无碳小车设计方案
8字无碳小车设计方案

设计一种小车,驱动其行走及转向的能量是根据能量转换原理, 由给定重力势能转换而得到的.该给定重力势能由竞赛时统一使用质量为1Kg 的标准砝码(¢50×65 mm,碳钢制作) 来获得4J 能量,要求砝码的可下降高度为400±2mm.标准砝码始终由小车承载,不允许从小车上掉落。
图1 为小车示意图。
图一要求小车在行走过程中完成所有动作所需的能量均由此给定重力势能转换而得,不可以使用任何其他来源的能量。
要求小车具有转向控制机构,且此转向控制机构具有可调节功能,以适应放有不同间距障碍物的竞赛场地。
要求小车为三轮结构。
在300~500mm 范围内产生一个“8”字型赛道障碍物间距值。
重物块从距小车底板400mm 的高处下落,带动主动轴转动,使小车运动,再通过齿轮传动和转向结构,实现在转动一定周期时,小车进行方向的改变,从而实现8 字的运动轨迹。
通过对命题的分析,我们小组有了一个比较清晰的思路。
我们在网上搜集资料,对每个结构的各种方案进行了比较,再结合我们的实际情况和自己想法,最后确定了以下结构。
对于各种参数的确定,我们只要是对齿轮进行了计算,其他参数是在原有的基础上进行了修改。
在设计过程中,我们主要采用了Auto CAD、Solidworks 软件进行辅助设计。
车架受力小,精度要求低,考虑到铝板密度小,强度对于小车也足够,而且方便加工,故本次制作选择3mm 厚铝板。
由于我们是后轮单轮驱动,前导向轮与驱动轮的横向距离过大会使小车在绕行8 字时轨迹不对称, 即一个圆大一个圆小。
为避免这种情况我们将驱动轮与导向轮的横向距离取消。
原动机构是把重物的重力势能转化为小车动能的装置.要求1。
驱动力适中,不至于小车转弯时速度过大倾翻.2.启动时提供足够的加速度使小车开始行走.3.到达终点时的速度要尽可能小,避免对小车过大的冲击. 同时使重块的动能尽可能的转化到驱动小车前进上,如果重块竖直方向的速度较大,不仅浪费了重物的动能,下落时对车架的冲击还会影响小车的运动。
无碳小车设计方案1
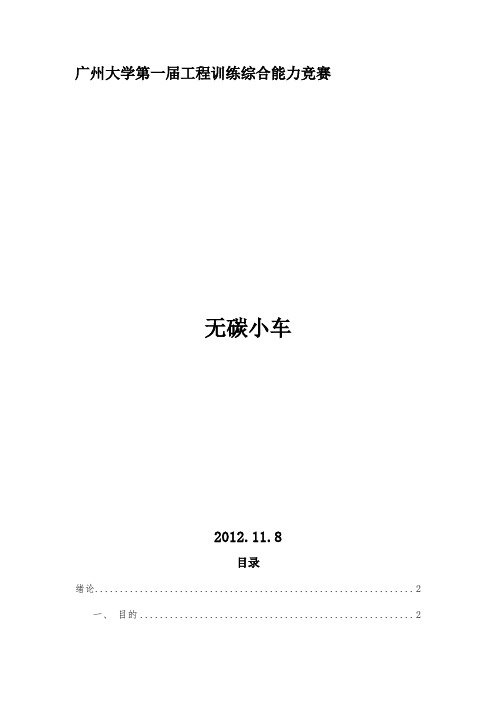
对于微调机构,我们小组提出了:
a.螺母b.键槽
但是对于我们小车的调整,我们认为键槽的可调性更大,更方便于我们在测试小车时的调整,以及使我们的调整空间更大。
技术设计
一、建立数学模型与参数确定:
1.运动学分析模型:
建立坐标系,小车的移动轨迹为余弦函数:
微分求的小车一个周期行走路程为:
,
,经测量,得到路程大概数值为2500mm左右。
1.竞赛主题:
本届竞赛主题为“无碳小车越障竞赛”。
要求经过一定的前期准备后,在比赛现场完成一套符合本命题要求的可运行装置,并进行现场竞争性运行考核。
2.竞赛命题:以重力势能驱动的具有方向控制功能的自行小车
设计一种小车,驱动其行走及转向的能量是根据能量转换原理,由给定重力势能转换来的。给定重力势能为4焦耳(取g=10m/s2),竞赛时统一用质量为1Kg的重块(¢50×65 mm,普通碳钢)铅垂下降来获得,落差400±2mm,重块落下后,须被小车承载并同小车一起运动,不允许从小车上掉落。图1为小车示意图。
一、车架
车架不用承受很大的力,精度要求低。考虑到重量加工成本等,车架采用铝板加工制作成。其中三角形结构紧凑但不能携带落下的重物、矩形结构平稳但材料浪费且增加小车自重,而三角形和矩形综合能汇集三角形和矩形的优点同时又避免了主要缺点,因此选用三角形和矩形综合型。
二、原动机构
