控制图基础知识介绍
控制图的原理及应用

s2
1( 2 4 ) 2 ( 3 4 ) 2 ( 4 4 ) 2 ( 5 4 ) 2 ( 6 4 ) 2
5 1
1 ( 2 )2 ( 1 )2 0 2 1 2 2 2 1 X 1 2 0 .5
4
4
7、样本标准偏差
国际标准化组织规定,把样本方差的正平方根作为样
本标准偏差,用符号S或σ表示,标准偏差又称标准差,其
LCL
第一种错误(α):生产者冒险率
生产质量相当良好,已达到允收水平,理应判为合格,但由于 控制线设置过窄,导致合格品误判为异常,其机率称为生产 者冒险率,因此种错误使生产者蒙受损失故得名之. 此冒险率又称为第一种错误 (TYPE Ⅰ ERROR) 简称(α).
3
UCL
2
1
CL
1
LCL
2
3
第二种错误(β) :消费者冒险率
LSL
规格下限
LCL 控制下限
其中: μ为正态总体的均值 σ为正态总体的标准差
CL 中心限
控制限与规格限(公差)的区别: 控制限用以区分偶然波动和异常波动,规范限用以区分合格与不合格
二、控制图由来
控制图简史:
20世纪20年代美国贝尔电话实验室成立了两个研究质量的课 题组,一为过程控制组,学术领导人为休哈特;另一为产品 控制组,学术领导人为道奇。其后,休哈特提出了过程控制 理论以及控制过程的具体工具——控制图。道奇与罗米格提 出了抽样检验理论和抽样检验表。
计算公式为:
s
1
n
2
xi x
n1i1
沿用计算样本变异数的例子,则那五个统计资料的标准差:
s 1 242(34)2(44)2(54)2(64)2 51
1 2 2 ( 1) 2 0 2 1 2 2 2
第六章控制图、过程能力和直方图
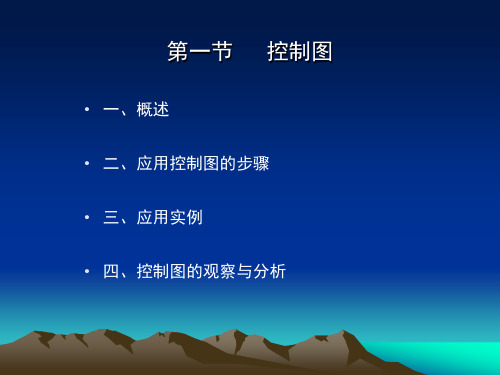
在工序控制中需要了解的三个方面,都能在控制图上得到。 (1) 在连续的生产监控中,有无变化的征兆; (2) 有无急剧的变化; (3) 有无越出控制范围的异常值。
--控制图的作用:
在质量诊断方面,可以用来度量过程的稳定性,即过程是否处于统计控制状态; 在质量控制方面,可以用来确定什么时候需要对过程加以调整,而什么时候则需使过程保持相应的稳定状态; 在质量改进方面,可以用来确认某过程是否得到了改进。
1.864
1.816
1.777
E2
2.660
1.772
1.457
1.290
1.134
1.109
1.054
1.010
0.975
m3A2
1.880
1.187
0.796
0.691
0.549
0.509
0.430
0.410
0.360
D3
-
-
-
-
-
0.076
0.136
0.184
0.223
d2
1.128
1.693
P
-
n -
(1- )
Pn
-
Pn
-
3
u
-
3
n
u
-
+
u
-
3
n
u -
c
-
3
c —
c
-
3
c +
控制系数选用表
n
2
3
4
5
6
7
8
9
10
A2
1.880
1.023
0.729
0.577
0.483
控制图基础知识与实例

控制图1控制图——过程控制的工具。
用来表示一个过程特性的图象。
它有两个基本用途:①用来判断过程是否一直受统计控制。
②用来帮助过程保持受控状态。
2控制图的构成::上控制线:中心线下控制线取样时间①收集:收集数据并画在图上。
②控制:根据过程数据计算试验控制线识别变差特殊原因并采取措施。
③分析及改进:确定普通变差的大小,并采取减少它的措施。
重复三个阶段,从而不断改进过程。
3控制图的益处:①供正在进行过程控制的操作者使用。
②有助于过程在质量上和成本上能持续地、可预见的保持下去。
③使过程达到:——更高的质量。
