化学镀镍液的稳定性研究
氯化钯实验评价化学镀镍溶液稳定性的方法与优化

氯化钯实验评价化学镀镍溶液稳定性的方法与优化赵涛; 张德忠; 毛祖国【期刊名称】《《电镀与精饰》》【年(卷),期】2019(041)010【总页数】4页(P43-46)【关键词】化学镀; 稳定性; 氯化钯; 稳定系数【作者】赵涛; 张德忠; 毛祖国【作者单位】武汉材料保护研究所有限公司湖北武汉430000【正文语种】中文【中图分类】TQ63化学镀镍溶液的稳定性是指镀液抵抗外界环境和杂质的干扰而不发生分解的能力,直接影响到镀液的使用周期和镀层性能[1]。
氯化钯实验是检验化学镀镍溶液稳定性的快捷方法,其原理是向镀液中加入外来氯化钯,利用还原剂将钯离子还原为钯核微粒,钯核在镀液中作为活性中心,产生催化剂的作用,加速镍离子在钯核上还原沉积,使镀液分解,生成大量黑色金属微粒,镀液开始变黑[2]。
镀液由滴加氯化钯至开始变黑的时间长短能够反映镀液稳定性的好坏,时间越长,稳定性越好。
该方法是由 Konard Parker[3]在 1987 年提出的,后来经过推广和改进,现已被广泛接受[4-8]。
但是该实验方法仍存在一定不足,如氯化钯水溶液难以配置、实验效率低、准确度低等[9-11]。
本文拟通过对氯化钯溶液配置方法、实验方法等进行选择优化,最终得出一种简单、有效、规范的化学镀镍溶液稳定性测试方法。
1 实验方法1.1 镀液成分硫酸镍20 g/L、次磷酸钠30 g/L、氢氧化钠10 g/L、己二酸15 g/L、醋酸钠10 g/L、柠檬酸15 g/L、乳酸20 mL/L、复合稳定剂10 mg/L。
1.2 氯化钯溶液的配置以浓盐酸(质量分数36%)、1000 g/L氯化铵溶液、200 g/L氯化钠溶液三种含Cl-溶液作为氯化钯溶解液,称取0.1000 g氯化钯于烧杯中,在充分搅拌的条件下向烧杯中逐渐加入少量溶解液,记录氯化钯完全溶解时各种溶解液的用量,最后将氯化钯溶液用去离子水定容至1 L,待用。
1.3 氯化钯实验氯化钯时间法:量取化学镀液50 mL至烧杯中,将烧杯浸入60℃的水浴中,待镀液温度恒定后,在搅拌条件下向烧杯中加入1 mL氯化钯溶液,记录镀液自加入氯化钯至开始变黑的时间。
化学镀镍艺配方

Sample
Substructure Sample 1 Sample 2 Sample 3
他们的工作是研究从柠檬酸镀液中电沉积镍一钨合金, 镀液在高温下进行。阴极是一个钢筒,钢筒内部按装上阳极, 仅在钢筒内的表面被镀覆。
4
1 化学镀镍历史(3)
镀层显示出很高的内应力,Brenner和Riddell认为存在柠檬 酸的氧化产物。为了解决这个问题,他们加入了一定量的还 原剂次亚磷酸盐。这时他们发现钢筒的外表除此以外镀上镍, 而且电流效率非常高,达到理论值的120%,这个结果说明 发生了类似电沉积的化学反应---发明化学镀镍。
2.2
羟基乙酸
HOCH2COOH
-
乙二胺
H2NCH2CH2COOH
13.5
丙二酸
HOOOCH2COOH
4.2
焦磷酸
H2O3POPO3H2
5.3
苹果酸
HOOOCH2CH(OH)COOH
3.4
21
4 化学镀镍溶液组成(7)
3) 配位体
丁二酸
水杨酸 酒石酸 苯二甲酸
乳酸 羟基醋酸
甘氨酸
22
4 化学镀镍溶液组成(8)
19
4 化学镀镍溶液组成(5)
3) 配位体
• 化学镀镍溶液经过几个循环(MTO)之后,必须补充镀液 中的配位体,以避免因生成亚磷酸镍而使镀液成糊状。
• 配位体对镀镍磷合金化学镀层耐蚀性影响深刻,同镍离子 生成五元环和六元环鳌合物的配位体所组成的镀液,其镀 层耐盐雾试验性能最佳。一般说来强络合剂比弱络合剂获 得的镀层磷含量高。
4 ) 缓冲剂 由于化学镀镍反应过程中,副产物氢离子的产生,所
以在沉积过程中溶液的pH值会连续下降。缓冲剂能有效 地稳定溶液的pH值。缓冲NaA和H+反应如下:
高稳定性化学镀镍磷合金工艺研究

无论 是零 件或 模 具 , 失 效 或 破坏 皆 自表 面 或 其 亚 表面 开始 , 因而 表 面 强 化技 术 是 材料 工程 中最 活
1 2 镀液 寿命 .
