02-DIN 281 轴承疲劳寿命预测值与试验数据的比较
滚针轴承的疲劳寿命与寿命预测模型研究

滚针轴承的疲劳寿命与寿命预测模型研究滚针轴承是工业领域常用的一种机械元件,广泛应用于汽车、飞机、机械设备等领域。
疲劳寿命是滚针轴承性能指标之一,它关系到滚针轴承的可靠性和使用寿命。
因此,疲劳寿命的评估和预测对于滚针轴承的设计和维护具有重要意义。
滚针轴承的疲劳寿命是指在给定负载条件下,滚道和滚针之间的接触疲劳损伤产生的寿命。
在滚动接触过程中,由于滚道和滚针之间的应力集中,会引起较大的应力和应变,导致材料的损伤和疲劳破坏。
因此,研究滚针轴承的疲劳寿命与寿命预测模型,有助于提高滚针轴承的可靠性和耐久性。
寿命预测模型是通过建立滚针轴承的寿命与相关因素之间的数学方程,来预测滚针轴承的使用寿命。
常用的寿命预测模型包括基于试验数据的经验模型和基于理论分析的数学模型。
在经验模型中,通过对大量滚针轴承试验数据的统计分析,提取出影响疲劳寿命的关键参数,并建立数学模型。
这些关键参数可以包括载荷、转速、温度、润滑条件等因素。
例如,经典的L10模型就是基于试验数据的经验模型,它假设疲劳寿命服从对数正态分布,并使用滚动元件的寿命极限来估计疲劳寿命。
与经验模型相比,理论分析模型更加精确和可靠,但也更加复杂。
理论分析模型一般基于滚针轴承的载荷分布、力学特性和材料疲劳性能等方面的理论知识。
例如,采用Hertz接触理论、接触疲劳理论和材料疲劳寿命模型等,可以建立滚针轴承疲劳寿命的数学模型。
除了寿命预测模型,滚针轴承的疲劳寿命还受到一些其他因素的影响。
例如,轴承的材料、几何形状、表面质量等都会对疲劳寿命产生影响。
为了更准确地预测滚针轴承的疲劳寿命,需要综合考虑这些因素。
为了验证寿命预测模型的准确性,研究人员通常会进行滚针轴承的寿命试验。
试验过程中,通过给定一系列固定载荷和转速的条件,观察滚针轴承的故障时间,从而得到实际的疲劳寿命数据。
然后,将这些实验数据与预测模型进行比较,并进行修正和优化。
总之,滚针轴承的疲劳寿命与寿命预测模型的研究对于提高滚针轴承的可靠性和使用寿命具有重要意义。
滚动轴承疲劳寿命威布尔分布三参数的研究
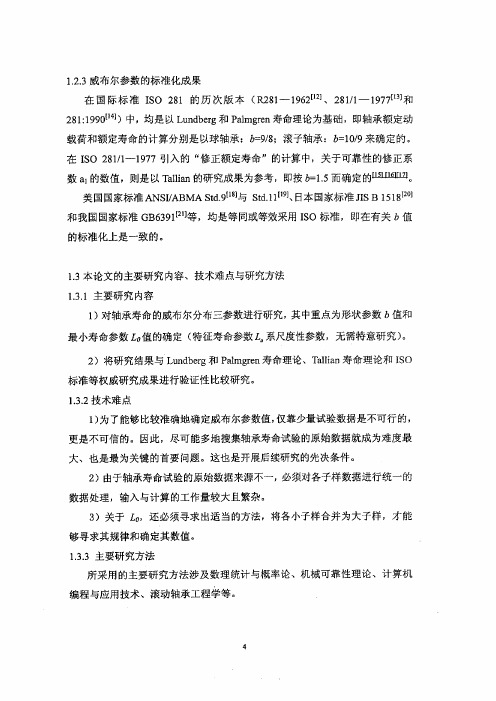
绘制出一条直线。该直线与F(三)=63.2%水平线相交的点所对应的寿命值,即 为三。值。若该直线与横坐标的夹角为0,则可得
二参数威布尔分布的研究重点是形状参数b值的确定,其代表性研究成果 为Lundberg和Palmgren寿命理论。三参数威布尔分布的研究重点则是在二参 数威布尔分布研究的基础上,主要关注最小寿命参数岛值的确定,其代表性研 究成果为Tallian寿命理论。ISO标准和有关国家标准则对轴承寿命的威布尔形 状参数作了权威性认同与规定。但是,由于威布尔参数的精确(高可靠性与高 置信度的)确定,特别是位置参数即最小寿命参数岛值的确定,需要大量的试 验作支撑,以寻求其统计规律性,财力、物力与时间耗费巨大,因此,有关研 究成果在种种局限性之下所导致的或者难以涉及,或者做不深入,或者做不准 确,就成为必然之事。也正因为如此,继续深入开展相关研究,以求不断完善 威布尔分布、尤其是三参数威布尔分布在轴承寿命方面的应用,其理论意义与 实用价值就十分重大。
1.3本论文的主要研究内容、技术难点与研究方法 1.3.1主要研究内容
