Fabrication of hydroxyl group modified monodispersed hybrid silica particles
二甲基硅氧烷基的环氧树脂,被用来制造导热复合材料和12微米的BN颗
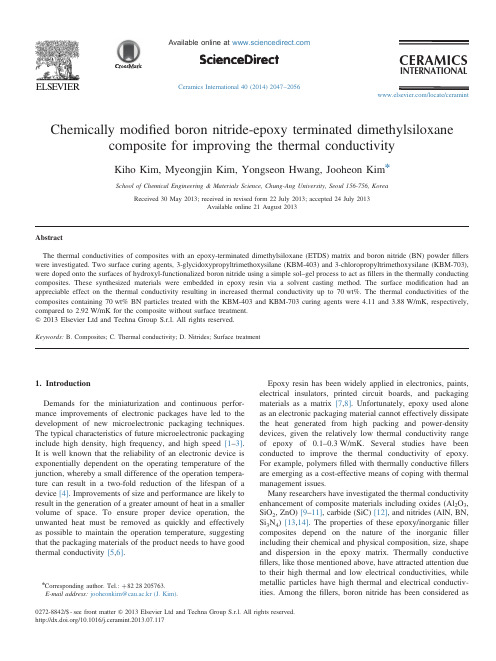
CERAMICSINTERNATIONALAvailable online at Ceramics International 40(2014)2047–2056Chemically modi fied boron nitride-epoxy terminated dimethylsiloxanecomposite for improving the thermal conductivityKiho Kim,Myeongjin Kim,Yongseon Hwang,Jooheon Kim nSchool of Chemical Engineering &Materials Science,Chung-Ang University,Seoul 156-756,KoreaReceived 30May 2013;received in revised form 22July 2013;accepted 24July 2013Available online 21August 2013AbstractThe thermal conductivities of composites with an epoxy-terminated dimethylsiloxane (ETDS)matrix and boron nitride (BN)powder fillers were investigated.Two surface curing agents,3-glycidoxypropyltrimethoxysilane (KBM-403)and 3-chloropropyltrimethoxysilane (KBM-703),were doped onto the surfaces of hydroxyl-functionalized boron nitride using a simple sol –gel process to act as fillers in the thermally conducting composites.These synthesized materials were embedded in epoxy resin via a solvent casting method.The surface modi fication had an appreciable effect on the thermal conductivity resulting in increased thermal conductivity up to 70wt%.The thermal conductivities of the composites containing 70wt%BN particles treated with the KBM-403and KBM-703curing agents were 4.11and 3.88W/mK,respectively,compared to 2.92W/mK for the composite without surface treatment.&2013Elsevier Ltd and Techna Group S.r.l.All rights reserved.Keywords:posites;C.Thermal conductivity;D.Nitrides;Surface treatment1.IntroductionDemands for the miniaturization and continuous perfor-mance improvements of electronic packages have led to the development of new microelectronic packaging techniques.The typical characteristics of future microelectronic packaging include high density,high frequency,and high speed [1–3].It is well known that the reliability of an electronic device is exponentially dependent on the operating temperature of the junction,whereby a small difference of the operation tempera-ture can result in a two-fold reduction of the lifespan of a device [4].Improvements of size and performance are likely to result in the generation of a greater amount of heat in a smaller volume of space.To ensure proper device operation,the unwanted heat must be removed as quickly and effectively as possible to maintain the operation temperature,suggesting that the packaging materials of the product needs to have good thermal conductivity [5,6].Epoxy resin has been widely applied in electronics,paints,electrical insulators,printed circuit boards,and packaging materials as a matrix [7,8].Unfortunately,epoxy used alone as an electronic packaging material cannot effectively dissipate the heat generated from high packing and power-density devices,given the relatively low thermal conductivity range of epoxy of 0.1–0.3W/mK.Several studies have been conducted to improve the thermal conductivity of epoxy.For example,polymers filled with thermally conductive fillers are emerging as a cost-effective means of coping with thermal management issues.Many researchers have investigated the thermal conductivity enhancement of composite materials including oxides (Al 2O 3,SiO 2,ZnO)[9–11],carbide (SiC)[12],and nitrides (AlN,BN,Si 3N 4)[13,14].The properties of these epoxy/inorganic filler composites depend on the nature of the inorganic filler including their chemical and physical composition,size,shape and dispersion in the epoxy matrix.Thermally conductive fillers,like those mentioned above,have attracted attention due to their high thermal and low electrical conductivities,while metallic particles have high thermal and electrical conductiv-ities.Among the fillers,boron nitride has been considered as/locate/ceramint0272-8842/$-see front matter &2013Elsevier Ltd and Techna Group S.r.l.All rights reserved./10.1016/j.ceramint.2013.07.117nCorresponding author.Tel.:þ8228205763.E-mail address:jooheonkim@cau.ac.kr (J.Kim).an attractive candidate due to its significantly high thermal conductivity($300W/mK),lack of toxicity,superior chemi-cal stability,electrical insulation properties,and relatively low cost.In order to obtain a higher thermal conductivity while maintaining the existing properties,filler loadings of60wt% or higher have traditionally been incorporated to form a heat conduction path in the matrix that is as continuous as possible. However,a highfiller content becomes rather inflexible with voids and cracks forming betweenfillers.Moreover,the BN/ epoxy slurry has a relatively low viscosity before drying, which facilitates the sedimentation of the BNfiller.As a result, BNfillers settle to the bottom of the compositefilm,the heat-conductive path is cut off,and the thermal conductivity decreases.In response to this issue,many studies have suggested fabrication of a surface-modified BN particle to preventfiller sedimentation[15,16].Recently,BN has been coated with a surface-curing agent to further enhance the thermal conductivity of polymer compo-sites,resulting in a reduction of sedimentation due to the lone-pair electron interaction of particle surfaces into the matrix.Gu et al.achieved a thermal conductivity of1.052W/mK using a hot disk instrument for epoxyfilled with silane-modified BN at a solid loading of60wt%[17].Yung et al.reported the effect of multi-modal particle size mixing on the formation of a thermally conductive network[18].Unfortunately,these previous experiments used nano-scale BN particles($1μm). Due to the small size of thefiller-containedfilm,heat passing through the boundary of the particles is more frequently the main cause of the phonon scattering.The diffuse boundary scattering due to the short wavelength in comparison to interface roughness of dominant phonon heat carriers not only reduces the phonon mean free path,but can also destroy the coherence of the phonons[19].Thermal resistance at particle junctions known as thermal boundary resistance or Kapitza resistance is one of the primary causes of heat transfer property reduction.In the presence of a heatflux across the boundary,this thermal resistance causes a temperature dis-continuity at the boundary.Due to the differences of the electronic and vibrational properties of various materials,an energy carrier will scatter when attempting to traverse the interface[20–22].It is known that hexagonal BN particles have a plate-like shape withflat surfaces corresponding to the basal planes of the hexagonal crystal structure.The basal plane of BN is molecularly smooth and has no surface functional groups available for chemical bonding or interactions.In contrast,the edge planes of the platelets have functional groups such as hydroxyl and amino groups.These functional groups allow the BNfiller to disperse in an organic solvent and chemically bond with other rge BN particles are significantly decreased in the edge plane areas,resulting in difficulty obtaining uniform dispersion and chemical bonding.To this end,Sato et al.employed0.7μm BN particles as a thermal conductivefiller on polyimide resin[23,24].For the effective use of micro-scale BN as afiller,another surface treatment is necessary to make the reaction site of the particle surface.In this study,a polymer matrix,dimethyl siloxane-basedepoxy,was employed to fabricate a thermally conductivecomposite and a12μm BN particle was adopted as acompositefiller to reduce phonon scattering and improve thethermal conductivity.To increase the affinity and dispersibilityof thefiller in the epoxy matrix,which is expected to provide agood thermal conductivity,two types of surface curing agentswere employed.The resulting surface curing agent-coated BNpossessed electrical insulating properties in addition toenhanced thermal conductivity due to reduced thermal resis-tance at the junction.The mechanical properties of thefabricated composites were measured and the data demon-strates that a small amount of surface curing agent enhancesthe thermal and mechanical properties.2.Experimental2.1.Synthesis of ETDSThe epoxy-terminated dimethysiloxane(ETDS)oligomerwas obtained from Shin-Etsu silicon(KF-105,equivalentweight(E.E.W)=490g/eq,density=0.99g/cm3).In ourprevious study,the weight ratio of the epoxy to the curingagent was determined to provide efficientflexibility of thematrix.In this study,the equivalent weight ratio of ETDS toDDM(4.4′-diamino diphenylmethane)was1:2.1.9g of DDMwas placed in a four-neck roundflask equipped with a refluxcondenser and was preheated to363K.9.5g of the ETDSresin was added and heated in an oil bath at363K for1hunder a N2atmosphere.The bubbles in the mixture wereremoved by placing the mixture in a vacuum oven for30minat room temperature.The mixture was then placed in an oilbath at323K for10min in a N2atmosphere.Thefinaldegassing was performed in a vacuum oven for1h at roomtemperature to remove air bubbles[25].2.2.Surface modification of BNThe detailed synthesis procedure is shown in Fig.1.First,micro-BN particles were suspended in a5M sodium hydro-xide solution at1101C for18h to attach more hydroxide ionsonto the surfaces.Because micro-BN particles have fewfunctional groups,surface treatment is necessary to facilitatechemical bonding with the surface curing agent.After basesolution dipping,the particles were rinsed with D.I.water and filtered several times to adjust the pH from basic to neutral. The micro-BN hydroxide particles were left in the furnace at801C for5h,cooled to room temperature,and then stored indesiccators.The BN particles were modified with two surface curingagents,KBM-403and KBM-703,obtained from Shin-EtsuSilicon by a sol-gel reaction.An appropriate amount of3-glycidoxypropyltrimethoxysilane(KBM-403;3–5%based onthe weight of the micro-BN particles)and3-chlorop-ropyltrimethoxysilane(KBM-703)were added to D.I.waterand stirred at501C for30min to achieve hydrolysis.Themicro-BN hydroxide particles were then dipped into theK.Kim et al./Ceramics International40(2014)2047–2056 2048resulting solution and stirred at 701C for 1h,followed by rinsing with D.I.water and filtering three times.The particles were then vacuum dried at 801C for 5h to remove the solvent.The amount of the coating solution necessary is preferably 0.05–10%by weight,based on the weight of the particles.When the amount of the coating solution is less than 0.05%by weight,there is a tendency for insuf ficient and non-uniform particle coating to occur.When the amount of the coating solution exceeds 10%by weight,the obtained particles may possess excessive thermal resistance,thereby causing a decrease of the thermal conductivity of the composite films [26].2.3.Preparation of the BN/epoxy compositesThe composites were prepared by solution blending and a casting method consisting of (a)adding surface curing agent-coated micro-BN to the ETDS epoxy resin (50,60,70wt%)for approximately 3h in N,N-dimethylformamide (DMF)until the synthesized materials were completely mixed,(b)fabricat-ing the composite films to a uniform thickness via a doctor blade on the Te flon mold,(c)pre-curing the films at 1501C for 3h until no air bubbles appeared on the surface followed by post-curing at 1801C for 5h,and (d)cooling to room temperature.2.4.CharacterizationFourier transform infrared (FT-IR;Parkin-Elmer Spectrum One)spectroscopy and X-ray photoelectron spectroscopy (XPS;VG-Microtech,ESCA2000)were employed to analyze the surface curing agent-coated BN.For FT-IR spectroscopy,the ATR mode was used to avoid the in fluences of moisture adsorbed on the potassium bromide (KBr)particles and the scans were performed using radiation in the frequency range of 400–4000cm À1.In the XPS analysis,a monochromatic Mg K αX-ray source was used at 1253.6eV and the Gaussian peak widths obtained by curve fitting were constant in each spectrum.Thermogravimetric analysis (TGA;TGA-2050,TAinstrument)of the samples was carried out to examine the thermal degradation of BN,BN-403,and BN-703.4mg of the samples were heated to 8001C at a heating rate of 101C/min under a nitrogen atmosphere.Field emission scanning electron microscopy (FE-SEM;Sigma,Carl Zeiss)was carried out to con firm the cross-sections of the component films before and after the silane treatment.The samples were sputtered with a thin layer of platinum to avoid the accumulation of charge before the FE-SEM observations.The thermal diffusivity (δ,mm 2s À1)at room temperature was measured on disk samples using a laser flash method (Netzsch Instruments Co.,Nano flash LFA 447System).The speci fic heat (C ,J g À1K À1)at room temperature was measured on disk samples via differential scanning calorimetry (DSC;Perkin-Elmer Co.,DSC-7System)and the bulk density (ρcomp ,g cm À3)of the specimens was measured using the water displacement method.The thermal conductivity (Ф,W mK À1)was calcu-lated using the following equation:Ф¼δC ρcompTo study the mechanical properties of the composite materials,mechanical analysis (DMA;Triton Instrument,Triton DMTA)was carried out.The storage modulus of the solid films was measured at a frequency of 1Hz.The temperature range was À180to 1801C with cooling and heating rates of 101C/min.3.Results and discussion3.1.Structure analysisThe chemical structures of the surface-modi fied BN were determined using Fourier transform infrared spectroscopy (FT-IR),thermogravimetric analysis (TGA),and X-ray photo-electron spectroscopy (XPS).Fig.2(a –c)shows the FT-IR spectra of pristine BN,BN-403,and BN-703,respectively.For pristine BN,the bands at 1400and 800cm À1indicate stretching vibration in the hexagonal BN.The absorption band of pristine BN at 2300–2380cm À1represents absorbed CO 2.Fig.1.Reaction scheme for the preparation of surface curing agent treated BN particle (BN-403,BN-703).K.Kim et al./Ceramics International 40(2014)2047–20562049Comparing the pristine BN and the surface curing agent-treated BN (BN-403and BN-703),the new band at 1100cm À1corresponds to stretching of the Si –O bonds,which existed in the pure surface curing agent.Detailed surface information of pristine BN,BN –OH,BN-403,and BN-703was collected by X-ray photoelectron spectroscopy (XPS)and the corresponding results are pre-sented in Fig.3.In the spectrum of pristine BN,there are only two elements of B and N.However,the O 1s signal emerges in the spectrum of BN –OH.This result implies that the hydroxyl groups were effectively introduced on the BN surfaces and edges via the sodium hydroxide treatment.These hydroxyl groups,acting as anchor sites,enabled attachment between the BN particles and surface curing agent.Moreover,the new peaks of C 1s and Si 2p can be assigned in the spectra of both BN-403and BN-703,indicating that both surface curing agents,403and 703,were successfully attached to the surface and edges of pristine BN particles.The detailed chemical bonding of fabricated,surface-treated BN particles was con firmed from the de-convoluted B 1s,Si 2p,and C 1s spectra,the results of which are shown in Fig.4.Fig.4(a and b)show the de-convoluted B 1s spectra of BN-403and BN-703,respectively.The B 1s spectra of both BN-403and BN-703showed a strong binding energy peak for the B –N bond