UG加工各参数详解(UG公司内部解释)
UG数控加工的参数设置【大全】

切削参数打开“切削参数”图标,系统会显示“切削参数”对话框,第一栏:策略(既一些加工参数值的设定)1、切削方向:顺铣:刀具一般多采用顺铣,因为由顺铣加工完成时工件的表示光洁度比较好!另一个原因是顺铣时刀具的受损要比逆铣轻的多!所以多采用顺铣。
从外向内用逆洗。
从内向外用顺洗。
2、逆铣:多适用于一些粗糙的工件开粗,加工完成后工件的光洁度不好,而且刀具受损严重!所以一般不利用逆铣。
3、切削角:当使用“单向式”切削,“往复式”切削“单向带轮廓”铣切削三种方法时在切削参数里才显示切削角的定义,其意思为所生成的刀轨是平行X向为零,平行于Y向为90度,可根据自己的要求定义切削角度,多采用45度斜进刀可在切削角下的度数栏内,输入所定义的角度值,如果想看一下角度方向时,可点示显示切削方向的图标。
3、壁:当使用“单向铣削”,“往复式铣削”和“跟随周边”时切削参数里面才有壁选项,“单向”和“往复”铣削里面只有三项。
其一:无,它的意思为只切削腔,不去清壁,其二,在起点:刀具在下刀后先把壁清理完,然后再切削腔。
其三,在终点:刀具在下刀后把腔切削完成后,到最后一刀把壁清理干净,无论是“起点”清壁还是“终点”清壁,都是以层为单位,如果没有“自动”清壁的情况使用在“终点”清壁。
如果有“自动”清壁时优先使用“自动”清壁,“自动”清壁的意思是:系统给计算一个最适合清壁时清壁。
4、添加精割削刀路数本功能是以UG5.0版本才增加的新功能,它能有效的控制几何体的余量更加均匀,所以在型腔铣开粗时打上对号,让其忝加“1”刀路数,精加工的步距可根据情况而定,但本步距最好要小一些。
5、毛坯:1、本栏下的毛坯距离和外部(面铣削对话框中)毛坯距离相同。
2。
Extend to part outline :是指毛坯延展,默认延展至体的最大外形轮廓线因此我们不采用。
3、合并距离:当所加工的平面为两个或两个以上时,指定距离大于或等于两个面之间的距离,想要学习UG编程领取学习资料在群496610960可以帮助你两个面刀路会自动合并成一个刀路,但要求所选择的面必须在同一高度上,所指定的值可使用刀具的百分比或mm。
UG加工功能的图标和解释

THREAD- 铣螺纹 用 螺 纹 铣 孔。
MILLING
刀铣螺纹
UG 加工常见图标功能解释
MILL_CO
该操作子类型用于应用机床控制事件,如
NTROL 机床控制 机 床 的 参 冷却液开/冷却液关或主轴正转/反转。
数设置
MILL_USE 用 户 自 定
该操作子类型允许使用定制 NX Open 程
型腔铣 、曲面铣 (三维加工)mill_contour
博思UG工作室 图标
英文注释
CAVITY-MILL
ZLEVEL-FOLLOW-CORE
中文注释
型腔铣
基本定义
标准型腔铣主要用于工件 的开粗
切削方式为跟随型芯的型 跟随型芯型腔铣 腔铣
CORNER-ROUGH
角落粗加工
清理角落残科的型腔铣
PLUNGE-MILLING
该操作子类型允许刀具在指定切削深度
COUNTER 倒角沉孔 钻 锥 形 沉 暂停指定的秒数或转数。埋头孔循环中
