液压支架用伸缩式两级液压缸设计
液压支架用伸缩式两级液压缸设计

25国内外煤矿生产支架使用的液压缸已经有了许多种类型,如单缸单作用、单缸双作用、多缸单作用、多缸双作用。
文中主要设计双作用伸缩液压缸。
这种液压缸的优点是调高范围大、属液压无极调高、操作方便灵活,但结构复杂、加工要求高、成本高。
本文基于伸缩式两级液压缸简要地分析了这类液压支架的设计,这一研究对于组合式液压缸的推广具有一定的意义。
1 系统设计分析1.1 液压系统图1是一个典型的液压系统,其构成要素是:动力元件——液压泵或送风装置,其作用是把原动力输入机械能转变为流体压力,使其可以为系统提供能源;执行元件——液压缸或气缸、液压马达或压缩空气发动机,其作用是把流体压力能转化为机械能,输出力和速度或力矩和转速,驱动负载做直线运动或旋转运动;控制元件——压力、流量和方向操控阀,作用是操纵和调整系统的流体压力、流量和流动的方向,以确保执行组件达到所需的输出力(或力矩)、移动速度和运动轨迹;辅助元素,确保系统正常运行所需要的辅助装置,包括管道、管接头、油箱或存储罐、过滤器皿和压力计;工作介质——液压油。
图1 典型的液压系统1.2 双级液压缸设计原理液压缸是将液压能转换为机械能的装置,驱动运行机制做来回式线性(或摆动)运动的液压执动器,根据作用方式分有单、双式,双作用式代表两腔都可以进出压力油,活塞(缸体)可以有正反两个相对方向的运动。
采用的组合液压缸即缸筒是由两个阶段或多个阶段的活塞缸套装而成,也叫做多阶段缸体。
伸出的顺序是:由大到小,推力则从大到小,速度从慢到快;缩回的顺序是:从小到大,速度从快至慢。
双伸缩类型的立柱工作机理如图2所示,立柱上升时高压液柱从A口注入立柱,B口和C口连接回液通道,在立柱1上升的时候,该过程液压支架用伸缩式两级液压缸设计分析朱纯才(阜矿集团机械制造分公司,辽宁 阜新 123000)摘要:双作用伸缩液压缸具有调高范围大、属液压无极调高、操作方便灵活的优点,但结构复杂、加工要求高、成本高。
一种双级伸缩式液压支柱的设计及使用

一种双级伸缩式液压支柱的设计及使用方家耀(浙江衢州煤矿机械总厂股份有限公司,浙江衢州324000)摘要:SDWSG系列单体液压支柱是一种由两组伸缩机构叠加组成的新型高外注式单体液压支柱。
液压行程大、支护范围广,可适合使用的工作面高度范围更大。
关键词:单体液压支柱;伸缩机构;支护中图分类号:TD355+.3文献标志码:BDesign and Application of a Kind of Two-Stage Telescopic High PropFANG Jia-yao(Zhejiang Quzhou Coal Mine MachineryPlant Co.,Ltd.,Quzhou324000,Zhejiang) Abstract:SDWSG series single hydraulic prop is a new type of single hydraulic prop with high external injection, which is composed of two sets of telescoping mechanisms.The hydraulic stroke is large,the support range is wide,and the working face height range suitable foruse is larger.Key words:single hydraulic prop;expansion mechanism;support引言SDWSG系列单体液压支柱(以下简称支柱)是一种由两组伸缩机构叠加组成的新型高外注式单体液压支柱。
