耐低温球铁生产工艺浅析
2MW风电轮毂低温球铁的生产工艺
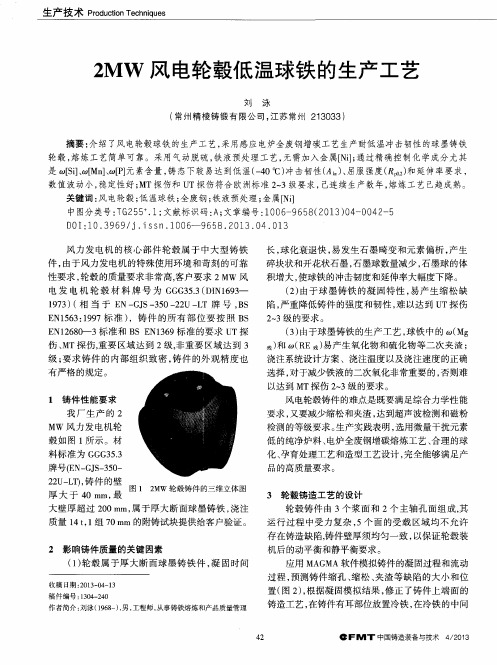
2 MW 风 电轮 毂低温球铁 的生产 工艺
刘 泳
( 常州精 棱铸 锻有 限公 司 , 江 苏常 州 2 1 3 0 3 3)
摘要 : 介 绍 了风 电轮 毂球铁 的生产 工艺 , 采 用感 应 电炉全废 钢增碳 工 艺 生产 耐低 温冲 击韧 性 的球 墨铸铁 轮毂 , 熔炼 工 艺简单 可 靠。采 用 气动脱 硫 , 铁 液预处 理 工艺 , 无 需加入 金属 [ N i ] ; 通过 精确 控 制 化 学成分 尤 其
1 9 7 3 ) ( 相 当于 E N— G J S 一 3 5 0— 2 2 U— L T牌 号 , B s
长, 球化衰退快 , 易发生石墨畸变和元素偏 析 , 产生 碎块状 和 开花状 石墨 , 石墨 球数 量减少 , 石 墨球 的体 积增大 , 使球铁的冲击韧度和延伸率大幅度下降。 ( 2 ) 由于球 墨铸铁 的凝 固特性 , 易产 生缩松缺 陷, 严重降低铸件 的强度和韧性 , 难 以达到 u T探伤
作者简介 : 刘泳( 1 9 6 8 一 ) , 男, 工程师, 从事铸铁熔炼和产品质量 管理
铸造工艺 , 在铸件有耳部位放置冷铁 , 在冷铁的中间
4 2
oFl Ⅵ r 中国铸造装备与技术 4 / 2 0 1 3
生产 技 术 P r o d u c t i o n T e c h n i q u e s
料标准为 G G G 3 5 . 3
牌 号( E N — G J S 一 3 5 0 一
2 2U L
-
厚大于
T 茎 图 1 2 M w 轮 毂 铸 件 的 三 维 立 体 图 3 轮 毂 铸 造 工 艺 的 设 计
科技成果——高韧性耐低温球墨铸铁生产技术
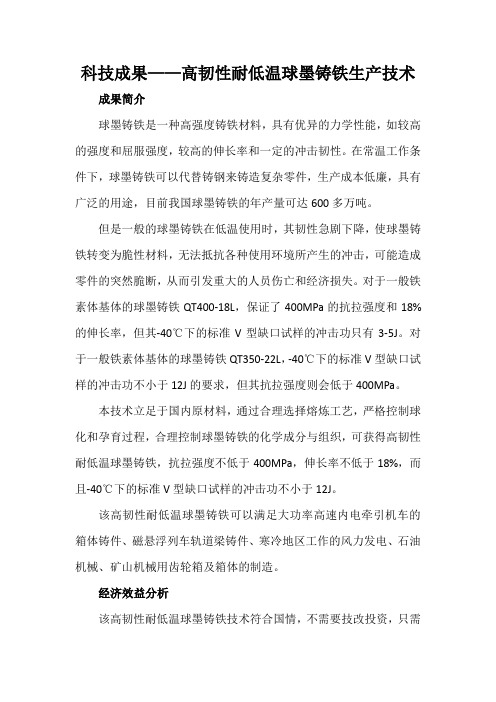
科技成果——高韧性耐低温球墨铸铁生产技术成果简介
球墨铸铁是一种高强度铸铁材料,具有优异的力学性能,如较高的强度和屈服强度,较高的伸长率和一定的冲击韧性。
在常温工作条件下,球墨铸铁可以代替铸钢来铸造复杂零件,生产成本低廉,具有广泛的用途,目前我国球墨铸铁的年产量可达600多万吨。
但是一般的球墨铸铁在低温使用时,其韧性急剧下降,使球墨铸铁转变为脆性材料,无法抵抗各种使用环境所产生的冲击,可能造成零件的突然脆断,从而引发重大的人员伤亡和经济损失。
对于一般铁素体基体的球墨铸铁QT400-18L,保证了400MPa的抗拉强度和18%的伸长率,但其-40℃下的标准V型缺口试样的冲击功只有3-5J。
对于一般铁素体基体的球墨铸铁QT350-22L,-40℃下的标准V型缺口试样的冲击功不小于12J的要求,但其抗拉强度则会低于400MPa。
本技术立足于国内原材料,通过合理选择熔炼工艺,严格控制球化和孕育过程,合理控制球墨铸铁的化学成分与组织,可获得高韧性耐低温球墨铸铁,抗拉强度不低于400MPa,伸长率不低于18%,而且-40℃下的标准V型缺口试样的冲击功不小于12J。