原动机构的作用是将重块的重力势能转化为小车的驱动力。小车对原动机构还有其它的具体要求。1.驱动力适中,不至于小车拐弯时速度过大倾翻,或重块晃动厉害影响行走。2.到达终点前重块竖直方向的速度要尽可能小,避免对小车过大的冲击。同时使重块的动能尽可能的转化到驱动小车前进上,如果重块竖直方向的速度较大,重块本身还有较多动能未释放,能量利用率不高。3.由于不同的场地对轮子的摩擦摩擦可能不一样,在不同的场地小车是需要的动力也不一样。在调试时也不知道多大的驱动力恰到好处。因此原动机构还需要能根据不同的需要调整其驱动力。4.机构简单,效率高。而带轮和链轮适用于电机作为动力的机构中。基于以上分析我们选择绳轮式原动机构
无碳小车s设计方案

无碳小车s设计方案设计方案:无碳小车S一、设计目标无碳小车S是一款以环保、节能为主题的城市代步工具,旨在提供方便快捷的交通解决方案,减少对环境的污染。
设计目标如下:1. 零排放:采用电动驱动方式,完全不产生尾气排放。
2. 高效节能:优化电池储能和动能回收技术,提高能源利用效率,延长续航里程。
3. 运行稳定:采用先进的智能控制系统和安全装置,确保车辆运行的稳定性和安全性。
4. 美观舒适:外观设计简洁大方,内部空间宽敞舒适,提供良好的驾乘体验。
二、设计要点及解决方案1. 动力系统:采用纯电动驱动方式,利用电池存储能量供给电机驱动车辆。
同时,结合动能回收技术,在制动过程中将动能转化为电能,提高能源利用效率和续航里程。
2. 能量储存系统:选择高能量密度、长循环寿命的锂离子电池,提供稳定可靠的能量供应。
3. 智能控制系统:借助先进的智能控制系统,实现对电动机的精准控制和能源管理。
系统能够根据车辆运行状况、车速、路况等数据,动态调整电机转速和功率输出,提高驾驶性能和能源利用效率。
4. 安全装置:配备智能制动系统、防抱死系统、车辆稳定控制系统等装置,提高车辆的稳定性和行驶安全性。
同时,还应配备侧面碰撞保护、主动安全预警系统等装置,提高车辆的被动安全性。
5. 外观设计:外观简约、流线型设计,减少气动阻力,提高行驶稳定性和驾驶舒适性。
选用高强度轻量化材料,提升车辆的安全性和能耗效率。
三、市场应用前景和竞争优势1. 市场应用前景:随着环保意识的提升和城市交通拥堵问题的日益突出,无碳小车S作为一种绿色、环保的交通工具,具有广阔的市场应用前景。
可以在城市内提供便捷的短途出行解决方案,满足人们的日常出行需求。
2. 竞争优势:(1) 零排放设计,符合环保理念;(2) 高效节能的动力和能源管理系统,延长续航里程;(3) 先进的智能控制系统和安全装置,提高车辆的安全性和稳定性;(4) 简洁大方的外观设计和舒适宽敞的内部空间,提供良好的驾乘体验。
8无碳小车设计方案

8无碳小车设计方案
无碳小车设计方案
无碳小车是一种环保、高效的交通工具,它不使用燃油,减少了污染物的排放,同时也不会释放二氧化碳等温室气体。
本文将介绍一种基于太阳能的无碳小车设计方案。
太阳能发电系统:该无碳小车将配备太阳能发电系统,由太阳能电池板吸收太阳能转化为电能供电。
太阳能电池板将安装在车辆的顶部,可以充分吸收阳光,并将电能储存于电池中。
节能驱动系统:无碳小车将采用电动驱动系统,以减少能量的浪费。
电机将由电池供电,通过驱动电机控制车轮的旋转,从而推动车辆运行。
相比传统燃油驱动的车辆,电动驱动无碳小车具有更高的能量利用效率。
轻量化设计:无碳小车将采用轻量化设计,通过使用轻质材料制造车身和车轮,减少车辆自重,从而降低能量消耗。
同时,轻量化设计还可以提高车辆的机动性和操控性,提高整车性能。
智能控制系统:无碳小车将配备智能控制系统,通过传感器和控制器实现车辆的智能控制。
通过实时监测车辆的速度、行驶状况和能量消耗,智能控制系统可以进行优化调整,提高整车能效。
能量回收系统:无碳小车将配备能量回收系统,通过制动能量回收和车身振动能量回收等方式,将能量回收并转化为电能存
