滚动轴承常见的失效形式及原因
常见轴承失效分析

对常见轴承失效分析的探讨摘要:轴承是社会生产最为关键的的零部件之一,同时也是最为损伤的零部件之一,所以,对于轴承的失效分析尤为重要,本文结合作者的工作经验主要阐述了轴承的失效分析,仅供参考。
关键词:轴承;失效分析一、轴承在生产中概述轴承是广泛应用于机械设备的零部件,是配套的精密零件,同时也是最易损坏的元件之一。
按轴承工作的摩擦性质来分,可分为滑动摩擦轴承(简称滑动轴承)和滚动摩擦轴承(简称滚动轴承)。
其中滚动轴承最常见,它一般由内、外两个套圈、一组滚动体和一个保持架组成。
本文结合工程案例主要分析了轴承的失效形式以及其改进的原因。
二、轴承损伤和失效的形式轴承在工作中丧失其规定的功能,导致故障或不能正常工作的现象称为失效。
轴承的失效可分为正常失效和早期失效两种。
按其损伤机理大致可分为:接触疲劳失效、磨损失效、断裂失效、塑性变形失效、腐蚀失效和游隙变化失效等几种基本形式。
1.接触疲劳失效接触疲劳失效是滚动轴承最常见的失效形式,是轴承表面受到交变应力的作用而产生的失效。
滚动轴承在高接触应力作用下,通过多次的应力循环后,在套圈或滚动体工作表面的局部区域产生小片或小块金属剥落,形成麻点或凹坑,从而引起振动,噪声增大,温度升高,磨损加剧,最终导致轴承不能正常工作的现象称为接触疲劳失效。
根据材质、工作条件、润滑条件等因素,接触疲劳失效可分为点蚀与剥落。
点蚀是由于表面出现麻点而失效,通常有非进展性和进展性之分,前者通常不影响轴承的使用,但如果使用一段时间后,由于某种原因,使点蚀不断扩展,进而形成进展性点蚀,表面会出现大面积的微剥落,最后使轴承失效。
剥落是在次表面产生疲劳裂纹,然后扩展至表面,使金属成片状脱落,可分为浅层剥落和硬化层剥落。
2.磨损失效工作过程中,轴承零件之间相对滑动摩擦导致工作表面金属不断损失的现象叫磨损。
持续的磨损会使轴承零件尺寸和形状变化,配合游隙增大,工作表面形貌恶化而丧失旋转精度,由此引起工作温度升高、振动、噪声、摩擦力矩增大等,导致轴承不能正常工作的现象叫磨损失效。
轴承损坏形式及原因分析

5、保持架的损坏
保持架的损坏,通常不易判断。若保持架坏了,轴承其它零件也 都坏掉了,这使得原因难以分析。造成架损坏主要原因有以下几种: 震动、转速太高磨损、卡死和歪斜等。
1)震动:当轴承处于震动状况下,轴承内部的力量可能导致保持 架出现疲劳裂痕,渐渐地,会使架破碎。
2)过高的转速:如果轴承以超出保持架材质所能承受的速度运转, 惯性力将使保持架破碎。
对策:油位应该略低于最下面一个滚动体的中心,轴承箱内润滑脂 填充约1/3至1/2空间。
3.油位太高或轴承箱润滑脂完全添满,这样会导致润滑剂充分搅拌而 产生高温或漏油。 对策:润滑脂添入箱内至1/2;若机油润滑,油位略低于最下方滚动 体的中心。
4.轴承间隙不适当,当有热流通过轴心时,导致内环过分膨胀。 对策:检查过热轴承的间隙是否是原始的设计范围,如果是,请改 用较大的间隙,改成C3或C3改成C4。
随着轴承不同程度的破坏,往往都是二次破坏的结果,要有效的 排除这些轴承问题,必须先观察这些轴承应用情况,然后再分析这 些损坏的原因。
轴承损坏形式及原因分析
一、轴承过热:
