最新008FPC制程能力(I)
FPC制程介绍

FPC的基本結構--材料篇 保護膠片(Cover Film)
保護膠片:表面絕 緣用. 常見的厚度有 1mil與1/2mil.
接著劑:厚度依客 戶要求而決定.
離形紙:避免接著 劑在壓著前沾附異物. 1mil=25μm
21
FPC的基本結構--材料篇 補強膠片(PI Stiffener Film)
銅箔 接著劑
基材
雙面板構成
18
FPC的基本結構--材料篇 銅箔基板(Copper Film)
銅箔:基本分成電解銅 (ED銅)與壓延銅(AR銅 )兩種. 厚度上常見的為 1oz、1/2oz與 1/3oz.1oz=35μm
基板膠片:常見的厚度 有1mil與1/2mil兩種. 1mil=25um
接著劑:厚度依客戶要 求而決定.
4
FPC特性的缺點
機械強度小. 易龜裂 製程設計困難 重加工的可能性低 檢查困難 無法單一承載較重的部品 容易產生折, 打, 傷痕 產品的成本較高
請 千 萬 愛 惜 FPC
5
FPC的產品應用
CD隨身聽 ▪ 著重FPC的三度空間 組裝特性與薄的厚 度. 將龐大的CD化 成隨身攜帶的良伴
時就會出現short 注:由于每家的機臺與產品不同,阻抗值可
58
後工程
外形打拔.(blanking) C/N(pitch 1mm~)打拔偏移
±0.15mm. C/N(pitch 0.5~1mm)打拔偏
移±0.1mm. C/N(pitch ~0.5mm)打拔偏
移±0.07mm. 製品外形±0.2mm.
磁碟機
11
FPC的產品應用
電腦與液晶螢幕 ▪ 利用FPC的一體線路 配置, 以及薄的厚 度. 將數位訊號轉 成畫面, 透過液晶 螢幕呈現
fpc-制程

在裸铜面上镀镍, 用来防止FPC表 面的铜被氧化或 腐蚀
7
FPC制程
冲孔:以CCD定位冲孔机针对后工站所需之 定位孔冲孔。
电测:利用电压、电流进行电性测试,判断 短、断路问题
冲切:所需fpc的外形大小成形 模具分类 1 钢模(精度高,成本高) 2 刀模(精度普通,成本低)
8
FPC制程
表面贴装:表面贴装器件(SMD) 其它:通孔插焊
箔通过过孔结构进行连接
钻孔
主要加工方式为激光(小孔)和机械
黑孔
1绝缘壁上附着形成导电功能 2 后续电镀铜
镀铜
加厚铜层足以抵抗后续加工和环境冲击
5
FPC制程 制作电路:贴干膜、曝光、显影、蚀刻、
脱膜 贴干膜: 干膜:抵抗蚀刻药液的介质 在蚀刻时保护所需要的铜面形成电路 曝光:利用紫外线使干膜中的光敏物质发生 光化学反应,是菲林上的图形转移到干膜上。 显影:干膜上图案显现,去掉未发生光感的 膜层,留下已感光的干膜。 蚀刻:利用药液将不需要的铜层腐蚀掉 脱膜:碱性药水将干膜和铜片之间的黏合破 坏,再利用水压剥除。 线路部分省略的步骤:酸洗,抗氧化,烘干
6
FPC制程 覆盖膜处理:假接、层压
CVL假接:MARK对位,进行预贴合。 CVL层压:给予一定温度使两材料之间黏合 丝印:用网版将油墨涂在基材上,再烘烤硬化 印刷用油墨主要分类: 感光型防焊油墨 热固型防焊/文字油墨 银浆
化学镍金:具有良好的接触导通性,而且 表面前处理: 还具有良好的装配焊接性能。 电镀镍金:良好的接触导通性,而且还具 有良好的耐摩擦性能。
1
FPC制程
FPC (Flexible Printed Circuit): 由柔性覆铜板
