钢铁企业能源管理系统及节能技术汇总
浅谈钢铁企业能源管理系统的建设与应用
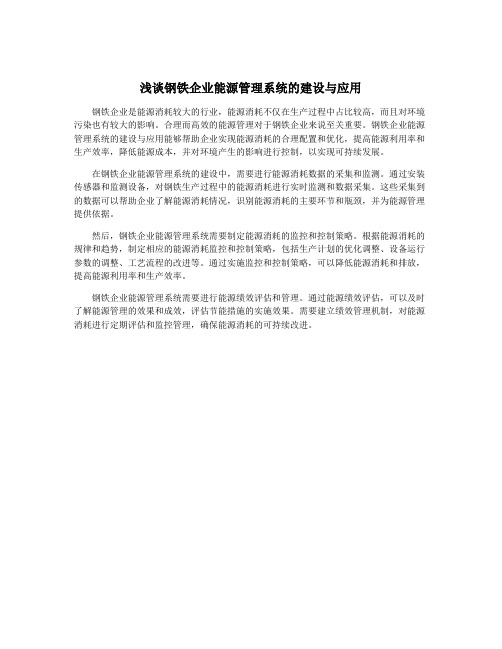
浅谈钢铁企业能源管理系统的建设与应用
钢铁企业是能源消耗较大的行业,能源消耗不仅在生产过程中占比较高,而且对环境污染也有较大的影响。
合理而高效的能源管理对于钢铁企业来说至关重要。
钢铁企业能源管理系统的建设与应用能够帮助企业实现能源消耗的合理配置和优化,提高能源利用率和生产效率,降低能源成本,并对环境产生的影响进行控制,以实现可持续发展。
在钢铁企业能源管理系统的建设中,需要进行能源消耗数据的采集和监测。
通过安装传感器和监测设备,对钢铁生产过程中的能源消耗进行实时监测和数据采集。
这些采集到的数据可以帮助企业了解能源消耗情况,识别能源消耗的主要环节和瓶颈,并为能源管理提供依据。
然后,钢铁企业能源管理系统需要制定能源消耗的监控和控制策略。
根据能源消耗的规律和趋势,制定相应的能源消耗监控和控制策略,包括生产计划的优化调整、设备运行参数的调整、工艺流程的改进等。
通过实施监控和控制策略,可以降低能源消耗和排放,提高能源利用率和生产效率。
钢铁企业能源管理系统需要进行能源绩效评估和管理。
通过能源绩效评估,可以及时了解能源管理的效果和成效,评估节能措施的实施效果。
需要建立绩效管理机制,对能源消耗进行定期评估和监控管理,确保能源消耗的可持续改进。
钢铁冶金流程节能实现及技术要点研究

钢铁冶金流程节能实现及技术要点研究【摘要】钢铁冶金是工业制造中一项重要的过程,而节能在这一过程中的意义也变得愈发重要。
本文通过对节能实现的现状分析和节能技术的应用现状的探讨,介绍了节能技术在钢铁冶金流程中的应用情况。
对节能技术的研究进展和关键技术要点进行了讨论,探讨了节能技术的推广与应用以及未来的发展方向。
通过对于钢铁冶金节能的重要性进行总结,强调了节能对环境和资源的重要意义。
通过本文的研究,可以为钢铁冶金行业的节能实践提供一定的参考和指导,推动钢铁行业不断迈向更加清洁、高效的方向。
【关键词】钢铁冶金、节能、实现、技术、要点、研究、流程、现状分析、应用现状、进展、关键技术、探讨、推广、应用、发展方向、意义、总结1. 引言1.1 钢铁冶金的重要性钢铁冶金作为现代工业中的重要产业之一,扮演着不可或缺的角色。
钢铁是一种基础材料,广泛应用于建筑、制造、交通运输等各个领域。
它的质量和产量直接影响到国民经济的发展和国家的安全。
在建设工程中,钢铁是支撑着高楼大厦的骨架;在交通运输中,钢铁是构建交通运输设施的主要材料;在制造业中,钢铁是制造各种设备和机械的基础。
随着经济的发展和科技的进步,钢铁冶金行业也在不断发展和改进。
钢铁冶金工艺的创新和提高效率,不仅可以提高生产效益,还能降低能源消耗和环境污染。
钢铁冶金的重要性不仅在于满足国民经济的需求,更在于推动节能减排,推动绿色可持续发展。
1.2 节能在钢铁冶金中的意义在钢铁冶金工业中,节能是一项至关重要的任务。
钢铁冶金作为国民经济的基础产业,其能耗巨大,占据了工业能耗的相当比重。
实现节能在钢铁冶金中具有重要意义。
节能可以有效减少能源消耗,降低生产成本。
钢铁生产过程中需要大量能源,包括电力、燃料等,而能源价格的上涨直接影响了生产成本。
通过节能技术的应用,可以减少能源消耗,降低生产成本,提高企业的竞争力。
节能可以降低对环境的污染。
钢铁冶金工业是重要的环境污染源,包括废气、废水、废渣等。
钢铁企业能源管理体系建设及节能途径
