川大机械制造工程学复习要点
机械制造工程学复习重点

第一章金属切削的基本原理第一节金属切削的基本概念一、金属切削的基本概念1、切削运动:金属切削时所需要的运动。
主运动:实现切削的最基本运动;方向:假设工件不动,刀具相对工件的运动方向.进给运动:实现主运动连续切削的运动;方向:假设工件不动,刀具相对于工件的运动方向。
2、切削过程中的工件表面已加工表面过渡表面待加工表面3、刀具切削部分的构成(三面两刃一尖)1)前刀面Ar 铁屑流出的表面2)主后刀面Aα与过渡表面对应的刀面3)副后刀面Aα'与已加工表面对应的刀面4)主切削刃S 前刀面与主后刀面的交线Ar×Aα5)副切削刃S'前刀面与副后刀面的交线Ar×Aα'6)刀尖主切削刃与副切削刃的交点S×S'4、刀具标注角度1)参考系的建立假定运动条件(不考虑进给运动)A、假定条件刀尖过截面圆心假定安装条件(理想安装刀具中心线垂直于工件轴线B、参考平面(描述刀具切削部分的空间位置)a、切削平面Ps:过主切削刃上的选定点与过渡表面相切的表面.b、基面Pr:(过切削刃上选定点,垂直于主运动向量的表面)c、正交平面Po:(过切削刃上选定点分别与Ps、Pr垂直)2)角度标注主偏角KrA、在Pr内:(如图1)副偏角Kr'(图1)B、在Ps面内刃倾角λs:Pr与S分别向Ps投影下的夹角(若刀尖为S上的最高点则λs为正,反之为负)前角γ0:前刀面Ar与Pr分别向P0投影C、在Ps面内(如图2) 后角α0:主后刀面Aα与ps分别向P0上投影(图2)D、在P0'内:副后角α0'如图3E、刀具工作角(切削角)(1)进给运动对工作角度的影响:若刀尖位置低于工件轴线所在水平面则其切削前角减小后角增大。
(2)安装位置对工件工作角的影响中心不等高(图3)刀杆中心线与进给方向不垂直二、切削用量1、切削速度v S上的选定点与主运动的速度;方向:主运动方向m/s2、进给量f 进给运动的速度v f:工件每转一周刀具相对工件轴向的位移量车削mm/r 刨削mm/行程钻mm/min3、背吃刀量a r 待加工表面与已加工表面的垂直距离.三、切削层参数切削层的截面尺寸(如图4)1、切削厚度a c2、切削宽度a w3、切削面积AcAc =a c×a w=f ×a p图4七、金属切除率Z w单位时间内所切除金属材料的体积Z w=v×f×ap mm3/min八、切削方式自由切削:只有一条直线刃参与切削非自由切削:两条以上直线刃同时参与切削,如铣削加工、车球头等.直角切削:λs=00斜角切削:λs≠00第二节金属切削变形理论一、切削变形的特点(摩擦、剪切、变形)第一变形区(工件上被剥离的部分通过该区变成铁屑)第二变形区(铁屑与A r发生摩擦的区域)第三变形区(已加工表面与Aα摩擦的区域)二、切削变形过程剪切滑移过程(剪切滑移面)剪切角:剪切滑移面与切削方向的夹角。
机械制造工程学复习要点

机械制造工程学复习要点第一章金属切削加工的基础1)理解并识记各种加工方法中主运动与进给运动。
