Troubleshooting_Guide
哈斯机床编码器线报警处理

LAST UPDATED: 09/13/2019西格玛 5 - 轴伺服电机和电缆 - 故障排除指南电子安全性:症状表检查电缆和接头。
请参阅电源线下一节。
检查相应的放大器组件。
请参阅伺服放大器 - 故障排除指南以对放大器障排除。
检查相应的伺服电机。
请参阅伺服电机下一仅限经典哈斯控制- 机器参数不正确。
确保轴电机类型具有正确的参数。
1.确定机器是否具有西格玛-1 或西格玛-5 电机。
注意:Sigma-5 轴电机具有用于编码器插头的推锁连接器。
2.运行参数检查器并选择西格玛-1 或西格玛-5 选项。
报警103 - 105轴轴错误过大,在零返回过程中。
轴零返回方向错误。
在零返回过程中,正在制造主传感器,使轴以相反方向返回零。
检查轴主开关,确保传感器顶部没有金属芯片。
串行数据通信故障/电气噪声西格玛-5伺服电机,非接触式编码器输出串行数据信号到控制。
如果串行数据信号丢失或变得不可靠,则控件将生成串行数据通信错误。
电气噪声可能导致来自编码器的串行数据信号变得不可靠,并导致误报。
请按照下面的故障排除指南操作,以帮助消除系统中的噪音。
1.机器接地不正确。
确保接地线尺寸正确。
此外,接地线应一直运行回电气面板。
2.来自其他设备的噪音。
确保机器不与其他机器共享电气服务。
3.PCB 或电机编码器处的散散编码器数据连接器,可能导致串行数据变得不可靠。
请参阅主处理器/编码器电缆部分。
4.松动的接地或高压电源连接器会将噪音引入系统。
◦电柜检查所有接地和高压电源端子(矢量驱动器、怀尔塔接触器、变压器)是否连接松动。
等)。
◦吊坠检查端子接头是否松动。
◦主轴头检查接地和电机电源端子有没有松动。
5.的铁氧体过滤器当伺服器打开时,抑制放大器和矢量驱动器产生的高频噪声。
确保它们安装在:◦编码器数据电缆。
确保所有编码器数据电缆中都安装了铁氧体滤波器 P/N 64 1252。
◦轴电机电源线。
确保 X、Y、Z轴电机电源线 [1] 中安装了铁氧体滤波器 P/N 64-1252。
曲霉菌检测技术要点及Troubleshooting

样本采集 患者准备
样本保存、运输
报告应用
13
报告签发
样本检测
如何保证检测质量?
人 环 机
法
14
料
曲霉菌的特点
霉菌的分布
– 占空气中真菌的12%来源于百科– 空气中真菌前三甲:
Cladosporium:37% Non-sporing:22.5% Yeast:18.3%
– 灰尘中真菌前三甲:
Yeast:50.6% Cladosporium:17%
Aspergillus:12%
来源于现代医药卫生20
15
曲霉菌的检测首要重视环境问题
以下工作应在超净台内完成: 试剂盒和耗材拆包装及密封 样本取样并加处理液
16
实验前准备
样本记录表
Step 4
– 准备一份可以识别微孔板上受检血清和对照血清的图表。用 其中一孔作为阴性对照血清使用(R3),两孔作为Cut-off对 照血清(R4),一孔用于阳性对照血清(R5)。
R3<0.4; R5>1.5
10
临床GM检测流程
11
曲霉菌抗原检测试剂盒
操作注意事项及技术要点
12
实验室工作流程
• 确保使用去离子水稀释洗液 • 如果用洗板机,确保正确注入洗液 • 按照说明书要求比例进行稀释 • 弃掉污染的R9并使用新的 • 不要把剩余的显色液重新倒回试剂瓶
42
曲霉菌抗原检测试剂盒-Troubleshooting Guide
问题 可能的原因 解决方案
• 丢弃污染的终止液并更换新的 • 不要把剩余的终止液倒回试剂瓶 • 避免终止液接触金属物品
解决方案
• 确保加入了50 µl 处理后的对照上清
易拉罐封盖缺陷及原因

常见原因Double Seam Defects: Troubleshooting Guide故障/缺陷头封太松头封太紧卷封长度/高度太长卷封长度/高度太短罐盖勾边太长罐盖勾边太短罐身勾边太长罐身勾边太短沉头太深沉头太浅接缝间隙太大牙齿皱纹反向皱纹卷封不完全(滑口)快口/锐边卷封碎裂假封罐盖勾边损坏大塌边罐身罐盖配合不良歪扭罐(灌身起棱)蘑菇状翻边不规则卷封/卷封波动封边弹开张口/卷封断裂常见原因● ● ● ● ●● ●●●●●●太紧 ● ● ● ●● ●太松 ● ● ● ● ●●●轮廓太窄● ● ● ● ●轮廓太宽 ● ● ● ●● ●●●轮廓磨损● ●●●轴承磨损● ● ●●●相对于压盖头太高 ●●头道封盖滚轮相对于压盖头太低 ● ● ●●●●● ●太紧 ● ● ● ● ● 太松 ● 轮廓太宽● ●●轮廓磨损●轴承磨损●●●●●●相对于压盖头太高 ●●●二道封盖滚轮相对于压盖头太低 ●●转臂磨损●●轴承不灵活 ●●●●太长/不返回●●头道/二道封盖滚轮 唇边接触罐身 ● ●直径太大 ● ●●半径不正确●●压盖头调得太低 ●●●直径减小或磨损 ●● 上唇边磨损●压盖头油脂太多●●●●●封罐轴——间隙过大●●脱罐杆凸轮调节● ● ●●●●●●针规高度不正确● ●●●压力太小● ● ●●●压力太大 ● ●● 弹簧损坏 ●●提升装置油脂太多●● ●灌装机弹簧压力太大 ●● 进盖器 ●●● 罐盖导向调节●●●● 盖在罐身上的定位不正确 ●●●● 罐盖导向/尬身导向调节 ●●进罐链/进罐星轮同步●●●进罐星轮/封盖头同步 ● ●●蘑菇状翻边 ●●● 大塌边●● 勾边不好●●●勾边损坏 ●●●切边太大 ●●罐盖切边太小● ● ● ●密封衬料太多●● ● ●密封衬料不规则 ●●●太短 ●●● ●罐身勾边太长●●沉头过深k●● ● 交货质量/包装质量不好 ●●罐过渡/输送不好常见原因●●●润滑不正确。
troubleshooting-guide

Troubleshooting GuideOpManager is a very simple and easy-to-use application and you will simply need to install the application and get started. That still does not rule out the fact that there might be a few issues coming in the way, slowing down your objective of getting your resources monitored by OpManager. This document helps you troubleshoot the common problems that you might encounter when using OpManager.The tips are classified as follows:1. Get over initial hiccups2. Monitoring Configurations3. Alerting and NotificationsTips to get over the initial hiccupsFollowing are a few tips which may be handy to get over your initial hiccups when using OpManager. For easier navigation, these are further classified as follows:∙Starting Trouble∙Discovery∙MappingStarting Trouble!∙Failed to establish connection with Web Server. Gracefully shutting down.∙Error Code 500: Error in applying the OpManager 6.0 license over opmanager 5.6 or the version upgraded from 5.0∙Can't create tables or not all the tables are created properly' error is displayed during OpManager startup.∙Error downloading client files from BEFailed to establish connection with Web Server. Gracefully shutting downCause 1While starting OpManager as 'root' user in Linux platform, the server goes down with the following message "Failed to establish connection with web server. Gracefully shutting down ..". This is because OpManager starts its Apache Web Server as 'nobody' user and 'nobody' group. The Apache Server may not have read and execute permissions to access the files under <OpManager Home> directory. Hence, the connection to the Apache Server will not be established and the OpManager server will gracefully shut down.Solution∙Change the value of the parameter Group in httpd.conf file found under <OpManager Home>/apache/conf/backup/ directory.Group #-1 to Group nobody∙Provide executable permission to"httpd" file available under <OpManager Home>/apache/bin/ by executing the following command:chmod 755 httpdOpManager server starts successfully after performing the above mentioned steps.Cause 2If you are using Linux 8.0/9.0 :In Linux 8.0/9.0, a file named libdb.so is not bundled. In earlier versions it was bundled. This file is needed by Apache. Without this, apache does not start in Linux 8.0. This results in the issue you are facing.SolutionThe file has been bundled with the product and is present in the /lib/backup directory in the latest version