注塑成型过程FMEA案例
汽车大灯配光镜注塑过程PFMEA范例

FMEA编号:项目名称:大灯过程责任编制人:FMEA日期(编车型年/车辆类型:关键日FMEA日期(修页码:核心小开机潜在的失效模式及后果分析(过程FMEA)垃圾/颗粒(PZK002)外观缺陷导致报废41.模具分型面较脏;2.车间清洁度不佳51.定期保养模具;2.车间增加湿度首件点检5100按照注塑开机标准作业书进行开机43448成形不足(PZK003)外观及功能缺陷导致报废51.模温、热流道温度未达到生产要求;2.注塑量不足;3.螺杆内有混有空气41.模具生产前预热;2.按照注塑工艺文件对生产工艺进行点检;3.充分清洗螺杆首件点检360按照注塑开机标准作业书进行开机53345银光丝(PZZ001)外观缺陷导致报废51.注塑速度过快;2.热流道、螺杆温度过高;3.模温过高;4.螺杆、针阀逃料41.按照注塑工艺文件对生产工艺进行点检;2.定期保养清理热流道针阀;3.定期对机床螺杆进行保养;1.按照质量管理点对产品全数检查2.班组长每班定时巡检480无垃圾/颗粒(PZZ002)外观缺陷导致报废41.模具分型面较脏;2.车间清洁度不佳;3.静电风机未开;4.机械手夹具太脏41.定期保养模具;2.车间增加湿度;3.静电风机点检;4.定期更换夹具夹片;1.按照质量管理点对产品全数检查2.班组长每班定时巡检696无成形不足(PZZ003)外观及功能缺陷导致报废51.模温、热流道温度未达到生产要求;2.注塑量不足;3.螺杆内有混有空气31.模具生产前预热;2.按照注塑工艺文件对生产工艺进行点检;3.充分清洗螺杆;4.定期保养模温机,更换老化水道1.按照质量管理点对产品全数检查2.班组长每班定时巡检690无气斑(PZZ004)外观缺陷导致报废51.注塑速度过快;2.热流道温度过低;3.模具排气不良5按照注塑工艺文件对生产工艺进行点检;1.按照质量管理点对产品全数检查2.班组长每班定时巡检41001.模具分型面开排气槽; 2.启用压缩注塑功能534601-d-1开机1-d-2注塑设备故障设备导致产品无法生产51.螺杆加热系统损坏;2.安全保护装置失灵;3.锁模装置损坏;4.人为误操作损坏设备31.按照注塑开机标准作业书进行开机;2.定期对设备维护每天对设备进行设备点检230无1-d-3剪浇口破坏产品有效面外观,浇口修剪不平整外观缺陷造成报废4 1.操作人员手套不洁净;2.操作人员动作不规范;3.工具不良41.定期更换手套及操作工具;2.按照作业指导书进行操作;3.员工培训 1.按照质量管理点对产品全数检查2.班组长每班定时巡检464无污染产品表面外观缺陷造成报废3 1.操作人员手套不洁净;2.料车较脏21.定期更换手套;2.按照标准清洁料车班组长每班定时巡检424无产品有效面碰伤外观缺陷造成报废3 1.操作人员动作不规范;2.产品摆放不合理2 1.按照作业指导书进行操作;2.按照存放工艺卡放置产品;3.员工培训班组长每班定时巡检424无1e移至车间物流产品损坏导致产品报废4物流人员拉取过多2严禁超过最大拉取数量物流人员平稳拖运648无1f堆场存储表面尘点较多和产品混放导致产品报废,造成产品错装21.堆场混乱;2.堆场标识不清;3.堆场环境较差3对堆场进行目视化管理;增加清洁次数物流人员按标识拉取产品636无1g移至装配车间产品散落导致产品报废4物流人员拉取过多2严禁超过最大拉取数量物流人员平稳拖运648无标记处数标记日期1-d-4取放产品更改文件号签字日期处数更改文件号签字。
