铝合金激光焊接难点及解决对策
激光焊接铝合金的难点及采取的工艺措施

激光焊接铝合金的难点及采取的工艺措施随着科技的发展,激光焊接技术在各个领域得到了广泛的应用,尤其是在金属材料的加工过程中。
激光焊接铝合金这一领域却面临着诸多挑战。
本文将从铝合金的特点、激光焊接的难点以及采取的工艺措施等方面进行详细的探讨。
一、铝合金的特点铝合金是一种具有优良性能的金属材料,它具有轻质、高强度、耐腐蚀等特点。
这些特点使得铝合金在航空、航天、汽车等领域具有广泛的应用前景。
铝合金的这些优点也给激光焊接带来了一定的难度。
铝合金的熔点较低,容易产生氧化膜,影响焊接质量。
铝合金的热导率较高,导致热量容易散失,需要采用较高的功率进行焊接。
铝合金的成分复杂,不同种类的铝合金之间存在化学成分差异,这也给激光焊接带来了一定的挑战。
二、激光焊接铝合金的难点1. 氧化膜的影响铝合金在加热过程中容易产生氧化膜,这层氧化膜不仅会影响焊缝的质量,还会导致气孔的产生。
因此,在激光焊接铝合金时,需要采取一定的措施去除氧化膜。
常用的方法有机械磨削、化学清洗和电化学清理等。
2. 热量散失问题铝合金的高热导率导致热量容易散失,这就需要在激光焊接过程中采用较高的功率进行加热。
过高的功率会导致焊缝过深,产生裂纹。
因此,在激光焊接铝合金时,需要寻找合适的功率平衡点。
3. 成分差异问题铝合金的成分复杂,不同种类的铝合金之间存在化学成分差异。
这就要求在激光焊接过程中,需要根据不同的铝合金种类选择合适的焊接参数和工艺措施。
还需要对铝合金的微观结构进行分析,以便更好地控制焊缝的形成和性能。
三、采取的工艺措施针对上述难点,本文提出以下几点工艺措施:1. 采用预处理方法去除氧化膜在激光焊接前,可以采用机械磨削、化学清洗和电化学清理等方法去除铝合金表面的氧化膜。
这样可以有效地减少氧化膜对焊缝质量的影响。
2. 调整激光功率平衡热量散失问题在激光焊接过程中,可以通过调整激光功率来平衡热量散失问题。
一般来说,随着激光功率的增加,焊缝深度也会增加。
激光焊接铝合金的难点及采取的工艺措施

激光焊接铝合金的难点及采取的工艺措施一、1.1 铝合金材料的特性铝合金是一种非常优良的金属材料,具有轻质、高强度、耐腐蚀等特点。
铝合金的这些优点也给激光焊接带来了一定的难度。
铝合金的高反射率使得激光束在焊接过程中容易产生散射,影响焊接质量。
铝合金的热导率相对较低,导致焊接过程中热量难以迅速传递到熔池,容易产生气孔等缺陷。
铝合金中含有较多的杂质元素,如铜、镁等,这些杂质会与激光发生反应,形成有害物质,影响焊接质量和稳定性。
二、2.1 激光焊接技术的发展为了克服铝合金激光焊接的难点,研究人员不断尝试改进激光焊接技术。
目前,主要采用的激光焊接方法有脉冲激光焊接、连续波激光焊接、调制激光焊接等。
其中,脉冲激光焊接是一种非常有效的方法,它可以实现高功率密度、短脉冲时间的焊接,有效提高焊缝质量。
研究人员还通过改进激光器结构、优化焊接参数等手段,进一步提高了激光焊接的效果。