and a weak binding energy peak for the B –OH bond at 190.4eV and 192eV,respectively [27,28].The B –OH peak resulted from the introduction of a hydroxyl group by the base treatment.In order to provide clearer evidence of chemical bonding between the BN particles and the silane curing agent,the Si 2p peak of these synthesized materials can be fitted by a curve with several component peaks.Fig.4(c and d)shows the de-convoluted Si 2p spectra of BN-403and BN-703,respectively.In the spectra of both BN-403and BN-703,the strong peak at the binding energy of 102.1eV represents the bond between silicon and oxygen originating from the BN particles (B –O –Si),indicating that the surface curing agent and BN particles are connected through the hydroxyl groups.The peak at 103.3eV is attributed to siloxane (Si –O –Si)resulting from the partial hydrolysis of the silane curing agent molecules during the silanization reaction.Moreover,the peak at 100.8eV is attributed to Si –C bonding in the silane curing agent molecules.These results are in agreement with the reaction mechanism of silane,including the hydrolysis of –OCH 3,condensation to oligomers,hydrogen bonds between oligomer and hydroxyl groups on the substrate,and the formation of the covalent linkage between silane and the substrate.The peak at 102.5eV is attributed to Si –OH bonding,indicating that some hydroxyl groups did not hydro-lyze and a small amount of hydroxyl group remained [29,30].This implies that the amount of hydroxyl groups on the BN surface was not suf ficient to make a uniform siloxane network and some hydroxyl groups in the surface curing agent were not hydrolyzed.This is due to the basal plane of the boron nitride particle surface having no functional groups.In addition,the silane coupling agent does not coat the surface uniformly such that the hydroxyl groups of the surface curing agent remained.The C 1s spectra of both BN-403and BN-703were de-convoluted to compare the structural differences of the two silane curing agents and the results are shown in Fig.4(e and f),respectively.In the spectra of both BN-403and BN-703,the strong peak at a binding energy of 284.7eV indicates the C –C bond and the weak peak at the binding energy of 283.44eV represents the C –Si bond,which exists in the surface curing agent structure.The primary difference between KBM-403and KBM-703is that KBM-403has ether and epoxide groups,whereas KBM-703has a chloride atom at the end of the carbon chain.In the C 1s spectrum of BN-403,C –O bonding is observed at a binding energy of 286.2eV,which originates from the ether and epoxide groups.However,in the case of BN-703,the peak at 285.9eV is attributed to C –Cl bonding,which can be explained by the existence of a chloride atom at the end of the carbon chain [31].Based on these results,it can be concluded that the silane treatment can effectively introduce the surface curing agent onto the surface ofBN.Fig.2.FT-IR spectra of (a)raw BN,(b)BN-403and (c)BN-703.Fig.3.X-ray photoelectron spectroscopy survey scans of (1)raw BN,(b)BN-OH,(c)BN-403,and (d)BN-703.K.Kim et al./Ceramics International 40(2014)2047–20562050Fig.4.XPS spectra of BN-403and BN-703.(a)XPS B 1s spectrum of BN-403:(b)XPS B 1s spectrum of BN-703:(c)XPS Si 2p spectrum of BN-403:(d)XPS Si 2p spectrum of BN-703;(e)XPS C 1s spectrum of BN-403:(f)XPS C 1s spectrum of BN-703.K.Kim et al./Ceramics International 40(2014)2047–20562051The compositions of the as-prepared BN,BN-403,and BN-703composites were further investigated via TGA (Fig.5).The experiments were performed up to 8001C in air at a heating rate of 101C min À1.Under these conditions,weight loss was not observed up to 8001C for pristine BN,whereas weight losses of about 4%and 3.6%were observed for BN-403and BN-703,respectively,due to thermal decomposition of the surface curing agents attached to the BN.The mass ratios of KBM-403/BN and KBM-703/BN for BN-403and BN-703were calculated to be 0.042/1and 0.037/1,respec-tively.Moreover,these ratios between BN and the surface curing agent are optimal to mix the surface curing agent-treated BN as a filler and the silane-based epoxy as a matrix [32].As reported by Itoh et al.,the surface curing agent is poorly dispersed in the particles when too little is added and the desired effect of improved crack formation resistance in the cured resin composition cannot be achieved [33].An excess of surface curing agent in the resin composition leads to a decreased thermal conductivity.This is because the redundant coupling agent causes phonon scattering and gives rise to a decreased thermal conductivity of the composites,resulting in low thermal conductivity materials.3.2.Thermal propertiesThe thermal conductivity of the composites is controlled by the intrinsic conductivities of the filler and matrix as well asthe shape,size,and loading level of the filler.Table 1shows the variations of the thermal conductivity of the BN/ETDS composites with nano-BN ($1μm),micro-BN (8μm,12μm),and a filler content ranging from 50to 70wt%.The thermal conductivity of pristine ETDS is approximately 0.2W/mK.It can be seen that as the weight fraction of these fillers increased,the thermal conductivity also increased consider-ably.With 12μm particles at loadings of 50wt%,60wt%,and 70wt%,the thermal conductivity increased by factors of 11.1,13.35,and 14.58,respectively,compared to the pure resin ($0.2W/mK).As shown for the three types of particles,the thermal conductivity is also a function of the particle size,where the results parallel the effect of the particle type.The highest thermal conductivity values were obtained from the 12μm particle-filled composites at all filler loading levels.This result can be explained by the thermal interface resistance caused by phonon boundary scattering.In theory,the scatter-ing of phonons in composite materials is primarily due to the existence of an interfacial thermal barrier from acoustic mismatch or damage of the surface layer between the filler and the rge particles tend to form fewer thermally resistant polymer-layer junctions than small particles at the same filler rge particles are therefore used as a thermal conducting filler because of their negligible phonon scattering effect and excellent thermal conductivity [34,35].In this paper,the use of a micro-filler to improve the thermal conductivity of composites was studied.The in fluence of the BN concentration and surface treatment on the thermal conductivity of BN/ETDS composites is presented in Fig.6.It can be seen that as the weight fraction of these synthesized materials increased,the calculated thermal conductivity of all of the investigated composites increased considerably.The use of surface curing agents clearly improved the thermal con-ductivities of the composites.At 12μm BN particle loadings of 50,60,and 70wt%,the thermal conductivities of the KBM-403-and KBM-703-treated BN/ETDS composites increased by factors of 1.17,1.23,and 1.41and 1.15,1.19,and 1.33compared to the untreated BN/ETDS composite,respectively.This effect could be explained by the enhanced dispersibility of particles in the composite caused by the surface curing agent.The two surface curing agents used contain an epoxide group and chloride functional groups that interact with the active groups of the epoxy matrix.Thus,the organic active groups or long molecular chains on the surface of the modi fied BN either react or entangle with the reactive groups of the epoxy matrix.The addition of surface curing agents totheFig.5.TGA thermograms of pristine BN,BN-403and BN-703.Table 1Thermal conductivity of various particle size and filler contents (W/mK).Size of BN particlesThermal conductivity at various filler concentration [W/mK]50wt%60wt%70wt%$1m m 1.49 1.67 2.158m m 2.16 2.35 2.7712m m2.322.732.92K.Kim et al./Ceramics International 40(2014)2047–20562052epoxy matrix therefore improves the interface bonding between the BN particles and matrix,leading to an enhanced thermal conductivity.In addition,this result could beexplained by the reduction of the phonon diffuse boundary scattering that constitutes a signi ficant part of the thermal resistance accompanying an imposed temperature gradient.The phonon scattering at interfaces,both for free surfaces and those bonded to other materials,observed for most real interfaces has yet to be quantitatively explained.The boundary resistance between two carefully bonded solids appears to be satisfactorily described by the acoustic impedance mismatch between the two media.The silane coupling agents acted as phonon transfer bridges between the polymer and the ceramic filler,which reduced the phonon boundary scattering and improved the thermal conductivity at low concentrations.As demonstrated in this study,the KBM-403treatment was more effective than KBM-703in enhancing the thermal conductivity.This can be explained by the ETDS/DDM polymerization mechanism.When the composite curing was performed at high temperature,epoxide groups in the ETDS react with DDM,and the ring opening and polymerization reactions proceed continuously.Similarly,epoxide groups in KBM-403react with DDM and are polymerized with ETDS.As a result,the boron nitride filler linked with the matrix through covalent bonding.However,KBM-703has a chloride group that instead forms non-covalent bonding,a dipole-dipole interaction,with the ETDS matrix.Therefore,KBM-403-Fig.6.Effect of surface treatment of BN particles on the thermal conductivity of BN/ETDS composites at various fillerconcentration.Fig.7.SEM cross section image of (a)–(b)BN/ETDS,(c)–(d)BN-403/ETDS and (e)–(f)BN-703/ETDS composites with 50wt%filler concentration.K.Kim et al./Ceramics International 40(2014)2047–20562053treated BN has a stronger interaction with the ETDS matrix along with good dispersibility and a higher thermal conduc-tivity than the KBM-703-treated BN composite.The differences in the cross-sectional images of each composite can be correlated to the existence of a silane coupling agent.Fig.7shows FE-SEM images of the cross-sections of50wt%BN/ETDS and two kinds of surface coupling agent-treated BN/ETDS compositefilms.As observed in Fig.7(a,c and e),all of the compositefilms appear to be homogeneously distributed.However,when the BN/epoxy compositefilm is observed at higher magnification (Fig.7(b)),it can be seen that the BNfiller settled to the bottom and a non-uniform distribution can be observed in the top of thefilm.This phenomenon is due to sedimentation of thefiller,which is an endemic problem of the casting method. BNfillers were well mixed for a sufficient time with the epoxy resin,maintaining goodfluidity at the high temperature,but sedimentation of thefiller progressed in the post curing step. On the other hand,the images in Fig.7(d and e)show a uniform cross-section of the silane coupling agent-treated BN, which was dispersed more uniformly and embedded in theepoxy,creating superior interface adhesion with the BN in the epoxy matrix.Uniform distribution of BN particles develops in the conduction carrier path.Moreover,BN has an idiopathic high surface energy,indicating that the phase interaction force between the epoxy and BN particles is very weak and suggesting that a low energy is needed to pull BN particles out from the matrix[36].The images in Fig.7(d and f)show an enhanced homogeneous distribution of BN particles throughout and a decrease of cracks and voids between the BN particles.This is further evidence that the surface curing agent enhanced the BN particle affinity with the matrix. Fig.7shows that the use of surface coupling agents effectively improves the homogeneous dispersion of BN particles in the epoxy,eliminates the agglomeration offiller, and decreases the void content and defects in the composites, resulting in an increased thermal conductivity.3.3.Mechanical propertiesThe mechanical properties of the composites with enhanced thermal conductivities were also measured by dynamic mechanical analysis(DMA).This was carried out to determine the improvement of the mechanical properties after the surface modification of the boron nitride particles in the polymer matrix.Since the operation temperature of the electronic package is generally about1501C,the stability of the composites was examined up to this temperature.The storage modulus of compositefilms with afiller content of70wt%is displayed in Fig.8as a function of temperature.As expected, the slopes of the curves tended to decrease near the glass temperature(T g).It can be clearly seen that the storage modulus of the composites increased withfiller surface modification,which is due to the mechanical reinforcement resulting from the strong interactions between BN and the ETDS matrix.As mentioned above,silane coupling agents improved the adhesive property between thefiller and matrix, as the stress is not well transferred when the same force is applied to the composite.The KBM-403in the composites prevented efficient treeing of the propagation of stress and,as a result,the storage modulus could be improved where the modulus of the KBM-403treated with the BN composite was higher than that of the KBM-703-treated BN composite. The tanδpeak position,which is a measure of the glass transition temperature(T g),shifted to higher temperatures with surface modification.The peak height was reduced when compared to that of the surface-untreated BN composite because the well dispersedfiller and sufficient incorporation of epoxy restricted the mobility of the epoxy chains,resulting in the higher mechanical properties observed for the surface-treated BN composites.4.ConclusionBN/epoxy compositefilms with different BN particle sizes and contents were successfully fabricated with a surface curing agent using a solvent casting method.The thermal conductiv-ities of polymer compositesfilled with various types of particles were evaluated and the thermal interface resistance theory was applied.Various particle tofiller ratios were tested and the12μmfiller demonstrated a higher performance,in the range of136–149%,than the nano-sizefiller($1μm). Furthermore,by applying micro-sized particles,the formation of conductive networks was maximized while minimizing the thermal interface resistance along the heatflow path.This thermal interface resistance is caused by phonon scattering in the interface of materials,which is the primary cause of decreased thermalconductivity.Fig.8.Storage modulus of ETDS and ETDS composites with70wt%filler concentration.K.Kim et al./Ceramics International40(2014)2047–2056 2054。
MEMS2.2 Bulk Micromachining(MEMS讲义)

T < 30oC: Steeper slope => higher activation energy EA The energy is associated with the oxidation reaction => reaction-limited.
(2.2)
primary oxidizing species, OH-, is formed by the
dissociation of water
H2O <---> OH- + H+
(2.3)
3. Reaction of the hydrated Si with complexing agent
(complexant) in the solution
mechanism of silicon wet etching
1. Injection of holes into the semiconductor
Si + 2h+ ---> Si2+
(2.1)
2. Attachment of hydroxyl group OH- to Si2+
Si2+ + 2(OH-) ---> Si(OH)2
However, thick layer are used as a mask anyway , especially for shallow etching, as the oxide is so easy to form and pattern.
