先进的叶轮机械叶片设计方法
风力发电机组的叶轮设计优化与性能分析

风力发电机组的叶轮设计优化与性能分析1. 引言风力发电作为一种可再生能源的重要形式,被广泛应用于电力供应系统。
叶轮作为风力发电机组中的核心部件,直接影响着发电机组的性能和效率。
本文旨在通过对风力发电机组叶轮的设计优化与性能分析,提出一种能够提高发电效率的叶轮设计方案。
2. 风力发电机组的工作原理风力发电机组利用风能将风动能转化为机械能,然后通过发电机将机械能转化为电能。
叶轮作为风力发电机组中的核心部件,承担着捕捉和利用风能的重要任务。
叶轮优化设计的目标是最大化风能的转化效率,提高发电机组的发电量。
3. 叶轮设计优化3.1 叶片数目和形状设计叶片数目和形状直接影响着风力发电机组的功率转化性能。
一般而言,叶片数目越多,转化效率越高。
然而,叶片数目过多会增加制造成本并增加风力发电机组的重量。
因此,需要综合考虑叶片数目和形状的设计,找到一个平衡点。
3.2 叶片长度和宽度设计叶片长度和宽度的设计也是叶轮设计中的重要因素。
叶片长度越长,捕捉风能的面积越大,风力发电机组的转化效率越高。
然而,过长的叶片会增加风力发电机组的叶轮重量,并对叶轮结构造成一定的负荷。
因此,需要对叶片长度和宽度进行优化设计。
3.3 叶片材料选择叶轮受到来自空气流动的巨大压力和弯曲力的影响,因此在叶片材料的选择上需要考虑其强度、轻量化和耐腐蚀性。
目前常用的叶片材料有玻璃纤维增强塑料(GFRP)和碳纤维增强塑料(CFRP)等。
在叶片材料的选择中,需要综合考虑材料的力学性能和经济性,以实现叶轮结构的优化设计。
4. 叶轮性能分析4.1 基于流体动力学的模拟分析通过建立风力发电机组的叶轮流体动力学模型,可以对叶轮的流场分布和压力分布进行模拟分析,了解叶轮在风力作用下的性能表现。
这可以为叶轮的优化设计提供有力的依据。
4.2 发电机组的发电量模拟叶轮是风力发电机组中能量转化的关键部件,其性能的优化直接影响发电机组的发电效率。
通过基于叶轮性能和风能资源的数据,可以进行发电量的模拟计算,评估叶轮优化设计的效果。
叶轮的设计

取:
: 8 0( n l m)
一
2 . 叶 片 螺线 平 面 图
t 一一 背 叶 片 与 涡 室 间隙 取 t = 1 mm
一
根 据 上 述 叶 轮 叶 片 曲面 螺 线 计 算 结 果 ,绘 制 叶 片 螺 线 。在
圆周 上 取 1 6 个 轴 面 ,每 两 个 轴 面 夹 角 为2 2 . 5 。 ,当 Z = O 时, 空 螺 线 在 平 面 上投 影 , 如 图 所示 :
1 9 9 7 , 2 0 ( 5 ) : 6 -1 3
3 . 叶片 厚 度 计算 确 定 叶片 厚 度 时 ,应 注 意 到 铸 造 的 可能 性 ,对 铸 铁 叶 轮 , 叶 片 最 小 厚 度 为3—4 毫 米 ,本 次 设 计 的叶 轮 材 料 选 用MT 一 4 ,叶 … 馘 拙 :
【 1 】 丁成伟 . 离心 泵 与 轴 流 泵 . 北京: 机械 工 业 出版社, 1 9 8 1
1 4 3— 1 5 8
【 2 ] A . J . 斯捷潘诺夫. 离心 泵 和 轴 流 泵 . 北京: 机 械 工 业 出 版 社
19 80: 7 4—9 3
【 3 】 劳学苏, 何希杰. 螺旋 离心泵的原理 与设计方法. 水泵技术
I
=
5. 6 8 7 (mm )
S - - 6( I T l m)
4 . 背 叶 片 的设 计
图 卜 1叶 轮 轴 面 投 影 图
背 叶片 的主 要作 用 是 减 压 ,其 减 压 程 度 决 定 了背 叶片 的 几 何 参 数 。 背 叶 片 对 于 一 般 的 泵 而 言 ,还 有 另 一 个 作 用 , 就 是 能