在 1 0mI镀 液 中 , 始 p 4 8 0 初 H: . ±0 1 施 镀 . , 面积 为 0 1d , 覆 时 间 达 2 ( 稀 土 ) 2 . m 镀 2h 无 、条 件
化学镀 Ni — P镀 液配 方很 多 , 并非 所有 的镀 液 但
2 1 镀 层 耐 腐 蚀 性
.
近年来 , 们逐 渐采 用 电化学 方法 , 过测定 镀 人 通
可与稀 土元 素匹配 , 在董 人瑞 等 研 究 的工艺 条 件
基 础上 , 进一 步对 工 艺 条件 、 镀层 性 能 、 金 组 织 进 合
行研 究 。
层 在 Na I 质 中 的腐蚀 电位 评 定耐 蚀性 。本 文 采 C介
用 动 电位 扫描 法测 定 镀层 在 Na I 质 中的极 化 曲 C介
线 来评 定 镀层 的 防腐 蚀 性能 。
图 1是 3 5 Na I p . ) 液 中 动 电 位 法 . C ( H4 5 溶 测 得 的新 鲜 镀 层 阴 、 阳极 极 化 曲 线 。 由实 测 的极 化 曲线 可 观 察 到 , 极 化 时 极 化 电 位 与 电 流 密 度 强 的对 数 成 线 性 关 系 的 塔 菲 尔 区 的 存 在 , 阴 极 变 由 化不 大 和 T fl 数 基 本 相 同 的事 实 表 明 , ae 常 3种 镀 液 得 到 的 镀层 对 阴 极过 程 的 影 响 不 明 显 。而 与此 同时 , 阳极 极 化 却 随 镀 液 不 同 变 化 较 大 。 由 数 据 采 集 器 采 集 的数 据 与计 算 机 联 网 得 到 的 3种 镀 层
碳钢化学镀镍工艺研究

碳钢化学镀镍工艺研究碳钢化学镀镍是一种常用的表面处理技术,能够在碳钢表面形成一层均匀、致密、具有良好耐腐蚀性能的镀镍层,从而提高碳钢的耐蚀性和机械性能。
在碳钢化学镀镍工艺研究中,主要包括前处理、镀液配方、电镀参数和后处理等方面。
首先,碳钢化学镀镍的前处理是确保镍镀层能够牢固附着在碳钢表面的重要步骤。
前处理主要包括去油、除锈和表面活化等。
去油是通过碱性溶剂或表面活性剂去除油、脂和污垢。
除锈通常采用酸性溶液,如盐酸或硫酸,去除碳钢表面的氧化铁皮。
表面活化是通过酸洗或电解方法,去除氧化膜,提高表面粗糙度,以利于镍镀层的附着力。
其次,镀液配方对于碳钢化学镀镍的质量和性能起到关键作用。
镀液的主要成分包括镍盐、酸、络合剂和添加剂等。
镍盐通常选择硫酸镍或氯化镍,作为镀液的镍源。
酸的选择通常是硫酸、硝酸或醋酸等,以调节镀液的pH值。
络合剂是增强镀液中镀镍离子稳定性和镀层均匀性的重要成分。
添加剂的选择通常根据不同的要求,如改善光亮度、增强附着力等。
在电镀参数方面,包括温度、电流密度和镀液搅拌速度等。
温度对镀层的致密性和附着力有重要影响。
温度过低会导致镀层孔隙度增加,附着性下降。
电流密度是控制镀层厚度和均匀性的重要参数。
适宜的电流密度可以提高镀层厚度,但过高会产生应力和孔洞。
镀液搅拌速度会影响镀层的均匀性和光亮度。