该高韧性耐低温球墨铸铁可以满足大功率高速内电牵引机车的箱体铸件、磁悬浮列车轨道梁铸件、寒冷地区工作的风力发电、石油机械、矿山机械用齿轮箱及箱体的制造。
经济效益分析
该高韧性耐低温球墨铸铁技术符合国情,不需要技改投资,只需
要适当改变现有生产工艺,能在较短时间内取得预期的效果,生产出符合技术指标的高韧性耐低温球墨铸铁件,可取得很好的经济效益,为提高制造企业档次、产品更新换代提供坚实的技术基础。
合作方式
以技术转让费或技术入股的方式进行合作,具体项目签订相应的合同。
超大功率风电机组低温球铁主轴的铸造工艺

超大功率风电机组低温球铁主轴的铸造工艺随着可再生能源的快速发展,风能作为一种清洁、可持续的能源形式,受到了广泛关注。
超大功率风电机组作为风能发电的核心设备之一,其关键部件之一——低温球铁主轴的铸造工艺备受关注。
低温球铁主轴是风电机组的核心组成部分之一,承载着风轮叶片的转动力矩,并将其传递给发电机。
由于风电机组的工作环境恶劣,主轴需要具备高强度、高耐磨、高抗腐蚀等特点。
而低温球铁作为一种优质铸造材料,具有良好的机械性能和耐腐蚀性能,因此成为了主轴铸造的理想选择。
低温球铁主轴的铸造工艺主要包括模具制作、熔炼、浇注、冷却和后处理等环节。
首先,根据主轴的设计要求,制作适应形状和尺寸的模具。
模具的制作需要考虑到主轴的复杂形状和内部结构,确保铸件的精度和质量。
接下来,进行熔炼工艺,将合适比例的生铁、废钢和合金料加入到高炉中进行熔炼,得到符合要求的铁水。
在浇注环节,需要将熔融的铁水倒入模具中,确保铁水充分填充模具的每个角落,避免产生气孔和缺陷。
为了提高铸件的质量,可以采用真空浇注或压力浇注等先进工艺。
浇注完成后,需要进行冷却处理,使铸件逐渐冷却固化,保证其内部结构的致密性和稳定性。
进行后处理工艺,包括去除模具、修整铸件表面、热处理和机械加工等。
去除模具时需要小心操作,避免对铸件造成损伤。
修整铸件表面可以采用机械加工或化学处理的方式,使其表面光滑平整。
热处理可以通过淬火、回火等方式,提高铸件的硬度和强度。
超大功率风电机组低温球铁主轴的铸造工艺是一个复杂而关键的过程。
通过合理的工艺流程和严格的质量控制,可以保证主轴的质量和性能,提高风电机组的工作效率和可靠性。
未来,随着技术的不断进步和创新,相信低温球铁主轴的铸造工艺将会得到进一步的优化和提升,为风能发电行业的发展做出更大的贡献。
低温球铁铸件的生产实践
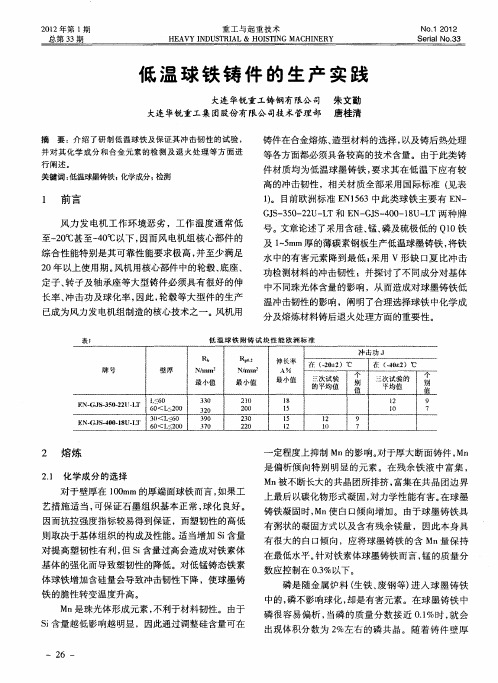
磷是随金属炉料 ( 生铁 、 废钢等) 进入球墨铸铁 中的, 磷不影响球化 , 却是有害元素。在球 墨铸铁 中
磷 很 容 易偏 析 , 当磷 的 质量 分 数 接 近 01 . %时 , 会 就 出现体 积分 数为 2 %左 右 的磷 共 晶 。随 着 铸件 壁 厚
一
2 一 6
重工与 起重 技术
HE AV 1 Y NDUS RI T AL & H0 S I I T NG MACHI RY NE
