数控车床横向进给系统设计
CK6140数控车床进给系统设计(全套图纸+论文)

摘要CK6140型数控机床,主运动系统采用1.26和1.58两种公比的混合公比传动系统,并用双速电机驱动,结构简单转速范围广。
合理地确定有关结构参数及动力参数,并对传动轴、齿轮、键等进行粗算及检验计算。
粗选步进电机及滚珠丝杠,构成开环控制系统。
关键词:数控;机床;开环控制第1章绪论1.1数控机床的发展趋势我国数控机床产量持续高速增长,根据市场需求和技术发展趋势,应重点推进高效、精密为核心的数控机床“”级工程,加强民展性能、高可靠性数控功能部件,积极开展复合加工机床、超精密数控机床和可重构制造系统的工程化研究等机械加工装备产业、构建数字化企业的重要基础,镄的民展一直备受人们关注。
数控机床以其卓越的柔性的自动化的性能、优异而稳定的精度、灵捷而多样化的功能引起世人瞩目。
它开创了机械产品向机电一体化发展的先河,因此数控技术成为先进成为先进制造技术的一项核心技术。
通过持续的开发研究以及对信息技术的深化应用,促进了数控机床性能和质量的进一步提升,使数控机床成为国民经济和国防建设发展的重要制造装备。
近6年来,我国数控金切机床(简称数控机床)产量一直以年均增长超过30%速度发展。
据初步统计,2004年数控机床的产量为51860台,事比增长40.8%,数控机床的消费量约74000台,事比增长32%。
数控机床需求的旺盛也促进了2004年内建的三资和民营机床厂以及数控机床品种的明显增加。
与此同时,甸进口的数控机床数量也在逐年同步增加,而且进口数控机床的消费额的增长趋势更快。
2004年数控机床的进口数量同比年增长30%,而进口消费额的增长却达52%,从而导致国产数控机床在国内市场消费额中的所占比例已不足30%。
之所以出现这一现象,其主要原因在于国内市场对技术和附加值高的高效、精密和高性能大型、重型数控机床需求增长,需要靠进口解决。
振兴我国数控机床市场占有率应着重于剖析数控机床及由其组成的制造系统(生产线)的技术现况及民展趋势,探讨使其能适应变批量,多品种、高质量、低成本以及具有快速响应的柔性和符合环保的未来生产模式的解决方案。
数控车床横向进给机构的设计
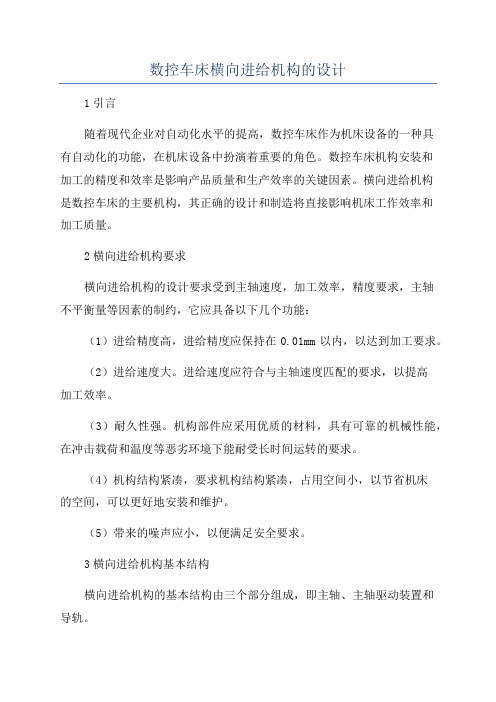
数控车床横向进给机构的设计
1引言
随着现代企业对自动化水平的提高,数控车床作为机床设备的一种具
有自动化的功能,在机床设备中扮演着重要的角色。
数控车床机构安装和
加工的精度和效率是影响产品质量和生产效率的关键因素。
横向进给机构
是数控车床的主要机构,其正确的设计和制造将直接影响机床工作效率和
加工质量。
2横向进给机构要求
横向进给机构的设计要求受到主轴速度,加工效率,精度要求,主轴
不平衡量等因素的制约,它应具备以下几个功能:
(1)进给精度高,进给精度应保持在0.01mm以内,以达到加工要求。
(2)进给速度大。
进给速度应符合与主轴速度匹配的要求,以提高
加工效率。
(3)耐久性强。
机构部件应采用优质的材料,具有可靠的机械性能,在冲击载荷和温度等恶劣环境下能耐受长时间运转的要求。
(4)机构结构紧凑,要求机构结构紧凑,占用空间小,以节省机床
的空间,可以更好地安装和维护。
(5)带来的噪声应小,以便满足安全要求。
3横向进给机构基本结构
横向进给机构的基本结构由三个部分组成,即主轴、主轴驱动装置和
导轨。
(1)主轴是提供进给力的重要部件。
数控车床横向进给机构的设计
