轴承钢夹杂物控制及成因分析
轴承钢中钙铝酸盐夹杂物的形成及控制

渣中各成分中, CaF2 对夹杂物的形成作用也比 较大. 无论在铝含量高或者低的时候, 加入 CaF 2 都 生成 了 许多 MgO #Al2O3 夹 杂; 这 有 可 能是 CaF2 能侵蚀炉 衬, 使 M gO 入 钢 液 中, 从 而 有 利 于 M gO#A l2O3夹杂的生成, 如图 7 所示.
图 5 低 Al 钢中 Al 2O3 夹杂 Fig. 5 Al2O3 incl usi ons in low-Al steel
图 7 加 CaF2 钢中 MgO#Al2O3 夹杂 Fig. 7 MgO#Al2O3 incl usions in steel with CaF2
渣中 M gO 成分对钢中 M gO#A l2O 3 夹杂的生成 影响比较小. 在渣系中 MgO 含量最高的钢中, 由于 酸溶 A l 不高, 其中没有发现 MgO#Al2O3 和 MgO 夹 杂; 而在渣中 M gO 含量并不高的钢中, 由于酸溶 Al 比较高, 能发 现很 多的 Mg O #A l2O 3 和 MgO 夹杂 生成. 21213 [ Ca] 含量的影响
轴承钢点状夹杂物成因及消除机理的探讨

第5卷第4期材 料 与 冶 金 学 报V ol 15N o 14 收稿日期:2006-05-08.作者简介:徐世铮(1937-),男,黑龙江哈尔滨人,苏联技术科学博士,东北大学教授.2006年12月Jour nal ofM ateria ls andM eta ll u rgyD ec .2006轴承钢点状夹杂物成因及消除机理的探讨徐世铮,马晓禾,赵卫东(东北大学 材料与冶金学院,沈阳110004)摘 要:轴承钢点状夹杂物严重影响钢的疲劳寿命.半个世纪以来,冶金工作者研究在精炼过程中如何消除轴承钢点状夹杂物.通过研究首次指出,精炼过程由渣中还原进入钢液中的钙是生成点状夹杂物的主要原因;并且从理论上分析用氯去除钢液中钙的工艺原理.关键词:轴承钢;点状夹杂物中图分类号:TF 76214 文献标识码:A 文章编号:1671-6620(2006)04-0250-03For mati on of globul ar incl usions i nbearing steel and their re m oval m echanis mXU Sh-i zheng ,MA X iao -he ,Z HAO W e-i dong(School ofM ateri als and M etall u rgy ,Northeastern Un ivers i ty ,Sh enyang 110004,Ch i n a)Ab stract :The for m ation of g l obu l ar i ncl usions i n bear i ng stee l i nfl uences seriously the fa tigue strength o f t he stee.l In t he pa rt ha lf o f a cen t ury ,m etall urg ists have m ade a l ot of st udies on the re m oval o f the globu l ar i nclusi on i n bear i ng stee l i n the process of refi n i ng .T his paper po i nted out t hat the m ain or i g i nati on o f t he i nclusi on i s fro m the reducti on of ca l c i u m from slag.The re fi ning process f o r the remova l o f [C a]is theo re ti ca lly ill ustra ted .K ey w ords :beari ng stee;l g l obu lar i ncl usion轴承钢是制造金属轴承的原料.检验轴承钢质量的主要项目是接触疲劳强度和冲击韧性,对其影响最大的是钢中[O ]、[H ]以及夹杂物的种类和数量、尺寸、分布,其中氧化物夹杂A l 2O 3和点状夹杂物)))m Ca O #n A l 2O 3对钢的疲劳强度危害最大[1].在轴承钢轧制过程,点状夹杂物沿着轧制轴向,使钢材产生裂纹.在轴承实验过程,这些裂纹导致零件破损.