三、3.1 工艺措施的选择针对铝合金激光焊接的难点,我们可以从以下几个方面采取相应的工艺措施:1. 提高激光功率:增加激光束的能量,有助于提高焊缝的形成速度和深度,从而减少气孔等缺陷的产生。
但是,过高的功率会导致焊缝过热,降低焊缝质量。
因此,需要在保证焊缝质量的前提下,合理选择激光功率。
2. 减小光斑直径:通过调整激光束的聚焦方式,减小光斑直径,有助于提高焊缝的精度和平滑度。
减小光斑直径还可以降低热量输入,减少气孔等缺陷的产生。
3. 优化焊接参数:根据铝合金的特性和具体焊接条件,合理选择焊接速度、焦距、电流等参数,有助于提高焊缝的质量和稳定性。
例如,适当降低焊接速度可以减少气孔的产生;增大电流可以提高焊缝的形成速度和深度。
4. 采用辅助气体保护:在激光焊接过程中,引入适当的辅助气体(如氩气、氮气等),可以有效地防止铝合金表面氧化和污染,提高焊缝的质量。
辅助气体还可以调节焊缝的形成过程,有助于改善焊缝的成形性能。
四、4.1 实际应用案例近年来,随着激光焊接技术的不断发展和成熟,铝合金激光焊接已经在航空、航天、汽车等领域得到了广泛应用。
铝合金激光焊接机的焊接缺陷控制工艺
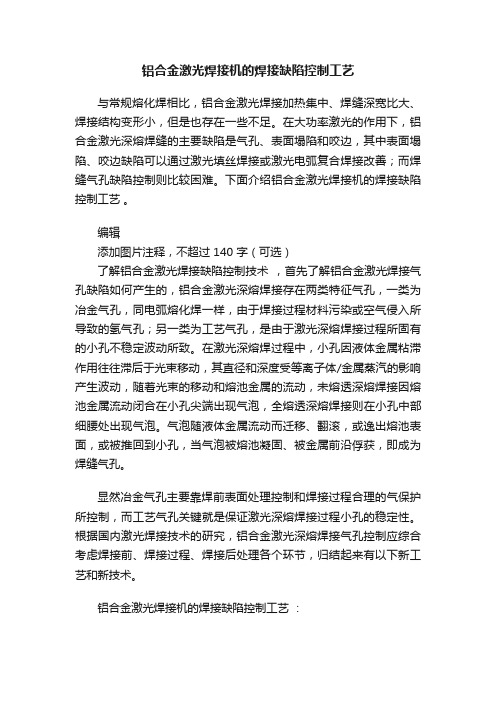
铝合金激光焊接机的焊接缺陷控制工艺与常规熔化焊相比,铝合金激光焊接加热集中、焊缝深宽比大、焊接结构变形小,但是也存在一些不足。
在大功率激光的作用下,铝合金激光深熔焊缝的主要缺陷是气孔、表面塌陷和咬边,其中表面塌陷、咬边缺陷可以通过激光填丝焊接或激光电弧复合焊接改善;而焊缝气孔缺陷控制则比较困难。
下面介绍铝合金激光焊接机的焊接缺陷控制工艺。
编辑添加图片注释,不超过 140 字(可选)了解铝合金激光焊接缺陷控制技术,首先了解铝合金激光焊接气孔缺陷如何产生的,铝合金激光深熔焊接存在两类特征气孔,一类为冶金气孔,同电弧熔化焊一样,由于焊接过程材料污染或空气侵入所导致的氢气孔;另一类为工艺气孔,是由于激光深熔焊接过程所固有的小孔不稳定波动所致。
在激光深熔焊过程中,小孔因液体金属粘滞作用往往滞后于光束移动,其直径和深度受等离子体/金属蒸汽的影响产生波动,随着光束的移动和熔池金属的流动,未熔透深熔焊接因熔池金属流动闭合在小孔尖端出现气泡,全熔透深熔焊接则在小孔中部细腰处出现气泡。
气泡随液体金属流动而迁移、翻滚,或逸出熔池表面,或被推回到小孔,当气泡被熔池凝固、被金属前沿俘获,即成为焊缝气孔。
显然冶金气孔主要靠焊前表面处理控制和焊接过程合理的气保护所控制,而工艺气孔关键就是保证激光深熔焊接过程小孔的稳定性。
根据国内激光焊接技术的研究,铝合金激光深熔焊接气孔控制应综合考虑焊接前、焊接过程、焊接后处理各个环节,归结起来有以下新工艺和新技术。
铝合金激光焊接机的焊接缺陷控制工艺:1.焊前处理方法。
焊前表面处理是控制铝合金激光焊缝冶金气孔的有效方法,通常表面处理方法有物理机械清理、化学清理,近年来还出现了激光冲击清理,这将进一步提高激光焊接自动化程度。
