均值极差控制图讲解学习
SPC培训(均值--极差控制图)

管制图的类型
• 6 管制图的选择方法 • 7 计量型数据管制图
•
• • • • •
a 与过程有关的控制图 b 使用控制图的准备 c X-R 图 d X- s 图 e ˜X- R图 f X-MR图
• 8 计数型数据管制图 • a p图
2004-8-28 教育訓練 培訓教材 3
b c d
np 图 c图 u图
172 173 175 176 174 174 4
备注
176 175 174 173 170 174 6
171 173 173 174 175 173 4
175 174 175 173 172 174 3
173 172 170 171 172 172 3
169 171 173 174 175 172 6
170 169 171 172 173 171 4
175 173 170 169 171 172 6
175 176 174 172 170 173 6
175 173 171 169 170 172 6
174 175 175 174 173 174 2
应记录人员、材料、环境、方法、机器或测量系统的任何变化,当控制图上出现信号时,这些记录将有助于采取纠正措
日期/时间 备注 日期/时间
2004-8-28
教育訓練 培訓教材
12
1-3、计算每个子组的均值(X)和极差 、计算每个子组的均值( )和极差R 对每个子组计算: 对每个子组计算: X=(X1+X2+…+Xn)/ n R=Xmax-Xmin 式中: 为子组内的每个测量值。 式中: X1 , X2 • • • •为子组内的每个测量值。n 表示子组 为子组内的每个测量值 的样本容量 1-4、选择控制图的刻度 、 4-1 两个控制图的纵坐标分别用于 X 和 R 的测量值。 4-2 刻度选择 :
均值极差控制图

Page 25
技术部培训教材
综反合激运式用开关电源变压器设计(1)
作均值控制图。
控制图中,有2个点超出下控制限,所以,可以得出结 论,生产过程并没有得到很有效的控制。但控制限内的 点分布比较正常。
Page 26
技术部培训教材
综反合激运式用开关电源变压器设计(1)
极差控制图:
分析不合格的原因,发现主要是由变压器输出电压不 稳定造成的,需制定措施加以改进。
控反制激图式开关电源变压器设计(1)
准则2:连续9点落在中心线同一侧。主要原因为过程平均值 变化。
Page 18
技术部培训教材
控反制激图式开关电源变压器设计(1)
准则3:连续6点递增或递减。产生趋势的原因可能是工具 逐渐磨损、维修逐渐变坏等,从而使得参数随着时间而 变化。
Page 19
技术部培训教材
第一步,取预备数据,依测定的先后顺序排列,通常数据 分成约20—25组,每组4—5个数据。
第二步,计算各组样本的平均数(X)i 与极差(R)
Xi Xi1 Xi2 ... Xim m
Page 9
Ri max{X1 j}-min {X1 j}
技术部培训教材
Ri max控{X1反j}制-mi激n图{X1式j} 开关电源变压器设计(1)
控反制激图式开关电源变压器设计(1)
准则4:连续14点相邻点上下交替。数据分层不够。如,两 名操作人员轮流进行操作;轮流使用两台设备。
Page 20
技术部培训教材
控反制激图式开关电源变压器设计(1)
准则5:连续3点有两点落在中心线同一侧的B区以外。过程 参数μ发生了变化。
Page 21
技术部培训教材
均值极差图(x-r图)分析
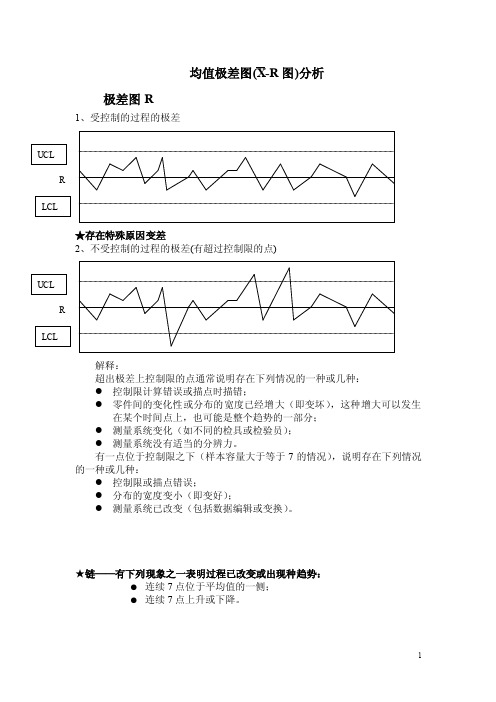
