数控机床的自动换刀装置设计
数控加工系统的自动换刀装置
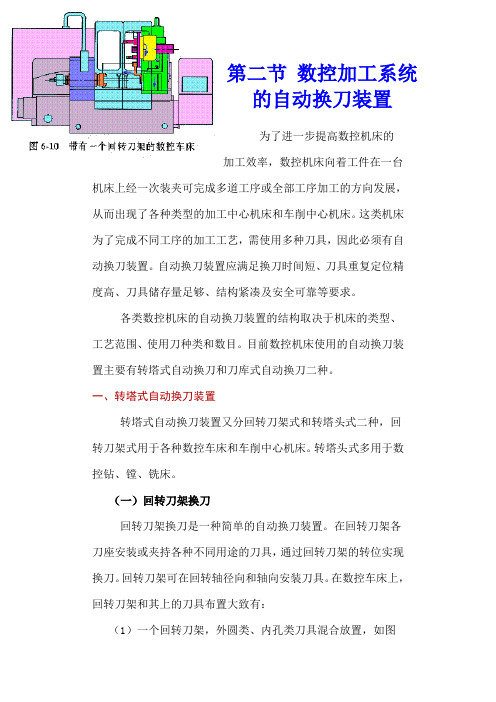
第二节数控加工系统的自动换刀装置为了进一步提高数控机床的加工效率,数控机床向着工件在一台机床上经一次装夹可完成多道工序或全部工序加工的方向发展,从而出现了各种类型的加工中心机床和车削中心机床。
这类机床为了完成不同工序的加工工艺,需使用多种刀具,因此必须有自动换刀装置。
自动换刀装置应满足换刀时间短、刀具重复定位精度高、刀具储存量足够、结构紧凑及安全可靠等要求。
各类数控机床的自动换刀装置的结构取决于机床的类型、工艺范围、使用刀种类和数目。
目前数控机床使用的自动换刀装置主要有转塔式自动换刀和刀库式自动换刀二种。
一、转塔式自动换刀装置转塔式自动换刀装置又分回转刀架式和转塔头式二种,回转刀架式用于各种数控车床和车削中心机床。
转塔头式多用于数控钻、镗、铣床。
(一)回转刀架换刀回转刀架换刀是一种简单的自动换刀装置。
在回转刀架各刀座安装或夹持各种不同用途的刀具,通过回转刀架的转位实现换刀。
回转刀架可在回转轴径向和轴向安装刀具。
在数控车床上,回转刀架和其上的刀具布置大致有:(1)一个回转刀架,外圆类、内孔类刀具混合放置,如图6-10所示。
(2)两个回转刀架,分别布置外圆和内孔类刀具。
如图6-11所示,上刀架的回转轴与主轴平行,用于装外圆类刀具;下刀架的回转轴与主轴垂直,用于装内孔类刀具。
图6-11 带有两个回转刀架的数图6-12 双排回转刀架外形图控车床(3)一个回转刀架,外圆类、内孔类刀具分别布置在刀架的一侧面,如图6-12所示。
回转刀架的回转轴与主轴倾斜,每个刀位上可装两把刀具,用于加工外圆和内孔。
回转刀架的工位数最多可达20余个,但最常用的是8、10、12和16工位4种。
工位数越多,刀间夹角越小,非加工位置刀具与工件相碰而产生的干涉可能性越大;在刀架布刀时要给予考虑,避免发生干涉现象。
回转刀架在结构上必须具有良好的强度和刚度,以承受粗加工时切削抗力和减小刀架在切削力作用下的位移变形,提高加工精度。
回转刀架还要选择可靠的定位方案和定位结构,以保证回转刀架在每次转位之后具有高的重复定位精度。
第4章 数控机床自动换刀装置
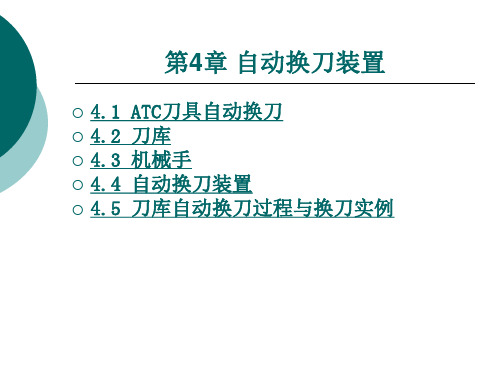
上一页 下一页 返回
4.2 刀库
统计了15000种工件,按成组技术分析,各种加工刀具所必需 的刀具数的结果是:4把刀的容量就可以完成95%左右的铣削 工艺,10把孔加工刀具可完成70%的钻削工艺,因此,14把刀 的容量就可完成70~以上的工件钻削工艺。如果从完成工件的
全部加工所需的刀具数目统计,所得结果是80%的工件完成全
上一页 下一页 返回
4.3 机械手
2. 刀库夹爪 刀库夹爪既起着刀套作用,又起着手爪的作用。如图4-19 所示为刀库夹爪图。
4.3.4 机械手结构原理
如图4-20所示,机械手结构及工作原理如下。 机械手有两对抓刀爪,分别由液压缸1驱动其动作。当液压 缸推动机械手抓刀爪外伸时,抓刀爪上的销轴3在支架上的 导向槽2向滑动,使抓刀绕销4摆动,抓刀爪合拢抓住刀具; 当液压缸间缩时,支架2上的导向槽迫使抓刀爪张开,放松 刀具。由于抓刀动作由机械机构实现,且能自锁,因此工作 安全可靠.
