数控加工程序编制
数控加工程序编制及操作

2) 铣较大平面
铣较大平面时,为了提高生产效率和提高加 工表面粗糙度,一般采用刀片镶嵌式盘形铣刀, 如图4.9所示。
3) 铣小平面或台阶面
铣小平面或台阶面时一般采用通用铣刀, 如图4.10所示。
4) 铣键槽
铣键槽时,为了保证槽的尺寸精度,一般用 两刃键槽铣刀,如图4.11所示。
5) 孔加工
孔加工时,可采用钻头、镗刀等孔加工类 刀具,如图4.12所示。
数控加工程序编制及操作
1、常用铣削刀具
数控铣床上所采用的刀具, 要根据被加工零件的材料、几何 形状、表面质量要求、热处理状 态、切削性能及加工余量等,选 择刚性好、耐用度高的刀具。常 用刀具见右图。
2、铣刀类型选择
1)加工曲面类零件
加工曲面类零件时,为了保证刀具切削刃与加工轮廓在切 削点相切,而避免刀刃与工件轮廓发生干涉,一般采用球头铣刀 ,粗加工用两刃铣刀,半精加工和精加工用四刃铣刀,如图4.8所示 。
若执行下述程序段 N10 G53 G90 X0 Y0 Z0 N20 G54 G90 G01 X50 Y0 Z0 F100 N30 G55 G90 G01 X100 Y0 Z0 F100 则刀尖点的运动轨迹如图4.31中OAB所示。
b、顺铣和逆铣对加工影响
ቤተ መጻሕፍቲ ባይዱ
在铣削加工中,采用顺铣还是逆铣方式是影响加工表面粗糙度的
重要因素之一。逆铣时切削力F的水平分力FX的方向与进给运动Vf方向相反, 顺铣时切削力F的水平分力FX的方向与进给运动Vf的方向相同。铣削方式的选 择应视零件图样的加工要求,工件材料的性质、特点以及机床、刀具等条件
综合考虑。通常,由于数控机床传动采用滚珠丝杠结构,其进给传动间隙很
3、铣刀结构选择——平装结构
数控加工程序编制数控车阶梯轴程序编制
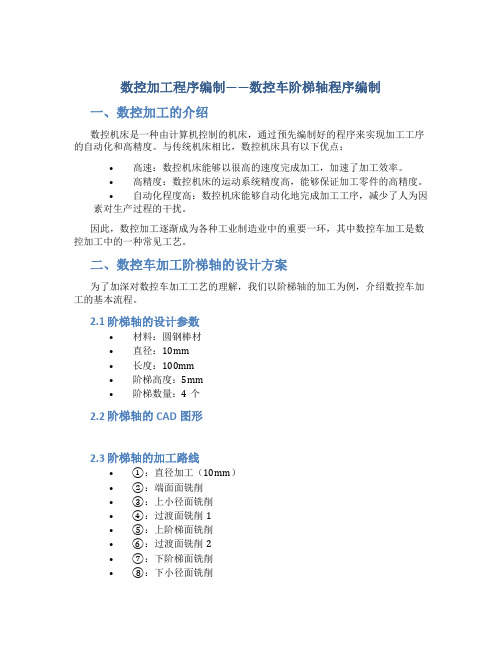
数控加工程序编制——数控车阶梯轴程序编制一、数控加工的介绍数控机床是一种由计算机控制的机床,通过预先编制好的程序来实现加工工序的自动化和高精度。
与传统机床相比,数控机床具有以下优点:•高速:数控机床能够以很高的速度完成加工,加速了加工效率。
•高精度:数控机床的运动系统精度高,能够保证加工零件的高精度。
•自动化程度高:数控机床能够自动化地完成加工工序,减少了人为因素对生产过程的干扰。
因此,数控加工逐渐成为各种工业制造业中的重要一环,其中数控车加工是数控加工中的一种常见工艺。
二、数控车加工阶梯轴的设计方案为了加深对数控车加工工艺的理解,我们以阶梯轴的加工为例,介绍数控车加工的基本流程。
2.1 阶梯轴的设计参数•材料:圆钢棒材•直径:10mm•长度:100mm•阶梯高度:5mm•阶梯数量:4个2.2 阶梯轴的CAD图形2.3 阶梯轴的加工路线•①:直径加工(10mm)•②:端面面铣削•③:上小径面铣削•④:过渡面铣削1•⑤:上阶梯面铣削•⑥:过渡面铣削2•⑦:下阶梯面铣削•⑧:下小径面铣削•⑨:倒角三、数控车阶梯轴程序编制3.1 G-code编写规范G-code是数控编程语言的一种,它是一种基于ASCII码的简单且通用的编程语言。
在数控车加工阶梯轴的程序编制中,我们需要规范化地编写G-code,以确保程序能够正确执行。
以下是G-code编写的常用规范:•每行不超过80个字符,以大写字母开头。
•数值统一使用绝对值模式。
•插补方式使用G01、G02、G03等。
•转速、进给速度、工具槽号计划时要使用变量,不要使用常量。
•在程序的起始位置加入T、S、F等代码,分别表示刀具、主轴转速、进给速度。
•在程序开头应该有G90和G54,分别表示绝对模式、坐标系的选择。
