内孔加工的对刀操作与输入
《模具零件数控加工技术》课程标准

《模具零件数控加工技术》课程标准课程代码020******* 课程类别专业课程课程类型理实一体课程课程性质必修课程课程学分6学分课程学时96学时修读学期第4学期适用专业模具设计与制造合作开发企业一汽模具制造有限公司执笔人刘宏伟、吴宇飞审核人李玉青1.课程定位与设计思路1.1课程定位本课程是模具设计与制造专业核心课程,专业必修课程。
其功能是通过加工项目训练方式,采取任务驱动的方法培养学生实施模具零件数控加工的能力。
本课程与前修课程识图与制图、机械制造基础、冲压模具设计与制造、模具零件普通机械加工技术、模具零件普通加工工艺制定与实践课程相衔接,共同培养学生模具制造的能力;与后续课程模具CAD/CAE/CAM一体化技术、模具零件数控铣加工工艺制定、编程与实践、模具设计与制造综合实训、就业综合培训、顶岗实习等课程相衔接,共同培养学生模具具设计与制造能力及岗位工作能力。
1.2设计思路通过对本专业模具数控加工、模具生产制造管理等工作岗位分析,确定了课程的设计思路为:以模具零件数控加工工艺实施能力的培养为中心,以典型的模具零件为课程教学实施载体,通过导柱、导套、凸模、凹模、固定板的加工项目训练,使学生能够独立完成机床生产准备,根据加工工艺编制程序,完成程序调用,能够选择合理的工件安装方式,完成工件安装和拆卸,完成零件的数控加工。
以工作过程导向设计课程教学,以任务驱动、问题引导、角色扮演、团队协作等方式实施教学,以过程考核、成果考核相结合的形式实施课程考核。
参考学时:96学时,参考学分:6学分。
2.课程目标通过本课程学习,使学生具备合理安排模具零件数控加工工序的能力,具备对较复杂零件进行数控加工工艺处理的能力,熟悉编程前数学处理的目的和基本方法;具有对轮廓加工,简单型面加工的数控程序手工编制能力,具备使用常用软件完成自动编程能力。
2.1能力目标(1)能够胜任企业数控编程岗位和数控机床操作岗位。
(2)能够合理确定走刀路线、正确选用切削用量和常用刀具。
对刀的方法

以下内容只有回复后才可以浏览一、对刀对刀的目的是确定程序原点在机床坐标系中的位置,对刀点可以设在零件上、夹具上或机床上,对刀时应使对刀点与刀位点重合。
数控车床常用的对刀方法有三种:试切对刀、机械对刀仪对刀(接触式)、光学对刀仪对刀(非接触式),如图 3-9 所示。
1、试切对刀1 )外径刀的对刀方法如图 3-10 所示。
Z 向对刀如 (a) 所示。
先用外径刀将工件端面 ( 基准面 ) 车削出来;车削端面后,刀具可以沿 X 方向移动远离工件,但不可 Z 方向移动。
Z 轴对刀输入:“ Z0 测量”。
X 向对刀如 (b) 所示。
车削任一外径后,使刀具 Z 向移动远离工件,待主轴停止转动后,测量刚刚车削出来的外径尺寸。
例如,测量值为Φ 50.78mm, 则 X 轴对刀输入:“ X50.78 测量”。
2 )内孔刀的对刀方法类似外径刀的对刀方法。
Z 向对刀内孔车刀轻微接触到己加工好的基准面(端面)后,就不可再作 Z 向移动。
