timing plan master
船长英语阅读理解

船长英语阅读理解(光盘64篇)1、Failing to identify pre-shipment damage and neglecting to make appropriate notations on bills of lading will deprive the carrier of his rights,limitations and immunities under the contract of carriage and may prejudice Club cover.Assertions are sometimes made by cargo interests that rust on a particular shipment is normal and will not affect its market value.Such comments should be disregarded.In all cases where a steel cargo is found to be rusty,it is imperative that remarks are made on the bills of lading,irrespective of the apparent severity of the rust.The bills of lading should also be claused to reflect any physical pre-shipment damage to the steel and/or wrappers(bends,tears,crimps,dents,deformation,crushing).Selecting the most appropriate clauses to describe pre-shipment damage is not always easy,and the attending surveyor should be consulted for advice.Where possible,the clausing should list the identification marks of the damaged GOODs,failing which the number of coils or packages should be quantified.Percentage estimates regarding the number of damaged pieces should not be given.If it is not possible to identify the damaged GOODs specifically,the words“some”or“several”may be acceptable.Any differences found between the ship and shore tally or ship and bill of lading figures must be noted on the bill of lading in the usual manner.1)The clausing on B/L is to reflect and make notation of ________ the cargoes and/or their wrappers.A.all damages incurred during the carriage by sea toB.all possible damages to and/or losses ofC.physical pre-shipment damages toD.pre-shipment damages to2) The pre-shipment rusts for which there are assertions made by cargo interests that they are normal and would not affect the cargo's market value shall ________.A.be claused on the Bill of LadingB.not be claused on the Bill of LadingC.be disregardedD.not be disregarded3) The proper topic of this paragraph is ________.A.The Principles for Clausing on Bills of LadingB.Losses of and Damages to Steel CargoesC.Legal Actions to Be Taken When Losses of and Damages to Cargoes Incurred D.The Functions of Clauses Made on Bills of Lading4) This paragraph is most likely compiled to protect the interests of ________.A.the carriersB.the shippersC.the merchantsD.the cargo owners2、MV Magellan was inbound from Rotterdam to berth 207at Southampton Container Terminal.At 0530the pilot boarded the ship at the Nab Tower pilot station.The pilot's and the master's passage plans were exchanged and the ship's pilot card was given to the pilot.The passage continued along the East Solent,during which time there were various VHF radio conversations between vessels and Southampton VTS,about restricted visibility.The VTS officer gave the pilot a countdown from 5 to 2 cables to the Gurnard buoy.This was given so that the pilot could judge the timing of the wheel-over manoeuvre for the 141° turn into the narrow Thorn Channel.The wheel-over occurred at about 0652 and the ship began to turn.At this time,the W Bramble and NE Gurnard buoys,which are at the entrance to Thorn Channel,could not be seen because of restricted visibility.Various helm and engine movements were made during the turn.However,when W Bramble and NE Gurnard buoys appeared,the pilot realized that the ship was in the wrong position for the heading she was on.Despite further helm and engine orders,the vessel grounded soon after,at 0700.It was not until about 0710 that the escort harbor launch informed VTS of the grounding.With the assistance of two tugs,the ship was refloated near the time of high water,and she safely berthed at 1232.1)MV Magellan applied wheel at ________ to turn into the narrow Thorn Channel.A.0530B.0652C.0700D.07102)The important navigational mark or marks at the entrance to the Thorn Channel is (are)________.A.Southampton Container TerminalB.the East SolentC.the Nab TowerD.the W Bramble and NE Gurnard buoys3)The suggestion of a countdown from 5to 2cables to the Gurnard buoy is ________.A.for the pilot to judge easily when the wheel should be used to make the turn into the narrow Thorn ChannelB.to remind the pilot that the depth around there is not sufficient for MV Magellan C.to inform the pilot that the visibility around the buoy is reduced furtherD.to request the pilot that further consideration should be given to the wheel-over manoeuvre for the 141° turn4)It can be concluded that the cause of the grounding was that ________.A.the Bramble and NE Gurnard buoys were disappearedB.the VHF radio conversations between vessels and Southampton VTS,about restricted visibility,were insufficient and improperC.Thorn Channel was too narrowD.there was an error of judgment by the pilot during the execution of the turn into Thorn Channel3、The endorsement of a nonnegotiable bill does not make the bill negotiable or give the transferee any additional right.A person to whom a nonnegotiable bill has been transferred by delivery and agreement to transfer title to the bill or to the GOODs which it represents acquires the title to the GOODs as against the transferor.The transferee may also notify the carrier of the transfer to him,and the carrier is then obligated directly to the transferee for any obligations the carrier owed to the transferor immediately before the notification.More specifically,the carrier is liable to the owner of GOODs transported under a nonnegotiable bill,subject to the right of stoppage in transit.Besides having to be the owner of the GOODs covered by the nonnegotiable bill,the claimant in such a case must have actually relied in GOOD faith on statements made by the carrier on the bill.The carrier is liable for having stated on the bill that he received GOODs when in fact he had not,and for having delivered the GOODs in a quantity,kind,weight or condition other than as stated on the bill.In general,the carrier must deliver the GOODs on demand of the consignee named in a nonnegotiable bill of lading.However,on the endorsement of a nonnegotiable bill,the GOODs may be delivered to a party entitled to their possession.The carrier is liable toward the person having title to,or a right to possession of,the GOODs for delivering them to a party not entitled to their possession.1)The endorsement of a nonnegotiable bill transfers ________.A.the title to the GOODs from the transferor to the transfereeB.the title to the GOODs from the transferee to the transferorC.in no way the title to the GOODs from the transferor to the transfereeD.the GOODs to the party entitled to their possession2)The transferee of a nonnegotiable bill acquires the title to the GOODs ________.A.by taking delivery of the bill and entering into an agreement to transfer title to the bill or to the GOODsB.by having the carrier actually delivered the GOODs to himC.by having the transferor endorsed the nonnegotiable billD.in no way3)In the event of a nonnegotiable bill has been actually transferred,if the carrier stated on the bill that he received GOODs when in fact he had not,________ is liable.A.heB.the transferorC.the transfereeD.the person having title to,or a right to possession of,the GOODs4)If the GOODs were thus transferred,and the carrier delivered the GOODs in a quantity,kind,weight or condition other than as stated on the bill,________.A.he is liableB.he is not liableC.it can not be determined whether he is liable or notD.whether he is liable or not is to be determined by the law of the ship‟s flag4、1620070900 LTMASTER SIDUSDEAR CAPTAINQUOTESAILING INSTRUCTIONS FOR YR VESSELTHIS IS R.S.PLATOU,OSLOSUBJ:FIXTURE OF YR VSLYOU ARE KINDLY REQUESTED TO PROCEED TO SAN NICOLAS(POSITION S 15°14′,W O 75°14′)TO LOAD BLAST FURNACE PELLETS FOR KAOHSIUNG,TAIWAN.