其功能、用途和操作方法与普通DW型外注式单体液压支柱基本相同。
其特点是结构新颖、伸缩方式灵活、支护行程和承载能力大、抗弯能力强、支护范围广、工作效率高,可替代多种普通规格的DW型外注式单体液压支柱。
1SDWSG系列单体液压支柱结构特征与工作原理1.1SDWSG系列单体液压支柱结构特征SDWSG系列单体液压支柱,主要由顶盖、三用阀、活柱体、复位弹簧、手把体、油缸、限位钢丝、活塞、Y型密封圈、底座体等零部件组成,其结构见图1O FSW3.15/50型三用阀结构特征见图2。
液压支架试验加载台移动梁升降液压缸同步控制系统
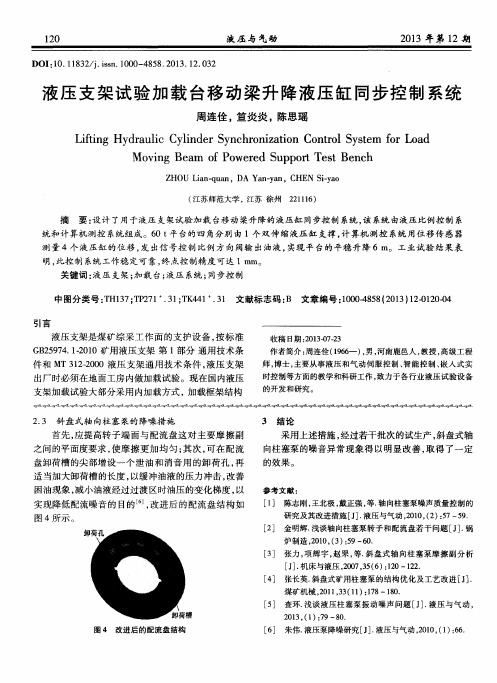
时控制等方 面的教学 和科研工作 , 致力于各 行业液压试 验设 备
的开 发 和研 究 。
3 结 论
首先 , 应 提 高转 子端 面 与配 流 盘 这 对 主要 摩 擦 副 之 间 的平面度 要 求 , 使 摩 擦更 加 均 匀 ; 其次 , 可在 配 流 盘 卸荷 槽 的尖部 增设 一 个 泄 油 和 消音用 的卸 荷 孔 , 再 适 当加大 卸荷 槽 的长度 , 以缓 冲油 液 的压力 冲击 , 改善
根据被试液压支架参数设计的加载台参数如下 :
加 载 台有效 加 载空 间 ( 长 ×宽 ×高 )= 5 5 0 0 mm×
2 6 0 0 mm ×7 5 0 0 mm :
加 载 台移 动梁 重量 : 6 0 t 。
升降油缸 : ① 最大工作压力 : 2 0 M P a ; ② 工作形式 : 双伸缩 ;
2 0 1 3年第 1 2期
液压与 气动
1 技 术参 数
1 2 1
形式如图 1 所示 。主要 由四立柱 、 移 动梁 、 升降油缸 、 插拔销及插拔油缸等组成。根据被试液压支架的试验 高度 , 采用 4个升降油缸 同步运动实现移动梁上下移
动, 调整 加载 台移 动梁 与底 座 之间 的距 离 。
明, 此控制 系统工作稳定可靠 , 终点控制精度可达 1 m m。
关 键词 : 液 压 支架 ; 加载台; 液 压 系统 ; 同步控 制
中图分类 号 : T H1 3 7; T P 2 7 1 . 3 1 ; T K 4 4 1 . 3 1 文献标 志 码 : B 文章编 号 : 1 0 0 0 - 4 8 5 8 ( 2 0 1 3 ) 1 2 - 0 1 2 0 - 0 4
伸缩式两级液压缸设计完成
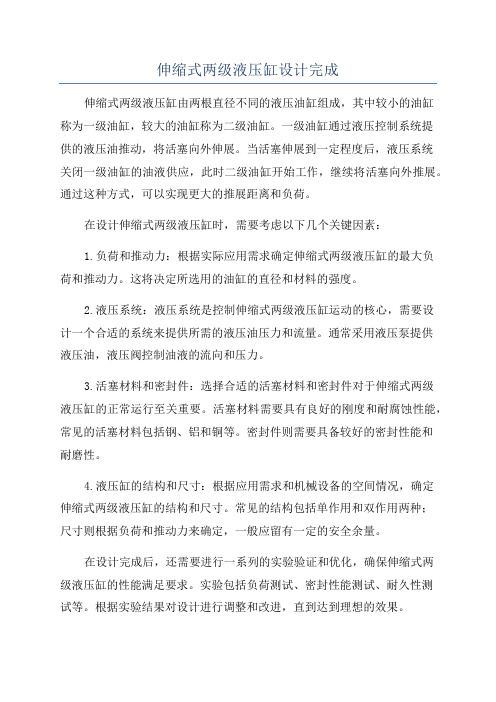
伸缩式两级液压缸设计完成伸缩式两级液压缸由两根直径不同的液压油缸组成,其中较小的油缸称为一级油缸,较大的油缸称为二级油缸。
一级油缸通过液压控制系统提供的液压油推动,将活塞向外伸展。
当活塞伸展到一定程度后,液压系统关闭一级油缸的油液供应,此时二级油缸开始工作,继续将活塞向外推展。
通过这种方式,可以实现更大的推展距离和负荷。
