金属切削原理与机床第三章 金属切削过程的基本理论
《金属切削原理与刀具》知识点总结

《金属切削原理与刀具》知识点总结第一章金属切削原理金属切削原理是金属切削工艺的基础,本章主要介绍了金属切削的基本原理,包括金属切削过程、刀具与被切削材料接触形式、切削能量与热力学原理、切削硬度与切削力的关系等。
第二章刀具材料与结构刀具材料与结构对切削加工的质量和效率有重要影响,本章主要介绍了刀具材料的选择与评价,以及刀具的结构与分类。
刀具材料的选择包括一般刀具材料、质子刀具材料和陶瓷刀具材料等。
第三章切削力分析与测定切削力是切削加工过程中的重要参数,正确定量和测定切削力对于提高切削加工的效率和质量至关重要。
本章主要介绍了切削力的分析与计算方法,以及切削力的测定方法,包括间隙力法、应力传感器法、功率法和应力波法等。
第四章刨削刨削是一种通过切削工具的多齿切削运动将金属材料切割成所需形状和尺寸的加工方法。
本章主要介绍刨削的工艺流程、刨削用刀具和切削参数的选择,以及刨削的切削力分析与测定方法。
第五章车削车削是一种利用车床刀具进行切削的加工方法,广泛应用于金属加工领域。
本章主要介绍了车削的工艺流程、车削刀具的选择和切削参数的确定,以及车削的主要工艺规律和效果评定方法。
第六章铣削铣削是一种通过旋转刀具进行切削的加工方法,广泛应用于金属加工和模具制造等领域。
本章主要介绍了铣削的工艺流程、铣削刀具的选择和切削参数的确定,以及铣削中的刀具磨损与刀具寿命评价方法。
第七章钻削钻削是一种利用钻头进行切削的加工方法,广泛应用于孔加工和螺纹加工等领域。
本章主要介绍了钻削的工艺流程、钻头的选择和切削参数的确定,以及钻削中的刀具磨损与刀具寿命评价方法。
第八章线切割线切割是一种利用细金属丝进行切削的加工方法,主要用于金属板材的切割。
本章主要介绍了线切割的工艺流程、线切割刀具的选择和切削参数的确定,以及线切割中的切削质量评价方法和切削速度对切割效果的影响。
此外,本书还包括金属切削中的润滑与冷却、数控机床中的刀具管理、切削机床中的刀具装夹等内容,为读者提供了全面的金属切削工艺和刀具知识。
哈工大版金属切削原理与刀具课件第3章共23页
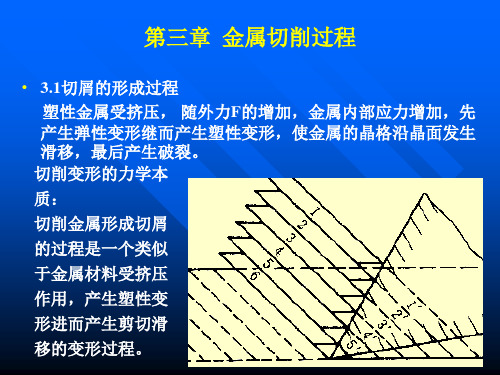
Vc在3~20m/min范围内提高,积屑瘤高度随着增加,刀具实际前角增大, 使剪切角φ增大,故变形系数Λh减小。Vc=20m/min时,Λh值最小。
Vc在20~40m/min范围内提高,积屑瘤逐渐消失,刀具实际前角减小,使 φ减小,Λh增大。在无积屑瘤的切削速度范围,切削速度愈高,变形系数 愈小。
3.3.2切削变形系数
• 切削层经塑性变形后,厚度增加,长度缩小。 • 假设:宽度不变,体积不变。 • 厚度变形系数:切屑厚度hch/切削层厚度hD
h
hch hD
• 长度变形系数:切削层长度LD/切屑长度Lch
L
LD Lch
由体积相等可推出两变形系数相等
•
=
h
=
L
• 变形系数在一定条件下反映金属的平均挤压程度。
纤维化金属粘附在前刀面上,使其流动速度非常低,这种切屑底层流 动速度较其它部分缓慢的现象称为滞流现象,该金属层叫滞流层。刀 屑这种摩擦实质上是切屑底层内的剪切滑移。变形性质为塑性变形。 造成前刀面的磨损和积屑瘤的形成。
3.2.3第三变形区
• 在已加工表面上与刀具后面挤压、摩擦形成的变形区域称为第三变形 区(Ⅲ)。
3.3.3相对滑移与变形系数的关系
Ah
hch
OM
sin( 2
o )
cos(
o )
cos o
ctg
sin o
hD
OM sin
sin
ctg in o
1
Ah cos o
h
(3 3)
1.切削厚度压缩比 h并不等于相对滑移ε
2.当 h =1时,ε并不等于零;即切屑还是
《金属切削原理与刀具》知识点总结
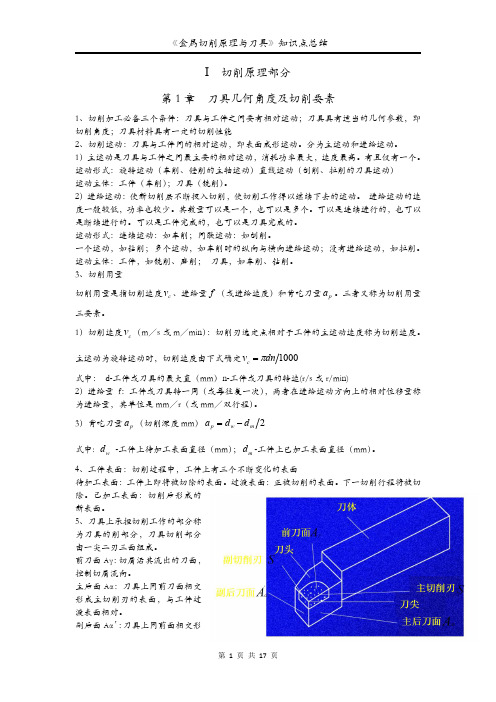