Z 轴对刀输入:“ Z0 测量”。
X 向对刀任意车削一内孔直径后,Z 向移动刀具远离工件,停止主轴转动,然后测量已车削好的内径尺寸。
例如,测量值为Φ 45.56mm, 则 X 轴对刀输入:“ X45.56 测量”。
3 )钻头、中心钻的对刀方法如图 3-11 所示。
Z 向对刀如( a )所示。
钻头 ( 或中心钻 ) 轻微接触到基准面后,就不可再作 Z 向移动。
Z 轴对刀输入:“ Z0 测量”。
X 向对刀如( b )所示。
主轴不必转动,以手动方式将钻头沿 X 轴移动到钻孔中心,即看屏幕显示的机械坐标到“ X0.0 ”为止。
X 轴对刀输入:“ X0 测量”。
2、机械对刀仪对刀将刀具的刀尖与对刀仪的百分表测头接触,得到两个方向的刀偏量。
有的机床具有刀具探测功能,即通过机床上的对刀仪测头测量刀偏量。
3、光学对刀仪对刀将刀具刀尖对准刀镜的十字线中心,以十字线中心为基准,得到各把刀的刀偏量。
二、刀具补偿值的输入和修改根据刀具的实际参数和位置,将刀尖圆弧半径补偿值和刀具几何磨损补偿值输入到与程序对应的存储位置。
第七课 数车内孔、内腔和套类零件加工(理论讲解)
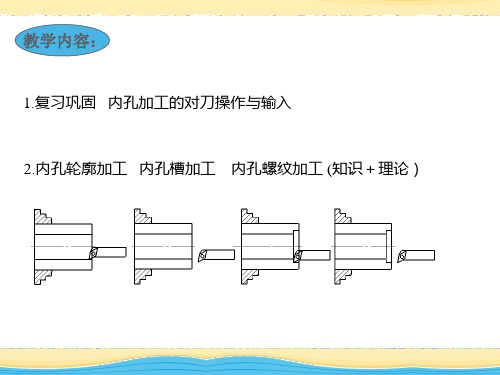
7.孔的精度 套类零件的精度有下列几个项目。
(1)孔的位置精度。 同轴度(孔之间或孔与某些表面间的尺寸精度)、平 行度、垂直度、径向圆跳动和端面圆跳动等。
铰孔是对较小和未淬火孔的精加工方法之一,在成批生
产中已被广泛采用。铰孔之前,一般先镗孔,镗孔后留些 余量,一般粗铰为0.15mm~0.3mm,精铰为0.04mm~ 0.15mm,余量大小直接影响铰孔的质量。
4.孔加工方法的选择 在车床中,孔的加工方法与孔的精度要求、孔径以及
孔的深度有很大的关系。一般来 讲,在精度等级为IT12、 IT13时,一次钻孔就可以实现。在精度等级为IT11,孔径 ≤10mm时,采用一次钻孔方式;当孔径>10~30mm时, 采用钻孔和扩孔方式;孔径>30~80mm时,采用钻孔、扩 钻、扩孔刀或车刀镗孔方式。在精度等级为ITl0、IT9,孔 径≤10mm时,采用钻孔以及铰孔方式;当孔径 >10~30mm时,采用钻孔、扩孔和铰孔方式;孔径 >30~80mm时,采用钻孔、扩孔、铰孔、或者用扩孔刀镗 孔方式。在精度等级为IT8、IT7,孔径≤10mm时,采用钻 孔及一次或二次铰孔方式;当孔径>10~30mm时,采用钻 孔、扩孔、一次或二次铰孔方式;当孔径>30~80mm时, 采用钻孔、扩钻(或者用扩孔刀镗孔)以及一次或二次铰孔 方式。
如出现Z方向的误差,则其修整办法相同。
二、内孔、内腔和套类零件(知识+理论)
课题一 盲孔零件的加工
本课题要求编程并加工如图6.1所示盲孔零件,毛 坯为φ53mm×100mm的棒料,材料为45钢。
a)零件图 b)实体图 图6.1 盲孔零件
一、基础知识 1.孔加工特点 (1)孔加工是在工件内部进行的,观察切削情况比较困 难,尤其是小孔、深孔更为突出。
简述对刀操作步骤

