FMEA失效模式及后果分析的评分标准
FMEA潜在失效模式及后果分析含表单及评价标准最新制定
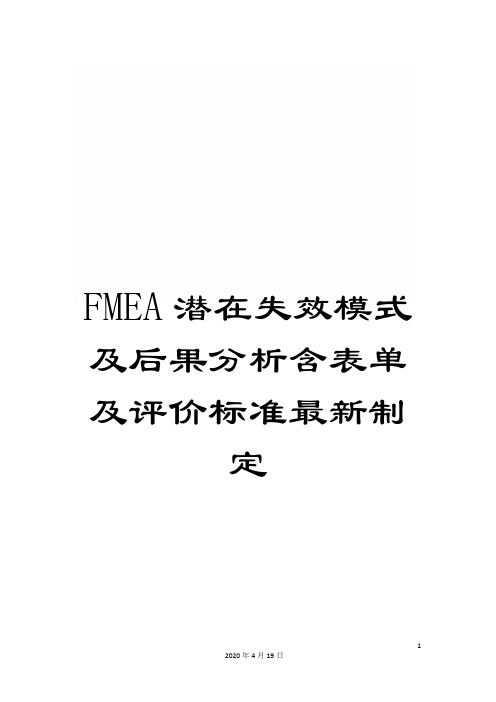
FMEA潜在失效模式及后果分析含表单及评价标准最新制
定
1
2020年4月19日
ZD-700-05
版本:10
QB
文件代码/版本:QI-02-09-A/0
潜在失效模式及后果分析
新制定
- 1 -
2020年4月19日
编制:审核:批准:
颁布日期:实施日期:
- 2 -
2020年4月19日
- 3 - 2020年4月19日
1. 目的:
1.1 认可并评价产品/过程中的潜在失效以及该失效的后果。
1.2 确定能否消除或减少潜在失效发生的机会并全部文件化。
2. 范围:
在进行FMEA时有三种基本的情形,每一种都有不同的范围或关注焦点:
2.1 对新设计、新技术或新过程,FMEA的范围是全部设计、技术或过程。
2.2 对现有设计或过程的修改(假设对现有设计或过程已有FMEA),FMEA的
范围是对设计或过程的修改、由于修改可能产生手工艺相互影响以及现
场的历史情况。
2.3 对现有的设计或过程用于新的环境、场所或应用(假设对现有设计或过
程已有FMEA),FMEA的范围是新环境或场所对现有设计或过程的影响。
3. 职责:
3.1 产品与技术中心:
3.1.1 负责本程序的制定与维护。
3.1.2 负责承担组织FMEA制定的发起者、对FMEA潜在模式及后果分析进行
管理。
3.1.3 负责对FMEA措施对策跟踪,以及组织小组人员对措施实施后风险顺
序数评估。
3.2 FMEA小组组长:负责调动和协调所有有关方面代表的积极参与,组织
- 4 -
2020年4月19日。
(完整版)新版FMEA失效模式及后果分析AP行动优先级评价准则

Very hign
8-10
Low-very low
7-10
M
Moderate
5-6
M
Hign
2-4
L
Very hign
1
L
高
Hign
6-7
Low-Very low
7-10
L
Moderate
5-6
L
Hign
2-4
L
Very hign
1
L
中
Moderate
4-5
Low-very low
7-10
L
Moderate
2-4
H
Very hign
1
H
中
Moderate
4-5
Low-very low
7-10
H
Moderate
5-6
H
Hign
2-4
H
Very hign
1
M
低
Low
2-3
Low-very low
7-10
H
Moderate
5-6
M
Hign
2-4
L
Very hign
1
L
非常低
Very low
1
Very hign-Very low
1-10
L
产品或工厂的影响高
Product or plant effect hign
7-8
非常高
Very hign
8-10
Low-very low
7-10
H
Moderate
5-6
H
Hign
2-4
H
FMEA问题等级评分标准
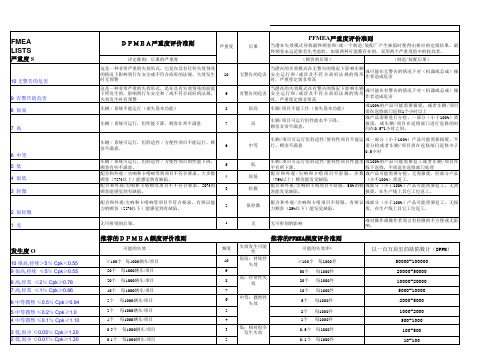
探测性
准则
探测方法的推荐范围
ABC
