精益生产与现场管理经典
精选精益生产之现场管理
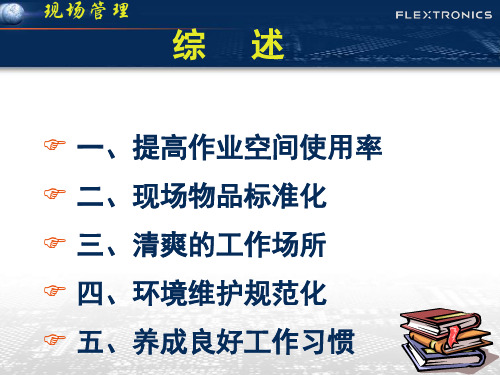
现场管理
总结
现场管理
一、提高作业空间使用率 二、现场物品标准化 三、清爽的工作场所 四、环境维护规范化 五、养成良好工作习惯
演讲完毕,谢谢观看!
(1)宽敞的工作场所变得窄小; (2)架、柜被杂物占据减少了使用价值 (3)寻找物品困难,浪费时间; (4)物品摆放杂乱,导致盘点失准。
现场管理
一、提高作业空间使用率
2、整理的内容
(1)将要和不要的东西分开;
(2)处理不要的东西: 丢弃、出售、循环..
(3)管理要的东西: 根据使用的频率
现场管理
一、提高作业空间使用率
3、整理的要领
(1)对工作场所要全面检查; (2)制定“要”和“不要”的标准; (3)将不要的物品清除出现场; (4)根据使用频率管理需要的物品; (5)制定废弃物处理方法; (6)坚持每日检查
现场管理
一、提高作业空间使用率
整理的要点
将需要和不需要的东西分开;
丢弃或处理不需要的东西;
清除脏污,保持工作场所干净亮丽。 稳定生产品质,消除隐患,减少工业 伤害 1、实施清扫(SEISO)的必要性:
(1)任何污物都可能降低效率,引发意外
(2)清洁之目的在于检查现场;
(3)通过检查,保持现场的最佳状态
现场管理
三、清爽的工作场所
2、清扫的内容:
(1)划定范围,分配工作;
(2)清理场地器材,及时发现潜在问题; (3)执行改善措施,确定清扫重点; (4)建立清洁规则,保持现场整洁。
现场管理
三、清爽的工作场所
3、清扫的实施要领:
(1)建立责任区;
(2)执行例行扫除,清理脏污; (3)调查污染源,排除或隔离; (4)建立清扫基准,确定规范。
精益生产之现场管理
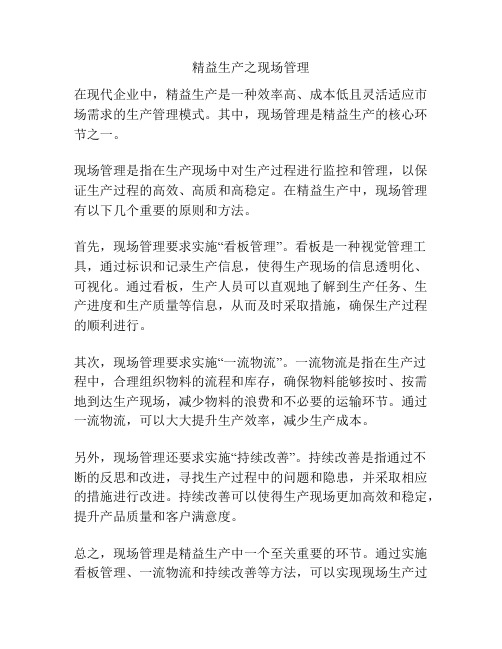
精益生产之现场管理在现代企业中,精益生产是一种效率高、成本低且灵活适应市场需求的生产管理模式。
其中,现场管理是精益生产的核心环节之一。
现场管理是指在生产现场中对生产过程进行监控和管理,以保证生产过程的高效、高质和高稳定。
在精益生产中,现场管理有以下几个重要的原则和方法。
首先,现场管理要求实施“看板管理”。
看板是一种视觉管理工具,通过标识和记录生产信息,使得生产现场的信息透明化、可视化。
通过看板,生产人员可以直观地了解到生产任务、生产进度和生产质量等信息,从而及时采取措施,确保生产过程的顺利进行。
其次,现场管理要求实施“一流物流”。
一流物流是指在生产过程中,合理组织物料的流程和库存,确保物料能够按时、按需地到达生产现场,减少物料的浪费和不必要的运输环节。
通过一流物流,可以大大提升生产效率,减少生产成本。
另外,现场管理还要求实施“持续改善”。
持续改善是指通过不断的反思和改进,寻找生产过程中的问题和隐患,并采取相应的措施进行改进。
持续改善可以使得生产现场更加高效和稳定,提升产品质量和客户满意度。
总之,现场管理是精益生产中一个至关重要的环节。
通过实施看板管理、一流物流和持续改善等方法,可以实现现场生产过程的高效、高质和高稳定,从而使企业能够更好地适应市场需求,提升竞争力。
在现代企业中,精益生产是一种效率高、成本低且灵活适应市场需求的生产管理模式。
其中,现场管理是精益生产的核心环节之一。
现场管理是指在生产现场中对生产过程进行监控和管理,以保证生产过程的高效、高质和高稳定。