原因: 1. 润滑脂或机油失效或选用错误。相应的办法是:选择正确的润滑脂
或机油,检查润滑脂或机油的相容性。 2.油位太低,润滑剂从油封流失,轴承箱内润滑脂不足。
7.安装轴承前轴承箱内的碎片,异物没有清除干净。 对策:仔细清洗轴承箱和轴承本身。
8.(交叉定位) 同一轴上有两个定位轴承,而引起的不对正或由于轴热膨胀而导致 轴承内部间隙不足。 对策:调整轴承箱与端盖之间的调整垫片,使轴承箱与外环之间有 一定的间隙。
9. 轴肩摩擦到轴承密封盖,轴肩部直径不正确与保持架摩擦。 对策:重新加工轴肩,检查肩部直径及圆角。
滚动轴承失效的四种形式
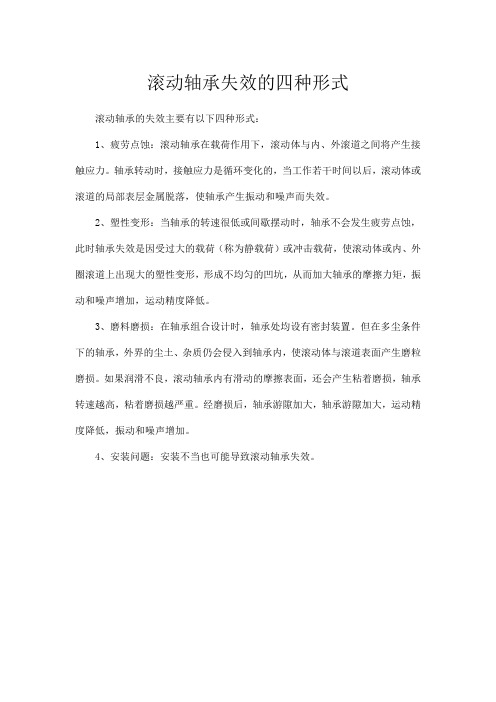
滚动轴承失效的四种形式
滚动轴承的失效主要有以下四种形式:
1、疲劳点蚀:滚动轴承在载荷作用下,滚动体与内、外滚道之间将产生接触应力。
轴承转动时,接触应力是循环变化的,当工作若干时间以后,滚动体或滚道的局部表层金属脱落,使轴承产生振动和噪声而失效。
2、塑性变形:当轴承的转速很低或间歇摆动时,轴承不会发生疲劳点蚀,此时轴承失效是因受过大的载荷(称为静载荷)或冲击载荷,使滚动体或内、外圈滚道上出现大的塑性变形,形成不均匀的凹坑,从而加大轴承的摩擦力矩,振动和噪声增加,运动精度降低。
3、磨料磨损:在轴承组合设计时,轴承处均设有密封装置。
但在多尘条件下的轴承,外界的尘土、杂质仍会侵入到轴承内,使滚动体与滚道表面产生磨粒磨损。
如果润滑不良,滚动轴承内有滑动的摩擦表面,还会产生粘着磨损,轴承转速越高,粘着磨损越严重。
经磨损后,轴承游隙加大,轴承游隙加大,运动精度降低,振动和噪声增加。
4、安装问题:安装不当也可能导致滚动轴承失效。
滚动轴承故障诊断
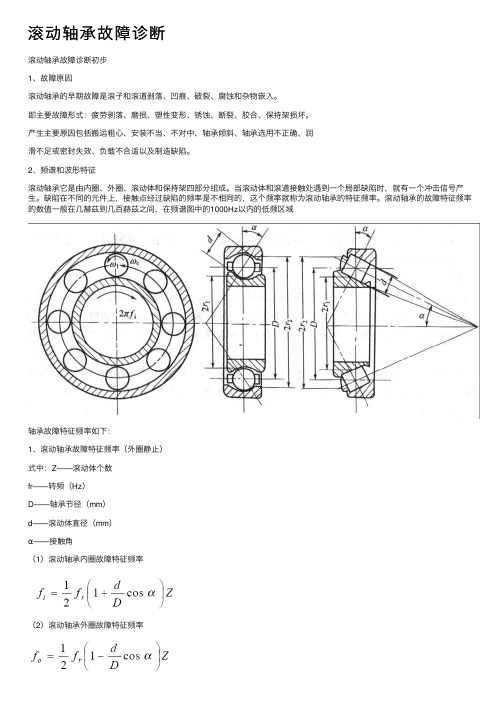
滚动轴承故障诊断滚动轴承故障诊断初步1、故障原因滚动轴承的早期故障是滚⼦和滚道剥落、凹痕、破裂、腐蚀和杂物嵌⼊。
即主要故障形式:疲劳剥落、磨损、塑性变形、锈蚀、断裂、胶合、保持架损坏。
产⽣主要原因包括搬运粗⼼、安装不当、不对中、轴承倾斜、轴承选⽤不正确、润滑不⾜或密封失效、负载不合适以及制造缺陷。
2、频谱和波形特征滚动轴承它是由内圈、外圈、滚动体和保持架四部分组成。
当滚动体和滚道接触处遇到⼀个局部缺陷时,就有⼀个冲击信号产⽣。
缺陷在不同的元件上,接触点经过缺陷的频率是不相同的,这个频率就称为滚动轴承的特征频率。
滚动轴承的故障特征频率的数值⼀般在⼏赫兹到⼏百赫兹之间,在频谱图中的1000Hz以内的低频区域轴承故障特征频率如下:1、滚动轴承故障特征频率(外圈静⽌)式中:Z——滚动体个数fr——转频(Hz)D——轴承节径(mm)d——滚动体直径(mm)α——接触⾓(1)滚动轴承内圈故障特征频率(2)滚动轴承外圈故障特征频率(3)滚动轴承滚动体特征频率(4)滚动轴承保持架特征频率2、滚动轴承故障特征频率的计算经验公式:⼆、滚动轴承故障诊断的要素滚动轴承由内圈、外圈、滚动体和保持架四部分组成,每个轴承部件对应⼀个轴承故障特征频率。
滚动轴承的故障频率分布有⼀个明显的特点,往往在低频和⾼频两个频段内都有表现。
所以在频率分析时,可以选择在这两个频段进⾏分析。
根据滚动轴承的故障形式在频域中的表现形式,将整个频域分为三个频段,既⾼频段、中频段和低频段。