I 切削原理部分第1章刀具几何角度及切削要素1、切削加工必备三个条件:刀具与工件之间要有相对运动;刀具具有适当的几何参数,即切削角度;刀具材料具有一定的切削性能2、切削运动:刀具与工件间的相对运动,即表面成形运动。
分为主运动和进给运动。
1)主运动是刀具与工件之间最主要的相对运动,消耗功率最大,速度最高。
有且仅有一个。
运动形式:旋转运动(车削、镗削的主轴运动)直线运动(刨削、拉削的刀具运动)运动主体:工件(车削);刀具(铣削)。
2)进给运动:使新切削层不断投入切削,使切削工作得以继续下去的运动。
进给运动的速度一般较低,功率也较少。
其数量可以是一个,也可以是多个。
可以是连续进行的,也可以是断续进行的。
可以是工件完成的,也可以是刀具完成的。
运动形式:连续运动:如车削;间歇运动:如刨削。
一个运动,如钻削;多个运动,如车削时的纵向与横向进给运动;没有进给运动,如拉削。
运动主体:工件,如铣削、磨削;刀具,如车削、钻削。
3、切削用量切削用量是指切削速度c v 、进给量f (或进给速度)和背吃刀量p a 。
三者又称为切削用量三要素。
1)切削速度c v (m/s 或m/min):切削刃选定点相对于工件的主运动速度称为切削速度。
主运动为旋转运动时,切削速度由下式确定1000dn v c π=式中:d-工件或刀具的最大直(mm)n-工件或刀具的转速(r/s 或r/min)2)进给量f:工件或刀具转一周(或每往复一次),两者在进给运动方向上的相对位移量称为进给量,其单位是mm/r(或mm/双行程)。
3)背吃刀量p a (切削深度mm)2m w p d d a -=式中:w d -工件上待加工表面直径(mm);m d -工件上已加工表面直径(mm)。
4、工件表面:切削过程中,工件上有三个不断变化的表面待加工表面:工件上即将被切除的表面。
过渡表面:正被切削的表面。
下一切削行程将被切除。
己加工表面:切削后形成的新表面。
5、刀具上承担切削工作的部分称为刀具的削部分,刀具切削部分由一尖二刃三面组成。
金属切削原理基本理论

当刀具作用于切屑层,切削刃由a相对运动至 O时,整个切削单元OMma就沿着OM面发生剪 切滑移;或者OM面不动,平行四边形OMma 受到剪切应力的作用,变成了平行四边形 OMm1a1 。
实际上切屑单元在刀具前面作用下还受到挤 压,因而底边膨胀为Oa2,形成近似梯形的切 屑单元OMm2a2 。
许多梯形叠加起来就迫使切屑向逆时针方 向转动而弯曲。因此也可以说,金属切削过程 是切削层受到刀具前面的挤压后,产生以剪切 滑移为主的塑性变形,而形成为切屑的过程。
一) 切屑的形成过程 我们将切屑形成过程近似地比拟为推挤一叠卡片的形象化模型。
刀具
工
件
切屑形成过程模拟
金属被切削层好比一迭卡片1´、2 ´ 、3 ´ 、4 ´…等,当刀具切入 时这迭卡片被摞到1、2、3、4….的位置。卡片之间发生滑移,这滑 移的方向就是剪切面。
当然卡片和前刀面接触这一端应 该是平整的,外侧是锯齿的、或呈不 明显的毛茸状。
金属切削的基本物理现象包括:切削变形、切削力、切削温度、 刀具磨损与刀具耐用度。本章将针对这些现象进行阐述。
§ 3-1 切削变形
切削过程中的各种物理现象,都是以切屑形成过程为基础的。 了解切屑形成过程,对理解切削规律及其本质是非常重要的,现以塑性 金属材料为例,说明切屑的形成及切削过程中的变形情况。
第Ⅰ变形区 近切削刃处切削层内产生的塑性变形区——剪切滑移变形; 第Ⅱ变形区 与前刀面接触的切屑底层内产生的变形区——挤压变形; 第Ⅲ变形区 近切削刃处已加工表层内产生的变形区——已加工表面变形。
三) 第一变形区内金属的剪切变形
追踪切削层上任一点P,可以观察切屑的变形和形成过程。