均值极差图(X-R 图)分析极差图R1、受控制的过程的极差★存在特殊原因变差2、不受控制的过程的极差(有超过控制限的点) 解释:超出极差上控制限的点通常说明存在下列情况的一种或几种: ● 控制限计算错误或描点时描错;● 零件间的变化性或分布的宽度已经增大(即变坏),这种增大可以发生在某个时间点上,也可能是整个趋势的一部分; ● 测量系统变化(如不同的检具或检验员); ● 测量系统没有适当的分辨力。
有一点位于控制限之下(样本容量大于等于7的情况),说明存在下列情况的一种或几种:● 控制限或描点错误;● 分布的宽度变小(即变好);● 测量系统已改变(包括数据编辑或变换)。
★链——有下列现象之一表明过程已改变或出现种趋势:● 连续7点位于平均值的一侧; ● 连续7点上升或下降。
(存在高于和低于极差均值的两种链)4、不受控制的过程的极差(存在长的上升链)解释:高于平均极差的链或上升链说明存在下列情况的一种或全部:●输出值的分布宽度增加,其原因可能是无规律的(如设备工作异常或固定松动)或是由于过程中的某个要素变化(如材料变化),是常见问题,需纠正;● 测量系统变化(如不同的检具或检验员);低于平均极差的链或下降链说明存在下列情况的一种或全部:● 输出值的分布宽度减小,这常常是一个好状态,应研究以便推广应用和改进过程;●测量系统改变,这会掩盖过程的真实性的变化。
★其它明显的非随机的图形 5、不受控制的过程的极差 (点离极差均值太近)(点离控制限太近)解释:各点与极差均值R 的距离:一般地,大约2/3的描点应落在控制限的中间1/3的区域内,1/3的描点应落在其外的2/3的区域内。
a )如果显著多于2/3以上的描点落在离极差均值R 很近之处(超过90%的点落在控制限1/3的区域内),说明存在下列情况的一种或全部: ● 控制限计算错误或描点时描错;● 过程或取样方法被分层;每个子组系统化包含了从两个或多个具有完全不同的过程均值的过程流的测量值(如用几根测量轴每一轴测一个数); ● 数据已经过编辑。
均值极差控制图讲解学习

5
控制图
控制图的类型
按控制图的用途分类: 分析用控制图 控制用控制图
根据质量数据的类型可分为: 计量值控制图 计数值控制图
需根据所控制质量指标的情况和数据性质分别加以选择。 例如下表:
6
控制图
数据类型 计量型
计数型
控制图名称 均值-极差控制图
均值-标准差控制图 中位数-极差控制图 单值-移动极差控制图 不合格品率控制图 不合格品数控制图
28
综合运用 至此,电加热管和线路板问题得到改善。需对QC小组活
动进行总结,将成果进行标准化,使QC小组活动的效果 得到维持。
运用质量工具开展QC小组活动,对当前存在的问题进行 分析、改善。
29
7控制图数据类型控制图名称简记计量型均值极差控制图均值标准差控制图中位数极差控制图单值移动极差控制图计数型不合格品率控制图p控制图不合格品数控制图np控制图缺陷数控制图c控制图单位缺陷数控制图u控制图xr控制图xs控制图r控制图xrs控制图8控制图?均值极差控制图
控制图
所有的产品和服务都是过程的结果。统计过程控制就是根 据产品质量的统计观点,运用数理统计方法对生产制造过 程和服务过程的数据加以收集、整理和分析,从而了解、 预防和监控过程的运行状态和水平。这是一种以预防为主 的质量控制方法。
9
R im{a1 X j} xm - {i1 X jn }
控制图
手表厂为了提高手表的质量,应用排列图分析造成手表 不合格的各种原因,发现“停摆”占第一位。为了解决停 摆问题,再次应用排列图分析造成停摆的原因。结果发现 主要是由于螺栓松动引发的螺栓脱落造成的,为解决问题, 应用控制图对装配作业中的螺栓扭矩进行过程控制。
平均值和极差控制图

xT /2 x 3
x
x 3 xT /2
TU UCL CL LCL
TL
样本顺序号
2.2平均值与极差控制图
极差R: 样本中最大值与 最小值之差
x1
x2
x3
x4
R
3
4.2
3.5
3.8
验工、绘图者的姓名,以及控制图的
名称编号等。