搭配防焊层制成的印刷线路板,主要功能为承载和连接。 覆铜板:挠性印制线路板的加工基板材料,由挠性 绝缘基膜与金属箔组成。 防焊层:覆盖在柔性印刷线路板导电图形上的有开 窗的外部绝缘层,可以是膜和油墨。
FPC PCB设计工艺制程能力

常规公差A1≤150 ±0.1A1>150 ±0.2最小公差A1≤150 ±0.05A1>150 ±0.1常规公差±0.05最小公差±0.03孔到边距离图一(A3)最小(两幅模具冲孔)0.3开孔大小图一(A4)最小0.5孔边到孔边距离图一(A5)最小0.2(钻孔)0.3(冲孔)常规公差±0.1最小公差±0.05常规公差(孔边到成型小于0.5)± 0.2最小公差(孔边到成型大于0.5)±0.05FPC宽度图一(A8)最小0.5FPC外形边距离图一(A9)最小0.5内倒角图一(A10)最小R0.2外倒角图一(A11)最小R0.2常规Φ0.15最小Φ0.075常规公差±0.05最小公差±0.05常规0.1最小0.075常规≥8μm 最小≥6μm 常规≥8μm 最小≥6μm 常规60μm 最小50μm 常规公差±0.02最小公差+0.01/-0.02常规公差±0.03最小公差±0.02常规公差±0.1最小公差±0.07常规公差±0.2最小公差±0.15常规公差±0.03最小公差±0.02常规公差±0.02最小公差±0.02常规公差±1‰最小公差±1‰常规公差±1.5‰(无胶材)±2‰(有胶材)最小公差±1.5‰(无胶材)±2‰(有胶材)常规公差100,90Ω+/-10%最小公差100,90Ω+/-10%常规公差0.5最小公差0.4常规公差0.2最小公差0.15常规公差0.5最小公差0.4常规<0.2最小<0.1常规公差±0.2最小公差±0.15焊盘距线路图三(D3)最小0.3常规公差±0.1最小公差±0.075开口大小图三(D1)最小0.1常规0.1最小0.075焊盘距线路图三(D3)最小0.175单层区域油墨工艺NA\OK化学镍厚常规2-5μm参考示图福 莱 克 斯 制 程 能 力 一 览 表溢胶量控制覆盖膜(溢胶+贴合)对位精度阻焊油墨开口距离焊盘图一(A1)图二(B1)图一(A7)图一(C4)总宽度150-200mmNA图二(B3)图二(B4)图一(C2)图三(D2)NA 差分阻抗最小开口间距NA 线路与板边距离(插拔端)相邻 pitch中心NA 孔铜厚度最小开口盖线plating copper厚度正反面线路相对偏移图三(C5)F PC外形线宽/线距内孔径孔中心到孔中心孔胚环制程能力单位(mm)插拔端图一(A2)线路与板边距离图一(C3)项目参考示图编号图一(A6)板边导通孔图二(B2)图三(C1)孔中心到FPC外形覆盖膜线路总宽度20mm以下总宽度20-150mm跨距pitch(第1Pin到最后Pin)最小开口标准值镀铜化学金厚常规≥0.03μm 电镀镍厚常规2-5μm 电镀金厚常规≥0.1μm 常规 1.2最小0.8文字高度表面处理NA图四(E1)常规0.15最小0.12常规0.5最小0.2常规0.3最小0.2常规0.15最小0.12常规公差0.3最小公差0.2常规0.2最小0.15阻容器件间距离图四(F2)最小0.3阻容器件距IC距离图四(F3)最小0.3器件本身焊盘距离图四(F5)最小0.15常规±5°最小±1°最小0201、Pitch0.38 