的增加, 偏析加重, 在热节部位磷共晶数量就多。当 磷量超过质量分数 0 7 . %时 , 0 基体 内出现了磷共晶 ,
使断 后伸 长率 急剧 降低 。 碳 当量 过高 , 将会 引起 石墨 漂浮 , 而石 墨漂浮 不
个 剐 值
三次试验的 F 值 均
l 2 l O
个 别 值
9 7
E
.
GJ - 5 . 2 j1 S 3 02 1.J T
I2 60 6 < L 0 0 20 3 0< L曼 O 6
30 3 3 0 2 3 90
21 O 2 0 0 2 0 3
基体组织。 铁水过热温度为 10 ~ 50 =浇注温度 50 l2 c, 【
为 1 3 ~ 3 0C 30 14 ̄。
采用冲入法进行球化处理 ,同时在炉前包 内进 行一次孕育处理 。 球化剂装包后要求先捣实 , 再覆盖 少量孕育剂及球铁铁末 , 并再次捣实 , 最后上面盖上 钢板。 翻炉时控制好球化剂起爆时机 , 在铁水翻出总
2 1 第 1期 0 2年 总第 3 3期
重 工与 起重 技术
HE AVY NDUS RI I T AL & H0I 1 NG MAC NE Sr I HI RY
低温球铁(-20℃)实验方案

抗低温冲击球铁实验方案1.使用原材料:生铁:Q10,Si≤1.0%,Mn≤0.3%,P≤0.03%,S≤0.02%,Ti≤0.045%。
(建议使用龙凤山生铁)废钢:使用薄钢板切边或其它高纯废钢。
C:<0.20%,Si:<0.40%,Mn<0.20%,P:<0.03%,S:<0.02%,Cr:<0.05%,Ti:<0.04%,Al:<0.01%,ΣT:<0.10%(总微量元素含量之和)球化剂、孕育剂:详见处理工艺。
其它材料:使用现有产品。
2.炉料配比:生铁约92.0%,废钢约8.0%,硅铁0.46%。
(最终炉料配比视材料成分而定)。
3.原铁水目标成分范围:C3.8±0.05%,Si1.00±0.05%,Mn≦0.15%,P≦0.03%,S≦0.02%,Ti≦0.040%,Cr≦0.05%。
4.铁水处理工艺:铁水最高升温至1520℃,出炉温度1510±10℃。
出炉时随流添加龙钇YFY- 80.5%。
倒入普通包内降温,温度至1450~1460℃时倒入球铁包球化处理。
球化剂加入量:龙钇FD- 3 1.1%。
孕育剂:龙钇YFY- 8包内加入0.5%。
覆盖剂:硅钢片0.5%。
5.浇注:浇注温度1370±10℃,浇注时随流加入龙钇YFY-2孕育剂0.1%。
6.最终成分目标:C=3.6±0.1%,Si=2.1±0.05%,Mn≦0.15%,P≦0.03%,S≦0.02%,Mg=0.035~0.045%,Re=0.008~0.015%。
6.需要添置的工具及设备:随流孕育漏斗及碳当量测定仪,光谱样模需要按要求更新。
总工办。
耐低温球铁生产工艺浅析
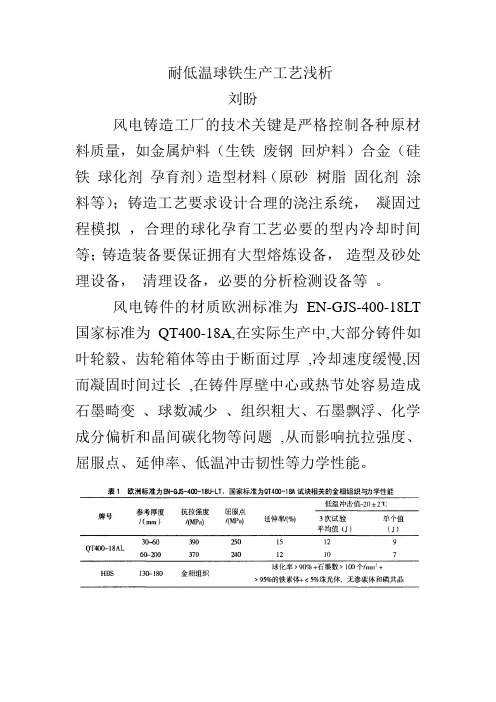
耐低温球铁生产工艺浅析刘盼风电铸造工厂的技术关键是严格控制各种原材料质量,如金属炉料(生铁废钢回炉料)合金(硅铁球化剂孕育剂)造型材料(原砂树脂固化剂涂料等);铸造工艺要求设计合理的浇注系统,凝固过程模拟,合理的球化孕育工艺必要的型内冷却时间等;铸造装备要保证拥有大型熔炼设备,造型及砂处理设备,清理设备,必要的分析检测设备等。