• ②控制图部分。是指根据概率统计的
原理,在普通坐标纸上作出两条控制
界限和一条中心线,然后把按时间顺
序抽样所得的质量特性值(或样本统
计量)以点子的形式依次描在图上,
从点子的动态分布情况来探讨工序质
量及其趋势的图形。
1.1控制图的概念
• 控制图是判别生产工序过程是否处于控制状态的一种 手段,利用它可以区分质量波动究竟是由偶然原因引 起的还是由系统原因引起的,以便针对具体情况,分 别给以有效的及时的解决,控制生产过程的质量。
①从工序中只能获得一个测定值,如每日电力消耗。
②一批内数据是均一的,不需测取多个计量值。如酒 精的浓度。
③因费用或时间关系,只允许得到一个计量值。如高 压容器的破坏试验。
④希望尽快发现并消除异常原因时。 ⑤计量值间隔时间长的情况下
2.1单值控制图(x控制图)
• (2)x控制图的作法
• x控制图的中心线和上下控制界限的确定
中心线CL:Control Limit
UCL上控制界限 CL中心值
LCL下控制界限
13
1.1控制图的概念
质
量
特
性
• 控制图的基本格式包括两个部分:
均值极差控制图
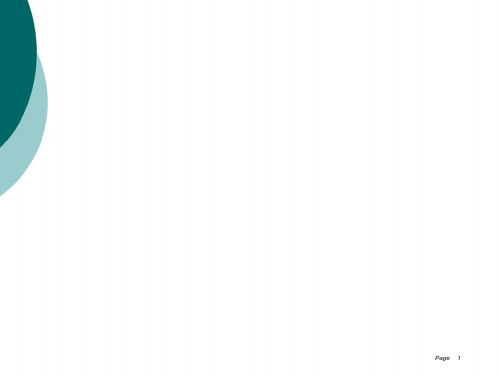
• 均值-极差控制图的作法
示例:
某手表厂为了提高手表的质量,应用排列图分析造成手表 不合格的各种原因,发现“停摆”占第一位。为了解决停 摆问题,再次应用排列图分析造成停摆的原因。结果发现 主要是由于螺栓松动引发的螺栓脱落造成的,为解决问题, 应用控制图对装配作业中的螺栓扭矩进行过程控制。
第一步,取预备数据,依测定的先后顺序排列,通常数据 分成约20—25组,每组4—5个数据。
k X ( X 1 X 2 X 3 ...... X K ) / k Xi / k(k为组数)
i 1
k R (R1 R2 R3 ...... Rk ) / k Ri / k
i 1
X 163.256 R 14.280
Page 13
控制图
Page 18
控制图
准则2:连续9点落在中心线同一侧。主要原因为过程平均值 变化。
Page 19
控制图
准则3:连续6点递增或递减。产生趋势的原因可能是工具 逐渐磨损、维修逐渐变坏等,从而使得参数随着时间而 变化。
Page 20
控制图
准则4:连续14点相邻点上下交替。数据分层不够。如,两 名操作人员轮流进行操作;轮流使用两台设备。
第二步,计算各组样本的平均数( )与极差(R)
Xi
Xi Xi1 Xi2 ... Xim m
Ri max{X1 j}-min {X1 j}
Page 10
Ri max{X1 j}-min {X1 j}
控制图
• 均值-极差控制图的作法
示例:
某手表厂为了提高手表的质量,应用排列图分析造成手表 不合格的各种原因,发现“停摆”占第一位。为了解决停 摆问题,再次应用排列图分析造成停摆的原因。结果发现 主要是由于螺栓松动引发的螺栓脱落造成的,为解决问题, 应用控制图对装配作业中的螺栓扭矩进行过程控制。
均值-极差(X-R)控制图
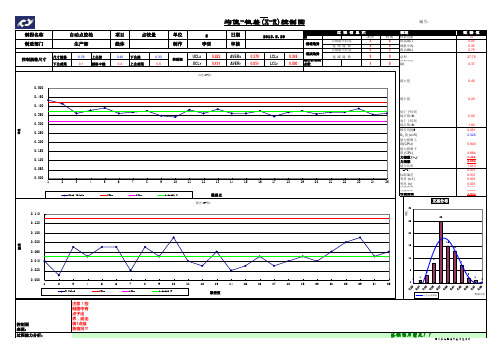
均值-极差(X-R)控制图编号:过 程 信 息 栏统计特性描述数 据 值数据重要趋势X 图R 图样本容量7534工程规范下限 (LSL)0.0599规格中线0.3533工程规范上限 (USL)0.75尺寸规格0.35上公差0.40下公差0.30UCLx 0.422AVERx 0.370LCLx 0.31899总和27.75下公差限0.1规格中线0.4上公差限0.8UCLr0.131AVERr0.051LCLr0.000超出控制线点数1读数均值 (X)0.37最大值0.45最小值0.29低于下控制线点数(X)0.00高于上控制线点数(X) 1.00极差均值R 0.051D 2 值 (n=5) 2.326能力指数上限(CPU) 5.800能力指数下限 (CPL) 4.884稳定过程能力指数 (C p ) 5.342稳定过程能力指数 (C pk ) 4.884能力比率 (CR) 1.013标准偏差(n-1)0.031标准偏差 (n)0.031变异 (n-1)0.001变异 (n)0.001性能指数 (P P ) 3.777性能比率 (PR)0.265性能指数 (P pk )3.453控制图表现:注意!