Improving the thermal stability of one-component
增材制造镍基高温合金裂纹形成机理及控制方法
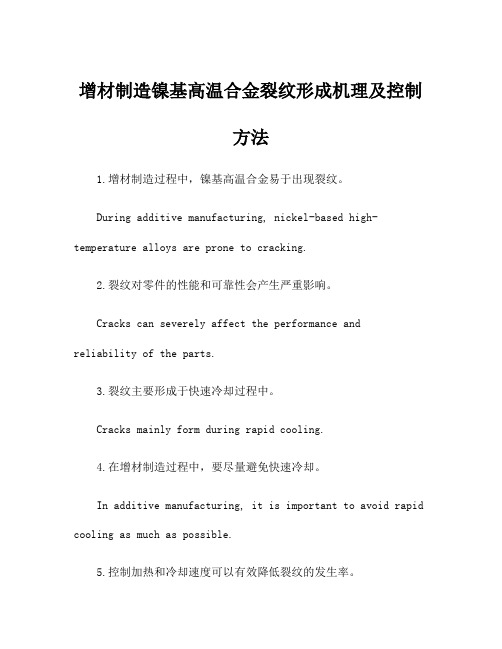
增材制造镍基高温合金裂纹形成机理及控制方法1.增材制造过程中,镍基高温合金易于出现裂纹。
During additive manufacturing, nickel-based high-temperature alloys are prone to cracking.2.裂纹对零件的性能和可靠性会产生严重影响。
Cracks can severely affect the performance andreliability of the parts.3.裂纹主要形成于快速冷却过程中。
Cracks mainly form during rapid cooling.4.在增材制造过程中,要尽量避免快速冷却。
In additive manufacturing, it is important to avoid rapid cooling as much as possible.5.控制加热和冷却速度可以有效降低裂纹的发生率。
Controlling the heating and cooling rates can effectively reduce the occurrence of cracks.6.合适的预热可以减少材料的残余应力。
Proper preheating can reduce the residual stress in the material.7.合理的工艺参数设置对于裂纹的控制至关重要。
Proper process parameter setting is crucial for controlling cracks.8.对材料的选择也会影响裂纹的形成。
Material selection also affects the formation of cracks.9.使用精细的粉末和合适的喷嘴可以减少裂纹的产生。
Using fine powder and suitable nozzles can reduce the formation of cracks.10.合适的气氛保护可以有效预防氧化带来的损坏。
耐火材料中萤石加入量

耐火材料中萤石加入量问题,并提供相关解释和实例。
耐火材料是指具有抗高温和耐磨损性能的材料,常用于高温工业设备和建筑物的部件。
而萤石是常见的耐火材料中的一种重要成分。
本文将详细探讨耐火材料中萤石的加入量对其性能的影响,并提供相关解释和实例。
首先,我们需要了解萤石的特性及其在耐火材料中的作用。
萤石,也被称为氟化钙,化学式为CaF2。
它具有很高的耐高温性能和化学稳定性,能够在高温环境下保持其结构稳定性。
此外,萤石还具有一定的导热性和导电性,并可降低耐火材料的脆性。
由于这些特性,萤石常被用作耐火材料的添加剂,以提升材料的综合性能。
然而,萤石的加入量并非越多越好,需要根据具体的应用和要求来确定。
通常,耐火材料中萤石的加入量在5到30之间。
以下是一些常见情况下的萤石加入量及其影响。
首先,考虑到防火材料的耐热性能,当需要增强耐火材料的耐高温性能时,可以适量增加萤石的加入量。
由于萤石具有高熔点和化学稳定性,其加入可以提升耐火材料的热稳定性和耐高温性能。
例如,对于用于高温炉窑内的耐火砖制造,适量加入萤石可以增强其耐火砖的耐高温性能,延长其使用寿命。
其次,考虑到耐火材料的热传导性能,当需要提高材料的导热性能时,适量加入萤石也是必要的。
萤石具有良好的导热性能,其热传导系数约为5.09 W/(m·K),高于大多数耐火材料的导热系数。
因此,在某些应用中,如炉膛壁和加热元件等需要良好的传热性能的部件,适量加入萤石可以提高耐火材料的热传导性能,促进热能的传递和利用。
此外,萤石的导电性能也可能影响耐火材料的应用性能。
当需要在高温环境下传导电流时,可适当增加萤石的含量。
比如,在电炉内部用于导电电极等部件,适量加入萤石可以增加耐火材料的导电性能,确保电能的传导和使用。
然而,过量的萤石加入量可能导致材料性能下降。
一方面,萤石的导热性能虽然好,但其热膨胀系数较大。
过量加入萤石可能导致材料的热膨胀系数增加,从而导致材料在高温情况下容易产生热应力和破裂。
高温稳定性英文
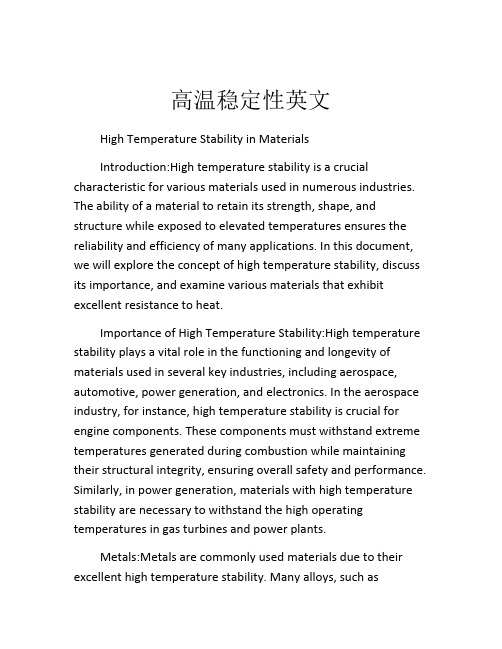
高温稳定性英文High Temperature Stability in MaterialsIntroduction:High temperature stability is a crucial characteristic for various materials used in numerous industries. The ability of a material to retain its strength, shape, and structure while exposed to elevated temperatures ensures the reliability and efficiency of many applications. In this document, we will explore the concept of high temperature stability, discuss its importance, and examine various materials that exhibit excellent resistance to heat.Importance of High Temperature Stability:High temperature stability plays a vital role in the functioning and longevity of materials used in several key industries, including aerospace, automotive, power generation, and electronics. In the aerospace industry, for instance, high temperature stability is crucial for engine components. These components must withstand extreme temperatures generated during combustion while maintaining their structural integrity, ensuring overall safety and performance. Similarly, in power generation, materials with high temperature stability are necessary to withstand the high operating temperatures in gas turbines and power plants.Metals:Metals are commonly used materials due to their excellent high temperature stability. Many alloys, such asnickel-based superalloys, exhibit outstanding resistance to heat. These alloys are used in gas turbines, where they can withstand temperatures over 1000°C while retaining their mechanical strength. Additionally, refractory metals like tungsten and molybdenum are known for their exceptional high temperature stability. They are utilized in applications where extreme heat resistance is required, such as furnace components, rocket nozzles, and electrical contacts.Ceramics:Ceramic materials are widely known for their high temperature stability. They are composed of non-metallic compounds and have crystalline structures, which contribute to their excellent thermal stability. Silicon carbide (SiC) is one of the most widely-used ceramics in high temperature applications. Its combination of high strength, stiffness, and low thermal expansion make it suitable for use in furnace linings, heat exchangers, and automotive components. Other ceramics like aluminum oxide (Al2O3) and zirconia (ZrO2) also possess high temperature stability and find applications in the aerospace and electronics industries.Composites:Composite materials, which consist of two or more different materials combined together, offer an opportunity to enhance high temperature stability. Fiber-reinforced composites, such as carbon fiber-reinforced polymers (CFRP), provide a high strength-to-weight ratio and exhibit excellent resistance to heat. CFPR composites are used extensively in aerospace and automotive industries, where they findapplications in aircraft fuselages, engine nacelles, andhigh-performance sports vehicles.Polymers:Although polymers generally have lower heat resistance compared to metals and ceramics, some polymers have been specifically designed to exhibit high temperature stability. Polyimides, for example, are known for their excellent thermal stability and are used in the aerospace industry for insulation, electrical wiring, and engine components. Polyether ether ketone (PEEK) is another high-performance polymer with excellent strength and resistance to heat, making it ideal for applications in the oil and gas industry, aerospace, and medical devices.Future Developments:Advancements in materials science and engineering continue to push the boundaries of high temperature stability. Ongoing research focuses on improving existing materials and developing new ones with enhanced heat resistance properties. Nanotechnology is being applied to enhance the performance of materials at high temperatures by creating nanostructured materials with unique properties. Additionally, the development of advanced coatings and surface treatments aims to enhance high temperature stability in a wide range of materials, extending their lifespan and performance in extreme environments.Conclusion:High temperature stability is a crucial property for materials utilized in various industries. Metals, ceramics, composites, and polymers with excellent resistance to heatenable the reliability and efficiency of many applications. Ongoing research and advancements in materials science will further expand the range and capabilities of high temperature stable materials, facilitating innovation and progress in a wide array of industries.。