BGA IC 最大80Pin连接器、SIM卡座等常规0.12最小0.1常规公差±0.3最小公差±0.25常规公差±0.05最小公差±0.03最小±0.03最大±0.02开孔大小图五(G4)最小0.8宽度图五(G10)最小0.5常规公差±0.3最小公差±0.25常规公差±0.05最小公差±0.03最小±0.03最大±0.03开孔大小图五(G4)最小0.8宽度图五(G10)最小0.5常规公差±0.1最小公差±0.05常规公差±0.2最小公差±0.15常规0.1最小0.05常规公差±0.05最小公差±0.03最小±0.02最大±0.02开孔大小图五(G4)最小0.8宽度图五(G10)最小0.5常规公差±0.3最小公差±0.2常规0.3最小0.2常规0.05最小-最大0.1常规 1.2指胶的总宽最小0.8指胶的总宽常规0.5最小0.4胶水种类NA NA 黑色热固、UV透明元件焊盘距板边距离图四(F4)最小0.5常规公差±0.3图五(G8)外形+贴合相对外形内缩溢胶范围SUS补强FR4补强点胶针头大小贴合相对FPC外形内缩厚度厚度图五(G3)外形图五(G5)图五(E6)图四(E5)图四(E4)厚度位置精度文字间距丝印PI补强文字线宽距焊盘距离器件封装大小图五(G9)图五(G6)NA 图五(G2)图五(G2)图五(G3)图五(G1)NA 图四(E2)图五(G7)图四(E3)图四(F1)位置精度外形+贴合贴合后总厚度图六(H1)图五(G1)图五(G3)NA 成品锡膏实际高度外形+贴合贴合高温绝缘膜贴合后总厚度贴合后总厚度厚度距板边距离SMTSMT器件偏移角度图四(F6)图四(F7)。
FPC模具制程能力表

已经是最小值
6.
间隙
孔径∮1-∮3mm,椭圆孔0.5-2.5mm 内≥0.7mm 孔径大于∮3mm,椭圆 0.6 孔3-5mm内≥0.8mm 孔径大于 ∮5mm,椭圆孔5-8mm内≥1mm 小于1.0mm* 0.5 ≥0.4 ≥0.50 ≥0.8 ≥1.1 ≥1.6 ≥1.8 ≥1.9 ≥2.3 ≥2.7 ≥2.9 ≥3.7 ≥4.0 ≥4.3 ≥4.6 ≥4.9 ≥5.1 ≥5.4 ≥5.8 ≥6.2 ≥6.8
160mm以上的长度每加长10mm安全值加1.0mm,限度加0.5mm
l
8
l
s
四个相邻方孔
I≥0.7 S≥0.7
I≥0.5 S≥0.5
9
l
s
圆孔与方孔相邻
I≥0.7 S≥0.7
I≥0.4
S≥0.4
10
s
四个相邻圆孔
I≥0.5 S≥0.5
I≥0.4
S≥0.4
11. 12.
圆角(R)
0.2
≥0.15 ≥0.3 ≥0.5 ≥0.6 ≥0.7 ≥0.7 ≥0.6 ≥1 ≥0.5 ≥0.6 ≥0.8 ≥0.6 ≥0.7 ≥1.0 同第7条 ≥0.8(外形) ≥0.6(内孔)
7.
1mm~3mm* 0.6 3mm-6mm* 0.9 6mm-10mm*1.3 10mm-15mm*1.7 15mm-20mm*1.9 20mm-25mm*2.1 25mm-30mm*2.6 30mm-35mm*2.9 35mm-40mm*3.1 方孔间隙: 孔长 * 40mm-50mm*4.2 间隙 50mm-60mm*4.5 60mm-70mm*4.6 70mm-80mm*4.9 80mm-90mm*5.1 90mm-100mm*5.3 100mm-110mm*5.6 110mm-120mm*6.2 120mm-140mm*6.6 140mm-160mm*7.1