叶轮的设计原理及应用

叶轮的设计原理及应用叶轮是一种常见的机械设备,它的设计原理和应用非常广泛。
叶轮常用于液体泵、风扇、涡轮机、喷气发动机等各种工程设备中。
下面将从设计原理、应用范围和优缺点等方面详细介绍叶轮。
叶轮的设计原理主要基于流体力学,叶轮即为固定叶片或转动叶片组成的旋转部件。
为了实现特定的流体机械任务,叶轮的设计取决于不同的应用和摩擦条件。
根据叶片的形状、布局和工作环境,叶轮可分为开式和密闭两种类型。
在涡轮机中,流体通过叶轮,叶轮将流体的动能转化为机械能,并推动传动系统工作。
叶轮的设计需要考虑以下几个因素:1. 流体参数:流速、密度、粘度和温度等参数会影响叶轮的设计。
不同的参数对叶轮的各项性能和工作效果都有显著影响。
2. 叶片类型:叶轮的性能主要由叶片的形状和数量决定。
根据叶片类型的不同,叶轮可以分为离心式、轴流式和混流式等。
3. 叶片布局:叶片的布局也会影响叶轮的性能。
布置叶片的角度和密度能够调节叶轮的扬程、流量和效率。
4. 材料选择:叶轮的工作环境对材料的选择提出了要求。
例如,在高温或高压环境中,必须选择能够耐受这些条件的耐热、耐腐蚀材料。
叶轮的应用非常广泛,以下是几个典型的应用领域:1. 液体泵:叶轮作为泵的核心部件,通过旋转产生离心力,将液体向外部压送。
在工业生产、供水系统和化工过程中广泛使用。
2. 风扇:叶轮通过旋转产生气流,用于降温、通风和气体传送,广泛应用于建筑、汽车、电子设备等领域。
3. 涡轮机:叶轮作为涡轮机的动力转换部件,将流体的动能转变为机械能,如水力发电和汽轮发电等。
4. 喷气发动机:喷气发动机中的叶轮通过喷气产生推力,实现飞机或其他飞行器的推进。
叶轮具有一些优缺点:优点:1. 高效能:叶轮的设计优化可以提高流体机械的效率,从而降低能源消耗和运行成本。
2. 灵活性:叶轮的尺寸、形状和材料可以根据具体应用需求进行定制,满足不同工况下的流体传输要求。
3. 负载适应性:叶轮能够根据系统负载的需求自动调整输出功率,对于泵类设备尤为重要。
叶轮设计 (2)

叶轮设计
叶轮设计是指设计和优化液压机械(如泵和涡轮机)中的
叶片形状和结构,以实现特定的流体力学性能和效率。
在叶轮设计过程中,需要考虑以下几个方面:
1. 流量要求:根据流体介质的特性和给定的工况条件,确
定所需的流量,并据此确定叶轮的尺寸和叶片的数量。
2. 动能转换:叶轮的设计需要将流体的动能转换为机械能,以实现提供所需工作的效果。
3. 叶轮类型:根据应用需求和流体特性,选择合适的叶轮
类型。
常见的叶轮类型包括离心式、轴流式和混流式等。
4. 叶片形状:根据流体传递时的流动特性,选择合适的叶
片形状,以最大程度地提高流体的能量转换和流动效率。
5. 叶片角度:叶片的角度对于流体的流动方向和速度分布
起着重要的作用。
通过优化叶片的进出口角度和弯曲角度,可以提高叶轮的效率和性能。
6. 叶片材料:选择合适的叶片材料,考虑其耐腐蚀性、强
度和疲劳寿命等因素。
常见的叶片材料包括不锈钢、铝合
金和钛合金等。
7. 叶轮结构:考虑叶轮的结构强度和刚度,以确保其能够
承受流体的压力和负载。
8. 叶片表面处理:优化叶片表面的润滑和阻力特性,以减
小摩擦和能量损失。
叶轮设计是一个复杂的工程问题,需要结合流体力学、机
械设计和材料科学等知识进行综合考虑和优化。
现代计算
机辅助设计和仿真技术的应用使得叶轮设计更加精确和高效。
叶轮制作方法

叶轮制作方法1. 引言叶轮是一种经常用于流体机械中的关键零件,其主要功能是将液体或气体流动的动能转化为机械能。
在叶轮的制作过程中,需要考虑到材料的选择、几何形状的设计以及加工工艺等因素。
本文将详细介绍叶轮制作的基本方法。
