台达机电产品实现龙门铣床同步定位控制功能
(优质)(数控加工)台达PM数控功能的应用

(数控加工)台达PM数控功能的应用台达20PM数控功能的应用摘要:本文简述台达DVP20PM运动控制型PLC的数控功能,及结合HMI在数控应用中的方法及特点。
具体包括主要四种输入G码的方法关键词:PLC运动控制逻辑控制数控系统G码1引言随着自动化设备对控制的高精度、高响应性需求的不断增加,自动化控制技术不断提高,精确的高速定位控制得到广泛应用,PLC这一工业控制产品也从早期的逻辑控制领域不断扩展到数控控制领域,实现了以往PLC无法完成的运动控制功能。
在运动控制中大多数采用我们熟悉的数控系统或者是计算机运动板卡来完成,虽然作为专门的产品能够实现复杂的运动轨迹控制,但同时要完成一些逻辑动作的控制就不如PLC灵活方便。
台达DVP20PM系列PLC是具有高速定位、双轴或叁轴线性及圆弧插补多功能的可编程控制器,结合了PLC逻辑动作控制和数控系统运动控制的各自优点,在功能上满足双轴或三轴插补的高速定位需求。
2数控功能应用介绍。
目前,在我们用DVP20DPM做过的数控案例中主要有液晶切片机,双轴立车,焊接轨迹控制,点胶轨迹控制,龙门数控钻床等等。
在这些应用中,都用到了数控系统的G码和M码指令。
目前20PM包括两款产品分别为20PM00D,与20PM00M.20PM00D支持的G代码功能如下:G0高速定位;G1双轴联动直线插补;G2顺时针圆弧插X3.1DVP20PM程序结构由于20PM主机结合了PLC顺序逻辑控制及双轴插补定位控制的功能,因此在程序架构上主要分为O100主程序、Ox运动子程序及Pn子程序等三大类,结合了基本指令、应用指令、运动指令及GCode指令,使程序设计更多元化,结构更清晰;程序采用PMSOFT软件进行编辑,参见图4。
图4程序设计界面(1)主程序。
主程序以O100作为起始标记,M102作为结束标记,是PLC顺序控制程序,主要为控制主机动作执行,在O100主程序区域中,可以使用基本指令及应用指令,或在程序中启动Ox0~Ox99运动子程序及调用Pn子程序。
台达PLC控制伺服ASDA说明

台达ASDA伺服简单定位演示系统【控制要求】1:由台达PLC和台达伺服组成一个简单的定位控制演示系统。
通过PLC发送脉冲控制伺服,实现原点回归、相对定位和绝对定位功能的演示。
2:监控画面:原点回归、相对定位、绝对定位。
附:ASD-A伺服驱动器参数必要设置注意:当出现伺服因参数设置错乱而导致不能正常运行时,可先设置P2-08=10(回归出厂值),重新上电后再按照上表进行参数设置。
附:PLC元件说明附:PLC与伺服驱动器硬件接线图控制程序:程序说明:1:当伺服上电之后,如无警报信号,X3=On,此时,按下伺服启动开关,M10=On,伺服启动。
2:按下原点回归开关时,M0=On,伺服执行原点回归动作,当DOG信号X2由Off→On变化时,伺服以5KHZ的寸动速度回归原点,当DOG信号由On→Off变化时,伺服电机立即停止运转,回归原点完成。
3:按下正转10圈开关,M1=On,伺服电机执行相对定位动作,伺服电机正方向旋转10圈后停止运转。
4:按下正转10圈开关,M2=On,伺服电机执行相对定位动作,伺服电机反方向旋转10圈后停止运转。