在设计伸缩式两级液压缸时,需要考虑以下几个关键因素:1.负荷和推动力:根据实际应用需求确定伸缩式两级液压缸的最大负荷和推动力。
这将决定所选用的油缸的直径和材料的强度。
2.液压系统:液压系统是控制伸缩式两级液压缸运动的核心,需要设计一个合适的系统来提供所需的液压油压力和流量。
通常采用液压泵提供液压油,液压阀控制油液的流向和压力。
3.活塞材料和密封件:选择合适的活塞材料和密封件对于伸缩式两级液压缸的正常运行至关重要。
活塞材料需要具有良好的刚度和耐腐蚀性能,常见的活塞材料包括钢、铝和铜等。
密封件则需要具备较好的密封性能和耐磨性。
4.液压缸的结构和尺寸:根据应用需求和机械设备的空间情况,确定伸缩式两级液压缸的结构和尺寸。
常见的结构包括单作用和双作用两种;尺寸则根据负荷和推动力来确定,一般应留有一定的安全余量。
在设计完成后,还需要进行一系列的实验验证和优化,确保伸缩式两级液压缸的性能满足要求。
实验包括负荷测试、密封性能测试、耐久性测试等。
根据实验结果对设计进行调整和改进,直到达到理想的效果。
总之,伸缩式两级液压缸的设计是一个复杂的过程,需要综合考虑多个因素。
只有在充分了解实际需求和材料特性的基础上,才能设计出性能稳定、工作可靠的液压缸。
液压支架双伸缩立柱结构及控制形式

液压支架双伸缩立柱结构及控制形式作者:张智勇来源:《中国新技术新产品》2014年第10期摘要:液压支架双伸缩立柱是液压支架承载与实现升降动作的主要液压部件,结构复杂,操作灵活、方便。
文章主要分析了液压支架双伸缩立柱的结构及控制形式,为液压支架设计提供了一种新的设计思路。
仅供参考。
关键词:液压支架;双伸缩立柱;结构分析;性能特点中图分类号:TG315.4 文献标识码:A液压支架双伸缩立柱是将支架顶梁和底座连接起来的主要部件。
它安装在支架上承受一定外部压力,当产生负荷时各级缸筒具有相同的承载力,而这种相同的承载力再由相应的单向阀将两个压力室分隔开的。
从这一方面来说,这就要求双伸缩立柱具有一定的强度和寿命长的特点。
但在具体使用中它的结构比较复杂,加工精度高,这样促使了购买成本高,即便是这样在煤矿生产中也被广泛使用。
1 双伸缩立柱的基本结构笔者将其基本结构分析如下。
它的结构主要有外缸、中缸和活柱两个缸体一个柱体等组合而成。
说起外缸它是有缸底焊接在一起的缸筒组成。
在它的上端装有导向套,可以起到限制和引导的作用,用来对密封元件支撑。
中缸就是与柱塞焊接或旋入一起的缸筒。
在它的上面同样有旋入或集成的导向套,用来对密封元件支撑。
活柱是配有导向环和外置动态活塞密封,在生产中把活柱塞腔和环形腔分隔开。
底阀用于双伸缩立柱,主要是用来控制立柱二级缸与小柱的伸缩。
在升柱时由固定的接口向下腔供液,达到一定程度时中缸体伸出,此时液力推开中缸下部的底阀使小柱逐渐伸出。
而在降柱时,再由另一个接口进入液体,此时中缸降缩至缸底,顶杆将底阀顶开使小柱下降。
2 双伸缩立柱的工作原理双伸缩立柱它是由控制阀组连接到立柱下腔口,来完成初撑力与工作阻力。
并由控制二级缸与活柱的伸缩程序,来加以保证控制两级缸获得相同的恒定工作阻力。
另外,液压支架双伸缩立柱在工作中实现立柱伸出,立柱负载的工作特性。
在工作中,双伸缩立柱通过外缸上的固定接口,压力液被引导至中缸底端,使中缸首先伸出。
液压支架双伸缩立柱导向结构工艺改进