3.2 程序编制过程3.2.1 直径加工(10mm)首先,我们需要使用G00命令进行快速定位,然后使用G01命令进行慢速切割加工。
这个步骤是阶梯轴的第一步,也是整个加工过程中最简单的一步。
数控机床的加工程序编制
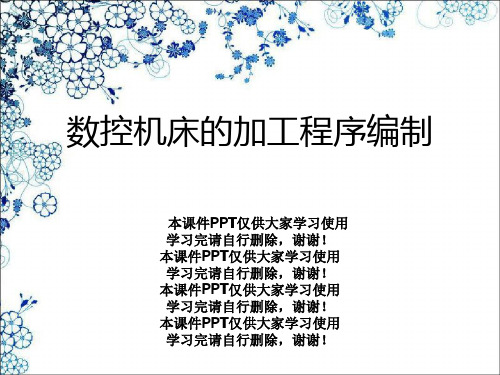
顺序号又称程序段号或程序段序号。位于程序 段之首,由地址符N和后续2~4数字组成。
顺序号的作用:对程序的校对和检索修改;作为 条件转向的目标,即作为转向目的程序段的名称。有 顺序号的程序段可以进展复归操作,指加工可以从程 序的中间开场,或回到程序中断处开场。
顺序号的使用规那么:为正整数,编程时将第 一程序段冠以N10,以后以间隔10递增,以便于修改。
这种从零件图分析到制成控制介质的全部过程, 称为数控加工的程序编制。
数控加工的过程演示如下:加工动画
数控加工流程:
2〕数控程序样本:
O10 N10 G55 G90 G01 Z40 F2000 N20 M03 S500 N30 G01 X-50 Y0 N40 G01 Z-5 F100 N50 G01 G42 X-10 Y0 H01 N60 G01 X60 Y0 N70 G03 X80 Y20 R20 … N80 M05 N90 M30
3〕尺寸字 尺寸字用于确定机床上刀具运动终点的坐标位
置。表示时间暂停的指令也包含在内。其中,用的 较多的尺寸地址符号有3组:
第一组 X,Y,Z,U,V,W,P,Q,R 用 于指令到达点的直线坐标尺寸;
第二组 A,B,C,D,E 用于指令到达点的的 角度坐标尺寸;
第三组 I,J,K 用于指令零件圆弧轮廓的圆心 坐标尺寸。
对于数控车床,其后的数字还兼作指定刀具长 度补偿和刀尖半径补偿用。T后面的数字分2位、4 位、6位。对于4位数字来说,如:
T XX
XX
当前刀具号 刀补地址号
7〕辅助功能字 辅助功能字的地址符是M,后续数字一般为1~3
位正整数,又称为M功能或M指令,用于指定数控 机床辅助装置的开关动作,常用M00~M99见表1 -2。
数控程序编写

控 加 工 程 序 程序主体 程序结束指令 程序结束符 程序段
// 开始符 // 程序名
// 程序主体 //程序结束指令 // 结束符
代码字 地址符 数字
数控加工程序的一般格式:
(1)程序开始符、结束符 程序开始符、结束符是同一个字符,ISO代码中是%,EIA代码中是EP, 书写时要单列一段。 (2)程序名 程序名有两种形式:一种是英文字母O和1~4位正整数组成;另一种是 由英文字母开头,字母数字混合组成的。一般要求单列一段。 (3)程序主体 程序主体是由若干个程序段组成的。每个程序段一般占一行。 (4)程序结束指令 程序结束指令可以用M02或M30。一般要求单列一段。
二、G02、G03指令编程格式(1): G02(G03)X(U)——Z(W)—— R——
圆弧顺、逆 圆弧终点坐标
绝对值 X、Z
F——
进给速度
确定圆心位置
刀架后置
刀架前置
增量值 U、W 混合编程 X、W
α≤180° 用+R 360°>α>180° 用-R
车床刀架前后置,圆弧顺逆不相同
刀架后置为标准,前置顺逆方向反
数控程序是针对刀具上的某一点即刀位点,按工件轮廓尺寸编制的。车刀的刀位点 一般为理想状态下的假想刀尖点或刀尖圆弧圆心点。但实际加工中的车刀,由于工 艺或其他要求,刀尖往往不是一理想点,而是一段圆弧。当加工与坐标轴平行的圆 柱面和端面轮廓时,刀尖圆弧并不影响其尺寸和形状,但当加工锥面、圆弧等非坐 标方向轮廓时,由于刀具切削点在刀尖圆弧上变动,刀尖圆弧将引起尺寸和形状误 差,造成少切或多切。这种由于刀尖不是一理想点而是一段圆弧,造成的加工误差, 可用刀尖圆弧半径补偿功能来消除。
