测、在线检测和误差补偿。
4)超精密加工的环境条件。
5)超精密加工的材料。
8、超精密切削实际选择的切削速度,经常是根据所使用的超精密机床的动特性和切削系统的动特性选取,即选择振动最小的转速。
9、超精密切削实际能达到的最小切削厚度和金刚石刀具的锋锐度、使用的超精密机床的性能状态、切削时的环境等都直接有关。
10、为实现超精密切削,刀具应具有如下性能:1)极高的硬度、极高的耐磨性和极高的弹性模量,以保证刀具有很长的寿命和很高的尺寸耐用度。
2)切削刃钝圆能磨得极其锋锐,切削刃钝圆半径r值极小,能实现超薄切削厚度。
3)切削刃无缺陷,切削时刃形将复印在加工表面上,能得到超光滑的镜面。
4)和工件材料的抗粘结性好、化学亲和性小、摩擦因素低,能得到极好的加工表面完整性。
11、SPDT——金刚石刀具切削和超精密切削。
12、晶体受到定向的机械力作用时,可以沿平行于某个平面平整地劈开的现象称为解理现象。
精密与超精密加工技术

精密与超精密加工技术综述0 前言就先进制造技术的技术实质性而论,主要有精密和超精密加工技术和制造自动化两大领域1。
前者包括了精密加工、超精密加工、微细加工,以及广为流传的纳米加工,它追求加工上的精度和表面质量的极限,可统称为精密工程;后者包括了设计、制造和管理的自动化,它不仅是快速响应市场需求、提高生产率、改善劳动条件的重要手段,而且是提高产品质量的有效方式。
两者有密切联系,许多精密和超精密加工要靠自动化技术才能达到预期目标,而不少制造自动化则有赖于精密加工才能达到设计要求。
精密工程和制造自动化具有全局性的、决策性的作用,是先进制造技术的支柱。
精密和超精密加工与国防工业有密切关系。
导弹是现代战争的重要武器,其命中精度由惯性仪表的精度所决定,因而需要高超的精密和超精密加工设备来制造这种仪表。
例如,美国“民兵”型洲际导弹系统的陀螺仪其漂移率为0.03~0.05°/h,加速度计敏感元件不允许有0.05μm的尘粒,它的命中精度的圆概率误差为500m;MX战略导弹(可装载10个核弹头),由于其制导系统陀螺仪精度比“民兵—Ⅲ”型导弹要高出一个数量级,因而其命中精度的圆概率误差仅为50~150m。
对射程4000km的潜射弹道导弹,当潜艇的位置误差对射程偏差的影响为400m、潜艇速度误差对射程偏差的影响为800m、惯性平台的垂直对准精度对射程偏差的影响为400m时,要求惯性导航的陀螺仪的漂移精度为0.001°/h、航向精度在1′以上、10小时运行的定位精度为0.4~0.7海里,因此,陀螺元件的加工精度必须达到亚微米级,表面粗糙度达到Ra0.012~0.008μm。
由此可知,惯性仪表的制造精度十分关键。
如1kg重的陀螺转子,其质量中心偏离其对称轴为0.5nm时,就会造成100m的射程误差和50m的轨道误差;激光陀螺的平面反射镜的平面度为0.03~0.06μm,表面粗糙度要求为Ra0.012μm以上;红外制导的导弹,其红外探测器中接受红外线的反射镜,其表面粗糙度要求达到Ra0.015~0.01μm[2]。
超精密机床结构
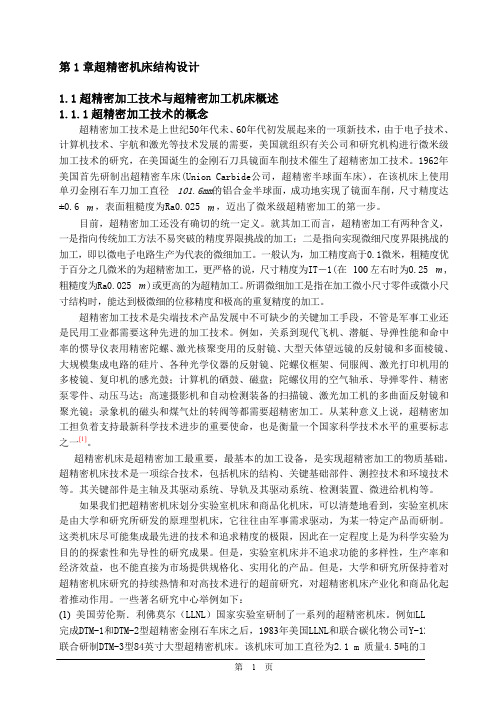
第1章超精密机床结构设计1.1超精密加工技术与超精密加工机床概述1.1.1超精密加工技术的概念超精密加工技术是上世纪50年代未、60年代初发展起来的一项新技术,由于电子技术、计算机技术、宇航和激光等技术发展的需要,美国就组织有关公司和研究机构进行微米级加工技术的研究,在美国诞生的金刚石刀具镜面车削技术催生了超精密加工技术。