1)对轴承寿命的威布尔分布三参数进行研究,其中重点为形状参数b值和 最小寿命参数如值的确定(特征寿命参数L系尺度性参数,无需特意研究)。
2)将研究结果与Lundberg和Palmgren寿命理论、Tallian寿命理论和ISO 标准等权威研究成果进行验证性比较研究。 1.3.2技术难点
#
图2--3 r=O,a=2,而∥取不同数值时的,(f)曲线
电机轴承的疲劳寿命预测与分析

电机轴承的疲劳寿命预测与分析引言:电机轴承是现代工业中广泛应用的关键部件之一。
作为机械设备中承受负载的重要部分,轴承的工作状态和寿命对设备的性能和可靠性有着直接的影响。
因此,对电机轴承的疲劳寿命进行预测和分析,对于提高设备的可靠性和延长使用寿命具有重要意义。
1. 疲劳寿命的概念与重要性疲劳寿命是指轴承在连续往复负载作用下可以正常工作的时间。
轴承在工作过程中会受到载荷的作用,特别是往复载荷对轴承的作用更加明显,这就会导致轴承表面出现疲劳裂纹。
如果这些疲劳裂纹得不到及时修复或处理,将会不可避免地导致轴承失效。
因此,对于电机轴承而言,准确预测和评估疲劳寿命具有重要的实际意义。
2. 疲劳寿命预测方法介绍疲劳寿命预测是通过对轴承的工作条件、载荷和材料等因素进行分析和计算,来预测轴承的寿命。
在实际应用中,常用的疲劳寿命预测方法主要包括经验法、理论模型法和数值模拟法。
(1)经验法:经验法是通过对大量现场数据和实验数据进行统计和分析,建立经验公式,以此预测轴承的疲劳寿命。
这种方法简单易行,但对数据的准确性要求较高,并且适用范围有限。
(2)理论模型法:理论模型法是通过分析轴承的工作原理和载荷特点,建立数学模型,并结合工程实践,进行寿命预测。
这种方法需要深入理解轴承的运行机制和数学模型的建立,适用于一些特定条件下的疲劳寿命预测。
(3)数值模拟法:数值模拟法是基于计算机技术的快速发展,通过建立轴承的三维模型,结合有限元分析等相关方法,对轴承的疲劳寿命进行模拟和预测。
这种方法具有较高的准确性和可靠性,但对于计算机硬件和软件的要求较高。
3. 疲劳寿命分析与故障诊断除了预测轴承的疲劳寿命,对于已经失效的轴承进行分析和故障诊断也是非常重要的。
通过对失效轴承的外观、疲劳裂纹特征等进行观察和分析,可以了解轴承失效的原因,并采取相应的措施,防止类似问题再次发生。
同时,对于已经失效的轴承进行分析和诊断,也可以为预测其他轴承的寿命和健康状况提供有价值的参考。
机床轴承寿命评估及预测技术研究
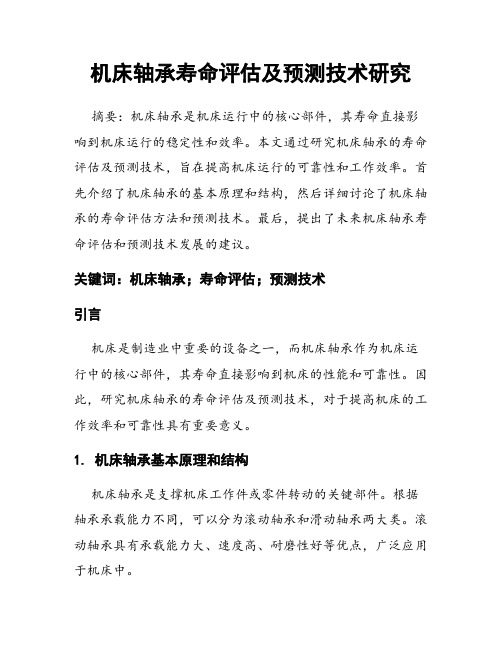
机床轴承寿命评估及预测技术研究摘要:机床轴承是机床运行中的核心部件,其寿命直接影响到机床运行的稳定性和效率。
本文通过研究机床轴承的寿命评估及预测技术,旨在提高机床运行的可靠性和工作效率。
首先介绍了机床轴承的基本原理和结构,然后详细讨论了机床轴承的寿命评估方法和预测技术。
最后,提出了未来机床轴承寿命评估和预测技术发展的建议。
关键词:机床轴承;寿命评估;预测技术引言机床是制造业中重要的设备之一,而机床轴承作为机床运行中的核心部件,其寿命直接影响到机床的性能和可靠性。
因此,研究机床轴承的寿命评估及预测技术,对于提高机床的工作效率和可靠性具有重要意义。
1. 机床轴承基本原理和结构机床轴承是支撑机床工作件或零件转动的关键部件。
根据轴承承载能力不同,可以分为滚动轴承和滑动轴承两大类。