5:按下坐标400000开关,M3=On,伺服电机执行绝对定位动作,到达绝对目标位置400,000处后停止。
6:按下坐标-50000开关,M4=On,伺服电机执行绝对定位动作,到达绝对目标位置-50,000处后停止。
7:若工作物碰触到正向极限传感器时,X0=On,Y10=On,伺服电机禁止正转,且伺服异常报警(M24=On)。
8:若工作物碰触到反向极限传感器时,X1=On,Y11=On,伺服电机禁止正转,且伺服异常报警(M24=On)。
9:当出现伺服异常报警后,按下伺服异常复位开关,M11=On,伺服异常报警信息解除,警报解除之后,伺服才能继续执行原点回归和定位的动作。
10:按下PLC脉冲暂停输出开关,M12=On,PLC暂停输出脉冲,脉冲输出个数会保持在寄存器内,当M12=Off时,会在原来输出个数基础上,继续输出未完成的脉冲。
数控机床多轴同步控制方法

数控机床多轴同步控制方法在机床控制中双轴或多轴同步控制是一种常见的控制方法,如动梁式龙门铣床的横梁升降控制,龙门框架移动式加工中心的龙门框架移动控制等。
虽然在这些情况下可以采用单电动机通过锥齿轮等机械机构驱动双边的方案,但是传动机构复杂、间隙较大,容易造成闭环控制系统的不稳定,而且运行噪声大,维护困难。
另外若用于负载转动惯量较大的场合,由于传动效率低,必然要选用功率很大的电动机,仅仅从经济性来考虑,这个方案就不太理想,因此采用两个电动机双边驱动是比较理想的方案,这就产生了双轴同步控制的问题。
1、机床多轴同步控制方案的比较1.1 普通机床的同步控制对于普通机床的双轴电动机同步控制一般有以下解决方案。
①由一套直流调速装置驱动两台直流电动机,两台电动机的电枢串联,励磁线圈并联。
为了保持速度同步,两电动机轴必须保持刚性连接。
两台电动机中只有一台电动机提供速度反馈信号,其控制示意图见图1。
②由两套交流变频调速系统分别控制作为主从轴的两台交流变频或伺服电动机,两台电动机各自提供自己的速度反馈信号。
为了保持速度同步,两电动机轴也须保持刚性连接,其控制示意图见2。
图1 直流调速系统的同步控制图2 交流调速系统的同步控制这两种控制系统都属于位置环开环系统,只能依靠轴的刚性连接保持电动机转速或位置的同步,且结构简单、可靠性较高,我们为用户改造的B2063铣刨床X轴传动即采用图2所示的控制方法。
这两种控制系统对电动机所连接的运动部件的实际位置不做检测,对于丝杠螺距、联轴节间隙、丝杠扭转、丝杠轴向变形等因素所产生的误差无法补偿,控制精度较差,因此不能应用于数控机床。
1.2 数控机床的同步控制数控机床不同于普通机床的地方,在于数控系统具有很强的控制功能,能够实现对位置、转矩等不同参的控制。
由于位置检测装置的引入,从而组成了位置速度双闭环系统,实现了位置同步控制。
数控机床的同步控制方法可以概括为:将同步电动机的给定位置参考量与两电动机位置反馈差值的调整量做比较后,作为被同步电动机的位置参考量,从而完成位置同步控制,其控制示意图见图3。
基于台达数控系统的CNC控制方案
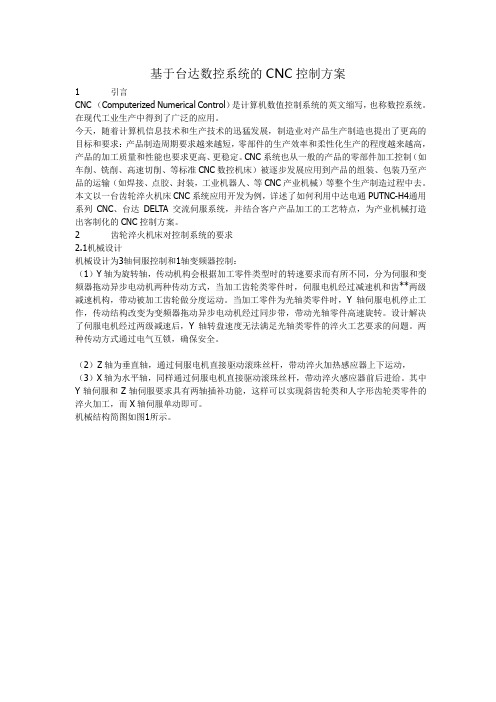
基于台达数控系统的CNC控制方案1 引言CNC (Computerized Numerical Control)是计算机数值控制系统的英文缩写,也称数控系统。
