车床切削振刀原因与改善对策
如何解决加工中车床振动震刀问题
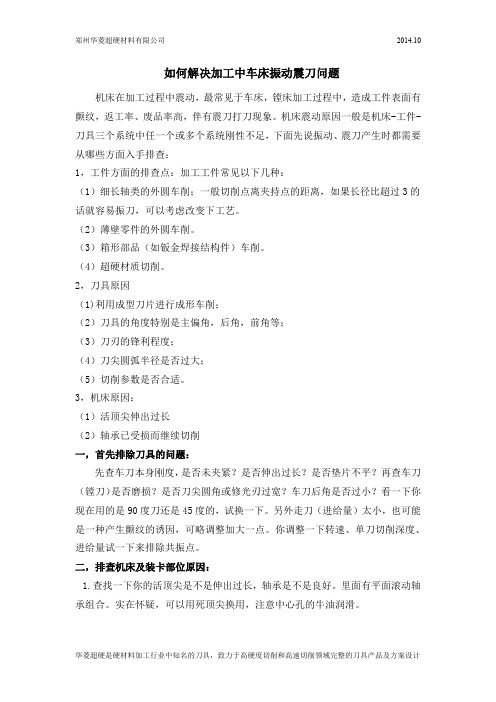
如何解决加工中车床振动震刀问题机床在加工过程中震动,最常见于车床,镗床加工过程中,造成工件表面有颤纹,返工率、废品率高,伴有震刀打刀现象。
机床震动原因一般是机床-工件-刀具三个系统中任一个或多个系统刚性不足,下面先说振动、震刀产生时都需要从哪些方面入手排查:1,工件方面的排查点:加工工件常见以下几种:(1)细长轴类的外圆车削;一般切削点离夹持点的距离,如果长径比超过3的话就容易振刀,可以考虑改变下工艺。
(2)薄壁零件的外圆车削。
(3)箱形部品(如钣金焊接结构件)车削。
(4)超硬材质切削。
2,刀具原因(1)利用成型刀片进行成形车削;(2)刀具的角度特别是主偏角,后角,前角等;(3)刀刃的锋利程度;(4)刀尖圆弧半径是否过大;(5)切削参数是否合适。
3,机床原因:(1)活顶尖伸出过长(2)轴承已受损而继续切削一,首先排除刀具的问题:先查车刀本身刚度,是否未夹紧?是否伸出过长?是否垫片不平?再查车刀(镗刀)是否磨损?是否刀尖圆角或修光刃过宽?车刀后角是否过小?看一下你现在用的是90度刀还是45度的,试换一下。
另外走刀(进给量)太小,也可能是一种产生颤纹的诱因,可略调整加大一点。
你调整一下转速、单刀切削深度、进给量试一下来排除共振点。
二,排查机床及装卡部位原因:1.查找一下你的活顶尖是不是伸出过长,轴承是不是良好。
里面有平面滚动轴承组合。
实在怀疑,可以用死顶尖换用,注意中心孔的牛油润滑。
2.查找一下你尾架顶夹紧情况,夹紧条件下是不是左右里、上下里与机床主轴不同心。
3.把大中小拖板都紧一些,尤其是中拖板。
4.如果是机床的尾架部分你暂时无法去检查,(第1、2点,需要一些钳工基础),可以试着从卡抓端向尾部走刀。
反车,可以最大程度削除尾端的不给力。
5.如果第4步还有情况,要看一下主轴了,当然,如是三抓,也要查一下,是不是螺旋槽有损坏。
四抓是人工自支调的,就不需检查了。
如果你的主轴瓦已经真的紧到位了,工件也不是薄壁空心件或悬伸过长,卡盘夹紧也没问题。
槽刀振刀解决方案(3篇)

第1篇一、引言槽刀振刀是数控机床加工过程中常见的一种加工缺陷,严重影响加工精度和表面质量。
本文针对槽刀振刀问题,分析了其产生的原因,并提出了一系列解决方案,旨在提高加工效率和产品质量。
二、槽刀振刀产生的原因1. 机床方面(1)机床刚性不足:机床主轴、立柱、工作台等部件刚性不足,容易产生振动。
(2)机床精度不高:机床导轨、轴承、齿轮等部件精度不高,导致加工过程中出现振动。
(3)机床装配不当:机床装配过程中,各部件间隙过大或过小,影响机床的整体刚性。
2. 加工参数方面(1)切削速度过高:切削速度过高,刀具与工件之间的摩擦力增大,容易产生振动。
(2)进给量过大:进给量过大,刀具与工件之间的切削力增大,导致振动加剧。
(3)切削深度过大:切削深度过大,刀具与工件之间的切削力增大,容易产生振动。
3. 刀具方面(1)刀具刃口磨损:刀具刃口磨损,切削力增大,容易产生振动。
(2)刀具刚性不足:刀具刚性不足,容易在切削过程中产生振动。
(3)刀具安装不当:刀具安装不当,导致刀具与机床主轴之间的间隙过大或过小,影响切削稳定性。
4. 工件方面(1)工件材料硬度不均匀:工件材料硬度不均匀,导致切削力不均匀,容易产生振动。