1962年美国首先研制出超精密车床(Union Carbide公司,超精密半球面车床),在该机床上使用单刃金刚石车刀加工直径101.6mm的铝合金半球面,成功地实现了镜面车削,尺寸精度达±0.6m,表面粗糙度为Ra0.025m,迈出了微米级超精密加工的第一步。
目前,超精密加工还没有确切的统一定义。
就其加工而言,超精密加工有两种含义,一是指向传统加工方法不易突破的精度界限挑战的加工;二是指向实现微细尺度界限挑战的加工,即以微电子电路生产为代表的微细加工。
一般认为,加工精度高于0.1微米,粗糙度优于百分之几微米的为超精密加工,更严格的说,尺寸精度为IT-1(在100左右时为0.25m,粗糙度为Ra0.025m)或更高的为超精加工。
所谓微细加工是指在加工微小尺寸零件或微小尺寸结构时,能达到极微细的位移精度和极高的重复精度的加工。
超精密加工技术是尖端技术产品发展中不可缺少的关键加工手段,不管是军事工业还是民用工业都需要这种先进的加工技术。
例如,关系到现代飞机、潜艇、导弹性能和命中率的惯导仪表用精密陀螺、激光核聚变用的反射镜、大型天体望远镜的反射镜和多面棱镜、大规模集成电路的硅片、各种光学仪器的反射镜、陀螺仪框架、伺服阀、激光打印机用的多棱镜、复印机的感光鼓;计算机的硒鼓、磁盘;陀螺仪用的空气轴承、导弹零件、精密泵零件、动压马达;高速摄影机和自动检测装备的扫描镜、激光加工机的多曲面反射镜和聚光镜;录象机的磁头和煤气灶的转阀等都需要超精密加工。
从某种意义上说,超精密加工担负着支持最新科学技术进步的重要使命,也是衡量一个国家科学技术水平的重要标志之一[1]。
精密和超精密加工的机床设备技术(PPT 88页)

精密和超精密加工技术
第4章 精密和超精密加工的机床设备
2019/12/12
3.1 精密和超精密机床发展概况及典型机床 简介
3.2 精密主轴部件 3.3 床身和精密导轨部件 3.4 进给驱动系统 3.5 微量进给装置 3.6 机床运动部件位移的激光在线检测系 3.7 机床的稳定性和减振隔振 3.8 减少变形和恒温控制
2019/12/12
2019/12/12
第1节 精密和超精密机床发展概况 及典型机床简介
二、典型机床简介
Union Carbide 公司 的半球机床
能加工直径100mm的半球,达到尺寸精
度正负0.6μm,表面粗糙度0.025μm。
精密空气轴承主轴采用多孔石墨制成 轴衬,径向空气轴承的外套可以调整 自动定心,可提高前后轴承的同心度, 以提高主轴的回转精度。
第2节 精密主轴部件
一、主轴轴承 主轴回转精度
回转精度——在主轴空载手动或机动低速旋转情况下, 在主轴前端安装工件或刀具的基面上所测得的径向跳动、 端面跳动和轴向窜动的大小。
影响回转精度的因素 (1)轴承精度和间隙的影响。 (2)主轴、支承座等零件中精度的影响。
关键在于精密轴承。
2019/12/12
类型:普通(各种精密超精密车、铣等)、专 用(磁盘超精密车床) 按工艺方法:超精密车床、超精密铣床、超精 密磨床、超精密研磨机、超精密抛光机床、超 精密特种加工机床、精密和超精密加工中心等
精度指标:目前,主轴回转精度为0.025um, 导轨直线度为1000000:0.025,定位精度为 0.013um/1000um,进给分辨率为0.005um,加
精密与超精密加工技术PPT课件

金刚石的热传导率是矿物中最大的,切削加工中发热量非常小。
23
精密与超精密加工技术
天然金刚石的加工多采用研磨加工方法,通常采用空气轴承 研磨机,由于振动小,可达到很低的粗糙度和极小的刃口半径。
