车架模态分析报告
探讨汽车副车架强度模态分析及结构优化

探讨汽车副车架强度模态分析及结构优化汽车副车架是汽车重要的承载结构之一,在汽车的安全性、舒适性和性能方面起着重要作用。
其强度和刚度对汽车的整体性能有着直接的影响。
对汽车副车架的强度模态分析及结构优化是至关重要的。
本文将就此话题展开探讨。
一、汽车副车架的结构及工作原理汽车副车架是指安装在汽车底盘上的用于支撑底盘组件的结构。
其主要作用是传递车辆的荷载,同时还要满足汽车悬挂系统的需求,以确保汽车在行驶过程中的舒适性和稳定性。
在日常使用中,汽车副车架还要承受来自路面的冲击和振动,并且要能够抵抗车辆制动时产生的扭矩和冲击力。
汽车副车架需要具有足够的强度和刚度,以确保汽车在各种工况下都能够安全可靠地行驶。
二、汽车副车架的强度模态分析1. 强度分析汽车副车架在使用过程中要承受各种不同方向的受载情况,主要包括拉伸、压缩、弯曲和剪切等载荷。
需要对汽车副车架进行强度分析,以确定其在不同工况下的应力分布和变形情况。
强度分析的目的是确认汽车副车架在设计工况下不会出现塑性变形或者破坏,从而保证汽车的安全性和可靠性。
通过有限元分析等方法,可以对汽车副车架进行受力分析,计算其在各种工况下的应力和变形,从而确定其是否满足设计要求。
2. 模态分析模态分析是指通过对汽车副车架进行振动特性的分析,确定其固有频率和振型。
汽车副车架在行驶过程中会受到来自路面的激励力,因此需要对其进行振动分析,以确认其固有频率和振型与激励频率不发生共振,从而避免产生过大的振动响应。
通过模态分析,可以确定汽车副车架的主要振动模态,并评估其对汽车驾驶舒适性和稳定性的影响。
三、汽车副车架的结构优化1. 结构轻量化汽车副车架在保证足够强度和刚度的前提下,需要尽可能减小自身的重量。
轻量化可以降低汽车的整体质量,提高汽车的燃油经济性和加速性能,同时还能减少对环境的影响。
轻量化的方法包括采用高强度、轻质材料、优化结构布局和加强节点等。
2. 结构优化通过有限元分析等方法对汽车副车架进行结构拓扑优化、形状优化和材料优化。
摩托车模态分析实训报告

一、实训背景摩托车作为一种交通工具,其安全性、稳定性和舒适性至关重要。
在摩托车设计过程中,结构模态分析是确保摩托车性能的关键环节。
通过对摩托车进行模态分析,可以预测摩托车在行驶过程中的振动特性,为优化设计提供依据。
二、实训目标1. 掌握摩托车结构模态分析的基本理论和方法;2. 熟悉有限元分析软件的使用;3. 通过实际操作,分析摩托车结构的振动特性;4. 提高动手能力和团队协作能力。
三、实训内容1. 摩托车结构模态分析基本理论(1)模态分析的概念及意义模态分析是研究结构振动特性的重要方法,通过分析结构的模态参数(固有频率、振型等),可以了解结构在受到外部激励时的响应特性。
在摩托车设计中,模态分析有助于预测摩托车在行驶过程中的振动情况,为优化设计提供依据。
(2)有限元方法有限元方法是一种数值方法,将连续体离散成有限个单元,通过求解单元方程组来分析结构的振动特性。
在摩托车结构模态分析中,常用的有限元方法有线性有限元方法和非线性有限元方法。
2. 摩托车结构有限元模型建立(1)摩托车结构几何建模首先,根据摩托车结构图纸,使用CAD软件建立摩托车结构的几何模型。
在建模过程中,应注意模型的准确性和简化程度。
(2)摩托车结构材料属性定义根据摩托车结构材料属性,为几何模型赋予相应的材料属性,如弹性模量、泊松比等。
