设备综合效率(OEE)
OEE设备综合效率
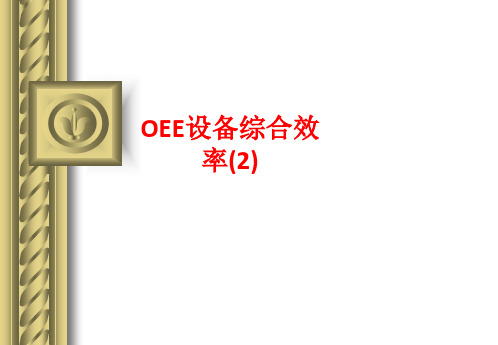
50 0
811 3.0 3.0
0 808
A6
98.63
97.81
72.57
72.73
99.52 71.23
99.63 70.88
Line A
292 318 246880 248178 1298
小时
4320
72
3276
55
1044
17
38
1
0
0
16
00Leabharlann 02200
0
0
0
1006
17
225
4
按照日本工程师学会(JIPE),TPM有如下定义:
(1)以最高旳设备综合效率为效率目旳;
(2)确立以设备一生为目旳旳全系统旳预防维修;
0
0
69
1
57
1
0
0
780
13
4
0
4
0
0
0
776
13
Line A
96.32
77.58
99.48 74.34
速度以有效操作时间为 权重加权计算
时间以合格品产量为权 重加权计算
OEE 新系统
OEE 新系统
OEE 新系统
为何要使用OEE
TPM 能够称为“全员参加旳生产力旳
管理和维护”或“带有日本特色旳美式旳 生产维修”。
OEE 旳时间利用表达图
720 总时间
690 操作时间
计划停 产时间
660 负荷时间 630 利用时间
停产时 间
吃饭时 间
600 净利用时间
效率停 产时间
有价值时间 590
不合格质量 停产时间
设备综合效率OEE计算公式和应用实例
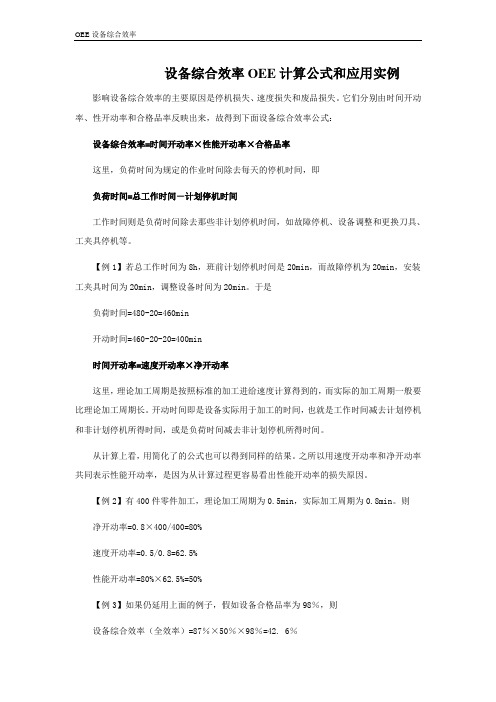
设备综合效率OEE计算公式和应用实例影响设备综合效率的主要原因是停机损失、速度损失和废品损失。
它们分别由时间开动率、性开动率和合格品率反映出来,故得到下面设备综合效率公式:设备综合效率=时间开动率×性能开动率×合格品率这里,负荷时间为规定的作业时间除去每天的停机时间,即负荷时间=总工作时间-计划停机时间工作时间则是负荷时间除去那些非计划停机时间,如故障停机、设备调整和更换刀具、工夹具停机等。
【例1】若总工作时间为8h,班前计划停机时间是20min,而故障停机为20min,安装工夹具时间为20min,调整设备时间为20min。
于是负荷时间=480-20=460min开动时间=460-20-20=400min时间开动率=速度开动率×净开动率这里,理论加工周期是按照标准的加工进给速度计算得到的,而实际的加工周期一般要比理论加工周期长。
开动时间即是设备实际用于加工的时间,也就是工作时间减去计划停机和非计划停机所得时间,或是负荷时间减去非计划停机所得时间。
从计算上看,用简化了的公式也可以得到同样的结果。
之所以用速度开动率和净开动率共同表示性能开动率,是因为从计算过程更容易看出性能开动率的损失原因。
【例2】有400件零件加工,理论加工周期为0.5min,实际加工周期为0.8min。
