控制图类型及其原理
控制图基础知识介绍

控制图基础知识介绍一. 前言:为使现场的质量状况达成目标,均须加以管理。
我们所说的 “管理”作业,一般均用侦测产品的质量特性来判断 “管理”作业是否正常。
而质量特性会随着时间产生显著高低的变化;那么到底高到何种程度或低至何种状态才算我们所说的异常?故设定一合理的高低界限,作为我们分析现场制程状况是否在 “管理”状态,即为控制图的基本根源。
控制图是于1924年由美国品管大师修哈特(W.A.Shewhart)博士所发明。
而主要定义即是[一种以实际产品质量特性与依过去经验所研判的过程能力的控制界限比较,而以时间顺序表示出来的图形]。
二.控制图的基本特性:一般控制图纵轴均设定为产品的质量特性,而以过程变化的数据为刻度;横轴则为检测产品的群体代码或编号或年月日等,以时间别或制造先后别,依顺序点绘在图上。
在管制图上有三条笔直的横线,中间的一条为中心线(Central Line,CL),一般用蓝色的实线绘制;在上方的一条称为控制上限(Upper Control Limit,UCL);在下方的称为控制下限(Lower Control Limit,LCL)。
对上、下控制界限的绘制,则一般均用红色的虚线表现,以表示可接受的变异范围;至于实际产品质量特性的点连线条则大都用黑色实线绘制。
控制状态:三.控制图的原理:1.质量变异的形成原因:一般在制造的过程中,无论是多么精密的设备、环境,它的质量特性一定都会有变动,绝对无法做出完全一样的产品;而引起变动的原因可分为两种:一种为偶然(机遇)原因;一种为异常(非机遇)原因。
(1)偶然(机遇)原因(Chance causes):不可避免的原因、非人为的原因、共同性原因、一般性原因,是属于控制状态的变异。
(2)异常(非机遇)原因(Assignable causes):可避免的原因、人为的原因、特殊性原因、局部性原因等,不可让其存上控制界限(UCL) 中心线(CL) 下控制界限(LCL)在,必须追查原因,采取必要的行动,使过程恢复正常控制状态,否则会造成很大的损失。
管制图的原理与应用培训教程

管制图的原理与应用培训教程管制图是统计质量控制的一种重要工具,其原理是通过对过程的各种测量数据进行统计分析,从而监控和改进生产过程,确保产品质量稳定。
1.1 基本原理管制图的基本原理是根据过程的测量数据,建立一组统计标准和控制限,通过对过程数据的监控和分析,判断过程是否处于控制状态。
如果过程数据表现为随机变动,即符合统计分布的规律,说明过程是稳定的,产品质量是可控的;如果过程数据出现特殊原因引起的偏离,即出现了异常变动,说明过程可能存在问题,需要及时纠正。
1.2 控制图原理管制图通常分为均值图和范围图两种,均值图用于监控过程的平均值,范围图用于监控过程数据的变异程度。
通过监控这两种图,可以及时发现过程的异常变动,从而采取措施改进生产过程。
1.3 应用原理管制图的应用原理是要建立合适的统计标准和控制限,根据过程的特点和要求,选择合适的统计方法和控制图类型,通过对过程数据进行分析和监控,及时发现过程的异常变动,确保产品质量是稳定的。
同时,管制图还可以帮助生产管理人员了解过程的变动规律,找出可能存在的问题,从而加强过程改进和持续改进的能力。
二、管制图的应用管制图广泛应用于生产制造、服务行业和质量管理等领域,是保证产品质量稳定性和质量管理的重要手段。
