液压系统回路设计
液压基本回路的安装与调试—顺序控制回路的设计、安装与调试
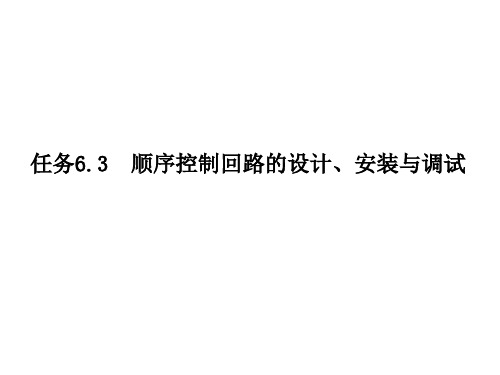
液压叠加阀组的安装步骤
教学目标
1.熟知顺序控制回路的类型及应用;
2.能够根据控制要求进行顺序控制回路的设计与 仿真;
3.能够根据原理图进行顺序控制回路的安装、调 试与故障排除。
知识点 顺序控制回路
作用:使系统中各执行元件严格的按规定的顺序 来动作。 分类:按控制方式的不同,分为三类:压力控制 、行程控制和时间控制。
1.行程控制式-换向可靠,但改变顺序困难
行 程 阀 控 制
1.行程控制式-调整方便,适合电控,应用广泛
行 程 开 关 控 制
1.行程控制式-调整方便,适合电控,应用广泛
行 程 开 关 控 制
2.器 控 制
2.压力控制式
任务实施 顺序阀控制 顺序动作回路设计、安装与调试
任务总结
1.行程控制顺序控制回路的类型及应用; 2.压力控制顺序控制回路的类型及应用。
一. 任务引入
思考:
1.顺序阀的顺序动作回路,顺序阀的安装位置如何确定? 2.为确保顺序动作,顺序阀的弹簧调定力如何调定,依据是什么?
二. 具体实施
要求: 1.确定所需液压元件,设计并绘制顺序阀的顺序控制液 压回路图; 2.应用Fluidsim软件进行对所设计的液压回路进行仿真; 3.在FESTO液压实训台上对液压回路进行安装和调试。
液压回路设计与组装实验
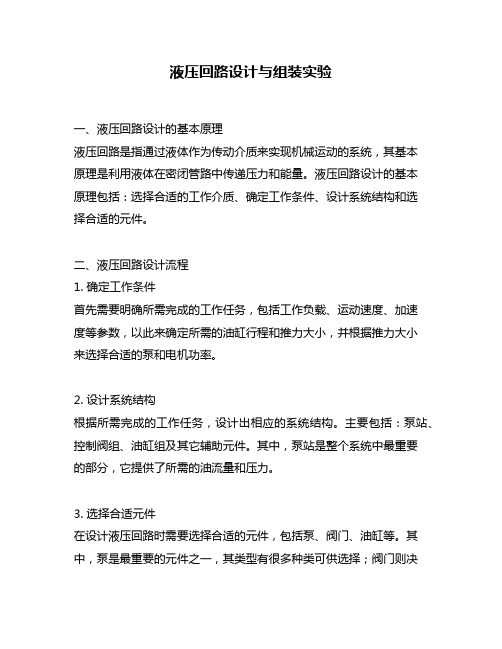
液压回路设计与组装实验一、液压回路设计的基本原理液压回路是指通过液体作为传动介质来实现机械运动的系统,其基本原理是利用液体在密闭管路中传递压力和能量。
液压回路设计的基本原理包括:选择合适的工作介质、确定工作条件、设计系统结构和选择合适的元件。
二、液压回路设计流程1. 确定工作条件首先需要明确所需完成的工作任务,包括工作负载、运动速度、加速度等参数,以此来确定所需的油缸行程和推力大小,并根据推力大小来选择合适的泵和电机功率。
2. 设计系统结构根据所需完成的工作任务,设计出相应的系统结构。
主要包括:泵站、控制阀组、油缸组及其它辅助元件。
其中,泵站是整个系统中最重要的部分,它提供了所需的油流量和压力。
3. 选择合适元件在设计液压回路时需要选择合适的元件,包括泵、阀门、油缸等。
其中,泵是最重要的元件之一,其类型有很多种类可供选择;阀门则决定了液压回路的控制方式和工作效率;油缸则是实现工作任务的关键元件。
三、液压回路组装实验步骤1. 确定实验目的首先需要明确实验目的,以此来确定所需的元件和工具。
2. 准备工具和材料根据所需完成的实验任务,准备好所需的工具和材料。
主要包括:泵、阀门、油缸、管路、油箱等。
3. 组装泵站将泵与电机连接起来,并将其放置在油箱上方。
然后将进口管道与油箱连接,出口管道与控制阀组连接。
4. 组装控制阀组根据设计图纸将各个控制阀门组合起来,并将其与泵站相连。
5. 组装油缸组根据设计图纸将各个油缸组合起来,并连接到控制阀组上。
6. 连接管路根据设计图纸依次连接各个元件之间的管路,保证系统密封性良好。
7. 填充液体并试运行在完成液压回路组装后,需要填充液体并进行试运行。