储于电池中。
能量回收系统可以提高整车的能量利用效率,减少能量浪费。
综上所述,基于太阳能的无碳小车设计方案包括太阳能发电系统、节能驱动系统、轻量化设计、智能控制系统和能量回收系统。
该设计方案既减少了能源的消耗,又减少了污染物的排放,达到了环保的目的。
未来,随着太阳能技术和电动驱动技术的进一步发展,无碳小车将成为一种主流的交通工具。
无碳小车8型设计方案

无碳小车8型设计方案
设计方案:
1. 设计理念:
- 采用无碳能源驱动,以减少对环境的污染。
- 紧凑型设计,方便通行于繁忙的城市道路。
- 注重安全性和舒适性,提供稳定的行驶和乘坐体验。
2. 外观设计:
- 车身外观简洁大方,利用轻质材料以提高车辆的能效。
- 采用流线型设计,减少空气阻力,提高行驶稳定性。
- 前脸设计简洁大方,装饰细节减少以提高能效。
3. 动力系统:
- 采用纯电动驱动,使用可充电电池作为能源。
- 采用高效电机,提供强劲动力并减少能源消耗。
- 车辆配备能源回收系统,通过制动时的能量回收降低能源浪费。
4. 内部空间设计:
- 设计舒适的座椅和腿部空间,以提供良好的乘坐体验。
- 提供足够的储物空间,满足日常旅行的需求。
- 具备智能控制系统,方便驾驶员操作车辆和乘客享受智能化服务。
5. 安全性设计:
- 配备多功能驾驶辅助系统,包括自动刹车、车道保持辅助等,提高驾驶的安全性。
- 采用坚固的车身结构和安全气囊系统,提供乘客更高的安全保护。
- 配备智能安全监测系统,实时监测车辆周围环境,避免潜在危险。
6. 其他特点:
- 具备智能导航系统,提供最短、最佳的路线规划,减少行驶时间和能源消耗。
- 安装太阳能充电板,利用太阳能为车辆充电以增加能源来源。
- 提供无线充电功能,方便用户随时充电。
以上是一个无碳小车8型的设计方案,综合考虑了环保性能、外观设计、动力系统、内部空间、安全性、智能化等多个方面的要求。
无碳小车结构设计报告_4

无碳小车结构设计报告一、设计概述根据题目要求,为达到“8”字绕行的目的,无碳小车应实现两个功能:重力势能的转换和周期性的转向。
据此可以将小车分为驱动机构和转向机构两部分。
驱动机构要求能量损耗小、传动比准确,优先选用齿轮机构。
转向机构因为轨迹重复性要求高,采用齿轮和拉杆结合控制前轮转向来满足小车走周期性“8”字要求。
二、设计方案1.小车以钢板做的底板为主体,上面安装三根吊挂重物的立杆。
2.使用滑轮机构将重块的能量通过细绳以转矩的形式传递到输入轴。
3.输入轴通过一级齿轮传动将能量传到驱动轴,带动驱动轮并驱使小车向前运动。
4.输入轴转动一圈,带动转动的大齿轮转动四分之一,使与之啮合的小齿轮转动二分之一,用连杆机构链接,使前轮走了一个圆时实现转向,从而小车走了“8”字形运动。
三、相关计算驱动机构转向齿轮(控制方向)转向机构(控制周期)1主动轮2驱动轮3主动轮4从动轮传动比2.5:1传动比1:2 主要零件尺寸:前轮半径后轮半径驱动1半径驱动2半径转向3半径转向4半径转向1半径转向2半径5mm 50mm 35mm 14mm 35mm 14mm 30mm 30mm厚度为10mm 厚度为6mm 设为转角30度,两个障碍物的距离为300毫米:设为小车的轨迹半径为x,则150*150-75*75=16875,对其开方约得130毫米。
由此可知,小车的轨迹为3.14*2*130*2=1632.8毫米,车轮要转5圈,所以轴的周长为2毫米才能保证小车在理论上转了8圈。
四、整体装配图五、作品创意1.优化各零件布局,降低小车重心2.三根立杆防止小车运行中重块摞动3. 不用其它额外的传动装置,直接由动力轴驱动轮子和转向机构,此种方式效率高、结构简单。