设计控制将不能和/或不可能找出潜在的起因/机理及后 续的失效模式,或根本没有设计控制
10
几乎不可能 绝对肯定不可能探测
不能探测或没有检查
X
设计控制只有很极少的机会能找出潜在的起因/机理及后 续的失效模式
9
很微小 控制方法可能探测不出来
只能通过间接或随机检查来实现控制
高
车辆/项目可运行但性能水平下降。 顾客非常不满意。
或产品需要进行分检、一部分(小于100%)需 报废,或车辆/项目在返修部门进行返修的时 间在0.5-1小时之间。
车辆/系统可运行,但舒适性/方便性项目不能运行,顾 客不满意。
6
中等
车辆/项目可运行但舒适性/便利性项目不能运 或一部分(小于100%)产品可能需要报废,不
车辆/项目可运行但舒适性/便利性项目性能水 或100%的产品可能需要返工或者车辆/项目在
平有所下降。
线下返修,不需送往返修部门处理
配合和外观/尖响和卡嗒项目不舒服。多数 或产品可能需要分检,无需报废,但部分产品
(75%以上)顾客能发觉缺陷
(小不100%)需返工。
配合和外观/尖响和卡嗒项目不舒服。50%的顾 或部分(小于100%)产品可能需要返工,无需
级低:失效不 太可能发生
≤0.01个 每1000件
1-10
可探测度 D
10 几乎不可能 9 很微小 8 微小 7 很小 6小 5 中等 4 中上 3高 2 很高 1 很高,肯定能检出
.推荐的DFMEA探测度评价准则
.推荐的PFMEA探测度评价准则
检查类别
准则:设计控制可能探测出来的可能性
探测度定 级
fmea打分规则
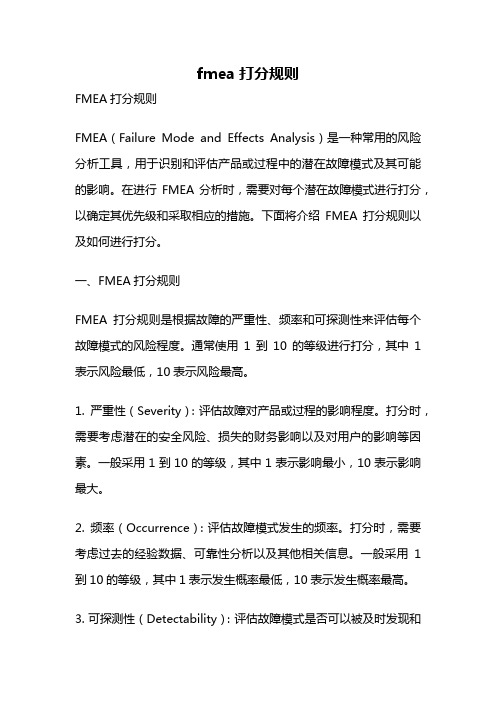
fmea打分规则FMEA打分规则FMEA(Failure Mode and Effects Analysis)是一种常用的风险分析工具,用于识别和评估产品或过程中的潜在故障模式及其可能的影响。
在进行FMEA分析时,需要对每个潜在故障模式进行打分,以确定其优先级和采取相应的措施。
下面将介绍FMEA打分规则以及如何进行打分。
一、FMEA打分规则FMEA打分规则是根据故障的严重性、频率和可探测性来评估每个故障模式的风险程度。
通常使用1到10的等级进行打分,其中1表示风险最低,10表示风险最高。
1. 严重性(Severity):评估故障对产品或过程的影响程度。
打分时,需要考虑潜在的安全风险、损失的财务影响以及对用户的影响等因素。
一般采用1到10的等级,其中1表示影响最小,10表示影响最大。
2. 频率(Occurrence):评估故障模式发生的频率。
打分时,需要考虑过去的经验数据、可靠性分析以及其他相关信息。
一般采用1到10的等级,其中1表示发生概率最低,10表示发生概率最高。
3. 可探测性(Detectability):评估故障模式是否可以被及时发现和探测。
打分时,需要考虑现有的检测手段、监测系统以及人工检查等因素。
一般采用1到10的等级,其中1表示可以容易地被探测到,10表示很难被探测到。
二、FMEA打分方法1. 计算风险优先数(Risk Priority Number,RPN):RPN是FMEA中用于确定优先级的指标,是通过将严重性、频率和可探测性的打分相乘得到的。