2)切削三要素:切削速度、进给量和背吃刀量3)刀具切削部分的组成;评定六个角度所需的坐标系定义;六个基本角度的定义;刀具材料应具备的性能要求;常用的刀具材料(硬质合金和高速钢);结构复杂的刀具一般是由高速钢整体制作;硬度最高是金刚石,但不能加工黑色金属;第二章金属切削过程的基本规律1)三个变形区,弹塑形变形集中在第一变形区;积屑瘤,前刀面磨损在第二变形区;加工硬化,残余应力集中在第三变形区。
2)切屑的类型;积屑瘤的定义及产生原因;最高温度在距前刀面上距离切削刃一定距离处;切削三要素对刀具寿命、切削温度的影响指数;刀具正常磨损的形式(前刀面、后刀面与前后刀面磨损);刀具磨损的原因(磨粒磨损等);刀具磨损的阶段;刀具磨钝标准的定义;刀具寿命和刀具总寿命之间关系;切削液的作用;刃倾角的功用;刃倾角的正负与切屑流向的关系;选择切削用量的原则;第三章机床与刀具1)GB/T15375-1994分11大类;机床型号中首尾字母的含义;内外传动链;车刀按结构分类;钻削时主运动和进给运动均是由刀具完成;麻花钻的切削部分的结构组成,几何参数,标准顶角;扩孔钻与麻花钻相比无横刃齿数多;扩孔能纠正孔的位置误差,而铰孔、浮动镗孔、珩磨孔及拉孔均不能纠正孔的位置误差;钻、扩、铰、拉孔属于定尺寸刀具加工,而镗孔则不是;孔径大于100mm时,采用镗孔;坐标镗床可以用来划线及测量孔距;拉削的方式;铣削的分类(顺铣与逆铣);顺铣与逆铣的不同点;单个磨粒磨削的过程(滑擦、耕犁和切削);磨削工艺特点;无心磨削的特点,如工件无需打中心孔,生产效率高等;2)砂轮的五个特性;粒度定义,粒度选择原则,砂轮硬度及组织的定义;齿轮技术要求;常见的齿形曲线及加工方法;插齿与滚齿的异同;剃齿与磨齿;齿轮加工时的安装角;第四章机械加工精度1)加工精度、加工误差、误差敏感方向;经济加工精度、尺寸精度、形状精度等定义;加工原理误差的定义;机床主轴的误差(轴向、径向与摆动);导轨误差(水平、垂直与平行);2)刀具的制造误差及磨损,刚度定义,工艺系统刚度与组成部分刚度之间的关系(取决与薄弱环节);工艺系统的热源(切削热、摩擦热和外部热源);刀具与工件的影响,减小工艺系统热源的措施;内应力定义及产生;工序能力系数;第五章机械加工表面质量表面质量的含义;表面质量与零件耐磨性、粗糙度;表面层的加工硬化及其评定指标;磨削烧伤的定义及磨削烧伤的形式(退火、回火与淬火);表面残余应力第六章机械加工工艺规程的制订1)生产过程、工艺过程的定义;工序、工步、进给、安装与工位的定义;生产纲领的定义与作用;工艺规程的定义;2)工艺规程的作用;制定机械加工工艺规程的原则;3)基准的定义、类型及其定义4)粗基准定义及其选取原则;精基准定义及其选取原则;研磨、铰孔是自为基准使用的例子。
四川大学机械制造基础重点(背)

冷加工部分1.在三个切削分离中,车外圆时主切削力最大,磨外圆时背向力最大2.磨具硬度是磨具工作时在外力作用下磨料脱离的难易程度3.车削时,切削热传出的途径中所占比例最大的是切屑4.车外圆时,能使切屑流向工件待加工表面的几何要素是刃倾角大于05.安装外车槽刀时,刀尖高于工件回转中心时,与其标注角度相比,其工作角度将会是前角变大,后角变小6.车削加工中,减小残留面积的高度,减小表面粗糙度值,可使用的正确方法有:1. 减小进给量2.减小背吃刀量7.刀具主偏角的选择会影响背向力和主切削刃平均负荷大小8.确定车刀前角大小的主要依据有:1. 