汽车电子硬件设计
汽车电子结构设计规范
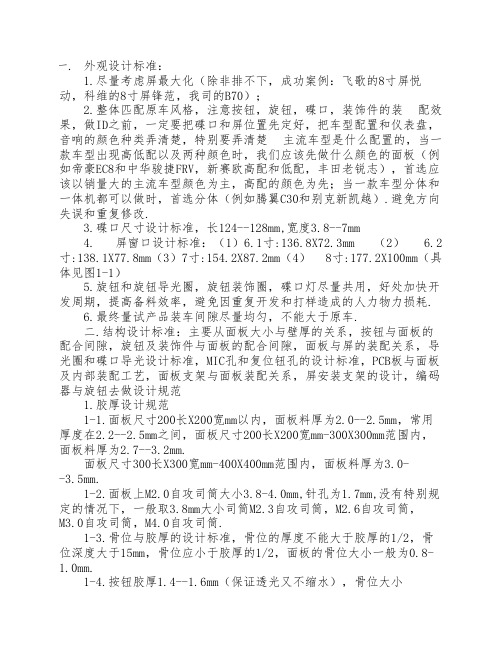
一. 外观设计标准:1.尽量考虑屏最大化(除非排不下,成功案例:飞歌的8寸屏悦动,科维的8寸屏锋范,我司的B70);2.整体匹配原车风格,注意按钮,旋钮,碟口,装饰件的装 配效果,做ID之前,一定要把碟口和屏位置先定好,把车型配置和仪表盘,音响的颜色种类弄清楚,特别要弄清楚 主流车型是什么配置的,当一款车型出现高低配以及两种颜色时,我们应该先做什么颜色的面板(例如帝豪EC8和中华骏捷FRV,新赛欧高配和低配,丰田老锐志),首选应该以销量大的主流车型颜色为主,高配的颜色为先;当一款车型分体和一体机都可以做时,首选分体(例如腾翼C30和别克新凯越).避免方向失误和重复修改.3.碟口尺寸设计标准,长124--128mm,宽度3.8--7mm4. 屏窗口设计标准:(1)6.1寸:136.8X72.3mm (2) 6.2寸:138.1X77.8mm(3)7寸:154.2X87.2mm(4) 8寸:177.2X100mm(具体见图1-1)5.旋钮和旋钮导光圈,旋钮装饰圈,碟口灯尽量共用,好处加快开发周期,提高备料效率,避免因重复开发和打样造成的人力物力损耗.6.最终量试产品装车间隙尽量均匀,不能大于原车.二.结构设计标准:主要从面板大小与壁厚的关系,按钮与面板的配合间隙,旋钮及装饰件与面板的配合间隙,面板与屏的装配关系,导光圈和碟口导光设计标准,MIC孔和复位钮孔的设计标准,PCB板与面板及内部装配工艺,面板支架与面板装配关系,屏安装支架的设计,编码器与旋钮去做设计规范1.胶厚设计规范1-1.面板尺寸200长X200宽mm以内,面板料厚为2.0--2.5mm,常用厚度在2.2--2.5mm之间,面板尺寸200长X200宽mm-300X300mm范围内,面板料厚为2.7--3.2mm.面板尺寸300长X300宽mm-400X400mm范围内,面板料厚为3.0--3.5mm.1-2.面板上M2.0自攻司筒大小3.8-4.0mm,针孔为1.7mm,没有特别规定的情况下,一般取3.8mm大小司筒M2.3自攻司筒,M2.6自攻司筒,M3.0自攻司筒,M4.0自攻司筒.1-3.骨位与胶厚的设计标准,骨位的厚度不能大于胶厚的1/2,骨位深度大于15mm,骨位应小于胶厚的1/2,面板的骨位大小一般为0.8-1.0mm.1-4.按钮胶厚1.4--1.6mm(保证透光又不缩水),骨位大小1.0mm,导向骨位 1.0mm.2.面板,按钮,旋钮及装饰件的间隙配合(具体见图2-2)2-1.面板和按钮,面板与装饰圈表面喷普通油漆的时候(油漆厚度0.08mm左右),长行程按钮(硅胶钮)与面板单边间隙为0.4mm,短行程轻触开关为0.25mm,跷跷板硅胶钮与轴平行方向间隙为0.5mm,与轴垂直方向为0.4mm.跷跷板轻触开关钮与轴平行方向间隙为0.5mm,与轴垂直方向为0.4mm.2-2.面板和按钮,面板与装饰圈表面喷橡胶油,PU,UV的时候(油漆厚度0.1mm左右),长行程按钮(硅胶钮)与面板单边间隙为0.4mm,短行程轻触开关为0.3mm,跷跷板硅胶钮与轴平行方向间隙为0.5mm.与轴垂直方向为0.4mm.跷跷板轻触开关钮与轴平行方向间隙为0.5mm,与轴垂直方向为0.4mm.小按钮与硅胶钮预压0.2mm,跨度较大的按钮预压0.3mm.2-3.按钮和面板骨位配合间隙设计规范(见图3-3),一定要做防呆设计,左边按钮和面板应写1,2,3,4,右边应写A,B,C,D.2-4.面板与电镀装饰圈间隙为单边0.2mm,按钮与电镀装饰圈单边间隙为0.5mm2-5.一般按钮导向骨位和面板导向骨位咬合尺寸应该大于7.5mm,能做大尽量做大,咬合尺寸小于8.0mm,按钮导向骨位和面板做到0.1mm,8.0-25mm导向骨间隙为0.12mm,后装式按钮,外表面要喷普通油的与面板导向骨位间隙为0.14mm,要喷UV和光油的为0.15mm.2-6.按钮与面板咬合的地方做模时不准分级,,以免影响手感,甚至造成卡键,按钮底部台面设计尽量做成平面,其次是阶梯状,再次没办法才做成弧面.2-7.按钮围骨与面板间隙统一为0.4mm,台面行程间隙为2.0mm,面板倒扣宽度在2.0--3.0mm之间与按钮行位孔行程预留2.0mm,左右间隙为0.4mm,导向骨位尽量做到按钮上,三个骨和四个骨位视围骨的大小和深度而定.2-8.当导光圈从底部透光时,大旋钮和面板单边间隙1.0mm,小旋钮为0.8mm,特殊情况例外.(见图示2-2)当导光圈从面板表面部透光时,喷油旋钮和导光圈单边间隙0.6mm.