RPN=Severity × Occurrence × Detectability。
根据RPN的大小,可以确定优先处理的故障模式。
2. 制定打分规则:根据实际情况和需求,制定FMEA打分规则。
例如,可以定义RPN大于100的故障模式为高风险,需要立即采取措施;RPN在50到100之间的故障模式为中风险,需要进行改进;RPN小于50的故障模式为低风险,可以接受。
完整版)新版FMEA失效模式及后果分析AP行动优先级评价准则
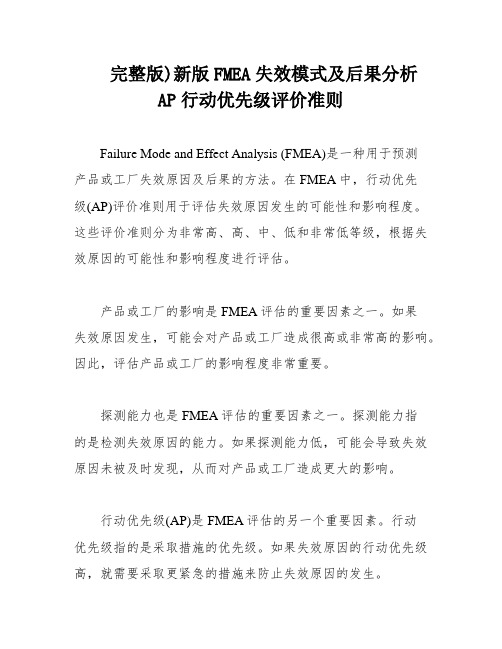
完整版)新版FMEA失效模式及后果分析
AP行动优先级评价准则
Failure Mode and Effect Analysis (FMEA)是一种用于预测
产品或工厂失效原因及后果的方法。
在FMEA中,行动优先
级(AP)评价准则用于评估失效原因发生的可能性和影响程度。
这些评价准则分为非常高、高、中、低和非常低等级,根据失效原因的可能性和影响程度进行评估。
产品或工厂的影响是FMEA评估的重要因素之一。
如果
失效原因发生,可能会对产品或工厂造成很高或非常高的影响。
因此,评估产品或工厂的影响程度非常重要。
探测能力也是FMEA评估的重要因素之一。
探测能力指
的是检测失效原因的能力。
如果探测能力低,可能会导致失效原因未被及时发现,从而对产品或工厂造成更大的影响。
行动优先级(AP)是FMEA评估的另一个重要因素。
行动
优先级指的是采取措施的优先级。
如果失效原因的行动优先级高,就需要采取更紧急的措施来防止失效原因的发生。
综上所述,FMEA是一种有效的方法,可用于预测产品或工厂失效原因及后果。
通过评估失效原因的可能性、影响程度、产品或工厂的影响、探测能力和行动优先级,可以采取相应的措施来防止失效原因的发生,从而确保产品或工厂的正常运行。
FMEA评价准则(第四版)
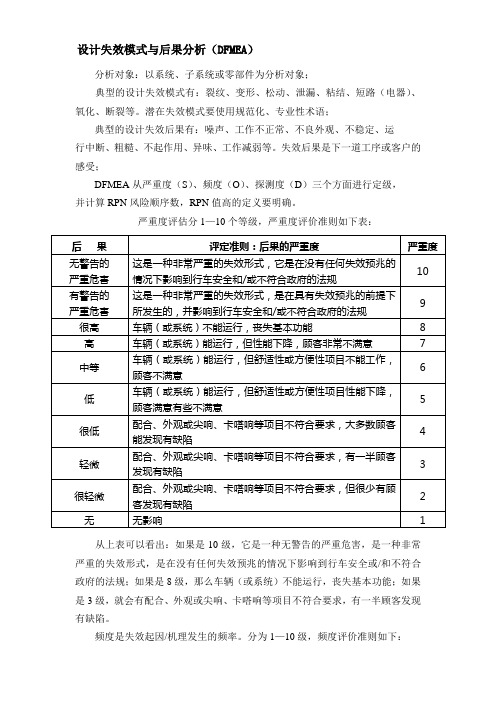
设计失效模式与后果分析(DFMEA)分析对象:以系统、子系统或零部件为分析对象;典型的设计失效模式有:裂纹、变形、松动、泄漏、粘结、短路(电器)、氧化、断裂等。
潜在失效模式要使用规范化、专业性术语;典型的设计失效后果有:噪声、工作不正常、不良外观、不稳定、运行中断、粗糙、不起作用、异味、工作减弱等。
失效后果是下一道工序或客户的感受;DFMEA从严重度(S)、频度(O)、探测度(D)三个方面进行定级,并计算RPN风险顺序数,RPN值高的定义要明确。
严重度评估分1—10个等级,严重度评价准则如下表:从上表可以看出:如果是10级,它是一种无警告的严重危害,是一种非常严重的失效形式,是在没有任何失效预兆的情况下影响到行车安全或/和不符合政府的法规;如果是8级,那么车辆(或系统)不能运行,丧失基本功能;如果是3级,就会有配合、外观或尖响、卡嗒响等项目不符合要求,有一半顾客发现有缺陷。
频度是失效起因/机理发生的频率。
分为1—10级,频度评价准则如下:从上表可看出:如果频度是10级,那么失效可能性很高几乎是不可避免的,每1000辆车或项目的失效可能大于100个;如果是6级,那么失效可能性中等,只是偶尔发生失效,每1000辆车或项目失效可能大于5;如果是2级,那么失效可能性低,相对很少发生失效,可能的失效率是千分之0.01。
