最新反应器设计
UASB厌氧反应器的设计

UASB厌氧反应器的设计一、UASB厌氧反应器的设计厌氧处理已经成功地于各种高、中浓度的废水处理中。
虽然中、高浓度的废水在相当程度上得到了解决,但是当污水中含有降低性物质时,如含有硫酸盐的味精废水在处理上仍有一定的难度。
在厌氧处理领域应用较为广泛的是UASB反应器,其与其它的厌氧处理工艺有一定的共同点。
包含厌氧处理单元的水处理过程一般包括预处理、厌氧处理(包括沼气的收集、处理和利用)、好氧后处理和污泥处理等部分,二、UASB系统设计1、预处理设施一般预处理系统包括粗格栅、细格栅或水力筛、沉砂池、调节(酸化)池、营养盐和pH调控系统。
格栅和沉砂池的目的是去除粗大固体物和无机的可沉固体,这对对于保护各种类型厌氧反应器的布水管免于堵塞是应有的。
当污水中含有砂砾时,例如以薯干为原料的酿酒废水,怎么强调去除砂砾的重要性也不过分。
不可生物降解的固体,在厌氧反应器内积累会占据大量的池容,反应器池容的不断减少终将导致系统完全失效。
由于厌氧反应对水质、水量和冲击负荷较为敏感,所以对于工业废水适当尺寸的调节池,对水质、水量的调节是厌氧反应稳定运行的保证。
调节池的作用是均质和均量,一般还可考虑兼有沉淀、混合、加药、中和和预酸化等功能。
在调节池中设有沉淀池时,容积需扣除沉淀区的体积;根据颗粒化和pH调节的要求,当废水碱度和营养盐不够需要补充碱度和营养盐(N、P)等;可采用计量泵自动投加酸、碱和药剂,通过调节池水力或机械搅拌达中和作用。
同时,酸化池或两相系统是去除和改变,对厌氧过程有降低作用的物质、改善生物反应条件和可生化性也是厌氧预处理的主要手段,也是厌氧预处理的目的之一。
仅考虑溶解性废水时,一般不需考虑酸化作用。
对于复杂废水,可在调节池中取得一定程度的酸化,但是完全的酸化是没有必要的,甚至是有害处的。
因为达到完全酸化后,污水pH会下降,需采用投药调整pH值。
另外有证据表明完全酸化对UASB反应器的颗粒过程有不利的。
对以下情况考虑酸化或相分离可能是有利的:(1)当采用预酸化可去除或改变对甲烷菌有毒或降低性化合物的结构时;(2)当废水存在有较高的Ca2+时,部分酸化可避免颗粒污泥表面产生CaCO3结垢;(3)在调节池中取得部分酸化效果可以通过调节池的合理设计取得。
环氧丙烷反应器设计
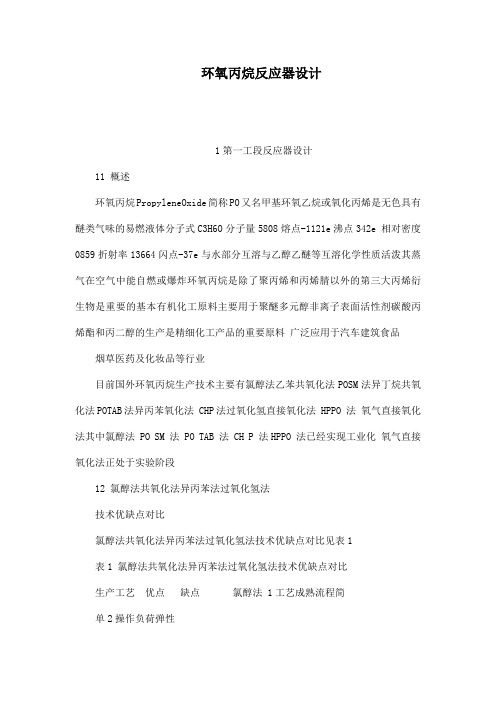
环氧丙烷反应器设计1第一工段反应器设计11 概述环氧丙烷PropyleneOxide简称PO又名甲基环氧乙烷或氧化丙烯是无色具有醚类气味的易燃液体分子式C3H6O分子量5808熔点-1121e沸点342e 相对密度0859折射率13664闪点-37e与水部分互溶与乙醇乙醚等互溶化学性质活泼其蒸气在空气中能自燃或爆炸环氧丙烷是除了聚丙烯和丙烯腈以外的第三大丙烯衍生物是重要的基本有机化工原料主要用于聚醚多元醇非离子表面活性剂碳酸丙烯酯和丙二醇的生产是精细化工产品的重要原料广泛应用于汽车建筑食品烟草医药及化妆品等行业目前国外环氧丙烷生产技术主要有氯醇法乙苯共氧化法POSM法异丁烷共氧化法POTAB法异丙苯氧化法 CHP法过氧化氢直接氧化法 HPPO 法氧气直接氧化法其中氯醇法 PO SM 法 PO TAB 法 CH P 法HPPO 法已经实现工业化氧气直接氧化法正处于实验阶段12 氯醇法共氧化法异丙苯法过氧化氢法技术优缺点对比氯醇法共氧化法异丙苯法过氧化氢法技术优缺点对比见表1表1 氯醇法共氧化法异丙苯法过氧化氢法技术优缺点对比生产工艺优点缺点氯醇法 1工艺成熟流程简单2操作负荷弹性大3选择性好4对原料丙烯的纯度要求不高5安全性高6投资少7有成本竞争力 1水耗大 2 产生大量废水及废渣每生产1t环氧丙烷产生40 50 t含氯化物废水和2 1 tCaCl2 3 消耗大量氯气和石灰原料污染环境 4 产生的次氯酸对设备的腐蚀严重共氧化法PO SM 法PO T BA 法 1 共氧化法克服了氯醇法腐蚀废水量大缺点 2 产品成本低联产品分摊成本 3 环境污染小 1 工艺流程长 2 原料品种多 3 丙烯纯度要求高 4 工艺操作压力高 5 设备造价高设备材质多采用合金钢 6 联产2 2 2 5t 苯乙烯或2 3 t 叔丁醇受市场因素制约7 废水含C OD 高异丙苯氧化法CH P 法与氯醇法相比 1 不需要氯气减少了设备腐蚀 2 废水量少与共氧法相比 1 无副产品使用异丙苯替代了乙苯异丙苯循环使用 2 不联产苯乙烯无需辅加设备 3 装置投资少比共氧化法低1 3 生产过程中产生大量A-甲基苯乙烯增加循环回收装置过氧化氢氧化法H PPO 法 1 工艺流程简单 2 产品收率高无副产品3 无污染属清洁工艺原料辅助原料产品的主要技术规格表1-3主要工艺物料消耗与规格名称规格用量丙烯工业级 22万ta 双氧水工业级18万ta 甲醇工业级 xxxta 氢气纯氢气 11万ta22 原辅料规格及消耗配比表2 原辅料规格及消耗配比原辅料规格配比原料双氧水工业级原料丙烯工业级原料丙烷工业级原料甲醇工业级催化剂 TS-1 7323 产品质量标准2-1产品规格等级项目指标优等品一等品合格水分质量分数002 002 01 醛质量分数001 003 01 环氧乙烷质量分数001 01 03 GB14491-2001产品外观要求透明液体无可见机械杂质工业用环氧丙烷应符合表1-1规格要求表2-2产品技术要求项目指标优等品一等品合格色度铂-钴色号号≤ 5 10 20 酸度质量分数以乙酸计算≤001 003 001 GB14491-2001环氧丙烷主要用与聚醚多元醇的生产和丙二醇和一些非离子表面活性剂这些靖西化工产品所以对于环氧丙烷的规格要求就要严格的多我们在项目生产中会严格把持产品的纯度和质量3 反应工段工艺简介4 反应工段工艺计算本工艺[4]是在压力为03MPa温度为55℃下在TS-1上进行的等温液固相催化反应41 催化反应过程的物料衡算411 计算用原始数据此处所选的8原始数据均为年产30万吨环氧丙烷的中间试验数据进入反应器时甲醇含量约为7226丙烯含量约为1093摩尔分数412 化学反应主反应[5]平行反应表5 反应中涉及到的物质的相对分子质量CH3OH H2O2 C3H6 C3H8 H2O C3H6O 32 34 42 44 18 58413 物料衡算过程催化合成甲醛过程是一个连续流动反应在定态下其物料衡算基本公式本工艺计算[6]以生产30万吨甲醛按300天计工业级别的甲醛质量分数为96则每小时一个反应器生产工业级别的环氧丙烷的质量其物质的量为并以其为基准4131 