双电机驱动系统消隙技术分析
双电机驱动系统消隙技术研究与实现的开题报告

双电机驱动系统消隙技术研究与实现的开题报告一、选题背景隙死点(Dead Zone)是因为双电机驱动系统中两个电机的性能差异,造成其运动轨迹不同步,引起的一种情况。
直接控制两个电机不能有效地解决隙死点问题,而且这种问题会影响整个系统的性能和精度。
因此,实现对双电机驱动系统中隙死点的消除变得至关重要。
二、研究目的和意义本研究的目的是探讨双电机驱动系统消隙技术,并提出新的解决方案。
消隙技术的目的是消除双电机驱动系统中的隙死点,提高整个系统的性能和精度,使得电机的控制更为精准,减少误差。
此外,该研究还可以为实际应用提供可靠的理论基础。
三、研究内容本研究的主要内容包括以下几个方面:1. 双电机驱动系统的建模和分析:本研究将对双电机驱动系统进行建模和分析,探讨其动力学特性和隙死点形成的原因。
2. 隙死点消除方法的研究和比较:本研究将研究现有的隙死点消除方法,如电流环反馈、速度环反馈、位置环反馈等,并进行比较研究。
3. 新的隙死点消除方法的研究:本研究将提出一种新的隙死点消除方法,探讨其实现原理和效果。
4. 实验验证:本研究将通过仿真和实际实验来验证所提出的隙死点消除方法的有效性和可行性。
四、研究方法本研究将采用理论研究和实验验证相结合的方法。
理论研究主要是对于双电机驱动系统的建模和分析、现有隙死点消除方法的研究和对应方案的比较以及新方法的提出和分析。
实验验证主要是通过仿真和实际实验来验证所提出的隙死点消除方法的有效性和可行性。
五、预期成果本研究的预期成果包括:1.双电机驱动系统的建模和分析。
2.现有隙死点消除方法的研究和对应方案的比较。
3.一种新的隙死点消除方法的提出和分析。
4.仿真和实际实验结果的分析。
5.针对研究结果,在某些应用领域实现双电机驱动系统的隙死点消除。
六、研究计划阶段时间节点研究内容第一阶段 1-3个月双电机驱动系统的建模和分析第二阶段 4-6个月现有隙死点消除方法的研究和对应方案的比较第三阶段 7-9个月一种新的隙死点消除方法的提出和分析第四阶段 10-12个月仿真和实际实验结果的分析七、参考文献[1] 高桂勋. 电机控制技术与应用. 机械工业出版社, 2012.[2] 李培超. 控制理论与工程应用. 北京航空航天大学出版社, 2013.[3] 王清剑, 洪哲. 电机传动控制系统. 机械工业出版社, 2006.[4] Tang, X. L., Lun, L., & Lai, C. H. (2004). Dead-zone compensation for hybrid switched reluctance motor drives. IEEE Transactions on Power Electronics, 19(2), 378-389.[5] Xu, K., Shen, W. X., & Bai, L. (2004). Dead-zone compensation for permanent-magnet brushless motor drives using self-adaptive fuzzysliding-mode control. IEEE Transactions on Industrial Electronics, 51(4), 771-779.。