在不考虑其它条件时这是最优的方式。
4.曲柄连杆面积所受压力较小,且面接触便于润滑,故磨损减小,制造方便,已获得较高精度;两构件之间的接触是靠本身的几何封闭来维系的,它不像凸轮机构有时需利用弹簧等力封闭来保持接触5.小车机构简单,单级齿轮传动,损耗能量少六、心得与体会在设计无碳小车的环节中,我们在此过程当中反复探索、不断前进。
无碳小车—结构设计方案5页

㈠无碳小车设计思路根据本届竞赛题目对无碳小车(以下简称:小车)功能设计、徽标设计的要求,我们首先确定如下的设计思路:1、根据能量守恒定律,物块下落的重力势能直接转化为小车前进的动能时,能量损失最少,所以小车前进能量来源直接由重物下落过程中减少的重力势能提供为宜。
2、根据小车功能设计要求(小车在前行时能够自动避开赛道上设置的障碍物),小车前进的路线具有一定的周期性;考虑到小车转向时速度有损失,小车前进的线路是命题设计要求的最优解。
3、结构的设计与成本分析、加工工艺设计统筹考虑,力求产品的最优化设计。
4、徽标反映本届竞赛主题:无碳小车㈡无碳小车设计方案以下是具体的设计方案介绍:一、徽标设计(图1)图1(1)设计说明:整个徽标是一个椭圆形的圈,包围着一个车轮,车轮下面写着“No Carbon”的字样。
其中,车轮代表着我们所做的无碳小车。
其后面是由众多抽象的“S”形条纹组成,代表着我们的无碳小车由所要求的“S”形跑到飞驰而出。
其下的“No Carbon”字样简单明了地说明了这届大赛的主题,并且外面的椭圆圈,代表着能量的意识,说明了势能与动能相互转换的过程。
最后,以整体上看,整个图形像一只眼睛。
看着远方,对未来全球实现无碳充满希望。
(2)材料:45钢(3)制作:激光打标机喷漆外圈红色R:255 G:0 B:0 内圈红色R:170 G:0 B:0 “No”R:85 G:85 :B::85 “Carbon”R:170 G:0 B:0车轮R:255 G:85 B:85 “S”R:255 G:85~170 B:0~85二、小车动力、动力—转向、转向系统1、小车的动力系统(图2)(1)方案:根据竞赛命题要求(小车前行过程中完成的所有动作所需的能量均重物损失最少,所以以绳拉力为动力为宜。
拉力作用于锥型原动轮(以下简称:原动轮)上,形成力矩,力矩对该原动轮产生转动效应,通过一系列齿轮的传动,将动力输出,使后轮转动,小车前进。
无碳小车 设计方案

设计方案说明书
一、能量转换设计方案
将给定的重力势能通过滑轮组合等转化为小车所需要的能量。
首先,通过滑轮的配合保证小车的动力来源以及速度的稳定。
重物与定滑轮1连接,通过定滑轮2与皮带轮3连接(绳缠绕在皮带轮上),皮带轮3固定在小车车轴上。
当重物下落时,重力势能通过滑轮组带动皮带轮运动,从而使车轮转动,具体情况如下图所示:
图一小车能量转换示意图
二、运动方向设计方案
利用凸轮机构来控制小车的前进方向,以躲避障碍物。
在小车前进过程中,为躲避障碍物需走S型路线,这就需要在小车行走过程中,在特定的位置改变小车的前进方向,通过一组凸轮机构即可实现小车的转弯。
车轴带动凸轮1转动,然后将运动轨迹通过导杆2 传递给滑块3,滑块3带动车轴4运动(车轴4做周期性摆动),从而达到小车改变方向的目的。
图二小车运动方向改变示意图。
- 1、下载文档前请自行甄别文档内容的完整性,平台不提供额外的编辑、内容补充、找答案等附加服务。
- 2、"仅部分预览"的文档,不可在线预览部分如存在完整性等问题,可反馈申请退款(可完整预览的文档不适用该条件!)。
- 3、如文档侵犯您的权益,请联系客服反馈,我们会尽快为您处理(人工客服工作时间:9:00-18:30)。