FMEA案例分析

点检
2
统
信号输 量
盒密封不良
目测
出异常
,或受潮氧
化
2 电气仪表系 传感器 传感器 无法计
统
信号输 量
出异常
9 零点输出过 大或电源性 能降低
3 仪表检测 3
3 电气仪表系 传感器 传感器 无法计 9
统
输出无 量
信号
桥路电压异 常
6 仪表检测 3
4 电气仪表系 传感器 传感器 无法计 9 传感器应变 6
该方法在 探测时有 多好
措施结果
采取的 措施
不
严 重 度 数
频 度 数
易 探 测 度
R .P . N
数
跟踪
?评审 ?确认 ?控制计划
13
潜在的失效模式及后果分析(设计 FMEA )
第 页,共 页
(2)项目名称
(5)车型年/类型
(8)核心小组
(9)功能 要求
左前车门 H8HX-A . -上、下车 -保护乘员免 受天气/噪音/ 侧碰撞的影响 a.车门附件 (如后视镜/门 锁/门铰链/及 门窗升降器的 支撑 b.为外观装饰 项目提供适当 的表面 c.喷漆和软内 饰
PFMEA 开始于基本的操作方法讨论完成时,完成时间早于生产 计划制定和生产批准之前
5
开发三部曲
6
控制计划 /过程流程 结合
产品质量计划顺序
过程流程清单 (包括所有的过程)
APQP程序 将启动这个过程
DFMEA
过程流程清单 转化为
过程控制计划
过程流程/ 控制计划 (所有的“”主要“过程)
PFMEA (所有的“”主要“过程)
带入杂质
对下道 工序
无法紧固 不能配合 不能连接 无法安装 损坏设备 危害操作者
完整实用的过程PFMEA实例(注塑企业)
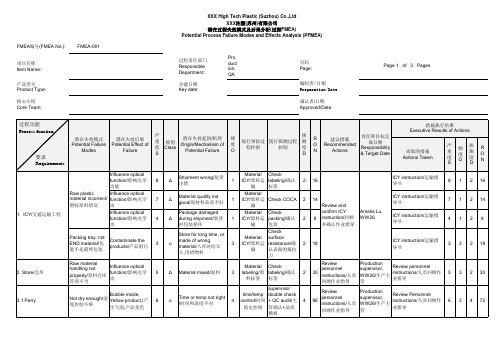
过程责任部门 Responsible Department:
Pro duct ion, QA
关键日期 Key date:
页码 Page:
编制者/日期 Preparation/Date
确认者/日期 Approved/Date
Page 1 of 3 Pages
பைடு நூலகம்
过程功能
Process function 要求
Imaging lens Dia.,
Dim 1: 5.78±0.03 Influence out of spec./镜头 assembly/影响装配
3
直径尺寸超规
Review PM mould
Order start
Production personnel instruction,
o
Wrong insert/嵌入错误
Contaminate the products/产品脏污
3
2. Store/仓库
Raw material handling not properly/原料仓库 管理不当
Influence optical function/影响光学 功
5
3.1 Perry
Not dry enough/湿 度控制不够
1
release
Dim check/尺
plan/订单开 寸确认
2
6
PM mould /点检 磨具
supervisor, incoming inspection WW26/生产主 optical inserts/人员回顾