导光圈与面板的单边间隙为0.1mm,电镀钮和电镀装饰圈的单边间隙0.8mm2-9.编码器和旋钮导光圈间隙单边0.1mm,编码器和旋钮配合孔位结构设计做到6.0mm,模厂模具做到5.96mm.2-10. 旋钮顶部电镀装饰件与旋钮装配设计时候应该考虑电镀层的厚度,预留0.15mm的装配尺寸,单个旋钮应该胶厚均匀,做到1.8mm厚. 2-11.KB板和面板装配时候,应该做两定位柱定位,跨度大点为宜,定位柱大小为1.2mm,PCB板孔位为1.4mm.2-12.AUX孔位尺寸为5.2mm,复位钮孔位尺寸为2.2mm,MIC孔单孔尺寸为1.3mm,双孔尺寸为1.0mm,安装麦克风的固定孔位为4.8mm(见图4-4)3.面板,屏,触摸屏及TFT板支架,面板支架设计3-1.面板和触摸屏正面的设计间隙为0.5mm,局部围骨为0.3mm,局部围骨必须在触摸屏可视区外,尽量靠边,今后新产品设计尽量做围骨最好不要包黑胶纸,减少生产负担;包胶纸的屏的上下左右与面板间隙为0.3mm,未包胶纸的屏上下左右与面板骨位间隙为0.25mm,触摸屏和屏排线区域预留0.6mm以上间隙,防止排线压断,7,8寸触摸屏正面左右上下共贴5条PRON海绵垫,6.1,6.2寸触摸屏左右下贴4条海绵垫(具体见图5-5和3D图).3-2.触摸屏和屏上边缘平齐,下边缘比屏小0.5mm,预留出触摸屏排线的位置,防止排线折断,设计面板骨位时候,应该以屏尺寸为准再偏0.6mm以上.3-3.面板遮光围骨厚1.0mm,高度高出触摸屏底部4mm(做围骨时应考虑水口的位置).3-4.面板和触摸屏接触区域上下左右做N条距离在15mm以内的1.0mm厚的骨位,防止面板变形和防止局部受力造成压屏3-5.TFT压屏支架尽量共用在量试的支架,6.1,6.2寸屏整块压屏支架厚度0.8mm,分开对称支架厚度1.0mm,尽量做对称的两条共用支架,7,8寸屏支架厚度1.0mm,采用上下两条安装或者整块安装,尽量共用. 3-6.面板支架与面板之间装配间隙为0.2mm,上下左右做骨位或者柱子定位,方便生产装配,出碟位置尽量留大,防止和碟片及两爪子干涉造成卡碟和出碟不顺现象发生.4.塑胶件材料及工艺规范4-1.旋钮导光圈和碟口导光片,遥控镜片,尽量共用,避免重复开模造成资源浪费.4-2.旋钮导光圈和碟口导光片材料目前有5种,(1)透明PC喷白油(705,714旋钮导光圈);(2)淡蓝PC(3)乳白色PC,(4)茶色.(5)橙色(玛驰在用).遥控镜片有两种材质:红棕色,紫褐色,做工艺图时尽量共用成熟的材料.4-3.所有面板材质使用ABS777-D(特殊情况除外),按钮材质为PC和ABS758-D,所有塑材工艺处理时,尽量使用目前公司在用的工艺,给生产带来负担),使用其它材质和工艺需测试组不准随便增加油漆和丝印种类(如哑黑油漆能共用尽量共用,以免和领导同意.4-4.所有需要喷灰色油漆的面板底材请用灰白色材质(同704凯美瑞面板),可防止划伤后露出黑底,喷灰色油漆的按钮材质可用灰白色PC或ABS758啤塑,直接喷油后镭雕.镭雕按钮工艺尽量简单,禁止多次喷涂.5.PCB板工艺设计规范.5-1.所有按键板厚度为1.2mm,GPS,SD,AUX,USB小板厚度1.2mm,出结构限高图时,应用不同颜色和图层以及阴影部分详细写出避位和元器件摆放区域,避免LAYOUT时出错.5-2.在走LAY板流程时,请同时附上结构图和原理图,图纸用恒晨共用的图框,注明设计师名字,项目名称,以及日期,修改后的板卡,请在流程表格里面注明修改事项,原因,修改后的版本号,最重要的是在图纸里注明详细修改事项,必要时去LAYOUT组当面5-3.所有PCB板线框图纸和拼板图由结构工程师提供,PCB板结构图和拼板时严格按图纸要求实行(具体见图).5-4.结构工程师画板卡结构图时,应该和硬件工程师一块讨论元器件的摆放位置和排插件的插口方向,排线的长度,元器件做成标准件,越详细越好,特别要考虑生产工艺是否能大批量生产.5-5.在做结构设计时候,请把TFT支架和面板支架接地,防止静电对电路和元器件造成破坏.5-6.LED灯数量和摆放位置尽量科学,旋钮导光一般采用3颗LED灯,类似迈腾上方透光钮用4颗灯,大导光圈导光面积大,也用4颗灯.5-7.目前PCB有两种手指,金手指和碳膜手指,此两种工艺可靠性差不多l,碳膜工艺简单便宜,请尽量用碳膜工艺.5-8 遥控接收头可根据不同高度加海绵垫,塑料套管,塑胶支架,因此物件属于PCB板组件,所以所加的垫片物料必须加到PCB板组件BOM单里,料号由结构工程师提供给BOM工程师..设计经常会出现的问题及对策.7-1.设计时经常会出现的严重问题:(1)出碟不顺. (2)严重卡键(包括装车和DVD面板).(3)触摸屏触摸不良(4)按钮按下去无功能.(5)屏装配过程中压坏或运输过程中容易破损.问题分析及预防:7-2.设计时的常见的普遍性问题:(1)漏光. (2)透光不均或不透光.(3)按钮手感不好,有摩擦音(4)旋钮手感不好,装配太紧.(5)装车有缝隙,或装不到位.。