在精益生产中,现场管理有以下几个重要的原则和方法。
首先,现场管理要求实施“看板管理”。
看板是一种视觉管理工具,通过标识和记录生产信息,使得生产现场的信息透明化、可视化。
通过看板,生产人员可以直观地了解到生产任务、生产进度和生产质量等信息,从而及时采取措施,确保生产过程的顺利进行。
在实施看板管理的过程中,需要设立不同类型的看板,如生产计划看板、物料投放看板、问题解决看板等。
精益生产现场管理和改善

精益生产现场管理和改善一、前言精益生产现场管理和改善是一种基于精益生产理念的管理方法,旨在推动企业的生产提高效率、降低成本,提高运营质量和客户满意度。
现场管理和改善意味着在生产现场进行措施和方法的制定、实施和监督,以确保生产过程能够完全符合客户需求。
本文将介绍精益生产现场管理和改善的实施内容和步骤,以及相关的案例和经验。
二、现场管理与精益生产1、现场管理现场管理是指在生产现场中针对一系列问题进行改善,包括市场需求、产品设计、生产过程和业务流程等方面。
现场管理需要关注产品质量、生产效率以及客户满意度等核心指标。
现场管理是企业精益生产的重要手段之一。
现场管理的核心理念是不断提高生产效率,降低成本,提升产品质量,并且保证满足客户需求,并对现场的各种问题进行持续改善。
现场管理需要通过实践掌握知识和技能,以帮助工人更好地管理生产现场、实施改进和增强质量导向的知识。
2、精益生产精益生产是一种基于持续改进和客户需求的管理方法,旨在最小化浪费和提高生产效率。
精益生产是一种针对整个生产过程的方法,主要包括从材料采购到产品交付的所有步骤。
精益生产通过优化生产流程、降低生产成本和提高产品质量,帮助企业面对市场竞争的环境。
精益生产强调对现有生产流程进行全面审查,以识别和消除浪费并推动生产流程的优化。
精益生产和现场管理相辅相成,一起推进整个生产过程的管理改进,是现代企业实现竞争优势的不二之选。
三、精益生产现场管理和改善的实施1、现场诊断现场诊断是指使用现场审核的方法和框架来识别现场问题和机会。
现场审核可以通过沟通设施、维修、检验、测试和操作人员等方面,发现现场生产过程中存在的问题和瓶颈。
现场诊断需要引入精益生产的方法和工具,如价值流图(VSM)、现场5S、总质量管理(TQM)以及安全生产等方法和工具,以准确识别生产过程中的浪费和机会点等。
现场诊断还需要通过对业务流程和上下游过程的评估,来发现产生的风险和机会点,以便制定适当的管理改善方案。
精益生产-班组管理-现场管理课件

精益生产-班组管理-现场管理
二、利润是如何产生的
获得利润的两大手法:
手法1: 降低成本
手法2: 增加营业额
通过改善消除浪费 提高附加价值实现
精益生产-班组管理-现场管理
三、价值流程图 ( VSM )
1、信息流 2、实物流 3、某公司从接单到交货的价值流程分析 4、作业:请将你们某个产品进行VSM
任何非必需的东西!
精益生产-班组管理-现场管理
五、工厂中的七大浪费 1、制造过多的浪费 2 、等待的浪费 3、搬运的浪费 4 、加工过程中的浪费 5、动作的浪费 6、生产不良品的浪费 7、库存的浪费
精益生产-班组管理-现场管理
制造过多的浪费
生产多于所需、 快于所需。
精益生产-班组管理-现场管理
等待的浪费
精益生产-班组管理-现场管理
精益思想告诉我们
要做精益生产的英雄, 不要做精益生产的烈士!