当切削层中金属某点P向切削刃逼近,到达点1时,此时其剪切应力达到材 料的屈服强度τ s,故点1在向前移动 的同时,也沿OA滑移,其合成运动 使点l流动到点2。2- 2 ´为滑移量, 当P点依次到达3、4点后,其流动方 向与前刀面平行,不再沿OM线滑移。 OA称为始剪切滑移线,OM称为终 剪切滑移线。
金属切削过程

四、切屑的变形评价
1. 厚度变形系数:
h
h ch hD
式中:hch——切屑厚度
hD ——切削层厚度
金属切削原理及刀具
四、切屑的变形评价
2. 长度变形系数:
l
lc l ch
式中:lc ——切削层长度
lch——切屑长度
金属切削原理及刀具
四、切屑的变形评价
3. 变形系数:
金属切削原理及刀具
第三章 金属切削过程 (the cutting process)
5、晶格的微观变形: 晶粒剪切滑移挤压示意
正常晶格
晶格拉伸
滑移
破坏
金属(material) 切屑(chips)
金属切削原理及刀具
金属切削过程:就是工件的被切削层金属在刀 具前刀面的推移下,沿着剪切面(即滑移面)产生剪 切变形并转变为切屑的过程。
3、“笨刀”切削模型
τ F
此时前角为0,后角也为0,相当于对金属进行正挤压,同样在 正压力的作用下,金属先后产生弹性变形、塑性变形,沿滑移面产 生剪切破坏。特点:一侧是自由的,故金属只能沿一侧分离成为切 金属切削原理及刀具 屑。
第三章 金属切削过程 (the cutting process)
3、理想剪切模型(the ideal cutting model)
F F ns F n F f
F s F ns F 前刀面上受正压力F nF s fF ns F n F f 和摩擦力
Ac
sin cos( 0 )
F s F ns F n F f
Fr
F F ns F n F ss F ns F n F rf
F s F ns F n F
金属切削原理与刀具习题及答案(全)1解析

一.单选题1.磨削时的主运动是( a )A.砂轮旋转运动 B工件旋转运动 C砂轮直线运动 D工件直线运动2.如果外圆车削前后的工件直径分别是100CM和99CM,平均分成两次进刀切完加工余量,那么背吃刀量(切削深度)应为( c )A.10mmB.5mmC.2.5mmD.2mm3.随着进给量增大,切削宽度会(c )A.随之增大B.随之减小 C与其无关 D无规则变化4.与工件已加工表面相对的刀具表面是( d )A.前面 B后面 C基面 D副后面5.基面通过切削刃上选定点并垂直于( c )A.刀杆轴线 B工件轴线C主运动方向 D进给运动方向6.切削平面通过切削刃上选定点,与基面垂直,并且( a )A.与切削刃相切B与切削刃垂直B.C与后面相切D与前面垂直7能够反映前刀面倾斜程度的刀具标注角度为 ( c )A主偏角B副偏角C前角D刃倾角8能够反映切削刃相对于基面倾斜程度的刀具标注角度为( d )A主偏角B副偏角C前角D刃倾角9外圆车削时,如果刀具安装得使刀尖高于工件旋转中心,则刀具的工作前角与标注前角相比会( a )A增大B减小C不变D不定10切断刀在从工件外表向工件旋转中心逐渐切断时,其工作后角( b )A逐渐增大B逐渐减小C基本不变D变化不定二填空题:1工件上由切削刃形成的那部分表面,称为_过渡表面______________.2外圆磨削时,工件的旋转运动为_____进给运动__________运动3在普通车削时,切削用量有_____________)三________个要素4沿__________主刀刃___________方向测量的切削层横截面尺寸,称为切削宽度.6正交平面参考系包含三个相互垂直的参考平面,它们是____基面_____,___切削平面________和正交平面7主偏角是指在基面投影上主刀刃与______进给方向________的夹角8刃倾角是指主切削刃与基面之间的夹角,在___切削平面________面内测量9在外圆车削时如果刀尖低于工件旋转中心,那么其工作前角会_______减小____________10刀具的标注角度是在假定安装条件和____运动__________条件下确定的.