2. 材料选择叶轮通常选择金属材料制作,如铜、铝、不锈钢等。
材料的选择需要考虑到叶轮在使用过程中所承受的压力、速度、温度以及介质的特性等因素。
一般来说,对于低速、低温环境下的叶轮,铝合金是一个较好的选择;而对于高速、高温环境下的叶轮,不锈钢则更为适合。
3. 几何形状设计在叶轮的几何形状设计中,需要考虑到叶轮的流向、叶片的形状以及叶片间的间距等因素。
3.1 叶轮的流向叶轮的流向是指在流体机械中,叶轮所承受的流体流动的方向。
一些叶轮要求只能接受单向流动,而另一些叶轮则能够适应双向流动。
在设计叶轮时,需要根据具体应用场景,确定叶轮的流向。
3.2 叶片的形状叶片是叶轮的关键部分,其形状的设计直接影响了叶轮的性能。
常见的叶片形状包括直线型、弯曲型、对称型和非对称型等。
在选取叶片形状时,需要考虑到流体的入口速度、流动特性以及期望的流量等因素。
3.3 叶片间的间距叶片间的间距也是叶轮设计中需要考虑的重要因素之一。
间距的大小将会影响到流体在叶轮中的通过速度。
较大的间距能够提高流体的流速,但也会导致液体或气体的泄露。
因此,需要在设计过程中对间距进行仔细的考虑和计算。
4. 加工工艺叶轮的加工工艺通常包括铸造、铣削、切割、折弯等步骤。
4.1 铸造铸造是制作叶轮的常用工艺之一。
在铸造过程中,首先需要制作一个模具,模具的形状与所需叶轮的几何形状相匹配。
然后,将选定的金属材料熔化,倒入模具中,并经过冷却固化。
最后,将模具移除,得到最终的叶轮。
4.2 铣削铣削是另一种常用的叶轮加工工艺。
在铣削过程中,首先需要使用CAD软件将叶轮的几何形状设计出来。
然后,使用数控铣床进行自动加工。
通过控制铣刀的移动轨迹和加工速度,可以精确地将叶轮的几何形状加工出来。
叶轮设计计算程序
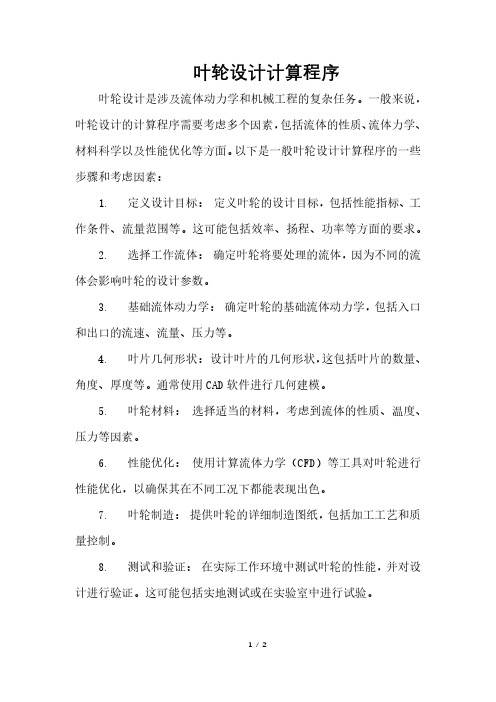
叶轮设计计算程序
叶轮设计是涉及流体动力学和机械工程的复杂任务。
一般来说,叶轮设计的计算程序需要考虑多个因素,包括流体的性质、流体力学、材料科学以及性能优化等方面。
以下是一般叶轮设计计算程序的一些步骤和考虑因素:
1. 定义设计目标:定义叶轮的设计目标,包括性能指标、工作条件、流量范围等。
这可能包括效率、扬程、功率等方面的要求。
2. 选择工作流体:确定叶轮将要处理的流体,因为不同的流体会影响叶轮的设计参数。
3. 基础流体动力学:确定叶轮的基础流体动力学,包括入口和出口的流速、流量、压力等。
4. 叶片几何形状:设计叶片的几何形状,这包括叶片的数量、角度、厚度等。
通常使用CAD软件进行几何建模。
5. 叶轮材料:选择适当的材料,考虑到流体的性质、温度、压力等因素。
6. 性能优化:使用计算流体力学(CFD)等工具对叶轮进行性能优化,以确保其在不同工况下都能表现出色。
7. 叶轮制造:提供叶轮的详细制造图纸,包括加工工艺和质量控制。
8. 测试和验证:在实际工作环境中测试叶轮的性能,并对设计进行验证。
这可能包括实地测试或在实验室中进行试验。
1/ 2
设计计算程序通常涉及使用专业的工程软件,如CAD(计算机辅助设计)、CFD(计算流体力学)等。
叶轮设计是一个高度专业化的领域,需要深厚的工程知识和经验。
设计程序的选择也取决于具体的应用和要求。
在进行叶轮设计之前,建议咨询具有相关经验的工程师或专业团队。
2/ 2。
燃气轮机透平叶片参数化设计及优化

析和方差分析。直观分析就是根据试验的结果分析试验
值随着因素水平的变化而变化的趋势,直观的找出使得
试验目标最优的因素水平的组合
第15页/共29页
透平叶片优化设计
响应面方法(RSM)
RSM就是寻求响应和因子集合之间的真实函数关系的一个合适的逼近式。 如果响应适合于因子的线性函数模型,则近似函数是一阶模型: 如果响应非线性,则必须用更高阶的多项式,例如二阶模型:
