模具制造流程
模具的生产流程

模具的生产流程
模具生产是工业制造中重要的环节之一,它主要涉及到从设计到
制造再到加工、修理、改造等方面的各个环节。
以下是模具的生产流程:
1、设计阶段:模具的制作始于设计,制作模具的设计师必须详细
地了解产品的使用要求、尺寸、形状等。
在设计过程中需要进行设计
评估,有利于确定所选的材料、加工技术和成型工艺等。
2、材料选择:在材料选择过程中,设计师必须考虑到模具材料的
机械性能、成本、精度等因素。
一般情况下,模具材料要求坚硬而不
易变形。
3、制造模具:制造模具的技术水平决定了模具的质量和精度,因此,制造模具的工作人员必须具备一定的专业知识。
4、加工模具:加工模具是需要反复校验和测试的,主要包括开槽、打孔、切割、抛光、磨削和刻蚀等。
在这个环节中,需要使用一些高
精度机床和其他装备,以确保各个部件的精度和质量。
5、测试和修理:在测试阶段,需要对模具进行加工测试,以检查
模具的质量和精度。
如果出现问题,需要对模具进行修理或修改。
6、维护和修理:模具在使用过程中会出现损坏、磨损、老化等
问题,需要及时进行维护和修理。
总之,模具生产是一个复杂的过程,需要多方面的专业技术和精湛的技艺。
只有经过严格的设计、制造、修理和维护,才能够确保模具的质量和使用寿命。
模具制造工艺流程(简易)
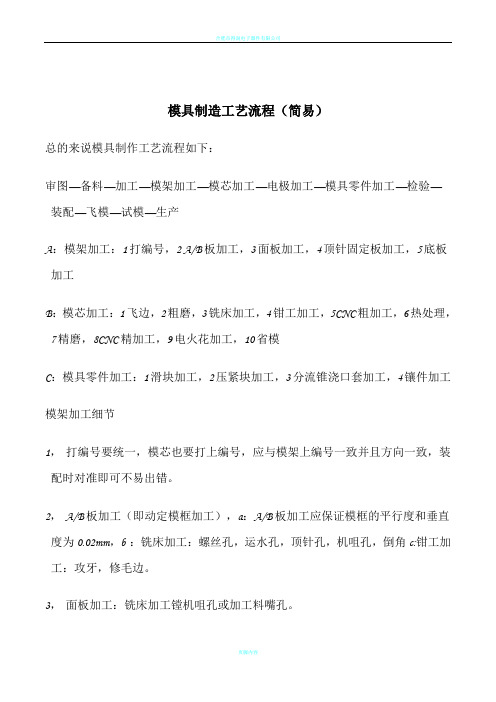
模具制造工艺流程(简易)总的来说模具制作工艺流程如下:审图—备料—加工—模架加工—模芯加工—电极加工—模具零件加工—检验—装配—飞模—试模—生产A:模架加工:1打编号,2 A/B板加工,3面板加工,4顶针固定板加工,5底板加工B:模芯加工:1飞边,2粗磨,3铣床加工,4钳工加工,5CNC粗加工,6热处理,7精磨,8CNC精加工,9电火花加工,10省模C:模具零件加工:1滑块加工,2压紧块加工,3分流锥浇口套加工,4镶件加工模架加工细节1,打编号要统一,模芯也要打上编号,应与模架上编号一致并且方向一致,装配时对准即可不易出错。
2,A/B板加工(即动定模框加工),a:A/B板加工应保证模框的平行度和垂直度为0.02mm,b :铣床加工:螺丝孔,运水孔,顶针孔,机咀孔,倒角c:钳工加工:攻牙,修毛边。
3,面板加工:铣床加工镗机咀孔或加工料嘴孔。
4,顶针固定板加工:铣床加工:顶针板与B板用回针连结,B板面向上,由上而下钻顶针孔,顶针沉头需把顶针板反过来底部向上,校正,先用钻头粗加工,再用铣刀精加工到位,倒角。
5,底板加工:铣床加工:划线,校正,镗孔,倒角。
(注:有些模具需强拉强顶的要加做强拉强顶机构,如在顶针板上加钻螺丝孔)模芯加工细节1)粗加工飞六边:在铣床上加工,保证垂直度和平行度,留磨余量1.2mm2)粗磨:大水磨加工,先磨大面,用批司夹紧磨小面,保证垂直度和平行度在0.05mm,留余量双边0.6-0.8mm3)铣床加工:先将铣床机头校正,保证在0.02mm之内,校正压紧工件,先加工螺丝孔,顶针孔,穿丝孔,镶针沉头开粗,机咀或料咀孔,分流锥孔倒角再做运水孔,铣R角。
4)钳工加工:攻牙,打字码5)CNC粗加工6)发外热处理HRC48-527)精磨;大水磨加工至比模框负0.04mm,保证平行度和垂直度在0.02mm之内8)CNC精加工9)电火花加工10)省模,保证光洁度,控制好型腔尺寸。
11)加工进浇口,排气,锌合金一般情况下浇口开0.3-0.5mm,排气开0.06-0.1mm,铝合金浇口开0.5-1.2mm排气开0.1-0.2,塑胶排气开0.01-0.02,尽量宽一点,薄一点。
模具制造的工艺流程
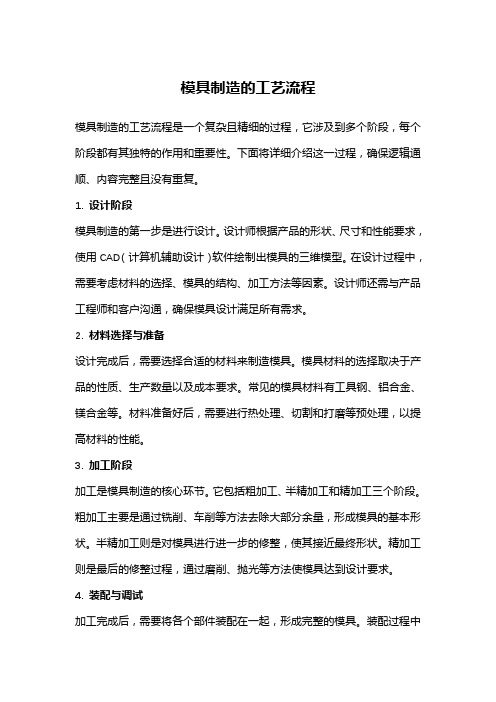
模具制造的工艺流程模具制造的工艺流程是一个复杂且精细的过程,它涉及到多个阶段,每个阶段都有其独特的作用和重要性。