FPC全制程技术讲解

FPC全制程技术讲解单片单面挠性印制板制造工艺单片多层,刚挠印制板制造工艺成立群单片单面挠性印制板制造工艺单片单面挠性印制板工艺流程单片单面挠性印制板工艺(一)材料的切割:挠性印制印制板的材料主要分为二大部份;第一类是:覆铜基板材料,按绝缘材料的类型又可分为聚酰亚胺和聚酯类;按导电铜箔的类型又可分为压延铜箔和电解铜箔;按结构分又可分为三层结构(有胶基材)和二层结构(无胶基材)。
第二类是:保护膜材料,按材料的类型可分为聚酰亚胺和聚酯类。
在材料的切割过程要做到切割尺寸的规整,避免使用正方形的切割尺寸。
对使用压延铜箔基材时要注意铜箔的压延方向与设计时的要求一致。
单片单面挠性印制板工艺(二)使用压板的目的:防止产品表面产生毛边。
钻孔时散发热量。
可引导钻头进入FPC板的轨道作用。
钻头的清洁作用。
压板的种类有酚醛树脂板,铝合金板,纸苯酚板。
酚醛树脂板本身有种轨道作用,铝合金板则散热好,纸苯酚板对钻头的磨损较小。
但是铝合金板的耐热性能不佳,在加工热量很大的时候,会产生铝的熔化在钻头尖部附着成一硬块。
所以一般在FPC钻孔加工中选用0.3mm—0.5mm厚度的酚醛树脂板作为压板。
单片单面挠性印制板工艺(二)使用垫板的目的:抑制毛边的产生。
让FPC板能充分贯通。
垫板以1.6mm—2.0mm厚度的酚醛树脂板为主要材料。
以材质来讲,比较软质的酚醛树脂板较为理想,太硬的板子会使钻头的切刃部位与垫板接触时发生缺口现象。
有效钻头刃长的计算:有效钻头刃长(mm)=钻头刃长(mm)-1.5mm有效钻头刃长的组成:有效钻头刃长=单片材料的厚度X叠层数+压板厚度(0.5mm)+ 过钻量(0.3mm,既钻入下层垫板的深度)在对保护膜材料进行叠层前,要对其粘结剂面的离形纸做“消应力”处理。
单片单面挠性印制板工艺(二)FPC的固定:将叠层后在二端打孔并订入定位销钉,装入钻床台面后在用1.5inch宽的美文纸单面胶带固定四周,使FPC材料与台面牢固紧密地结合在一起不能有上下跳动和左右晃动的现象出现。
FPC制程能力

≥0.2mm
文件编号
修订状态
文件名称
FPC制程能力
生效日期
页码
第4页共5页
3.6表面处理
项目
内容
常规
表面处理
沉镍厚度
60-120u,
沉金厚度
1-3u,,
3.7外型加工/靶冲孔
项目
内容
常规
外形冲切
外形尺寸(手指到边)公差:
±0.075mm(精模制作、激光切割)
外形尺寸(手指到边)公差:
±0.05mm
钻孔孔径公差(非镀通孔)
±0.025mm
PTH/板电
PTH孔最小孔壁铜厚
双面板7um--13um;多层板12um--18um
板电夹具最大/最小尺寸
500*250mm/250mm*10mm
3.3图形线路
项目
内容
常规
菲林最小线宽/线隙
最小孔环
单边0.1mm(普通单双面板)
单边0.125mm(3\4层多层板)
±0.10mm(普通钢模)
外形尺寸(手指到边)公差:
≥±0.20mm(刀模)
外形尖角允用过渡圆角
R≥0.15mm(钢模),R≥0.3mm(刀模)
定位孔中心到外形边间距
≥2.5mm
单元与单元最小间距
≥0.5mm(用于跳冲),普通1-2mm