对于钢中点状夹杂物的成因,有许多学说,诸如在出钢过程炉渣混入钢液、炉渣中(Fe O )、[O]、[H ]及炉渣碱度过高等.半个多世纪以来,为消除轴承钢点状夹杂物研究采用合成渣洗,电炉电石渣)))白渣同炉渣洗,出钢前加大插铝量,电炉钢液钢包吹氩,钢包钢液真空吹氩,RH,DH 精炼轴承钢,VAD 精炼轴承钢,ASEA -SKF 精炼轴承钢,LF-VD 精炼轴承钢,钢包喷Ca-S i 粉,钢包喷A l-S i 粉.由于未能对生成点状夹杂物机理有一个理论说法.使得去除点状夹杂物的精炼工艺效果不佳.因此,本文从热力学角度来分析点状夹杂物在精炼过程的成因,并由此制订出相应的合理精炼工艺.1 在精炼轴承钢过程中,[Ca]在生成点状夹杂物的作用多年精炼轴承钢实践得知,在强还原条件下,渣中Ca O 被还原进入钢液[Ca].为从热力学角度计算,给出轴承钢成分及炉渣成分相关数据,列于表1,表2.计算炉渣组元活度是采用全电子系炉渣理论完成计算的[2].计算渣中各元素原子活度系数U i :U i =Ekj=1X j e-E ij/RT-1(1)式中,k )渣中组元数;E ij )置换能,kJ.计算出:U(A l)=21331;U(Ca)=21410.[A l]+3/4O2y(A l O115)l g K p=37790/T-81457K p1873=51025#1011k A l=X(A l)#U(A l)/A[A l]#p M A l/4O2(2) p3/4O2=X(A l)U(A l)/A[A l]#k A l=11044#10-11p O2=2128#10-10Pa,[O]=0100012%[C a]+1/2O2y(C a O)k(Ca)=X(Ca)#U(C a)/A[C a]#p M(Ca)/4O2(3)l g K p=37197/T-712K1873=4157#1012计算得出:a[Ca]=2#10-6,[Ca]=5#10-6%表1GC r15S M i n钢成分及相关数据Tab le1Composition and re lated data o f GCr15S M i n st ee lC S i M n C r P S Ca A l H O Fe质量分数/%1100015011001150010201010100201030100050100395193相对原子质量122855523132402811656摩尔分数4145@10-2917@10-3917@10-3116@10-2315@10-41166@10-4217@10-5519@10-41134@10-41101@10-40191f[i]113661174113501686112991139911251a[i]113360187113511029010026010420100061p*i /Pa116@10-76102@10-1518@10373131186@1052161@10226p i /Pa212@10-752718@10324418@1021126表2精炼轴承钢炉渣成分及相关数据Tab l e2Co m position o f slag and re la t ed da t aCaO S i O2M gO A l2O3F e O M nO CaF2S O质量分数/%4217817144141812012901760124315013摩尔分数Xi011920106901088010940100301001010210100201552 Mi242322由1873K降至1773K,氧分压由21281# 10-10Pa降至612#10-12Pa.则w[Ca]由5# 10-6%降至211#10-6%.得出钢液降温100e 时,钢中钙由于脱氧能力的提高,58%的[Ca]将与[O]反应生成CaO.其将在钢液内残留的刚玉或外来夹杂物这些现成表面上析出,形成m Ca O #n A l2O3.随钢液温度降低还有反应[H]y1/2 {H2}也将在上述现成表面上析出,而强化了液态点状夹杂物聚集长大.上述分析得出,要降低[C a],一是降低渣中(Ca O)的量,也就是降低炉渣碱度,但不能完全去除点状夹杂;另一种办法就是去除[Ca].2氯化法去除钢液中的钙采用氩气做载体,向钢液内吹入氩氯混合气体.当气泡上升至钢液表面,气泡与钢液相处于平衡状态,此时气泡内的总压力为110@105Pa.气泡内各组分的分压间关系为:E p M eCl+E p M e+p C l2+p A r=110@105Pa(4)因为氩不参与反应,初始气泡中p i C l2=110@105 -p A r,Pa.