2.焊接工艺参数稳定性优化控制。
铝合金激光焊接过程工艺参数通常主要有激光功率、离焦量、焊接速度,以及气保护的成分和流量等。
这些参数既影响焊接区域的保护效果,又影响激光深熔焊接过程的稳定性,从而影响焊缝气孔。
激光焊接铝合金的难点及采取的工艺措施

激光焊接铝合金的难点及采取的工艺措施随着科技的发展,激光焊接技术在各个领域得到了广泛的应用,尤其是在金属材料的加工过程中。
激光焊接铝合金这一领域仍然存在许多技术难题。
本文将从以下几个方面探讨激光焊接铝合金的难点及采取的工艺措施。
一、铝合金材料的特性铝合金具有轻质、高强度、耐腐蚀等优良性能,因此在航空、航天、汽车等领域得到了广泛应用。
铝合金的热导率较低,热量传导速度较慢,这给激光焊接带来了一定的困难。
铝合金中含有大量的铝和硅元素,这些元素容易与氧原子发生化学反应,形成氧化膜,影响焊缝的质量。
二、激光焊接工艺参数的选择1. 功率密度功率密度是激光焊接过程中最重要的参数之一。
过高的功率密度会导致焊缝过深,产生裂纹;而过低的功率密度则会导致焊缝熔合不完全,产生气孔。
因此,选择合适的功率密度对于保证焊缝质量至关重要。
一般来说,铝合金的激光焊接功率密度应控制在3-5kW/cm2之间。
2. 频率和波长激光器的频率和波长对激光焊接的效果也有重要影响。
一般来说,波长越短,能量越高,焊缝熔合效果越好。
不同的铝合金材料对波长的适应性不同,需要根据实际情况进行选择。
频率的选择也会影响到焊缝的形成过程,一般建议控制在10-20kHz之间。
3. 焊接速度焊接速度是指激光束在单位时间内通过的距离,它直接影响到焊缝的形成过程。
过快的焊接速度会导致焊缝过深,产生裂纹;而过慢的焊接速度则会导致焊缝熔合不完全,产生气孔。
因此,选择合适的焊接速度对于保证焊缝质量至关重要。
一般来说,铝合金的激光焊接速度应控制在1-3m/s之间。
三、工艺措施针对上述难点,我们可以采取以下几种工艺措施:1. 预处理为了去除铝合金表面的氧化膜,可以在焊接前进行酸洗或碱洗等预处理方法。
这样可以有效地提高焊缝的质量,减少气孔等缺陷的产生。
2. 优化激光参数根据铝合金的特性和实际需求,合理调整激光功率密度、频率和波长等参数,以获得最佳的焊接效果。
还可以采用多波长焊接、双光束焊接等方法,进一步提高焊缝的质量。
铝合金激光焊接中的常见问题解决方法
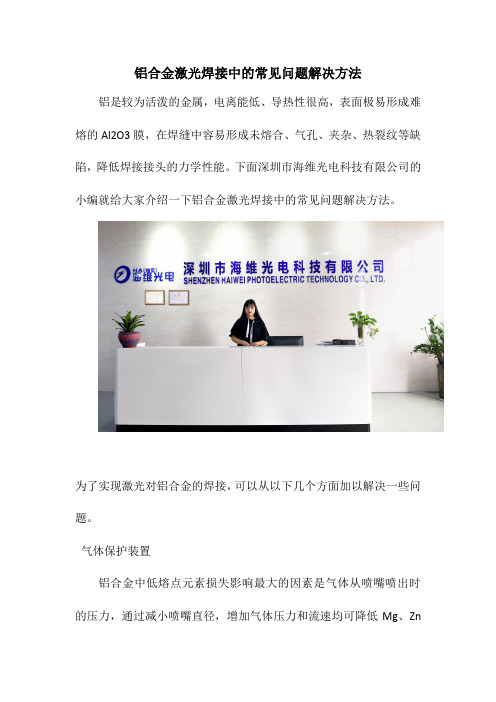
铝合金激光焊接中的常见问题解决方法铝是较为活泼的金属,电离能低、导热性很高,表面极易形成难熔的Al2O3膜,在焊缝中容易形成未熔合、气孔、夹杂、热裂纹等缺陷,降低焊接接头的力学性能。
下面深圳市海维光电科技有限公司的小编就给大家介绍一下铝合金激光焊接中的常见问题解决方法。
为了实现激光对铝合金的焊接,可以从以下几个方面加以解决一些问题。
气体保护装置铝合金中低熔点元素损失影响最大的因素是气体从喷嘴喷出时的压力,通过减小喷嘴直径,增加气体压力和流速均可降低Mg、Zn等在焊接过程中的烧损,同时也可以增加熔深。