外形边到剪切线
≥2.0mm
定位孔中心距离剪切线
≥3.0mm
半圆孔最小直径
覆盖膜最小开窗间距
0.5mm(钢模加工)
覆盖膜最小开窗间距
0.1mm(钻孔)
覆盖膜最小冲孔
0.6mm(钢模加工)
开窗到焊盘最小
0.05mm,安全值0.10mm
FPC的介绍
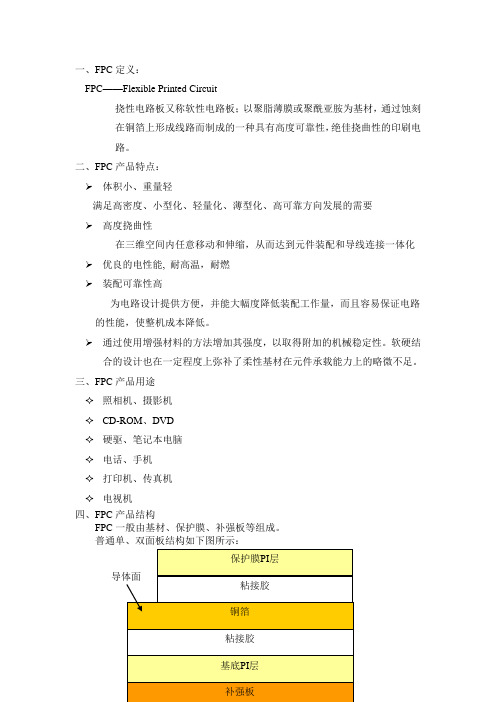
一、FPC定义:FPC——Flexible Printed Circuit挠性电路板又称软性电路板;以聚脂薄膜或聚酰亚胺为基材,通过蚀刻在铜箔上形成线路而制成的一种具有高度可靠性,绝佳挠曲性的印刷电路。
二、FPC产品特点:体积小、重量轻满足高密度、小型化、轻量化、薄型化、高可靠方向发展的需要高度挠曲性在三维空间内任意移动和伸缩,从而达到元件装配和导线连接一体化 优良的电性能, 耐高温,耐燃装配可靠性高为电路设计提供方便,并能大幅度降低装配工作量,而且容易保证电路的性能,使整机成本降低。
通过使用增强材料的方法增加其强度,以取得附加的机械稳定性。
软硬结合的设计也在一定程度上弥补了柔性基材在元件承载能力上的略微不足。
三、FPC产品用途✧照相机、摄影机✧CD-ROM、DVD✧硬驱、笔记本电脑✧电话、手机✧打印机、传真机✧电视机四、FPC产品结构FPC一般由基材、保护膜、补强板等组成。
普通单、双面板结构如下图所示:(单面板)(双面板)注:1、导体铜箔的分类电解铜(ED)压延铜(RA)其特点如下表所示:2、常用材料规格:◆基材:五、FPC生产流程:1、总体流程图示:2、流程分解◆钻孔:钻定位孔及零件过孔。
注意钻孔程序及叠板方式(铜面及胶面的面向)◆沉铜:即在基材表面及过孔孔壁沉积上一层化学铜◆电镀:提高孔内镀层的均匀性,保证整个板面(孔内及孔口附近的整个镀层)厚度达到一定要求,使双面基材上下镀通◆金相切片:对沉铜、镀铜之后的品质检查(是否有孔空洞、无铜象、镀铜厚度)◆贴膜:将感光膜通过一定的压力、温度粘贴于基材上。
干膜贴在板材上,经曝光显影后,使线路基本形成。
在此过程中干膜主要起到影像转移的功能,而且在蚀刻进程中起到保护线路的作用。
◆曝光:使线路通过干膜的作用转移到板材上。
利用光感应方式,将曝光光源通过制品线路形状的菲林(胶片),照射到感光膜上,使之感光。
被光射到的感光膜形成保护层,未被光射到的感光膜则没有保护层。
FPC制程介绍

沖型 Blanking
印刷 Screen Printing
表面黏著/組裝 SMT & Assembly
電測/目檢 Elec.-test & Visual Inspection
Chesive Base Film Adhesive Copper
Adhesive Coverlay
Permissible Limit 容許極限 100 ppm
1000 ppm
1000 ppm 1000 ppm 1000 ppm
Multiple e-test & visual
主要設備:空板電測機 對已沖型之空板產品人工
利用5倍放大鏡進行外觀檢 查,分离良品與不良品.判斷 不良項目及數量,分類統計形成品質報告,並反饋 到前制程以方便改善措施之及時執行. 電測通過制具通過探針給線路兩端通電,測出產品空 板性能,分離短路.斷路等不良品,統計數量並分析原 因,并將不良品剔除. 貼合背膠等固定產品之零件等.