大学机械设计制造及其自动化特色专业实践报告设计项目:工业产品力学分析实践、工业产品材料分析与设计实践班级:实践小组名称:报告撰写人:提交日期:2012/6/17大学机电工程系目录1 设计任务 (4)1.1无碳小车整体动力学分析报告 (4)1.2无碳小车各构件材料力学性能分析报告 (4)1.3无碳小车典型零件材料组织分析 (4)2 设计过程 (4)2.1 机构设计 (4)2.2 机构简图分析 (5)2.2.1主要机构组成 (5)2.2.2原理 (5)2.2.3自由度分析 (5)2.3 机构立体图分析 (6)2.3.1车架 (8)2.3.2原动机构 (8)2.3.3转向机构 (8)2.3.4行走机构 (9)2.4 参数分析模型 (9)2.4.1 动力学分析模型 (9)2.4.2运动学分析模型 (10)2.4.3急回运动特性、传动角、死点分析 (11)2.4.4灵敏度分析模型 (12)2.4.5参数确定 (13)2.5零部件设计 (13)3设计结果与总结 (14)4参考文献 (14)附:Matlab编程源代码 (15)1 设计任务1.1无碳小车整体动力学分析报告含无碳小车各机构运动学分析(运动轨迹计算、机构各构件长度尺寸确定等)无碳小车动力学分析,各运动副摩擦分析、各构件受力分析。
要求Matlab编程计算(附源代码)1.2无碳小车各构件材料力学性能分析报告含各构件强度分析、刚度分析基于结构安全的无碳小车各构件结构优化方案。
要求Matlab编程计算(附源代码)1.3无碳小车典型零件材料组织分析取无碳小车中典型金属材料进行材料组织分析,给出3种以上材料试样制作方法、组织照片等。
2 设计过程2.1 机构设计行进动作分解小车主要由四个机构组成:发条动力机构、齿轮传动机构、曲柄连杆机构、连杆前轮转向机构。
2.2.1主要机构组成机构由曲柄1和连杆2、滑块C 组成的曲柄连杆机构(一下简称R )、连杆3和连杆4组成,共5个活动构件。
2.2.2原理传动齿轮A 在发条带动下作顺时针旋转运动,一方面通过车轴带动驱动后轮前进,另一方面通过曲柄连杆机构带动转向“连杆4”,从而带动小车有规律地左右摇摆,实现小车前进过程中自动转弯的效果。
2.2.3自由度分析a)自由度分析的必要性:通过自由度分析可以知道机构的运动受到了多少约束,这样在画简图的时候,就可以知道机构的运动方式了。
约束不足或约束多了,机构都不能提供正常的运动。
例如死机构等,所以对设计进行自由度的分析是作为制造的前条件。
b)自由度计算:总共有5个活动构件:曲柄连杆机构R (曲柄1、连杆2、滑块C )、杆3、杆4。
有7个低副 :机构中ABCDE 为转动副。
构件CD 为移动副。
有0个高副所以,自由度F=3*5-(2*7+0)=1我们的势能小车只有唯一的原动件齿轮7,我们通过计算得出小车的自由度为1,所以能够保证小车具有确定的运动。
AB2CDE143前轮转弯机构D大图曲柄连杆机构R大图2.3.1车架车架不用承受很大的力,精度要求低。
考虑到重量加工成本等,车架采用木材加工制作成三角底板式。
可以通过回收废木材获得,已加工。
2.3.2原动机构原动机构的作用是将发条的弹性势能转化为小车的驱动力。
能实现这一功能的方案有多种,就效率和简洁性来看齿轮最优。
小车对原动机构还有其它的具体要求。
1.驱动力适中,不至于小车拐弯时速度过大倾翻,或重块晃动厉害影响行走。
2.到达终点前重块竖直方向的速度要尽可能小,避免对小车过大的冲击。
同时使发条的动能尽可能的转化到驱动小车前进上,如果重块竖直方向的速度较大,发条本身还有较多动能未释放,能量利用率不高。
3.由于不同的场地对轮子的摩擦摩擦可能不一样,在不同的场地小车是需要的动力也不一样。
在调试时也不知道多大的驱动力恰到好处。
因此原动机构还需要能根据不同的需要调整其驱动力。