风电铸件的材质欧洲标准为EN-GJS-400-18LT 国家标准为QT400-18A,在实际生产中,大部分铸件如叶轮毅、齿轮箱体等由于断面过厚,冷却速度缓慢,因而凝固时间过长,在铸件厚壁中心或热节处容易造成石墨畸变、球数减少、组织粗大、石墨飘浮、化学成分偏析和晶间碳化物等问题,从而影响抗拉强度、屈服点、延伸率、低温冲击韧性等力学性能。
注:控制难点是低温冲击性能,EN-GJS-350-22LT球墨铸铁-40℃的冲击吸收功A KV要求达到12 J,单个试样最低值应>9J; EN-GJS-400-18LT球墨铸铁-20℃的冲击吸收功A KV要求达到12J, 单个试样最低值应>9J.要使球墨铸铁达到上述性能,必须进行以下两个方面的研究:(1)化学成分的确定化学成分决定了球墨铸铁的基体组织和铁素体中合金元素的固溶量, 不同的基体组织及其固溶度决定了不同的力学性能, 常见的球墨铸铁基体组织为铁素体.珠光体和奥氏体奥氏体具有良好的塑性和韧性,特别是低温冲击韧度。
但奥氏体球墨铸铁需要加入大量的合金元素,制造成本高,珠光体球墨铸铁具有高的强度和良好的塑性和韧性,但其无法达到EN-GJS-350-22LT和EN-GJS-400-18LT球墨铸铁的塑性和韧性要求。
铁素体基体本身具有优良的塑性和韧性,但铁素体球墨铸铁由于有其他元素的存在使铁素体基体得到固溶强化,所以铁素体基体球墨铸铁的塑性和韧性取决于铁素体基体中合金元素的固溶量,因此有必要对球墨铸铁的化学成分进行系统研究,确保得到稳定的强度和塑性以及低温冲击韧度要求全部合格。
耐低温冲击风电球铁铸件生产工艺要点

lw t mp r t r mp c o g n s e ur me t o e ea u e i a t u h e sr q ie n . t
Ke r :du tl r n;lw e y wo ds c i io e o tmpe au e i a ttu hn s rt r mp c o g es;wi o rca tn ;prc s nd p we si g oes
tel e ecnet o i n S P o rw m tr l te bt r ( ) dp E SF ly a ouain l y te h o rt otns fS,M , , f a aei s h e e; 2 A o tR Mgie ao snd l z ga o, h w h a, t l ri l
XI ANG i fn L U Jn hபைடு நூலகம்i Ha- e g , I i - a
低温球墨铸铁
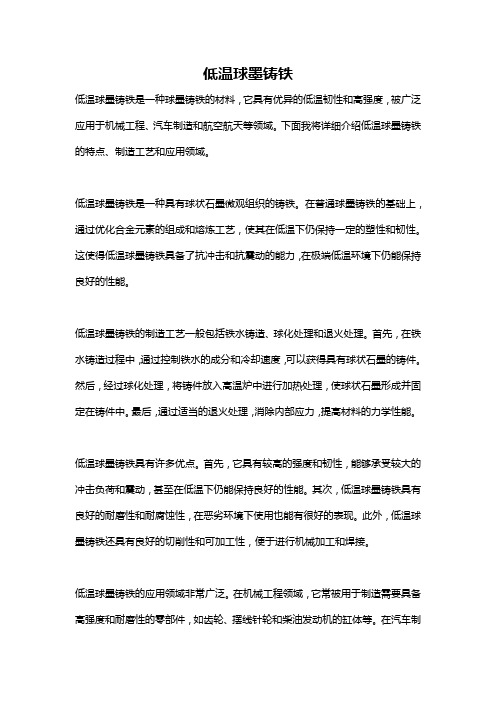
低温球墨铸铁低温球墨铸铁是一种球墨铸铁的材料,它具有优异的低温韧性和高强度,被广泛应用于机械工程、汽车制造和航空航天等领域。
下面我将详细介绍低温球墨铸铁的特点、制造工艺和应用领域。