时包装损坏
输
包装
并确认作业指导
ICY instruction/运输指 导书
ICY instruction/运输指 导书
塑胶件FMEA
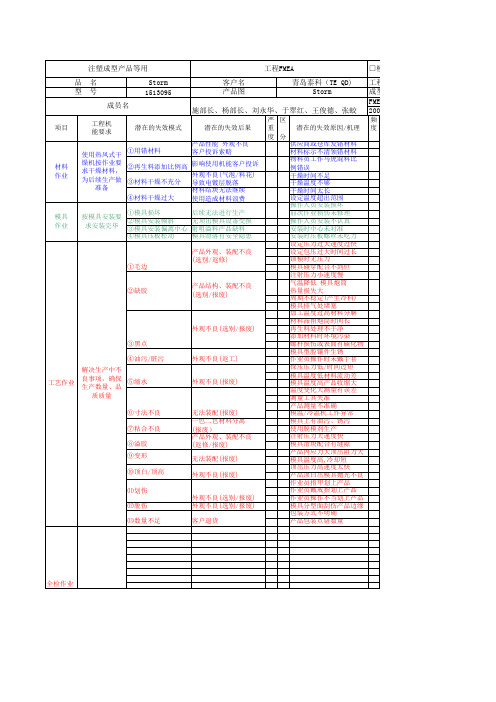
卸模进行抛光
抛光后加大该区顶针直径
下发<模具维修单〉
作业员修平指甲
禁止留长指甲
作业时组长确认检查
作业员摘除首饰
禁止戴首饰上岗
作业时组长确认检查
教导正确的操作产品手法
组长负责对上岗人员培训
按照<作业指导书〉作业
停机维修模具
组长负责对上岗人员培训
填写<模具维修记录〉
教导员工明确包装要求
作业前讲解包装事项
注塑成型产品等用
工程FMEA
□模具 ■注塑 □喷涂 □印刷
品名
Storm
客户名
青岛泰科(TE QD) 工程责任部门
型号
1513095
产品图
Storm
成型车间
成员名
FMEA预定完成日及计划开始日 施部长、杨部长、刘永华、于翠红、王俊德、张蛟 2008年11月15日
项目
材料 作业
模具 作业
工程机 能要求
废弃利用该再生料
制作再生料利用工作流程
执行<再生料利用培训>
对车间环境进行清扫保持湿度
定期清扫加料桶过滤面
主管严格监督车间卫生状况
检查螺杆并进行表面抛光处理
预存螺杆备件
管制<设备备件库存记录>
卸模分解对模具镶件进行清洗
依shot数保养模具
执行<模具保养计划>
要求作业员带手套操作产品
组长对作业要求进行检查
潜在的失效模式
潜在的潜在的失效原因/机理 度
度分
产品性能 外观不良
供应商或仓库发错材料
使用热风式干 燥机按作业要 求干燥材料, 为后续生产做
准备
①用错材料
FMEA实例(注塑企业)-最完整最典型最实用

措施执行结果 Executive Results of Actions 严 重 度 S 8 7 4 3 探 测 度 D 2 2 2 2
采取的措施 Actions Taken
频 度 O
R O N
8 7 4 3
Δ Δ Δ o
Shipment wrong Material quality not good Package damaged during shipment Store for long time, or made of wrong material
Production, QA
Page 1 of 3 Pages
过程功能 Process function
潜在失效模式 Potential Failure Modes 潜在失效后果 Potential Effect of Failure
要求 Requirements
Influence optical function Influence optical function Influence optical function Contaminate the products Influence optical function Bubble inside, Yellow product,
6
o
Time or temp not right
4
4
96
6
3
4
72
3.2 Molding
Imaging lens Dia., Dim 1: 5.78± 0.03 Influence assay out of spec.