超高分子量聚乙烯英文

超高分子量聚乙烯英文Ultrahigh Molecular Weight PolyethyleneUltrahigh Molecular Weight Polyethylene (UHMWPE) is a remarkable polymer that has gained significant attention in various industries due to its exceptional properties. This unique material is characterized by its exceptionally long polymer chains, resulting in a molecular weight that is significantly higher than that of conventional polyethylene. This distinguishing feature bestows UHMWPE with a remarkable combination of physical and mechanical properties that make it a highly versatile and sought-after material.One of the most notable characteristics of UHMWPE is its exceptional wear resistance. The long polymer chains in UHMWPE create a highly ordered and tightly packed molecular structure, which provides superior resistance to abrasion and impact. This makes UHMWPE an ideal material for applications where wear and tear are a significant concern, such as in the production of bearings, gears, and other mechanical components.In addition to its exceptional wear resistance, UHMWPE also exhibits excellent toughness and impact resistance. The long polymer chainsin UHMWPE are able to absorb and dissipate energy efficiently, which helps to prevent the material from cracking or breaking under stress. This property makes UHMWPE a popular choice for applications where impact resistance is crucial, such as in the production of protective equipment, sports gear, and medical implants.Another key advantage of UHMWPE is its chemical resistance. The material is highly resistant to a wide range of chemicals, including acids, bases, and solvents. This makes UHMWPE an ideal choice for applications where exposure to harsh chemicals is a concern, such as in the production of chemical processing equipment and storage tanks.In addition to its physical and mechanical properties, UHMWPE also exhibits excellent thermal stability. The material can withstand high temperatures without degrading, making it suitable for use in applications where exposure to heat is a concern, such as in the production of industrial machinery and equipment.One of the most significant applications of UHMWPE is in the medical field. The material's exceptional biocompatibility, low friction, and wear resistance make it an ideal choice for the production of medical implants, such as artificial joints and bone replacement components. UHMWPE is also used in the production of medicalequipment, such as surgical instruments and prosthetic limbs.In the industrial sector, UHMWPE is widely used in the production of a wide range of products, including conveyor belts, chute liners, and wear-resistant components for machinery. The material's low coefficient of friction and excellent abrasion resistance make it an ideal choice for these applications, where minimizing wear and tear is crucial.Another important application of UHMWPE is in the production of sports and recreational equipment. The material's high impact resistance and low weight make it a popular choice for the production of items such as skis, snowboards, and protective gear for various sports.Despite its many advantages, UHMWPE is not without its challenges. The material's high molecular weight and complex molecular structure can make it difficult to process and manufacture. Additionally, the cost of UHMWPE can be higher than that of other polymer materials, which can limit its use in certain applications.Despite these challenges, the demand for UHMWPE continues to grow, driven by the material's exceptional properties and its wide range of applications. As research and development in the field of polymer science continue to advance, it is likely that new andinnovative applications for UHMWPE will emerge, further solidifying its position as a critical material in a wide range of industries.In conclusion, Ultrahigh Molecular Weight Polyethylene is a remarkable polymer that has captured the attention of scientists, engineers, and industry professionals around the world. Its unique combination of physical, mechanical, and chemical properties make it an invaluable material in a wide range of applications, from medical implants to industrial equipment. As the demand for UHMWPE continues to grow, it is clear that this material will play an increasingly important role in shaping the future of technology and innovation.。
高熵合金的结构调控及储能研究

高熵合金的结构调控及储能研究1.高熵合金是一种由五种或更多组元组成的合金材料。
High-entropy alloy is an alloy material composed of five or more elements.2.高熵合金具有优异的力学性能和耐高温性能。
High-entropy alloys have excellent mechanical properties and high temperature resistance.3.结构调控是改善高熵合金性能的关键。
Structural control is the key to improving the performance of high-entropy alloys.4.通过合金元素的选择和比例调控,可以实现高熵合金的微观结构调控。
By controlling the selection and proportion of alloy elements, the microstructure of high-entropy alloys can be controlled.5.增强高熵合金的微观结构均匀性可以提高其力学性能。
Enhancing the microstructure homogeneity of high-entropy alloys can improve their mechanical properties.6.调控高熵合金的晶格缺陷可以提高其热稳定性。
Controlling the lattice defects of high-entropy alloys can improve their thermal stability.7.高熵合金可以作为储能材料,用于制备高性能的储能器件。
High-entropy alloys can be used as energy storage materials to prepare high-performance energy storage devices.8.通过合金化和微观结构调控,可以实现高熵合金的储能性能优化。
树脂基复合材料的多尺度结构调控
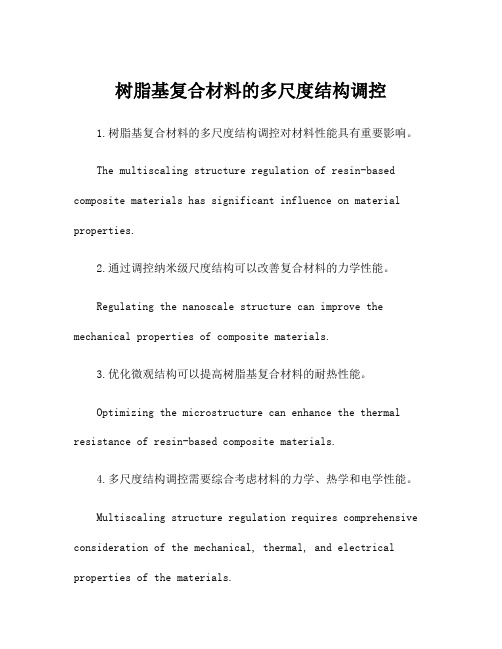
树脂基复合材料的多尺度结构调控1.树脂基复合材料的多尺度结构调控对材料性能具有重要影响。
The multiscaling structure regulation of resin-based composite materials has significant influence on material properties.2.通过调控纳米级尺度结构可以改善复合材料的力学性能。
Regulating the nanoscale structure can improve the mechanical properties of composite materials.3.优化微观结构可以提高树脂基复合材料的耐热性能。
Optimizing the microstructure can enhance the thermal resistance of resin-based composite materials.4.多尺度结构调控需要综合考虑材料的力学、热学和电学性能。
Multiscaling structure regulation requires comprehensive consideration of the mechanical, thermal, and electrical properties of the materials.5.纳米级结构的调控可以提高材料的强度和韧性。