简述对刀操作步骤简述对刀操作步骤对刀是工业生产中非常重要的一项操作,它是保证加工精度和生产效率的关键。
下面将详细介绍对刀操作步骤。
一、准备工作1.检查设备:首先需要检查设备是否正常运转,如主轴、夹头、定位装置等是否有异常情况。
2.清洁设备:清洁主轴、夹头、定位装置以及刀具等部件,确保没有油污或异物附着。
3.选择合适的刀具:根据加工件的要求选择合适的刀具,并检查其尺寸和磨损情况。
4.安装夹具:根据加工件的形状和尺寸选择合适的夹具,并正确安装在设备上。
二、调整主轴1.卸下旧刀具:用专门的扳手卸下旧刀具,并将其放到指定位置。
2.清洁主轴锥孔:用干净的布擦拭主轴锥孔,确保没有油污或异物附着。
3.安装新刀具:将新刀具插入主轴锥孔中,并用扳手紧固螺母,注意不要过紧或过松。
4.调整刀具位置:将新刀具调整到正确的位置,保证其与工件接触面垂直或倾斜角度正确。
5.检查刀具偏心:用专门的测量工具检查刀具是否偏心,如有偏心情况需要进行调整。
三、校正夹具1.固定加工件:将加工件放置在夹具上,并用螺丝或卡子固定住。
2.校正夹具:用专门的测量工具检查夹具是否水平或垂直,如有不平情况需要进行调整。
3.调整夹紧力:根据加工件的材质和尺寸选择合适的夹紧力,并用扳手调整夹头螺丝松紧度。
四、试运行和修正误差1.试运行设备:在对刀完成后,需要进行试运行设备,并观察其运转情况和加工效果。
2.检查误差:用专门的测量工具检查加工件的尺寸和形状是否符合要求,如有误差需要进行修正。
3.修正误差:根据误差情况选择合适的方法进行修正,如重新对刀、更换刀具或调整夹头等操作。
总结对刀是加工过程中非常重要的一项操作,它直接关系到加工件的精度和生产效率。
通过以上步骤的详细介绍,相信大家已经对对刀操作有了更深入的了解,希望能够在实际生产中有所帮助。
数控内孔镗刀的对刀
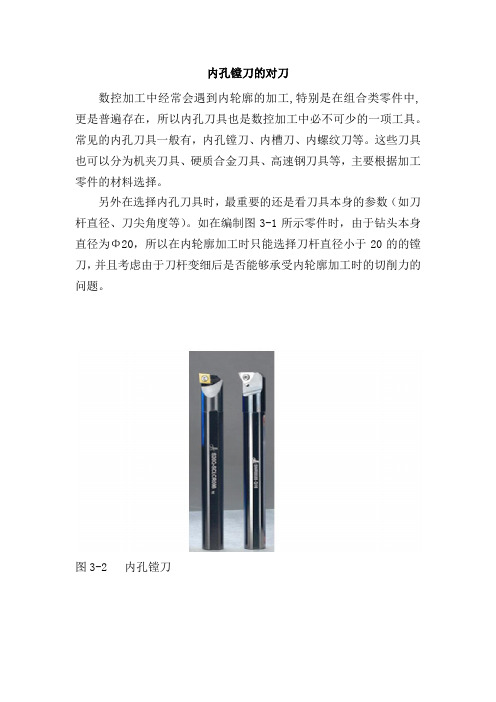
内孔镗刀的对刀数控加工中经常会遇到内轮廓的加工,特别是在组合类零件中,更是普遍存在,所以内孔刀具也是数控加工中必不可少的一项工具。
常见的内孔刀具一般有,内孔镗刀、内槽刀、内螺纹刀等。
这些刀具也可以分为机夹刀具、硬质合金刀具、高速钢刀具等,主要根据加工零件的材料选择。
另外在选择内孔刀具时,最重要的还是看刀具本身的参数(如刀杆直径、刀尖角度等)。
如在编制图3-1所示零件时,由于钻头本身直径为Φ20,所以在内轮廓加工时只能选择刀杆直径小于20的的镗刀,并且考虑由于刀杆变细后是否能够承受内轮廓加工时的切削力的问题。
图3-2 内孔镗刀图3-3 内孔镗刀图3-4 高速钢刃磨的内螺纹刀图3-5 机夹内槽刀图3-6 机夹内螺纹刀以内孔镗刀为例,阐述内孔刀具的对刀步骤:对刀原理与对外圆刀一致。
(1)手动模式下,试切工件内圆;(图形示意作了放大处理)图3-7 试切内圆(2)刀具沿Z方向退出,保持X坐标不变;(3)测量试切内轮廓直径,记为ρ,按“OF FSETSETTING”键(参数输入),→进入“补正”→“形状”→“测量”补偿参数设定界面→将光标移到与刀位号相对应的番号下(如:G001,代表一号刀具),输入X ρ,点击“测量”键确定输入值。