反应器进口物料的计算根据表3表5中各组分的数据计算可得纯甲醇的物质的量10133kmolh水物质的量18281kmolh丙烯153226kmolh丙烷9428kmolh双氧水36264kmolh表6原料液的组成及含量物质摩尔分数物质的量kmolh CH3OH 7226 10133 H2O2 259 36264 H2O 1303 18281 C3H6 1093 153226C3H8 07 9428 NH3 05 7243 4132 反应器出口物料的计算甲醇的物质的量 10133kmolh生成环氧丙烷的物质的量34814kmolh水的物质的量217623kmolh未反应的双氧水的物质的量1451kmolh丙烯的物质的量1184kmolh丙烷的物质的量9427kmolh丙二醇甲醚的物质的量068kmolh表7 反应器出口主要气体的组成及含量物质摩尔分数物质的量kmolh CH3OH 84 10133 C3H6O 15 34814 H2O 91 217623 H2O2 006 1451 PE 004 1022C3H8O2-2 001 068 NH3 002 7243 C3H6 50 1184 42 合成甲醛过程的热量衡算热量衡算过程以03MPa下的液体为计算基准反应液体于常压下进入反应器在催化剂作用下进行恒温反应反应器出口气体以离开反应器总的热量衡算式为421 各物质比热容的计算每个组分的热容与温度的函数式即CpabTcT2表8 各物质平均温度为的物性物质 C3H8 1837 250-1500 C3H6 8256 250-1500 H2O 1907 250-1500 CH3OH 250-1500 CpC3H818372816×10-1T-1319×10-8T2 CpC3H682562174×10-1T-09692×10-6T2Cp32241907×10-3T-10057×10-6T2Cp21147084×10-3T-2586×10-6T2把T27350323K带入上述公式得同理可计算其他物质的比热容其结果如下表表9 各物质在平均温度为的物质C3H8 C3H6 H2O CH3OH C3H6O H2O2 9424 78207 318 4133 13799 50284422 各物质焓值的计算计算焓热量是时在等温条件下反应的参考态32315℃03Mpa又双氧水的消耗量为由得即为了维持反应器内温度为32315℃应每小时从反应器移走的热量43用量的确定列管式固定床反应器的壳程走冷凝水移走反应放出的热量使冷凝水从20 ℃升温到40℃表10 冷凝水的物性数据名称平均分子量密度比热容导热系数冷凝水 18 9957 4178 0618 由得冷凝水用量在工程上要确定反应器的几何尺寸首先得确定一定生产能力下所需的催化剂容积再根据工程实验所提供的反应器资料最后确定出反应器的几何尺寸522 催化剂容积的计算5221 催化剂用量的计算合成环氧丙烷的反应是一个气固相催化反应催化剂的用量需要根据反应工程上通过单位催化剂列物料衡算的动力学方程才能得出合成甲醛的动力学方程为其中PO环氧丙烷式中各物质摩尔分数的计算合成环氧丙烷的反应在双氧水转化率为84时到达平衡达平衡时双氧水的摩尔浓度为求解动力学方程由定义有查得令即则两边同时积分得其中用辛普森数值积分法求解定积分数值积分法为其中实用于奇数个数据点n为偶数f的角标代表选取数据点的编号且点与点之间等间距表11 与的关系0 012 024 036 048 060 072 084114913161515 1786 2203 2857 4167 7992 则因此催化剂所需质量反应采用的催化剂为钛硅分子筛催化剂成粒状粒度为6mm堆密度为比表面积为54故反应所需的体积523 列管根数的确定由催化剂所算得反应器体积太小反应物流量过大故选择用停留时间与流量的关系得出反应器总体积一小时的体积流量反应时间取十分钟反应器体积根据中间试验的结果列管规格为管长为L18m解方程得n2475根524 列管式固定床反应器壳体内径的确定由公式[11]式中D壳体内径 mmt管中心距 mm横过管束中心线的管束b 一般取 mm管子采用正三角形排列故带入公式得标准化后核算过程管长和壳径应相适应一般取LD为46对该反应器因此所设计的反应器符合实际情况实际催化剂用量53 等温固定床列管式反应器的设计计算结果表12 等温固定床列管式反应器的设计计算结果序号项目数据 123456789101112 列管式反应器入口温度列管式反应器出口温度反应压力原料甲醇的量原料丙烯的量原料水的量催化剂床层高度塔径催化剂用量列管根数列管规格管子排列方式50℃50℃03MPa10133kmolh153236kmolh18281kmolh18m38m58048kg2107根Φ57×25mm三角形排列第二工艺工段反应器设计4 反应工段工艺计算本工艺[4]是在压力为03MPa温度为55℃下在TS-1上进行的等温液固相催化反应41 催化反应过程的物料衡算411 计算用原始数据此处所选的8原始数据均为年产30万吨环氧丙烷的中间试验数据进入反应器时甲醇含量约为766丙烯含量约为58摩尔分数412 化学反应主反应[5]平行反应表5 反应中涉及到的物质的相对分子质量CH3OH H2O2 C3H6 C3H8 H2O C3H6O 32 34 42 44 18 58413 物料衡算过程催化合成环氧丙烷过程是一个连续流动反应在定态下其物料衡算基本公式此设备的进料为第一设备以生产50万吨甲醛按300天计工业级别的环氧丙烷质量分数为96则每小时一个反应器生产工业级别的环氧丙烷的质量其物质的量为并以其为基准4131 反应器进口物料的计算根据表3表5中各组分的数据计算可得纯甲醇的物质的量9840670kmolh水物质的量2171248kmolh丙烯744475kmolh丙烷45823molh双氧水10879kmolh氨水29432kmolh表6原料液的组成及含量物质摩尔分数物质的量kmolh CH3OH 9221 9840670H2O2 01 10879 H2O 1303 217124 C3H6 698 744475 C3H8 043 45823 NH3 028 29432 4132 反应器出口物料的计算甲醇的物质的量[7]984067kmolh生成环氧丙烷的物质的量10335kmolh水的物质的量218158kmolh未反应的双氧水的物质的量054kmolh丙烯的物质的量73414kmolh丙烷的物质的量4582kmolh氨水29432kmolh表7 