在现代工业生产中得到了广泛的应用。
今天,随着计算机信息技术和生产技术的迅猛发展,制造业对产品生产制造也提出了更高的目标和要求:产品制造周期要求越来越短,零部件的生产效率和柔性化生产的程度越来越高,产品的加工质量和性能也要求更高、更稳定。
CNC系统也从一般的产品的零部件加工控制(如车削、铣削、高速切削、等标准CNC数控机床)被逐步发展应用到产品的组装、包装乃至产品的运输(如焊接、点胶、封装,工业机器人、等CNC产业机械)等整个生产制造过程中去。
本文以一台齿轮淬火机床CNC系统应用开发为例,详述了如何利用中达电通PUTNC-H4通用系列CNC、台达DELTA交流伺服系统,并结合客户产品加工的工艺特点,为产业机械打造出客制化的CNC控制方案。
2 齿轮淬火机床对控制系统的要求2.1机械设计机械设计为3轴伺服控制和1轴变频器控制:(1)Y轴为旋转轴,传动机构会根据加工零件类型时的转速要求而有所不同,分为伺服和变频器拖动异步电动机两种传动方式,当加工齿轮类零件时,伺服电机经过减速机和齿**两级减速机构,带动被加工齿轮做分度运动。
当加工零件为光轴类零件时,Y轴伺服电机停止工作,传动结构改变为变频器拖动异步电动机经过同步带,带动光轴零件高速旋转。
设计解决了伺服电机经过两级减速后,Y轴转盘速度无法满足光轴类零件的淬火工艺要求的问题。
两种传动方式通过电气互锁,确保安全。
(2)Z轴为垂直轴,通过伺服电机直接驱动滚珠丝杆,带动淬火加热感应器上下运动,(3)X轴为水平轴,同样通过伺服电机直接驱动滚珠丝杆,带动淬火感应器前后进给。
其中Y轴伺服和Z轴伺服要求具有两轴插补功能,这样可以实现斜齿轮类和人字形齿轮类零件的淬火加工,而X轴伺服单动即可。
机械结构简图如图1所示。
2.2 零件加工的工艺要求(1)机床要求能够加工直齿轮、斜齿轮、人字形齿轮、阶梯齿轮的淬火加工。
数控系统中同步控制及自动对刀功能的实现

数控系统中同步控制及自动对刀功能的实现陈鹏(广州数控设备有限公司,广东广州510530)摘要:以广州数控设备有限公司生产的GSK208D 系列数控系统(GSK208D 雕铣数控系统)为例,介绍如何在数控系统中通过增加同步控制及自动对刀功能来提高加工效率及加工精度的方法。
关键词:GSK208D 雕铣数控系统;同步控制;自动对刀0引言在工件加工过程中,刀具调整、工件装卸等辅助时间在加工周期中占比相当大,减少辅助时间对提高加工效率至关重要,因此自动对刀功能便显现出极大的优越性。
此外,一般的设备装夹一次只能加工一个零件,如果装夹一次能加工多个零件,就能成倍提高效率,降低成本。
本文将介绍在数控系统中增加同步控制和自动对刀功能及嵌入操作界面来简化操作、提高效率的方法。
1控制原理1.1同步控制在一些机床上,如双立轴(Z 和A 两个立轴)龙门雕铣机床(图1),通过外部控制信号来切换同步控制的启动和关闭,同步控制启动时可以通过仅指令其中一个立轴使Z 和A 两个进给轴同步驱动。
成为同步控制标准的轴为主控轴,与主控轴同步移动的轴为从控轴。
为了做到机械的同步动作,还需对同步控制中的主控轴和从控轴的伺服驱动单元进行同步性调整。
启动同步控制,与主控轴保持同步而使从控轴移动的运行称为同步运行;而关闭同步控制,使主控轴、从控轴各自独立移动的运行称为通常运行[1]。