上一页 下一页 返回
4.3 机械手
4.3.5 机械手的驱动机构
如图4-21所示为机械手的驱动机构。汽缸1通过杆6带动机械 手臂升降。当机械手在上边位置时,液压缸4通过齿条2、齿 轮3、传动盘5、杆6带动机械手臂回转;当机械手在下边位置 时,汔缸7通过齿条9、齿轮8、传动盘5和杆6,带动手臂回转。 如图4-22所示为机械手臂和手爪结构图。手臂的两端各有一 手爪。刀具被带弹簧1的活动销4紧靠着固定爪5。锁紧销2被 弹簧3弹起,使活动销4被锁位,不能后退,这就保证了在机 械手运动过程中,手爪中的刀具不会被甩出。当手臂在上方 位置从裙位置转过750时锁昆锁2被挡块压下,活动锁4就可以 活动,使得机械手可以抓住主轴和刀套中的刀具。
数控机床的自动换刀装置设计
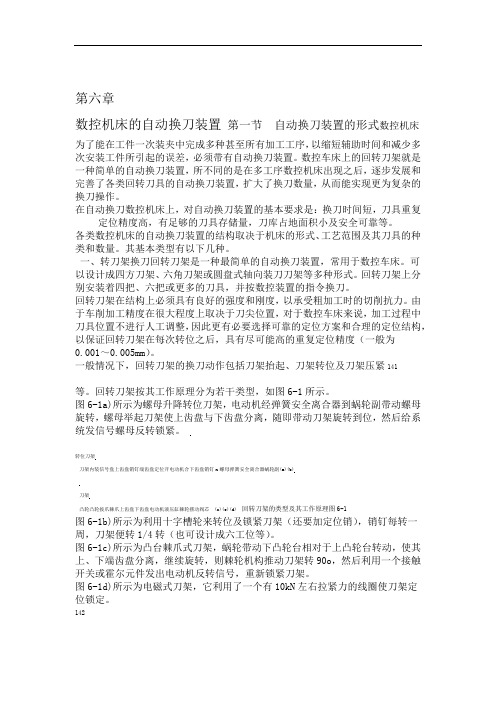
第六章数控机床的自动换刀装置第一节自动换刀装置的形式数控机床为了能在工件一次装夹中完成多种甚至所有加工工序,以缩短辅助时间和减少多次安装工件所引起的误差,必须带有自动换刀装置。
数控车床上的回转刀架就是一种简单的自动换刀装置,所不同的是在多工序数控机床出现之后,逐步发展和完善了各类回转刀具的自动换刀装置,扩大了换刀数量,从而能实现更为复杂的换刀操作。
在自动换刀数控机床上,对自动换刀装置的基本要求是:换刀时间短,刀具重复定位精度高,有足够的刀具存储量,刀库占地面积小及安全可靠等。
各类数控机床的自动换刀装置的结构取决于机床的形式、工艺范围及其刀具的种类和数量。
其基本类型有以下几种。
一、转刀架换刀回转刀架是一种最简单的自动换刀装置,常用于数控车床。
可以设计成四方刀架、六角刀架或圆盘式轴向装刀刀架等多种形式。
回转刀架上分别安装着四把、六把或更多的刀具,并按数控装置的指令换刀。
回转刀架在结构上必须具有良好的强度和刚度,以承受粗加工时的切削抗力。
由于车削加工精度在很大程度上取决于刀尖位置,对于数控车床来说,加工过程中刀具位置不进行人工调整,因此更有必要选择可靠的定位方案和合理的定位结构,以保证回转刀架在每次转位之后,具有尽可能高的重复定位精度(一般为0.001~0.005mm)。
一般情况下,回转刀架的换刀动作包括刀架抬起、刀架转位及刀架压紧141等。
回转刀架按其工作原理分为若干类型,如图6-1所示。
图6-1a)所示为螺母升降转位刀架,电动机经弹簧安全离合器到蜗轮副带动螺母旋转,螺母举起刀架使上齿盘与下齿盘分离,随即带动刀架旋转到位,然后给系统发信号螺母反转锁紧。
转位刀架刀架内装信号盘上齿盘销钉端齿盘定位开电动机合下齿盘销钉n螺母弹簧安全离合器蜗轮副(a)(b)刀架凸轮凸轮拔爪棘爪上齿盘下齿盘电动机液压缸棘轮摆动阀芯(c)(e)(d)回转刀架的类型及其工作原理图6-1图6-1b)所示为利用十字槽轮来转位及锁紧刀架(还要加定位销),销钉每转一周,刀架便转1/4转(也可设计成六工位等)。
数控机床自动换刀装置
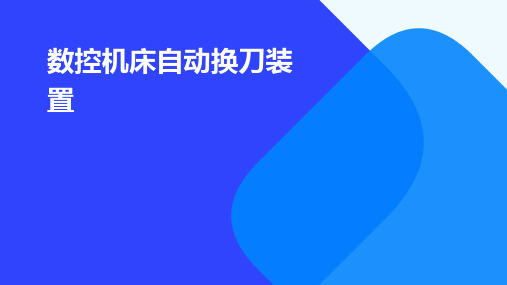
02
数控机床自动换刀装置 的结构与设计
刀库设计
刀库容量
根据数控机床的加工需求, 合理设计刀库容量,确保 能够存放足够数量的刀具。
刀具存放方式
采用合适的刀具存放方式, 如刀具架、刀具套等,以 便于刀具的存取和管理。
刀库布局
根据数控机床的整体布局 和加工要求,合理布置刀 库的位置和方向,以提高 换刀效率和加工精度。