——更低的单件成本。
——更高的有效能力。
④为讨论过程的性能提供共同的语言。
⑤区分变差的特殊原因和普通原因,作为采取局部措施或对系统采取措施的指南。
第二章计量型数据控制图第一节均值和极差图参见“均值和极差控制图”1.收集数据1.1子组大小:一般为4-5件(连续生产的产品的组合)。
各子组样本应一样。
选择原则:一子组各样本间出现的变差的机会小。
子组内变差主要由普通原因造成。
1.2子组频率:应在适当时间收集足够的子组,能反映潜在的变化。
过程处于稳定,频率可减少。
(每班两次、每小时一次或其他频率)。
1.3子组组数:≧25个。
总单值≧100个。
2.控制图及记录原始数据:①X图绘在R图的上方。
下面再接一个数据栏。
②X和R值为纵坐标,时间为横坐标。
③数据栏应包括:每个读数空间、读数、和、均值、极差以及日期/时间或其他识别子组的代码的空间等。
3.计算均值(X)和极差(R):X=( X1+X2+…+X n)/n R=X MAX﹣X MINX1,X2,…X n——测量值。
n——子组容量。
4.控制图刻度;①对X图:坐标刻度最大值-最小值≧2(X max–X min)②对R图:坐标刻度最大值≧2R max5.计算控制限:①平均极差(R)及过程平均值(X)R=(R1+R+2…+R K)/K(1X2+…+X K)/KK——子组的数量。
控制图使用培训讲义

均值-极差
计 量 值 正态 分布 均值-标准差 中位数-极差
控制图
控制图 控制图
X R
控制图
控制图 控制图 控制图 控制图 控制图 控制图 控制图
X S
Me-R
单值-移动极差 控制图
X-Rs p np u c
计件值
二项 分布 泊松 分布
不合格品率 不合格品数 单位缺陷数 缺陷数
控制图 控制图 控制图 控制图
S =
X
n i =1
i
X
2
n 1
标准偏差也叫标准差,描述各数据偏离平均数的距离(离差)的平均数,标准差能 反映一个数据集的离散程度,标准偏差越小,这些值偏离平均值就越少,过程就约 一致。
3.统计与概率论简介
什么叫偏差?
m = 总体均值
i
偏差(偏离均值(离差)的大小)
标准差是过程变化程度的计量。
3.统计与概率论简介
Z值表
4.均值极差图( Xbar-R图)
生产过程中用控制图对过程质量特性进行测定、记录、评 估,从而监察过程是否处于控制状态,对过程异常提前进行 预警。 控制图种类有多种,而使用最多的是均值极差控制图 (Xbar-R图)。
4.均值极差图( Xbar-R图)
控制图类别
数值 分布 控制图 简记
类过程)。
2.变差
过程能力与顾客需求的关系:
过程能力由造成变差的普通原因来确定,在处于统计控制状态下的运行过 程,数据收集到后就能证明过程能力,而不考虑规范相对于过程分布的位 置和/或宽度的状况如何。 (规范:指顾客的要求,如产品标准要求) 内外部的顾客更关注过程的输出与规范的关系如何,而不考虑过程的变差 如何。(过程的输出:指产品、服务等)
控制图
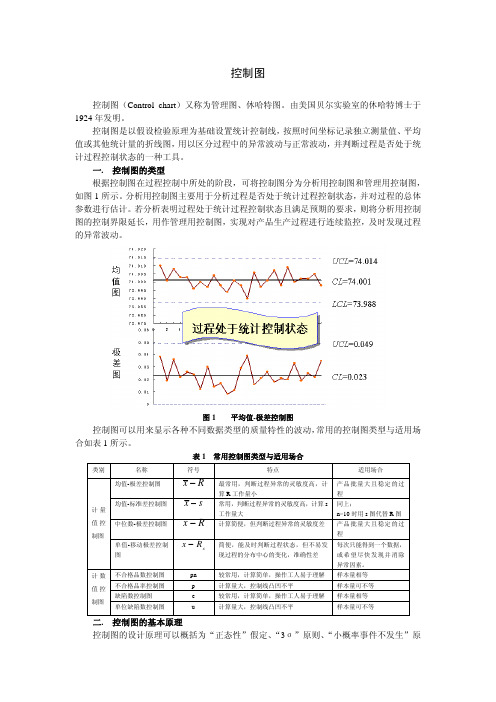
控制图控制图(Control chart)又称为管理图、休哈特图。
由美国贝尔实验室的休哈特博士于1924年发明。
控制图是以假设检验原理为基础设置统计控制线,按照时间坐标记录独立测量值、平均值或其他统计量的折线图,用以区分过程中的异常波动与正常波动,并判断过程是否处于统计过程控制状态的一种工具。
一. 控制图的类型根据控制图在过程控制中所处的阶段,可将控制图分为分析用控制图和管理用控制图,如图1所示。
分析用控制图主要用于分析过程是否处于统计过程控制状态,并对过程的总体参数进行估计。