最后,碳钢化学镀镍后需要进行适当的后处理,以提高镀层的性能。
后处理主要包括清洗和退火。
清洗可以去除镀液残留和不良杂质,保持镀层的光亮度和一致性。
退火能够消除镀层内部应力,提高其耐腐蚀性能和机械性能。
综上所述,碳钢化学镀镍工艺研究的关键点包括前处理、镀液配方、电镀参数和后处理等方面。
这些步骤的合理选择和控制,能够得到质量良好、性能稳定的碳钢化学镀镍层。
对于碳钢产品的耐蚀性和机械性能提升具有重要意义。
化学镀镍

化学镀镍張正東发表于: 2010-8-18 16:10 来源: 半导体技术天地化学镀化学镀是在无电流通过(无外界动力)时借助还原剂在同一溶液中发生氧化还原作用,从而使金属离子还原沉积在自催化表面表面上的一种镀覆方法。
化学镀与电镀的区别在于不需要外加直流电源,无外电流通过,故又称为无电解镀(Electroless Plating)或“自催化镀”(Autocatalytic Plating)。
所以化学镀可以叙述为一种用以沉积金属的、可控制的、自催化的化学还原过程,其反应通式为:上述简单反应式指出,还原剂Rn+经氧化反应失去电子,提供给金属离子还原所需的电子,还原作用仅发生在一个催化表面上。
因为化学镀的阴极反应常包括脱氢步骤,所需反应活化能高,但在具有催化活性的表面上,脱氢步骤所需活化能显著降低。
化学镀的溶液组成及其相应的工作条件也必须是使反应只限制在具有催化作用的零件表面上进行,而在溶液本体内,反应却不应自发地产生,以免溶液自然分解。
对于某一特定的化学镀过程来说,例如化学镀铜和化学镀镍时,如果沉积金属(铜或镍)本身就是反应的催化剂,那么,这个化学镀的过程是自动催化的,基本上是与时间成线性关系,相当于在恒电流密度下电镀,可以获得很厚的沉积层。
如果在催化表面上沉积的金属本身不能作为反应的催化剂,那么一旦催化表面被该金属完全覆盖后,沉积反应便终止了,因而只能取得有限的厚度。
例如化学镀银时的情形,这样的过程是属于非自动催化的。
化学镀不能与电化学的置换沉积相混淆。
后者伴随着基体金属的溶解;同时,也不能与均相的化学还原过程(如浸银)相混淆,此时沉积过程会毫无区别地发生在与溶液接触的所有物体上。
随着工业的发展和科技进步,化学镀已成为一种具有很大发展前途的工艺技术,同其他镀覆方法比较,化学镀具有如下特点:(1)可以在由金属、半导体和非导体等各种材料制成的零件上镀覆金属;(2)无论零件的几何形状如何复杂,凡能接触到溶液的地方都能获得厚度均匀的镀层,化学镀溶液的分散能力优异,不受零件外形复杂程度的限制,无明显的边缘效应,因此特别适合于复杂零件、管件内壁、盲孔件的镀覆;(3)对于自催化的化学镀来说,可以获得较大厚度的镀层,甚至可以电铸;(4)工艺设备简单,无需电源、输电系统及辅助电极,操作简便;(5)镀层致密,孔隙少;(6)化学镀必须在自催化活性的表面施镀,其结合力优于电镀层;(7)镀层往往具有特殊的化学、力学或磁性能。
稀土对化学镀镍镀速