例如,在发动机缸体的加工中,需要使用不同种类的刀具进行粗加工、半精加工和精加工。数控机床 自动换刀装置可以在加工过程中自动识别需要更换的刀具,并快速、准确地完成换刀操作,保证了加 工过程的连续性和稳定性。
应用案例二:航空航天业
航空航天业对零部件的加工精度和效率要求极高,数控机床自动换刀装置在航空 航天业中也有着广泛的应用。例如,在飞机机身和机翼的制造中,需要使用大型 五轴数控机床进行加工,而大型五轴数控机床的换刀时间较长,影响了加工效率 。
数控机床自动换刀装置的应用,可以大大缩短换刀时间,提高加工效率。同时, 由于航空航天业对零部件的加工精度要求极高,数控机床自动换刀装置的精确性 和稳定性也得到了充分验证,为航空航天业的发展提供了有力支持。
应用案例三:模具制造业
模具制造业是数控机床自动换刀装置的重要应用领域 之一。在模具的制造过程中,需要使用不同种类的刀 具进行粗加工、半精加工和精加工。数控机床自动换 刀装置的应用,可以大大提高模具的加工效率和精度 。
分类与比较
按换刀方式分类
数控机床自动换刀装置可分为机械手换刀和机器人换刀两种 方式。机械手换刀方式具有结构简单、成本低等优点,但换 刀速度较慢;机器人换刀方式具有换刀速度快、精度高等优 点,但结构复杂、成本较高。
按刀库类型分类
数控机床自动换刀装置可分为固定刀库和旋转刀库两种类型 。固定刀库具有容量大、换刀速度快等优点,但结构复杂、 成本较高;旋转刀库具有结构简单、成本低等优点,但容量 较小、换刀速度较慢。
第2章自动换刀装置
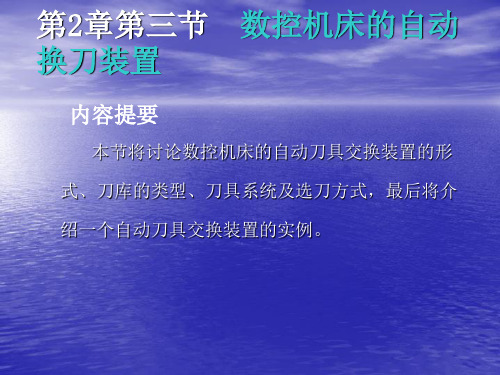
➢ 这类换刀装置应用最广泛。
刀库装在机床的工作台上 ,这种换刀装置,直接利 用机床本身及刀库的运动 进行换刀。当某一刀具加 工完毕从工件退出后,即 开始进行自动换刀 。
现在的中小型加工中心,刀 库不是装在工作台上,而是 装在立柱上的一个托架上。 采用刀库在托架的导轨上平 行于X方向运动与主轴的上 下运动实现换刀。
2.为什么需要自动换刀装置:
• 缩短非切削时间,提高生产率,可使非切削时间减少到20
%~30%;
• “工序集中”,扩大数控机床工艺范围,减少设备占地面积; • 提高加工精度;
– 数控机床对ATC要求:
• 换刀时间尽可能短; • 刀具重复定位精度高; • 刀具储存量足够; • 结构紧凑,便于制造、维修、调整; • 布局应合理,使机床总布局美观大方; • 较好的刚性,避免冲击、振动及噪声,运转安全可靠; • 防屑、防尘装置。
第2章第三节 数控机床的自动 换刀装置
内容提要
本节将讨论数控机床的自动刀具交换装置的形 式、刀库的类型、刀具系统及选刀方式,最后将介 绍一个自动刀具交换装置的实例。
一、概述
1.什么是自动换刀装置:
• 储备一定数量的刀具并完成刀具的自动交换功能的装置 • ATC:Automatic Tool Changer
当刀库的容量大、刀具较重或机床总体布局等原因, 刀库也可作为一个独立部件,装在机床之外
刀库远离主轴,常常要 附加运输装置,来完成 刀库与主轴之间刀具的 运输。
•为了缩短换刀时间,可采用带刀库的双
主轴或多主轴换刀系统
三、刀 库
• 1、刀库的形式
(1)盘式刀库
自动换刀装置