Grinding-treatment
主要設備: 刷磨機;微蝕槽;水洗槽.加熱系統;
作用:清潔表面氧化膜.使板面 平整性均一,一般用於貼乾膜前 或化鍍金之表面處理。
流程(原理) 流程:酸性脫酯水洗磨刷水洗吹乾 原理:刷磨輪在高速轉動下,刷磨輪與板 面的快速摩擦將板面磨平整(先粗後細800 1000目)
不導電,起到絕緣作用,通過NC,衝型後在上面已形成 圓型方形開口,使用假接著機將CVL貼在銅箔上,假接 著機上有定位PIN.CVL与銅箔上定位孔準確定位,使用 一定的壓力及溫度使二者貼合在一起再經過人工校正 定位,貼加強片等完成作業
CVL Lamination
主要設備:快速壓合機.真空壓合 將已貼合的CVL与銅箔經過 高溫高壓緊密附合,壓合機為 高溫高壓設備.將貼有CVL的 銅箔放在壓合機工作臺上.利用其高溫高壓將CVL中的
- 1、下载文档前请自行甄别文档内容的完整性,平台不提供额外的编辑、内容补充、找答案等附加服务。
- 2、"仅部分预览"的文档,不可在线预览部分如存在完整性等问题,可反馈申请退款(可完整预览的文档不适用该条件!)。
- 3、如文档侵犯您的权益,请联系客服反馈,我们会尽快为您处理(人工客服工作时间:9:00-18:30)。
008F P C制程能力(I)文件更改/审批表CT-DCC-F-004 A1、范围:此文件是FPC 制作能力指南,FPC 的设计及制作工具将遵循此标准进行。
2、FPC 结构图:2.1单面板聚酸亚胺胶粘剂( AD)铜箔( CU ) 胶粘剂( AD ) 聚酸亚胺( PI )胶粘剂(AD)补强板(PI )2.2 双面板2.3裸铜板 基材 补强板 补强板聚酸亚胺( PI)胶粘剂铜箔( CU ) 胶粘剂( AD ) 聚酸亚胺( PI) 胶粘剂( AD ) 铜箔胶粘剂(AD )聚酸亚胺( PI) 胶粘剂(AD )补强板(PI )3、FPC材料3.1 基材和覆盖膜常用规格:3.2 其它材料4、FPC 尺寸5、开料5.1 PNL宽度:250mm;长度:最大500mm。
5.2开料方向:250mmMD (此方向的挠曲性好,拼板时FPC需要挠曲的位置与此方向尽量一致)。
6、钻孔6.1钻孔孔径6.2孔边到线路边最小间距6.3孔边到孔边最小间距6.4 其它6.4.1 PTH孔必需保证最小环宽0.1mm。
6.4.2 NPTH孔不须加大。
6.4.3 NPTH成品孔径公差为±0.05mm, PTH成品孔径公差为±0.076mm。
6.4.4 所有基材定位孔(含干菲林对位孔)的孔径为2.0mm,覆盖膜定位孔2.5mm。
7、黑孔/板电孔壁镀铜厚度:≥7um8、干菲林/蚀刻8.1根据不同的板,线宽、线距补偿如下:8.2最小线宽/线距:2.5mil/2.5mil;工艺导线为6~8mil。
8.3对密集型线距小于5mil(含)需在pcs的外型边蚀刻宽1.5mm的排气槽, 排气槽的末段覆盖膜对应处钻直径2.0mm的孔。
8.4双面板及多层板外层线路层孔环的最小宽度单边:4mil,安全为6mil,多层板内层线路层孔环的最小宽度单边保证8mil。
8.5 线宽与线距公差:双面板+/-20%;单面板:+/-10%。
8.6对于线路到外形边距离:8.6.1如此超制程线路面与冲外形定位孔靶标图形为同一面,线到边的距离最小0.14mm。
8.6.2如因某种原因此超制程线路面与外形定位孔靶标图形不在同一面,线到边的距离最小0.2mm。
9、压覆盖膜9.1 对位公差9.2覆盖膜开窗能力见模具能力。
9.3覆盖膜对位孔的位置与基材上对位PAD相同,孔径为φ2.0mm。
9.4覆盖膜开窗距PAD单边最小0.04mm。