of OpManager. Copy it to the /lib directory and restart OpManager.This solution has worked for those using Fedora and Madrake Linux too.If you continue to face the problem, then execute the script StartWebSvr (this will be a .bat file in Windows installation and .sh file in Linux installation) in the /apache folder of OpManager installation and send us the output.If yours is a Debian Linux, then check if libgdbm.so.2 is available under /usr/lib directory. If not, you can install the stable version of libgdmg1. Download this package from the url/stable/libs/libgdbmg1Error Code 500: Error in applying the OpManager 6.0 license over opmanager 5.6 or the version upgraded from 5.0CauseLicense issued for OpManager 6.0 fresh installation does not work when you upgrade 5.x version to 6.xSolutionThis issue is encountered when you evaluate OpManager 5.6 and subsequently apply the new license for OpManager 6.0. Follow these steps to move the database to the new fresh installation of OpManager 6.0 exe\bin1. Shut down OpManager. (If OpManager is running as a service, stop the service from ControlPanel > Services window)2. Download upgrade pack from this link,/products/opmanager/service-packs.html3. Run the script 'UpdateManager.bat (UpdateManager.sh for Linux) in the <opmanager-home>/bin folder. This opens the Update Manager tool.4. Click "Install" and then click "Browse" to select the Upgrade Pack file (the .ppm file that you'ddownloaded).5. Follow the on-screen instructions to apply the Service/Upgrade Pack.6. Once the upgrade is complete, start OpManager Server.7. Take the backup of these folders/OpManager/mysql/data/OpManager/conf//OpManager/users8. Uninstall OpManager.9. Download OpManager version 6.0 using this link/products/opmanager/download.html?pro10. Move the folders back to the new installation in the same location.11. Start OpManager and apply the license.If you feel this is cumbersome, the simplest solution would be to request OpManager 5.0 license from our license teamCan't create tables or not all the tables are created properly' error is displayed during OpManager startupThe data tables may be corrupted. You can repair the corrupt tables. Run the repairdb.bat under \bin directory. After this, run the ReInitializeOpManager.bat script in the same directory. This will remove all the tables created. Restart OpManager.Error downloading client files from BECauseThis error occurs when the database tables are corrupted. The corruption can happen due to improper shutdown of OpManager such as during power outages.SolutionThe database must be repaired and OpManager needs a restart. Here are the detailed steps:1. Stop OpManager Service2. Open a command prompt and change directory to /opmanager/bin3. Execute RepairDB.bat/sh. This repairs all the corrupt tables.4. After it finishes executing, run it once again to ensure all corrupt tables are repaired.5. Restart OpManager.Discovery∙Devices are not discovered∙Devices are identified by IP Address and not host names.Devices are not discoveredCauseThis can happen if the ping requests to device get timed out.SolutionTo resolve this, increase the ping timeout in the file /conf/ping.properties and try again.Devices are identified by IP addresses and not by host namesCauseIf DNS Server address is not set properly in the machine hosting OpManager, the DNS names of the managed devices cannot be obtained from the DNS server.The other possible reasons could be:∙The DNS Server is not reachable∙The DNS Server is down during discovery.∙The DNS Server does not exist.SolutionEnsure that the DNS Server is reachable and configure the DNS Server address properly.Mapping∙Some of my Routers are discovered as Desktops or Servers.∙How are Servers categorized in OpManager? Some servers are classified under desktops! Some of my Routers are discovered as Desktops or ServersCauseThe devices may not be SNMP enabled or the SNMP agent in the device is not responding to queries from OpManager.SolutionEnable SNMP and rediscover the device. Despite this, if you face issues, troubleshoot as follows: ∙Do you see a blue star in the device icon on the maps? This implies that the device responds to SNMP request from OpManager. The device is still not classified properly? Simply edit the category from the device snapshot page.∙If SNMP agent is not running on the router, it will be classified as a server or desktop.You can verify this by the blue star appearing on the top left corner of the device icon for the SNMP-enabled devices. To categorize the device properly, start the SNMP agent in the device.Refer to Configuring SNMP agents in Cisco Devices for details. Rediscover the device withcorrect SNMP parameters.∙If the SNMP agent is running on the router and you still do not see the blue star in the device icon, then check if the SNMP parameters are properly specified during discovery. If not,rediscover the device with correct SNMP parameters.