生产线的平衡
《生产线平衡》课件

对生产线上的作业要素进行路径规划,减少重复行走和等待时间,降低能耗和生 产成本。
提高作业要素的效率
培训与技能提升
对生产线上的作业人员进行培训和技能提升,提高其操作熟 练度和工作效率。
引入激励机制
建立有效的激励机制,激发作业人员的工作积极性和创造力 ,提高生产效率。
引入自动化设备
自动化设备的应用
。
谢谢聆听
引入先进的自动化设备,如机器人、 自动化流水线等,提高生产线的自动 化水平,降低人工成本和出错率。
技术升级与改造
对现有生产线进行技术升级与改造, 实现数字化、智能化生产,提高生产 效率和产品质量。
04 生产线平衡的实践案例
案例一:某汽车制造企业的生产线平衡优化
要点一
总结词
要点二
详细描述
通过生产线平衡优化,提高生产效率,降低生产成本。
计算方法
生产线平衡率 = (最短作业要素时间 / 平 均作业要素时间)× 100%。
B
C
影响因素
生产线平衡率受到作业要素周期时间、作业 要素负荷率等多种因素的影响。
优化方法
通过调整作业要素的分配、改进作业方法等 措施,可以提高生产线平衡率,降低生产成 本。
D
作业要素周期时间
作业要素周期时间
指完成一个作业要素所需的时间。它 是生产线平衡评估的重要指标之一。
计算方法
作业要素周期时间 = (作业要素时 间 / 总作业要素数)× 100%。
影响因素
作业要素周期时间受到设备性能、作 业方法、作业环境等多种因素的影响 。
优化方法
通过改进设备、优化作业方法、提高 作业效率等措施,可以缩短作业要素 周期时间,提高生产效率。
生产线平衡

生产线平衡率的计算方法
平衡率是评价一条产线的重要指标,平衡率高就表示在同等 条件下平衡损失就少,也就是说平衡率高的产线人均产能就 高。
目的:通过平衡生产线提高生产效率同时使生产现场更 加容易理解“一个流”的必要性及对于真正实现“OPF”进 而导入“cell production”的重要意义。
平衡生产线的意义
游戏时间
平衡生产线的意义
通过Line balancing我们可以达到以下几个目的:
有效减少工时损失进而提高作业员及设备工装的工作效率; 减少产品的C/T和pitch time,最终导致Takt time 的减少,提高productivity. 提高OEE & OME. 减少WIP,更容易真正实现“OPF”。 在Line balancing 基础上,实现单元生产,提高了生产对柔性化市场的应变能 力。
Line balance rate = ∑Standard time/(bottleneck time*person qty) = ∑ Standard time/(Pitch time*person qty)
Line imbalance rate =1-Line balance rate
Remark: Pitch time 是指生产线每产出一个batch产品所消耗 的时间,这里我们定义batch size 为1pcs, 所以pitch time=bottleneck time, 理想情况下pitch time=Takt time.
