柔性制造系统FMS教学内容
(国内标准)FMS实训教学指导书

(国内标准)FMS实训教学指导书实训教学指导书机电一体化柔性装配系统PLC控制天津市龙洲科技仪器有限公司目录机电一体化柔性装配系统概述 (1)第一单元上料单元 (5)一、单元简介 (5)二、实训目的 (7)三、实训设备 (7)四、实训内容与步骤 (8)五、控制要求 (9)六、I/O编号分配表 (14)第二单元下料单元 (16)七、单元简介 (16)八、实训目的 (18)九、实训设备 (18)十、实训内容与步骤 (18)十一、控制要求 (19)十二、I/O编号分配表 (22)第三单元加盖单元 (24)一、单元简介 (24)二、实训目的 (25)三、实训设备 (25)四、实训内容与步骤 (26)五、控制要求 (27)六、I/O编号分配表 (29)第四单元穿销单元 (31)一、单元简介 (31)二、实训目的 (32)三、实训设备 (32)四、实训内容与步骤 (32)五、控制要求 (34)六、I/O编号分配表 (36)第五单元模拟单元 (38)一、单元简介 (38)二、实训目的 (39)三、实训设备 (39)四、实训内容与步骤 (39)五、控制要求 (40)六、I/O编号分配表 (42)第六单元图像识别单元 (44)一、单元简介 (44)二、实训目的 (45)三、实训设备 (45)四、实训内容与步骤 (45)五、控制要求 (46)六、I/O编号分配表 (48)第七单元伸缩换向单元 (50)一、单元简介 (50)二、实训目的 (52)三、实训设备 (52)四、实训内容与步骤 (52)五、控制要求 (53)六、I/O编号分配表 (56)第八单元检测单元 (58)一、单元简介 (58)二、实训目的 (59)三、实训设备 (59)四、实训内容与步骤 (59)五、控制要求 (60)六、I/O编号分配表 (62)第九单元液压单元 (64)一、单元简介 (64)二、实训目的 (65)三、实训设备 (65)四、实训内容与步骤 (65)五、控制要求 (66)六、I/O编号分配表 (69)第十单元分拣单元 (71)二、实训目的 (72)三、实训设备 (72)四、实训内容与步骤 (72)五、控制要求 (73)六、I/O编号分配表 (77)第十一单元升降梯立体仓库单元 (79)一、单元简介 (79)二、实训目的 (83)三、实训设备 (83)四、实训内容与步骤 (83)五、控制要求 (85)六、I/O编号分配表 (91)第十二单元悬挂式高空搬运单元 (93)一、单元简介 (93)二、实训目的 (95)三、实训设备 (95)四、实训内容与步骤 (96)五、控制要求 (97)六、I/O编号分配表 (101)第十三单元传送单元 (103)一、转角单元 (103)第十四单元装配生产线全程连续控制 (105)一、实训目的 (105)二、实训设备 (105)三、实训内容与步骤 (105)四、控制要求 (108)五、系统全程控制中需注意的问题 (109)六、I/O编号分配表 (109)七、主站控制变量传送分配表 (109)附录 (111)附录1:上料单元电源系统图 (111)附录2:上料单元气动原理图 (112)附录3:上料单元PLC控制接线图 (113)附录4:下料单元电源系统图 (114)附录5:下料单元PLC控制接线图 (115)附录6:加盖单元电源系统图 (116)附录7:加盖单元PLC控制接线图 (117)附录8:穿销单元电源系统图 (118)附录9:穿销单元气动原理图 (119)附录10:穿销单元PLC控制接线图 (120)附录11:模拟单元电源系统图 (121)附录12:模拟单元气动原理图 (122)附录14:图像识别单元电源系统图 (124)附录15:图像识别单元PLC控制接线图 (125)附录16:伸缩换向单元电源系统图 (126)附录17:伸缩换向单元气动原理图 (127)附录18:伸缩换向单元PLC控制接线图 (128)附录19:检测单元电源系统图 (129)附录20:检测单元PLC控制接线图 (130)附录21:液压单元电源系统图 (131)附录22:液压单元油路原理图 (132)附录23:液压单元PLC控制接线图 (133)附录24:分拣单元电源系统图 (134)附录25:分拣单元气动原理图 (135)附录26:分拣单元PLC控制接线图 (136)附录27:升降梯立体仓库单元电源系统图 (137)附录28:升降梯立体仓库单元气动原理图 (138)附录29:升降梯立体仓库单元PLC控制接线图 (139)附录30:悬挂式高空搬运单元电源系统图 (140)附录31:悬挂式高空搬运单元PLC控制接线图 (141)附录32:电源系统总图 (143)附录33:电源系统用电分配图 (144)附录34:气路连接总图 (145)附录36:移动配电平台用户扩展接口分配图 (147)机电一体化柔性装配系统概述Me093399型机电一体化教学系统是以工业生产中的自动化装配生产线为原型开发的教学、实验、实训综合应用平台。
第一章 FMS柔性生产制造实训系统使用说明书

第一章 FMS柔性生产制造实训系统使用说明书一、引言FMS柔性生产制造实训系统是我公司为提高学生动手能力和实践技能而设计、生产的一套实用性实训设备。
该装置由10套各自独立而又紧密相连的工作站、一套工业化输送线和一套主控单元组成。
这10个单元分别为:供料检测单元、操作手单元、加工单元、搬运单元、图像检测单元、提取单元、安装单元、液压冲压单元、三菱6自由度工业机器人单元、自动仓储单元组成。
该实训装置的一大显著特点是:采用模块化结构设计、具有较好的柔性,即每个单元各有一套PLC控制系统独立控制。
将10个模块分开培训可以容纳较多的学员同时学习。
在基本单元模块培训完成以后,通过组建PROFIBUS DP网络,又可以将相邻的两个单元、三个单元……直至多个单元连在一起,学习复杂系统的控制、编程、装配和调试技术。
由于该系统囊括了机电一体化专业学习中所涉及的诸如电机驱动、气动、PLC(可编程控制器)、传感器、等多种技术,给学生提供了一个典型的综合科技环境,使学生将学过的诸多单科专业知识在这里得到全面认识、综合训练和相互提升。
因此该套装置非常适合对在校学生和初上岗位的工程技术人员进行培训,是培养机电一体化人才的理想设备。
通过该套系统可以学到:1.各个单元的工作原理2.各种传感器的使用3.气动元件的使用和调整4.技术技能5.学习方法等在实训过程中,通过这套系统还可以培训和发展学员如下能力;团队精神、合作精神和组织能力。
课程的进行和培训形式可按下述方式进行:1.计划2.安装3.编程4.调试5.操作6.系统维护和故障检测培训内容包括:(一)机械1.机械结构、传动原理。
2.气缸、气阀等气动控制原理。
(二)电子1.电子元件的正确连线。
柔性制造系统(FMS)

(四)布置作业
学生分组讨论,在老师做补充说明的基础上由学生代表归纳、总结
学生归纳(教师补充)
学生分组讨论,在老师做补充说明的基础上由。
10分
20分
15分
10分
2分
四.柔性制造系统(FMS:Flexible Manufacture System)
