电池组件检验标准(09版)
电池组件检验标准
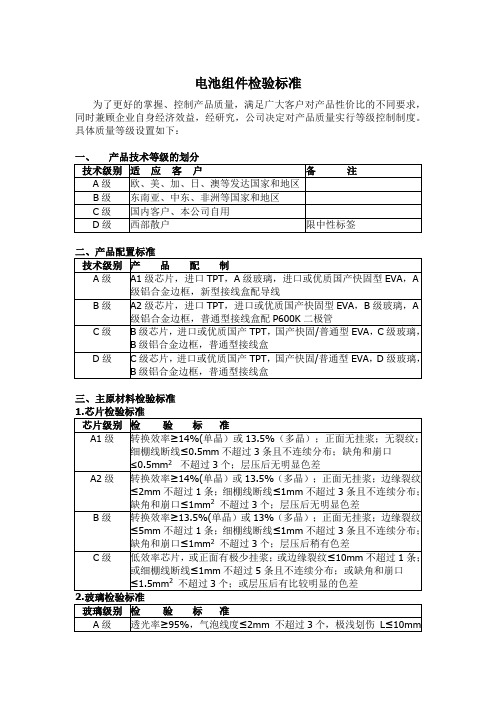
透光率≥91%,气泡线度≤2mm不超过3个,极浅划伤L≤15mm不超过3条;崩边向中间延伸≤2mm不超过3个;平整度≤5%
C级
透光率≥91%,气泡线度≤3mm不超过3个,浅划伤L≤20mm不超过3条;崩边向中间延伸≤2mm不超过3个;平整度≤5%
D级
透光率≥90%,气泡线度≤4mm不超过3个,浅划伤L≤25mm不超过3条;崩边向中间延伸≤2mm不超过3个;平整度≤5%
D级
C级芯片,进口或优质国产TPT,国产快固/普通型EVA,D级玻璃,B级铝合金边框,普通型接线盒
三、主原材料检验标准
1.芯片检验标准
芯片级别
检验标准
A1级
转换效率≥14%(单晶)或13.5%(多晶);正面无挂浆;无裂纹;细棚线断线≤0.5mm不超过3条且不连续分布;缺角和崩口≤0.5mm2不超过3个;层压后无明显色差
表面氧化均匀,表面无划伤、无鼓包;两端线度尺寸相差≤0.3mm
TPT无皱痕,表面干净,拱起点高度≤0.2mm;硅胶均匀;接线盒粘接牢固,表面干净
B级
≤±5%
公差≤1.0mm
两端尺寸相差≤0.5mm
芯片无挂浆,边缘裂纹≤5mm不超过1条,细栅线断线≤1mm不超过3条且不连续分布,缺角和崩口≤1mm2不超过3个,表面无明显色差;玻璃极浅划伤L≤15mm不超过3条;组件气泡≤3mm2不超过3个;芯片间距离不小于1mm,芯片与边框间距离不小于6mm
表面氧化均匀,表面无划伤、无鼓包;两端线度尺寸相差≤0.5mm
TPT少量皱痕,表面干净,拱起点高度≤0.2mm;硅胶均匀;接线盒粘接牢固,表面干净
D级
≤±10%
公差≤2.0mm
两端尺寸相差≤1mm
芯片有极少挂浆,边缘裂纹≤15mm不超过1条,细栅线断线≤1mm不超过5条且不连续分布,缺角和崩口≤1.5mm2不超过3个,表面有比较明显的色差;玻璃极浅划伤L≤30mm不超过3条;组件气泡≤5mm2不超过3个;芯片间距离不小于0.5mm,芯片与边框间距离不小于5mm
电池检验标准
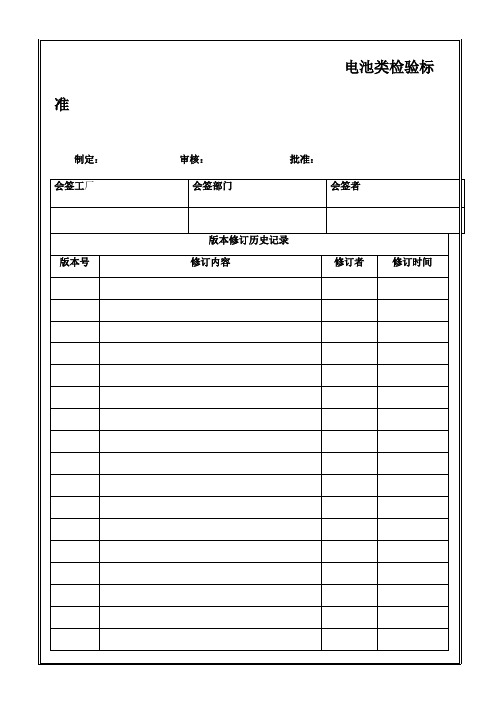
每批抽检2个进行拆机检验,检验内容为对照样品或承认书要求进行核对保护板的各零件和PCB规格是否一致。此项检验完成后要重新包装和检验,以防造成不良。
6.注意事项
a、电池在存放、使用中正负极不可以短路且不可接反以免损坏电芯影响电池效能。
b、非充电电池切不可加热、充电,以免发生爆炸、漏液等危险。
电池类检验标准
制定:审核: 批准:
会签工厂
会签部门
会签者
版本修订历史记录
版本号
修订内容
修订者
修订时间
1.目的
明确电池类材料的来料检验依据,确保来料品质符合我司工艺及客户要求。
2.适用范围
适用于本公司所有电池类(含可充式镍镉、镍氢、锂离子、锂聚合物电池等)材料的来料检验。