汽车的电子硬件设计

《汽车电子硬件设计》-详细目录发布时间:2011-05-29 22:58:53我把目录给整理了一下,并且把一部分以图形的方式画了出来,全部画出来以后可以通过图形化的方式把内容给联系起来,这样对我也是一种直观的整理方式。
对《汽车电子硬件设计》的建议第0章汽车电子和产业概览汽车电子企业和汽车电子产业链汽车电子企业的变化我国的汽车电子产业第1章汽车电子环境1.1 气候与化学环境基本温度实验、模块的外壳防护等级、湿热试验、化学环境和盐雾1.2 机械负荷振动、冲击和跌落1.3 电气负荷过电压与反电压、开路与短路、地偏移和供电的非理想情况1.4 电磁兼容电源传导干扰、静电第2章汽车电子开发流程2.1 质量体系TS16949、八项基本原则2.2 电子产品的开发流程模块的开发流程、V型过程、职责划分、团队构建、Review方法、文件系统、流程化的思考第3章汽车电子硬件设计方法3.1 可靠性预测元器件失效率计算、失效分布、使用的修正和降额设计3.2 最坏情况分析基本介绍、极值分析法、均方根分析、蒙特卡罗分析、PSPICE 3.3 DFMEA故障解决方法、DFMEA的基本内容3.4 故障树分析基本介绍、实际应用3.5 潜在路径分析熔丝盒问题、潜在电路的分析3.6 热分析稳态的散热计算、热特性参数、PCB导线设置第4章元器件注意事项4.1 对于元器件的规范要求ROHS、氧化和湿敏4.1 电阻选值、元件工艺、最坏精度、散热分析、防浪涌能力、大封装问题4.2 电容数字电路的噪声、旁路电容和去耦电容、MLCC电容、铝电解电容、钽电容、容值偏差4.3 二极管特性和参数、稳压管的使用、细致的功耗计算4.4 三极管饱和的条件、注意事项4.5 功率MOSFET管开启关闭特性、直接耦合驱动电路三章内容联系第5章汽车电子低压电源设计5.1电源反接保护二极管电路、PMOS管电路、NMOS管电路、继电器、开关控制电路的设计5.2 瞬态抑制静电电容、TVS管的使用、MOV的使用5.3 电压监测迟滞门限和状态图、过压与欠压电路、Bulk电容5.4 低压降稳压器稳压原理、LDO的热分析、电容ESR引起的震荡5.5 静态电流的管理静态电流的限制、静态电流控制策略第6章汽车电子输入与输出接口6.1 输入输出的规范化整理连接器的选型考虑、I/O功能框图6.2 开关输入设计的基础要求开关和线束、输入开关状态分析6.3 低电平和高电平有效电路接口设计约束、电路的正向设计、从外部到内部的验证、从内部到外部的验证、实际微调6.4 模拟输入接口组合开关的电路、电流转换电路6.5 智能功率器件开关的功耗分析、感性负载保护、反接保护、故障诊断电路与波形、模拟诊断的计算6.6 继电器应用继电器参数分析、继电器的各种电压、浪涌电压的抑制、触点保护第7章主控单元与模块设计7.1 单片机的输入输出口IO驱动能力、MCU功耗分析、AD转化误差、内置AD的使用、未使用的引脚7.2 单片机的时钟与复位复位详解、时钟选择、高速CAN的时钟精度第8章电子制图设计8.1 原理图设计原理图绘制要点、 BOM的整理和规范8.2 地线策略地线策略设计目标、地线间的连接处理8.3印刷电路板的设计布局规则、走线的规则8.4 DFM设计可制造性的设计要点、可测试性设计8.5印刷电路板的加工过程和工艺第9章汽车电子工程师的成长与杂谈9.1 汽车电子硬件工程师的成长9.2 认识汽车产品质量的重要性9.3 硬件工作内容和重心的转变9.4 在组织中学习和规范化改进9.5 汽车电子领域工程师的工作机会和发展机遇9.6 给毕业生和在校学生的几条建议《汽车电子硬件设计》-硬件设计方法发布时间:2011-05-29 22:56:56其实从一个角度而言,整本书都可以不要,但是这个章节确实需要让每一位在汽车电子领域从事硬件设计的工程师去重视。
基于OMAP5912的汽车电子音频系统硬件设计

基于OMAP5912的汽车电子音频系统硬件设计
凌乐;朱善安
【期刊名称】《电子器件》
【年(卷),期】2007(030)002