2.1 生产制造领域在生产制造领域,管制图常用于监控生产线和工序的质量控制,通过对生产过程的监控和分析,发现潜在的质量问题,及时采取措施进行调整和改进,提高生产效率和产品质量。
2.2 服务行业在服务行业,管制图可以用于监控服务质量,发现服务过程中可能存在的问题和偏差,及时调整和改进服务流程,提高服务质量和客户满意度。
2.3 质量管理在质量管理领域,管制图可以用于监控和分析各种质量数据,发现产品质量的变异规律,判断产品是否合格,及时发现产品质量异常,减少质量损失。
2.4 实例应用以汽车制造业为例,汽车制造企业通过管制图对生产过程进行监控和分析,及时发现生产过程中可能存在的问题和异常,减少废品率和质量损失,提高产品质量和生产效率。
第二节-控制图原理

第二节-控制图原理什么是控制图控制图是一种用于监测和控制工程过程的可视化工具。
通常用于监测质量控制过程的统计数据,以便及时识别潜在问题并采取适当措施。
控制图也可以用于监测设备可靠性、生产进度等方面。
控制图的分类控制图可分为过程控制图和直方图。
过程控制图过程控制图是一种监测过程稳定性并指导改进的可视化工具。
它可以帮助我们在过程中及时发现不正常现象,以便采取适当措施,确保过程在稳定状态下运行。
过程控制图通常包括三种类型:一种是X-控制图,一种是S-控制图,另一种是R-控制图。
1.X控制图X控制图是一种数据类型控制图,用于监测均值是否稳定。
X控制图在原理上是比较简单的,是通过标准上下限范围内连续数据点的变化情况来判断过程是否稳定的。
2.S控制图S控制图用于监测数据分布的散布状况,通过这个散布情况来判断过程的稳定性。
如果散布过于广泛,则表明过程不稳定。
3.R控制图R控制图是一种可视的数据类型控制图,用于监测组内差异的大小和组间差异的大小。
如果组内差异很大,则表明过程不稳定。
直方图直方图是一种用于描述数据分布情况的图表。
它将数据进行分段,然后把每个分段的数据条数用柱状图表示出来,以便看出数据的分布规律。
直方图通常可以用于评估数据的分布形状,以便在研究中进行比较,并检测极端值/离群值。
如何制作控制图制作控制图的步骤如下:1.收集数据并进行分析首先我们需要收集数据,可以使用过程采样或过程监控系统,或手工记录过程数据。
然后对数据进行分析,计算出均值、标准差、极差等基本统计量。
2.设定控制限根据数据的均值、标准差和其他基本统计量,我们可以计算出控制限。
控制限是用来指导控制图的范围。
一般我们会选用3倍标准差作为上下控制限,即所谓的3σ控制图。
3.绘制控制图一旦确定了控制限,我们就可以开始绘制控制图了。
绘制控制图可以手动绘制,也可以使用计算机软件自动生成。
控制图的应用控制图的应用非常广泛,特别是在工业制造中。
经常使用控制图来监控生产过程,以及检测过程中的变化。
控制图应用的原理
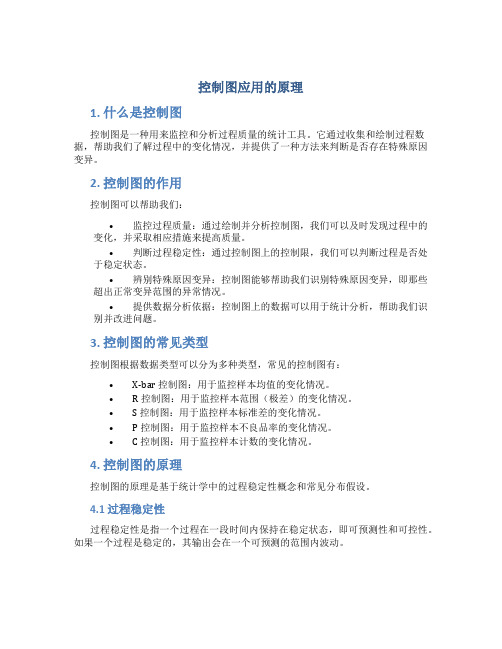
控制图应用的原理1. 什么是控制图控制图是一种用来监控和分析过程质量的统计工具。
它通过收集和绘制过程数据,帮助我们了解过程中的变化情况,并提供了一种方法来判断是否存在特殊原因变异。
2. 控制图的作用控制图可以帮助我们:•监控过程质量:通过绘制并分析控制图,我们可以及时发现过程中的变化,并采取相应措施来提高质量。