滚动轴承具有承载能力大、速度高、耐磨性好等优点,广泛应用于机床中。
2. 机床轴承寿命评估方法机床轴承寿命评估是通过对轴承状态进行监测和分析,计算出轴承的剩余寿命,从而判断轴承是否需要更换或维修的技术。
目前,常用的轴承寿命评估方法包括传统方法和基于状态监测的方法。
传统方法主要包括经验法和统计法。
经验法是根据实际经验和数据来评估轴承寿命,具有简单易行的特点,适用于一些常见的轴承故障模式。
统计法是通过对大量轴承的寿命数据进行统计分析,建立概率模型来评估轴承寿命。
基于状态监测的方法是将传感器安装在轴承上,实时监测轴承的运行状态,通过分析传感器数据和建立数学模型,实现对轴承寿命的评估。
这种方法具有精度高、实时性强的特点,适用于对机床轴承寿命进行长期监测和预测。
3. 机床轴承寿命预测技术机床轴承寿命预测是在轴承寿命评估的基础上,通过建立预测模型和算法,对轴承未来的寿命进行预测的技术。
目前,常用的轴承寿命预测技术包括基于统计学方法、人工智能方法和机器学习方法。
基于统计学方法主要是通过统计分析轴承的寿命数据,建立概率模型来预测轴承未来的寿命。
这种方法简单易行,但对于一些复杂的轴承情况可能预测结果不准确。
轴承寿命预测与损伤诊断方法研究

轴承寿命预测与损伤诊断方法研究轴承是机械设备中重要的零部件,其寿命直接影响到设备的使用寿命和可靠性。
因此,轴承寿命预测和损伤诊断方法的研究具有重要意义。
本文将介绍轴承寿命预测与损伤诊断的相关方法和技术。
一、轴承寿命预测方法轴承寿命预测是通过一定的方法和技术对轴承的寿命进行估算。
常用的轴承寿命预测方法有试验法、统计法和仿真法。
试验法是通过实验数据的分析和处理来预测轴承的寿命。
试验法的优点是直观、可靠,但其缺点是耗时耗力,且结果受试验条件和环境的影响较大。
统计法是通过对大量轴承的寿命数据进行统计分析,建立数学模型来推算寿命。
统计法的优点是能够综合考虑多种因素对寿命的影响,但其缺点是建立合理的统计模型需要大量的轴承寿命数据。
仿真法是利用计算机仿真技术,基于轴承的工作条件和负载情况,建立数学模型进行仿真计算,得到轴承的寿命指标。
仿真法的优点是灵活、快速,且结果的准确性较高,但其缺点是需要准确的输入参数和模型。
二、轴承损伤诊断方法轴承损伤诊断是通过监测轴承的振动、声音、温度等信号,结合信号处理和模式识别技术,对轴承的损伤情况进行判断和预警。
振动诊断是轴承损伤诊断中常用的方法之一。
通过对轴承振动信号的采集和分析,可以判断轴承的运行状态和损伤程度。
常用的振动参数包括加速度、速度和位移等,通过对这些参数的分析,可以了解轴承的损伤情况。
声音诊断是通过对轴承工作时的声音信号进行监测和分析,判断轴承的损伤情况。
轴承在损伤状态下会产生特定频率和幅值的声音信号,通过对这些信号的分析,可以诊断轴承的损伤情况。
温度诊断是通过监测轴承的工作温度,判断轴承的运行状态和损伤程度。
轴承在损伤状态下会产生摩擦热,从而导致轴承的温度升高。
通过对轴承温度的监测和分析,可以诊断轴承的运行状态。
三、轴承寿命预测与损伤诊断方法的研究进展近年来,随着传感器技术、信号处理技术和机器学习技术的发展,轴承寿命预测和损伤诊断方法取得了一定的进展。
在轴承寿命预测方面,随着试验技术的更新和计算机仿真技术的成熟,基于试验和仿真的方法在寿命预测中得到了广泛应用。