【摘要】文章以车载汽车电子多媒体音频系统为研发背景,采用TI公司的双核(ARM+DSP)芯片0MAP5912,构建出低功耗、高性能的音频系统硬件平台.详细介绍了OMAP平台的系统结构,并结合其特点,分别从电源模块、存储模块、音频模块、接口模块这四个方面描述了整套音频系统的硬件设计.并针对该系统,给出了Bootloader烧写和Linux移植的实现方法,为应用软件的开发提供了完整的硬件平台.
【总页数】4页(P721-724)
【作者】凌乐;朱善安
【作者单位】浙江大学电气工程学院,杭州,310027;浙江大学电气工程学院,杭州,310027
【正文语种】中文
【中图分类】TN912
【相关文献】
1.基于AU7842A的车载数字音频系统的硬件设计 [J], 杜亮;黄静;马杰;陈杰;章涵博
2.OMAP5912双核通信及其数字音频系统实现 [J], 潘涛涛;张正炳;夏振华
3.基于OMAP5912的嵌入式语音识别系统硬件设计 [J], 王玉宏;张雪英;白静;杨斌
4.基于TMS320DM6446的音频系统硬件设计 [J], 韩哲鑫;伍爽
5.基于TMS320DM6446的音频系统硬件设计的研究 [J], 翁哲
因版权原因,仅展示原文概要,查看原文内容请购买。
汽车电子功能安全标准ISO26262解析(三)——硬件部分

汽车电子功能安全标准ISO26262解析(三)——硬件部分汽车电子功能安全标准ISO26262解析(三)——硬件部分原创pianpian_zct 最后发布于2017-12-29 13:09:34 阅读数13865 收藏展开1. The necessary activities and processes for the product development at the hardware level include:(1) the hardware implementation of the technical safety concept;(2) the analysis of potential hardware faults and their effects;(3) the coordination with software development.为了满足ISO26262,硬件方面需要做的工作包括:(1) 功能安全概念的硬件实现;(2) 潜在硬件失效及后果分析;(3) 与软件开发协同合作。
2. 硬件功能安全相关工作:硬件功能安全方面相关工作包括:(1) 5.5 initiation of product development at the hardware level: 启动硬件设计具体包括哪些工作包?目的是决定并计划硬件设计每个阶段的功能安全活动。
输入:完善后的项目计划、完善前的安全计划、完善后的集成测试计划输出:完善后的安全计划(2) 5.6 specification of hardware safety requirements: 定义硬件功能安全需求输入:安全计划、安全概念、系统设计说明书、硬件软件接口说明输出:硬件安全需求(包括测试和验证标准)、完善的硬件软件接口说明、硬件安全需求验证报告如何定义硬件功能安全需求,使用什么工具软件,模板如何?They are derived from the technical safety concept and system design specification.硬件功能安全需求来源于系统安全概念和系统设计文档。
关于汽车电子电气架构设计与优化的研究
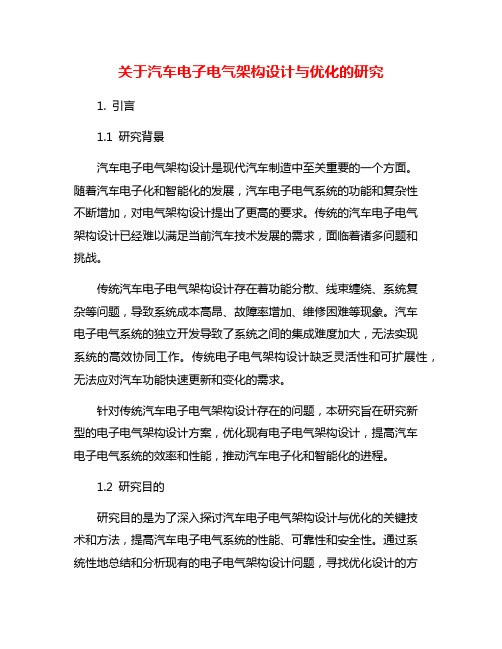
关于汽车电子电气架构设计与优化的研究1. 引言1.1 研究背景汽车电子电气架构设计是现代汽车制造中至关重要的一个方面。
随着汽车电子化和智能化的发展,汽车电子电气系统的功能和复杂性不断增加,对电气架构设计提出了更高的要求。
传统的汽车电子电气架构设计已经难以满足当前汽车技术发展的需求,面临着诸多问题和挑战。
传统汽车电子电气架构设计存在着功能分散、线束缠绕、系统复杂等问题,导致系统成本高昂、故障率增加、维修困难等现象。
汽车电子电气系统的独立开发导致了系统之间的集成难度加大,无法实现系统的高效协同工作。
传统电子电气架构设计缺乏灵活性和可扩展性,无法应对汽车功能快速更新和变化的需求。
针对传统汽车电子电气架构设计存在的问题,本研究旨在研究新型的电子电气架构设计方案,优化现有电子电气架构设计,提高汽车电子电气系统的效率和性能,推动汽车电子化和智能化的进程。
1.2 研究目的研究目的是为了深入探讨汽车电子电气架构设计与优化的关键技术和方法,提高汽车电子电气系统的性能、可靠性和安全性。