下面将详细介绍这一过程,确保逻辑通顺、内容完整且没有重复。
1. 设计阶段模具制造的第一步是进行设计。
设计师根据产品的形状、尺寸和性能要求,使用CAD(计算机辅助设计)软件绘制出模具的三维模型。
在设计过程中,需要考虑材料的选择、模具的结构、加工方法等因素。
设计师还需与产品工程师和客户沟通,确保模具设计满足所有需求。
2. 材料选择与准备设计完成后,需要选择合适的材料来制造模具。
模具材料的选择取决于产品的性质、生产数量以及成本要求。
常见的模具材料有工具钢、铝合金、镁合金等。
材料准备好后,需要进行热处理、切割和打磨等预处理,以提高材料的性能。
3. 加工阶段加工是模具制造的核心环节。
它包括粗加工、半精加工和精加工三个阶段。
粗加工主要是通过铣削、车削等方法去除大部分余量,形成模具的基本形状。
半精加工则是对模具进行进一步的修整,使其接近最终形状。
精加工则是最后的修整过程,通过磨削、抛光等方法使模具达到设计要求。
4. 装配与调试加工完成后,需要将各个部件装配在一起,形成完整的模具。
装配过程中需要注意各部件之间的配合间隙和位置精度。
装配完成后,需要进行调试,检查模具的动作是否顺畅、尺寸是否合格等。
5. 试模与修正调试合格后,开始进行试模。
试模是在生产条件下模拟实际生产过程,以检验模具的性能和可靠性。
试模过程中可能会发现一些问题,如尺寸超差、表面质量不佳等。
这时需要对模具进行修正,直至达到生产要求。
6. 验收与交付修正完成后,模具需要进行验收。
验收包括外观检查、尺寸测量、性能测试等多个方面。
验收合格后,模具就可以交付给客户使用了。
交付时,需要提供相关的技术文件和操作说明书,以便客户能够正确地使用和维护模具。
7. 维护与保养模具在使用过程中,需要定期进行维护和保养。
这包括清洁模具表面、检查模具的磨损情况、润滑模具的运动部件等。
五金模具制造工艺流程
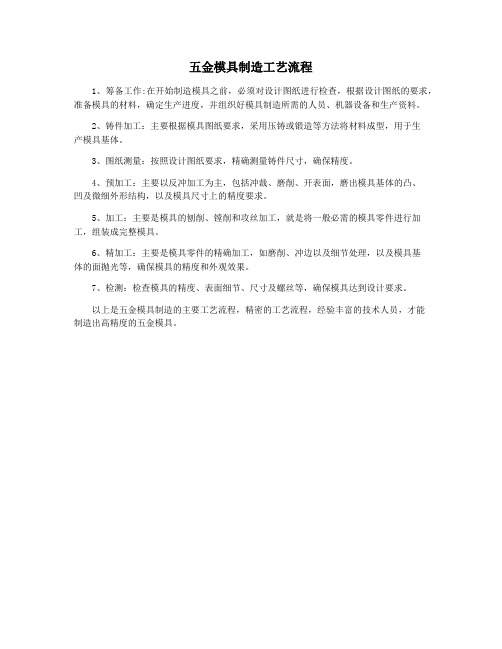
五金模具制造工艺流程
1、筹备工作:在开始制造模具之前,必须对设计图纸进行检查,根据设计图纸的要求,准备模具的材料,确定生产进度,并组织好模具制造所需的人员、机器设备和生产资料。
2、铸件加工:主要根据模具图纸要求,采用压铸或锻造等方法将材料成型,用于生
产模具基体。
3、图纸测量:按照设计图纸要求,精确测量铸件尺寸,确保精度。
4、预加工:主要以反冲加工为主,包括冲裁、磨削、开表面,磨出模具基体的凸、
凹及微细外形结构,以及模具尺寸上的精度要求。
5、加工:主要是模具的刨削、镗削和攻丝加工,就是将一般必需的模具零件进行加工,组装成完整模具。
6、精加工:主要是模具零件的精确加工,如磨削、冲边以及细节处理,以及模具基
体的面抛光等,确保模具的精度和外观效果。
7、检测:检查模具的精度、表面细节、尺寸及螺丝等,确保模具达到设计要求。
以上是五金模具制造的主要工艺流程,精密的工艺流程,经验丰富的技术人员,才能
制造出高精度的五金模具。
模具制作流程顺序

模具制作流程顺序在工业生产中,模具制作是一个至关重要的环节,它直接关系到产品的质量、产能以及成本效益。
下面将介绍模具制作的基本流程,帮助大家更好地了解这一过程。
第一步:产品设计模具制作的第一步是产品设计。
在这个阶段,设计师需要根据产品的要求和规格,绘制出详细的产品设计图纸。
这些设计图纸将成为后续模具制作的依据,因此设计的准确性至关重要。
第二步:模具设计一旦产品设计确定,接下来就是进行模具设计。
模具设计师会根据产品设计图纸,制定出模具的结构、尺寸和加工方式。
在设计过程中,需要考虑到模具的使用寿命、生产效率以及成本控制等因素,以确保最终的模具能够满足生产需求。
第三步:材料选择选择合适的材料是模具制作过程中的关键步骤。
通常情况下,模具制作会选用金属材料,如钢铁、铝合金等。