双电机消隙转台伺服系统的设计10

双电机消隙转台伺服系统的设计摘要:由于机械传动系统中齿轮轮齿的间隙会形成非线性误差,它影响着系统的动态性能和稳态精度。
本文针对齿轮传动中存在的齿隙非线性,以双电机驱动实现消除齿隙。
本文着重描述了该系统的控制原理和软硬件设计,根据所需消隙转矩和负载转矩、运动速度和加速度的关系,设计了实时消隙转矩补偿控制器实现系统完全消隙。
实验结果表明,采用双电机消隙的转台的定位精度得到有效的提高。
关键词:伺服系统;双电机消隙;定位精度0引言天线的性能参数如指向、波瓣宽度、增益等可以通过设计、计算和测试来确定,转台是天线性能参数测试时的主要设备,它可以为天线提供多种运动方式,并提供具体的位置信息。
但是由于机械加工时存在误差和机械磨损以及传动齿轮之间存在间隙,转台控制系统的跟踪精度和稳定性往往达不到预设的要求,所以消除齿轮间隙以提高传动精度显得尤为重要。
1实施方案1.1伺服系统硬件设计图1 双电机消隙伺服系统控制框架双电机消隙伺服系统控制框架如图所示,天线控制单元(威纶通触摸屏EMT3070A)通过自由协议和PCC间进行通信,实现速度指令、状态控制和状态信息等控制操作。
控制模块是实现系统闭环的关键环节,它接受来自编码器的转台位置参数和来自触摸屏、PCC的输入指令,对转台位置进行控制,并进行数字校正,实现转台的精确定位,同时监控转台运转情况,通过机械限位和软件监测实现转台的保护功能。
1.2双电机消隙原理采用双电机传动的方法来消除传动间隙,就要使一台电机工作在速度模式,作为消隙驱动的主动电机,输出的主动力矩和测试转台的运动方向一致;另外一台电机则工作在力矩控制模式下,作为消隙驱动的从动电机,为消隙机构的齿圈提供向后的张紧力。
图2 双电机消隙结构当转台顺时针运动时,电机1为速度控制模式,电机2为电流控制模式,两台电机分别作为主动电机和从动电机,力矩分别为M1、M2,则提供的总力矩M=M1-M2。
当转台工作在逆时针模式时,情况正好相反。
双电机驱动系统消隙技术分析
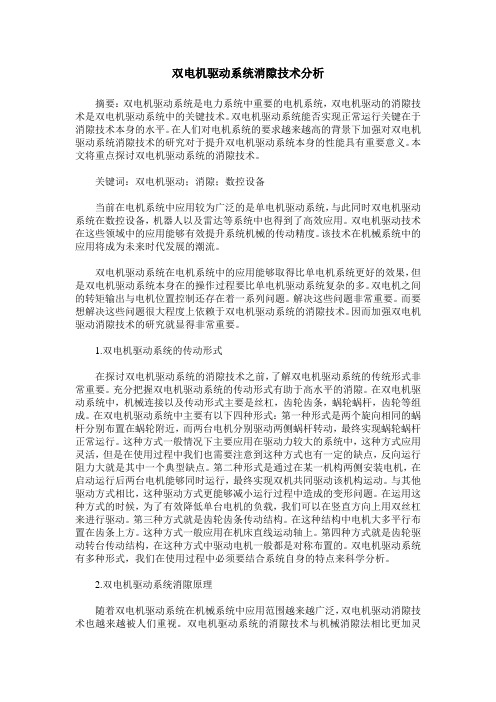
双电机驱动系统消隙技术分析摘要:双电机驱动系统是电力系统中重要的电机系统,双电机驱动的消隙技术是双电机驱动系统中的关键技术。
双电机驱动系统能否实现正常运行关键在于消隙技术本身的水平。
在人们对电机系统的要求越来越高的背景下加强对双电机驱动系统消隙技术的研究对于提升双电机驱动系统本身的性能具有重要意义。
本文将重点探讨双电机驱动系统的消隙技术。
关键词:双电机驱动;消隙;数控设备当前在电机系统中应用较为广泛的是单电机驱动系统,与此同时双电机驱动系统在数控设备,机器人以及雷达等系统中也得到了高效应用。
双电机驱动技术在这些领域中的应用能够有效提升系统机械的传动精度。
该技术在机械系统中的应用将成为未来时代发展的潮流。
双电机驱动系统在电机系统中的应用能够取得比单电机系统更好的效果,但是双电机驱动系统本身在的操作过程要比单电机驱动系统复杂的多。
双电机之间的转矩输出与电机位置控制还存在着一系列问题。
解决这些问题非常重要。
而要想解决这些问题很大程度上依赖于双电机驱动系统的消隙技术。
因而加强双电机驱动消隙技术的研究就显得非常重要。
1.双电机驱动系统的传动形式在探讨双电机驱动系统的消隙技术之前,了解双电机驱动系统的传统形式非常重要。