低温球墨铸铁是一种具有球状石墨微观组织的铸铁。
在普通球墨铸铁的基础上,通过优化合金元素的组成和熔炼工艺,使其在低温下仍保持一定的塑性和韧性。
这使得低温球墨铸铁具备了抗冲击和抗震动的能力,在极端低温环境下仍能保持良好的性能。
低温球墨铸铁的制造工艺一般包括铁水铸造、球化处理和退火处理。
首先,在铁水铸造过程中,通过控制铁水的成分和冷却速度,可以获得具有球状石墨的铸件。
然后,经过球化处理,将铸件放入高温炉中进行加热处理,使球状石墨形成并固定在铸件中。
最后,通过适当的退火处理,消除内部应力,提高材料的力学性能。
低温球墨铸铁具有许多优点。
首先,它具有较高的强度和韧性,能够承受较大的冲击负荷和震动,甚至在低温下仍能保持良好的性能。
其次,低温球墨铸铁具有良好的耐磨性和耐腐蚀性,在恶劣环境下使用也能有很好的表现。
此外,低温球墨铸铁还具有良好的切削性和可加工性,便于进行机械加工和焊接。
低温球墨铸铁的应用领域非常广泛。
在机械工程领域,它常被用于制造需要具备高强度和耐磨性的零部件,如齿轮、摆线针轮和柴油发动机的缸体等。
在汽车制造领域,低温球墨铸铁常被用于制造发动机的缸体和曲轴箱等关键部件。
在航空航天领域,它也被广泛应用于制造飞机引擎的转子、涡轮叶片和燃烧室等关键部件。
总之,低温球墨铸铁是一种具有良好低温韧性和高强度的材料。
经过优化的制造工艺,它能够在低温环境下保持良好的性能,并具有优异的耐磨性和耐腐蚀性。
在机械工程、汽车制造和航空航天等领域,低温球墨铸铁被广泛应用于制造各种关键零部件,发挥着重要的作用。
- 1、下载文档前请自行甄别文档内容的完整性,平台不提供额外的编辑、内容补充、找答案等附加服务。
- 2、"仅部分预览"的文档,不可在线预览部分如存在完整性等问题,可反馈申请退款(可完整预览的文档不适用该条件!)。
- 3、如文档侵犯您的权益,请联系客服反馈,我们会尽快为您处理(人工客服工作时间:9:00-18:30)。
耐低温球铁生产工艺浅析刘盼风电铸造工厂的技术关键是严格控制各种原材料质量,如金属炉料(生铁废钢回炉料)合金(硅铁球化剂孕育剂)造型材料(原砂树脂固化剂涂料等);铸造工艺要求设计合理的浇注系统,凝固过程模拟,合理的球化孕育工艺必要的型内冷却时间等;铸造装备要保证拥有大型熔炼设备,造型及砂处理设备,清理设备,必要的分析检测设备等。
风电铸件的材质欧洲标准为EN-GJS-400-18LT 国家标准为QT400-18A,在实际生产中,大部分铸件如叶轮毅、齿轮箱体等由于断面过厚,冷却速度缓慢,因而凝固时间过长,在铸件厚壁中心或热节处容易造成石墨畸变、球数减少、组织粗大、石墨飘浮、化学成分偏析和晶间碳化物等问题,从而影响抗拉强度、屈服点、延伸率、低温冲击韧性等力学性能。
注:控制难点是低温冲击性能,EN-GJS-350-22LT球墨铸铁-40℃的冲击吸收功A KV要求达到12 J,单个试样最低值应>9J; EN-GJS-400-18LT球墨铸铁-20℃的冲击吸收功A KV要求达到12J, 单个试样最低值应>9J.要使球墨铸铁达到上述性能,必须进行以下两个方面的研究:(1)化学成分的确定化学成分决定了球墨铸铁的基体组织和铁素体中合金元素的固溶量, 不同的基体组织及其固溶度决定了不同的力学性能, 常见的球墨铸铁基体组织为铁素体.珠光体和奥氏体奥氏体具有良好的塑性和韧性,特别是低温冲击韧度。