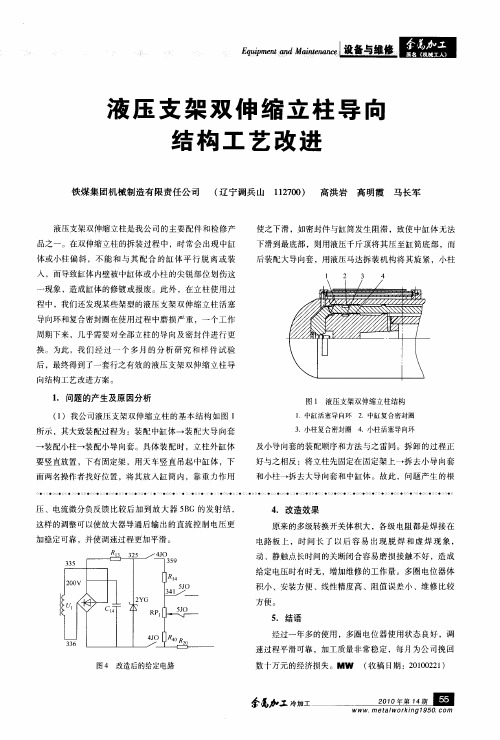
改进后的导向结构可以有效地解决上述拆装过程 中不能
平行压入或抽 出而划伤缸体 内壁这一 问题 ,经过批量生
产 5 台并投 入井下使用 ,在一 个生产周期 后升井 检修 0
时发现 ,活塞导向环和复合密封圈各处磨损正常 ,未出 现上述 图 2中的 一侧严重磨损 ,另一侧磨损较轻 的非 正 常磨损现象 ,改进后的立柱导 向性 能良好 ,本次工艺 改 进宣告成功。MW
经过一年多的使用 ,多圈 电位 器使用状 态 良好 ,调 速过程平滑可靠 ,加工质量非 常稳 定 ,每月为公 司挽 回
图 4 改造后的给定 电路
数十万元的经济损失 。MW
( 收稿 日期 :2 10 2 ) 0 0 2 1
参磊 工 ̄D j - r
WWW et wor i g 7 50 com m a1 k n 9 .
面两名操作者找好位置 ,将其放入缸筒 内 ,靠重力作 用
压 、电流微分负反馈 比较后 加到放 大器 5 G的发射结 , B 这样 的调整可 以使放大器导通后输 出的直 流控制 电压更
加稳定可靠 ,并使调速过程更加平 滑。
4 .改造效果
原来的多级转换 开关体积 大 ,各级电阻都 是焊接在
图 3 经过工艺改进后的双伸缩
立柱导向结构
1 .中缸活塞导向环 2 .中缸复合密封圈
()活 塞导 向环 的磨损 a ()复 合密封 圈 的磨损 b 3 .小柱 复合 密封 圈 4 .小柱活 塞导 向环
图2 活塞导 向环和复合密封圈的磨损现象
3 .效果反及成果总结
改进后的液压支架双伸缩立柱结构如图 3 所示 。
2 .解决方案的制定
综合以上两种原因,我们对双伸缩 立拄的导 向结构
液压支架双伸缩立柱结构的优化设计

液压支架双伸缩立柱结构的优化设计师志亮【摘要】针对液压支架双伸缩立柱结构存在的问题,对缸口结构,缸口的卡键,上腔接头座,缸底与缸配合结构及底阀选型等具体进行了优化分析,提出了具体改进措施,为煤矿安全生产提出了合理化建议,对井下使用与维护都有较好的效果.【期刊名称】《煤矿机电》【年(卷),期】2019(040)003【总页数】3页(P33-35)【关键词】液压支架;双伸缩立柱;缸口;卡键;底阀;上腔接头座【作者】师志亮【作者单位】同煤集团力泰有限责任公司,山西大同037036【正文语种】中文【中图分类】TD355+.90 引言液压支架是现代化综采工作面的主要设备,而双伸缩立柱是液压支架的核心部件,它的性能及可靠性直接影响到液压支架的性能和可靠性,进而影响到综采工作面的安全和生产效率。
近年来,同煤集团使用双伸缩立柱支架的较多,其优点是调高范围大,操作方便灵活,属液压无级调高,但在使用及大修过程中,发现因其部分结构设计不合理,造成使用中故障频发,且修理困难,修复率较低,大修成本居高不下。
经过多次调研、计算、考证,针对双伸缩立柱部分结构的问题,对其进行优化设计。
1 缸口结构问题双伸缩立柱要保证其调高范围大,在升到高处时,其缸口承受的偏载力较单伸缩立柱大许多,故缸口设计的合理性十分重要。
由缸口结构图1中(a)所示,这种结构的双伸缩立柱在井下使用过程中缸口易变形,会导致缸口O形圈漏液,更为严重的是缸口变形后,在修理拆解缸口导向套时,90%的导向套拧不开,即使能拧开,缸口密封面也会严重受伤,造成大量报废,修理成本大大增加。