则净开动率=0.8×400/400=80%速度开动率=0.5/0.8=62.5%性能开动率=80%×62.5%=50%【例3】如果仍延用上面的例子,假如设备合格品率为98%,则设备综合效率(全效率)=87%×50%×98%=42. 6%我们把上面的公式和例子总结成以下的序列,得到(A)每天工作时间=60×8=480min。
(B)每天计划停机时间(生产、维修计划、早晨会议等)=20min。
(C)每天负荷时间=A-B=460min。
(D)每天停机损失=60min(其中故障停机=20min,安装准备=20min,调整=20min)。
oee设备综合效率

OEE设备综合效率
生产效率在制造业中起着至关重要的作用,而OEE(Overall Equipment Effectiveness)设备综合效率是一个关键的评估指标。
本文将探讨OEE设备综合效率的定义、计算方法、影响因素以及提高OEE的策略。
1. OEE设备综合效率的定义
OEE是一个综合性指标,用于衡量设备在生产过程中的综合表现。
它综合考虑了设备的开动率、性能率和质量率,反映出设备的整体运行效率。
2. OEE的计算方法
OEE的计算方法为:OEE = 开动率 x 性能率 x 质量率。
其中,开动率指的是设备实际运行时间占总时间的比例,性能率表示设备运行速度与设计速度之比,质量率表示合格品数量与总产量之比。
3. OEE设备综合效率的影响因素
影响OEE设备综合效率的因素多种多样,包括设备故障率、设备维护计划、操作人员技能等。
有效管理这些因素对提高OEE至关重要。
4. 提高OEE的策略
4.1 定期维护
定期维护设备可以减少故障率,提高设备的可靠性和稳定性,进而提升OEE。
4.2 持续改善
不断优化生产流程和设备设置,引入先进技术和管理方法,可以提高设备的性能率和质量率。
4.3 操作人员培训
提高操作人员的技能和知识水平,可以减少操作失误,提高设备的开动率和生产质量。
结语
OEE设备综合效率是一个关键的生产效率指标,通过科学的管理和技术手段提高设备的OEE,可以提升生产效率、降低生产成本,实现制造业的可持续发展。
有效管理OEE,是企业迈向产业4.0的重要一步。
以上内容仅为理论探讨,实践中具体落地还需根据不同企业的实际情况和需求来进行调整和优化。
综合设备效率OEE

主要内容
为什么引进OEE 如何计算OEE
八大损失及改进措施
主要内容
为什么引进OEE 如何计算OEE
八大损失及改进措施
为什么引进OEE
OEE的概念
OEE(Overall Equipment Effectiveness),即设备 综合效率,最早由日本能率协会顾问公司提出,OEE是用 来考察设备在时间上的利用情况,也考察由于操作和工艺 造成的性能降低和合格品率的问题,更全面地体现了全员 参与关注设备的思想。
1、设备利用率:(计算TEEP时用)
在整个日历时间中去除休止时间后的可利用时间所占的比例。
设备利用率=
日历时间-休止时间
日历时间
×100% =
负荷时间