为完成对工件的多工序加工而设置的存储及更换 刀具的装置称为自动换刀装置(Automatic Tool Changer, ATC)。 自动换刀装置应当满足的基本要求为:
刀具换刀时间短且换刀可靠。 刀具重复定位精度高。 足够的刀具储存量。 结构简单,便于制造、维修、调整。 布局合理,机床总布局美观大方。
编码识别装置
接触式刀具识别装置的原理
非接触式磁性识别原理图
光导纤维刀具识别原理图
刀座编码方式
对每个刀座都进行编码,刀具也编号,并将刀具放到与 其号码相符的刀座中,换刀时刀库旋转,使各个刀座依次经 过识刀器,直至找到规定的刀座,刀库停止旋转。
如图所示为圆盘形刀库的刀 座编码装置。在圆盘的圆周上均 匀分布若干个刀座,其外侧边缘 上装有相应的刀座识别装置2。 刀座编码的识别原理与刀具编码 完全相同.
(6)主轴箱及主轴带着刀具上升;
(7)机床工作台快速向左返回,将刀库 从主轴下面移开,同时将工件移至主轴 数控立式镗铣床
下面,使主轴上的刀具对准工件的加工
面。
四、刀具交换装置
1、利用刀库与机床主轴的相对运动实现刀具交换
这种自动换刀装置只有一个刀库, 不需要其他装置,结构极为简单,然而 换刀过程却较为复杂。 另外,由于刀库置于工作台上,因 而减少了工作台的有效使用面积。这种 换刀装置多用于小型低价位的加工中心。
转塔头主轴通常只适应于工序较少,精度要求 不太高的机床,如数控钻床、铣床等。
一、自动换刀装置的型式——转塔头式换刀装置
优点: 省去了自动松、夹、装刀、卸刀以及刀具搬运等一系 列的复杂操作,从而缩短了换刀时间(仅为2s左右), 并提高了换刀的可靠性。
缺点: 由于空间位置的限制,使主轴部件结构不能设计得十 分坚实,因而影响了主轴系统的刚度。为了保证主轴的 刚度,必须限制主轴数目,否则将使结构尺寸大大增加。
数控机床自动换刀系统的设计与优化方法

数控机床自动换刀系统的设计与优化方法数控机床自动换刀系统作为现代制造业中的关键设备之一,其设计和优化对于提高生产效率和产品质量至关重要。
本文将讨论数控机床自动换刀系统的设计原理、关键技术以及优化方法,旨在指导工程师和研究人员进行相关工作。
首先,数控机床自动换刀系统的设计原理主要包括以下几个方面:刀具库、刀具传递机构和换刀动作控制。
刀具库是存放刀具的地方,通常设计成可自动旋转、抬升和倾斜的结构,以便于刀具的选择和取放。
刀具传递机构用于将所需刀具从刀具库传递到机床主轴上,并确保刀具的正确位置和方向。
换刀动作控制则通过编程和传感器来实现,保证换刀过程的准确性和稳定性。
在设计数控机床自动换刀系统时,我们需要注意一些关键技术。
首先是刀具库的设计,刀具库的容量和结构需要根据实际工作中所涉及到的刀具种类和数量进行合理规划。
其次是刀具传递机构的设计,传递机构需要具备快速、准确的传递能力,同时要考虑到刀具重量对传递机构的负荷影响,确保稳定性。
换刀动作控制需要精确控制刀具的位置和方向,可以采用光电传感器或编码器等传感器,通过编程实现动作的控制和判断。
为了进一步优化数控机床自动换刀系统的性能,我们可以采取一些优化方法。
首先是刀具库的优化,可以采用高效的刀具存放方案,如采用自动尺寸检测技术,将刀具按照尺寸进行分类存放,方便快速选择和取放。
其次是刀具传递机构的优化,可以采用更先进的传递机构设计,如采用电磁吸盘或气动夹持装置等,提高传递速度和准确性。
此外,还可以通过改进换刀动作控制算法,优化换刀过程的稳定性和精度。
