PDC钻头工作原理及相关特点
PDC钻头的特点与合理使用的探讨

174PDC钻头代表了钻头的一个新的发展阶段。
这种钻头通过破碎岩石作用钻进岩石。
安全系数高,风险低。
金刚石复合片为聚晶片,后约1/32in,镶嵌在已植入钻头本体预先所钻的洞内的碳化物金属块里。
1 PDC钻头的结构PDC钻头结构有钢体与胎体两种类型,其中胎体钻头的材料为铸造碳化钨粉,经烧结制成钻头,在烧结时钻头工作面留下窝槽,然后再在窝槽上直接焊接复合片。
钢体钻头的材料为整块合金钢经机械加工铸成,然后在碳化钨齿柱上将复合片制成切削齿,并将切削齿镶嵌在钻头体上,保径部位也是将金刚石块或其他耐磨性材料镶嵌在钻头体上,为防止冲蚀,可在钻头工作面上喷涂一层耐磨材料。
PDC钻头工作面的几何形状其对钻头的稳定性、井底清洗、钻头磨损及钻头各部荷载的分布都有明显的影响。
钻头工作面性状有五个基本要素,包括顶部、内锥、肩部、侧面与保径。
2 PDC钻头的工作原理PDC钻头实际上就是微型切削片刮刀钻头,所以PDC 钻头的工作原理基本与刮刀钻头的基本相同,在软至中硬的地层中钻头通过剪切方式将岩石破碎,在较小的钻压下就能够完成高机械钻速。
由于聚晶金刚石层极薄(1mm)左右、极硬,且比碳化钨衬底的耐磨性高100倍以上,因此在切削岩石过程中刃口能保持自锐。
3 PDC钻头的特点PDC钻头特点主要有以下几个方面:即没有活动的零件,切削钻用能力强,钻头有较长的使用寿命,和比其它类型钻头相比较其机械钻速和抗冲击性更高,最适合于井下动力钻井。
获得极高的机械钻速,与牙轮钻头相比,PDC钻头本身没有活动件,可防止掉牙轮等井下事故与复杂情况的发生。
4 PDC钻头适用性PDC钻头主要在软至中硬地层中比较适用,地层有适度的研磨性,PDC钻头在砾石、燧石及大段不均质地层中应该避免使用。
同时根据地层的具体情况要选择合适的PDC钻头,当遇到硬且脆的地层则要选择布齿密度大、切削齿初刃小的钻头类型;遇到软土地层则需要选择布局密度小、切削齿初刃大的钻头,增加钻头的吃入深度以及有助于井底清洗,防止钻头泥包。
pdc钻头

PDC钻头1. 简介PDC钻头是一种常用于石油钻井的钻探工具。
PDC钻头由多个聚晶体金刚石(Polycrystalline Diamond Compact)切削元件组成,被广泛应用于地层钻探、岩石切割和石油开采中。
本文将介绍PDC钻头的结构、原理以及应用领域。
2. 结构PDC钻头主要由刀翼、钻头体和连接部分组成。
2.1 刀翼刀翼是PDC钻头的重要组成部分,通常由金刚石切削元件制成。
刀翼的数量、形状和布局对钻头的钻井性能和钻孔质量起着重要作用。
刀翼一般采用均匀分布的方式,以保证钻头在钻井过程中的均匀磨损。
2.2 钻头体钻头体是连接刀翼和连接部分的主要结构,通常由钢铁材料制成。
钻头体的设计需要考虑到钻井环境、井眼尺寸和钻头的稳定性等因素。
钻头体一般具有良好的强度和刚度,以确保钻头在高强度的钻井过程中不会发生变形或破损。
2.3 连接部分连接部分是将钻头与钻杆连接在一起的部分,通常采用标准的API连接方式。
连接部分需要具有良好的密封性和承载能力,以确保钻头和钻杆之间的传递力矩和转速。
3. 原理PDC钻头通过刀翼上的金刚石切削元件对地层进行切削和磨损,从而实现钻井的目的。
PDC钻头利用金刚石的高硬度和强大的切削能力,能够在岩石中快速切削并形成孔道。
PDC钻头的切削原理主要有两种:剪切和破碎。
3.1 剪切剪切是PDC钻头常用的切削方式之一。
当PDC钻头旋转时,刀翼上的金刚石切削元件与地层接触,通过相对运动切削地层。
金刚石的高硬度和切削元件的锋利边缘使得PDC钻头能够在地层中形成清晰而平滑的孔道。
3.2 破碎破碎是PDC钻头另一种常用的切削方式。
当地层硬度较高时,剪切切削效果可能不佳。
此时,PDC钻头通过施加较大的冲击力将地层破碎,进而形成孔道。
4. 应用领域PDC钻头广泛应用于石油、天然气和水井钻探领域。
其高效的切削能力和稳定的性能使其成为钻井操作中的重要工具。
4.1 石油钻井在石油钻井中,PDC钻头常用于垂直井、水平井和定向井的钻铤作业。
PDC钻头工作原理及相关特点