Regulating the nanoscale structure can improve the strength and toughness of the materials.6.微观结构对树脂基复合材料的导电性能有显著影响。
The microstructure has a significant influence on the electrical conductivity of resin-based composite materials.7.调控介观结构有助于改善复合材料的耐磨性能。
环氧化天然胶乳天然胶乳并用提高探空气球胶膜气密性的研究
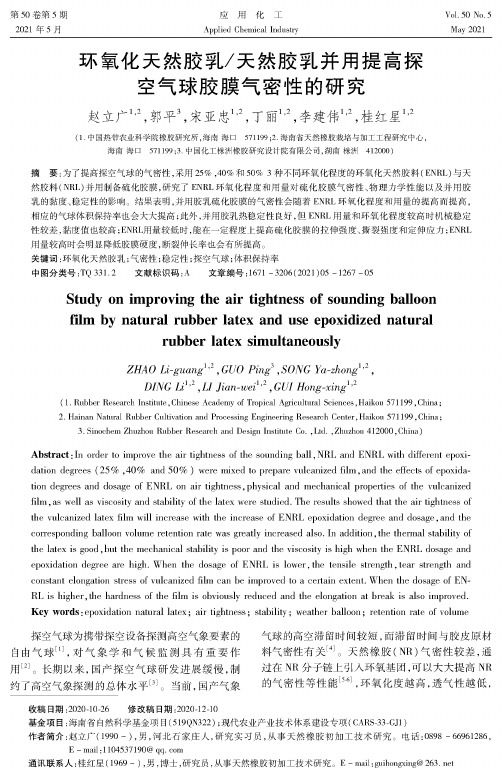
应用化工Appeoed ChemocaeIndustey第50卷第5期2021年5月Vol. 50 No. 5May2021环氧化天然胶乳/天然胶乳并用提高探空气球胶膜气密性的研究赵立广V ,郭平3,宋亚忠V ,丁丽V,李建伟V ,桂红星(1-中国热带农业科学院橡胶研究所,海南海口 5711992海南省天然橡胶栽培与加工工程研究中心,海南海口 571199;3-中国化工株洲橡胶研究设计院有限公司,湖南株洲412000)摘要:为了提高探空气球的气密性,采用25%,40%和50% 3种不同环氧化程度的环氧化天然胶料(ENRL )与天 然胶料(NRL )并用制备硫化胶膜,研究了 ENRL 环氧化程度和用量对硫化胶膜气密性、物理力学性能以及并用胶 乳的黏度、稳定性的影响。
结果表明,并用胶乳硫化胶膜的气密性会随着ENRL 环氧化程度和用量的提高而提高, 相应的气球体积保持率也会大大提高;此外,并用胶乳热稳定性良好,但ENRL 用量和环氧化程度较高时机械稳定性较差,黏度值也较高;ENRL 用量较低时,能在一定程度上提高硫化胶膜的拉伸强度、撕裂强度和定伸应力;ENRL 用量较高时会明显降低胶膜硬度,断裂伸长率也会有所提高。
关键词:环氧化天然胶乳;气密性;稳定性;探空气球;体积保持率中图分类号:TQ331.2 文献标识码:A 文章编号:1671 -3206(2021)05 -1267 -05Sthdy on improving the air tightness of sounding balloonfilm by nathral rpbbee latex and uss eroxinized natsrairpbbee latex simultaneouslyZHAO Li-guang 1,2 , GUO Ping 3 ,SONG Ya-zhoog 1,2 ,DING L- - , LI Jian-gei 1 - , GUI Hong-xing 1,2( 1.RubbeeReseaech InstotuteChoneseAcademyooTeopocaeAgeocuetueaeScoencesHaokou 571199%Chona ; 2.Haonan NatueaeRubbeeCuetoeatoon and Peoce s ongEngoneeeongReseaech CenteeHaokou 571199%Chona ;3. S onochem Zhuehou RubbeeReseaech and Desogn InstotuteCo.Ltd.Zhuehou 412000%Chona )Abstract : In order to improve the air tightnes s of the sounding bll , NRL and ENRL with dOferent epoxi dation deareas (25% ,40% and 50% ) were mixed to prepare vulcanized film , and the OW c -s of epoxida- toon degeeesand dosageooENRLon aoetoghtne s physocaeand mechanocaepeopeetoesootheeuecanoeedooem %aswe e aseoscosotyand staboeotyootheeateiweeestudoed.Theeesuetsshowed thattheaoetoghtne s ootheeuecanoeed eateiooem wo e onceeasewoth theonceeaseooENRLepoiodatoon degeeeand dosageand the co e spondongba e oon eoeumeeetentoon eatewasgeeateyonceeased aeso.In addotoon %thetheemaestaboeotyootheeateiosgood %butthemechanocaestaboeotyospooeand theeoscosotyoshogh when theENRLdosageand epoiodatoon degeeeaeehogh.When thedosageooENRLoseoweethetensoeesteength % t eaesteength andconstanteeongatoon stee s ooeuecanoeed ooem can beompeoeed toaceetaon eitent.When thedosageooEN- RLoshogheethehaedne s ootheooem osobeoouseyeeduced and theeeongatoon atbeeak osaesoompeoeed.Key words : epoiodatoon natueaeeatei ; aoetoghtne s ; staboeoty ; weatheeba e oon ; eetentoon eateooeoeume探空气球为携带探空设备探测高空气象要素的 自由气球[1],对气象学和气候监测具有重要作用⑵。
硅等离子体
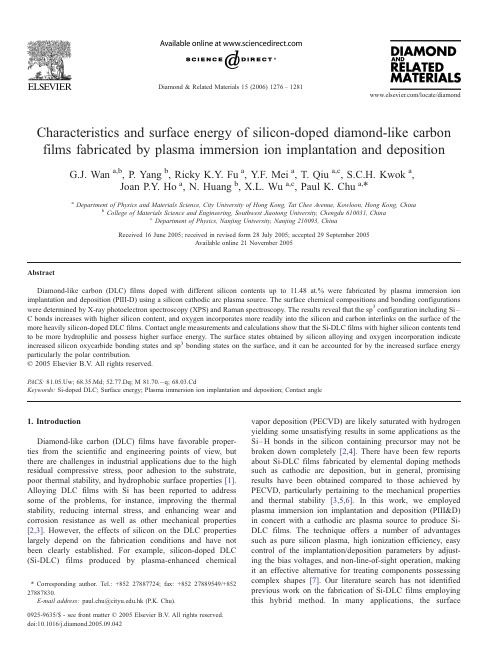
Characteristics and surface energy of silicon-doped diamond-like carbon films fabricated by plasma immersion ion implantation and depositionG.J.Wan a,b ,P.Yang b ,Ricky K.Y .Fu a ,Y .F.Mei a ,T.Qiu a,c ,S.C.H.Kwok a ,Joan P.Y .Ho a ,N.Huang b ,X.L.Wu a,c ,Paul K.Chu a,*aDepartment of Physics and Materials Science,City University of Hong Kong,Tat Chee Avenue,Kowloon,Hong Kong,ChinabCollege of Materials Science and Engineering,Southwest Jiaotong University,Chengdu 610031,ChinacDepartment of Physics,Nanjing University,Nanjing 210093,ChinaReceived 16June 2005;received in revised form 28July 2005;accepted 29September 2005Available online 21November 2005AbstractDiamond-like carbon (DLC)films doped with different silicon contents up to 11.48at.%were fabricated by plasma immersion ion implantation and deposition (PIII-D)using a silicon cathodic arc plasma source.The surface chemical compositions and bonding configurations were determined by X-ray photoelectron spectroscopy (XPS)and Raman spectroscopy.The results reveal that the sp 3configuration including Si–C bonds increases with higher silicon content,and oxygen incorporates more readily into the silicon and carbon interlinks on the surface of the more heavily silicon-doped DLC films.Contact angle measurements and calculations show that the Si-DLC films with higher silicon contents tend to be more hydrophilic and possess higher surface energy.The surface states obtained by silicon alloying and oxygen incorporation indicate increased silicon oxycarbide bonding states and sp 3bonding states on the surface,and it can be accounted for by the increased surface energy particularly the polar contribution.D 2005Elsevier B.V .All rights reserved.P ACS:81.05.Uw;68.35.Md;52.77.Dq;M 81.70.Àq;68.03.CdKeywords:Si-doped DLC;Surface energy;Plasma immersion ion implantation and deposition;Contact angle1.IntroductionDiamond-like carbon (DLC)films have favorable proper-ties from the scientific and engineering points of view,but there are challenges in industrial applications due to the high residual compressive stress,poor adhesion to the substrate,poor thermal stability,and hydrophobic surface properties [1].Alloying DLC films with Si has been reported to address some of the problems,for instance,improving the thermal stability,reducing internal stress,and enhancing wear and corrosion resistance as well as other mechanical properties [2,3].However,the effects of silicon on the DLC properties largely depend on the fabrication conditions and have not been clearly established.For example,silicon-doped DLC (Si-DLC)films produced by plasma-enhanced chemicalvapor deposition (PECVD)are likely saturated with hydrogen yielding some unsatisfying results in some applications as the Si–H bonds in the silicon containing precursor may not be broken down completely [2,4].There have been few reports about Si-DLC films fabricated by elemental doping methods such as cathodic arc deposition,but in general,promising results have been obtained compared to those achieved by PECVD,particularly pertaining to the mechanical properties and thermal stability [3,5,6].In this work,we employed plasma immersion ion implantation and deposition (PIII&D)in concert with a cathodic arc plasma source to produce Si-DLC films.The technique offers a number of advantages such as pure silicon plasma,high ionization efficiency,easy control of the implantation/deposition parameters by adjust-ing the bias voltages,and non-line-of-sight operation,making it an effective