1.不同产品的特性差异
生产线平衡分析简介

生产线平衡分析简介一、生产线平衡的定义流动的作业中上下工序之间,存在供应关系,一旦工序作业时间相差太大,就会造成某些用时短的工序,出现等待的现象,其中工时损失相当客观,当工序之间的作业时间差距很少,生产中等待的时间很少,生产效率达到最高时,我们称为生产线平衡率。
二、生产线平衡分析的目的1短短生产一个产品的组装时间〈增加单位时间的生产量>2.提高生产线的工作效率〈包括作业人员,设备>3.减少工作间的准备工作4.提高生产线的平衡5.对新的流程作业方式改善制造方法三、生产线平衡分析方法生产线平衡分析是对改善流程作业的最适用的方法,在改善之前必须对工序进行分析。
1先确认分析对象,生产线和对象工程的范围。
6.实施对象生产线的工程分析把握现状。
7.实施各工程的时间分析<如设定标准时间就灵活运用》8.制作速度图表9.计算生产线平衡率。
四、改善生产线平衡的方法1对作业长的工序进行改善,其改善方法有:11分割作业,把一部分作业分配到作业短的工序中去。
12进行作业改善,缩短作业时间1.3作业机械化1.4提高机械化的能力1.5增加作业员或替换技能水平更高的作业员2.对作业时间短的工序进行改善2.1分割那部份的作业,将其分配到其他时间短的工序中去,省略那一工序。
2.2可从作业长时间的工序中抽一部分工作过来。
2.3可以与其他作业时间之工序相结合。
2.4分配至两个以上的工序,尽量让一个人去作。
五、生产线平衡率的计算1.平衡率的计算方法:生产平衡率二各工程净时间的总和/时间最长的工程作业时间经XIO0%2.不平衡的计算方法不平衡率=Io0%-平衡率(%)如:生产一个产品的总时间为136秒,人力为19人,时间最长的工序为10秒,那他的生产平衡率为:生产平衡率=136S∕(10SX19人)X100%=71.6%不平衡率=IO0%-716%=28.4%。
生产线平衡(line balance)
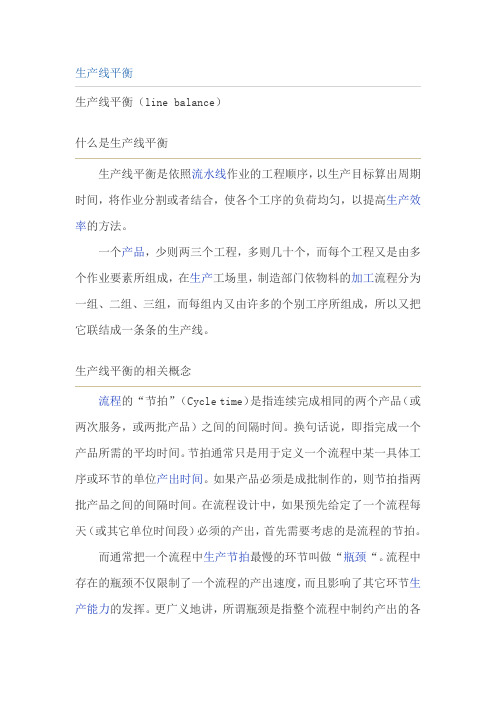
生产线平衡(line balance)什么是生产线平衡生产线平衡是依照流水线作业的工程顺序,以生产目标算出周期时间,将作业分割或者结合,使各个工序的负荷均匀,以提高生产效率的方法。
一个产品,少则两三个工程,多则几十个,而每个工程又是由多个作业要素所组成,在生产工场里,制造部门依物料的加工流程分为一组、二组、三组,而每组内又由许多的个别工序所组成,所以又把它联结成一条条的生产线。
生产线平衡的相关概念流程的“节拍”(Cycle time)是指连续完成相同的两个产品(或两次服务,或两批产品)之间的间隔时间。
换句话说,即指完成一个产品所需的平均时间。
节拍通常只是用于定义一个流程中某一具体工序或环节的单位产出时间。
如果产品必须是成批制作的,则节拍指两批产品之间的间隔时间。
在流程设计中,如果预先给定了一个流程每天(或其它单位时间段)必须的产出,首先需要考虑的是流程的节拍。
而通常把一个流程中生产节拍最慢的环节叫做“瓶颈“。
流程中存在的瓶颈不仅限制了一个流程的产出速度,而且影响了其它环节生产能力的发挥。
更广义地讲,所谓瓶颈是指整个流程中制约产出的各种因素。
例如,在有些情况下,可能利用的人力不足、原材料不能及时到位、某环节设备发生故障、信息流阻滞等,都有可能成为瓶颈。
正如“瓶颈”的字面含义,一个瓶子瓶口大小决定着液体从中流出的速度,生产运作流程中的瓶颈则制约着整个流程的产出速度。
瓶颈还有可能“漂移”,取决于在特定时间段内生产的产品或使用的人力和设备。
因此在流程设计中和日后的日常生产运作中都需要引起足够的重视。
与节拍和瓶颈相关联的另一个概念是流程中的“空闲时间”空闲时间是指工作时间内没有执行有效工作任务的那段时间,可以指设备或人的时间。