•判断过程稳定性:通过控制图上的控制限,我们可以判断过程是否处于稳定状态。
•辨别特殊原因变异:控制图能够帮助我们识别特殊原因变异,即那些超出正常变异范围的异常情况。
•提供数据分析依据:控制图上的数据可以用于统计分析,帮助我们识别并改进问题。
3. 控制图的常见类型控制图根据数据类型可以分为多种类型,常见的控制图有:•X-bar 控制图:用于监控样本均值的变化情况。
•R 控制图:用于监控样本范围(极差)的变化情况。
•S 控制图:用于监控样本标准差的变化情况。
•P 控制图:用于监控样本不良品率的变化情况。
• C 控制图:用于监控样本计数的变化情况。
4. 控制图的原理控制图的原理是基于统计学中的过程稳定性概念和常见分布假设。
4.1 过程稳定性过程稳定性是指一个过程在一段时间内保持在稳定状态,即可预测性和可控性。
如果一个过程是稳定的,其输出会在一个可预测的范围内波动。
控制图通过绘制上下控制限来判断过程是否稳定。
如果数据点落在控制限内,说明过程在统计上是稳定的;如果数据点超出控制限,说明过程可能出现了特殊原因变异。
4.2 正态分布假设控制图利用正态分布假设来判断过程的稳定性。
根据中心极限定理,当样本数量足够大时,样本平均值会近似服从正态分布。
绘制控制图时,我们通常假设样本平均值的分布是正态的,并以此为基础计算控制限。
4.3 控制限的计算方法控制限是用于判断过程稳定性的参考线。
通常情况下,控制限由平均线、上控制限和下控制限组成。
上控制限和下控制限的计算方法通常有以下几种:•3σ原则:上控制限等于平均值加上3倍标准差,下控制限等于平均值减去3倍标准差。
控制图的原理及应用
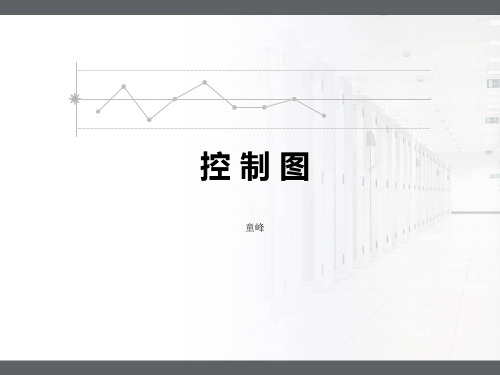
常态(正态)分布
=P[Z>z]
0
z
原则常态分布右边机率值
Z
Z
Z
0.00
0.500000000
1.50
0.066807201
3.00
0.001349898
0.01
0.496010644
1.51
要永久维持制造过程很正常旳生产,不让波动旳事项发生,
几乎是不可能旳。但当波动发生时,应立即查出原因,并加
以根除,或改善。
须调查原因
“波动”
成Resul果t
控制上限
控制下限
Time
波动分类 一般原因 特殊原因
出现次数 次数多
次数甚少
影响 微小 明显
结论 不值得调查原因 值得彻底调查其原因
明显旳波动,显示有特殊原因存在。假如做得到旳话,应加 以鉴定及矫正。控制界线以经济旳方式区别了这两种波动。
平衡曲线示意图
发生机率
UCL
α
β
LCL 一.第一种错误:虚发警报 二.第二种错误:漏发警报
第一种错误
第二种错误
1δ 2δ 3δ 4δ 5δ 6δ
利用经济平衡点措施求得,两种错误旳经济点:在±3δ处是最经济旳控制界 线
五、控制图旳应用
5.1 、控制图旳作用 5.2 、控制图旳分类 5.3 、控制图旳选用原则 5.4 、控制图旳计算 5.5 、控制图旳判断
LCL
第一种错误(α):生产者冒险率
生产质量相当良好,已到达允收水平,理应判为合格,但因为 控制线设置过窄,造成合格品误判为异常,其机率称为生产 者冒险率,所以种错误使生产者蒙受损失故得名之. 此冒险率又称为第一种错误 (TYPE Ⅰ ERROR) 简称(α).