探测度是指在零部件、子系统或系统投产之前,用现行设计控制方法来探测潜在失效起因/机理(设计薄弱部分)的能力评价指标,分1—10级:探测度评价准则如下表:从上表可以看出:如果是10级,那么探测性是绝对不肯定。
也就是用现行的设计控制将不能或不可能找出潜在的起因/机理及后续的失效模式,或根本没有设计控制;如果是6级,那么用现行设计控制有较少的机会能找出潜在起因/机理及后续的失效模式。
三、过程失效模式与后果分析(PFMEA)分析对象:以加工工艺过程的每道工序为分析对象;典型的过程失效模式有:弯曲、粘合、毛刺、转运损坏、断裂、变形脏污、安装调试不当、接地、开路、短路、工具磨损等;过程的失效后果分两种:下道工序而言:有无法紧固、无法钻孔/攻丝、无法加工表面、危害操作者、不配合、不连续、损坏设备等;对最终使用者而言:有噪声、工作不正常、不起作用、不稳定、牵引动力、外观不良、粗糙、费力、异味、工作减弱、间歇性工作、车辆控制减弱等。
FMEA失效模式及后果分析的评分标准
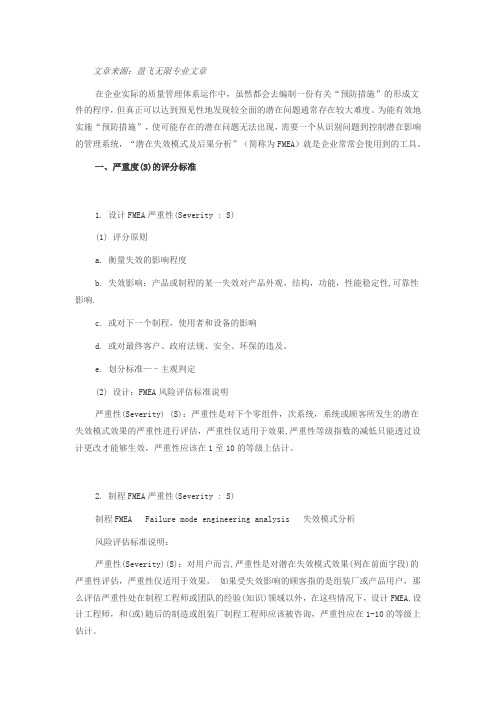
文章来源:盈飞无限专业文章在企业实际的质量管理体系运作中,虽然都会去编制一份有关“预防措施”的形成文件的程序,但真正可以达到预见性地发现较全面的潜在问题通常存在较大难度。
为能有效地实施“预防措施”,使可能存在的潜在问题无法出现,需要一个从识别问题到控制潜在影响的管理系统,“潜在失效模式及后果分析”(简称为FMEA)就是企业常常会使用到的工具。
一、严重度(S)的评分标准1. 设计FMEA严重性(Severity : S)(1) 评分原则a. 衡量失效的影响程度b. 失效影响:产品或制程的某一失效对产品外观,结构,功能,性能稳定性,可靠性影响.c. 或对下一个制程,使用者和设备的影响d. 或对最终客户、政府法规、安全、环保的违及。
e. 划分标准—–主观判定(2) 设计:FMEA风险评估标准说明严重性(Severity) (S):严重性是对下个零组件,次系统,系统或顾客所发生的潜在失效模式效果的严重性进行评估,严重性仅适用于效果,严重性等级指数的减低只能透过设计更改才能够生效,严重性应该在1至10的等级上估计。
2. 制程FMEA严重性(Severity : S)制程FMEA Failure mode engineering analysis 失效模式分析风险评估标准说明:严重性(Severity)(S):对用户而言,严重性是对潜在失效模式效果(列在前面字段)的严重性评估,严重性仅适用于效果,如果受失效影响的顾客指的是组装厂或产品用户,那么评估严重性处在制程工程师或团队的经验(知识)领域以外,在这些情况下,设计FMEA,设计工程师,和(或)随后的制造或组装厂制程工程师应该被咨询,严重性应在1-10的等级上估计。
二. 发生率(O)的评分标准1. 设计FMEA发生性:Occurrence (O)(1) 评分原则a. 某一原因而导致失效发生的几率b. 划分标准:Cpk、主观判定、统计资料(2) 设计:FMEA发生率评估标准说明发生性(Occurrence) (O):发生性是特定原因或结构(在上字段中列出)将会发生的可能性,发生等级数字(可能性)有其含义但不一定是个数值,透过设计更改来取消或控制一个或多个失效模式的原因或结构是使发生等级下降的唯一方法。