通过系统性地总结和分析现有的电子电气架构设计问题,寻找优化设计的方法和手段,探讨新型电子电气架构设计方案,以期为汽车电子电气系统的发展提供有益的参考和指导。
通过研究电子电气架构设计与实际应用的关系,进一步验证优化设计方案的可行性和实用性,帮助制造商和研究机构更好地理解和应用先进的电子电气架构技术。
通过本研究的开展,希望能够为汽车电子电气架构设计领域的发展提供新思路和新方法,促进汽车电子电气系统的创新与进步,推动整个汽车行业向更加智能化、电气化和互联化的方向发展。
2. 正文2.1 汽车电子电气架构设计的重要性汽车电子电气架构设计是现代汽车研发中至关重要的一环。
随着汽车技术的不断发展和智能化水平的提升,传统的电气架构已经难以满足对汽车功能和性能的需求。
设计一个高效、可靠的电子电气架构对于实现汽车功能的完美展现和优化汽车性能具有至关重要的作用。
汽车电子与控制技术-5底盘电控系统(eps)

在实际EPS系统上应用设计的控制算法,并进行实验验证。通过实验数据的分析和处理,可以进一步 评估控制算法的实际效果和性能表现。同时,实验结果也可以为算法的改进和优化提供有价值的参考 信息。
05 EPS系统性能评价与优化 方向
性能评价指标体系建立
操控稳定性
EPS系统应能够提供稳定的操控 性能,包括转向灵敏度、回正 性能和路感传递等。
排除故障实践案例分享
01
02
03
案例一
一辆汽车出现转向沉重故 障,经过检查发现EPS电 机损坏,更换电机后故障 排除。
案例二
一辆汽车出现转向异响故 障,经过检查发现转向机 构磨损严重,更换转向机 构后故障排除。
案例三
一辆汽车出现转向失灵故 障,经过检查发现EPS控 制模块内部故障,更换控 制模块后故障排除。
07 总结与展望
本次项目成果回顾
实现了底盘电控系统的基本功能
01
在本次项目中,我们成功实现了底盘电控系统(EPS)的基本功
能,包括转向助力控制、稳定性控制、节能控制等。
优化了系统性能
02
通过对EPS系统的优化,提高了系统的响应速度、控制精度和稳
定性,进一步提升了车辆的操控性和安全性。
完成了实验验证
转向异响故障
可能原因有转向机构磨 损、电机轴承磨损、控 制模块内部故障等,导 致转向时产生异常噪音。
转向失灵故障
EPS系统完全失效,方 向盘变得非常沉重且无 法转动,可能原因包括 电机损坏、控制模块故 障、电源故障等。
故障诊断流程和方法介绍
故障诊断流程
首先进行初步检查,包括检查EPS系统电源、保险丝、连接器等是否正常;然后进行系 统自诊断,利用专用诊断仪读取故障代码和数据流;最后根据故障代码和数据流进行故
基于OMAP5912的汽车电子音频系统硬件设计

第30卷 第2期2007年4月电子器件Ch inese Jou r nal Of Elect ro n DevicesVol.30 No.2Ap r.2007H ar dw ar e Design of Automobile Audio System B a sed on OMAP5912L I N G L e ,Z H U S ha n 2an(Col lege o f Elect rical Engi neeri n g ,Zhej i ang Univers it y ,Hang zhou 310027,Chi na )Abstract :This paper introduces t he hardware design of automobile audio syst em based on OMAP5912.The design in 2tegrates a high performance DSP subsystem based on a low pow er TMS 32OC55x DSP and a MPU subsystem based on t he ARM9Microprocessor for t he optimal combination of high per formance wit h low power consumption.Thi s paper explains the system design and t he c ircuit design includi ng power module ,memory module ,audio m odule and interfacem odule.Bootloader programming and Linux transplant are al so given.K ey w or ds :automo bil e el ect ronics ;a udio syst em ;OMA P5912;circuit design EEACC :7810;6450基于OM AP5912的汽车电子音频系统硬件设计凌 乐,朱善安(浙江大学电气工程学院,杭州310027)收稿日期6225作者简介凌 乐(82),男,硕士在读,从事嵌入式系统,虚拟实验室,计算机网络等研究,@;朱善安(52),男,博士,教授,博导,从事预测自适应控制理论与工业应用,ID 自整定理论与工业应用,基于机的智能控制系统,信息传输与自动化系统等研究,z @zj 。