当一个流程中各个工序的节拍不一致时,瓶颈工序以外的其它工序就会产生空闲时间。
这就需要对生产工艺进行平衡。
制造业的生产线多半是在进行了细分之后的多工序流水化连续作业生产线,此时由于分工作业,简化了作业难度,使作业熟练度容易提高,从而提高了作业效率。
生产线平衡

生产线平衡生产线平衡生产线平衡是指在生产过程中,通过合理地安排和调配各种生产资源,使得生产过程中的各个环节能够协调配合,达到最佳的生产效果,减少浪费和提高质量。
生产线平衡不仅可以实现生产资源的合理利用,还可以降低生产成本,提高生产效率和质量,从而为企业的发展创造更大的利润空间。
生产线平衡的主要目标是在最短的时间内生产出最大数量的产品,并保证产品质量稳定。
实现这个目标需要根据市场需求制定合适的生产计划,合理分配生产资源,设定生产节拍和工作标准,监测生产过程中的瓶颈和问题,并及时采取措施加以解决。
生产线平衡的实现过程可以分为以下几个步骤:1. 生产计划制定:根据市场需求和企业的生产能力,制定合理的生产计划,明确生产任务和时间节点。
2. 生产资源分配:根据生产计划和生产能力,合理分配所需的生产资源,包括人员、设备、原材料等。
3. 工作标准设定:根据产品的生产要求和企业的生产能力,设定合适的工作标准和生产节拍,确保生产过程中各个环节的协调配合。
4. 生产监控:对生产过程中的各个环节进行监控,及时发现问题和瓶颈,并采取相应的措施进行调整和优化。
5. 优化改进:通过对生产数据的分析和总结,不断优化生产过程和工作标准,减少浪费和提高生产效率和质量。
生产线平衡的重要性:1. 提高生产效率和质量:通过合理利用生产资源和设定工作标准,可以提高生产效率和产品质量,减少生产中的浪费和失误。
2. 降低生产成本:生产线平衡可以减少生产中的浪费和废品,优化生产过程,从而降低生产成本。
3. 提高客户满意度:通过生产线平衡,企业能够按时交付满足客户需求的产品,提高客户满意度和忠诚度,为企业的长期发展打下坚实的基础。
4. 优化人力资源管理:生产线平衡需要遵循一定的生产流程和工作标准,可以优化人力资源的管理和培训,构建有效的生产团队。
5. 改善企业形象:通过生产线平衡,企业可以提高产品质量和生产效率,为客户提供更好的产品和服务,改善企业形象和口碑。
生产线平衡分析与改善(最全面的IE分析-生产线平衡)

2023/12/24
8
二、流水生产线概述
1、 流水生产的基本概念 ● 流水线生产的分类
➢单人单产品式 ➢单产品固定式 ➢多产品固定式 ➢自由流水式 ➢连续传动流水式 ➢ 间歇传动流水式 ➢分组式
设某一产品从原料到成品,需经过A、B、C、D四个工序,其基本标 准工时(秒/个)及相关生产效率、良率、投入机台/人员数分别见表11: 可以求各工序每小时产量为: A工序每小时产量=(3600秒÷6.90)×90%×95%×1=470.87个 B工序每小时产量=(3600秒÷5.1)×80%×99.5%×1=470.87个 C工序每小时产量=(3600秒÷34.40)×100%×99.9%×2=209.09个 D工序每小时产量=(3600秒÷30.40)×100%×99.5%×2=238.8个 。
IE工业工程
-----生产线平衡
主讲:
课 程 内容
生产线平衡 一、生产线平衡的概述 二、流水生产线概述 三、生产线平衡的设计 四、生产线平衡的方法及改善原则 5、案例分析
2023/12/24
2
1.概念
一、生产线平衡的概述
生产线平衡即对生产的全部工序进行平均化,调整作业 负荷,以使各作业的时间尽可能相近的技术手段与方法,它 是生产流程设计及作业标准化中最重要的方法,是通过平衡 生产线使现场真正实施生产同步化,从而达到“一个流”的 理想。
2023/12/24
。
28