alternative for treating components possessing complex shapes [7].Our literature search has not identified previous work on the fabrication of Si-DLC films employing this hybrid method.In many applications,the surface0925-9635/$-see front matter D 2005Elsevier B.V .All rights reserved.doi:10.1016/j.diamond.2005.09.042*Corresponding author.Tel.:+852********;fax:+852********/+852********.E-mail address:paul.chu@.hk (P.K.Chu).Diamond &Related Materials 15(2006)1276–1281/locate/diamondproperties,particularly the surface free energy and surface tension,are very important.They affect important surface properties such as hydrophilicity,adhesion to the substrate, and adsorption behavior in many circumstances.In this paper,we report the characterization as well as surface energy investigation of the Si-DLC films produced by this hybrid technique.2.Experimental detailsFilm deposition was conducted in our plasma immersion ion implantation and deposition(PIII&D)equipment that has been described in detail elsewhere[7–9].P-type silicon (100)wafers were used as the substrate.The silicon plasma was generated by a cathodic arc plasma source composed of a pure silicon cathode.The triggering voltage was¨3kV and the main arc current was maintained at around120A. The arc duration time was about250A s and the repetition frequency was60Hz.The emitted silicon plasma drifted through a90-curved magnetic duct to eliminate deleterious macro-particles and was subsequently attracted to the silicon substrate biased at aÀ100V DC(direct current).At the same time,acetylene gas was bled into the PIII&D chamber as the carbon precursor.The streaming silicon plasma collided with the C2H2molecules causing partial ionization, and the films were deposited by reaction of ionized silicon with ionized acetylene and some unionized molecules. Different C2H2gas flows were used to control the silicon doping content and the instrumental conditions are summa-rized in Table1.Raman spectra were acquired on a Renishaw RM3000micro-Raman system with a laser source wavelength of514nm and the spectra were collected by scanning from800to2200cmÀ1.X-ray photoelectron spectroscopy(XPS)was performed using a PHI 5600equipped with a monochromatic Al K a X-ray source(1486.6 eV)to determine the surface composition and chemical states.The surface free energy was determined by a contact angle test using the sessile drop method on the JY-82contact angle goniometer at ambient humidity and temperature.Doubly distilled water and five additional test liquids,glycerin, formamide,diiodomethane,glycol,and tritolyl phosphate, were used to determine the hydrophilicity as well as surface energy of the samples.In each test,six measurements were conducted on each sample taken from five different fields on the deposited wafer to obtain good statistics.The surface energy of the films was calculated using the Zimans and Good method[10]by combining the Young equation and the Van Oss equation of the work of adhesion[11,12]:W a¼2c p l c p sÀÁ1=2þ2c d l c d sÀÁ1=2¼c l1þcos hðÞ;ð1Þwhere W a is work of adhesion,h is the contact angle,c l,c l d and c l p are the surface tension and its dispersive and polar components of the liquid phases,respectively,and c s d and c s p are the dispersive and polar components of the solid phases, respectively.Eq.(1)can be further simplified as:c l1þcos hðÞ2c dlÀÁ1=2¼c d sÀÁ1=2þc p sÀÁ1=2c p lcl1=2ð2ÞBy using the archival relative surface tension component values of the test liquids shown in Table2[10–12]and solving Eq.(2)with the contact angles measured from more than two test liquid/solid interfaces,we can obtain c s d and c s p.The surface tension is defined to be the sum of the dispersive c s d and polar c s p contributions.In our experiments,six test liquid/solid interfaces were chosen to obtain good statistics.3.Results and discussionRaman spectroscopy is a common and powerful tool to study the structural properties of DLC due to the high scattering efficiency of the carbon-to-carbon bonding states.Fig.1shows the Raman spectra acquired between800and2200cmÀ1from the Si-DLC films.All the spectra reveal a typical DLC structure characterized by one band composed of the main G(graphite) peaks and D(disordered)shoulder.This is in contrast toTable1PECVD instrumental parametersSample number F C2H2(sccm)Pressure(Torr)Bias voltage(V)Silicon arc sourceTriggervoltageMain arccurrent#120 4.0Â10À4À100(DC)3kV120A (250A s,60Hz)#215 3.2Â10À4 #310 1.8Â10À4 #45 1.0Â10À4Table2Surface tension parameters of the test liquids at20-CLiquid c LV c p LV c d LVDouble distilled water72.851.021.8Glycol48.319.029.3Diiodomethane50.8 2.348.5Formamide58.218.739.5Tritolyl phosphate40.9 1.739.2Glycerin63.426.437.0Intensity/a.u.Wavenumber / cm-1Fig.1.Raman spectra of Si-DLC films produced by PIII&D.G.J.Wan et al./Diamond&Related Materials15(2006)1276–12811277graphite that typically shows two separate peaks at¨1550and ¨1350cmÀ1[13].The Raman line shape changes to being less asymmetrical corresponding to the changes in the diamond-like structure with higher silicon content at decreased C2H2partial pressure.All the main peaks show obvious low frequency shift compared to graphite,and a slight shift to a lower frequency for the G peaks can be observed.This is consistent with the increase in the diamond-like structure.On the other hand,the shift of the G band may be partially related to the de-straining action of silicon,and the shift of the D band arises from increased disorder due to increases in the averaged bond lengths[14].Detailed deconvolution of the Raman spectra intothe two peaks is useful to discern the DLC structure,for example,the sp3to sp2ratio,graphite cluster size,and extent of disorder[13].Table3lists the fitted results of the Raman spectra of the Si-DLC films.The ratio of the Raman signal I D/ I G is one important empirical factor to evaluate the carbon–carbon bonding states in the DLC film,and a smaller I D/I G value is commonly correlated with an increased sp3to sp2ratio [13,15].We observe the decreased I D/I G trend with silicon doping increasing from samples#1to#2and#4and a small deviation in sample#3showing slightly