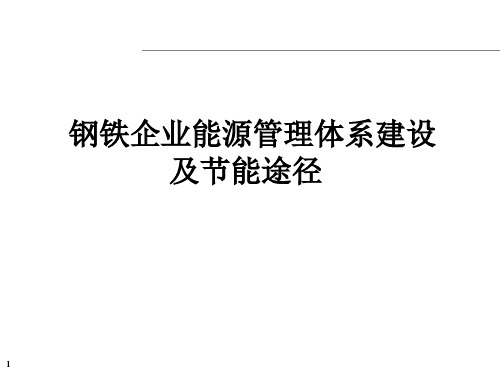
7
一.钢铁企业能源管理的组织机构模式
(一)钢铁企业能源管理组织机构
目前钢铁企业最Βιβλιοθήκη 见的能源管理组织机构是公司三级 能源管理网络(也称三级节能网络)。
一级 公司能源管理委员会
公司能源决策机构,确定能源方针、 节能目标。下设能源办公室,负责 能委会日常工作
二 级 生产厂(部)能源管 理领导推进小组
“十一五”期间,中国钢铁工业的节能减排成就
6
引言 钢铁与绿色
引言:钢铁与绿色 第一章:钢铁企业能源管理体系建设
一.钢铁企业能源管理的组织机构模式 二.能源管理体系建设必要性和主要思路 三.宝钢能源管理体系实施案例 四.能源管理体系实施要点与建议
第二章:钢铁企业节能途径及发展趋势
一.钢铁企业节能途径 二.钢铁企业节能工作发展趋势
情况并作出评价;分析能源
目标值管理:公司能源管理部门负责一级目 标,对二、三级目标实施管理;各生产厂部负责 二级目标,对三、四级目标实施管理;各生产车 间、设备负责三、四级的管理。
管理指标完成情况,寻找下 步改善指标的措施和建议, 供领导决策。
11
引言:钢铁与绿色 第一章:钢铁企业能源管理体系建设
1.能源管理工作涉及面较小,还没有发动全体员工将能源管理工作融入到本职工作中 去,仅靠能源管理人员能力效果有限。 2.能源管理指标均已以能源消耗为范围,没有将对其有较大影响的生产技术、设备管 理指标作为相关职能部门的管理要求进行控制,从而难以发挥其他职能部门的作用, 形成能源管理部门单打独斗的局面。 3.能源管理还是以事后管理为主,没有开展事前、过程管理,影响节能效果。 4.能源管理偏重指标、数字管理,对节能项目管理没有具体、专有的推进流程,尤其 对投资较小的项目管理、推进困难。 5.能源管理工作在市场经济条件下与能源成本、企业效益结合不够。
冶金企业能源管理-第二章 能源管理模式
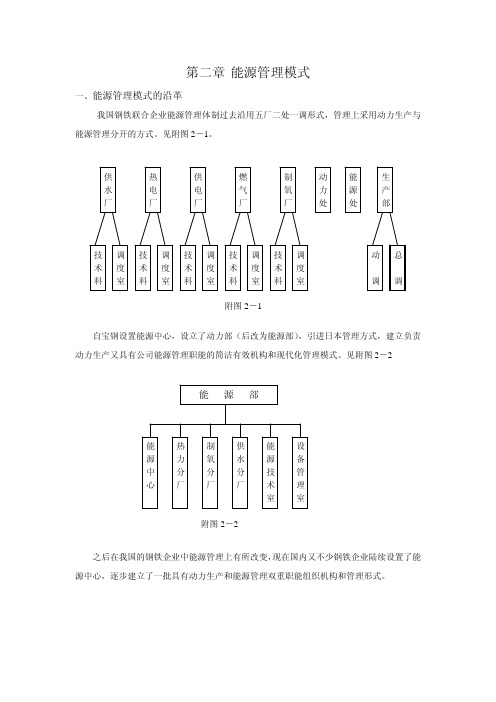
第二章 能源管理模式一、能源管理模式的沿革我国钢铁联合企业能源管理体制过去沿用五厂二处一调形式,管理上采用动力生产与能源管理分开的方式。
见附图2-1。
自宝钢设置能源中心,设立了动力部(后改为能源部),引进日本管理方式,建立负责动力生产又具有公司能源管理职能的简洁有效机构和现代化管理模式。
见附图2-2之后在我国的钢铁企业中能源管理上有所改变,现在国内又不少钢铁企业陆续设置了能源中心,逐步建立了一批具有动力生产和能源管理双重职能组织机构和管理形式。
附图2-1附图2-2二、能源管理体制及业务分工按照新型的能源管理体制,采用现代化管理模式,需要制定公司能源方针、节能目标决策公司能源重大事项,为此公司应建立公司能源管理委员会,并明确能源部能源管理职能。
1、公司能源管理委员会(1)组织机构能源管理委员会设主任一名,副主任两名,及委员若干。
主任一般由主管生产的副总经理或总工程师担任,副主任由总经理生产助理和能源部部长担当。
生产部部长、设备部部长、安环部部长、技术部部长、物质部部长、办公室主任及炼铁厂厂长、炼钢厂厂长、焦化厂厂长、各轧钢厂厂长等为委员。
见图2-3附图2-3能源管理委员会下设办公室,设置在能源部。
具体工作由能源管理高级工程师(或工程师)担当。
(2)能源管理委员会的任务能源管理委员会是公司能源决策机构。
其任务是:●制订公司能源方针,节能目标。
●审议公司能源中长期规划,年度计划,年度总结,决定主要节能措施。
●审定、部署能源重大项目,解决重大问题。