四、生产线平衡的改善方法与原则
2、平衡率改善的图示。
2023/12/24
29
四、生产线平衡的改善方法与原则
生产线平衡

生产线平衡什么是生产线平衡?生产线平衡是指在制造业中,通过合理安排工作站的工作内容和工作时间,使得各个工作站之间的工作负荷达到一致,从而实现整个生产线的高效运行和提高生产效率。
生产线平衡可以有效地减少生产过程中的浪费,并降低生产成本。
生产线平衡的优势1.提高生产效率:通过合理安排工作站的工作负荷,避免因工作站负荷过大或过小而导致的生产效率低下的情况发生,从而提高生产效率。
2.减少生产过程中的浪费:生产线平衡可以避免一些工作站因工作内容过多而产生等待时间,以及其他工作站因工作内容过少而导致的工作站闲置的情况。
这样可以最大程度地减少生产过程中的浪费,提高资源利用率。
3.增强生产线的灵活性:通过生产线平衡,可以使得生产线上各个工作站之间的工作负荷相对均衡,从而增强生产线的灵活性和应对能力。
当需要进行产品类型或生产数量的调整时,可以比较容易地实现,而不需要对整个生产线进行大幅度的调整。
4.提高产品质量:生产线平衡可以减少生产过程中的等待时间和工作站的闲置时间,从而减少了生产线上人为因素对产品质量的影响。
工人在有充足时间完成任务的情况下,可以更加专注和仔细地完成工作,提高产品质量。
实施生产线平衡的步骤1.确定生产线的结构:首先需要明确生产线中包含哪些工作站,以及它们之间的工作关系。
这有助于确定工作站之间的工作负荷平衡目标。
2.测量工作站的工作时间:对于每个工作站,需要测量其完成工作所需的具体时间。
这有助于了解每个工作站的工作负荷情况,为后续的平衡安排提供依据。
3.分配工作到每个工作站:根据上一步测量得到的工作时间,合理地分配工作到每个工作站。
将工作任务合理分配,并确保每个工作站的工作负荷均衡。
4.调整工作站的工作时间:如果发现某些工作站的工作负荷过重或过轻,可以适当调整工作站的工作时间,使得工作负荷达到平衡。
5.定期评估和调整:生产线平衡并非一次性的过程,而是需要定期评估和调整。
随着生产线上产品类型和数量的变化,需要及时地对生产线进行评估和调整,以保持生产线的平衡状态。
生产线平衡概述

生产线平衡概述1. 简介生产线平衡是指在生产过程中,合理分配工作环节的工作量,以实现各个工作环节的协同配合,提高生产效率和产品质量。
生产线平衡的目标是最大限度地优化生产线的运作,避免工作环节之间的阻塞和浪费,提高整体生产效率。
2. 生产线平衡的优势生产线平衡可以带来许多优势,包括: - 提高生产效率:生产线平衡能够避免工作环节之间的堵塞和浪费,使得生产线的运作更加顺畅,从而提高生产效率。
-降低生产成本:通过合理分配工作环节的工作量,能够避免某些环节过度工作,减少生产成本,提高经济效益。
- 提高产品质量:生产线平衡可以确保每个工作环节都能够得到适当的时间和资源,从而提高产品质量,减少次品率。
- 加强员工协作:生产线平衡需要各个工作环节之间的协作和配合,能够增强员工的团队意识和协作能力。
3. 实现生产线平衡的方法要实现生产线平衡,可以采取以下方法: - 流程分析:对生产线上的每个工作环节进行详细分析,确定每个环节所需的时间和资源,找出潜在的瓶颈和浪费,以便进行优化。
- 工作流程设计:根据流程分析的结果,重新设计工作流程,合理分配工作环节的工作量和时间,确保各个环节之间的协调与顺畅。
- 人员培训:对参与生产线的员工进行培训,使他们了解整个生产线的运作和各个工作环节的重要性,提高工作效率和协作能力。
- 设备优化:通过升级和改善设备,提高其性能和稳定性,减少设备故障和停机时间,确保生产线的持续运转。
4. 生产线平衡的实施步骤以下是实施生产线平衡的基本步骤: 1. 确定目标:明确生产线平衡的目标和期望效果,例如提高生产效率、降低生产成本等。