3.抽样标准依据MIL-STD-105E正常检验一次抽样方案 II级水平,其它根据抽样标准书执行。 电气特性:严重缺陷(CR)AQL=0;主要缺陷(Maj)AQL=0.4;次要缺陷(Min)AQL=0.65。外观:严重缺陷(CR)AQL=0;主要缺陷(Maj)AQL=0.65;次要缺陷(Min)AQL=1.5。
万用表、分容柜、
电池测
试仪
★
4
包装
核对有无物料信息贴纸、环保贴纸及贴纸内容是否清晰、完整、正确
目检
★
确认外包有无破损、碰撞痕迹
目检
★
有无混料、错料、短装现象
目检
★
零件的包装是否可保护零件不变形
目检
★
5.1重点尺寸检验
用卡尺测量本体长、宽、厚、引线长度或直径、高度(属软包装的电池以实装确认为主)
注:电池测试时在正负极处必须垫绝缘片防止电池短路危险,测完后减去相应厚度。
电池检验标准
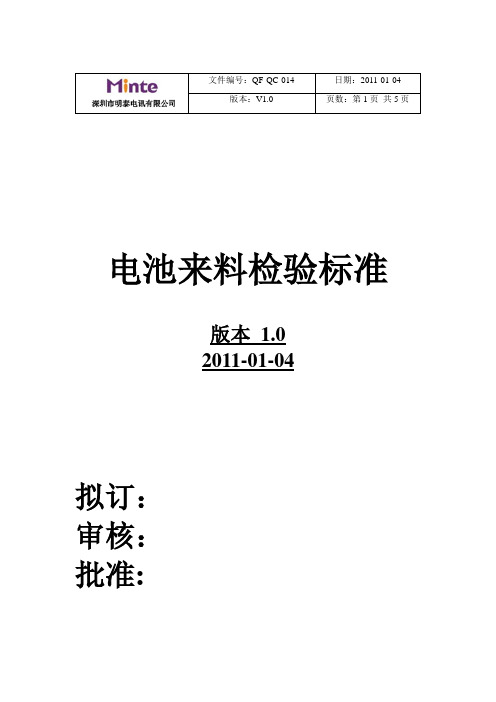
版本:V1.0 页数:第1页共5页电池来料检验标准版本 1.02011-01-04拟订:审核:批准:版本:V1.0 页数:第2页共5页版本修订状态版本状态日期修订人修订位置和原因1.0 2011-01-04 原始版本文件编号:QF-QC-014 日期:2011-01-04版本:V1.0 页数:第2页共5页1.抽样计划1.1 一般检测:GB/T 2828.1-20031.2 AQL 水准:CR=0;MA:0.65 MI:1.01.3 本物品采用单次抽样正常检验。
1.4 尺寸测量、性能测试:1~500:5PCS501~1000 10PCS1000 以上:20PCS2.抽样频率2.1 同一来料验收单的物料为一批次抽样.3.抽样方法3.1 本物品采用隨机抽样.3.2 5 个包裝单位及5 个以下包裝单位,需从每个包裝单位內取样.3.3 5~25 个包裝单位,至少从5 个包裝单位內取样.3.4 25 个以上包裝单位,需从包裝单位的平方根数內取样.4.定义4.1 BOM ( BILL OF MATERIAL):物料清单.4.2 FAA (FIRST ARTICLE APPROV AL RECORD):第一次样本确认.文件编号:QF-QC-014 日期:2011-01-04版本:V1.0 页数:第3页共5页4.3 DCN/ECN (DESIGN/ENGINEER CHANGE NOTE):设计/工程更改通知.4.4 致命缺陷(Critical Defect) : 产品存在对使用者的人身及财产安全构成威胁的缺陷。
4.5 主要缺陷( Major Defect ) : 产品存在以下五种缺陷为主要缺陷。
---功能缺陷影响正常使用;---性能参数超出规格标准;---漏元件、配件及主要标识;多出无关标识及其他可能影响产品性能的物品;---包装存在可能危及产品性能的缺陷;---结构及外观方面存在让客户难以接受的严重缺陷。