材料的选择直接影响到模具的硬度、耐磨性以及成本,因此需要根据具体的生产需求和预算来进行选择。
第四步:加工制造一旦模具设计和材料选择完成,就开始进行加工制造。
这个阶段包括数控加工、电火花加工、线切割等工艺过程,以将设计图纸中的模具形态逐步呈现出来。
加工制造的质量和精度直接决定了最终模具的使用效果,因此需要高度重视。
第五步:热处理为了提高模具的硬度和耐用度,通常会进行热处理。
热处理是通过控制材料的加热和冷却过程,改变其内部结构,从而获得所需的硬度和强度特性。
正确的热处理可以显著延长模具的使用寿命,降低生产成本。
第六步:组装调试完成热处理后,就可以进行模具的组装和调试工作。
这个阶段包括模具零部件的组装,以及与生产设备的配合调试。
通过仔细的组装和调试,可以确保模具在生产过程中能够正常运行,并获得高质量的成品。
结语模具制作是一个复杂而精密的过程,需要设计师、工程师和技术工人之间紧密合作,共同完成从设计到制造的每一个环节。
只有通过精心的规划和严谨的执行,才能制作出高质量、高效率的模具,为企业的生产提供有力保障。
希望本文能够帮助大家更好地了解模具制作的流程和重要性。
模具制作的六个流程

模具制作的六个流程英文回答:1. Pattern Design:The initial step in mold making involves designing the pattern, which serves as the blueprint for the mold. The pattern is typically fabricated from wood, plastic, or metal and accurately represents the geometry of the final product.2. Mold Design:Based on the pattern, the mold is designed. It consists of two halves to enable separation and extraction of the molded object. The mold cavities are designed to match the pattern's shape and incorporate features such as gates and vents for material flow during molding.3. Core Making:Cores are used to create hollow or recessed sections within the molded object. They are fabricated separatelyand positioned within the mold to form the desired cavities. Cores must be designed with proper draft angles tofacilitate ejection from the mold.4. Mold Fabrication:The mold is fabricated using various materials, such as aluminum, steel, or composite materials. The mold components are machined or cast to precision tolerances to ensure accurate reproduction of the pattern shape. Gating and venting systems are incorporated into the mold tocontrol material