反应器出口主要气体的组成及含量物质摩尔分数物质的量kmolh CH3OH 7663 984067 C3H6O 008 34814 H2O 1699 218158 H2O2 00 0544 NH3 023 29432 C3H8 036 45823 C3H6 57 73414 42 合成环氧丙烷过程的热量衡算热量衡算[8]过程以03MPa下的液体为计算基准反应液体于常压下进入反应器在催化剂作用下进行恒温反应反应器出口气体以离开反应器总的热量衡算式为421 各物质比热容的计算每个组分的热容与温度的函数式即CpabTcT2表8 各物质平均温度为的物性物质 C3H8 1837 250-1500 C3H6 8256 250-1500 H2O 1907 250-1500 CH3OH 250-1500 CpC3H818372816×10-1T-1319×10-8T2CpC3H682562174×10-1T-09692×10-6T2Cp32241907×10-3T-10057×10-6T2Cp21147084×10-3T-2586×10-6T2把T27350323K带入上述公式得同理可计算其他物质的比热容其结果如下表表9 各物质在平均温度为的物质C3H8 C3H6 H2O CH3OH C3H6O H2O2 9424 78207 318 4133 13799 50284422 各物质焓值的计算计算焓热量是时在等温条件下反应的参考态32315℃03Mpa又双氧水的消耗量为由得即为了维持反应器内温度为32315℃应每小时从反应器移走的热量43冷凝水用量的确定列管式固定床反应器的壳程走冷凝水移走反应放出的热量使冷凝水从20 ℃升温到40℃表10 冷凝水的物性数据名称平均分子量密度比热容导热系数冷凝水 18 9957 4178 0618 由得冷凝水用量522 催化剂容积的计算5221 催化剂用量的计算合成甲醛的反应是一个气固相催化反应催化剂的用量需要根据反应工程上通过单位催化剂列物料衡算的动力学方程才能得出合成甲醛的动力学方程为其中PO环氧丙烷式中各物质摩尔分数的计算合成环氧丙烷的反应在双氧水转化率为96时到达平衡达平衡时双氧水的摩尔浓度为求解动力学方程由定义有查得令即则两边同时积分得其中用辛普森数值积分法求解定积分数值积分法[10]为其中实用于奇数个数据点n为偶数f的角标代表选取数据点的编号且点与点之间等间距表11 与的关系0 012 024 036 048 060 072 08425833271438464602558823775491191258709 则因此催化剂所需质量反应采用的催化剂为活性炭吸附钛硅分子筛催化剂成粒状粒度为6mm堆密度为比表面积为54故反应所需的体积由催化剂所算得反应器体积太小反应物流量过大故选择用停留时间与流量的关系得出反应器总体积一小时的体积流量反应时间取十分钟反应器体积总体积根据中间试验的结果列管规格为管长为L18m解方程得n2385根524 列管式固定床反应器壳体内径的确定由公式[11]式中D壳体内径 mmt管中心距 mm横过管束中心线的管束b 一般取 mm管子采用正三角形排列故带入公式得标准化后核算过程管长和壳径应相适应一般取LD为46对该反应器因此所设计的反应器符合实际情况53 等温固定床列管式反应器的设计计算结果表12 等温固定床列管式反应器的设计计算结果序号项目数据 123456789101112 列管式反应器入口温度列管式反应器出口温度反应压力原料甲醇的量原料丙烯的量原料水的量催化剂床层高度塔径催化剂用量列管根数列管规格管子排列方式50℃50℃03MPa10133kmolh153236kmolh18281kmolh18m4m2385根Φ57×35mm三角形排列2132料液泵设计计算由于是泵加料取由于料液流量过大选用2个加料泵流量单个泵流量密度进料管管径设料液至加料孔的高度弯头取90弯头则料液由平均黏度和各组分黏度关系7液体料液加料泵在料液面与进料孔面之间列伯努利方程泵的实际功率取泵的总效率则泵的实际功率则流量为查泵性能图可得选型如下泵规格G263-165-132N 流量263m3 扬程165m汽蚀余量3m31 固定床DNPN将固定反应器视为筒体本设计采用一般的反应釜由反应器内物料为液相由则圆整32 筒体壁厚最大操作压力为设计压力P取最大工作压力的10511倍[2]本设计取设计压力设计温度T根据筒体设计压力和设计温度选择材料Q345R许用应力为焊缝系数=10双面对接焊100无损探伤表3-1 焊接接头系数φ无损检测的长度比例焊接接头形式全部局部双面焊对接接头或相当于双面焊的对接接头085 单面焊对接接头沿焊缝根部全长有紧贴基本金属的垫板09 08 理论厚度钢板负偏差C1腐蚀裕量C2C22mm单面面腐蚀表3-2 钢板负偏差C1钢板厚度 2 22 25 28-30 22-35 38-4 45-55 负偏差 013 014 015 016 018 02 02 钢板厚度6-7 8-25 26-30 32-34 36-40 42-50 52-60 负偏差 06 08 09 1 11 12 13根据内压圆筒壁厚的计算公式带入以上数据得根据工程要求和钢材的使用壁厚范围圆整后取校核筒体水压试验强度根据式因为Q345R的屈服极限所以取代入得故水压试验满足强度要求33 封头封头包括有椭圆形碟形锥形球冠形封头平板封头等多种类型从工艺操作要求考虑对封头形状无特殊要求球冠形封头平板封头都存在较大的边缘应力且采用平板封头厚度较大故不宜采用半球形封头受力最好壁厚最薄重量轻但深度大制造较难中低压小设备不宜采用碟形封头存在局部应力受力不如椭圆形封头标准椭圆形封头制造比较容易受力状况比碟形封头好综合考虑该精馏塔设计内压温度等因素最终确定采用标准椭圆形封头选釜体的封头选标准椭球型代号EHA标准JBT47462002封头以Q345R为材料标准形封头壁厚其中整体冲压钢板负偏差代入得根据工程要求和钢材的使用壁厚范围圆整后取与前计算的筒体壁厚一致内表面积封头的标准为EHA 4000×13-Q235R JBT 4746综上筒体和封头选材都为Q235R壁厚34 筒体长度HDN4000mmH18M以内径为公称直径的椭圆形封头的尺寸内表面积和容积可得由于使用的是标准封头所以所以可得封头的高度h2m整体塔高度第三部分塔设备设计第1章固定床反应器设备设计说明书1材料的选择在刚度或结构设计为主的场合应尽量选用普通碳素钢在以强度设计为主的场合应根据压力温度介质等使用限制选用Q235由于容器设计压力为014MPa使用温度为50℃故筒体和封头都选择Q345RQ345R钢是屈服强度为340MPa级的压力容器专用板它具有良好的综合力学性能和工艺性能选择椭圆形封头2 