第二章 PDC 钻头工作原理及相关特点PDC 钻头是依靠安装在钻头体上的切削齿切削地层的,这些切削齿有复合片切削齿和齿柱式两种结构,它们的结构以及在钻头上的安装方式如图1-2所示。
复合片式切削齿是将复合片直接焊接在钻头体上预留的凹槽内而形成的。
它一般用于胎体钻头;齿柱式切削齿是将复合片焊接在碳化钨齿柱上而形成的,安装时将其齿柱镶嵌或焊接在钻头体上的齿空内,它一般用于钢体钻头,也有用于胎体钻头的。
复合片(即聚晶金刚石复合片)是切削齿的核心。
复合片一般为圆片状,其结构如图1-3所示,它是由人造聚晶金刚石薄层及碳化钨底层组成,具有高强度、高硬度及高耐磨性,可耐温度750℃。
人们早就从实验中发现,岩石的诸力学强度中,抗拉强度最低,剪切强度次之,而抗压强度最高,抗压强度往往比剪切强度高数倍至十多倍。
显然采用剪切方式破碎岩石比用压碎方式要容易而有效的多。
PDC 钻头的复合片切削结构正是利用了岩石这一力学特性,采用高效的剪切方式来破碎岩石,从而达到了快速钻井的(a) 复合片式切削齿 (b)齿柱式切削齿图1-2 切削齿在钻头上的安装方式图1-3 复合片的结构图1-4 PDC 钻头的切削方式目的。
当PDC钻头在软到中等级硬度地层进时,复合片切削齿在钻压和扭矩作用下克服地层应力吃入地层并向前滑动,岩石在切削齿作用下沿其剪切方向破碎并产生塑性流动,切削所产生的岩削呈大块片状,这一切削过程与刀具切削金属材料非常相似(见图1-4)。
被剪切下来的岩屑,再由喷嘴射出泥浆带走至钻头与井壁间的环空运至井外。
PDC钻头因使用了聚晶金刚石复合片作切削元件而使得切削齿有很高的硬度和耐磨性。
PDC齿的缺点是热稳定性差,当温度超过700℃时,金刚石层内的粘结金属将失效而导致切削齿破坏,因此PDC齿不能直接烧结在胎体上而只能采用低温钎焊方式将其固定在钻头体上。
在工作中,切削齿底部磨损面在压力作用下一直与岩石表面滑动摩擦要产生大量的摩擦热,当切削齿清洗冷却条件不好,局部温度较高时,就有可能导致切削齿的热摩损(350-700℃时,切削齿的磨损速度很快,这一现象称为切削齿的热磨损)而影响钻头正常工作,所以钻头要避免热磨损出现就必须有很好的水力清洗冷却,润滑作用配合工作,这就是要求泥浆从喷嘴流出后水力分布要合理,能有效地保护切削齿,这即是对钻头水力计的基本要求之一。
PDC钻头
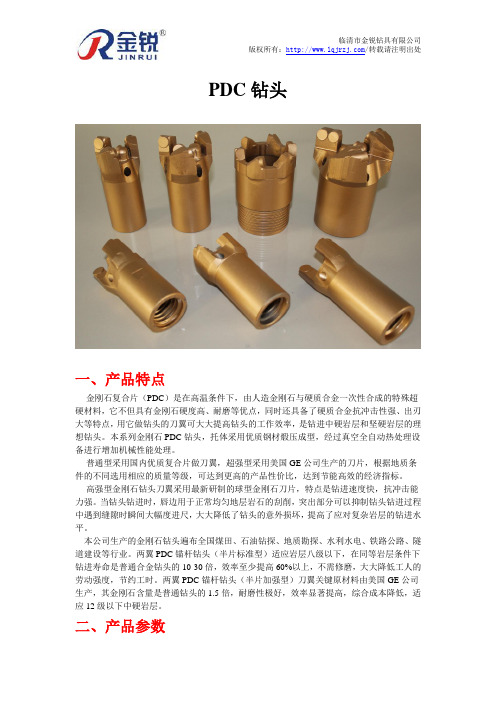
PDC钻头一、产品特点金刚石复合片(PDC)是在高温条件下,由人造金刚石与硬质合金一次性合成的特殊超硬材料,它不但具有金刚石硬度高、耐磨等优点,同时还具备了硬质合金抗冲击性强、出刃大等特点,用它做钻头的刀翼可大大提高钻头的工作效率,是钻进中硬岩层和坚硬岩层的理想钻头。
本系列金刚石PDC钻头,托体采用优质钢材煅压成型,经过真空全自动热处理设备进行增加机械性能处理。
普通型采用国内优质复合片做刀翼,超强型采用美国GE公司生产的刀片,根据地质条件的不同选用相应的质量等级,可达到更高的产品性价比,达到节能高效的经济指标。
高强型金刚石钻头刀翼采用最新研制的球型金刚石刀片,特点是钻进速度快,抗冲击能力强。
当钻头钻进时,唇边用于正常均匀地层岩石的刮削,突出部分可以抑制钻头钻进过程中遇到缝隙时瞬间大幅度进尺,大大降低了钻头的意外损坏,提高了应对复杂岩层的钻进水平。
本公司生产的金刚石钻头遍布全国煤田、石油钻探、地质勘探、水利水电、铁路公路、隧道建设等行业。
两翼PDC锚杆钻头(半片标准型)适应岩层八级以下,在同等岩层条件下钻进寿命是普通合金钻头的10-30倍,效率至少提高60%以上,不需修磨,大大降低工人的劳动强度,节约工时。
两翼PDC锚杆钻头(半片加强型)刀翼关键原材料由美国GE公司生产,其金刚石含量是普通钻头的1.5倍,耐磨性极好,效率显著提高,综合成本降低,适应12级以下中硬岩层。