X方向对刀完毕。
(4)试切工件端面,刀具沿X方向退出,保持Z坐标不变;(图形示意作了放大处理)图3-8 试切端面(5)按“OF FSETSETTING”键(参数输入),→进入“补正”→“形状”→“测量”补偿参数设定界面→将光标移到与刀位号相对应的番号下(如:G001,代表一号刀具),输入Z 0,点击“测量”键确定输入值。
对刀完毕。
对刀完毕后,此时工件坐标系(编程坐标系)的原点,就设置到了端面与轴线的交点上了。
内槽刀、内螺纹刀的对刀方法与镗刀的对刀稍微有点区别,我们将在实践活动中,具体给大家描述。
840D简明教程
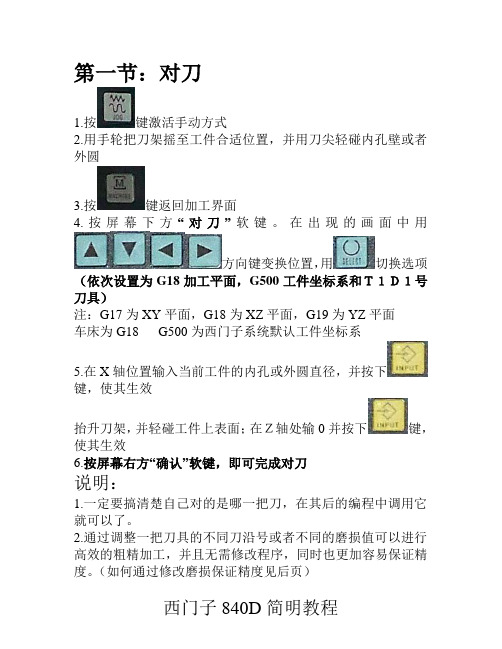
第一节:对刀1.按键激活手动方式2.用手轮把刀架摇至工件合适位置,并用刀尖轻碰内孔壁或者外圆3.按键返回加工界面4.按屏幕下方“对刀”软键。
在出现的画面中用方向键变换位置,用切换选项(依次设置为G18加工平面,G500工件坐标系和T1D1号刀具)注:G17为XY平面,G18为XZ平面,G19为YZ平面车床为G18 G500为西门子系统默认工件坐标系5.在X轴位置输入当前工件的内孔或外圆直径,并按下键,使其生效抬升刀架,并轻碰工件上表面;在Z轴处输0并按下键,使其生效6.按屏幕右方“确认”软键,即可完成对刀说明:1.一定要搞清楚自己对的是哪一把刀,在其后的编程中调用它就可以了。
2.通过调整一把刀具的不同刀沿号或者不同的磨损值可以进行高效的粗精加工,并且无需修改程序,同时也更加容易保证精度。
(如何通过修改磨损保证精度见后页)第二节:磨损值的调整与计算磨损值的意义在于它会沿+X方向或者-X方向按给定的数值发生偏移,以做到留下加工余量或者调节精度的作用。
几点常识:1.外圆应该留正的磨损值,内孔留负值2.西门子系统磨损值为单边的余量,即半径值(Fanuc为直径值)精加工磨损值的计算方法:(理想值—测量值)/2+当前磨损值=精加工磨损值范例:有一工件内径基本尺寸要求为500mm上偏差+0.06,下偏差0,预留了-0.5mm的磨损值,现测量得出实际尺寸为498.86mm,问磨损值应该改为多少?答:由提示得出此工件内孔的理想尺寸应为500.03mm,根据公式(理想值—测量值)/2+当前磨损值=精加工磨损值推出:(500.03-498.86)/2+(-0.5)=0.085所以最终磨损值应为0.085mm第三节:程序的测试与模拟西门子840D具有强大的图形仿真及交互帮助能力。
通过仿真可以检验那些没有绝对把握的程序,并可以在系统的提示下,把程序修改正确,是非常好用的功能。
在模拟环境中机床是被锁住的,但屏幕坐标照常运动,并有形象的3D模拟加工动画。
数控车床对刀步骤
数控车床对刀步骤
1. 对刀工具:0-150mm游标卡尺、三爪扳手和压刀扳手、刀具90度外圆车刀、毛坯φ50x83
2. 选择刀位:刀位要和程序对应
3. 装夹车刀:双手拧紧即可
4. 装夹工件:保证三爪的三个面与毛坯接触,伸出长度5
5.