分析。
精益生产-班组管理-现场管理
河流与水库
在生产过程中,一定设法使物流、
信息流、价值流让其不断流动,切切 不可停止,停止的东西不能创造附加 价值。
物流
物留
精益生产-班组管理-现场管理
精益思想告诉我们
• 企业经营的目的是制造利润
• 在不同的历史阶段,企业获得利润的 方法是不同的。 售价=成本+利润(计划经济时) 售价—成本=利润(市场经济时) 售价—利润=成本(精益思想 TPS)
精益生产-班组管理-现场管理
精益生产中的重要理念
精益生产-班组管理-现场管理
精益思想告诉我们
• 以客户的需求为中心 • 把下道工序当作我们的客户 • 质量的标准就是零缺陷 • 工作在现场 • 态度决定一切
精益生产生产车间现场管理

精益生产生产车间现场管理何谓现场1.现场包含“现”与“场”两个因素。
2•“现”就是现在,现时的意思,强调的是时间性。
3•“场”就是场所,地点的意思,强调的是区域性。
4•“现”与“场”结合在一起,就是赋予了一定时间的特定区域。
5.对于制造型企业来说,现场就是生产车间。
走进现场1.现场的“三忙”现象: 忙乱:表面上看每个人都很忙,其实,尽在做多余的事情,或者所做的是无功效。
(瞎忙)盲目:由于太忙,人们总是机械地做事,没有工作方向,效率不高。
迷茫:长期盲目的工作导致人们思想麻木,意识迷茫,整天不知自己在干什么,干什么都是糊里糊涂。
2.现场最关注的是产量:分析现状----找出瓶颈---采取措施----解决问题----提高产量(显示能力)3.现场的功能:输出产品。
4.现场管理的核心要素:4M1E人员(Man):数量,岗位,技能,资格等。
机器(Machine):检查,验收,保养,维护,校准材料(Material):纳期,品质,成本方法(Method):生产流程,工艺,作业技术,操作标准环境(Environment): 5S,安全的作业环境现场管理的金科玉律1.当问题(异常)发生时,要先去现场。
2.检查现物(有关的物件)现象(表现出的特征)。
3.当场采取暂行处理措施。
4.发掘真正的原因并将它排除。
5.标准化以防止再次发生。
生产活动的6条基本原则1.后工程是客户作业的好坏由后工程的评价来定不接受不合格,不制造不合格,不传递不合格2.必达生产计划年计划、月计划、每日、每小时按计划生产----生产计划的保证3.彻底排除浪费浪费是指:不做也可以的事,没有也可以的物4.作业的标准化有标准作业书,作业基准书,不是标准化标准化是作出规定,遵守而且改善这个规定,不停地进行改善---遵守---再改善的活动才可称为标准化。
5.有附加价值的工作管理的目的是谋求更大的附加价值(利润)现场要有大局观,辨别生产瓶颈,采取最优对策6.积极应对变化基本要求------决定标准书等作业的基本,养成遵守的习惯先观察------事前收集情报,采取下一步措施掌握实力------ 提咼技能和扩大实力,提咼设备稼动率等现场的日常工作1.现场的质量管理现场如何确保优良品质呢?避免失误的5原则:a、取消此作业b、不要人做c、使作业容易化d、检查e、降低影响2.现场的成本管理降低成本最佳方法,就是剔除过度的资源耗用a、改进质量:工作过程的质量,合理的5Mb、提高生产力以降低成本:不断地改善c、降低库存:流动资金、储藏、搬运、质量隐患、新产品d、缩短生产线:合理的生产线工人e、减少机器停机时间f、减少空间g、现场对总成本降低的作用3.交货期:管理者的主要工作之一4.现场实际作业应把握的内容a、生产作业计划的合理性、生产计划与实际困难、计划调整的影响b、人员状况、员工的技能、缺料设备故障引起的停产、不良品对策及处理c、零部件/工装夹具/生产辅料是否齐全、生产是否正常、工作方法可否改善5.现场的基本方法深入一线、信息畅通、了解生产能力、注意员工状态、时间/动作研究6.现场的注意事项异常处理的制度化、现场教育、解释、工作职责明确、公正评价员工现场管理的实施方法1.日常管理的要点a、重视所有管理项目今天抓品质,明天弄设备?b、决定重点管理项目原则:“不给下个工程或客户添异常”,决定重点项目“应该做怎样的程度为止”,管理水平的设定c、管理的习惯化量化及明确一些日常工作,管理习惯化2.日常管理的进行方法P- D- C- A 管理循环如作业管理,目标为生产计划的达成、生产率的提高。