4.6 次要缺陷(Minor Defect) : 上述缺陷以外的其他不影响产品之使用的缺陷。
光伏组件电池板检验规范

本部分按照GB/T1.1-2009和Q/CNEG0202-2016给出的规则起草。
本部分起草单位:本标准主要起草人:本标准于2017年首次发布。
外购光伏组件检验规范1范围本标准规定了工程技术部对外购组件的制程工艺与质量的管控、原材料质量的管控以及对组件外观、功率和EL抽检流程。
本标准适用于外购光伏组件的检验。
2规范性引用文件下列文件中的条款通过本标准的引用而成为本标准的条款。
凡是注日期的引用文件,其随后所有的修订版均不适用于本标准。
凡是不注日期的引用文件,其最新版本适用于本标准。
GB/T2828.1—2012计数抽样检验程序3术语和定义3.1抽样计划依据计数值单次抽样计划表一般检验水平II实施,有特殊要求时依照特殊要求执行。
3.2AQLAcceptedqualitylevel可接受质量水平。
4管理内容与方法4.1检验执行依据4.1.1抽样计划根据GB/T2828.1—2012II表执行,有特殊要求时按特殊要求执行。
4.1.2允收标准致命缺陷(CRI):AQL0严重缺陷(MAJ):AQL0.65轻微缺陷(MIN):AQL1.04.2检验方案表1导电异物面积=$4mm2,任何导电体之间异物距导电体距离之4.3 检验流程图详见附录A4.4 检验流程4.4.1接到采购验货通知后,要求验货供应商提供待验货清单,核对待检验组件的功率是否符合出货要求,并从清单中挑选出需要检验及测试功率的组件,要求供应商提前挑出来放在验货区,并将待测功率组件恒温。
4.4.2供应商提供验货组件原材料详细清单并现场核实,如果发现所用材料与BOM 表不一致,此批组件做拒收处理。
4.4.3 供应商对验货组件进行拆包,在拆包的过程中验货人员确认拆包过程包装箱上的信息等是否符合我司出货要求。
4.4.4 组件外观检验验货人员针对出货前的产品进行外观抽检,依据GB-T2828.1/Lelve2/AQLMA=0.65MI=1.0标准进行抽样,并依据《外购晶硅组件成品检验标准》要求对产品进行判定,将结果记录在《光伏组件检验清单》、ELIV 接线盒位置不被短边框盖住,背板开口完全在接线盒内部。
组件原材料检验标准

辅助材料检验标准(太阳电池组件)太阳电池组件玻璃检验标准1. 适用范围本规范适用于各种规格型号太阳能组件专用玻璃的进厂质量检验。
2. 引用标准GB/T9963-1998钢化玻璃国家检验标准GB2828-1987周期检查计数抽样程序及抽样标准3. 检验项目外观检验,几何尺寸检验和性能检验。
3.1 外观检验项目说明缺陷允许数量表面状况表面清洁、光亮、平整,不允许有擦不掉的白雾状或棕黄色等附着物。
不允许磨边平滑、整齐,不允许有锯齿状存在。
杂质直径0.5mm以下不限小于2.0mm2每平方米不得超过2个爆边爆边长度不超过5mm,自玻璃边部向玻璃表面延伸不得超过3mm,自表面向玻璃厚度方向延伸不得超过玻璃厚度的1/3。