风力发电机组轴承的滚道疲劳寿命预测方法研究

风力发电机组轴承的滚道疲劳寿命预测方法研究引言:随着清洁能源的需求不断增加,风力发电逐渐成为各国重要的能源转换方式之一。
然而,风力发电机组在运行过程中常常遭遇极端的环境条件和工作负荷,这对轴承的可靠性和寿命提出了严峻的要求。
滚道疲劳是导致轴承失效的主要原因之一,因此预测风力发电机组轴承的滚道疲劳寿命成为了当前研究的重点。
本文将介绍相关文献中的预测方法,并提出一种新的预测方法。
一、传统的滚道疲劳寿命预测方法1. 基于经验公式的预测方法经验公式是一种简化的预测方法,它基于理论和实验数据的分析,通过将轴承的工作负荷、转速、清洗频率等参数纳入考虑,得出滚道疲劳寿命的预测值。
这种方法具有较高的实用性,但仍存在一定的误差。
2. 基于有限元分析的预测方法有限元分析是一种基于数值计算的方法,它通过对轴承内部力学行为进行分析,得出滚道疲劳寿命的预测值。
该方法考虑了轴承的材料特性、几何结构和工作负荷等因素,能够提供较精确的预测结果。
然而,由于有限元分析需要大量的计算资源和时间,该方法在实际应用中存在一定的局限性。
二、新的滚道疲劳寿命预测方法考虑到传统方法的局限性,本文提出了一种新的滚道疲劳寿命预测方法,该方法结合了统计学和机器学习技术。
1. 基于统计学的预测方法统计学是一种强大的工具,它能够分析数据之间的关系,找出规律和趋势。
本文中,我们将通过收集大量的轴承运行数据,对滚道疲劳寿命进行统计分析。
通过分析工作负荷、转速、使用时间等因素与滚道疲劳寿命之间的关系,建立数学模型,从而预测轴承的寿命。
2. 基于机器学习的预测方法机器学习是一种人工智能的方法,它通过训练模型从数据中学习和预测。
我们将使用机器学习算法对轴承运行数据进行处理和分析,并建立预测模型。
通过输入轴承的工作负荷、转速等参数,模型可以输出滚道疲劳寿命的预测结果。
相比传统方法,机器学习方法能够更准确地捕捉到轴承寿命与各种因素之间的复杂关系。
三、实验验证和结果分析为了验证提出的方法,我们将运行一系列的实验。
高速动车组轴承的动载荷影响下的疲劳寿命评估

高速动车组轴承的动载荷影响下的疲劳寿命评估概述:随着高速铁路的不断发展,高速动车组的运营速度也越来越快。
高速动车组轴承作为关键部件之一,承载着列车的重量和动力,其疲劳寿命评估成为了必要的研究课题。
本文旨在探讨高速动车组轴承在动载荷下的疲劳寿命评估方法和影响因素,以提高轴承的可靠性和运行安全性。
1. 疲劳寿命评估方法1.1 疲劳寿命概念疲劳寿命是指轴承在特定负荷下能够承受的循环载荷循环次数。
通过评估轴承的疲劳寿命,可以预测轴承的使用寿命,避免轴承失效导致的问题。
1.2 动载荷下的疲劳寿命评估方法动载荷下的疲劳寿命评估方法包括实验测试和数值模拟两种途径。
实验测试方法包括疲劳试验和寿命试验。
在试验中,采集轴承承受动载荷时的应力应变数据,并通过对数据分析,计算得出轴承的疲劳寿命。
数值模拟方法利用有限元分析等数值方法对轴承的应力分布进行模拟计算,然后通过疲劳损伤理论和疲劳寿命模型,评估轴承的疲劳寿命。
2. 影响因素2.1 轴承材料轴承材料的选择对疲劳寿命有重要影响。
常用的轴承材料有铬钢和高碳钢等。
不同材料的组织结构和力学性能会影响轴承的承载能力和耐疲劳性能。
2.2 动载荷动载荷是指轴承在运行中承受的载荷,包括垂直载荷和横向载荷。
动载荷的大小和方向会直接影响轴承的疲劳寿命。