数控加工程序编制的步骤及标准

数控加工程序编制的步骤及标准
一、程序编制的内容与步骤
程序编制是指从零件图纸到编制零件加工程序和制作控制介质的全部过程。
它可分为手工编程和自动编程两类。
手工编程时,整个程序的编制过程是由人工完成的,其编程内容和步骤如下图所示。
二、程序编制的代码标准
数控机床的零件加工程序,可通过拨码盘、键盘、穿孔纸带、磁带及磁盘等介质输入到数控装置中。
常用的标准穿孔纸带有五单位(五列孔,宽17.5mm)和八单位(八列孔,宽25.4mm)两种。
目前广泛应用的八单位穿孔纸带的代码标准有两种:EIA(Electronic Industries Association,美国电子工业协会)标准和ISO(International Standard Organization,国际标准化组织)标准。
ISO标准又被称为ASCII(American Standard Code for Information Interchange,美国信息交换标准码)标准,如表下表所示:
ISO标准又被称为ASCII
八单位穿孔纸带。
数控加工的程序编制
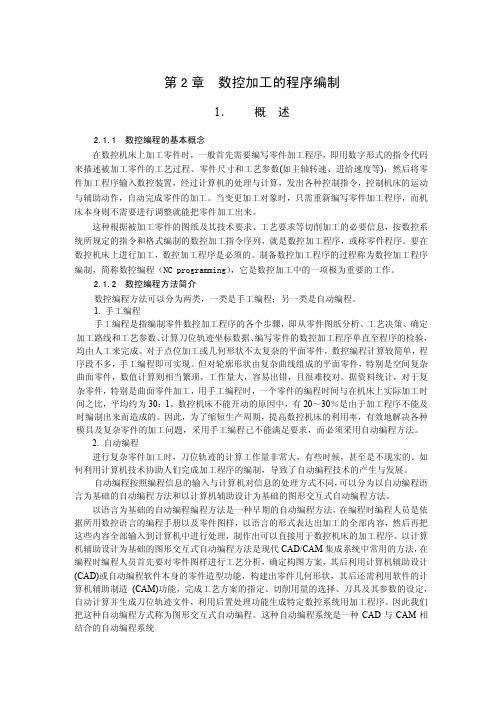
第2章 数控加工的程序编制1.概述2.1.1 数控编程的基本概念在数控机床上加工零件时,一般首先需要编写零件加工程序,即用数字形式的指令代码来描述被加工零件的工艺过程、零件尺寸和工艺参数(如主轴转速、进给速度等),然后将零件加工程序输入数控装置,经过计算机的处理与计算,发出各种控制指令,控制机床的运动与辅助动作,自动完成零件的加工。
当变更加工对象时,只需重新编写零件加工程序,而机床本身则不需要进行调整就能把零件加工出来。
这种根据被加工零件的图纸及其技术要求、工艺要求等切削加工的必要信息,按数控系统所规定的指令和格式编制的数控加工指令序列,就是数控加工程序,或称零件程序。
要在数控机床上进行加工,数控加工程序是必须的。
制备数控加工程序的过程称为数控加工程序编制,简称数控编程(NC programming),它是数控加工中的一项极为重要的工作。
2.1.2 数控编程方法简介数控编程方法可以分为两类,一类是手工编程;另一类是自动编程。
手工编程1.手工编程是指编制零件数控加工程序的各个步骤,即从零件图纸分析、工艺决策、确定加工路线和工艺参数、计算刀位轨迹坐标数据、编写零件的数控加工程序单直至程序的检验,均由人工来完成。
对于点位加工或几何形状不太复杂的平面零件,数控编程计算较简单,程序段不多,手工编程即可实现。
但对轮廓形状由复杂曲线组成的平面零件,特别是空间复杂曲面零件,数值计算则相当繁琐,工作量大,容易出错,且很难校对。
据资料统计,对于复杂零件,特别是曲面零件加工,用手工编程时,一个零件的编程时间与在机床上实际加工时间之比,平均约为30:1。
数控机床不能开动的原因中,有20~30%是由于加工程序不能及时编制出来而造成的。
因此,为了缩短生产周期,提高数控机床的利用率,有效地解决各种模具及复杂零件的加工问题,采用手工编程已不能满足要求,而必须采用自动编程方法。
2. 自动编程进行复杂零件加工时,刀位轨迹的计算工作量非常大,有些时候,甚至是不现实的。
数控车床的程序编制步骤
数控车床的程序编制步骤数控车床程序编制是将零件加工的工艺要求和加工参数转换为机床能够执行的指令序列并载入数控系统,使机床按照程序要求自动完成加工过程。