汽车电子车载通信终端EMC设计

汽车电子车载通信终端EMC设计摘要:车辆网络的主要组成部分,车辆通信终端(英文名字是TelematicsBOX,称为“T -盒),承担车辆之间的网络和数据通信网络在车外,身体的重要功能,如数据采集、远程控制,所以越来越多的广泛应用,特别是在电动汽车远程服务的技术规范和管理制度的国家标准(GB / T32960),使T箱前端装载率将大大提高,设计在满足车辆段对车载通信终端变化的功能需求的同时,也要应对电磁兼容设计带来的挑战。
本文主要介绍了T-box和EMC设计分析。
关键词:汽车;电子车载;通信终端;EMC设计1车载通信终端EMC设计T-Box的EMC测试主要包括辐射测试、抗干扰测试和ESD测试,其中重测、BCI测试和ESD测试是重点。
如果在产品设计之初考虑不当,NG就会出现在测试中,重新测试的结果会导致个别频率点超过设定的标准。
产品在BCI测试中受到干扰时,监测数据会出现乱码。
ESD会导致接口损坏或驱动IC失效等,所以有必要从设计分析的源头入手,在实验中采取有效的对策,以降低产品的EMC风险。
1.1车载通信终端RE问题及解决措施RE测试是衡量被试品通过空间辐射对其他设备的骚扰能力。
汽车电子的RE测试检测频率一般从0.1MHz开始,最高可以达到3GHz,几乎覆盖到所有通讯行业频率,造成RE超标的原因是多方面的,如设计电路有缺陷、PCB布局问题、结构屏蔽效能低、器件选型问题等等,因此需要针对具体问题而具体分析,在笔者的一个项目曾经遇到低频段1.2MHz频点严重超标,通过排除法定位了来自电感器件问题,采用全封闭电感替代半封闭电感后,通过实验再次验证,辐射明显降低了。
如图1、图2所示。
图1整改前测试图片图2整改后测试图片针对RE辐射问题,常见的解决办法如下:1.1.1降低干扰源辐射能量T-BOX内部电路各个器件工作时钟CLK频率也各不相同,从几百KHz一直到几十MHz,通常为了降低时钟对外能量辐射,在器件收发时钟线上串联10-22Ω不等的电阻,让时钟脉冲上升沿变为缓慢上升;同时对时钟线要做包地处理;空间上与其他布线之间要满足3W原则;其他模拟信号电路要远离时钟干扰源。
- 1、下载文档前请自行甄别文档内容的完整性,平台不提供额外的编辑、内容补充、找答案等附加服务。
- 2、"仅部分预览"的文档,不可在线预览部分如存在完整性等问题,可反馈申请退款(可完整预览的文档不适用该条件!)。
- 3、如文档侵犯您的权益,请联系客服反馈,我们会尽快为您处理(人工客服工作时间:9:00-18:30)。
《汽车电子硬件设计》-详细目录发布时间:2011-05-29 22:58:53我把目录给整理了一下,并且把一部分以图形的方式画了出来,全部画出来以后可以通过图形化的方式把内容给联系起来,这样对我也是一种直观的整理方式。
对《汽车电子硬件设计》的建议第0章汽车电子和产业概览汽车电子企业和汽车电子产业链汽车电子企业的变化我国的汽车电子产业第1章汽车电子环境1.1 气候与化学环境基本温度实验、模块的外壳防护等级、湿热试验、化学环境和盐雾1.2 机械负荷振动、冲击和跌落1.3 电气负荷过电压与反电压、开路与短路、地偏移和供电的非理想情况1.4 电磁兼容电源传导干扰、静电第2章汽车电子开发流程2.1 质量体系TS16949、八项基本原则2.2 电子产品的开发流程模块的开发流程、V型过程、职责划分、团队构建、Review方法、文件系统、流程化的思考第3章汽车电子硬件设计方法3.1 可靠性预测元器件失效率计算、失效分布、使用的修正和降额设计3.2 最坏情况分析基本介绍、极值分析法、均方根分析、蒙特卡罗分析、PSPICE 3.3 DFMEA故障解决方法、DFMEA的基本内容3.4 故障树分析基本介绍、实际应用3.5 潜在路径分析熔丝盒问题、潜在电路的分析3.6 热分析稳态的散热计算、热特性参数、PCB导线设置第4章元器件注意事项4.1 对于元器件的规范要求ROHS、氧化和湿敏4.1 