∙The router is discovered as a server or desktop if the IP Forwarding parameter of the device is set to false. To set the value of this parameter to true1. Invoke /opmanager/bin/MibBrowser.bat2. Expand RFC1213-MIB.3. In the ip table, click ipForwarding node.4. Type 1 in the Set Value box and click Set SNMP variable on the toolbar.5. Rediscover the device with correct SNMP parameters.Similarly, for switches and printers too, enable SNMP in the device and rediscover.How are Servers categorized in OpManager? Some servers are classified under desktops! Following devices are automatically classified under servers based on response to SNMP/telnet request to the devices:∙Windows 2003 Server∙Windows 2000 Server∙Windows Terminal Server∙Windows NT Server∙Linux Servers∙Solaris ServersFollowing devices are classified under desktops:∙Windows 2000 Professional∙Windows XP∙Windows NT Workstation.∙Windows Millinium Home Edition∙Devices not responding to SNMP and TelnetIf any of the servers are classified under desktops, simply import them into servers. Refer the steps mentioned to check for SNMP.Monitoring Configurations∙Despite SNMP being enabled on the device, the dial graphs for CPU, Memory, and Disk Utilization are not seen.∙Telnet/WMI-based resource monitor is not showing any data∙WMI Monitors are not working. It always says 'error # access denied'∙Some more WMI monitoring errors with error codesDespite SNMP being enabled on the device, the dial graphs for CPU, Memory, and Disk Utilization are not seen.CauseSNMP may not be enabled, or the SNMP agent is not responding to requests.SolutionCheck the SNMP configurations, rediscover the device and re-add the monitors. Troubleshoot as follows:The possible reasons for the graphs not appearing are:∙The Resource monitors may not have been associated to this device. Associate the monitors.∙Check if SNMP is enabled properly on this device. If Yes, the Agent may not have responded to the SNMP request. Check if the Agent is responding using the Mib Browser.∙If the device has just been added, wait for the first poll to happen.Following are the steps to troubleshoot:1. In the device snapshot page, scroll down to the monitors list. Click the Edit icon against amonitor. For instance, let us try the CPU Utilization monitor. Click the Test Monitor link in the resulting screen. See if the monitor responds to the test request. If it does, you will see thedial graph.2. If there is an error message after step#1, it can be because of the snmp request to the cpuvariable getting timed-out, or the oid may not be implemented in the MIB.3. To confirm the reasons mentioned above, invoke the tool MibBrowser.bat present in /bindirectory. Load the Host Resource mib and query the oid .1.3.6.1.2.1.25.3.3.1.2 for the device that is not showing the cpu dial.4. If there is a response for the query in MibBrowser, it implies that the OID is implemented andthe dial not appearing can be due to snmp timeout. So, you will need to configure the snmptimeout by including the parameter DATA_COLLECTION_SNMP_TIMEOUT 15 in the fileNmsProcessesBE.conf for the process 'PROCESS com.adventnet.nms.poll.Collector'. Look for the following default entry in this file:PROCESS com.adventnet.nms.poll.CollectorARGS POLL_OBJECTS_IN_MEMORY 25 POLL_JDBC true MAX_OIDS_IN_ONE_POLL 15 AUTHORIZATION true DATA_COLLECTION_QUERY_INTERVAL 120000PASS_THRO_ALL_POLLING_OBJECTS true CLEAN_DATA_INTERVAL 999999Include the mentioned additional parameter. Now the changed entry will be as shown below: PROCESS com.adventnet.nms.poll.CollectorARGS POLL_OBJECTS_IN_MEMORY 25 POLL_JDBC true MAX_OIDS_IN_ONE_POLL 15 AUTHORIZATION true DATA_COLLECTION_QUERY_INTERVAL 120000PASS_THRO_ALL_POLLING_OBJECTS true CLEAN_DATA_INTERVAL 999999DATA_COLLECTION_SNMP_TIMEOUT 155. On the other hand, if there is no response in the Mib Browser, it implies that the OID is notimplemented. The vendor must be requested to implement this variable for you. As analternative, you can associate a telnet/wmi-based monitor for this device. Delete the existingSNMP-based monitor, Click the Add Monitor link again and select telnet/wmi-based monitors. Telnet/WMI-based resource monitor is not showing any data∙If you have added a Telnet/SSH/WMI based Resource monitor, check if the UserName and Password specified are correct. Click the 'Password' link to configure the correct usernameand password to the device.∙Ensure that you have configured the domain administrator user name and password for WMI Monitors if the device is in a domain. Configure as <domain name>\<admin user name> in the User Name field. If the device is in a workgroup, it is sufficient to configure the deviceusername and password.