控制图中有点子出界,或出现7点链条情况!!!日期n 1234567891011121314151617181920212223242510.4500.4100.3700.3500.3500.3200.3600.3300.3500.2900.3800.3500.3900.3500.3500.3500.3600.3500.3500.340######################20.4100.4100.3900.3800.4000.3700.3600.3900.3700.3500.4000.3800.4100.3600.3800.4000.3400.3900.3700.380######################30.4400.4200.3200.4000.4200.3900.3800.4000.3200.3800.3600.3500.3500.3700.3500.3700.3300.3600.4000.350######################均值0.4330.4130.3600.3770.3900.3600.3670.3730.3470.3400.3800.3600.3830.3600.3600.3730.3430.3670.3730.3570.367#########0.3530.360极差0.0400.0100.0700.0500.0700.0700.0200.0700.0500.0900.0400.0300.0600.0200.0300.0500.0300.0400.0500.040######################过程能力特足!!备注:控制规格尺寸过程能力分析:2013.5.29制造部门生产部李训控制限日期审核递增趋势递减趋势制程名称点较量自动点胶枪g 点数最大长度递 增 链 数点数最大长度递 减 链 数项目线体单位制作0.0000.050 0.100 0.150 0.200 0.250 0.3000.350 0.4000.450 0.50012345678910111213141516171819202122232425均值数据点均值(X-图)Data ValuesUCLxLCLxAverage X0.0000.020 0.040 0.060 0.0800.1000.120 0.140 12345678910111213141516171819202122232425极差极差值极差(R-图)R ValueUCLrLCLrAverage R13825151372151015202530频数数据区间正态分布正态分布曲线四川长虹包装印务有限公司。
均值极差控制图课件
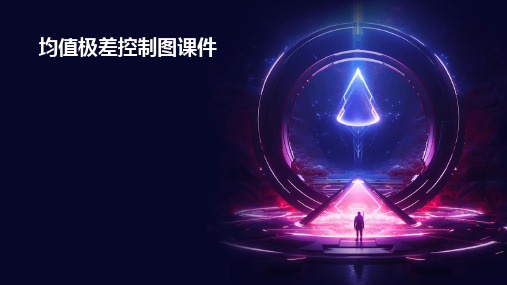
在质量管理中的应用
监控产品质量
均值极差控制图可以用于监控产品质量,及时发现产品质量的异 常波动,采取相应措施进行调整。
提高产品质量稳定性
通过对产品质量的监控,均值极差控制图可以帮助企业提高产品质 量的稳定性,提高客户满意度。
预防质量事故
及时发现产品质量的异常波动,采取相应措施进行调整,可以预防 质量事故的发生,减少质量损失。
CHAPTER
02
均值极差控制图的原理
均值极差控制图的概念
01
均值极差控制图是一种用于监控 过程稳定性和异常波动的质量控 制工具,通过计算样本均值和极 差来评估过程的稳定性。