不允许划伤深度小于0.5mm,宽度在1mm以下,长度小于5mm轻微划伤允许存在宽度在1mm以下,长度小于等于10mm 每平方米不得超过2处宽度在1mm以下,长度小于等于20mm 每平方米不得超过1处宽度在1mm以上不允许气泡1mm×2mm 每平方米不得超过2个毛面玻璃0.5×1mm以下允许存在气线宽度小于0.5mm长度小于10mm 每平方米不超过4处气线宽度0.5—1mm,长度小于10mm 每平方米不超过2处缺角小于3mm×3mm 2处结石、突起、翘角、裂纹不允许存在弯曲度平面玻璃弓形≤3‰允许存在毛面玻璃弓形≤3‰允许存在波形≤2‰允许存在3.2 几何尺寸3.2.1 长度,宽度符合订货协议要求,允许偏差为±1.0mm。
3.2.2 厚度尺寸公差为±0.2mm。
3.2.3 直角度误差小于其所在边长的±2‰。
3.3 性能检验检验项目标准要求备注机械强度重1024克的钢球,自高度为1米处,自由落体从玻璃正面砸下,玻璃完好无损。
透光率>90%钢化粒度大于40粒/5cm*5cm 国产玻璃70—80 粒/5cm*5cm 进口玻璃比重 2.5g/cm34. 检测仪器,仪表及工卡量具钢板尺或钢卷尺、游标卡尺或千分尺、钢球。
电池产品检验标准
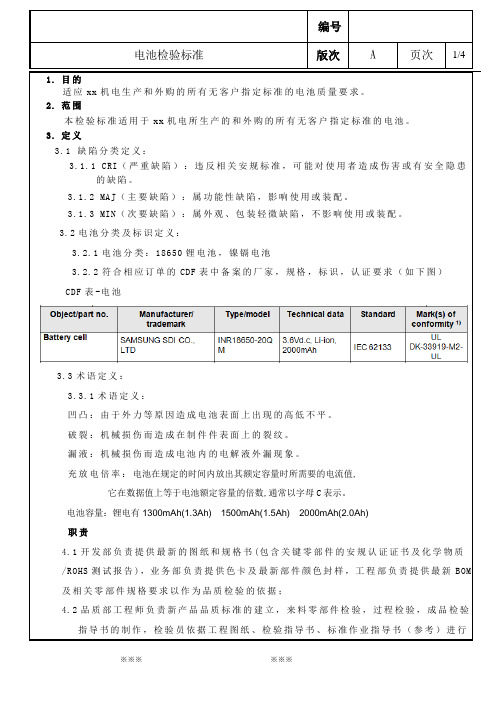
1.目的适应xx机电生产和外购的所有无客户指定标准的电池质量要求。
2.范围本检验标准适用于xx机电所生产的和外购的所有无客户指定标准的电池。
3.定义3.1 缺陷分类定义:3.1.1 CRI(严重缺陷):违反相关安规标准,可能对使用者造成伤害或有安全隐患的缺陷。
3.1.2 MAJ(主要缺陷):属功能性缺陷,影响使用或装配。
3.1.3 MIN(次要缺陷):属外观、包装轻微缺陷,不影响使用或装配。
3.2电池分类及标识定义:3.2.1电池分类:18650锂电池,镍镉电池3.2.2符合相应订单的CDF表中备案的厂家,规格,标识,认证要求(如下图)CDF表-电池3.3术语定义:3.3.1术语定义:凹凸:由于外力等原因造成电池表面上出现的高低不平。
破裂:机械损伤而造成在制件件表面上的裂纹。
漏液:机械损伤而造成电池内的电解液外漏现象。
充放电倍率:电池在规定的时间内放出其额定容量时所需要的电流值,它在数据值上等于电池额定容量的倍数,通常以字母C表示。
电池容量:锂电有1300mAh(1.3Ah) 1500mAh(1.5Ah) 2000mAh(2.0Ah)职责4.1开发部负责提供最新的图纸和规格书(包含关键零部件的安规认证证书及化学物质/ROHS测试报告),业务部负责提供色卡及最新部件颜色封样,工程部负责提供最新BOM 