∙Despite the correct user name and password, if you are still unable to see the dial graphs in Windows devices, try the following stepso Open a command prompt and change directory to /opmanager/conf/application/scripto Type cscript cpu.vbs <device name> <domain name\admin username> <password> If this command returns a proper output, you should be able to see the dials. If youencounter an error such as Error # Access denied, very the login credentials onceagain.o If the monitored device is Windows XP, try the following option too:▪Go to Administrative Tools -->Local Security Policy Select Security Options▪From the options on the right, select Network access: Sharing and securitymodel for local accounts▪Right-click and select Properties▪Change the privelege from Guest to Classic.▪Remove and re-add the monitors.▪Check to see if the monitors are up.WMI Monitors are not working. It always says 'error # access denied'CauseLogin credentials are incorrect.SolutionFollow the steps below:1. Verify if you have provided the domain administrator username and password to connect tothe device as mentioned in the above tip. If the device is in a domain the user name shouldbe like "domain name\administrator name".2. If the login credentials as specified in step 1 are correct, then try associating a WMI basedmonitor ( preferably, a Free/Used Space in MB/GB graph ) to the Exchange Server using the Resource Monitors -> Add Monitor -> WMI based monitor -> Free/Used Disk Space in MB/GB.You should get the list of drives available in the device.3. If step #2 does not go through, then try enabling the WMI, RPC services on the Windowssystem and try the same again.4. This can also happen if the DCOM settings are not configured properly.You can check the exact error for this when you run a vbs script from the command prompt as incmd> cd [OpManagerHome]\conf\application\scripts\cmd> cscript cpu.vbs [machinename] [domainname]\[username] [password]5. You can also try configuring the dcom settings as mentioned below:From the Run Prompt of your Windows 2k Server, type \"dcomcnfg\" and expand the treeunder Component Services -> Computers. Click on the My Computer Icon from the Icon bar and select Default Properties. Check the following:Enable Distributed COM on this computerEnable COM Internet Services on this computerSelect the Default Impersonation Level as \"Impersonate\".You can also edit the COM Security settings if needed.6. If the above 4 steps do not help, try changing the service Log-on details as followsGo to Windows Service UI.Open "Properties" dialog of the "ManageEngine OpManager" serviceGo to "Log On" tabIn the "Log on as" option select "This Account" and enter domain name\username andpassword, which has rights to access WMI data.Save and restart opmanager.Note: This will make the tray icon and splash screen disappear.Some more WMI monitoring errors with error codes∙80070005 - Access is denied∙80041064 - User credentials cannot be used for local connections∙800706BA - The RPC server is unavailable∙80041010 - Invalid class∙80041003 - Access Denied∙80040154 - WMI Components are not registered∙80080005 - Internal execution failure in the WMI Service∙8004106C - WMI is taking up too much memory∙8004100E - Invalid namespace∙80041017 - Invalid queryThe error codes and the resolutions are explained below:80070005 - Access is deniedCauseThis error occurs when incorrect login credentials are configured.Solution∙If the device is in a domain, ensure to configure the correct domain name, user name, and password. If the device is in a workgroup, it is sufficient to configure only the user name and password. For instance, if the domain name is BigDom, username is admin, in the user name field, type BigDom\admin.∙It is also not necessary to specify the user name and password for devices that have user access from the machine where OpManager is installed.∙Despite the correct credentials, if you still face issues, troubleshoot further using the following steps:o Check if the user account is valid in the target machine by opening a command prompt and executing the following command:net use \\<monitored device name>\ADMIN$ /u:"<Domain Name\User Name>""<password>"If this command throw errors, the provided user account is not valid on the targetmachine.o Check if 'Remote DCOM' is enabled in the monitored workstation. If it is not enabled, enable it as follows:1. Select Start > Run2. Type dcomcnfg in the text box and click OK3. Select the Default Properties tab4. Select the Enable Distributed COM in this machine checkbox5. Click OKTo enable DCOM on Windows XP hosts:1. Select Start > Run2. Type dcomcnfg in the text box and click OK3. Click on Component Services > Computers > My Computer4. Right-click and select Properties5. Select the Default Properties tab6. Select the 'Enable Distributed COM' in this machine checkbox7. Click OKIf the above steps do not help, try changing the service Log-on details as follows:∙Go to Windows Service UI.