合理评估动载荷对轴承产生的影响,可以采取有效措施进行载荷分配和减载,延长轴承的寿命。
2.3 运行环境运行环境对轴承的疲劳寿命有着重要影响。
高速动车组运行的环境包括温度、湿度、尘埃、振动等多个因素。
这些因素会加剧轴承的磨损和疲劳损伤,需要采取相应的防护措施,如增加润滑剂的使用、改善密封等。
2.4 轴承设计和装配轴承的设计和装配质量也会对疲劳寿命产生影响。
合理的轴承设计能够减少应力集中和摆动,提高疲劳寿命。
同时,正确的轴承装配和预紧力调整也能够提高轴承的寿命。
3. 提高轴承疲劳寿命的措施3.1 材料技术的改进通过研究新型轴承材料,如高强度、高韧性的合金材料,可以提高轴承的承载能力和耐疲劳性能,延长其使用寿命。
滚动轴承疲劳寿命及可靠性强化试验技术现状及发展

滚动轴承疲劳寿命及可靠性强化试验技术现状及发展2007.11.29 来源:«现代零部件»作者:李兴林关键词:轴承,机械零部件滚动轴承是广泛应用的重要机械基础件,其质量的好坏直截了当阻碍到主机性能的优劣,而轴承的寿命那么是轴承质量的综合反映,在中国轴承行业〝十一五〞进展规划中,重点要求开展提高滚动轴承寿命和可靠性工程技术攻关。
低载荷、高转速的传统轴承寿命试验方法周期长、费用高且试验结果的可靠性差,而强化试验那么在保持接触疲劳失效机理一致的前提下,大大地缩短试验时刻,降低了试验成本,从而加快了产品的开发周期和改进步伐,因此轴承寿命强化试验受到越来越多的关注、研究和应用。
轴承快速寿命试验包含了比轴承寿命强化试验更为广泛的内涵,它不仅在寿命试验方面,而且在寿命试验的设计,寿命数据的处理、分析,寿命的推测评估,轴承失效的快速诊断、分析、处理等系统技术方面具有更新更广的内容。
轴承寿命理论的现状及进展早在1939年,Weibull提出滚动轴承的疲劳寿命服从某一概率分布,这确实是后来以其名字命名的Weibull分布,认为疲劳裂纹产生于滚动表面下最大剪切应力处,扩展到表面,产生疲劳剥落,Weibull给出了生存概率S与表面下最大剪切应力τ、应力循环次数N和受应力体积V的关系:〔1〕瑞典科学家Palmgren通过数十年的数据积存,于1947年和Lundberg一起提出了滚动轴承的载荷容量理论,又通过五年的试验研究,该理论才得以完善。
该理论认为接触表面下平行于滚动方向的最大交变剪切应力决定着疲劳裂纹的发生,考虑到材料冶炼质量对寿命的阻碍,同时指出:应力循环次数越多、受力体积越大,那么材料的疲劳破坏概率就越大,提出了统计处理接触疲劳问题的指数方程:〔2〕式中S——轴承使用寿命τ0——最大动态剪切应力振幅z0——最大动态剪切应力所在的深度c、e、h——待定指数,由轴承试验数据确定V——受应力体积N——应力循环次数,以万次计通过推导和大量轴承试验数据分析,获得Lundberg-Palmgren额定寿命运算公式:(3)式中L10 ——差不多额定寿命,百万转Cr ——差不多额定动载荷,NP ——当量动载荷,Nε——寿命指数,球轴承取3,滚子轴承取10/3该公式1962年已由ISO列为举荐标准,并于1977年修正为正式的国际标准ISO 281/1-1977。
- 1、下载文档前请自行甄别文档内容的完整性,平台不提供额外的编辑、内容补充、找答案等附加服务。
- 2、"仅部分预览"的文档,不可在线预览部分如存在完整性等问题,可反馈申请退款(可完整预览的文档不适用该条件!)。