及相关零部件规格要求以作为品质检验的依据;4.2品质部工程师负责新产品品质标准的建立,来料零部件检验,过程检验,成品检验指导书的制作,检验员依据工程图纸、检验指导书、标准作业指导书(参考)进行☆检验标准:符合规格书中放电倍率性能测试要求6.6.2高温自放电性能☆试验方法:1C充电后,搁置30min,分别以5C,5C,1C进行放电至终止电压,记录放电容量/时间,放入烘箱40℃30天后,进行1C放电至终止电压☆检验标准:符合测试大纲中的高温自放电要求6.6.3充放电循环寿命测试☆试验方法:1C充电后,搁置10min,以10C放电到2.75V,完成一个循环,搁置30min,重复上述步骤。
电池主要性能检验标准及检测方法
内阻
• 电流通过电池时所遇到的阻力。它包括电池内部各元件 (电极、隔膜、电解液等)所具有的欧姆内阻和电化学反 应过程中的极化内阻。电池内阻是电池的一个重要参数。 电池的内阻愈小,其适应大电流放电的性能愈强。 • 电池内阻包括欧姆内阻和极化内阻,极化内阻又包括电化 学极化与浓差极化。内阻的存在,使电池放电时的端电压 低于电池电动势和开路电压,充电时端电压高于电动势和 开路电压。 • 电池的内阻不是常数,在放电过程中随时间不断变化,因 为活性物质的组成、电解液浓度和温度都在不断地改变。 • 欧姆电阻遵守欧姆定律;极化电阻随电流密度增加而增大, 但不是线性关系,常随电流密度的对数增大而线性增大。
循环寿命
BAK:1C循环100次,容量保持率大于90% 1C循环300次,容量保持率大于80%
荷电保持能力
BAK
贮存性能
BAK
跌落
BAK
振动
BAK
温度循环
BAK
恒温恒湿
BAK
高低温性能
BAK
BAK
低压
BAK
热冲击
BAK
过充
BAK:3C/4.6v
三三电三
LAND或擎天检测柜 LAND或擎天检测柜 电热鼓风恒温干燥箱
电压
1)开路电压 电池在开路状态下的端电压称为开路电压。电池的开 路电压等于电池的正极的还原电极电势与负极电极电势之 差。 2)工作电压 工作电压指电池接通负载后在放电过程中显示的电压, 又称放电电压。在电池放电初始的工作电压称为初始电压。 3)电池在接通负载后,由于欧姆电阻和极化过电位的存在, 电池的工作电压低于开路电压。
容量
电池的容量是指在一定的放电条件下,可以从电池获得的电量,以符号C标 识,单位常用“安培﹒小时” 表示。简称安时(Ah)或毫安时(mAh); 电池的容量又有理论容量、实际容量和额定容量之分。 理论容量(C0):是假设电极的活性物质参加电极的成流反应所给出的电量, 是根据活性物质的质量按照法拉第定律计算求得的。 实际容量:是指在一定的放电条件下电池实际放出的电量。当恒电流放电时: C = I T。其值小于理论值。 额定容量:是指设计和制造电池时,规定或保证电池在一定的放电条件下, 应该放出的最低限量的电流。 方型锂电容量的计算: 以一定的充电速率( 恒流充电至4.2V,再以 以一定的充电速率(1C)恒流充电至 恒流充电至 ,再以4.2V 恒压充电至电流小于 0.02C,之后以一定的放电速率 放电至3.0V(2.75V)的容量(容量以 或 ,之后以一定的放电速率(1C)放电至 放电至 ( )的容量(容量以Ah或 mAh表示;C为充放电倍率单位 ,高于1200mAh的型号以 表示; 为充放电倍率单位1/h,高于 的型号以0.5c充放)。 充放)。 表示 为充放电倍率单位 的型号以 充放