在试运行过程中需要检查系统是否正常运行,并根据需要进行调整。
四、液压回路组装实验注意事项1. 在组装过程中需要遵循安全操作规程,注意防止液体泄漏和高压伤害。
2. 在选择元件时需要保证其质量可靠,以免影响实验结果。
3. 在组装过程中需要按照设计图纸进行操作,保证系统结构合理。
液压基本回路设计
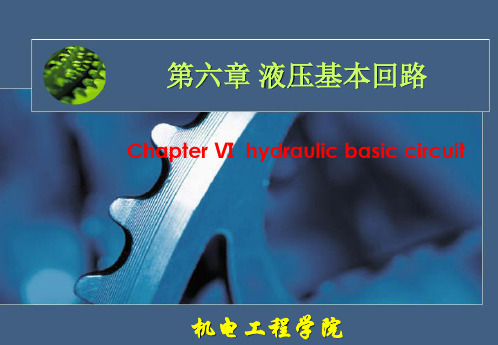
机构的回油腔吸油。闭式回路结构紧凑,只需很小的补油箱,但 冷却条件差,为了补偿工作中油液的泄漏,一般设补油泵,补油 泵的流量为主泵流量的10%~15%,压力调节为3×105~10×105Pa。
节流调速回路分类
支路(旁路)节流调速
(1)工作原理 溢流阀正常工作是关闭
的,只有过载时才打开, 作安全阀使用。见右图。
支路(旁路)节流调速
(2)速度—负载特性
pT p1 F A1
qT
CT AT
pTm
CT
AT
(
F A1
)m
q1 qB qT
v
q1
qB
CT
AT
(
F A1
)m
A1
A1
支路(旁路)节流调速
当m 0.5时
3
Kv
dF dv
2A12 F CT AT
2 A1F qB A1v
支路(旁路)节流调速
支路(旁路)节流调速
支路(旁路)节流调速
结论:
➢这种回路只有节流损失而无溢流损失;泵压随 负载变化,即节流损失和输入功率随负载而增 减。因此,本回路比前两种回路效率高。
➢由于本回路的速度-负载特性很软,低速承载 能力差,故其应用比前两种回路少,只用于高 速、重载、对速度平稳性要求不高的较大功率 的系统,如牛头刨床主运动系统、输送机械液 压系统等。
蓄能器保压回路
利用限压式变量油泵的保压回路
在讲单作用式叶片变量泵 时,已提到过,当定子与转 子圆心偏移量(单作用式叶 片变量泵)很小或斜盘倾斜 角很小时,泵的流量仅能维 持自身泄漏,对油路不输出 油液,但泵仍在一定压力下 运转,对外输出恒定压力, 则可使系统压力恒定(参见 泵一章有关内容),此时泵 输出功率较小(功率=流量 ×压力)。
液压系统三缸同步_顺序动作回路的设计与分析_邓乐

Mining & Processing Equipment 53近年来,随着环境保护意识的增强,垃圾的处理和综合利用受到关注。
在为某公司生产的垃圾送料器液压系统设计时,遇到了要求三个液压缸同步前进,然后顺序后退的回路设计问题,这里,液压系统的主要作用是完成垃圾的送料,为保证垃圾能够可靠地送料,要求在一个工作循环中,三个液压缸同步前进,到位后三个液压缸依次顺序后退至原位(此时卸料)。
1 主要技术问题及解决方法针对以上问题,在细致地分析了系统主要功能要求的基础上,可以把该系统设计的主要问题归纳为两个:单因此可以采用1所分别为固接Ⅲ缸筒外的机分流同步阀的出口相连(如图2、3所示)。
其实现位移同步运动的原理为:缸筒左移时,Ⅰ、Ⅲ缸筒依靠单向分流同步阀实现同步,同时利用机械挡块1、3的作用迫使挡块2移动,从而使缸筒Ⅱ与Ⅰ、Ⅲ同步运动;缸筒右移时,则按Ⅰ→Ⅱ→Ⅲ的顺序运动。
当机械挡块1、3按照图1中虚线所示的方式连接、而油路连接不改变时可以实现三缸筒同步向右移动,而按Ⅰ→Ⅱ→Ⅲ的顺序向左移动。
三缸顺序动作可以采用行程控制方式 (行程阀和行程开关如图2所示)或压力控制方式(顺序阀或压力继电器)。