flow.5. Assembly and Testing:The mold halves are assembled and aligned precisely.The core(s), if used, are inserted into the mold cavity.The mold is then tested for proper operation and any necessary adjustments are made to ensure molding efficiencyand product quality.6. Mold Maintenance:Regular mold maintenance is crucial to ensure optimal performance and longevity. Cleaning, lubrication, and inspection are essential maintenance tasks that help extend mold life and minimize production downtime.中文回答:1. 样板设计:模具制作的第一步是设计样板,作为模具的蓝图。
模具制造流程
模具制造流程
模具制造流程是将产品的设计图纸或样件通过一系列的工艺步骤制作成模具的过程。
模具是用于生产产品的专用工具,它的制造具有复杂和精细的特点,以下是一般的模具制造流程:
1.产品分析和设计:根据客户提供的产品图纸或样品,进行详
细的分析和设计工作。
包括确定产品的尺寸、材料、工艺要求等等。
设计师需要使用CAD软件绘制出模具的三维图纸。
2.材料准备和加工:根据设计图纸,选择适当的模具材料,通
常是合金钢。
然后将所需的材料切割成需要的形状和尺寸。
接下来,通过数控机床进行精确加工,如铣削、钻孔、铣平等。
3.模具零件组装:将各个模具零件按照设计图纸进行组装。
通
常包括模座、上模、下模、侧剪、顶针等零部件。
所有的零部件需要精确安装,并加以调试和校准,以确保模具的正常运行。
4.模具表面处理:使用各类表面处理技术,如电镀、喷涂等,
对模具进行表面保护和增加耐磨性能。
这样可以延长模具的使用寿命,提高生产效率。
5.模具试模和调试:在模具制造完成后,进行试模和调试工作。
将模具安装到注塑机或压铸机上,注入合适的材料进行试产,检查产品的质量,以调整和改进模具设计。
6.模具出厂和维护:经过试模和调试验证无误后,模具可以出
厂交付给客户使用。
同时,制造商也要为模具的维护提供支持,
定期进行检查和保养,以确保模具的正常运行和良好的使用寿命。
总之,模具制造流程是一个复杂而精细的过程,在模具制造中,设计和技术水平起着至关重要的作用。
只有设计合理,加工精细,才能生产出具有高质量和高效益的模具,提高产品的质量和生产效率。
模具制造管理流程
模具制造管理流程模具制造是工业生产中的重要环节,它涉及到各个行业的产品制造。
而要保证模具制造的质量和效率,就需要一个科学合理的管理流程。
本文将介绍模具制造的管理流程,包括设计、加工、检验和维护等环节。
一、设计阶段在模具制造的设计阶段,首先需要进行产品的设计分析,确定产品的形状、尺寸和结构等要求。
然后,根据产品的要求,进行模具的设计,包括模具的结构、零件的尺寸和材料等。
设计阶段的关键是要保证模具的功能和结构满足产品的要求,同时考虑到模具的加工和使用的方便性。
设计人员需要具备丰富的经验和专业知识,以确保设计的准确性和可行性。
二、加工阶段在模具制造的加工阶段,首先需要准备加工所需的材料和零件。
然后,根据设计图纸,进行模具的加工和制造。
加工包括车削、铣削、钻孔、磨削等工艺,以及热处理、表面处理等工艺。
加工阶段的关键是要保证模具的尺寸和形状的精确度,同时确保模具的强度和耐用性。