9.5钻孔覆盖膜开窗边缘到线路图形间距最小0.030mm。
9.6模具覆盖膜开窗边缘到线路图形间距最小0.1mm(倒扣板最小间距0.15mm)。
9.7覆盖膜开窗圆孔边到圆孔边0.05mm(含)以上做贴压覆盖膜工艺, 0.05mm 以下做防焊工艺;槽孔直径大于0.6mm(含) 做贴压覆盖膜工艺,小于0.6mm 做防焊工艺。
9.8钢片孔距离焊盘最小0.07mm 。
9.9覆盖膜开窗在铜皮上之开窗最小0.5mm 。
9.10 BGA 产品覆盖膜开窗9.10.1 BGA 位最小开窗0.35mm,孔与孔最小间距0.05mm ,覆盖膜开窗采用钻孔钻出,超出此能力做油墨工艺;9.10.2 BGA 位覆盖膜开窗到钢片孔开窗为槽产品,优先考虑钻孔钻出,设计钻孔资料按下图要求进行设计,超出钻孔制作能力,可考虑做油墨工艺;9.10.3 BGA 位焊盘与线路连接部位宽度相同的产品,需将连接焊盘的线路,修小至焊盘宽度的60%(客户同意的情况下,优先考虑修改线路),如客户不同意修改直接做油墨工艺,如下图;9.11模组产品覆盖膜开窗9.11.1覆盖膜开窗在0.65-0.9MM,孔与孔之间≤0.08MM ,采用模具冲出; 9.11.1覆盖膜开窗在0.65-0.9MM,孔与孔之间>0.08MM ,采用钻孔钻出;此设计不合理 钢片孔与BGA 位正确设计方法 临近钢片孔的正确设计方法 再将临近钢片孔9.12镂空板产品覆盖膜开窗9.12.1镂空手指边(左右)到覆盖膜开窗最小安全距离0.4 MM;9.12.1覆盖膜开窗原则,顶层覆盖膜开窗比底层覆盖膜开窗大;9.13覆盖膜搭配要求9.13.1 0.5OZ单面板:选择12.5UM(或以上)胶厚的覆盖膜。
9.13.2 1OZ单面板:选择25UM(或以上)胶厚的覆盖膜,线距≥0.075MM可选择20UM(或以上)胶厚的覆盖膜。
9.13.3 0.5OZ底铜+镀孔(板面不镀铜)的双面板:选择12.5UM(或以上)胶厚的覆盖9.13.4 0.5OZ底铜+整板镀铜的双面板:选择20UM胶厚的覆盖膜,BGA类/触摸屏类/背光源类及密集线路区域线距≥0.085MM在有客户要求的情况下可选用15UM(或以上)胶厚的覆盖膜。
9.13.5 1OZ底铜+镀孔(板面不镀铜)的双面板,优先选用25UM(或以上)胶厚的覆盖膜,线距≥0.1MM的产品可选择20UM(或以上)胶厚的覆盖膜。
9.13.6 1OZ底铜+整板镀铜的双面板,优先选用30UM(或以上)胶厚的覆盖膜,线距≥0.15MM的产品可选择25UM(或以上)胶厚的覆盖膜。
9.13.7 镂空板底层覆盖膜:选择15UM胶厚的覆盖膜。
9.13.8多层板内层:选择12.5UM(或以上)胶厚的覆盖膜,优先选用15UM胶厚的覆盖膜。
9.13.9 使用无胶基材产品须选择20UM(或以上)胶厚的覆盖膜,优先选用20UM胶厚的覆盖膜。
10、冲孔最大冲孔板厚:0.4mm11、字符11.1字符最小丝印宽度为4.8mil,厚度为7um-10um。
11.2 字符到焊盘最小间距为6mil。
11.3字符间距及线条间距最小6mil以上。
11.4字符高度最小为0.75mm以上。
11.5丝印热固阻焊油墨,网印菲林在客户资料开窗基础上单边预大0.2mm。
12、压补强板12.1补强板和胶层配本要求(胶带除外)。
12.2补强板定位孔φ2.0mm。
12.3补强板啤图形能力同覆盖膜开窗能力。
12.4补强宽度设计必须大于另一面覆盖膜开窗。
13、电测试13.1最小测试PAD宽度 :0.20mm;13.2最小测试PAD≥0.25MM测试治具使用0.2MM测试针生产;13.3最小测试PAD<0.25MM测试治具使用0.15MM测试针生产。