(POSITION N 22°37′,E 120°15′).STOWAGE FACTOR 0.461CUBIC METERS PER METRIC TONNE ACCORDING TO TIME CHARTERER SHOUGANG HIERRO PERU S.A.LAYCAN:16 OCT/26 OCT QUANTITY:FULL CARGOTERMS:ACCORDING TO TIME CHARTER NYPE:FIOAGENT LOAD PORT:CONSORCIO EMPRESARIAL AGNA V S.A.TELEPHONE(0051)330-6605 FAX:(0051)330-2664AGENT DISCH PORT:TO BE COMMUNICATED TO U SHORTLY.REPORTS:ETA MUST BE SENT“MINIHIERRO”LIMA AND TO SAN NICOLAS 5DAYS IN ADV ANCE,AND CONFIRMED 48HRS AND 24HRS BEFORE ARRIV ALSPECIAL ATTENTION:WHEN CONTACT MADE WITH THE RADIO STATION OAS AT SAN JUAN,A PRE-STOWAGE HATCH LIST WITH SEQUENCE OF LOADING TO BE SENT TO LOAD PORT NOT LESS THAN 48HRS IN ADV ANCE.THE RADIO STATION WILL ALSO COMMUNICATE BERTHING INSTRUCTIONS.ON ARRIV AL SUPPLIER REQUIRES YOUR PRE-STOWAGE PLAN PRIOR TO LOADING,TOTAL CARGO,ESTIMATED HATCH TONNAGE,LOADING SEQUENCE,FUEL WATER AND STORES ON BOARD,DRAUGHT,STABILITY AND TRIM ON FINISHING LOADING.DEBALLASTING:ALLOWED AT BERTH PROVIDED CLEAN SUBJECT TO APPROV AL BY PORT AUTHORITY.SURVEYS:HOLDS TO BE INSPECTED BEFORE LOADING.CARGO OFFICER TO ACCOMPANY INSPECTOR.ON AND OFF HIRE SURVEYS REQUIRED ACCORDING TO CHARTER PARTY.FURTHER INSTRUCTIONS TO FOLLOW SHORTL Y.BEST REGARDS ROTASJ/KNMEND QUOTE1)The nominated agent for the Vessel at the loading port is ________.A.MINIHIERRO B.CONSORCIO EMPRESARIAL AGNA V S.A.C.SAN NICOLAS D.SAN JUAN2)The BERTHING INSTRUCTIONS will be obtained from ________.A.the agent at the loading portB.discharge port authorityC.further instructions to follow shortlyD.the radio station OAS at San Juan3)On and off hire surveys should be carried out ________.A.in accordance with the charter-partyB.as per further instructionsC.by the cargo officer on boardD.48 hours prior to arrival at the loading port4)According to this fixture,________.A.the vessel is not liable for the expenses of loading and dischargingB.the cargo will be discharged at San NicolasC.the freight of this voyage is likely to be charged as per measurement tonnage of the cargoD.the canceling date of this fixture is 16 Oct.5、 A Passenger Ship Safety Certificate shall be issued for a period not exceeding 12 months.A Cargo Ship Safety Construction Certificate,Cargo Ship Safety Equipment Certificate and Cargo Ship Safety Radio Certificate shall be issued for a period specified by the Administration which shall not exceed five years.An Exemption Certificate shall not be valid for longer than the period of the certificate to which it refers.(i)When the renewal survey is completed within three months before the expiry date of the existing certificate,the new certificate shall be valid from the date of completion of the renewal survey to:(1)for a passenger ship,a date not exceeding 12 months from the date of expiry of the existing certificate;(2)for a cargo ship,a date not exceeding five years from the date of expiry of the existing certificate;(ii)When the renewal survey is completed after the expiry date of the existing certificate,the new certificate shall be valid from the date of completion of the renewal survey to:(1)for a passenger ship,a date not exceeding 12 months from the date of expiry of the existing certificate;(2)for a cargo ship,a date not exceeding five years from the date of expiry of the existing certificate;(iii)when the renewal survey is completed more than three months before the expiry date of the existing certificate,the new certificate shall be valid from the date of completion of the renewal survey to:(1)for a passenger ship,a date not exceeding 12 months from the date of completion of the renewal survey;(2)for a cargo ship,a date not exceeding five years from the date of completion of the renewal survey.1)The valid period of an Exemption Certificate for Cargo Ship Safety Equipment Certificate shall be ________.A.longer than five years B.shorter than five yearsC.longer than 12 months D.shorter than 12 months2)When the renewal survey is completed within one month before the expiry date of the existing Cargo Ship Safety Construction Certificate,the new certificate shall be valid ________.A.from the date of completion of the renewal survey to a date not exceeding 12 months from the date of expiry of the existing certificateB.from the date of completion of the renewal survey to a date not exceeding five years from the date of expiry of the existing certificateC.from the date of expiry of the existing certificate to a date not exceeding12 months from the dateD.from the date of expiry of the existing certificate to a date not exceeding five years from the date3)When the renewal survey is completed on a date which is 99 days before the expiry date of the existing Cargo Ship Safety Radio Certificate,the new certificate shall be valid ________.A.from the date of completion of the renewal survey to a date not exceeding 12 months from the date of expiry of the existing certificateB.from the date of completion of the renewal survey to a date not exceeding five years from the date of expiry of the existing certificateC.from the date of expiry of the existing certificate to a date not exceeding12 months from the dateD.from the date of completion of the renewal survey to a date not exceeding five years from that date4)It can be concluded that the actual period of validity of a new Passenger Ship Safety Certificate is less than 12months if the renewal survey is completed ________.A.4 months before its expiry dateB.3 months before its expiry dateC.2 months before its expiry dateD.after its expiry date6、An aircraft lift on board RFA Argus was loaded beyond its safe working load of 18.4 tonnes.There were no injuries to any personnel,or material damage to the ship or its equipment.During a planned stay in port,500compressed CO2cylinders were required to be landed.These were normally stowed on a lower deck and needed to be transferred to the weather deck before being taken ashore.Before the vessel's arrival in port,the planned operation was discussed between various officers and senior ratings,one of whom was to supervise final discharge of the cylinders from the ship.Once in port,a senior rating gave instructions to three juniors to transfer a number of cylinders to the weather deck.He then left them alone to load the cylinders onto the platform of an aircraft lift.The cylinders weighed 19.95 tonnes,which was greater than they had been instructed to load.In addition to this excess weight they added a fork lift truck weighing 5.5 tonnes.The lift was then raised.When it reached the weather deck,the lift was unable to stow at the correct level.When investigated it was discovered that the load of both CO2 bottles and the fork lift truck was greater than its safe working load(SWL)and this had prevented the locking cleats at the flight deck(weather deck)engaging.The lift was taken out of service for testing and inspection.1)The safe working load of the aircraft lift is ________ tonnes.A.18.4B.19.95C.5.5D.5002)The aircraft lift was overloaded by a weight which is ________ more than its SWL A.1.55B.3.95C.5.5D.7.053)It was the ________ that had prevented the locking cleats at the flight deck (weather deck)engaging.A.fork liftbottlesB.CO2C.overloaded weightD.the three juniors4)It is implied in the passage that ________.A.the lift should be raised slowly to avoid the accidentB.the aircraft lift on board RFA Argus should be driven by super powerC.the senior rating should give instructions in more detail to the three juniors to transfer a number of cylinders to the weather deckD.if the unloading operation was supervised by an officer who has sufficient experience of the loads,lifting equipment and