粗加工时的前角比精加工小2. 高速钢刀具前角比硬质合金刀具小3. 加切削液时前角应加大9.机床床身导轨面的常用精加工方法有:1. 导轨磨削2. 宽刀细刨10.刀具切削部位材料应具备的性能是:高的硬度,高的耐磨性,高的耐热性,足够的强度和韧性和一定的工艺性能11.产生积屑瘤的条件是:1. 切削塑性金属2. 中等切削速度粗加工时可利用积屑瘤,精加工时应尽量避免积屑瘤12.切削热的三个主要来源是:1. 基本变形区2. 切削与前刀面的摩擦变形区3. 工件已加工表面与刀具后刀面间的摩擦13.固结磨具中的气孔在切削过程中起裸露磨粒棱角,容屑,散热的作用14.拉削加工中,其主运动:拉刀的直线运动,其进给运动:拉刀每齿升高量来实现15.调质一般安排在粗加工之后16.在基面内测量的角度有主偏角和副偏角17.改变主偏角的大小可以改变主切削刃参加切削的长度18.淬火热处理一般安排在半精加工之后19.工件装夹中,最常用的正确定位方法有完全定位和不完全定位20.可以加工平面的机床有铣床,刨床和车床21.在切削平面内测量的角度是刃倾角22.成形磨削时,应选硬度高粒度号大的砂轮23.退火一般安排在毛坯制造之后,淬火一般安排在半精加工之后24.切削热对切削过程的影响主要表现在:1. 加速刀具磨损2. 有利于防止工件表面变形硬化 3. 导致工件产生热变形,或桌上工件表面影响加工精度25.切削力和切削热的产生主要来自材料的变形和工件、刀具与切屑面的摩擦两个方面26.安排箱体类零件工艺过程时,一般遵循:先面后孔和先粗后精27.切削加工是如何划分阶段的?目的和意义如何?为了保证切削加工质量,按尺寸公等级和表面粗糙度Ra值来划分阶段1. 避免因残余应力的释放而影响加工精度2. 避免粗加工时较大的夹紧力和切削力所引起工件的弹性变形和热变形对精度的影响3. 先粗加工一遍,可及时发现毛坯的内在缺陷而决定取舍,以免浪费更多的工时4. 可合理使用机床5. 便于工艺过程中热处理工序的安排28.简述电火花加工、电解加工、超声波加工和激光加工的基本原理电火花加工:在加工过程中,使工具与工件之间不断产生脉冲性的火花放电,靠放电时局部、瞬时产生的高温把金属蚀除下来。
《机械制造工程学》复习提纲.doc

《机械制造工程学》复习提纲选用教材:卢秉恒主编.机械制造技术基础(第3版).北京:机械工业出版社,2008 参考教材:熊良山等主编.机械制造技术基础.武汉:华屮科技大学出版社,2007 冯之敬主编.机械制造工程原理(第2版).北京:清华大学出版社,2008 第1章机械加工方法制造活动的定义;零件的制造过程;机械加工方法。
重点要求:零件的成形原理和常见机械加工方法。
第2章金属切削原理与刀具1.刀具结构与种类:切削运动、切削用量和切削层参数;刀具切削部分组成、刀具标注角度参考系和刀具标注角度;刀具种类(包括车刀结构特点、麻花钻结构特点及其刀具角度、铳刀结构特点及其刀具角度、拉刀结构特点及其刀具角度、砂轮结构特点及其参数)刀具材料(包括:刀具材料应具备的性能和常用的刀具材料)2.金属切削过程及其物理现象:掌握金属切削过程的基本理论,金属切削过程的物理现象,金属切削过程屮切削用量的选择。
切削力、切削热与切削温度及其主要影响因索。