∙Open "Properties" dialog of the "ManageEngine OpManager" service∙Go to "Log On" tab∙In the "Log on as" option select "This Account".∙Configure the user name and password here of the account which has access to the remote machine. Save and restart opmanager.∙Try the above 3 steps again.Note: You will not find the tray icon and splash screen after you make these changes.80041064 - User credentials cannot be used for local connectionsCauseThis error is encountered when you specify the Username and password for monitoring the machine where OpManager is running.SolutionDo not specify Username and password for the localhost. To resolve the issue, remove the configured user name and password from "Passwords" link in the device snapshot page.800706BA - The RPC server is unavailable.CauseThis error is encountered when the RPC and WMI services are not running and if the device is not pingable.Solution∙Check if the device is up and running, and pingable.∙Check the Remote Procedure Call(RPC) and Windows Management Instrumentation(WMI) Services are running1. Select Start > Run2. Type 'services.msc' in the text box and click OK3. In the listed services, see if the status of RPC and WMI services are shown as started.4. Start the services if it is not started.∙ A firewall might be configured on the remote computer. Such exceptions mostly occur in Windows XP (with SP 2), when the default Windows firewall is enabled. Disable the defaultFirewall in the Windows XP machine as follows:1. Select Start > Run2. Type Firewall.cpl and click OK3. In the General tab, click Off4. Click OK.∙If the firewall cannot be disabled, Enable Remote Administration(for administrators) by executing the following command on the remote machine : "netsh firewall set serviceRemoteAdmin"∙ A firewall might be blocking the WMI traffic. Give access to WMI traffic in the firewall. You will need to open the ports 445,135 in the firewall.80041010 - Invalid classCauseThis error occurs when the required WMI class is not registered.Solution∙Check whether the desired application is installed.∙To register all the WMI classes for the installed application. Run the below commands: o For Windows 2000 'winmgmt /resyncperf' command from the monitored device.o For Windows XP and 2003 'wmiadap /f' command from the monitored device. 80041003 - Access DeniedCauseThis error occurs when the user name provided does not have sufficient access privileges to perform the operation.Solution1. It is possible that this user does not belong to the Administrator group for this host machine.2. Try moving the user to the Administrator Group of the workstation.3. Try with an administrator (preferably a Domain Administrator) account.80040154 - WMI Components are not registeredCauseThis error occurs when the WMI is not available in the remote windows workstation. This happens in Windows NT. Such error codes might also occur in higher versions of Windows if the WMI Components are not registered properly.Solution∙Install WMI core in the remote workstation. This can be downloaded from the Microsoft web site.∙Register the WMI DLL files by executing the following command in the command prompt: winmgmt /RegServer∙Install the WMI for Windows NT by downloading the below exe:/downloads/details.aspx?displaylang=en&FamilyID=C174CFB1-EF67-471D-9277-4C2B1014A31E80080005 - Internal execution failure in the WMI ServiceCauseThis error occurs when there is some internal execution failure in the WMI Service (winmgmt.exe) running in the host machine. The last update of the WMI Repository in that workstation could have failed.SolutionRestart the WMI Service in the remote workstation:1. Select Start > Run.2. Type Services.msc and click OK.3. In the Services window that opens, select Windows Management Instrumentation service.4. Right-click and select Restart8004106C - WMI is taking up too much memoryCauseThis error occurs when WMI is taking up too much memory. This could be caused either by low memory availability or excessive memory consumption by WMI.Solution∙WMI is taking up too much memory.∙This could be caused either by low memory availability or excessive memory consumption by WMI.∙Try restarting or reinstalling the wmi service.8004100E - Invalid namespaceCauseInvalid namespace Compiler is not a normal error. It is possible that the desired application using the namespace is not installed properly.Solution∙Try re-installing the application or the WMI services alone.∙Contact with logs.80041017 - Invalid queryCause'Query was not syntactically valid' is not a normal error. It is possible that the desired application using the namespace is not installed properly.Solution∙Try reinstalling the application or the WMI services alone.