l ⾼频阶段指频率范围处于2000-5000Hz 的频段,主要是轴承固有频率,在轴承故障的早期,⾼频段反映⽐较敏感;中频阶段指频率范围处于800-1600Hz 的频段,⼀般是由于轴承润滑不良⽽引起碰磨产⽣的频率范围;l 低频阶段指频率范围处于0-800Hz 的频段,基本覆盖轴承故障特征频率及谐波;在⾼频段和低频段中所体现的频率是否为轴承故障频率,还要通过其他⽅法进⾏印证加以确认。
轴承主要失效形式

轴承的主要失效形式1、剥离损伤状态:轴承在承受旋转载荷时,内圈、外圈的滚道或滚动体面由于滚动疲劳而呈现鱼鳞状的剥离现象。
原因:载荷不当;安装不良(非直线性);力矩载荷;异物进入、进水;润滑不良、润滑剂不合适;轴承游隙不适当;轴承箱精度不好、轴承箱的刚性不均、轴的挠度大;生锈、侵蚀点、擦伤和压痕(表面变形现象)。
措施:检查载荷的大小;改善安装方法、改善密封装置、停机时防锈;使用适当粘度的润滑剂、改善润滑方法;检查轴和轴承箱的精度;检查游隙。
2、剥离损伤状态:呈现出带有轻微磨损的暗面,暗面上由表及里有多条深至5~10μm,的微小裂缝,并在大范围内发生微小脱落(微小剥离)。
原因:润滑剂不合适;异物进入了润滑剂内;润滑剂不良造成表面粗糙;配对滚动零件的表面质量不好。
措施:选择润滑剂;改善密封装置;改善配对滚动零件的表面粗糙度。
3、卡伤损伤状态:卡伤是指由于在滑动面的微小烧伤汇总而产生的表面损伤,表面为滑道面、滚道面圆周方向的线状伤痕。
滚子断面的摆线状伤痕靠近滚子端面的轴环面的卡伤。
原因:过大载荷、过大预压;润滑不良;异物咬入;内圈外圈的倾斜、轴的挠度;轴、轴承箱的精度。
4、擦伤损伤状态:所谓擦伤,是在滚道面和滚动面上,由随着滚动的打滑和油膜热裂产生的微小烧伤汇总而成的表面损伤。
原因:高速轻载荷;急加减速;润滑剂不适当;水的进入。
措施:改善预压;改善轴承游隙;使用油膜性好的润滑剂;改善润滑防震;改善密封装置。
5、断裂损伤状态:由于对滚道的挡边或滚子角的局部施加冲击或过大载荷,而使其一小部分断裂。
原因:安装时受到了打击;载荷过大;跌落等;使用不良。
措施:改善安装方法(采用热装、使用适当的工具夹);改善载荷条件;轴承安装到位,使挡边受支承。
6、裂纹、裂缝损伤状态:滚道轮或滚动体有事会产生裂纹损伤。
如果继续使用,裂纹将发展为裂缝。
原因:过大过盈量;过大载荷、冲击载荷;剥落有所发展;由于滚道轮或安装构件的接触而产生的发热和微震磨损;蠕变造成的发热;锥轴的锥角不良;轴的圆柱度不良;轴台阶的圆角半径比轴承倒角大而造成与轴承倒角的干扰。
滚动轴承常见的失效形式与原因分析
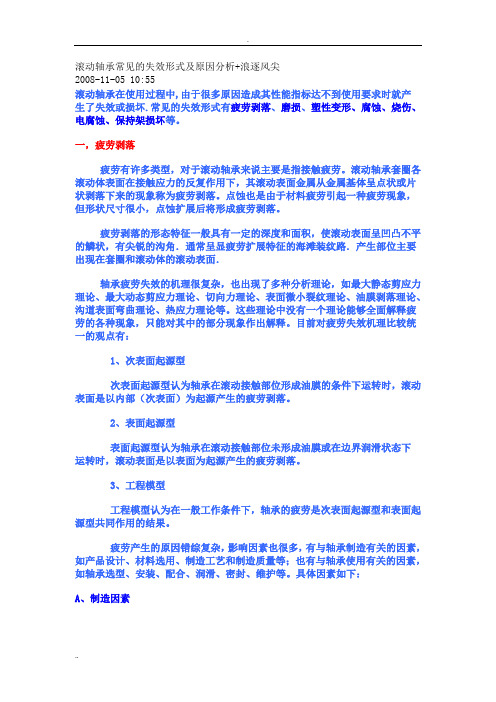
滚动轴承常见的失效形式及原因分析+浪逐风尖2008-11-05 10:55滚动轴承在使用过程中,由于很多原因造成其性能指标达不到使用要求时就产生了失效或损坏.常见的失效形式有疲劳剥落、磨损、塑性变形、腐蚀、烧伤、电腐蚀、保持架损坏等。
一,疲劳剥落疲劳有许多类型,对于滚动轴承来说主要是指接触疲劳。
滚动轴承套圈各滚动体表面在接触应力的反复作用下,其滚动表面金属从金属基体呈点状或片状剥落下来的现象称为疲劳剥落。