FMS是由两台以上CNC机床组成并配备有自动化物料贮运子系统的制造系统,它是适用于中小批量、较多品种加工的高柔性、高智能的制造系统。
8.1.2FMS的定义
柔性制造系统是由数控加工设备、物流贮运装置和计算机控制系统组成的自动化制造系统,它包括多个柔性制造单元,能根据制造任务或生产环境的变化迅速进行调整,适用于多品种、中小批量生产。
(二)、自主、合作、探究(讲授新课)
8.1.1FMS的形成与发展
对于大批量、少品种的生产情况,一般采用自动流水线制造设备,包括物流设备和相对固定的加工工艺,这称为刚性自动化(Fixed Automation)方式。其优点是生产效率很高,缺点是设备固定,产品更新对自动流水线改动大等。追求高生产率,是选择自动流水线最主要的依据。因此,一种灵活、适应强的FMS方式应运而生。
FMS经历了一个由简到繁的发展过程,主要结构和组成有计算机数控系统(CNCS)、柔性制造单元(FMC)、柔性制造生产线(FML)和柔性制造系统(FMS)。
一.计算机数控系统(CNCS:Computerized Numerical Control System)
二.柔性制造单元(FMC:Flexible Manufacturing Cell)
三.FMS的作用
FMS是一个计算机化的自动化制造系统,能以最少的人工干预加工任一范围的零件族工件。FMS的加工系统包括铣削加工中心、车削加工中心、主轴箱更换式机床等设备。加工系统中所需设备的类型、数量、尺寸等均由被加工零件的类型、尺寸范围和批量大小来决定。目前主要有两类零件在FMS中加工,即棱柱体零件(包括箱体形、平板形等)和回转体类零件。因此,加工系统的结构既取决于被加工零件的类型、形状、尺寸、精度要求,也取决于批量大小及FMS的自动化程度。FMS既可由铣削加工中心(MC)或车削加工中心(TC)等同一类型的设备组成,也可由数控机床、其他专用设备、加工中心等多类型的设备组成。加工系统担任把原材料转化为最终产品的任务,是FMS的基石。
计算机集成制造技术-柔性制造系统

FMS的配置与投资
系统成本:USD 1797195.00 (从表3-5中扣除C项)
确定FMS总经济效益计算项目
直接劳动工时费 调整工时费 间接劳动费用 生产准备费 场地费 生产维持费 库存费 工装夹具费用 废品损失费用
1、直接劳动工时费计算
现有生产系统的直接劳动需求
2、调整工时费
3、间接劳动费用
4、生产准备费
5、场地费用
6、生产维持费
7、库存费用
8、工装夹具费用
9、废品损失费用
FMS年成本节省总值
投资回收率ROR (Rate of Recycle)
ROR = P/C
式中 P – 平均年盈利; C – 第一次投资成本。
FMS的组成
通常由四大部分组成: 加工单元; 自动物料运输及管理系统; 计算机控制与管理装置; 辅助工作站。
FMS的加工单元
加工单元是FMS的主体,用以进行零件 的机械加工。
加工单元的机床必须具备的条件:
①具有CNC计算机数控装置,并且有能与计 算机直接通信的DNC接口装置;
②具有自动工件托盘交换装置(APC)及自动 刀具交换装置(ATC);
I、C、O、M码
I — 输入 C — 控制 O — 输出 M — 机制
AMS系统结构
AMS厂房平面布置图
ห้องสมุดไป่ตู้
FMS的技术经济效益核算项目
FMS总投资 FMS总经济效益 投资回收率 综合评介结论
FMS总投资
示例的系统目标: 建立新的FMS系统,用以代替现行的由两
条传统生产线组成的生产系统,生产箱体零 件,年产量为19000件。
柔性制造系统FMS教学内容