在优化设计过程中,还需要充分考虑数控机床自动换刀系统的可靠性和安全性。
可靠性是指系统在长时间运行中的稳定性和故障率,我们可以通过选用高质量的部件和进行严格的测试来提高可靠性。
安全性是指系统在使用过程中的安全保障,我们需要设置安全装置,如机械锁或密码锁等,防止误操作或意外伤害的发生。
总结起来,数控机床自动换刀系统的设计与优化需要考虑刀具库、刀具传递机构和换刀动作控制等关键技术。
数控机床自动换刀系统的设计与优化方法

数控机床自动换刀系统的设计与优化方法随着工业自动化的不断发展,数控机床自动换刀系统的设计与优化成为了现代制造业中的重要课题。
自动换刀系统的设计及其优化将直接影响到机床的生产效率、工件加工质量和操作人员的工作安全。
因此,本文将探讨数控机床自动换刀系统的设计原理以及进行系统优化的方法与技巧。
数控机床自动换刀系统一般包括刀库、刀臂、刀杆及刀具,其工作原理主要通过机械臂或伺服电机的驱动,将机床上的刀具自动更换。
而系统的设计与优化则需要考虑以下几个方面:首先,需要充分考虑机床的具体工艺需求,确定自动换刀系统的基本功能。
例如,切削加工中是否需要进行多种不同刀具的切换,是否需要对不同刀具进行刃磨和测量等。
不同工艺需求将直接影响到自动换刀系统的设计与优化。
其次,需要考虑自动换刀系统的结构设计。
合理的结构设计能够提高系统的稳定性和工作效率,并降低故障率。
一般来说,自动换刀系统的结构主要包括刀库结构、刀臂结构以及刀杆结构。
在设计过程中,需要充分考虑机床的空间限制、刀具数量以及换刀的速度等因素。
同时,需要关注自动换刀系统的动力传递和控制电路设计。
动力传递系统的设计主要包括伺服电机的选型、减速器的设计以及传动链的布置等。
而控制电路的设计则需要考虑自动控制装置和信号传输装置等,以确保系统的稳定性和可靠性。
另外,还需要考虑自动换刀系统的安全性。
刀具在运行过程中可能会产生较大的动力和惯性力,因此在设计过程中需要充分考虑刀具的固定、刀具与工件之间的安全间隙以及系统紧急停机装置的设置等,以确保操作人员的安全。
在完成基本的设计后,系统的优化工作则需从以下几个方面展开。
首先是换刀时间的优化。
通过减少换刀时间可以提高机床的利用率,并减少生产成本。
换刀时间的优化可以从刀具定位、刀具固定方式以及刀具检测等方面进行。
其次是系统的可靠性优化。
这需要考虑到刀库的结构设计、刀具的装卸方式以及系统故障的自我诊断与修复等。
同时,充分考虑刀具的损耗和磨损,合理安排刀具的使用周期,减少系统故障的发生。
- 1、下载文档前请自行甄别文档内容的完整性,平台不提供额外的编辑、内容补充、找答案等附加服务。
- 2、"仅部分预览"的文档,不可在线预览部分如存在完整性等问题,可反馈申请退款(可完整预览的文档不适用该条件!)。
- 3、如文档侵犯您的权益,请联系客服反馈,我们会尽快为您处理(人工客服工作时间:9:00-18:30)。
第六章数控机床的自动换刀装置第一节自动换刀装置的形式数控机床为了能在工件一次装夹中完成多种甚至所有加工工序,以缩短辅助时间和减少多次安装工件所引起的误差,必须带有自动换刀装置。
数控车床上的回转刀架就是一种简单的自动换刀装置,所不同的是在多工序数控机床出现之后,逐步发展和完善了各类回转刀具的自动换刀装置,扩大了换刀数量,从而能实现更为复杂的换刀操作。