点蚀也是由于材料疲劳引起一种疲劳现象,但形状尺寸很小,点蚀扩展后将形成疲劳剥落。
疲劳剥落的形态特征一般具有一定的深度和面积,使滚动表面呈凹凸不平的鳞状,有尖锐的沟角.通常呈显疲劳扩展特征的海滩装纹路.产生部位主要出现在套圈和滚动体的滚动表面.轴承疲劳失效的机理很复杂,也出现了多种分析理论,如最大静态剪应力理论、最大动态剪应力理论、切向力理论、表面微小裂纹理论、油膜剥落理论、沟道表面弯曲理论、热应力理论等。
这些理论中没有一个理论能够全面解释疲劳的各种现象,只能对其中的部分现象作出解释。
目前对疲劳失效机理比较统一的观点有:1、次表面起源型次表面起源型认为轴承在滚动接触部位形成油膜的条件下运转时,滚动表面是以内部(次表面)为起源产生的疲劳剥落。
2、表面起源型表面起源型认为轴承在滚动接触部位未形成油膜或在边界润滑状态下运转时,滚动表面是以表面为起源产生的疲劳剥落。
3、工程模型工程模型认为在一般工作条件下,轴承的疲劳是次表面起源型和表面起源型共同作用的结果。
疲劳产生的原因错综复杂,影响因素也很多,有与轴承制造有关的因素,如产品设计、材料选用、制造工艺和制造质量等;也有与轴承使用有关的因素,如轴承选型、安装、配合、润滑、密封、维护等。
具体因素如下:A、制造因素1、产品结构设计的影响产品的结构设计是根据使用性能目标值来确定的,这些目标值如载荷容量、寿命、精度、可靠性、振动、磨损、摩擦力矩等。
在设计时,由于各种原因,会造成产品设计与使用的不适用或脱节,甚至偏离了目标值,这种情况很容易造成产品的早期失效。
滚动轴承常见的失效形式及原因分析
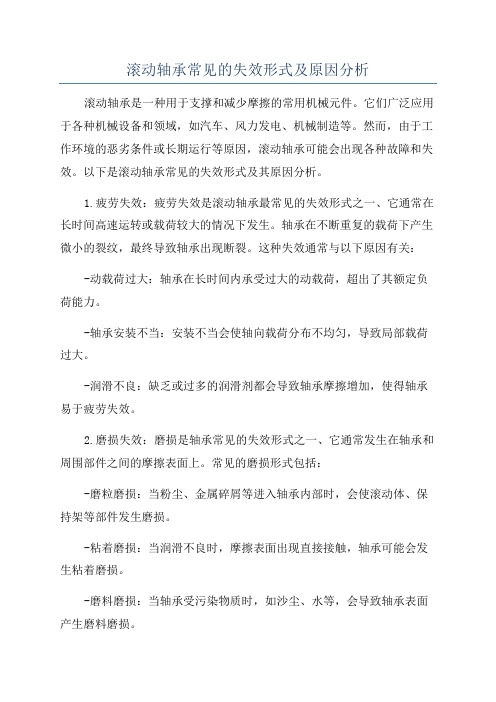
滚动轴承常见的失效形式及原因分析滚动轴承是一种用于支撑和减少摩擦的常用机械元件。
它们广泛应用于各种机械设备和领域,如汽车、风力发电、机械制造等。
然而,由于工作环境的恶劣条件或长期运行等原因,滚动轴承可能会出现各种故障和失效。
以下是滚动轴承常见的失效形式及其原因分析。
1.疲劳失效:疲劳失效是滚动轴承最常见的失效形式之一、它通常在长时间高速运转或载荷较大的情况下发生。
轴承在不断重复的载荷下产生微小的裂纹,最终导致轴承出现断裂。
这种失效通常与以下原因有关:-动载荷过大:轴承在长时间内承受过大的动载荷,超出了其额定负荷能力。
-轴承安装不当:安装不当会使轴向载荷分布不均匀,导致局部载荷过大。
-润滑不良:缺乏或过多的润滑剂都会导致轴承摩擦增加,使得轴承易于疲劳失效。
2.磨损失效:磨损是轴承常见的失效形式之一、它通常发生在轴承和周围部件之间的摩擦表面上。
常见的磨损形式包括:-磨粒磨损:当粉尘、金属碎屑等进入轴承内部时,会使滚动体、保持架等部件发生磨损。
-粘着磨损:当润滑不良时,摩擦表面出现直接接触,轴承可能会发生粘着磨损。
-磨料磨损:当轴承受污染物质时,如沙尘、水等,会导致轴承表面产生磨料磨损。
3.返现失效:轴承返现是指滚动体和滚道之间的剥离、严重滚道表面损伤或磨擦减小所引起的失效。
返现失效的原因主要有:-轴承清洗不当:清洗过程中使用的溶剂或清洁剂残留在轴承内部,导致润滑性能下降,滚动体容易返现。
-轴承热胀冷缩:当轴承受到温度变化时,轴承和轴承座之间的配合间隙有可能发生变化,导致轴承返现。
-润滑不良:缺乏或过多的润滑剂会导致轴承受到不均匀的载荷分布,容易引起轴承返现。