若分析表明过程处于统计过程控制状态且满足预期的要求,则将分析用控制图的控制界限延长,用作管理用控制图,实现对产品生产过程进行连续监控,及时发现过程的异常波动。
图1 平均值-极差控制图控制图可以用来显示各种不同数据类型的质量特性的波动,常用的控制图类型与适用场合如表1所示。
表1 常用控制图类型与适用场合二. 控制图的基本原理控制图的设计原理可以概括为“正态性”假定、“3σ”原则、“小概率事件不发生”原理和“统计反证推断”思想。
具体说就是,假定所收集的质量特性数据服从正态分布,在此假定下,过程特性值落在分布中心上下各三倍标准差范围内的概率是99.73%,也就是说质量特性值落在上下三倍标准差之外的概率仅为0.27%,这是一个小概率事件,而“小概率事件不发生”原理认为小概率事件在一次观测中不发生,因此,一旦控制图出现“小概率事件发生”的现象,则表明过程发生了异常变化,这就是“统计反证推断”思想。
表2和表3分别表示计量值控制图和计数值控制图的中心线和控制界限的公式,以及样本量的确定。
表2 计量值控制图的中心线和控制界限表3 计量值控制图的中心线和控制界限三. 控制图的应用控制图显示随时间采集的数据和由这些数据计算出的波动;控制图与过程能力分析结合在一起称为统计过程控制(SPC)。
图2是一个典型的SPC的应用流程。
图2 典型的SPC的应用流程。
控制图介绍

2.1什么是控制图控制图由正态分布演变而来。
正态分布可用两个参数即均值μ和标准差σ来决定。
正态分布有一个结论对质量管理很有用,即无论均值μ和标准差σ取何值,产品质量特性值落在μ±3σ之间的概率为99.73%,落在μ±3σ之外的概率为100%-99.73%= 0.27%,而超过一侧,即大于μ+3σ或小于μ-3σ的概率为0.27%/2=0.135%≈1‰,休哈特就根据这一事实提出了控制图。
由于上下的数值大小不合常规,再把分布图上下翻转180°,这样就得到一个单值控制图,称μ+3σ为上控制限,记为UCL,称μ为中心线,记为CL,称μ-3σ为下控制限,记为LCL,这三者统称为控制线。
规定中心线用实线绘制,上下控制限用虚线绘制。
综合上述,控制图是对过程质量数据测定、记录从而进行质量管理的一种用科学方法设计的图。
图上有中心线(CL)、上控制限(UCL)和下控制限(LCL),并有按时间顺序抽取的样本统计量数值的描点序列。
2.2质量数据与控制图2.2.1计量型数所确定的控制对象即质量指标应能够定量。
所控制的过程必须具有重复性,即表现出统计规律性。
所确定的控制对象的数据应为连续值。
计量型控制图:能反映计量型数据特征,用来绘制、分析计量型数据的控制图。
2.2.2计数型数据控制对象只能定性不能而不能定量。
只有两个取值。
与不良项目有关。
计数型控制图:能反映计数型数据特征,用来绘制、分析计数型数据的控制图。
2.2.3质量数据的特性质量数据的分布遵循三种特性:计量型数据服从正态分布;计件型数据服从二项分布;计点型数据服从泊松分布。
2.3控制图原理根据来源的不同,质量因素可分成设备(machine)、材料(material)、操作(man)、工艺(method)、环境(environment),即4M1E五个方面;从对质量的影响大小来看,质量因素可分成偶然因素(简称偶因)与异常因素(简称异因)两类。
QC工具之管理图(控制图)

➢ LCL =D3R
● 单值—移动极差控制图(X-Rs图)
X图的上中下控制限计算公式为:
➢ UCL=X+2.66R ➢ CL=X ➢ LCL =X-2.66R Rs图的上中下下控制限计算公式为: ➢ UCL=3.267Rs
➢ CL=Rs ➢ LCL =-3.267Rs