日历时间 ×100%
总日历时间
计划停机时间(年修、定修、节假日) 非设备因素停机时间(停电、待料)
休止时间
负荷时间(总的可用生产时间)
如何计算OEE
如何计算OEE
OEE计算困惑:性能开动率为何会大于1
1、原则上,理论加工时间不大于实际加工周期,即速 度开动率是不会大于100%的;
2、国内企业经过不断升级改造或为超产拼速度,许 多设备当前加工运转速度超出了设计速度;
3、这样如果仍使用原有数据为基准,则使速度开动 率超过100%,进而使性能开动率超过100%。
为什么引进OEE
OEE和TEEP的总体水平
世界先进企业的OEE水平 80-85%
世界先进企业的TEEP水平 70-75%
74.6-%-77.4% 59.7%-63.5%
69.3%-72.4% 57.2%-60.3%
考察主要设备的 OEE值和TEEP值, 有利于企业对当前 设备管理情况有一 个总体认识。
OEE设备综合效率

OEE的重要性
01
02
03
04
提高生产效率
通过提高设备的OEE,可以减 少设备停机时间、降低故障率,
从而提高生产效率。
降低生产成本
高OEE意味着更少的废品和更 高的产出,从而降低生产成本
机械和工艺性能。
良品率
03
指设备在生产过程中能够生产出合格品的比例,反映了设备的
质量控制能力和产品合格率。
02 影响OEE设备综合效率的 因素
设备故障与维护
设备故障
设备故障是影响OEE的重要因素之一 。定期维护和检查设备,确保其正常 运行,可以减少故障发生的概率。
预防性维护
实施预防性维护计划,定期更换磨损 部件,可以延长设备使用寿命,降低 故障率。
备件管理
建立完善的备件库存管理 制度,确保备件及时供应, 缩短设备维修时间。
优化生产计划与调度
均衡生产计划
合理安排生产计划,确保 设备在不同时间段内负载 均衡,避免设备过度使用 或闲置。
实时调度调整
根据生产实际情况,实时 调整生产计划和调度,确 保设备利用率最大化。
优先级排序
根据产品需求和设备能力, 合理安排生产优先级,提 高关键设备的利用率。
培育改进文化
通过培育改进文化,使员工树立起持续改进的意识,将改进工作融入 日常工作中,形成全员参与的氛围。
06 OEE设备综合效率的实际 应用案例
案例一:某制造企业的OEE提升
总结词
通过实施精益生产,提高设备利用率
VS
详细描述
该制造企业通过引入精益生产理念,优化 生产流程,减少浪费,实现了OEE的提升 。具体措施包括定期维护保养设备、采用 自动化技术减轻工人负担、制定合理的生 产计划等。这些措施有效地提高了设备的 利用率和生产效率,降低了生产成本。
什么是OEE设备综合效率?
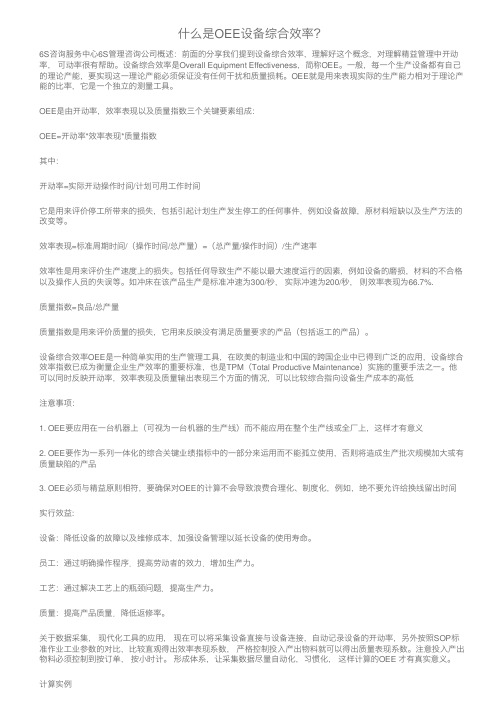
什么是OEE设备综合效率?6S咨询服务中⼼6S管理咨询公司概述:前⾯的分享我们提到设备综合效率,理解好这个概念,对理解精益管理中开动率,可动率很有帮助。