二、产品参数最佳适应岩层参数表:行号类型适应岩层1 普通PDC钻头F<10的软—中硬岩2 加强PDC钻头F=10-12的中硬岩3 高强PDC钻头F<18的硬岩金刚石复合片(PDC)钻头钻进规程建议参数表:行号规格mm 钻进规程参数钻压(Kg)转速(rpm)泵量(1╱min)1 Ф28 300—700 300—350 150—2002 Ф30 300—700 300—350 150—2003 Φ32 300—700 300—350 150—2004 Φ48 300—700 300—350 120—1605 Φ56 320—800 250—350 130—1806 Φ75 480—1200 200—300 150—2007 Φ94 640—1600 150—250 200—2508 Φ110 880—2200 120—200 200—3009 Φ152 1500—3000 100—200 500—85010 Φ190 1800—4000 100—200 600—120011 Φ230 2200—4500 100—200 750—140012 Φ270 2400-5000 100—200 1000-1500三、产品说明1、正常作业时,严禁突然反转改变运行方向,以防止复合片钻头脱落。
PDC钻头的特点和破岩机理

前言自PDC钻头问世以来,以其优良的性能及随之而带来的经济效益,越来越多的受道现场作业队的青睐。
然而美中稍有不足的是,在现场的应用中,PDC只是PDC 而以,也就是说,作业人员对其了解还不是很深刻。
鉴于此,本人欲从其特点,包括PDC钻头的设计特点和它的结构特点,还有其破岩机理上给予归纳、总结和分析、推理,以期望能为现场作业提供一点技术上的借鉴和参考.PDC钻头的特点和破岩机理摘要:本文在简要介绍了PDC钻头的物质成份,两大类别(胎体钻头和刚体钻头)及其不同物质在钻井作业过程中所起的作用的基础上,归纳、总结了PDC钻头特点,包括其设计特点和结构特点;同时较详细地分析了在打定向井时,PDC钻头的结构特征因素对造斜率的影响;另外也在分析、归纳、总结国内外专家、学者的独特见解的基础上,对PDC钻头的破岩机理,也在一定程度上给予阐述.并在此基础上,最后也提出了一些PDC钻头的选型依据.关键词: PDC钻头; 特点; 机理分析Abstract:This themsis briefly introduces which materials PDC bit is made from,how it is manufactured,and the different types of PDC bits,also shows you the principal functionsof the different materials of PDC bit in drilling----on the basis of these,summaries the characteristics of PDC bit,including its designing characteristics and structural characteristics,and specificly analyses the effect of its structural characteristics on the leaning ration in the controlled directional drilling.At the same time ,after studying the specific ideas of the different experts at home and abroad,to some extent,analyses and summaries the rock breaking mechanism of PDC bit.In the end ,on this basis,gives you some facters that can help you how to choose PDC bit effiently.Key words: PDC bit; characteristics; Mechanism analysis正文:近年内,随着PDC钻头的广泛应用,PDC钻头在型号和质量上都进行了较大的改进,已经在软到硬的地层中逐步使用,并且取得了较好的经济效益,为更好地使用PDC 钻头,使其最大限度地发挥优势,以便更好地服务于钻井作业,特从其特点和破岩机理方面撰写此文.PDC钻头者,就是聚晶金刚石复合片钻头,即Polycrystalline Diamond Compact Bit.