柔性制造系统FMS教学内容柔性制造系统F M S柔性制造系统(FMS)1.概述1.1 柔性制造系统的发展1967年,英国莫林斯公司⾸次根据威廉森提出的FMS基本概念,研制了“系统24”。
其主要设备是六台模块化结构的多⼯序数控机床,⽬标是在⽆⼈看管条件下,实现昼夜24⼩时连续加⼯,但最终由于经济和技术上的困难⽽未全部建成。
同年,美国的怀特·森斯特兰公司建成 Omniline I系统,它由⼋台加⼯中⼼和两台多轴钻床组成,⼯件被装在托盘上的夹具中,按固定顺序以⼀定节拍在各机床间传送和进⾏加⼯。
这种柔性⾃动化设备适于在少品种、⼤批量⽣产中使⽤,在形式上与传统的⾃动⽣产线相似,所以也叫柔性⾃动线。
⽇本、前苏联、德国等也都在60年代末⾄70年代初,先后开展了FMS的研制⼯作。
1976年,⽇本发那科公司展出了由加⼯中⼼和⼯业机器⼈组成的柔性制造单元(简称FMC),为发展FMS提供了重要的设备形式。
柔性制造单元(FMC)⼀般由1~2台数控机床与物料传送装置组成,有独⽴的⼯件储存站和单元控制系统,能在机床上⾃动装卸⼯件,甚⾄⾃动检测⼯件,可实现有限⼯序的连续⽣产,适于多品种⼩批量⽣产应⽤。
70年代末期,柔性制造系统在技术上和数量上都有较⼤发展,80年代初期已进⼊实⽤阶段,其中以由3~5台设备组成的柔性制造系统为最多,但也有规模更庞⼤的系统投⼊使⽤。
1982年,⽇本发那科公司建成⾃动化电机加⼯车间,由60个柔性制造单元(包括50个⼯业机器⼈)和⼀个⽴体仓库组成,另有两台⾃动引导台车传送⽑坯和⼯件,此外还有⼀个⽆⼈化电机装配车间,它们都能连续24⼩时运转。
这种⾃动化和⽆⼈化车间,是向实现计算机集成的⾃动化⼯⼚迈出的重要⼀步。
与此同时,还出现了若⼲仅具有柔性制造系统的基本特征,但⾃动化程度不很完善的经济型柔性制造系统FMS,使柔性制造系统FMS的设计思想和技术成果得到普及应⽤。
迄今为⽌,全世界有⼤量的柔性制造系统投⼊了应⽤,仅在⽇本就有175套完整的柔性制造系统。
SGFMS-01 FMS柔性生产制造实训系统

SGFMS-01 FMS柔性生产制造实训系统一、产品概述FMS柔性生产系统是使用柔性制造技术中最具代表性的制造自动化系统,可实现多品种、中小批量的加工管理。
柔性制造技术是在自动化技术、信息技术及制造技术的基础上,将以往企业中相互独立的工程设计、生产制造及经营管理等过程,在计算机及其软件的支撑下,构成一个覆盖整个企业的完整而有机的系统,以实现全局动态最优化,总体高效益、高柔性,并进而赢得竞争全胜的智能制造技术。
它是当今世界制造自动化技术发展的前沿科技。
本实训系统是专门为职业院校、职业教育培训机构研制的FMS柔性生产实训系统,根据机电类、自动化类、先进制造类行业、企业中工业自动化应用的特点,对柔性制造技术的工作过程进行研究,对工业现场设备进行提炼和浓缩,并针对实训教学活动进行专门设计,融机、光、电、气,包含了PLC、机器人、传感器、气动、工业控制网络、电机驱动与控制、计算机等诸多技术领域,整个系统由MES生产管理系统、WINCC监控系统、主控PLC和下位PLC通过网络通讯技术构成一个完整的多级计算机控制系统,通过训练,使学生了解FMS的基本组成和基本原理,让学生全面掌握机电一体化技术的应用开发和集成技术,帮助学生从系统整体角度去认识系统各组成部分,从而掌握机电控制系统的组成、功能及控制原理。
可以促进学生在机械设计、电气自动化、自动控制、机器人技术、计算机技术、传感器技术、数控技术等方面的学习,并对电机驱动及控制技术、PLC 控制系统的设计与应用、计算机网络通信技术和现场总线技术、高级语言编程等运用技能得到实际的训练,激发学生的学习兴趣,使学生的机电系统的设计、装配、调试能力均能得到综合提高。