4.偏磨失效:偏磨是指轴承滚动体在滚道上发生偏磨,导致滚道表面形变或表面破坏。
-不均匀载荷:长期承受不均匀载荷会导致滚动体在滚道上的位置发生偏移,从而引起偏磨失效。
-润滑不良:过多或过少的润滑剂会导致轴承滚动体和滚道之间的摩擦增加,从而引起偏磨。
轴承损坏形式及原因分析

浅的坑痕,呈结晶壮的破坏壮。这是 由于润滑不良所致。例如;少油或由 于温升所造成的黏度改变,使油膜无 法将接触面分离,表面有瞬间的接触。 办法:改善润滑。
精选可编辑ppt
10
9) 微动腐蚀
轴承环与轴或轴承箱之间有相对 运动才发生的现象。这是由于太松的 配合或轴承座变形所致。
由的旋转。
精选可编辑ppt
23
10.具有两个或多个轴承的轴心耦合时,产生不正确的直线偏差或角度 歪斜。 对策;由调整片来调整正确的对位,确保轴心耦合在一条直线上, 尤其是当轴上同时有三个或多个轴承运转时,更得注意。
11.轴的直径过大,导致内环膨胀过多,减少轴承间隙。 对策: 1)研磨轴径,使轴与轴承内环之间获得一适当的配合。 2) 改用径向间隙大的轴承。
7.安装轴承前轴承箱内的碎片,异物没有清除干净。 对策:仔细清洗轴承箱和轴承本身。
8.(交叉定位) 同一轴上有两个定位轴承,而引起的不对正或由于轴热膨胀而导致 轴承内部间隙不足。 对策:调整轴承箱与端盖之间的调整垫片,使轴承箱与外环之间有 一定的间隙。
9. 轴肩摩擦到轴承密封盖,轴肩部直径不正确与保持架摩擦。 对策:重新加工轴肩,检查肩部直径及圆角。
精选可编辑ppt
26
10.外环与轴承箱扭曲,轴与内环扭曲。是由于箱孔圆角过大;没有足 够的支撑。轴肩圆角过大,没有足够支撑,两端面靠不实。 对策:重新加工箱孔圆角和轴肩的圆角。
11.不正确的安装方式,用锤直接敲到轴承上,导致轴承工作表面有磕 伤。 对策:选择正确的安装方法:套筒法、加热法、油压法等。
精选可编辑ppt
2
3、轴承的受力痕迹
通常轴承在运转工作一段时间后,在工作表面都会有明显的 受力痕迹,并非所有的痕迹的出现就表示轴承坏掉了,轴承在正常
- 1、下载文档前请自行甄别文档内容的完整性,平台不提供额外的编辑、内容补充、找答案等附加服务。
- 2、"仅部分预览"的文档,不可在线预览部分如存在完整性等问题,可反馈申请退款(可完整预览的文档不适用该条件!)。
- 3、如文档侵犯您的权益,请联系客服反馈,我们会尽快为您处理(人工客服工作时间:9:00-18:30)。
滚动轴承常见的失效形式及原因分析滚动轴承在使用过程中由于很多原因造成其性能指标达不到使用要求时就产生了失效或损坏.常见的失效形式有疲劳剥落、磨损、塑性变形、腐蚀、烧伤、电腐蚀、保持架损坏等。
一,疲劳剥落疲劳有许多类型,对于滚动轴承来说主要是指接触疲劳。
滚动轴承套圈各滚动体表面在接触应力的反复作用下,其滚动表面金属从金属基体呈点状或片状剥落下来的现象称为疲劳剥落。
点蚀也是由于材料疲劳引起一种疲劳现象,但形状尺寸很小,点蚀扩展后将形成疲劳剥落。
疲劳剥落的形态特征一般具有一定的深度和面积,使滚动表面呈凹凸不平的鳞状,有尖锐的沟角.通常呈显疲劳扩展特征的海滩装纹路.产生部位主要出现在套圈和滚动体的滚动表面.轴承疲劳失效的机理很复杂,也出现了多种分析理论,如最大静态剪应力理论、最大动态剪应力理论、切向力理论、表面微小裂纹理论、油膜剥落理论、沟道表面弯曲理论、热应力理论等。