其结构见图1-1所示,它示以金刚石为原料加入粘结剂在高温下烧结而成.复合片为圆片状,金刚石层厚度一般小于1mm,切削岩石时作为工作层,碳化钨基体对聚晶金刚石薄层起支撑作用.两者地有机结合,使PDC既具有金刚石地硬度和耐磨性,又具有碳化钨地结构强度和抗冲击能力.由于聚晶金刚石内晶体间地取向不规则,不存在单晶金刚石固有地解理面,所以PDC的抗磨性及强度高于天然金刚石的,且不易破碎.PDC由于多种材料的存在,热稳定性较差,同时脆性较强,不能经受冲击载荷.PDC钻头的特点1973年美国开发了聚晶金刚石复合片钻头,国外广泛应用于软-中硬地层.在中东和北海的深井及海洋钻井中首先获得了高井尺、高钻速,大大缩短了建井周期,降低了钻井成本,受到了钻境界的广泛重视,成为钻井工具的一项重大成就.国内对PDC钻头也引起了极大的关注和兴趣,随着钻井技术人员对PDC钻头的认识和实践,它正在逐步取得较好的使用效果.按钻头材料及切削齿结构划分,PDC钻头有钢体和胎体两大类别(间上图1-2) 胎体钻头用碳化钨粉末烧结而成,用人造聚晶金刚石复合片钎焊在碳化钨胎体上,用天然金刚石保径.碳化钨胎体耐冲蚀、耐磨、强度高、保径效果好.钻头水眼水道面积可以根据钻井工艺需要的水力参数来设计,有较大的灵活性.胎体外形可以根据地层特点设计,变化胎体形状只要改变模具而不需要增加设备.钢体PDC钻头,是用镍、铬、钼合金机械加工成形.经过热处理后在钻头体上钻孔,强人造聚晶金刚石复合片压入(紧配合)钻头体内,用柱状碳化钨保径.它比胎体钻头成本低20%左右,但不耐磨且易被冲蚀.PDC钻头的设计特点1.PDC钻头采用爪型设计PDC钻头的性能在很大程度上取决于切削齿的质量,PDC钻头都采用了高质量爪型齿和环形齿,经过与其它类型复合片对比试验分析,证明它具有抗剪强度高、耐冲击、寿命长、热稳定性能好的特点,与同尺寸普通PDC齿相比,爪型齿的金刚石含量提高了2.7倍,抗冲击破坏能力提高2倍.2.大刀翼设计全部PDC钻头系列的刀翼进行加高加大,采用超大排屑流道设计,可以更加有效的运移钻屑,清洗钻头,防止钻头泥包,提高机械钻速.3.抗回旋设计采用力学平衡设计,对PDC钻头进行螺旋保径设计、轨道布齿设计、缓冲块设计以保证钻头抗回旋性能.4.防泥包涂层设计和制造技术QP系列钻头可根据地层情况进行防泥包涂层设计,它采用了独特的对钻头表面负离子处理技术,使钻头表面带有负电荷,在钻头周围形成一个阳板,形成电流,钻头与钻井液之间形成一个水的集区,其作用就如同润滑剂或象隔板,在钻进中,泥页岩钻屑中的负离子与钢体表面的负电荷相斥,从而起到防泥包的效果.5.可修复性钢体PDC钻头的本体磨损和切削齿破碎后可进行修复和更换,使得钻头的使用成本大大降低.PDC钻头结构特征及此因素对造斜率的影响钻头的费用在一口井中的总费用中所占的比例不是很大,但选好和用好一只钻头对提高机械钻速、提高造斜率和降低全井费用却是关系重大.为了高速、优质、低成本地钻好定向井,应从定向钻井的独特性出发优选钻头.定向造斜段钻井的特点使使用井下马达,钻头转速高,钻头切削齿和钻头外径磨损快钻头寿命缩短.在定向段钻进过程中,需要钻头能保持住所要求的工具面角度,如果所选的钻头布能提供合适的导向能力,就会获取布到所设计的造斜率或偏离所定的方位.这样,就会增多纠斜和扭方位的次数或增多更换下部钻具组合的次数.由于PDC钻头具有无活动件、适应高转速低钻压钻进工况之特点和钻头使用寿命长的优点,因此更适合与动力钻具配合使用,多次现场施工结果表明,动力钻具+PDC钻头钻进方式有利于提高钻井速度,减少起下钻次数、保证钻具安全,取得了动力钻具+牙轮钻头钻进方式无法比拟的技术经济效益.常规定向井施工主要时通过选择合适的造斜工具(弯接头+动力钻具、单弯动力钻具、双弯动力钻具等)调整侧向力的大小,从而控制造斜率的高低,而同样的侧向力与不同结构的PDC 钻头配合对造斜率时有极大的影响的。
PDC使用注意

PDC钻头使用技术探索一.PDC钻头的主要特点1.PDC钻头所采用的聚晶金刚石复合片是由薄层人造金刚石和碳化钨片基体组成的,该复合片经高温高压粘合为不可分割的整体,金刚石层由许多小晶粒组成,晶粒以不规则的方式组合在一起,使复合片的强度和耐磨性达到最佳。