∙Contact support with logs.For any other error codes, refer the MSDN knowledge base.Alerting and Notification∙Email notifications are not received∙Error! page is displayed when a profile is selected∙Modem-based SMS notifications are not workingEmail notifications are not receivedCauseProfile may not be associated to the device, or the mail-server settings may be incorrectSolutionCheck if the notification profile is associated to the deviceCheck if the correct criterion is selected in the profile configurationEnsure the mail-server settings are configured correctly.Error! page is displayed when a profile is selected.CauseThe profile name may contain special characters or a spaceSolutionYou will not be able to delete the profile from the client in such case. So, follow the steps below:1. Stop OpManager2. Open the file /conf/alert.filters3. Remove the <FILTER>...</FILTER> element containing the profile configuration.4. Restart OpManager.Modem-based SMS notifications are not working. The message 'Check the modem settings' alone is seen.There are quite a few things that you need to take note of when configuring modem-based sms alerts. Here it goes:Prequisites to configure SMS alerts:∙Need to have the supported mobile and modem, Sim Card, Serial Cable, and USB Driver.∙Works only on Windows OSRequired USB Driver:The modem and the mobile vendors provide the required modem/mobile drivers. For instance, you can get the driver for Nokia from the following link:/A4144937Required Cables:This depends on your mobile phone model. For Nokia 62xx/63xx, you need DLR-3P cable. Newer Nokia models use DKU-9 USB cable. In such case you need to download the driver from Nokia's website, which creates a virtual communication port. Other brands have their own cables, usually USB ones. GSM Modems have a serial port and so you will need a standard serial cable.Identifying the port at which the modem/mobile is connected:1. Go to My Computer->Control Panel->System->Hardware->Device Manager- >ports.2. Here you will find the port to which the Modem\Mobile is connected.3. If it is not available, then4. Go to My Computer->Control Panel->System->Hardware->Device Manager->Modems.After the system system detects the port to which the Modem\Mobile is connected, connect it to OpManager as follows:1. Start OpManager.2. Go to Admin->SMS Server Settings.3. Type the port number to which the modem/mobile is connected in the SMS Server Settingspage.4. If the Mobile\Modem is connected to the specified port, the Mobile\Modem details are shown.5. Configure an SMS alert from Admin->Notification Profiles->SMS Alert->Modem based SMSand associate to the devices.OpManager is ready to send the SMS notifications whenever an alarm is generated.System detects the port to which the modem/mobile is connected but OpManager fails to detect it:∙Ensure that the mobile or modem is supported in OpManager.∙Ensure that the correct port number is correct and is of the format - COM5 or com5.∙Also check for the validity of the SIM.KnowledgebaseFor further tips to troubleshoot or find resolutions, dig into our online knowledgebase or write to us at our Support Portal.。
DM3028A EM3028A Troubleshooting Guide

Specifications Operation: playback only File Format: Windows .wav, PCM, mono, 16-bit, 22.05 or 44.1 KHz Maximum Number of Sound Segments
Direct Mode: 8 Binary Mode: 128 Sequential Mode: 128 Memory Type: CompactFlash card (type 1, 5V), 8 ~ 128 MB Supply Voltage: 10 ~ 32 VDC Audio Output: 40W (8 Ohm load), bridged output DM3028A Dimensions: 5.6’’ x 4.2’’ EM3028A Dimensions: 6.0’’ x 4.8’’ x 1.7’’
troubleshooting标准作业流程

Troubleshooting(故障排查)的标准作业流程通常包括以下步骤:
1.定义问题:首先,需要明确遇到的问题是什么,确定是否确实存在故障。
2.收集信息:从故障的表现、系统内部和外部依赖的系统以及日志等各方面收集尽可能多的信息。
这些信息可能包括错误消息、系统日志、用户反
馈等。
3.归纳整理和分析:对这些收集到的信息进行归纳整理和分析,以找出可能的原因或故障发生的范围。
4.定位问题:通过前面的分析,逐步定位到故障发生的具体子系统或模块。
5.假设和排除:基于前面的分析,做出一些假设,排除一些不太可能发生故障的部件,进一步缩小故障范围。
6.测试和验证:对假设进行测试和验证,例如,如果假设是某个模块存在问题,那么可以尝试替换或修改这个模块,然后观察系统是否恢复正常。
7.记录和反馈:无论问题是否得到解决,都需要记录下这次的故障排查过程,以便未来遇到类似问题时可以参考。
同时,如果问题没有得到解决,
还需要将问题反馈给相关人员或团队,以便进行更深入的研究和解决。
以上就是一个通用的Troubleshooting流程,但具体的流程可能会因系统、应用、环境等因素而有所不同。
在实际操作中,需要根据具体情况进行调整和优化。
AGM Trouble Shooting Guide Line

Problem ReasonSolution Big Bag 空了换袋(when AGM Big Bag is at the line:)Nozzle not sucking AGM 真空泵出问题或者关闭和E&I 一起检查真空泵输送管道中AGM Jam打开管道清洁Panel Mate 上Receive 未打开在P/V 上打开Receiver 看Reseive顶端的阀门是否能打开和E&I一起检查看AGM Bigbag清洁空气的阀门是否能打开Receiver Filter 堵塞清洁Filter 或者更换由于输送管道泄漏,无真空密封管道Butterfly Valve 没打开检查开关,或调整气压Butterfly 的气缸无法正常工作更换气缸Receiver 中没有AGMFill sensor 的low level 输入有误检查、调整Butterfly Valve 始终打开和 E&I 一起检查气阀、气缸,如果需要则更换Auger 损坏更换Auger有人手动打开Receiver 蝶阀,导致AGM 倾倒入Hopper 的Lower level 设得太高 (> 10%)调整到10%以下异物混入AGM, eg. big bags 的编织袋清洁jam, 在更换Big bag 时小心Jet Gun 气压太低调整压力异物混入AGM ,导致管道堵塞清洁jam, 清洁整个系统Auger 伺服电机仍在运转Auger 损坏,更换Auger Jam 在Hopper 或者输送管道中see above 生产线没停, 但是core 中没有AGMAGM 流量计失效更换流量计AGM Trouble Shooting Guide Line管道中 AGM Jam Hopper 里AGM Jam Hopper 里没有AGM Receiver 里没有AGM 由于没有AGM ,生产线停下来仅在片的一侧有AGM Jet Gun有问题更换或者修复Jet Gun片中AGM的总量不对调节AGM SetPoint片中AGM分布不正确Jet