吹气方式有直吹和侧吹两种,还可以在焊件上下同时吹气,焊接中根据实际情况选择吹气方式。
表面处理铝合金对激光具有高反作用,对铝合金进行适当的表面预处理,如阳极氧化、电解抛光、喷沙处理、喷砂等方式,可以显著提高表面对光束能量的吸收。
研究表明,铝合金去除氧化膜后的结晶裂纹倾向比原始态铝合金大。
为了既不破坏铝合金表面状态,又能简化激光焊接工程工艺过程,可以采用焊前预处理的办法升高工件表面温度,以提高材料对激光的吸收率。
激光器参数焊接激光器分为脉冲激光器和连续激光器,脉冲激光器波长1064nm时光束特别集中,脉冲单点能量比连续激光器的大。
但是脉冲激光器的能量一般不超过,所以一般适用薄壁焊件。
脉冲模式焊接激光焊接时应选择合适的焊接波形,常用脉冲波形有方波、尖峰波、双峰波等,通常一个脉冲波时间以毫秒为单位,在一个激光脉冲作用期间内,金属反射率的变化很大。
铝合金表面对光的反射率太高,当高强度激光束射至材料表面,金属表面将会有60%-98%的激光能量因反射而损失掉,且反射率随表面温度变化。
因此一般焊接铝合金时最优选择尖形波(见图 1 )和双峰波,波形上升阶段是为提供较大的能量使铝合金熔化,一旦工件中“小孔”形成,开始进行深熔焊时,金属熔化后液态金属对激光的吸收率迅速增大,此时应迅速减小激光能量,以小功率进行焊接,以免造成飞溅。
铝合金激光焊接技术难点分析
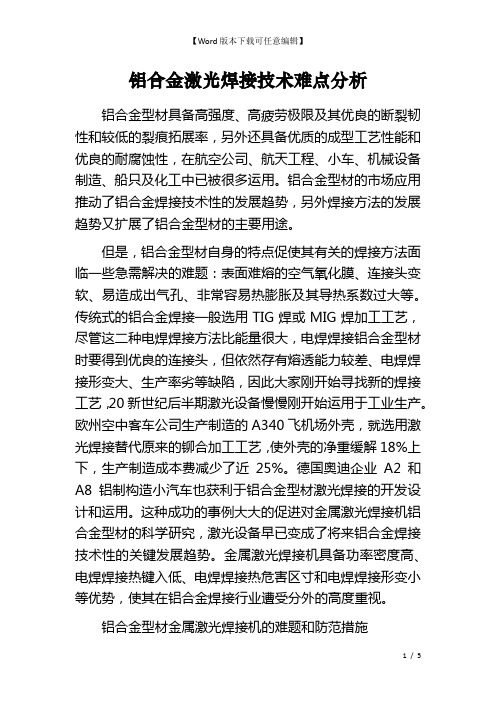
铝合金激光焊接技术难点分析铝合金型材具备高强度、高疲劳极限及其优良的断裂韧性和较低的裂痕拓展率,另外还具备优质的成型工艺性能和优良的耐腐蚀性,在航空公司、航天工程、小车、机械设备制造、船只及化工中已被很多运用。
铝合金型材的市场应用推动了铝合金焊接技术性的发展趋势,另外焊接方法的发展趋势又扩展了铝合金型材的主要用途。
但是,铝合金型材自身的特点促使其有关的焊接方法面临一些急需解决的难题:表面难熔的空气氧化膜、连接头变软、易造成出气孔、非常容易热膨胀及其导热系数过大等。
传统式的铝合金焊接一般选用TIG焊或MIG焊加工工艺,尽管这二种电焊焊接方法比能量很大,电焊焊接铝合金型材时要得到优良的连接头,但依然存有熔透能力较差、电焊焊接形变大、生产率劣等缺陷,因此大家刚开始寻找新的焊接工艺,20新世纪后半期激光设备慢慢刚开始运用于工业生产。
欧州空中客车公司生产制造的A340飞机场外壳,就选用激光焊接替代原来的铆合加工工艺,使外壳的净重缓解18%上下,生产制造成本费减少了近25%。
德国奥迪企业A2和A8铝制构造小汽车也获利于铝合金型材激光焊接的开发设计和运用。
这种成功的事例大大的促进对金属激光焊接机铝合金型材的科学研究,激光设备早已变成了将来铝合金焊接技术性的关键发展趋势。
金属激光焊接机具备功率密度高、电焊焊接热键入低、电焊焊接热危害区寸和电焊焊接形变小等优势,使其在铝合金焊接行业遭受分外的高度重视。
铝合金型材金属激光焊接机的难题和防范措施1.铝合金型材表面的高可逆性和高传热性这一特性能够用铝合金型材的外部经济构造来表述。