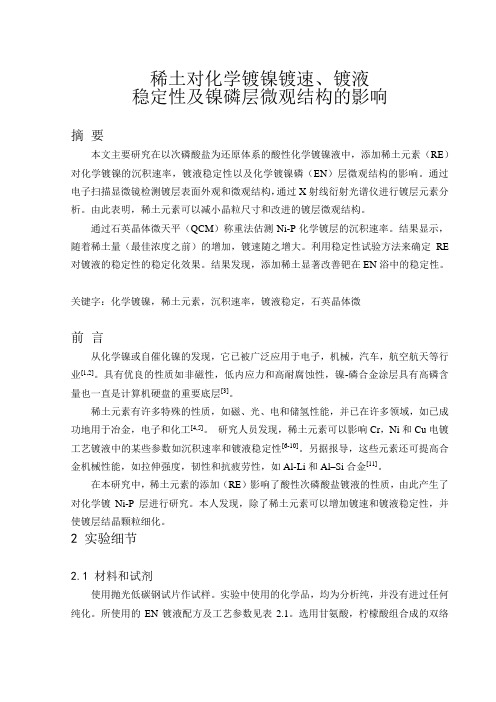
稀土对化学镀镍镀速、镀液稳定性及镍磷层微观结构的影响摘要本文主要研究在以次磷酸盐为还原体系的酸性化学镀镍液中,添加稀土元素(RE)对化学镀镍的沉积速率,镀液稳定性以及化学镀镍磷(EN)层微观结构的影响。
通过电子扫描显微镜检测镀层表面外观和微观结构,通过X射线衍射光谱仪进行镀层元素分析。
由此表明,稀土元素可以减小晶粒尺寸和改进的镀层微观结构。
通过石英晶体微天平(QCM)称重法估测Ni-P化学镀层的沉积速率。
结果显示,随着稀土量(最佳浓度之前)的增加,镀速随之增大。
利用稳定性试验方法来确定RE 对镀液的稳定性的稳定化效果。
结果发现,添加稀土显著改善钯在EN浴中的稳定性。
关键字:化学镀镍,稀土元素,沉积速率,镀液稳定,石英晶体微前言从化学镍或自催化镍的发现,它已被广泛应用于电子,机械,汽车,航空航天等行业[1,2]。
具有优良的性质如非磁性,低内应力和高耐腐蚀性,镍-磷合金涂层具有高磷含量也一直是计算机硬盘的重要底层[3]。
稀土元素有许多特殊的性质,如磁、光、电和储氢性能,并已在许多领域,如已成功地用于冶金,电子和化工[4,5]。
研究人员发现,稀土元素可以影响Cr,Ni和Cu电镀工艺镀液中的某些参数如沉积速率和镀液稳定性[6-10]。
另据报导,这些元素还可提高合金机械性能,如拉伸强度,韧性和抗疲劳性,如Al-Li和Al–Si合金[11]。
在本研究中,稀土元素的添加(RE)影响了酸性次磷酸盐镀液的性质,由此产生了对化学镀Ni-P层进行研究。
本人发现,除了稀土元素可以增加镀速和镀液稳定性,并使镀层结晶颗粒细化。
2 实验细节2.1 材料和试剂使用抛光低碳钢试片作试样。
实验中使用的化学品,均为分析纯,并没有进过任何纯化。
所使用的EN镀液配方及工艺参数见表2.1。
选用甘氨酸,柠檬酸组合成的双络合体系[12]。
电镀液的初始pH 值是用稀NaOH 溶液调节至4.5±0.1。
使用去离子水清洗玻璃器皿。
使用数字控制恒温器(Memert )控制镀液温度为85±1℃(大气环境下)。
实验15光亮镀锌及化学镀镍实验报告
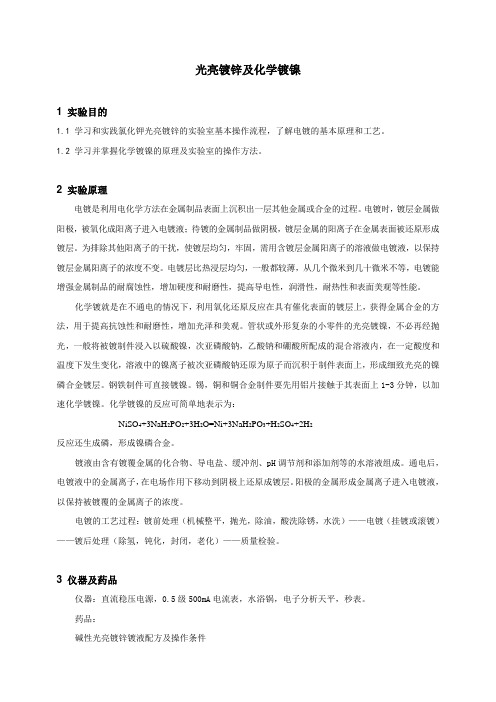
光亮镀锌及化学镀镍1 实验目的1.1 学习和实践氯化钾光亮镀锌的实验室基本操作流程,了解电镀的基本原理和工艺。
1.2学习并掌握化学镀镍的原理及实验室的操作方法。
2 实验原理电镀是利用电化学方法在金属制品表面上沉积出一层其他金属或合金的过程。
电镀时,镀层金属做阳极,被氧化成阳离子进入电镀液;待镀的金属制品做阴极,镀层金属的阳离子在金属表面被还原形成镀层。
为排除其他阳离子的干扰,使镀层均匀,牢固,需用含镀层金属阳离子的溶液做电镀液,以保持镀层金属阳离子的浓度不变。
电镀层比热浸层均匀,一般都较薄,从几个微米到几十微米不等,电镀能增强金属制品的耐腐蚀性,增加硬度和耐磨性,提高导电性,润滑性,耐热性和表面美观等性能。