- 3、如文档侵犯您的权益,请联系客服反馈,我们会尽快为您处理(人工客服工作时间:9:00-18:30)。
DIN 281 轴承疲劳寿命预测值与试验数据的比较作者:Michael Kotzalas, Gerald Fox摘要 随着近年来滚子轴承的技术进步,业内掀起了一股重新评定轴承寿命预测值算法的浪潮。
其意义对于风电齿轮箱行业尤为重要,在该行业对轴承的计算寿命 L10的标准要求是 20 年。
现在世界上有许多预测轴承寿命的公式或方法,但这些不同的方法所提供的预测值差别也很大。
为了建立一种先进的、公认的预测轴承寿命L10的方法,使之成为统一依据,德国工业规范(DIN)已经建立了一种算法标准, 它假设了典型的轴承的设计、制造工艺以及预期的失效模式损坏机理。
该标准通过各成员公司的公开的试验结果来验证,或与这些公司的预测算法进行比较验证。
为了进一步地思考 DIN 算法的有效性,正确地预测滚子轴承的疲劳寿命,本文将来自六家顶级制造厂、包括铁姆肯公司在内的标准的产品——圆锥滚子轴承(TRB)的试验结果,与DIN和铁姆肯公司的预测算法进行了比较。
所选择的试验数据包括了当今试验程序中的不同操作条件、油膜厚度、装配偏差(不对中)、负荷差别和滚道座圈表面碎屑压痕状况。
调查的结果显示:轴承制造厂的专有技术算法——本例中的铁姆肯公司专有技术算法——更加精确地预测到了他们的产品的实际性能。
事实上,对于低负荷,以 DIN 算法预测的疲劳寿命趋于偏高,对于含有碎屑污染的工况下预测值则趋于偏低。
23轴承疲劳试验 本文的轴承疲劳寿命试验结果是从作者的实验室收集到的。
试验仅采用了标准的产品或现有的圆锥滚子轴承(TRB ),在科学地控制的工况下的轴承试验结果与轴承用户使用结果是不相关的。
选择的试验涉及了来自六家顶级制造厂、包括铁姆肯公司在内的轴承,和不同的工况。
总体上不同的工况包括油膜的厚薄、轴承的不对中、载荷的大小和滚道表面的碎屑压痕状况。
所有的试验都是在作者的实验室内进行的,采用的是 first-in-four 方法案,见图1。
该试验方案中,中心轴承承受的径向负荷来自液压汽缸,而端部轴承的负荷则通过轴与轴承座产生。
当其中一个轴承出现有6 mm2(0.01平方英寸)面积裂纹时,试验就会停止。
此时,其余三个轴承试验也会暂停,得到该四个轴承的样品 L 15.91寿命。
前言 当今,滚子轴承技术巳经有了长足的进步。
通过清洁度更高的钢材的使用、新的表面光洁度和金相技术、以及耐磨损涂层料的应用,上述进步已经在设计和制造中可以见到。
另外,在滚子轴承性能的理念和模型化方面也有进步。
计算机的使用,提高和完善了对轴承分析的水平,过去不可能做到的事情,现在己经是标准的实践方法。
例如,在预测轴承性能的领域中当今已经开展了大量的研究活动[1-7]。
这对于许多条件苛刻的和高度复杂的应用场合的意义变得特别重要。
例如,对于风力透平齿轮箱行业,20 年的轴承计算寿命 L 10 是一种标准的要求。
在与当今轴承分析中所有研究中活动有关的一个至关重要的问题是:为了预测轴承疲劳寿命,已经形成了许多的专有技术方法。
但这些方法变化太大,使工程师们为选用轴承而犯难,因为,看上去完全相同的轴承, 但根据其所用的方法,居然会得出截然不同的、预测的寿命。