烷基酚醛树脂羟基羧基
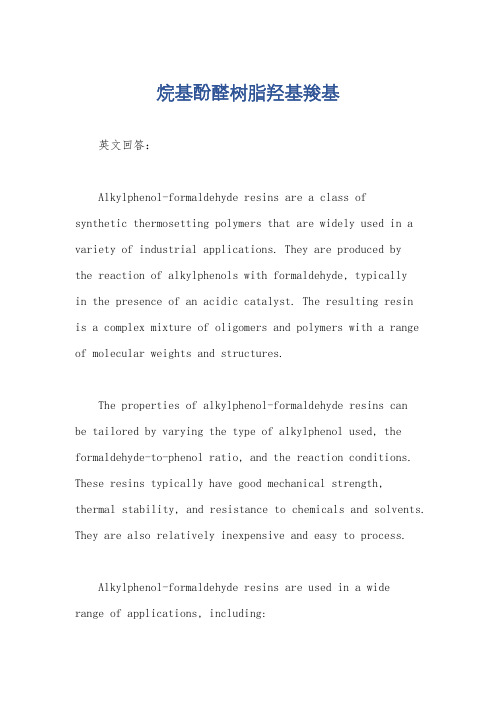
烷基酚醛树脂羟基羧基英文回答:Alkylphenol-formaldehyde resins are a class ofsynthetic thermosetting polymers that are widely used in a variety of industrial applications. They are produced bythe reaction of alkylphenols with formaldehyde, typicallyin the presence of an acidic catalyst. The resulting resinis a complex mixture of oligomers and polymers with a range of molecular weights and structures.The properties of alkylphenol-formaldehyde resins canbe tailored by varying the type of alkylphenol used, the formaldehyde-to-phenol ratio, and the reaction conditions. These resins typically have good mechanical strength, thermal stability, and resistance to chemicals and solvents. They are also relatively inexpensive and easy to process.Alkylphenol-formaldehyde resins are used in a widerange of applications, including:Molding compounds: Alkylphenol-formaldehyde resins are used to produce molded parts for a variety of applications, including electrical components, automotive parts, and consumer products.Laminates: Alkylphenol-formaldehyde resins are used to produce laminates, which are made by bonding layers of paper or fabric together with a resin. Laminates are usedin a variety of applications, including countertops, flooring, and wall panels.Adhesives: Alkylphenol-formaldehyde resins are used as adhesives in a variety of applications, including wood bonding, metal bonding, and paper bonding.Coatings: Alkylphenol-formaldehyde resins are used as coatings in a variety of applications, including metal coatings, wood coatings, and paper coatings.Alkylphenol-formaldehyde resins have been used commercially for over 50 years. However, concerns have beenraised about the potential environmental and health effects of these resins. Alkylphenols are endocrine disruptors, which means that they can interfere with the hormonal system. They have been linked to a variety of adverse effects in wildlife, including reproductive problems, developmental abnormalities, and immune system dysfunction.In response to these concerns, the use of alkylphenol-formaldehyde resins has been restricted in some countries. In the United States, the Environmental Protection Agency (EPA) has banned the use of alkylphenol-formaldehyde resins in baby bottles and other children's products. The EPA is also considering restrictions on the use of these resins in other applications.中文回答:烷基酚醛树脂。
检测器的种类及选择方法
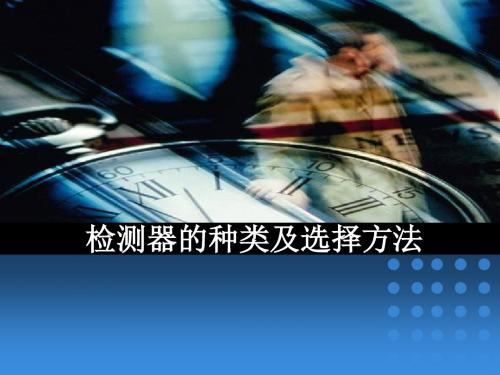
荧光检测 fluorescence and (b) chemiluminescence profiles of HRP-immunolabeled GFP.
电化学检测器(ECD)
电化学检测器是测量物质的电信号变化,对具有氧化还原 性质的化合物,如含硝基、氨基等有机化合物及无机阴、阳 离子等物质可采用电化学检测器。包括极谱、库仑、安培和 电导检测器等。前三种统称为伏安检测器,用于具有氧化还 原性质的化合物的检测,电导检测器主要用于离子检测。其 中安培检测器(AD)应用较广泛,更以脉冲式安培检测器最为 常用。 原理:在两电极之间施加一恒定电位,当电活性组分经过 电极表面时发生氧化还原反应(电极反应),电量(Q)的大小符 合法拉第定律Q=nFN。因此,反应的电流(I)为:I=nFdN/ dt,式中n为每摩尔物质在氧化还原过程中转移的电子数,F 为法拉第常数,N为物质的摩尔数,t为时间。当流动相的流 速一定时,dN/dt与组分在流动相中的浓度有关。
紫外检测器(UV)
The data showed that glucuronidation of the 3- and 40-hydroxyls resulted in band I λmax hypsochromic shifts (or blue shift) of 13-30 and 5-10 nm, respectively. Glucuronidation of the 5-hydroxyl group caused a band II λmax hypsochromic shift of 5-10 nm. In contrast, glucuronidation of the 7-hydroxyl group did not cause any λmax change in band I or II λmax, whereas glucuronidation of the 6hydroxyl group did not cause predictable changes in λmax values. The paper demonstrated for the first time that a rapid and robust analysis method using λmax changes in online UV spectra can be used to pinpoint region-specific glucuronidation of flavones and flavonols with hydroxyl groups at the 40-, 3-, 5-, and/or 7-position(s).
木质素分子在储能器件中的应用研究进展
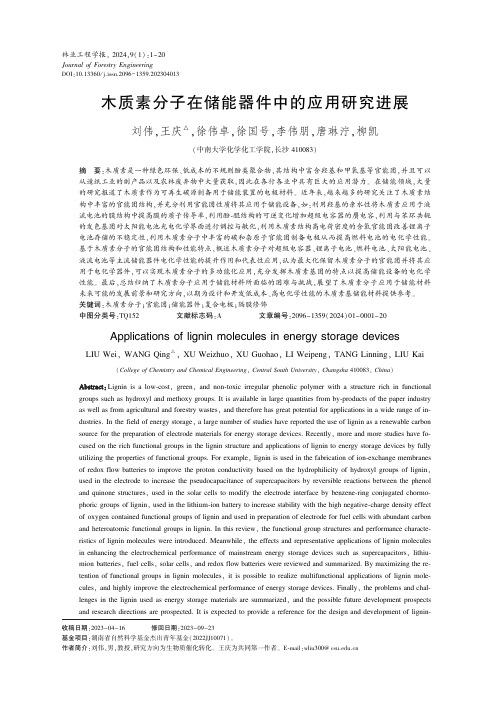
林业工程学报,2024,9(1):1-20JournalofForestryEngineeringDOI:10.13360/j.issn.2096-1359.202304013收稿日期:2023-04-16㊀㊀㊀㊀修回日期:2023-09-23基金项目:湖南省自然科学基金杰出青年基金(2022JJ10071)㊂作者简介:刘伟,男,教授,研究方向为生物质催化转化㊂王庆为共同第一作者㊂E⁃mail:wliu300@csu.edu.cn木质素分子在储能器件中的应用研究进展刘伟,王庆ә,徐伟卓,徐国号,李伟朋,唐琳泞,柳凯(中南大学化学化工学院,长沙410083)摘㊀要:木质素是一种绿色环保㊁低成本的不规则酚类聚合物,其结构中富含羟基和甲氧基等官能团,并且可以从造纸工业的副产品以及农林废弃物中大量获取,因此在各行各业中具有巨大的应用潜力㊂在储能领域,大量的研究报道了木质素作为可再生碳源制备用于储能装置的电极材料㊂近年来,越来越多的研究关注了木质素结构中丰富的官能团结构,并充分利用官能团性质将其应用于储能设备,如:利用羟基的亲水性将木质素应用于液流电池的膜结构中提高膜的质子传导率,利用酚⁃醌结构的可逆变化增加超级电容器的赝电容,利用与苯环共轭的发色基团对太阳能电池光电化学界面进行调控与敏化,利用木质素结构高电荷密度的含氧官能团改善锂离子电池存储的不稳定性,利用木质素分子中丰富的碳和杂原子官能团制备电极从而提高燃料电池的电化学性能㊂基于木质素分子的官能团结构和性能特点,概述木质素分子对超级电容器㊁锂离子电池㊁燃料电池㊁太阳能电池㊁液流电池等主流储能器件电化学性能的提升作用和代表性应用,认为最大化保留木质素分子的官能团并将其应用于电化学器件,可以实现木质素分子的多功能化应用,充分发挥木质素基团的特点以提高储能设备的电化学性能㊂最后,总结归纳了木质素分子应用于储能材料所面临的困难与挑战,展望了木质素分子应用于储能材料未来可能的发展前景和研究方向,以期为设计和开发低成本㊁高电化学性能的木质素基储能材料提供参考㊂关键词:木质素分子;官能团;储能器件;复合电极;隔膜修饰中图分类号:TQ152㊀㊀㊀㊀㊀文献标志码:A㊀㊀㊀㊀㊀文章编号:2096-1359(2024)01-0001-20ApplicationsofligninmoleculesinenergystoragedevicesLIUWei,WANGQingә,XUWeizhuo,XUGuohao,LIWeipeng,TANGLinning,LIUKai(CollegeofChemistryandChemicalEngineering,CentralSouthUniversity,Changsha410083,China)Abstract:Ligninisalow⁃cost,green,andnon⁃toxicirregularphenolicpolymerwithastructurerichinfunctionalgroupssuchashydroxylandmethoxygroups.Itisavailableinlargequantitiesfromby⁃productsofthepaperindustryaswellasfromagriculturalandforestrywastes,andthereforehasgreatpotentialforapplicationsinawiderangeofin⁃dustries.Inthefieldofenergystorage,alargenumberofstudieshavereportedtheuseofligninasarenewablecarbonsourceforthepreparationofelectrodematerialsforenergystoragedevices.Recently,moreandmorestudieshavefo⁃cusedontherichfunctionalgroupsintheligninstructureandapplicationsoflignintoenergystoragedevicesbyfullyutilizingthepropertiesoffunctionalgroups.Forexample,ligninisusedinthefabricationofion⁃exchangemembranesofredoxflowbatteriestoimprovetheprotonconductivitybasedonthehydrophilicityofhydroxylgroupsoflignin,usedintheelectrodetoincreasethepseudocapacitanceofsupercapacitorsbyreversiblereactionsbetweenthephenolandquinonestructures,usedinthesolarcellstomodifytheelectrodeinterfacebybenzene⁃ringconjugatedchormo⁃phoricgroupsoflignin,usedinthelithium⁃ionbatterytoincreasestabilitywiththehighnegative⁃chargedensityeffectofoxygencontainedfunctionalgroupsofligninandusedinpreparationofelectrodeforfuelcellswithabundantcarbonandheteroatomicfunctionalgroupsinlignin.Inthisreview,thefunctionalgroupstructuresandperformancecharacte⁃risticsofligninmoleculeswereintroduced.Meanwhile,theeffectsandrepresentativeapplicationsofligninmoleculesinenhancingtheelectrochemicalperformanceofmainstreamenergystoragedevicessuchassupercapacitors,lithiu⁃mionbatteries,fuelcells,solarcells,andredoxflowbatterieswerereviewedandsummarized.Bymaximizingthere⁃tentionoffunctionalgroupsinligninmolecules,itispossibletorealizemultifunctionalapplicationsofligninmole⁃cules,andhighlyimprovetheelectrochemicalperformanceofenergystoragedevices.Finally,theproblemsandchal⁃lengesintheligninusedasenergystoragematerialsaresummarized,andthepossiblefuturedevelopmentprospectsandresearchdirectionsareprospected.Itisexpectedtoprovideareferenceforthedesignanddevelopmentoflignin⁃林业工程学报第9卷basedenergystoragematerialswithlowcostandhighelectrochemicalperformance.Keywords:ligninmolecules;functionalgroups;energystoragedevices;compositeelectrode;membranemodification㊀㊀随着国际能源结构由化石能源向风㊁光电等绿色可再生能源的转变[1],储能装置,如超级电容器㊁锂离子电池㊁燃料电池㊁液流电池等得到了广泛应用㊂近年来,为增进储能装置的环境效益,降低储能装置对环境的影响,使用替代的可再生材料,构建绿色环保的储能装置吸引了众多学者的关注,并取得了一系列重大突破㊂纤维素㊁木质素等生物质材料凭借其价格低廉㊁储量丰富㊁对环境无污染以及可再生等优点被认为是用于开发和改进储能装置的理想选择[2-6]㊂特别是木质素,作为一种无毒的天然芳香聚合物,不仅具有酚羟基㊁甲氧基㊁甲基㊁羰基以及羧基等众多官能团可应用于储能材料,而且作为造纸工业的副产品可以大量廉价获取(每年产量高达5000万t)[7]㊂木质素应用于储能装置的一种策略是通过水热或高温等方法将其转变为碳材料并用作导电电极㊂由于所形成的碳材料具有多维互连的多孔结构㊁合适的孔径分布以及高表面积等特点,应用于超级电容器㊁锂离子电池等储能装置可表现出高性能的比电容㊁出色的循环效率以及高稳定性㊁高能量密度等优势[3,8-9]㊂同时通过对木质素前驱体的元素掺杂,可以对所合成碳材料的氧化还原等表面化学性质进行调控,实现适用于不同储能装置的电化学功能[10-11]㊂然而此策略仅以木质素为碳源,忽视了木质素分子刚性苯环和柔性长链兼具的结构以及丰富的表面官能团,限制了木质素在储能装置中的应用㊂另一种策略是直接将木质素高分子应用于储能器件中,利用木质素分子化学结构的多样性,实现多种储能器件的构建㊂木质素分子中与苯环相共轭的羟基㊁羧基等通过醌式互变可容纳电荷,在超级电容器中增加电极材料的赝电容性能[12],用于锂离子电池的电极则起到稳定锂离子的作用[13]㊂基于可逆的氧化还原性,木质素分子可以作为液流电池天然的电子传递体,并很容易进行化学修饰,进一步增强电荷传递性能[6]㊂由于发色基团的存在,木质素分子易受紫外和可见光的激发,可用于太阳能电池阳极材料的敏化剂制备[14]㊂同时基于木质素分子的柔性芳香链结构和带电荷的表面基团,木质素分子还可用于离子传导隔膜的制备,从而进一步应用于锂离子电池㊁燃料电池和液流电池中[15-17]㊂典型应用如图1所示㊂由此可见,基于官能团的修饰,极大拓展了木质素分子在储能器件中的应用范围㊂图1㊀木质素分子在储能设备中的应用Fig.1㊀Applicationsofligninmoleculesinenergystoragedevices木质素分子在储能器件中的应用并非对传统储能材料的简单替代,其分子结构和基团的多样性为不同储能装置面临的效率提升瓶颈㊁安全稳定性等诸多问题提供了解决方案㊂通过化学改性㊁修饰,木质素分子能够用于解决储能器件中电化学界面的电荷传输㊁电极膨胀㊁性能退化㊁催化剂脱落等问题;因此,理解木质素分子基团㊁结构与电化学储能器件性能之间的构效关系是推动木质素可再生材料功能化应用的关键所在㊂笔者将从木质素分子的结构和性能出发,讨论木质素分子对超级电容器㊁锂离子电池㊁燃料电池㊁太阳能电池㊁液流电池等主流储能器件电化学性能的提升作用,并介绍其中的代表性应用㊂1㊀木质素分子的官能团特点及化学性质㊀㊀木质素是植物细胞壁的重要组成部分,它作为黏结剂同纤维素和半纤维素构成植物细胞壁骨架,使植物细胞具有一定的机械强度和负重能力㊂植物细胞壁从外到内包括胞间层(ML)㊁初生壁(P)以及次生壁(S)三部分,其中次生壁又分为外层(S1)㊁中层(S2)和内层(S3)㊂一般认为,植物细胞中的木质素大量分布在胞间层(ML),随着深入细胞内部含量减少,在次生壁内2㊀第1期刘伟,等:木质素分子在储能器件中的应用研究进展层又有增加,堆积在次生壁角隅处[18]㊂木质素的结构十分复杂,是由苯基丙烷类结构单元通过碳⁃碳键和醚键连接而成的三维高分子化合物㊂最近20多年已经提出了十几种结构模型,如:针叶材木质素结构模型㊁阔叶材木质素结构模型㊁禾本科植物木质素结构模型等[19]㊂目前并不清楚木质素确切的化学结构,但根据其基本结构单元的不同可将木质素分为3种类型:由紫丁香基丙烷单元形成的紫丁香基木质素(S⁃木质素)㊁由愈创木酚丙烷单元形成的愈创木基木质素(G⁃木质素)以及由对羟基苯基丙烷单元形成的对羟基苯基木质素(H⁃木质素)[20]㊂不同木质素结构模型具有一定的差异,如针叶材木质素主要由愈创木基丙烷单元形成,阔叶材木质素主要由紫丁香基丙烷单元和愈创木基丙烷单元形成的,草类植物木质素则包括上述3种基本结构单元[21]㊂木质素则通过主要结构单元间的缩合键(β⁃O⁃4,α⁃O⁃4,β⁃β)和非缩合键(α⁃5,β⁃1,5⁃5ᶄ)组成庞大分子结构[22]㊂图2展示了木质素的基本结构㊁主要化学基团及其参与的电化学反应㊂图2㊀木质素的典型结构及化学基团参与的电化学反应示意图Fig.2㊀Typicalstructuresofligninandelectrochemicalreactionsinvolvingchemicalgroups1.1㊀木质素的分离方法木质素可以从各种植物组织中分离而来,根据分离原理的不同大致可以概括为物理方法㊁化学方法以及生物方法,不同的分离方法得到的木质素结构㊁官能团保留程度和物化性质均有较大区别㊂物理方法主要是将木质素作为可溶性成分进行溶解,然后与植物中的纤维素等不溶性组分进行分离㊂天然木质素也被称为Brauns木质素㊁可溶性木质素,一般通过物理手段获得,因此保留了天然木质素的基本结构,具有较高的酚羟基含量㊂通过机械研磨后萃取得到的木质素称为磨木木质素(milledwoodlignin),其比较接近天然木质素,通常含有2% 3%的木聚糖类和一些聚酚类的杂质[23]㊂通过有机溶剂,在一定的温度和压力下将木质素溶解出来,称之为有机溶剂木质素(organosolvlignin)㊂常见的萃取有机溶剂包括醇类(甲醇㊁乙醇㊁正丁醇等)㊁酸类(甲酸㊁乙酸等)㊁乙醚㊁丙酮㊁乙酸乙酯㊁苯酚㊁二甲亚砜等[24]㊂其中,乙醇法提取木质素是目前研究最广泛㊁技术最成熟的方法,可以获得纯度较高和相对分子质量较低的乙醇木质素,结构中含有较多的愈创木基和紫丁香基结构以及较多的醇羟基,但酚羟基较少[25]㊂近年来离子液体和低共熔溶剂法也被用于木质素的分离提取㊂通常认为离子液体具有良好的成氢键性质㊁π⁃π相互作用和疏水相互作用可以促进木质素在离子液体中的溶解[26-27]㊂化学法是采用化学试剂处理,通过化学反应得到的木质素㊂与物理分离方法不同,化学法采用的3林业工程学报第9卷试剂与木质素分子发生化学反应,因此处理得到的木质素在结构和表面官能团的种类及数量上与天然木质素具有一定区别㊂工业上木质素的化学分离通常是基于造纸工艺,从产生的碱性黑液中加酸沉淀分离得到木质素,其结构和性质与不同的造纸工艺相关㊂从碱性黑液中分离得到的是硫酸盐木质素(kraftlignin)㊂由于黑液从氢氧化钠和硫化钠的强碱性环境中产生,导致木质素结构中单元侧链α或β位连接的醚键发生部分断裂,因此硫酸盐木质素的相对分子质量相较于其他木质素偏低,同时产生更多的末端含氧基团[28]㊂此外,通过加酸沉淀木质素导致其结构中还含有少量的羧基㊂这种方式得到的硫酸盐木质素呈疏水性,需要对其进行改性以提高其反应性,且其结构中含有脂肪族硫醇基团,导致其具有特殊气味[29]㊂通过酸性亚硫酸盐制浆法可得到木质素磺酸盐(lignosulfonate),亚硫酸盐的使用在木质素的侧链上引入了大量的磺酸基,并且酸性环境导致其具有较高分子量和高灰分含量[30]㊂从烧碱或烧碱/蒽醌制浆过程中分离得到的木质素为碱木素(sodalignin),与硫酸盐木质素相比,碱木素不含硫,因此它比硫酸盐木质素和木质素磺酸盐更类似于天然木质素,更有利于木质素的化学改性㊂生物法主要是通过特定的酶去处理生物质得到木质素㊂酶将纤维素以及半纤维素转换成糖,而木质素作为复杂且稳定的大分子不会与酶发生反应,因此反应结束得到的固体渣称为酶解木质素㊂相比碱木质素,酶解木质素含氮源,且结构接近于原始木质素,并且平均分子量更高,但是其含氧官能团数量偏低的特性在一定程度上限制了其在储能设备中的应用[31]㊂1.2㊀木质素中的官能团木质素中存在醇羟基㊁酚羟基㊁羧基㊁甲氧基以及羰基等官能团,这些官能团在木质素中的分布和含量与植物原材料的种类㊁提取方法等相关[32]㊂正是因为木质素结构中含有丰富的官能团,使得木质素具有多样的化学性质㊂羟基是木质素中重要的官能团,在木质素结构中有酚羟基和醇羟基两种类型㊂酚羟基则分为缩合型和游离型㊂游离的酚羟基在木质素结构中只占一小部分,大部分还是以缩合型的结构存在,即木质素结构单元之间连接的醚键㊂用甲醛等甲基化试剂可以判断木质素结构中羟基的类型,评价木质素的醚化或缩合程度,判断木质素的溶解性能和参加反应的能力[33]㊂木质素的羟基能参与一系列化学改性反应,如交联或络合反应;而木质素的邻苯二酚结构容易失去两个电子形成邻苯醌结构,并形成可逆的互变形式,赋予了木质素电化学储能能力㊂木质素结构中存在一定量的羰基结构,分布在木质素结构的侧链上,主要有共轭羰基和非共轭羰基两种[34]㊂羰基作为含氧极性不饱和基团,很容易与亲核试剂发生加成反应,可以通过与含氧亲核试剂的反应向木质素结构中引入更多的含氧官能团㊂同时,在电化学反应中,能够通过加氢反应,可逆地与一个电子和一个质子结合形成羟基结构,实现电荷存储的功能㊂在原始木质素中是不存在羧基结构的,但是在化学提取过程中木质素会发生氧化反应产生少量的羧基结构㊂例如,通过强碱蒸煮等氧化方式得到的碱木质素由于其侧链发生氧化,会产生较多的羧基[35]㊂羧基这种酸性官能团的引入不仅可以增加木质素的溶解性,还能提高其表面活性,赋予木质素一些化学性质㊂羧基可以在制备多孔碳时充当造孔剂,在储能领域作为亲水基团的羧基可以提高氢离子的传导率㊂同时在电化学反应中,羧基也可以直接接受电子完成电荷存储的反应㊂2㊀木质素分子在储能器件中的应用2.1㊀超级电容器超级电容器是一种新型的储能设备,其电化学性能介于传统电容器和化学电池之间,结构主要由电极㊁集流体㊁电解液以及隔膜组成㊂超级电容器与电池相比具有功率密度高㊁充放电速度快㊁使用寿命长㊁安全无污染等优点,但是其能量密度较低㊁电极成本高㊁自放电速率大等缺点在一定程度上阻碍了其商业化应用㊂电极材料作为超级电容器的核心器件,对电容器的性能有着决定性的作用,探索低成本的电极对超级电容器