充分把握双电机驱动系统的传动形式有助于高水平的消隙。
在双电机驱动系统中,机械连接以及传动形式主要是丝杠,齿轮齿条,蜗轮蜗杆,齿轮等组成。
在双电机驱动系统中主要有以下四种形式:第一种形式是两个旋向相同的蜗杆分别布置在蜗轮附近,而两台电机分别驱动两侧蜗杆转动,最终实现蜗轮蜗杆正常运行。
这种方式一般情况下主要应用在驱动力较大的系统中,这种方式应用灵活,但是在使用过程中我们也需要注意到这种方式也有一定的缺点,反向运行阻力大就是其中一个典型缺点。
第二种形式是通过在某一机构两侧安装电机,在启动运行后两台电机能够同时运行,最终实现双机共同驱动该机构运动。
与其他驱动方式相比,这种驱动方式更能够减小运行过程中造成的变形问题。
双电机消隙
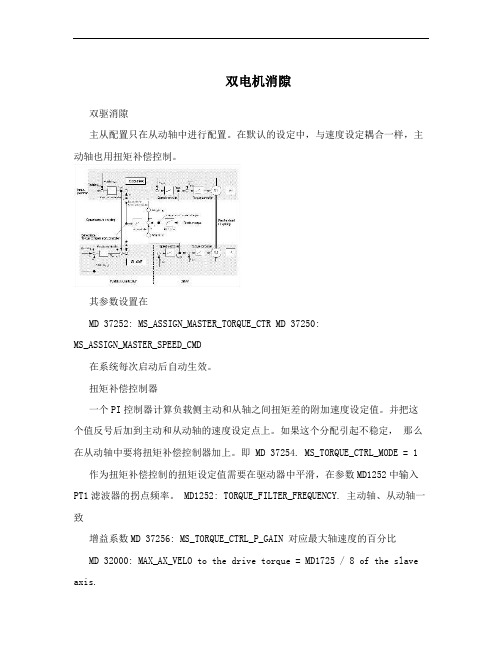
双电机消隙双驱消隙主从配置只在从动轴中进行配置。
在默认的设定中,与速度设定耦合一样,主动轴也用扭矩补偿控制。
其参数设置在MD 37252: MS_ASSIGN_MASTER_TORQUE_CTR MD 37250:MS_ASSIGN_MASTER_SPEED_CMD在系统每次启动后自动生效。
扭矩补偿控制器一个PI控制器计算负载侧主动和从轴之间扭矩差的附加速度设定值。
并把这个值反号后加到主动和从动轴的速度设定点上。
如果这个分配引起不稳定,那么在从动轴中要将扭矩补偿控制器加上。
即 MD 37254. MS_TORQUE_CTRL_MODE = 1 作为扭矩补偿控制的扭矩设定值需要在驱动器中平滑,在参数MD1252中输入PT1滤波器的拐点频率。
MD1252: TORQUE_FILTER_FREQUENCY. 主动轴、从动轴一致增益系数MD 37256: MS_TORQUE_CTRL_P_GAIN 对应最大轴速度的百分比MD 32000: MAX_AX_VELO to the drive torque = MD1725 / 8 of the slave axis.在默认设定中积分部分是无效的积分时间常数 MD 37258: MS_TORQUE_CTRL_I_TIME 以秒为单位输入。
扭矩补偿控制器的输出受参数MD 37260: MS_MAX_CTRL_VELO.的限制设定 MD 37256: MS_TORQUE_CTRL_MODE = 3或MS_TORQUE_CTRL_P_GAIN = 0,就可以使扭矩补偿控制器无效。
扭矩的分配可以通过扭矩补偿器的输入变量参数化。
从动轴的驱动扭矩可以用MD37268加权。
MD 37268: MS_TORQUE_WEIGHT_SLAVE,而主动轴的MD 37268: MS_TORQUE_WEIGHT_SLAVE, =(100 –MS_TORQUE_WEIGHT_SLAVE).当使用扭矩补偿器时机械耦合绝对是必须的,否则驱动器会从静止加速。
双电机驱动消隙技术及其在数控设备中的应用

-
PT1
++
过滤器
张力扭矩
平衡系数
机械连接
位置设定值 + -
位置
+
控制器 nset=0
位置实际值
从动轴
速度 nact 控制器 iset
扭矩 iact 控制器
电机 M2
编码 器2
图 4 主从驱动控制原理图 Fig.4 Control principle chart of master-slave drive