与牙轮钻头靠牙齿对岩石的冲击、压碎作用破碎岩石不同,PDC钻头主要依靠切削齿对岩石的剪切作用破碎岩石,利用剪切作用破碎岩石比压裂作用破碎岩石所需能量小得多,所以PDC钻头能以很小的钻压实现更有效的钻进,这一点对井斜的控制尤为重要。
2.PDC钻头在钻进中磨损缓慢而且具有自锐性,所以钻头在使用寿命期内,可保持切削齿锐利,可一直保持较高的机械钻速。
3. PDC钻头没有活动部件,所以钻头使用寿命长,没有金属物落井的危险。
4. PDC钻头依靠剪切作用破碎岩石,井底压差对钻头破碎岩石影响小,因而有利于在深井、高密度钻井液条件下获得较高的机械钻速。
5. PDC钻头对提高钻速、降低成本是十分有利的,但也有一些缺点:一是使用范围有局限性,对地层的选择性太强,一般只适宜在砂、泥岩地层使用;二是价格较高,有时使用PDC钻头在经济上不一定合算。
二. 根据地层特性选型地层硬度表1.地层级别为1—2的软地层,选用排屑空间大,清洗条件好,复合片直径不小于19毫米的大复合片钻头。
2.地层级别为3的软地层,选用低密度布齿,排屑空间大的常规复合片金刚石钻头或相当的大复合片金刚石钻头。
3.地层级别为4的软地层和5的中硬地层,选用中密度布齿或高密度布齿,排屑空间适中的常规复合片金刚石钻头。
4.对于含硬夹层的软--中硬地层,选用混合齿(热稳定聚晶金刚石和常规复合片金刚石)钻头和抗回旋钻头等。
5.对于易缩径地层,选用双心或偏心钻头;6.含砾或高研磨性岩石地层,不宜选用PDC钻头。
三.PDC钻头使用中易出现的问题及对策1.泥包问题。
产生钻头泥包现象的原因一般是泥浆性能差和操作不当所至,表现为泥浆高粘切、送钻切菜式,建议所用钻井液流变性要好,粘切一定要低,送钻力求均匀。
pdc钻头名词解释
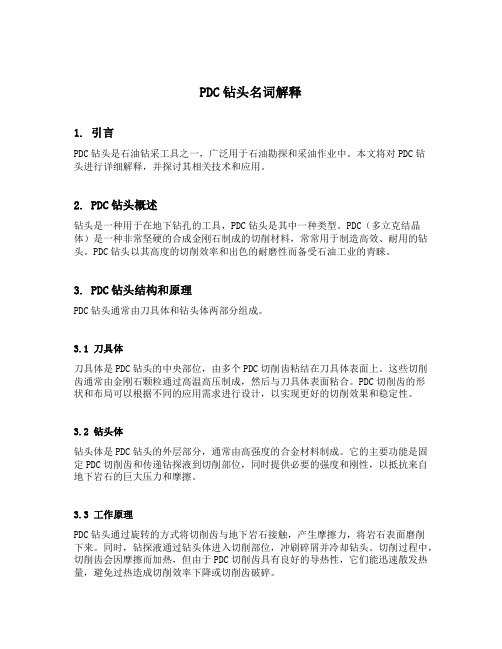
PDC钻头名词解释1. 引言PDC钻头是石油钻采工具之一,广泛用于石油勘探和采油作业中。
本文将对PDC钻头进行详细解释,并探讨其相关技术和应用。
2. PDC钻头概述钻头是一种用于在地下钻孔的工具,PDC钻头是其中一种类型。
PDC(多立克结晶体)是一种非常坚硬的合成金刚石制成的切削材料,常常用于制造高效、耐用的钻头。
PDC钻头以其高度的切削效率和出色的耐磨性而备受石油工业的青睐。
3. PDC钻头结构和原理PDC钻头通常由刀具体和钻头体两部分组成。
3.1 刀具体刀具体是PDC钻头的中央部位,由多个PDC切削齿粘结在刀具体表面上。
这些切削齿通常由金刚石颗粒通过高温高压制成,然后与刀具体表面粘合。
PDC切削齿的形状和布局可以根据不同的应用需求进行设计,以实现更好的切削效果和稳定性。
3.2 钻头体钻头体是PDC钻头的外层部分,通常由高强度的合金材料制成。
它的主要功能是固定PDC切削齿和传递钻探液到切削部位,同时提供必要的强度和刚性,以抵抗来自地下岩石的巨大压力和摩擦。
3.3 工作原理PDC钻头通过旋转的方式将切削齿与地下岩石接触,产生摩擦力,将岩石表面磨削下来。
同时,钻探液通过钻头体进入切削部位,冲刷碎屑并冷却钻头。
切削过程中,切削齿会因摩擦而加热,但由于PDC切削齿具有良好的导热性,它们能迅速散发热量,避免过热造成切削效率下降或切削齿破碎。
4. PDC钻头的优势相比传统的钻头类型,PDC钻头具有许多优势。
4.1 高效切削PDC钻头采用多个粘合在刀具体上的PDC切削齿,这种设计可以实现高效的切削,快速消耗岩石表面,提高钻探效率。
4.2 耐磨性强PDC切削齿具有良好的耐磨性,能够承受长时间的高强度切削,减少了频繁更换切削齿的需要,提高了钻头的使用寿命。
4.3 高度稳定PDC钻头的切削齿布局和形状经过精心设计,可以实现平衡切削力和稳定性。
它们减少了钻头的震动和偏离轨迹的可能性,确保了钻孔的准确度和质量。
4.4 适应多种地质环境PDC钻头可以适应各种地质环境,如软土、硬岩、砾石等。
pdc钻头的原理与应用

PDC钻头的原理与应用1. 简介PDC钻头是一种新型的刀具,它采用多个聚晶金刚石(Polycrystalline Diamond Compact,PDC)片嵌入钢体基体制成,广泛用于石油勘探和开发领域。