喷入钢液的氩氯气泡上浮达钢液表面时,气泡内将含有C l2、Ca、CaC l2、A l、A l C l3、C r、Cr C l3、M n、M nC l2、S i、Si C l4、C、CC l4、H2、H C l、Fe、Fe C l2.钢液中各元素与氯反应为:[Ca]+C l2y C a C l2(g)K1873=3184#1016[A l]+3/2C l2y A l C l3(g)K1873=6139#109[S i]+2C l4y S i C l4(g)K1873=3133@105[M n]+C l2y M nC l2(g)K1873=1105#106[C]+2C l2y CC l4(g)K1873=1146#106[H]+1/2C l2y H C l(g)K1873=3170#105[Fe]+C l2y FeC l2(g)K1873=6171#103将初始氯分压p i Cl定为310@104Pa情况下,平衡各分压计算值如表3:251第4期徐世铮等:轴承钢点状夹杂物成因及消除机理的探讨表3氯化产物平衡分压值Tab l e3Equ ili b rium pa rtia l p ressures of ch lo ride products Pap C l2pC a C l2pHC lpM nC l2pFeC l2pAlC l3pC r C l2pSiC l4219#10-10219#1041124#10-4119#10-6411#10-9110#10-9217#10-19由上表可见,钢液中各元素氯化次序为:Ca y H y M n y Fe y A l y C r y Si钙是优先氯化的元素,采用氯化去除是可行的.3精炼工艺参数的确定311加氯方式的选择氯化脱除钢液中钙的工艺,可在RH、DH、VAD、LF-VD精炼轴承钢过程中实施.为考虑首次工业性实验简便可行而选用SL钢包喷粉.312氯进入钢液的方式采用卤化物-氧化物合成粉剂[3](其成分见表4),用氩气做载体,经SL喷粉罐-喷枪,喷入钢包.表4合成粉剂成分Tab l e4Co m position o f compound powde r%CaO S i O2A l2O3M gO质量分数38~5812~157~127~11CaF2F eO CC l4质量分数5~7<0155~515粉剂粒度平均直径为01165mm.313卤化物配入量及卤化物合成粉剂用量计算按钢液中w[C a]=01002%计算[Ca]+C l2y C a C l2401m o l20015m o l每吨钢去除20g钙需015m o lC l2.采用CC l4分解生成C l2去除[Ca].炼钢温度下CC l4分解完全.每吨钢需用0125 m o lCC l4,即3815g,考虑到钢中其他元素氯化耗氯,配入50~60g CC l4/t为考虑,初始p i C l2为3#10-4Pa计,氩气用量为350~420L/.t在氧化物粉剂[3]中配入515%CC l4时,卤化物合成粉剂用量为1~111kg/.t若配入量为3%CC l4时,粉剂用量为117~2kg/.t供氩速度v A r=50~70L/m i n.钢液开喷温度为1600e时,吹毕温度为1520~1510e,可喷吹6~7m i n;喷吹时间依据出钢温度相应调整.314喷粉喉口临界速度从动力学角度出发,研究在炼钢温度条件下,为保证喷入钢液的气粉流中,粉剂不侵入钢液而导出粉剂在喷嘴喉口的临界速度v c.v c=8g(Q s/Q p-1)+12R/r Q p3(k Q s/Q p-1)1/2#(e R(Q s/Q p-1)-1)1/2(5)式中:Q s,Q p为钢液、粉剂密度,kg/m3;r为粉剂中平均粉粒半径,m;R为粉剂与钢液间界面张力, N/m;k为粉粒在钢液中阻力系数.将下列数据代入(5)式Q s=6800kg/m3,Q p=3410kg/m3,R=1152 N/m,k=113,得出临界速度:v c=(163138+01479r+1112#10-2/r)1/2,m/s(6) 4结语从热力学角度分析,在炼钢温度下当p O2[ 213#10-10Pa的条件下,促使渣中Ca O被还原成钙进入钢液中.精炼后随钢液温度降低,钢液中钙的脱氧能力提高,在w[C a]有01002%时,有58%的[Ca]参加脱氧反应生成初生C a O,又有反应2[H]y{H2},同时在钢液中现存夹杂物表面同时析出并长大,形成了m Ca O#n A l2O3点状夹杂物.