电阻选值、元件工艺、最坏精度、散热分析、防浪涌能力、大封装问题4.2 电容数字电路的噪声、旁路电容和去耦电容、MLCC电容、铝电解电容、钽电容、容值偏差4.3 二极管特性和参数、稳压管的使用、细致的功耗计算4.4 三极管饱和的条件、注意事项4.5 功率MOSFET管开启关闭特性、直接耦合驱动电路三章内容联系第5章汽车电子低压电源设计5.1电源反接保护二极管电路、PMOS管电路、NMOS管电路、继电器、开关控制电路的设计5.2 瞬态抑制静电电容、TVS管的使用、MOV的使用5.3 电压监测迟滞门限和状态图、过压与欠压电路、Bulk电容5.4 低压降稳压器稳压原理、LDO的热分析、电容ESR引起的震荡5.5 静态电流的管理静态电流的限制、静态电流控制策略第6章汽车电子输入与输出接口6.1 输入输出的规范化整理连接器的选型考虑、I/O功能框图6.2 开关输入设计的基础要求开关和线束、输入开关状态分析6.3 低电平和高电平有效电路接口设计约束、电路的正向设计、从外部到内部的验证、从内部到外部的验证、实际微调6.4 模拟输入接口组合开关的电路、电流转换电路6.5 智能功率器件开关的功耗分析、感性负载保护、反接保护、故障诊断电路与波形、模拟诊断的计算6.6 继电器应用继电器参数分析、继电器的各种电压、浪涌电压的抑制、触点保护第7章主控单元与模块设计7.1 单片机的输入输出口IO驱动能力、MCU功耗分析、AD转化误差、内置AD的使用、未使用的引脚7.2 单片机的时钟与复位复位详解、时钟选择、高速CAN的时钟精度第8章电子制图设计8.1 原理图设计原理图绘制要点、BOM的整理和规范8.2 地线策略地线策略设计目标、地线间的连接处理8.3印刷电路板的设计布局规则、走线的规则8.4 DFM设计可制造性的设计要点、可测试性设计8.5印刷电路板的加工过程和工艺第9章汽车电子工程师的成长与杂谈9.1 汽车电子硬件工程师的成长9.2 认识汽车产品质量的重要性9.3 硬件工作内容和重心的转变9.4 在组织中学习和规范化改进9.5 汽车电子领域工程师的工作机会和发展机遇9.6 给毕业生和在校学生的几条建议《汽车电子硬件设计》-硬件设计方法发布时间:2011-05-29 22:56:56其实从一个角度而言,整本书都可以不要,但是这个章节确实需要让每一位在汽车电子领域从事硬件设计的工程师去重视。
一个普遍意义上的问题是,当我们了解完需求,把内动定义好,从电路图设计开始到电路图绘制完成,有什么样的一个形式来说明这个设计是可靠的呢?这个问题的提出是在于,如何能够说服自己和说服整个团队,电路的设计是经过精心考虑的,能够在前期的考虑中,就完全考虑了后面可能出现的问题,包括需要通过的设计验证试验、调试中可能出现的问题、装车过程中可能出现的问题和未来潜在的设计更改。
在以上的示意图中,大概归纳出了失效率&寿命估计、故障&原因分析、极端条件下的最坏情况的分析、潜在电路和潜在的模式分析和稳态和暂态的热状态分析这些内容,作为一个模块的强壮性的依据,换句话来说,也就是设计的靠谱程度。
这与在各个方面应用较多的强壮性设计方法,并没有冲突,本质上这块内容可以统统划分到容差分析里头,作为校核电路的内部指标(模块内生性的一些参数)和外部指标(根据系统要求的基本输出参数)。
在汽车中,有着太多的零件,而电子模块往往起着控制的作用,要是它趴下了,一个较小的子系统也就趴下了。
以车身控制器为例,车门、车窗、雨刮、车灯和门禁系统,哪个功能失效了,消费者可是要求索赔的,车商还得Cover经销商的问题,一旦累计到某个程度,还必须召回这些车辆。
所以在要求电子模块里头,质量问题也就成了最基本的要求,设计使用时间和整个模块的故障率都是要求较高的,毕竟没人要求一个MP3或者电风扇使用15年。
以下为目录,我将努力在每个小节的地方写清楚为什么?和之间的相互联系,作为每章理清思路的开始。
在补充以后,有不明白的地方可以提出来。
第3章汽车电子硬件设计方法3.1模块的可靠性预测如前面所说的那样,模块的无故障使用时间是需要工程师进行评估的。
这是从元件的失效率开始计算模块的子功能系统的失效率,最后大致得出整个模块的失效率,这个指标是需要进行控制的。
对于元件失效来说,是需要在实际运行中进行统计得出来的,由于汽车电子的特殊性,它并不具备自己失效数据库(汽车OEM负责调查汽车质量,控制模块仅仅作为一部分,很难单独进行大量的统计)。
不像做军工的可以参考MIL-HDBK-217F2,做通信的可以参考Telcordia Issue或者HRD5。