设备综合效率是Overall Equipment Effectiveness,简称OEE。
⼀般,每⼀个⽣产设备都有⾃⼰的理论产能,要实现这⼀理论产能必须保证没有任何⼲扰和质量损耗。
OEE就是⽤来表现实际的⽣产能⼒相对于理论产能的⽐率,它是⼀个独⽴的测量⼯具。
OEE是由开动率,效率表现以及质量指数三个关键要素组成:OEE=开动率*效率表现*质量指数其中:开动率=实际开动操作时间/计划可⽤⼯作时间它是⽤来评价停⼯所带来的损失,包括引起计划⽣产发⽣停⼯的任何事件,例如设备故障,原材料短缺以及⽣产⽅法的改变等。
效率表现=标准周期时间/(操作时间/总产量)=(总产量/操作时间)/⽣产速率效率性是⽤来评价⽣产速度上的损失。
包括任何导致⽣产不能以最⼤速度运⾏的因素,例如设备的磨损,材料的不合格以及操作⼈员的失误等。
如冲床在该产品⽣产是标准冲速为300/秒,实际冲速为200/秒,则效率表现为66.7%.质量指数=良品/总产量质量指数是⽤来评价质量的损失,它⽤来反映没有满⾜质量要求的产品(包括返⼯的产品)。
设备综合效率OEE是⼀种简单实⽤的⽣产管理⼯具,在欧美的制造业和中国的跨国企业中已得到⼴泛的应⽤,设备综合效率指数已成为衡量企业⽣产效率的重要标准,也是TPM(Total Productive Maintenance)实施的重要⼿法之⼀。
他可以同时反映开动率,效率表现及质量输出表现三个⽅⾯的情况,可以⽐较综合指向设备⽣产成本的⾼低注意事项:1. OEE要应⽤在⼀台机器上(可视为⼀台机器的⽣产线)⽽不能应⽤在整个⽣产线或全⼚上,这样才有意义2. OEE要作为⼀系列⼀体化的综合关键业绩指标中的⼀部分来运⽤⽽不能孤⽴使⽤,否则将造成⽣产批次规模加⼤或有质量缺陷的产品3. OEE必须与精益原则相符,要确保对OEE的计算不会导致浪费合理化、制度化,例如,绝不要允许给换线留出时间实⾏效益:设备:降低设备的故障以及维修成本,加强设备管理以延长设备的使⽤寿命。
OEE(设备综合效率)分析与管理ppt课件

故障是冰山的一角
“如果我们问一问为什么会发生这样的情况——为什么、为什么、—— 我们通常能找出问题,以及解决问题的方法。
灰尘、污垢、原料粘附 磨损、偏斜、松动、泄露 腐蚀、变形、伤痕、裂纹 温度、震动、声音等异常
故障
灰尘、污垢、原料粘附 磨损、偏斜、松动、泄露 腐蚀、变形、伤痕、裂纹 温度、震动、声音等异常
OEE衡量的是礁石的大小,说明应该先从哪块暗礁着手处理。
8.OEE可带来的管理效益
1.企业规划: A、可以为企业规划提供客观科學的決策依据。 B、可以为企业提供很多的增值意見和建议。
2.生产管理: A、现场实时数据的收集,建立监控管理系统。 B、对OEE数据分析,规避潜在风险,降低设备六大损失,挖掘设备最大潜能。 C、为企业精益生产管理提供可视化的生产報告。
您是不是正在制造一个不合格产品
早晨机器的启动需要花去一定的时间
二、OEE的定义及开展目的
1.OEE是什么?