the overall operation,the accident would had been avoided7、Coastal conditionsThe area described in the volume presents the mariner with a generally adverse combination of navigational factors which are outline below.Local Topography.The Dover Strait is shallow and only is 18miles wide at its narrowest point.Passage through the strait is further constricted by a series of narrow banks,running NE-SW.The seabed is also littered with wrecks.Natural Conditions.There are strong tidal streams in the strait.Sea level may differ from that predicted and in particular may be lower than expected due to negative tidal surges.The area is also subject to gales and poor visibility.Risk of Collision.There is a high risk of collision caused by the density of vessel traffic on passage through the strait,including deep-draught vessels,and crossing traffic,including ferries and high speed craft.Mine danger areaThere are two areas off the N coast of France,which remain dangerous because of mines lied in the war of 1939-1945.Due to the lapse of time the risk to surface navigation is now considered to be no more dangerous than that the ordinary risks of navigation but a very real risk still exists with regard to anchoring,fishing or any form submarine or seabed activity.1)The crossing traffic in the Dover Strait is probably running ________.A.NE-SWB.SE-NWC.N-SD.E-W2)According to the passage,the risk of collision in the Dover Strait is caused by ________.A.gales and poor visibilityB.a series of narrow banksC.the density of vessel traffic on passage through the strait and crossing trafficD.a generally adverse combination of navigational factors3)It is inferred that ________.A.although the tidal streams in Dover Strait is strong,there were few ships sunk in it B.most of the wrecks in Dover Strait were deep-draught vessels,ferries and high speed craftC.the wrecks are not dangers to surface navigationD.there were many ships sunk in Dover Strait4)It is implied in the passage that ________.A.mine is not a danger to surface navigation in Dover StraitB.the width of Dover Strait is not so narrowC.the natural conditions in Dover Strait are too serousD.collision with deep-draught vessels or ferries or high speed craft in Dover Strait is hardly avoidable8、The contract of carriage of GOODs by sea is usually concluded as between theshipper and the carrier,either directly or through their respective agents.Consequently,by virtue of the historic principle of privity of contract,only the shipper and the carrier have the right to take action against one another under the contract of carriage.The only clear exception to the rule was where the party having the right to sue assigned that right under a separate agreement to another party.On the other hand,when GOODs are sold(as they typically are)prior to shipment,the terms of sale generally resultin the risk in the GOODs passing from the seller(the shipper)to the buyer(the consignee or endorsee,in the case of a bill of lading,or the party entitled to take delivery under a waybill)when the GOODs cross the ship's rail in the port of loading.Therefore,although the law recognizes that the shipper alone has the right to sue the carrier in contract for subsequent cargo loss or damage occurring while the carrier had charge of the shipment,the shipper is not usually the party who actually suffers that loss.Frequently,also,depending on the terms of sale,the shipper will no longer be the owner of the GOODs at the time when the loss or damage occurs,and so will be unable to sue the carrier in tort.1)The contract of carriage of GOODs by sea is usually concluded as between ________.A.the seller and the buyerB.the shipper and the consignee or endorseeC.the carrier and the consignee or endorseeD.the shipper and the carrier2)When GOODs are sold prior to shipment the risk in the GOODs passes ________.A.from the shipper to the carrierB.from the seller to the buyerC.from the carrier to the shipperD.from the buyer to the seller3)It is concluded ________ that only the shipper and the carrier have the right to take action against one another under the contract of carriage.A.by maritime lawsB.by a mainstay of the common law in particularC.by virtue of the historic principle of privity of contractD.by shipping practice4)When GOODs are sold prior to shipment the shipper ________.A.is not usually the party who actually suffers the subsequent lossB.is usually the party who actually suffers the subsequent lossC.will still be the owner of the GOODs at the time when the loss or damage occurs D.will be responsible for the loss of or damage to the cargo he shipped9、The 4,426gt Swedish vessel Skagern sailed for her next port,Strood,with a draught of 5.95m.The master soon realized,however,that he would not make the tide for berthing if he proceeded to the Medway as planned,to pick up the pilot at the North East Spit.He therefore decided to change the passage plan by shortening the distance and embarking his pilot at the Sunk light vessel.The officer on watch,2/O,was told to make the necessary adjustments and lay off the new courses.The 2/O made the original plan based on waypoints calculated and entered by another officer.These had been marked on the various charts and had already been entered into the GPS navigator.When he amended the passage plan he used the GPS to calculate a new course from a waypoint off Lowestoft direct to the Sunk pilot station.In doing so,he didn't realize he had missed out a pre-programmed waypoint in the GPS for a position to the east of the East Shipwash buoy.He didn't notice that his course line intersected the 5m depth contour to the west of the East Shipwash buoy.The master did not check the amended passage plan and Skagern continued with her passage.2/O came on watch again four hours before the vessel was due to arrive at the pilot station.One hour before arrival at the Sunk 2/O prepared to embark the pilot.He saw the North Shipwash buoy and passed about three cables to the east of it.Shortly afterwards he saw two more buoys ahead of him,the East Shipwash on his port bow and the North-West Shipwash on his starboard.It did not occur to him that anything might be wrong.Shortly afterwards,Skagern ran aground at a full speed of 14 knots.He had found the Shipwash Bank.Although two tugs were dispatched from Harwich to standby,the master was able to de-ballast his vessel and refloat her successfully with the aid of the main engine.There was no pollution and there appeared to be no damage.1)To embark the pilot earlier Skagern ________.A.speeded upB.shortened the distance by adjusting the planned passageC.made the tideD.engaged trade every two weeks2)The grounding was caused by the reason of ________.A.the second officer missed a waypoint when steaming to the pilot stationB.the depth around the pilot station is 5.95m which is not sufficient to allow the vessel to keep always afloatC.the GPS had something wrong when calculating the courseD.the vessel did not make the tide due to her late arrival3)The vessel was refloated ________.A.with the aid of reverting her main engine and pressing up slack ballast tanks B.herself by pumping out some of her ballast and the aid of her main engine C.with the aid of her main engine and the two tugs from HarwichD.with the aid of tide and tugs4)The lessen of this accident is that ________.A.without proper planning of the ballasting and de-ballasting programme the vessel is likely to be involved in such accident as groundingB.a vessel should be well prepared for grounding when proceeding toward pilot stationC.when grounded,a vessel should try to contact the nearest coast station to apply for the aid of tugsD.in