三判断题:判断下面的句子正确与否,正确的在题后括号内画”√”,错误的画”×”1在外圆车削加工时,背吃刀量等于待加工表面与已知加工表面间的距离.(√)2主运动即主要由工件旋转产生的运动.( )3齿轮加工时的进给运动为齿轮坯的啮合转动.( √ )4主运动.进给运动和切削深度合称为切削量的三要素.( ) 5进给量越大,则切削厚度越大.( √ )6工件转速越高,则进给量越大( )7刀具切削部分最前面的端面称为前刀面( )8主偏角即主刀刃偏离刀具中心线的角度.( )9前角即前面与基面间的夹角,在切削平面内测量.( )10刀尖在刀刃的最高位置时,刃倾角为正.( √ )四名词解释:1切削运动-----2切削用量-----3切削厚度-----4基面------5前角-----五计算题某外圆车削工序,切削前工件直径为80mm,要求切削后工件直径为78 mm,一次切除余量,假定工件转速为300 r/min,刀具进给速度为60mm/min,试求切削用量三要素及切削面积.(1)已知d w=80mm=0.08m,n=300r/min=5r/s则Vc= πd w n=3.14×0.08×5=1.26(m/s)(2)已知V f=60mm/min则f=v f/n=60÷300=0.2(mm/r)(3)已知dw=80mm,dm=78mm,则ap=1/2(dw-dm)=1/2(80-78)=1(mm)(4)Ac=f×ap=0.2×1=0.2(mm2).刀具材料基本训练1选择题:四个选项中只有一个是正确的,将正确选项前的字母填在题后括号内。
金属切削原理与刀具练习题111
金属切削原理与刀具练习题第一章刀具的基本定义切削运动和切削用量一、填空1.将工件上的被切削层转化成切屑所需要的运动是。
2.切削加工时与的相对运动称为切削运动。
3.切削运动分为和两类。
4.工件在切削过程中形成三个不断变化着的表面,即:表面、表面和表面。
5.切削用量是衡量和大小的参数,包括、三个要素。
6.金属切屑层的参数有、及。
7.车削外圆时,当主、副切削刃为直线,刃倾角为零度,主偏角小于90°时,切削层横截面为形。
8.当刃倾角为0°,主偏角为90°,切削深度为5mm,进给量为0.4mm/r时,切削宽度是mm,切削厚度是mm,切削面积是mm²。
二、判断1.使新的切削层不断投入切削的运动称为主运动。
()2.切削用量就是用来表征切削运动大小的参数,是金属切削加工之前操作者调整机床的依据。
()3.无论哪种切削加工,主运动往往不止一个。
()4.工件的旋转速度就是切削速度。
()5.工件每转一分钟,车刀沿着进给方向运动的距离称为进给量。
()6.由于在切削刃上各点相对于工件的旋转半径不同,所以切削刃上各点的切削速度也不同。
()7.主运动的特征是速度高,消耗的功率大。
()8.进给运动的速度较低,消耗功率小,可以是一个、两个或多个。
()9.进给量是衡量进给运动大小的参数。
()10.车削时工件的旋转运动是主运动;刨削时刨刀的往复直线运动是主运动。
()11.切削面积由切削深度和进给量决定。
()12.切屑层的参数通常在平行于主运动方向的基面内测量。
()三、选择1.在各种切削加工中,()只有一个。
A、切削运动B、主运动C、进给运动2.主切削刃正在切削着的表面称为()表面。
A、已加工B、待加工C、过渡3.车削加工的切削运动形式属于()A、工件转动,刀具移动B、工件转动,刀具往复运动C、工件不动,刀具作回转运动4.()的大小直接影响刀具主切削刃的工作长度,反映其切削负荷的大小。
A、切削深度B、进给量C、切削速度5.切削厚度与切削宽度随刀具()大小的变化而变化。
金属切削原理与刀具复习大纲
2. 各种刀具材料使用于加工什么材料?