24
ห้องสมุดไป่ตู้
精密与超精密加工技术
1)刀尖的磨损 在切削距离到达100km以前,后刀面磨损急剧上升,以后磨损逐渐减
27
精密与超精密加工技术
(1)超精密磨削表面的形成机制
超精密磨削获得的极低的表面粗糙度,主要靠砂轮精细修整得到的大量的、 等高性很好的微刃来实现微量切削作用。
(1) 对产品高质量的追求 (2) 对产品小型化的追求 (3) 对产品高可靠性的追求 (4) 对产品高性能的追求
10
精密与超精密加工技术
国际知名超精密加工研究单位与企业主要有: 美国LLNL实验室和Moore公司 英国Granfield大学和Tayler公司 德国Zeiss(蔡司)公司和Kugler公司 日本东芝机械、丰田工机和不二越公司等
3
精密与超精密加工技术
世界发达国家均予以高度重视。最近启动的研究 计划包括 :
美国的NNI(National nanotechnologyinitiative)纳米计划 英国的多学科纳米研究合作计划IRC(Interdisciplinary research collaboration in nanote-chnology), 日本的纳米技术支撑计划
精密与超精密加工技术
1
内容
1、超精密加工技术概述 2、超精密加工技术的发展历程 3、超精密加工的范畴 4、超精密加工的主要研究领域 5、超精密加工的主要方法 6、超精密加工的发展趋势
- 1、下载文档前请自行甄别文档内容的完整性,平台不提供额外的编辑、内容补充、找答案等附加服务。
- 2、"仅部分预览"的文档,不可在线预览部分如存在完整性等问题,可反馈申请退款(可完整预览的文档不适用该条件!)。
- 3、如文档侵犯您的权益,请联系客服反馈,我们会尽快为您处理(人工客服工作时间:9:00-18:30)。
理论上,系统误差可以被消除。
精密加工技术-LYD
1. 精密加工概念
1.2.2 随机误差(random error、accidental error)
相同条件下,多次测量时,大小、方向都变化的误差 例如:加工过程中因为不规则振动、温度波动或材料不均 匀等原因引起的误差。 理论上,随机误差不能够被消除。运用数理统计与概率分析方法 可以评定随机误差的影响程度,并在一定程度上减小随机误差的 影响。 随机误差一般表现为正态分布
粱延德 大连理工大学机械学院教授 大连理工大学工程训练中心主任 大连理工大学机械学院中心实验室主 任 大连理工大学机械创新中心主任 大连理工大学金工课程教学负责人
精密加工技术-LYD
精密与超精密加工技术
第一章 绪 论
梁延德
大连理工大学
精密加工与非传统加工技术
第一章
绪
论
梁延德
引起工件加工误差(输出误差)的原始误差:
前道工序带来的加工误差
机床自身的误差
——输入误差
——内部误差
外来振动、温度变化等 ——外部误差
精密加工技术-LYD
2. 原始误差的消除与迟钝化
例如:悬臂簧片机构,若在A点输入 位移,则在B点可以得到较 高精度 的位移输出
精密加工技术-LYD
2. 原始误差的消除与迟钝化
大连理工大学
1. 精密加工概念
1.1 加工精度
——加工对象的实测几何参数相对理想几何 参数的符合程度
尺寸精度 机械加工精度 形状精度 位置精度
精密加工技术-LYD
1. 精密加工概念
x a)精密度高 b)正确度高 c)精确度高
精密加工技术-LYD
1. 精密加工概念
1.2
加工误差
加工误差——加工对象的实测几何参数相 对理想几何参数的偏离程度 加工精度通过加工误差来度量