对缸口结构进行了优化改进设计,如图1(b)所示。
改进措施包括以下几点。
1) 缸口增加了加强箍,增加了缸口抗拉强度,防止塑性变形。
2) 缸口密封部位远离缸口,将原来的密封部位与螺纹连接部位更换位置,这样不但可以使密封部位的缸壁厚一些,而且也使密封部位远离易变形的缸口,优化后的结构可防止因缸口变形而导致漏液,同时为防止缸口螺纹井下锈蚀,缸口端面增加设计一道防潮O形圈。
两级单作用液压缸设计计算书

专业液压缸毕业、生产设计、兼职液压设计 QQ34682Q3468285 85
△d= d1P 试*[(d22+ d12)/(d22- d1 2)]/E =8.32*10-5 (m)
经查密封圈样本,该变形量在密封圈间隙允许范围内。
其中
E ——套筒材料的弹性模量,MPa,钢材 E=2.06*105MPa
其中
P 试 —— 液压缸的试验压力,MPa,P 试=1.25P=20MPa
p — 材料的许用强度,MPa, p= b/n=600/3=200MPa n ——安全系数,取 3
b ——材料的强度极限,45 钢, b=600MPa 液压缸壁厚验算:对最终采用的缸筒壁厚应进行四方面的验算
a.额定压力应低于一定的极限值,以保证工作安全 额定压力 PN≤0.35σ(s d22-d12)/d12=0.35*355*(0.12-0.092)=29MPa
足 达 到 负 载 要 求 , 则 柱 塞 直 径 d1 ≥ √[4F/ ( π Pᶯ ) ]=√[4*80000/ (3.14*16*0.9)]=84mm 内孔尺寸依标准 GB/T2348-1993 圆整为 90mm
其中
ᶯ --- 液压缸工作效率,取 0.9
2.液压缸缸筒壁厚计算,套筒材料选 45 钢,壁厚暂定为 δ=5mm。
其中 F 推 ——液压缸 20MPa 最大推力,190000N d4 ——连接螺纹中径,mm d4= d5 -2*3/8H=96.7mm d5 ——螺纹大径,98mm H ——连接螺纹牙高,H=√3/2P=1.732mm
P ——连接螺纹螺距,2mm
L ——连接螺纹有效长度,17mm
专业液压缸毕业、生产设计、兼职液压设计 QQ34682 8585
- 1、下载文档前请自行甄别文档内容的完整性,平台不提供额外的编辑、内容补充、找答案等附加服务。
- 2、"仅部分预览"的文档,不可在线预览部分如存在完整性等问题,可反馈申请退款(可完整预览的文档不适用该条件!)。
- 3、如文档侵犯您的权益,请联系客服反馈,我们会尽快为您处理(人工客服工作时间:9:00-18:30)。
第1章绪论1.1课题背景介休倡源煤炭有限责任公司是凯嘉能源集团有限责任公司属下企业。
公司前身为介休市连福镇镇办煤矿,2005年8月,由义棠煤业整体并购,2006年4月,省煤整办批准介休倡源煤炭有限责任公司整合金山坡煤矿和西兴煤矿, 2007年12月, 义棠煤业、投资、介休义民投资三方签署合作协议,共同投资建设介休倡源煤炭有限责任公司。
公司注册资本为1.6亿元,现有资产总额8亿多元,员工1600多名,其中:中专以上学历员工450多名,初级以上职称员工90多名。
公司位于介休市连福镇,朝南相望是生态原始、风景独特的天峻山,西距介休市20km,北距大运高速、108国道及南同浦铁路干线义安站20km,东与介沁公路相邻, 地理位置优越,交通便利。