第三章 金属切削过程的基本规律
第一变形区:(基本变形区) OA~OM之间的区域,是切削 第二变形区: 第三变形区: 过程中的主要变形区,是切削 切屑底层与前刀面之间的摩擦 工件已加工表面与刀具后刀面之 力和切削热的主要来源。 间的挤压、摩擦变形区域。 变形区。主要影响切屑的变形 主要特征: 造成工件表面的纤维化与加工硬 和积屑瘤的产生。 剪切面的滑移变形 化。
带状切屑
节状切屑
粒状切屑
三、变形程度的表示方法
1.
变形系数:( 切削厚度压缩比Λ h )
h ch h hD
厚度变形系数:
长度变形系数:
lc l lch
h l 1
根据体积不变原理数:
hch OM cos( o ) cos( o ) hD OM sin sin
延长刀具寿命,便于刀具的制造,资源丰富,价格低廉。
2. 常用刀具材料
高速钢 硬质合金 陶瓷
有钨钴类硬质合金、 钨钛钴类硬质合金和 钨钛钽(铌)类硬质 合金。 推广使用新型刀具 材料如涂层刀具、陶瓷 刀具、天然金刚石、聚 晶金刚石、立方氮化硼 等。 能制造结构复杂 的成形刀具
超硬刀具材料
(1)硬质合金的分类
3-3 切削热
一、切削热的来源:
切削层挤 裂变形 前刀面与切 屑摩擦
切削热的分布:
热量的20%∼50%传给刀具→ 刀具磨损、硬度降低
二、影响切削温度的因素分析
1、切削用量对切削温度的影响:Vc →f →ap
vc、f、ap↗ θ ℃↗
x c y
C v f
ap
z
用YT15刀具,切削45#钢时( σ b=75kg/cm2)
金属切削的基本理论
上一页 下一页 返回
3.2 切削变形
相应的轮廓算术平均偏差Rα为
Ra 1 Rz mm
用圆头刀加工时,残留层4的最大高度Rz为:
2.实际粗糙度
Rz f 2 mm
8
实际粗糙度是在理论粗糙度上叠加着非正常因素,例如:积屑 瘤、鳞刺、刀具磨痕和切削振纹等附着物和痕迹,因此,增 大了残留面积的高度值。
刀具几何形状和切削运动对表面粗糙度的影响主要是通过刀 具的主偏角、副偏角、刀尖圆弧半径厂以及进给量对切削后 工件上的残留层高度来体现的。主偏角、副偏角、进给量越 小表面粗糙度越小;刀尖圆弧半径厂越大,表面粗糙度越小。
如图3-8所示,用尖头刀加工时,残留层的最大高度Rz为
Rz
f
mm
cot cot '
教学单元3 金属切削的基本理论
3.1 知识引入 3.2 切削变形 3.3 切削力 3.4 切削热与切削温度 3.5 刀具磨损
教学单元3 金属切削的基本理论
金属切削的基本理论是关于金属切削过程中基本物理现象变 化规律的理论。金属切削过程就是刀具从工件表面上切除多 余的金属,形成切屑和已加工表面的过程。伴随这一过程将 产生一系列物理现象,包括切削变形、切削力、切削温度和 刀具磨损等,而这些现象均以切削过程中金属的弹性、塑性 变形为基础,将直接或间接地影响工件的加工质量和生产率 等。生产实践中出现的积屑瘤、鳞刺、振动等问题,又都同 切削过程中的变形规律有关。因此,了解并掌握这些变化规 律,对分析解决切削加工中出现的问题有着十分重要的意义。
(1)积屑瘤和鳞刺影响钻附在刀刃上的积屑瘤顶端切入加工表 面后使已加工表面粗糙不平。在已加工表面上垂直于切削速 度方向会产生突出的鳞片状毛刺,通常称作鳞刺(如图3-9所 示)。
《金属切削原理》课件
金属切削在机械制造中的应用
加工精度:金属切削可以精确地加工出各种形状和尺寸的零件 加工效率:金属切削可以提高生产效率,缩短生产周期 加工范围:金属切削可以加工各种金属材料,包括钢、铝、铜等 加工质量:金属切削可以保证加工质量,提高产品的可靠性和耐用性
金属切削在航空航天领域的应用
飞机制造:金属 切削用于制造飞 机机身、机翼、 发动机等部件