3
o
Wrong insert
1
Order start Dim check release plan
注塑产品_PFMEA案例

共 4页 编制
最初编 制日期
FMEA 编号
201
FMEA 版本号
A
电话号码
FMEA 最新 更改日期
过程
要求
潜在失效模式 潜在的失效后果
严
重 等 潜在的失效原因/
度级
机理
S
控制预防
产品表面缩水
产品外观不合格 顾客抱怨
产品尺寸偏大 与相关零件不匹配,
或偏小
使顾客不满意
4、注塑成型
通过注塑机和模 产品表面烧焦 具成型生产出颜 色、外观、尺寸 、性能合格的产
2
《成型条件表》每班 次点检
4
48
2/16
编号: 总成
零件名称/零件号/工 序名称
产品编号:
CFT小组成 员:
分总成
潜在的失效模式及后果分析-PFMEA
零件
设 计/ 过 程 责 任 部 门
制 造 部
关键日期:(要求PFMEA编制完成日及预计生产开始日期)
Hale Waihona Puke PFMEA编制预定完成日:
预计生产开始日:8
9/16
2013-01
A/0
措施结果 R
ODP N
10/16
2013-01
A/0
措施结果 R
ODP N
11/16
2013-01
A/0
措施结果 R
ODP N
12/16
2013-01
A/0
措施结果 R
ODP N
13/16
2013-01
A/0
措施结果 R
ODP N
14/16
2013-01
A/0
不正确
作业
7
注塑FMEA
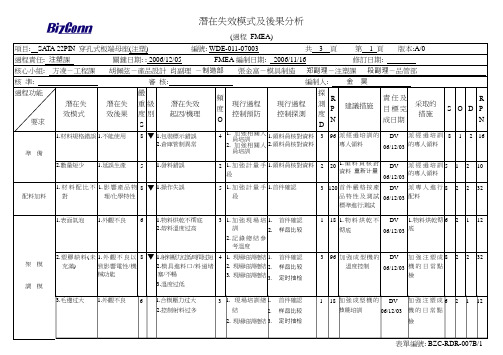
84
加強物料的標
示管控
DV
06/12/03
加強現場5S
工作
7
1
2
14
水口料入庫
1.包裝損傷
1.材料泄漏
6
1.搬運方法不當
2
1.采用正確的方法
1.入庫檢驗
2
24
加強現場培訓
DV
06/12/03
Hale Waihona Puke 采用正確的方法61
2
12
表單編號: BZC-RDR-007B/1
員培訓
1.領料員核對資料
2.領料員核對資料
3
96
派經過培訓的
專人領料
DV
06/12/03
派經過培訓
的專人領料
8
1
2
16
2.數量短少
1.延誤生產
5
1.發料錯誤
2
1.加強計量手
段
1.領料員核對資料
2
20
1.領料員核對資料重新计量
DV
06/12/03
派經過培訓
的專人領料
5
1
2
10
配料加料
1.材料配比不
對
1.影響產品物
加強注塑成
機的日常點檢
8
2
2
32
3.毛邊过大1.外觀不良61.合模壓力过大31.現場培訓總1.首件確認118加強成型機的DV加強注塑成62112
2.控制射料过多結2.样品比较技能培訓06/12/03機的日常點
2.現場培訓總結3.定时抽检檢
表單編號: BZC-RDR-007B/1
項目:SATA22PIN穿孔式板端母座(注塑)編號:WDE-011-07003共3頁第2頁版本:A/0
塑料注塑成型PFMEA分析

等)N
度度度
射出机料管4定期清理料管模具日常保1次/30分464机台尽可能固定颜色生管/注塑
有黑斑养生产
缩水4保压过小2依照标准成型成型条件每批216
条件表点检表
8保压过小2依照标准成型成型条件每批232
条件表点检表
胶芯穿孔4模具灌点2零件寿命管制成型条件每批216
过大点检表
8模具灌点2零件寿命管制成型条件每批232
过大点检表
■
包装
混料6
未按照标准
作
2
依照制造通知
单填写
224标签贴错6
未按照标准
作业
2
依照制造通知
单填写
224功能丧失
无法组装
无法组装
外观不良
功能丧失
外观不良。