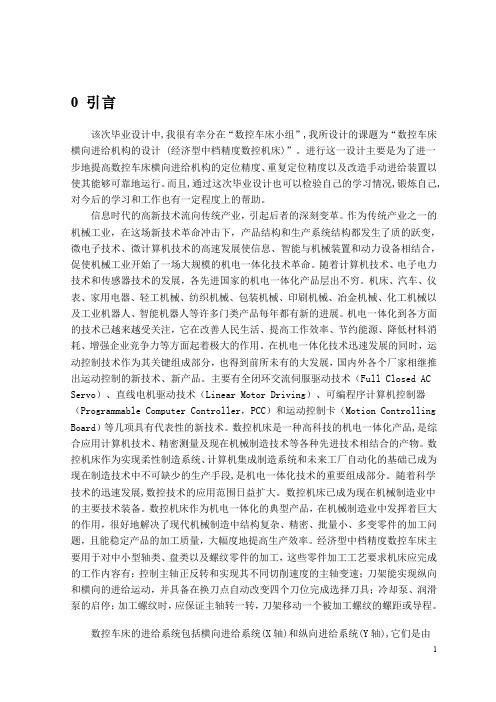
0 引言该次毕业设计中,我很有幸分在“数控车床小组”,我所设计的课题为“数控车床横向进给机构的设计 (经济型中档精度数控机床)”。
进行这一设计主要是为了进一步地提高数控车床横向进给机构的定位精度、重复定位精度以及改造手动进给装置以使其能够可靠地运行。
而且,通过这次毕业设计也可以检验自己的学习情况,锻炼自己,对今后的学习和工作也有一定程度上的帮助。
信息时代的高新技术流向传统产业,引起后者的深刻变革。
作为传统产业之一的机械工业,在这场新技术革命冲击下,产品结构和生产系统结构都发生了质的跃变,微电子技术、微计算机技术的高速发展使信息、智能与机械装置和动力设备相结合,促使机械工业开始了一场大规模的机电一体化技术革命。
随着计算机技术、电子电力技术和传感器技术的发展,各先进国家的机电一体化产品层出不穷。
机床、汽车、仪表、家用电器、轻工机械、纺织机械、包装机械、印刷机械、冶金机械、化工机械以及工业机器人、智能机器人等许多门类产品每年都有新的进展。
机电一体化到各方面的技术已越来越受关注,它在改善人民生活、提高工作效率、节约能源、降低材料消耗、增强企业竞争力等方面起着极大的作用。
在机电一体化技术迅速发展的同时,运动控制技术作为其关键组成部分,也得到前所未有的大发展,国内外各个厂家相继推出运动控制的新技术、新产品。
主要有全闭环交流伺服驱动技术(Full Closed AC Servo)、直线电机驱动技术(Linear Motor Driving)、可编程序计算机控制器(Programmable Computer Controller,PCC)和运动控制卡(Motion Controlling Board)等几项具有代表性的新技术。
数控机床是一种高科技的机电一体化产品,是综合应用计算机技术、精密测量及现在机械制造技术等各种先进技术相结合的产物。
数控机床作为实现柔性制造系统、计算机集成制造系统和未来工厂自动化的基础已成为现在制造技术中不可缺少的生产手段,是机电一体化技术的重要组成部分。
数控技术课程设计数控车床横向和纵向进给系统设计(全套图纸)
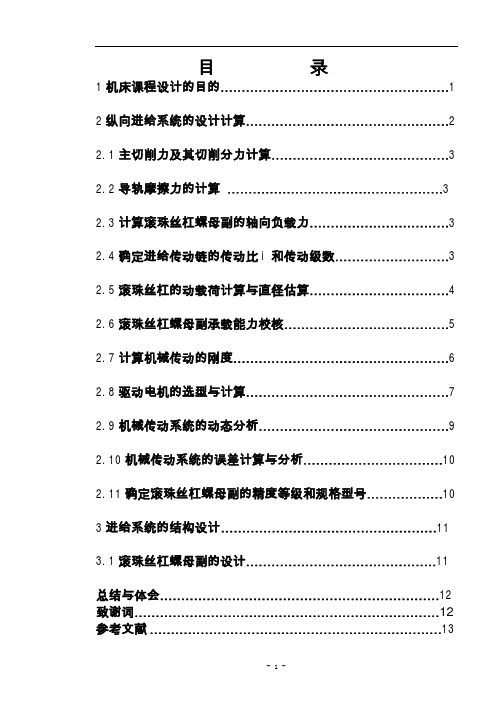
2纵向进给系统的设计计算 (2)2.1主切削力及其切削分力计算 (3)2.2导轨摩擦力的计算 (3)2.3计算滚珠丝杠螺母副的轴向负载力 (3)2.4确定进给传动链的传动比i和传动级数 (3)2.5滚珠丝杠的动载荷计算与直径估算 (4)2.6滚珠丝杠螺母副承载能力校核 (5)2.7计算机械传动的刚度 (6)2.8驱动电机的选型与计算 (7)2.9机械传动系统的动态分析 (9)2.10机械传动系统的误差计算与分析 (10)2.11确定滚珠丝杠螺母副的精度等级和规格型号 (10)3进给系统的结构设计 (11)3.1滚珠丝杠螺母副的设计 (11)总结与体会 (12)致谢词 (12)参考文献 (13)1数控技术课程设计的目的通过本课程设计的训练,使学生在完成数控机床及金属切削机床的结构课程学习之后,让学生能够运用所学的知识,独立完成数控机床传动系统的设计,从而使学生进一步加深和巩固对所学知识的理解和掌握,并提高学生的分析、设计能力,同时巩固《金属切削机床》课程的部分知识。
全套图纸,加1538937061.运用所学理论及知识,进行数控机床部分机械结构设计,培养学生综合设计能力;2.掌握数控机床传动系统的设计方法和步骤;3.掌握设计的基本技能,具备查阅和运用标准、手册、图册等有关技术资料的能力;4.基本掌握编写技术文件的能力。