➢ UCL=X+A3S ➢ CL=X ➢ LCL =X-A3S
S图的上中下下控制限计算公式为:
➢ UCL=B4S ➢ CL=S ➢ LCL =B3S
●中位数—极差控制图(~X-R图)
X图的上中下控制限计算公式为:
➢ UC~L=X+m3A2R ➢ C~L=X ➢ LC~L =X-m3A2R
R图的上中下下控制限计算公式为:
四、控制图的分类:
序号 管理图的种类
活用
是平均值和不均衡的管理图最众所周知。但是不能够与规格值 1 XーR 管理图 进行比较。
2 ~X-R 管理图 ①中的平均式作为中央值管理图(不经常使用)。
X 管理图 单纯的数据和移动范围的管理图比较简单。
3
XーRS 管理图
管理幅度和其它的规格线加入后,可以检测出不合格(规格偏 差)。近期经常被使用。
点子出界 点子排列不随机
3、控制图的具体判断准则:
1)判稳准则:控制中的描点在随机排列情况下,符合下列条件之 一的即可判稳 连续25个点,落在控制界外的点为0。 连续35个点,落在控制界外的点数小于或等于1。 连续100个点,落在控制界外的点数小于或等于2。
2)判异准则:GB/T4091—2001《常规控制图》标准规定有8种判异 准则模式 ①一个点落在A区以外:
R图的上中下下控制限计算公式为:
控制图基础知识介绍

控制图基础知识介绍控制图基础知识介绍⼀.前⾔:为使现场的质量状况达成⽬标,均须加以管理。
我们所说的 “管理”作业,⼀般均⽤侦测产品的质量特性来判断 “管理”作业是否正常。
⽽质量特性会随着时间产⽣显著⾼低的变化;那么到底⾼到何种程度或低⾄何种状态才算我们所说的异常?故设定⼀合理的⾼低界限,作为我们分析现场制程状况是否在 “管理”状态,即为控制图的基本根源。
控制图是于1924年由美国品管⼤师修哈特(W.A.Shewhart)博⼠所发明。
⽽主要定义即是[⼀种以实际产品质量特性与依过去经验所研判的过程能⼒的控制界限⽐较,⽽以时间顺序表⽰出来的图形]。
⼆.控制图的基本特性:⼀般控制图纵轴均设定为产品的质量特性,⽽以过程变化的数据为刻度;横轴则为检测产品的群体代码或编号或年⽉⽇等,以时间别或制造先后别,依顺序点绘在图上。
在管制图上有三条笔直的横线,中间的⼀条为中⼼线(Central Line,CL),⼀般⽤蓝⾊的实线绘制;在上⽅的⼀条称为控制上限(Upper Control Limit,UCL);在下⽅的称为控制下限(Lower Control Limit,LCL)。
对上、下控制界限的绘制,则⼀般均⽤红⾊的虚线表现,以表⽰可接受的变异范围;⾄于实际产品质量特性的点连线条则⼤都⽤⿊⾊实线绘制。
控制状态:三.控制图的原理:1.质量变异的形成原因:⼀般在制造的过程中,⽆论是多么精密的设备、环境,它的质量特性⼀定都会有变动,绝对⽆法做出完全⼀样的产品;⽽引起变动的原因可分为两种:⼀种为偶然(机遇)原因;⼀种为异常(⾮机遇)原因。
(1)偶然(机遇)原因(Chance causes):不可避免的原因、⾮⼈为的原因、共同性原因、⼀般性原因,是属于控制状态的变异。
(2)异常(⾮机遇)原因(Assignable causes):可避免的原因、⼈为的原因、特殊性原因、局部性原因等,不可让其存上控制界限(UCL) 中⼼线(CL) 下控制界限(LCL)在,必须追查原因,采取必要的⾏动,使过程恢复正常控制状态,否则会造成很⼤的损失。
- 1、下载文档前请自行甄别文档内容的完整性,平台不提供额外的编辑、内容补充、找答案等附加服务。
- 2、"仅部分预览"的文档,不可在线预览部分如存在完整性等问题,可反馈申请退款(可完整预览的文档不适用该条件!)。