本文将介绍PDC钻头的原理和应用。
2. PDC钻头的原理PDC钻头的原理是将多个聚晶金刚石片嵌入钢体基体制成,利用聚晶金刚石的高硬度和耐磨性,以及钢体基体的韧性和强度,实现高效的钻井作业。
PDC钻头的原理主要包括以下几个方面:2.1 聚晶金刚石片PDC钻头采用的聚晶金刚石片由多个金刚石颗粒和金属结合剂组成,具有高硬度、耐磨性好等特点。
聚晶金刚石片通过特定的制备工艺,使得每个金刚石颗粒都与周围的颗粒紧密结合,形成一个整体。
2.2 钢体基体钢体基体是PDC钻头的主体部分,它由高强度的钢材制成。
钢体基体承载着聚晶金刚石片,并且通过特定的工艺将聚晶金刚石片与钢体基体紧密结合,形成一个整体结构。
钢体基体具有良好的韧性和强度,能够有效地传递钻井力,同时保护聚晶金刚石片。
2.3 刀具形态PDC钻头的刀具形态通常有平面PDC钻头、锥度PDC钻头和斜面PDC钻头等。
不同形态的刀具适用于不同的地质条件和钻井需求。
例如,平面PDC钻头适用于较硬的地质层,而锥度PDC钻头适用于软、粉状的地质层。
2.4 作用原理PDC钻头在钻井作业中,通过旋转和下压力来完成钻井作业。
当PDC钻头旋转时,聚晶金刚石片切削岩石,同时钢体基体提供支撑和切削力。
通过连续的旋转和下压力,PDC钻头可以持续地切削岩石,实现高效的钻井作业。
3. PDC钻头的应用PDC钻头由于其优良的性能,在石油勘探和开发领域得到了广泛的应用。
主要应用于以下几个方面:3.1 石油勘探PDC钻头可以在石油勘探中使用,用于钻取各种类型的地层。
由于其高硬度和耐磨性,PDC钻头可以有效地切削各种岩石,包括硬质岩石和软质岩石。
在石油勘探中,PDC钻头可以提高钻探的效率,减少钻井时间,降低勘探成本。
- 1、下载文档前请自行甄别文档内容的完整性,平台不提供额外的编辑、内容补充、找答案等附加服务。
- 2、"仅部分预览"的文档,不可在线预览部分如存在完整性等问题,可反馈申请退款(可完整预览的文档不适用该条件!)。
- 3、如文档侵犯您的权益,请联系客服反馈,我们会尽快为您处理(人工客服工作时间:9:00-18:30)。
第二章 PDC 钻头工作原理及相关特点PDC 钻头是依靠安装在钻头体上的切削齿切削地层的,这些切削齿有复合片切削齿和齿柱式两种结构,它们的结构以及在钻头上的安装方式如图1-2所示。
复合片式切削齿是将复合片直接焊接在钻头体上预留的凹槽内而形成的。
它一般用于胎体钻头;齿柱式切削齿是将复合片焊接在碳化钨齿柱上而形成的,安装时将其齿柱镶嵌或焊接在钻头体上的齿空内,它一般用于钢体钻头,也有用于胎体钻头的。
复合片(即聚晶金刚石复合片)是切削齿的核心。
复合片一般为圆片状,其结构如图1-3所示,它是由人造聚晶金刚石薄层及碳化钨底层组成,具有高强度、高硬度及高耐磨性,可耐温度750℃。
人们早就从实验中发现,岩石的诸力学强度中,抗拉强度最低,剪切强度次之,而抗压强度最高,抗压强度往往比剪切强度高数倍至十多倍。
显然采用剪切方式破碎岩石比用压碎方式要容易而有效的多。
PDC 钻头的复合片切削结构正是利用了岩石这一力学特性,采用高效的剪切方式来破碎岩石,从而达到了快速钻井的(a) 复合片式切削齿 (b)齿柱式切削齿图1-2 切削齿在钻头上的安装方式图1-3 复合片的结构图1-4 PDC 钻头的切削方式目的。
当PDC钻头在软到中等级硬度地层进时,复合片切削齿在钻压和扭矩作用下克服地层应力吃入地层并向前滑动,岩石在切削齿作用下沿其剪切方向破碎并产生塑性流动,切削所产生的岩削呈大块片状,这一切削过程与刀具切削金属材料非常相似(见图1-4)。
被剪切下来的岩屑,再由喷嘴射出泥浆带走至钻头与井壁间的环空运至井外。
PDC钻头因使用了聚晶金刚石复合片作切削元件而使得切削齿有很高的硬度和耐磨性。
PDC齿的缺点是热稳定性差,当温度超过700℃时,金刚石层内的粘结金属将失效而导致切削齿破坏,因此PDC齿不能直接烧结在胎体上而只能采用低温钎焊方式将其固定在钻头体上。
在工作中,切削齿底部磨损面在压力作用下一直与岩石表面滑动摩擦要产生大量的摩擦热,当切削齿清洗冷却条件不好,局部温度较高时,就有可能导致切削齿的热摩损(350-700℃时,切削齿的磨损速度很快,这一现象称为切削齿的热磨损)而影响钻头正常工作,所以钻头要避免热磨损出现就必须有很好的水力清洗冷却,润滑作用配合工作,这就是要求泥浆从喷嘴流出后水力分布要合理,能有效地保护切削齿,这即是对钻头水力计的基本要求之一。