精益生产现场管理和改善

精益生产现场管理和改善在当今竞争激烈的市场环境中,企业要想生存和发展,就必须不断提高生产效率、降低成本、提高产品质量。
精益生产作为一种先进的生产管理理念和方法,已经被越来越多的企业所采用。
而精益生产现场管理和改善则是精益生产的核心环节,它直接关系到企业的生产效率、产品质量和成本控制。
一、精益生产现场管理的重要性生产现场是企业创造价值的地方,也是各种问题和浪费最容易暴露的地方。
有效的现场管理能够及时发现和解决问题,减少浪费,提高生产效率和产品质量。
1、提高生产效率通过合理的布局、优化的工艺流程和标准化的作业,能够减少生产过程中的等待、搬运和不必要的动作,从而提高生产效率。
2、保证产品质量在生产现场,对生产过程进行严格的监控和检验,能够及时发现和纠正质量问题,保证产品质量的稳定性和一致性。
3、降低成本减少浪费、提高设备利用率、降低库存等,都能够有效地降低生产成本。
4、增强企业竞争力高效的现场管理能够使企业在短时间内满足客户的需求,提高客户满意度,增强企业在市场中的竞争力。
二、精益生产现场管理的主要内容1、 5S 管理5S 是整理(Seiri)、整顿(Seiton)、清扫(Seiso)、清洁(Seiketsu)和素养(Shitsuke)这 5 个词的缩写。
通过实施 5S 管理,能够创造一个整洁、有序、安全的工作环境,提高工作效率和员工的工作积极性。
整理:区分必需品和非必需品,将非必需品清除出工作现场。
整顿:将必需品按照规定的位置摆放整齐,并进行标识,方便取用。
清扫:清除工作现场的灰尘、油污、垃圾等,保持现场干净整洁。
清洁:将整理、整顿、清扫工作制度化、规范化,保持工作现场的良好状态。
素养:培养员工养成良好的工作习惯和行为规范,自觉遵守各项规章制度。
2、标准化作业标准化作业是指对生产过程中的每个作业环节都制定明确的标准,包括作业顺序、作业方法、作业时间、作业质量要求等。
标准化作业能够确保每个员工都按照相同的标准进行操作,提高作业效率和产品质量的稳定性。
精益生产_现场管理
·看板是由订单引起,将订单分类:
A:HR,重复周期性订单(按看板生产,可以做库存) B:LR,重复非周期性订单(按订单生产,不做库存) C:陌生订单
第九个工具——快速切换
·由新乡重夫提出的“单分钟换模。”
·换线改善流程步骤:
1、区分外部和内部换线; 2、内部换线外部化; 3、缩短内部换线的时间; 4、改善外部换线,缩短换线总时间; 5、(改善后)内部、外部换线作业标准化,确保在规定时间内完成 内部换线。引申入5S管理。
嘉兴启晟碳材料有限公司
精益生产
主讲人:龚兵兵
基础篇
1896年,丰田佐吉发明第一台半自动织布机。
1924年,丰田喜一郎发明第一台全自动织布机。 1937年,JIT(just in time)“准时化”观念的正式提出。 1973年,丰田英二、大野耐一完成丰田体系。
1984年,丰田入主美国汽车行业,当年扭亏为盈。
·精益生产的机理是:
员工第一、客户第二、老板第三;
第六个工具—改善
·定义:
改善是KAIZEN;Kai=改变;Zen=好、更好;
·改善的基本理念:
前提员工在各自的工作区域内进行小规模的持续的增值的改变,以 产生积极影响;
·改善是自下而上的,改革是自上而下的。
改善的基础是标准化作业,终点也是标准化作业。 改善基础:节拍时间,作业顺序。
七种浪费
1、过量生产(对在制品的控制); 2、库存(原材料、在制品、成品); 3、运输(无价值的转运); 4、等待(人等机器、机器等人、人等人、不均衡); 5、动作(换模具、换工装的工作时间、不标准动作对时间的浪费); 6、不必要的过程(如进货检验等不增值的行为); 7、次品(返工、返修、报废) 。
精益生产与现场管理经典
人是生产经营活动中最重要的一个要素,其它要素都要通过人的参与才 能发挥作用。