本实训系统是一种典型的FMS柔性生产实训系统,它由上料单元、检测分拣单元、搬运单元、数控加工单元、图像处理单元、机器人装配单元、条形码识别单元、物流仓储单元组成,配有变频调速板链式传输线构成环形生产线。
上述机构均安装在工业型材桌面上,系统中的机械结构、电气控制回路、执行机构完全独立,采用工业标准件设计。
柔性制造系统FMS方案
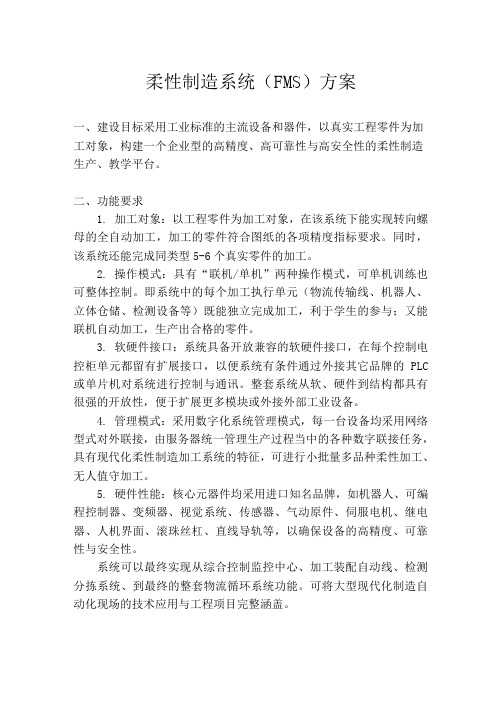
柔性制造系统(FMS)方案一、建设目标采用工业标准的主流设备和器件,以真实工程零件为加工对象,构建一个企业型的高精度、高可靠性与高安全性的柔性制造生产、教学平台。
二、功能要求1.加工对象:以工程零件为加工对象,在该系统下能实现转向螺母的全自动加工,加工的零件符合图纸的各项精度指标要求。
同时,该系统还能完成同类型5-6个真实零件的加工。
2.操作模式:具有“联机/单机”两种操作模式,可单机训练也可整体控制。
即系统中的每个加工执行单元(物流传输线、机器人、立体仓储、检测设备等)既能独立完成加工,利于学生的参与;又能联机自动加工,生产出合格的零件。
3.软硬件接口:系统具备开放兼容的软硬件接口,在每个控制电控柜单元都留有扩展接口,以便系统有条件通过外接其它品牌的PLC 或单片机对系统进行控制与通讯。
整套系统从软、硬件到结构都具有很强的开放性,便于扩展更多模块或外接外部工业设备。
4.管理模式:采用数字化系统管理模式,每一台设备均采用网络型式对外联接,由服务器统一管理生产过程当中的各种数字联接任务,具有现代化柔性制造加工系统的特征,可进行小批量多品种柔性加工、无人值守加工。
5.硬件性能:核心元器件均采用进口知名品牌,如机器人、可编程控制器、变频器、视觉系统、传感器、气动原件、伺服电机、继电器、人机界面、滚珠丝杠、直线导轨等,以确保设备的高精度、可靠性与安全性。
系统可以最终实现从综合控制监控中心、加工装配自动线、检测分拣系统、到最终的整套物流循环系统功能。
可将大型现代化制造自动化现场的技术应用与工程项目完整涵盖。
、加工零件及技术要求图1零件图1耳-14¥1——貝曙闵星于埋盏話秦黑空畫益扯二弓X S 晞盂囂釁s i i s m s p l -薪器•雷+器書“ 匸至E:劈期5&沪「二70」徒叭眇他嘰*皆強堂工n*+5H三1—X L -L .1-sj ri.H 啊*"•甘・>1I ;群i 更“6fifjl*010毎*ltllKit.钻孔、攻丝铁平而k端而,内孔外圆及外圆 槽图3加工部位示意图零件外径尺寸基本在①50-①200之间,长度在80-200之间,材料为20CrMnTi。
十四.柔性制造系统(FMS)

刀具: 模块式(TMS):刀柄,刀杆,接长杆,接上套,刀夹,刀 模块式(TMS):刀柄,刀杆,接长杆,接上套,刀夹,刀 体,刀头,刀刃等. 整体式(TSG):镗铣类整体数控工具系统 整体式(TSG):镗铣类整体数控工具系统 夹具:统一基准,敞开性好 夹具:统一基准,敞开性好
– – 托盘:运输载体,各单元的接口. 托盘:运输载体,各单元的接口. 组合夹具:
ISO托盘的标准:ISO/DIS8526-1(2) ISO托盘的标准:ISO/DIS8526完全标准化的元件组合而成. 基本元件8 基本元件8大类:基础件,支承件,定位件,导向件,压紧 件,紧固件,合件,其他件. 两大类型: 槽系组合夹具:键和槽定位. 孔系组合夹具:孔,销定位.
1.