公司井田面积4.62km2,可采煤层6层,可采储量32702kt,设计能力为90万吨/年。
公司实行董事会领导下的总经理负责制,股东会、董事会、监事会、党总支、工会组织齐全,有14个职能部门以及综采、普采等9个生产基层队。
倡导文明,源远流长。
公司秉承“以德为魂,诚信为本”的企业精神,近年来,在生产经营、企业管理、员工队伍、企业文化、环境建设、后勤保障等方面都发生了巨大的变化,使一个名不见经传的小煤矿改造成为年产90万吨原煤的新型煤炭企业,使一个生态恶化的旧矿井改造成为环境优美的绿色生态矿井。
公司被介休市人民政府授予“优秀管理先进单位”等荣誉称号。
在凯嘉集团的统领下,公司将以“高水平规划、高标准建设、高质量管理”为指导思想,致力于基础建设和未来发展,全体员工将以百折不挠的精神和敢为人先的勇气,高起点、高标准,努力把公司打造成为管理科学、装备先进、安全文明、集约高效的标准化煤炭企业。
1.2液压支架简述20世纪50年代前在国外煤矿生产中基本上采用木支架,木顶梁或金属摩擦支柱和铰接顶梁来支护顶板。
1954年英国首先研制出液压支架,通过对液压支架的逐步完善改进,进而普遍推广使用使采煤工作面采煤过程中的落煤,装煤,运煤和支护等工序全部实现了机械化。
到20世纪90年代初,寻找到适合矿区资源条件的先进采煤方法,采用了放顶煤技术。
随着计算机技术和自动化技术的普及应用与提高为煤矿生产自动化和提高生产提供了新的出路。
支架上使用的液压缸也发展延伸了许多种类型,轻载,重载。
单缸单作用,单缸双作用,多缸单作用,多缸双作用。
这里主要设计双作用伸缩液压缸。
优点:调高围大,属液压无极调高,操作方便灵活,但结构复杂,加工要求高,成本高。
本型立柱主要用于薄煤层和大采高支架上。
缺点:由于本型某些缸径立柱的中缸强度裕度偏小,遇有采煤工作面基本顶压力显现强烈时中缸有时会出现鼓胀现象,损坏立柱。
支架技术特征参数:型号:ZY5000/17/35型掩护式液压支架高度:(最低~最高)1.7~3.5m宽度:(最小~最大)1.43~1.6m中心距:1.5m初撑力:(P=31.5MPa)3877 KN工作阻力:4000 KN对底板前端比压:0.64~2.5 MPa支护强度:0.80~0.87 MPa移架步距:700mm泵站压力:31.5MPa操作方式:邻架控制1.3液压支架立柱特点液压支架上的立柱实际上是推力液压缸的一种,其特点如下:①:立柱是支架实现支撑和承载的主要部件,他直接影响支架的工作性能。
因此,立柱除应具有合理的工作阻力和可靠的工作特性外,还必须由足够的抗压和抗弯强度,密封性好,结构简单并能适合支架的工作需要。
②立柱一般由活塞,活塞杆,缸体三部分组成。
由于支架工作时,立柱承载大,而降柱力较小,故活塞杆直径均较大,常采用空心结构,以保证足够的刚度活塞一般用Y型密封圈,铜环导向,缸体底部焊接。
缸体与缸盖之间用钢丝,螺纹或卡环连接。
为了防止外部煤层等脏物进入缸体,在导向套上要装防尘圈。
对于单伸缩立柱,为了扩大支架的支护高度围,可采用机械加长杆,如图1.1图1.1带有机械加长杆的双作用伸缩式立柱1—缸头,2—油口,3—前端盖,4—缸体,5—活塞,6—活塞杆,7—后端盖图1.2双伸缩式立柱1—后端盖,2,3,4,5,6,7—卡箍,卡键,鼓型密封圈,导向环,8—下活柱,9活塞,10—缸筒,11,12,13,14—导向环,导向衬套,蕾型密封圈,防尘圈,15柱头,16底阀③立柱的头部结构均为球形,与顶梁或底座之间的连接采用销轴或压块固定,以使立柱在工作时由一定的适应性。