1.2自动对刀自动对刀就是在数控系统中通过执行对刀专用程序及G31程序跳转指令来使刀具移动碰触对刀仪得到刀具长度、半径、磨损量等相关数据的方法,其中对刀仪是自动对刀功能实现的关键设备。
在自动对刀功能使用前应对对刀仪在工作台上的位置坐标进行标定,并将标定后坐标存储到数控系统的变量中去,为下一步的使用提供基准。
在G31指令之后指定轴移动,可以像G01一样进行直线插补。
若在执行G31指令期间输入外部跳转信号(即对刀仪动作触发信号)SKIP <X002#1>,则中断该指令的执行并转入执行下一程序段。
台达伺服在加工中心刀库中的应用
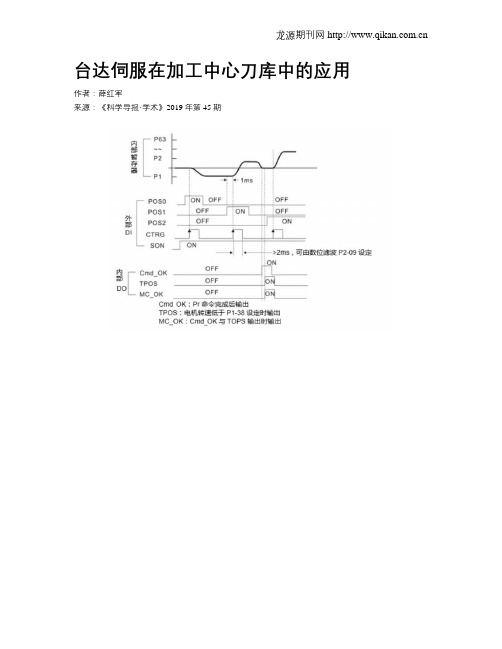
台达伺服在加工中心刀库中的应用作者:***来源:《科学导报·学术》2019年第45期摘; 要:本文介绍了台达伺服在加工中心刀库定位中的应用,用实例说明了台达伺服的位置控制功能及使用步骤,结合FANUC数控系统的PMC程序、NC程序,分析了加工中心刀库控制的一种基本方法。
关键词:位置(PR)模式;速度模式;电子齿轮比;PMC编程1; 数控机床刀库的控制方案1.1; 液压马达、电磁阀及接近开关组成的计数器控制方案这种方式故障率高,液压部分能耗高,油渍的污染是一个无法避免的问题。
1.2; 占用数控系统的一个NC轴作为PMC轴,或者采用I/O LINK轴必须购买与数控系统配套的伺服驱动和电机,这种方式故障率低但费用高。
1.3; 采用一个独立的伺服系统仅占用数控PMC部分一些I/O点,也可完成控制任务,故障率和成本都较低。
下面就FANUC 系统配台达A2伺服的方案进行详述。
此刀库刀塔控制方案,可以满足不同刀位数量与机械机构的需求,是一个既灵活又富于弹性的系统。
2; 硬件配置2.1; FANUC 0iF系列系统2.2; 伺服驱动器台达ASD-A2-2023-U,伺服电机ECMA-EA1320RS,带绝对编码器。
2.3; 加工中心为立加结构刀塔位置固定不动,无机械手,主轴移动到换到位进行换刀。
2.4; 伺服电机到刀盘的减速比240:1,24个刀位。
3; 控制要求自动进行刀位的寻找,也可手动旋转刀盘进行装卸。
4; 台达伺服设定主要相关参数4.1; 模式选择刀盘的定位需要伺服工作在位置(PR)模式,驱动器接受位置命令,控制电机至目标位置。
位置命令由内部缓存器提供(共64 组缓存器),可利用DI 信号选择缓存器编号;刀盘的手动旋转需要伺服工作在速度(S)模式,驱动器接受速度命令,控制电机至目标转速。
速度命令可由内部缓存器提供(共3组缓存器),命令的选择则根据DI 信号来选择。
将伺服参数P1-01设为08,PR-S模式,位置-速度混合模式,通过外部DI(S-P)信号进行切换。
应用840D的同步动作功能实现机床的特殊控制

2
同步动作的结构
同步动作如何使用由条件定义, 其求值运算以实
时方式进行, 这些动作是对实时事件的反应 。此外, 同 步动作还包含动作有效级的说明和对编程实时变量的 询问频率, 以及对启动动作的执行频率说明 。因此, 一 个动作可以一次也可以循环触发 。 同步动作由多达 5 个具有不同任务的指令单元组 成, 结构如下: IDS) ( 1 ) 识别号( ID、 围通过识别号确定。 一个同步动作的有效性范