但奥氏体球墨铸铁需要加入大量的合金元素,制造成本高,珠光体球墨铸铁具有高的强度和良好的塑性和韧性,但其无法达到EN-GJS-350-22LT和EN-GJS-400-18LT球墨铸铁的塑性和韧性要求。
铁素体基体本身具有优良的塑性和韧性,但铁素体球墨铸铁由于有其他元素的存在使铁素体基体得到固溶强化,所以铁素体基体球墨铸铁的塑性和韧性取决于铁素体基体中合金元素的固溶量,因此有必要对球墨铸铁的化学成分进行系统研究,确保得到稳定的强度和塑性以及低温冲击韧度要求全部合格。
(2)热处理工艺的确定球墨铸铁的铸态组织一般为铁素体和珠光体的混合组织。
但因为珠光体组织强度高,塑性及韧性差,所以在低温球墨铸铁中要尽量消除珠光体组织,除在成分设计上尽可能减少促进珠光体形成的元素,还需对球墨铸铁进行高温退火热处理,以最大限度地减少珠光体的存在。
一.风电铸件用生铁与废钢设计化学成分的原则是高碳、中硅、低锰、低磷和低硫,在力学性能达到的情况下,尽量不加入其它合金,炉料中带来的合金元素(在这里应看作杂质)总量越低越好。
选用球化指数SB 小于0.6% ,Ti元素小于0.04% 的生铁和纯净度高的低锰碳素废钢,注意废钢的选择不能有焊缝、油漆、铁锈等,回炉料最好是同类材质的成分,铁液中杂质越少越好,尤其是反球化干扰元素如Pb、As 、Ti等,熔炼时必须进行铁液过热处理。
炉料中首选低磷、低硫、低锰的Q10 或Q12 生铁,废钢为优质A3或槽钢、工字钢等。
正常配料为:生铁Q10 (C 4. 2 ,Si 0. 94) 58 % ,废钢(C 0. 25 ,Si 0. 4) 22 % ,回炉料(C 3. 5 ,Si 2. 1) 20 % ,当温度达到 1 450~1 460 ℃时,炉前用快速分析仪测定CE、C和Si ,并根据实测情况加以调整。
出炉温度≥1 480~1 510 ℃;球化处理:稀土球化剂,用量1. 5 %;一次孕育处理为75Si2Fe 0. 5 %~0. 6 % ,在孕育剂上盖干净铁屑、覆盖剂和铁板,适当紧实。
生产风电铸件应选择优质的生铁,主要体现在①生铁最好是共晶成分的,避免过共晶的成分,否则生铁内部就会出现过共晶的粗大石墨,这样会影响铸件石墨形态②P含量要小于0.046% ,以避免凝固时产生磷共晶③微量反球化干扰元素的控制,在铸件中有些元素能破坏和阻碍石墨球化,这些元素即所谓的球化干扰元素,干扰元素分为两类,一是消耗球化元素型干扰元素,它们与镁、稀土生成MgS,MgO,MgSe 等,使球化元素降低,从而破坏了球状石墨形成另一类是晶间偏析型干扰元素,包括锡、锑、砷、铜、钛、铝等在共晶结晶时,这些元素富集在晶界,促进使碳在共晶后期形成畸形的枝晶状石墨,球化干扰元素原子量越大,其干扰作用越强,现在许多研究都已找到了干扰元素在铸铁中的临界含量,当这些元素含量小于临界含量时,并不能形成畸变石墨。