人又是最具创造力的动物,只有坚持以人为本的思想来研究生产系统, 并使每个人都关心和参加改善活动,实施精益才能取得最佳效果。
5.精益原则及实践
1)确定价值
价值是指 ➢在正确的时间, ➢以适当的价格 ➢提供给客户 ➢所需要的产品或服务的能力
制造成本的增加
减少浪费,改善成本的方法
Tools
Loss层别
Loss解析
VA/VE DFSS
Lean BPI/BPR
IE/TPM KAIZEN
QC/QM 6Sigma
总投入
产品设计 LOSS
制造方法 LOSS
制造执行 LOSS
•不必要或不符合产品使用 目的的功能 •加工或组装困难的形状、 尺寸、结构或材质 •过于严格的公差或完整度 •导致加工工时增加的设计
➢因此在实施丰田生产方式改进的时候,如果你已做好80%的准备,就 应付诸行动,在行动的过程中完成另外的20%,这远胜于坐等100%的 准备完毕,因为静待最后的20%所造成的延误根本起不到任何作用。
5)持续渐进与突破变革
稳健发展是丰田的一个显著特点,在这一点上,丰田甚至有一些保守。 某些世界五百强的企业,其发展过程犹如过山车般,一时间声誉鹊起,一时 间又频临破产。而丰田则是用渐进式的改进代替突破式的变革,积小改善为 大改善。大野耐一先生在谈及丰田的发展模式时说过,丰田要向龟兔赛跑中 的乌龟学习,虽然缓慢但是坚忍不拔,最终就能够战胜对手。
➢Overproduction 生产过剩 ➢Correction 改正 ➢Material Movement 材料搬运 ➢Processing 加工过程 ➢Inventory 库存 ➢Waiting 等待 ➢Motion 动作
精益生产生产车间现场管理
精益生产车间现场管理:提升效率与品质的关键策略一、现场布局优化,提升空间利用率1. 合理规划生产线布局,减少物料搬运距离。
根据生产流程,将相关工序紧密排列,降低在制品的移动次数,提高生产效率。
2. 采用流线型设计,确保生产流程顺畅。
通过分析生产过程中的瓶颈环节,优化设备布局,使物料流动更加顺畅。
3. 创设整洁、有序的现场环境。
定期清理现场,消除不必要的物品,确保生产空间宽敞,降低安全事故发生的概率。
二、标准化作业,确保生产稳定性1. 制定详细的生产作业指导书,明确各工序操作规程。
让员工按照标准作业,减少人为失误,提高产品质量。
2. 开展技能培训,提高员工操作水平。
针对不同岗位需求,组织专业培训,提升员工技能,降低生产过程中的不良品率。
3. 落实岗位责任制,强化员工责任心。
明确各岗位职责,确保每位员工都能认真负责地完成本职工作。
三、目视化管理,提高现场透明度1. 利用颜色、标识等手段,对现场进行分区、定置。
使员工一目了然,快速找到所需物品,提高工作效率。
2. 设立看板系统,实时展示生产进度、质量状况。
让员工了解生产现状,便于及时调整生产计划。
3. 建立异常反馈机制,鼓励员工发现问题、解决问题。
通过目视化管理,让问题无处藏身,确保生产顺利进行。
四、持续改善,推动现场管理不断提升1. 开展全员参与的质量管理活动,激发员工潜能。
鼓励员工提出合理化建议,不断优化生产流程。
2. 定期组织现场巡查,查找问题根源。
针对发现的问题,制定改进措施,落实整改。
3. 建立持续改善的长效机制,将现场管理纳入日常工作中。
通过持续改进,不断提升车间现场管理水平。
五、库存控制,减少浪费提高响应速度1. 实施准时制生产(JIT),减少在制品和成品库存。
通过精确的需求预测和订单管理,降低库存成本,提高资金周转率。
2. 推行看板管理系统,实现按需生产。
根据生产线的实际消耗情况,动态调整物料供应,避免过量生产。
3. 建立库存预警机制,及时发现潜在问题。
精益生产与现场管理
精益生产与现场管理近年来,精益生产和现场管理在工业界广泛应用,帮助企业提高生产效率、降低成本、提高质量和客户满意度。
精益生产的核心理念是消除浪费,通过优化生产流程和资源利用,提高价值创造的能力。
精益生产强调以客户需求为导向,实现按需生产和及时交付。
它引入了一系列工具和方法,如价值流图、5S、Kanban等。