第18页/共29页
透平叶片优化设计
案例
参与正交试验设计的变量为: 其余参数L,a1,和a2取值与原始叶型相同。
和叶片数z,它们的水平设置如表所示,
第19页/共29页
透平叶片优化设计
案例
①任一列的所有水平的重复数 相同;②任两列的所有可能的水 平组合的重复数相同。凡满足 这两个条件的表就可以称为正 交表。
第6页/共29页
透平叶片参数化表达
二维叶形
控制厚度分布的各参数意义如下: —前缘厚度,定义为中弧线前缘
点圆半径尺与L的比值; —尾缘厚度,定义为中弧线尾缘
点圆半径凡与L的比值; —最大厚度,定义为中弧线上最
大圆的半径凡与L的比值; —最大厚度位置,定义为前缘点
到最大圆圆心的轴向距离瓜与轴向弦 长L的比值;
叶片设计及优化
正问题法
己知叶栅的几何参数,要求解出流场,求得叶片表面的速度、压力等分布。 正问题方法设计叶片,就是利用正问题的计算结果修改几何参数,反复进 行正问题计算直到获得满意的气动参数分布为止。
反问题法
给定叶片表面的压力分布,通过数值方法反求得叶片的几何形状。
数值优化设计 通常需要在某种叶片参数化表达基础之上,通过流场模拟及优化算法,确
第7页/共29页
某离心叶轮叶片改型设计研究

10.16638/ki.1671-7988.2021.05.019某离心叶轮叶片改型设计研究*覃玄,朱涛(湖北汽车工业学院汽车工程学院,湖北十堰442002)摘要:该文以某高压比离心叶轮为研究对象,以改善叶轮流动特性和提升叶轮的气动性能为目标对其叶片进行改型设计。
文章基于ANSYS BladeGen,采用四阶Bezier曲线对叶轮叶顶弧线以及叶根弧线进行参数改变,通过流场数值模拟分析得到最终设计叶型。
数值模拟结果表明,新设计叶型离心叶轮相较于原叶轮压比提高了0.87%,效率提升了5.69%,达到了本次改型设计的目标。
关键词:离心叶轮;Bezier曲线;叶型设计中图分类号:U462 文献标识码:A 文章编号:1671-7988(2021)05-66-04Research on the Blade Modification Design of a Centrifugal Impeller*Qin Xuan, Zhu Tao( Hubei University of Automotive Engineering Department of Automotive Engineering, Hubei Shiyan 442002 )Abstract: This article is aimed to improve the flow characteristics and aerodynamic performance of a centrifugal impeller. Based on ANSYS BladeGen, by using four order Bezier curve the parameters of tip arc and the hub arc were changed, then the final blade was obtained through the numerical calculation of the flow field. The results show that, the newly designed centrifugal impeller has a 0.87% increase on the pressure ratio and a 5.69% increase on the efficiency, which also has achieved the goal of this article.Keywords: Centrifugal impeller; Bezier curve; Blade designCLC NO.: U462 Document Code: A Article ID: 1671-7988(2021)05-66-04引言压气机是废气涡轮增压器的重要组成部分,本文研究的离心叶轮则为压气机的核心部件[1]。