刀具磨损与刀具使用寿命。
重点要求:切削参数的定义;刀具标注角度参考系与刀具标注角度的定义;常用刀具角度的表达方法;金属切削过程三个变形区的特征及其积屑瘤产生与控制。
影响切削变形的主要因素。
第3章金属切削机床常用机床的分类、特点、基本结构和型号;机床的成形运动;形成发生线的方法。
重点要求:机床的成形运动与形成发生线的方法。
第4章机床夹具原理与设计基准的概念;工件在夹具屮的定位原理;定位误差的分析与计算;工件的夹紧。
重点要求:定位基本原理;自由度与定位方案的分析;定位误差的分析与计算。
第5章机械制造质量分析与控制工艺系统几何误差;工艺系统受力变形引起的误差;工艺系统受热变形引起的误差;加工误差的正态分布规律及其计算与分析方法;机械加工表面质量对机器使用性能的影响;影响表面粗糙度的因素;影响加工表面物理机械性能的因素。
重点要求:加工精度、加工误差和原始误差的定义;获得加工精度的方法;工艺系统受力变形对加工精度的影响;第6章工艺规程设计工艺规程及设计原则和所需的原始资料;工艺规程设计的内容和步骤;工艺路线的拟定;加工余量的确定;工序尺寸及公差的确定;吋间定额的确定;工艺方案的经济分析;保证装配精度的装配方法;装配工艺规程设计;机械加工工艺性评价;重点要求:工艺规程设计的基本概念与方法;零件工艺规程设计;机械加工工艺过程的组成;定位基准的选择原则;加工阶段的划分;工艺尺寸链分析与计算;保证装配精度的装配方法及其应用场合。
机械制造技术复习纲要
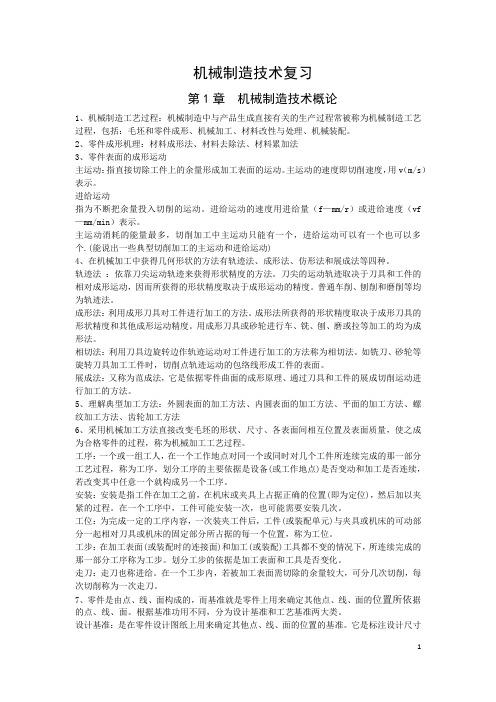
机械制造技术复习第1章机械制造技术概论1、机械制造工艺过程:机械制造中与产品生成直接有关的生产过程常被称为机械制造工艺过程,包括:毛坯和零件成形、机械加工、材料改性与处理、机械装配。
2、零件成形机理:材料成形法、材料去除法、材料累加法3、零件表面的成形运动主运动:指直接切除工件上的余量形成加工表面的运动。
主运动的速度即切削速度,用v(m/s)表示。
进给运动指为不断把余量投入切削的运动。
进给运动的速度用进给量(f—mm/r)或进给速度(vf —mm/min)表示。
主运动消耗的能量最多,切削加工中主运动只能有一个,进给运动可以有一个也可以多个.(能说出一些典型切削加工的主运动和进给运动)4、在机械加工中获得几何形状的方法有轨迹法、成形法、仿形法和展成法等四种。
轨迹法:依靠刀尖运动轨迹来获得形状精度的方法。
刀尖的运动轨迹取决于刀具和工件的相对成形运动,因而所获得的形状精度取决于成形运动的精度。
普通车削、刨削和磨削等均为轨迹法。
成形法:利用成形刀具对工件进行加工的方法。
成形法所获得的形状精度取决于成形刀具的形状精度和其他成形运动精度。
用成形刀具或砂轮进行车、铣、刨、磨或拉等加工的均为成形法。
相切法:利用刀具边旋转边作轨迹运动对工件进行加工的方法称为相切法。
如铣刀、砂轮等旋转刀具加工工件时,切削点轨迹运动的包络线形成工件的表面。
展成法:又称为范成法,它是依据零件曲面的成形原理、通过刀具和工件的展成切削运动进行加工的方法。