4.机构简单,效率高。
2.3.3转向机构转向机构是本小车设计的关键部分,直接决定着小车的功能。
转向机构也同样需要尽可能的减少摩擦耗能,结构简单,零部件已获得等基本条件,同时还需要有特殊的运动特性。
能够将旋转运动转化为满足要求的来回摆动,带动转向轮左右转动从而实现拐弯避障的功能。
能实现该功能的机构有:凸轮机构+摇杆、曲柄连杆+摇杆、曲柄摇杆、差速转弯等等。
其中本小车中采用曲柄连杆+摇杆机构优点:运动副单位面积所受压力较小,且面接触便于润滑,故磨损减小,制造方便,已获得较高精度;两构件之间的接触是靠本身的几何封闭来维系的,它不像凸轮机构有时需利用弹簧等力封闭来保持接触。
缺点:一般情况下只能近似实现给定的运动规律或运动轨迹,且设计较为复杂;当给定的运动要求较多或较复杂时,需要的构件数和运动副数往往比较多,这样就使机构结构复杂,工作效率降低,不仅发生自锁的可能性增加,而且机构运动规律对制造、安装误差的敏感性增加;机构中做平面复杂运动和作往复运动的构件所长生的惯性力难以平衡,在高速时将引起较大的振动和动载荷,故连杆机构常用于速度较低的场合。
在本小车设计中由于小车转向频率和传递的力不大故机构可以做的比较轻,可以忽略惯性力,机构并不复杂,利用MATLAB 进行参数化设计并不困难,加上个可以利用轴承大大减小摩擦损耗提高效率。
对于安装误差的敏感性问题我们可以增加微调机构来解决。
2.3.4行走机构行走机构即为三个轮子,轮子又厚薄之分,大小之别,材料之不同需要综合考虑。
有摩擦理论知道摩擦力矩与正压力的关系为:δ⋅=N M对于相同的材料δ为一定值。
而滚动摩擦阻力RN RM f δ⋅==,所以轮子越大小车受到的阻力越小,因此能够走的更远。
但由于加工问题材料问题安装问题等等具体尺寸需要进一步分析确定。
2.4 参数分析模型2.4.1 动力学分析模型 a 、驱动驱动轮受到的力矩M A ,曲柄轮受到的扭矩M 1,N A 为驱动轮A 受到的压力,F A 为驱动轮A 提供的动力,有221λ⋅=+M i MM A (其中2λ是考虑到摩擦产生的影响而设置的系数)R F N M A A A ⋅+⋅=δb 、转向假设小车在转向过程中转向轮受到的阻力矩恒为M C ,其大小可由赫兹公式求得,)11(1222121E E R B N cc c μμπσ-+-⋅=bB N c c 2⋅⋅=σ由于b 比较小,故241bBM c c μσ=对于连杆的拉力F C ,有lr c 11sin 2sin θθ⋅=21cos )cos 1(arcsin2c c l c θααπθ⋅-⋅--=12sin cos c c c c c F M θθ⋅⋅⋅=)sin(21c c c F M θθ+⋅⋅=c 、小车行走受力分析设小车惯量为I ,质心在则此时对于旋转中心O ’ 的惯量为I ’])[(2321a a m I I A +-+='ρ(平行轴定理))()(21221a a RN d a r N F I A B A c c A A --⋅-+-⋅⋅-⋅=⋅'ρδρδρα小车的加速度为:A A a ρδ⋅=2r aR a A =2.4.2运动学分析模型a 、驱动:当驱动轴(曲柄)转过的角度为2θd ,则有22r dh d =θ则曲柄轴(轴1)转过的角度i d d 21θθ=小车移动的距离为(以A 轮为参考)2θd R ds ⋅=b 、转向:当转向杆与驱动轴间的夹角α为时,曲柄转过的角度为1θ则α与1θ满足以下关:()()1221211222cos sin sin cos 1θθαα⋅+⋅-⋅++-⋅=r r c b c l解上述方程可得1θ与α的函数关系式()1θαf =c 、小车行走轨迹只有A 轮为驱动轮,当转向轮转过角度α时,则小车转弯的曲率半径为1tan a b+=αρ小车行走ds 过程中,小车整体转过的角度ρβdsd =当小车转过的角度为β时,有⎩⎨⎧⋅=⋅-=ββcos sin ds dy ds dx为求解方程,把上述微分方程改成差分方程求解,通过设定合理的参数得到了小车运动轨迹2.4.3急回运动特性、传动角、死点分析急回运动特性:曲柄摇杆机构中,曲柄虽作等速转动,而摇杆摆动是空回行程的平均速度却大于工作行程的平均速度。