一般每半年召开一次委员会会议。
特殊需要时另定。
(3)能源管理委员会办公室能源管理委员会办公室设置在能源管理室,负责能源管理委员会日常工作。
具体负责:●贯彻上级能源方针。
●编制能源节约目标、能耗指标。
●筹办能源管理委员会会议。
●推广节能先进技术,调研能源重大问题,提出解决措施。
●编制公司能源平衡表。
●定期召开能源联络员会议。
(4)能源联络员制度为了做好各部门的能源管理工作,同时要求各部门设置一名专职(或兼职)能源联络员。
钢铁企业能耗分析及节能对策研究

一、中国十大钢铁企业能耗分析
中国十大钢铁企业的能耗较高,其中高炉炼铁的能耗占据了钢铁生产总能耗 的较大比例。根据相关数据,2019年我国钢铁行业重点大中型企业吨钢综合能耗 为604.52千克标准煤/吨,比上年下降3千克标准煤/吨;生铁产量为8.07亿吨, 同比增长9.7%;粗钢产量为9.95亿吨,同比增长10.8%。可以看出,中国钢铁行 业的能源消耗总量和钢铁产量之间存在着较为密切的关系。
钢铁企业能耗分析及节能对策 研究
01 一、背景介绍
目录
02 二、能耗分析
03 三、节能对策
04 四、案例分析
05 五、结论
06 参考内容
一、背景介绍
钢铁企业是全球能源消耗的重要行业之一,其能源消耗主要集中在炼钢、炼 铁、轧钢等生产环节。由于能源价格的上涨和环保政策的压力,钢铁企业的能源 消耗问题越来越受到。因此,研究钢铁企业的能耗现状和存在的问题,探讨节能 对策,对提高钢铁企业的竞争力、实现可持续发展具有重要意义。
3、提高员工节能意识
钢铁企业应该加强员工节能意识的培养和教育,让员工充分认识到节能降耗 的重要性和意义。同时,要建立健全的节能考核和激励机制,鼓励员工积极参与 节能工作,形成全员参与的节能文化。
4、优化生产计划和物流管理
钢铁企业应该优化生产计划和物流管理,合理安排生产计划和生产流程,避 免生产过程中的浪费和损失。同时,要采用先进的物流管理技术和设备,提高物 流运输效率和质量,降低物流成本和能源消耗。
5、加强废弃物回收和利用
钢铁企业应该加强废弃物的回收和利用,尽可能减少废弃物的排放和对环境 的污染。同时,可以利用废弃物进行二次资源的开发和使用,提高资源利用率和 经济效益。例如,可以利用炼钢渣生产矿渣水泥等建筑材料等。
钢铁企业节能管理制度

----------------------------精品word 文档值得下载值得拥有--------------------------------------------------企业根据生产耗能设备对燃料的实际要求,对燃料实行新型管理模式,即围绕管理目标,对燃料管理的几个环节,计划、采购、结算、储存、运行,做到事前燃料技术标准明确,费用有预算,事中风险控制,进程动态监控,事后经济活动分析,为此特制定企业燃料管理制度如下:1、企业生产所需要的一切燃料,其技术标准由企业运行部门提出,会同企业节能主管部门共同编制,并经企业节能领导小组主管总工程师批准后执行。
2、企业燃料的经营部门(供应部门)必须严格按照企业审定的燃料技术标准进行市场采购,通过燃料市场的信息调研,制定燃料采购计划,并做好燃料计划的实施,燃料合同的签订,合同的正常履行等管理,保证生产用燃料的需求。
3、企业燃料的经营部门应认真做好燃料进厂的检斤、检质管理,落实燃料验收制度,进厂的每车(船)燃料都要过秤检斤,抽样化验,做好格式化记录,并及时对照计划、合同,核对数量、品种和质量。