(3)摩托车结构约束设置根据摩托车实际受力情况,为几何模型设置相应的约束条件,如边界约束、支撑约束等。
3. 摩托车结构模态分析(1)划分网格将几何模型划分为有限元网格,以便进行有限元分析。
(2)求解模态参数使用有限元分析软件求解摩托车结构的模态参数,包括固有频率、振型等。
(3)分析结果分析根据求解得到的模态参数,分析摩托车结构的振动特性,如频率分布、振型等。
四、实训心得体会1. 摩托车结构模态分析的重要性通过本次实训,我深刻认识到摩托车结构模态分析在摩托车设计中的重要性。
通过对摩托车结构进行模态分析,可以预测摩托车在行驶过程中的振动情况,为优化设计提供依据,提高摩托车的性能和安全性。
探讨汽车副车架强度模态分析及结构优化

探讨汽车副车架强度模态分析及结构优化1. 引言1.1 研究背景汽车副车架是汽车重要的结构部件之一,承担着支撑车身、吸收冲击力、传递动力等重要功能。
随着汽车的发展,人们对汽车副车架的要求也越来越高,希望能够在保证结构强度的前提下减轻重量,提高燃油效率和安全性。
现有汽车副车架结构往往存在过多的冗余部分和设计缺陷,导致结构重量过大、强度不足等问题。
对汽车副车架进行强度模态分析和结构优化显得尤为重要。
通过分析副车架在不同工况下的受力特点和振动模态,可以发现潜在的弱点和瓶颈,从而有针对性地进行结构优化,提高其整体性能。
基于以上背景,本文将针对汽车副车架的强度模态分析和结构优化展开研究,旨在为汽车工程领域提供更有效的设计方案和优化策略,促进汽车轻量化、高效化的发展。
1.2 研究意义汽车副车架是汽车重要的结构部件之一,其负责支撑整车重量并承载各种动态载荷。
对汽车副车架进行强度模态分析和结构优化是非常重要的,具有以下几个方面的研究意义:汽车副车架的强度模态分析可以帮助工程师了解其在不同工况下的受力情况,从而预测可能存在的强度问题,为设计提供参考和改进方向。
通过分析副车架的振动模态,可以确定其固有频率和形态,进而评估结构的动力性能和耐久性。
结构优化可以有效地降低副车架的重量,提高结构的刚度和强度,降低振动和噪音,进而改善车辆的行驶性能和安全性。
通过优化设计,可以有效地降低生产成本和能源消耗,提高汽车整体的竞争力。
研究汽车副车架强度模态分析及结构优化还可以推动汽车工程技术的进步和创新,促进汽车制造业的可持续发展。
通过优化设计,可以提高汽车的整体性能和环保性能,满足不断提升的市场需求和法规标准。
对汽车副车架进行强度模态分析和结构优化具有重要的意义和价值。
1.3 研究目的研究目的是为了深入探讨汽车副车架的强度和振动特性,为设计和优化提供理论支持和技术指导。
具体包括以下几个方面的目标:1. 分析副车架的承载能力和抗疲劳性能,找出存在的弱点和瓶颈,为提高车辆整体结构的稳定性和安全性提供依据。
纯电动客车车架结构模态分析与优化设计

纯电动客车车架结构模态分析与优化设计世界各国对环保的日益重视,电动车成为了汽车工业的一个热门领域。
内燃机客车污染的问题被广泛关注,而纯电动客车迅速发展,具有环保、经济等多方面的优势,受到了越来越多人的青睐。
在纯电动客车设计中,车架结构是至关重要的一个组成部分,它决定了车辆整体的强度、刚度、耐久性等参数,因此对电动客车车架结构进行模态分析和优化设计变得越来越必要。
一、电动客车车架结构模态分析车架结构模态分析是对车辆在振动力作用下的固有振动模态进行分析,从而确定车辆在不同振动模态下的固有频率和振动形式。