2纵向进给系统的设计计算设计参数如下:工作台工作台质量 kg m T 600= 最大加工受力N F W 1500= 快进速度s m v f /2.0max =工作台导轨摩擦力 N F R 5.2= 工作行程m s W 7.0=减速机构丝杠螺母机构(图2),已知数据如下:图2 丝杠螺母机构轴承轴向刚度 800/L K N m µ=丝杠螺母刚度 800/M K N m µ=螺母支座刚度 1000/TMK N mµ=丝杠传动效率 0.9sp η=丝杠长度 0.5sp L m=丝杠轴承、丝杠螺母摩擦力矩, 2.5R sp M N m =g轴承平均间距 1550L mm =导程10sp h mm = 最大转速常数 60000A = 支承方式 双推—双推 伺服电机电机转子惯量320.0510M J kg m −=×g2.1主切削力及其切削分力计算取机床的机械效率0.8η=,/1w z F F =,/0.35c z F F =,/0.2v z F F =则有 1500z w F kF N N ==工作台横向进给方向载荷c F 和工作台垂直进给方向载荷v F 为0.350.351500525c z F F N N ==×= 0.20.21500300v z F F N N ==×=2.2导轨摩擦力的计算导轨受到垂向切削分力300v F N =,纵向切削分力c F =525N ,移动部件的全部质量(包括机床夹具和工件的质量)m=600kg ,查表得镶条紧固力2000g f N =,取0.15(3002000300525)=×+++468.75N =计算在不切削状态下的导轨摩擦力0F µ和0F 0()0.15(3002000)345g F W f N µµ=+=×+= 00()0.2(3002000)460g F W f N µ=+=×+=2.3计算滚珠丝杠螺母副的轴向负载力计算最大轴向负载力max a Fmax (300468.75)768.75a y F F F N N µ=+=+= 计算最小轴向负载力min a F min 0345a F F N µ==2.4确定进给传动链的传动比i 和传动级数取步进电动机的步距角 1.5α=°,滚珠丝杠的基本导程010L mm =,进给传动链的脉冲当量0.004/p mm P δ=,则有0 1.51010.423603600.004p L i αδ×===× 根据结构需要,确定各传动齿轮的齿数分别为120z =、2208z =,模数m=2,齿宽b=20mm 。
数控车床横向进给机构的设计

数控车床横向进给机构的设计数控车床横向进给机构是数控车床中的一个重要组成部分,它的设计质量直接影响数控车床的加工精度和效率。
下面将针对数控车床横向进给机构的设计进行详细的介绍,涵盖机构的类型选择、结构设计、传动方式和控制系统等方面。
1.机构类型选择:数控车床横向进给机构常见的类型有液压机械式、液压液压式以及电动机械式等。
液压机械式机构结构简单,但存在液压缸阻尼大,加工设备容易产生震动的缺点。
液压液压式机构较为常见,其结构复杂但具有较好的进给平稳性。
电动机械式机构结构简单、响应速度快,但容易出现因为接触不良而导致的冲击及振动。
根据实际需求,在设计中应选择适合的机构类型。
2.结构设计:数控车床横向进给机构主要由进给轴、导轨、滚珠螺杆、螺母等组成。
进给轴负责传动力,并保证传动平稳性。
