打磨工艺规范修订稿
打磨工通用工艺规范

打磨工通用工艺规范打磨工通用工艺规范标准化管理部编码-[99968T-6889628-J68568-1689N]T—0908—23打磨工通用工艺规范编制/日期:审核/日期:批准/日期:打磨工通用工艺规范1适用范围本守则规定了宜工集团结构厂打磨工艺要求。
本守则适用于宜工集团结构厂下料打磨清渣,焊接件打磨工艺2术语2.1打磨:通过使用手提工具操作除去工件表层材料从而使工件获得所需要的形状或表面粗糙度2.2打磨修整:将焊缝局部不规则处打磨消除2.3全部打磨:从一侧(或两侧)打磨整个焊缝表面但不改变整个焊缝形状2.4磨平:从一侧(或两侧)打磨整个焊缝,使其厚度同周围表面相同3打磨设备3.1角向磨光机,直磨机3.2砂轮磨片钹型砂轮型号:125X6X22.2(MM)百叶蝶不锈钢碗刷4操作规程4.1操作前准备工作4.2操作规范°,循序渐进(A→B),不得用力过猛而导致表面凹陷。
5打磨工艺规范5.1打磨参数5.2 Array焊前打磨5.2.1打磨范围:全部焊缝两侧各25-50mm。
5.2.2操作方法:打磨长大焊缝时用安装了不锈钢碗刷的角磨机或者直柄打磨机沿焊缝方向进行打磨;对于需要激光跟踪自动焊的焊缝只能用直柄打磨机进行打磨;在相对焊接附件较大的工件表面焊接附件时使用百叶蝶对焊接表面进行打磨。
5.2.3技术要求:打磨出金属光泽、保证焊接区域没有氧化膜、打磨纹路与焊缝方向平行且均匀、打磨深度不超过0.2mm。
5.3焊缝余高的打磨5.3.2操作方法:角磨机工作时要与被打磨面平行,使焊缝余高被去除;当焊缝有凹陷时以不伤母材为标准,严禁用百叶蝶端部斜铲被打磨面。
5.4去除表面划伤5.4.1打磨范围:取矩形框,覆盖划伤区域。
5.4.2操作方法:使用打磨工具沿一定的方向打磨,不超过矩形框。
5.4.3技术要求:被打磨表面要求平滑;不伤母材,以母材的被去除量不超过0.2mm为标准;被打磨部分表面纹路要求一致,大部件及车体沿车体纵向、小件沿焊缝方向;严禁无规律打磨。
车间打磨规范标准最新
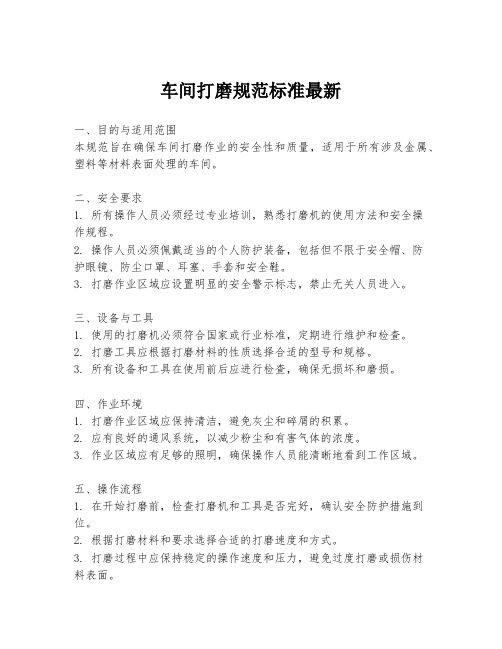
车间打磨规范标准最新一、目的与适用范围本规范旨在确保车间打磨作业的安全性和质量,适用于所有涉及金属、塑料等材料表面处理的车间。
二、安全要求1. 所有操作人员必须经过专业培训,熟悉打磨机的使用方法和安全操作规程。
2. 操作人员必须佩戴适当的个人防护装备,包括但不限于安全帽、防护眼镜、防尘口罩、耳塞、手套和安全鞋。
3. 打磨作业区域应设置明显的安全警示标志,禁止无关人员进入。
三、设备与工具1. 使用的打磨机必须符合国家或行业标准,定期进行维护和检查。
2. 打磨工具应根据打磨材料的性质选择合适的型号和规格。
3. 所有设备和工具在使用前后应进行检查,确保无损坏和磨损。
四、作业环境1. 打磨作业区域应保持清洁,避免灰尘和碎屑的积累。
2. 应有良好的通风系统,以减少粉尘和有害气体的浓度。
3. 作业区域应有足够的照明,确保操作人员能清晰地看到工作区域。
五、操作流程1. 在开始打磨前,检查打磨机和工具是否完好,确认安全防护措施到位。
2. 根据打磨材料和要求选择合适的打磨速度和方式。
3. 打磨过程中应保持稳定的操作速度和压力,避免过度打磨或损伤材料表面。