通过模态分析可以确定车辆关键零部件的固有频率和振动形式,进而进行结构优化设计,充分利用车辆的材料和积弱优势,提高车辆的强度和耐久性。
纯电动客车车架结构模态分析涉及到不同的振动模态,包括两个关键点的弯曲模态、两个支撑点横向平移模态、前后支撑点扭转模态、车体略微弯曲模态等。
通过使用有限元的方式进行车架结构的有限元分析,可以得出模态分析结果。
基于分析结果绘制模态图谱,可以清晰地看到不同模态下车架结构的弯曲振动形态,包括固有频率和振动阶次等参数,为进一步的优化设计提供了基础数据。
二、纯电动客车车架结构优化设计基于模态分析结果,纯电动客车车架结构的优化方案主要有以下几个方面:1.材料选择和加强。
根据模态分析结果,选择优化材料,并加强车架结构的强度和刚度。
由于纯电动客车的整备质量较重,需要用到高强度和高韧性的材料来增加车架的强度,如采用高硬度的钢-铝-铁复合材料,可以提高车架的强度和刚度。
2.设计结构需考虑动态负载。
纯电动客车运行时会产生一定的动态负载,因此在设计车架结构时需要考虑动态负载和振动的变化,保证车架结构的稳定性。
3.改进连接点和结构。
车架结构各个部件通过连接点组合起来,因此需要设计合理的连接点和正确的方式连接各个部件,确保车架结构与车身的耦合效果达到最优。
4.最优化设计。
模态分析结果可以指导最优化设计,根据车架结构的耐久性和运行效果要求得出最优化方案,提高车架质量和安全性。
汽车车架的动力学分析--模态分析

图1-3 一阶弯曲
图1-4 二阶弯曲
图1-5 二阶扭转
图1-6 三阶弯曲
图1-7 前端局部模态
图1-8 弯扭组合
4.3汽车模态分析结果的评价指标
工程结构要具有与使用环境相适应的动力学特性。一辆汽车结构优劣的基本着眼点是在弯曲和扭转方面总的动态性能。如果汽车结构动力学特性不能与其使用环境相适应,即结构模态与激励频率藕合,或汽车子结构之间有模态藕合,都会使汽车产生共振,严重时会使整个汽车发生抖振,车内噪声过大,局部产生疲劳破坏等[5]。模态分析是计算结构的固有频率及其相应振型。结构的固有频率是评价结构动态性能的主要参数,当结构固有频率和工作频率一致时,就会发生共振现象,产生较大的振幅,大大降低寿命。固有振型是发生共振现象时结构的振动形式。
[6]黄华,茹丽妙.重型运输车车架的动力学分析[J].车辆与动力技术,2001.6
6参考文献
[1]余志生.汽车理论[M].北京:清华大学出版社, 1989
[2]丁丽娟.数值计算方法[M].北京:北京理工大学出版社, 1997
[3]王勖成,邵敏.有限元基本原理和数值方法[M].北京:清华大学出版社.1997
[4]傅志方,华宏星.模态分析理论与应用,上海交通大学出版社,2000
[5]《汽车工程设计》编辑委员会.汽车工程手册.试验篇.北京:人民交通出版社.2001.6
4车架模态计算与结果分析
4.1模态分析步骤
对车架进行模态分析主要有以下步骤:
(l)在Pro/E中建立车架的三维模型。
(2)施加边界条件和载荷(对于自由模态不施加约束条件),定义分析类型和求解方法并进行网格划分、提交求解器求解。
(3)提取结果,进行可视化处理,对结束进行分析。
基于HyperWorks的车架模态分析

第"期
张胜兰等: 基于 1234567589 的车架模态分析
Z %% Z