OEE代表整体设备效能; 这是一种严格的机器总体性能的衡量手段,揭示时间浪费存在于哪里,统计各种时间浪费,目的在于实现改进。
总时间损失
生产转换
故障停机
传统效率衡量方式只计算了部分时间损失
计划外停机
速度缓慢
设备损坏
设备综合效率(OEE)
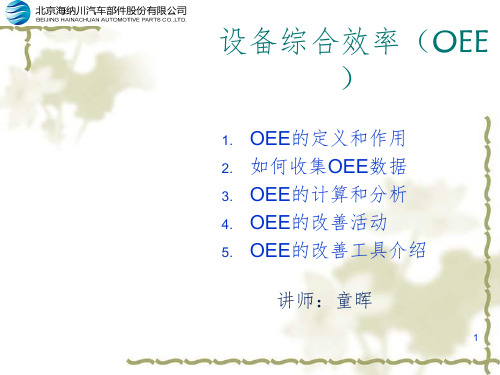
20
生产线OEE的计算
❖时间开动率: 按瓶颈工序设备做基准 停机时间基准(1) 瓶颈工序自身停止 (2) 因为别的工序引起的瓶颈工序停止
❖性能开动率: 按瓶颈工序理论C/T 基准 ❖合格品率: 检查工序或者最终工序为基准,合格 品数量上再排除返工的数量
理论Circle Time的确定原则
① 设备初始说明书上记录的时间 ② 设备初始时说明书上没有记录的理论Circle Time 或 现在运行设备Circle Time 比记录上的理论Circle Time快 的情况时以测定的最佳时间定为基准 ③ 设备已更新改造情况下以改善后的最佳时间定为基准
17
性能开动率计算的建议
检
综 合
维
效 率
修
85
%
人
以 上
员
的
关
系
及
分
改
工
善 活
动
手段分类 正常运行
日常维护
定期维修 状态维修 事后维修 改善维修 (可靠性、 可维修性) 主动维修
实施活动
分工
防止劣化
测知劣化
防止劣化
操作员 点检员
正常操作
复位、调整
清扫、找出潜在缺陷、处理 加油
紧固
低技术要求的日常点检 定期点检
小检修
定期诊断分析
2. 设置和调整:从上一个生产品种生产结束到下一个生产 品种生产出来
3. 空转与短暂停机:设备空转和未预料到的(未计划的)小 于10分钟的设备停机
4. 速度损失:运行的操作速度低于该品种生产时的标准设 计速度所耗费的时间
5. 质量与返工:机器生产不合格品和在线返工不合格品所 花费的时间
- 1、下载文档前请自行甄别文档内容的完整性,平台不提供额外的编辑、内容补充、找答案等附加服务。
- 2、"仅部分预览"的文档,不可在线预览部分如存在完整性等问题,可反馈申请退款(可完整预览的文档不适用该条件!)。
- 3、如文档侵犯您的权益,请联系客服反馈,我们会尽快为您处理(人工客服工作时间:9:00-18:30)。
【实行OEE的意义】
设备:降低设备的故障以及维修成本, 加强设备管理以延长设备的使用寿命。 员工:通过明确操作程序.提高劳动者 的效力.增加生产力。 工艺:通过解决工艺上的瓶颈问题.提 高生产力。 质量:提高产品质量.降低返修率。
中岛清一全员生产维护的五大要素
1、TPM致力于设备综合效率最大化的目标 2、TPM在整个设备一生建立彻底的预防维修体制 3、TPM由各部门共同推行(包括工程、操作、 维修部门) 4、TPM涉及每个雇员,从最高经理到现场工人 5、TPM通过动机管理,即通过自主的小组活动 使PM体制得到推动
正常操作
改 善 活 动
设备综合效率Level评价表
•外注品或其他工程部品迟延納入所引起之待料。 无符合时间 •突发故障引起之停止时间。 停 故障 机 时 换工程调整 •模具、治工具之交換、调整 、试加工之时间。 间 •运转时间-(加工数× C.T) 速 空转.临时停机 度 •设备基准加工速度与实际加工速度之差。 损 速度低减 •加工数×(实际C.T-基准C.T) 失 •正常生产时作出不良品之时间。 不 不良修整 •选別、修理不良品而致设备停止有效稼动之时间。 运 实 良 转 质 损 •生产开始时,自故障小停止至回复运转时,条件之设定、 暖机产率 试加工、试冲等制作不良品之时间。 时 上 失 间 运 有 转 效 •实际产生附加价值的时间。 时 运 价值运转时间 •生产良品所花的时间。 转 间 時 间
OEE数据收集表格的设计
OEE表的填写标准