另外PDC钻头应避免在高硬度,高研磨性的地层中高转速钻进,以免造成局部摩擦温度过高。
§2.1 PDC钻头及钻进主要影响因素§2.1.1 PDC钻头结构介绍聚晶金刚石复合片分柱式和片式两种,常用的形状有圆形、尖形及半圆形等。
通常以柱式方式镶嵌在胎体上。
1. 切削齿的布置切削齿的布置与所钻地层及钻头类型有关,它将影响到钻头的机械钻速、总进尺和磨损。
切削齿布置越多,磨损越慢,钻头寿命越长,但机械钻进速度越低。
切削齿的布置应使每个切削齿的切削力、所切削的岩石量、载荷、扭矩、磨损以及水力清洗等都相同,所以有等切削、等功率、等磨损设计要求。
2. 切削齿出刃与胎体是指切削刃与钻头体之间的距离。
切削齿可以是全出刃,也可以是部分出刃:全出刃一般用于钻软地层,全出刃切削齿对钻头清洗有利,且钻速较高;部分出刃用于较硬地层,它的切削齿强度较高,但钻头清洗相对较困难,适用于油基钻井液中钻进;硬质合金胎体钻头由于是铸造形成,不受加工限制。
3. 切削齿的排列方向有关PDC钻头的切削齿的排列方式的研究目前较多。
为了便于清除以利于钻进,切削齿在钻头体上排列还应注意侧倾角和后倾角。
侧倾角在钻进时产生外推力,在钻井液的清洗作用下侧倾角能协助将岩屑排出钻头中心,有效清洗钻头。
后倾角除有利于钻头切削齿的清洗外,在硬岩层切削力增大时可以减少切削齿的颤动,有利于保护切削刃,延长其寿命。
后倾角一般为︒0。
后倾角愈大,~︒25机械钻速愈低,但在硬地层中后倾角可减少切削刃的损坏。
图2.1 侧倾角与后倾角示意图§2.1.2 影响PDC钻头钻进速度的主要因素影响钻进速度的主要因素有很多,而且互相交织在一起而变得十分复杂。
要想把所有的影响因素反应到一个统一的钻速模式中是很困难的。
但其中影响较大、变化规律较明显的因素有钻压、转速、牙齿磨损、水力参数、压差、钻井液性能等,而其中与井底流动直接发生关系的有转速、水力参数、压差、钻井液性能等。
1. 转速对钻速的影响从机械破岩的原理来看,随着转速n的增加,钻速v也相应增加。
通过现场m和室内的试验得出的典型转速与钻进速度呈指数关系,且指数小于1。
这反映出钻头破碎岩石的时间效应问题。
它们之间的关系用数学形式可表达为:λ∝(2.1)nvm式中λ为转速指数,是岩石自然属性,它随地质条件和埋藏深度不同而异。
2. 水力参数对钻速的影响水力参数引起的井底净化程度对钻速有较大的影响。
井底净化是靠射流水力功率来完成的,如果水力功率不够,净化不充分,使岩屑留在井底而造成重复切削,导致实际钻速的下降。
同时,射流水功率在一定程度上还有水力破岩的作用。
1975年美国阿莫科研究中心在大量试验的基础上给出了水力参数和机械转速合理匹配的关系曲线(图 2.2),该曲线将图分为水力净化完善和水力净化不完善的两个区。
一定的钻速就意味着单位时间内钻出的岩屑总量,而清除这些岩屑就需要相应的水力功率。
如果实际水力功率小于清岩所需的水力功率,井底就会积存岩屑,影响钻速的提高。
由于水力破岩的作用已经受钻压的限制,净化程度只是从保证机械破岩效果方面影响转速,也就是说在排除水力破岩的作用条件下,如果破岩效率一定,在井底净化达到充分后无论如何提高水力功率也不可能提高转速。
6单位水功率钻速图2.2 钻速与水力参数关系曲线根据图2.2中的曲线回归可得:31.08527.0jcj N υ= (2.2) 并通过大量的试验得到:jc j m H N N v v C == (2.3) 式中: cj N ——净化充分时的钻头比水功率,2/mm W ;j v ——净化充分时的钻速,h m /; cN ——实际钻头比水功率,2/mm W ;m v ——实际钻速,h m /; H C ——水力参数影响系数。
水力参数的影响系数不能大于1,这是因为净化充分后的钻井机械钻速不会提高。
若按(2.3)计算出的H C 值大于1时,说明井底已充分净化,H C 值取1。
由(2.3)可得:j H m v C v ⋅= (2.4)3. 压差对钻速的影响压差是指井底压力与地层压力之差值。