裙座材料的选择裙座不直接与塔内介质接触也不承受塔内介质的压力因此不受压力容器用材的限制可选用较经济的普通碳素结构钢故选用Q235-A3 接管的材料选用Q235-B作为补强圈的材料部分接管用20法兰选用20具体将在装配图上注明11气体和液体的进出口装置由Vs 为流体的体积流量m3su 为适宜的流体流速ms常压气体进出口管气速可取1020ms液体进出口速度可取0815 ms选用气体流速为15ms代入上式计算得圆整之后气体进出口管径为d250mm 选液体流速为15ms由代入上公式得圆整之后气体进出口管径为d40mm 底液出口管径选择12原料液进出管的选择1进料管300mm选的流体输送用无缝钢管《GBT8163-2008流体输送用无缝钢管》标记10- -GBT8163-2008查《GBT17395-2008无缝钢管尺寸外形重量及允许偏差》具体参数见表3-1 2出料管当时d034md40mm选的流体输送用无缝钢管《GBT8163-2008流体输送用无缝钢管》弯管结构R 为650mm标记10--GBT8163-2008查《GBT17395-2008无缝钢管尺寸外形重量及允许偏差》具体参数见表3-1表2-1普通钢管尺寸及单位长度理论重量外径mm 壁厚mm 单位长度理论重量kgm 325 75 5873 48 3 333 13筒体和封头的设计材料选择筒体的设计化工设备机械基础厚度计算解得圆整后表3-1筒体的容积面积及重量公称直径Dgmm 一米高的容积Vm3 一米高的内裹面积Fgm2 壁厚Smm 一米高筒节钢板理论重量kg 900 0636 283 4 79 封头的设计选用标准GB_T 25198-2010_压力容器封头图3-1椭圆形封头的结构示意图选用标准GB_T 25198-2010_压力容器封头表3-2筒体的容积面积及重量公称直径Dgmm 曲面高度h1mm 直边高度H2mm 厚度Smm 重量Gkg 900 220 30 4 292 14法兰的设计1管法兰的选择选用标准HG20593-97板式平焊钢制管法兰欧洲体系图3-2板式平焊钢制法兰PL表4-1PN06MPa60bar板式平焊钢制管法兰mm管子直径mm 法兰内径mm 螺栓孔中心圆直径mm 公称直径mm 螺栓孔直径mm 螺栓孔数量n 法兰外径mm 法兰厚度mm 法兰理论重量kg 液体进出口57 59 125 50 18 4 165 19 25 气体进出口325 328 400 300 22 12 445 26 135 标记液体进出口HG20593法兰PL57-06FFQ235-A气体进出口HG20593法兰PL325-06FFQ235-A2容器法兰的选择选用标准JBT4701-2000甲型平焊法兰标记法兰P900-4010-JBT4701-2000图3-3甲型平焊法兰平面密封面代号P表4-2PN025MPa甲型平焊法兰的结构尺寸mm公称直径 DNmm 法兰mm 螺柱D D1 δ d 规格数量900 1015 980 40 18 M16 36三反应釜釜体的设计31 固定床DNPN将固定反应器视为筒体本设计采用一般的反应釜由反应器内物料为液相由则圆整32 筒体壁厚最大操作压力为设计压力P取最大工作压力的10511倍[2]本设计取设计压力设计温度T根据筒体设计压力和设计温度选择材料Q345R许用应力为焊缝系数=10双面对接焊100无损探伤表3-1 焊接接头系数φ无损检测的长度比例焊接接头形式全部局部双面焊对接接头或相当于双面焊的对接接头085 单面焊对接接头沿焊缝根部全长有紧贴基本金属的垫板09 08 理论厚度钢板负偏差C1腐蚀裕量C2C22mm单面面腐蚀表3-2 钢板负偏差C1钢板厚度 2 22 25 28-30 22-35 38-4 45-55 负偏差 013 014 015 016 018 02 02 钢板厚度6-7 8-25 26-30 32-34 36-40 42-50 52-60 负偏差 06 08 09 1 11 12 13根据内压圆筒壁厚的计算公式带入以上数据得根据工程要求和钢材的使用壁厚范围圆整后取校核筒体水压试验强度根据式因为Q345R的屈服极限所以取代入得故水压试验满足强度要求33 封头封头包括有椭圆形碟形锥形球冠形封头平板封头等多种类型从工艺操作要求考虑对封头形状无特殊要求球冠形封头平板封头都存在较大的边缘应力且采用平板封头厚度较大故不宜采用半球形封头受力最好壁厚最薄重量轻但深度大制造较难中低压小设备不宜采用碟形封头存在局部应力受力不如椭圆形封头标准椭圆形封头制造比较容易受力状况比碟形封头好综合考虑该精馏塔设计内压温度等因素最终确定采用标准椭圆形封头选釜体的封头选标准椭球型代号EHA标准JBT47462002封头以Q345R为材料标准形封头壁厚其中整体冲压钢板负偏差代入得根据工程要求和钢材的使用壁厚范围圆整后取与前计算的筒体壁厚一致内表面积封头的标准为EHA 4000×13-Q235R JBT 4746综上筒体和封头选材都为Q235R壁厚34 筒体长度HDN4000mmH18M以内径为公称直径的椭圆形封头的尺寸内表面积和容积可得由于使用的是标准封头所以所以可得封头的高度h2m整体塔高度。
聚合氯化铝合成新型反应器设计与智能控制技术创新
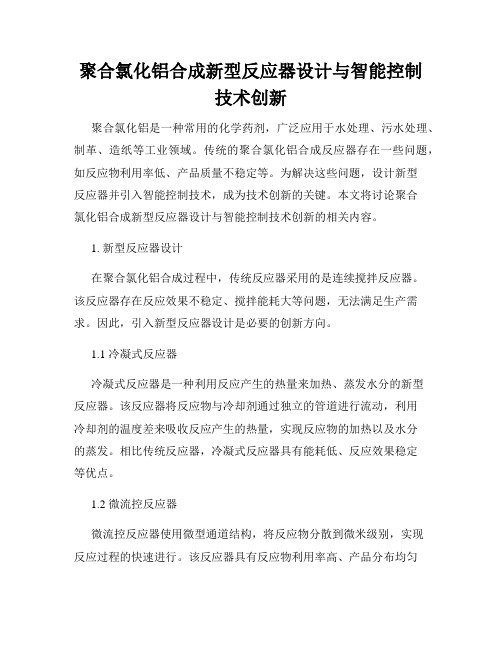
聚合氯化铝合成新型反应器设计与智能控制技术创新聚合氯化铝是一种常用的化学药剂,广泛应用于水处理、污水处理、制革、造纸等工业领域。
传统的聚合氯化铝合成反应器存在一些问题,如反应物利用率低、产品质量不稳定等。
为解决这些问题,设计新型反应器并引入智能控制技术,成为技术创新的关键。
本文将讨论聚合氯化铝合成新型反应器设计与智能控制技术创新的相关内容。
1. 新型反应器设计在聚合氯化铝合成过程中,传统反应器采用的是连续搅拌反应器。
该反应器存在反应效果不稳定、搅拌能耗大等问题,无法满足生产需求。
因此,引入新型反应器设计是必要的创新方向。
1.1 冷凝式反应器冷凝式反应器是一种利用反应产生的热量来加热、蒸发水分的新型反应器。
该反应器将反应物与冷却剂通过独立的管道进行流动,利用冷却剂的温度差来吸收反应产生的热量,实现反应物的加热以及水分的蒸发。
相比传统反应器,冷凝式反应器具有能耗低、反应效果稳定等优点。
1.2 微流控反应器微流控反应器使用微型通道结构,将反应物分散到微米级别,实现反应过程的快速进行。
该反应器具有反应物利用率高、产品分布均匀等优势。