加工人员需要具备良好的技术和操作能力,以确保加工的质量和效率。
三、检验阶段在模具制造的检验阶段,首先需要对加工完成的模具进行外观检查,包括尺寸、形状和表面质量等。
然后,进行功能性检验,测试模具的使用效果和性能。
检验阶段的关键是要保证模具的质量和可靠性,确保模具能够满足产品的生产要求。
检验人员需要具备严谨的工作态度和专业的技术能力,以确保检验的准确性和可靠性。
四、维护阶段在模具制造的维护阶段,首先需要对模具进行定期的保养和维护,包括清洁、润滑和更换易损件等。
然后,根据使用情况和维护记录,进行模具的修理和更换。
维护阶段的关键是要保证模具的正常运行和使用寿命,提高模具的利用率和生产效率。
维护人员需要具备专业的技术知识和维修经验,以确保维护的及时性和有效性。
总结模具制造的管理流程涉及到设计、加工、检验和维护等环节,每个环节都需要专业的人员和科学的管理方法。
只有通过严格的管理流程,才能保证模具制造的质量和效率,满足产品的生产需求。
因此,企业在进行模具制造时,应注重管理流程的建立和优化,提高模具制造的质量和效率。
模具制作的工艺流程
模具制作的工艺流程模具制作工艺流程模具制作是工业生产中必不可少的环节之一,它是现代工业产品制造的基础和关键环节。
下面将详细介绍模具制作的工艺流程。
一、模具设计模具制作的第一步是进行模具的设计。
根据客户提供的产品图纸和要求,模具设计师会使用CAD、UG、ProE等软件进行三维模型的建立和设计。
这一步是确定模具的结构和尺寸,以及模具所需材料的选择。
二、模具加工在模具设计完成后,需要进行模具的加工。
首先是进行钢材的选择和准备,根据模具设计的要求选取合适的材料,通常常用的材料有P20钢、45#钢、718H钢等。
接下来是进行铣床加工、车床加工、电火花加工等一系列的加工工艺,将钢材加工成所需的模具零件。
这一步需要高精度的机械设备以及熟练的技术工人。
三、模具组装模具加工完成后,需要进行模具的组装。
将各个零部件进行装配,并进行调整、校正,确保模具的精度和质量。
这一步需要对模具零部件的加工精度要求非常高,以确保模具的使用寿命和生产效率。
四、模具调试完成模具组装后,需要进行模具的调试。
通过在注塑机上进行模具安装和调试,检查模具的运行情况和产品的质量。
在这个过程中,需要调整模具的工艺参数,如温度、压力、速度等,以获得最佳的生产效果。
五、模具试产调试完成后,进行模具试产。
在试产过程中,进行模具的性能测试,检查产品的尺寸、表面质量、强度等指标,确保模具能够满足生产需要。
同时,对模具进行调整和改进,以提高模具的使用寿命和生产效率。
六、模具维护模具试产合格后,需要进行模具的维护。
定期对模具进行清洁、润滑和保养,以延长模具的使用寿命。
同时,定期检查模具的磨损情况,对损坏或磨损的零部件进行更换,确保模具的正常运行。
模具制作是一个复杂而具有挑战性的过程,需要高精度的设备和专业的技术工人。
只有通过严格的工艺流程和质量控制,才能生产出高质量的模具,为工业生产提供稳定可靠的支持。
模具制造生产计划流程
模具制造生产计划流程模具制造生产计划流程是指根据客户需求和订单要求,进行模具制造的过程。
以下是一个典型的模具制造生产计划流程:1. 搜集客户需求和订单要求:与客户沟通,了解客户的需求和订单要求,包括模具的类型、规格、数量等。
2. 制定生产计划:根据客户需求和订单要求,制定模具制造的生产计划,包括制造的时间安排、人员调配、生产设备的使用等。
3. 申请和采购原材料:根据生产计划,申请原材料,并与供应商进行沟通和采购,确保原材料的供应充足。
4. 设计模具结构:根据客户需求和订单要求,进行模具的结构设计,确定模具的形状、尺寸等。
5. 制作模具零部件:根据模具结构设计图纸,分解模具结构,制作模具的各个零部件。
6. 组装模具:将制作好的模具零部件进行组装,组成完整的模具。