热力学分析得出,用氯去除钢液中钙的可能性和合理性.对采用氯去除钢中钙的精炼工艺及相应的工艺参数进行了必要的理论分析和研究,为精炼工艺的制定提供依据.参考文献:[1] . . Å»¼À, . . Å»¼À. ¶ÀºѺĶǿÀ½À´ºÑϽ¶¼ÄÂÀ½½±³¼ºÃı½Î[M]. ºË±Ê¼À½±.1983.179-192. [2] . . º´ÀÂÑ¿. . . ¶½Ñ¿Éº¼À³. .¡. ÄÀ¾±Çº¿ . .À¿À¾±Â¶¿¼À. ¶Àºĺɶüº ÿÀ³Í½¶¼ÄÂÀÃı½¶Á½±³º½Î¿ÍÇ ÂÀȶÃÃÀ³[M]. ¶Ä±½½ÅÂĺÑ,Àü³±.1987.8-89.[3]徐世铮,刘沛环,刑玉录,等.喷射冶金用合成粉剂及其制造工艺:中国,8510031.1[P].1988.252材料与冶金学报第5卷。
钢中夹杂物的产生与去除途径
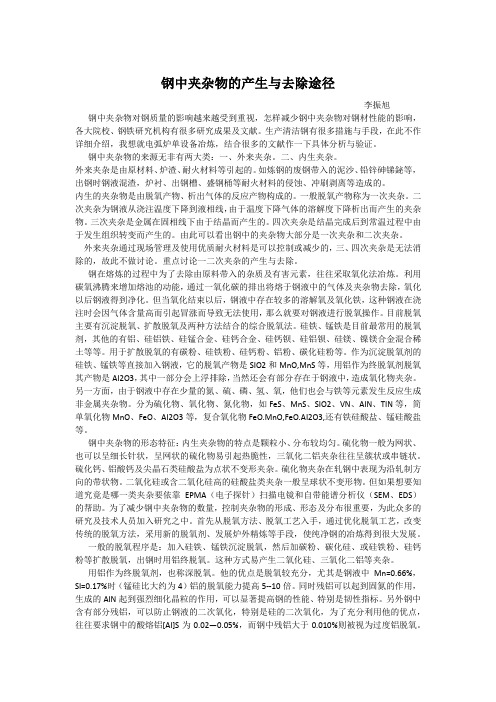
钢中夹杂物的产生与去除途径李振旭钢中夹杂物对钢质量的影响越来越受到重视,怎样减少钢中夹杂物对钢材性能的影响,各大院校、钢铁研究机构有很多研究成果及文献。
生产清洁钢有很多措施与手段,在此不作详细介绍,我想就电弧炉单设备冶炼,结合很多的文献作一下具体分析与验证。
钢中夹杂物的来源无非有两大类:一、外来夹杂。
二、内生夹杂。
外来夹杂是由原材料、炉渣、耐火材料等引起的。
如炼钢的废钢带入的泥沙、铅锌砷锑鉍等,出钢时钢液混渣,炉衬、出钢槽、盛钢桶等耐火材料的侵蚀、冲刷剥离等造成的。
内生的夹杂物是由脱氧产物、析出气体的反应产物构成的。
一般脱氧产物称为一次夹杂。
二次夹杂为钢液从浇注温度下降到液相线,由于温度下降气体的溶解度下降析出而产生的夹杂物。
三次夹杂是金属在固相线下由于结晶而产生的。
四次夹杂是结晶完成后到常温过程中由于发生组织转变而产生的。
由此可以看出钢中的夹杂物大部分是一次夹杂和二次夹杂。
外来夹杂通过现场管理及使用优质耐火材料是可以控制或减少的,三、四次夹杂是无法消除的,故此不做讨论。
重点讨论一二次夹杂的产生与去除。
钢在熔炼的过程中为了去除由原料带入的杂质及有害元素,往往采取氧化法冶炼。
利用碳氧沸腾来增加熔池的动能,通过一氧化碳的排出将熔于钢液中的气体及夹杂物去除,氧化以后钢液得到净化。
但当氧化结束以后,钢液中存在较多的溶解氧及氧化铁,这种钢液在浇注时会因气体含量高而引起冒涨而导致无法使用,那么就要对钢液进行脱氧操作。
目前脱氧主要有沉淀脱氧、扩散脱氧及两种方法结合的综合脱氧法。
硅铁、锰铁是目前最常用的脱氧剂,其他的有铝、硅铝铁、硅锰合金、硅钙合金、硅钙钡、硅铝钡、硅镁、镍镁合金混合稀土等等。
用于扩散脱氧的有碳粉、硅铁粉、硅钙粉、铝粉、碳化硅粉等。
作为沉淀脱氧剂的硅铁、锰铁等直接加入钢液,它的脱氧产物是SIO2和MnO,MnS等,用铝作为终脱氧剂脱氧其产物是AI2O3,其中一部分会上浮排除,当然还会有部分存在于钢液中,造成氧化物夹杂。
轴承钢点状夹杂物成因及消除机理的探讨

轴承钢点状夹杂物成因及消除机理的探讨
1 夹杂物成因
轴承钢点状夹杂物是指在轴承精锻件表面上存在的散落的一些硬
性物质,一般为硬质磨料、金属颗粒、研磨颗粒、合金残留物等。
一
般情况下,它们是在制造过程中被其他金属粒子进入轴承精锻件表面,或是由于轴承精锻的原料的杂质性导致的,也有可能是安装使得夹杂
物进入密封下的。
2 消除机理
夹杂物消除的主要方式有采用抛光、热处理、氣力清理和物理化
学处理等方式。
抛光是最常用的夹杂物消除方式,这种方法是采用彼此间准备磨
料把夹杂物磨掉,对夹杂物消除效果较好。
热处理是把轴承精锻件放入高温下,使夹杂物在高温下熔化,然
后把夹杂物去掉,这个方法使轴承精锻件得到跳漆和表面变深,达到
清理夹杂物的效果。
气力清理是采用压缩空气加水分子粒子以及其它微小纳米粒子对
轴承夹杂物进行清理,这种方法可以去除较大的硬质磨料以及漆料等
物质,效果也很明显。
物理化学处理是一种新型的夹杂物消除技术,它采用特制的药液,可以彻底清除夹杂物,物理化学处理不仅能够有效移除夹杂物,而且
还能够在表面形成一层防护膜,从而保护表面,使轴承更加耐久。
4 结论
轴承的精锻件表面点状夹杂物的形成很重要,主要是由于精锻原
料的杂质性、制造过程中的夹杂物进入等原因导致,也可能还有安装
的原因。
为了解决点状夹杂物的问题,还可以采用抛光、热处理、气
力清理以及物理化学处理等技术来清除夹杂物,达到良好的消除效果。
钢中夹杂物控制原理