在聚合氯化铝合成过程中,微流控反应器能够有效降低反应时间、提高产量。
2. 智能控制技术创新传统的聚合氯化铝合成过程中,操作人员需要根据经验和试错来控制反应条件,存在操作难度大、反应条件不稳定等问题。
引入智能控制技术,可以有效提高反应的稳定性和控制精度。
2.1 模型预测控制模型预测控制是一种基于数学模型的先进控制方法。
该方法通过建立聚合氯化铝合成反应的动态模型,预测未来时间段内的状态,并根据预测结果进行控制。
通过模型预测控制,可以在一定程度上解决传统控制方法中的滞后和误差问题,提高反应的稳定性和控制精度。
2.2 数据驱动控制数据驱动控制是一种基于大数据和机器学习的控制方法。
该方法通过收集大量的反应过程数据,构建反应过程的数据模型,并利用机器学习算法进行建模和预测。
基于数据驱动的控制方法,可以实现对聚合氯化铝合成过程的自适应调节和优化控制,提高产品质量和反应效率。
光催化反应器的设计

通过改进材料的晶体结构、表面性质和能带结构,提高其光催化活 性、稳定性和持久性。
材料组合与复合
将不同材料进行组合或复合,实现优势互补,提高光催化效果。
反应器的大型化与集成化
扩大反应器规模
研究如何将光催化反应器从实验 室规模扩大到工业规模,实现大 规模应用。
集成化反应器设计
将多个光催化反应器集成在一起 ,形成模块化、一体化的光催化 系统,提高整体效率。
提高光能的利用率
高效光收集系统
研究和发展高效的光收集系统,将更多入射光转化为可以利用的 光能。
光能转化效率提升
优化光催化材料的能带结构,提高光能转化为化学能的效率。
光波长拓展
研究如何利用不同波长的光,拓展光催化反应器的应用范围。
反应器的稳定性与持久性
长期运行性能测试
对光催化反应器进行长时间运行性能测试,评估其稳定性和持久性。
能耗与产率的评估
能耗
能耗是衡量光催化反应器经济性能的重要指标之 一,它表示为了获得一定量的目标产物所消耗的 能量。
影响因素
能耗与产率受到多种因素的影响,如光源的波长 、强度、照射角度,反应器的设计、操作温度和 压力等。
产率
产率是衡量光催化反应器性能的重要指标之一, 它表示单位时间内生成目标产物的量。
光催化反应的应用
光催化反应在污水处理领域的应用
01
利用光催化剂可以将有机污染物降解为无害的物质,从而达到
净化水质的目的。
光催化反应在能源转化领域的应用
02
光催化剂可以将太阳能转化为电能或氢能,为可再生能源的利
用提供了一种有效途径。
光催化反应在有机合成领域的应用
Hale Waihona Puke 03光催化剂可以用于合成有机化合物,具有高效、环保和条件温
固定床生物反应器开发计划

固定床生物反应器开发计划一、固定床生物反应器开发计划概述 (1)1.1 固定床生物反应器的概念与意义 (1)1.2 开发计划的目标与需求分析 (2)二、固定床生物反应器的设计原理 (2)2.1 生物反应动力学基础 (2)2.2 反应器结构设计要素 (2)三、固定床生物反应器的材料选择 (2)3.1 载体材料的筛选 (2)3.2 反应器主体材料的考量 (3)四、固定床生物反应器的构建技术 (3)4.1 固定化技术的应用 (3)4.2 反应器组装工艺 (3)五、固定床生物反应器的运行参数优化 (4)5.1 温度与pH值的控制 (4)5.2 底物浓度与流量调节 (4)六、固定床生物反应器的功能评估 (4)6.1 反应效率评估指标 (4)6.2 稳定性与可靠性测试 (5)七、固定床生物反应器的应用领域拓展 (5)7.1 在生物制药中的应用深化 (5)7.2 在环境治理中的创新应用 (5)八、固定床生物反应器开发的风险与挑战 (6)8.1 技术风险 (6)8.2 市场与竞争挑战 (6)一、固定床生物反应器开发计划概述1.1 固定床生物反应器的概念与意义固定床生物反应器是一种重要的生物反应设备,在生物工程、环境工程等众多领域有着广泛的应用。
它通过固定化生物催化剂,如酶或微生物,在特定的载体上形成固定床层,使底物与生物催化剂进行高效的反应。
这种反应器具有反应效率高、稳定性强、产物易于分离等优点,对于提高生物反应的工业化水平有着不可替代的作用。
例如在生物制药领域,可用于生产特定的药物成分,相比传统的反应方式,能够更精准地控制反应条件,提高产品的纯度和产量。
1.2 开发计划的目标与需求分析本开发计划的主要目标是研制出一种功能卓越、适用性强的固定床生物反应器。
在需求分析方面,从工业生产角度看,需要满足大规模、连续化生产的要求,提高生产效率以降低成本。
从技术角度,要实现对反应过程中各种参数,如温度、pH值、底物浓度等的精确控制,同时要保证生物催化剂的活性和稳定性。
新型化学反应器的设计与制造技术
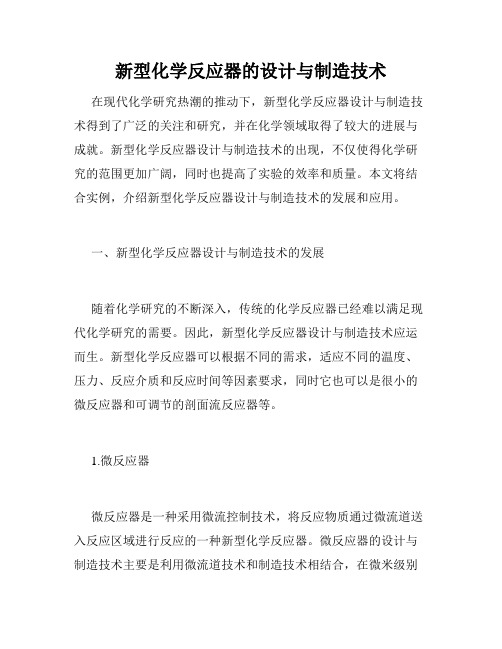
新型化学反应器的设计与制造技术在现代化学研究热潮的推动下,新型化学反应器设计与制造技术得到了广泛的关注和研究,并在化学领域取得了较大的进展与成就。
新型化学反应器设计与制造技术的出现,不仅使得化学研究的范围更加广阔,同时也提高了实验的效率和质量。
本文将结合实例,介绍新型化学反应器设计与制造技术的发展和应用。
一、新型化学反应器设计与制造技术的发展随着化学研究的不断深入,传统的化学反应器已经难以满足现代化学研究的需要。
因此,新型化学反应器设计与制造技术应运而生。
新型化学反应器可以根据不同的需求,适应不同的温度、压力、反应介质和反应时间等因素要求,同时它也可以是很小的微反应器和可调节的剖面流反应器等。
1.微反应器微反应器是一种采用微流控制技术,将反应物质通过微流道送入反应区域进行反应的一种新型化学反应器。
微反应器的设计与制造技术主要是利用微流道技术和制造技术相结合,在微米级别上进行化学反应,具有小尺寸、低成本、反应速率快等优势。
微反应器也是现代化学研究的重要手段之一,其应用领域广泛,包括有机合成、药物合成等。
2.可调节剖面流反应器可调节剖面流反应器是一种能够调节反应剖面的化学反应器。
它可以调节反应器内的反应深度,从而使反应物和催化剂之间的接触变得更加充分,反应速率也相应地提高。
可调节剖面流反应器的设计和制造技术主要是利用微流体学、计算机仿真技术和3D 打印技术等。
可调节剖面流反应器适用于异相催化反应、气液反应等。
二、新型化学反应器的应用新型化学反应器在化学研究中的应用越来越普遍,下面我们将介绍其中的两个方面。
1.药物制备新型化学反应器设计与制造技术在药物制备中具有广阔的应用前景。