其中: CLAMP1XP 为夹具 1 在 X 轴正向的机床坐 标位置; CLAMP1XN 为夹具 1 在 X 轴负向的机床坐标 位置; CLAMP1YP 为夹具 1 在 Y 轴正向的机床坐标位 置; CLAMP1YN 为夹具 1 在 Y 轴负向的机床坐标位 置。 将同步程序“PROG_EVENT. SPF ” 复制在标准循 环或用户循环或制造商循环下并装载激活 。 ③PLC 编程: 建立功能块如 FC100 , 并在 OB1 中调 用。FC100 如下编制:
A A I32. 0 DB10. DBX190. 0 / / 机床使能 / / 加工程序中 $ A_OUT[ 9] 对应 PLC 控制 位 DB10. DBX190. 0 = #YV1 / / 在夹具 1 工作区, 夹具 1 阀得电, 可以对 夹具 1 工作区域加工 / / 离开夹具 1 工作区, 夹具 1 夹紧 A I32. 0 A DB10. DBX190. 1 = #YV2 / / 加工程序中 $ A_OUT[ 10] 对应 PLC 控 制位 DB10. DBX190. 1 / / 在夹具 2 工作区, 夹具 2 阀得电, 可以对 夹具 2 工作区域加工 / / 离开夹具 2 工作区, 夹具 2 夹紧 ……
3
同步动作的应用举例
【机床知识】大型龙门式动梁机床同步调整技术

【机床知识】大型龙门式动梁机床同步调整技术大型龙门式动梁机床的 W 轴多采用同步驱动技术,也就是常说的龙门同步功能。
具体步骤如下:一、参数部分1.设定选项参数MD19310[0]设为1 龙门同步轴功能有效.2.基本相关参数(1)MD37100:龙门同步轴类型,由十位A 和个位B 组成,即AB其中,A=0 主动轴A=1 同步轴B=0 无龙门同步轴B=1 龙门同步组1B=2 龙门同步组2……最多可以有8 组龙门同步轴(每组一个主动轴,一个同步轴)也就是说,MD37100=0 无龙门同步轴MD37100=1 龙门同步组1 的主动轴MD37100=11 龙门同步组1 的同步轴MD37100=2 龙门同步组2 的主动轴MD37100=12 龙门同步组2 的同步轴MD37100=3 龙门同步组3 的主动轴MD37100=13 龙门同步组3 的同步轴……若该参数设置有误,会出现10650“通道 %1 轴 %2 龙门机床数据错误,错误代码%3”或10651“通道%1 龙门同步配置错误,错误代码%2”报警。
GMCwmh 系列机床W1 的MD37100 设为2,W2 的MD37100设为12;GMCw 系列机床W1 的MD37100 设为1,W2 的MD37100 设为11。
(2)MD37110:龙门同步的主动轴和同步轴之间位置偏差警告极限值超过此值会输出10652“通道 %1 轴 %2 龙门同步超过警告极限”报警,龙门同步无法正常启动,W1、W2 不能同步运行,当偏差极限小于该参数中设定值后,龙门同步自动重新启动。
要求W1、W2 的MD37110 设定的数值相同,且大于0。
此值依据龙门跨距不同会有变化,标准为:0.05mm/1000mm。
(3)MD37120:龙门同步启动后的主动轴和同步轴之间位置误差(回参考点后的误差)两轴的位置误差超出该参数的设定值后,输出10653“通道%1 轴 %2 超过同步误差极限”报警,龙门同步轴停止,防止机床损坏。