钢中夹杂物控制原理钢中夹杂物控制原理钢中氧的存在形式T[O]=[O]溶+[O]夹(1)转炉吹炼终点:[O]夹=>0,T[O]→[O]溶=200~1000ppm [O]溶决定于:l 钢中[C],转炉吹炼终点钢中[C]与a[O] 关系如图l 渣中(FeO);l 钢水温度。
1 顶底复吹转炉炉龄C–Fe的选择性氧化平衡点根据式[C] + [O] = {CO} (1) lg (Pco/ac* [%O])= 1149/T–2.002以及反应[Fe] + [O] = (FeO)(2) lg aFeo/[%O] = 6317/T – 2.739得到反应(FeO)+ [C] = [Fe] + {CO} (3) lg (Pco/ac* aFeo)= –5170/T+4.736结论钢液中C-Fe的选择性氧化平衡点为[C]=0.035%,也就是说终点[C] < 0.035%时,钢水的过氧化比较严重。
图1-1的统计数据也说明了这点。
同时由式(1)可以求出此时熔池中的平衡氧含量为740ppm。
理论分析1)终点[C]-[O]关系1) 当终点[C]<0.04%时钢水的终点氧含量较高 2) 当终点[C]在0.02~0.04%范围时,有些炉次钢水氧波动在平衡曲线附近(区域Ⅰ)有些炉次钢水氧含量则远离平衡曲线(区域Ⅱ ,说明在该区域钢水过氧化严重。
2)温度对氧含量的影响20040060080010001200140016001800160016201640166016801700172017401760终点温度(℃)终点氧含量(p p m )终点[0]在终点[C] = 0.025~0.04%时,终点氧含量虽然较分散,但总的趋势是随着终点温度的升高,终点氧基本呈上升趋势。
1620℃~1680℃之间,氧含量总体水平较低,平均为702ppm,该范围的炉次共占总炉次的30%左右;出钢温度大于1680℃时,终点钢水氧含渣中(FeO+MnO )增加,终点[O]有增加趋势; 终点[C]<0.04%,渣中(FeO+MnO )增加且波动较大,说明此时吹氧脱碳是比较困难的,而铁则被大量氧化。
轴承钢点状夹杂物成因及消除机理的探讨
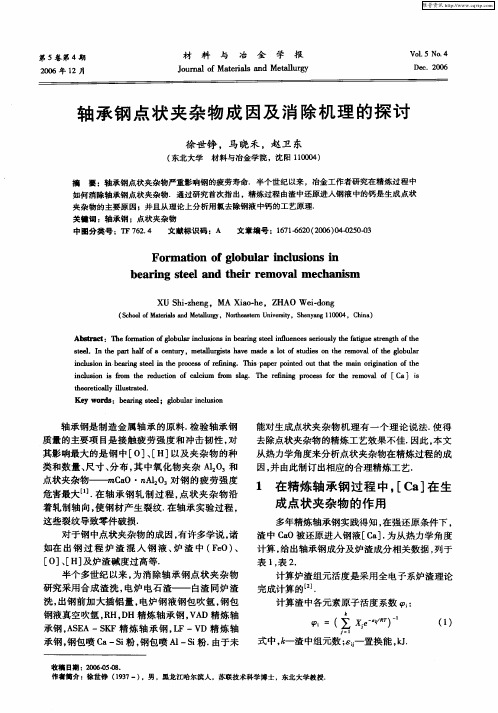
[ ][ ] O 、 H 及炉渣碱度过高等. 半个 多世 纪 以来 , 消 除轴 承 钢 点状 夹杂 物 为 研究采用合成渣洗 , 电炉电石渣—— 白渣同炉渣 洗, 出钢前 加 大 插 铝量 , 电炉 钢 液 钢包 吹 氩 , 钢包 钢 液真 空吹 氩 ,H, H 精炼 轴 承 钢 , A R D V D精 炼 轴 承 钢 ,S A—S F精 炼 轴 承 钢 ,F—V AE K L D精 炼 轴 承钢 , 钢包 喷 C a—s 粉 , i 钢包 喷 —s粉 . i 由于未
维普资讯
第 5卷 第 4期
2O O 6年 1 2月
材
料
与 冶 金
ห้องสมุดไป่ตู้
学
报
V L 5 No 4 o . De .2 0 c 06
J un l fMaeil n tl ry o ra trasa d Meal g o u
轴 承 钢 点 状 夹 杂 物 成 因及 消 除 机 理 的 探 讨
ic s n i f m h e ut n o M i f m l .T e r nn rcs frtermo ̄ o C ]i nl i s r te r c o fc c m r s g h e i poes o uo o d i u o a i f g h e v f[ a s
能对生 成点 状夹 杂 物 机 理 有 一个 理 论 说 法 . 得 使 去除点 状夹 杂物 的精 炼工 艺效 果不 佳 . 因此 。 本文 从热 力学角 度来 分析 点状 夹杂 物在 精炼 过 程 的成 因 , 由此 制订 出相 应 的合理 精炼 工艺 . 并
其影响最大的是钢 中[ ] [ 以及夹杂物的种 0 、 H] 类和数量 、 尺寸 、 分布, 中氧化物夹杂 A , 其 1 和 0 点 状夹 杂物— — , a ・ A , 钢 的 疲 劳 强 度 , O nl 对 I C 0 危害最大…. 在轴承钢轧制过 程 , 点状夹杂 物沿 着轧制轴 向, 使钢材产生裂纹. 在轴承实验过程 。 这些 裂纹 导致零 件破 损 . 对于 钢 中点状 夹杂 物 的成 因 , 许 多学说 , 有 诸
铁道车辆用车轴钢夹杂物分析及改善措施

铁道车辆用车轴钢夹杂物分析及改善措施摘要:在铁道车辆中,车轴钢是非常总要的一项内容。