导轨用于引导进给轴的运动方向,保证其运动的准确性。
滚珠螺杆和螺母是横向进给机构的主要传动部件,用于将转动运动转化为线性运动。
在结构设计中,应注意进给轴与导轨、滚珠螺杆与螺母之间的配合精度,确保传动平稳性和精度。
同时,合理选择结构材料,保证机构的刚性和稳定性。
3.传动方式:在传动方式的选择中,应根据实际需求和工作环境的要求综合考虑,选择合适的传动方式。
4.控制系统:在控制系统的设计中,应确保控制精度和稳定性,使数控车床能够稳定、精确地进行横向进给运动。
综上所述,数控车床横向进给机构的设计应综合考虑机构类型选择、结构设计、传动方式和控制系统等方面。
只有合理选择机构类型、优化结构设计、选择合适的传动方式和控制系统,才能设计出性能良好的数控车床横向进给机构,提高加工精度和效率。
数控车床纵向进给系统和横向进给系统的设计
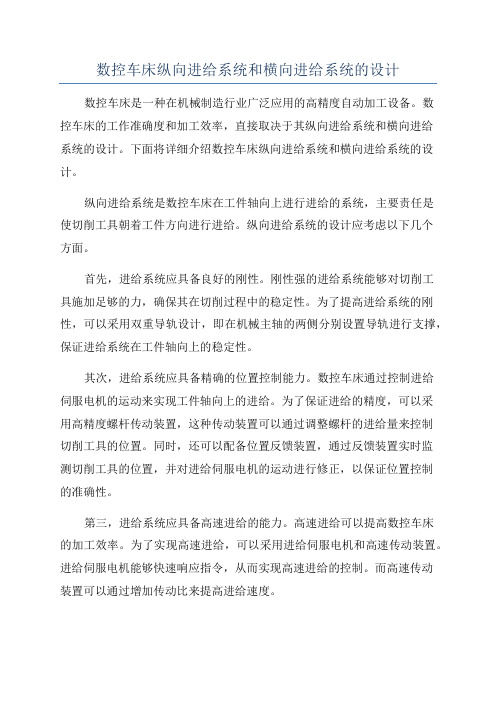
数控车床纵向进给系统和横向进给系统的设计数控车床是一种在机械制造行业广泛应用的高精度自动加工设备。
数控车床的工作准确度和加工效率,直接取决于其纵向进给系统和横向进给系统的设计。
下面将详细介绍数控车床纵向进给系统和横向进给系统的设计。
纵向进给系统是数控车床在工件轴向上进行进给的系统,主要责任是使切削工具朝着工件方向进行进给。
纵向进给系统的设计应考虑以下几个方面。
首先,进给系统应具备良好的刚性。
刚性强的进给系统能够对切削工具施加足够的力,确保其在切削过程中的稳定性。
为了提高进给系统的刚性,可以采用双重导轨设计,即在机械主轴的两侧分别设置导轨进行支撑,保证进给系统在工件轴向上的稳定性。
其次,进给系统应具备精确的位置控制能力。
数控车床通过控制进给伺服电机的运动来实现工件轴向上的进给。
为了保证进给的精度,可以采用高精度螺杆传动装置,这种传动装置可以通过调整螺杆的进给量来控制切削工具的位置。
同时,还可以配备位置反馈装置,通过反馈装置实时监测切削工具的位置,并对进给伺服电机的运动进行修正,以保证位置控制的准确性。
第三,进给系统应具备高速进给的能力。
高速进给可以提高数控车床的加工效率。
为了实现高速进给,可以采用进给伺服电机和高速传动装置。
进给伺服电机能够快速响应指令,从而实现高速进给的控制。
而高速传动装置可以通过增加传动比来提高进给速度。
横向进给系统是数控车床在工件切削方向上进行进给的系统,主要责任是使切削工具按照设定的路径进行进给。
横向进给系统的设计应考虑以下几个方面。
首先,进给系统应具备较高的定位精度。
切削工具在横向进给过程中需要按照设定的路径进行移动,为了保证移动的准确性,可以采用高精度传动装置和位置反馈装置。
高精度传动装置可以提供精确的进给量,而位置反馈装置可以实时监测工具位置,从而实现位置控制的准确性。
其次,进给系统应具备较高的速度响应能力。
切削工具在横向进给过程中需要快速响应指令,以满足加工要求。
为了实现高速响应,可以采用高速伺服电机和高速传动装置。
数控车床横向进给系统设计

数控车床横向进给系统设计
一、系统概述
采用数控车床横向进给系统,实现对外圆面、内圆面、铣坯和端面的
加工。
该进给系统是由伺服电机、传动装置、减速机、控制系统以及传动
系统等组成,实现对工件的无级调速和定长加工。
二、系统结构
1、伺服电机
采用伺服电机对车床横向进给实现无级调速,伺服电机采用伺服电机,功率为2.2kW,有效的提高了加工精度和效率。
2、传动装置
采用变位传动装置实现车床横向进给,其中最主要的部件有:滑轮、