精密加工技术-LYD
1. 精密加工概念
加工误差的数学表达
随机误差 (残差)
系统误差
精密加工技术-LYD
1. 精密加工概念
1.3 加工误差测定的基本原则 1.3.1 过程稳定性原则
加工工艺系统、测量系统自身及周围环境要稳定。 ——温度、湿度、气压、振动等因素 测量次数要稳定 测量操作要稳定(操作者及其工作状态)
——非正常原因导致的大值误差 在误差分析时,应首先将粗大误差剔除。
一般 用正确度(correctness) 表示系统误差的影响 用精密度(precision) 表示随机误差的影响
用精确度(accuracy) 表示系统误差和随机误差的综合影响
精密加工技术-LYD
1. 精密加工概念
x a)随机误差小、 系统误差大 精密度高 b)系统误差小、 随机误差大 正确度高 c)随机误差小、 系统误差小 精确度高
Abbe比较原则(阿贝误差原理) 比较测量时,标准尺如果不在被测件中心线或其 延长线上,会产生一阶误差(阿贝误差)
精密加工技术-LYD
误差的传递与合成
精密加工技术-LYD
采用了误差统计规律数据处理方法。
精密加工技术-LYD
3、关于机床的精度
例如,按ISO标准推荐的±3σ散差处理办法,来测量一台加工中心
上某一个坐标精度, 若对其中的某一定位点在正、反方向趋近该定位点
,定位七次(N=7),其每一次实测数据如下:+4μm、+2μm、+1μm、0 、-1μm、-2μm、-4μm。按ISO标准规定,该定位点散差的平均值为 △Xn=0,其散差3σ约为7.35μm。 该点定位误差分布如图1所示。
精密加工技术-LYD
2. 加工精度的历史演进
目前标志性的精密加工技术:
加工精度 ≤ 0.01μm 的圆度加工技术
0.01μm 级 的加工尺寸精度技术 0.01~0.001μm 级 的精密位移技术
0.01μm 级 的主轴回转精度技术 0.1μm/1m的直线度加工技术 0.1角秒级的分度技术 0.001μm 级的切削加工技术
1.3.2 以高测低原则
量具的精度必须高于被测件要求的精度
精密加工技术-LYD
1. 精密加工概念
十分之一原则:
测量或加工系统的准确度应不大于工件所要求精度的1/10 (比工件所要求的精度高一个数量级)
三分之一原则: 测量或加工系统的精密度(均方差σ)应不大于工件所要求 精密度的1/3
上述二原则是判定量具或加工系统自身误差是否可以忽略的标准
精密加工技术-LYD
3、关于机床的精度
其他几种标准尽管处理数据上有所区别,但都反映了要按误差统 计规律来分析测量定位精度,即对数控机床某一可控轴行程中某一个
定位点误差,应该反映出该点在以后机床长期使用中成千上万次在此
定位的误差,而我们在测量时只能测量有限次数(一般5~7次)。为 了真实反映这个定位点周围一组随机分散的点群定位误差分布范围,
精密加工技术-LYD
精密加工技术-LYD
精密和超精密加工技术
第二章 误差理论基础
梁延德
1. 误差的传递与合成
1.1 误差传递定律
数学推导:(略) 应用: 解算工艺尺寸链的基础
精密加工技术-LYD
1. 误差的传递与合成
1.2 误差的合成
——用于有多项误差存在时
系统误差按代数和合成,若不知符号则按绝对值合成
精密加工技术-LYD
1. 精密加工概念
随机误差的一般特性
【1】小的随机误差出现的概率大,大的随机误差出现的概率小; 【2】绝对值相等的正负随机误差出现的概率相等(对称性或相消性)
【3】随机误差分布范围有限性
随机误差一般表现为正态分布
精密加工技术-LYD
1. 精密加工概念