本文首先分析了LZ50车轴钢生产工艺流程,其次探讨了夹杂不合原因,最后就改进措施及效果进行研究,以供参考。
关键词:车轴钢;大颗粒夹杂物;炼钢;中间包;浸入式水口引言随着高碳铬不锈钢技术标准的不断升级,特钢行业对航空轴承材料的质量要求越来越高。
G95Cr18是高碳高铬马氏体不锈钢典型钢种之一,具有良好的耐蚀、抗高温能力,作为轴承材料在航空工业中得到广泛应用。
该钢中夹杂物(尤其是氧化物、点状夹杂)显著降低钢的塑性、韧性和疲劳寿命,使钢的加工性能变坏,对钢材表面光洁度和焊接性能有直接影响1LZ50车轴钢生产工艺流程国内某钢厂车轴钢采用80t电转炉冶炼-80tLF精炼-80tVD真空脱气—连铸准690mm大圆连铸坯—铸坯红送—热轧250mm×250mm工艺流程生产。
采用电转炉冶炼,其成分要求如表1所示。
出钢要求C0.10%~0.51%,P≤0.010%,出钢温度范围为1640~1680℃。
LF精炼主要采用铝脱氧,LF精炼工序在调白渣后,保持时间≥25min。
LF出钢参考温度为1655~1675℃;VD真空处理需在高真空度(≤67Pa)下保持时间≥20min;脱气目标:钢液中[H]≤1.5×10-6,软吹时间≥15min。
连铸过程中过热度保持在(25±5)℃,中间包使用碱性覆盖剂,保护渣采用车轴钢专用保护渣,连铸二冷水配水采用弱冷工艺,拉速控制在0.20~0.24m/min,同时配备有结晶器电磁搅拌(M-EMS)、二冷区电磁搅拌(S-EMS)、末端电磁搅拌(F-EMS)。
连铸坯在红送到加热炉后其预热温度为700~900℃,加热速度≤150℃/h,均热温度控制在1260~1290℃;开轧温度1200~1250℃,终轧温度控制在850~950℃。
2夹杂不合原因分析(1)扫描电镜及能谱分析。
钢中高的氧含量形成较多的氧化物夹杂,通过稀土让氧化物夹杂变性,最终呈点状夹杂形态,所以表现为点状夹杂超标。
轴承钢夹杂物控制技术研究
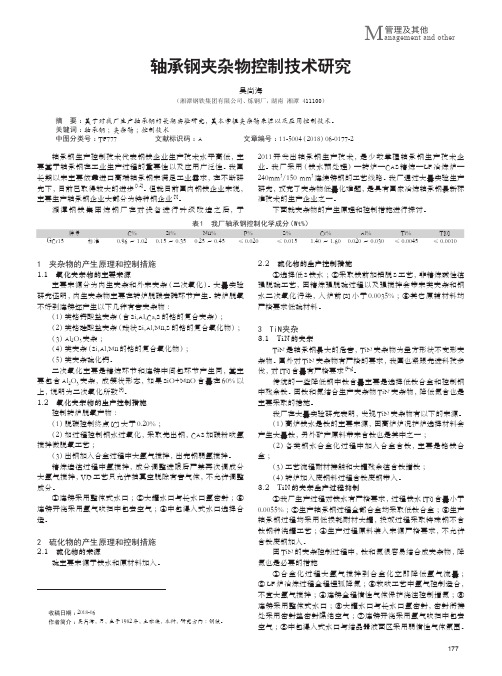
管理及其他M anagement and other 轴承钢夹杂物控制技术研究吴尚海(湘潭钢铁集团有限公司、炼钢厂,湖南 湘潭 411100)摘 要:基于对我厂生产轴承钢的长期实验研究,基本掌握夹杂物来源以及应用控制技术。
关键词:轴承钢;夹杂物;控制技术中图分类号:TF777 文献标识码:A 文章编号:11-5004(2018)06-0177-2轴承钢生产控制技术代表钢铁企业生产技术水平高低,主要基于轴承钢在工业生产过程的重要性以及应用广泛性。
我国长期以来主要依靠进口高端轴承钢来满足工业需求,在不断研究下,目前已取得较大的进步[1,2]。
但就目前国内钢铁企业来说,主要生产轴承钢企业大部分为特种钢企业[3]。
湘潭钢铁集团炼钢厂在对设备进行升级改造之后,于2011开发出轴承钢生产技术,是少数掌握轴承钢生产技术企业。
我厂采用(铁水预处理)—转炉—CAS精炼—LF冶炼炉—240mm3/150 mm3连续铸钢的工艺线路。
我厂通过大量实验生产研究,攻克了夹杂物低量化难题,是具有国家冶炼轴承钢最新标准技术的生产企业之一。
下面就夹杂物的产生原理和控制措施进行探讨。
表1 我厂轴承钢控制化学成分(Wt%)牌号C%Si%Mn%P%S%Cr%Al%Ti%T[0] GCr15标准0.96~1.020.15~0.350.25~0.45≤0.020≤0.015 1.40~1.600.020~0.030≤0.0045≤0.00101夹杂物的产生原理和控制措施1.1 氧化夹杂物的主要来源主要来源分为内生夹杂和外来夹杂(二次氧化)。
大量实验研究证明,内生夹杂物主要在转炉脱碳去磷环节产生。
转炉脱氧不好到连铸坯产生以下几种有害夹杂物:(1)类铬钙酸盐夹杂(含Si,Al,Ca,S的铬的复合夹杂);(2)类铬硅酸盐夹杂(球状Si,Al,Mn,S的铬的复合氧化物);(3)Al2O3夹杂;(4)类夹杂(Si,Al,Mn的铬的复合氧化物);(5)类夹杂硫化钙。
- 1、下载文档前请自行甄别文档内容的完整性,平台不提供额外的编辑、内容补充、找答案等附加服务。
- 2、"仅部分预览"的文档,不可在线预览部分如存在完整性等问题,可反馈申请退款(可完整预览的文档不适用该条件!)。
- 3、如文档侵犯您的权益,请联系客服反馈,我们会尽快为您处理(人工客服工作时间:9:00-18:30)。
•搅拌时间与夹杂物数目及粒度分布
0.06
钢中夹杂物控制
夹 杂 物 数 目 ( mm 2 )