2. 流程分析:对生产线进行详细的流程分析,找出每个环节的工作量、时间和资源需求。
3. 工作流程设计:根据流程分析结果,重新设计工作流程,确定每个环节的工作内容和时间安排。
4. 人员培训:对参与生产线的员工进行培训,让他们了解新的工作流程和各个环节的工作内容。
- 1、下载文档前请自行甄别文档内容的完整性,平台不提供额外的编辑、内容补充、找答案等附加服务。
- 2、"仅部分预览"的文档,不可在线预览部分如存在完整性等问题,可反馈申请退款(可完整预览的文档不适用该条件!)。
- 3、如文档侵犯您的权益,请联系客服反馈,我们会尽快为您处理(人工客服工作时间:9:00-18:30)。
第四章生产线的平衡4.1定义及专有名词术语工厂的生产作业,常由各种不同功能的机器做各种加工处理,按顺序完成零件,再由零件装配成产品。
使整个生产流程能顺利进行,没有停顿,等待或闲置现象,便是生产线平衡问题(Line Balancing Problem)。
工作站含量时间可简称工作站时间,例如在图4-1中,若A、B、C、D四站工作时间分别为20、30、50、30分,则D产品为每间隔50分钟,才能生产一单位,这是由于C站耗时50分,虽D站仅需30分,每一单位生产时,必须等待20分钟所致。
同理A与B站也可闲置30分及20分,仍不延误每50分生产一单位D产品,由此可知生产一单位产品需时间多少,全由生产线工作站中工作含量时间最多者决定。
这最多的工作时间,称为周期时间(Cycle Time),在本例中周期时间为50分钟,故生产率γ应为周期时间C的倒数,即C=1/γ。
各站的闲时可由周期时间与该站工作时间之差表示。
将各站间时总计,称为平衡滞延时间(Balance Delay Time)。
在图4-1中,若各站工作时间均相等,周期时间也与各站工作时间相同,各站均无闲时,也无平衡滞延时间,我们称此生产线已达百分之百或完全平衡(Perfect Balance)。
如此,物料流动速度不变,各站工作顺序而下,也达到最高生产效率。
事实上在实际作业中,完全平衡很难达到,总会有少许多余闲时出现,最简单办法是让空闲人员兼做一些间接性工作。
装配线(Assembly Line)依装配产品的数目可分为三类,如图4-2(a)(b)(c)所示。
(1)单产品装配线(Single-Model Assembly Line)即装配单项产品与零件;(2)多产品批次装配线(Batch or Multimodel Assembly Line)即多项产品分别以批次装配完成,批量很大时,与单产品装配线无异,批量小时,则与后述多产品装配线相似;(3)多产品装配线(Mixed-Model Assembly Line)为多项产品同时在装配线完成。
(a)单产品装配线(c)多产品装配线(b)多产品批次装配线图4-2 装配线分类图定义:装配线平衡又称工序同期化,就是根据流水线节拍的要求,采取各种技术、组织的措施来调整各工作地的单件作业时间,使它们等于节拍或节拍的整数倍。
目的:对装配线实行平衡技术,其目的是使所设计的装配线所需工作地数最少,同时使各工作地作业间尽可能接近节拍,减少忙闲不均的现象,并符合高效率和按节奏生产的要求。
一、为什么要进行装配线时间平衡例:某装配线有6道工序,其作业顺序和工序时间如下:(节拍为5分钟/件)为了解决以上问题,必须对装配线的工作进行新的组合分析,重新组合工作地。
二、进行装配线平衡的内容(原则)1 按工序先后顺序,合理地把作业分配给每一个工作地;2 每个工作地综合作业时间要尽量接近节拍,并使装配线所设计工作地最少3 各工作地空闲时间要少,工作地之间负荷均匀,以保证流水线时间损失最低三、装配流水线节拍节拍:流水线上连续出产两件相同制品的时间间隔,一般用r表示。