2 同步—顺序动作回路的几种方案根据以上分析,可以拟定以下4个方案:(1) 方案1如图2所示,采用行程阀实现三缸顺序动作。
工作过程为:启动后,电磁换向阀1左位接通,Ⅰ、Ⅱ、Ⅲ三缸筒同步左移;至左端点时,缸筒Ⅰ压下行程开关1XK,使阀1右位接通;三缸进、出油口转换,首先缸筒Ⅰ右移,至右端点时压下行程阀3,接着缸筒Ⅱ右移,Ⅱ至右端点时压下行程阀2,缸Ⅲ右移,Ⅲ至右位时压下行程开关2XK,阀1左位接通,完成一个工作循环。
(2) 方案2如图3所示,与方案1不同之处是采用两个顺序阀实现三缸的顺序动作,其中顺序阀2的动作压力比阀3的小,左移时三缸同步,右移时按照Ⅰ、Ⅱ、Ⅲ的顺序移动,其动作顺序为:假设三缸筒处于右位时为原位,Ⅲ压下2XK,当阀1左位接通时,三缸筒同步左移,同时Ⅲ松开2XK,移至左端时,Ⅰ压下1换向,右位接通,缸筒Ⅰ首先右移,右端时,开顺序阀2右移动,力进一步增加,阀32X成一个工作循环。
液压系统设计计算
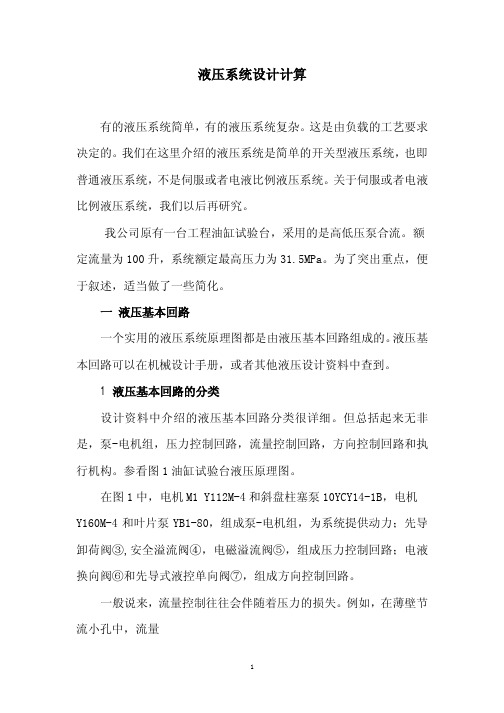
液压系统设计计算有的液压系统简单,有的液压系统复杂。
这是由负载的工艺要求决定的。
我们在这里介绍的液压系统是简单的开关型液压系统,也即普通液压系统,不是伺服或者电液比例液压系统。
关于伺服或者电液比例液压系统,我们以后再研究。
我公司原有一台工程油缸试验台,采用的是高低压泵合流。
额定流量为100升,系统额定最高压力为31.5MPa。
为了突出重点,便于叙述,适当做了一些简化。
一液压基本回路一个实用的液压系统原理图都是由液压基本回路组成的。
液压基本回路可以在机械设计手册,或者其他液压设计资料中查到。
1 液压基本回路的分类设计资料中介绍的液压基本回路分类很详细。
但总括起来无非是,泵-电机组,压力控制回路,流量控制回路,方向控制回路和执行机构。
参看图1油缸试验台液压原理图。
在图1中,电机M1 Y112M-4和斜盘柱塞泵10YCY14-1B,电机Y160M-4和叶片泵YB1-80,组成泵-电机组,为系统提供动力;先导卸荷阀③,安全溢流阀④,电磁溢流阀⑤,组成压力控制回路;电液换向阀⑥和先导式液控单向阀⑦,组成方向控制回路。
一般说来,流量控制往往会伴随着压力的损失。
例如,在薄壁节流小孔中,流量d Q C A = (1) 此公式的使用条件为0.5l d≤。
式中Q —经过薄壁小孔的流量,3/m s ;d C —薄壁小孔流量系数,对于紊流,0.600.61d C = ; 0A —孔口面积,2m ; ρ—流体的密度,3/kg m ; p ∆—压力差,12p p p ∆=−,Pa ;d —小孔的直径,m ; l —小孔的长度,m 。
这种压力能损失往往转化为热能,使液压系统升温。
在理论上,变量泵不会因为流量或压力的变量产生能量损失。
2 液压基本回路的联结液压基本回路,特别是液压元件,在液压原理图中的联结,要么是并联,要么是串联。
二 液压系统原理图1 液压系统原理图应该包括的的基本内容一个符合要求的液压原理图除了表示系统外,还应该包括两个基本内容:液压元件明细表和电磁铁动作顺序表。
液压基本回路及典型液压系统

1压力控制回路
1压力控制回路