- 3、如文档侵犯您的权益,请联系客服反馈,我们会尽快为您处理(人工客服工作时间:9:00-18:30)。
控制图基础知识介绍一. 前言:为使现场的质量状况达成目标,均须加以管理。
我们所说的 “管理”作业,一般均用侦测产品的质量特性来判断 “管理”作业是否正常。
而质量特性会随着时间产生显著高低的变化;那么到底高到何种程度或低至何种状态才算我们所说的异常?故设定一合理的高低界限,作为我们分析现场制程状况是否在 “管理”状态,即为控制图的基本根源。
控制图是于1924年由美国品管大师修哈特(W.A.Shewhart)博士所发明。
而主要定义即是[一种以实际产品质量特性与依过去经验所研判的过程能力的控制界限比较,而以时间顺序表示出来的图形]。
二.控制图的基本特性:一般控制图纵轴均设定为产品的质量特性,而以过程变化的数据为刻度;横轴则为检测产品的群体代码或编号或年月日等,以时间别或制造先后别,依顺序点绘在图上。
在管制图上有三条笔直的横线,中间的一条为中心线(Central Line,CL),一般用蓝色的实线绘制;在上方的一条称为控制上限(Upper Control Limit,UCL);在下方的称为控制下限(Lower Control Limit,LCL)。
对上、下控制界限的绘制,则一般均用红色的虚线表现,以表示可接受的变异范围;至于实际产品质量特性的点连线条则大都用黑色实线绘制。
控制状态:三.控制图的原理:1.质量变异的形成原因:一般在制造的过程中,无论是多么精密的设备、环境,它的质量特性一定都会有变动,绝对无法做出完全一样的产品;而引起变动的原因可分为两种:一种为偶然(机遇)原因;一种为异常(非机遇)原因。
(1)偶然(机遇)原因(Chance causes):不可避免的原因、非人为的原因、共同性原因、一般性原因,是属于控制状态的变异。
(2)异常(非机遇)原因(Assignable causes):可避免的原因、人为的原因、特殊性原因、局部性原因等,不可让其存上控制界限(UCL) 中心线(CL) 下控制界限(LCL)在,必须追查原因,采取必要的行动,使过程恢复正常控制状态,否则会造成很大的损失。
2.控制界限的构成:控制图是以常态分配中的三个标准差为理论依据。
中心线为平均值,上、下控制界限为平均数加减三个标准差()的值,以判断过程中是否有问题发生。
此即修哈特博士(W.A.Shewhart)所创造的方法。
控制图即以3个标准差为基础,换句话说,只要群体是常态分配,则自该群体进行取样时,用取出的数值加以平均计算来代表群体,则每进行10000次的抽样会有27次偶然机会,不予计较。
同样我们平均抽样时如有超出时,判定为异常,则误判的机率也是千分之三。
因为假设机率存在的前提,所以控制界限以加减3个标准差来订立,应是最符合经济效益的。
(偶然原因的变动) (异常原因的变动)σ3±控制图的控制界限是把常态分配图形旋转90°后,在平均值处绘成中心线(CL),平均值加三个标准差处绘成上控制界限(UCL),在平均值减三个标准差处绘成下控制界限(LCL)。
四.控制图的种类:1.按数据性质分类:(1)计量值控制图:所谓计量值是指控制图的数据均属于由量具实际量测而得;如长度、重量、浓度等特性均为连续性的,常用的有: (a) 平均数与极差控制图( Chart) (b) 平均数与标准差控制图( Chart) (c) 中位数与极差控制图( Chart)(d) 个别值与移动极差控制图( chart) (e) 最大值与最小值极差控制图( chart) (2)计数值控制图:所谓计数值是指控制图的数据均属于以单位计数者而得;如不合格数、缺点数等间断性数据等。