因为铝合金型材中存有相对密度挺大的自由电子,自由电子遭受激光器(明显的无线电波)逼迫振动而造成次级线圈无线电波,导致明显的反射面波和较差的散射波,因此铝合金型材表面对激光器具备较高的透射率和不大的消化率。
另外,自由电子的布朗运动受激而越来越更加强烈,因此铝合金型材也具备很高的传热性。
对于铝合金型材对激光器的高可逆性,世界各国已作了很多科学研究,实验得出结论,开展适度的表面预备处理如喷砂工艺、打磨砂纸打磨抛光、表面有机化学腐蚀、表面镀、高纯石墨镀层、气体炉中空气氧化等均能够减少光线反射面,合理地扩大铝合金型材对光线动能的消化吸收。
铝激光连续焊气孔

铝激光连续焊气孔引言:激光焊接作为一种高效、精密的焊接方法,广泛应用于金属材料的连接。
然而,在铝材料的激光焊接过程中,常会出现气孔缺陷,对焊接质量造成影响。
本文将探讨铝激光连续焊气孔的形成原因及其解决方法。
一、气孔形成原因:1. 气体释放:在激光焊接过程中,铝材料中的气体(如氧、氮、水蒸汽等)会因受热而释放出来,形成气孔。
2. 表面氧化:铝材料的氧化膜会影响焊接过程中的气体释放,导致气孔的形成。
3. 激光功率不匹配:激光功率过低或过高都会导致焊接过程中的气体释放不完全,从而产生气孔。
二、气孔的危害:1. 强度降低:气孔的存在会使焊缝的强度大大降低,影响焊接接头的承载能力。
2. 导电性下降:气孔会使焊接接头的导电性下降,影响电子设备的正常工作。
3. 漏液漏气:气孔会导致焊接接头的密封性下降,造成液体或气体的泄漏。
三、解决方法:1. 优化焊接参数:合理选择激光功率、焦点位置和扫描速度等参数,以提高焊接过程中的气体释放效果,减少气孔的形成。
2. 表面处理:采用去氧化、除油等方法,去除铝材料表面的氧化膜和污染物,提高焊接质量。
3. 氩气保护:在焊接过程中,使用氩气进行保护,减少氧气的接触,从而减少气孔的形成。
4. 预热处理:通过预热铝材料,可以提高其热导率,减少气体在焊接过程中的积聚和释放,从而减少气孔的形成。
5. 激光焊接头设计:合理设计焊接接头的结构,减少焊接过程中的气体积聚和释放,降低气孔的形成。
结论:铝激光连续焊气孔的形成是由气体释放、表面氧化和激光功率不匹配等原因引起的。
气孔的存在会降低焊接接头的强度和导电性,影响设备的正常工作。
为了解决气孔问题,可以优化焊接参数、表面处理、氩气保护、预热处理和合理设计焊接接头的结构等方法。
通过这些措施,可以有效减少铝激光连续焊气孔的形成,提高焊接质量和接头的性能。
铝合金激光焊接的问题如何解决

激光在现今的机械加工行业中应用十分广泛,再加上由于激光技术具有焊接热输入低,焊接受热区域影响小和不易变形等特点,因而在铝合金焊接领域受到格外的重视。
但是从另一方面来说,激光加工由于铝合金的加工特点,在对铝合金激光焊接加工时,会存在一些焊接难点。