5. 使用加力杆逐一夹紧使其毛坯受力均匀
6. Z轴对刀
7. 使用录入使主轴正转,转速500转每分钟
8. 手动方式快速移动至工件
9. 用手轮方式匀速进给平面
10. 此时沿X轴方向匀速退刀Z轴不动
11. 点击刀补按键找到相应的刀补号输入Z0.0点击输入(广数系统)或者测量(发那科系统)
12. X向对刀
13. 车削外圆长度3至5mm直径进刀1.5mm左右
14. 此时沿Z轴退刀X向不动
15. 用游标卡尺测量外圆直径
16. 在相应刀补号输入相应X值
17. 法那科系统:点击测量,广数系统:点击输入
18. 对刀验证法:点击录入输入T0101;输入G00 X54.0 Z3.0; 点击循环启动拿游标卡尺测量刀具到工件X Z向的距离对应即可.。
Fanuc系统数控车加工工艺与技能训练模块六 内孔、内腔和套类零件加工
⑤钻φ16的孔,深为30 mm; ⑥镗φ18孔,深28 mm; ⑦镗φ20孔,深30 mm; ⑧倒内孔1×45º 的倒角 ⑨切断 (3)刀具选择 ①外圆刀,设为1号刀 ②φ3 mm钻头,设为2号刀 ③切断刀,设为3号刀 ④φ16 mm钻头,设为4号刀 ⑤镗刀,设为6号刀 2.程序编制 选取工件轴线与工件右端面的交点O为工件坐标原点。 程序如下:
图6.10 塞规
9.孔加工指令 (1)G01 在数控车床上加上孔,无论是钻孔还是镗孔,都可以 用G01指令来实现。 (2)固定循环(G71、G72、G90、G94) 前面学过的外圆粗车循环(G71)、端面粗车循环 (G72)、外圆(内圆)车削循环(G90)和端面车削循 环(G94)都可以用干孔的加工。详见本课题中前面所述 “孔加工的方法”。
(a)整体式镗刀 (b)机夹式镗刀 图6.4 常用镗刀 (6)铰刀 精度要求较高的内孔,除了采用高速精镗之外, 一般是经过镗孔后用铰刀铰削。 铰刀有机用铰刀和手用铰刀2种,由工作部分、颈 和柄等组成,如图6.5所示。
(a)机用铰刀 (b)手用铰刀 图6.5 铰刀 3.孔加工的方法 (1)钻孔 钻孔前,先车平零件端面,钻出一个中心孔。 (用短钻头钻孔时,只要车平端面,不一定要钻出 中心孔)。将钻头装在车床尾座套筒内,并把尾座 固定在适当位置上,这时开动车床就可以用手动进 刀钻孔,如图6.6所示。
7.孔的精度 套类零件的精度有下列几个项目。 (1)孔的位置精度。 同轴度(孔之间或孔与某些表面间的尺寸精度)、平 行度、垂直度、径向圆跳动和端面圆跳动等。 (2)孔径和长度的尺寸精度。 (3)孔的形状精度(如圆度、圆柱度、直线度等)。 (4)表面粗糙度 要达到哪一级表面粗糙度,一般按加工图样上的规 定。 8.孔的测量 (1)内径千分尺测量 当孔的尺寸小于25mm时,可用内径术 车孔是常用的孔加工方法之一,可用作粗加工,也可用 作精加工。车孔精度一般可达IT7~IT8,表面粗糙度 Ra1.6~3.2μm。车孔的关键技术是解决内孔车刀的刚性问 题和内孔车削过程中的排屑问题。 为了增加车削刚性,防止产生振动,要尽量选择粗的刀 杆,装夹时刀杆伸出长度尽可能短,只要略大于孔深即可。 刀尖要对准工件中心,刀杆与轴心线平行。精车内孔时, 应保持刀刃锋利,否则容易产生让刀,把孔车成锥形。 内孔加工过程中,主要是控制切屑流出方向来解决排屑问 题。精车孔时要求切屑流向待加工表面(前排屑),前排屑主 要是采用正刃倾角内孔车刀。加工盲孔时,应采用负的刃 倾角,使切屑从孔口排出。
数控加工常见的对刀方法
数控加工常见的对刀方法对刀是数控加工中的主要操作和重要技能。
在一定条件下,对刀的精度可以决定零件的加工精度,同时,对刀效率还直接影响数控加工效率。
仅仅知道对刀方法是不够的,还要知道数控系统的各种对刀设置方式,以及这些方式在加工程序中的调用方法,同时要知道各种对刀方式的优缺点、使用条件等。
一、对刀原理对刀的目的是为了建立工件坐标系,直观的说法是,对刀是确立工件在机床工作台中的位置,实际上就是求对刀点在机床坐标系中的坐标。