14、表面电镀:15、冲外形15.1模具能力15.2外形刀口到线路图形间距最小0.2mm。
15.3连片出货模具连接位最小0.6mm,防撕裂线比连接位宽度最小大0.6 mm (连接位为大铜皮不需增加防撕裂线),连接位处离线路距离≥0.3MM(大铜皮除外),尽可能设计在大铜皮或离线路较远的位置。
15.4钢模定位孔中心到外形边2.5mm,刀模定位孔中心到外形边3.5mm。
15.5蚀刻刀模不可冲切带有PI补强在5MIL以上的产品外形,须开钢模冲切外形。
15.6模具面向设计:金手指面朝刀口冲切,若该产品有FPR补强且与金手指不在同一面,则优先FR4补强朝上冲切。
15.7 灯条类产品外形模具长方向不共刀口,短方向共用刀口往进料方向延伸一个单元。
15.8 拉焊手指类BGA产品FPC长度在20MM以上需在拉焊手指尾端增加一连接位,外形需一次性成型冲出,不可分半冲切,以免影响外形半孔精度。
16、切割16.1 FPC外形:16.1.1 最大切割厚度:0.26MM;厚度小于0.18㎜:公差±0.1mm;厚度大于0.18㎜: 公差±0.15mm。
16.1.2 最小切割间距:外形到圆孔/方孔0.3MM(若<0.3MM则须允许破孔),外形到线路/焊盘距离直线0.2MM、拐角/转弯处0.3MM。
16.1.3 拼板最小间距:两PCS之间的切割线至切割线间距最小5MM16.1.4 最小孔:原则上FPC外形不切孔,采用钻孔,若有特殊原因须切孔最小孔≥1.5MM16.1.5 最小R角:≥1.2MM16.1.6 带3M胶纸产品:3M胶纸部分外形必须为直线,不可有拐角/转弯/圆角,若有则须先切割外形后再贴3M胶纸,3M胶纸单独切割再单件贴。
16.1.7 分层/多层分层板:分层区域外形必须为直线,不可有拐角/转弯/圆角等,若有则需开模生产。
16.2覆盖膜:16.2.1最小切割间距:0.2mm(包含圆孔、方孔、线、焊盘到边距离、圆孔到圆孔、方孔到方孔、切割线到切割线)16.2.2最小孔: 0.8mm,最小方孔: 单边1mm16.3纯胶:16.3.1 规则条贴纯胶(直线无转弯):纯胶不做切割,由组装手工分条,但需加剪切孔以方便分条,拼板间距为零间距。
16.3.2 不规则条贴纯胶(有转弯):切割小条总长不超过60MM,拼板间距每条之间大于5MM。
16.3.3 单PCS贴纯胶:拼板间距大于2MM。
16.4 PI补强:16.4.1 最大切割厚度:0.2MM16.4.2 最小孔:不能切孔16.4.3 最小拼板间距:2MM16.5 电磁膜/3M胶纸:16.5.1 最小切割间距: 两PCS之间的切割线至切割线间距最小2MM16.5.2 最小孔:原则上不切孔,采用钻孔,若有特殊原因须切孔最小孔≥1.5MM17、多层板17.1内层孔边到线路图形最小间距 : 0.225mm。
17.2 内层外形边到线路图形最小间距: 0.225mm。
17.3 压基材排气孔到分层窗口最小距离: 1mm。
18、钢片补强18.1 模冲钢片:普通钢片18.2 模冲钢片:精密钢片18.3 模冲钢片:异形钢片18.4 蚀刻钢片:18.5 工程在设计资料时需核对客户资料要求钢片的尺寸厚度是否超出该规格的制程能力,若超出制程能力则建议客户更改厚度或接受破孔现象。
19、板厚19.1板厚公差能力19.2 若客户公差严于公司板厚公差能力,建议客户放宽公差至公司板厚公差能力范围内,若客户要求必须达到,则提出评审是否更改工艺方式生产。
19.3 因导电纯胶结构的特殊性,40UM导电纯胶经压合后会减薄约15-20UM,工程设计材料配比时该材料厚度按25UM计算。