! " # 有限元网格剖分时, 应根据分析的目的并结合模型的特 点, 选择适当的单元类型, 并根据计算机的能力和要求的精度确 定合适的网格大小, 划分网格。 ! $ # 单元质量对有限元计算结果有较大影响。 在有限元网格 划分时, 检查并控制单元的质量参数显得尤为重要。 网格检查内 容一般为是否有重复的节点、 重复的或缺少的单元, 以及高度畸 变或翘曲的单元。单元尺寸应得到控制, 如单元长宽比 ’%&; 单 单元翘曲角’)&(; 单元尺寸应尽量均匀, 要避免特 元内角 1’&(; 别小的单元。在使用 *+,) 单元时, 须分清主次, 即同一个节点 只能丛属于一个主点。 ! - # 施加载荷和边界条件是有限元模型的精华, 这一步需要 的是经验和根据经验做出某种简化或者取舍的勇气。
【 摘要】 这里介绍了 ,-./012034 有限元分析流程, 讨论了建模中应注意的几个问题, 并以某公司 新开发的中巴车车架为研究对象,利用 ,-./012034 建立以壳单元为基本单元的车架有限元分析模 型, 分析了该车架的前七阶固有频率及振型, 为车架响应分析提供了重要的模态参数, 同时也为结构 的改进设计提供了理论依据。 关键词:车架;有限元分析;模态分析;!"#$%&’%() 【 *+),%-.,】 !"#$%&’()* #+) ,-"-#) ).)/)"# 0"0.1*-* /)#+%& %, #+) ,-./012034 *%,#20$)3 &-*(’**)* *)4)$0. 5’)*#-%"* %, AJQ /%&).-"63 *)#* ’7 #+) 0"0.1*-* /%&). %, #+) /-&&.) *-8) 9’* ,$0/) 91 #0:-"6 *+).. ’"-# 0* 90*-( ’"-#3 0"0.18)* #+) ,$0/) ;* ,%$/)$ *)4)" "0#’$0. ,$)5’)"(-)* 0"& (%$$)*7%"& /%&) *+07)*3 *’77.-)* -/< 7%$#0"# /%&0. 70$0/)#)$ ,%$ #+) $)*7%"*) 0"0.1*-* 0"& ,%’"&0#-%" -" #+)%$1 #% -/7$%4) &)*-6" %, #+) 4)+-(.) ,$0/)= /$" 0’%1)2 3%-4$5 3676,$ $8$4$7, -7-8")6)5 9’1-8 -7-8")6)5 !"#$%&’%() 文献标识码:K
车架模态分析思想报告总结
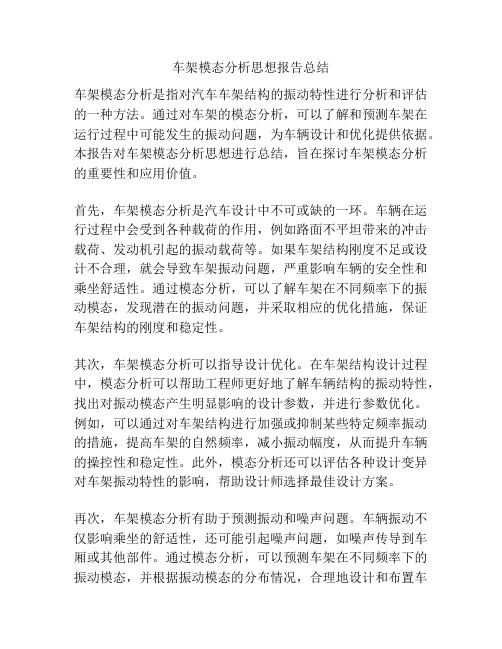
车架模态分析思想报告总结车架模态分析是指对汽车车架结构的振动特性进行分析和评估的一种方法。
通过对车架的模态分析,可以了解和预测车架在运行过程中可能发生的振动问题,为车辆设计和优化提供依据。
本报告对车架模态分析思想进行总结,旨在探讨车架模态分析的重要性和应用价值。
首先,车架模态分析是汽车设计中不可或缺的一环。
车辆在运行过程中会受到各种载荷的作用,例如路面不平坦带来的冲击载荷、发动机引起的振动载荷等。
如果车架结构刚度不足或设计不合理,就会导致车架振动问题,严重影响车辆的安全性和乘坐舒适性。
通过模态分析,可以了解车架在不同频率下的振动模态,发现潜在的振动问题,并采取相应的优化措施,保证车架结构的刚度和稳定性。
其次,车架模态分析可以指导设计优化。
在车架结构设计过程中,模态分析可以帮助工程师更好地了解车辆结构的振动特性,找出对振动模态产生明显影响的设计参数,并进行参数优化。
例如,可以通过对车架结构进行加强或抑制某些特定频率振动的措施,提高车架的自然频率,减小振动幅度,从而提升车辆的操控性和稳定性。