higher I D/I G ratio than sample#2.Nonetheless,it should be noted that the aforementioned relationship between the D and G bands in the Raman spectra is established for pure DLC films and not Si-DLC films,which should be more complicated.For instance, the Raman peak at approximately1450cmÀ1associated with Si–C bonds can also affect the intensity and position of the G peak,albeit at a lower scattering efficiency[2],but on the other hand,the conspicuous second-order peak of the Si substrate at approximately960cmÀ1,of which the intensity is proportional to the optical transparency of the film,produces errors in the deconvolution by affecting the background of the D peaks[3]. This may be the reason why some of the specific fitting parameters appear to be scattered.From this point of view,XPS may offer a more reliable analysis in this case because it provides more accurate information on the surface structures and bonding states of the films.In fact,it has been shown to disclose the structure of DLC and Si-DLC films more effectively[14,16,17].The surface compositions of the Si-DLC films derived from the C1s,Si2p,and O1s photoelectron core level XPS spectra are listed in Table4.Our results indicate that the Si dose is indeed increased by reducing the mass flow,that is,partial pressure of C2H2.It can also be observed that the oxygen content is negligibly low in the silicon doped film with the smallest silicon concentration,which is related to the small oxygen concentration in most DLC films,and that oxygen incorporation increases with higher silicon doping.The C1s spectrum is most useful in identifying the chemical states of the Si-DLC films.The surface chemical states of carbon in the Si-DLC films include mainly C_C(sp2),C–C(sp3),Si–C(sp3), and C_O.As shown in Fig.2,peak deconvolution is conducted by fixing the energies of the four bonding states at 283.3T0.1,284.2T0.1,285.1T0.1and286.5T0.1eV,respec-tively[14–18].The sp3fraction and two different sp3to sp2 ratios calculated by sp3([Si–C]+[C–C])/sp2([C_C])for the Si-DLC film,and sp3([C–C])/sp2([C_C])for amorphous carbon reveal detailed bonding state changes in the films,as shown in Table4.The results are plotted in Fig.3as a function of the C2H2flow conditions.We can see that the sp3to sp2ratio of the former increases from samples#1to#4monotonically, and the latter increases from sample#1to#2first and then decreases slightly with silicon doping increasing.It can be concluded that silicon is likely incorporated in the film by replacing carbon atoms to form sp3bonds.At low silicon doping level,the sp3fraction for interlinks of DLC increases, as there are more induced disordered states of carbon–carbon bonds(including sp3)by Si alloying.In contrast,at a high silicon doping concentration,Si incorporation can reduce the sp3fraction of interlinks of DLC by replacing carbon in the sp3 matrix,while the overall sp3fraction including[Si–C]and[C–C]in the films increases,as shown in Table4and Fig.3.The configurations of silicon and carbon on the surface are likely more complicated due to the oxygen incorporating effects.To reveal more details,the Si2p and O1s XPS spectra were recorded.As shown in Fig.4,the Si2p peaks of the Si-DLC films prepared under high C2H2partial pressure with the smallest amount of silicon are relatively symmetric and centered around100.5eV due to Si–C bonding only[18,19].The results indicate that no oxidation has occurred and very little oxygen is present on the surface.With increasing silicon concentration, the Si2p peaks of samples(#2,#3,#4increasingly)are more asymmetrical exhibiting a higher-shift shoulder that can be ascribed to silicon oxycarbide(SiO x C y:SiOC3,SiO2C2SiO3C) bonding states[19,20].It shows that some of the silicon atoms (or silicon carbide)on the surface combine readily with oxygen by the natural oxidation process.This can be further confirmed by the marked oxygen composition changes with higher silicon concentration.As shown in the O1s spectra in Fig.4,oxygen forms both C_O(531.2T0.2eV)and SiO x C y(532.3T0.2eV) bonds and the latter becomes more noticeable at higher silicon concentration[20].It should also be noted that oxidation willTable3The fitting results of Raman spectra of Si-DLC films prepared by PIII&DSample no.D-peak(cmÀ1)G-peak(cmÀ1)FWHM(D)FWHM(G)I D/I G#11289.51500.6200.00187.470.452 #21275.21487.6199.17193.550.393 #31291.71495.8198.35187.200.410 #41258.21478.3162.38204.900.284Table4Compositions of the Si-DLC films obtained by XPS,sp3to sp2ratio and sp3 fraction calculated by deconvoluting of C1s spectra of the prepared films Samples Si(at.%)O(at.%)C(at.%)sp3([Si–C]+[C–C])/sp2([C_C])sp3([C–C])/sp2([C_C])sp3fraction a#1 2.89 1.495.710.2890.2380.218 #27.76 3.0589.190.4400.2610.294 #310.01 5.1184.880.5580.2500.338 #411.48 5.2983.230.6070.2490.357a sp3fraction represents(sp3[Si–C]+sp3[C–C])/(sp2[C_C]+ sp2[C_O]+sp3[Si–C]+sp3[C–C]).G.J.Wan et al./Diamond&Related Materials15(2006)1276–1281 1278not affect the aforementioned conclusions on the sp 3fraction,as silicon is known to form only the sp 3bonding state even as silicon oxycarbide species.The surface energy results reveal important thermodynamic properties of the films.In general,the higher the surface energy of the solid substrate relative to the surface tension of the liquids,the better is the hydrophilicity and the smaller is the contact angle as well as the better the adhesion to the substrate.Surface energy arises from the imbalance of the force between atoms ormolecules at the interface.Several types of van der Waals interactions contribute to the surface energy that is dictated by two factors,dispersive c d and polar c p [10].Fig.5shows the contact angles with water,surface energy,ratio of c p /c d and Si doping concentrations in the Si-DLC films as a function of the flow of C 2H 2and deposition conditions.The water contact angles decrease and the surface tension increases monotonically with higher silicon concentrations indicating that our Si-DLCa cbdBinding energy (eV)288.0 288.0 284.0284.0 Binding energy (eV)Binding energy (eV)288.0 288.0 284.0284.0 Binding energy (eV)Fig.2.Deconvoluted C1s core level