4. 打磨完成后,及时清理打磨区域,确保无残留的碎屑和粉尘。
六、质量控制1. 打磨后的表面应达到规定的平整度、光洁度和尺寸精度。
2. 对打磨后的工件进行质量检验,确保符合设计和工艺要求。
3. 记录每次打磨作业的参数和结果,以便进行质量追踪和分析。
七、事故处理与预防1. 发生事故时,立即停止作业,按照应急预案进行处理。
2. 对事故原因进行调查,采取有效措施防止类似事故的再次发生。
3. 定期对作业人员进行安全教育和技能培训,提高安全意识和操作技能。
八、规范的更新与维护本规范应根据技术进步、工艺改进和实际操作经验进行定期的更新和维护。
九、结束语车间打磨作业是生产过程中的重要环节,严格遵守本规范标准,不仅能够保证作业的安全性,还能提高产品质量和生产效率。
希望通过本规范的实施,进一步提升车间打磨作业的整体水平。
产品打磨工艺规范

4、打磨需要注意的几点
• ①安全 • 安全防护设施:眼镜、口罩 • 角磨机防护罩 • 电源 • 严禁带手套 • 围裙
• ②打磨方法 • 打磨顶盖周边毛刺及长条边毛刺时,用福友牌 A120#磨片; • 打磨表面压痕、凹凸时用A100#磨片; • 打磨底盘毛剌用A60#或A80#磨片; • 喷涂返修件打磨可先用A100#磨片磨平后,再用 天虎牌木砂纸AA-180#抛光; • 外观表面打磨以15°~30°倾斜角度为宜,打磨 移动速度、力度要均匀,以磨印无粗糙手感,表 面光滑为准(一般目视无弧形水波状磨痕为合 格)。
钣金产品打磨工艺规范
主讲:
1、哪些产品需要打磨?
• ①所有喷涂件(仅限对外观要求较严格的) 如:前面板、顶盖、右围板 • ②焊接以后有较大毛刺的 如:底盘(材质较厚的(1.5mm以上的)
2、打磨所需工具
• ①角磨机 • ②平磨机
3、打磨片的选择
• 福友牌A120#、A100#、A80#、A60# • 天虎牌木砂纸AA-180#
5、常见打磨质量问题
• • • • ①凹凸不平 ②过渡打磨 ③磨痕太深 ④变形
END!
谢谢大家!
打磨工艺规范与要求(2024版)

可编辑修改精选全文完整版打磨工艺规范与要求1. 焊前打磨打磨范围:全部焊缝两侧20~50mm操作方法:打磨焊缝时用安装了不锈钢刷的直柄打磨机沿焊缝方向进行打磨;多层焊接时,每焊完一层需打磨去除不规则的焊缝、飞溅、氧化层,保证焊接平滑过渡技术要求:打磨出金属光泽,保证焊接区域无氧化膜,打磨纹路与焊缝方向平行且均匀、打磨深度不超过母材厚度的5%为标准。
2. 焊缝余高的打磨打磨范围:焊缝两侧各20-50mm的区域。
操作方法:角磨机工作时要与被打磨面平行,使焊缝余高被去除;当焊缝有凹陷时以不伤母材为标准,严禁用千叶片端部斜铲被打磨面、不得用力过猛而导致表面凹陷。
技术要求:被打磨表面要求平滑;不伤母材,以母材的被去除量不超过5%为标准;被打磨部分表面纹路要求一致,沿焊缝方向,严禁无规律打磨。
3 去除表面划伤打磨范围:划伤区域操作方法:使用打磨工具沿一定的方向打磨技术要求:被打磨表面要求平滑;不伤母材,以母材的被去除量不超过5%为标准;被打磨部分表面纹路要求一致,严禁无规律打磨。
4. 去除焊接飞溅打磨范围:焊缝两侧各40-50mm,超过此范围的飞溅参照表面划伤打磨方法进行打磨操作方法:使用打磨工具沿焊缝方向打磨技术要求:打磨出金属光泽、保证焊接区域没有飞溅物;打磨纹路与焊缝方向平行;打磨深度不超过母材厚度的5%为标准。