SINKING
孔
如果需要驻留,可使用该操作子类型。
该操作子类型创建攻丝循环,即进给到
TAPPING
攻丝
用 丝 锥 攻 孔内,主轴反转,然后进给退到孔外。
螺纹 G84
此操作子类型使用螺旋切削来铣削螺纹
镗孔
该操作子类型允许镗刀连续进给进入和 用 镗 刀 将 退出部件。 孔镗大
G65
该操作子类型允许绞刀连续进给进入和
RELAMIN
铰孔 用 铰 刀 将 退出部件。
G
孔较大
G85
该操作子类型允许刀具在指定切削深度
COUNTER 沉孔 沉孔锪平 暂停指定的秒数或转数。沉头孔循环中
UG加工中文对照
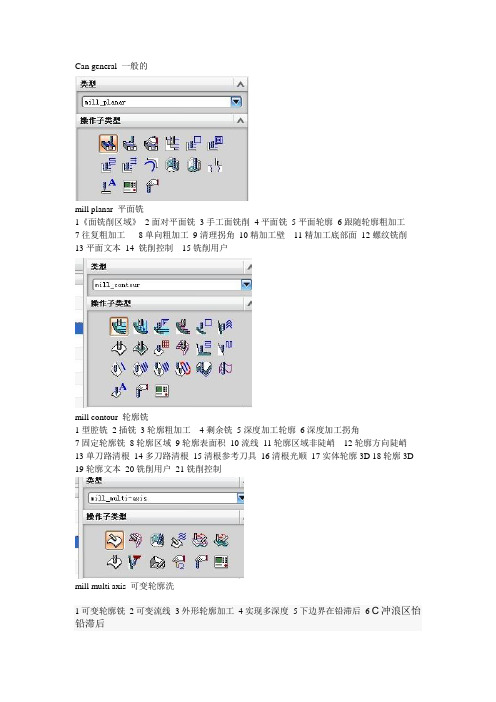
Can general 一般的
mill planar 平面铣
1《面铣削区域》2面对平面铣3手工面铣削4平面铣5平面轮廓6跟随轮廓粗加工
7往复粗加工8单向粗加工9清理拐角10精加工壁11精加工底部面12螺纹铣削
13平面文本14 铣削控制15铣削用户
mill contour 轮廓铣
1型腔铣2插铣3轮廓粗加工4剩余铣5深度加工轮廓6深度加工拐角
7固定轮廓铣8轮廓区域9轮廓表面积10流线11轮廓区域非陡峭12轮廓方向陡峭
13单刀路清根14多刀路清根15清根参考刀具16清根光顺17实体轮廓3D 18轮廓3D 19轮廓文本20铣削用户21铣削控制
mill multi axis 可变轮廓洗
1可变轮廓铣2可变流线3外形轮廓加工4实现多深度5下边界在铅滞后6C冲浪区怡铅滞后
7固定轮廓铣8深度加工5轴铣9选择刀具10一般运动11铣削用户12铣削控制
Drill孔加工
1孔加工2点钻3钻4啄钻5断屑钻6镗孔
7铰孔8沉头孔加工9钻埋头孔10出屑11螺纹铣削12铣削控制
Hole making 孔加工
1铣削控制2孔加工3铣孔4手工钻孔
Turning变相车加工
1中心孔2中心线钻孔3中心钻啄钻4中心钻断屑5中心钻铰孔6中心钻出屑
7面加工8粗车9退刀粗车10粗堂11退刀粗堂12精车
13精镗14退刀精镗15教学模式16外槽17内槽18槽面
19外螺纹OD 20内螺纹ID 21切断22进给杆停止位23车削控制24车削用户。
UG _加工参数5
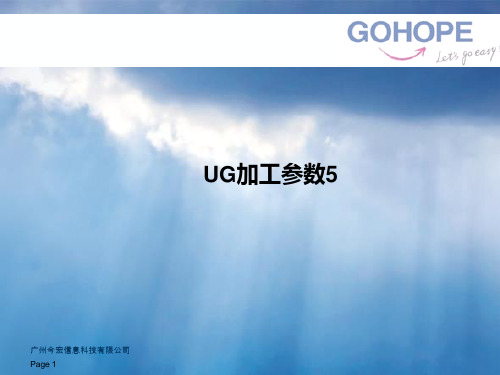
态
Empty Locked
加工时间显示
广州今宏信息科技有限公司 Page 6
Approved
查看动画>>
Empty Locked Approved 空刀轨 刀轨已生成,但是不含有效运动。一些示例包括查找不到凹部的清根操作,或者没有要切削的 IPW 的型 腔铣操作。并非设计为包含运动的操作(如机床控制)将不会显示此状态。 已锁定 将保护刀轨以防刀轨被覆盖。 如果您已编辑某个刀轨,或者使用类似清根手工切削顺序的功能,但是不希望意外地覆盖刀轨,则请使 用此功能。 如果已选择用户默认设置的选项在版本升级中锁定刀轨,则当打开在先前发行版中保存的文件时,也将 显示已锁定状态 已批准 刀轨在其当前状态可接受。 几何体或刀具参数更改会将操作设置为重新生成状态。如果您已知刀轨仍然是最新的,则您可以通过更 改其状态为已批准来覆盖重新生成状态。