4、企业燃料的经营部门对燃料入厂全过程发出的有关燃料的各种经营与技术文件必须随实物同时到达并存档,作为运行与结算的依据。
5、企业燃料的运行部门应及时配合经营部门做好入厂燃料检斤、检质管理,同时还要做好入炉煤的检斤、检质。
6、做好燃料的贮存管理,按照进厂燃料的种类、规格、分区存放,标明燃料特点,并设专人管理油库和煤场,保持煤场设施完善与完好。
7、企业节能主管部门应会同运行部门根据进厂的元煤情况,时常研究,配煤掺烧管理,在企业当前负荷情况下,将多种煤质的煤按照一定的比例进行配煤燃烧。
8、做好库存管理,定期进行库存盘点,建立元煤库存盘点台帐,做到帐、物相符,同时对进煤、煤耗、存煤进行统计分析。
9、执行好燃料分析化验制度,定期将燃料取样,进行化验分析,建立燃料技术档案。
浅谈钢铁企业能源管理系统的建设与应用
浅谈钢铁企业能源管理系统的建设与应用随着工业的快速发展,钢铁企业成为了国家经济的重要支柱产业之一。
而在钢铁生产过程中,能源消耗的比例非常大,因此建设和应用能源管理系统成为了钢铁企业实现节能减排的重要手段。
一、能源管理系统的定义和意义能源管理系统是指通过科学的方法,对企业的能源运行和使用进行规划、管理、监测、评估并不断改进的一种管理体系。
能源管理系统不仅可以帮助企业提升能源利用效率,降低成本,提高质量和产品竞争力,还可以缓解能源供给压力,降低碳排放,为可持续发展做出贡献。
1.确定能源管理目标和方案根据企业的实际情况,制定能源管理目标,制定相应的能源管理计划和方案,明确任务、责任及分工。
能源管理方案必须符合国家和地方有关能源法律法规,同时也要满足企业的生产经营需要,尽可能地减少能源和经济的消耗。
2.建立能源监测系统建立合理、完整的能源监测系统,包括现场监测和远程监测,实现对能源的全面监控和数据采集。
通过数据分析,发现能源消耗的瓶颈和优化机会,为采取节能措施提供依据。
3.实施能源效率分析根据能源使用数据和生产数据,分析能源消耗状况和生产过程的能源效率,发现问题和优化机会,制定改进方案,提高能源利用效率,降低能源消耗成本。
4.制定能源管理措施与计划根据能源效率分析和能源管理目标,制定能源管理措施与计划,包括节能技术的研发与应用、能源设备的选型与更新、能源管理制度的完善,以及员工培训和参与等方面。
5.实施能源管理与评估实施能源管理措施和计划,并通过持续监测和评估,不断完善和提高能源管理水平,达到节能减排和经济效益的最大化。
1.提高能源利用效率和经济效益,降低成本和排放通过优化能源消耗结构,提高能源利用效率和节能减排水平,降低能源成本和生产成本,不仅可以提高企业的经济效益,还可以减少对能源的需求,降低对环境的影响,贯彻可持续发展理念。
2.促进科技创新和技术进步在能源管理系统的建设和应用过程中,需要结合先进的技术和管理理念,推动科技创新和技术进步,提高企业的核心竞争力和市场竞争力。
浅谈钢铁企业能源消耗分析及节能措施
浅谈钢铁企业能源消耗分析及节能措施作为第二次工业革命最重要的产物之一,钢铁工业在国民经济中占据的地位不言而喻,但是发展钢铁工业仍然有很多限制因素,譬如污染排放、能源消耗等问题,仍然制约着国家钢铁企业的发展规模,因此国家把钢铁工业节能减排工作作为重点产业进行开发。
和西方发达国家相比,我国的钢铁工业节能减排方面做的还不够。
因此为了进一步降低钢铁工业的能耗和排放,选择更合适的节能策略便成为我们应该考虑的问题。
标签:钢铁企业;能源消耗;节能措施1 钢铁企业节能减排的重要意义1.1 节能减排工作是企业社会责任的体现坚持节能减排战略是我国工业发展的重要原则之一,钢铁工业作为一种高能耗高排放又必不可少的国民经济支柱工业之一,更加引起国家人民和有关部门的重视。