此外,模态分析还可以评估各种设计变异对车架振动特性的影响,帮助设计师选择最佳设计方案。
再次,车架模态分析有助于预测振动和噪声问题。
车辆振动不仅影响乘坐的舒适性,还可能引起噪声问题,如噪声传导到车厢或其他部件。
通过模态分析,可以预测车架在不同频率下的振动模态,并根据振动模态的分布情况,合理地设计和布置车辆的各个部件,以减少振动对车辆结构和乘坐环境的影响,从而降低噪声问题。
最后,车架模态分析可以提高车辆开发的效率和准确性。
传统的震动台试验需要耗费大量时间和资源,并不适用于大规模的车辆开发过程。
而通过有限元分析和模态分析技术,可以在计算机上进行虚拟试验,快速准确地评估车架的振动特性。
这不仅节省了试验成本,也提高了开发效率。
而且,模态分析可以同时考虑多种载荷情况下的振动问题,及时发现和解决潜在问题,保证车辆的安全和可靠性。
车架分析报告

1前言随着旅游事业的发展,出门旅行人员不断增加,人们所携带的行李也随之增多,这就客观地要求整车制造厂提供一些具有大行李仓结构的高档次大客车,而布置大行李仓就需要有全承载式或带有中部桁架结构的半承载式底盘。
本分析报告就基于XXXX客车底盘厂新近开发的XXXX型桁架式底盘,分析了其在不同使用条件下的强度和刚度及结构的动态特性,并据此对其进行结构改进优化设计。
2 有限元模型介绍及简化方法2.1 结构型式该底盘车架主要是由铆焊等方式连接而成的复杂空间结构。
主要分三段,前后段采用槽型截面的大梁,中段采用矩形管组焊方法构成桁架结构,其构件主要是由梁、板组成。
因没有完整的车架图纸,由顾客授权按第一次提供的前后段车架图纸及第二次提供的中部桁架图纸组合成用于分析的车架模型,由于这三段车架局部存在干涉,在建模时将前板簧后吊耳上端横梁前移10mm;后板簧前吊耳上端连接板前端截掉60mm。
具体结构见图2.1三维实体模型。
图2.1三维结构模型2.2 简化方法因前后段车架为成熟结构,本次优化主要是针对中部桁架结构进行分析和优化,而且尽可能保证对原结构不做太大的改动,同时根据常规分析方法本次分析只考虑悬架上部结构,对悬架下部结构不予考虑,并确定了如下几点原则进行模型简化:①、为比较准确地模拟有关应力集中问题,本次采用板壳单元建模,同时也便于对结构进行细化处理;在划分单元时主要采用四边形单元,局部也采用少量三角形单元。
②、在建模过程中略去了一些对分析结果影响很小的工艺孔,以方便网格的划分。
③、对于焊接结构,本文采用两种方法模拟:a.结点重合,即各构件连接处通过单元平滑过渡。
这种方法计算结果连续性好,但建模工作量非常大,且连接部件的单元大小有一定差异,这些均给采用结点重合工作带来了许多不便,本项目在尽可能的情况下使用了此种方法;b.使用MPC单元模拟焊接处,考虑到建模效率,此方法也在局部采用。
2.3 有限元模型通过以上简化方法,本次分析共使用了50671个节点,共48873个单元,其中48636个四边形单元,237个三角形单元,另外还有1188个MPC焊接单元。
- 1、下载文档前请自行甄别文档内容的完整性,平台不提供额外的编辑、内容补充、找答案等附加服务。
- 2、"仅部分预览"的文档,不可在线预览部分如存在完整性等问题,可反馈申请退款(可完整预览的文档不适用该条件!)。
- 3、如文档侵犯您的权益,请联系客服反馈,我们会尽快为您处理(人工客服工作时间:9:00-18:30)。
110ZH车架模态分析报告编制:审核:批准:2006年 3 月 15 日第一章 车架模态分析一、模态分析模态分析是研究结构动力特性一种近代方法,是系统辨别方法在工程振动领域中的应用。