二.耐低温球铁的化学成分与配料目前风电铸件的最终化学成分大致控制在C3.4%-3.7%,Si1.9%-2.3%,Mn<=0.3%,S<=0.015%,P<=0.045%,Mg残0.04%--0.06%,RE残<=0.018%,低CE,低Mn低S低P,以及尽可能低的Cr.Mo.Ti.Sn.V 等正偏析元素。
其它元素如Ni 基本不加,在CE 方面,大件取下限,小件取上限,主要是调整含 C 量,Si含量基本不变化,特别值得一提的是含SI 量的控制,生产初期,为了提高低温冲击韧性,将含Si 量控制在 2.0% 以下,甚至 1.6%一 1.8%的低限,结果低温冲击韧性非常好,普遍达到17、18 、19J ,但抗拉强度却维持勉强合格且不稳定,有时还不合格,非常矛盾的抗拉强度与低温冲击韧性一直困绕着技术人员,经过不断地摸索,一次次的调整、实验,反反复复的验证,最终确定合理的最佳含Si 量在 1.9%一 2.3% 之间,低于 1.9% 时低温冲击韧性非常好,但抗拉强度却不稳定; 高于 2.3% 时,则低温冲击韧性不稳定。
其它元素无论大件还是小件基本不变,Ni元素在生产风电铸件的初期,多数企业都加人约0.3%一0.5%的比例,主要为促进低Si 量而带来的石墨化能力不足和增加铸件的抗拉强度,后来在实践中发现,如果NI 元素低于0.5% 时,基本不起作用,只有大于0.5% 时,才能起到固溶强化铁素体的作用,考虑到Ni 的价格,降低生产成本,所以就取消不加。
但如果生产EN-GJS-350-22LT材质时,就必须使含Si 量控制在1.9% 以下,同时要加入Ni 元素。
低硅加镍与适度高硅量相比,前一种方式的铸件质量更稳定,低温冲击韧性与抗拉强度的相互关系更协调。
大致配料是(60% -80% 生铁)+ (15%-25% 废钢)+(15% -20% 回炉料),球化剂 1.4%-1.7% ,炉前孕育剂0.6%-0.9% ,瞬时孕育剂0.15%-0.25% ,特别提出加1.0%-1.5%的SiC ,分别加在炉内和包内,一方面SiC与Fe 反应置换出来的单质C 起促进石墨核心质点等作用,另一方面单质C 与铁液中的硅氧化物反应生成CO 等气体上浮,带走内部的炉渣等夹渣物,起净化铁液作用。
在配料计算方面,使用office软件中的excel 程序,结合各类元素的实际吸收率编辑公式计算,快捷准确,为整个配料减少误差,保持产品质量的稳定性。
三.耐低温球铁液的过热处理各种炉料按一定的比例进行熔炼,有一个主要工艺就是过热处理,其目的就是消除炉料的遗传性,关于铁液的遗传性主要表现在①炉料结构信息的保留,如C 原子种类、颗粒粗细以及不均匀性等。
如果废钢,白口铸铁多时,则白口倾向增大,是因为FeC 分子被保留下来作为核心的缘故,同样,如果生铁中含有粗大石墨的生铁,未彻底熔化的C 原子集团会促使粗大石墨的析出,无形中增大了孕育效果的困难,致使石墨数量大大减少,最终影响铸件力学性能②成分遗传效应:炉料中的Pb 、TI 、Sn 、Sb、As等微量元素以及Ni.Cu.Cr.Mo.V…等合金元素会发生各种遗传效应,如强碳化物形成元素促使铸件收缩、裂纹、白口倾向增大,微量表面活性元素会产生特殊形状的石墨,如水草型,蝌蚪型等; 气体元素H、N容易形成气孔等。