减速箱和环形齿轮。
滑轮采用机械滑轮,具有安全可靠、使用简单、容易
安装等优点;减速箱采用放大减速箱,具有转速调节范围大、转速稳定等
特点。
3、控制系统
采用智能控制系统实现车床横向进给的调节,该系统使用普通的计算
机硬件,实现硬件与软件的协同工作,完成调节进给量和定长加工的功能。
4、传动系统
传动系统采用滑环传动,具有传动比高、安装方便等优点,实现车床
横向进给的定长加工功能。
三、系统特性
1、无级调速
采用伺服电机实现无级调速,可根据不同的加工要求,调节车床的横向进给速度。
2、定长加工
采用传动系统实现定长加工。
679 经济型数控车床横向进给系统设计
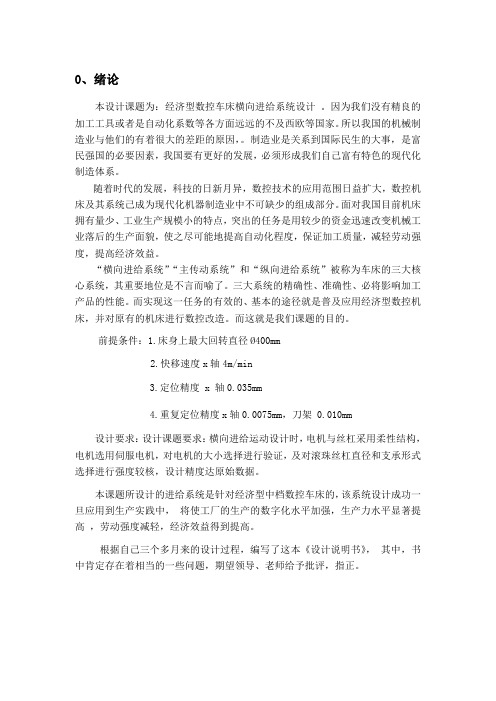
0、绪论本设计课题为:经济型数控车床横向进给系统设计 。
因为我们没有精良的 加工工具或者是自动化系数等各方面远远的不及西欧等国家。
所以我国的机械制 造业与他们的有着很大的差距的原因,。
制造业是关系到国际民生的大事,是富 民强国的必要因素,我国要有更好的发展,必须形成我们自己富有特色的现代化 制造体系。
随着时代的发展,科技的日新月异,数控技术的应用范围日益扩大,数控机 床及其系统己成为现代化机器制造业中不可缺少的组成部分。
面对我国目前机床 拥有量少、工业生产规模小的特点,突出的任务是用较少的资金迅速改变机械工 业落后的生产面貌,使之尽可能地提高自动化程度,保证加工质量,减轻劳动强 度,提高经济效益。
“横向进给系统”“主传动系统”和“纵向进给系统”被称为车床的三大核 心系统,其重要地位是不言而喻了。
三大系统的精确性、准确性、必将影响加工 产品的性能。
而实现这一任务的有效的、基本的途径就是普及应用经济型数控机 床,并对原有的机床进行数控改造。
而这就是我们课题的目的。
前提条件:1.床身上最大回转直径Ø400mm2.快移速度x轴4m/min3.定位精度 x 轴0.035mm4.重复定位精度x轴0.0075mm,刀架 0.010mm设计要求: 设计课题要求: 横向进给运动设计时, 电机与丝杠采用柔性结构, 电机选用伺服电机,对电机的大小选择进行验证,及对滚珠丝杠直径和支承形式 选择进行强度较核,设计精度达原始数据。
本课题所设计的进给系统是针对经济型中档数控车床的, 该系统设计成功一 旦应用到生产实践中, 将使工厂的生产的数字化水平加强,生产力水平显著提 高 ,劳动强度减轻,经济效益得到提高。
根据自己三个多月来的设计过程,编写了这本《设计说明书》, 其中,书 中肯定存在着相当的一些问题,期望领导、老师给予批评,指正。
1、国内外发展概况及现状介绍从上世纪五十年代数控技术开始发展到1965 年,数控装置从最初的电子管 元件、晶体管元件、集成电路到目前使用比较普遍的小型计算机和微处理器共经 历了五代的发展。
- 1、下载文档前请自行甄别文档内容的完整性,平台不提供额外的编辑、内容补充、找答案等附加服务。
- 2、"仅部分预览"的文档,不可在线预览部分如存在完整性等问题,可反馈申请退款(可完整预览的文档不适用该条件!)。
- 3、如文档侵犯您的权益,请联系客服反馈,我们会尽快为您处理(人工客服工作时间:9:00-18:30)。
1、数控机床进给系统概述1.1 伺服进给系统概述数控机床的伺服进给系统由伺服驱动电路、伺服驱动装置、机械传动机构和执行部件组成。