0.05 0.04 0.03 0.02 0.01 0 2.8-5.6 5.6-11.2 11.222.4 >22.4 长搅拌时间 短搅拌时间
夹杂物粒度( μ m)
图12
气体搅拌时间与夹杂物 数量及粒度分布的影响
[Ti]含量控制
出钢过程下渣量中Ti的还原: 出钢过程主要加入Al、C、Si、Mn、Cr。
[Ti]含量控制
在出钢温度下,只有 Al能还原渣中的Ti。 即出钢过程如果用 Al脱氧,则下渣中 的(TiO2) 能被Al 还原进入钢液。
图1 氧化物标准生成自由能随温度的变化
[Ti]含量控制
LF精炼过程(TiO2) 的还原 铝还原(TiO2)的反应: 4[Al]+3(TiO2)=3[Ti]+2(Al2O3) (2) 在1800oC高温下,碳还原TiO2的反应: (TiO2)+[C]=(TiO)+CO (3) (TiO2)+[C]=[TiC]+CO (4) 在>1850oC高温下,碳还原TiO2的反应: 2[C]+(TiO2)=[Ti]+2CO (5) 上述反应表明:如果在低温下,能先除去初炼炉的下渣 量,再用Al、C进行脱氧还原,就能减少(TiO2) 的 还原。
钢中夹杂物控制
浇注工艺参数控制 提高浇注系统用耐火材料的质量档次, 提高中包抗侵蚀、抗冲刷的能力,减少 外来夹杂物。 严格按工艺要求砌筑浇注系统,保证浇 注系统清洁、充分烘烤、干燥并保持至 浇注。
钢中夹杂物控制
浇注工艺参数控制 采用氩封保护浇注,防止二次氧化形成 大颗粒族状Al2O3夹杂物。
钢中夹杂物控制
脱氧夹杂物控制 钢中脱氧夹杂物含量是由初炼炉终点[O]含 量决定的。 初炼炉终点[O]含量是由终点[C]含量控制 的。
钢中夹杂物控制
当[C] ≤0.042% 时,平衡[O]≥0.0591% ,但 实际[O]≥1200PPm; 当[C] ≥ 0.80% 时,平衡[O]≤0.0030% ,但 实际[O] ≤ 300PPm。 当出炼炉终点碳较低时,出钢过程先增碳可 降低[O]。
0.3
0.2 0.1
0
0 1 2 B=(N 3 +N 4 )/N 5 6
钢中夹杂物控制
当(Al2O3%)一定时, 随渣碱度的提高,aAl、 aCa随之提高;在提高 渣碱度的同时提高 (Al2O3%),则aAl随 之提高,而aCa降低。 因此,要降低[O]并减少 钢液中含Ca的点状夹杂 物,应当提高渣碱度并 增加(Al2O3%)。
轴承钢夹杂物控制
冶炼工艺流程
LF炉
偏心底出钢电炉
VD炉 连铸
轴承钢内在冶金质量
[Ti]含量 [O]含量 [N]含量 [H]含量 高倍夹杂物
[Ti]含量控制
初炼炉[Ti]的氧化:
[Ti]+2[O]= TiO2 (1) 1600oC下,[Ti%]×[O%]2=2.8×10-6 当终点[Ti]≤0.0008%时,钢液终点平衡 [O]≥0.0591%,此时,平衡[C]≤0.042%。
钢中夹杂物控制
0.020
钢液降温时产生的夹杂物(%)
0.03%Al 0.010 0.05%Al
在相同[C]时, 一次加Al 量越多, 其温降时 生成的夹 杂物越少。
0.10%Al
0 0.2 0.4 0.6 0.8 1.0 1.2 1.4
C%
图5 钢液温降时产生的夹杂物(二次夹杂物)
钢中夹杂物控制
实际钢中低倍蓝脆夹杂物成因分析
2007年6月份起,分析了28炉次56个试样的 夹杂物,夹杂物主要分为两种,其典型 成分如下:
实际钢中低倍蓝淬夹杂物成因分析
第一种夹杂物扫描电镜分析照片: 以铝硅钙为主的氧化物(11568炉号 , 485-1,150方)
第一种夹杂物扫描电镜分析成分: ================================================ Element Intensity Weight% AT% K-Value Z A F ================================================ O 10.527 45.606 60.870 0.13478 0.97343 2.77313 1.00000 Na 1.311 1.809 1.680 0.00744 1.03978 1.87950 0.99200 Al 17.098 17.614 13.940 0.10504 1.04607 1.29328 0.98886 Si 18.818 21.601 16.423 0.12499 1.01747 1.35825 0.99761 Cl 0.692 1.329 0.800 0.00836 1.07768 1.18656 0.99178 K 0.564 1.190 0.650 0.00827 1.07727 1.08388 0.98330 Ca 4.329 9.853 5.249 0.07045 1.05626 1.05695 0.99932 Mn 0.154 0.998 0.388 0.00652 1.20507 1.01315 1.00000 Total 100.000 100.000 0.46585 该夹杂物是以Si、Al、Ca为主的氧化物,还含有少量的Na、K、Mn等元 素,尺寸较大。 