2 )利用蓄能器的保压回路: 这种 蓄能器借助蓄能器来保持系统压力, 补偿系统泄漏。图5-10所示为利用虎 钳做工件的夹紧。将换向阀移到阀左 位时,活塞前进将虎钳夹紧,这时泵 继续输出的压力油将蓄能器充压,直 到卸荷阀被打开卸载,此时作用在活 塞上的压力由蓄能器来维持并补充液 压缸的漏油作用在活塞上,当工作压 力降低到比卸荷阀所调定的压力还低 时,卸荷阀又关闭,泵的液压油再继 续送往蓄能器。本系统可节约能源并 回路是利用压力控制阀来控制系统整体或某 一部分的压力,以满足液压执行元件对力或转矩要求的回路, 这类回路包括调压、减压、增压、保压、卸荷和平衡等多种 回路。 1.1 调压回路:调压回路的功用是使液压系统整体或部分的 压力保持恒定或不超过某个数值。在定量泵系统中,液压泵 的供油压力可以通过溢流阀来调节。在变量泵系统中 , 用安 全阀来限定系统的最高压力,防止系统过载。若系统中需要 二种以上的压力,则可采用多级调压回路。
中南大学——液压与气动技术 2019年2月2日星期六
2 速度控制回路 1. 快速与慢速的换接回路:
5.2 速度控制回路
2.两种慢速的换接回路:图5-16a中的两个调速阀并联,由换向 阀实现换接。两个调速阀可以独立地调节各自的流量.互不影响;但是. 一个调速阀工作时另一个调速阀内无油通过,它的减压阀不起作用而 处于最大开口位置,因而速度换接时大量油液通过该处将使机床工作 部件产生突然前冲现象。因此它不宜用于在工作过程中的速度换接, 只可用在速度预选的场合。 图5-16b所示为两调速阀串联的速度换接回路。当主换向阀D左位 接人系统时,调速阀B被换向阀C短接;输入液压缸的流量由调速阀A 控制。当阀C右位接入回路时,由于通过调速阀B的流量调得比A小, 所以输入液压缸的流量由调速阀B控制。在这种回路中的调速阀A一直 处于工作状态,它在速度换接时限制着进入调速阀B的流量,因此它的速 度换接平稳性较好,但由于油液经过两个调速阀,所以能量损失较大。
(完整word版)液压系统回路设计

1、液压系统回路设计1.1、 主干回路设计对于任何液压传动系统来说, 调速回路都是它的核心部分。
这种回路可以通过事先的调整或在工作过程中通过自动调整来改变元件的运行速度, 但它的主要功能却是在传递动力(功率)。
根据伯努力方程: 2d v p q C x ρ∆= (1-1)式中 q ——主滑阀流量d C ——阀流量系数v x ——阀芯流通面积p ∆——阀进出口压差ρ——流体密度其中 和 为常数, 只有 和 为变量。
液压缸活塞杆的速度:q v A= (1-2) 式中A 为活塞杆无杆腔或有杆腔的有效面积一般情况下, 两调平液压缸是完全一样的, 即可确定 和 所以要保证两缸同步, 只需使 , 由式(1-2)可知, 只要主滑阀流量一定, 则活塞杆的速度就能稳定。
又由式(1-1)分析可知, 如果 为一定值, 则主滑阀流量 与阀芯流通面积成正比即: ,所以要保证两缸同步, 则只需满足以下条件:, 且此处主滑阀选择三位四通的电液比例方向流量控制阀,如图1-1所示。
图1-1 三位四通的电液比例方向流量控制阀它是一种按输入的电信号连续地、按比例地对油液的流量或方向进行远距离控制的阀。
比例阀一般都具有压力补偿性能, 所以它输出的流量可以不受负载变化的影响。