这些理论中没有一个理论能够全面解释疲劳的各种现象,只能对其中的部分现象作出解释。
目前对疲劳失效机理比较统一的观点有:1、次表面起源型次表面起源型认为轴承在滚动接触部位形成油膜的条件下运转时,滚动表面是以内部(次表面)为起源产生的疲劳剥落。
2、表面起源型表面起源型认为轴承在滚动接触部位未形成油膜或在边界润滑状态下运转时,滚动表面是以表面为起源产生的疲劳剥落。
3、工程模型工程模型认为在一般工作条件下,轴承的疲劳是次表面起源型和表面起源型共同作用的结果。
疲劳产生的原因错综复杂,影响因素也很多,有与轴承制造有关的因素,如产品设计、材料选用、制造工艺和制造质量等;也有与轴承使用有关的因素,如轴承选型、安装、配合、润滑、密封、维护等。
具体因素如下:A、制造因素1、产品结构设计的影响:产品的结构设计是根据使用性能目标值来确定的,这些目标值如载荷容量、寿命、精度、可靠性、振动、磨损、摩擦力矩等。
在设计时,由于各种原因,会造成产品设计与使用的不适用或脱节,甚至偏离了目标值,这种情况很容易造成产品的早期失效。
2、材料品质的影响:轴承工作时,零件滚动表面承受周期性交变载荷或冲击载荷。
由于零件之间的接触面积很小,因此,会产生极高的接触应力。
在接触应力反复作用下,零件工作表面将产生接触疲劳而导致金属剥落。
就材料本身的品质来讲,其表面缺陷有裂纹、表面夹渣、折叠、结疤、氧化皮和毛刺等,内部缺陷有严重偏析和疏松、显微孔隙、缩孔、气泡、白点、过烧等,这些缺陷都是造成轴承早期疲劳剥落的主要原因。
在材料品质中,另一个主要影响轴承疲劳性能的因素是材料的纯洁度,其具体表现为钢中含氧量的多少及夹杂物的数量多少、大小和分布上。
3、热处理质量的影响:轴承热处理包括正火、退火、渗碳、淬火、回火、附加回火等。
其质量直接关系到后续的加工质量及产品的使用性能。
4、加工质量的影响:首先是钢材金属流线的影响。
钢材在轧制或锻造过程中,其晶粒沿主变形方向被拉长,形成了所谓的钢材流线(纤维)组织。
试验表明,该流线方向平行于套圈工作表面的与垂直的相比,其疲劳寿命可相差2.5倍。
其次是磨削变质层。
磨削变质层对轴承的疲劳寿命与磨损寿命有很大的影响。
变质层的产生使材料表面层的组织结构和应力分布发生变化,导致表面层的硬度下降、烧伤,甚至微裂纹,从而对轴承疲劳寿命产生影响。
受冷热加工条件及质量控制的影响,产品在加工过程中会出现质量不稳定或加工误差,如热加工的材料淬、回火组织达不到工艺要求、硬度不均匀和降低,冷加工的几何精度超差、工作表面的烧伤、机械伤、锈蚀、清洁底低等,会造成轴承零件接触不良、应力集中或承载能力下降,从而对轴承疲劳寿命产生不同程度的影响。
B、使用因素使用因素主要包括轴承选型、安装、配合、润滑、密封、维护等。
不正确的安装方法很容易造成成轴承损坏或零件局部受力产生应力集中,引起疲劳。
过大的配合过盈量容易造成内圈滚道面张力增加及零件抗疲劳能力下降,甚至出现断裂。
润滑不良会引起不正常的摩擦磨损,并产生大量的热量,影响材料组织和润滑剂性能。
如果润滑不当,即便选用再好的材料制造,加工精度再高,也起不到提高轴承寿命的效果。