(2)工件表面质量差:工件表面质量差,如存在毛刺、划痕等,影响切削稳定性。
(3)工件尺寸不稳定:工件尺寸不稳定,导致加工过程中切削力不均匀,容易产生振动。
三、槽刀振刀解决方案1. 机床方面(1)提高机床刚性:选用高刚性的机床,提高机床主轴、立柱、工作台等部件的刚性。
(2)提高机床精度:选用高精度的机床,确保机床导轨、轴承、齿轮等部件的精度。
(3)优化机床装配:合理调整机床各部件间隙,提高机床整体刚性。
2. 加工参数方面(1)合理选择切削速度:根据工件材料、刀具和机床性能,选择合适的切削速度。
(2)合理选择进给量:根据工件材料、刀具和机床性能,选择合适的进给量。
(3)合理选择切削深度:根据工件材料、刀具和机床性能,选择合适的切削深度。
切削振动产生原因和解决

细长杆立铣刀铣削深型腔时 常采用插铣方法
插铣就是刀具象钻头一样轴向 进刀,当铣削深的型腔时,通 常长杆的悬伸大于3倍的刀杆 直径,我们推荐使用轴向进刀 的插铣方法,但是立铣刀刀片 刃口有一定的径向切削刃,刀 具供应商有技术资料证明此刀 具在插铣时的最大吃刀宽度 PlungeMill是专门用于模具和 航空工业的大直径插铣刀,它 最大的特点是高效率和超大切 宽,通常用于大型深腔模具的 开粗。
切削振动的原因
刀具在切削工件时发生振动需要有下面三 个条件同时存在: 第一是包括刀具在内的工艺系统刚性不足 导致其固有频率低, 第二是切削产生了一个足够大的外激力, 第三是这个外激力的频率与工艺系统的固 有频率相同随即产生共振
分清自激振动和强迫振动
。
刀具振动实际应该叫“切削振动,通常发生在长悬臂刀杆的镗削和铣削,薄 壁件的切削加工,细长杆的车削等等。当环保做为车间考核的标准时,高速 钻削产生的高频啸叫也和振动噪音一起列为技术公害。 切削振动顾名思义只有在刀具进行切削时才产生,如果振动来自非切削因素 如不稳定的机床地基,机床丝杠的间隙,主轴轴承的损坏甚至几百米以外火 车的经过而产生的震动我们叫做强迫振动,这种振动不伴随噪音而非我们讨 论的话题。 切削振动产生噪音,但噪音并不是全由切削振动引起发生,机夹刀片铣刀在 100米以上的切削速度每齿走刀在0.1毫米以上铣削3毫米的切深,即便是铣削 灰口铸铁也会产生接近90分贝的噪音,而低频切削振动噪音常低于此值。 切削振动是自激振动是一种正弦波振动,除了用专业仪器测量振频与波长外 ,最明显的是工件被加工表面有振纹。
薄壁工件的铣削加工
薄壁工件铣削发生振动的原因完全来自于工件,这种工件被叫做箱式或者 碗式零件(box like or bowl like shape workpiece),由于振动来自于工件本身 ,那么技术人员各显神通,国外在处理这类零件的铣削加工主要以改善工 件夹持为主,例如增加合适的辅助支撑点,在夹具和机床工作台面之间加 装一层木板,用粗大的橡皮条或者弹簧勒在壳体的外面,在箱体内部充满 湿沙子等等,奇思妙想不一而足。在铣削薄腹板时,推荐使用90度面铣刀 以减小对腹板的轴向切削力。
降低颤振几率、提高切削稳定性的措施

在金属切削加工领域,细长杆件的车削、薄壁件的切削加工或采用长悬臂刀杆进行镗削和铣削等场合,切削振动是一种破坏正常切削过程的极其有害的现象,是影响工件表面质量和加工精度的首要因素。
如何最大限度的降低刀具切削振动?一、消除数控刀具切削振动的基本途径分析数控刀具切削振动模型可知,刀具在切削工件时发生自激振动依赖两个基本条件:①工艺系统刚性不足导致其固有频率低;②刀具相对于工件切入、切出的动态切削过程产生足够大的激振力,并且激振力的频率与工艺系统的固有频率相同或非常接近。