•
• • •
广州今宏信息科技有限公司 Page 9
刀轨分割(Tool Path Divide)
新功能 可以通过以下方式切割刀轨, 切削时间 切削长度 选中的动作 通过刀柄(刀具有夹持部分时才 生效,在传递处分割)
查看动画>>
广州今宏信息科技有限公司 Page 10
IPW云图
查看视频>>
广州今宏信息科技有限公司 Page 7
操作导航器程序组
刀路锁定及拆分
新功能
广州今宏信息科技有限公司 Page 8
交互式的刀轨编辑器 • 完全重建的刀轨编辑器;让导轨 编辑更简单,更柔性化 可以从图形窗口或刀轨运动列表 中选着刀轨范围 无论是单通路刀轨还是多通路刀 轨,全部都进行刀轨干涉检查 倒序刀轨和裁剪刀轨 测量任意刀路点
UG加工各参数详解
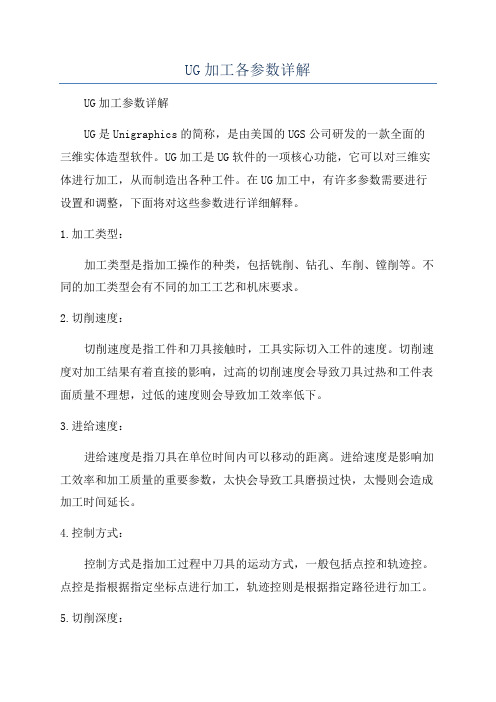
UG加工各参数详解UG加工参数详解UG是Unigraphics的简称,是由美国的UGS公司研发的一款全面的三维实体造型软件。
UG加工是UG软件的一项核心功能,它可以对三维实体进行加工,从而制造出各种工件。
在UG加工中,有许多参数需要进行设置和调整,下面将对这些参数进行详细解释。
1.加工类型:加工类型是指加工操作的种类,包括铣削、钻孔、车削、镗削等。
不同的加工类型会有不同的加工工艺和机床要求。
2.切削速度:切削速度是指工件和刀具接触时,工具实际切入工件的速度。
切削速度对加工结果有着直接的影响,过高的切削速度会导致刀具过热和工件表面质量不理想,过低的速度则会导致加工效率低下。
3.进给速度:进给速度是指刀具在单位时间内可以移动的距离。
进给速度是影响加工效率和加工质量的重要参数,太快会导致工具磨损过快,太慢则会造成加工时间延长。
4.控制方式:控制方式是指加工过程中刀具的运动方式,一般包括点控和轨迹控。
点控是指根据指定坐标点进行加工,轨迹控则是根据指定路径进行加工。
5.切削深度:切削深度是指每次切削过程中刀具与工件之间的距离。
切削深度的设置需要根据工件的材料和形状进行调整,过大的切削深度会导致刀具过载,过小则会影响加工效率。
6.刀具半径补偿:刀具半径补偿是指在加工过程中对刀具半径进行调整,以保证加工结果的准确度。
刀具半径越大,补偿值就越大。
7.刀具选型:刀具选型是根据加工类型和工件材料选择合适的刀具。
不同的刀具有不同的加工特点和适用范围,选择合适的刀具对加工质量和效率有重要影响。
8.加工路径:加工路径是指刀具在加工过程中的运动轨迹。
合理的加工路径可以最大程度地减小加工时间和刀具磨损,提高加工效率。
9.刀具刃数:刀具刃数是指刀具刀边的数量,不同的刀具刃数适用于不同的加工类型和工件材料。
刀具刃数越多,加工效率和质量越高。
10.刀具进给速率:刀具进给速率是指刀具在加工过程中的进给速度。
刀具进给速率的调整需要根据加工精度和加工表面的要求进行合理设定。
UG加工部分中英文翻译对照
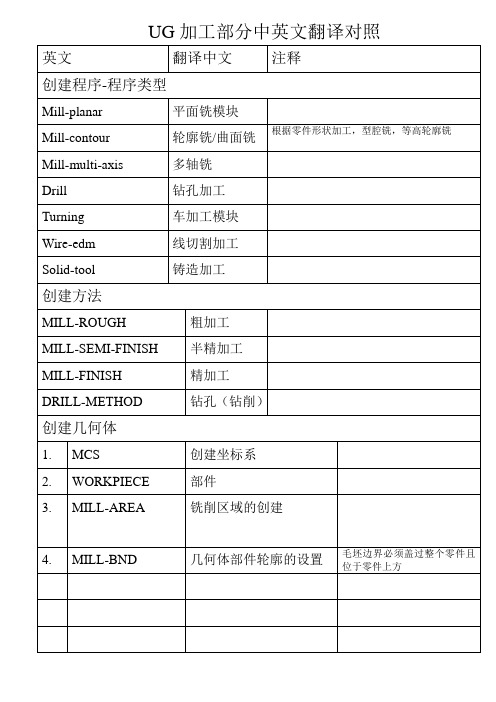
创建刀具时刀号参数:1.“补偿寄存器”为长度补偿。