上班第一时间填写OEE表上的日期、班次、 机器号、设定速度 开班清理、点检、润滑后填写开停车时间 开机至机器正常运行时填写试车时间 运行过程中出现如缺料、小停机、调整等填 写相应项,吃饭停机后要填写吃饭时间 设备故障维修时填写故障项目和停机时间 不得提前填写或推迟填写
OEE要应用在一台机器上(视一条生产 线为一台机器也可)而不能应用在整个 生产车间或全厂上,这样才有意义。
理论速度和实际速度
理论Cycle Time : 设备制造公司提示的或者设备设置后 最佳的状态下单位产品的生产所需要的时间(更新改造 后的设备按当前状态计算)。 实际Cycle Time : 作业环境和限制条件等发生影响后实 际开动时得到的结果上平均使用的开动速度
单品种生产线OEE的计算
设某生产线一个工作日的生产资料如表
工作时 间 1440 计划停 机时间 500 待料停 电时间 30 故障停 机时间 115 调整时 间 12 完成产 返修和废 品数 品件数 203 51 瓶颈标 准时间 3
多批次多品种生产线计算OEE
生产线,产品规格几十种; 每种产品规格,相应的理论加工时间都不相同; 算出每种规格的实际产量所需时间,总和后除以开 动时间作为生产线的性能开动率; 算出每种规格的合格品率,加权平均后作为生产线 的合格品率; 时间开动率不随产品规格变化,无须分产品规格计 算。
开动时间 净开动 时间
=
速 度 损 失
性 能 开动率
=
实际生产量 理论生产量
有价 值开 动时 间
废 品 损 失
合格 品率
=
合格品数量 加工量
产能利用率TEEP=设备利用率×OEE
【OEE】要注意的问题
我们做OEE不是为了在数字和报表中体现我们的 OEE达到了多么要的水平,如果OEE超过了 100%,那就说明我们的理论循环时间设置偏大 (亦即单位时间里的理论产量设置偏低),要么 就是我们在负荷运行(透支设备的未来水平)。 而这两种情况当然是要不得的。
通过6大损失计算OEE
设 备 负荷时间 开动时间 净开动 时间 六大损失 设备故障 安装调整 空转短暂 停 机 速度降低 加工废品 初 期 未 达 产 合格 品率
全效率计算
停 机 损 失
时间 开动率
=
开动时间 负荷时间
速 度 损 失
性 能 开动率
=
实际生产量 理论生产量
有价 值开 动时 间
废 品 损 失
目标
手段分类 防止劣化
实施活动 测知劣化 防止劣化
分 操作员
工 点检员
操 作 人 员 与 点 检 维 修 人 员 的 关 系 及 分 工
正常运行 复位、调整 清扫、找出潜在缺陷、处理 维 护 活 动 设 备 综 合 效 率 85 以 上 % 加油 日常维护 紧固 低技术要求的日常点检 小检修 定期点检 定期维修 定期诊断分析 定期修理 状态维修 不定期检修 状况早期发现准确及时报告 事后维修 突发修理 减轻负荷提高强度,提高可靠性 改善维修 (可靠性、 可维修性) 按故障后果决定适当的维修策略 技术改造以改善设备性能与精度 适当技术措施提高可维修性 主动维修 改变设计,永久消灭故障 故障根源诊断 监测诊断
分厂/车间根据生产实际,提出每种规格产品的新的理论加工 时间; 该理论加工时间应是现阶段稳定生产时基本达不到但能接近 的值; 公司设备部门组织人员对新的理论加工时间进行审核; 一旦确认,即以该理论加工时间作为计算依据; 对于新的技改,相应指标应重新审定; 给出技改创新率的评价参数,关注设备技改进步;
率×性能开动率×合格品率
通过8大损失计算TEEP
设 备 八大损失 计划停机 设备 利用率 时间 开动率
利用率计算
负荷时间 停 机 损 失
=
外部因素 设备故障 安装调整 空转短暂 停 机 速度降低 加工废品 初 期 未 达 产
工作时间 开动时间 开动时间 负荷时间
管 理 指 标
时间 开动率 开动时间 负荷时间 × 100
90% 以上 性能开动率 理论C/T × 生产量 加动时间 × 100
开动时 间
纯开动时间 价 值 加动时间 不良 LOSS
95% 以上 合格品率 良品数量 投入数量 × 100