密封不良容易使杂质进入轴承内部,既影响零件之间的正常接触形成疲劳源,又影响润滑或污染润滑剂。
根据疲劳产生的机理和主要影响因素,可以有针对性地提出预防措施。
如对表面起源损伤引起的疲劳,可以通过对零件表面进行表面强化处理,对次表面起源型疲劳可以通过改善材料品质等措施。
而提高零件加工质量尤其是零件表面质量、提高使用质量、控制杂质流入轴承内部、保证润滑质量等措施对预防和延缓疲劳都有十分重要的意义。
二、表面塑性变形表面塑性变形主要是指零件表面由于压力作用形成的机械损伤。
在接触表面上,当滑动速度比滚动速度小得多的时候会产生表面塑性变形。
表面塑性变形分为一般表面塑性变形和局部表面塑性变形两类。
A、一般表面塑性变形:是由于粗糙表面互相滚动和滑动,同时,使粗糙表面不断产生塑性碰撞所造成,其结果形成了冷轧表面,从外观上看,这种冷轧表面已被辗光,但是,如果辗光现象比较严重,在冷轧表面上容易形成大量浅裂纹,浅裂纹进一步发展可能(在粗糙表面区域区)导致显微剥落,但这种剥落很浅,只有几个微米,它能够覆盖很宽的接触表面。
根据弹性流体动压润滑理论,一般表面塑性变形产生的原因是由于两个粗糙表面直接接触,其间没有形成承载的弹性流体动压润滑膜.因此,当油膜润滑参数小于一定值时,将产生的一般表面塑性变形.一般油膜润滑参数值越小表面塑性变形越严重.B、局部表面塑性变形:局部表面塑性变形是发生在摩擦表面的原有缺陷附近。
最常见的原有缺陷,如压坑(痕)、磕碰伤、擦伤、划伤等。
1、压坑(痕):压坑(痕)是由于在压力作用下硬质固体物侵入零件表面产生的凹坑(痕)现象。
压坑(痕)的形态特征是:形状和大小不一,有一定深度,压坑(痕)边缘有轻微凸起,边缘较光滑。
硬质固体特的来源是轴承零件在运转中产生的金属颗粒、密封不良造成轴承外部杂质侵入。
压坑(痕)产生的部位主要在零件的工作表面上。
预防压坑(痕)的措施主要有:提高零件的加工精度和轴承的清洁度、改善润滑、提高密封质量等。
2、磕碰伤:磕碰伤是由于两个硬质特体相互撞击形成的凹坑现象。
磕碰伤的形态特征视两物体形状和相互撞击力的不同其形状和大小不一,但有一定深度,在其边缘处常有突起。
磕碰伤主要是操作不当引起的。
产生部位可以在零件的所有表面上。
预防磕碰伤的措施主要有:提高操作者的责任心、规范操作、改进产品容器的结构和增加零件的保护措施等。
3、擦伤:擦伤是两个相互接触的运动零件,在较大压力作用下因滑动摩擦产生的金属迁移现象。
严重时可能伴随烧伤的出现。
擦伤的形状不确定,有一定长底和宽度,深度一般较浅,并沿滑动(或运动)方向由深而浅。
擦伤可以在产品制造过程中产生也可以在使用过程中产生。
轴承制造成过程中的擦伤预防措施与磕碰伤的预防措施相同。
使用中的擦伤预防措施主要是从防止“打滑”方面考虑,改进产品内部结构、提高过盈配合量、调整游隙、改善润滑、保证良好接触状态等。
4、划(拉)伤划(拉)伤是指硬质和尖锐物体在压力作用下侵入零件表面并产生相对移动后形成的痕迹。
划伤一般呈线型状,有一定深度,宽度比擦伤窄,划伤的伤痕方向是任意的,长度不定。
产生部位主要在零件的工作表面和配合表面上。
而拉伤只发生在轴承内径(过盈)配合面上,伤痕方向一般与轴线平行,有一定长度、宽度和深度,并成组出现。
划伤可以在轴承制造过程中产生也可在使用中产生。