2.“刀具补偿寄存器”为半径补偿,在G41 G42时用
l-planar类型下:
1.
Mill
端铣刀(平面铣刀)
2.
CHAMFER-MILL
倒角刀
3.
BALL-MILL
球刀
4.
SPHERICAL-MILL
球状铣刀
5.
T-CUTTER
MILL-ROUGH
粗加工
MILL-SEMI-FINISH
半精加工
MILL-FINISH
精加工
DRILL-METHOD
钻孔(钻削)
创建几何体
1.
MCS
创建坐标系
2.
WORKPIECE
部件
3.
MILL-AREA
铣削区域的创建
4.
MILL-BND
几何体部件轮廓的设置
毛坯边界必须盖过整个零件且位于零件上方
T形铣刀(专用刀)
2.drill类型下:
1.
SPOTFACING-TOOL
键槽铣刀
用于斜面或曲面上的孔加工
2.
SPOTDRILLING-TOOL
中心钻
钻中心孔
3.
DRILLING-TOOL
麻花钻
4.
BORING-BAR
镗刀
5.
REAMER
铰刀
6.
COUNTERBORING-TOOL
沉头孔刀
用于加工沉头孔
UG加工部分中英文翻译对照
英文
翻译中文注释创建程序-源自序类型Mill-planar
平面铣模块
Mill-contour
轮廓铣/曲面铣
ug摆线加工参数计算
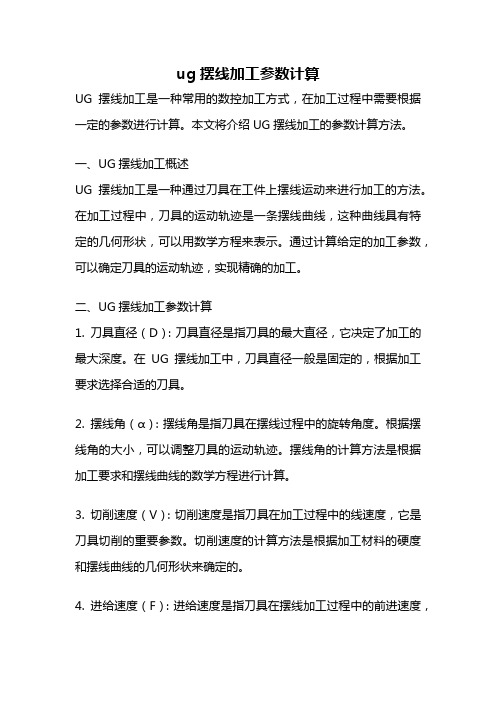
ug摆线加工参数计算UG摆线加工是一种常用的数控加工方式,在加工过程中需要根据一定的参数进行计算。
本文将介绍UG摆线加工的参数计算方法。
一、UG摆线加工概述UG摆线加工是一种通过刀具在工件上摆线运动来进行加工的方法。
在加工过程中,刀具的运动轨迹是一条摆线曲线,这种曲线具有特定的几何形状,可以用数学方程来表示。
通过计算给定的加工参数,可以确定刀具的运动轨迹,实现精确的加工。
二、UG摆线加工参数计算1. 刀具直径(D):刀具直径是指刀具的最大直径,它决定了加工的最大深度。
在UG摆线加工中,刀具直径一般是固定的,根据加工要求选择合适的刀具。
2. 摆线角(α):摆线角是指刀具在摆线过程中的旋转角度。
根据摆线角的大小,可以调整刀具的运动轨迹。
摆线角的计算方法是根据加工要求和摆线曲线的数学方程进行计算。
3. 切削速度(V):切削速度是指刀具在加工过程中的线速度,它是刀具切削的重要参数。
切削速度的计算方法是根据加工材料的硬度和摆线曲线的几何形状来确定的。
4. 进给速度(F):进给速度是指刀具在摆线加工过程中的前进速度,它决定了加工的进给量。
进给速度的计算方法是根据加工要求和摆线曲线的数学方程进行计算。
5. 加工深度(h):加工深度是指刀具在加工过程中的切削深度,它决定了加工的精度和加工时间。
加工深度的计算方法是根据加工要求和摆线曲线的数学方程进行计算。
6. 切削力(Fc):切削力是指刀具在切削过程中对工件的作用力,它是刀具切削的重要参数。
切削力的计算方法是根据切削速度、进给速度和刀具结构等参数进行计算。
三、UG摆线加工参数计算实例以一个具体的UG摆线加工实例来说明参数的计算方法。