Gun压力太低调节Core Drum真空不对检查Core Drum真空,是否有网面B/UProblem ReasonBig Bag Station is empty(when AGM Big Bag is at the line:)Vacuum pump is defect or switched off.Jam in the feed pipesReceiver is switched off at the Panel MateCan the Valve on the top of Reciever open?can the Cleaning Air Valve open?Receiver Filter is blockedNo vacuum in feed pipes due to leakageButterfly Valve doesn´t switchAir Cylinder Butterfly is defect.No AGM in ReceiverFill sensor low level has wrong value inputButterfly Valve stays openAuger is brokenSomebody dumped manually the receiver contentsin a full hopperLower level is set too high (> 10%)Jam at the Auger through wrong things in the AGM,eg. parts of the big bags.Pressure of the Jet Gun too lowJam in the Funnel due to wrong parts in the AGM.Auger servo is runningJam in Hopper/ at the FunnelNo Line stop, but AGM is missing in the core AGM Flowmeter defectNo AGM in Hopper Jam in Hopper Jam at the AGMFunnelLine stop: No AGM AGM Trouble Shooting Guide LNo AGM in ReceiverAGM only on one side of the diaper Malmanufactured Jet Gun, due to that fact wrong AGM FlowWrong AGM amount in diaperJet Gun pressure too lowVacuum Core millhouse not on the correct valueWrong AGM Distribution in theDiaperide LineSolutionRefillNozzle not sucking AGMCheck the pump with E&IClean Feed pipesSwitch the Receiver onCheck wih E&ICheck wih E&IExchange Filter (Procedure is discribed below)Seal leakageCheck switch/AdjustmentsExchange Air CylinderCheck adjustment.Check Butterfly Valve with an E&I, check the Air Cylinder, if necessary, exchange them.Exchange AugerAdjust Lower level correctlyClear the jam, be careful at the preparation of the big bags.Adjust PressureClear the jam, clean the system.Auger is broken, exchange Augersee aboveExchange FlowmeterExchange or repair Jet GunAdjust AGM value at the panelmate adjust pressureCheck the system。
通信机房高频开关电源故障处理流程
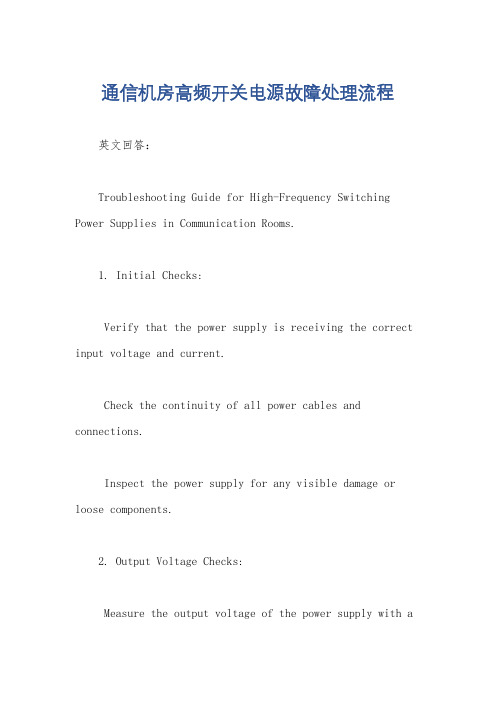
通信机房高频开关电源故障处理流程英文回答:Troubleshooting Guide for High-Frequency Switching Power Supplies in Communication Rooms.1. Initial Checks:Verify that the power supply is receiving the correct input voltage and current.Check the continuity of all power cables and connections.Inspect the power supply for any visible damage or loose components.2. Output Voltage Checks:Measure the output voltage of the power supply with amultimeter.Compare the measured voltage to the specified output voltage.If the output voltage is significantly different, the power supply may be faulty.3. Load Test:Connect a load to the output of the power supply.The load should be rated for the maximum current output of the power supply.Observe the output voltage and current while the load is connected.If the output voltage drops significantly or the current exceeds the specified limit, the power supply may be overloaded or faulty.4. Ripple and Noise Measurements:Connect an oscilloscope to the output of the power supply.Measure the ripple and noise on the output waveform.Excessive ripple and noise can indicate a faulty power supply or load.5. Component Inspection:If the initial checks and tests have not identified the fault, proceed to inspect the components within the power supply.Look for burnt or damaged components, such as capacitors, transistors, and diodes.Replace any faulty components with new ones of the same type and value.6. Power Supply Replacement:If the fault cannot be repaired, the entire power supply may need to be replaced.Ensure that the replacement power supply has the same voltage and current ratings as the original.Reconnect all cables and connections and verify that the system is operating properly.中文回答:通信机房高频开关电源故障处理流程。
- 1、下载文档前请自行甄别文档内容的完整性,平台不提供额外的编辑、内容补充、找答案等附加服务。
- 2、"仅部分预览"的文档,不可在线预览部分如存在完整性等问题,可反馈申请退款(可完整预览的文档不适用该条件!)。
- 3、如文档侵犯您的权益,请联系客服反馈,我们会尽快为您处理(人工客服工作时间:9:00-18:30)。
Troubleshooting GuideRe v. 0.2 –October 2014Flightradar24 ABTable of ContentsINTRODUCTION (3)NORMAL OPERATION (4)TYPICAL DISRUPTIONS (5)RECEIVER OFFLINE (6)FURTHER TROUBLESHOOTING (7)IntroductionThis Guide has been prepared to help you identify and resolve basic issues affecting the performance of the Flightradar24 receiver and associated equipment, including connection to the Internet and uploading aircraft messages to our central servers.In normal operation, you should not have to perform any monitoring or maintenance.Your receiver is monitored remotely and we will send an automated email alert if it has been offline for more than 6 hours. If the receiver is still offline for more than 24 hours our support team will contact you to get it back online.It is important that you let us know whenever you change your email address.This is our primary method of contact, using the address you supplied when you applied for a receiver. This address is also linked to your Premium account and validates your free Subscription.Your Premium account has