控制图
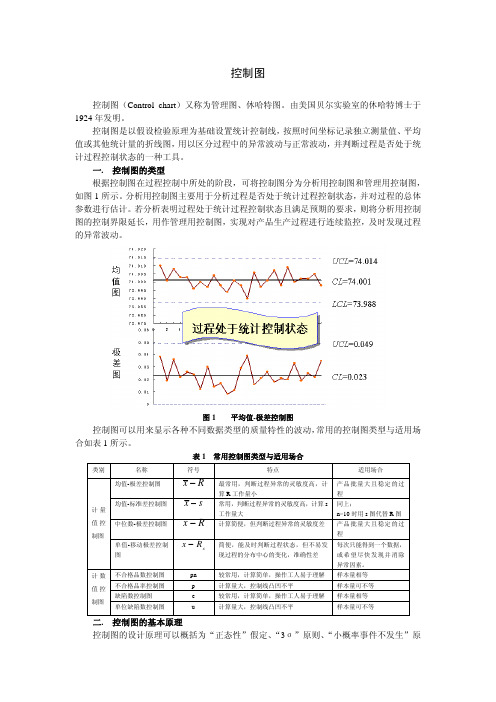
控制图控制图(Control chart)又称为管理图、休哈特图。
由美国贝尔实验室的休哈特博士于1924年发明。
控制图是以假设检验原理为基础设置统计控制线,按照时间坐标记录独立测量值、平均值或其他统计量的折线图,用以区分过程中的异常波动与正常波动,并判断过程是否处于统计过程控制状态的一种工具。
一. 控制图的类型根据控制图在过程控制中所处的阶段,可将控制图分为分析用控制图和管理用控制图,如图1所示。
分析用控制图主要用于分析过程是否处于统计过程控制状态,并对过程的总体参数进行估计。
若分析表明过程处于统计过程控制状态且满足预期的要求,则将分析用控制图的控制界限延长,用作管理用控制图,实现对产品生产过程进行连续监控,及时发现过程的异常波动。
图1 平均值-极差控制图控制图可以用来显示各种不同数据类型的质量特性的波动,常用的控制图类型与适用场合如表1所示。
表1 常用控制图类型与适用场合二. 控制图的基本原理控制图的设计原理可以概括为“正态性”假定、“3σ”原则、“小概率事件不发生”原理和“统计反证推断”思想。
具体说就是,假定所收集的质量特性数据服从正态分布,在此假定下,过程特性值落在分布中心上下各三倍标准差范围内的概率是99.73%,也就是说质量特性值落在上下三倍标准差之外的概率仅为0.27%,这是一个小概率事件,而“小概率事件不发生”原理认为小概率事件在一次观测中不发生,因此,一旦控制图出现“小概率事件发生”的现象,则表明过程发生了异常变化,这就是“统计反证推断”思想。
表2和表3分别表示计量值控制图和计数值控制图的中心线和控制界限的公式,以及样本量的确定。
表2 计量值控制图的中心线和控制界限表3 计量值控制图的中心线和控制界限三. 控制图的应用控制图显示随时间采集的数据和由这些数据计算出的波动;控制图与过程能力分析结合在一起称为统计过程控制(SPC)。
图2是一个典型的SPC的应用流程。
图2 典型的SPC的应用流程。
控制图的原理及其分类
•
1、
功的路 。20.7.3020.7.30Thursday, July 30, 2020
成功源于不懈的努力,人生最大的敌人是自己怯懦
•
2、
。0 4:23:34 04:23:3 404:237 /30/20 20 4:23:34 AM
每天只看目标,别老想障碍
•
3、
。20.7 .3004:2 3:3404: 23Jul-2 030-Jul-20
宁愿辛苦一阵子,不要辛苦一辈子
•
4、
。04:2 3:3404: 23:340 4:23Thursday, July 30, 2020
• •
积极向上的心态,是成功者的最基本要素 5、
。20.7 .3020.7 .3004:2 3:3404: 23:34July 30, 2020
生活总会给你谢另一个谢机会,大这个机家会叫明天 6、
。2 020年7 月30日 星期四 上午4 时23分3 4秒04:2 3:3420. 7.30
人生就像骑单车,想保持平衡就得往前走
•
7、
。202 0年7月 上午4 时23分2 0.7.300 4:23July 30, 2020
•
8、业余生活要有意义,不要越轨。20 20年7 月30日 星期四4 时23分 34秒04 :23:343 0 July 2020
M20.7.3020.7.30
我们必须在失败中寻找胜利,在绝望中寻求希望
•
9、
。上 午4时23 分34秒 上午4 时23分0 4:23:34 20.7.30
• 10、一个人的梦想也许不值钱,但一个人的努力很值 钱。7/30/2020 4:23:34 AM04:23:342020/7/30
控制图的基本特性与原理