假设需要加工一个直径为100mm的摆线曲线工件,刀具的直径为10mm,摆线角为60度,切削速度为200m/min,进给速度为0.1mm/r,加工深度为0.5mm。
根据给定的摆线角和工件直径,可以计算出摆线曲线的数学方程。
然后,根据切削速度和摆线曲线的几何形状,可以计算出刀具的线速度。
UG加工工艺参数设置说明
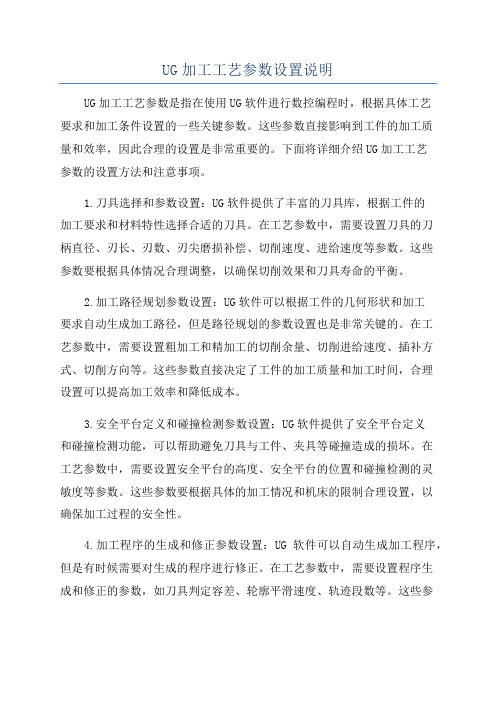
UG加工工艺参数设置说明UG加工工艺参数是指在使用UG软件进行数控编程时,根据具体工艺要求和加工条件设置的一些关键参数。
这些参数直接影响到工件的加工质量和效率,因此合理的设置是非常重要的。
下面将详细介绍UG加工工艺参数的设置方法和注意事项。
1.刀具选择和参数设置:UG软件提供了丰富的刀具库,根据工件的加工要求和材料特性选择合适的刀具。
在工艺参数中,需要设置刀具的刀柄直径、刃长、刃数、刃尖磨损补偿、切削速度、进给速度等参数。
这些参数要根据具体情况合理调整,以确保切削效果和刀具寿命的平衡。
2.加工路径规划参数设置:UG软件可以根据工件的几何形状和加工要求自动生成加工路径,但是路径规划的参数设置也是非常关键的。
在工艺参数中,需要设置粗加工和精加工的切削余量、切削进给速度、插补方式、切削方向等。
这些参数直接决定了工件的加工质量和加工时间,合理设置可以提高加工效率和降低成本。
3.安全平台定义和碰撞检测参数设置:UG软件提供了安全平台定义和碰撞检测功能,可以帮助避免刀具与工件、夹具等碰撞造成的损坏。
在工艺参数中,需要设置安全平台的高度、安全平台的位置和碰撞检测的灵敏度等参数。
这些参数要根据具体的加工情况和机床的限制合理设置,以确保加工过程的安全性。
4.加工程序的生成和修正参数设置:UG软件可以自动生成加工程序,但是有时候需要对生成的程序进行修正。
在工艺参数中,需要设置程序生成和修正的参数,如刀具判定容差、轮廓平滑速度、轨迹段数等。
这些参数的设置要根据具体情况进行调整,以确保所生成的程序符合加工要求并且能够在机床上正确执行。
5.模拟和验证参数设置:UG软件可以进行加工路径的模拟和验证,以帮助排除可能的错误和问题。
在工艺参数中,需要设置模拟和验证的参数,如刀具轨迹的显示精度、刀具检测的方式等。
这些参数的设置要根据具体情况进行调整,以确保模拟和验证的结果准确可靠。
需要注意的是,UG加工工艺参数的设置要充分考虑工件的几何形状、材料特性、加工方式、机床的性能和限制等因素。
- 1、下载文档前请自行甄别文档内容的完整性,平台不提供额外的编辑、内容补充、找答案等附加服务。
- 2、"仅部分预览"的文档,不可在线预览部分如存在完整性等问题,可反馈申请退款(可完整预览的文档不适用该条件!)。
- 3、如文档侵犯您的权益,请联系客服反馈,我们会尽快为您处理(人工客服工作时间:9:00-18:30)。
参考刀具部分中显示相应的状态:例如,参考刀具:无。单击: o 编辑可更改当前的参考刀具。 o 选择可以获得有关当前参考刀具的信息、选择现有的刀具或创建新的刀具作为 参考刀具。 o 显示可以查看所使用的参考刀具。