7. 模具调试和测试:对组装好的模具进行调试和测试,确保模具的正常运行和质量达标。
8. 生产模具样品:根据客户需求和订单要求,使用调试好的模具进行试模生产,制作模具样品。
9. 检验和质量控制:对生产的模具样品进行检验和质量控制,确保模具样品的质量符合要求。
10. 生产模具批量产品:根据客户需求和订单要求,使用调试好的模具进行批量生产,制作模具批量产品。
11. 检验和质量控制:对生产的模具批量产品进行检验和质量控制,确保模具批量产品的质量符合要求。
12. 准备发货:检验合格的模具批量产品准备发货,包装并做好相应的标记。
13. 发货和售后服务:将模具批量产品按照客户要求进行发货,并提供售后服务,处理客户的问题和反馈。
以上是模具制造生产计划流程的常规步骤,实际生产过程中可能会因客户需求、订单特殊要求等而有所调整。
在整个生产计划流程中,需要严格控制每一道工序的质量,及时进行沟通和协调,确保生产计划的顺利进行和模具产品的质量达标。
- 1、下载文档前请自行甄别文档内容的完整性,平台不提供额外的编辑、内容补充、找答案等附加服务。
- 2、"仅部分预览"的文档,不可在线预览部分如存在完整性等问题,可反馈申请退款(可完整预览的文档不适用该条件!)。
- 3、如文档侵犯您的权益,请联系客服反馈,我们会尽快为您处理(人工客服工作时间:9:00-18:30)。
模具制作流程设计资料号发布时间:2006 02/16 一、接受任务书成型塑料制件的任务书通常由制件设计者提出,其内容如下:1. 经过审签的正规制制件图纸,并注明采用塑料的牌号、透明度等。
2. 塑料制件说明书或技术要求。
3. 生产产量。
4. 塑料制件样品。
通常模具设计任务书由塑料制件工艺员根据成型塑料制件的任务书提出,模具设计人员以成型塑料制件任务书、模具设计任务书为依据来设计模具。
二、收集、分析、消化原始资料收集整理有关制件设计、成型工艺、成型设备、机械加工及特殊加工资料,以备设计模具时使用。
1. 消化塑料制件图,了解制件的用途,分析塑料制件的工艺性,尺寸精度等技术要求。
例如塑料制件在外表形状、颜色透明度、使用性能方面的要求是什么,塑件的几何结构、斜度、嵌件等情况是否合理,熔接痕、缩孔等成型缺陷的允许程度,有无涂装、电镀、胶接、钻孔等后加工。
选择塑料制件尺寸精度最高的尺寸进行分析,看看估计成型公差是否低于塑料制件的公差,能否成型出合乎要求的塑料制件来。
此外,还要了解塑料的塑化及成型工艺参数。
2. 消化工艺资料,分析工艺任务书所提出的成型方法、设备型号、材料规格、模具结构类型等要求是否恰当,能否落实。
成型材料应当满足塑料制件的强度要求,具有好的流动性、均匀性和各向同性、热稳定性。
根据塑料制件的用途,成型材料应满足染色、镀金属的条件、装饰性能、必要的弹性和塑性、透明性或者相反的反射性能、胶接性或者焊接性等要求。
3. 确定成型方法采用直压法、铸压法还是注射法。
4、选择成型设备根据成型设备的种类来进行模具,因此必须熟知各种成型设备的性能、规格、特点。
例如对于注射机来说,在规格方面应当了解以下内容:注射容量、锁模压力、注射压力、模具安装尺寸、顶出装置及尺寸、喷嘴孔直径及喷嘴球面半径、浇口套定位圈尺寸、模具最大厚度和最小厚度、模板行程等,具体见相关参数。
要初步估计模具外形尺寸,判断模具能否在所选的注射机上安装和使用。
5. 具体结构方案(一)确定模具类型如压制模(敞开式、半闭合式、闭合式)、铸压模、注射模等。
(二)确定模具类型的主要结构选择理想的模具结构在于确定必需的成型设备,理想的型腔数,在绝对可靠的条件下能使模具本身的工作满足该塑料制件的工艺技术和生产经济的要求。
对塑料制件的工艺技术要求是要保证塑料制件的几何形状,表面光洁度和尺寸精度。
生产经济要求是要使塑料制件的成本低,生产效率高,模具能连续地工作,使用寿命长,节省劳动力。