因此,从数控刀具的选择和使用角度考虑,消除切削振动的基本途径是抑制激振力和提高刀具抗振性。
二、抑制激振力消除数控刀具切削振动合理选择切削用量和刀具几何角度都是抑制激振力的有效途径。
对于数控机床普遍采用的机夹刀具而言,在刀具选择和切削用量选择过程中应注意以下几个方面:1、尽量选用切削刃锋利的刀片以减小切削力数控机床所采用的机夹刀片材料主要有非涂层硬质合金、涂层硬质合金、金属陶瓷、陶瓷、立方氮化硼和人造金刚石等 6 大类。
由于金刚石类刀具不适合加工黑色金属,陶瓷和立方氮化硼刀片刃口通常都有负倒棱,金属陶瓷韧性差不适用于振动切削场合,而化学涂层刀片不及物理涂层刀片刃口锋利,涂层硬质合金刀片不及非涂层硬质合金刀片锋利,所以出于减小切削力考虑,应尽量选用非涂层或物理涂层的钴基硬质合金刀片。
另外,刀片的前角和后角大小也影响着切削刃的锋利程度。
具有正前角和大后角的刀片在镗削或铣削中的切削楔入角最小,切削必然轻快,不易产生振动。
2、注重车镗刀具的主偏角、副偏角和刀尖圆弧半径的选择对于外圆车削或内孔镗削,选择主偏角Kr = 90°的刀具产生的径向切削力最小,轴向切削力最大,有利于消除切削振动。
同时,为了避免刀具副切削刃与工件已加工表面摩擦而产生颤动,车镗刀具的副偏角应尽量选择较大的。
另外,根据经验,无论是镗削还是铣削,在相同的背吃刀量a p下,刀尖圆弧半径R 越大,细长刀杆发生切削振动的倾向就越大。
数控机床加工过程中的振刀原因分析及处理措施

数控机床加工过程中的振刀原因分析及处理措施摘要:数控机床是近年来工业生产中普遍使用的先进设备之一,可以提高加工的精度、效率和质量。
在数控机床的加工过程中,振刀是一个常见的问题,会对加工效果和机床寿命产生负面影响。
因此,解决振刀问题是数控机床加工过程中不可缺少的一环。
针对不同的问题原因,需要采取相应的解决方法。
除了要从技术层面上优化设备和加工流程,更需要提高员工的技术素养和操作能力,以便更有效地避免和解决振刀问题,确保数控机床的正常运行和稳定性,最终达到优化工业生产的目标。
关键词:机床加工;振刀;原因分析;处理措施数控机床振刀问题是在机床加工过程中常见的一种故障,其主要体现为刀具在加工过程中出现强烈的振动和噪声,严重时可能会导致零件加工质量不合格、刀具的损坏和机床的报废等问题。
因此,对于数控机床的振刀问题,需要进行深入分析,并采取相应的处理措施进行解决。
解决数控机床振刀问题,提高机床加工精度和效率,同时减少机床维修成本和损失。
一、数控机床加工过程中的振刀的主要原因(一)切削力不稳定当切削力过大或不平稳时,会导致刀具产生振动。
这可能是由于加工条件设置不当或刀具选择不当引起的。
(二)振刀刀具损伤刀具损伤或磨损不均会导致刀具振动,影响加工质量和刀具寿命。
应及时更换刀具并检查刀具安装情况,确保刀具正确安装。
(三)工件长不稳定工件太长或不稳定时,会引起切削过程的振动,影响加工精度和表面质量。
应考虑加工过程中的支撑和夹紧方式,并选择适当的刀具和切削参数。
(四)加工用液过少加工过程中液体的作用是冷却切屑和切削部位、减轻刀具和工件的摩擦,从而减少切屑的堆积和刀具的磨损。
如果液体不足或缺乏冷却润滑,会增加切削力并导致工件和刀具的振动[1]。
(五)机床本身问题如果机床存在运动不平稳、主轴轴承损坏或变形等问题,也会引起刀具振动。