它的作用是接收数控系统发出的进给速度和位移指令信号,由伺服驱动电路作转换和放大后,经伺服驱动装置(直流、交流伺服电动机,功率步进电机,电业脉冲马达等)和机械传动机构,驱动机床的工作台、主轴刀架等执行部件实现工作进给和快速移动。
数控机床的伺服进给系统与一般机床的进给系统有本质的差别,他能根据指令信号精确地控制执行部件的运动速度与位置,以及几个执行部件按一定运动规律所合成的运动轨迹。
1.2 伺服进给系统分类数控私服进给系统按有无位置检测和反馈进行分类,有以下三种:(1)开环伺服系统(2)半闭环伺服系统(3)闭环伺服系统1.3 伺服进给系统的基本要求(1)精度要求(2)响应速度(3)调速范围(4)低速、大转矩1.4 主要设计任务已知参数:最大加工直径D m a x=400m m,工作台及刀架重:30㎏;最大轴向力:130㎏;导轨静摩擦系数:0.2;行程:360m m;步进电机:110B F003;步距角:0.75°;电机转动惯量:J=1.8×10-2㎏.c m.s-2;设计要求:车床控制精度:0.005m m(即为脉冲当量);加速时间:25m s;最大进给速度:V=2.5m/m i n。
m a x2、运动设计2.1传动方案拟定数控机床按控制方式分为开环、闭环、半闭环,由于采用直流式交流伺服电机的闭环控制方案,结构复杂,技术难度大,调试和维修困难,造价也高。
闭环控制可以达到很好的机床精度,能补偿机械传动系统中各种误差,消除间隙、干扰等对加工精度的影响,一般应用于要求高的数控设备中,由于数控车床加工精度不十分高,采用闭环系统的必要性不大。
若采用直流或交流伺服电机的半闭环控制,精度较闭环控制的查,但是稳定性好,成本较低,调试维修较容易;但是对于经济型数控机床来说必要性不大。
故在本次设计中,采用开环控制步进电机驱动。
确定设计任务后,初步拟定三种传动方案即1电机直接与丝杠相连;2电机通过同步带的传动带动丝杠转动;3电机通过齿轮传动带动丝杠转动。
步进电机具有如下优点 :(1)电动机的输出转角与输入的脉冲个数严格成正比,故控制输入步进电动机的脉冲个数就能控制位移量;(2)电动机的转速与输入的脉冲频率成正比,与要控制脉冲频率就能调节步进电动机的转速;(3)停止送入脉冲时,只要维持绕组内电流不变,电动机轴可以保持在某个固定位置上,不需要机械制动装置;(4)变通电相序即可以改变电动机的转向;(5)进电动机存在齿间相邻误差,但是不会产生累积误差;(6)进电动机转动惯量小,启动、停止迅速。
滚珠丝杠副具有摩擦数小传动效率高,所需的传动转矩小;灵敏度高,传动平稳,不易产生爬行;随着精度和定位精度高,磨损小,寿命长,精度保持性好,可通过预紧间隙消除措施提高轴承刚度和反向精度,运动具有可性。
故在本次设计中采用步进电机带动X向工作台移动。
传动方案1的结构简单,但是消除由步进电动机引起的振动等现象能力较差,故在本次设计中不采用方案1;传动方案2采用同步带传动保持恒定传动比,传动精度高工作平稳,结构紧凑,无噪声,有良好减振性能,但制造工艺比较复杂,传递功率较小,寿命较低,故在本次设计中不易采用。
所以本次设计中采用方案3的齿轮传动,其主要特点是效率高,结构紧凑,工作可靠,寿命长,传动比稳定,传动过程中采用消隙齿轮,消除正反转齿轮间隙提高传动精度,性价比高。
2.2降速比计算由于选用的步进电机型号为110B F 003,步距角为0.75。
数控车床的脉冲当量为0.005m m 。
降速比i 按下式计算: 5.2005.0360675.0360=⨯⨯==δθs i式中 θ—步进电机的步距角,(°); δ—脉冲当量,mm ; s —丝杠螺距,㎜; 取s=6㎜。