的发展具有重要意义㊂木质素是一种可再生的碳源,可通过简单碳化的方法制备得到高比表面积的碳材料㊂木质素结构中三维芳香结构也有助于形成多孔碳结构,并且含有S㊁N元素可以制备得到掺杂的碳材料[2],因此常被应用于超级电容器性能提升的研究中㊂木质素结构中存在的大量含氧官能团可以与材料形成良好的结合,提升材料的韧性等,并且丰富的邻苯酚结构能够发生氧化还原反应,因此木质素分子在凝胶㊁膜㊁柔性超级电容器等领域具有很好的研究前景㊂4㊀第1期刘伟,等:木质素分子在储能器件中的应用研究进展2.1.1㊀木质素衍生碳材料木质素作为一种可持续再生的碳源,具有低成本和高储量的优点,通过碳化制备得到的碳材料在超级电容器领域得到了广泛的研究㊂目前的文献报道中,通常采用水热㊁模板法或者直接煅烧等方法,结合化学活化或物理活化等方法,将木质素碳化制备成多孔碳材料(图3a)应用在超级电容器中[2,36]:1)制备高密度硬碳㊂因为储能机理的限制,通常碳材料的质量比容量是比较低的,虽然可以通过构建孔道,提升碳材料的比表面以提高容量,但是同时碳的刚性也会变弱㊂相较于质量比容量,实现高密度体积比容量对于碳材料在实际中的应用更加具有意义㊂Herou等[37]应用木质素衍生的碳纤维作为碳源,在高压力下制备得到了高密度碳电极㊂4MPa下的压缩使碳纳米纤维电极的微米级空隙体积从92%降低到21%,堆积密度提高了6倍㊂2)木质素分子中富含芳香结构和多种官能团,能够作为添加剂与其他材料结合,可以起到调节形貌和元素掺杂的作用㊂Long等[38]报道了一种以ZIF⁃8有机金属框架材料为模板制备的高度石墨木质素衍生碳多孔材料㊂木质素在高温煅烧下发生解聚和重聚反应形成石墨烯结构与ZIF⁃8结合,得到了高度石墨化多孔N㊁O⁃双掺杂碳材料,在10000次循环后,容量保有率高达130%㊂3)制备高比表面积碳基气凝胶材料㊂木质素分子含有大量的含氧基团(如羟基㊁醚键),能够与交联剂高效地结合得到木质素空气凝胶,再经碳化即得到超高比表面积的多孔碳基空气凝胶㊂Beau⁃camp等[10]用聚乙二醇二缩水甘油醚为交联剂并结合冷冻干燥的方法,制备木质素基水凝胶,合成的水凝胶溶胀度高达1600%㊂碳化后得到的碳基空气凝胶仍然保持良好的空隙结构,在对称超级电容器中,1A/g的电流密度下比容量为18.7F/g㊂木质素进行碳化得到碳基材料作为电极,在电容器中发生的储能行为是双电层电化学吸附行为,引入木质素分子中的杂原子则可以产生赝电容以提升存储电荷的能力㊂2.1.2㊀木质素⁃碳基复合电极材料碳基材料以其优良的导电性和机械性能在超级电容器领域得到了广泛的关注,但是提升碳基材料的容量是当前比较关注的问题㊂木质素分子中的苯环能够与石墨烯形成π⁃π键结合,羟基等官能团能够与碳材料表面的官能团结合,并且木质素分子存在邻苯二酚结构,这种结构容易发生可逆的氧化还原反应,同时提升电极材料储存电荷的能力(图3b)㊂与具有良好导电性的碳基材料复合能够弥补木质素导电能力差的问题,同时也能够提升材料的储能性能㊂Zhou等[9]以活性炭为碳源与脱硫木质素(KL)进行复合制备了木质素⁃碳基复合材料㊂经过硝酸处理后的活性炭(TAC)表面产生更多的含氧官能团,能够促进与木质素分子的结合㊂通过简单的超声过程,可得到木质素包覆的活性炭复合材料KL/TAC,表现出比TAC更高的容量,在循环伏安测试中显示出明显的氧化还原峰,这说明木质素发生了氧化还原反应,并且对容量的提升起到了重要作用㊂Liu等[39]以木质素磺酸盐(LS)为添加剂,通过球磨的方式与石墨烯复合㊂随着木质素含量的增加,石墨烯表面越发平滑,这可以归因于木质素分子中的芳香结构能与石墨烯形成共轭结构㊂但是由于LS能够溶解在水中,随着充放电循环的进行,电容器的性能随着LS的溶解也随之降低㊂为此,Ail等[40]探究了不同硫化程度的木质素与碳的复合材料对于性能的影响,研究表明,部分脱硫的木质素(DSLS)比LS和KL具有更加良好的离子传输能力,并且表现出很高的法拉第储能贡献㊂但是DSLS与石墨烯的复合材料的容量很低(<5F/g),也明显低于Liu等[39]采用LS与石墨烯制备材料的电容量(ʈ30F/g),这说明木质素的硫化程度对制备所得材料的性能有很大影响㊂木质素一方面能够提供丰富的氧化还原反应,提高材料性能;另一方面,木质素分子量较大,具有很多的支链,丰富的芳香结构和官能团能够与碳材料形成多种共价键,从而提升材料的力学性能㊂Wang等[41]制备的木质素修饰的石墨烯复合膜,比未经修饰的石墨烯膜具有更强的韧性,木质素分子的存在也能够有效防止石墨烯纳米片的堆积以及保持结构的稳定性㊂Tanguy等[42]以木质素为功能添加剂,与石墨烯聚苯胺结合制备柔性超级电容器的膜电极,表现出比碳纳米纤维具有更好的力学和电容量性能,即使在不同的弯曲角度下,电容器仍然能够表现良好(10000圈循环,保有率70%)㊂木质素分子中含有的苯二酚结构作为主要存储电能的结构(理论比容量约为308F/g)[43],提高邻苯二酚含量是提升容量的关键㊂木质素结构中甲氧基含量高㊂Sun等[44]选用HBr/LiBr将木质素(AL)的甲氧基选择性地转化为羟基,获得处理的木质素(DAL),其中酚羟基的含量比未经处理的高出87%,与氧化石墨烯(rGO)的复合材料比容量5林业工程学报第9卷(414.5F/g)相比,未处理的AL/rGO容量高出接近一倍㊂Yang等[45]将木质素进行裂解得到芳香化合物,再聚合后材料中酚羟基的含量比原始木质素高出6倍㊂在1A/g的电流密度下,酚羟基聚合物/石墨烯复合材料的比容量是纯石墨烯的5倍,是木质素石墨烯复合材料的2倍(图3c)㊂此外,Yang等[46]还将低价值芳香嵌段共聚物在甲醇的作用下再次聚合,与石墨烯复合得到的材料比木质素石墨烯复合材料具有更佳的电化学性能㊂a)木质素衍生的N掺杂多孔碳[36];b)木质素⁃碳复合材料[40];c)木质素解聚⁃再聚合得到的高醌基含量聚合物[45];d)碳纤维基底聚苯胺⁃木质素复合材料[51]㊂图3㊀木质素在超级电容器中的应用Fig.3㊀Applicationsofligninmoleculesinsupercapacitors2.1.3㊀木质素⁃导电高分子复合材料木质素分子具有丰富的官能团,能与其他高分子发生广泛的相互作用㊂木质素与导电高分子[如聚苯胺(PAN),聚二氧乙基噻吩(PEDOT)等]进行复合[47],一方面导电高分子提供良好的电导率,另一方面木质素能够提供赝电容,并且能够提升材料的稳定性㊂导电高分子通过灵活调节聚合度㊁添加电活性官能团等手段可以对性能进行调控,但是实际过程中高分子材料与电解液接触的有效表面积较低,导致电容量相对较低㊂通过与小型的分子(磺酸盐)复合能够改善导电聚合物的性能,但是磺酸盐等会随着循环充放电从材料中析出,材料稳定性较弱㊂磺化木质素磺酸钠中含有大量的磺酸基团,并且木质素分子量很大,能够与导电高分子组合紧密,有效地解决小型阴离子从高分子材料中析出的问题,提高材料的稳定性㊂木材作为木质素最直接的来源,直接将原生木材与导电高分子复合能够大大降低电极成本㊂Gabriella等[48]报道了一种低成本的新型树皮/PDOET复合电极,原生树皮通过水热进行磺化,以此提升与PDOET之间的静电相互作用㊂Tran等[49]采用磺化松树木片/聚吡咯复合材料,在电流密度为8.0mA/cm2时,该复合材料达到了186S/m的高电导率㊂直接采用原生木材在一定程度上能够降低生产成本,但木材中残留了纤维素等不能提供容量的物质,这造成了大量的死体积㊂Li等[50]采用原位复合的方法制备了聚苯胺/木质素复合电极材料,复合电极表现出良好的电子传导能力和优异的电容性能㊂在电流密度为1A/g时,比电容可达到553.7F/g,并且表现出良好的倍率性能和循环稳定性(电流密度10A/g,5000次循环,容量保有率68.01%)㊂Dianat等[51]制备了一种木质素磺酸盐修饰的聚苯胺纳米纤维/碳纤维织物复合电极(图3d),其中LS与聚苯胺能够通过磺酸基团与聚苯胺中的胺正离子形成稳定结构㊂在大电流密度100A/g的充放电条件下比容量仍达到489F/g,木质素显著提高了倍率性能,得到的复合电极表现出极佳的循环性能(10A/g,15000次)㊂6。
端羟基聚二甲基硅氧烷英文字母
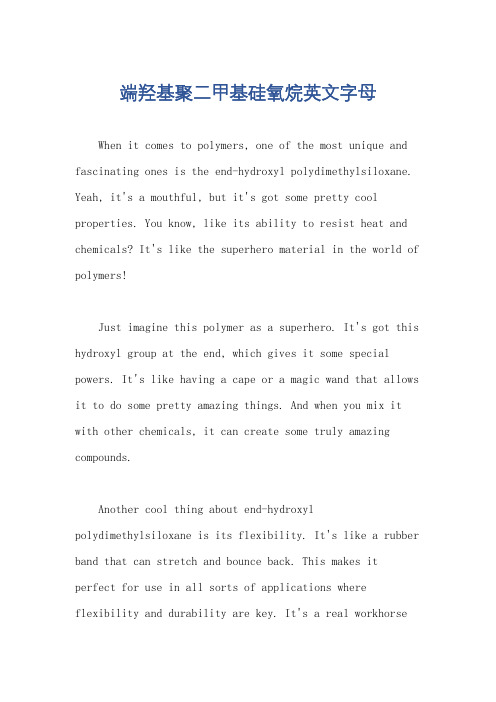
端羟基聚二甲基硅氧烷英文字母When it comes to polymers, one of the most unique and fascinating ones is the end-hydroxyl polydimethylsiloxane. Yeah, it's a mouthful, but it's got some pretty cool properties. You know, like its ability to resist heat and chemicals? It's like the superhero material in the world of polymers!Just imagine this polymer as a superhero. It's got this hydroxyl group at the end, which gives it some special powers. It's like having a cape or a magic wand that allows it to do some pretty amazing things. And when you mix it with other chemicals, it can create some truly amazing compounds.Another cool thing about end-hydroxyl polydimethylsiloxane is its flexibility. It's like a rubber band that can stretch and bounce back. This makes itperfect for use in all sorts of applications whereflexibility and durability are key. It's a real workhorseof a polymer!Oh, and did you know that it's also found in a lot of personal care products? Yeah, that's right! Its unique properties make it a great ingredient in things like hair conditioners and skin lotions. It helps to make them smoother and easier to apply. So, not only is it a superhero in the lab, but it's also a beauty booster in your bathroom cabinet!So, there you have it! End-hydroxyl polydimethylsiloxane is a pretty amazing polymer with a lot of cool uses. Whether you're a scientist or just.。
butyl(丁基橡胶)-石墨烯纳米复合材料
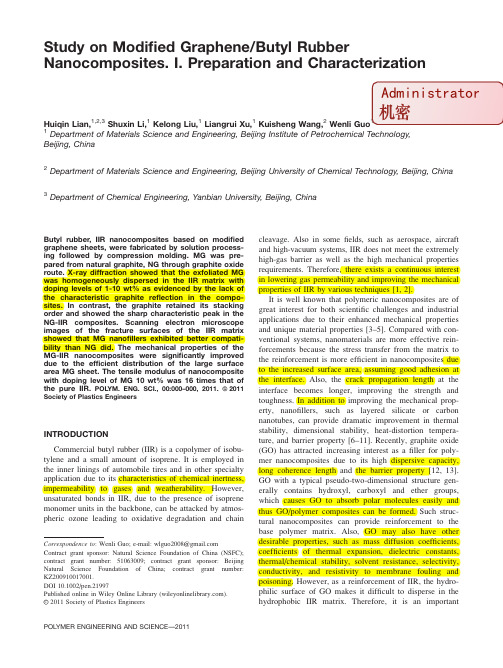
Study on Modified Graphene/Butyl Rubber Nanocomposites.I.Preparation and CharacterizationHuiqin Lian,1,2,3Shuxin Li,1Kelong Liu,1Liangrui Xu,1Kuisheng Wang,2Wenli Guo11Department of Materials Science and Engineering,Beijing Institute of Petrochemical Technology,Beijing,China2Department of Materials Science and Engineering,Beijing University of Chemical Technology,Beijing,China 3Department of Chemical Engineering,Yanbian University,Beijing,ChinaButyl rubber,IIR nanocomposites based on modified graphene sheets,were fabricated by solution process-ing followed by compression molding.MG was pre-pared from natural graphite,NG through graphite oxide route.X-ray diffraction showed that the exfoliated MG was homogeneously dispersed in the IIR matrix with doping levels of1-10wt%as evidenced by the lack of the characteristic graphite reflection in the compo-sites.In contrast,the graphite retained its stacking order and showed the sharp characteristic peak in the NG-IIR composites.Scanning electron microscope images of the fracture surfaces of the IIR matrix showed that MG nanofillers exhibited better compati-bility than NG did.The mechanical properties of the MG-IIR nanocomposites were significantly improved due to the efficient distribution of the large surface area MG sheet.The tensile modulus of nanocomposite with doping level of MG10wt%was16times that of the pure IIR.POLYM.ENG.SCI.,00:000–000,2011.ª2011 Society of Plastics EngineersINTRODUCTIONCommercial butyl rubber(IIR)is a copolymer of isobu-tylene and a small amount of isoprene.It is employed in the inner linings of automobile tires and in other specialty application due to its characteristics of chemical inertness, impermeability to gases and weatherability.However, unsaturated bonds in IIR,due to the presence of isoprene monomer units in the backbone,can be attacked by atmos-pheric ozone leading to oxidative degradation and chain cleavage.Also in somefields,such as aerospace,aircraft and high-vacuum systems,IIR does not meet the extremely high-gas barrier as well as the high mechanical properties requirements.Therefore,there exists a continuous interest in lowering gas permeability and improving the mechanical properties of IIR by various techniques[1,2].It is well known that polymeric nanocomposites are of great interest for both scientific challenges and industrial applications due to their enhanced mechanical properties and unique material properties[3–5].Compared with con-ventional systems,nanomaterials are more effective rein-forcements because the stress transfer from the matrix to the reinforcement is more efficient in nanocomposites due to the increased surface area,assuming good adhesion at the interface.Also,the crack propagation length at the interface becomes longer,improving the strength and toughness.In addition to improving the mechanical prop-erty,nanofillers,such as layered silicate or carbon nanotubes,can provide dramatic improvement in thermal stability,dimensional stability,heat-distortion tempera-ture,and barrier property[6–11].Recently,graphite oxide (GO)has attracted increasing interest as afiller for poly-mer nanocomposites due to its high dispersive capacity, long coherence length and the barrier property[12,13]. GO with a typical pseudo-two-dimensional structure gen-erally contains hydroxyl,carboxyl and ether groups, which causes GO to absorb polar molecules easily and thus GO/polymer composites can be formed.Such struc-tural nanocomposites can provide reinforcement to the base polymer matrix.Also,GO may also have other desirable properties,such as mass diffusion coefficients, coefficients of thermal expansion,dielectric constants, thermal/chemical stability,solvent resistance,selectivity, conductivity,and resistivity to membrane fouling and poisoning.However,as a reinforcement of IIR,the hydro-philic surface of GO makes it difficult to disperse in the hydrophobic IIR matrix.Therefore,it is an importantCorrespondence to:Wenli Guo;e-mail:wlguo2008@Contract grant sponsor:Natural Science Foundation of China(NSFC);contract grant number:51063009;contract grant sponsor:BeijingNatural Science Foundation of China;contract grant number:KZ200910017001.DOI10.1002/pen.21997Published online in Wiley Online Library().V C2011Society of Plastics EngineersPOLYMER ENGINEERING AND SCIENCE—-2011Administratorissue to improve the compatibility of the GO sheet with the IIR matrix.Moreover,methods used to prepare polymeric nano-composites include in-situ polymerization [14],solution mixing [15],melting compound [16],and cocoagulating of polymeric composite solution [17].Considering the manufacture process of the IIR,slurry and solution pro-cess,the solution mixing is promising to fabricate IIR hybrids in the IIR industry.In this study,we report for the first time the fabrication of well-dispersed modified graphene in IIR composites through solution process.The MG nanosheets are homo-geneously dispersed in the IIR matrix with doping level of 1–10wt%.Compared with the pure IIR,the resulting nanocomposite membranes exhibit dramatic enhancement of mechanical properties.To the best of our knowledge,this is the first report of totally exfoliated graphite to reinforce IIR with outstanding mechanical property.The properties of vulcanization plateau,gas barrier,cure capa-bility,and rubber damping are under study and the results will be published in the near future.EXPERIMENTAL PROCEDURES MaterialsNatural graphite flakes with a partical size of 30l m were purchased from Aladdin Reagent Company (China).Cetyltrimethylammonium bromide (CTAB)was bought from Fuchen Chemical Reagents(Tianjin,China).Butyl rubber (IIR 1751)was obtained from YanShan Petrochem-ical Company of China.The other reagents (NaOH,NaNO 3,and KMnO 4)of analytical grade and 98%H 2SO 4,30%H 2O 2were purchased from Sinopharm Chemical Reagent Co.Ltd.