④立柱的供液方式由供液和外供液两种方式。
除双伸缩立柱采用供液方式外,单伸缩立柱多为外供液,这种方式结构简单加工维修方便。
双伸缩式立柱工作原理图:图1.3双伸缩立柱原理图:A,B,C:液口1一级缸体,2一级活塞,3底阀,4二级活塞,5活塞杆1.4双伸缩式立柱结构及工作原理如图1.3所示,升柱时高压液体从液口A进入立柱,液口B 和C连通回液管路,升柱过程分为两个阶段,首先下活柱伸出只有下活柱完全伸出后,柱单向阀才能开启使上活柱伸出,降柱时,高压液体从B和C同时进入,液口A连通回液管路。
降柱过程也分为两步完成。
第一步是下活柱缩回缸体此时上活柱由于柱单向阀处于闭锁状态,所以不会下缩,当下活柱完全缩回后,单向阀阀芯顶杆与缸体凸台相碰而使单向阀开启,上活柱下腔可以回液,故上活柱缩回。
承载时,顶板对上活柱的作用力将由上活柱下腔被闭锁的液体承受并传递给下活柱,这时上下活柱所承受的压力是相等的。
所以这种立柱也称等负载双伸缩立柱。
当下活柱的液体达到安全阀的调定压力时,安全阀开启,下活柱缩回,当下活柱完全缩入缸体中,只有上活柱承载时,顶板的作用力使上活柱缩回。
1.5.双伸缩式立柱运行及负载特点:这种立柱由于下活柱先伸先缩,上活柱后伸后缩。
在煤层变化不大时,上活柱的伸出长度是不变的。
因此上活柱相当于立柱的液压加长杆。
由于上活柱的长度可以自由调节,比单伸缩立柱调节机械加长杆方便的多,所以目前应用的越来越多,它的缺点是价格较高。
由于等负载双伸缩立柱上,下活柱活塞面积不等,所以在相同的泵站压力下,上活柱伸出撑紧顶板的初撑力小于下活柱伸出撑紧顶板的初撑力。
因此,在煤层厚度变化较大时,上活柱的伸出长度有时也要变化,造成初撑力太小,不利于板顶维护。
另外,在承载时,由于负载相同,上活柱下腔的压力会大于下活柱下腔的压力,如果压力太大,会造成下活柱形成的缸体在高压下膨胀变形,影响下活柱的正常升降,甚至导致导向套和立柱咬死。
所以,在煤层厚度变化较大时或冲击地压大的煤层,使用这种等负载双伸缩立柱要给以注意。
第二章双伸缩立柱结构设计计算2.1 原始数据:一级缸行程1000mm,二级缸700mm,工作压力:31.5Mpa 工作阻力P=4000KN 2.2 设计要求:容:设计说明书,装配图,主要零件图2。
建模,整体装配。
要求:根据原始数据设计进行液压支架双伸缩式立柱的结构设计,进行各零件的三维建模与立柱的整体装配及运动仿真。
双伸缩式立柱是一种推力液压缸。
液压缸是液压系统中的执行元件,是液压系统中的核心部件,不同类型的液压缸组成零部件也不同,但其大致由缸体、活塞、活塞杆、缸底、缓冲装置、排气装置、支承座以及导向、密封、防尘装置等组成。
根据设计的液压缸的使用要求不同可选择设计各零部件。
2.3工况分析并确定液压缸参数2.3.1支架的承载过程支架的承载过程是指支架与顶板之间相互力学作用的过程,包括初撑,承载增阻和恒阻三个阶段。
如图2.1(一)初撑阶段图2.1 双伸缩式立柱工作曲线图在升架过程中,当支架的顶板接触顶梁,直到立柱下腔的液体压力逐渐上升到泵站工作压力时,停止供液,液控单向阀立即关闭,这一阶段称为支架的初撑阶段,此时支架对顶板的支撑力为初撑力支撑式支架的初撑力为:式中 D —支架立柱的缸径,mPb —泵站的工作压力,MPan---支架立柱的数量。