例:某流水线计划日产量为150件,采用两班制生产,每班规定有21分钟停歇时间,计划不合格品率为2%,计算流水线节拍。
缺点:1 浪费了时间资源。
2 出现了忙闲不均的现象。
3 浪费了人力资源。
四、进行装配线平衡的步骤1.确定装配流水线节拍,2.计算装配线需要的最少工作地数S min,设t i为工序i的工作时间。
3.组织工作地。
(1)保证各工序之间的先后顺序(2)每个工作地的工序时间之和(Tei)不能大于节拍(Tei<r)(3)各工作地的时间尽量接近或等于节拍(Tei→r)(4)应使工作地数目最少4.计算工作地时间损失系数S , r 为理想状态的理论值,对装配线进行平衡,要使时间损失系数尽可能小。
图4- 时间损失示意图4.2 生产线平衡所需考虑的因素(1)生产线布置:生产线的布置将影响平衡的改进,在现有生产线中,工具、夹具与小型设备等的调整,通常不列入生产线平衡作业中,唯传送带(Conveyors)大型设备等装置,不易改变位置,属于区域限制(Zoning Constraints)情形,对以后平衡改进作业,具有很大影响。
所以生产新产品或建新厂时,也应注意工厂布置对生产线平衡影响的程度,通常最后对于主要装配线,尽可能使其接近完全平衡,并对区域或部门限制的情形,应尽量减少。
(2)产品的性质:由于其工作要素的时间分配与先后次序相异,对生产线平衡具有不同的影响。
Kilbridge与Wester两位调查研究,获得下列两点结论:(1)相同周期时间及其他情形同时,产品中工作要素时间短者数量多及时间长者数量少,越易获得平衡。
(2)工作要素先后次序限制越少,也越易获得平衡。
(3)周期时间:也是影响平衡难易程度的主要因素。
最佳周期时间依据Kilbridge与Wester两位的研究,应考虑有关产品成本的内外在因素,诸如学习成本,时间成本,滞延成本(Balance-delay Cost),需求量与生产率,工作人员缺勤与转换,各类设备成本,以及库存量成本等。
事实上,周期时间常由生产率符合需求量决定,即TC q=(4-1)式中:C 为周期时间,T 为时间,q 表示在T 时间内的需求量。
将总工作含量时间除周期时间,若不为整数,显而易见,无法获得完全平衡。
即使除尽,有时因工作要素先后次序关系,仍无法获得完全平衡。
(4)学习因素(Learning Factor ):工作人员由于学习效应,时间越久,其工作经验增长后,所需处理作业时间渐减。
所以某工作站原为瓶颈作业站,却渐渐变成非瓶颈作业站,因而整个生产线的周期时间也可能变短。
(5)个人行为因素:生产线上工作人员,其技能高低,缺勤率大小,抱怨程度等个人行为因素,与工作环境及工作场所设计的优劣等外在因素,具有同等影响工作要素的时间长短的程度。
由于个人操作时间,每次不尽相同,其事件分配的变异数也不尽相同。
所以如何给予适当合宜的宽放时间(Allowances )应由工作研究分析者制定。
(6)其他因素:在多产品批次装配线或多产品装配线时,对于某产品其平衡程度较优,对其他项产品平衡或较差。
如何取舍,使达到两全其美,必须考虑很多因素。
诸如不同产品作业的难易,不同生产率与需求量等,但通过以总成本为最后标准。
此外生产线在实际情形中,常发生停工待料,或某工作站机器故障等情形,也需要迅速予以改正。
4.3 平衡生产线作业方法生产线及装配线平衡(实际上,装配线也是生产线之一),除后述平衡理论与方法外,一般改进方法可由下述途径获得。
(1) 改良作业方法 (2) 改变机器速度(3) 多种项目联合生产线(4) 料堆或加班对付操作较慢机器 (5) 分割作业 (6) 移动操作员(7) 增进工作人员绩效4.4 平衡滞延理论设C=周期时间k P =第K 工作站含量时间,也就是第K 工作站处理时间,K=1、2、……、nk D =第K 工作站的闲时。