与手动调节的普通液压阀相比, 它能提高系统的控制水平。
它和电液伺服阀的区别见表1-1。
表1-1 比例阀和电液伺服阀的比较项目 比例阀 伺服阀低, 所以它被广泛应用于要求对液压参数进行连续远距离控制或程序控制, 但对控制精度和动态特性要求不太高的液压系统中。
又因为在整个举身或收回过程中, 单缸负载变化范围变化比较大(0~50T), 而且举身和收回时是匀速运动, 所以调平缸的功率为, 为变功率调平, 为达到节能效果, 选择变量泵。
综上所可得, 主干调速回路选用容积节流调速回路。
容积节流调速回路没有溢流损失, 效率高, 速度稳定性也比单纯容积调速回路好。
为保证值一定, 可采用负荷传感液压控制, 其控制原理图如图1-2所示。
液压回路设计缺陷及改进

第8卷第4期浙江工贸职业技术学院学报V ol.8No.42008年12月JOURNAL OF ZHEJIANG INDUSTRY&TRAD E VOCATIO NAL COLLEG E Dec .2008液压回路设计缺陷及改进郑秀丽王文深(浙江工贸职业技术学院,浙江温州325003)摘要:本文介绍了液压回路常见的一些设计缺陷,对故障的原因进行了简要的分析归纳,并提出了改进的措施,目的是使读者对液压设备进行设计时能做到最合理,能避免一些常见的错误。
关键词:液压回路;设计缺陷;改进中图分类号:TH122文献标识码:A 文章编号:1672-0105(2008)04-0057-04Disadvanta ges of Hydr aulic Cir cuit Design and Its I mpr ovementZheng Xiuli,Wang W enshin(Zhejiang Industry &Trade V ocational College,W enzhou Zhejaing 325003)Abstract:This paper introduces some disadvantages of hydraulic circuit and also analyzes the reasons for it.Countermeansures are proposed to make readers understand about the rationality of hydraulic pressure design.Key words:Hydraulic circuit,Design disadvantages;Improvement液压技术在机械行业中是比较新的技术,在现代工业中得到越来越广泛的应用。
但是由于液压回路设计上的缺陷,使液压设备达不到预定要求甚至不能正常工作。
回路设计缺陷是先天性的,比较难于彻底消除。
- 1、下载文档前请自行甄别文档内容的完整性,平台不提供额外的编辑、内容补充、找答案等附加服务。
- 2、"仅部分预览"的文档,不可在线预览部分如存在完整性等问题,可反馈申请退款(可完整预览的文档不适用该条件!)。
- 3、如文档侵犯您的权益,请联系客服反馈,我们会尽快为您处理(人工客服工作时间:9:00-18:30)。
1、液压系统回路设计
1.1、 主干回路设计
对于任何液压传动系统来说,调速回路都是它的核心部分。