事实上钢铁工业正是以为其基础的高排放,所以钢铁工业的节能减排潜力巨大,能够在我国的节能减排可持续发展战略计划中担负起更大的责任,完成更重要的任务。
因此,我国钢铁部门有关负责人要提高认识,优化思想,争取做好节能减排工作。
1.2 节能减排工作是可持续发展的必由之路从改革开放到现在,我国的经济发展水平和工业发展水平以一种极高的速度发展着,同时因为自然环境各种条件的制约,高速发展的背后要面临资源短缺、生态破坏的难题,为了提高人民生活质量和生活体验,钢铁工业提高节能减排水平已经势在必行。
2 炼钢厂能耗现状分析2.1 炼钢厂能源消耗构成目前情况下,我国炼钢工业消耗能源主要是以下两个方面,一种是直接的原材料能源消耗,譬如焦炉煤气、氧气、电、蒸汽、压缩空气和水等钢铁工业发展中必不可少的原材料,另一种是间接的消耗,譬如铁水、废钢、石灰、铁矿、耐火材料等发展工业中不可避免的损耗。
因此要完成节能降耗任务,钢铁工业就应该从这两方面入手提高材料利用率,降低消耗。
2.2 炼钢厂工序能耗构成分析转炉工序中的能源消耗主要是由原料消耗和回收两方面构成的,能源消耗的主体是氧气、焦炉煤气、电、蒸汽、压缩空气和水,而回收部分主要是通过对蒸汽的回收完成的。
钢铁行业能源管理体系实施指南
钢铁行业能源管理体系实施指南1.钢铁行业能源管理体系实施指南包括能源消耗分析和节能技术应用。
The implementation guidelines for energy managementsystem in the steel industry include energy consumption analysis and application of energy saving technologies.2.实施能源管理体系可以降低钢铁行业的能源消耗和生产成本。
Implementing an energy management system can reduceenergy consumption and production costs in the steel industry.3.制定能源管理计划是钢铁企业实施能源管理体系的重要步骤。
Developing an energy management plan is an important step for steel companies to implement an energy management system.4.钢铁企业可以通过优化设备和工艺来提高能源利用率。
Steel companies can improve energy efficiency byoptimizing equipment and processes.5.建立能源监测和数据分析系统是能源管理体系的核心内容。
Establishing an energy monitoring and data analysis system is the core of an energy management system.6.钢铁行业应该积极推广先进的节能技术和装备。
The steel industry should actively promote advanced energy saving technologies and equipment.7.加强员工培训和意识提升是能源管理体系实施的关键。
钢铁企业能源管理系统及节能技术汇总