photoelectron spectra of Si-DLC films produced by PIII&D:(a)sample #1,(b)sample #2,(c)sample #3,and (d)sample #4.24681012S i c o n t e n t / a t . %s p 2 / s p 2 r a t i oF C2H2Fig.3.sp 3/sp 2ratio,silicon concentrations calculated by XPS of Si-DLC films and the relationship with C 2H 2flow conditions.I n t e n s i t y / a .u .Binding Energy / eVC=OFig.4.XPS Si2p and O1s core level spectra of Si-DLC films prepared by PIII&D.G.J.Wan et al./Diamond &Related Materials 15(2006)1276–12811279films with higher silicon concentration tend to be more hydrophilic.With regard to the surface energy,the two components vary and contribute differently.There is no obvious change in the dispersive components with higher silicon doping concentration,as the doses are relatively low without changing substantially the main interlinks of the carbon atoms as well as density of the films.The dispersive contribution is built up from a single interaction,which is generated by the movement of electrons around an atom or molecule depending largely on the kind and density of the materials.This effect should be insignificant in Si–C bonds compared to other bonding states because silicon and carbon are isoelectronic.The polar components increase obviously with higher silicon concentra-tions as shown in Fig.5.Thus,the increased surface tension mainly arises from the higher polar contribution.The polar component is built up from different forces/interactions,like hydrogen bonds,covalent bonds and dipole–dipole interactions.The difference in the polar contribution to the total surface energy plays a critical role in determining the hydrophilicity for a polar liquid like water [10,21].The increased polar contribution of the Si-DLC with increased Si contents is accordingly related to the surface bonding states obtained by silicon alloying and oxygen incorporation.It should be noted that the Si-doped amorphous carbon materials reported in the literature appear to exhibit contra-dicting surface energy trends with increased silicon doping content,but it is well established that the surface properties depend critically on the preparation methods.To our knowl-edge [22,23],Si-DLC films produced by PECVD show decreased surface energy and are more hydrophobic with higher silicon concentrations.This is mainly ascribed to the substantially decreased dispersive component arising from excessive hydrogen bonding with silicon to form Si–H as well as increased defects such as vacancies that reduce the film density and change the electron distribution largely compared to silicon replacing carbon.Si-DLC films fabricated by a pure silicon doping method like cathodic arc or sputtering show consistent results and produce relatively high polar componentscompared to other DLC films or some metals (Ni,Ti,Al)doped DLC [24].P.Zhang et al.conclude that the adsorption of oxygen on the surface plays an important role on the polar component of the metal doped DLC (a-C:Me)films including Si-DLC,and Si–O bonds contribute to the high polar component of a-C:Si films [24].Similar results are observed in our case.The increased polar component of our prepared samples can be accounted for mainly by the surface states characterized by silicon oxycarbide bonding states.They are more polar than the silicon to carbon and carbon to carbon bonding states.The increased sp 3configuration interlinks may contribute partly to it.More probably,some silicon atoms at the surface can readily form chemical bonds with oxygen without the hydrogen passivating effects as revealed in cases by PECVD.4.ConclusionSilicon-doped DLC films were produced by plasma immersion ion implantation and deposition (PIII&D)and cathodic arc plasma deposition.We observe increased sp 3fraction configurations as well as more oxidation taking place on the Si-DLC films with higher silicon contents.The samples exhibit increased surface energy and become more hydrophilic with increased silicon doping content due to surface states obtained by silicon alloying as well as oxygen incorporation.This trend is dissimilar to that observed from films deposited using conventional PECVD.Our results address potentially the drawbacks of PECVD DLC in many applications.The increased surface energy of films prepared by this novel method should be beneficial to film adhesion particularly for DLC coatings in microelectronic and some biological applica-tions.For instance,the more hydrophilic surface may enable the DLC film to produce a more effective anti-bacterial coating with F conditioning _bio-films in vivo [25,26],and potentially better anti-thrombosis properties in blood contacting applica-tions by reducing fibrinogen interactions with the film surface [22,27].AcknowledgementsWe would like to thank Dr.Wilson K.W.Wong of City University of Hong Kong for assistance in the XPS analysis.This work was financially supported by Hong Kong Research Grants Council (RGC)Competitive Earmarked Research Grant (CERG)#CityU 1120/04E,Hong Kong RGC and NSFC Joint Scheme N _CityU101/03,as well as NSFC No.30370407of China.References[1]J.Robertson,Prog.Solid State Chem.21(1991)199.[2]A.L.Baia Neto,R.A.Santos,F.L.Freire Jr.,S.S.Camargo Jr.,R.Carius,F.Finger,W.Beyer,Thin Solid Films 293(1997)206.[3]C.S.Lee,K.R.Lee,K.Y .Eun,K.H.Yoon,J.H.Han,Diamond Relat.Mater.11(2002)198.[4]P.Papakonstantinou,J.F.Zhao,P.Lemoine, E.T.McAdams,J.A.McLaughlin,Diamond Relat.Mater.11(2002)1074.S u r f a c e e n e r g y / m N .m -1F C2H2C o n t a c t a n g l e /D e g r e eγp / γdS i c o n t e n t / a t .%Fig. 5.Water contact angles,surface energy,c p /c d ratio and Si doping concentrations of the Si-DLC films and the relationship with flow rate of C 2H 2.G.J.Wan et al./Diamond &Related Materials 15(2006)1276–12811280[5]J.R.Shi,X.Shi,Z.Sun,E.Liu,H.S.Yang,L.K.Cheah,X.Z.Jin,J.Phys.,Condens.Matter11(1999)5111.[6]W.J.Wu,M.H.Hon,Surf.Coat.Technol.111(1999)134.[7]P.K.Chu,S.Qin,C.Chan,N.W.Cheung,rson,Mater.Sci.Eng.,RRep.17(1996)207.[8]P.K.Chu,J.Vac.Sci.Technol.,B22(1)(2004)289.[9]R.K.Y.Fu,Y.F.Mei,G.J.Wan,G.G.Siu,Paul K.Chu,Y.X.Huang,X.B.Tian,S.Q.Yang,J.Y.Chen,Surf.Sci.573(2004)426.[10]R.J.Good,J.Adhes.Sci.Technol.2(6)(1992)1269.