5. 焊缝接头的打磨打磨范围:对焊缝接头及段焊起弧点收弧点使用直磨机进行打磨操作方法:使用安装了合金旋转锉的直磨机对焊缝接头及段焊起弧点、收狐点进行打磨技术要求:焊缝接头的打磨要求外形与焊缝余高一致;段狐起弧点收狐点的打磨要求在去除焊接缺陷的情况下表面没有尖锐的棱角;不伤母材,以母材的被去除量不超过母材厚度的5%为标准。
6. 焊缝磨平打磨范围:焊缝及焊缝两侧各15~25mm。
操作方法:先用角磨机和千叶片沿焊缝方向进行打磨,千叶片与工作面保持5~15°夹角,循序渐进,使焊缝磨平,母材的被去除量不超过0.2mm为标准;当焊缝有凹陷时应补焊后再打磨,不得用力过猛导致表面凹陷。
打磨工艺规范
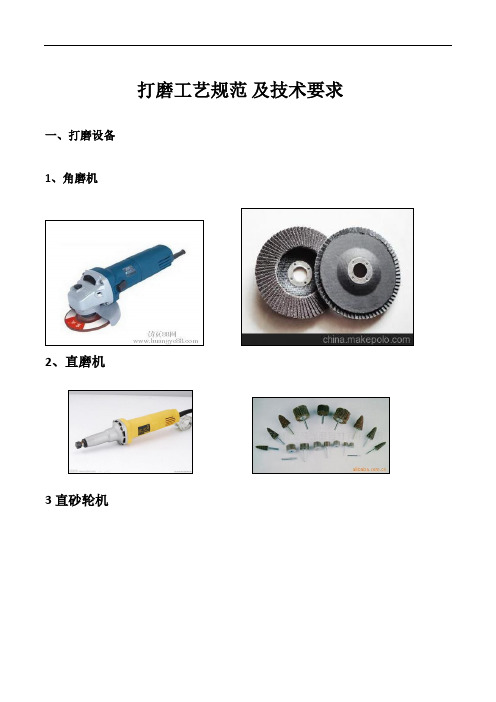
打磨工艺规范及技术要求一、打磨设备1、角磨机2、直磨机3直砂轮机4拉丝机二操作规程1、打磨前准备:1、1工作前应检查砂轮有无损坏,防护装置就是否完好;试机,并进行调整,确保砂轮无抖动现象.1、2戴好口罩与护目镜,穿好工作防护服。
1、3 打磨前必须确保工件表面无其她杂物,发现有表面缺陷等应先补焊后再打磨。
1、4 进行首件打磨,检查就是否符合打磨要求,并经质检或主管确认无误,方可开始批量作业.2、操作规范2、1 安装砂轮时,必须核对砂轮允许得最高转速就是否与主轴转速相适应。
2、2 需打磨得产品应放置平稳,小件需加以固定,以免在打磨过程中产品位导致加工缺陷。
2、3 正确使用打磨工具,及时检查与更换磨损严重得砂轮磨片。
2、4 打磨时应紧握打磨工具,砂轮片与工作面保持一定合理得角度循序渐进不得用力过猛而表面凹陷.2、5在打磨过程中发现产品表面有气孔,夹渣,裂纹等现象时应及时通知金工车间进行补焊。
2、6 打磨结束后需进行自检,打磨区域应无明显得磨纹与凹陷,周边无焊接飞溅物,符合产品设计与工艺要求.产品应归类存放,堆放整齐有序.三打磨工艺规范及技术要求1、焊前打磨1、1打磨范围:全部焊缝两侧1、2操作方法:打磨焊缝时用安装了不锈钢刷得直柄打磨机沿焊缝方向进行打磨;多层焊接时,每焊完一层需打磨去除不规则得焊缝飞溅、氧化层,保证焊接平滑过渡1、3技术要求:打磨出金属光泽,保证焊接区域无氧化膜,打磨纹路与焊缝方向平行且均匀、打磨深度不超过母材厚度得5%为标准。
2、焊缝余高得打磨2、1打磨范围:焊缝两侧2、2操作方法:角磨机工作时要与被打磨面平行,使焊缝余高被去除;当焊缝有凹陷时以不伤母材为标准,严禁用千叶片端部斜铲被打磨面、不得用力过猛而导致表面凹陷。
2、3技术要求:被打磨表面要求平滑;不伤母材,以母材得被去除量不超过5%为标准;被打磨部分表面纹路要求一致,沿焊缝方向,严禁无规律打磨.3去除表面划伤3、1打磨范围:划伤区域3、2操作方法:使用打磨工具沿一定得方向打磨3、3技术要求:被打磨表面要求平滑;不伤母材,以母材得被去除量不超过5%为标准;被打磨部度得5%为标准。
工艺规范修订计划

工艺规范修订计划一、引言工艺规范是指为了保证产品质量和生产效率,对生产过程中所涉及的工艺、设备、材料等进行规范和要求的文件。
随着科技的不断发展和工艺技术的更新迭代,现有的工艺规范需要进行修订以适应新的生产要求和技术水平。