performance statistics for your receiver, with range plots and graphs showing maximum distance, aircraft tracked and reported hits and positions.The performance stats can be found in your Premium account under Your Feeds -> More Info.We very much appreciate you hosting our equipment and our Support team is there to help you operate it to its maximum potential, delivering quality messages and best possible range.In addition to the Guide, do not hesitate to contact us at Support@ for further help and advice. Please quote the radar ID you were given when the receiver was first activated and which is shown in your Premium Account.Normal OperationNormal OperationWe have supplied two versions of receiver. They perform exactly the same but the earlier version, shown on the left, does not have a Power LED.The receiver should be powered using the supplied 5VDC, 1A, 2.1mm, CENTER POSITIVE power adapter and connected to the antenna by the coax cable. The Ethernet cable should be connected to your router.Under normal operations the receiver front LEDs should be lit as follows:Power (where fitted) Steady GreenMode-S Should flicker non periodic in red when aircraft data is received.GPS Should flicker once per second. Green is OK, red may indicate a problem.The rear Ethernet port should show green and yellow LEDs when connected to your local network via your router or network extender.Typical Disruptions Typical DisruptionsOne or more of the following may disrupt normal service:1. No GPS PositionCheck that the GPS antenna is connected and that it’s lo cated where it can get asatellite fix. The antenna is weatherproof and can be located outside. Does theGPS green LED flicker?2. Poor or reduced aircraft rangeCheck that the Mode-S external antenna is connected to the receiver and isinstalled in the optimum location. Also check the coax connections are tight and are dry. Moisture can cause a signal short. Does the Mode-S red LED flicker?3. No data is being uploaded to our server – Receiver OfflineCheck the power supply is working and connected to the receiver. Where fitted,does the Power LED show green? Also check that the Ethernet cable is connected to your local network and you have an active Internet connection.To check that the receiver is connected to your local network, open a browser and type in the receiver IP address to open the browser interface page. The IP address is shown in your Premium account.Receiver Offline Receiver OfflineIf we notice that the receiver has been offline for more than 6 hours we will send you an automated alert via email.“F-XXXX1 Receiver Offline Since 2014-05-23 03:57:52 CEST”On receipt, first check all cables are connected, power is available and the receiver is connected to your local network which has a good internet connection.If everything looks OK, please login to your Premium account and check the receiver status to see if the receiver has come online since the alert was sent.If not, contact Support@ for further advice.Further TroubleshootingIf the receiver is still offline, there is no GPS position or the aircraft range is poor, our Technical Support may ask you to make more detailed checks to see if the problem is caused by a defective receiver or component.Mode S LED is not flickering and GPS LED is steady red when antenna is disconnected. The coax cable, antenna orreceiver may be faultyIf you have another Mode-Sreceiver, such as a DVB-TUSB, please connect ourcoax cable and antenna.If the DVB-T doesn’t workwith our coax and antenna,please test our receiverusing a different coax cableand antenna if you havethese. If the LEDs remainas before, the receiver mayneed replacing.If you don’t have anotherMode-S receiver but dohave a multimeter, pleasecheck if there's connectionon ground / signal on thecoax. If the coax cable andconnectors are OK, thereceiver may needreplacing.Poor range. In a good location with no local obstacles, the external antenna should provide a range in excess of 200 nautical miles. Your Premium Account statistics will show your range plots and distance graph. Antenna, coax cable orreceiver may be faulty orthere are bad connections.Check the coax connectionsat the receiver and antennaare tight. Make sure there isno water at the antennaconnection which should besealed with self-amalgamating tape.If you have another Mode-Sreceiver, such as a DVB-TUSB, please connect ourcoax cable and antenna.If the DVB-T doesn’t workwith our coax and antenna,please test our receiverusing a different coax cableand antenna if you havethese. If the LEDs remainas before, the receiver mayneed replacing.If you don’t have anotherMode-S receiver but dohave a multimeter, pleasecheck if there's connectionon ground / signal on thecoax. If the coax cable andconnectors are OK, thereceiver may needreplacing.Further Troubleshooting© Flightradar24 AB Rev 0.2 Oct 2014 Page 11。