2.3 丝杠螺母机构的选择与计算 2.3.1 确定滚珠丝杠副的导程 滚珠丝杠副的导程按下式计算:(2-1)式中 h P —滚珠丝杠副的导程,(㎜); Vmax —工作台最高移动速度,(min m ); max n —电机最高转速,(min r ); 由设计任务查得: min 5.2max mV =查阅《数控机床系统设计》得: 步进电机110BF003的最高转速min500max r n =。
将数值代入上式可得:5≥h P ㎜。
故取6==s P h ㎜。
2.3.2 强度计算 1.动载强度计算1)对于燕尾型导轨的牵引力计算F m =KF X +f(F Z +2F Y +G) (2-2)取 K=1.4 f=0.2考虑工作台在移动过程中只受G 影响maxmax n V P h ≥故 F 1m =fG=0.2×30×9.8 =58.8(N)考虑工作台在加工时静止只受F X 影响 故 F 2m = KF X=1.4×9.8×130 =1783.6(N)取F max = F 2m2.计算最大动载荷 C当转速min 10rn ≥时,滚珠丝杠螺母的主要破坏形式是工作表面的疲劳点蚀,因此要进行动载强度计算,其计算动载荷)(N c C 应小于或等于滚珠丝杠螺母副的额定动载荷,即r eq H d c F F f f T C ≤=3' (2-3) 式中 d f —动载荷系数; H f —硬度影响系数; eq F —当量动载荷,N ;r F —滚珠丝杠螺母副的额定动载荷,N ; 'T —寿命,以r 610为一个单位。
(2-4) 式中 T —使用寿命,h ; N —循环次数;eq n —滚珠丝杠的当量转速,min r 。
查表取 T=15000 hmin 667.416610005.2max r s v n eq =⨯==代入数据可的:3751015000667.41660'6=⨯⨯=T查 [1]表5-1取2.1=d f 查 [1]表5-2取f H =1.0N T n T eq 66101060'-==当工作载荷单调连续或周期性单调连续变化时,则N F F F F F m m eq 667.120838.586.178********min max =+⨯=+=+≈式中 max F 、min F —最大和最小工作载荷,N 。
所以 计算可的:KN C c 5.10667.12080.12.13753=⨯⨯⨯=查手册选取CBM4006-5型滚珠丝杠副(c a C KN C >=851.15),所以刚度满足要求。
3.静载强度计算 当转速min10rn ≤时,滚珠丝杠螺母的主要破坏形式为滚珠接触面上产生较大塑性变形,影响正常工作。
为此进行静载强度计算,最大计算静载荷为:N F f f F H d oc 32.21406.17830.12.1'max =⨯⨯== 式中 H f '—硬度影响系数;查手册可得:CBM4006-5型滚珠丝杠副额定静载荷oc oa F N C >=47985,所以满足要求。