this age of the GPS and push-button navigation,it is all too easy to be lulled into a false sense of security and assume the position indicated is correct10、The Company should establish a safety and environmental protection policy which describes how the objectives will be achieved.The Company should ensure that the policy is implemented and maintained at all levels of the organization both ship based as well as shore based.If the entity who is responsible for the operation of the ship is other than the owner,the owner must report the full name and details of such entity to the Administration.The Company should define and document the responsibility,authority and interrelation of all personnel who manage,perform and verify work relating to and affecting safety and pollution prevention.The Company is responsible for ensuring that adequate resources and shore based support are provided to enable the designated person or persons to carry out their functions.To ensure the safe operation of each ship and to provide a link between the company and those on board,every company,as appropriate,should designate a person or persons ashore having direct access to the highest level of management.The responsibility and authority of the designated person or persons should include monitoring the safety and pollution prevention aspects of the operation of each ship and to ensure that adequate resources and shore based support are applied,as required.The Company should clearly define and document the master's responsibility with regard to:implementing the safety and environmental protection policy of the Company;motivating the crew in the observation of that policy;issuing appropriate orders and instructions in a clear and simple manner;verifying that specified requirements are observed;and reviewing the SMS and reporting its deficiencies to the shore based management.The Company should ensure that the SMS operating on board the ship contains a clear statement emphasizing the Master's authority.The Company should establish in the SMS that the master has the overriding authority and the responsibility to make decisions with respect to safety and pollution prevention and to request the Company's assistance as may be necessary.1)The Company should ensure that the policy is implemented and maintained at all levels of the organization both ship based as well as shore based.The ORGANIZATION refers to ________.A.IMOB.SMSC.the AdministrationD.the construction of the Company2)The overriding authority and the responsibility to make decisions with respect to safety and pollution prevention is on the part of ________.A.the highest level of management of the CompanyB.DPC.the master of the shipD.the owner or the entity who is responsible for the operation of the ship3)________ are/is not the master's responsibility defined and documented by the Company.A.reviewing the SMS and reporting its deficiencies to the shore based management B.motivating the crew in the observation of the safety and environmental protection policy of the CompanyC.issuing appropriate orders and instructions in a clear and simple manner and verifying that specified requirements are observedD.providing a link between the company and those on board4)This passage is probably extracted from ________.A.IMDG Code B.ISM CodeC.SOLAS D.Marpol11、The tug Vegesack was towing a barge engaged in“stone-fishing”in the vicinity of the Beach End buoy in Harwich Channel.Tug and tow were part of a dredging programme.During the dredging contract,the practice was for the dredging craft,Vegesack,to nominate the passing side for vessels.The barge was difficult to control in tidal and traffic conditions,and the master needed to exercise considerable skill and anticipation,as well as having to liaise closely with VTS and passing vessels.The German master had been issued with a pilotage exemption certificate and had been operating in the channel for nearly two months before the incident.The ferry Dana Anglia was outbound from Harwich in daylight and GOOD visibility.When she was close to North Shelf buoy,VTS called Vegesack and agreed that Vegesack,who was in the middle of the channel,would move to the north side.This would enable both Dana Anglia and Bencomo,an inbound vessel currently passing No5 buoy,to pass to the south.VTS gave this passing information to the two vessels.While passing Platters buoy,Bencomo called Vegesack,requesting her to move to the north.Vegesack said she was going to move to the Harwich(or south)side,and instructed Bencomo to pass to the north.VTS then intervened and confirmed with Vegesack that she wanted both vessels to pass to the north.At this time,Dana Anglia was approaching North West Beach buoy and could see Vegesack heading south,in。
timing的学习计划是啥意思
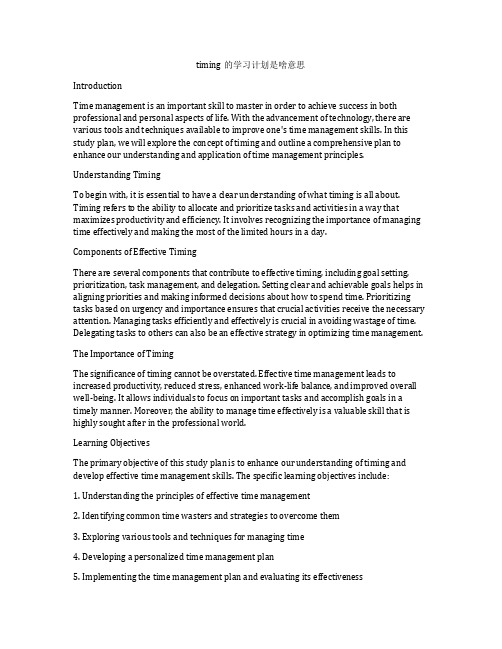
timing的学习计划是啥意思IntroductionTime management is an important skill to master in order to achieve success in both professional and personal aspects of life. With the advancement of technology, there are various tools and techniques available to improve one's time management skills. In this study plan, we will explore the concept of timing and outline a comprehensive plan to enhance our understanding and application of time management principles.Understanding TimingTo begin with, it is essential to have a clear understanding of what timing is all about. Timing refers to the ability to allocate and prioritize tasks and activities in a way that maximizes productivity and efficiency. It involves recognizing the importance of managing time effectively and making the most of the limited hours in a day.Components of Effective TimingThere are several components that contribute to effective timing, including goal setting, prioritization, task management, and delegation. Setting clear and achievable goals helps in aligning priorities and making informed decisions about how to spend time. Prioritizing tasks based on urgency and importance ensures that crucial activities receive the necessary attention. Managing tasks efficiently and effectively is crucial in avoiding wastage of time. Delegating tasks to others can also be an effective strategy in optimizing time management. The Importance of TimingThe significance of timing cannot be overstated. Effective time management leads to increased productivity, reduced stress, enhanced work-life balance, and improved overall well-being. It allows individuals to focus on important tasks and accomplish goals in a timely manner. Moreover, the ability to manage time effectively is a valuable skill that is highly sought after in the professional world.Learning ObjectivesThe primary objective of this study plan is to enhance our understanding of timing and develop effective time management skills. The specific learning objectives include:1. Understanding the principles of effective time management2. Identifying common time wasters and strategies to overcome them3. Exploring various tools and techniques for managing time4. Developing a personalized time management plan5. Implementing the time management plan and evaluating its effectivenessStudy PlanWeek 1-2: Understanding Time Management PrinciplesDuring the first two weeks, we will focus on understanding the principles of effective time management. This will involve reading relevant literature, attending webinars, and engaging in discussions to gain insights into the importance of time management and its impact on productivity.Week 3-4: Identifying Time Wasters and Strategies to Overcome ThemIn the following two weeks, we will explore common time wasters and develop strategies to overcome them. This will include identifying personal