- 1、下载文档前请自行甄别文档内容的完整性,平台不提供额外的编辑、内容补充、找答案等附加服务。
- 2、"仅部分预览"的文档,不可在线预览部分如存在完整性等问题,可反馈申请退款(可完整预览的文档不适用该条件!)。
- 3、如文档侵犯您的权益,请联系客服反馈,我们会尽快为您处理(人工客服工作时间:9:00-18:30)。
偏重 偏轻
强度增大、重量增重、成本 增加
4
强度减弱、重量不足,顾客 投诉
5
干
干燥时间长 浪费资源
2
燥
时间
干燥时间短 产品湿
4
料枪风压不够 原料密度过大 原料密度过小 未检查出 未检查出
2 调整料枪风压
每两小时对风压进行点检
2 更换原料密度
每小时对机位产品进行巡查
4 更换原料密度
每小时对机位产品进行巡查
3
重新设定预压时间及返工 重新预压
对预压时间进行点检并作记录
3 36
压力设定错误、未对预压 压力进行检查
2
重新设定预压压力及返工 重新预压
对预压压力进行点检并作记录
2 16
压力设定错误、未对预压 压力进行检查
2 重新设定预压压力
对预压压力进行点检并作记录
2 12
模具未安装好、参数设定 与质量不符
2
检查模具及调整啤机参数
P32R
潜在 失效 模式
料枪凹进
潜在 失效 后果
影响外观
过程责任
关键日期
严重 度S 级别
潜在失效 起因∕机理
4
料枪螺丝未锁
编 制人
FMEA日期(编 制)
频度 O
现行过程 控制预防
(修订)
现行过程控制探测
探测 度D RPN
建议措施
3 重新安装料枪
安装好料枪后指导员进行复检
2 24
料枪开花
影响外观
4
重量
MSA分析
2 20
FMEA编号
核心小组
责任及 目标完 成日期
采取的措施
QR-Q-073
措施结果
S
O
D RPN
2/3
项
目
车型年 ∕车辆 类型
零件最∕ 过程
过终程 功能
编检号
要求
查
外观
74978/9-4CL0A 74976/77-4CL0A 74976/77-4CL0A-PAD
2
4
2 对于盘点数进行抽检
每月进行仓库数量盘点
2 16
盘点数据错误
2 对于盘点数进行抽检
每月进行仓库数量盘点
3 18
未对仓库消防设施进行点 检
2
按规定期限限进行点检确认
3 30
时间设定错误、未对预压 时间进行检查
4 重新设定预压时间
对预压时间进行点检并作记录
3 36
时间设定错误、未对预压 时间进行检查
3 检查产品是否有湿潮
每批次隔日全检确认
2 检查产品是否有湿潮
每批次隔日全检确认
2 16 3 24 3 60 3 18 3 24
时间长
浪费资源
2
时间
时间短
货品结合达不到要求
4
产
品
组
温度高
浪费资源
4
装
温度
温度低
货品结合达不到要求
4
装车方法
产品外观
4
碰伤
客户投诉
4
外观 包装方法错 客户投诉、难包装
5
包
标签错
过程FMEA项ຫໍສະໝຸດ 目车型年 ∕车辆 类型
零件∕ 过程
过程 功能
编号
要求
74978/9-4CL0A 74976/77-4CL0A 74976/77-4CL0A-PAD
P32R
过程责任 关键日期
潜在 失效 模式
潜在 失效 后果
严重 度S 级别
编 制人
潜在失效 起因∕机理
FMEA日期(编 制)
频度 O
现行过程 控制预防
每次开机对温度进行点检
3 24
装车方法不正确,未按要 求作业
2 重新装车
对每个车仔装车方法进行检查
2 16
操作方法不正确
3 全检
教育及培训作业员按工作指引操作 2 24
工作指引错误或未按指引 作业
2 全检
更正工作指引教育及培训作业员按 工作指引操作
2
20
工作不认真
2 全检
教育及培训作业员
2 24