由上式可知,支架初撑力的大小取决于泵站的工作压力,立柱的缸径和立柱的数量,合理的初撑力是防止直接顶过早的因下沉而离层,减缓顶板下沉速度,增加其稳定性和保证安全生产的关键。
一般采用提高泵站工作压力的方法来提高初撑力,以免缸径过大。
(二)承载增阻阶段支架初撑结后,随着顶板的下沉,立柱下腔的液体压力逐渐升高,支架对顶板的支撑力也随之增大,呈现增阻状态,这一过程为支架的承载增阻阶段。
32104⨯=n p D p b c π(三) 恒阻阶段随着顶板压力的进一步增加,立柱下腔的液体压力越来越高,当升高到安全阀的调定压力时,安全阀打开溢流,立柱下降,液体压力随之降低。
当降到安全阀的调定压力时,安全阀关闭。
随着顶板的继续下沉,安全阀重复这一过程,又由于安全阀的作用,支架的支撑力维护在某一恒定数值上,这是支架的恒阻阶段,此时,支架对顶板的支撑力称为工作阻力,它是由支架安全阀的调定压力决定的,支撑式支架的工作阻力为式中 Pa —支架安全阀的调定压力,MPa其它意义同前。
2.3.2.立柱负载分析及确定工作阻力为P=4000KN.立柱(液压缸)负载主要包括:初撑力、摩擦阻力、惯性阻力、重力、密封阻力和背压阻力等。
(1):初撑力的大小是相对于工作阻力而言,并与顶板的性质有关。
较大的初撑力可以使支架较快达到工作阻力,防止顶板3104a p p n π=⨯过早的离层,增加顶板的稳定性。
对于不稳定和中等稳定顶板,为了维护机道上方的顶板,应取较高的初撑力,约为工作阻力的80%;对于稳定顶板,初撑力不宜过大,一般不低于工作阻力的60%,对于周期来压强烈的顶板,为了避免大面积垮落对工作面的动载威胁,应取较高的初撑力。
本设计选支撑掩护式支架,综合考虑取其初撑力为工作阻力的60%。
所以,初定初撑力Pc=4000×60%=2400 KN(2)摩擦阻力:由于液压缸的摩擦阻力相对于初撑力很小,故可忽略不计。
(3)惯性阻力、重力:液压缸垂直布置,但其较重的一级缸及缸头安装在支架底座上面,且其工作时运动量很小,不属于快速往复运动型,故惯性阻力、重力可不以考虑。
(4)密封阻力和背压阻力:将密封阻力考虑在液压缸的机械效率中去,取液压缸的机械效率为0.9背压阻力是液压缸回油路上的阻力,初算时可不考虑,其数值在系统确定后才能定下来。
依据上面分析可得液压缸工作曲线图,图2.1曲线上的t0,t1,t2,分别表示支架的初撑增阻和恒阻阶段的时间。
2.3.3 初步确定液压缸参数表2.1液压缸径系列:表2.2活塞杆直径系列:表2.3液压缸外径系列(GB/T2348-1993):(1)二级缸的径和壁厚根据受力知道,只要满足二级缸受力,则一级缸定能满足,于是由: 32104⨯=n p D p b c π式中 D —— 支架立柱的缸径,mPb ——泵站的工作压力,MPaN —— 支架立柱的数量。
Pc —— 撑力得: 23410PcD Pbn π=⨯=4×2400/(3.14×31.5×4×1000)D=155.7mm根据表2.1缸筒径系列(GB /T2348-93),选二级缸径2D =160mm壁厚的计算:max max /{2.3[]3}p P D P δσ≥-式中 δ—— 壁厚max P ——最高允许压力。