fmea评分标准rpn

fmea评分标准rpnFMEA评分标准RPN。
FMEA(Failure Mode and Effects Analysis)是一种系统性的、有组织的、以团队为基础的方法,用于识别和评估设计或过程中可能出现的故障模式及其影响。
RPN(Risk Priority Number)是FMEA中常用的一种评分方法,用于对故障模式的风险进行排序,以确定优先处理的故障模式。
本文将详细介绍FMEA评分标准RPN的相关内容。
首先,RPN的计算公式为RPN = Severity × Occurrence × Detection。
其中,Severity代表故障的严重程度,Occurrence代表故障的发生频率,Detection代表故障的检测能力。
这三个参数分别用1至10的等级来评分,等级越高代表风险越大。
通过将这三个参数相乘,可以得到每个故障模式的RPN值。
其次,RPN值的范围通常为1至1000,这是因为Severity、Occurrence和Detection的等级范围均为1至10,所以RPN的最大值为10 × 10 × 10 = 1000。
根据RPN值的大小,可以对故障模式的风险进行排序,以确定哪些故障模式需要优先处理。
一般来说,RPN值大于等于100的故障模式被认为是高风险的,需要优先处理。
另外,对于RPN值较高的故障模式,团队可以采取一些措施来降低其风险。
例如,可以通过改进设计、加强监控、提高检测能力等方式来降低故障的严重程度、减少故障的发生频率、提高故障的检测能力,从而降低RPN值。
通过不断优化和改进,可以有效降低产品或过程中的潜在风险,提高其可靠性和稳定性。
最后,需要注意的是,RPN值只是一种评估风险的方法,它并不能完全代表实际的风险水平。
在实际应用中,团队还需要综合考虑其他因素,如潜在的影响范围、历史数据、专家意见等,来全面评估故障模式的风险。
因此,在使用RPN值进行风险排序时,团队需要谨慎对待,不可片面依赖RPN值,而应该结合实际情况进行综合分析。
- 1、下载文档前请自行甄别文档内容的完整性,平台不提供额外的编辑、内容补充、找答案等附加服务。
- 2、"仅部分预览"的文档,不可在线预览部分如存在完整性等问题,可反馈申请退款(可完整预览的文档不适用该条件!)。
- 3、如文档侵犯您的权益,请联系客服反馈,我们会尽快为您处理(人工客服工作时间:9:00-18:30)。
F M E A失效模式及后果
分析的评分标准
标准化工作室编码[XX968T-XX89628-XJ668-XT689N]
导语:潜在失效模式及后果分析(FailureModeandEffectsAnalysis,简记为FMEA),是分析系统中每一产品所有可能产生的故障模式及其对系统造成的所有可能影响,并按每一个故障模式的严重程度,检测难易程序以及发生频度予以分类的一种归纳分析方法。
今天,小编为大家精心准备了有关F M E A的评分标准,绝对的干货!