02
它主要用于连续生产过程中,通 过对样本数据的分析,及时发现 异常波动,采取相应措施,确保 生产过程的稳定性和产品质量。
均值极差控制图的绘制方法
01
02
03
04
选择合适的样本大小和抽样间 隔,按照时间顺序抽取样本。
计算每个样本的均值和极差。
将计算出的均值和极差分别绘 制在横坐标和纵坐标上,形成
控制图。
在控制图上标注出样本的均值 和极差,并根据判异准则判断
过程是否处于受控状态。
均值极差控制图的判异准则
均值超出控制限
缺点
对数据分布敏感
均值极差控制图对数据的分布敏 感,如果数据分布不正态,控制
图的性能可能会受到影响。
无法处理异常值
如果数据集中存在异常值,均值 极差控制图的控制限可能会被扭 曲,导致异常值被误判为正常数
据。
对数据量要求较高
对于小样本数据,均值极差控制 图的性能可能会受到影响,因为 小样本数据的均值和极差可能会
跨部门协同管理
通过跨部门的数据共享和整合,利用控制图实现协同管理,提高 整个组织的运营效率和响应速度。
- 1、下载文档前请自行甄别文档内容的完整性,平台不提供额外的编辑、内容补充、找答案等附加服务。
- 2、"仅部分预览"的文档,不可在线预览部分如存在完整性等问题,可反馈申请退款(可完整预览的文档不适用该条件!)。
- 3、如文档侵犯您的权益,请联系客服反馈,我们会尽快为您处理(人工客服工作时间:9:00-18:30)。
控制图
p控制图。用于控制对象为不合格品率或合格品率等计数 值质量指标的场合。
np控制图。用于控制对象为不合格品数的场合。由于计算 不合格品率需要进行除法,比较麻烦。所以在样本大小相 同的情况下,用此图比较方便。
c控制图。用于控制一部机器、一个部件、一定的长度、 一定的面积或任何一定的单位中所出现的缺陷数目。例如 ,铸件上的砂眼数,机器设备的故障数等等。
简记 X-R 控制图 X-S 控制图
-R 控制图 X-Rs 控制图
p控制图 np 控制图 c 控制图 u 控制图
7
控制图
均值-极差控制图。是最常用、最基本的控制图,它用于控制对
象为长度、重量、强度、纯度、时间和生产量等计量值的场合 。
均值-标准差控制图。此图与均值-极差控制图相似,只是用标
准差图(S图)代替极差图(R图)而已。极差计算简便,故R图得 到广泛应用,但当样本大小n>10或12时,应用极差估计总体标 准差的效率减低,最好应用S图代替R图。
控制图
所有的产品和服务都是过程的结果。统计过程控制就是根 据产品质量的统计观点,运用数理统计方法对生产制造过 程和服务过程的数据加以收集、整理和分析,从而了解、 预防和监控过程的运行状态和水平。这是一种以预防为主 的质量控制方法。
统计过程控制主要解决两个基本问题:一是过程运行状态 是否稳定,二是过程能力是否充分。
根据质量数据的类型可分为: 计量值控制图 计数值控制图
需根据所控制质量指标的情况和数据性质分别加以选择。 例如下表:
6
控制图
数据类型 计量型
计数型
控制图名称 均值-极差控制图
均值-标准差控制图 中位数-极差控制图 单值-移动极差控制图 不合格品率控制图 不合格品数控制图
缺陷数控制图 单位缺陷数控制图
14
控制图 第五步,绘制控制图
15
控制图 判异准则
准则1:一点落在A区以外。
16
控制图 准则2:连续9点落在中心线同一侧。主要原因为过程平均
值变化。
17
控制图 准则3:连续6点递增或递减。产生趋势的原因可能是工具
逐渐磨损、维修逐渐变坏等,从而使得参数随着时间而 变化。
18
控制图 准则4:连续14点相邻点上下交替。数据分层不够。如,两
名操作人员轮流进行操作;轮流使用两台设备。
19
控制图 准则5:连续3点有两点落在中心线同一侧的B区以外。过程
参数μ发生了变化。
20
控制图 准则6:连续5点中有4点落在中心线同一侧的C区以外。参