下面是数控车床程序编制的典型步骤:1.了解零件图纸和工艺要求:仔细研究零件图纸,了解零件的尺寸要求、形状要求以及表面质量要求等,还要确定零件的加工顺序和工艺路线。
2.选择工具和刀具:根据零件的要求和加工工艺,选择合适的车刀、镗刀、钻刀及其加工参数。
3.制定加工工艺:根据零件的尺寸要求和形状要求,制定适当的车削切削参数和轮廓刀补偿值,并确定刀具路径。
4.确定坐标系和参考点:选择适当的坐标系和参考点,并确定零点的坐标位置。
5.数控系统参数设置:根据机床和数控系统的特点,设置数控系统的参数,如坐标系、移动速度、进给量等。
6.编写数控程序:使用数控编程语言,按照零件加工工艺要求,逐步编写数控程序。
7.先练习:在计算机仿真软件中,根据编写的数控程序进行仿真操作,以验证程序正确性。
修正程序错误。
8.载入数控系统:将编写好的数控程序,通过U盘、本地网络等方式,载入数控系统中。
9.导入刀具和工件坐标:确定刀具的初始位置、起刀点和工作零点,导入数控系统中。
10.设置工件坐标系:根据图纸和实际加工需求,设置工件坐标系和坐标偏移。
11.调试程序:使用手动操作或自动操作,对数控系统进行调试,确保程序的安全性和准确性。
12.加工实践:进行实际加工操作,监控加工过程中各项参数的变化,并及时调整。
13.检验零件:完成加工后,根据图纸要求进行零件的测量和检验,确保零件质量满足要求。
14.优化程序:根据实际加工情况,调整和优化数控程序,提高加工效率和质量。
15.存档和备份:将编写好的数控程序进行保存和备份,以备后续使用。
总结起来,数控车床程序编制是一项精细的工作,需要熟悉机床、工具和数控系统的基本原理,同时要具备良好的图纸分析和数控编程能力。
通过以上步骤的严格执行,可以确保数控车床加工过程的准确性和安全性。
机床数控技术第3章数控加工程序的编制
6. 程序校验和首件试切
程序送入数控系统后,通常需要经过试运行和首 件试切两步检查后,才能进行正式加工。通过试运行, 校对检查程序,也可利用数控机床的空运行功能进行 程序检验,检查机床的动作和运动轨迹的正确性。对 带有刀具轨迹动态模拟显示功能的数控机床可进行数 控模拟加工,以检查刀具轨迹是否正确;通过首件试 切可以检查其加工工艺及有关切削参数设定得是否合 理,加工精度能否满足零件图要求,加工工效如何, 以便进一步改进,直到加工出满意的零件为止。
1—脚踏开关 2—主轴卡盘 3—主轴箱 4—机床防护门 5—数控装置 6—对刀仪 7—刀具8—编程与操作面板 9—回转刀架 10—尾座 11—床身
3.2 数控车削加工程序编制
数控车床主要用来加工轴类零件的内外圆柱面、 圆锥面、螺纹表面、成形回转体表面等。对于盘类零 件可进行钻、扩、铰、镗孔等加工。数控车床还可以 完成车端面、切槽等加工。
3. 程序名
FANUC数控系统要求每个程序有一个程序名,
程序名由字母O开头和4位数字组成。如O0001、 O1000、O9999等
3.2.3 基本编程指令
1. 快速定位指令G00
格式:G00 X(U)_ Z(W)_;
说明:
(1) G00指令使刀具在点位控制方式下从当前点以快移速度 向目标点移动,G00可以简写成G0。绝对坐标X、Z和其增 量坐标U、W可以混编。不运动的坐标可以省略。
3.2.1 数控车床的编程特点
(1)在一个程序段中,可以用绝对坐标编程,也可用 增量坐标编程或二者混合编程。
(2)由于被加工零件的径向尺寸在图样上和在测量时 都以直径值表示,所以直径方向用绝对坐标(X)编程时 以直径值表示,用增量坐标(U)编程时以径向实际位移 量的2倍值表示,并附上方向符号。
数控加工程序编制-加工中心-孔类零件程序编制全解
G88循环