5、理解典型加工方法:外圆表面的加工方法、内圆表面的加工方法、平面的加工方法、螺纹加工方法、齿轮加工方法6、采用机械加工方法直接改变毛坯的形状、尺寸、各表面间相互位置及表面质量,使之成为合格零件的过程,称为机械加工工艺过程。
工序:一个或一组工人,在一个工作地点对同一个或同时对几个工件所连续完成的那一部分工艺过程,称为工序。
划分工序的主要依据是设备(或工作地点)是否变动和加工是否连续,若改变其中任意一个就构成另一个工序。
机械制造工程学基础部复习
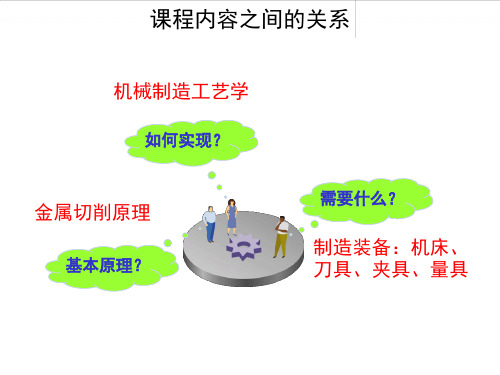
切削变形的表示方法——变形系数
剪切角、相对滑移均很难测量通过对切屑的测量 厚度变形系数:切屑厚度与切削厚度之比 长度变形系数:切削长度与切屑长度之比 切削宽度变化不大
积屑瘤现象
现象:粘结冷焊积屑瘤(积屑瘤现象) 特点:在前刀面上生成一个非常坚硬的金属堆积物,其硬度比工件硬度
高2—3.5倍,而且不是一直驻留在刀面上,而是以一定的频率反复生长 和脱落。 产生条件:1)塑性材料;2)带状切屑;3)切削速度不高 对切削过程的影响:
切削用量三要素
切削速度v、进给量 f、切削深度ap称为切削用量三要素
➢ 切削速度是刀刃上选定点相对于工件的主运动的速度 ➢ 进给速度是刀刃上选定点相对于工件的进给运动的速度 ➢ 切削深度是工件上待加工表面和已加工表面间的垂直距离
车刀的组成
车刀由刀柄(刀体)和刀头(切削部分)构成 刀头由三面二刃一尖组成
为切屑,另一支沿刀具后刀面形成已加工表面。变形复杂
➢ 第I变形区已扩展到切削层下方,使已加工表面下一部分已发生塑性变形 ➢ 刀具磨损后有一棱面,与已加工表面磨擦,也产生变形 ➢ 切削刃有钝圆半径,一方面改善散热条件,增加强度而设计的圆弧,另一方
面由于制造原因,不可能绝对锋利
钝圆半径的影响
➢ 在刀刃(设为一条线)之下的金属层不能被切下,经刃口挤压下去, 产生很大的弹塑性变形,并留在已加工表面上
➢ 经过最低点后,弹性变形部分恢复,与后刀面发生接触,同时产生 磨擦,进一步发生弹塑性变形
➢ 刀具离开后,仍有弹性恢复
钝圆半径越大,这种现象越严重 第III变形区的变形将影响:尺寸、加工硬化、表面形状、粗
糙度
切削力
切削力的来源:
➢ 弹塑性变形抗力 ➢ 磨擦阻力
川大机械制造工程学复习要点

第一章金属切削加工中的基本定义1.金属切削加工——金属切削刀具和工件按一定规律作相对运动,通过刀具上的切削刃切除工件上多余的(或预留的)金属,从而使工件的形状、尺寸精度及表面质量都合乎预定要求,这样的加工称为金属切削加工。
切削加工的目的:是被加工零件的尺寸精度、形状和位置精度、表面质量达到设计与使用要求。
2.金属切削加工过程中的两在要素:成形运动(切削运动)、刀具。
3.工件表面形状与成形方法:(1)表面都可以看成是一根母线沿着导线运动而形成的,一般情况下母线和导线可以互换,特殊表面如圆锥表面不可互换。
母线和导线统称为发生线。
(2)发生线的形成方法:轨迹法(切削刃与被加工表面为点接触,发生线为接触点的轨迹线)、成形法(曲线形的母线由切削刃直接形成,直线形的导线由轨迹法形成)、相切法(刀具边旋转边作轨迹运动,需两个独立的成形运动)、展成法(需一个独立的成形运动)。