本文将就工艺规范修订计划进行详细论述。
二、修订目的为提升生产效率、降低产品缺陷率,并满足市场需求,制定工艺规范修订计划的主要目的如下:1. 更新技术要求:根据科技进步和市场需求,修订老旧工艺规范,加入最新的技术要求,确保产品具备较高的竞争力。
2. 优化流程设计:通过修订规范,优化生产流程,减少不必要的工序和环节,提高生产效率和产品质量。
3. 强化安全措施:修订规范时,加强对生产过程中安全隐患的考虑,确保生产过程安全可靠。
4. 规范操作要求:修订规范时,明确操作人员的职责和操作要求,避免人为因素导致的生产问题。
三、修订内容经过调研和分析,我们计划对以下几个方面的内容进行修订:1. 工序的调整:根据新的技术要求和生产实际,对已有的工序进行调整和优化,提高生产效率和产品质量。
2. 设备更新要求:对老旧设备进行评估,根据现有技术水平,制定设备更新要求,确保设备的正常运行和生产效率。
3. 材料要求的更新:根据市场上新出现的材料,修订材料使用规范,确保产品的性能和可靠性。
4. 安全措施加强:在修订规范时,加入更严格的安全要求,确保生产过程中的安全性。
四、修订流程1. 制定修订计划:根据修订目的和内容,制定详细的修订计划,明确修订的时间节点和责任人。
2. 调研与收集信息:对新的技术要求和市场需求进行调研,收集各方面的信息,为修订提供依据。
3. 修订草案起草:根据调研结果和收集到的信息,起草修订草案,确保修订的具体内容和要求明确清晰。
4. 内部评审:组织内部相关人员对修订草案进行评审,提出修改意见和建议,完善修订草案。
5. 外部专家评审:邀请行业内相关专家对修订草案进行评审,提供专业意见,确保修订的准确性和实用性。
打磨工艺规范

打磨工艺规范一、打磨设备1.角磨机2.直磨机二、操作规程1. 打磨前准备:1.1工作前应检查砂轮有无损坏,防护装置是否完好;试机,并进行调整,确保砂轮无抖动现象。
1.2 戴好口罩和护目镜,穿好工作防护服。
1.3 打磨前必须确保工件表面无其他杂物,发现有表面缺陷等应先补焊后再打磨。
1.4 进行首件打磨,检查是否符合打磨要求,并经质检或主管确认无误,方可开始批量作业。
2.操作规范2.1 安装砂轮时,必须核对砂轮允许的最高转速是否与主轴转速相适应。
2.2 需打磨的产品应放置平稳,小件需加以固定,以免在打磨过程中产品位移而导致加工缺陷。
2.3 正确使用打磨工具,及时检查和更换磨损严重的砂轮磨片。
2.4 打磨时应紧握打磨工具,砂轮片与工作面保持5-15°,循序渐进(A→B),不得用力过猛而导致表面凹陷。
2.5 在打磨过程中发现产品表面有气孔,夹渣,裂纹等现象时应及时通知电焊工补焊。
?2.6 打磨结束后需进行自检,打磨区域应无明显的磨纹和凹陷,周边无焊接飞溅物,符合产品设计和工艺要求。
产品应归类存放,堆放整齐有序。
三、打磨工艺规范及技术要求1. 焊前打磨打磨范围:全部焊缝两侧20~50mm操作方法:打磨焊缝时用安装了不锈钢刷的直柄打磨机沿焊缝方向进行打磨;多层焊接时,每焊完一层需打磨去除不规则的焊缝、飞溅、氧化层,保证焊接平滑过渡技术要求:打磨出金属光泽,保证焊接区域无氧化膜,打磨纹路与焊缝方向平行且均匀、打磨深度不超过母材厚度的5%为标准。
2. 焊缝余高的打磨打磨范围:焊缝两侧各20-50mm的区域。