应及时检修机床并保证机床安全性和可靠性。
二、数控机床加工过程中的振刀的处理措施在实际应用中,需要结合具体加工情况和原因进行分析,采取合适的处理措施。
切削振动的产生及解决

90的主偏角铣刀比如CoroMill390刀体,配 以轻快的切削刃口刀片和正前角槽型的刀 片,切削力最为轻快。
内孔镗削时刀片刃形角越小越好
55 °
80°
这样副主偏角很大,副刃口与被加工面的颤动接触区小,颤动很难变 成振动,副切削刃挤屑的机会也小,例如在镗削内孔时,镗刀的主偏 角假设为93度,使用CCMT的刀片其副主偏角为7度,使用DCMT的 刀片副主偏角为32度,切削要轻快的多。但是刃形角小的刀片安全 性差。
细长杆立铣刀铣削深型腔时 常采用插铣方法
插铣就是刀具象钻头一样轴向 进刀,当铣削深的型腔时,通 常长杆的悬伸大于3倍的刀杆 直径,我们推荐使用轴向进刀 的插铣方法,但是立铣刀刀片 刃口有一定的径向切削刃,刀 具供应商有技术资料证明此刀 具在插铣时的最大吃刀宽度 PlungeMill是专门用于模具和 航空工业的大直径插铣刀,它 最大的特点是高效率和超大切 宽,通常用于大型深腔模具的 开粗。
调整切削参数的方法
调整切削参数只对切
削振动不严重的刀具 可能有效,一般的调 整方法如下:降低刀 具或者工件的回转速 度,减小切深并提高 刀具每转或者铣刀每 齿走刀量。在内螺纹 的车削中若产生振动 ,可将完成螺纹车削 的进刀步骤减少1至2 刀。。
合理安排走刀的工艺路线
合理安排走刀的工艺路线对于铣削加工 非常重要。铣削有顺铣和逆铣之分,传 统的铣削理论将逆铣有利于减少铣削振 动,其实是指有利于抑制丝杠的间隙产 生的振动。如今的铣削设备大都安装了 滚珠甚至滚柱丝杠,所以逆铣消振的意 义不大。无论是顺铣还是逆铣只要铣削 力的方向与工件的夹持方向一致就有利 于消除弯板类零件的振动如图
类似鱼鳞
类似鱼鳞但是之间的波纹很 大又平缓
车削加工出现振刀打刀的原因分析及解决办法

车床在加工过程中的振动,伴有振刀打刀现象,造成工件表面有颤纹,返工率、废品率高。
我们需要从哪些方面入手排查呢?1. 工件与刀具方面(1)工件方面1)细长轴类的外圆车削。
一般切削点离夹持点的距离,如果长径比超过3的话就容易振刀,可以考虑改变下工艺;2)薄壁零件的外圆车削;3)箱形部品(如钣金焊接结构件)车削;4)超硬材质切削。
(2)刀具原因1)利用成型刀片进行成形车削;2)刀具的角度特别是主偏角,后角,前角等;3)刀刃的锋利程度;4)刀尖圆弧半径是否过大;5)切削参数是否合适。
首先排除刀具的问题,先查车刀本身刚度,是否未夹紧?是否伸出过长?是否垫片不平?再查车刀(镗刀)是否磨损?是否刀尖圆角或修光刃过宽?车刀后角是否过小?看一下你现在用的是90度刀还是45度的,试换一下。
另外,走刀(进给量)太小,也可能是一种产生颤纹的诱因,可略调整加大一点。
你调整一下转速、单刀切削深度、进给量试一下来排除共振点。
2. 排查机床及装卡部位原因1)查找一下你的活顶尖是不是伸出过长,轴承是不是良好。
里面有平面滚动轴承组合。
实在怀疑,可以用死顶尖换用,注意中心孔的牛油润滑;2)查找一下你尾架顶夹紧情况,夹紧条件下是不是左右里、上下里与机床主轴不同心;3)把大中小拖板都紧一些,尤其是中拖板;4)如果是机床的尾架部分你暂时无法去检查(第1、2点,需要一些钳工基础),可以试着从卡抓端向尾部走刀。