其中,价值流图可以帮助企业识别生产流程中的非价值增加的环节,通过消除或优化这些环节,提高效率;而5S是一种组织方法,通过清理、整理、整顿、清洁和素养来改善工作环境,提高工作效率;Kanban是一种生产管理工具,通过控制生产和库存的流动,使生产过程更加平稳。
与此同时,现场管理也是提高生产效率和质量的重要手段。
它强调现场问题解决和持续改善,通过强化现场管理和培养现场管理团队,推动问题的快速解决和根本解决。
现场管理倡导管理者的现场存在和现场领导,管理者要亲自到现场了解问题和推动改善,通过现场作业标准和现场问题解决的方法,实现问题的快速定位和解决。
这两种方法的结合被广泛认为是提高企业绩效和竞争力的有效途径。
精益生产强调流程和资源的优化,现场管理强调问题解决和改善,二者相辅相成。
通过精益生产的优化,现场管理的问题解决更加有依据和效果;而现场管理则促进了精益生产的持续改善和推广。
将二者结合起来,可以实现生产过程的全面管理和优化,推动企业持续改进和发展。
然而,要实现精益生产和现场管理的有效结合,并不是一件容易的事情。
首先,企业需要建立相应的管理体系和文化,营造持续改进的环境;其次,管理者需要具备相应的知识和技能,能够正确运用工具和方法;最后,企业需要给予足够的支持和资源,推动精益生产和现场管理的推广和落地。
总之,精益生产和现场管理作为一种管理方法和思维方式,对于企业提高效率和质量具有重要意义。
通过合理运用精益生产和现场管理的原则和方法,可以优化生产流程、提高产品质量、降低成本、增加客户价值,实现企业的可持续发展。
- 1、下载文档前请自行甄别文档内容的完整性,平台不提供额外的编辑、内容补充、找答案等附加服务。
- 2、"仅部分预览"的文档,不可在线预览部分如存在完整性等问题,可反馈申请退款(可完整预览的文档不适用该条件!)。
- 3、如文档侵犯您的权益,请联系客服反馈,我们会尽快为您处理(人工客服工作时间:9:00-18:30)。
① 多余的仓库 ② 多余的搬运人员 ③ 多余的库管人员 ④ 多余计算机使用
制造成本的增加
精选课件 12
减少浪费,改善成本的方法
Tools
Loss层别
Loss解析
VA/VE DFSS
Lean BPI/BPR
IE/TPM KAIZEN
QC/QM 6Sigma
总投入
产品设计 LOSS
制造方法 LOSS
Unevenness:不均衡
Fluctuations in work schedule 工作计划的波动
Current Process Methods:目前的工艺方法
Using unchallenged and unimproved processes使用没 有挑战性和发展性的工艺方法
• 什么是精益? • 精益生产旨在于生产的各个区域排除浪费,包
括客户关系,产品设计,供应链和工厂管理 • 它的目的是要用更少的人力资源,更少的库存,
更少的时间,更少的空间来生产产品以快速响 应客户的需求,同时以最经济有效的方式来保 证产品的高质量。
精选课件 5
Time-Based Strategies 基于时间的策略
浪费的原因
✓ Overburden超负荷 ✓ Unevenness不均衡 ✓ Process Methods
工艺方法
➢Lack of Employee Involvement 缺乏员工的参与
精选课件 15
Contributors to Waste 造成浪费的原因
Overburden:超负荷
People or machines pushed beyond their capabilities 超出机器或人员能力限度以外
在科技和信息快速发展下,不但要在产品设计、品质、价格、生产力等 方面与对手竞争,更重要的是在时间方面竞争,企业的成败往往决定于时间。
• 缩短从概念形成到产品研发上市的时间
• 缩短接受订单到产品交付的时间
• 缩短反应顾客需求变化的时间
• 缩短产品交货或履行服务所需的时间
➢ 所有的业务都有流程, ➢ 区分增值和不增值的流程步骤, ➢ 持续不懈地消除不增值的活动, ➢ 即是精益的过程。
精选课件
2
1. 何谓精益?