常用的有: (a) 不良率控制图(P chart)(b) 不良数控制图(Pn chart,又称np chart 或d chart) (c) 缺点数控制图(C chart)(d) 单位缺点数控制图(U chart) 2.按控制图的用途分类:(1)解析用控制图:这种控制图先有数据,后有控制界限(μ与σ未知的群体)。
(a) 决定方针用 (b) 制程解析用 (c) 制程能力研究用 (d) 制程控制的准备(2)控制用控制图:先有控制界限,后有数据(μ与σ已知之群体)。
其主要用途为控制过程的质量,如有点子超出控制界限时,则立即采取措施(原因追查→消除原因→再发防止的研究)。
μσ3+σ3-UCLCLLCLσ-X RX -R X -~Rm X -SL -3.计数值与计量值控制图的应用比较.1.计量值控制图: (1) 控制图:(a)先行收集100个以上数据,依测定的先后顺序排列。
(b)以2—5个数据为一组(一般采4—5个),分成约20—25组。
(c)将各组数据记入数据表栏位内。
(d)计算各组的平均值X(取至测定值最小单位下一位数)。
(e)计算各组之极差R(最大值-最小值=R)。
(f)计算总平均X(g)计算极差的平均R: (h)计算控制界限X 控制图:中心线(CL)= X 控制上限(UCL)= 控制下限(LCL)= R 控制图:中心线(CL)= 控制上限(UCL)= 管制下限(LCL)= 之值,随每组的样本数不同而有差异,但仍遵循三个标准差的原理计算而得,今已被整理成常用系数表。
(i)绘制中心线及控制界限,并将各点点入图中。
(j)将各数据履历及特殊原因记入,以备查考、分析、判断。
(2) 管制图:将数据(每组为一单位)依大小顺序排列,最中间的一个数据称为中位数;如为偶数个数值,则中间两数值的平均值即为中位数。
(a)收集数据并排列之(同 之数据收集方式步骤(a)(b)(c))。
(b)求各组的中位数 。
R X -)(/1/)......(321为组数k k Xi i kk X X X X X K =∑=++++=k Ri i k k R R R R X k /1/)......(321=∑=++++=R A X 2+R A X 2-R R D 4R D 3432,,D D A R X -~R X -(c)求各组的极差R 。
(d)计算中位数的总平均数 。
(e)计算 : (f)计算控制界限:控制图:中心线(CL)= 控制上限(UCL)= 控制下限(LCL)= R 控制图:中心线(CL)= 控制上限(UCL)= 控制下限(LCL)= 系数 相同亦可从系数表查得。
(g)同 控制图的步骤(i),(j)。
(3)X-Rm 控制图(a)收集数据20~25个,并依先后顺序排列记入数据栏内。
(b)求个别移动值Rm 。
如 (c)求平均值(d)求移动极差平均 :(e)计算控制界限X 控制图: 中心线(CL)= 控制上限(UCL)= 控制下限(LCL)=Rm 控制图: 中心线(CL)= 。
控制上限(UCL)= 。
管制下限(LCL)= 。
系数 同样可自系数表中查得。
(f)同 控制图的步骤(i),(j)。
2.计数值控制图: (1)P 控制图: (a) 收集数据20—25组,每组的样本数应一致,且最好能显现有1个以上的不良数(样本数如每组不一致,会导致控制界限的跳动,初期导入较不X ~ki X i kk X X X X K /~1/)~.....~~(~21=∑=+++=kRi i k k R R R R K/1/).....(21=∑=+++=X ~X~R A m X 23~+RA m X 23~-R R D 4R D 34323,,D D A m R X -1;.....,3,2,1,1-==-=+k n n i X X Rmi i i ,......,23212X X Rm X X Rm -=-=X 1/1/).....(21-∑=-+++=k Xi k X X X X k m R []1/1/)1(....21-∑=--++=k Rmi k k Rm R R m R m m X m R E X 2+m R E X 2-m R m R D 4m R D 3342,,D D E R X -适当)。