滚珠丝杠螺母的主要参数如表2-1所示: 表2-15.2005.0360675.0360=⨯⨯==δθs i3、动力计算3.1 传动件转动惯量的计算 3.1.1 齿轮转动惯量的计算 1、传动比的计算2、初步分配传动比按获得最小转动惯量的原则分配传动比i=i 1i 2 i 2=21i (3-1)得 i 1=1.52 i 2=1.64 3、初步估计齿轮模数m=1.25 小齿轮Z 1=27大齿轮 412752.1112=⨯==Z i Z171=b ㎜ 202=b ㎜mm mz d 75.332725.111=⨯== mm mz d 25.514125.122=⨯==mm d d 5.42225.5175.332211=+=+=α小齿轮303=Z大齿轮493064.1324=⨯==Z i Zmm b 263= mm b 284=mm mZ d 5.373025.133=⨯==mm mZ d 25.614925.144=⨯== mm d d 375.49225.615.372432=+=+=α4、转动惯量的计算有下式计算齿轮的转动惯量: 1241077.0-⨯=b d J (3-2) 式中 d —齿轮分度圆直径,mm ;b —齿轮宽度,mm 。
将数值代入上式可得:512411070.1101775.3377.0--⨯=⨯⨯⨯=J ㎏·㎡ 512421062.10102025.5177.0--⨯=⨯⨯⨯=J ㎏·㎡ 512431096.310265.3777.0--⨯=⨯⨯⨯=J ㎏·㎡ 512441034.30102825.6177.0--⨯=⨯⨯⨯=J ㎏·㎡ 3.1.2 工作台的转动惯量工作台的转动惯量按下式计算:62102-⨯⎪⎭⎫ ⎝⎛=W S J w π (3-3)式中 W —工作台(包括工件)的质量,㎏; S —丝杠螺距,㎜。
将数值代入上式可得:4621027.0103026--⨯=⨯⨯⎪⎭⎫ ⎝⎛=πw J ㎏·㎡3.1.3 丝杠的转动惯量丝杠的转动惯量按下式计算:12010477.0-⨯=L d J s (3-4) 式中 0d —滚珠丝杠直径,㎜; L —支承距,㎜。
由珠丝杠的参数可得:400=d ㎜,360=L ㎜。
所以 31241071.010*******.0--⨯=⨯⨯⨯=s J ㎏·㎡ 3.1.4 负载折算到电动机轴上的转动惯量负载折算到电动机轴上的转动惯量为:4525522531027.01070.1271062.101096.341271034.301071.0------⨯+⨯+⨯+⨯+⨯⨯+⨯=0000442.0=㎏·㎡w s J J z J J z z J J J +++++=12123222143.2 电动机力矩计算3.2.1 计算加速力矩a M=0.092N ·m3.2.2 计算摩擦力矩f MN ·m式中 η—传动链总效率,取8.0=η。
3.2.3 计算附加摩擦力矩0M30max 0010)21(2-⨯-=ηπηiSF M16.0=N ·m式中 η—传动链总效率,取8.0=η;0η—滚珠丝杠未预紧时的效率,取9.00=η。
3.2.4 根据公式计算快速空载启动时电动机所需力矩 o f a M M M M ++=16.028.0092.0++==0.532N ·m3.3 丝杠螺母机构的传动刚度计算滚珠丝杠一端轴向支撑,丝杠的最小拉压刚度min ∆K 和最大拉压刚度max ∆K 分别为:m NmmNl Ed K μππ7191019.736041006.2404552max2min =⨯≈⨯⨯⨯⨯==∆m NmmNl Ed K μππ25871087.2510041006.2404562min2max =⨯=⨯⨯⨯⨯==∆Tn J M r a 6.9=025.06.95000000442.0⨯⨯=3105.28.0268.58-⨯⨯⨯⨯=π28.0≈30102-⨯=iSF M f πη3210)9.01(8.05.2266.1783-⨯-⨯⨯⨯=π式中 E —弹性模量。