③物理特征的保存:如粘度、表面张力、凝固时的白口、收缩、气孔、裂纹倾向等都可能存在遗传。
炉料中的这些金属结构组织及成分信息的遗传因子或载体遗传下来形成弥散质点成为潜在的结晶核心,这些核心与石墨结晶的核心质点有着很大的差异,势必造成石墨形态的变异,降低球化率,减少石墨数量。
过热处理实际操作一般选择1500一1520 ℃,保温时间一般在5min左右,从而使铁液的熔体结构发生明显变化,微观均匀性明显提高。
四.耐低温球铁用球化剂、孕育剂的合理选择目前生产风电铸件使用的球化剂和孕育剂基本特点是高镁、低稀土,用在壁厚60-200mm规格的大吨位铸件的一般是钇基重稀土,而用在壁厚30 -60mm 规格的小吨位铸件的则是轻稀土。
依据大量生产实际反馈的信息, 球化剂的成分中Mg、RE、Ca 的范围应在0.5% 的偏差,Si的范围应在2% 的偏差,同时还应注重Mg 、RE 、Ca等元素与Si 元素比例关系,使Mg、RE 、Ca等元素的氧化物最小,尤其是MgO 要低,实际可以控制MgO/Mg 比值<=0.1 ,还有就是Ba 元素的应用,大量的生产验证,含Ba 的球化剂比不含Ba 的球化剂反应更平稳,抗球化衰退时间更长,更重要的是反应后炉渣更易于扒掉。
球化剂生产企业尽可能使用盖板、组合模具、石墨涂料、SiC涂料等设施,使球化剂自身密度大、致密无疏松、无气孔、无夹渣物等,从而使实际使用中吸收率稳定,长期稳定球化效果。
合金的粒度从各个生产企业的情况来看,大致有5-25mm 、5 -30mm等粒度分布,哪种粒度最合适这与处理包的大小、处理的温度有很大关系,一般小包小粒度,大包大粒度,处理温度高时,粒度应小些,其原则就是粒度的分布使其紧实后堆积密度最大,从而使起爆延缓,较小的粒度在反应过程中上浮的速度相对缓慢,从而提高Mg 元素的吸收率,减少加人量。
合金的形状应是多面体形,最佳是球状,主要使合金难于熔化,破碎工艺是机械式的,各种形状都有,压力成型的椭圆球状、立体圆柱的球化剂就是此目的。
五.耐低温球铁液的处理温度从球化反应角度来讲,处理温度愈低愈好,但针对于重量在8-10t ,壁厚在60 -200mm的叶片轮毂来说,最佳的球化处理温度在1450 -1460 ℃,这样的温度一方面使Mg 元素有最大的吸收率,另一方面使铁液在浇注时有良好的充型能力,一般推荐浇注温度在1340 -1360 ℃之间比较合适,在某生产齿轮箱小风电铸件的企业,因采用消失模造型工艺,考虑到消失模生产的特殊性,采取的球化处理温度在1500 - 1510℃,因而选择的球化剂、孕育剂的成分与粒度也和生产叶片轮毂所选用的有所差异,生产的铸件力学性能中抗拉强度特别高,而延伸率就相对于树脂砂造型低一些、但低温冲击韧性能一直很好并且很稳定。
在实际生产中,依据铸件的壁厚状况、不均匀程度,熔炼设备与造型浇注的距离等等因素,采取最佳的球化处理温度,从而保证优良而稳定的球化率和石墨数量。