在自动换刀数控机床上,对自动换刀装置的基本要求是:换刀时间短,刀具重复定位精度高,有足够的刀具存储量,刀库占地面积小及安全可靠等。
各类数控机床的自动换刀装置的结构取决于机床的形式、工艺范围及其刀具的种类和数量。
其基本类型有以下几种。
一、转刀架换刀回转刀架是一种最简单的自动换刀装置,常用于数控车床。
可以设计成四方刀架、六角刀架或圆盘式轴向装刀刀架等多种形式。
回转刀架上分别安装着四把、六把或更多的刀具,并按数控装置的指令换刀。
回转刀架在结构上必须具有良好的强度和刚度,以承受粗加工时的切削抗力。
由于车削加工精度在很大程度上取决于刀尖位置,对于数控车床来说,加工过程中刀具位置不进行人工调整,因此更有必要选择可靠的定位方案和合理的定位结构,以保证回转刀架在每次转位之后,具有尽可能高的重复定位精度(一般为0.001~0.005mm)。
一般情况下,回转刀架的换刀动作包括刀架抬起、刀架转位及刀架压紧等。
回转刀架按其工作原理分为若干类型,如图6-1所示。
图6-1a)所示为螺母升降转位刀架,电动机经弹簧安全离合器到蜗轮副带动螺母旋转,螺母举起刀架使上齿盘与下齿盘分离,随即带动刀架旋转到位,然后给系统发信号螺母反转锁紧。
(e)(d)(c)(b)(a)图6-1 回转刀架的类型及其工作原理图6-1b)所示为利用十字槽轮来转位及锁紧刀架(还要加定位销),销钉每转一周,刀架便转1/4转(也可设计成六工位等)。
图6-1c)所示为凸台棘爪式刀架,蜗轮带动下凸轮台相对于上凸轮台转动,使其上、下端齿盘分离,继续旋转,则棘轮机构推动刀架转90º,然后利用一个接触开关或霍尔元件发出电动机反转信号,重新锁紧刀架。
图6-1d)所示为电磁式刀架,它利用了一个有10kN 左右拉紧力的线圈使刀架定位锁定。
图6-1e)所示为液压式刀架,它利用摆动液压缸来控制刀架转位,图中有摆动阀芯、拨爪、小液压缸;拨爪带动刀架转位,小液压缸向下拉紧,产生10kN 以上的拉紧力。
这种刀架的特点是转位可靠,拉紧力可以再加大,但其缺点是液压件难制造,还需多一套液压系统,有液压油泄漏及发热问题。
图6-2所示为数控车床的六角回转刀架,它适用于盘类零件的加工。
这种刀架的全部动作由液压系统通过电磁换向阀和顺序阀进行控制,其换刀过程如下:(1)刀架抬起。
当数控装置发出换刀指令后,压力油由A 进入压紧液压缸的下腔,活塞上升,刀架体抬起,使定位活动插销与固定插销脱离。
同时,活塞杆下端的端齿离合器与空套齿轮结合。
压盘齿轮活塞B图6-2 数控车床的六角回转刀架(2)刀架转位。
当刀架抬起之后,压力油从C 孔转入液压缸左腔,活塞向右移动,通过连接板带动齿条移动,使空套齿轮作逆时针方向转动,通过端齿离合器使刀架转过60º。
活塞的行程应等于齿轮节圆周长的1/6,并由限位开关控制。
(3)刀架压紧。
刀架转位之后,压力油从B 孔进入压紧液压缸的上腔,活塞带动刀架体下降。
缸体的底盘上精确地安装六个带斜楔的圆柱固定插销,利用活动插销消除定位销与孔之间的间隙,实现反靠定位。
刀架体下降时,定位活动插销与另一个固定插销卡紧,同时缸体与压盘的锥面接触,刀架在新的位置定位并压紧。
这时,端齿离合器与空套齿轮脱开。
(4)转位液压缸复位。
刀架压紧后,压力油从D孔进入转位油缸右腔,活塞带动齿条复位,由于此时端齿离合器已脱开,齿条带动齿轮在轴上空转。
如果定位和压紧动作正常,拉杆与相应的接触头接触,发出信号表示换刀过程已结束,可以继续进行切削加工。