1 传动间隙影响数控设备的原理分析
伺服系统中传动间隙的表现形式具有多样性,为 方便分析,将伺服传动系统中所有间隙等效为1个来考 虑。用 2Δ 来表示传动间隙的宽度,传动间隙的特性如 图 1(a)所示,其中 φa 和 φb 分别为电机输入轴转角和
* “十一五”国防基础科研项目。
84 航空制造技术· 2009 年第 17 期
采用主从驱动方式,即2个伺服电机共同承担负 载。采用扭矩补偿控制器实现伺服电机之间的扭矩平 衡分配,且扭矩补偿控制器根据伺服电机的具体性能分 配相应的负载扭矩。一般地,在同一坐标进给上应尽量 采用同型号、同性能的伺服电机,以简化系统的设置。 当主、从伺服电机性能不相同时,需要根据其扭矩平衡 系数调整扭矩匹配。
传动间隙限制了系统精度的提高,而在传动间隙不 可避免的情况下,如何采取措施尽可能地消除传动间隙 就非常必要。
除了在设计传动机构时尽量减小间隙外,大多采用 机械消隙的方法,即利用消隙齿轮和弹簧预紧等方法来
(-1,j0)
幅值 Im 频率 σ
-1/N(A) G(jω)
(a)系统稳定情况
(-1,j0)
幅值 Im 频率 σ
∑M
电机 1 转矩曲线
双电机电气消隙与单电机机械消隙对比

双电机电气消隙与单电机机械消隙对比导语:本文从原理、性价比、结构等方面说明双电机电气消隙与单电机机械消隙的区别。
一)机械消隙产品(法国REDEX产品):单个电机输入两个齿轮输出形式,(REDEX产品为一个电机输入,两个减速机带齿轮输出,通过专利技术,在减速机中间加预负载,运用机械原理将减速机内部及齿轮齿条之间的背隙全部消除)如图示:二)双电机电气消隙产品(德国STOBER产品):双电机输入两个齿轮输出形式(即,两个电机输入,两个减速机带齿轮输出,运用电气控制,致使一个电机驱动的时候,另一个电机进行制动,将齿轮齿条及减速箱内部背隙全部消除)如图示:德国STOBER双电机电气消隙与其他消隙产品的比较:STOBER电气消隙系统特点如下:结构区别:双电机电气消隙原理是将其中一个电机做制动处理,从而取得预加载力。
也就是说,一个电机驱动一个电机制动,从而消除减速机及齿轮齿条的背隙;性能优越:重复定位精度可以达到0.01(1道以内);控制灵活:需要大力矩加速的时候,两个电机可以同时驱动;硬件要求:齿条和减速机的精度没有要求,可以通过电气补偿方式让消隙效果达到最好;成本控制:比同等的欧洲机械消隙产品成本低;发展前景:性能优越、精度高、成本低,在竞争日益激烈的市场中越来越受到各个厂家的青睐;同行业应用:目前中国生产大型机床,龙门镗铣、落地镗等需要做齿条传动消隙处理的机床基本上都使用的是STOBER双电气消隙产品,主要客户应用情况见部分客户列表REDEX机械式消隙系统特点如下:结构区别:单电机机械消隙实际是通过反向的扭动其中一个齿轮来获取预加载力,也就相当于将一个齿轮固定,在另一个齿轮上加了一个扭力弹簧;性能一般:只能满足一般应用(重复定位精度一般都在0.02以上);模式固定:机械方式预设的单一工作模式,不能根据实际需求做调整;硬件要求:减速机和齿条的精度要求比较高,硬件产品的精度越高消隙效果越好,相应的增加了硬件的成本;发展现状:机械消隙产品设计巧妙,通过简单的结构消除了齿轮与齿条之间的背隙,随着社会发展,机床精度要求越来越高,机械消隙产品已经不能满足应用,越来越多的被高精度、低成本的电气消隙产品所取代。