组件检验标准
1. 目的本标准提出对太阳电池组件进行检验的工艺过程、内容及要求,保证产品质量。
2. 适用范围适用于质量部门对太阳电池组件的成品检验和生产上的质量自检。
3. 使用的设备和工具(1)直尺;(2)卷尺;(3)塞尺;(4)游标卡尺4.2电性能测试:检验工具:太阳能模拟器、计算机检验内容:太阳电池组件的电性能检验方法:打开太阳能模拟器和计算机,打开测试软件;用标准组件校准太阳能模拟器;用连接工装连接组件输出的正、负极;开始测试组件,间隔几秒会在屏幕上弹出I-V曲线以及相关参数界面;保存对话框中的参数与I-V曲线,观察曲线无异常;组件功率误差在标称功率要求(0~+3%或±3%)内为合格,否则降档。
同时对外观进行以上外观检验标准检验,不符合以上外观检验要求,降级入库。
检验水平:全检4.3数据:检验工具:(计算机数据检验)根据出厂数据格式进行数据备份,各类数据需准确一致;数据实行全检。
4.4绝缘试验:检验工具:耐压测试仪检验内容:组件直流电压耐压检验条件:环境温度:室温,相对湿度:≤75%检验方法:将组件引出线短路后接到绝缘测试仪的正极;将组件暴露的金属部分接到绝缘测试仪的负极,以不大于500V/s的速度增加绝缘测试仪的电压,直到等于1000V加上两倍的系统最大电压,维持此电压1分钟。
如果系统的最大电压不超过50V,应以不大于500V/s的速度增加绝缘测试仪的电压,直到等于500V,维持此电压2分钟;试验中不应该产生击穿现象,漏电流小于50μA,绝缘电阻大于500兆欧。
表面无破裂。
检验水平:0.5%。
若批量数少于200片,最少抽检一片。
4.5抽检检验的判别:a.抽检检验的比例为20%。
电池测试标准判断标准
电池测试标准判断标准
电池测试标准判断标准如下:
●容量测试:电池容量是指电池放电的能量大小,通常用安时(Ah)
表示。
容量测试是确定电池能供给多长时间的重要参数,测试方法主要有恒流放电法、恒功率放电法等。
●内阻测试:电池内阻是指电流通过电池时所遇到的电阻,通常用
欧姆(Ω)表示。
内阻测试是确定电池放电时能否提供足够电流的重要参数,测试方法主要有交流内阻测试法、直流内阻测试法等。
●循环寿命测试:循环寿命是指电池能够经受多少次充放电后仍能
正常使用的次数,通常用循环次数表示。
循环寿命测试是验证电池使用寿命的重要参数,测试方法主要有充放电循环测试法、加速循环测试法等。
组件成品外观检验标准
作业类别成品检验发布日期1、目的为了使组件产品质量满足质量要求,明确组件的等级判定标准,制订本规定。
2、范围本要求适用于本公司生产的标准系列晶体硅太阳电池组件的成品质量等级判定。