那么对于从事焊接加工的操作者来说,如何解决这些难题呢?铝合金激光焊接问题一:铝合金对激光吸收率低这个问题主要是由于铝合金材料的问题,由于铝合金对激光束的高初始反射率及其本身的高导热性,使铝合金在未熔化前对激光的吸收率很低。
对于这个问题,解决方法主要有以下几个方面:1、对铝合金材料进行表面预处理工艺。
例如生产中常用的砂纸打磨、表面化学浸蚀、表面镀等预处理措施。
增加材料对激光的吸收率。
2、让光斑尺寸减小,使激光功率密度增加。
3、改变焊接结构,使激光束在间隙中形成多次反射,便于铝合金进行激光焊接加工。
铝合金激光焊接问题二:易产生气孔和热裂纹铝合金激光焊接过程中会轻易产生气孔和热裂纹的情况,对于这个问题,解决方法主要有以下几个方面:1、在焊接过程中调整激光功率波形,可以减少气孔不稳定塌陷,改变激光束照射的角度以及在焊接中施加磁场作用,也可以让焊接时产生的气孔得到有效控制。
2、在使用YAG激光器时,可以通过调整脉冲波形,控制热输入,以减少结晶裂纹。
铝合金激光焊接问题三:焊接接头力学性能下降焊接过程中合金元素的烧损,使铝合金焊接接头的力学性能下降。
对于这个问题,解决方法主要有以下几个方面:由于铝合金焊接产生的气孔不稳定,导致焊接接头的力学性能。
铝合金主要包括Zn、Mg 、Al三种元素。
在焊接时,铝的沸点均高于其他两种元素的沸点。
所以在铝合金元素焊接时可以加入一些低沸点合金元素,有利于小孔的形成,焊接的牢固性。
- 1、下载文档前请自行甄别文档内容的完整性,平台不提供额外的编辑、内容补充、找答案等附加服务。
- 2、"仅部分预览"的文档,不可在线预览部分如存在完整性等问题,可反馈申请退款(可完整预览的文档不适用该条件!)。
- 3、如文档侵犯您的权益,请联系客服反馈,我们会尽快为您处理(人工客服工作时间:9:00-18:30)。
铝合金激光焊接难点及解决对策
一、概述
铝合金具有高比强度、高比模具和高疲劳强度以及良好的断裂韧性和较低的裂纹扩展率,同时还具有优良的成形工艺性和良好的抗腐蚀性。
因此,广泛应用于各种焊接结构和产品中。
传统的铝合金焊接一般采用TIG焊或MIG焊工艺,但所面临的主要问题是焊接过程中较大的热输入使铝合金变形大,焊接速度慢,生产效率低。
由于焊接变形大,随后的矫正工作往往浪费大量的时间,增加了制造成本,影响了生产效率和生产质量,而激光焊接具有功率密度高、焊接热输入低、焊接热影响区小和焊接变形小等特点,使其在铝合金焊接领域受到格外的重视。
铝合金激光焊接的主要难点在于:
1、铝合金对激光束的高初始反射率及其本身的高导热性,使铝合金在未熔化前对激光的吸收率低,“小孔”的诱导比较困难。
2、铝的电离能低,焊接过程中光致等离子体易于过程和扩散,使得焊接稳定性差。
3、铝合金激光焊接过程中容易产生气孔和热裂纹。
4、焊接过程中合金元素的烧损,使铝合金焊接接头的力学性能下降。
二、铝合金激光焊接的问题和对策
1、铝合金对激光的吸收率问题
材料对激光的吸收率由下式决定
ε=0.365{ρ[1+β(т-20)]/λ}1/2
式中ρ—铝合金20度的直流电阻率,Ω.M
β—电阻温度系数,℃-1
т—温度,℃