(China)and were used as received with-out further purification.Ultrapure water with resistivity of 18M O was produced by a Milli-Q(Millipore,USA)and was used for solution preparation.Preparation of MG/NG-IIR Composite SheetsThe procedure used to prepare the MG-IIR nano-composite sheets was shown in Fig. 1.First,based on Hummers’method [18],the graphite was oxidized by con-centrated sulfuric acid to create polar hydrophilic groups (ÀÀCOOH,C ¼¼O,ÀÀOH)on the surface.The GO was dispersed in cetyltrimethylammonium bromide solution (20wt%)and ultrasonicated for 0.5h,followed by me-chanical stirring at 258C for 24h.During this process,the tertiary amine reacted with the carboxylic groups on the oxidized surface via an acid-base reaction or via hydrogen bonding between the surface ÀÀOH or C ¼¼O group and the amine groups.The suspension was filtrated and washed three times with water,dried at 408C in a vacuum for 24h.The resulting MG was added into the 15wt%solution of IIR in hexane by sonication for 0.5h to form a colloidal suspension.Then the mixture was stirred for 6h at 258C.The amounts of MG/NG added were 0,1,3,5,10wt%ofthe mass of rubber.The composite solution was then coa-gulated by adding methanol and the precipitated nanocom-posite was dried in a vacuum.Finally,sheet samples were prepared by vacuum compression molding using a 2mm thick spacer at 1008C under 10MPa for ing this procedure,the NG-IIR composite sheets were prepared.CHARACTERIZATION AND MEASUREMENTS The as-made membrane was characterized by X-ray diffraction (XRD,Scintag PAD X diffractometer,Cu K a source,operated at 45kV and 40mA).The samples were scanned with 58/min between 2y of 28–308.SEM observation was performed using Tecnai T12,at an acceleration voltage of 15kV with gold -posite samples were imaged by first fracturing in liquid nitrogen.TGA was performed using a TA Instrument Q500attached to an automatic programmer from ambient tem-perature to 5008C at a heating rate of 108C/min in a nitro-gen atmosphere.A TA instrument Q1000was used to record the DSC traces at a heating rate of 108C/min.Measurements of mechanical properties were con-ducted at 25628C according to relevant ISO standard (ISO 37).Tensile tests were measured on an Autograph AGS-J SHIMADZU universal testing machine at a cross-head speed of 500mm/min.The reported values were the average of five measurements.RESULTS AND DISCUSSIONThe FTIR spectra of NG,GO,and MG were shown in Fig.2.The FT-IR spectrum of NG showed no significant features.While that of GO showed quite differentFIG.1.Schematic representation for the fabrication of MG-IIR nano-composite membrane.2POLYMER ENGINEERING AND SCIENCE—-2011DOI 10.1002/pencharacter by the presence of new bands.The broad bandat3405cm21could be assigned to stretching of the ÀÀOH groups on the GO surface.The bands at1720and 1070cm21were associated with stretching of the C¼¼Oand CÀÀO stretching vibrations of carboxylic groupsrespectively.The FTIR spectrum of MG confirmed theeffective functionalization of graphene.The double bandsat2849and2919cm21were antisymmetric and symmet-ric CÀÀH stretching vibrations of theÀÀCH2ÀÀgroups from surfactant molecules[19]respectively.The bands at 1463and1127cm21were corresponding to CÀÀH bend-ing and the C-N stretching vibration respectively.The spectrum also showed a C¼¼C peak at1574cm21corre-sponding to the skeletal vibration of graphene sheets[20]. These spectral features showed that MG was successfully synthesized.The XRD patterns of the NG,GO,MG were shown inFig.3.The sharp diffraction peak around26.5o for pris-tine graphite(Fig.3a)showed that the basal spacing was0.34nm.Because of the strong Van der Waals force andstatic electric force between the sheets of graphite,thesheet was difficult to disperse.Thus a relatively strongoxidative acid was used to oxidize the graphite creatingpolar groups on the surface of graphite sheet.The surfac-tant of cetyltrimethyl ammonium bromide was used to functionalize the oxidized graphite through acid-base reaction to obtain stable exfoliated graphene sheets.As shown in Fig.3a,the GO showed two diffraction peaks at 2y of9.7o and25.3o,corresponding to a d-spacing of0.91 and0.35nm,respectively,and indicated that the GO was not fully oxidized and the additional peak at25.3o was that of unoxidized graphite.From Fig.3b,MG showed no characteristic peak indicating that the modified graphene sheet had been exfoliated completely.The XRD patterns of MG/NG-IIR nanocomposites membranes with different doping levels were presented in Fig.4.As shown in Fig.4a,the broad peak of2y around 15o appeared in IIR and NG-IIR membranes,due to the amorphous phase of IIR.Toki et al.[21]reported that the amorphous peak of IIR changed during uniaxial deforma-tion.In this case,with NG loading increase,the broad peak shifted slightly,from2y of14.7o in IIR to14.4o in 10wt%NG-IIR composite.It was deduced that NG did not influence the crystallization behavior of IIR very much.From Fig.4a,the diffraction peak at2y around 26.5o appeared in NG and NG-IIR composites because the NG retained its stacking order in the composite.XRD diffraction curves of MG-IR nanocomposites were shown in Fig.4b.The diffraction ascribed to graphite or oxidized graphite did not appear in all of the XRD patterns of composites,indicating the complete exfoliation of the MG in the IIR matrix.SEM images of the fractured surfaces of the as-made MG-IIR and NG-IIR composites were shown in Fig.5. SEM images of NG-IIR composites showed a smooth to-pography with the NG remained its stacking order in the IIR matrix(Fig.5a and b).In contrast,the MG-IIR com-posites appeared a rough surface and the MG dispersed in IIR matrix homogenously(Fig.5c and d).This is likely due to the organic modifier on the surface of MG produc-ing good compatibility with IIR matrix.These results were coincident with the XRD test.TGA under a nitrogen atmosphere was performed on NG,MG,IIR and MG-IIR composites to obtain the struc-ture of MG and composites,as well as to determine the effects of the MG on the thermal stability of the compo-sites.The resulting curves were shown in Fig.6.From FIG.2.FT-IR spectra of NG,GO andMG.FIG.3.The XRD patterns of(a)NG,GO and(b)MG.The curves are shifted vertically for clarity.DOI10.1002/pen POLYMER ENGINEERING AND SCIENCE—-20113FIG.4.The XRD patterns of composites(a)NG-IIR and(b)MG-IIR.The curves are shifted vertically forclarity.FIG.5.SEM images of fracture surface of(a,b)NG-IIR nanocomposites and(c,d)MG-IIR nanocompo-sites.4POLYMER ENGINEERING AND SCIENCE—-2011DOI10.1002/penNG curve of Fig.6a,graphite maintained its weight under the test condition.The curve of MG indicated that MG was composed of 17wt%graphene and 83wt%organicmodifiers.The functional surface contributed to the dis-persion of MG in the IIR solution as well as to the com-patibility with the IIR matrix in the composite membrane.Figure 6b indicated that the IIR began to decompose at 2698C and degraded completely at 4158C.In the case of MG/IIR composites,the weight loss below 3008C was attributed to the decomposition of the small organic molecules on the surface of graphene.Table 1listed the temperature at 5wt%loss of the TGA curve of IIR and MG-IIR composites.The pure IIR lost 5wt%at 3248C and the value was the highest of all the curvesobtained.FIG.6.(a)TG curves of NG and MG;(b)TG curves of MG-IIR nano-composites and (c)DTG curves of MG-IIR nanocomposites.TABLE 1.Thermal propertiesofpureIIRandMG-IIRnanocomposites.IIR 1%MG-IIR 3%MG-IIR 5%MG-IIR 10%MG-IIRT 5wt%(8C)a 324297321256236T mrv (8C)b 372368375378383a Temperature at 5wt%loss.bTemperature at the maximum reactivevelocity.FIG.7.DSC curves of MG-IIRnanocomposites.FIG.8.Tensile stress-strain curve of (a)MG-IIR nanocomposites and (b)NG-IIR nanocomposites.DOI 10.1002/pen POLYMER ENGINEERING AND SCIENCE—-20115The temperature at5wt%loss decreased with the increas-ing MG content when the MG contents were3,5,and10wt%in composites respectively.This might be due to theamount of small molecule of organic modifier increasedwith the increasing MG content.Thefirst derivative of the TGA curve(DTA curvesshown in Fig.6c showed the variation in weight withtime(dW/dT)as a function of temperature.The DTApeaks indicated the temperature of the maximum reactivevelocity.Table1listed the temperature at the maximumreactive velocity of the DTA curve of IIR and MG-IIRcomposites.Pure rubber reached the maximum reactivevelocity at3728C.The value of1wt%MG-IIR nanocom-posite was3688C and it was lower than that of IIR.Thismight be that the amount of graphene was too low toinfluence the thermal stability of the composite,whilesmall organic molecules on the surface of graphene withlow decomposition temperature induced the thermaldecomposition.For all other composites,the temperatureat the maximum reactive velocity increased with increas-ing graphene content,and for the10wt%composite itwas increased by118C compared with pure IIR.Thisindicated that the thermal stability of IIR was improvedby the addition of graphene.A significant number ofpapers had reported increased thermal stability of variouspolymers using graphene asfiller[15,22,23].T.Kuilaet al.reported that the better thermal stability of gra-phene/polyethylene composite system was due to the highaspect ratio of the monodispersed graphene layers whichacted as a barrier and inhibited the emission of small gas-eous molecules[23].DSC for the MG/IIR nanocomposites was shown inFig.7.The glass transition(T g)temperature of IIR wasobserved at270.58C,and the MG loading increased,theT g values of composites which were269.28C,268.68C, 268.98C,and269.18C with the loading levels of1,3,5, 10wt%,respectively.All the composites showed aslightly higher T g than that of pure IIR;among them thehighest one was268.68C of3wt%MG-IIR nanocompo-site.It indicated that the effective exfoliation of the MGincreased the T g due to the interaction between MG andpared with the results of graphene/polystyrenenanocomposite[24],the incorporation of PS nanoparticleson graphene sheets resulted in an increase in T g by178C,while the exfoliated MG did not influence the T g of MG-IIR nanocomposite very much.Therefore,the properties of nano-filler influenced the phase behavior of polymer matrix.The interaction between MG and IIR is under further study.The typical stress–strain curves for the MG-IIR and NG-IIR compositesfilms were presented in Fig.8.The mechanical performance of MG/IIR and NG/IIR compos-itefilms was significantly increased compared with pure IIRfilm(Fig.8a and b).The effect of MG content on mechanical properties of the nanocomposites was shown in Table 2.Stresses at 100%,200,and300%elongation of composites increased along with the MG loading increase.Therefore,in this study,MG-IIR nanocomposites had higher mechanical properties than that of pure IIR.On the basis of these stress–strain curves of tensile tests(Fig.8a and b),Young’s moduli were taken as the linear regression of the initial linear part of stress–strain curves.Figure9a showed the representative calculated Young’s moduli of IIR,NG-IIR,and MG-IIR.The corre-sponding Young’s modulus values were shown in Fig.9b. The addition of MG grapheneflakes significantly increased the Young’s modulus.Remarkably,the Young’s modulus of10wt%MG-IIR was16times that of pure IIR.In comparison,the10wt%NG-IIR compositesTABLE 2.Mechanical properties of pure IIR and MG-IIR nanocomposites.Stress at 100%(MPa)Stress at200%(MPa)Stress at300%(MPa)IIR0.170.190.181%MG-IIR0.250.230.183%MG-IIR0.440.380.295%MG-IIR0.540.430.3110%MG-IIR0.770.590.40FIG.9.(a)Representative calculated Young’s moduli of IIR,NG-IIR,and MG-IIR based on the slope of the elastic region.