[11]C.J.Van Oss,M.K.Chaudhury,R.J.Good,Chem.Rev.88(1988)927.[12]M.Amaral,M.A.Lopes,J.D.Santos,R.F.Silva,Biomaterials23(2002)4123.[13]A.C.Ferrari,J.Robertson,Phys.Rev.,B61(20)(2000)14095.[14]J.F.Zhao,P.Lemoine,Z.H.Liu,J.P.Quinn,P.Maguire,J.A.Mc Laughlin,Diamond Relat.Mater.10(2001)1070.[15]B.K.Tay,X.Shi,H.S.Tan,H.S.Yang,Z.Sun,Surf.Coat.Technol.105(1998)155.[16]P.Me´rel,M.Tabbal,M.Chaker,S.Moisa,J.Margot,Appl.Surf.Sci.136(1998)105.[17]J.X.Liao,W.M.Liu,T.Xu,Q.J.Xue,Carbon42(2004)387.[18]J.F.Moulder,W.F.Stickle,P.E.Sobol,K.D.Bomben,in:J.Chatain(Ed.),Handbook of X-ray Photoelectron Spectroscopy,Perkin-Elmer,Eden Prairie,MN,1992.[19]C.K.Park,S.M.Chang,H.S.Uhm,S.H.Seo,J.S.Park,Thin Solid Films420–241(2002)235.[20]R.P.Socha,ajalehto,P.Nowak,Surf.Interface Anal.34(2002)413.[21]D.H.Kaelble,J.Moacanin,Polymer18(1977)475.[22]T.I.T.Okpalugo, A.A.Ogwu,P.D.Maguire,J.A.D.MuLaughlin,Biomaterials25(2004)239.[23]M.Grischke,A.Hieke,F.Morgenweck,H.Dimigen,Diamond Relat.Mater.7(1998)454.[24]P.Zhang,B.K.Tay,G.Q.Yu,u,Y.Q.Fu,Diamond Relat.Mater.13(2004)459.[25]A.Grill,Diamond Relat.Mater.12(2003)166.[26]A.Auditore,C.Satriano,U.Coscia,G.Ambrosone,V.Parisi,G.Marletta,Biomol.Eng.19(2002)85.[27]B.Ivarsson,I.Lundstrom,CRC Crit.Rev.Biocompat.2(1)(1986)1.G.J.Wan et al./Diamond&Related Materials15(2006)1276–12811281。
- 1、下载文档前请自行甄别文档内容的完整性,平台不提供额外的编辑、内容补充、找答案等附加服务。
- 2、"仅部分预览"的文档,不可在线预览部分如存在完整性等问题,可反馈申请退款(可完整预览的文档不适用该条件!)。
- 3、如文档侵犯您的权益,请联系客服反馈,我们会尽快为您处理(人工客服工作时间:9:00-18:30)。
Wood Sci Technol(2011)45:383–388DOI10.1007/s00226-010-0321-yO R I G I N A LImproving the thermal stability of one-component polyurethane adhesives by addingfiller materialSebastian Clau b•Karin Allenspach•Joseph Gabriel•Peter NiemzReceived:27March2009/Published online:30March2010ÓSpringer-Verlag2010Abstract The aim of the current study is to improve the thermal stability of one-component moisture-curing polyurethane adhesives.The approach here tends to add suitablefiller materials to the adhesive and to study the resulting effects.The investigation covers mechanical tests to determine the shear strength of the glued wood joints according to EN302-1(2004).Furthermore,the distribution of thefiller material within the adhesive is shown by means of environmental scanning electron microscopy combined with energy-dispersive X-ray spectroscopy analysis.The thermal stability of the glued wood joints could be significantly improved by adding chalk with a volume fraction of30%to the adhesive.IntroductionOne-component polyurethane adhesives(1C PUR)are increasingly used for the bonding of wood.The properties of the reacted polymers(like elasticity,strength, temperature,and moisture resistance)are influenced by the prepolymer as well as by additives like surfactant,catalyst,and especiallyfiller material.Filler materials are non-volatile,non-gluing matters,which are insoluble in the mon fillers arefibres(glassfibre,mica),powders(cellulose,aluminium oxide,silica), sheet-like materials(talc),cubic materials(chalk,barytes)(Zeppenfeld and Grunwald2005)or nowadays nano-particles(Park et al.2009)or functionalised nanoclays(Dodiuk et al.2006).S.Clau b(&)ÁK.AllenspachÁP.NiemzETH Zurich,Institute for Building Materials,Schafmattstrasse6,8093Zurich,Switzerlande-mail:sclauss@ethz.chJ.GabrielPurbond,Industriestrasse17a,6203Sempach Station,SwitzerlandIn the past,several investigations on different types of adhesives andfillers have been carried out.The mechanical properties of polyvinyl acetate depending on morphology and chemical structure of thefiller material(calcium carbonate)were investigated by Kovacˇevic´et al.(1996).The influence of the samefiller on the rheological and adhesion properties of a water-based polyurethane dispersion was investigated by Mun˜oz Mila´n et al.(2005).Mansouri and Pizzi(2007)improved the performance of urea–formaldehyde and phenol–formaldehyde resin by adding micronised polyurethane powder.Sepulcre-Guilabert et al.(2001)proposed natural ultramicronised calcium carbonate and mixtures of fumed silica with natural ultramicronised calcium carbonate asfiller for solvent-based PUR.Investigations on the structure–property relationships of1C PUR adhesives for wood,including adhesives withfibrousfillers,and their sensitivity to low wood moisture content(WMC)were carried out by Beaud et al.(2006).In contrast, Richter and Schierle(2002)and Schro¨dter and Niemz(2006)investigated the adhesive performance of1C PUR under high moisture and temperature conditions. It can be concluded that the bonding strength of1C PUR adhesives decreases with increasing WMC and temperature,respectively.The investigations mentioned above show that the adhesion of joints produced with adhesives containingfillers was noticeably increased.The goal of this study is to investigate if comparable improvements are also achievable for the use of1C PUR adhesives under high temperature exposure.Materials and methodsThree laboratory adhesives were produced by Purbond(Sempach Station,Switzer-land)with a varyingfiller material content.Thereby chalk was mixed into the adhesive using volume fractions of15and30%.The adhesives’parameters are listed in Table1.All bondings were carried out with beech wood(Fagus sylvatica L.).The raw density q at an equilibrium moisture content x of(12±1)% amounted to(745±34)kg/m3.The one-sided application of the adhesives was carried out with a spread of150g/m2and a pressing pressure of0.7MPa.To investigate the influence of thefiller material content on the shear strength,15 specimens of each group were tempered in a drying chamber for1h at100and 150°C,respectively.Another group of specimens was conditioned at different relative humidities(35,65,85,95%RH)at a temperature of20°C.Table1Adhesives’structural propertiesAdhesive A B CFiller content(%)01530 Isocyanat(%)151515 Open time(min)606060 Viscosity(mPas)6,5809,34013,960The shear strength was determined according to EN302-1(2004).The specimens were tested using a displacement-controlled universal testing machine (Zwick Z100)under standard climatic conditions(20°C,65%RH).The shear strain e was evaluated with a video-extensometer.After recording the stress–strain curve until