第七章控制图95第七章控制图一.前言:为使现场的质量状况达成目标,均须加以管理。
我们所说的“管理”作业,一般均用侦测产品的质量特性来判断“管理”作业是否正常。
而质量特性会随着时间产生显著高低的变化;那么到底高到何种程度或低至何种状态才算我们所说的异常?故设定一合理的高低界限,作为我们分析现场制程状况是否在“管理”状态,即为控制图的基本根源。
控制图是于1924年由美国品管大师修哈特(W.A.Shewhart)博士所发明。
而主要定义即是[一种以实际产品质量特性与依过去经验所研判的过程能力的控制界限比较,而以时间顺序表示出来的图形]。
二.控制图的基本特性:一般控制图纵轴均设定为产品的质量特性,而以过程变化的数据为刻度;横轴则为检测产品的群体代码或编号或年月日等,以时间别或制造先后别,依顺序点绘在图上。
在管制图上有三条笔直的横线,中间的一条为中心线(Central Line,CL),一般用蓝色的实线绘制;在上方的一条称为控制上限(Upper Control Limit,UCL);在下方的称为控制下限(Lower Control Limit,LCL)。
对上、下控制界限的绘制,则一般均用红色的虚线表现,以表示可接受的变异范围;至于实际产品质量特性的点连线条则大都用黑色实线绘制。
控制状态:96 品管七大手法上控制界限(UCL)中心线(CL)下控制界限(LCL)三.控制图的原理:1.质量变异的形成原因:一般在制造的过程中,无论是多么精密的设备、环境,它的质量特性一定都会有变动,绝对无法做出完全一样的产品;而引起变动的原因可分为两种:一种为偶然(机遇)原因;一种为异常(非机遇)原因。
(1)偶然(机遇)原因(Chance causes):不可避免的原因、非人为的原因、共同性原因、一般性原因,是属于控制状态的变异。
(2)异常(非机遇)原因(Assignable causes):可避免的原因、人为的原因、特殊性原因、局部性原因等,不可让其存在,必须追查原因,采取必要的行动,使过程恢复正常控制状态,否则会造成很大的损失。
质量师中级知识--控制图原理
控制图原理⼀、控制图的结构控制图(Control Chart)是对过程质量特性值进⾏测定、记录、评估,从⽽监察过程是否处于控制状态的⼀种⽤统计⽅法设计的图。
图上有中⼼线(CL,Central line)、上控制限(UCL,Upper Control limit)和下控制限(LCL,lower Control limit),并有按时间顺序抽取的样本统计量数值的描点序列,参见图4.2-1。
UCL与LCL统称为控制线。
若控制图中的点落在UCL与LCL之外或点在UCL与LCL之间但排列不随机,则表明过程异常。
控制图有⼀个很⼤的优点,在图中将所描绘的点⼦与控制界限相⽐较,从⽽能够直观地看到产品或服务的质量的变化。
控制图构成必有中⼼线,上下控制限中的⼀条或两条和按时间顺序抽取的样本点⼦连线。
⼆、控制图的重要性1、是贯彻预防原则的重要⼯具,控制图可⽤以直接控制与诊断过程,是质量管理⼯具的重要组成部分。
2、可以应⽤于不同⾏业及不同规模的企业。
3、控制图应⽤推⼴反映了管理现代化的程度。
三、产品质量的统计观点1、产品质量具有变异性。
给定的公差范围体现了产品的变异性。
2、产品质量的变异具有统计规律性。
影响产品的因素可分为异常因素和偶然因素两类。
偶然因素对产品质量影响微⼩,是过程固有的难以消除,异常因素对产品质量影响⼤,不是过程所固有的,不难消除。
前者约占过程的85%,后者约占过程的15%。
由于异常因素不是过程所固有,故容易发现,通常可由过程控制⼈员⾃⾏消除,⽽不必求⾼⼀级的管理⼈员。
由于偶然因素是过程所固有,故难以发现。
偶然因素涉及到⼈、机、料、法、环、测等整个系统的改进,故需由⾼⼀级⼈员决策。