(b)Dependence ofYoung’s modulus on loading offillers in MG-IIR and NG-IIR nanocom-posites.6POLYMER ENGINEERING AND SCIENCE—-2011DOI10.1002/penimproved3.5times only,as shown in Fig.9b.It might be that the NG stacks did not exfoliate or intercalate in the IIR matrix.This result coincided with the results of the XRD and SEM analysis.Therefore,from the result of mechanical properties,it was deduced that the modifier on the surface of the gra-phene sheet not only caused the sheet to disperse in the IIR matrix,but also bonded to the large rubber chain in two dimensions,which gave the nanocomposite better tensile performance.According to the reference[25],gra-phene layers in poly(vinyl chloride)matrix enhanced the mechanical properties of PVC,because of the strong interfacial adhesion.Therefore,in our case,MG-IIR nano-composites had higher mechanical properties than the pure IIR,which may be due to the homogenous distribu-tion of exfoliated MG and the good compatibility with polymer matrix.CONCLUSIONMG-IIR nanocomposites were prepared by solution processing.SEM and XRD analysis indicated that the exfoliated MG was homogeneously disperse in the IIR matrix.The addition of MG greatly improved the mechan-ical property of the nanocomposites.The nanocomposites with10wt%MG showed the highest Young’s modulus, 3.4MPa,which was about16times higher than that of pure IIR,0.21MPa.REFERENCES1.S.Takahashi,H.A.Goldberg,C.A.Feeney,D.P.Karim,M.Farrell,K.O’Leary,and R.Paul,Polymer,47,3083 (2006).2.Y.Liang,W.Cao,Z.Li,Y.Wang,Y.Wu,and L.Zhang,Polym.Test.,27,270(2008).3.N.A.Kotov,Nature,442,254(2006).4.M.A.Pulickel and M.T.James,Nature,447,1066(2007).5.E.P.Giannelis,Adv.Mater.,8,29(1996).6.Camenzinda,W.R.Caserib,and S.E.Pratsinis,Nano Today,5,48(2010).7.S.C.Tjong,Mater.Sci.Eng.,R53,73(2006).8.Suresha,B.N.Ravi Kumar,M.Venkataramareddy,and T.Jayaraju,Mater.Des.,31,1993(2010).9.H.Kim and C.W.Macosko,Polymer,50,3797(2009).10.Y.Liang,Y.Wang,Y.Wu,Y.Lu,H.Zhang,and L.Zhang,Polym.Test.,24,12(2005).11.E.Burgaz,H.Lian,R.H.Alonso,L.Estevez,and E.P.Gian-nelis,Polymer,50,2348(2009).12.Y.Lian,Y.Liu,T.Jiang,J.Shu,H.Lian,and M.Cao,J.Phys.Chem.C,114,21(2010).13.K.Kalaitzidou,H.Fukushima,and L.T.Drzal,Compos.Sci.Technol.,67,2045(2007).14.J.M.Herrera-Alonso,Z.Sedlakova,and E.Marand,J.Membr.Sci.,349,251(2010).15.S.Ansari and E.P.Giannelis,J.Polym.Sci.Part B:Polym.Phys.,47,888(2009).uki, A.Tukigase,and M.Kato,Polymer,43,2185(2002).17.L.Q.Zhang,Y.Z.Wang,Y.Q.Wang,Y.Sui,and D.S.Yu,J.Appl.Polym.Sci.,78,1873(2000).18.W.S.Hummers and R.E.Offeman,J.Am.Chem.Soc.,80,1339(1958).19.P.J.Thistlethwaite and M.S.Hook,Langmuir,16,4993(2000).20.T.Szabo,O.Berkesi,and I.Dekany,Carbon,43,3186(2005).21.S.Toki,I.Sics,B.S.Hsiao,S.Murakami,M.Tosaka,S.Poompradub,S.Kohjiya,and Y.Ikeda,J.Polym.Sci.Part B:Polym.Phys.,42,956(2004).22.Q.L.Bao,H.Zhang,J.X.Yang,S.Wang,D.Y.Tong,R.Jose,S.Ramakrishna,C.T.Lim,and K.P.Loh,Adv.Funct.Mater.,20,1(2010).23.T.Kuila,S.Bose,C.E.Hong,M.E.Uddin,P.Khanra,N.H.Kim,and J.H.Lee,Carbon,49,1033(2011).24.A.S.Patole,S.P.Patole,H.Kang,J.Yoo,T.Kim,and J.Ahn,J.Colloid Interface Sci.,350,530(2010).25.S.Vadukumpully,J.Paul,N.Mahanta,and S.Valiyaveettil,Carbon,49,198(2011).DOI10.1002/pen POLYMER ENGINEERING AND SCIENCE—-20117。
4-羟基-3,5-二甲氧基肉桂酸英文
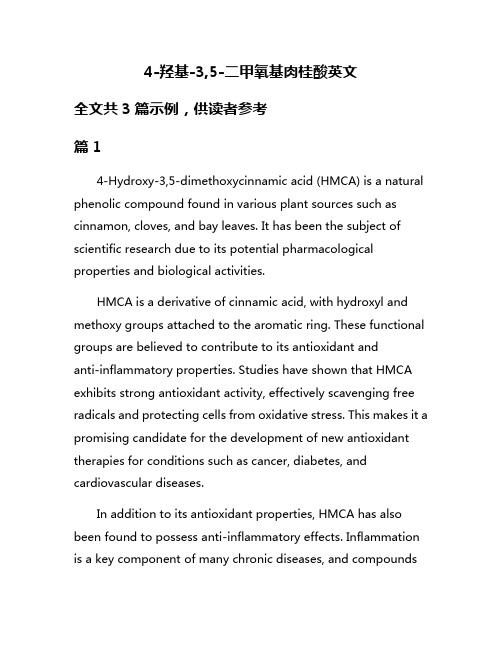
4-羟基-3,5-二甲氧基肉桂酸英文全文共3篇示例,供读者参考篇14-Hydroxy-3,5-dimethoxycinnamic acid (HMCA) is a natural phenolic compound found in various plant sources such as cinnamon, cloves, and bay leaves. It has been the subject of scientific research due to its potential pharmacological properties and biological activities.HMCA is a derivative of cinnamic acid, with hydroxyl and methoxy groups attached to the aromatic ring. These functional groups are believed to contribute to its antioxidant andanti-inflammatory properties. Studies have shown that HMCA exhibits strong antioxidant activity, effectively scavenging free radicals and protecting cells from oxidative stress. This makes it a promising candidate for the development of new antioxidant therapies for conditions such as cancer, diabetes, and cardiovascular diseases.In addition to its antioxidant properties, HMCA has also been found to possess anti-inflammatory effects. Inflammation is a key component of many chronic diseases, and compoundslike HMCA that can modulate inflammatory pathways may have therapeutic potential. Research has shown that HMCA can inhibit the production of pro-inflammatory cytokines and enzymes, reducing inflammation in various experimental models.Furthermore, HMCA has been studied for its potential anticancer properties. In vitro studies have demonstrated that HMCA can inhibit the growth and proliferation of cancer cells, as well as induce apoptosis or programmed cell death. These findings suggest that HMCA may have potential as an anticancer agent, either alone or in combination with other chemotherapeutic drugs.Overall, the research on 4-Hydroxy-3,5-dimethoxycinnamic acid is still in its early stages, and more studies are needed to fully understand its pharmacological properties and potential therapeutic applications. However, the preliminary data is promising, and HMCA may represent a novel natural compound with diverse biological activities that could benefit human health. Further research and clinical trials are necessary to explore the full potential of HMCA as a therapeutic agent.篇2Title: 4-Hydroxy-3,5-dimethoxy cinnamic acid: A reviewIntroduction4-Hydroxy-3,5-dimethoxy cinnamic acid, also known as ferulic acid, is a natural compound found in various plants. It is a type of phenolic acid that has been studied for its potential health benefits and therapeutic properties. In this review, we will explore the chemical structure, sources, bioavailability, pharmacological activities, and potential applications of4-hydroxy-3,5-dimethoxy cinnamic acid.Chemical structure4-Hydroxy-3,5-dimethoxy cinnamic acid is a derivative of cinnamic acid with two methoxy groups at the 3 and 5 positions. It has a molecular formula of C10H10O4 and a molecular weight of 194.18 g/mol. The compound has a white crystalline appearance and is slightly soluble in water. The chemical structure of 4-hydroxy-3,5-dimethoxy cinnamic acid gives it unique properties that contribute to its biological activities.Sources4-Hydroxy-3,5-dimethoxy cinnamic acid is naturally found in various plants, including fruits, vegetables, grains, and herbs. Some of the common dietary sources of ferulic acid include oats, rice bran, wheat germ, and coffee beans. The compound is alsopresent in significant amounts in fruits such as apples, oranges, and pineapples. In addition to dietary sources,4-hydroxy-3,5-dimethoxy cinnamic acid can be synthesized in the laboratory for research purposes.BioavailabilityThe bioavailability of 4-hydroxy-3,5-dimethoxy cinnamic acid refers to the extent and rate at which the compound is absorbed, metabolized, and distributed in the body. Studies have shown that ferulic acid can be absorbed in the gastrointestinal tract and reach systemic circulation. However, the bioavailability of the compound can be influenced by factors such as formulation, dosage, and interactions with other compounds. Further research is needed to optimize the bioavailability of4-hydroxy-3,5-dimethoxy cinnamic acid for therapeutic applications.Pharmacological activities4-Hydroxy-3,5-dimethoxy cinnamic acid has been studied for its various pharmacological activities, including antioxidant, anti-inflammatory, anti-cancer, neuroprotective, andcardio-protective effects. The compound acts as a potent antioxidant by scavenging free radicals and reducing oxidative stress in cells and tissues. In addition, 4-hydroxy-3,5-dimethoxycinnamic acid has anti-inflammatory properties that can help alleviate inflammation and pain in conditions such as arthritis and asthma.Furthermore, ferulic acid has shown promising anti-cancer effects by inhibiting tumor growth, inducing apoptosis, and preventing metastasis in various cancer cell lines. The compound also exhibits neuroprotective properties by protecting neurons from oxidative damage and promoting nerve cell regeneration. Additionally, 4-hydroxy-3,5-dimethoxy cinnamic acid has been shown to have cardio-protective effects by improving heart function, reducing cholesterol levels, and preventing atherosclerosis.Potential applicationsDue to its diverse pharmacological activities,4-hydroxy-3,5-dimethoxy cinnamic acid has potential applications in the fields of medicine, pharmacy, and cosmetology. The compound can be utilized in the development of novel drugs for the treatment of oxidative stress-related diseases, inflammatory disorders, cancer, neurodegenerative disorders, and cardiovascular diseases. In addition,4-hydroxy-3,5-dimethoxy cinnamic acid can be incorporatedinto skincare products for its antioxidant and anti-aging properties.ConclusionIn conclusion, 4-hydroxy-3,5-dimethoxy cinnamic acid is a natural compound with a wide range of pharmacological activities and potential applications. Further research is needed to explore the mechanisms of action, synergistic effects, and safety profile of ferulic acid for clinical use. The compound shows promise as a therapeutic agent for various health conditions and may lead to the development of new treatments in the future.篇34-Hydroxy-3,5-dimethoxy cinnamic acid (HDCA) is a natural compound found in various plants such as cinnamon, nutmeg, and cloves. It belongs to the class of cinnamic acids and is known for its antioxidant and anti-inflammatory properties. In this article, we will explore the various aspects of HDCA, including its chemical structure, biological activities, and potential therapeutic applications.Chemical Structure:HDCA is a phenolic compound with a molecular formula of C12H14O5 and a molecular weight of 238.24 g/mol. It is derivedfrom cinnamic acid by the addition of hydroxyl and methoxy groups at the 4 and 3,5 positions, respectively. The structure of HDCA consists of a central benzene ring with a carboxyl group at one end and hydroxyl and methoxy groups at the other end.Biological Activities:HDCA has been shown to possess a range of biological activities, making it a promising candidate for therapeutic purposes. One of the key properties of HDCA is its antioxidant activity, which helps to scavenge free radicals and protect cells from oxidative damage. In addition, HDCA has been found to exhibit anti-inflammatory effects by inhibiting the production of pro-inflammatory cytokines and enzymes.Therapeutic Applications:Due to its antioxidant and anti-inflammatory properties, HDCA has shown promise in the treatment of various diseases and conditions. Some potential therapeutic applications of HDCA include:1. Neurodegenerative Diseases: HDCA has been studied for its potential neuroprotective effects in neurodegenerative diseases such as Alzheimer's and Parkinson's disease. Itsantioxidant properties may help to protect neurons from oxidative stress and improve cognitive function.2. Cardiovascular Diseases: HDCA has been shown to have beneficial effects on cardiovascular health by reducing inflammation and oxidative stress in the blood vessels. This may help to improve blood flow and reduce the risk of cardiovascular diseases such as atherosclerosis.3. Cancer: HDCA has also been studied for its anticancer properties, with research indicating that it may inhibit the growth and spread of cancer cells. Its antioxidant and anti-inflammatory effects may help to reduce the risk of cancer development and progression.4. Skin Health: HDCA has potential applications in skincare due to its antioxidant properties, which can help to protect the skin from environmental damage and aging. It may also have anti-inflammatory effects that could be beneficial for conditions such as acne and eczema.Overall, 4-Hydroxy-3,5-dimethoxy cinnamic acid (HDCA) is a natural compound with promising therapeutic potential. Further research is needed to fully understand its mechanisms of action and explore its possible applications in the treatment of various diseases. However, the current evidence suggests that HDCAcould be a valuable addition to the arsenal of natural compounds with health-promoting properties.。