工作不认真
每小时对工艺进行点检 每小时对工艺进行点检 安装好料枪后指导员进行复检
2 12 2 18 2 16
FMEA编号
核心小组
责任及 目标完 成日期
采取的措施
QR-Q-073
措施结果
S
O
D RPN
1/3
过程FMEA
项
目
车型年 ∕车辆 类型
零件∕ 过程 过程 功能外观
编成号
要求
型
74978/9-4CL0A 74976/77-4CL0A 74976/77-4CL0A-PAD
4
预压压力
预压压力偏大 难生产及浪费资源
3
尺寸偏大
难实装
6
规格尺寸
尺寸偏小
实装松动及难实装
6
入料不饱
货品强度及不能使用
4
供应商来料品质不良
1 退回供应商
对每批来料进行抽查两包检查密度 2
4
供应商来料品质不良 供应商来料品质不良 盘点数据错误
1 退回供应商
对每批来料进行两包抽查密度
2
4
1 退回供应商
对每批来料抽查一包进行原料外观 检查
送错货、客户投诉
6
装
漏检 异物混入
客户投诉
5
多装
浪费资源
4
数量
少装
客户投诉
5
最
外观 判定
误判警报
浪费资源
5
终 检
准确
漏判警报
不合格品送给客户、客户投 诉
5
查
工作不认真
3 全检
教育及培训作业员
3 18
工作不认真
2 全检
教育及培训作业员
3 24
工作不认真
2 全检
每次开机对温度进行点检
2 16
工作不认真
2 全检
并作记录
毛边
难实装及影响外观
2
模具未安装好、模具老化 2 重新安装模具、检修模具 上模前对模具进行点检并作记录
2
8
建议措施
变形
难实装及不能使用
外观
重压(重成 型)
不能使用
成
料枪凸出
难实装及不能使用
型
3
工艺参数与实际质量不符 2 调整工艺时间
3
工艺参数与实际质量不符 3 调整工艺时间
4
料枪螺丝未锁
2 重新安装料枪
每小时对生产产品进行检查并作记 录
3
36
模具未安装好、参数设定 与质量不符
2
检查模具及调整啤机参数
每小时对生产产品进行检查并作记 录
3
36
料枪坏、未点检
2 更换料枪
上模前对料枪进行点检
3 24
成
顶烂
不能使用
4
型
融着率低
货品强度不够、客户投诉
6
外观
融着率高
浪费资源
4
起鼓(发涨) 难实装及不能使用
5
顶针及弹簧变形
2 更换顶针及弹簧
上模前对顶针及弹簧进行点检
2 16
蒸汽压力不够及蒸汽时间 过短
2
重新设定蒸汽压力及蒸汽 每两小时对蒸汽压力和东汽时间进
时间
行点检,并作记录
2
24
蒸汽压力过高及蒸汽时间 过长
2
重新设定蒸汽压力及蒸汽 每两小时对蒸汽压力和东汽时间进
时间
行点检,并作记录
2
16
水喉坏、蒸汽时间过长
上模前对水喉进行点检,及每两小 2 调整水喉及调整蒸汽时间 时对蒸汽时间进行点检,并作记录 2 20
(修订)
现行过程控制探测
探测 度D RPN
密度大
强度增大、重量超重、成本 增加
2
进 料
密度
密度小
强度减弱、重量不足,顾客 投诉
2
外观 色差
产品外观
2
仓
无法交货
4
库
数量
数量不准确
库存积压过多,周转率低
3
管
理
防火 消防设施过期 安全隐患
5
时间过长
浪费资源
3
预压时间
预
时间过短
产品收缩及难生产
4
压
预压压力偏小 产品收缩及难生产
2 全检
用顔色标签区别及教育及培训作业 员
2
20
工作指引错误或未按指引 作业
2 全检
更正工作指引教育及培训作业员按 工作指引操作
2
16
工作指引错误或未按指引 作业
2 全检
更正工作指引教育及培训作业员按 工作指引操作
2
20
基准过严
3
培训考核合格才可上岗工 作
MSA分析
2 30
基准过松
2
培训考核合格才可上岗工 作