回顾制造业的历史
手工艺
• 只是根据客户规格生产 • 单件生产…每个产品是唯一的 • 变化的质量 • 小库存 • 高成本…为富人生产
大规模
• 互换部件 - Whitney • 劳动力分工 - Taylor • 装配线 - Ford • 低变异 - Ford • 劳工斗争
Frederick Taylor
精选课件
•返工、修理、废弃产生的浪费 13
3. 浪费的识别
Identification and Elimination of Waste 识别和消除浪费
➢ 消除浪费可以有效降低成本 – 精益生产方式的特征
➢ 消除浪费的前提在于是否发现浪费 – 目视管理可以有效发现浪费 – 思维方式的逆转可以有效发现浪费
➢ 所有的员工都必须通过他们的工作来识别和消除浪费
➢ 浪费存在于所有的工作中和机构的所有层次中。
精选课件 14
Types of Waste 浪费的种类
8 Types of Waste:八种浪费
➢Overproduction 生产过剩 ➢Correction 改正 ➢Material Movement 材料搬运 ➢Processing 加工过程 ➢Inventory 库存 ➢Waiting 等待 ➢Motion 动作
精选课件
VA NVA
1 2
3 4
5 6
7 8
Current
当前的
VA NVA
VA
1
2
3
1
4
3
6
4
7
6
8Байду номын сангаас
8
Improved
改进后的
Idea l
理想的
6
精益的衡量标准 流程周期效率=增值时间/总提前期
•精益的流程是指流程中增值时间超出该流程总提前期的25% •见下表:一般的周期效率和世界一流水平的周期效率
精益生产与现场管理
第一讲 精益生产概论 第二讲 设备管理与TPM 第三讲 现场目视管理 第四讲 工作现场的品质管理 第五讲 有效地推进车间管理 第六讲 如何做好现场管理 第七讲 如何做好车间人员管理
精选课件
1
第一讲 精益生产概论
1. 何谓精益? 2. 为什么精益? 3. 浪费的识别 4. 精益意识培养 5. 精益原则及实践
工厂可以随心所欲 的成本(内部)
根
每
个 公 司
材料费
根据制造
能源费
方法的
据 企 业 的 不
都
人工费
发生费用
同
一
而
样
其他
不
同
精选课件 11
5)正是浪费和低效率导致成本恶化
第一次浪费
制
① 设备过剩
② 库存过剩
造
③ 人员过剩
业
第二次浪费
的
生产过多的浪费
浪
费
第三次浪费
认
库存过剩的浪费
识
多余的折旧费 多余的保养费 多余的利息负担 多余的保管费 多余的劳务费
制造执行 LOSS
•不必要或不符合产品使用 目的的功能 •加工或组装困难的形状、 尺寸、结构或材质 •过于严格的公差或完整度 •导致加工工时增加的设计
•机器设备的不合理 •布局路线的不合理 •作业方法的不合理
良品
不良 LOSS
•等待/延迟/交换/故障导致的损失 •作业者熟练度/士气低下导致的损失 •未遵守标准作业导致的效率损失
精选课件 7
2. 为什么精益?
1)企业经营的目的是什么?
制造产品?
制造利润?
企业经营的真正目的在于制造利 润,因此在企业的整个运营过程中, 如何获得最大的利润是企业运行的
头等大事!!!
精选课件 8
2)获得利润的思考方法
在不同的历史阶段,企业对获得利润的思考方法是不同的。 (A)售价=成本+利润(成本主义,计划经济时) (B)利润=售价-成本(售价主义,市场经济时) (C)成本=售价-利润(利润主义,精益思想)
精益Lean
• 高度多样化 • 小批量 • 六西格玛质量 • 参与 / 授权的劳动力
1875 1900 1925 1950精选课19件75 2000 3
From JIT To TPS To Lean
1943 - 1978
1978
S h in g iju ts u
1992
精选课件
1996
Lean
4
典型的精益定义
精选课件 9
3)如何增加经营利润
① 扩大生产规模
– (高投资、高风险)
② 提高价格
– (破坏市场,降低竞争力)
③ 降低成本
– (无需投资、回报丰厚)
利 润
售价
成 本
利
润
售价
成 本
成本降低10%,等于经营规模扩大一倍
精选课件 10
4)成本取决于制造的方法(生产组织和运营)
不能由工厂随心所欲 的成本(外部)