如果未打开启用基于层的 IPW 首选项,您将在生成刀轨时看到一条警告信息。选择否, 打开该首选项然后继续。如果所需的用于参考操作的基于层的 IPW 信息是在一个较早的 会话中生成并保存的,那么当前操作将使用已存储的 IPW。否则,您将得到一条出错消息,
提示您重新生成参考操作。
基于层的 IPW 适用于拐角和壁上的阶梯面。该选项并不考虑切削层模式中由相邻刀路留 下的毛坯。它忽略切削区域内的刀痕,并认为其已完全移除。
3. 在型腔铣操作中,转至空间范围部分(在切削参数对话框上),选择使用基于层的 IPW 选项。
参考刀具选择不可用。软件自动选择所有符合条件的型腔铣/深度加工操作作为参考操 作。
系统将对参考操作留下的毛坯进行计算,并将本次操作的刀轨限制在该体积之内。
注意:如果参考操作更改了,则软件将基于层的操作标记为过期。
• 必须选择一个直径大于当前操作所用刀具的刀具。 • 如果参考刀具的半径与部件拐角的半径之差很小,则所要去除的材料的厚度可能会
因过小而检测不到。您可以指定一个更小的加工公差,或选择一个更大的参考刀具, 以获得更佳效果。如果使用较小的加工公差,则软件将能够检测到更少量的剩余材 料,但这可能需要更长的处理时间。选择较大的参考刀具可能是上策。 重叠距离 重叠距离将待加工区域的宽度沿切面延伸指定的距离。 按照参考刀具的直径沿切面定义的区域宽度。只有当您为参考刀具指定了偏置时,重叠距离才可 用。
部件 “部件”表示将为部件表面指定的全局余量和当前部件表面的环余量(如果有)添加到检查曲面的 余量值(上述的)中。如果将当前检查曲面用作下一子操作的部件表面,则应将“添加的余量”选 项设置为“部件”。
相交 如果检查曲面与驱动曲面相交不只一次,则可指定正确的交集来停止刀具运动。默认值是 1。
要执行的子操作 仅当存在多个检查曲面时才使用“要执行的子操作”。如果首先到达当前检查曲面,则它允许指定 跳转到哪个子操作。有七种选择:
切削参数“边界逼近”是“平面铣”和“型腔铣”中的公用参数。 当边界或岛中包含二次曲线或 B 样条时,使用边界逼近(跟随周边、跟随部件、轮廓铣)可以 减少处理时间并缩短刀轨。其原因是系统通常要对此类几何体的内部刀路(即远离岛边界或主边 界的刀路)进行不必要的处理,以满足公差限制。 边界逼近使用刀轨中第二个和第三个刀路(第一个刀路是距边界最近的刀路,第二个刀路是紧随 其后的刀路,以此类推)的指定“步距”的一部分作为“近似公差”,以允许刀具作更长的直线运动。
在底切处理中应用水平安全距离
在面铣削中,防止底切切换为打开后,避让的最小间距就应用于刀柄。水平和竖直安全距离用于 确定进刀/退刀应该超出切削区域的距离。
注意:打开防止底切后,处理时间将延长。如果没有确定底切区域,则关闭该功能以缩短 处理时间。 关闭防止底切后,系统将不会考虑底切几何体。这将导致处理竖直壁面时的公差更加宽松。在“加 工”中导入要处理的几何体时,关闭此选项有助于补偿因搬运或模型不够干净所带来的问题。 安全距离添加到任何部件/检查余量值中。例如:如果部件余量为 1 mm,检查余量为 2 mm, 并且最小安全距离为 0.5 mm,夹持器和刀柄将清除实际部件几何体的量至少为 1.5 mm, 清除检查几何体的量为 2.5 mm。