⑥
(工程物量) 99% 以上
设备综合效率 = 时间开动率 × 性能开动率 × 合格品率 × 100 = 85%以上
OEE = 0.85 * 0.91 * 0.93= 71.9%
生产线OEE的计算
时间开动率: 按瓶颈工序设备做基准 停机时间基准(1) 瓶颈工序自身停止 (2) 因为别的工序引起的瓶颈工序停止 性能开动率: 按瓶颈工序理论C/T 基准 合格品率: 检查工序或者最终工序为基准,合 格品数量上再排除返工的数量
设备损失结构分析图
从6大损失到16大损失
生产活动中的16大损失
1 2 3 8大设备损失 4 5 6 7 8 9 10 设备故障 切换 切刀/ 工夹具的更换 开关机 小停机 速度损失 缺陷/ 返工 工厂计划停产 管理损失 运作损失 生产线管理损失 后勤和运输 测量和调节损失 能源损失 备品备件损失 原材料损失
练习:多批次多品种OEE计算
某车间某设备某日的生产记录如下: 错峰限电停机40分钟;等待计划30分钟;设备卡管1次,停机30分 钟;由于信号控制故障停机40分钟;该日由于当班操作人员小张临时 请假,导致替班人员一人无法照看四台设备,停机60分钟;该日型号 生产四个批次,累计工艺切换和调整时间时间为20分钟;该日早班清 扫设备用时10分钟,相应的产品批次情况为:
型号 A B C D 产能(个/分) 生产数量 63 60 60 79 12600 12000 15000 13790 不良品 180 160 150 188
设备 LOSS的构造和指标
设 备 6大 LOSS
设备1台当故障频度 作 业 时 间 计划 维持 停止 LOSS 速度 LOSS ④ 速度 回转数 10%以上 UP ⑤ 工程 不良 初期 收率 工程别不良率(修理 包含) 0.1以下 初期收率 LOT SIZE 的 90%以上 ③ ② ① 故障 10分以上 – 1回以下 负 荷 时 间 准备 调整 空转 瞬间 停止 准备调整时间 / 回 10分以下 空转,瞬间停止频度 10分以下-3回/月以下 理论 CYCLE TIME实现
案例:单台设备综 合 设 备 效 率 (OEE)计算
例题:
假设有一工厂某设备某班某天工作时间为8小时,其 中用餐、休息时间为1小时,在上线和收工之前的开 会、点检、清扫需费时30分钟,因突发故障而停机时 间为20分钟,而且每天必须换线2次,每次15分钟, 每天必须更换刀具1次,费时10分钟;生产线生产周 期为0.4分钟,当天生产数量为750个产品,其中不 合格品为50个。请计算其总设备效率。
TPM “三全”理念和OEE
全 效 率 全 过 程 全 员
目标
对象/范围
基础
设备的六大损失
1. 2.
3.
4.
5.
6.
设备停机时间损失 设置与调整损失 空转与短暂停机损失 速度降低损失 残次品损失 产量损失(从安装到稳定生产、或班次)
六大损失定义
1. 停机:未预料到的大于10分钟的设备停机,丧失原有功 能或需要更换零部件的时间。 2. 设置和调整:从上一个生产品种生产结束到下一个生产 品种生产出来 3. 空转与短暂停机:设备空转和未预料到的(未计划的)小 于10分钟的设备停机
【实行OEE的意义】
OEE的解决方案能够使得制造商在世界占有一席之地。另外. 可以获得以下几方面效益。 企业规划: A、可以为企业规划提供客观科学的决策依据。 B、可以为企业提供很多的增值意见和建议。 生产管理: 1、能收集到生产线的实时数据,以便建立车间监控管理系 统。 2、能分析/跟踪生产设备的有效利用情况,以便最大化挖掘 设备生产潜力。 3、能分析/跟踪生产上的潜在风险和六大损失,以便降低生 产成本、提高生产力。 4、能为企业精益生产管理提供可视化的生产报告。
时
间
5大人力损失
11 12 13 14
3大原材料与能源损失
成 本
15 16
联合利华世界500强在经过近10年的OEE的管理,2010 年才从12大损失向16大损失迈进。