反车,可以最大程度削除尾端的不给力;5)如果第4步还有情况,要看一下主轴了,当然,如是三抓,也要查一下,是不是螺旋槽有损坏。
四抓是人工自支调的,就不需检查了。
3. 采用其他一些抑制振刀的对策如果你的主轴瓦已经真的紧到位了,工件也不是薄壁空心件或悬伸过长,卡盘夹紧也没问题。
采用其他一些抑制振刀的对策。
目前应用于加工现场中有一些比较具体而实用的方法:1)减轻造成振动的部份的工作重量,惯性越小越好;2)针对振动最大的地方予以固定或夹持,如中心架、工作保持器等;3)提高加工系统的刚性,例如使用弹性系数较高的刀柄或使用加入动态减振器的特殊抗震力,以吸收冲击能量;4)从刀片与工作旋转方向下功夫;5)改变刀具的外型与进角,刀具鼻端半径越小越好,以降低切削阻力。
数控机床切削时振动的消减方法探讨
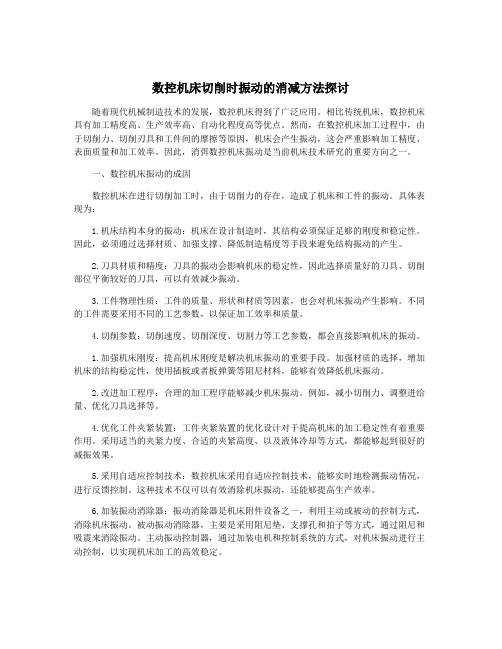
数控机床切削时振动的消减方法探讨随着现代机械制造技术的发展,数控机床得到了广泛应用。
相比传统机床,数控机床具有加工精度高、生产效率高、自动化程度高等优点。
然而,在数控机床加工过程中,由于切削力、切削刃具和工件间的摩擦等原因,机床会产生振动,这会严重影响加工精度、表面质量和加工效率。
因此,消弭数控机床振动是当前机床技术研究的重要方向之一。
一、数控机床振动的成因数控机床在进行切削加工时,由于切削力的存在,造成了机床和工件的振动。
具体表现为:1.机床结构本身的振动:机床在设计制造时,其结构必须保证足够的刚度和稳定性。
因此,必须通过选择材质、加强支撑、降低制造精度等手段来避免结构振动的产生。
2.刀具材质和精度:刀具的振动会影响机床的稳定性,因此选择质量好的刀具、切削部位平衡较好的刀具,可以有效减少振动。
3.工件物理性质:工件的质量、形状和材质等因素,也会对机床振动产生影响。
不同的工件需要采用不同的工艺参数,以保证加工效率和质量。
4.切削参数:切削速度、切削深度、切割力等工艺参数,都会直接影响机床的振动。
1.加强机床刚度:提高机床刚度是解决机床振动的重要手段。
加强材质的选择,增加机床的结构稳定性,使用插板或者板弹簧等阻尼材料,能够有效降低机床振动。
2.改进加工程序:合理的加工程序能够减少机床振动。
例如,减小切削力、调整进给量、优化刀具选择等。
4.优化工件夹紧装置:工件夹紧装置的优化设计对于提高机床的加工稳定性有着重要作用。
采用适当的夹紧力度、合适的夹紧高度、以及液体冷却等方式,都能够起到很好的减振效果。
5.采用自适应控制技术:数控机床采用自适应控制技术,能够实时地检测振动情况,进行反馈控制。
这种技术不仅可以有效消除机床振动,还能够提高生产效率。
6.加装振动消除器:振动消除器是机床附件设备之一,利用主动或被动的控制方式,消除机床振动。
被动振动消除器,主要是采用阻尼垫、支撑孔和拍子等方式,通过阻尼和吸震来消除振动。
- 1、下载文档前请自行甄别文档内容的完整性,平台不提供额外的编辑、内容补充、找答案等附加服务。
- 2、"仅部分预览"的文档,不可在线预览部分如存在完整性等问题,可反馈申请退款(可完整预览的文档不适用该条件!)。
- 3、如文档侵犯您的权益,请联系客服反馈,我们会尽快为您处理(人工客服工作时间:9:00-18:30)。
车床切削振刀原因与改善对策
一般使用车床进行机械加工时,会发生所谓的“振刀”的场合约有以下几种场合:
(一)利用成型刀片进行成形车削。
(二)细长圆杆的外圆车削。
(三)薄肉圆杆的外圆车削。
(四)箱形部品(如钣金焊接结构件)车削。