time wasters and brainstorming solutions to eliminate or minimize their impact on productivity.Week 5-6: Exploring Time Management Tools and TechniquesThe next phase of the study plan will involve researching and experimenting with various time management tools and techniques. This may include using digital calendars, to-do lists, and other apps to organize tasks and schedules.Week 7-8: Developing a Personalized Time Management PlanIn this phase, we will take into consideration the insights gained from the previous weeks and develop a personalized time management plan. This plan will be tailored to individual needs and preferences, taking into account specific goals and priorities.Week 9-10: Implementing and Evaluating the Time Management PlanThe final two weeks will be dedicated to implementing the personalized time management plan and evaluating its effectiveness. This will involve tracking progress, making adjustments as necessary, and reflecting on the overall impact of improved timing on productivity and well-being.ConclusionIn conclusion, effective timing is a crucial aspect of achieving success in both personal and professional endeavors. This study plan aims to enhance our understanding of timing and develop practical time management skills. By exploring the principles of time management, identifying time wasters, exploring tools and techniques, and developing a personalized time management plan, we aim to optimize our use of time and improve overall productivity.。
权力的48条法则
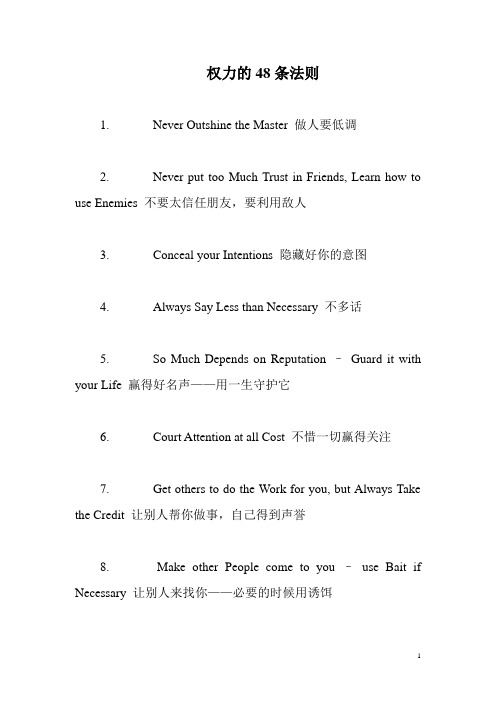
权力的48条法则1. Never Outshine the Master 做人要低调2. Never put too Much Trust in Friends, Learn how to use Enemies 不要太信任朋友,要利用敌人3. Conceal your Intentions 隐藏好你的意图4. Always Say Less than Necessary 不多话5. So Much Depends on Reputation –Guard it with your Life 赢得好名声——用一生守护它6. Court Attention at all Cost 不惜一切赢得关注7. Get others to do the Work for you, but Always Take the Credit 让别人帮你做事,自己得到声誉8. Make other People come to you –use Bait if Necessary 让别人来找你——必要的时候用诱饵9. Win through your Actions, Never through Argument 用行动而不是争吵来获胜10. Infection: Avoid the Unhappy and Unlucky会传染,得避开不快和不幸的人11. Learn to Keep People Dependent on You 学会让人依靠你12. Use Selective Honesty and Generosity to Disarm your Victim 用有选择的诚实和大方来缓和与你受害者的矛盾13. When Asking for Help, Appeal People’s Self-Interest, Never to their Mercy or Gratitude 寻求帮助时,迎合他人自己的兴趣而不是他们的仁慈和感激14. Pose as a Friend, Work as a Spy 以朋友的姿态像间谍一样地工作15. Crush your Enemy Totally 打击敌人不遗余力16. Use Absence to Increase Respect and Honor 利用缺席提升地位和名气17. Keep Others in Suspended Terror: Cultivate an Air of Unpredictability 让别人陷入不知名的恐惧中,让你周围的空气充满未知性18. Do Not Build Fortresses to Protect Yourself –Isolation is Dangerous 不要用围城保护自己——隔离是危险的19. Know Who You’re Dealing with –Do Not Offend the Wrong Person 知道你正在对付的人是谁——不要得罪错了人20. Do Not Commit to Anyone 不要向任何人承诺21. Play a Sucker to Catch a Sucker –Seem Dumber than your Mark 扮猪吃猪——巧妙掩饰你的智慧(自认为翻得好玩的一句)22. Use the Surrender Tactic: Transform Weakness into Power 使用投降策略:把弱点转化为优点23. Concentrate Your Forces 集中火力24. Play the Perfect Courtier 溜须拍马25. Re-Create Yourself 重塑自己26. Keep Your Hands Clean 保持双手干净(身家清白)27. Play on People’s Need to Believe to Create a Cult like Following 满足群众需求以培养一群信徒28. Enter Action with Boldness 大胆地行动29. Plan All the Way to the End 预先想好所有的方法30. Make your Accomplishments Seem Effortless 让你的成功看起来毫不费力31. Control the Options: Get Others to Play with the Cards you Deal 控制选择:让别人打出你想要的牌32. Play to People’s Fantasies 满足人们的幻想33. Discover Each Man’s Thumbscrew 找出每个人的死穴34. Be Royal in your Own Fashion: Act like a King to be treated like one 忠于自己的风格:你当自己是个人物,别人也当你是个人物35. Master the Art of Timing 把握时机36. Disdain Things you cannot have: Ignoring them is the best Revenge 轻视你得不到的:忽略他们是最好的报复37. Create Compelling Spectacles 做出引人注目的事迹38. Think as you like but Behave like others 想一套(你喜欢的)做一套(像别人一样的)39. Stir up Waters to Catch Fish 混水摸鱼40. Despise the Free Lunch 天下没有免费的午餐41. Avoid Stepping into a Great Man’s Shoes 不要模仿大人物42. Strike the Shepherd and the Sheep will Scatter 打败领头者,跟风者将会一哄而散43. Work on the Hearts and Minds of Others 用别人的想法工作44. Disarm and Infuriate with the Mirror Effect 善于利用(消除或者激化)镜像效应45. Preach the Need for Change, but Never Reform too much at Once 鼓吹变化的需要,但切不可一次改变太多46. Never appear too Perfect 永远不要表现太完美47. Do not go Past the Mark you Aimed for; In Victory, Learn when to Stop 不要超过既定目标,面对成功,知道什么时候停步48. Assume Formlessness 无招胜有招来源:《权力的48条法则》另外一个不完整的版本:第一条永远不要比你的上司更出色。
评审阶段及内容清单模板

3.8
防错清单(初版) Preliminary Error Proofing List
产品DV & PV试验大纲 3.9 DV & PV Test Plan
零部件OTS封样件 3.10 Component OTS release Sample
3.11
零部件OTS认可报告 Component OTS Release Report
模具验收计划 Mould approval plan
分供方清单 3.1 Subsupplier List
物料清单(初版) 3.2 Preliminary MBOM
3.3
过程流程图(更新) Flow Chart (Update)
3.4
PFMEA及检查清单(更新) PFMEA and Checklist (Update)
初始分供方清单 2.9 Initial Subsupplier List
质量管理计划 2.10 QPN
2.11
项目成本分析与管理 Project Cost Analysis And Management
项目风险分析与管理 2.12 Project risk Analysis And Management
模具验收报告 3.15 Mold Acceptance Report
3.16 设备/产线(工装)/测试设备量检具验收单 Equipment/Production Line(Tooling) /Gage Pre-acceptance Report
3.17
尺寸测量计划 Part test Plan
3.18
项目进度计划 Project Timing Plan
表单编号
责任人/部门
销售工程师
Engineering all英文职位描述-工程师

Engineering DeptPRODUCT LINE MANAGER:Responsibility:A - Lead the Product line team:–Manage the team to improve the team knowledge and reach technical targets–Define and make apply priorities inside the team–Make the whole team apply APQP (plan review, project review, toll gates, etc…)–Generate weekly report with the teamB - Lead his own projects as a Project Engineer.–Lead the project inside TRELLEBORG group. Communicate frequently with other departments and TRELLEBORG Technical center; usemanaging tools for project: CPL data base, “to do “list, timing plan, etc…–Generate an overall timing plan for each part, including all requiredactivities (tooling, assembly process, supply parts, etc...) and ensures itsregular follow up from start of competition till hand over to production –Manage all planned activities by assuring the respect of technicalperformance, timing, costs, and quality level–Follow TQS during the project life; identify and put in place actions plan to restore expected margin–Prepare and execute tollgates sign-off–Participate in all technical meetings with customers–Manage productivity actions like continuous improvement plan (CIP3)–Comply with and participate to the entire request of the company for quality and environmental managementRequirement:–English speaking–Engineer–Management capabilities–Between 5 to 10 years of automotive project management background–Technical knowledge: rubber, mechanical. Knowledge about thermoplastic and steel would be appreciatedPRODUCT ENGINEERResponsibility:–Lead the project inside TRELLEBORG group. Communicate frequently with other departments and TRELLEBORG Technical center; use managing tools for project: CPL data base, “to do “list, timing plan, etc…– Generate an overall timing plan for each part, including all required activities (tooling, assembly process, supply parts, etc...) and ensures its regular follow up from start of competition till hand over to production– Manage all planned activities by assuring the respect of technical performance, timing, costs, and quality level–Follow TQS during the project life; identify and put in place actions plan to restore expected margin– Prepare and execute tollgates sign-off- Participate in all technical meetings with customers– Manage productivity actions like continuous improvement plan (CIP3)–Comply with and participate to the entire request of the company for quality and environmental managementRequirement:- English speaking- Engineer- Between 2 to 5 years of automotive project management