failure,the wood failure percentage was estimated visually in steps of 10%.In addition,an environmental scanning electron microscope(ESEM)was used, and the bondline was analysed by means of energy-dispersive X-ray spectroscopy (EDX)to investigate the penetration depth and distribution of the adhesives within the wood.The EDX analysis allows for chemical characterisation of the specimens and thereby to distinguish between adhesive,wood andfiller material,which contains a high amount of calcium.Results and discussionThe shear strength of the glued wood joints increased significantly with a higher content offiller material.The graphs in Fig.1indicate an increase of strength at standard climatic conditions,but also after temperature exposure.The maximum increase amounted to52%at100°C using30%filler.The wood failure percentage was also increased compared to adhesives withoutfiller(Table2)as a consequenceTable2Mean shear strength and median wood failure percentage of adhesive joints at varying climatic conditionsConditions AdhesiveA B CT(°C)RH(%)x(%)s(MPa)WF(%)s(MPa)WF(%)s(MPa)WF(%)150–0.09.42(1.30)010.89(3.28)5013.61(2.28)70100– 1.710.86(2.18)012.26(2.41)7016.24(2.43)70 2035 6.513.48(1.85)10016.35(1.47)10017.72(1.90)90 206511.812.29(1.85)5012.74(2.38)2016.37(1.54)30 208516.59.10(2.02)208.98(2.49)010.81(1.43)0 209521.4 5.58(2.70)0 5.44(1.87)0 6.44(2.54)0s mean tensile shear strength,standard derivation in brackets,WF median wood failure percentage,T temperature,RH relative humidity,x mean wood moisture contentof the better adhesion between wood and adhesive,which subsequently exceeded the wood strength.The effect of thefiller material decreased with increasing WMC.At6.5%wood moisture,the maximum overall increase of shear strength amounted to31%at30%filler material.Schro¨dter and Niemz(2006)determined maximum compression shear strength at about12%WMC within a similar investigation on commercially available1C PUR adhesives.From this,it follows that after the drying process, internal compression stresses arise within the bondline,which have a positive effect in the case of tensile load.In contrast to the specimens exposed to high temperatures,the average increase in shear strength at21.4%WMC was relatively low(15%);however,there was no significance at the5%level(Fig.2).This means that thefiller material had no substantial effect on the shear strength at high WMC.The limiting factor for the adhesive bond is the moisture resistance of the adhesive itself,independent of its filler material content.Hydrolytic effects are a possible explanation for the lower shear strength.The main reason for the increased shear strength is the reduced penetration into the cell lumina,which is clearly shown by the combined ESEM/EDX micrograph (Fig.3).On the left side(30%filler),a completelyfilled bondline and empty pores document a good bond.The adhesive withoutfiller(right side)on the other hand, shows a poorly bonded adherend.The adhesivefilled out pores even500l m away from the bondline;however,the joint starved instead.Already Suchsland(1958) advised that there is no relationship between the penetration depth and the bonding quality as long as the adhesivefills out the topmost surface forming cell layer.Because calcium carbonate was used asfiller material,the element calcium can be easily used for detecting the substance with EDX.It turned out that thefiller material was homogeneously dispersed within the adhesive matrix(Fig.3,picture detail)and no separations could be detected.Fig.3ESEM micrograph of1C PUR adhesive with30%filler(left),withoutfiller(right)and EDX mapping of calcium(picture detail)ConclusionChalk turned out to be a suitablefiller material,which is easily addable to the adhesive,well miscible and cost efficient and it significantly improves the thermal stability of glued wood joints in the aimed temperature range.For future studies,it would be of particular interest tofind suitable alternativefiller materials and to determine the optimalfiller material content regarding costs and bonding properties. Acknowledgments The authors would like to thank Gabriele Peschke from the Fracture Mechanics of Concrete Group at the Institute for Building Materials(ETH Zurich)for her support at the ESEM.ReferencesBeaud F,Niemz P,Pizzi A(2006)Structure-property relationships in one-component polyurethane adhesives for wood:sensitivity to low moisture content.J Appl Polym Sci101(6):4181–4192 Dodiuk H,Belinski I,Dotan A,Kenig S(2006)Polyurethane adhesives containing functionalized nanoclays.J Adhes Sci Technol20(12):1345–1355EN302-1(2004)Adhesives for load-bearing timber structures—test methods—Part1:determination of bond strength in longitudinal tensile shear strengthKovacˇevic´V,Lucˇic´S,Hace D,Cerovecˇki Zˇ(1996)Tensile properties of calcium carbonate reinforced poly(vinyl acetate).J Adhes Sci Technol10(12):1273–1285Mansouri HR,Pizzi A(2007)Recycled micronized polyurethane powders as active extenders of UF and PF wood panel adhesives.Holz Roh Werkst65(4):293–299Mun˜oz Mila´n AB,Pe´rez-Limin˜ana A,Ara´n-Aı´s F,Torro´-Palau A,Orgile´s-Barcelo´AC(2005)Effect of the amount of calcium carbonate asfiller on the rheological and adhesion properties of a water-based polyurethane dispersion.Macromol Symp221:33–41Park SW,Kim BC,Lee DG(2009)Tensile strength of joints bonded with a nano-particle-reinforced adhesive.J Adhes Sci Technol23(19):95–113Richter K,Schierle M(2002)Behaviour of1K PUR adhesives under increased moisture and temperature conditions.Lignovisionen4:149–154Schro¨dter A,Niemz P(2006)Investigations on the failure behaviour of glue joints at high temperatures and relative humidity.Holztechnologie47(1):24–32Sepulcre-Guilabert J,Ferra´ndiz-Go´mez TP,Martı´n-Martı´nez JM(2001)Properties of polyurethane adhesives containing natural calcium carbonate plus fumed silica mixtures.J Adhes Sci Technol 15(2):187–203Suchsland O(1958)On the penetration of glue in wood gluing and the significance of the penetration depth for the strength of glue joints.Holz Roh Werkst16(3):101–108Zeppenfeld G,Grunwald D(2005)Klebstoffe in der Holz-und Mo¨belindustrie.DRW-Verlag, Leinfelden-Echterdingen。