模态是机械结构的固有振动特性,每一个模态具有特定的固有频率、阻尼比和模态振型。
这些模态参数可以由计算或试验分析取得,这样一个计算或试验分析过程称为模态分析。
这个分析过程如果是由有限元计算的方法取得的,则称为计算模态分析;如果通过试验将采集的系统输入与输出信号经过参数识别获得模态参数,称为试验模态分析。
振动模态是弹性结构的固有的、整体的特性。
如果通过模态分析方法搞清楚了某结构在某一易受影响的频率范围内各阶主要模态的特性,就可能预言结构在此频段内在外部或内部各种振源作用下实际振动响应。
因此,模态分析是结构动态设计及设备的故障诊断的重要方法。
由于车架的结构振动会直接引起驾驶室振动,所以分析三轮摩托车振动时,应对车架进行模态和响应分析,优化车架结构,并从工艺设计上保证乘客的安全、舒适。
三轮摩托车车架是一个多自由度弹性振动系统,作用于这个系统的各种激扰力就是使摩托车产生复杂振动的动力源。
引起各种激扰力的因素可概括为两类:一是摩托车行驶时路面不平度对车轮作用的随机激振;二是发动机运转时引起的简谐激振。
如果这些激励力的激振频率和车架的某一固有频率相吻合时,就会产生共振,并导致在车架上某些部位产生数值很大的共振动载荷,影响乘骑的舒适性,而且往往会造成车架有被破坏的危险。
因此,车架的动态设计要求车架具有一定的固有频率和振型,这样才能保证车架具有良好的动态特性。
本次分析主要针对车架进行模态分析,以期预计车架主要模态的固有频率和形状,并借以指导车架改进设计,达到优化摩托车动态性能的目的。
1、模态分析处理本次分析采用自由边界条件下的模态分析(即不添加任何边界支撑和约束力,计算车架的自由模态。
)和添加6个车架的边界条件状态下的模态分析(左右板簧4个,前轮支撑轴承处2个)。
1.1、模型材料参数车架材料为:Q235,有限元分析过程中材料参数为:密度 7829 kg/m^3杨氏模量 196000 N/mm^2柏松比 0.31.2、网格划分由于车架模型较复杂,采用映射网格划分难度较大,所以采用自由网格划分。
元素 十节点四面体全局单元尺寸 30指定材料 Q235网格类型 3D网格适应性 h网格中的单元数 43911网格中的节点数 86966十节点四面体单元的数量 43911层 11.3车架的模态附100ZH车型发动机的参数如下:额定功率 5.6KW额定转速 8000RPM最大功率 9.5KW最大转速 8500±500 RPM最大扭矩 10N•M最大扭矩转速 7500±500 RPM怠速转速 1500±100 RPM在自由模态中,存在六个刚体模态:三个移动模态,三个转动模态。
这六个刚体模态的固有频率都接近0HZ。
在确定模态分析频率范围时,频率下限可定位0HZ;在考虑到实际发动机转速对应的频率和路面激励对应的频率,上限可定为200HZ。
在本次分析中去这个范围内的前十阶模态作为分析结果。
1.4 模态分析结果1.4.1自由模态分析结果1.4.1.1一阶模态分析结果下图为车架一阶模态节点位移放大显示图。
模态频率 最大位移 最小位移43.31 1.006e+000 1.414e-003下图为车架一阶模态应力图。
应力图中黄色标记均是应力集中严重的地方,如果该模态的频率在设计中不可避免,应该在焊接工艺和质量检验过程中予以重视。
1.4.1.2二阶模态分析结果下图为车架二阶模态节点位移放大显示图。