λ—激光束的波长
对于铝合金来说,吸收率是温度的函数,在铝合金表面熔化、汽化前。
由于铝合金对激光的高反射,吸收率将随温度的升高而缓慢增加,一旦铝合金表面熔化、汽化,对激光的吸收率就会迅速增加。
为提高铝合金对激光的吸收,可以采用以下方法:
ü采取适当的表面预处理工艺表1所示为铝在原始表面(铣、车加工后)、电解抛光、喷砂(300目砂子)及阳极氧化(氧化层厚度u m级)4种表面状态下对入射光束能量的吸收情况。
由此可见,阳极氧化和喷砂处理可以显著提高铝对激光束的能量吸收。
另外,砂纸打磨、表面化学浸蚀、表面镀、石墨涂层及空气炉中氧化等表面预处理措施对激光束的吸收是有效的。
ü激光器参数调整选用短焦距透镜和低阶模输出均可使光斑尺寸减小,激光功率密度增大,铝合金对激光束的吸收率也增加。
ü焊接结构设计将工件坡口设计成斜30℃角,这样激光束能在空隙中多次反射,形成一个人工小孔,从而增加激光束的吸收率。
表1 铝表面状态对CO2激光束吸收率的影响
2、小孔效应及等离子体对铝合金激光焊接的影响。
在铝合金激光焊接过程中,小孔的出现可以大大提高材料对激光的吸收率,焊接可以获得更多的能量,但由于低熔点合金元素的蒸发,使得光致等离子体易于过程和散热,小孔的稳定性差,从而影响焊接成形和接头的力学性能,并且容易产生气孔等焊接缺陷,所以小孔的诱导性和稳定成为研究一个重点。
根据相关资料可知,在不同的铝合金焊接中均均存在一个激光能量密度阀值,低于此值时熔点很低,而一旦达到或者超过此值,熔深会大大提高,当工件上的激光功率密度达到
3.5*106W/cm2时,产生等离子体,这是深熔焊开始的标志;功率密度低于此值时,进行热传导焊接;而深熔焊与热传导焊之间的过度区,两者交替进行,使得焊深波动很大。
研究表明,诱导小孔所需的能量密度阀值的高低主要和铝合金中某些低沸点合金元素(如Mg\Zn等)的含量成反比。
合金元素含量越高,其阀值越低。
主要原因是铝合金元素Mg\Zn 的沸点大大低于铝的沸点。
Mg的沸点为1090度,Zn的沸点低于1000度,而铝的沸点为2467度。
合金元素大量蒸发形成蒸汽压有利于小孔的形成,所以某些低沸点合金元素(Li)的加入有利于小孔的形成,使得铝合金易焊。
有的研究指出,在相同的条件下用氦气作保护气比用氩气作保护气获得的熔深小。
原因是与氩气相比,氦气重量轻,气压低,对凹陷熔深的作用小;氦的离子化能量高,等离子体温度低,难以对熔池表面加热。
但在采用高功率激光器低速焊时,氦气可以获得深熔焊。
但现在很多研究采用两种气体联合保护,调整其混合比例,可以获得很好的熔深和焊缝成形。
采用氮气保护时,即使焊速很高,也能获得深熔焊。
但容易产生未焊透,焊缝成形不良。
激光焊接过程中产生的等离子体能吸收激光能量,改变光束的聚焦状态,使焊缝的深宽比减小。
等离子体的不稳定会导致熔深不等,影响焊缝成形及其接头的力学性能。
近几年来,有的学者采用在工件表面预置粉未来减弱等离子体在高度方向上的膨胀跳动,使等离子在工件表面能维持跳动幅度的相对稳定。