K=1、2、……、n则总工作含量时间应为1nk k P =∑平衡滞延时间BD 应为111()n n nk k k k k k BD D C P nC P =====-=-∑∑∑ (4-2)若以百分率表示1nC ()10%0nkk P BD nC=-=⨯∑ (4-3)平衡生产线目的,是使BD 越小越好,若BD 为零,即为完全平衡。
若k P 已知且为常数,故kP C ≤,要达到完全平衡,则必须1nkk PC =∑为整数,此为必要条件。
然而实际情形,各作业或工作元素常有先后次序,即使1nkk PC =∑为整数,可能并非正好全部安排,而得完全平衡。
设min N 为生产线工作站数的最小值,得1minmin int nk k P N eger n n C =⎧⎫⎪⎪⎪⎪=≥⎨⎬⎪⎪⎪⎪⎩⎭∑ (4-4) 若单独作业的时间,超过周期作业时间半数以上时,这种作业,两个无法合并在一起,设N 为生产线工作站的可行最小值(Feasible Minimum ),则min fes k N numb er of k P ⎧=⎨⎩所以实际上工作站数目的最小值,应为min N 与fes N 中的最大者。
由前(4-2)式知,若周期时间固定,欲使BD 小,则必n 越小才行。
所以通常在平衡生产线时,使工作站数目越少,越能达到我们的目的。
若周期时间并不固定,则应在许多周期时间可能值中,分别获得BD ,比较后选择。
周期时间的可能值应在下式间max 1nk k P C P =≤≤∑唯有时间C 值尚有其他限制,例如必须符合需求量,依(4-1)式知maxT P C q≤≤在某些情形下,我们是固定工作站数目,要使周期时间减低,达到提高生产率的目的。
而各作业时间k P 通常不是固定常数,实为随机变数,通常平衡生产线分析人员,常不给工作站百分之百负荷,使有安全因素可使作业在规定时间内完成,而分析时间则设k P 为固定常数,较易处理。
除了各作业先后次序限制外,尚有区域限制,即各种设备随工厂布置结果,必须安装在某一特定区域。
因此作业无法与不在此区域内执行的作业合并在一个工作站完成。
另因大件产品的装配线,工作人员仅能在大件的前后方式上下部位作业,此称为位置限制(Positional Constraints )。
4.5生产线平衡启发式求解法事实上,由于整个生产线例如有70个工作站与105个在先关系,极为普遍,则可能排序办法有1058570!/210=种,即使由电子计算机求解,计算时间耗用也很大。
在实际情形中,尚有地区限制,因此,我们常用启发式求解法(Heuristic Method )寻觅近似答案,使简单快速,代替数学模式的繁琐求解。
这里我们将探讨几种以手算(by hand )来帮助解决生产线平衡问题的方法。
这些方法是属于启发式法则,意指是建立在逻辑及一般合理的判断上,并不能保证所得解一定是最佳解,但几乎可达到近似最佳解。
各种启发式求解法简述如下: (1) 最大候选法则(Largest-candidate rule )这种方法最为简单,它以单元时间的大小作为分配工作单元给工作站的依据,并考虑工艺顺序和Takttime 的限制来分配工作站。
(2)Kilbridge与Wester法Kilbridge与Wester法最主要的是以先后次序为重点,将作业分成纵列,第一纵列包括没有在先情形的作业,第二纵列是直接后随第一纵列的作业,以此类推。
可知我们目标是尽量将右边纵列能向左侧合并。
在同一纵列间可相互先后,当然作业也可向右移,只是与目标相反,不得已时在使用,然后再设法按周期时间合并。
(3)阶位法(相对位置加权法)阶位法(Ranked Positional Weight)是Helgeson与Birnie两人在1961年提出的求解法。