模态频率 最大位移 最小位移48.68 1.003e+000 1.549e-003下图为车架二阶模态应力图。
1.4.1.3 三阶模态分析结果下图为车架三阶模态节点位移放大显示图。
模态频率 最大位移 最小位移52.84 1.060e+000 5.214e-003下图为车架三阶模态应力图。
应力图中黄红色标记均是应力集中严重的地方,如果该模态的频率在设计中不可避免,应该在焊接工艺和质量检验过程中予以重视。
1.4.1.4 四阶模态分析结果下图为车架四阶模态节点位移放大显示图。
模态频率 最大位移 最小位移76.93 1.004e+000 1.014e-003下图为车架四阶模态应力图。
应力图中黄色标记均是应力集中严重的地方,如果该模态的频率在设计中不可避免,应该在焊接工艺和质量检验过程中予以重视。
1.4.1.5 五阶模态分析结果下图为车架五阶模态节点位移放大显示图。
模态频率 最大位移 最小位移85.86 1.005e+000 1.094e-003下图为车架五阶模态应力图。
应力图中黄色标记均是应力集中严重的地方,如果该模态的频率在设计中不可避免,应该在焊接工艺和质量检验过程中予以重视。
1.4.1.6 六阶模态分析结果下图为车架六阶模态节点位移放大显示图。
模态频率 最大位移 最小位移96.43 1.006e+000 9.177e-003下图为车架六阶模态应力图。
应力图中黄色标记均是应力集中严重的地方,如果该模态的频率在设计中不可避免,应该在焊接工艺和质量检验过程中予以重视。
1.4.1.7 七阶模态分析结果下图为车架七阶模态节点位移放大显示图。
模态频率 最大位移 最小位移 109.5 1.021e+000 7.040e-003下图为车架七阶模态应力图。
应力图中黄色标记均是应力集中严重的地方,如果该模态的频率在设计中不可避免,应该在焊接工艺和质量检验过程中予以重视。
1.4.1.8 八阶模态分析结果下图为车架八阶模态节点位移放大显示图。
模态频率 最大位移 最小位移136.9 1.039e+000 5.669e-002下图为车架八阶模态应力图。
应力图中黄色标记均是应力集中严重的地方,如果该模态的频率在设计中不可避免,应该在焊接工艺和质量检验过程中予以重视。
1.4.1.9 九阶模态分析结果下图为车架九阶模态节点位移放大显示图。
模态频率 最大位移 最小位移158.3 1.038e+000 4.064e-003下图为车架九阶模态应力图。
应力图中黄色标记均是应力集中严重的地方,如果该模态的频率在设计中不可避免,应该在焊接工艺和质量检验过程中予以重视。
1.4.1.10 十阶模态分析结果下图为车架十阶模态节点位移放大显示图。
模态频率 最大位移 最小位移184.1 1.039e+000 5.669e-002下图为车架十阶模态应力图。
应力图中黄色标记均是应力集中严重的地方,如果该模态的频率在设计中不可避免,应该在焊接工艺和质量检验过程中予以重视。
1.4.2 带约束条件的模态分析结果增加车架的边界条件状态下的模型如下图。
左右板簧共4个铰链支座,前面马头支撑轴承处1个铰链支座和1个限制垂直方向位移,但不限制旋转的约束条件。
参考平面图如下:1.4.2.1一阶模态分析结果下图为车架一阶模态节点位移放大显示图。
模态频率 最大位移 最小位移 7.891 1.014e+000 4.478e-002下图为车架一阶模态应力图。
应力图中黄色标记均是应力集中严重的地方,如果该模态的频率在设计中不可避免,应该在焊接工艺和质量检验过程中予以重视。