对于数控车床来说,在加工前首先要选择对刀点,对刀点是指用数控机床加工工件时,刀具相对于工件运动的起点。
对刀点既可以设在工件上(如工件上的设计基准或定位基准),也可以设在夹具或机床上,若设在夹具或机床上的某一点,则该点必须与工件的定位基准保持一定精度的尺寸关系。
对刀时,应使指刀位点与对刀点重合,所谓刀位点是指刀具的定位基准点,对于车刀来说,其刀位点是刀尖。
对刀的目的是确定对刀点(或工件原点)在机床坐标系中的绝对坐标值,测量刀具的刀位偏差值。
对刀点找正的准确度直接影响加工精度。
在实际加工工件时,使用一把刀具一般不能满足工件的加工要求,通常要使用多把刀具进行加工。
在使用多把车刀加工时,在换刀位置不变的情况下,换刀后刀尖点的几何位置将出现差异,这就要求不同的刀具在不同的起始位置开始加工时,都能保证程序正常运行。
为了解决这个问题,机床数控系统配备了刀具几何位置补偿的功能,利用刀具几何位置补偿功能,只要事先把每把刀相对于某一预先选定的基准刀的位置偏差测量出来,输入到数控系统的刀具参数补正栏指定组号里,在加工程序中利用T指令,即可在刀具轨迹中自动补偿刀具位置偏差。
刀具位置偏差的测量同样也需通过对刀操作来实现。
二、对刀方法在数控加工中,对刀的基本方法有试切法、对刀仪对刀和自动对刀等。
本文以数控铣床为例,介绍几种常用的对刀方法。
1、试切对刀法这种方法简单方便,但会在工件表面留下切削痕迹,且对刀精度较低。
加工中心对刀方法全解!再也不用担心对刀啦
加工中心对刀方法全解!再也不用担心对刀啦1. 加工中心的Z向对刀加工中心的Z向对刀一般有以下三种方法:1) 机上对刀方法一这种对刀方法是通过对刀依次确定每把刀具与工件在机床坐标系中的相互位置关系。
其具体操作步骤如下。
(1) 把刀具长度进行比较,找出最长的刀作为基准刀,进行Z向对刀,并把此时的对刀值(C)作为工件坐标系的Z值,此时H03=0。
(2) 把T01、T02号刀具依次装在主轴,通过对刀确定A、B的值作为长度补偿值。
(此方法没有直接去测量刀具补偿,而是通过依次对刀确定的与方法三不同.)(3)把确定的长度补偿值(最长刀长度减其余刀具长度)填入设定页面,正、负号由程序中的G43、G44来确定,此时一般用G44H—表示。
当采用G43时,长度补偿为负值。
这种对刀方法的对刀效率和精度较高,投资少,但工艺文件编写不便,对生产组织有一定影响。
2) 机上对刀方法二这种对刀方法的具体操作步骤如下:(1) XY方向找正设定如前,将G54中的XY项输入偏置值,Z项置零。
(2) 将用于加工的T1换上主轴,用块规找正Z向,松紧合适后读取机床坐标系Z项值Z1,扣除块规高度后,填入长度补偿值H1中。
(3) 将T2装上主轴,用块规找正,读取Z2,扣除块规高度后填入H2中。
(4) 依次类推,将所有刀具Ti用块规找正,将Zi扣除块规高度后填入Hi中3) 机外刀具预调+机上对刀这种对刀方法是先在机床外利用刀具预调仪精确测量每把刀具的轴向和径向尺寸,确定每把刀具的长度补偿值,然后在机床上用最长的一把刀具进行Z向对刀,确定工件坐标系。
这种对刀方法对刀精度和效率高,便于工艺文件的编写及生产组织,但投资较大。
2. 对刀数据的输入(1) 根据以上操作得到的对刀数据,即编程坐标系原点在机床坐标系中的X、Y、Z值,要用手动方式输入到G54~G59中存储起来。
操作步骤如下:①按【MENU OFFSET】键。
②按光标移动键到工件坐标系G54~G59。
- 1、下载文档前请自行甄别文档内容的完整性,平台不提供额外的编辑、内容补充、找答案等附加服务。
- 2、"仅部分预览"的文档,不可在线预览部分如存在完整性等问题,可反馈申请退款(可完整预览的文档不适用该条件!)。
- 3、如文档侵犯您的权益,请联系客服反馈,我们会尽快为您处理(人工客服工作时间:9:00-18:30)。
机械制造技术《数控车加工》
Produced by Miss Xie
内孔加工的对刀操作与输入
一 二