急回特性是连杆机构重要的运动特性,其急回运动的程度通常用行程速比系数来衡量。
在曲柄连杆滑块机构中,推程传动角γ的大小是表示机构传动效率高低、传动性能优劣的一个重要参数。
所以,如何在保证运动要求的前提下,获得优良的传动性能,就是设计的目的。
死点指的是机构的传动角γ=0,这时主动件会通过连杆作用于从动件上的力恰好通过其回转中心,所以出现了不能使构件AB 即从动件转动的顶死现象,机构的这种位置称为死点。
设滑块的行程速比系数K 、滑块的冲程H ,曲柄的长度a 和连杆的长度b 。
根据作图法设计原理可得: 极位夹角θ=180°(K -1)/(K+1)在△AC 1C 2中有:H 2=(b+a)2+(b-a)2-2(b+a)(b-a)cosθ整理得: )cos 1(2)cos 1(2b 22θθ-+-=a H (1)由上述几何关系可见,在已知K(已知θ)和H 的情况下,对应曲柄的某一长度a ,机构的其它几何尺寸b 可确定。
其中曲柄的转角为Ф=+︒180θ对应着机构的推程,即为推程运动角。
而曲柄的转角Ф=θ-︒180则对应着机构的回程,即回程运动角。
极限位置11C AB 和22C AB 分别为推程的起始位置和终止位置。
如图所示21AC C ∠0≠,所以机构有急回作用,此时行程速度变化系数为K=θθ-︒÷+︒180180当机构以曲柄AB 为原动件时,从动件滑块与BC 所夹的锐角即为传动角,其最小传动角将出现在曲柄AB 垂直机架的位置。
即ABC ∠推程最小传动角min γ必出现推程起始位置11C AB 或曲柄滑块路程近垂直位置ABC 时 当以曲柄AB 为原动件时,因为机构的最小传动角min γ≠0,所以机构无死点位置。
但当以滑块为主动件时,因为机构从动件曲柄AB 与BC 存在两处共线位置,故有两个死点位置。
本机构AB 为原动件,所以无死点位置 2.4.4灵敏度分析模型A B2CDE143小车一旦设计出来在不改变其参数的条件下小车的轨迹就已经确定,但由于加工误差和装配误差的存在,装配好小车后可能会出现其轨迹与预先设计的轨迹有偏离,需要纠正。
其次开始设计的轨迹也许并不是最优的,需要通过调试试验来确定最优路径,着同样需要改变小车的某些参数。
为了得到改变不同参数对小车运行轨迹的影响,和指导如何调试这里对小车各个参数进行灵敏度分析。
通过MATLAB编程得到幅值周期方向i -0.0117 -0.09158 528.135b 176.5727 -35.3795 578.82R -0.3163 16.39132 528.1437a1 1.465469 -0.27592 528.5547曲柄半径r1 23.71445 -18.9437 535.3565d 0.040819 -117.738 528.1465转向杆的长-1.63769 3.525236 527.5711连杆长度-176.955 -196.268 477.35612.4.5参数确定单位:mm转向轮与曲柄轴轴心距 b=150;摇杆长c=60;驱动轮直径D=35;驱动轮A与转向轮横向偏距a1=70驱动轮B与转向轮横向偏距a2=70;驱动轴与转向轮的距离d=127;曲柄长r1=132.5零部件设计需加工的零件:a.驱动轴6061空心铝合金管。