该夹杂物具有类似于保护渣的成分,初步分析是在钢锭模尾部半径较小 的情况,由于采用铺渣操作且保护渣加入量多,浇注前期注速控制过快发 生保护渣卷入造成的,并在凝固过程聚集长大形成了大颗粒塑性夹杂物。
夹杂物粒度(μm) 图10 真空脱气对夹杂物粒度分布的影响
钢中夹杂物控制
氩气泡对夹杂物的浮选作用
夹杂物与气泡的碰撞概率(%)
10 50um 1 夹杂物尺寸
20um
0.1 10um 5um
软吹氩流量越小,气 泡尺寸越小,夹杂 物去除效率越高。
0.01
0.001 1 2 3 4 5
气泡直径(×10-3m) 图11 氩气泡尺寸对夹杂物去除的影响
实际钢中低倍蓝淬夹杂物成因分 析
第二种夹杂物扫描电镜分析照片: 以铝及以铝镁为主的氧化物(11741炉号, 485-1, ∮90mm )
•
第二种夹杂物扫描电镜分析成分:
Element Intensity Weight% AT% K-Value Z A F ======================================== O 2.224 23.690 34.296 0.02594 0.95125 2.41459 1.00000 Mg 0.995 2.712 2.584 0.00596 0.99052 1.20861 0.95543 Al 25.830 73.388 62.999 0.15868 1.02139 1.13898 0.99998 Ca 0.029 0.210 0.121 0.00047 1.03047 1.08110 1.00000
图15 精炼渣组成对钢中残余铝含量和残余钙含量的影响 ——a[Al]×10-6; ┅a[Ca]×10-11
钢中夹杂物控制
符合高碱度、低熔点 的炉渣组成位于 55%CaO、40% Al2O3%、SiO2< 10%的附近区域内, 其熔点在1500oC左 右。选用该区域炉渣 成分较为合适。
图16 CaO- Al2O3-2SiO2相图
钢中夹杂物控制
加铝量与脱氧产物数量的关系
脱氧时产生的夹杂物(%)
0.06 0.03%Al 0.05%Al
在相同[C]时,一次 加Al量越多其生 成的一次夹杂物 也越多,其排除 时间也越充分。
0.04
0.10%Al
0.02
0
0.2 0.4 0.6 0.8 1.0 1.2 1.4
C%
图4 脱氧时产生的夹杂物(一次夹杂物)
Total
100.000 100.000 0.19105
该夹杂物以O、Al为主,另外还含有少量的Mg、Ca等元素。 该夹杂物主要是Al氧化产物成分,分析是浇注过程二次氧化造成的。在浇 注过程注流表面铝含量和氧含量都很高的情况下极易生成大颗粒Al2O3簇群, 特别是浇注后期帽头充填阶段,散流补缩二次氧化更为严重,尤其是最后锭 盘钢液温度低导致钢液粘度增加,致使二次氧化生成的大颗粒Al2O3簇群在 钢液凝固过程难以排除。
0.01
0.5
1.0
1.5
2.0
2.5
加铝量(kg/t)
图3
加铝量对残留 [O]的影响
钢中夹杂物控制
脱氧夹杂物的变形能力 当[O]高时: 先用Al脱氧,后用Si、Mn脱氧,其复合夹 杂物变形能力低。 先用Si、Mn脱氧,后用Al脱氧,其复合夹 杂物变形能力高。 因此,应通过控制脱氧元素来控制脱氧夹 杂物的变形能力。
[Ti]含量控制
VD精炼过程(TiO2) 的还原 在3000oC或真空中发生下列反应: (TiO2)+2[TiC]=3[Ti]+2CO (TiO)+[TiC]=2[Ti]+CO
(8) (9)
[Ti]含量控制
降低初炼炉终点[Ti],需降低终点[C]。 出钢过程少下渣,需多留钢、使用前期 出钢口、快速回炉。 出钢后需先除渣。 除渣前不用Al脱氧。 使用低Ti合金铁和造渣材料。
凝固过程产生的夹杂物 (%) 在相同[C]时,一次加 Al量越多,其凝固 过程产生的夹杂物 越少。
0.03%Al
0.001
0.05%Al
0.10%Al
0
0.2
0.4
0.6
0.8
1.0