化学镀就是在不通电的情况下,利用氧化还原反应在具有催化表面的镀层上,获得金属合金的方法,用于提高抗蚀性和耐磨性,增加光泽和美观。
管状或外形复杂的小零件的光亮镀镍,不必再经抛光,一般将被镀制件浸入以硫酸镍,次亚磷酸钠,乙酸钠和硼酸所配成的混合溶液内,在一定酸度和温度下发生变化,溶液中的镍离子被次亚磷酸钠还原为原子而沉积于制件表面上,形成细致光亮的镍磷合金镀层。
钢铁制件可直接镀镍。
锡,铜和铜合金制件要先用铝片接触于其表面上1-3分钟,以加速化学镀镍。
化学镀镍的反应可简单地表示为:NiSO4+3NaH2PO2+3H2O=Ni+3NaH2PO3+H2SO4+2H2反应还生成磷,形成镍磷合金。
镀液由含有镀覆金属的化合物、导电盐、缓冲剂、pH调节剂和添加剂等的水溶液组成。
通电后,电镀液中的金属离子,在电场作用下移动到阴极上还原成镀层。
阳极的金属形成金属离子进入电镀液,以保持被镀覆的金属离子的浓度。
电镀的工艺过程:镀前处理(机械整平,抛光,除油,酸洗除锈,水洗)——电镀(挂镀或滚镀)——镀后处理(除氢,钝化,封闭,老化)——质量检验。
3 仪器及药品仪器:直流稳压电源,0.5级500mA电流表,水浴锅,电子分析天平,秒表。
油田设备化学镀镍镀液稳定性及废液处理研究

其 中 : z/ 为 主 盐 与 还 原 剂 的 浓 度 比 ; +c k为 络 合 剂 种 类 及 浓 度 } s为 稳 定 剂 种 类 及 浓 度 } a为 加 速 剂 种 类 及 浓 度 } h为 缓 冲 剂 种 类 及 浓 度 ; W表 面活性 种 类及 浓 度 。 ① 主 盐 和 还 原 剂 的 浓 度 对 镀 液 的 稳 定 性 有 影 响 , 其 是 二 者 的 浓 度 比更 重 要 。 究 结 果 表 明 最 佳 尤 研 硫 酸 镍 浓 度 为 2 ~ 3 g 1次 亚 磷 酸 钠 浓 度 为 2 ~ O O /, 5 3 g 1 主 盐 与 还 原 剂 的 最 佳 摩 尔 配 比 为 0 3 O 5。 5 /, .~ . ② 络 合 剂 对 镀 液 稳 定 性 影 响 至 关 重 要 。 不 同 种 类 的 络 合 剂 与 用 量 直 接 决 定 了 镀 液 抗 自 然 分 解 的 能 力 , 其是 对 亚磷 酸根 的 容忍 能力 。 理配 比的双 络 尤 合
份 的J , x值 范 围 。
关 键 词 : 学镀 } 定 性 } 液 处 理 化 稳 废
1 引言
盐 酸 腐 蚀 在 大 多 数 炼 油 装 置 中 都 会 发 生 , 别 特 是 当 它 与 含氯 化 物 的氨 或 胺 盐 的沉 淀 共 同作 用 时 , 会 更 容 易发 生腐 蚀 。 且 大 多数 原 油 中存在 硫化 物 , 而 这 些 硫 化 物 本 身 有 腐 蚀 性 , 分 解 后 转 化 成 硫 化 氢 热 后 也 会 产 生 腐 蚀 。 时 原 油 中 也 含 有 环 烷 酸 , 其 浓 同 在 度 较 低 时 多 产 生 点 蚀 , 度 较 高 时 则 产 生 槽 状 或 沟 浓 状 腐 蚀 , 且 腐 蚀 速 度 更 快 “ 。