- 1、下载文档前请自行甄别文档内容的完整性,平台不提供额外的编辑、内容补充、找答案等附加服务。
- 2、"仅部分预览"的文档,不可在线预览部分如存在完整性等问题,可反馈申请退款(可完整预览的文档不适用该条件!)。
- 3、如文档侵犯您的权益,请联系客服反馈,我们会尽快为您处理(人工客服工作时间:9:00-18:30)。
先进的叶轮机械叶片设计方法
对于透平机械叶片的设计,CAESES是一个功能灵活强大的平台,并包含了先进的端壁造型优化方法等。
所有参数化叶片模型都可以与网格划分和仿真工具紧密关联,从而运行自动化CFD仿真分析及优化设计。
应用案例包括涡轮增压器、汽轮机、风扇和泵等——包括轴流、离心或者混流等形式。
西门子,丰田,MTU,KSB,Spencer Turbine和IHI等国际知名的公司都正在使用CAESES来设计叶轮机械部件。
为何(选用)CAESES?
●灵活稳定的参数化模型;
●高度客户定制,开放所有细节,并全面整合到现有工作流程中;
●综合考虑模型设置中的几何/制造约束;
●智能地减少参数数量;
●提供了综合调整模型细节的可能性,例如,能够更好地控制空化或漩涡等局
部流动现象;
●针对所有设计变体的一次性预处理;
●一切都以自动化为目标,以实现高效的形状优化;
●来自CAESES支持团队超快的技术支持。
涡轮增压器里的压气机模型,全参数化可调节,自动化设计
将叶片模型连接到CFD并自动进行分析
叶片设计——高效和灵活
CAESES里的叶片模型可以快速手动创建,也可以自动创建。
创建单个叶片或分离叶片的模型,都可以采用现有模板或进行客户定制,例如:
●创建任意参数化2D轮廓,包括以现有叶片作为基准进行自动化拟合;
●基于任意子午轮廓(导入的数据,创建的参数化曲线),可以将二维叶片截
面映射到三维流面上;
●定义任意前尾缘形状,包括圆形,椭圆形,钝的,弯曲的;
●任意的中弧线定义方式,基于beta角或者theta角,即叶片气流角或者叶型
包角等;
●任意厚度分布定义(导入的数据,参数化曲线,数学公式定义);
●基于半径(常数,可变)并考虑到应力和结构约束的圆角控制;
●先进的3D曲面生成技术,可以生成高质量的形状和确定可行的设计方案。
参数化的几何模型
对于新设计模型的自动化CFD分析,CAESES可以提供自动处理后的参数化几何模型,例如周期性的流体域。
它(允许客户)调整叶片的形状同时可以自动生成网格而不需要手动操作。
参数化静子模型,为自动化网格生成的包含端壁造型的周期性流体域
在一个循环中全自动化完成CFD和应力分析
CAESES先进和稳定的CAD功能使得您可以同时方便的创建参数化的周期性固体区域模型,包括特殊的星型结构等。
因此,在一次循环中,可以同时进行应力分析和CFD分析。
使用CAESES提供的模型,通过一次自动化循环将这两个进程融合在一起可以节省很大一部分的手动工作。
基于CAESES生成的固体模型的应力分析
“我们在5月份启动了评估CAESES的试点工程,在7月份它帮助我们解决了一个时间紧急的工作并在10月份正式成为了我们的设计工具。
从那以后,(通过CAESES)我们为复杂的部件创建了灵活稳定的参数化模型,这使得我们能够优化之前难以设计的模型。
”——Tilmann auf dem Kampe,西门子-大型燃气轮机
-空气动力技术主管。