基于层的 IPW 基于层的 IPW 使用先前“型腔铣”和/或“深度加工”操作中的 2D 切削区域来确定和加工剩余材 料。这些先前的操作被称作参考操作。“基于层的 IPW”仅限于“型腔铣”或“深度铣”操作,且使用 与先前操作相同的刀轴。余料铣削和参考操作必须属于同一几何体组。 使用基于层的处理中的工件的好处
IPW 和参考刀具
默认的切削顺序是“层优先”。 使用参考刀具进行深度加工
使用参考刀具进行深度加工
使用参考刀具对陡峭部分深度加工
使用参考刀具进行深度加工和清根 参考刀具补充了清根的使用,如下所示。
深度加工和清根
防止底切通过使系统在生成刀轨时考虑底切几何体,从而防止刀柄与部件几何体之间产生摩擦。 进行型腔铣时打开防止底切后,系统将对刀柄应用完整的“水平间距”(在“进刀/退刀”方法下指 定),但如果“水平安全距离”大于刀具半径,则会应用刀具半径。当刀柄位于底切之上且距离与 刀具半径相等时,随着刀具更深地切过切削层,刀具将逐渐从底切处移走。当刀柄接触到底切时 将应用完整的“水平安全距离”。
2. 驱动圆弧 A1 直到刀具到达检查曲面 L2 与驱动曲面 A1 的切点。 3. 驱动直线 L2 直到它到达某个新的检查曲面。 如果驱动曲面余量与刀具半径之和:
• 小于圆角半径,则刀具在多个检查曲面子操作中将首先到Байду номын сангаас A1,然后执行第二个和第 三个子操作。
• 大于圆角半径,则刀具在多个检查曲面子操作中将首先到达 L2,然后跳过第二个子操 作并执行第三个子操作。
使加工过程进一步自动化。 • 您还可以将此选项与刀具夹持器检查选项结合使用,以便可以使用较短的刀具(这些刀
具刚度更大)在型腔内切削到更深的位置。在后续操作中较长的刀具仅需沿较短的刀 具由于夹持器触碰而无法到达的壁面切削即可。有关更多信息,请参阅多个长度刀具 序列。
3D IPW 生成的刀轨
使用基于层的 IPW
• “基于层的 IPW”可以高效地切削先前操作中留下的拐角和阶梯面。 • 加工简单部件时,刀轨处理时间较 3D IPW 显著减少;加工大型的复杂部件时,所需
时间更是大大减少。 • 您可以在一步操作中使用较大的刀完成较深的切削,然后在后续操作中使用同一刀具完
成深度很浅的切削以清除阶梯面。 • 与使用 3D IPW 选项相比,刀轨更加规则。 • 您可以将多个粗加工操作合并在一起,以便对给定的型腔进行粗加工和余料铣削,从而
“下一个”表示将使用紧接着的下一个子操作。此为默认值。
“跳过一个”表示将使用下一个之后的子操作。
下例对此进行了说明,其中驱动曲面余量环中有三个连续刀路子操作,并有两条相交直线 L1 和 L2 以及一条联接这两条直线的圆弧 A1:
1. 驱动直线 L1 直到: 刀具到达第一个检查曲面 A1 与驱动曲面 L1 的切点,或 刀具接触近侧的第二个检查曲面 L2。 如果首先到达 A1,则执行紧接着的下一个子操作。如果首先到达 L2,则跳过一个子 操作。
应用的重叠距离值限制在刀具半径内。 陡峭角 指定陡角,以便将切削区域进一步限制在包含在指定的陡角中的墙角。