回转刀架除了采用液压缸驱动转位和定位销定位外,还可以采用电动机-马氏机构转位和鼠盘定位,以及其它转位和定位机构。
二、换主轴换刀更换主轴换刀是带有旋转刀具的数控机床的一种比较简单的换刀方式。
这种主轴头实际上就是一个转塔刀库,如图6-3所示。
主轴头有卧式和立式两种,通常用转塔的转位来更换主轴头,以实现自动换刀。
在转塔的各个主轴上,预先安装有各工序所需要的旋转刀具,当发出换刀指令时,各主轴头依次地转到加工位置,并接通主运动,使相应的主轴带动刀具旋转。
而其它处于不加工位置上的主轴都与主运动脱开。
这种更换主轴换刀装置,省去了自动松、夹、卸刀、装刀以及刀具搬运等一系列的复杂操作,从而缩短了换刀时间,并提高了换刀的可靠性。
但是由于空间位置的限制,使主轴部件结构尺寸不能太大,因而影响了主轴系统的刚性。
为了保证主轴的刚性,必须限制主轴的数目,否则会使结构尺寸增大。
因此,转塔主轴头通常只适用于工序较少、精度要求不太高的机床,例如数控钻、铣床等。
图6-4 更换主轴箱换刀三、更换主轴箱换刀有的数控机床像组合机床一样,采用多主轴箱,利用更换主轴箱达到换刀的目的,如图6-4所示。
主轴箱库8吊挂着备用主轴箱2~7。
主轴箱两端的导轨上,装有同步运行的小车Ⅰ和Ⅱ,它们在主轴箱库与机床动力头之间运送主轴箱。
根据加工要求,先选好所需的主轴箱,待两小车运行至该主轴箱处时,将它推到小车Ⅰ上,小车Ⅰ载着主轴箱与小车Ⅱ同时运动到机床动力头两侧的更换位置。
当上一道工序完成后,动力头带着主轴箱1上升到更换位置,夹紧机构将主轴箱1松开,定位销从定位孔中拨出,推杆机构将主轴箱1推到小车Ⅱ上,同时又将小车Ⅰ上的待用主轴箱推到机床动力头上,并进行定位夹紧。
与此同时,两小车返回主轴箱库,停在下次待换的主轴箱旁的空位。
也可通过机械手10在刀库9和主轴箱1之间进行刀具交换。
这种换刀形式,对于加工箱体类零件,可以提高生产率。
四、带刀库的自动换刀系统此类换刀装置由刀库、选刀机构、刀具交换机构及刀具在主轴上的自动装卸机构等四部分组成,应用最广泛。
图6-5所示为刀库装在机床的工作台(或立柱)上的数控机床的外观图。
图6-5 刀库与机床为整体式的数控机床图6-6 刀库与机床为分体式的数控机床图6-6所示为刀库装在机床之外,成为一个独立部件的数控机床的外观图。
此时,刀库容量大,刀具可以较重,常常要附加运输装置来完成刀库与主轴之间刀具的运输。
带刀库的自动换刀系统,整个换刀过程比较复杂。
首先要把加工过程中要用的全部刀具分别安装在标准的刀柄上,在机床外进行尺寸预调整后,插入刀库中。
换刀时根据选刀指令在刀库上选刀,由刀具交换装置从刀库和主轴上取出刀具,进行刀具交换,然后将新刀具装入主轴,将用过的刀放回刀库。
采用这种自动换刀系统,需要增加刀具的自动夹紧、放松机构、刀库运动及定位机构,常常还需要有清洁刀柄及刀孔、刀座的装置,因而结构较复杂。
其换刀过程动作多、换刀时间长。
同时,影响换刀工作可靠性的因素也较多。
为了缩短换刀时间,可采用带刀库的双主轴或多主轴换刀系统,如图6-7所示。
由图可知,当水平方向的主轴在加工位置时,待更换刀具的主轴处于刀换刀位置,由刀具交换装置预先换刀,待本工序加工完毕后,转塔头回转并交换主轴(即换刀)。
这种换刀方式,换刀时间大部分和机加工时间重合,于提高主轴的结构刚度,刀库上刀具数目也可增加,对多工序加工有利。