3、铝合金的激光焊接性性问题。
Ø气孔问题,铝合金种类不同,产生的气孔类型也不同。
一般认为,铝合金在焊接过程中产生以下几类气孔:
氢气孔。
铝合金在有氢的环境中熔化后,其内部的含氢量可达到0.69ml/100g以上。
但凝固以后,其平衡状态下的溶氢能力最多只有0.036ml/100g,两者相差近20倍。
因此,在由液态向固态转变的过程中,液态铝上多余的氢气必定要析出。
如果析出的氢不能顺利上浮逸出,就会聚集成气泡残留在固态铝合金成为气孔。
日本学者在封闭的条件下将焊缝气孔中的气体收集起来进行分析,得出的结果为:氢气占90%,氮气占10%。
因此通常认为减少焊缝气孔的有效措施就是断焊接时的供氢源。
保护气体产生的气孔。
有研究认为,在高能激光焊接铝合金的过程中,由于熔池底部小孔前沿金属的强烈蒸发,使保护气体被卷入熔池形成气泡,当气泡来不及逸出而残留在固态铝合金中即成为气孔。
表2是A5083合金激光焊接气孔中保护气体的含量。
表2 A5083合金激光焊接气孔中保护气体的含量
小孔塌陷产生的气孔。
在激光焊接过程中,当表面张力大于蒸气压力时,小孔将不能维持稳定而塌陷,金属来不及填充就形成了孔洞。
Matsunawa教授的实时小孔观察试验引起了激光焊接领域的极大关注,相关的小孔模型研究和直接观察研究工作大量涌现。
随之而来,对减少或避免铝合金激光焊接中的气孔缺陷也提出了很多实际措施,如调整激光功率波形,减少小孔不稳定塌陷,改变光束焦点高度和倾斜照射,在焊接过程时施加电磁经场作用以及在真空中进行焊接等。
近几年来,又有研究者采用填丝或预置合金粉未、复合热源和双焦点技术来减少气孔的产生,取得了不错的效果。
Ø裂纹问题
铝合金属于典型的共晶合金,在激光焊接快速凝固下更容易产生热裂纹,焊缝金属结晶时在柱状晶边界形成AL-Si或Mg-Si等低熔点共晶是导致裂纹产生的原因。
为减少热裂纹,可以采用填丝或预置合金粉未等方法进行激光焊接。
使用YAG激光器时,调节脉冲波形,控制热输入也可以减少结晶裂纹。
三、铝合金激光焊接的发展前景
铝合金激光焊接最为人引人关注的特点是其高效率,而要充分发挥这种高效率就是把它运用到大厚度深熔焊接中。
因此,研究和使用大功率激光器进行大厚度深熔焊接将是未来发展的必然趋势。
大厚度深熔焊更加突出了小孔现象及对焊缝气孔的影响,因此小孔形成机理及控制变得更加,它必将成为未来学术界及工业界共同关心和研究的热点问题。
改善激光焊接过程的稳定性和焊缝成形、提高焊接质量是人们追求的目标。
因此,激光-电弧复合工艺、填丝激光焊接、预置粉未激光焊接、双焦点技术以及光束整形等新技术将会得到理一步完善和发展。
另外,有人发现在CO2激光焊接溶池中存在几安培的固定电流、焊接区的外加磁场会影响熔池的流动状态以及光致等离子体的形态和稳定。
因此采用某种形式的磁场有可能改善铝合金激光焊接进程的稳定性和焊缝质量。
所以,采用辅助电流,通过其形成的电磁力控制熔池的流动状态,从而改善焊接过程的稳定性,提高焊缝质量,也可能受到更多研究者的关注。