操作方法:角磨机工作时要与被打磨面平行,使焊缝余高被去除;当焊缝有凹陷时以不伤母材为标准,严禁用千叶片端部斜铲被打磨面、不得用力过猛而导致表面凹陷。
技术要求:被打磨表面要求平滑;不伤母材,以母材的被去除量不超过5%为标准;被打磨部分表面纹路要求一致,沿焊缝方向,严禁无规律打磨。
3 去除表面划伤打磨范围:划伤区域操作方法:使用打磨工具沿一定的方向打磨技术要求:被打磨表面要求平滑;不伤母材,以母材的被去除量不超过5%为标准;被打磨部分表面纹路要求一致,严禁无规律打磨。
工艺规范修订方案

工艺规范修订方案一、背景介绍工艺规范作为一种标准文件,用于指导和规范企业的生产过程,保证产品质量和安全。
然而,由于市场需求、技术进步等因素的变化,已有的工艺规范可能存在适应性差、不完善等问题。
因此,有必要对现有的工艺规范进行修订,以适应新的发展需求。
二、修订目的本次工艺规范的修订旨在:1. 提高工艺流程的效率和质量,以适应市场需求的变化;2. 更新工艺规范中的技术指标,使其符合最新的行业标准和法规要求;3. 强化工艺操作的安全性,减少事故和意外事件的发生。
三、修订内容1. 修订工艺流程:根据市场需求和技术发展的要求,对现有的工艺流程进行调整和优化,以提高生产效率和产品质量。
2. 更新技术指标:结合最新的行业标准和法规要求,对工艺规范中的技术指标进行更新和修改,确保其与国家标准和法规保持一致。
3. 安全防护要求:针对工艺操作中可能存在的安全风险,增加相应的安全防护要求,以减少事故和意外事件的发生。
四、修订流程1. 召开修订会议:邀请相关技术人员、生产人员和管理人员参加修订会议,明确修订的目标和范围。
2. 收集意见和建议:通过线上调查、专家咨询等方式,收集各方的意见和建议,形成修订初稿。
3. 专家评审:邀请相关领域的专家对修订初稿进行评审,提出修改意见和建议,形成修订终稿。
4. 内部审批:将修订终稿提交给企业内部审批机构,经过审查和批准后形成正式的工艺规范修订方案。
5. 公示和实施:对修订方案进行公示,并组织培训和指导,确保全体员工熟悉和理解修订后的工艺规范。
五、修订后的效益1. 提高生产效率:通过修订工艺流程和更新技术指标,可以提高生产线的效率,减少生产时间和成本。
2. 提升产品质量:通过更新技术指标和加强质量控制要求,可以提升产品质量,增加市场竞争力。
3. 加强安全管理:通过增加安全防护要求和规范操作流程,可以减少事故和意外事件的发生,保障员工的人身安全。
六、总结本次工艺规范修订方案旨在提高生产效率、提升产品质量和加强安全管理。
- 1、下载文档前请自行甄别文档内容的完整性,平台不提供额外的编辑、内容补充、找答案等附加服务。
- 2、"仅部分预览"的文档,不可在线预览部分如存在完整性等问题,可反馈申请退款(可完整预览的文档不适用该条件!)。
- 3、如文档侵犯您的权益,请联系客服反馈,我们会尽快为您处理(人工客服工作时间:9:00-18:30)。
打磨工艺规范
WEIHUA system office room 【WEIHUA 16H-WEIHUA WEIHUA8Q8-
打磨工艺规范
一、打磨设备
1.角磨机
2.直磨机
二、操作规程
1. 打磨前准备:
工作前应检查砂轮有无损坏,防护装置是否完好;试机,并进行调整,确保砂轮无抖动现象。