钢铁企业能源管理系统及节能技术汇总钢铁行业是中国重要的支柱产业之一。
随着这些企业规模和产量的增长,它们的能源消耗也在不断增加。
如何有效地管理和节约能源成为钢铁企业所面临的重要问题。
本文将对钢铁企业能源管理系统以及节能技术进行汇总和介绍。
钢铁企业能源管理系统钢铁企业能源管理系统(EMS)是钢铁企业为了解决能源问题而设计的一种信息管理系统。
EMS能够监测钢铁企业的各种能源使用情况、节能措施、能源消耗比率等信息。
通过EMS的数据分析和处理,钢铁企业可以更好地制定出科学合理的节能方案,降低能源成本,提高生产效率。
EMS主要包括以下模块:能源计量管理模块能源计量管理模块是EMS中最基础的环节。
该模块能够通过传感器、智能电表等手段对钢铁企业的能源使用情况进行监测,如电、水、气等。
同时,它还能够提供实时能源消耗情况和历史数据查看。
能源诊断分析模块能源诊断分析模块是EMS中最重要的环节。
该模块能够采集、分析钢铁企业的各种数据,如工艺流程、设备状态、运行时间等,提供能源消耗数据及其影响因素,为明确能效提升方向提供支持。
可支持数据分析方法用于建模,评估和优化能源系统的运行效率。
能源管理评价模块能源管理评价模块能够评价钢铁企业的能源管理水平。
通过制定指标体系、标准评估流程等手段,建立能源管理评价体系。
并对资料进行分析为企业能源规划提供参考建议。
节能技术钢铁企业节能技术主要有以下五类:热系统节能技术热系统节能技术包括高效热交换器的应用、热回收等。
通过热能回收,可将废气及烟道余热回收,再进行二次利用。
能源回收技术能源回收技术主要是通过集中式供热与分散采暖的形式将冷热能集成,使能源回收再利用。
燃烧技术燃烧技术包括高效燃烧、燃烧控制等。
燃烧设备采用先进控制技术,通过氧气浓度、烟气排放温度等多个参数实现对燃烧过程的可控和优化。
废渣资源化技术废渣资源化技术通过技术手段可将钢铁企业排放的废渣再利用。
包括钢渣混凝土、矿渣水泥等。
系统集成技术系统集成技术主要是对各种技术手段的综合应用,不断完善能源系统,提高系统能效,降低生产成本。
- 1、下载文档前请自行甄别文档内容的完整性,平台不提供额外的编辑、内容补充、找答案等附加服务。
- 2、"仅部分预览"的文档,不可在线预览部分如存在完整性等问题,可反馈申请退款(可完整预览的文档不适用该条件!)。
- 3、如文档侵犯您的权益,请联系客服反馈,我们会尽快为您处理(人工客服工作时间:9:00-18:30)。
《一》钢铁企业能源管理系统(EMS)简介
1.概述
能源管理系统是钢铁企业信息化系统的一个重要组成部分,在能源数据进行采集、加工、分析,处理以实现对能源设备、能源实绩、能源计划、能源平衡、能源预测等方面发挥着重要的作用。
能源介质种类主要包括:高炉煤气(BFG)、焦炉煤气(COG)、转炉煤气(LDG)、氧气(O2)、氮气(N2)、氩气(Ar)、压缩空气(Air)、蒸汽、氢气(H2)、生活水、工业净环水、工业浊环水、浓盐水、除盐水、软化水、电力等。
能源介质信息包括:压力、流量、温度、煤气热值、供水品质(水质)、阀门开闭、调节阀开度、开关信号、动力设备运行状态、主生产线设备的运行状态等。
环保信息包括:环保设备的运行情况、外排水中主要污染物的浓度、流量、主要废气排放点的外排放废气中烟(粉)尘、SO2、NOx、CO2 等污染因子的浓度和流量、污染物排放总量、大气质量指标、厂界噪音等。
2.系统架构
典型能源系统架构包括能源调度管理中心、通讯网络、远程数据采集单元等三级物理结构,如下图示:
系统结构示意图
数据流
3.系统功能
EMS监控部分分为4 个子系统,即电力系统、动力系统、水系统和环保系统。
其中动力系统包括燃气系统、蒸汽系统、氧氮氩系统,水系统包括化学水、工业水和生活水。
1)数据的实时采集与监控
通过建立可靠的数据采集系统(SCADA系统)对能源潮流数据(如电流、电压、压力、温度、流量、环境数据等)、设备状态(如开、停、阀门开度、报警信号等)等进行采集;提供过程监视、操作控制、实时调整等画面,过程曲线及信息显示等辅助界面、大屏幕等完成能源设备状态及潮流的监视功能;提供过程控制和实时调整,参数设定窗口等实现控制功能;并对信息进行归档。
2)基础数据管理
包括介质参数管理、维护单位管理、计量设备管理、测点耗量关系、用户权限设置、以及其他需人工录入的参数管理界面。
3)能源管理功能
将采集的数据进行归纳、分析和整理,结合生产计划和检修计划的数据,实现基础能源管理功能,包括能源实绩分析管理、能源计划管理、运行支持管理、能源质量管理、能源平衡管理等。
4)环境监测功能
对环保设备运行状态的监测,对水、烟气等污染源排放进行监测、分析和管理。
《二》钢铁企业主要工艺涉及的节能技术
→焦化工序(干熄焦技术、焦炉煤气脱硫净化技术)
→烧结球团工序(烧结余热回收利用技术、球团废热循环再利用技术、烧结烟气湿法/干法脱硫技术)
→炼铁工序(高炉煤气余热余压发电技术TRT、高炉热风炉双预热技术、高炉煤气汽动鼓风技术、高炉煤气干法布袋除尘技术、高炉炉渣利用技术)
→炼钢工序(转炉“负能”炼钢技术、转炉烟气高效利用技术、转炉烟气干法除尘技术、电炉烟气余热回收除尘技术)
→轧钢工序(加热炉蓄热式燃烧技术)
综合性节能技术(能源管理及优化调控技术、燃气-蒸汽联合发电技术、全燃高炉煤气锅炉发电技术)
《三》钢铁节能减排相关的技术
结合公司的目前在节能环保方向(余热回收及发电)的主要业务,归纳了如下11种节能技术:
1、干熄焦技术(焦炭显热、焦炉煤气余热)
2、烧结余热
余热利用有两种方式:
第一种是热利用,即利用余热来助燃、预热、干燥、供热、供暖等。
(1)用作点火炉助燃空气:将冷却机废气除尘后,输送至点火炉空气管道内,以节省点火燃料;
(2)预热烧结混合料:在点火炉前设置预热炉,冷却机废气由鼓风机送入预热炉内,对混合料进行预热,以提高混合料温度,降低固体燃料消耗;
(3)热风烧结:此方法是在烧结机点火后,继续以 300~1000℃热风或热废气向料层提供热量,进行烧结;
(4)产生蒸汽供暖、供热:该方法通过余热锅炉产生蒸汽,送至管网供全厂使用。
第二种是动力利用,即将热能用作余热锅炉或其它余热回收装置的热源,生产蒸汽将其转化为电或机械能,如余热发电。
3、高炉炉顶煤气余压发电技术TRT
高炉炉顶煤气余压发电装置(Top Gas Pressure Recovery Turbine, 简称 TRT)是在减压阀前将煤气引入一台透平膨胀机作功,将压力能和热能转化为机械能并驱动发电机发电的一种能量回收装置。
TRT 在运转中不需要燃料,不改变原高炉煤气的品质和正常使用,却回收了相当可观的能量(约占高炉鼓风机所需能量的 30%),同时又净化了煤气,减少了噪音,改善了炉顶压力控制品质,且不产生新的污染,发电成本极低,是典型的高效节能环保装置。
4、高炉热风炉双预热技术
高炉热风炉双预热技术是指同时预热高炉煤气和助燃空气的技术,这不仅会明显提高热风炉的理论燃烧温度,而且有利于提高热风炉的寿命,降低能源消耗。
5、高炉煤气汽动鼓风技术