微反应器、可调节剖面流反应器等新型反应器的出现,使得药物合成更加精确和有效。
例如在大型药物企业,采用微反应器制备药物的工艺流程,可以使药物的质量得到保证,并且大大提高生产效率。
2.环境保护新型化学反应器设计与制造技术在环境保护中也有着重要应用。
新型化学反应器设计与优化
新型化学反应器设计与优化化学反应器是化学工业中最为重要的基础设备之一,它是一个可以将化学原料转化为化学产物的装置。
而随着科技的发展,新型化学反应器的设计与优化也越来越受到研究者的关注。
本文将探讨新型化学反应器的设计与优化以及其在化学工业中的应用。
一、新型化学反应器的设计新型化学反应器的设计通常包括以下方面:反应物进料、反应室、产物出料、搅拌匀速、热平衡控制等。
1. 反应物进料反应物进料通常采用一些自动控制设备,如泵等,来控制反应物的加入量和速度。
同时,为了保证反应物能够充分混合和反应,需要考虑进料口的位置和形状,以及入口流动的特性等。
2. 反应室反应室应该具有良好的混合性能、传热性能和传质性能。
常见的反应室结构包括插管式反应器、流动式反应器等。
插管式反应器是一种常见的反应器结构,它通常由高效的搅拌设备、反应室和包围反应室的外层组成。
而流动式反应器则是一种新型反应器结构,它的反应物通过内置的小孔进入反应室,并在反应室内形成涡流,加快反应速度。
3. 产物出料产物出料需要一个合适的出料口,以便于收集和分离产物。
一些反应器还需要进行一些后续处理,如蒸馏等,为了方便这些处理,需要使产物出料口和后续处理设备相连通。
4. 搅拌匀速搅拌匀速可以加快反应的进行,同时也能够保证反应物充分混合。
搅拌的强度和速度需要考虑到反应物的物理和化学特性,以及反应室的规格等,不能太强或太弱。
5. 热平衡控制热平衡控制是一个很重要的问题,因为反应会产生热量,而过度的热量会引起反应器失控,从而导致反应发生爆炸等。
为了保证反应器热平衡,需要通过换热装置等降温控制技术来控制反应器的温度。
二、新型化学反应器的优化新型化学反应器的优化主要包括以下方面:反应速率、反应选择性、高效利用资源等。
1. 反应速率反应速率是化学反应器设计和优化的重要指标之一。
为了提高反应速率,可以采用一些加速物、催化剂、调节反应物比例等措施来调节反应速率。
2. 反应选择性反应选择性是指反应产物中想要的成分的比例。
新型化学反应器设计与实现
新型化学反应器设计与实现随着化学工业的发展,化学反应器也在不断地发展。
新型化学反应器设计与实现是一个重要的课题。
化学反应器是化学工业生产中非常重要的设备。
如何设计和实现一种新型化学反应器,可以提高生产效率,改善产品质量,减少废弃物排放,保护环境等方面都具有重大的意义。
一、新型化学反应器的设计原则在新型反应器的设计中,应该考虑以下几个方面:一是反应器的选择,二是反应器底部的设计,三是反应器的搅拌方式,四是反应器的加热和冷却方式。
1、反应器的选择反应器的选择应该根据反应物的特性来选择。
比如说,反应物是液态,那么选择液体反应器,反应物是气体,那么选择气体反应器,反应物是固态、粘稠液态,那么选择固体或半固体反应器。
2、反应器底部的设计反应器底部的设计是反应器工作的重要因素。
对于一些易于结晶的反应物,可以考虑采用圆弧形底部结构,这样可以防止结晶物粘在底部,影响反应的进行。
对于反应物萃取,亦或是升华等,可以将反应器底部设计成圆锥形,利用这种形状的结构,精准控制反应物的位置,方便反应的进行。
3、反应器的搅拌方式反应器的搅拌方式通常是通过机械搅拌和气液搅拌两种方式实现的。
机械搅拌方式主要是通过搅拌叶片转动来实现反应物混合,这种方式适合高速反应。
气液搅拌方式是通过气体通入反应器中来实现反应物的混合。
这种方式适合低速反应。
4、反应器的加热和冷却方式反应器的加热和冷却方式通常有三种:传导式加热、对流式加热和辐射式加热。
传导式加热是通过热能从反应器壁向反应物传导来实现加热效果。
对流式加热是通过流体在反应器中流动带走热能来实现加热效果。
辐射式加热是直接通过辐射热来加热反应器。
二、新型化学反应器的实现新型化学反应器的实现需要考虑以下几个方面:反应器的材料、反应器的性能、反应器的使用效率等等。
1、反应器的材料新型反应器的材料应该保证反应不被材料吸附、吸附、溶解,以保持材料的稳定性和反应的准确性。
材料应该符合绿色环保,低碳,低能源,低污染的要求,最好是可以循环使用的材料。
新型反应器设计与优化
新型反应器设计与优化随着人类社会的发展,现代化生产方式已经逐渐替代了传统手工生产方式,一切的工业生产都需要借助化学反应器来完成。
反应器作为处理原料和生成产品的重要工具,在工业生产中扮演着越来越重要的角色。
而为了适应现代化生产的要求以及环境保护的需要,目前反应器技术也在不断地进步和优化。
新型反应器的设计与优化是一个重要的研究领域,在此我们将从几个方面来分析新型反应器的设计与优化。
一、反应器设计原则反应器设计的第一原则是使反应物在反应器内达到最佳反应状态。
反应器内部的优化设计包括反应器的结构优化和器壁材料优化等。
要充分利用反应器内部的时间和空间,使反应物得以均匀混合,达到热平衡和质量平衡。
同时,还需要控制反应器内的温度和压力等因素,使反应物在反应器内能够达到最佳的反应状态。
二、反应器材质优化反应器壁材质的优化可以减少反应器的损耗和能量消耗,提高反应器的使用寿命。
在反应器材质的选择上,需要考虑到反应物质的化学性质、温度、压力等因素。
同时,还需要考虑到反应物质的腐蚀性和耐磨性等因素,选择适合的反应器材质。
三、反应器传热与质量传递的优化反应器内部反应物的传热和质量传递是反应器正常运行的重要因素,因此反应器的设计和优化也应该考虑这些因素。
传热和质量传递的优化可以通过改变反应器的形状、流体的流速、壁面传热比等来实现。
通过这些方法,反应物质可以在反应器内充分混合,达到最佳的反应状态。
同时,还可以提高反应器的传热效率和质量传递效率,减少能量消耗,降低运行成本。
四、反应器的自动化控制随着科技的不断发展,反应器的自动化控制也得到了越来越大的重视。
反应器自动化控制可以在反应器运行过程中实时监测反应物质的状态,及时调整反应器内的温度、压力和流速等因素,使得反应物质在反应器内保持最佳的状态。
同时,还可以减少人工操作,降低运营成本。
五、反应器的环保优化随着环保意识的不断提高,反应器的环保优化也越来越受到关注。
反应器的环保优化包括污染物排放控制、废物处理和能量消耗等因素。
新型反应器设计与优化