二、相关知识
(二)固定循环功能
(5)精镗循环(G76) 指令格式: G76 X_ Y_ Z_ R_ Q_ F_
精镗时,主轴在孔底定向停止后,向刀尖反方向移 动,然后快速退刀。
这种带有让刀的退刀不会划伤已加工平面,保证了 镗孔精度。
程序格式中,Q 表示刀尖的偏移量,一般为正数, 移动方向由机床参数设定。
1
钻中心孔
2
钻φ5mm通孔
3
攻丝
螺纹孔加工工序卡
刀具规格
类型
材料
A4中心钻
高速钢
Φ4.2mm麻花钻 高速钢
M5mm细牙丝锥 高速钢
主轴转速 (r/min)
1200 600 80
进给速度 (mm/min)
20 30 64
(6)编制零件螺纹孔钻中心孔加工程序
四、拓展知识
用西门子802D孔及螺纹加工循环指令加工图零件。
(二)固定循环功能
(2)带停顿的钻孔循环(G82) 指令格式:
G82 X_Y_Z_P_R_F_
G82循环
该指令除了要在孔底暂停外,其它动作与G81相同。暂 停时间由地址P给出。此指令主要用于加工盲孔,以提 高孔深精度。
二、相关知识
(二)固定循环功能
(3)断屑式深孔加工循环(G73)
指令格式: G73 X_Y_Z_Q_R_F_
三、工作任务的完成
(一)数控加工工艺的制订
4.刀具准备,填写刀具卡
序号
1 2 3
4
5 6 7
刀具号
T05 T06 T07
名称 麻花钻 麻花钻 镗刀
T08 镗刀
T09 中心钻 T10 机用铰刀 T11 麻花钻
刀具规格 直径
第3章:数控加工程序的编制
刀具中心的走刀路线为:
对刀点1→对刀点2 →b→c→c’→下刀点2→下刀点1
各基点及圆心坐标如下: A(0,0) B(0,40) C(14.96,70) D(43.54,70) E(102,64) F(150,40) G(170,40) H(170,0) O1(70,40) O2(150,100)
10 20 =10
60O
17.321
N18 G90 G00 Z100.;
10 20 =10
60O
17.321
N19 X0. Y0. M05; N20 M30;
10 20 =10
60O
孔加工注意事项:
孔加工循环指令是模态指令,孔加工数据 也是模态值;
撤消孔加工固定循环指令为G80,此外, G00、G01、G02、G03也可起撤消作用;
N016 G01 X45.0 W0 F100;
切槽
N017 G04 U5.0;
延迟
N018 G00 X51.0 W0;
退刀
退刀 N019 X200.0 Z350.0 T20 M05 M09;
N020 X52.0 Z296.0 S200 T33 M03 M08;
N021 G33 X47.2 Z231.5 F1.5;
(5)复杂轮廓一般要采用计算机辅 助计算和自动编程。
二、数控铣床编程中的特殊功能指令
(1)工件坐标系设定指令 G54~G59
G54~G59无需在程序段中给出工件 坐标系与机床坐标系的偏置值,而是安 装工件后测量出工件坐标系原点相对机 床坐标系原点在X、Y、Z向上的偏置值, 然后用手动方式输入到数控系统的工件 坐标系偏置值存储器中。系统在执行程 序时,从存储器中读取数值,并按照工 件坐标系中的坐标值运动。
- 1、下载文档前请自行甄别文档内容的完整性,平台不提供额外的编辑、内容补充、找答案等附加服务。
- 2、"仅部分预览"的文档,不可在线预览部分如存在完整性等问题,可反馈申请退款(可完整预览的文档不适用该条件!)。
- 3、如文档侵犯您的权益,请联系客服反馈,我们会尽快为您处理(人工客服工作时间:9:00-18:30)。