这项工作需要较多的时间,采取可靠性软件已经把完成简化;在自己需要亲手做的情况下,可以选择元件计数法或应力分析法,前者适用于缺乏足够的时间下得出简要结果,后者是设计到了需要确认的阶段清晰化的结果。
3.1.1 MIL-HDBK-217F美国的军标是一份久经考验的材料,由于其统计的样本较早,IC企业的工艺和可靠性都有着飞速的提升,以它的数值来进行评估,结果是很悲观并且不太切合实际。
因此往往根据这份材料来做一个相对结果,然后根据企业自身的数据对数据进行调整。
仔细看这份材料,里头有着我们使用的所有元件的失效率计算公式,也给出了各个参数所对应的数值,可以根据这些材料手头算算。
3.1.2 元件的失效分布单个元件的损坏,往往会形成不同的结果,这样的不同表现形式的失效也会对模块产生不同的影响。
而我们在分析这些结果的时候,也可以得到这种结果是依照一定的概率进行分布的。
217F并不给出失效的分布,338B则给出了完整的失效分布。
3.1.3 分布的简化事实上,338B给出了太多的失效模式,这使得我们的故障原因和错误树分析会非常复杂,而且我们比较关心一些关键性的失效模式,这样我们就需要对某些分布进行合并和简化。
这个事情是需要公司进行积累的,比较简单的方法是找元器件的提供商给出其分析的数据,往往可以较为简单的达到目的。
3.1.4 降额设计元件的失效率是直接与其各种载荷直接相关的,也就是其标称的值,需要采取一定的降额使用才能达到一个较为理想的结果。
而在算完一遍失效率以后,再去调整每个元件的额度是较为痛苦的,因此这里可以参考GJBZ3593进行一个前置的处理。
然后根据前面的失效率检查,确认结果才进行调整,后续的工作会做得有效些。
3.2 最坏情况分析PS:做这项工作时间最久,也最有感情。
元件的失效往往不一定在稳定的状态下,有时候是在恶劣的环境下,各种载荷和条件集中在一起的时候,使得模块突然超过了其容忍程度。
因此估计在各种最坏条件下,模块中的电路的各种参数和特性是非常有必要的。
这里需要保证,模块的各个主要功能符合规定的范围,实际状态达不到损坏的范围,因此热状态的分析往往是最坏情况分析的一个主要研究对象,这部分内容与热分析有着一定的重叠和交叉。
我们要分析的误差,大概可分为初始偏差、汽车环境变化引起的偏差和退化效应引起的部分。
对于数字电路和模拟电路分别有着需要关注的内容,方法一般有三种,极值法、均方根法和蒙特卡洛。
3.2.1 整合复杂的情况最基础的情况,是需要把每个元件建立起基础的参数文档。
一个最为简单的例子,是将电阻的精度,在各种条件下的最坏值给计算出来,我们看到的精度是正常状态下的。
另外一个重要的事情,是得把电路分析的方法找回来,由于计算过程中需要引入大量的模型,构成的回路较多。
可能需要在节点电压法和网孔电流法的支持下,使用矩阵进行运算。
3.2.2 极值分析法相对而言,这是最悲观和最简单的方法,将所有的输入参数分为上限和下限,就可以得到整个电路的上限和下限。
至于如何选择,则可以用灵敏度和求导方法求取上下限参数组合。
3.2.3 均方根分析相对乐观一点,也把某些坏的情况忽略了,将所有的参数的方差整理出来,得出系统的方差,然后选择覆盖模块的概率范围。
3.2.4 蒙特卡罗分析采用随机抽样的方法是较为简单的,不停的在一个范围内进行随机数代入,得出系统的分布的柱状图,能够精确的知道模块在大量应用的实际情况。
这是必不可少的步骤,在计算中需要一些技巧,我做了一个例子。
3.2.5 PSPICE的应用用软件的方法当然是简单的,但是模型建立也需要费时间,一般作为某些电路分析的必要内容。
我其实推荐大家使用Mathcad,可以做得更为精确,特别是熬过初始的建立的那个阶段。
3.3 FMEA失效模式的影响分析在一个相对复杂的系统中,如果不能从减少潜在故障的角度去考虑问题,将可能收获诸多的问题。
在国际汽车质量要求越来越苛刻的条件下,汽车电子模块中进行失效模式的分析是非常有必要的。
由于这块内容需要更多经验,我曾经做过的东西好像实在是有些差距,这里只是给出了一些基本的参考材料。
3.3.1 找问题这里要说的,是我当初在涉及寻找故障中采取的一些标准化方法。
当初的某个车在路试的时候,转向灯的驱动电路烧毁,光是寻找这个原因就花费了大量的时间,最后找到的原因是门锁驱动抑制感性没做好。
按照当初的看法,如果有一份完整的DFMEA,长时间的无头绪调查和排查型实验毫无价值。
3.3.2 实际内容这部分整理了一些基础的内容,由于没有太多经验,只能尽力写些基础的材料,篇幅不大。
3.4 故障树分析故障树在某些故障的分析过程中,是一种非常好用的工具,在分析某些重大的故障和问题的时候,相对给力。