- 1、下载文档前请自行甄别文档内容的完整性,平台不提供额外的编辑、内容补充、找答案等附加服务。
- 2、"仅部分预览"的文档,不可在线预览部分如存在完整性等问题,可反馈申请退款(可完整预览的文档不适用该条件!)。
- 3、如文档侵犯您的权益,请联系客服反馈,我们会尽快为您处理(人工客服工作时间:9:00-18:30)。
This article appeared in a journal published by Elsevier.The attached copy is furnished to the author for internal non-commercial research and education use,including for instruction at the authors institutionand sharing with colleagues.Other uses,including reproduction and distribution,or selling or licensing copies,or posting to personal,institutional or third partywebsites are prohibited.In most cases authors are permitted to post their version of thearticle(e.g.in Word or Tex form)to their personal website orinstitutional repository.Authors requiring further informationregarding Elsevier’s archiving and manuscript policies areencouraged to visit:/copyrightFabrication of hydroxyl group modified monodispersed hybrid silica particles and the h-SiO 2/TiO 2core/shell microspheres as high performance photocatalyst for dye degradationZhe-Ying Shen a ,Long-Yu Li a ,Yat Li b ,Chang-Chun Wang a ,⇑aKey Laboratory of Molecular Engineering of Polymers (Minister of Education),Department of Macromolecular Science and Laboratory of Advanced Materials,Fudan University,Shanghai 200433,People’s Republic of China bDepartment of Chemistry and Biochemistry,University of California,Santa Cruz,CA 95064,United Statesa r t i c l e i n f o Article history:Received 2September 2010Accepted 11October 2010Available online 16October 2010Keywords:Core/shellHybrid silica particles Anatase titania shell Click reaction Photocatalysta b s t r a c tThe monodisperse hybrid silica particles (h-SiO 2)were firstly prepared by a modified sol–gel process and the surface was modified in situ with double bonds,then abundant carboxyl moieties were introduced onto the surface of the silica core via thiol–ene click reaction.Afterward,the h-SiO 2/TiO 2core/shell micro-spheres were prepared by hydrolysis of titanium tetrabutoxide (TBOT)via sol–gel process in mixed eth-anol/acetonitrile solvent,in which the activity of TBOT could be easily controlled.The carboxyl groups on the surface of silica particles promote the formation of a dense and smooth titania layer under well con-trol,and the layer thickness of titania could be tuned from 12to 100nm.The well-defined h-SiO 2/TiO 2core/shell structures have been confirmed by electron microscopy and X-ray photoelectron spectroscopy studies.After calcination at 500°C for 2h,the amorphous TiO 2layer turned into anatase titania.These anatase titania-coated silica particles showed good photocatalytic performance in degradation of methyl orange aqueous solution under UV light.Ó2010Elsevier Inc.All rights reserved.1.IntroductionThe nanocrystalline titania particles as a heterogeneous photo-catalyst have attracted significant attention in the last few decades,due to their applications in water splitting [1],removing organic pollutants from environment [2–4]and eliminating bacteria and fungi in water [5].However,nanosized titania powders with high surface area are not thermally stable [6],and could easily lose their surface area at elevated temperature through phase transforma-tion and crystallite growth.For preparation of high performance photocatalyst,titania is usually coated onto inert supports,such as porous silica,carbon fibers,glass fibers and beads [3,4].Many ef-forts have been made to encapsulate nano-or sub-micron size sil-ica microspheres with titania so as to create more accessible photocatalytic sites,meanwhile,enhance the adsorption of organic toxin.Titania-shell composite particles are prepared by sol–gel pro-cesses [2–4],or coating of titania nanoparticles onto the silica or polymer microspheres through the layer-by-layer (LBL)technique [3,7].Although the LBL technique shows good control on the size and uniformity of the resulting particles,the LBL method is moretedious with long synthetic steps.Alternatively,a simple sol–gel method is more attractive.However,the high reactivity of titania precursors leads to several challenges in utilizing the sol–gel ap-proach for titania shell deposition,such as the ease aggregation of the coated microspheres,and the difficulty in the formation of regular shell-layer with controlled shell thickness of titania [2,3].Thus,to achieve a dense,uniform titania coating onto the surface of silica microspheres via sol–gel method remains challenging.Recently,Lee et al.[8]and Meng et al.[9]reported a new class of hybrid silica microspheres covered with vinyl groups on the sur-face prepared by one-pot approach.These hybrid silica micro-spheres should allow modification of the silica surface with click chemistry without the need of silane coupling agents,which could address the low efficiency and incomplete surface modification.Click chemistry,which is now extensively used in design and prep-aration of complex functional molecules due to its quantitative,ra-pid reactions with inoffensive by-product (if any)that can be easily removed.More importantly,it offers rich opportunities in func-tionalization and stabilization of nanoparticles.For instance,cop-per(I)catalyzed Huisgen [3+2]dipolar cycloaddition between an alkyne and azide is readily to be utilized to prepare a variety of functional materials as a post functionalization strategy.Other reactions,such as Diels–Alder reactions,metal-free dipolar cyc-loadditions and thiol–ene(yne)chemistry are of importance as well.So far,the reaction between thiols and vinyl groups has been0021-9797/$-see front matter Ó2010Elsevier Inc.All rights reserved.doi:10.1016/j.jcis.2010.10.023⇑Corresponding author.Fax:+862151630302.E-mail address:ccwang@ (C.-C.Wang).mostly implemented for the synthesis of networks andfilms as highlighted by Hoyle et al.[10].To date,thiol–ene click reaction has attracted much research interest as it is easy to execute under facile reaction conditions, and also it is versatile in reactants.Campos et al.[11]reported dif-ferent types of polymer functionalization based on thermal and photochemical initiated thiol–ene click reaction.Goldmann and coworkers[12]demonstrated the surface modification of poly(divinylbenzene)with PNIPAM and PHEMA via thiol–ene and azide–alkyne reactions,respectively.Connal et al.[13]employed LBL assembly technique to alternately deposit PMA-thiol/PMA-ene and poly(vinylpyrrolidone)(PVP)onto silica particles.The resulting thiol–ene cross-linked PMA capsules can be widely ap-plied in drug delivery system.However,all the above-mentioned thio–ene click reactions were performed on the surface of organic substrates.The modification of inorganic microspheres by click reaction is rarely explored[14].Here we report,for thefirst time,the surface modification of the hybrid silica particles(h-SiO2)through click reaction between mer-captoacetic acid and the vinyl groups located on the surface of sil-ica particles.The reaction resulted in hybrid silica particles covered with carboxylic acid groups,these particles could be well dispersed in water.Besides,the hydroxyl groups on the surface of hybrid sil-ica particles could facilitate titania deposition via sol–gel process in a mixed ethanol/acetonitrile solvent,in which the activity of tita-nium tetrabutoxide(TBOT)could be easily controlled.The core size and shell thickness of the core/shell nanoparticles can be well manipulated.After calcination at500°C for2h,the amorphous titania turned into polycrystalline anatase titania.These silica core–titania shell microspheres showed significant photocatalytic activity in dye degradation under UV light irradiation.2.Materials and methods2.1.MaterialsVinyl triethoxy silane(VTES)and sodium dodecylbenzene sulfo-nate(SDBS)were purchased from Sinopharm Chemical Reagent Co. Ltd.Mercaptoacetic acid from ACORS and titanium tetrabutoxide (TBOT)from Shanghai Qiangsheng Chemical Reagent Co.Ltd.,were used as received.Azobisisbutyronitrile(AIBN)was purchased from Sinopharm Chemical Reagent Co.Ltd.and recrystallized in ethanol. Acetonitrile was purchased from Shanghai Qiangsheng Chemical Reagent Co.Ltd.and purified by distillation.Aqueous ammonia solution(28%),ethanol from Shanghai Qiangsheng Chemical Re-agent Co.Ltd.and deionized water were used as received.2.2.Synthesis of vinyl-functionalized hybrid silica microspheres and modification with mercaptoacetic acidVinyl-functionalized silica microspheres were synthesized according to the literature reported method[9].VTES3.8g and SDBS0.039g(0.3ÂCMC)(critical micelle concentration)were added into30ml water under vigorous stirring for1h,then0.5 ml aqueous ammonia solution(28%)was added,and the mixture was heated at50°C for48h.The resulting microspheres were sep-arated by centrifugation and washed several times with deionized water.0.05g AIBN and0.174g mercaptoacetic acid with a molar ratio of1:1(thiol:alkene)were added to a10ml ethanol solution con-taining0.1g vinyl-functionalized silica microspheres.After bub-bled with N2at45°C for30min,the solution was heated at 80°C for additional24h for complete reaction.Samples were also prepared with different amount of mercaptoacetic acid varied from molar ratio of0.5:1to5:1(thiol:alkene).2.3.Synthesis of h-SiO2/TiO2core/shell microsphereThe deposition of TiO2shell on carboxyl-modified h-SiO2parti-cles was performed by controlled hydrolysis of TBOT in the etha-nol/acetonitrile(3/1,V/V)mixed solvent in the presence of ammonia solution as catalyst.Typically,0.04g of carboxyl-modi-fied h-SiO2particles were dispersed in160ml of ethanol/acetoni-trile(3/1,V/V)and then mixed with1.2ml of25wt.