第二章数控加工程序编制----作业题详解一、数控铣床、钻床编程作业1. 使用刀具长度补偿和固定循环指令加工如图所示的零件中A、B、C三个孔N01 G91 T1 M06;换刀N02 M03 S600;主轴启动N02 G43 H01;设置刀具补偿N03 G99 G81 X120.0 Y80.0 Z-21.0 R-32.0 F100;钻孔AN04 G99 G82 X30.0 Y-50.0 Z-38.0 R-32.0 P2000;锪孔BN05 G98 G81 X50.0 Y30.0 Z-25.0 R-32.0 P2000;钻孔CN06 G00 X-200.0 Y-60.0;返回起刀点N07 M05;N08 M02;2. 毛坯为120mm×60mm×10mm铝板材,5mm深的外轮廓已粗加工过,周边留2mm余量,要求加工出如图所示的外轮廓及φ20mm深10mm的孔,试编写加工程序。
(1)根据图纸要求,确定工艺方案及加工路线1)以底面为定位基准,两侧用压板压紧,固定于铣床工作台上;2)工步顺序:①钻孔φ20mm;②按线路铣削轮廓(2)选择机床设备//ABCDEFGOO选用数控铣钻床。
3)选用刀具采用φ20mm的钻头,铣削φ20mm孔;φ10mm的立铣刀用于轮廓的铣削,并把该刀具的直径输入刀具参数表中。
数控钻铣床没有自动换刀功能,钻孔完成后,直接手工换刀。
(4)确定切削用量切削用量的具体数值应根据该机床性能、相关的手册并结合实际经验确定,详见加工程序。
(5)确定工件坐标系和对刀点在XOY平面内确定以O点为工件原点,Z方向以工件上表面为工件原点,建立工件坐标系,如图所示。
采用手动对刀方法对刀。
(6)编写程序2)铣轮廓程序(手工安装好φ10mm立铣刀)O0002;G54 G90 G00 Z5.0 S1000 M03;X-5.0 Y-10.0;G41 D01 X5.0 Y-10.0;C(26.8,45),D(57.3,40) E(74.6,30)G01 Z-5.0 F150.0;G01 Y35.0;G01 X15.0 Y45.0;G01 X26.8;G02 X57.3 Y40.0 R20.0;G03 X74.6 Y30.0 R20.0;G01 X85.0;G01 Y5.0;G01 X-5.0;G40 G00 Z100.0;M05;M02;3. 如图所示零件,进行打中心孔、钻孔、攻螺纹等加工。
刀具: T01(中心钻)T02(Ф8.5钻头)T03(倒角钻头)T04(M10丝锥)O0003 ;主程序N10 G54 G90 G00X0 Y0 Z250.0 ;选择工件坐标系,快进到换刀点N15 T01 M06 ;换上01号刀具—中心钻N20 S1500 M03 M08 ;启动主轴,开冷却液N25 M98 P0100 ;在四个孔中心孔位置打中心孔N30 T02 M06 ;换02号刀具—Ф8.5钻头N35 S1000 M03 M08 ;启动主轴,开冷却液N40 M98 P0200 ;钻四个孔N45 T03 M06 ;换03号刀具—倒角N50 S1500 M03 M08 ;启动主轴,开冷却液N55 M98 P0300 ;给每个孔倒角N60 T04 M06 ;换04号刀具—M10丝锥N65 S200 M03 M08 ;启动主轴,开冷却液N70 M98 P0400 ;对四个孔攻丝N75 G28 ;返回参考点主程序结束N80 M30 ;主程序结束O0100;钻中心孔子程序N85G99G81X-40.0Y0R2.0Z-1.5F10.0;钻中心孔循环,钻第1个孔的中心孔N90 M98 P0500 ;调用孔位置子程序(二级调用),钻2、3、4孔的中心孔N95 M99 ;O0200 ;钻孔子程序N100G99G81X-40.0Y0R2.0Z-17.0F10.0 ;钻第1个孔N105 M98 P0500 ;调用孔位置子程序,钻2、3、4孔N110 M99 ;O0300 ;倒角子程序N115 G99G81X-40.0Y0.R2.0Z-1.0F20.0 ;第1个孔倒角N120 M98 P0500 ;调用孔位置子程序,对2、3、4孔倒角N125 M99 ;O0400 ;攻丝子程序N130 G99G84X-40.0Y0R2.0Z-17.0F10.0 ;攻第1个孔N135 M98 P0500;调用孔位置子程序,对2、3、4孔攻丝N140 M99 ;O0500 ;位置子程序N150 X0 Y40.0 ;第2个孔的位置N155 X40.0 Y0 ;第3个孔的位置N160 X0.0 Y-40.0 ;第4个孔的位置N165 G00 X0 Y0 Z250; 回起刀点N170 M05N175 M99 ;4. 加工如图所示零件1.工艺分析此零件加工内容为凸台和槽。
凸台加工余量较小,采用Φ18mm平底刀一次性完成加工。
槽加工由于槽宽为20㎜,故可先用Φ18mm平底刀去余量,再用Φ10mm平底刀(由R6圆弧决定刀具)完成精加工。
零点设在零件上表面与其轴线的交点处。
本次作业只需要对槽进行粗铣和精铣。
2.加工步骤:(1)槽粗加工T1 Φ18mm平底刀(2)凸台加工T2 Φ18mm平底刀(3)槽精加工T3 Φ10mm平底刀注:这样安排加工可减少一次换刀。
O0001;槽粗加工T01 M6; Φ18mm平底刀G90 G54 G0 X-10. Y-2. S600 M03;G00 G43 Z50.H1; 起始点,H1为刀长补偿号Z10.; 安全点G01 Z-5. F100;X10.;X0;Y13.;槽精加工:T03 M6; Φ10平底刀,G90 G54 G00 X00 Y17.S600M03;G43 Z50. H02;Z10.;M98 P1001;G00 Z50.;M05;M30;O1001;槽精加工子程序G01Z-5.F50;G01G41 D03 X6.;刀具半径补偿为5.0G03 X0 Y23.R6.; 沿R6的圆弧切向进刀(即切向切入)G01 X-4.;G03 X-10. Y17. R6.;G01 Y8.;X-14.;G03 X-20. Y2. R6.;G01 Y-6.;G03 X-14.Y-12. R6.;G01 X14.;G03 X20. Y-6.. R6.;G01 Y2.;G03 X14. Y8. R6.;G01 X10.;Y17.;G03 X4. Y23. R6.;G01X0.;G03 X-6. Y17. R6.; 沿R6的圆弧切向退刀(即切向退出)M99;5. 加工如图所示零件走刀路线:粗铣和精铣B面-----粗镗、半精镗和精镗φ60H7孔----钻、扩、铰φ12H8孔---M16螺纹钻孔、攻丝本次作业只需要对B面进行粗铣和精铣。
刀具编号:T01---粗铣B面铣刀T13---精铣B面铣刀T02---粗镗刀φ60H7T03---半精镗刀T04---精镗刀T05---钻中心孔刀φ12H8孔T06---钻孔刀T07---扩孔刀(锪孔刀)P0005---位置子程序粗铣B面------面铣刀(刀具直径较大〉45mm)O0001N1 G92 X0 Y0 Z50.0 ;N2 T01 M06;N3 G90 G00 Z10.0;N4 X-135.0 Y45.0;N5 S300 M03;N6 G43Z0.5 H01 M08;N7 G01X75. 0 F70;N8 Y-45.0;N9 X-135.0 M09; N10 G00 G49 Z10. 0 M05; N11 X0 Y0; 精铣B 面-------端铣刀 N12 T13 M06; N13 X-135.0 Y45.0; N14 G43 Z0 H13 S500 M03; N15 G01 X75.0 F50 M08; N16 Y-45.0; N17 X-135.0 M09; N18 G00 G49 Z10.0 M05; N19 X0 Y0;6. 对下图零件在加工中心上进行数控编程,要求在图中标出编程坐标系及坐标原点,需加工外形、钻孔及攻丝。