文章来源:盈飞无限专业文章
在企业实际的质量管理体系运作中,虽然都会去编制一份有关“预防措施”的形成文件的程序,但真正可以达到预见性地发现较全面的潜在问题通常存在较大难度。
为能有效地实施“预防措施”,使可能存在的潜在问题无法出现,需要一个从识别问题到控制潜在影响的管理系统,“潜在失效模式及后果分析”(简称为FMEA)就是企业常常会使用到的工具。
一、严重度(S)的评分标准
1.设计FMEA严重性(Severity:S)
(1)评分原则
a.衡量失效的影响程度
b.失效影响:产品或制程的某一失效对产品外观,结构,功能,性能稳定性,可靠性影响.
c.或对下一个制程,使用者和设备的影响
d.或对最终客户、政府法规、安全、环保的违及。
e.划分标准—–主观判定
(2)设计:FMEA风险评估标准说明
严重性(Severity)(S):严重性是对下个零组件,次系统,系统或顾客所发生的潜在失效模式效果的严重性进行评估,严重性仅适用于效果,严重性等级指数的减低只能透过设计更改才能够生效,严重性应该在1至10的等级上估计。
2.制程FMEA严重性(Severity:S)
制程FMEA?Failuremodeengineeringanalysis?失效模式分析
风险评估标准说明:
严重性(Severity)(S):对用户而言,严重性是对潜在失效模式效果(列在前面字段)的严重性评估,严重性仅适用于效果,如果受失效影响的顾客指的是组装厂或产品用户,那么评估严重性处在制程工程师或团队的经验(知识)领域以外,在这些情况下,设计FMEA,设计工程师,和(或)随后的制造或组装厂制程工程师应该被咨询,严重性应在1-10的等级上估计。
二.发生率(O)的评分标准
1.设计FMEA发生性:Occurrence(O)
(1)评分原则
a.某一原因而导致失效发生的几率
b.划分标准:Cpk、主观判定、统计资料
(2)设计:FMEA发生率评估标准说明
发生性(Occurrence)(O):发生性是特定原因或结构(在上字段中列出)将会发生的可能性,发生等级数字(可能性)有其含义但不一定是个数值,透过设计更改来取消或控制一个或多个失效模式的原因或结构是使发生等级下降的唯一方法。
推荐的评估的标准:整个团队应该赞同一项评估标准和等级体系,保持一致性,即便就单个产品分析进行修改。
2.?制程FMEA发生性:Occurrence(O)
发生性(Occurrence)(O):发生性是指特定失效原因与结构预计会发生性的频率(列在上栏),发生性等级数字有其含义但不一定是一个数值,用1-10的等级来估计发生性的可能性,就这种等级而言,只有导致失效模式的发生性应该加以考虑,而失效侦测的方法不在这里考虑。
三.难检度(D)的评分标准
1.?设计FMEA侦测性:detection(D)
评分原则:在现行的控制措施下,侦测失效发生的能力。
划分标准:主观判定,统计资料。
侦测性(detection)(D):侦测性是对第二类现行设计管制能力的评估,目的是为了测出一个潜在的原因与结构(设计弱点),或者是对每三类现行设计管制之能力的评估,目的是发现随后失效模式,在零组件,子系统或系统投入生产之前。
取得较低的等级,规划好的设计控制(如:预防措施,验证,和(或)验收行动)应从总体上加以改进。
推荐的评估的标准:即使针对个别地制程分析进行修改,团队也应该赞同并保持一致地侦侧性评估标准与评分等级。
评估标准与评分等级如下表:
2.制程FMEA侦测性:detection(D)
推荐的评估标准:(团队应该赞同一项评估标准和一致的等级标准,即使为某一单个制程分析作点修改)。