这种回路可以通过事先的调整或在工作过程中通过自动调整来改变元件的运行速度,但它的主要功能却是在传递动力(功率)。
根据伯努力方程: 2d v p q C x ρ∆= (1-1)
式中 q ——主滑阀流量
d C ——阀流量系数
v x ——阀芯流通面积
p ∆——阀进出口压差
ρ——流体密度
其中d C 和ρ为常数,只有v x 和p ∆为变量。
液压缸活塞杆的速度:
q v A
= (1-2) 式中A 为活塞杆无杆腔或有杆腔的有效面积
一般情况下,两调平液压缸是完全一样的,即可确定1121A A =和1222A A =所以要保证两缸同步,只需使12q q =,由式(1-2)可知,只要主滑阀流量一定,则活塞杆的速度就能稳定。
又由式(1-1)分析可知,如果p ∆为一定值,则主滑阀流量q 与阀芯流通面积成正比即:v q x ∞,所以要保证两缸同步,则只需满足以下条件:
11p c ∆=,22p c ∆=且12v v x x =
此处主滑阀选择三位四通的电液比例方向流量控制阀,如图1-1所示。
图1-1 三位四通的电液比例方向流量控制阀
它是一种按输入的电信号连续地、按比例地对油液的流量或方向进行远距离控制的阀。
比例阀一般都具有压力补偿性能,所以它输出的流量可以不受负载变化的
影响。
与手动调节的普通液压阀相比,它能提高系统的控制水平。
它和电液伺服阀的区别见表1-1。
所以它被广泛应用于要求对液压参数进行连续远距离控制或程序控制,但对控制精度和动态特性要求不太高的液压系统中。
又因为在整个举身或收回过程中,单缸负载变化范围变化比较大(0~50T),而且举身和收回时是匀速运动,所以调平缸的功率为P Fv
=,为变功率调平,为达到节能效果,选择变量泵。
综上所可得,主干调速回路选用容积节流调速回路。
容积节流调速回路没有溢流损失,效率高,速度稳定性也比单纯容积调速回路好。
为保证p∆值一定,可采用负荷传感液压控制,其控制原理图如图1-2所示。
它主要利用负荷传感和压力补偿技术,可用单泵(或一组泵)驱动多个执行元件,各执行元件运动速度仅依赖于各节流阀开启度,而与各执行元件的负载压力和其它执行元件的工作状态无关。
即使当泵的输出流量达不到实际需要时,各执行元件运动速度的比例关系仍然可以得到保持。
此系统的这一特有的独立调速功能大大减少了作业中操纵者协调各执行元件动作所花费的时间,不但显著提高了作业效率,而且有效减轻了操作者的劳动强度。
另外,能够以最节省能量的方式实现调速,系统无溢流损失,并以推动执行元件动作所需的最低压力供油。
在工作间隙(发动机不停机,各执行元件处于无载状态,不动作),系统自动调节泵的排量到最小值。
可以有效降低功率损耗、减小液压系统的温升,所以它是一种性能较好的新型液压系统。
一般的同步回路还有:机械连接同步回路;用分流阀或分流集流阀的同步回路;用调速阀的同步回路;串联缸的同步回路等,但这些同步回路同步精度一般比较低,而且大多数只是保证速度同步而不能保证位置同步,受负载变化的影响较大。
图1-2 LS 同步控制系统原理图
图中两个执行元件中的最高压力,可以通过单向阀选出,作为负荷传感压力LS P 分别引到负荷传感阀和各压力补偿阀的弹簧腔。