双电机驱动机床进给系统消隙控制
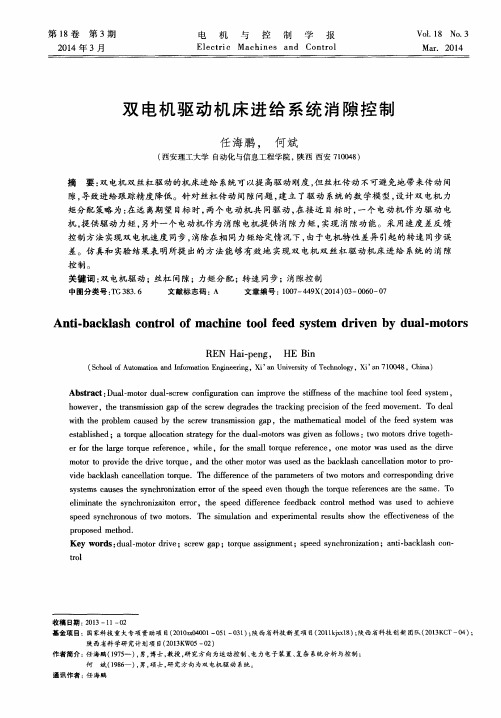
( S c h o o l o f A u t o ma t i o n a n d I n f o r m a t i o n E n g i n e e r i n g , X i ’ a n U n i v e r s i t y o f T e c h n o l o g y , X i ’ a n 7 1 0 0 4 8 ,C h i n a )
控制。
关 键词 : 双 电机驱 动 ;丝杠 间隙 ;力矩分 配 ; 转 速 同步 ;消 隙控 制
中 图分 类 号 : T G3 8 3 . 6 文献标志码 : A 文章 编 号 : 1 0 0 7 — 4 4 9 X( 2 0 1 4 ) 0 3 — 0 0 6 0 - 0 7
An t i - b a c k l a s h c o n t r o l o f ma c h i n e t o o l f e e d s y s t e m d r i v e n b y d u a l - mo t o r s
Abs t r a c t: Du a l — mo t o r d u l— a s c r e w c o n f i g u r a t i o n c a n i mp r o v e t h e s t i f f n e s s o f t h e ma c h i ne t o o l f e e d s y s t e m,
h o we v e r ,t h e t r a n s mi s s i o n g a p o f t h e s c r e w d e g r a d e s t h e t r a c k i n g p r e c i s i o n o f t h e f e e d mo v e me n t .T o d e a l
双电机电气消隙

双电机电气消隙
未来数控机床的发展趋势主要是大型和重型,因而机床的行程越来越长,对精度的要求也就越来越高。
要消除齿轮齿条传动中产生的背隙,有两种方式,一是:机械消隙,二是双电机电气消隙。
机械消隙是单个电机输入两个齿轮输出的形式,目前有法国的REDEX.而双电机消隙属于双电机输入两个齿轮输出的形式。
双电机消隙目前有德国的STOBER以及台湾的SunUs等。
双电机消隙就是两个电机通过齿轮与赤道仪的主齿轮啮合,并按双电机消隙控制曲线进行驱动,永远不会出现两个电机输出转矩同时为零的情况,即任何时候两个电机至少有一个会对主齿轮施加不为零的转矩,在此转矩的作用下,主齿轮的运动间隙就不可能存在。
当然,此转矩必须大于转动链本身的摩擦力矩。
在实际消隙方式下,当系统需要的输出合力矩为零(静止)时,两通道电机的电枢电流为±Io(消隙偏置电流),其输出力矩大小相等方向相反;当系统需要的输出合力矩增加时,两通道电机的电枢电流随图二的曲线变化,其中一个通道的输出力矩将继续增加,另一个通道的输出力矩逐渐减小至零再增加,由阻力源变为动力源
双电机消隙的优势。
相对于机械消隙,双电机消隙具有性能上的优势,重复定位精度可达到0.01;控制灵活,需要加大扭力是,两个电机可