理想的FMS应具有8 理想的FMS应具有8种柔性:
运行柔性 系统处理其局部故障并维持继续生产原定工件族的 能力 6. 批量柔性: 在成本核算上适应不同批量的能力 7. 扩展柔性: 根据生产需要方便地模块化进行组建和扩展能力 8. 生产柔性: 系统适应生产对象变换的范围和综合能力5.二, Nhomakorabea成和类型:
基本组成: 1. 由计算机控制和管理 2. 采用了CNC控制为主的多台加工设备和其 采用了CNC控制为主的多台加工设备和其 他生产设备. 3. 系统中的加工设备和生产设备通过物料输 送装置连接.
FMS基本组成 FMS基本组成
FMS的两个主要特点:柔性和自动化 FMS的两个主要特点:柔性和自动化
- 1、下载文档前请自行甄别文档内容的完整性,平台不提供额外的编辑、内容补充、找答案等附加服务。
- 2、"仅部分预览"的文档,不可在线预览部分如存在完整性等问题,可反馈申请退款(可完整预览的文档不适用该条件!)。
- 3、如文档侵犯您的权益,请联系客服反馈,我们会尽快为您处理(人工客服工作时间:9:00-18:30)。
柔性制造系统F M S柔性制造系统(FMS)1.概述1.1 柔性制造系统的发展1967年,英国莫林斯公司首次根据威廉森提出的FMS基本概念,研制了“系统24”。
其主要设备是六台模块化结构的多工序数控机床,目标是在无人看管条件下,实现昼夜24小时连续加工,但最终由于经济和技术上的困难而未全部建成。
同年,美国的怀特·森斯特兰公司建成 Omniline I系统,它由八台加工中心和两台多轴钻床组成,工件被装在托盘上的夹具中,按固定顺序以一定节拍在各机床间传送和进行加工。
这种柔性自动化设备适于在少品种、大批量生产中使用,在形式上与传统的自动生产线相似,所以也叫柔性自动线。
日本、前苏联、德国等也都在60年代末至70年代初,先后开展了FMS的研制工作。
1976年,日本发那科公司展出了由加工中心和工业机器人组成的柔性制造单元(简称FMC),为发展FMS提供了重要的设备形式。
柔性制造单元(FMC)一般由1~2台数控机床与物料传送装置组成,有独立的工件储存站和单元控制系统,能在机床上自动装卸工件,甚至自动检测工件,可实现有限工序的连续生产,适于多品种小批量生产应用。
70年代末期,柔性制造系统在技术上和数量上都有较大发展,80年代初期已进入实用阶段,其中以由3~5台设备组成的柔性制造系统为最多,但也有规模更庞大的系统投入使用。
1982年,日本发那科公司建成自动化电机加工车间,由60个柔性制造单元(包括50个工业机器人)和一个立体仓库组成,另有两台自动引导台车传送毛坯和工件,此外还有一个无人化电机装配车间,它们都能连续24小时运转。
这种自动化和无人化车间,是向实现计算机集成的自动化工厂迈出的重要一步。
与此同时,还出现了若干仅具有柔性制造系统的基本特征,但自动化程度不很完善的经济型柔性制造系统FMS,使柔性制造系统FMS的设计思想和技术成果得到普及应用。
迄今为止,全世界有大量的柔性制造系统投入了应用,仅在日本就有175套完整的柔性制造系统。
国际上以柔性制造系统生产的制成品已经占到全部制成品生产的75%以上,而且比率还在增加。
1.2 柔性制造系统的定义柔性制造系统(简称FMS)是由数控加工设备、物料储运装置和计算机控制系统等组成的自动化制造系统。
它包括多个柔性制造单元,能根据制造任务或生产的变化迅速进行调整,适用于多品种中、小批量生产。
(依据:中华人民共和国国家军用标准-武器装备柔性制造系统术语)美国国家标准局(United States National Bureau of Standards)认为是:“由一个传输系统联系起来的一些设备(通常是具有换刀装置的加工中心)。
传输装置把工件放在托盘或其它联接装置上送到各加工设备,使工件加工准确、迅速和自动。
中央计算机控制机床和传输系统,可同时加工几种不同的工件”。