井底压差将使岩石强度增加并对岩屑产生压持效应,从而影响了钻头的破岩效率,使得机械钻速降低。
它对钻速的影响规律如图(2.3)所示。
根据曲线,可导出压差对钻速影响关系。
p图2.3 压差与钻速关系曲线p m e v v ∆-=001714.00(2.5) 式中:m v ——实际速度,h m /;0v ——零压差时的钻速,h m /;e ——自然对数的底数; p ∆——压差,kPa 。
4. 钻井液性能对钻速的影响钻井液性能对钻进的影响是复杂的,因为钻井液各种性能之间关系密切,改变钻井液一种性能常会引起其它性能的相应变化,因此要单独评价某一种钻井液性能对钻速的影响相当困难。
大量的试验研究证明,钻井液密度、粘度、失水量和固相含量及其分散性能都对钻速具有不同的影响。
①钻井液密度对钻速的影响提高钻井液密度将增加井底压差,使钻速相应下降。
降低钻井液密度虽能提高钻速,但受地质条件的限制,不能任意降低。
②钻井液粘度对钻速的影响钻井液粘度并不直接影响钻速,它是通过对循环系统压耗和井底净化等作用的影响而间接影响钻速。
在地面功率一定的条件下,降低钻井液粘度可以降低循环系统的压耗,提高钻头压力降,从而使钻速相应提高。
③钻井液固相含量及其分散性对钻速的影响实践证明,钻井液固相含量对钻速影响较大,因此必须严格控制固相含量。
钻井液中不仅固相含量对转速有影响,固体颗粒的分散度对钻速有影响。
实验证明,钻井液内小于m1 的固相颗粒越多,对钻速的影响越大(约大12倍左右)。
固相含量相同时,分散性钻井液比不分散钻井液的钻速低,固相含量越小,两者差别约大。
为了提高转速,应尽量采用低固相不分散钻井液。
此外,钻井液失水等对钻速都有一定影响。
但这些性能与钻井液粘度、固相含量及分散性等因素有关,增加钻井液失水常会钻井液粘度,因此难于测定他们对钻速的独立影响。
钻井实践证明,钻井液性能是影响钻速的极重要因素。
但钻井液性能常受井下工作条件的影响,难于严格控制,因此至今尚未有能确切反映钻井液性能影响规律的数学模式作为优选钻井液性能的客观依据,这是优选钻进参数中需要进一步研究解决的重要课题。
§2.2 PDC钻头的损坏PDC钻头的损坏情况很多,原因也各不相同,主要有断齿、泥包、冲蚀、喷嘴或通道堵塞、喷嘴周围及本身损坏等。
断齿问题:PDC钻头钻进过程中要承受各种交变载荷,这些都直接会导致断齿。
同时钻头还要受到涡动,岩削的冲击,研磨和泥浆的冲蚀,虽然这些破坏在初期不会导致断齿,但最终往往是以断齿结束。
钻头泥包问题:所谓“钻头泥包”,就是钻头在钻进过程中,切削岩石的切削力很大,从可变形的塑性岩石中挤出水,导致岩削紧贴在钻头体上,若岩削未及时排除,会越积越多,产生泥包。
泥包对钻头的负面影响很大,常可导致三个方面的问题:1.在钻头上堆积了大量的切削,使切削齿不能接触地层,导致机械钻井速度下降;2.在钻头上堆积大量的粘屑,使其像油箱内的活塞似的工作,在起下钻的时导致压力波动和轴吸压力;3.钻头泥包生成后,钻井液不能充分冷却PDC复合片,直接影响复合片的寿命。
涡动问题:1987年,美国的BREET提出这种现象是由于PDC钻头的涡动现象造成的,他认为涡动的原因是随着钻头的旋转,钻头的瞬时旋转中心在钻头工作面上的位置不断发生变化,造成钻头作不规则的旋转运动。
钻头在钻进过程受深度侧向不平衡力的作用而被推向井壁,钻头的一侧与壁间发生摩擦。
钻头在侧向不平衡力、侧向摩擦力、转动扭矩的联合作用下产生不规则运动,其瞬时旋转中心不再是钻头的几何中心,此时的运动状态就称为涡动,而且涡动一旦产生就很难停止。
同时,由于较高的转速,钻头涡动运动产生很大的离心力,将钻头一侧推向井壁,产生更大的摩擦力,从而进一补增强钻头涡动,最终造成钻头的破坏。
射流反弹破坏问题:在PDC钻头的初始阶段,由于水力设计的不合理,过大的射流作用在井底,部分形成漫流,部分则反弹作用到钻头的表面,高速射流直接冲蚀钻头,造成钻头的中心部位首先破坏,从而使整个钻头功能丧失。
§2.3本章小节本章介绍了PDC钻头设计必然涉及的、在进行钻头设计时必须遵守的基本原则,如:切削齿的布置、出刃、排列方向、转速、水力参数、压差对钻速的影响,以及喷射钻井技术和流道形状的设计原则等等。