background-Technical knowledge: rubber, mechanical. Knowledge about thermoplastic and steel would be appreciatedDESIGNER:Responsibility:1. Responsible for product design and injection mold design. Follow-up moldmanufacture process, mold trial and improvement.2. Participate to APQP activities for product design and mold optimization3. Participate to CIP3 activities, production support. Comply with the entire request ofcompany for quality and environmental management.4. Support project engineer to design testing fixture. Loading board and unloading board.5. Support production to improve rubber mold issues.Requirement:- English reading- 3D software experience (UG, Catia, Ideas)-Technical knowledge: mechanic and mold designPROCESS MANAGERRequirementLead and manage process and prototype team (~ 8 persons)1 - Responsible for the definition, installation and start up of process :timing plan,cell design and lay out according production capacity need,PFMEA,machines specification,process parameters,process documents,Run at Rate,Machine cost,quality, security, and environment,Main processes are :Chemical and surface treatmentBounding depositMolding assembly2- Make the whole project team apply APQP flow chart3 – participate to continuous improvement for productivity and quality4 - support production team for process technical aspects5 - responsible for preparing samples of new products6 - comply with and participate to the entire request of the company for quality and environmental management7 - responsible for Engineering team CIP38 - responsible for Plant layoutRequirement:English speakingEngineerManagement capabilitiesFamiliar with automotive proceduresBetween 5 to 10 years of mechanical and or process backgroundTechnical knowledge: rubber, mechanical and chemical treatment for metal parts, assembly processMaintenance knowledge would be appreciatedPROCESS ENGINEERResponsibility:1, Conduct project assignments to develop new tooling, modifications and alterations of existing tooling, jigs, fixtures, mechanisms and attachments used in the manufacture of Company products.2, Develop new process parameters and continue to improve existing process.3, Conduct manufacturing/Assembly methods studies and prepare for process document.4,Cell design and layout according production capacity. As assigned.5,Others required by APQP procedure such as FMEA , as assigned.6,Machines specification , as assigned.7,Training and instruct prototype employees for new projects sample preparation as assigned.8,Support production team for process technical aspect and train operators9,Assist manager on CIP3 project, as assigned.10, Others assigned by manager.Requirement:English speakingFamiliar with automotive proceduresTechnical knowledge: rubber, mechanical and chemical treatment for metal parts, assembly processMaintenance knowledge would be appreciatedResponsibility:Lead and Manage the Material team:1 - Manage the team to improve the team knowledge. Define and make apply priorities inside the team2 – responsible for WUXI recipe:-- For local products, define and valid recipe including mixing process parameters and material properties-- For localized parts, copy recipe coming from other TC and valid process parameters and material properties-- For exported parts, define with other TC recipe during development phase , valid process parameters and material properties during industrialization phase.3 – responsible for coating:- Internal phosphate line- Painting- subcontracted coating (ex: metal jacket, zinc nickel,…)4 – Responsible for mixing process parameters. Define and validate optimized process parameters.5 - responsible for bonding system:Define chemical system and valid process parameters for bounding system6 –Support Quality department and Production team for quality issues due to recipe, mixing, coating and bonding system7 – Participate to continuous improvement for productivity8 – responsible for preparing compound for new products9 – Material correspondent with Europe and US for Material topics10 – Support environmental managementRequirement:- English speaking- Engineer- Management capabilities- Good knowledge of rubber, mixing, coating and bounding system- Between 5 to 10 years of rubber background as Material EngineerResponsibility:1 – responsible for recipe:-- For local products, define and valid recipe including mixing process parameters and material properties-- For localized parts, copy recipe coming from other TC and valid process parameters and material properties-- For exported parts, define with other TC recipe during phase 1 and 2, valid process parameters and material properties during phase 32 – Responsible for mixing process parameters. Define and validate optimized process parameters.3 - responsible for bonding system:Define chemical system and valid process parameters for bounding system4 –Support Quality department and Production team for quality issues due to recipe, mixing, coating and bonding system5 – Participate to continuous improvement for productivity6 – responsible for preparing compound for new productsRequirement:- English speaking- Engineer- knowledge of rubber, mixing, coating and bounding systemENGINEERING COORDINATION MANAGER (APQP MANAGER)工程协调经理Responsibility:Lead and Manage the APQP team:1 - Coach the team to improve the team knowledge. Define and make apply priorities inside the team2 – Make the whole project team apply APQP flow chart3 – Identify with Project Managers main risks for projects. Manage risk reduction plans4 – Check and support up-dating of main APQP documents: CPL, timing plan, action plans, toll gates, …5 – Support FMEA and PFMEA6 – APQP correspondent with Europe and US for parts developed with others TC as well as internal activities7 – responsible for prototype quality control plan and support prototype quality. Insure parts are order by customer or other TRELLEBORG companies8 –support Product Line Manager for weekly reporting9 – support Engineering Director for monthly reporting10 – Archive managementRequirement:- English speaking- Engineer- Management capabilities- Good knowledge of automotive procedures- Between 5 to 10 years of quality and/or project management backgroundEngineering Coordinator (APQP ENGINEER)Responsibility:1 – Make the whole project team apply APQP flow chart2 – Identify with Project Managers main risks for projects. Manage risk reduction plans3 – Check and support up-dating of main APQP documents: CPL, timing plan, action plans, toll gates, …4 – Support FMEA and PFMEA5 – For parts developed with TC, correspond with Europe and US6 – responsible for prototype quality control plan and support prototype quality. Insure parts are order by customer or other TRELLEBORG companies8 –support Product Line Manager for weekly reporting9 – Archive management and distributeRequirement:- English speaking- Engineer- Good knowledge of automotive procedures- Between 2 to 5 years of quality and/or project management background.LAB SUPERVISORRESPONSIBILITY:1. Manage the testing team to improve measures2. Help the testing team to improve measures3. Check frequently the accuracy of testing machines. Participate to the maintenanceand calibration of the testing machines.4. Check testing jigs design5. Check and accept all the new testing equipment including on line testing equipments6. Manage the testing orders7. Perform lab management according to standard lab procedure8. Support production parts daily checkingREQUIREMENT:EngineerManagement skillWell organized and sensitive to accuracyMechanical backgroundExperience in laboratoryLABORATORY TECHNICIAN:RESPONSIBILITY:1 –Measure and test metal, rubber and finished