新材料硬度 高,耐磨性 好,对刀具 寿命和加工 效率产生影 响
新材料热导 率低,切削 过程中热量 难以散发, 对刀具和工 件产生影响
新材料化学 活性强,易 与刀具材料 发生化学反 应,影响刀 具寿命和加 工质量
新材料加工 难度大,对 刀具材料和 加工工艺提 出更高要求
新材料加工 过程中产生 的废料处理 问题,对环 保和资源利 用提出挑战
切削热的ห้องสมุดไป่ตู้生与散失
切削热的产生:刀具与工件之间的摩擦和剪切作用 切削热的散失:通过刀具、工件和切屑的传导、对流和辐射等方式 切削热的影响:影响刀具寿命、工件加工精度和表面质量 切削热的控制:通过优化刀具材料、切削参数和冷却方式等手段
切削表面的形成与变化
切削过程:刀具与工件之间的相对运动 切削力:刀具与工件之间的相互作用力 切削温度:刀具与工件之间的摩擦热 切削表面:刀具与工件之间的接触面
火箭制造:金属 切削用于制造火 箭发动机、燃料 箱、控制系统等 部件
卫星制造:金属 切削用于制造卫 星外壳、太阳能 电池板、天线等 部件
空间站制造:金 属切削用于制造 空间站外壳、太 阳能电池板、生 命支持系统等部 件
金属切削在汽车工业领域的应用
汽车零部件制造:金属切削用于生产汽车发动机、变速箱、底盘等零部件 汽车车身制造:金属切削用于生产汽车车身、车门、车窗等车身部件 汽车模具制造:金属切削用于生产汽车模具,如冲压模具、注塑模具等 汽车维修与保养:金属切削用于汽车维修与保养,如更换损坏的零部件、修复车身损伤等
- 1、下载文档前请自行甄别文档内容的完整性,平台不提供额外的编辑、内容补充、找答案等附加服务。
- 2、"仅部分预览"的文档,不可在线预览部分如存在完整性等问题,可反馈申请退款(可完整预览的文档不适用该条件!)。
- 3、如文档侵犯您的权益,请联系客服反馈,我们会尽快为您处理(人工客服工作时间:9:00-18:30)。
1.切削温度的计算 • (1)每秒产生的切削热计算
q= Fzv (J/s); 式中:q——每秒钟产生的切削 热 Fz——主切削力(N);
v——切削速度(m/s)。
单位切削热计算
2. 切削热的分布
2. 切削热的分布
二、影响切削热传导的主要因素
• (1)工件材料的导热性能
• (2)刀具材料的导热性能
❖积屑瘤的硬度比工件材料的硬度高,能代替
切削刃进行切削,起到保护切削刃的作用。
❖使实际前角增大,切削轻快。
因此,粗加工时可利用积屑瘤。
❖积屑瘤的顶端伸出切削刃之外,而且在不断
地产生和脱落,使切削层公称厚度不断变化,影 响尺寸精度。
❖此外,还会导致切削力的变化,引起振动, ❖并会有一些积屑瘤碎片粘附在工件已加工表
切削液对切削力的影响
•
以冷却为主的水溶液对切削力影响
很小,而润滑性能强的切削油能较明显
地降低切削力,因其可降低摩擦和塑性
变形。
• 其他因素
• 刀具棱面:应选较小宽度,使Fy减小。
• 刀具圆弧半径:增大,切削变形、摩 擦增大,切削力增大。
• 刀具磨损:后刀面磨损增大,刀具变 钝,与工件挤压、摩擦增大,切削力增 大。
通常将合力F分
2.切削力的分解
切削力Fz(Fc)
解为相互垂直的三个
分力:切削力 Fc 、 进给力 Ff 、背向力 Fp 。
总切削力在主运动方向的分力,
大小约占总切削力的80%~
背向力 Fy(Fp)
90% 。Fc消耗的功率最多,约 占总功率的90%左右,是计算
机床切削功率、选配机床电机、
校核机床主轴、设计机床部件
图3- 19 切削速度对切削力的影响
切削速度υc
➢切削速度在5~20m/min区域内增加时,积屑瘤高度
逐渐增加,切削力减小;
➢切削速度继续在20~35m/min范围内增加,积屑瘤逐
渐消失,切削力增加;
➢在切削速度大于35m/min时,由于切削温度上升,摩