戴好口罩和护目镜,穿好工作防护服。
打磨前必须确保工件表面无其他杂物,发现有表面缺陷等应先补焊后再打磨。
进行首件打磨,检查是否符合打磨要求,并经质检或主管确认无误,方可开始批量作业。
2.操作规范
安装砂轮时,必须核对砂轮允许的最高转速是否与主轴转速相适应。
需打磨的产品应放置平稳,小件需加以固定,以免在打磨过程中产品位移而导致加工缺陷。
正确使用打磨工具,及时检查和更换磨损严重的砂轮磨片。
打磨时应紧握打磨工具,砂轮片与工作面保持5-15°,循序渐进(A→B),不得用力过
猛而导致表面凹陷。
在打磨过程中发现产品表面有气孔,夹渣,裂纹等现象时应及时通知电焊工补焊。
打磨结束后需进行自检,打磨区域应无明显的磨纹和凹陷,周边无焊接飞溅物,符合产品设计和工艺要求。
产品应归类存放,堆放整齐有序。
三、打磨工艺规范及技术要求
1. 焊前打磨
打磨范围:全部焊缝两侧20~50mm
操作方法:打磨焊缝时用安装了不锈钢刷的直柄打磨机沿焊缝方向进行打磨;多层焊接时,每
焊完一层需打磨去除不规则的焊缝、飞溅、氧化层,保证焊接平滑过渡
技术要求:打磨出金属光泽,保证焊接区域无氧化膜,打磨纹路与焊缝方向平行且均匀、打磨
深度不超过母材厚度的5%为标准。
2. 焊缝余高的打磨
打磨范围:焊缝两侧各20-50mm的区域。
操作方法:角磨机工作时要与被打磨面平行,使焊缝余高被去除;当焊缝有凹陷时以不伤母材
为标准,严禁用千叶片端部斜铲被打磨面、不得用力过猛而导致表面凹陷。
技术要求:被打磨表面要求平滑;不伤母材,以母材的被去除量不超过5%为标准;被打磨部分表面纹路要求一致,沿焊缝方向,严禁无规律打磨。
3 去除表面划伤
打磨范围:划伤区域
操作方法:使用打磨工具沿一定的方向打磨
技术要求:被打磨表面要求平滑;不伤母材,以母材的被去除量不超过5%为标准;被打磨部分表面纹路要求一致,严禁无规律打磨。
4. 去除焊接飞溅
打磨范围:焊缝两侧各40-50mm,超过此范围的飞溅参照表面划伤打磨方法进行打磨
操作方法:使用打磨工具沿焊缝方向打磨
技术要求:打磨出金属光泽、保证焊接区域没有飞溅物;打磨纹路与焊缝方向平行;打磨深度
不超过母材厚度的5%为标准。
5. 焊缝接头的打磨
打磨范围:对焊缝接头及段焊起弧点收弧点使用直磨机进行打磨
操作方法:使用安装了合金旋转锉的直磨机对焊缝接头及段焊起弧点、收狐点进行打磨
技术要求:焊缝接头的打磨要求外形与焊缝余高一致;段狐起弧点收狐点的打磨要求在去除焊
接缺陷的情况下表面没有尖锐的棱角;不伤母材,以母材的被去除量不超过母材厚
度的5%为标准。
6. 焊缝磨平
打磨范围:焊缝及焊缝两侧各15~25mm。
操作方法:先用角磨机和千叶片沿焊缝方向进行打磨,千叶片与工作面保持5~15°夹角,循序渐进,使焊缝磨平,母材的被去除量不超过为标准;当焊缝有凹陷时应
补焊后再打磨,不得用力过猛导致表面凹陷。
技术要求:焊缝高度与母材在同一水平面上,被打磨表面要求平滑(或平滑过渡)不伤母材,
母材的被去除量不超过母材厚度5%为标准。
四、打磨质量
1.在打磨过程中发现质量缺陷(气孔,夹渣,裂纹等现象)应停止作业并通知相关人员处理,
严禁凭经验私自处理
2. 打磨后整体应无毛刺、凹坑和焊接不良处
3. 打磨后整体尺寸应符合产品尺寸要求,表面应无明显打磨不均匀现象。
编制:审核:批准:。