products (static, dynamic, creeping, fatigue, …)2 –Generate data’s repor t3 – Generate measurement work instructions4 – Do the Commissioning for testing jigs5 – Helps the testing team to improve measures, procedures end organization6 –Participate to the maintenance and calibration of the testing machines. Check frequently the accuracy of testing machines.REQUIREMENT:- College or junior university- 2 to 5 years of testing background- English speakingLABORATORY TECHNICIAN: 3D operatorRESPONSIBILITY:1 – 3D measurements for metal, rubber and finished products2 –Generate data’s report3 – Responsible for the maintenance and calibration of the 3D machine4 – Helps the testing team to measure and characterize all parts (static, dynamic, creeping, fatigue …)REQUIREMENT:- College or junior university- 2 to 5 years of 3D measurement background- English speakingCOST ESTIMATERESPONSIBILITY:1. Define new product process2. Study Molding Cell and production capacity3. Quote product cost thanks to Trelleborg Quotation Sheet4. For new production, analyze real cost, update TQS and define action plan forproductivity5. Quote mixing compound with purchasing department6. Analyze cost impact for Engineering change and VA/VEREQUIREMENT:Good experience for compound processSensitive to cost calculationENGINEERING DIRECTORRESPONSIBILITY:1 – Organize Engineering Department to develop new programs2 – Provide equipments to the Engineering team3 – Participate to strategic decision for new programs4 – Support purchasing, production and quality departments for technical aspects5 –Make proposal and participate to the decision for new investments for the plant according to new programs and production capacity6 – responsible for safety aspect for Engineering team7 – Responsible for cost aspects for new programs: TQS, investments, cycle time REQUIREMENT:English speakingManagement experience and skillMinimum 5 to 10 years experience in project managementGood knowledge of rubber and automotiveInternational experience is needed to work with other Technical Centers.。
timing改变学习计划

timing改变学习计划IntroductionIn the fast-paced and ever-evolving world of education, it is important for students to be adaptable and flexible in their study plans. One aspect that can greatly impact a student's ability to learn and succeed is timing. Whether it be the timing of when to study, how long to study for, or when to take breaks, timing plays a crucial role in shaping a student's study plan.In this article, we will explore the various ways in which timing can impact a student's study plan and discuss strategies for optimizing timing to enhance learning and academic success. The impact of timing on study plansTiming can have a profound impact on a student's ability to learn and retain information. Studies have shown that the timing of when students study can affect their ability to recall information. For example, research has found that studying before bed can improve memory retention, as the brain consolidates and stores information during sleep. Additionally, the timing of study sessions can also impact a student's focus and concentration. For instance, some students may find it more beneficial to study in shorter, focused bursts, while others may prefer longer study sessions with regular breaks. Understanding and harnessing the power of timing can help students maximize their learning potential and improve their study habits.Furthermore, timing also plays a crucial role in scheduling and planning for exams and assessments. Students must carefully plan and allocate their study time to ensure that they cover all necessary material and have enough time to review and revise before exams. Effective time management and strategic timing are essential components of a successful study plan.Strategies for optimizing timing in study plansNow that we understand the importance of timing in study plans, let's explore some strategies for optimizing timing to enhance learning and academic success.1. Identify your peak learning timesEvery student has periods during the day when they are most alert and focused. It is important to identify these peak learning times and schedule study sessions during these periods. Some students may find that they are more productive in the morning, while others may prefer to study in the evening. By aligning study sessions with one's peak learning times, students can maximize their ability to absorb and retain information.2. Take regular breaksIt is important for students to take regular breaks during study sessions to rest and recharge their minds. Studies have shown that taking short breaks during study sessions can improve focus and productivity. The Pomodoro Technique, for example, recommends studying for 25 minutes followed by a 5-minute break. By incorporating regular breaks into their study plan, students can maintain their concentration and prevent burnout.3. Create a study scheduleEffective time management is essential for successful study plans. Students should create a study schedule that outlines when and what subjects or topics they will study each day. This can help students stay organized, prioritize their study time, and ensure that they cover all necessary material before exams.4. Use spaced repetitionSpaced repetition is a learning technique that involves reviewing information at increasing intervals over time. This method has been found to improve long-term retention and recall of information. By incorporating spaced repetition into their study plan, students can reinforce their learning and better retain information for exams and assessments.5. Utilize technologyTechnology can be a valuable tool for optimizing timing in study plans. There are numerous apps and tools available that can help students track and manage their study time, set reminders for study sessions, and create digital flashcards for spaced repetition. By leveraging technology, students can streamline their study routines and make the most of their study time.6. Adapt to changes in routineFlexibility is key when it comes to timing in study plans. Students should be prepared to adapt their study routines to accommodate changes in their schedules or unexpected events. This may involve adjusting study times, reorganizing study sessions, or finding alternative study environments. By remaining adaptable, students can ensure that timing changes do not disrupt their study plans.ConclusionIn conclusion, timing plays a critical role in shaping a student's study plan. By understanding the impact of timing on learning and implementing strategies to optimize timing, students can enhance their study habits and improve their academic performance. It is important for students to identify their peak learning times, take regular breaks, create a study schedule, utilize spaced repetition, leverage technology, and remain flexible in their study routines in order to make the most of their study time.Ultimately, by effectively managing timing in their study plans, students can maximize their learning potential and achieve academic success.。
整套APQP Timing Plan Sheet
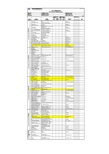