擦系数减小,切削力下降。一般切削速度超过90m/min
二、影响切削力的因素
1. 工件材料 2. 切削用量
•影响较大的因素主要是工件材 料的强度、硬度和塑性。
•材料的强度、硬度越高,则屈 服强度越高,切削力越大。
•在强度、硬度相近的情况下, 材料的塑性、韧性越大,则刀具
前面上的平均摩擦系数越大,切
削力也就越大。
进给量f和背吃刀量ap
进给量f和背吃刀量ap增加, 使切削力Fc增加。
• (3)周围介质。
• (4)切屑与刀具的接触时间
• 车削加工时,50%-86%由切屑带走,40%-10% 由车刀传出,9%-3%传入工件,1%传入介质(空
气)。切削速度越高或切削厚度越大,则切屑带
走的热量越多。
•
钻削加工时,28%由切屑带走,14.5%传给
刀具,52.5%传入工件,5%传给周围介质。
金属切削层的变形和切屑
塑性金属切屑形成 过程四个阶段: 弹性变形、 塑性变形、 剪切滑移 切离过程。
切削塑性金属的三个变形区
第一变形区金属的滑移
刀刃钝圆情况下已加工表面的形成过程:
2. 变形系数ξ
➢切屑厚度hch与切削层的厚
度hD之比称为厚度变形系数, 用ξh 表示,ξh = hch/hD ;
➢挤裂(节状)切屑
外形特征:刀屑接触面有裂纹,外表面是锯齿形。
形成条件:采用较低的切削速度和较大的进给量,
刀具前角较小,粗加工中等硬度的钢材料
特点:切削力波动较大,工件表面较粗糙
➢崩碎切屑:在切削铸铁和黄铜等脆性材料时, 切削层金属发生弹性变形以后,一般不经过塑 性变形就突然崩落,形成不规则的碎块状屑片, 即为崩碎切屑。
影响前刀面摩擦系数的主要因素
• 工件材料 • 切削厚度 • 刀具前角 • 切削速度 • 上述四个因素是影响前刀面摩擦系数
的主要因素。
切削厚度
• 切削厚度ac增加时,μ也略为下 降,如10钢的ac从0.1mm增大到 0.18mm,μ从0.74降至0.72。因为ac 增加后正应力也随之增大。在一般 切削速度范围内,前角γ0愈大,则μ 值愈大。因为随着γ0增大,正应力 减小,故μ增加。
小加工硬化倾向。
第三节 切削力
切削过程中,刀具 施加于工件使工件材料 产生变形,并使多余材 料变为切屑所需的力, 称为切削力(cutting force) 。
一、切削力的来源、切削合力及分力、切削功率
1. 切削力的来源
切削力来自于金属切削过程中克服 被加工材料的弹、塑性变形抗力和 刀具与工件及刀具与切屑之间摩擦 阻力。
4. 刀具磨损
5. 切削液
6. 刀具材料
刀具材料与被加工 材料间的摩擦系数,影响到 摩擦力的变化,直接影响着 切削力的变化。
第四节 切削热和切削温度
一、切削热的产生与传导
金属切削过程的三个变形区就是产生切削热 (cutting heat)的三个热源:
1)切屑变形所产生的热量,是切削热的主要来 源; 2)切屑与刀具前刀面之间的摩擦所产生的热量; 3)工件与刀具后刀面之间的摩擦所产生的热量。
面上,增大表面粗糙度和导致刀具磨损。
在精加工时应尽可能避免积屑瘤的产生。
(四)抑制或消除积屑瘤的措施
➢ 采用低速或高速切削,由于切削速度是通过切削温度
影响积屑瘤的,以切削45钢为例,在低速vc<3m/min 和较高速度vc≥60m/min范围内,摩擦系数都较小,故
不易形成积屑瘤;
➢ 采用高润滑性的切削液,使摩擦和粘结减少; ➢ 适当减少进给量、增大刀具前角、减小切削变形; ➢ 适当的热处理来提高工件材料的硬度、降低塑性、减
(二)积屑瘤的形成原因
当切屑沿刀具的前刀面流出时,在一定的温度与压力作 用下,与前刀面接触的切屑底层受到很大的摩擦阻力,致使 这一层金属的流出速度减慢,形成一层很薄的“滞流层”。 当前刀面对滞流层的摩擦阻力超过切屑材料的内部结合力时, 就会有一部分金属粘结或冷焊在切削刃附近,形成积屑瘤。