它的出现标志了机械制造行业进入了一个新的发展阶段,克服了原来机械生产线只适合于大批量生产的刚性特征,能够适应中小批量、多品种的柔性生产方式,而且将手工操作减少到最低,具有很高的自动化特征。
随着社会对多品种、中小批量产品的认同,对短生产周期、低制造成本的需求增加,加上微电子技术、计算机技术、通信技术、机械与控制设备技术的日益成熟,柔性制造技术得到了广泛的应用。
2.FMS的功能及优点2.1 FMS的功能(1)能自动控制和管理零件的加工过程,包括制造质量的自动控制、故障的自动诊断和处理、制造信息的自动采集和处理;(2)通过简单的软件系统变更,便能制造出某一零件族的多种零件;(3)自动控制和管理物料(包括工件与刀具)的运输和存储过程;(4)能解决多机床下零件的混流加工,且无需增加额外费用;(5)具有优化的调度管理功能,无需过多的人工介入,能做到无人加工。
2.2 FMS的优点采用柔性制造系统有许多优点,主要有以下几个方面:1)设备利用率高一组机床编入柔性制造系统后的产量,一般可达这组机床在单机作业时的三倍。
柔性制造系统能获得高效率的原因,一是计算机把每个零件都安排了加工机床,一俟机床空闲,即刻将零件送上加工,同时将相应的数控加工程序输入这台机床。
二是由于送上机床的零件早已装卡在托盘上(装卡工作是在单独的装卸站进行),因而机床不用等待零件的装卡。
2)减少设备投资由于设备的利用率高,柔性制造系统能以较少的设备来完成同样的工作量。
把车间采用的多台加工中心换成柔性制造系统,其投资一般可减少三分之二。
3)减少直接工时费用由于机床是在计算机控制下进行工作,不需工人去操纵。
唯一用人的工位是装卸站。
这就减少了工时费用。
4)减少了工序中在制品量,缩短了生产准备时间和一般加工相比,柔性制造系统在减少工序间零件库存数量上有良好效果。
有的减少了80%。
这是因为缩短了等待加工时间5)改进生产要求有快速应变能力柔性制造系统有其内在的灵活性,能适应由于市场需求变化和工程设计变更所出现的变动,进行多品种生产。
而且还能在不明显打乱正常生产计划的情况下,插入备件和急件制造任务。
6)维持生产的能力许多柔性制造系统设计成具有当一台或几台机床发生故障时仍能降级运转的能力。
即采用了加工能力有沉余度的设计,并使物料传送系统有自行绕过故障机床的能力,系统仍能维持生产。
7)产品质量高减少零件装卡次数,一个零件可以少上几种机床加工,设计更好的专用夹具,更加注意机床和零件的定位都有利于提高零件的质量。
8)运行的灵活性运行的灵活性是提高生产率的另一个因素。
有些柔性制造系统能够在无人照看的情况下进行第二和第三班的生产。
9)产量的灵活性车间平面布局规划得合理,需要增加产量时,增加机床,以满足扩大生产能力的需要。
2.3 FMS柔性的体现(1)机床的柔性,系统中的机床通过配置相应的刀具、夹具、NC程序等,即可加工给定零件族中的零件。
生产需求发生变化时,系统可以方便地扩展、收缩或重构。
(2)加工柔性,以不同加工工序和工艺加工一个零件的能力或在给定的一个工艺规划下以不同的加工路线实现零件的加工(制造工作站间和加工功能间的互换和替代)。
(3)产品的柔性,能够经济和迅速地转变生产产品。
(4)零件流动路线柔性,系统在加工零件过程中出现局部故障时,能重新选择工件路径并继续加工。
(5)产量柔性,运行系统适应不同产量并具有好的操作效益。
(6)扩展的柔性,能够在需要时容易地、模块化地扩展系统的可能性。
(7)操作柔性,能对每一种零件改变工序顺序。
(8)生产柔性,FMS能够生产各类零件。
(9)故障控制柔性,当系统中的设备出现故障时,制造系统对故障的处理能力。
3.FMS的分类3.1 按系统的规模(1)FMC柔性制造单元(Flexible Manufacturing Cell)一般是由1~2台数控机床、加工中心、工业机器人及物料运输存贮设备等组成。