三、影响模具结构及模具个别系统的因素很多,很复杂:1. 型腔布置。
根据塑件的几何结构特点、尺寸精度要求、批量大小、模具制造难易、模具成本等确定型腔数量及其排列方式。
对于注射模来说,塑料制件精度为3级和3a级,重量为5克,采用硬化浇注系统,型腔数取4-6个;塑料制件为一般精度(4-5级),成型材料为局部结晶材料,型腔数可取16-20个;塑料制件重量为12-16克,型腔数取8-12个;而重量为50-100克的塑料制件,型腔数取4-8个。
对于无定型的塑料制件建议型腔数为24-48个,16-32个和6-10个。
当再继续增加塑料制件重量时,就很少采用多腔模具。
7-9级精度的塑料制件,最多型腔数较之指出的4-5级精度的塑料增多至50%。
2. 确定分型面。
分型面的位置要有利于模具加工,排气、脱模及成型操作,塑料制件的表面质量等。
3. 确定浇注系统(主浇道、分浇道及浇口的形状、位置、大小)和排气系统(排气的方法、排气槽位置、大小)。
4. 选择顶出方式(顶杆、顶管、推板、组合式顶出),决定侧凹处理方法、抽芯方式。
5. 决定冷却、加热方式及加热冷却沟槽的形状、位置、加热元件的安装部位。
6. 根据模具材料、强度计算或者经验数据,确定模具零件厚度及外形尺寸,外形结构及所有连接、定位、导向件位置。
7. 确定主要成型零件,结构件的结构形式。
8. 考虑模具各部分的强度,计算成型零件工作尺寸。
以上这些问题如果解决了,模具的结构形式自然就解决了。
这时,就应该着手绘制模具结构草图,为正式绘图作好准备。
四、绘制模具图要求按照国家制图标准绘制,但是也要求结合本厂标准和国家未规定的工厂习惯画法。
在画模具总装图之前,应绘制工序图,并要符合制件图和工艺资料的要求。
由下道工序保证的尺寸,应在图上标写注明"工艺尺寸"字样。
如果成型后除了修理毛刺之外,再不进行其他机械加工,那么工序图就与制件图完全相同。
在工序图下面最好标出制件编号、名称、材料、材料收缩率、绘图比例等。
通常就把工序图画在模具总装图上。
1. 绘制总装结构图绘制总装图尽量采用1:1的比例,先由型腔开始绘制,主视图与其它视图同时画出。
五、模具总装图应包括以下内容:1. 模具成型部分结构2. 浇注系统、排气系统的结构形式。
3. 分型面及分模取件方式。
4. 外形结构及所有连接件,定位、导向件的位置。
5. 标注型腔高度尺寸(不强求,根据需要)及模具总体尺寸。
6. 辅助工具(取件卸模工具,校正工具等)。
7. 按顺序将全部零件序号编出,并且填写明细表。
8. 标注技术要求和使用说明。
六、模具总装图的技术要求内容:1. 对于模具某些系统的性能要求。
例如对顶出系统、滑块抽芯结构的装配要求。
2. 对模具装配工艺的要求。
例如模具装配后分型面的贴合面的贴合间隙应不大于0.05mm模具上、下面的平行度要求,并指出由装配决定的尺寸和对该尺寸的要求。
3. 模具使用,装拆方法。
4. 防氧化处理、模具编号、刻字、标记、油封、保管等要求。
5. 有关试模及检验方面的要求。
七、绘制全部零件图由模具总装图拆画零件图的顺序应为:先内后外,先复杂后简单,先成型零件,后结构零件。
1. 图形要求:一定要按比例画,允许放大或缩小。
视图选择合理,投影正确,布置得当。
为了使加工专利号易看懂、便于装配,图形尽可能与总装图一致,图形要清晰。
2. 标注尺寸要求统一、集中、有序、完整。
标注尺寸的顺序为:先标主要零件尺寸和出模斜度,再标注配合尺寸,然后标注全部尺寸。
在非主要零件图上先标注配合尺寸,后标注全部尺寸。
3. 表面粗糙度。
把应用最多的一种粗糙度标于图纸右上角,如标注"其余3.2。
"其它粗糙度符号在零件各表面分别标出。
4. 其它内容,例如零件名称、模具图号、材料牌号、热处理和硬度要求,表面处理、图形比例、自由尺寸的加工精度、技术说明等都要正确填写。