(三)积屑瘤对起削过程的影响
研究、掌握并能灵活应用金属切削基本理论, 对有效控制切削过程、保证加工精度和表面质量, 提高切削效率、降低生产成本,合理改进、设计 刀具几何参数,减轻工人的劳动强度等有重要的 指导意义。
第一节 金属切削层的变形
一、切屑的形成过程及切屑类型
(一)切屑的形成过程
1.切削变形的力学本质
切削金属形成切 屑的过程是一个类似 于金属材料受挤压作 用,产生塑性变形进 而产生剪切滑移的变 形过程。
时,切削力无明显变化。
➢在切削脆性金属工件材料时,因塑性变形很小,刀
屑界面上的摩擦也很小,所以切削速度υc 对切削力Fc 无明显的影响。
➢在实际生产中,如果刀具材料和机床性能许可,采
用高速切削,既能提高生产效率,又能减小切削力。
3. 刀具几何参数
➢前角的影响: γo↑ →切削变形↓→切削
力↓。(塑性材料)
Q=Q弹+Q塑+Q前+Q后 Q=Q屑+Q工+Q刀+Q介
切削热向切屑、工件、刀具以及周围的介 质传导,使它们的温度上升,从而导致切 削区内的切削温度(cutting temperatures) 上升。
用高速钢车刀及与之相适应的切削速度切削 钢料时,切削热传出的比例是:切屑传出的 热约为50%~86%;工件传出的热约为40%~ 10%;刀具传出的热约为9%~3%;周围介质 传出的热约为1%。
总切削力在垂直于工作 平面方向的分力,Fp不
及计算刀具强度等必不可少的 参数。
消耗功率。但容易使工 件变形,甚至可能产生
进给力Fx (Ff)
振动,影响工件的加工 精度。是进行加工精度 分析、计算工艺系统刚 度以及分析工艺系统振 动时,所必须的参数。
总切削力在进给方向的分力 ,进给力也作功,但只占总 功的1%~5%。是设计、校核 机床进给机构,计算机床进 给功率不可缺少的参数
➢而切削层长度lc与切屑长
度lch之比称为长度变形系数, 用ξl表示,ξl=lc/lch 。
➢变形系数越大,切屑越厚
越短,切削变形越大。
剪切角:剪切角是出自金属切削层产生剪切
滑移的一个特定参数。
• φ=45º-β+γ0 • β——刀和屑界面的摩擦角(º);tanβ=μ;
• μ为刀和屑界面的摩擦系数。当刀和 屑界面出现粘结和滞留层时,μ值(内磨 擦)比一般外摩擦时大得多。
• 金属切削是用刀具从工件表面上切去多余 的金属,形成已加工表面的过程,也是工件的切 削层在刀具前面挤压下产生塑性变形,形成切屑 被切下来的过程。
• 切削过程中的许多物理现象,如切削力、 切削热、刀具磨损等,都与金属的变形及其变 化规律有密切的关系,研究切削过程对保证加 工质量、提高生产率、降低成本和促进切削加 工技术的发展,有着十分重要的意义。
重点是切削变形程度的表示方法、切削热的计算及影 响因素分析、切削力的影响因素、刀具磨损与破损的原因 和刀具耐用度的选择。
难点是切削力与切削热影响因素分析。
第三章 金属切削过程的基本理论
在金属切削过程(cutting process)中,始终存在着 刀具切削工件和工件材料抵抗切削的矛盾,从而产生 一系列物理现象,如切削变形、切削力、切削热与切 削温度以及有关刀具的磨损与刀具寿命、卷屑与断屑 等。
切削速度对摩擦系数的影响
பைடு நூலகம்
切削速度对变形系数的影响
进给量对变形系数的影响
前角对变形系数的影响
前角对摩擦系数的影响
(二)切屑的类型
➢带状切屑
外形特征:它的内表面是光滑的,外表面是毛茸 茸的。 形成条件:用大前角的刀具、较高的切削速度和 较小的进给量,切削塑性材料 优点:切削过程平稳,切削力波动较小,已加工 表面粗糙度较小。 缺点:切屑连续不断,不太安全或可能擦伤已加 工表面,因此要采取断屑措施。