数控加工设备间由小规模的工件自动运输装置连接,并由计算机对它们进行生产控制和管理,具有适应加工多品种产品的灵活性。
可将其视为一个规模最小的FMS,系统对外设有接口,可与其它单元组成FMS。
它是FMS向廉价化小型化方向发展的一种产物。
FMC问世并应用于生产比FMS晚6~8年。
其特点是实现单机柔性自动化,迄今已进入普及应用程度。
FMC有两大类:加工中心配上托盘交换系统APC(Automatic Pallet Changer)(3-1)具有托盘交换系统的FMC数控机床配工业机器人(3-2)由NC机床和ROBOT组成的FMC(2)FMSFMS通常包括4台或更多的数控加工设备(加工中心与切削中心等、FMM或FMC,是由FMC为子系统构成的系统。
FMS的控制、管理功能也比FMC强,对数据管理与通信网络的要求更高。
由集中的控制系统及物料系统连接起来,可在不停机的情况下实现多品种、中小批量的加工管理。
FMS是使用柔性制造技术最具代表性的制造自动化系统。
(3)FML柔性制造生产线(Flexible Manufacturing Line)是处于单一或少品种大批量非柔性自动线与中小批量多品种FMS之间的生产线。
它是以离散型生产中的FMS和连续性生产过程中的分散型控制系统(DCS)为代表,其特点是实现生产线柔性化及自动化,但柔性较低,专用性较强、生产率较高、生产量较大,相当于数控化的自动生产线,一般用于少品种、中批量生产。
因此,可以说FML相当于专用FMS,对物料系统的柔性要求低于FMS,但生产效率更高。
(4)FMF柔性制造工厂(Flexible Manufacturing Factory)是以FMS为子系统构成,柔性制造由FMS扩大到全厂范围。
配以自动化立体仓库,用计算机系统进行有机的联系,采用从订货、设计、加工、装配、检验、运送至发货的完整FMS。
实现全厂范围内的生产管理过程、设计过程、制造过程和物料运储过程的全盘自动化,即实现自动化工厂的目标。
3.2 按应用对象分类(1)切削加工FMS(2)钣金加工FMS(3)焊接FMS(4)柔性装配系统等4.FMS的组成和结构4.1 FMS的组成柔性制造系统的主要组成:(1)工作站(2)物料传送系统(3)计算机控制设备(4)管理及控制软件(5)其它重要单元4.1.1 硬件系统制造设备:数控加工设备(如加工中心)、测量机、清洗机等;自动化储运设备:传送带、有轨小车、AGV、搬运机器人、立体库、中央托盘库、物料或刀具装卸站、中央刀库等;计算机控制系统及网络通信系统。
简单介绍如下:加工系统柔性制造系统采用的设备由待加工工件的类别决定,主要有加工中心、车削中心或计算机数控(CNC)车、铣、磨及齿轮加工机床等,用以自动地完成多种工序的加工。
磨损了的刀具可以逐个从刀库中取出更换,也可由备用的子刀库取代装满待换刀具的刀库。
车床卡盘的卡爪、特种夹具和专用加工中心的主轴箱也可以自动更换。
物料系统物料系统用以实现工件及工装夹具的自动供给和装卸,以及完成工序间的自动传送、调运和存贮工作,包括各种传送带、自动导引小车、工业机器人及专用起吊运送机等。
储存和搬运系统搬运的物料有毛坯、工件、刀具、夹具、检具和切屑等;储存物料的方法有平面布置的托盘库,也有储存量较大的巷道式立体仓库。
毛坯一般先由工人装入托盘上的夹具中,并储存在自动仓库中的特定区域内,然后由自动搬运系统根据物料管理计算机的指令送到指定的工位。
固定轨道式台车和传送滚道适用于按工艺顺序排列设备的柔性制造系统,自动引导台车搬送物料的顺序则与设备排列位置无关,具有较大灵活性。
工业机器人可在有限的范围内为1~4台机床输送和装卸工件,对于较大的工件常利用托盘自动交换装置(APC)来传送,也可采用在轨道上行走的机器人,同时完成工件的传送和装卸。
4.1.2 软件系统系统支持软件:操作系统、网络操作系统、数据库管理系统等;FMS运行控制系统:动态调度系统、实时故障诊断系统、生产准备系统,物料(工件和刀具)管理控制系统等。