1.4.2.2二阶模态分析结果下图为车架二阶模态节点位移放大显示图。
模态频率 最大位移 最小位移23.23 1.000e+000 2.946e-003下图为车架二阶模态应力图。
应力图中黄色标记均是应力集中严重的地方,如果该模态的频率在设计中不可避免,应该在焊接工艺和质量检验过程中予以重视。
1.4.2.3 三阶模态分析结果下图为车架三阶模态节点位移放大显示图。
模态频率 最大位移 最小位移33.79 1.021e+000 7.222e-004下图为车架三阶模态应力图。
应力图中黄色标记均是应力集中严重的地方,如果该模态的频率在设计中不可避免,应该在焊接工艺和质量检验过程中予以重视。
1.4.2.4四阶模态分析结果下图为车架四阶模态节点位移放大显示图。
模态频率 最大位移 最小位移43.32 1.003e+000 3.362e-002下图为车架四阶模态应力图。
应力图中黄色标记均是应力集中严重的地方,如果该模态的频率在设计中不可避免,应该在焊接工艺和质量检验过程中予以重视。
1.4.2.5五阶模态分析结果下图为车架五阶模态节点位移放大显示图。
模态频率 最大位移 最小位移58.12 1.020e+000 9.492e-003下图为车架五阶模态应力图。
应力图中黄色标记均是应力集中严重的地方,如果该模态的频率在设计中不可避免,应该在焊接工艺和质量检验过程中予以重视。
1.4.2.6六阶模态分析结果下图为车架六阶模态节点位移放大显示图。
模态频率 最大位移 最小位移76.77 1.003e+000 1.123e-003下图为车架六阶模态应力图。
应力图中黄色标记均是应力集中严重的地方,如果该模态的频率在设计中不可避免,应该在焊接工艺和质量检验过程中予以重视。
1.4.2.7七阶模态分析结果下图为车架七阶模态节点位移放大显示图。
模态频率 最大位移 最小位移84.40 1.022e+000 2.614e-003下图为车架七阶模态应力图。
应力图中黄色标记均是应力集中严重的地方,如果该模态的频率在设计中不可避免,应该在焊接工艺和质量检验过程中予以重视。
1.4.2.8八阶模态分析结果下图为车架八阶模态节点位移放大显示图。
模态频率 最大位移 最小位移99.36 1.009e+000 2.760e-003下图为车架八阶模态应力图。
应力图中黄色标记均是应力集中严重的地方,如果该模态的频率在设计中不可避免,应该在焊接工艺和质量检验过程中予以重视。
1.4.2.9九阶模态分析结果下图为车架九阶模态节点位移放大显示图。
模态频率 最大位移 最小位移104.1 1.003e+000 6.285e-003下图为车架九阶模态应力图。
应力图中黄色标记均是应力集中严重的地方,如果该模态的频率在设计中不可避免,应该在焊接工艺和质量检验过程中予以重视。
1.4.2.10十阶模态分析结果下图为车架十阶模态节点位移放大显示图。
模态频率 最大位移 最小位移119.8 1.121e+000 6.729e-003下图为车架十阶模态应力图。
应力图中黄色标记均是应力集中严重的地方,如果该模态的频率在设计中不可避免,应该在焊接工艺和质量检验过程中予以重视。
2、模态分析结果的衡量标准根据分析的结果和经验数据,带边界约束的分析结果比较接近于实际情况,所以选取带边界约束的分析结果进行分析。
对分析结果的衡量主要有两方面:一是考量车架振动对车架造成的疲劳破坏;二是分析车架的振动对影响乘骑的舒适性造成的影响。
十阶模态对应振动频率如下表(单位:HZ)。