休哈特控制图的实质就是区分偶然因素与异常因素。
四、控制图原理(⼀)控制图的形成:将通常的正态分布转个⽅向,使⾃变量增加的⽅向垂直向上,将µ、µ+3σ、µ-3σ分别标为CL、UCL和LCL,就得到⼀张控制图。
控制图的原理及应用
本:
,其平均值 x1, x有2,如…,下xn性质:
x
E(x)
(x)
n
和 则可通过k组大小为n的样本得到:
ˆ x
ˆ R
d2
其中, 是由n来d2确定的控制系数,可以通过查取计量控制图系数表(见表7-4)
得到。
12
二、计量值控制图
• 所以,由控制界限的一般公式即可得到图的控制界限为:
• 式中,
4
一、控制图基本原理
质 量 特 性 值
O
UCL CL
LCL 样本组号
5
一、控制图基本原理
(二)控制图的统计原理
1. 原理 3
当质量特性值服从正态分布时, 3即
X ~ N(, 2)
如果 生E(产X )过程中仅存在偶然因素,那么其产品质量特性值将会有
99.73%落在
的范围内。 3
6
一、控制图基本原理
c4
由此可以得到 图中x s 图的控x制界限为:
UCL
3 x 3s
n
c4 n
CL x
x
A3s
LCL
3
n
x
3s c4 n
x
A3s
• 式中
A3
3 c4
n
18
二、计量值控制图
• s图的控制界限为:
UCL c4 3
1 c42
3 s
1 c42 s c4
B4s
CL c4 s
LCL
• (三)控制图的分类——计量
分布 控制图类型 符号表示
适用范围及特点
平均值—极 差
控制图
xR 图
用于判断过程质量特性的均值以及极差(间接估算标 准差)是否处于所要求的水平,针对重量、长度、强 度等计量值控制对象,适用于产品批量较大且较为稳 定的工序,是最常用、最基本的控制图。判断工序异 常的灵敏度高,且极差计算工作量小
- 1、下载文档前请自行甄别文档内容的完整性,平台不提供额外的编辑、内容补充、找答案等附加服务。
- 2、"仅部分预览"的文档,不可在线预览部分如存在完整性等问题,可反馈申请退款(可完整预览的文档不适用该条件!)。
- 3、如文档侵犯您的权益,请联系客服反馈,我们会尽快为您处理(人工客服工作时间:9:00-18:30)。
X—Rs图 Pn图
计算移动极差Rsi 计算平均不合格品率
P图
计算各组不合格品率pi
C图
计算各样本的平均缺陷数
U图
计算各样本的单位缺陷数ui
计算公式
备注
xij——第I样本中的第j个数据i=1,2…k; j=1,2…n;
max(xij)——第i样本中最大值; min(xij)——第i样本中最大值。
——n为奇数时,第i样本中按大 小顺序排列起的数据列中间位置的数据
• 应用度。
若点子落在控制界限内,认为工序的波动是正常的波动;8 若点 子
控制图基本构造
控制上线UCL
x(或x、R、S等)
控制中线CL 控制下线LCL
0 1 2 3 4 5 6 7 8 9 10 11 12 13 14 15 16 17 18
样本号(或时间)
控制图的构造
1 值或其统计量为纵坐标的平面坐
1/p~5/p
尽可能使样本中缺 陷数C=1~5
18
图名称 图
步骤
(1)计算各样本平均值 (2)计算各样本极差Ri
图 (1)找出或计算出各样本的 中位数
(2)计算各样本极差Ri
L—S图
(1)找出各组最大值Li和最小 值Si (2)计算最大值平均值 和 最小值平均值
(3)计算平均极差
(4)计算范围中值M
pn p C U
计算简便,但效果较差些, 便于现场使用 一张图可同时控制均值和方 差,计算简单,使用方便 简便省事,并能及时判断工 序是否处于稳定状态。缺点 是不易发现工序分布中心的 变化。 较常用,计算简单,操作工 人易于理解 计算量大,管理界限凹凸不 平 较常用,计算简单,操作工 人易于理解,使用简便 计算量大,管理界限凹凸不 平