而拉伤只发生在轴承安装拆卸过程中。
预防轴承制造过程中的划伤与预防磕碰伤的措施相同。
预防使用中划伤与预防压坑(痕)的措施基本相同。
预防拉伤的措施是严格安装拆卸规程、保证配合面的清洁、安装时在配合面上适当润滑等。
综上所述,预防表面塑性变形的措施是要正确选用轴承、增强材料的耐磨性,保证润滑的有效性、注意安装方法、提高轴承密封装臵的密封性等。
三、磨损:在力的作用下,两个相互接触的金属表面相对运动产生摩擦,形成摩擦副。
磨擦引起金属消耗或产生残余变形,使金属表面的形状、尺寸、组织或性能发生改变的现象称为磨损。
磨损过程包含有两物体的相互作用、黏着、擦伤、塑性变形、化学反应等几个阶段。
其中物体相互作用的程度对磨损的产生和发展起着重要的作用。
磨损的基本形工有:疲劳磨损、黏着磨损、磨料(粒)磨损、微动磨损和腐蚀磨损等。
产生磨损的主要原因:A、异物通过了密封不良的装臵(或密封圈)进入了轴承内部。
B、润滑不当。
如润滑油中的杂质未过滤干净、润滑方式不良、润滑剂选用不当、润滑剂变质等。
C、零件接触面上的材料颗粒脱离,D、锈蚀。
如,由于轴承使用温度变化产生的冷凝水、润滑剂中添加剂的腐蚀性特质等原因形成的锈蚀。
实际中多数磨损属于综合性磨损,预防对策应根据磨损的形式和机理分别采取措施。
对于微动磨损,可以采用小游隙或过盈配合来减少使用过程中的微动磨损;可在套圈与滚动体之间采用稀润滑剂润滑或分别包装来减少运输过程的微动磨损;另外,轴承应放在无振动环境下保管,或将轴承内外圈隔离存放可以防止保管过程中产生的微动磨损。
对于黏着磨损可以采取提高加工精度、增强润滑效果等措施来解决。
对于磨料(粒)磨损,可以采用表面强化处理、表面润滑处理(如渗硫、磷化、表面软金属膜涂层等)、改善轴承密封结构、提高零件加工精度、保证润滑油过滤质量、减少制造和使用过程中对表面的损伤等方法来解决。
对于腐蚀磨损,应减少轴承使用环境中腐蚀物质的侵入、对零件表面进行耐腐蚀处理或采用耐腐蚀材料制造产品等手段来解决。
另外,还可以从产品结构设计和制造的角度进行改进,如提高零件的加工精度、减少磨削加工中产生的变质层、保证弹性流体动压润滑膜等实现预防磨损的目的。
四、腐蚀:金属与其所处环境中的物质发生化学反应或电化学反应变化所引起的消耗称为腐蚀。
金属腐蚀的形式多种多样,就金属与周围介质作用的性质来分可以分为化学腐蚀和电化学腐蚀两类。
化学腐蚀是由于金属与周围介质之间的纯化学作用引起的。
其过程中没有电流产生,但有腐蚀物质产生。
这种物质一般都覆盖在金属表面上形成一层疏松膜.化学反应形成的腐蚀机理比较简单,主要是物体之间通过接触产生了化学反应,如金属在大气中与水产生的化学反应形成的腐蚀(又称为锈蚀)电化学腐蚀是由于金属与周围介质之间产生电化学作用引起的。
其基本特点是在腐蚀的同时又有电流产生。
电化学反应的腐蚀机理主要是微电池效应。
就滚动轴承而言,产生腐蚀的主要原因有:A、轴承内部或润滑剂中含有水、碱、酸等腐蚀物质B、轴承在使用中的热量没有及时释放,冷却后形成水分C、密封装臵失效D、轴承使用环境湿度大E、清洗、组装、存放不当腐蚀产生部位:零件各表面都会有。
按程度有腐蚀斑点或腐蚀坑(洞),斑点和蚀坑一般呈零星或密集分布,形状不规则,深度不定,颜色有浅灰色、红褐色、灰褐色、黑色。