(b) 计算每组的不良率P 。
(c) 计算平均不良率P 。
(d) 计算控制界限: 中心线(CL):控制上限(UCL):控制下限(LCL):(e) 同 控制图步骤(i),(j)。
(2)pn 控制图: (又称np 控制图,d 控制图) (a)收集数据,步骤同P 控制图(a)项操作。
(b)计算平均不良数 。
(c)计算控制界限:中心线(CL) 控制上限(UCL) 控制下限(LCL) (d)绘控制界限,并将点点入a 图中。
(e)记入数据履历及特殊原因,以备检讨、分析、判断。
(3)C 控制图:(a)收集数据,步骤同P 控制图(a)项操作。
(b)计算平均缺点数 :(c)计算控制界限: 中心线 控制上限(UCL)= 控制下限(LCL)= (d)同pn 控制图的步骤(d),(e)。
(f) 记入数据履历及特殊原因,以备检讨、分析、判断。
(4)U 控制图:(a)收集20—25组数据(可取不同单位大小),每组样本应考虑含有1—5个缺点。
)(.....21为组数总检查数总不良个数k kPkP P P ++≠=P nP P P )1(3-+n P P P )1(3--RX -).(P n n P kPni i kn P /1=∑==组数总不良个数)()(p n p n ==)1(3p p n p n -+=)1(3p p n p n --=C k Ci i kk C C C C i/1.....21=∑=+++=CCL =)(C C 3+CC 3-(b)计算平均单位缺点数 : (c)计算控制界限: 中心线(CL)= 控制上限(UCL)= 控制下限(LCL)= (d)同C 控制图(d)步骤。
3.控制点的点绘要领:(1)各项工序名称、控制特性、测定单位、设备别、操作(测定)、样本大小、材料别、环境变化…等任何变更资料应清楚填入,以便资料的分析整理。
(2)计量值双控制图( 等)。
其X 控制图与R 控制图的控制界限宽度取法,一般原则以组的样本数(n)为参考,X 控制图的单位分度宽约为R 控制图的 倍。
(纵轴控制界限宽度约20—30m/m;横轴各组间隔约2-5mm)。
(3)中心线(CL)以实线记入,控制界限则记入虚线;各线上须依线别分别记入CL,UCL,LCL 等符号。
(4)CL,UCL,LCL 的数值位数计算比测定值多两位数即可。
(各组数据的平均计算数则取此测定值多一位数)。
(5)点之绘制有[²],[○],[△],[³]…等,最好由厂内统一规定。
(6)双控制图,二个控制图的绘制间隔限最少距20mm 以上,可行的话最好30mm 左右。
U n C n n n C C C U K K ∑∑=+++++==..........2121检查总样本数缺点总数UnUU 3+nUU 3-,...~,R X R X --n1东莞德信诚精品培训课程(部分)内审员系列培训课程查看详情TS16949五大工具与QC/QA/QE品质管理类查看详情 JIT东莞德信诚公开课培训计划>>> 培训报名表下载>>>/download/dgSignUp.doc六.控制图的判断:1.控制状态的判断(过程在稳定状态): (1)多数点子集中在中心线附近。