但这种换刀方式难保证精镗加工所需要的主轴精度。
因此,这种换刀方式主要用于钻床,也可以用于铣镗床和数控组合机床。
第二节 刀 库一、刀库的功能在自动换刀装置中,刀库是最主要的部件之一。
刀库是用来贮存加工刀具及辅助工具的地方。
其容量、布局以及具体结构,对数控机床的设计都有很大影响。
二、刀库的形式根据刀库的容量和取刀的方式,可以将刀库设计成各种形式。
常见的形式有如下几种。
(一)直线刀库刀具在刀库中是直线排列,如图6-8a )所示。
其结构简单,刀库容量小,一般可容纳8~12把刀具,故较少使用。
此形式多见于自动换刀数控车床,在数控钻床上也采用过此形式。
(二)圆盘刀具此形式存刀具少则6~8把,多则50~60把,其中有多种形式。
(1)如图6-8b )所示的刀库中,刀具径向布局,占有较大空间,刀库位置受限制,一般置于机床立柱上端,其换刀时间较短,使整个换刀装置较简单。
(2)如图6-8c )所示的刀库中,刀具轴向布局,常置于主轴侧面。
刀库轴心线可垂直放置,也可以水平放置,此种形式使用较多。
(3)如图6-8d )所示的刀库中,刀具与刀库轴心线成一定角度(小于90º)呈伞状布置,这可根据机床的总体布局要求安排刀库的位置,多斜放于立柱上端,刀库容量不宜过大。
上述三种圆盘刀库是较常用的形式,其存刀量最多为50~60把,存刀量过多,则结构尺寸庞大,与机床布局不协调。
为进一步扩大存刀量,有的机床使用多圈分布刀具的圆盘刀库,如图6-8e )所示;多层圆盘刀库,如图6-8f )所示;多排圆盘刀库,如图6-8g )所示。
多排圆盘刀库每排4把刀,可整排更换。
后三种刀库形式使用较少。
(k)(j)(g)(f)(e)(d)(c)(b)(a)(h)(i)图6-8 刀库的各种形式(三)链式刀库链式刀库是较常用的形式。
这种刀库刀座固定在环形链节上。
常用的有单排链式刀库,如图6-8h)所示。
这种刀库使用加长链条,让链条折叠回绕可提高空间利用率,进一步增加存刀量,如图6-8i)所示。
链式刀库结构紧凑,刀库容量大,链环的形状可根据机床的布局制成各种形状。
同时也可以将换刀位突出以便于换刀。
在一定范围内,需要增加刀具数量时,可增加链条的长度,而不增加链轮直径。
因此,链轮的圆周速度(链条线速度)可不增加,刀库运动惯量的增加可不予考虑。
这些为系列刀库的设计与制造提供了很多方便。
一般当刀具数量在30~120把时,多采用链式刀库。
(四)其它刀库刀库的形式还有很多,值得一提的是格子箱式刀库。
图6-8j)所示的为单面式,由于布局不灵活,通常刀库安置在工作台上,应用较少。
图6-8k)所示的为多面式,为减少换刀时间,换刀机械手通常利用前一把刀具加工工件的时间,预先取出要更换的刀具(所配数控系统应具备该项功能)。
该刀库占地面积小,结构紧凑,在相同的空间内可以容纳的刀具数目较多。
但由于它的选刀和取刀动作复杂,现已较少用于单机加工中心,多用于FMS(柔性制造系统)的集中供刀系统。
三、刀库的容量刀库中的刀具并不是越多越好,太大的容量会增加刀库的尺寸和占地面积,使选刀时间增长。
刀库的容量首先要考虑加工工艺的需要。
根据以钻、铣为主的立式加工中心所需刀具数的统计,绘制出图6-9所示的曲线。
曲线表明,用10把孔加工刀具可完成70%的钻削工艺,四把铣刀可完成90%的铣削工艺。
据此可以看出,用14把刀具就可以完成70%以上的钻铣加工。