1.2.3 粗大误差(parasitic error)
n
n
2 1 2 2 2 3 2 n
i 1
2 i
n
图1 定位误差分布范围
精密加工技术-LYD
3、关于机床的精度
图1显示,在该定位点上,当正反方向反复定位时,将有99.96%的
可能性在±3σ=14.7μm范围以内。在德国VDI标准内规定5σ,将得到
比这更大的误差。因此,这一重复定位精度为14.7μm。从1998年以来 ,国际上开始试运行新标准,按4σ处理将得到重复定位精度为 10.5μm,但该算法反映了95%左右定位点范围。 按日本JIS标准处理上述情况, 将得到重复定位精度为±4μm。 从这里看出,JIS标准规定精度 是最松的,而VDI标准要求最为 严格。 图1 定位误差分布范围
随即误差按方根法合成 未知的各种误差(包括系统误差)按随机误差处理
精密加工技术-LYD
1. 误差的传递与合成
精密加工技术-LYD
1. 误差的传递与合成
精密加工技术-LYD
1. 误差的传递与合成
精密加工技术-LYD
1. 误差的传递与合成
精密加工技术-LYD
1. 误差的传递与合成
精密加工技术-LYD
常值性系统误差
系统误差 机械加工误差 随机误差 粗大误差
变值性系统误差
精密加工技术-LYD
2. 精密加工概念
1.2.1 系统误差(systematic error)
常值性系统误差——相同条件下,多次测量时,大小、方向都不 变的误差
例如:仪器、衡器、量具的对零误差。
变值性系统误差——相同条件下,多次测量时,大小、方向有规 律变化的误差
误差迟钝化方向与误差补偿
精密加工技术-LYD
3. 误差均化原理
误差均化原理 ——利用相互作用件间的误差相互抵消或减小的方法
例如:三平板研磨法(减小平面度误差) 例如:端齿盘(鼠牙盘)研磨法(圆分度误差封闭性原理) 例如:静压支承法(减小平面度、圆柱度、表面粗糙 度误差)
精密加工技术-LYD
4. 阿贝误差原理
精密加工技术-LYD
2. 加工精度的历史演进
200年的人类社会工业化历史 :
昨天的精密加工——今天的普通加工
精密加工技术-LYD
2. 加工精度的历史演进
精密加工技术-LYD
2. 加工精度的历史演进
目前:
加工精度 ≥1μm , Ra ≥0.2μm 加工精度 0.1~1μm , Ra 0.02~0.1μm 加工精度 ≤0.1μm , Ra ≤ 0.01μm ——普通加工 ——精密加工 ——超精密加工
精密加工技术-LYD
3、关于机床的精度
机床的单轴定位精度是指在该轴行程内任意一个点定位时的误差范 围,它直接反映了机床的加工精度能力,所以是数控机床最关键技术指 标。 目前世界各国对该指标的规定、定义、测量方法和数据处理等有所 不同,在各类数控机床样本资料介绍中,常用的标准有美国标准(NAS) 和美国机床制造商协会推荐标准、德国标准(VDI)、日本标准(JIS) 、国际标准化组织(ISO)和我国国家标准(GB)。在这些标准中规定最低 的是日本标准,因为它的测量方法是使用单组稳定数据为基础,然后又 取出用±值把误差值压缩一半,所以用它的测量方法测出的定位精度往 往比用其他标准测出的相差一倍以上。
1. 误差的传递与合成
精密加工技术-LYD
1. 误差的传递与合成
精密加工技术-LYD
1. 误差的传递与合成
精密加工技术-LYD
1. 误差的传递与合成
精密加工技术-LYD
2. 原始误差的消除与迟钝化
把已有的原始误差对输出误差的影响消除或减小到 允许程度以内的方法称为“原始误差的消除”或“原始 误差的迟钝化”