八、.校对、审图、描图、送晒A.自我校对的内容是:1. 模具及其零件与塑件图纸的关系模具及模具零件的材质、硬度、尺寸精度,结构等是否符合塑件图纸的要求。
2. 塑料制件方面塑料料流的流动、缩孔、熔接痕、裂口,脱模斜度等是否影响塑料制件的使用性能、尺寸精度、表面质量等方面的要求。
图案设计有无不足,加工是否简单,成型材料的收缩率选用是否正确。
3. 成型设备方面注射量、注射压力、锁模力够不够,模具的安装、塑料制件的南芯、脱模有无问题,注射机的喷嘴与哓口套是否正确地接触。
4. 模具结构方面1). 分型面位置及精加工精度是否满足需要,会不会发生溢料,开模后是否能保证塑料制件留在有顶出装置的模具一边。
2). 脱模方式是否正确,推广杆、推管的大小、位置、数量是否合适,推板会不会被型芯卡住,会不会造成擦伤成型零件。
3). 模具温度调节方面。
加热器的功率、数量;冷却介质的流动线路位置、大小、数量是否合适。
4). 处理塑料制件制侧凹的方法,脱侧凹的机构是否恰当,例如斜导柱抽芯机构中的滑块与推杆是否相互干扰。
5). 浇注、排气系统的位置,大小是否恰当。
5. 设计图纸1). 装配图上各模具零件安置部位是否恰当,表示得是否清楚,有无遗漏2). 零件图上的零件编号、名称,制作数量、零件内制还是外购的,是标准件还是非标准件,零件配合处理精度、成型塑料制件高精度尺寸处的修正加工及余量,模具零件的材料、热处理、表面处理、表面精加工程度是否标记、叙述清楚。
3). 零件主要零件、成型零件工作尺寸及配合尺寸。
尺寸数字应正确无误,不要使生产者换算。
4). 检查全部零件图及总装图的视图位置,投影是否正确,画法是否符合制图国标,有无遗漏尺寸。
6. 校核加工性能(所有零件的几何结构、视图画法、尺寸标'等是否有利于加工)7. 复算辅助工具的主要工作尺寸B.专业校对原则上按设计者自我校对项目进行;但是要侧重于结构原理、工艺性能及操作安全方面。
描图时要先消化图形,按国标要求描绘,填写全部尺寸及技术要求。
描后自校并且签字。
C.把描好的底图交设计者校对签字,习惯做法是由工具制造单位有关技术人员审查,会签、检查制造工艺性,然后才可送晒。
D..编写制造工艺卡片由工具制造单位技术人员编写制造工艺卡片,并且为加工制造做好准备。
在模具零件的制造过程中要加强检验,把检验的重点放在尺寸精度上。
模具组装完成后,由检验员根据模具检验表进行检验,主要的是检验模具零件的性能情况是否良好,只有这样才能俚语模具的制造质量。
九、试模及修模虽然是在选定成型材料、成型设备时,在预想的工艺条件下进行模具设计,但是人们的认识往往是不完善的,因此必须在模具加工完成以后,进行试模试验,看成型的制件质量如何。
发现总是以后,进行排除错误性的修模。
塑件出现不良现象的种类居多,原因也很复杂,有模具方面的原因,也有工艺条件方面的原因,二者往往交只在一起。
在修模前,应当根据塑件出现的不良现象的实际情况,进行细致地分析研究,找出造成塑件缺陷的原因后提出补救方法。
因为成型条件容易改变,所以一般的做法是先变更成型条件,当变更成型条件不能解决问题时,才考虑修理模具。
修理模具更应慎重,没有十分把握不可轻举妄动。
其原因是一旦变更了模具条件,就不能再作大的改造和恢复原状。
十、整理资料进行归档模具经试验后,若暂不使用,则应该完全擦除脱模渣滓、灰尘、油污等,涂上黄油或其他防锈油或防锈剂,关到保管场所保管。
把设计模具开始到模具加工成功,检验合格为止,在此期间所产生的技术资料,例如任务书、制件图、技术说明书、模具总装图、模具零件图、底图、模具设计说明书、检验记录表、试模修模记录等,按规定加以系统整理、装订、编号进行归档。
这样做似乎很麻烦,但是对以后修理模具,设计新的模具都是很有用处的。
返回上一页top 南阳理工学院机电系机械设计研究室维护制作© JDX00223 ALL RIGHTS RESERVED。