(见图3)
控制图的两类错误
❖ 当工序正常时,点子仍有落在控制界限外面的可能,此时会发生将正 常波动判断为 非正常波 动的错误——误发信号的错误,这种错误称
为第一类错误,控制图犯第一类错误 的概率记为α
❖ 设总体均值μ0在异常因素的作用下移至μ1 ,σ不变。此时,点子应落
在控 制界限外以发出警报。但却也存在点子落在控制界限内不发警 报的可能。这将导致将非正常波动判断 为正常波动的错误——漏发 信号的错误,这种错误称为第二类错误,控制图第二类错误的概率记
2
和下控制线LCL
3
CL、上控制线UCL
9
控制图应用
在实际生产过程中,坐标系及三条控制线是由质量管理人员 事先经过工序能力调查及其数据 的收集与计算绘制好的。工 序的操作人员按预先规定好的时间间隔抽取规定数量的样品 ,将 样品的测定值或其统计量在控制图上打点并联接为质量 波动曲线,并通过点子的位置及排 列情况判断工序状态。
∴由异常因素造成的波动称为不正常的波动。此时的工序处于不稳定状态 或非受
控状态。对这样的工序必须严加控制。
3
图a 图c
公差上限
公差下限 公差上限
图b
公差下限
时间 图d 生产过程的几种状态
公差上限 公差下限 公差上限 公差下限
4
二 统计工序控制的概念
在生产过程中,判别工序是否在受着异常因素 的影响可以采取下面的方法 :每隔一定的时间 间隔,在生产的产品中进行随机抽样,并根据 样本数据观察质量特性值的分布状态 。若工序 分布状态不随时间的推移而变化(即如图a) 说明工序处于稳定状态,只 受着偶然因素的影 响;若工序分布状态随着时间的推移发生变化( 如图b,c,d),说 明工序处于非稳定状态,正在有 异常因素影响着它,必须立即采取措施消除异 常因素的影响 。
• 对质量波动的影响并不大,一般来说,并不超出工序规格范围; • 因素的影响在经济上并不值得消除; • 在技术上也是难以测量、难以避免的; • 由偶然因素造成的质量特性值分布状态不随时间的变化而变化。
∴由偶然因素造成的质 量波动称为正常的波动,这种波动一般通过公差加以反映,此时
2 异常因素(系统因素)
概念:利用统计规律判别和控制异常因素造成 的质量波动,从而保证工序处于控制状态的手 段 5
三 统计工序控制与产品检查的 区别
统计工序控制与产品检查有着本质的区别。
检查是通过比较产品质量特性测量值与规格要求 ,达到
剔除不合格品的目的,是事后把关。统计工序控制是通 过样本数据分布状态估计总体 分布状态的变化,从而达 到预防异常因素造成的不正常质量波动,消除质量隐患
量
2 3 收集预备数据
4 各种控制图控制界限的计算方法及计算公式不同,但其
计算
(1)计算各样本参数(见表3)
(2)计算分析用控制图控制线(见表4)
5 作分析用控制图并判断工序是否处于稳定状态
6 与规格比较,确定控制用控制图
7
17
3 收集预备数据
控制收图集名称预备数据样的本目数 的k 只为作样分本析容 用量 控n 制图以判断备 工注序状态
L—S图用 A9
2.695 1.826 1.522 1.363 1.263 1.914 1.143 1.104 1.072
21
二 各类控制图作法举例
1
控制图(平均值——极差控制图)
• 确定方法
休哈特控制图控制界限是以3σ原理确定的。即以质量 特性统计量的均值作为控制中线CL; 在距均值±3σ处作 控制上、下线。由3σ原理确定的控制图可以在最经济的
条件下达到保证 生产过程稳定的目的。
13
3σ原理
设工序处于正常状态时,质量特性总体的均值为μ0,标准偏差 为σ, 设三条控制线的位置分别为CL= μ0 、UCL= μ0 +kσ,LCL= μ0 -kσ。