(五)超硬材质切削。
(六)轴承已受损而继续切削等。
当振刀发生时,刀具、工件与车床的振动往往导致工厂内部有刺耳的噪音,而其振幅大小单边达数十微米(μm)以上,有时其至高达100微米以上亦所在多闻。
这种振刀不仅造成刀具或工件的夹持变松之外,同时也因其吵闹的噪音对操作人员造成不良的身心影响,而加工精度也因此无法达成客户的要求,因此各工具机厂莫不战战兢兢地将振刀问题之排除视为草大的挑战。
本文简要的描述“振刀”的分类与挑除的方法,并且以一个实际的案例说明振刀的问题排除与防治之道。
透过仪器的实测,将原来的振动藉由局部的修改设计而达到高达十倍以上的改善成果。
一、基本方法
有关工具机的颤振(Chattering)学理分析在工具机研究上属於相当艰深的
一门学问,其产生来源与加工材质、机械设计及切削条件有着相当的关联[2,3],一般以上图来解释整个切削系统,其中“切削过程”牵涉到材质(工件)的硬度、进给的大小等等,而“机器结构”部份则牵涉到工具机各单体结构强度设计,诸如主轴轴承、头部本体,刀盘设计以及刀具夹持等特性。
由於学理有着一大堆数学方程式[4],在此不对此部份做深入的介绍,仅将一般客户常发生的振刀现象,概分成以下两类:
(一)强制振动(Forced Vibration)
这是在断续切削而导致的强制振动或者是因转动零件有瑕玼而造成的振动,一般常见常见的如轴承的损坏而造成的异音或齿轮啮合不佳以及工件夹持不佳、主轴摆幅过大等现象皆属此类。
这类问题中,断续车削属於加工技术问题,而
零件瑕玼即大部份来自於工具机的装配技术及其关键零组件的品质控制,而且也与机台结构设计理念有关。
其特徵为振动的特性与转数的大小有直接的关联。
(二)自激振动(Self-excited Uibration)
这是因为切削加工时具有周期性的工作凹凸不平特性造成周期相位的少许
错开而又反覆重叠的再生效果所产生的影响一般又可称之为“共振”(Resonance),其主因来自於工具机结构的自然频率受到激发或者是工件夹持系统的自频率过
低而受到激发所引起。
由於结构的自然频率只随夹持或固定方式的改变而改变,因此振刀发生时,改变切削条件(如改变转速)往往石以改善切削振动,然而在某些无法改变切削速度的场合(如攻牙或某些材质的切削),往往只有借助於夹持方式的变更,甚至於改变刀具或刀具固定方式才能解决这类问题。
二、抑制振刀的对策
依据研究所得的振刀原理,目前应用於加工现场中有一些比较具体而实用的方法:
(一)尽量选择切削阻抗较小的一切条件,亦即最适当的刀具进给速率与切削速度(或主轴转速)。
(二)调整切削速度以避开共振。
(三)减轻造成振动的部份的工作重量,惯性越小越好。
(四)针对振动最大的地方予以固定或夹持,如中心架、工作保持器等。
(五)提高加工系统的刚性,例如使用弹性系数较高的刀柄或使用加入动态减振器(Dynamic Damper)的特殊抗震力,以吸收冲击能量。
(六)从刀片与工作旋转方向下功夫(工作将刀具下压同时也增高刀具的稳定性)。
(七)改变刀具的外型与进角,例如:鼻端半径(Nose Radius)越小越好,以降低切削阻力。
侧倾角(Sick Rake Angle) 必须取正值,以使切削方向更近垂直。
後倾角(Back Rake Augle) 最好为正值,惟甚去屑切屑能力相对变差,因此一般可选用槽刑刀以使倾角变为负值,但仍保有正值的切削效果。
(八)导角(Lead Augle)越小越好,最好为零。