数μ发生了变化。
21
控制图 准则7:连续15点在C区中心线上下。现象是参数σ变小。
实际可能为数据分层不够或数据造假。
控制图是对过程质量特性值进行测定、记录、评估,从而 监察过程是否处于控制状态的一种用统计方法设计的图。
1
控制图 控制图示例
2
控制图 控制图原理
1、质量波动理论 偶然波动 异常波动
2、小概率事件
3
控制图
统计控制状态:过程处于稳定状态。 技术控制状态:过程能力指数满足要求。
状态Ⅰ:统计控制状态与技术控制状态同时达到,是最理想的状态。 状态Ⅱ:统计控制状态未达到,技术控制状态达到。 状态Ⅲ:统计控制状态达到,技术控制状态未达到。 状态Ⅳ:统计控制状态与技术控制状态均未达到,是最不理想的状态。 一般改进的途径:状态Ⅳ→状态Ⅲ→状态Ⅰ
控制图
n=5 ,查表得A2=0.577 D3=0 得到极差图控制限
UCLR=2.144x14.280≈30.188 CLR=14.280
LCLR= ----
D4=2.114
得到均值图控制限 UCL=16.256+0.577x14.280≈171.496 CL=163.256 LCL=163.256-0.577x14.280≈155.016
22
控制图 准则8:连续8点在中心线两侧,但无一在C区中。主要原
因为数据分层不够。
23
综合运用 线路板的不良:运用因果图进行分析后,认为主要原因在
于输出电压不稳定,从而影响了其他部件的工作。所以, 针对线路板的输出电压,作改善活动。 第一步,检验100个线路板的输出电压。获得相关数据:
4
控制图
控制图的目的 控制图和其它的统计图不同,因为它不但能够把数据用曲 线表示出来,观察其变化的趋势,而且能显示数据波动是 属于偶然波动还是异常波动,以指示某种现象是否正常, 从而采取适当的措施。
利用控制限区分 是否为异常波动
5
控制图
控制图的类型
按控制图的用途分类: 分析用控制图 控制用控制图
i1
k R(R1R2R3.....R.k)/k R/ik
i1
X16.2356R1.2 480
控制图
第四步,计算控制界限。 X 图中心线(CL)=X 控制上限(UCL)= X A2 R 控制下限(LCL)= X A2 R
R控制图:中心线(CL)= R
控制上限(UCL)= D4 R 控制下限(LCL)= D 3 R
中位数-极差控制图。此图与均值-极差控制图也很相似,只是用
中位数图代替均值图。由于中位数的计算比均值简单,所以多 用于现场需要把测定数据直接记入控制图进行管理的场合。
单值-移动极差控制图。多用于下列场合:(1)采用自动化检查
和测量对每一个产品都进行检验的场合;(2)取样费时、昂贵 的场合;(3)如化工等过程,样品均匀,多抽样也无太大意义 的场合。由于它不像前三种控制图那样能取得较多的信息,所 以它判断过程变化的灵敏度也要差一些。
第一步,取预备数据,依测定的先后顺序排列,通常数据 分成约20—25组,每组4—5个数据。
第二步,计算各组样本的平均数(X i)与极差(R)
Xi Xi1Xi2...Xim m
R im{a1 X j} xm - {i1 X jn }
控制图 数据表
11
控制图
第三步,计算总平均和极差的平均。
k X(X1X2X3.....X .K)/kX/ik(k为组 ) 数
u控制图。当样品的大小变化时应换算成每单位的缺陷数 并用u控制图。
9
R im{a1 X j} xm - {i1 X jn }
控制图
均值-极差控制图的作法
示例:
某手表厂为了提高手表的质量,应用排列图分析造成手表 不合格的各种原因,发现“停摆”占第一位。为了解决停 摆问题,再次应用排列图分析造成停摆的原因。结果发现 主要是由于螺栓松动引发的螺栓脱落造成的,为解决问题, 应用控制图对装配作业中的螺栓扭矩进行过程控制。