化 学 镀 层 因 其 具 有 较 而 强 的 耐 磨 和 抗 蚀 性 在 油 田及 化 工 生 产 中 得 到 较 为 广 泛的 应用 。与 电镀相 比化学 镀 主要 具 有 以下几 方面 优点 : ① 良好 的 均 镀 能 力 。 化 学 镀 镍 可 以 克 服 镀 件 几 何 形 状 复 杂造 成 的 电镀 层 不 均 匀 等 缺 陷 , 其是 对 尤 有 深 槽 , 孔 的零 件 施 镀 更 显 出 优 势 } 深 ② 化 学 镀 镍 层 不仅 硬 度 高 , 可 以通 过 热 处理 还 调 整 再 行 提 高 , 耐 磨 性 良好 , 某  ̄ T 故 在 - Y面 可 以 替 代 硬 铬 使用 , 学 镀 镍 层 良好 地 兼备 了耐 蚀 与 耐 磨性 化
- 1、下载文档前请自行甄别文档内容的完整性,平台不提供额外的编辑、内容补充、找答案等附加服务。
- 2、"仅部分预览"的文档,不可在线预览部分如存在完整性等问题,可反馈申请退款(可完整预览的文档不适用该条件!)。
- 3、如文档侵犯您的权益,请联系客服反馈,我们会尽快为您处理(人工客服工作时间:9:00-18:30)。
众所周知,在电镀镍时金属离子的不足是靠阳极镍溶解来补充的,而化学镀镍时,每时每刻
镍离子的消耗若无处补给,镀液会逐渐不平衡,需要加镍盐补充镍离子的不足。
随着化学镀的进行,还原剂的含量也会发生变化,一方面反应过程消耗还原剂,另一方面还
原剂也会被氧化生成有害物质。
例如以次磷酸盐作还原剂的酸性镀液,次磷酸盐被氧化生成
亚磷酸盐是不可避免的,而亚磷酸盐对化学镀镍是有害物质。
此外,镀液尚有自然分解、PH
值随时改变等问题。
因此,可以说化学镀镍液从一开始使用就存在自然分解、值变化、主盐浓度减少、还原剂浓
度减少诸多问题,随时影响化学镀镍液的稳定性。
这也可以说是化学镀镍工艺难以掌握的原
因所在。
以上是说明化学镀镍液不稳定的根源,具体地分析镀液不稳定的原因,还与镀液的
配制方法、各成分比例、镀前工件处理、操作工艺条件等因素有关。
1.关于镀液自然分解现象
化学镀镍液使用与不使用都会发生自然分解现象,出现这种情况若不及时采取有效措施,则
自然分解会越来越快。
自然分解的表面现象是镀液产生大量气泡,严重时溶液会呈现泡沫状,这时会使镀层发黑,或镀层生成许多形状不规则的黑色粒状沉淀物,使生产无法进行下去。
除了镀液生成气泡外,镀液的颜色开始变淡。
因此当发现镀液生成气泡、颜色变淡,这就显
示了镀液已发生自然分解,应尽快进行处理,如补加络合剂等,使其不再继续分解。
2.镀液的成分配比影响
(1)次磷酸盐浓度的影响如果镀液中次磷酸盐浓度过高,虽可以提高沉积速度,但会造成镀液的自然分解,尤其对于酸性镀液,且当 PH值偏高时,镀液自然分解的趋势就会愈严重。
当
次磷酸盐浓度过高时,加速了镀液内部的还原作用,这时如存在其他不稳定因素(局部温度过高、在加热器附近或有混浊沉淀物等)特别容易诱发镀液自然分解。