(3)成形运动是形成发生线所需成形运动的总和。
4.切削运动:(1)主运动:刀具和工件之间产生的最主要的相对运动,它是刀具切削刃及其毗邻的刀面切入工件材料使切削层金属转变成切屑从而形成新鲜表面的运动。
特点:速度高、消耗机床功率最大、唯一、可以由刀具或工件完成。
方向:切削刃上选定点相对于工件的瞬时主运动方向。
速度:(2)进给运动:由机床或人力提供完成工件成形的运动。
特点:速度低、消耗机床功率少、一般不唯一、可由刀具或工件完成。
方向:切削刃上选定点相对于工件的瞬时进给运动方向。
5.切削深度:指已加工表面和待加工表面之间的垂直距离。
6.切削用量三要素:主运动速度v、进给量f、切削深度a p。
(参照图1-1)切削用量三要素直接影响切削力的大小、切削温度的高低、刀具磨损、刀具耐用度,同时还对生产率、加工成本、加工质量都有很大的影响。
7.刀具几何角度:(1)刀具切削部分组成:“一尖两刃三面”。
(前刀面上有切屑流出,主后刀面与加工表面相对,副后刀面与已加工表面相对)(2)角度标注参考系的建立基于两点假设:i.假定进给运动速度为零;ii.假定刀具安装底面或轴线与基面或切削平面平行或垂直。
机械制造期末复习重点.doc

—、名词解释:1、生产过程:从原材料或半成品到成品制造岀来的各有关劳动过程的总和称为工厂的生产过程。
2、单位切削力:单位切削力p是指切除单位切削层面积所产生的主切削力。
3、工序:指一个(或一纟R)工人在一个工作地点(如一台机床或一个钳工台),对一个(或同时对儿个)工件连续完成的那部分工艺过稈,称为工序。
区分工序的主要依据是:工作地点固定和工作连续。
(丁序是组成丁•艺过程的基本单元)4、安装:安装是指工件通过一次装夹后所完成的那一部分工序。
5、工位:一次装夹屮,可先后在机床上占有不用的位置进行加工,每个位置上所完成的那一部分工序称为一个工位。
6、工步:当加丁•表面、切削刀具、切削用量都不变的情况下所完成的那部分丁序,称为工步。
(T•步是构成丁•序的基本单兀)。
7、走刀:走刀(又称工作行程)是指刀具相对工件加T•表曲进行一次切削所完成的那部分工作。
(每个工步可包括一次走刀或几次走刀)。
8、生产纲领:指包括备品、备件在内的该产品的年产量。
产品的年生产纲领就是产品的年生产量。
9、单件生产:单个地生产不同结构和不同尺寸的产品10、成批生产:一年屮分批、分期地制造同一产品。
11、大量生产:全年屮重复制造同一产品。
特点:产品品种少、产量大,长期重复进行同一产品的加工。
12、机械加工工艺过程、机械加工工艺规程:用机械加T的方法,直接改变原材料或毛坯形状、尺寸和性能等,使Z变为合格零件的过程,称为机械加工T艺过程,又称T艺路线或工艺流程;规定零件机械加工工艺过程和操作方法等的工艺文件称为机械加工工艺规程13、结构工艺性:零件的结构工艺性,是指零件的形状、尺寸是否符合对质量、生产率高的要求。
14、基准:在零件图上或实际的零件上,用来确定其它点、线、血位置时所依据的那些点、线、面,称为基准。
15、设计基准:零件设计图样上用来确定其它点、线、面位置的基准,为设计基准。
16、工艺基准:是加工、测量和装配过稈屮使用的基准,又称制造基准。