美特尔金属制品股份有限公司QP_F074_00项目Program:进度 Progress in %计划开始日期plan start date实际开始日期Actual Start Date计划完成日期plan finish date实际完成日期Actual finishDate204060801001.1客户要求确认Customer Needs Confirm 图纸、技术文件、特殊要求、项目信息等Drawing,Technicial doc,specialrequirement, program information ect. 销售负责人Sales Responsible 1.2项目启动会议Program kick off meeting 会议纪要Meeting Minutes销售负责人Sales Responsible 1.3设定开发目标Setup develop goal质量目标、成本目标、产能要求、OTS 目标和MR目标Quality Goal,Cost Goal, Capability Requirements, OTS Goal& MR Goal 销售负责人Sales Responsible 1.4建立CFT小组和APQP活动计划Setup CFT Team & APQP activity PlanCFT小组名单,APQP计划表CFT Team member,APQP Plan Sheet 项目经理Program Manager 1.5开发可行性评估Develop Feasibility Assessment 新产品开发可行性评估报告New Products develop feasibility assessment reportCFT1.6 可行性总结Feasibility Summary小组可行性承诺Team Feasibility Commitment CFT1.7 产品特殊特性辨识special characteristics identify 特殊特性清单special characteristics list 产品工程Product Engineering 1.8建立初始BOM Setup Originial BOMBOM表BOM产品工程Product Engineering 1.9 初步设定制造工艺流程Create manufactoring process flow 工艺流程图Process Flow Chart 产品工程Product Engineering 1.10 明确分供方Ensure sub-supplier分供方清单Sub-supplier list采购,资材Purchasing,Material 1.11 建立分供方APQP活动计划Create APQP计划表APQP Plan Sheet 质量Quality 1.12 产品保证计划Product warranty plan产品保证计划Product warranty plan 产品工程Product Engineering 1.13 阶段评审Phase Review阶段评审表Phase Review Record项目经理Program Manager2.1 设计FMEADesign FMEAN/A N/A 2.2 制造和装配设计Design for manufacturing &assembly N/A N/A 2.3 设计验证Design verificationN/A N/A 2.4 设计审查Design reviewN/A N/A2.5设定新制工装、夹具、治具清单Create new process method,fixture,tooling list 新增设备、仪器、工装、模具清单New equipment,instrument,fixture, tooling list模具工程,产品工程,质量Tooling Engineering,Product Engineering&Quality2.6制定工装、夹具、治具开发计划Work out fixture,Jia,Tooling Plan 甘特图Gantt chart模具工程,产品工程、质量2.7样件生产材料购买计划及实施Sample material purchasing Plan&Perform采购申请单(PR)采购,资材2.8制定样件生产的工艺流程Sample production process flow 工艺流程图Process Flow Chart 产品工程Product Engineering 2.9样件生产工艺流程评审Sample Process Fow Review 工艺流程评审表Process Flow Review Form CFT 2.10制定样件生产控制计划Sample production control Plan 控制计划表Control Plan Form 质量 Quality 2.11 样件生产控制计划评审Control Plan Review控制计划评审表Control Plan Review FormCFT 2.12 样件生产计划制定与实施FA Production Plan&Perform 试模/试生产申请单Trail run request CFT2.13样件提交FA sample Submission 客户反馈意见Customer feedback &suggestion 销售负责人 Sales 2.14样件生产总结FA Trail Run Summary 试模/试生产报告,FA报告Trail Run Report,FA Report CFT 2.15 可行性总结Feasibility Summary 小组可行性承诺Team Feasibility Commitment CFT2.16 阶段评审Phase Review 阶段评审表Phase Review Record 项目经理 Program Manager3.1包装标准Packaging standards产品包装标准Product packaging standards产品工程Product Engineering 3.2产品/过程质量体系Product/process quality system 产品/过程质量体系检查表Product/process quality system checklist 质量Quality3.3制定试生产工艺流程Trail Run Process Flow 工艺流程图Process Flow Chart产品工程Product Engineering 3.4试生产工艺流程评审Trail Run Process Flow Review 工艺流程评审表Process Flow Review CFT3.5规划试生产场地及物流动线Trail Run Plant& logistics flow 场地平面布置图Plant Layout产品工程Product Engineering 3.6 试生产场地规划及物流动线设定评审Plant layut and logistics flow 场地平面布置图评审表Plant Layout ReviewCFT3.7 特性矩阵图Characteristics matrix产品过程特性矩阵图Product process characteristic matrix 产品工程Product Engineering 3.8 制定PFMEA Work out PFMEA PFMEA产品工程Product Engineering 3.9 PFMEA评审PFMEA Review PFMEA评审表 PFMEA Review Form CFT 3.10 制定试生产控制计划Work out trail run CP Plan 控制计划表Contorl Plan(CP) Sheet 质量Quality 3.11 试生产控制计划评审Trail Run CP Review控制计划评审表CP ReviewCFT3.12 制定试生产材料购买计划及实施Material purchasing Plan&Perform 采购申请单(PR) 采购,资材Purchasing,Material3.13 编制试生产SOPWork out production SOP 作业指导书SOP 产品工程Product Engineering 3.14 编制试生产SIPWork out production SIP 标准检验规范SIP 质量Quality3.15 编制包装作业指导Work out Packaging SOP包装说明书PI产品工程Product Engineering 3.16 包装认定Packaging Determine 包装方案评审Packaging method Review CFT 3.17 材料性能及表面处理性能测试计划Material properties and surface treatment performance test Plan 测试计划表Test Plan Sheet质量Quality 3.18 测量系统分析计划MSA Plan 测量系统分析计划表MSA Plan Sheet 质量Quality 3.19 初始过程能力研究计划Original Process Capability Study 初始过程能力研究计划表Original Process Capability Study Plan 质量Quality3.20 阶段评审Phase Review 阶段评审表Phase Review Record 项目经理Program Manager4.1 试生产计划制定与实施Trail Run Plan and Perform 试模/试生产申请单Trail Run Request FormCFT 4.2 试生产总结Trail Run Summary试模/试生产报告,FA报告Trail Run Report,FA ReportCFT 4.3 测量系统分析结果 MSA 测量系统分析报告MSA Report 质量Quality 4.4初始过程能力研究结果Original process capability study Result初始过程能力研究报告Original process capability report 质量Quality 4.5设备能力研究结果Equipment capacity study results 设备能力研究结果报告CMK Equipment capacity study results 设备维护Equipment maintenance 4.6材料性能及表面处理性能测试结果Material properties and surface 材料性能及表面处理性能报告Material properties and surface treatment performance test Report质量Quality4.7分供方PPAP(PSW)批准Sub-Supplier PPAP(PSW)Approval 供应商PPAP提交/PSW文件签署Supplier PPAP Submission/PSW Approval 质量、产品工程Quality & Product Engineering 4.8固化批量生产用文件Formal mass productionprocedure 场地布局及物流动线图、工艺流程、控制计划、SOP、SIP、PI、BOM Plant Layout, process Flow, Control Plan,SOP,SIP,PI,BOMCFT4.9 产品质量策划总结和认定Product Quality Summary 产品质量策划总结和认定报告Product Quality Summary Report 质量Quality 4.10 PPAP提交PPAP Submission PSW批准文件PSW Approval Doc质量Quality4.11阶段评审Phase Review 阶段评审表Phase Review Record 项目经理Program Manager5.1 减少变差Reduce variation控制图Control chart质量Quality5.2 客户满意度调查Customer Satisfaction Survey 客户满意度调查表Customer Satisfaction Survey Form 客服Customer service5.3 交付Delivery产品交付绩效KPIProduct delivery KPI performance客服Customer service5.F e e d b a c k , A s s e s s m e n t a n d C o r r e c t i v e A c t i o n 反馈、评估和纠正措施顾客Client :产品描述Part description:递交日期 PPAP date :项目组长 Project leader:批量生产日期SOP date:Rev00项目阶段Project Stage策划内容Planning Content 见证资料Evidence Data 开始日期 Start Date2.P r o d u c t D e s i g n & D e v e l o p m e n t 产品设计和开发3.P r o c e s s D e s i g n a n d D e v e l o p m e n t 过程设计和开发完成日期 Finish dateRESPONSIBLE责任人4.r o d u c t a n d P r o c e s s V a l i d a t i o n 产品和过程验证Remark 备注1.P l a n a n d D e f i n e P r o g r a m 计划和定义项目Metal Component Engineering Ltd.APQP 计划进度表(汽车件)APQP Timing Plan Sheet(Automotive)供方Vendor:产品编号 Part number :版本Revision number:。
生产计划专业术语英语
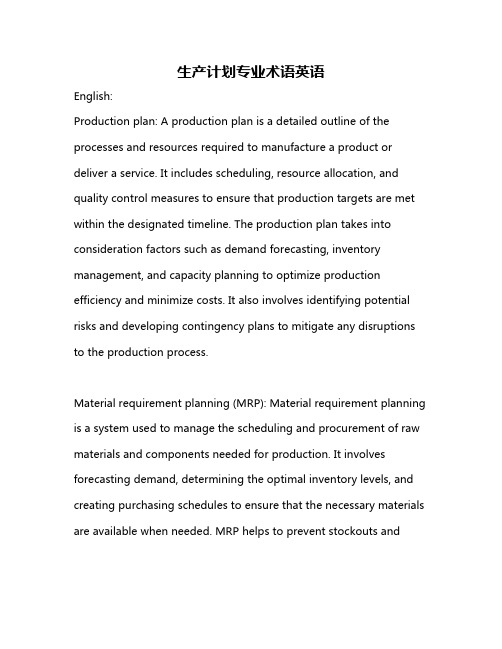
生产计划专业术语英语English:Production plan: A production plan is a detailed outline of the processes and resources required to manufacture a product or deliver a service. It includes scheduling, resource allocation, and quality control measures to ensure that production targets are met within the designated timeline. The production plan takes into consideration factors such as demand forecasting, inventory management, and capacity planning to optimize production efficiency and minimize costs. It also involves identifying potential risks and developing contingency plans to mitigate any disruptions to the production process.Material requirement planning (MRP): Material requirement planning is a system used to manage the scheduling and procurement of raw materials and components needed for production. It involves forecasting demand, determining the optimal inventory levels, and creating purchasing schedules to ensure that the necessary materials are available when needed. MRP helps to prevent stockouts andoverstock situations, thereby reducing inventory holding costs and improving production efficiency.Master production schedule (MPS): The master production schedule is a detailed plan that specifies the quantity and timing of the products to be manufactured over a specific time period. It takes into consideration factors such as customer demand, production capacity, and inventory levels to create a feasible and efficient production schedule. The MPS serves as a crucial communication tool between different departments within the organization and helps to coordinate and align production activities with overall business objectives.Capacity planning: Capacity planning involves determining the optimal level of production capacity needed to meet the demand for products or services. It considers factors such as equipment availability, labor resources, and production processes to ensure that the production facilities operate at their maximum efficiency without overloading or underutilizing their resources. Effective capacity planning is essential for optimizing the use of resources and meeting production targets while minimizing costs.中文翻译:生产计划:生产计划是制造产品或提供服务所需的详细流程和资源的大纲。