新型反应器设计与优化随着科学技术的不断发展,新型反应器设计与优化成为了化学工程领域的一个热门话题。
反应器是化学过程工程中至关重要的设备,其设计和优化可以直接影响到生产效率和产品质量。
因此,研究人员们一直在探索新型反应器的设计和优化方法,以提高反应器的效率和性能。
一、反应器设计的目标和挑战反应器设计的目标是实现高效的反应转化率和选择性,同时保证反应器的安全性和稳定性。
然而,实现这些目标并不容易,因为反应器设计面临着许多挑战。
首先,反应器设计需要考虑反应物的物理化学性质和反应条件。
不同的反应物具有不同的反应速率和热力学特性,因此需要选择合适的反应器类型和操作条件。
此外,反应物的浓度、温度和压力等参数也会对反应器的性能产生影响。
其次,反应器设计还需要考虑反应过程的传质和传热问题。
反应物必须能够充分接触到催化剂或反应介质,以实现高效的反应转化率。
因此,反应器的内部结构和流体动力学特性需要进行优化,以提高传质和传热效率。
最后,反应器设计还需要考虑反应过程的安全性和环境友好性。
反应过程中可能会产生有害物质或高温高压等危险条件,因此需要采取相应的安全措施。
此外,反应器设计还需要考虑废物处理和能源利用等环境问题。
二、新型反应器设计的方法和技术为了克服反应器设计的挑战,研究人员们提出了许多新型的反应器设计方法和技术。
首先,一些研究人员利用计算流体力学(CFD)模拟和优化技术,对反应器的内部流体动力学特性进行研究和优化。
通过对反应器内部流体流动的模拟和分析,可以揭示流体动力学特性对反应转化率的影响,并提出相应的改进措施。
其次,一些研究人员利用催化剂设计和表面改性技术,提高反应物与催化剂之间的接触效率。
催化剂是反应过程中的关键因素,通过优化催化剂的结构和表面性质,可以提高反应物的吸附和扩散能力,从而提高反应转化率。
此外,一些研究人员还利用多相流动技术和微观反应器设计,实现反应物的快速混合和传质。
通过将反应物分散到微观尺度的通道中,可以实现更高的传质效率和反应速率。
- 1、下载文档前请自行甄别文档内容的完整性,平台不提供额外的编辑、内容补充、找答案等附加服务。
- 2、"仅部分预览"的文档,不可在线预览部分如存在完整性等问题,可反馈申请退款(可完整预览的文档不适用该条件!)。
- 3、如文档侵犯您的权益,请联系客服反馈,我们会尽快为您处理(人工客服工作时间:9:00-18:30)。
乙酸乙酯反应器的设计12345678910111213141516171819姓名:张国华20班级:化学工程与工艺二班21学号:3009207057222324252627282930313233343536目录3738第一章背景介绍 (3)3940411 乙酸乙酯的理化性质 (3)42432 乙酸乙酯的用途 (3)44第二章乙酸乙酯的发展 (4)4546471 乙酸乙酯的实验室制法 (4)48492 工业合成乙酸乙酯的工艺 (5)50第三章设计的方法与步骤 (6)5152531 物料核算 (8)541-1 流量计算 (8)551-2 反应体积及时间的计算........................................................................。
(9)56572 热量核算 (10)582-1 能量衡算 (10)592-2 换热设计 (13)60第四章设计心得 (14)61626364第五章文献检索 (15)65666768一、背景介绍69701、乙酸乙酯的理化性质71乙酸乙酯ethyl acetate 简写EA72乙酸乙酯又称醋酸乙酯。
纯净的乙酸乙酯是无色透明具有刺激性气味的液73体,是一种用途广泛的精细化工产品,具有优异的溶解性、快干性,用途广泛,74是一种非常重要的有机化工原料和极好的工业溶剂,被广泛用于醋酸纤维、乙基75纤维、氯化橡胶、乙烯树脂、乙酸纤维树酯、合成橡胶、涂料及油漆等的生产过76程中。
其主要用途有:作为工业溶剂,用于涂料、粘合剂、乙基纤维素、人造革、77油毡着色剂、人造纤维等产品中;作为粘合剂,用于印刷油墨、人造珍珠的生产;78作为提取剂,用于医药、有机酸等产品的生产;作为香料原料,用于菠萝、香蕉、79草莓等水果香精和威士忌、奶油等香料的主要原料。
我们所说的陈酒很好喝,就80是因为酒中含有乙酸乙酯。
乙酸乙酯具有果香味。
因为酒中含有少量乙酸,和乙81醇进行反应生成乙酸乙酯。
因为这是个可逆反应,所以要具有长时间,才会积累82导致陈酒香气的乙酸乙酯。
83危险特性:易燃,其蒸气与空气可形成爆炸性混合物。
遇明火、高热能引起84燃烧爆炸。
与氧化剂接触会猛烈反应。
在火场中,受热的容器有爆炸危险。
其蒸85气比空气重,能在较低处扩散到相当远的地方,遇明火会引着回燃。
燃烧86(分解)产物:一氧化碳、二氧化碳。
现场应急监测方法:气体检测管法87实验室监测方法:无泵型采样气相色谱法(WS/T155-1999,作业场所空气)88应急处理处置方法:一、泄漏应急处理迅速撤离泄漏污染区人员至安全区,89并进行隔离,严格限制出入。
切断火源。
建议应急处理人员戴自给正压式呼吸器,90穿消防防护服。
尽可能切断泄漏源,防止进入下水道、排洪沟等限制性空间。
小91量泄漏:用活性炭或其它惰性材料吸收。
也可以用大量水冲洗,洗水稀释后放入92废水系统。
大量泄漏:构筑围堤或挖坑收容;用泡沫覆盖,降低蒸气灾害。
用防93爆泵转移至槽车或专用收集器内,回收或运至废物处理场所处置。
942、乙酸乙酯的用途95其主要用途有:作为工业溶剂,用于涂料、粘合剂、乙基纤维素、人造革、96油毡着色剂、人造纤维等产品中;作为粘合剂,用于印刷油墨、人造珍珠的生产;97作为提取剂,用于医药、有机酸等产品的生产;作为香料原料,用于菠萝、香蕉、98草莓等水果香精和威士忌、奶油等香料的主要原料。
用作溶剂,及用于染料和一99些医药中间体的合成。
是食用香精中用量较大的合成香料之一,大量用于调配香100蕉、梨、桃、菠萝、葡萄等香型食用香精。
是硝酸纤维素、乙基纤维素、乙酸纤101维素和氯丁橡胶的快干溶剂,也是工业上使用的低毒性溶剂。
还可用作纺织工业102的清洗剂和天然香料的萃取剂,也是制药工业和有机合成的重要原料。
103二、乙酸乙酯的发展1041051、乙酸乙酯制备过程106实验室制法107化学方程式:108CH3CH2OH+CH3COOH==CH3CH2OOCCH3+H2O乙酸乙酯的109制取:先加乙醇,再加浓硫酸(加入碎瓷片以防暴沸),最后加乙酸110然后加热(可以控制实验)。
1111:酯化反应是一个可逆反应。