此外,溶液中次磷酸盐含量过高,容易产生亚磷酸盐的沉淀。
因为当次磷酸盐含量过高时且
值也偏高时,亚磷酸镍的允许浓度(称为极限浓度,高于此浓度即会生成沉淀)就大大降低,
在较低浓度下就会发生沉淀,使镀液处于不稳定状态。
(2 )镍盐浓度的影响如果溶液中镍盐浓度偏高,且 PH值也较高时,就容易生成亚磷酸镍和氢氧化镍沉淀,使溶液混浊,极易发生自发分解现象。
(3)络合剂含量的影响络合剂应选择合适,既能充分地络合镍离子,又能提高镀液中亚磷酸镍的沉淀点。
试验表明,当镀液中镍盐浓度、温度、PH值一定时,亚磷酸镍在溶液中的溶度积也是一定的。
这时如果溶液中络合剂浓度偏低,同样能降低亚磷酸镍的允许浓度,使镀液不
稳定。
(4) 值调整剂含量的影响在镀液中其他成分不变的条件下,如果过高地增加值调整剂的浓度,容易产生亚磷酸镍及氢氧化镍沉淀;同时也易加速还原剂的分解。
亚磷酸盐的允许浓度与溶液值有着密切的关系,石桥等人试验结果证明,当PH=4.0时,极
限浓度为 0.25mol/L; PH=5.0时,极限浓度为0303mol/L ; PH=6时极限浓度为0.003mol/L。
说
明PH值越高,亚磷酸盐浓度的允许极限浓度越低。
因此,可以看出,当酸性镀液的pH值高于5后,镀液稳定性变坏。
在酸性镀液加入乳酸,在碱性镀液加入柠檬酸盐,不仅对镍离子有络合作用,而且有提高亚
磷酸盐极限浓度的作用。
3.镀液配制方法的影响
还原剂:次磷酸盐在配制时加得过快或未完全溶解,都会使局部的次磷酸盐含量过高,而产
生亚磷酸镍沉淀,造成镀液不稳定。
加碱过快:配制溶液时或生产过程中调值时,加碱时不能过快,否则会使镀液局部的值过高,容易产生氢氧化镍沉淀。
配制溶液时的顺序:配制溶液时顺序不当也会造成镀液不稳定,前面已论述按一定顺序加配
溶液的重要性。
镀前处理的影响:镀前处理是电镀工作者十分重视的工序,它不仅影响电镀件的质量,同时
还会影响到镀液的稳定性。
因为将镀前处理的酸性或碱性溶液带入镀槽,会污染镀液,并会
使化学镀镍液的pH值发生变化。
如果将其他具有催化活性的金属杂质带入镀液,就可能成
为溶液自发分解的触发剂。
因此镀件在进入镀槽前必须清洗干净,尤其是需要用钯盐活化后
才能进行化学镀镍的非金属零件,若未将钯金属离子清洗干净而将其带入镀槽,将在其上优
先还原出镍,沉淀在镀液中,对镀液稳定性影响极大。
4.操作工艺方法的影响
局部过热:化学镀镍槽如果采用电炉、蒸汽直接加热,就会使镀液局部过热(温度超过96度),且当pH值偏高时,很容易引起镀液自然分解。
镀液负荷:镀液的负荷过高或过低,尤其在负荷过低时对槽液稳定性影响较大,因为此时沉
积速度过高,所获得的镀层比较疏松,镍结晶颗粒可能从镀层上脱落到镀液中,而形成自催
化还原中心,促使溶液自发分解。
工装:使用的工装夹具,应进行防蚀保护,以防止镀液对其腐蚀,否则一旦挂具被腐蚀,势
必会增加镀液的杂质,而影响镀液的稳定性。