当负荷传感阀芯及各压力补偿阀芯达到平衡时,各节流口前压力1p 为负荷传感压力LS P 加上负荷传感阀下腔弹簧压力KL p ; 各节流口后压力2p 均为负荷传感压力LS P 加上压力补偿阀左腔弹簧压力KC p ,两节流口压力差为:
12KL KC p p p p p ∆=-=-
可知,p ∆只与两弹簧弹力有关,所以只要保证两弹簧压力差恒定,则p ∆值基本为一定值。
因而通过各节流口流向执行元件的流量与各节流口大小有关,而与每一执行元件的负载压力无关。
为保证桅杆工作时的垂直度,选用一种倾角传感器,将检查到的角度偏差信号转换成电信号,控制电液比例方向流量控制阀,从而调节桅杆的垂直度。
组干回路如图1-3所示。
图1-3 主干回路
1、2 其它回路选择
1、平衡回路
平衡回路的功用在于防止垂直或倾斜放置的液压缸和与之相连的工作部件因自重而自行下落。
桅杆后仰和前倾时都要平衡,因此连接油缸两端的回油路上都要设有起平衡作用的阀。
下面主要考虑两种平衡回路,分别如图1-4和1-5所示。
图1-4 用直控平衡阀的平衡回路
用直控平衡阀的平衡回路。
调整平衡阀的开启压力,使其稍大于立式液压缸活塞及其工作部件自重在液压缸下腔所产生的压力,活塞部件则不会因自重而下落。
活塞下降时,运动平稳,但功耗较大。
图1-5 用远控平衡阀平衡的回路
用远控平衡阀平衡的平衡回路。
远控平衡阀的开启取决于控制压力,与载荷无关。
在活塞下行时,平衡阀被控制油打开,被压很小,故系统效率较高。
但活塞部件有可能加速下滑,以致产生振荡,所以应在平衡阀的控制口接入节流阀。
2、锁紧回路
锁紧回路的功用是在液压执行元件不工作时切断其进、出油通道,确切地使是它保持在既定的位置上。
下面也主要考虑两种锁紧回路,如图1-6和1-7所示。
图1-6 用换向阀锁紧的回路
用换向阀锁紧的回路。
三位四通换向阀在中位时,分别与油缸相连的两油路被封闭,构成了双向锁紧回路。
采用换向阀锁紧,回路简单,但是锁紧精度较低。
图1-7 用液控单向阀双向锁紧的回路
用液控单向阀双向锁紧的回路。
用两个液控单向阀可实现对液压缸的双向锁紧。
图示位置时,液压泵卸荷,两个液控单向阀均为关闭,活塞被所在不动。
活塞可以在任意位置被锁紧。
考虑桅杆的功能要求:由于桅杆自身重力的作用,举身过程要比较平稳,而且在任意位置要能被锁定,所以被压阀的压力值要设得比较小;工作是也要很好的被锁住;前倾是也要平稳和能被锁住,所以被压阀值要设得比较大。
再考虑
到平衡和锁紧的功能,可以使用液控平衡阀来同时实现这两个作用。
其原理如图1-8所示。
图1-8 用液控平衡阀的平衡锁紧回路
举身过程中,开始时桅杆自重对液压缸的压力比较大,进油路压力很大,所以回油路上的被压值很小,随着举身过程的进行桅杆自重对缸的压力减小,回油路上的被压值也随着增加。
前倾过程中,进油路上压力值很小,所以回油路上的被压值特别大,收回过程和此分析相反。
要锁紧时可以可以用换向阀切断进油路,从而靠平衡阀直接锁住。
1、3 液压回路综合
把上面选出的各种回路组合画在一起,再经过修改、整理后,可得到总的液压系统原理图,如图1-9所示。
图1-9液压系统原理图
1-负荷传感变量泵 2-单向阀 3-三位四通电液比例换向阀 4-平衡阀 5-单向阀
6-梭阀 7-负荷传感阀 8-压力切断阀 9-压力补偿阀 10-滤油器。