为了提高酯的产量,必须尽量使112反应向有利于生成酯的方向进行。
一般是使反应物酸和醇中的一种过113量。
在工业生产中,究竟使哪种过量为好,一般视原料是否易得、价114格是否便宜以及是否容易回收等具体情况而定。
在实验室里一般采用115乙醇过量的办法。
乙醇的质量分数要高,如能用无水乙醇代替质量分116数为95%的乙醇效果会更好。
催化作用使用的浓硫酸量很少,一般117只要使硫酸的质量达到乙醇质量的3%就可完成催化作用,但为了能118除去反应中生成的水,应使浓硫酸的用量再稍多一些。
1192:制备乙酸乙酯时反应温度不宜过高,要迅速升温至170℃左120右,温度在140℃时会产生乙醚和亚硫酸或乙烯等杂质。
液体加热至121沸腾后,应改用小火加热。
事先可在试管中加入几片碎瓷片,以防止122液体暴沸。
1233:导气管不要伸到Na2CO3溶液中去,防止由于加热不均匀,124造成Na2CO3溶液倒吸入加热反应物的试管中。
125⒊1:浓硫酸既作催化剂,又做吸水剂。
126⒊2:Na2CO3溶液的作用是:⑴饱和碳酸钠溶液的作用是冷凝127酯蒸气,减小酯在水中的溶解度(利于分层),除出混合在乙酸乙酯128中的乙酸,溶解混合在乙酸乙酯中的乙醇。
⑵Na2CO3能跟挥发出129的乙酸反应,生成没有气味的乙酸钠,便于闻到乙酸乙酯的香味。
1301313-3:为有利于乙酸乙酯的生成,可采取以下措施:132⑴制备乙酸乙酯时,反应温度不宜过高。
133⑵最好使用冰醋酸和无水乙醇。
同时采用乙醇过量的办法。
134⑶起催化作用的浓硫酸的用量很小,但为了除去反应中生成的135水,浓硫酸的用量要稍多于乙醇的用量。
136⑷使用无机盐Na2CO3溶液吸收挥发出的乙酸。
1373-4:用Na2CO3不能用碱(NaOH)的原因。
138虽然也能吸收乙酸和乙醇,但是碱会催化乙酸乙酯彻底水解,导139致实验失败。
140⒊5乙稀与醋酸直接酯化生产醋酸乙酯用磷酸盐作催化剂. 141⒊6乙醛缩合法:以烷基铝为催化剂将乙醛进行缩合反应生产醋142酸乙酯国外工业生产大多采用此工艺。
1431442、工业乙酸乙酯的合成工艺145目前世界上工业乙酸乙酯主要制备方法有乙酸酯化法、乙醛缩合146法、乙烯加成法和乙醇脱氢法等。
传统的乙酸酯化法工艺在国外被逐147步淘汰,而大规模生产装置主要是乙醛缩合法和乙醇脱氢法,在乙醛148原料较丰富的地区万吨级以匕的乙醛缩合法装置得到了广泛的应用。
149乙醇脱氧法是近年开发的新工艺,在乙醇丰富且低成本的地区得到了150推广最新的乙酸乙酯生产方法是乙烯加成法,1998年在印度尼西亚151迈拉库地区采用日本昭和电工专利技术建成了50 kt/a生产装置。
152(1)乙酸酯化法153乙酸酯化法是传统的乙酸乙酯生产方法,在催化剂存在下,由乙154酸和乙醇发生酯化反应而得。
反应除去生成水,可得到高收率,该法155生产乙酸乙酯的主要缺点是成本高、设备腐蚀性强,在国际上是属于156被淘汰的工艺路线157(2)乙醛缩合法158在催化剂乙醇铝的存在下,两个分子的乙醛自动氧化和缩合,重159排形成一分子的乙酸乙酯。
该方法加世纪70年代在欧美、日本等地160已形成了大规模的生产装置,在生产成本和环境保护等方面都有着明161显的优势162(3)乙醇脱氢法163采用铜基催化剂使乙醇脱氢生成粗乙酸乙酯,经高低压蒸馏除去164共沸物,得到纯度为99.8%以上乙酸乙酯。
165(4)乙烯加成法166在以附载在二氧化硅等载体上的杂多酸金属盐或杂多酸为催化167剂的存在下,乙烯气相水合后与气化乙酸直接酯化生成乙酸乙酯。
该168反应乙酸的单程转化率为66%,以乙烯计乙酸乙酯的选择性为94%。
169Rhone.Poulenc、昭和电工和BP等跨国公司都开发了该生产工艺。
170由于上海石化股份有限公司具有丰富的乙烯、乙酸和乙醛,故本文对乙酸酯化法、乙醛缩合法和乙烯加成法生产乙酸乙酯的技术经济指标171 予以对比分析。
172 三、设计的方法与步骤173 (由于自己对原来高中学的一个反应很感兴趣,所以选择乙酸乙酯反应器作为自174 己的设计目标,假设的设计条件如下:) 175 1.设计条件176 ○1生产规模:2600吨/年 177 ○2生产时间:连续生产8000小时/年,间歇生产6000小时/年 178 ○3物料消耗:按5%计算 179 ○4乙酸的转变化率:54% 180 2.反应条件181 反应温度在等温下进行,反应温度为800C ,以少量的浓硫酸为催化剂,硫182 酸量为总物料量的1%,当乙醇过量时,其动力学方程为:—r A =kC A 2.。
A 为乙183 酸,建议采用配比为乙酸:丁醇=1:5(摩尔比)。
反应物料密度为0.85Kg/L ,反184 应的速率常数k 为15.00L/(kmol*min )。
185 1、设计方案简介186 根据设计任务书所提供的条件和要求,通过对现有资料的分析对比,初步确187 定工艺流程。
对选定的工艺流程、主要设备的型式以及数值积分计算等进行简要188 的论述。
189 2、主要设备的工艺设计计算190 ①反应的物料衡算、热量衡算、动量衡算 191 ②催化剂床层高度计算 192 ③出口转化率计算193 3、典型辅助设备的选型和计算:194 包括典型辅助设备的主要工艺尺寸计算和设备型号规格的选定 195196 主要符号一览表197 198199V ——反应釜的体积 200 t ——反应时间201 0A c ——反应物A 的起始浓度 202 0B c ——反应物的B 起始浓度 203 0S c ——反应物S 的起始浓度 204 f ——反应器的填充系数 205 i D ——反应釜的内径 206 H ——反应器筒体的高度 207 2h ——封头的高度208P ——操作压力 209 P c ——设计压力 210 φ——取焊缝系数 211 [σ]t——钢板的许用应力 212 C 1——钢板的负偏差 213 C 2——钢板的腐蚀裕量 214 S ——筒壁的计算厚度 215 d S ——筒壁的设计厚度 216 n S ——筒壁的名义厚度 217 j H ——反应器夹套筒体的高218 度219 v ——封头的体积220 T P ——水压试验压力221j D ——夹套的内径222 Q ——乙酸的用量 223 Q0——单位时间的处理量224225 226 摘要:本选题为年产量为年产2600吨的间歇釜式反应器的设计。
通过物227 料衡算、热量衡算,反应器体积为35.4m 、换热量为65.510/h KJ ⨯。