单击此处编辑母版标题样 控制图类型及其式原理
单击此处编辑母版副标题样式
1
13.1 基本概念
• 影响因素分类 • 统计工序控制的概念 • 统计工序控制与产品检查的区别
2
一
1
•小对生产过程一直起作用的因素。如材料成分、规格、硬度等的 微小变化;设备的微
; 震动;刃具的正常磨损;夹具的弹性变型及微小松动;工人操作的微 小不均匀性等
况
的图表。它是判断工序是 否处于稳定状态、保持生产过程始终 处
于正常状态的有效工具。
控制图与趋势图的比较
采用趋势图可以掌握不断变化着的工序状态。为了判别工序的质量波动
是正常波动还是非正常波动,在趋势图的基础上,控制图发生如下变化 :
①纵坐标可能是质量特性值,也可能是其统计量,如
、R
等;
• 控制图基本②构增造加上、中、下三条控制线作为判断工序有无异常的标准和尺
13.2
• 控制图及其基本构造 • 控制图的类型 • 控制界限制图及其基本构造
产生:控制图是由美国贝尔(Bell)通信研究所的休哈特(W.A Shewhart)
博
士发明的,因 此也称休哈特控制图。
定义:控制图是反映和控制质量特性值分布状态随时间而发生的变动情
、下限内侧,即UCL>TU;LCL< TL。而是要看受控工序 的工序能力是否满足给定的Cp值要求。
20
样本大小
2 3 4 5 6 7 8 9 10
A2 1.880 1.023 0.729 0.577 0.483 0.419 0.373 0.337 0.308
表5 控制图系数表
R图用
D3
D4
-
2.267
为β。
• 控制界限与两类错误的关系
放宽控制界限,即k越大,第一类错误的概率α越小,第二类错误的 概率β越大;反之,加严控制界限,即k越小,第一类错误的概率α越 大,第二类错误的概率β减小。控制界限系数k的确定应以两类错误
判断的总损失最小为原则。
理论证明,当k=3时,即控制图上下界限距中心线CL为±3σ时,14 合
-
2.575
-
2.282
-
2.115
-
2.004
0.076
1.924
0.136
1.864
0.184
1.816
0.223
1.777
M3A2 1.880 1.187 0.796 0.691 0.549 0.509 0.432 0.412 0.363
X图用 E2
2.660 1.772 1.457 1.290 1.184 1.109 1.054 1.010 0.975
11
类别
计 量 值 控 制 图
计 数 值 控 制 图
名称
均值—极差 控制图
中位数—极 差控制图 两极控制图
单值—移动 极差控制图
不合格品数 控制图
不合格品率 控制图
缺陷数控制 图
单位缺陷数 控制图
管理图
表1
控制图种类及适用场合
特
点
符号
最常用,判断工序是否异常
的效果好,但计算工作量大
L—S X—Rs
。数图据采集的方法是间隔随机抽样。为能反映工序总体状
况,图数据应在一般1k0=~20~1255天内收集一般,3~并6 应详细图地的样记本录容在量常事取先3或准5
备L—好S图的调查表内。数据收集的个数参见表2。
X—Rs图
K=2表0~230控制图的样本与1样本容量
pn图、 p 图 C图、U图
一般k=20~25
在坐标图上画出三条控制线,控制中线一般以细实线表示
,控制上下线以虚线表示。
将预备 数据各样本的参数值在控制图中打点。 根据本节介绍的控制图的判断规则判断工序状态是否 稳定
,若判断工序状态不稳定,应查明原因,消除不稳定因素 ,重新收集预备数据,直至得 到稳定状态下分析用控制图
6 与规格比较,确定控制用控制图
适用场合
适用于产品批量较大 而且稳定正常的工序 。
因各种原因(时间费 用等)每次只能得到 一个数据或希望尽快 发现并消除异常原因 样本容量相等