3、参考文件3.1.地面用晶体硅太阳电池组件--浙江光普能源有限公司组件工艺标准4、术语和定义优质:外观、电性能均良好A级:外观有不良,电性能正常B级:外观有较严重不良和组件内有多处低效片和裂片,通过返工,电性能基本正常(两种情况可同时存在)。
报废:外观有严重不良或电性能异常,低效片或裂片较多,不值得返工或无法返工。
5、检验方法5.1.组件的外观检验应在不低于1000lx的照度下,距离0.5米,裸眼视力在1.2以上对每一个组件仔细检查。
5.2.对于铝型材和钢化玻璃划伤的检验:采用在1000lx的照度下,距离1米,裸眼视力在1.2以上对材料进行观察,若看不见的则判定为优质组件,看的见的则判定为A-1级组件。
5.3.对于色差组件的检验:采用在1000lx的照度下,距离2米,裸眼视力在1.2以上对垂直放置在桌面上的组件进行观察,若没有明显色差则判定为优质组件,有明显色差的则判定为A-1级组件。
5.4.通过EL测试后,存在隐裂电池片的组件,根据隐裂电池片数量、单片裂纹条数、隐裂裂纹的形状、失效面积的尺寸来进行判定。
6、检验及判定规则6.1组件产品质量等级分为:优质、A、B级、报废4种。
6.2等级区分只为针对组件的判定,对于客户只有B级、报废作为特殊组件,其余统称为优质组件。
长度≤5cm,宽度≤2mm同优质同优质个不允许条无多余胶带伸到流水孔外面积≤4mm²、每根边框数量≤面积≤8mm²,数量≤长度≤5cm,宽度≤同优质同优质不允许接线盒上有硅胶组件电池颜色均匀一致,颜色范围从黑色开始,经深蓝色、蓝色到淡蓝色,允许相近颜色,但不允许电池片跳色,如:从黑色到蓝色。
优质组件颜色区分标识:单晶黑色和多晶蓝色无需标识,单晶蓝色组件需在组件背面标识"LS",多晶淡蓝色需在组件背面标识不在电池片上,a)不允许有三角形缺口和尖锐形缺大于0.5mm。
- 1、下载文档前请自行甄别文档内容的完整性,平台不提供额外的编辑、内容补充、找答案等附加服务。
- 2、"仅部分预览"的文档,不可在线预览部分如存在完整性等问题,可反馈申请退款(可完整预览的文档不适用该条件!)。
- 3、如文档侵犯您的权益,请联系客服反馈,我们会尽快为您处理(人工客服工作时间:9:00-18:30)。
关于设置产品质量等级的规定
文件编号:
发布日期:
版本(次:
批准人:
审核人:
制订人:
为了更好的掌握、控制产品质量,满足广大客户对产品性价比的不同要求,同时兼顾企业自身经济效益,经研究,公司决定对产品质量实行等级控制制度。
具体质量等级设置如下:
一、产品技术等级的划分
二、产品配置标准
三、主原材料检验标准
1.芯片检验标准
2.玻璃检验标准
3.铝合金检验标准
4.涂锡带检验标准
尺寸公差≤±0.01mm,涂锡层均匀,易于焊接,抗拉强度好,不易断裂。
5.EVA、TPT检验标准
按照供应商出产标准及工艺要求进行检验。
四、成品检验标准。