以同时驱动,而两个电机反方向驱动是可消除背隙;成本控制,由于是同时使用两个伺服电机,股伺服电机的型号可选用较小的,这样成本不会高于机械消隙;双电机消隙具有良好的发展前景,由于其性能优越,精度高,成本低,在竞争日益激烈的市场中越来越受到各大厂家的青睐。
- 1、下载文档前请自行甄别文档内容的完整性,平台不提供额外的编辑、内容补充、找答案等附加服务。
- 2、"仅部分预览"的文档,不可在线预览部分如存在完整性等问题,可反馈申请退款(可完整预览的文档不适用该条件!)。
- 3、如文档侵犯您的权益,请联系客服反馈,我们会尽快为您处理(人工客服工作时间:9:00-18:30)。
双电机驱动系统消隙技术分析
摘要:双电机驱动系统是电力系统中重要的电机系统,双电机驱动的消隙技术是双电机驱动系统中的关键技术。
双电机驱动系统能否实现正常运行关键在于消隙技术本身的水平。
在人们对电机系统的要求越来越高的背景下加强对双电机驱动系统消隙技术的研究对于提升双电机驱动系统本身的性能具有重要意义。
本文将重点探讨双电机驱动系统的消隙技术。
关键词:双电机驱动;消隙;数控设备
当前在电机系统中应用较为广泛的是单电机驱动系统,与此同时双电机驱动系统在数控设备,机器人以及雷达等系统中也得到了高效应用。
双电机驱动技术在这些领域中的应用能够有效提升系统机械的传动精度。
该技术在机械系统中的应用将成为未来时代发展的潮流。
双电机驱动系统在电机系统中的应用能够取得比单电机系统更好的效果,但是双电机驱动系统本身在的操作过程要比单电机驱动系统复杂的多。
双电机之间的转矩输出与电机位置控制还存在着一系列问题。
解决这些问题非常重要。
而要想解决这些问题很大程度上依赖于双电机驱动系统的消隙技术。
因而加强双电机驱动消隙技术的研究就显得非常重要。
1.双电机驱动系统的传动形式
在探讨双电机驱动系统的消隙技术之前,了解双电机驱动系统的传统形式非常重要。
充分把握双电机驱动系统的传动形式有助于高水平的消隙。
在双电机驱动系统中,机械连接以及传动形式主要是丝杠,齿轮齿条,蜗轮蜗杆,齿轮等组成。
在双电机驱动系统中主要有以下四种形式:第一种形式是两个旋向相同的蜗杆分别布置在蜗轮附近,而两台电机分别驱动两侧蜗杆转动,最终实现蜗轮蜗杆正常运行。
这种方式一般情况下主要应用在驱动力较大的系统中,这种方式应用灵活,但是在使用过程中我们也需要注意到这种方式也有一定的缺点,反向运行阻力大就是其中一个典型缺点。
第二种形式是通过在某一机构两侧安装电机,在启动运行后两台电机能够同时运行,最终实现双机共同驱动该机构运动。
与其他驱动方式相比,这种驱动方式更能够减小运行过程中造成的变形问题。
在运用这种方式的时候,为了有效降低单台电机的负载,我们可以在竖直方向上用双丝杠来进行驱动。
第三种方式就是齿轮齿条传动结构。
在这种结构中电机大多平行布置在齿条上方。
这种方式一般应用在机床直线运动轴上。
第四种方式就是齿轮驱动转台传动结构,在这种方式中驱动电机一般都是对称布置的。
双电机驱动系统有多种形式,我们在使用过程中必须要结合系统自身的特点来科学分析。
2.双电机驱动系统消隙原理
随着双电机驱动系统在机械系统中应用范围越来越广泛,双电机驱动消隙技术也越来越被人们重视。
双电机驱动系统的消隙技术与机械消隙法相比更加灵
活,效果也更好。
采用双电机驱动系统消隙技术能在不需要专门的消隙机构发挥作用的前提下实现对数控机床控制的零间隙传动。