对刀 内孔车刀的对刀方法
Produced by Miss Xie
一、对刀
对刀是数控机床加工前必需的准备工作。对刀是数控加 工中的主要操作和重要技能,在一定条件下,对刀精度可以 决定零件的加工精度,同时,对刀效率还直接影响数控加工 效率。
MEM 【磨耗】
***
***
*** 【 】
S 0 08:16:18 【 】Fra bibliotek【形状】
【(操作)】
数控车常用的对刀方法有试切对刀、机械对刀仪对刀、 光学对刀仪对刀等,数控车最常用试切对刀法进行对刀操作。 刀架转位后,各刀具的刀尖不在同一点上。对刀操作可以调 整数控车床每一把刀,将各刀的刀位点统一到同一个工件坐 标系的某个位置,使各刀尖点均能按同一工件坐标系指定的 位置移动,从而使编程时不用考虑刀具的安装位置。对刀的 目的就是确定编程原点在机床坐标系中的位置,并将对刀数 据(X、Z方向零点位置)输入到相应的存储位置,数控车床 根据程序自动计算出刀具在机床坐标系中的坐标,从而指挥 刀具运动,对刀点可以设在零件上、夹具上或机床上,对刀 时应使用对刀点与刀位点重合。试切对刀的对刀点一般在零 件上。
6.按OFSJSET键,显示画面如下所示,然后按[形状]下的软功 能键,用↑键或↓键移动光标到相应的刀号位置,如1号刀在 G01,输入“Z0”,按测量软键,完成Z方向对刀。
工具补正/形状 番号 X
G01 G02 G03 G04 G05 G06 G07 G08 0.000 0.000 0.000 0.000 0.000 0.000 0.000 0.000
工具补正/形状 番号 X G01 0.000 G02 0.000 G03 0.000 G04 0.000 G05 0.000 G06 0.000 G07 0.000 G08 0.000 O0001 Z 0.000 0.000 0.000 0.000 0.000 0.000 0.000 0.000 R 0.000 0.000 0.000 0.000 0.000 0.000 0.000 0.000 T 0 0 0 0 0 0 0 0 T0101 N00001
Produced by Miss Xie
二、内孔车刀的对刀方法
7.切削内孔,进行X方向对刀。
车刀接近工 件下屑即可
X方向进刀
切削外圆
沿X方向退刀
Produced by Miss Xie
二、内孔车刀的对刀方法
8.用卡尺或千分尺测量切削外圆直径。 9 .按OFSJSET键,显示画面下图所示,然后按[形状]下的软功 能键,用↑键或↓键移动光标到相应的刀号位置,如4号刀在 G04,输入“X直径值”,按测量软键,完成X方向对刀。
Produced by Miss Xie
二、内孔车刀的对刀方法
车刀接近工件端面
刀尖和端面重合
沿X方向退刀
移动刀具时注意控制进给速度,不能太快,还要均匀,一般 训练初期对刀用手摇方式,熟练后方可选用手动方式,当刀具 距离工件较近时,一定改为手摇方式。
Produced by Miss Xie
二、内孔车刀的对刀方法
Z
0.000 0.000 0.000 0.000 0.000 0.000 0.000 0.000 *** 【 】
O0001 R
N00001 T
MEM *** *** 【磨耗】 【形状】
0.000 0 0.000 0 0.000 0 0.000 0 0.000 0 0.000 0 0.000 0 0.000 0 S 0 T0101 08:16:18 【 】 【(操作)】
Produced by Miss Xie
二、内孔车刀的对刀方法
1 .按工作方式区下的MDI键。 2 .按PROG键切换屏幕,输入“T0101;”,按INSRT键,按循环 启动键,使1号刀(内孔车刀)处于工作位置。 3 . 输入“M03 S500;”,按INSRT键,按循环启动键,使主轴 转动。 4 .按工作方式区下的手动键,利用方向键结合快速移动键及 进给倍率旋钮移动1号刀,接近工件毛坯端面。 5 .进行Z方向对刀。