%ammonia solution at room temperature.Finally,a TBOT solution(from 0.8ml to 2.0ml)in32ml of an ethanol/acetonitrile(3/1,V/V) was added to the above h-SiO2dispersion under stirring.After the hydrolysis reaction performed at room temperature for1h, the h-SiO2/TiO2core/shell microspheres were washed with aceto-nitrile using sonication for three times,and the particles were col-lected by centrifugation.The resulting particles were then dried in a vacuum oven at40°C till reaching a constant weight.To obtain anatase titania shell,the composite particles were calcined at 500°C for2h.2.4.Photocatalytic activity measurementThe photocatalytic activities of the calcined h-SiO2/TiO2micro-spheres were measured by the degradation of methyl orange in water.Twenty milligram h-SiO2/TiO2microspheres were added to100ml methyl orange aqueous solution(10mg/l).The mixture was stirred for1h in dark to ensure methyl orange absorbed by the catalyst before UV light exposure.An800W high-pressure Hg lamp with CuSO4solution as a cutofffilter was used as UV light source.The UV absorption spectra of the samples were collected by Lambda35Spectrometer(PerkinElmer,America).The concentra-tion of methyl orange was monitored on the basis of UV absorption peak centered at465nm.2.5.CharacterizationHigh Resolution Transmission Electron Microscopy(HR-TEM) images were taken on a JEM-2010(JEOL,Japan)TEM at an acceler-ating voltage of200kV.Samples were dispersed in acetonitrile and then transferred to a carbon coated copper grid.Energy dispersive X-ray spectroscopy was performed on a SUPERSCAN SSX-550scan-ning electron microscope(SEM)(Shimadz,Japan)at an accelerat-ing voltage of15kV.Samples dispersed in acetonitrile were transferred onto a glass slide at room temperature and sputter-coated with Au.Hydrodynamic diameter(Dh)measurements and Zeta-pH titration were conducted by dynamic light scattering (DLS)with a ZEN3600(Malvern,UK)Nano-ZS instrument con-nected to MPT-2(Malvern,UK)Automatic titrator.Infrared spectra were recorded on an Fourier transform infrared spectrometer(IR Prestige-21,Shimadz,Japan).The dried samples were mixed with KBr,and then compressed to a plate for measurement.Powder X-ray diffraction(XRD)patterns were collected on a X’Pert Pro(Panalytical,Netherlands)diffractometer with Cu K a radiation at k=0.154nm operating at40kV and40mA.3.Results and discussion3.1.Synthesis of vinyl-functionalized silica microspheres andmodification with mercaptoacetic acidThe detailed synthetic approach for the h-SiO2/TiO2core/shell microspheres is illustrated in Scheme1.The vinyl-functionalized silica particles were prepared by one-pot sol–gel process under dif-ferent SDBS surfactant concentrations.The size and the polydisper-sity index(PDI)of as-prepared hybrid particles were characterizedZ.-Y.Shen et al./Journal of Colloid and Interface Science354(2011)196–201197by TEM and DLS,respectively.The results are summarized in Ta-ble1.The surfactant concentration had a great influence on the size and the uniformity of the silica particles.When the surfactant concentration of0.3ÂCMC was used,the size of silica particles is around121nm,and more importantly,the PDI is about0.05,indi-cating the as-prepared hybrid silica particles are very uniform.The particle size of the hybrid silica particles could be modulated by the surfactant concentration(Table1).To determine the existence of the vinyl groups on particle surface,we performed FTIR analysis on the particles.As shown in Fig.1a,the absorption peaks centered at966cmÀ1,1602cmÀ1are characteristic peaks of vinyl groups (A CH@CH2),while1008cmÀ1,1409cmÀ1are characteristic peaks of Si A C vibration,thus confirming the presence of Si A CH@CH2 groups.In addition,the peaks observed at around1133cmÀ1and 1049cmÀ1suggest the formation of polysiloxanes structure,which is consistent with the literature reported values[9].The surface of the silica particles was modified with different amount of mercaptoacetic acid through a click reaction between the thiol and alkene groups that was initiated by AIBN at50°C. After the surface modification,the appearance of A C@O (1710cmÀ1)and A COOH(3478cmÀ1)FTIR peaks support the suc-cessful coating of carboxyl groups on the particle surface(Fig.1). We observe the A C@O and A COOH peaks increase with thiol:alk-ene molar ratio from1:1to3:1,and then remained more or less the same with further increase of the molar ratio(Fig.1b–e).This data suggested the amount of mercaptoacetic acid less than molar ratio of1:1(thiol:alkene)was not sufficient to complete the sur-face modification,until the molar ratio reach3:1(thiol:alkene).We also carried out zeta potential measurement for pure hybrid silica particles and the core/shell microspheres with different de-grees of modification asa function of pH.As shown in Fig.2,pure silica particles showed an isoelectric point is at pH=3.4.After sur-face modification,the isoelectric point moves toward lower pH val-ues of2.3,1.9and1.6for the samples prepared with molar ratio of 1:1,3:1,5:1(thiol:alkene),respectively.The data confirmed the modification of carboxyl groups onto the silica surface,and the in-crease of the carboxyl groups onto the surface of silica particles as the molar ratio increase.Besides,a significant increase in aqueous dispersibility is another direct evidence that supports the presenceof carboxyl groups on the surface of hybrid silica particles[15].The carboxyl groups modified with the molar ratio of1:1on the surface of silica particles was determined to be100l mol/g determined by acid–base titration.3.2.Synthesis of h-SiO2/TiO2core/shell microspheresThe h-SiO2/TiO2core/shell microspheres were prepared by the controllable hydrolysis of TBOT that catalyzed by ammonium cat-ions in an ethanol/acetonitrile mixed solvent.It is expected that the carboxyl groups on the particle surface attracted the positively charged NHþ4,which further drew the negatively charged TiOÀspecies together,and thereby facilitate the coating of titania via sol–gel process[16].A series of experiments were conducted to investigate the effect of the TBOT feed on the morphology of theillustrates the synthetic approach for the preparation of monodisperse mercaptoacetic acid modified silica cores and anatase titaniasol–gel process.Table1A summary of the structural properties of the silica particles prepared with differentsurfactant concentrations.Sample code SDBS(ÂCMC)Particle size(nm)PDISilica-10.12180.11Silica-20.21870.15Silica-30.31210.05Silica-40.41160.04Silica-50.71240.12Note:VTES=3.8g,NH3ÁH2O=0.5ml.Z.-Y.Shen et al./Journal of Colloid and Interface Science354(2011)196–201199of(a)mercaptoacetic acid modified silica microspheres;h-SiO2/TiO2core/shell microspheres before calcination with titania61nm(Sample B);(d)73nm(Sample C);(e)100nm(Sample D);and(f)calcined Sample B with shell thickness of59nm.FTIR spectra(Fig.6)revealed the compositive change of h-SiO2/TiO2structure after calcination.In Fig.6,the broad bands at500–900cmÀ1are corresponding to the Ti A O A Ti vibration.The peak at1641cmÀ1was attributed to O A H bending for Ti A OH,Si A OH and water,and the broad bands at2800–3800cmÀ1were assigned to O A H,N A H and C A H stretching.Significantly,we observed the N A H vibrational peak centered at1400cmÀ1,as an indication of the presence of NHþ4ions[16],which supports the proposed role of ammonium solution in the TiO2shell growth.After calcination at500°C for2h,the Ti A O A Ti vibration peak was enhanced signif-icantly,which might result from the removal of organic composi-tion and/or the formation of crystalline TiO2shell.The signals around1100cmÀ1corresponding to asymmetric vibration of Si A O A Si were also enhanced.More importantly,the disappearance of the N A H(1400cmÀ1)and the C A H(3180cmÀ1)peaks indicates the removal of N A H and C A H groups from organic component dur-ing calcination.The broad peak centered at3400cmÀ1can be attributed to the O A H vibration for Ti A OH and Si A OH groups. The remained A OH also known as surface hydroxylation are advantageous for photocatalytic activity of titania as it provides higher capacity for oxygen absorption[17–19].To determine the crystal structure,we performed XRD studies on both titania-coated silica particles before and after calcination at500°C for2h,the XRD patterns are shown in Fig.7.Before cal-cination,we did not observe any diffraction peaks from20°to80°2h,indicating the as-prepared titania shell was amorphous.In con-trast,the calcined structure exhibited multiple diffraction peaks, which can be indexed to the anatase phase(JCPDS File No.21-1272)of TiO2.The results confirmed the transformation of amor-phous to anatase phase of TiO2shell.3.3.Photocatalytic studyThe photocatalytic properties of h-SiO2/TiO2core/shell micro-spheres were evaluated through the degradation of methyl orange in water under UV light irradiation(Fig.8).All samples were cal-cined at500°C for2h,and equal weight of h-SiO2/TiO2micro-sphere catalysts were used in the measurement.There was almost no degradation of methyl orange without photoactive cata-lyst as expected.Meanwhile,all calcined h-SiO2/TiO2microspheres200Z.-Y.Shen et al./Journal of Colloid and Interface Science354(2011)196–201showed significant photocatalytic activity in the degradation of methyl orange.Sample B with the smallest shell thickness showed the best photocatalytic activity,which can be attributed to the lar-ger surface area compared to Samples C and D.Besides,such kind of monodispersed catalytic particles has additional advantages for easy separation and high recyclability.The capability of synthesiz-ing highly controllable anatase phase titania-coated silica micro-spheres opened up new opportunities in other applications such as photo-initiated polymerization and solar cells.4.ConclusionWe demonstrated the rational synthesis of h-SiO2/TiO2core/ shell microspheres by using carboxyl group modified silica particle as cores and titania as shell via the controllable hydrolysis of TBOT. The thickness of titania shell can be well tuned by the amounts of TBOT used in the hydrolyzation.The resulting core/shell h-SiO2/ TiO2microspheres were nearly monodisperse,where the titania shell is a dense and smooth amorphous layer.After calcination, the amorphous layer turned into anatase titania shell,which exhibited significant photocatalytic activity in degradation of methyl orange in water.The capability of synthesizing well-de-fined crystalline titania-coated silica particles opened up new opportunities in many applications including photo-catalysis and solar cells.AcknowledgmentsWe thank Prof.X.Y.Ni for the help in photocatalytic experi-ments.This work was supported by National Science Foundation of China(Grant Nos.20974023,21034003and51073040),National Science Foundation for Distinguished Young Scholars of China (50525310),the Cultivation Fund of the Key Scientific and Techni-cal Innovation Project,Ministry of Education of China(No.707023). Yat Li would like to acknowledge the Advanced Scholars Program of Fudan University.References[1]E.Reisner,J.D.Powell,C.Cavazza,J.C.Fontecilla-Camps,F.A.Armstrong,J.Am.Chem.Soc.131(2009)15729.[2]D.P.Wang,H.C.Zeng,Chem.Mater.21(2009)4811.[3]P.Wilhelm,D.Stephan,J.Colloid Interface Sci.293(2006)88.[4]P.Wilhelm,D.Stephan,J.Photochem.Photobiol.A185(2007)19.[5]J.C.Yu,W.Ho,J.Yu,H.Yip,P.K.Wong,J.C.Zhao,Environ.Sci.Technol.39(2005)1175.[6]J.W.Lee,M.R.Othman,Y.Eom,T.G.Lee,W.S.Kim,J.Kim,MicroporousMesoporous Mater.116(2008)561.[7]H.Nakamura,M.Ishii,A.Tsukigase,M.Harada,H.Nakano,Langmuir21(2005)8918.[8]Y.Lee,J.Park,C.Oh,S.G.Oh,Y.C.Kim,Langmuir23(2007)10875.[9]Z.Meng,C.Xue,Q.Zhang,X.Yu,K.Xi,X.Jia,Langmuir25(2009)7879.[10]C.E.Hoyle,T.Y.Lee,T.Roper,J.Polym.Sci.,Part A:Polym.Chem.42(2004)5301.[11]L.M.Campos,K.L.Killops,R.Sakai,J.M.J.Paulusse, D.Damiron, E.Drockenmuller,B.W.Messmore,C.J.Hawker,Macromolecules41(2008)7063.[12]A.S.Goldmann,A.Walther,L.Nebhani,R.Joso,D.Ernst,K.Loos,C.Barner-Kowollik,L.Barner,A.H.E.Muller,Macromolecules42(2009)3707.[13]L.A.Connal,C.R.Kinnane,A.N.Zelikin,F.Caruso,Chem.Mater.21(2009)576.[14]S.S.Balamurugan, E.Soto-Cantu,R.Cueto,P.S.Russo,Macromolecules43(2010)62.[15]L.Shen,A.Stachowiak,S.K.Fateen,ibinis,T.A.Hatton,Langmuir17(2001)288.[16]P.Wang,D.Chen,F.Q.Tang,Langmuir22(2006)4832.[17]J.G.Yu,H.G.Yu,B.Cheng,X.J.Zhao,J.C.Yu,W.K.Ho,J.Phys.Chem.B107(2003)13871.[18]M.Ye,Q.Zhang,Y.Hu,J.Ge,Z.Lu,L.He,Z.Chen,Y.Yin,Chem.Eur.J21(2010)6243.[19]Z.Liu,X.Quan,H.Fu,X.Li,K.Yang,Appl.Catal.B52(2004)33.Z.-Y.Shen et al./Journal of Colloid and Interface Science354(2011)196–201201。