在双电机驱动系统中主要是采用2套伺服电机组成的联动系统。
在双电机驱动系统中主要是通过采用2个方向完全相反的伺服电机来进行消隙的。
在双电机驱动系统中,如果系统反向运行,此时正向驱动电机就能够输出一个能够消除间隙的正向扭矩,从而最终达到消隙的目的;相反,当系统正向运行时,反向驱动电机就能输出一个能够消除间隙的反向扭矩,从而实现消隙。
这就是双机驱动系统系统消隙的原理。
在双电机驱动系统中无论是系统正向还是反向运行,都会有一个伺服电机与之相对应。
运用这种方式驱动,电机本身的负载功率会显著增强。
这种方式虽然能够有效消隙,但是造价却非常昂贵,因而这种方式在实际操作中不常见。
为了更加有效地消隙,有必要采用一种经济价值更加低廉的方案。
在双电机驱动系统中我们发现当系统本身只是单方向运行的时候,此时驱动扭转方向不会发生变化,也就不会出现间隙问题,也就是说只有在驱动扭矩的方向发生变化的时候,间隙问题才会出现。
因此在双电机驱动系统中我们就可以通过对伺服系统协调控制,让2个伺服电机来共同承担系统负载。
采用这种方式既能够有效的消除间隙,同时还可以降低整个系统的负载,因而这种方式在实际操作过程中应用较多。
上文提到双电机驱动系统消隙技术与机械消隙法相比,有着显著优点。
接下来我们就来详细分析双电机驱动系统消隙技术的优点。
在长期实践中我们发现消隙技术具有以下四个优点:一是双机驱动系统结构更加简单,成本也非常低。
在使用过程中不需要专门的机械消隙机构。
后期维护费用也将有效降低。
二是双机驱动系统精度更高。
双机驱动系统消隙技术能够有效的消除定位精度误差,从而提高系统的精度。
三是它能够有效解决瞬态误差。
四是双机驱动系统消隙技术是由两个电机共同来承担负载的,因而在使用过程中我们完全可以选择那些小容量的伺服驱动器以及电机。
3.消隙技术的应用过程中的注意事项
双电机驱动消隙技术如今在数控领域得到了广泛应用。
在应用过程中我们对于有些事项必须要保持高度重视:一是在双机驱动系统中在消隙期间,两台电机基本上是处于异齿啮合状态,也就是说此时如果一台电机输出拖动扭矩,另外一台电机就不能施加拖动扭矩。
二是要慎重选择电机的功率和转矩。
这两个重要指标都会对双电机驱动消隙技术造成影响。
我们在应用过程中必须要对这两个问题保持高度重视,要学会通过多种手段来使这一技术能够发挥最优水平。
当前双电机驱动系统在数控领域中得到了广泛应用,而今虽然单电机系统是主流,但是双电机驱动系统有着单电机系统不可比拟的优点。
在双电机驱动系统运行过程中间隙问题是一个非常重要的问题。
转矩间隙最终会影响到整个系统的运行,同时也会使得产品发生变形。
因而我们必须要高度重视双电机驱动系统的消隙技术。
本文详细分析了双电机驱动系统的转动形式,而后又深入分析了双电机驱动系统消隙的原理,最后分析了双电机驱动系统消隙技术在应用过程中的需
要注意的事项。
双电机驱动消隙技术比机械消隙法更具优势,运用这种方法能够有效地消隙。
参考文献:
[1]程登元.一种双电机消隙伺服系统[J].雷达科学与技术,2009(5).
[2]国力,龚时华,李斌.七轴五联动螺旋桨加工机床控制系统关键技术[J].华中科技大学学报(自然科学版),2007(33).
[3]志兵,孙志强.双电动机消除驱动在大重型机床上的应用[J].制造技术与机床,2010(4).。