(不是作业题)其中:T01—铣削外形刀具 T02—钻孔刀具 T03—攻右旋螺纹刀具O003N001 G92 X0 Y0 Z150 建立工件坐标系,并设置对刀点Q (0,0,150)(程序起点) N002 M06 T01 M03 S600 换1号刀,主轴正转,转速600r/minN003 G90 G00 G41 X-50 Y-80 D01 绝对编程,刀具快速移动到点A (-50,-80)并建立起1号刀的半径补偿ZASN004 G43 Z-10 H01 刀具向下移动到点S,Z=-10mm处并建立起刀具的长度补偿N005 G01 Y-15 F60·直线插补至点B(加工AB段)N006 G03 Y15 R15 逆时针圆弧插补至点C(加工BC段)N007 G01 Y30 直线插补至点D(加工CD段)N008 X-40 Y50 直线插补至点E(加工DE段)N009 X-10 直线插补至点F(加工EF段)N010 G03 X10 Y50 R10 F50 逆时针圆弧插补至点G(加工FG段)N011 G01 X40 F100 直线插补至点H(加工GH段)N012 G02 X50 Y40 R10 顺时针圆弧插补至点I(加工HI段)N013 G01 Y-40 直线插补至点J(加工IJ段)N014 G02 X40 Y-50 R10 顺时针圆弧插补至点K(加工JK段)N015 G01 X10 Y-50 直线插补至点L(加工KL段)N016 G03 X-10 Y-50 R10 逆时针圆弧插补至点M(加工LM段)N017 G01 X-30 Y-50 直线插补至点N(加工MN段)N018 G02 X-50 Y-30 顺时针圆弧插补至点P(加工NP段)N019 G01 Y0 直线插补(退刀)至点TN020 G49 Z150 向上退刀至Z=150mm处并取消刀具的长度补偿N021 G40 X0 Y0 M05 快速回到对刀点Q(0,0,150)N022 M06 T02 S800 M03 换2号刀,主轴正转,转速800r/minN023 G00 G43 Z50 H02 刀具向下移动到Z=50mm处并建立起刀具的长度补偿N024 G99 G81 X0 Y20 Z-10 R5 F100 在点A1(0,20)处钻通孔,完成后返回参考平面N025 Y-20 M05 在点A2(0,20)处钻通孔,完成后返回参考平面N026 G00 G49 X0 Y0 Z150 退刀至对刀点Q(0,0,150)并取消刀具长度补偿N027 M06 T03 S800 M03 换3号刀,主轴正转,转速800r/minN028 G00 G43 Z50 H03 刀具向下移动到Z=50mm处并建立起刀具的长度补偿N029 G99 G84 X0 Y20 Z-10 R5 F100 在点A1(0,20)处加工螺纹孔,完成后返回参考平面N030 Y-20 M05 在点A2(0,20)处加工螺纹孔,完成后返回参考平面N031 G00 G49 X0 Y0 Z150 退刀至对刀点Q(0,0,150)并取消刀具长度补偿N032 M05 M02 主轴停转,程序结束7. 在数控钻床上加工如图所示的两个螺纹孔A1、A2。