高炉煤气汽动鼓风技术主要是利用高炉本身产生的富余煤气,通过锅炉燃烧产生蒸汽,蒸汽驱动工业汽轮机带动风机运转对高炉鼓风。
常规汽动鼓风技术通常是采用中温中压参数凝汽式汽轮机,由工业汽轮机直接带动鼓风机运行,实现高炉煤气→蒸汽→冷风的能源转换。
6、转炉“负能炼钢”技术
负能炼钢指炼钢过程中回收的煤气和蒸汽能量大于实际炼钢过程中消耗的水、电、风和气等能量总和。
要实现转炉工序“负能炼钢”,一方面要努力降低炼钢耗能;另一方面要加强能量回收,提高回收效率。
提高转炉煤气和转炉烟气余热回收率和利用率是实现转炉“负能炼钢”的重要保障。
7、高炉炉渣显热回收技术
炉渣的显热回收方法大致分为两类:一类是利用循环空气回收炉渣显热,然后通过余热锅炉以蒸汽的形式回收显热,如风淬法;另一类是将高温炉渣注入容器内,在容器周围用水循环冷却,以蒸汽形式回收炉渣显热,如环形床法。
8、转炉烟气高效利用技术
烟气能量的高效转换与回收利用是转炉工序能耗实现“负值炼钢”的主要途径。
烟气能量回收主要以烟气显热和化学能转换为中、低热值的转炉煤气,中、低压蒸汽两种方式并加以回收利用。
转炉余热锅炉生产蒸汽既可以供饱和蒸汽发电设施,也可用于精炼。
9、电炉烟气余热回收利用除尘技术
电炉烟气余热回收形式基本都是蒸汽,回收装置主要有两种:热管余热回收装置和余热锅炉回收装置。
热管余热回收装置有较大优势。
10、轧钢加热炉蓄热式燃烧技术
蓄热式燃烧技术是一种烟气余热回收技术,其核心是高温空气燃烧技术,即利用
高温烟气对助燃空气或/和煤气进行预热。
蓄热式燃烧技术的工作原理是,一组蓄热式烧嘴在正常工作时,两只燃烧器不会处于同一种工作状态。
当一只烧嘴处于燃烧工作状态时,此燃料通路开通、常温空气(常温煤气)通过炽热的蓄热体,被加热为热空气(热煤气)去助燃(燃烧);另一只烧嘴一定处于蓄热状态作为烟道,此燃料通路关闭,燃烧产物在引风机的作用下经燃烧通道到蓄热体,使蓄热体蓄下热量后,经烟道由烟囱低温排出。
经过一段时间后,换向阀换向,两只烧嘴的工作状态互换,两种工作状态交替进行,周而复始。
通过蓄热体,出炉烟气的余热得到回收利用。
具有足够传热能力和含热能力的蓄热体,能使烟气余热得到充分的回收,将空气预热到很高的温度。
11、燃气-蒸汽联合循环发电技术
燃气-蒸汽联合循环发电技术充分利用钢铁企业低热值高炉煤气,由燃气轮机循环以及汽轮机循环所组成,煤气的热能既利用了烟气的做功能力发电,又利用了蒸汽的做功能力发电,从而更大限度的提高了能源利用效率。
该技术将钢铁企业高炉等副产煤气经除尘器净化加压后与经空气过滤器净化加压后的空气混合进入燃气轮机燃烧室内混合燃烧,高温高压烟气直接在燃气透平内膨胀做功并带动发电机完成燃机的单循环发电。
燃气轮机做功后的高温排气送入余热锅炉,产生高、中压蒸汽后进入蒸汽轮机作功,带动发电机组发电,形成煤气-蒸汽联合循环发电系统,系统中锅炉和汽机均可外供蒸汽,灵活组成热电联产系统。
该技术主要工艺流程图如下:
《四》能源管理系统的效益
a)完善能源信息的采集、存储、管理和提高能源的有效利用率
b)实现对能源介质的分散控制和集中管理
c)提高企业能源管理水平,减少管理环节,优化管理流程,建立客观能源消耗评价体系
d)降本增效,提高劳动生产率
e)加快系统的故障处理,提高对全厂性能源事故的反应能力
f)通过优化能源调度和平衡指挥系统,节约能源和改善环境
g)深化能源数据的挖掘、加工、处理、分析,为“节能改造”提供能源决策依据
附录:
钢铁企业节能减排技术/能源回收利用技术/污染治理技术
精心打造未来11。