在下图中,多个拐角不会切削到同一个最低层。软件不会一直向下加工到右角,因为它在 接触右角中的底部面之前检测到凸垫。
陡峭角
使用参考刀具进行型腔铣操作 下图是使用自动块作为毛坯的型腔铣路径,它没有参考刀具或 IPW。
检查曲面变为驱动曲面是指,将使用下一编号更高的子操作,该子操作的当前检查曲面为驱动曲 面。
检查曲面变为部件表面是指,将使用下一编号更高的子操作,该子操作的当前检查曲面为部件表 面。
指定驱动曲面将弹出一个“跳过几何体”对话框,以便用户指定面、曲线或临时平面。 将使用下 一编号更高的子操作,该子操作中指定的跳过几何体为驱动曲面。
要为此会话临时启用“基于层的 IPW”,可在首选项中设置此选项。对于此默认值,请 按如下方法导航:首选项→加工→配置→启用基于层的 IPW。
2. 如果出现提示,请重新为参考操作生成刀轨。
以下条件必须满足。参考操作必须:
o 与基于层的操作来自用一几何体组。
o 使用同一刀轴。
o 使用的刀具至少应和当前操作中的刀具同样大。
注意:第二个刀路的实际步距和近似公差分别是指定步距的 75% 和 25%。第三个刀路的 实际步距和近似公差均为指定步距的 50%。
边界逼近
注意:如果边界和所有岛中仅包含直线和弧,那么边界逼近不会缩短刀轨。
要加工上一个刀具未加工到的拐角中剩余的材料时,可使用参考刀具,如下说示。
参考刀具
如果是刀具拐角半径的原因,则剩余材料会在壁和底部面之间;如果是刀具直径的原因,则剩余 材料会在壁之间。在选择了参考刀具的情况下,操作的刀轨与其他型腔铣或深度加工操作相似, 但是会仅限制在拐角区域。 参考刀具通常是用来先对区域进行粗加工的刀具。软件计算指定的参考刀具剩下的材料,然后为 当前操作定义切削区域。 创建一个使用参考刀具的操作
注意:若将临时平面指定为检查曲面,则在平面子功能对话框处于活动状态时,当前驱动 曲面、部件表面和检查曲面会临时取消高亮显示。 停止位置 根据检查几何体的不同,停止位置可以是“近侧”、“远侧”、“在曲面上”、“驱动曲面-检查曲面相切” 或“部件表面-检查曲面相切”。
警告:用于“检查曲面”与凹陷的驱动曲面相切情形下的当前“驱动曲面-检查曲面相切”算法无 法在刀具半径稍小于驱动曲面曲率半径的情形下工作。 余量 “余量”允许指定在“检查曲面”上留下多少余量。如果该曲面的停止位置为“在曲面上”,则不会对曲 面应用余量(全局余量、环余量或单独的表面余量)。
防止底切选项还会影响刀具在底部面边的行为。有关更多信息,请参见底部面边的行为。 使用底切处理
要铣削延展部分之下的面: 1. 定义 T 型刀或夹持器/刀柄直径小于刀具直径的铣刀,该刀具将伸到底切区域。 2. 关闭切削参数对话框上策略页面中的防止底切。 3. 打开切削参数对话框上空间范围页面中的使用刀具夹持器。 4. 在进刀/退刀方法对话框中,定义要应用于刀具/刀具夹持器非切削部分的最小安全距离 (A)。
“检查曲面”允许为当前子操作最多指定五个检查曲面。要选择多个检查曲面,请设置与第一个检 查曲面相关的选项,然后选择该曲面。然后可按类似方法选择第二个检查曲面。完成后,选择“确 定”返回到“连续刀轨运动”对话框。