为了建立一种先进的、公认的预测轴承寿命 L 10 的方法中,并使之成为统一的依据,德国工业规范(DIN )[5和6]已经建立了一种算法标准, 它假设典型的轴承的设计、制造工艺以及预期的损坏机理制造工艺以及预期的失效模式。
如同任何标准化活动一样,该标准的有效性仅通过各成员公司公开试验结果或比较他们的预测算法来进行验证。
由于在新的美国齿轮制造商协会(AGMA )风力透平齿轮箱标准6006[8]里,使用 DIN 281.4 标准作为轴承寿命选用的预测标准,因此,需要通过与轴承疲劳试验数据相比,来对该标准的准确性进行调查,这就是本文的目的。
图1 轴承试验设置4疲劳寿命预测 在轴承疲劳试验数据收集后,采用铁姆肯公司样本方法和铁姆肯公司先进专有方法以及 DIN281.1 和DIN281.4的算法,对疲劳寿命进行预测。
将从轴承外圈边缘上测得的平均温度用作确定润滑剂的性能,测得的平均载荷区的大小用作确定 48 组中每一组的对轴承施加的推力负荷。
通过轴弯曲变形的分析以及轴承座套中预先设置的偏差,就可估算出轴承装配偏差。
对于所有预测算法而言,上述各输入值都是必要的。
然而,铁姆肯公司的先进方法和 DIN 281.4 方法,还需输入滚道修形和表面光洁度的数据。
当并不知道所有试验轴承的设计滚道修形和表面光洁度时,如对最终的用户而言,可以釆用每一种制成工具的默认滚道修形和光洁度。
两种算法中的滚道修形都采用某些改良的(如对数式的)滚道形式。
在 48 个试验组的寿命预测后,就可进行Weibull 法分析,将试验数据与 5 类操作条件结合起来,为了做到这一点,将每一个试验组内的各个轴承试验寿命转化成相应的预测寿命 L 15.91。
这样,就可为所有的操作组别进行 Weibull 法分析,以确定每一种预测算法的有效性。
可将 Weibull 法分析结果、以 90% 的可信度间隔方式绘制成图 2 至图 6 中的图形。
最后,下列公式(1)中规定的[4]、全部的总加权误差就可为铁姆肯公司和其它的顶级制造厂分别加以确定。
从公式(1)中可以看出:总加权误差(TWE )表示与 90% 置信带有的寿命预测的误差。
TWE 的结果显示在图 7中。
标准的试验设置采用 ISO 等级粘度的矿物油,此油由循环系统供给。
为了防止在完全配制的油中因添加物的原因,而使轴承疲劳性能产生任何改变,润滑剂仅包括防锈和抗氧化(R&O )添加物。
循环油通过40mm 独立的过滤器进行过滤。
即使设置了这样的过滤器,但由于实验室总体的环境原因,所有试验轴承箱所测得的 ISO4406 油清洁度等级是在 15/12。
在利用前述标准的试验设置时,为了达到所要求的操作环境,对试验装置内的不同的参数进行了控制。
例如,将润滑剂的入口温度设定在不同的数值,以达到所要求的润滑剂成膜条件。
通常厚膜试验在37.8℃(100°F )油入口温度下运行,而薄膜试验则在82.2℃(180°F )油入口温度下运行。
为了达到所要求的轴承不对中状态,在轴承座外使用液压加力来设定不同偏差。
最后,碎屑压痕条件是在更加特殊的设置中形成的,釆用的办法是:将轴承部件预先进行压痕处理。
期间,将单一的轴承在 4448 kN (1000磅)纯推力负荷下、在含有碎屑的润滑剂中、转动2000转。
碎屑是以硬化了的工具钢 T15、制成 25 μm 至 53μ m 尺寸的颗粒。
该碎屑以 0.5mg/ml 的比值混入经过高度过滤了的 ISO VG 032 矿物油中,该矿物油中仅含有 R&O 添加物。
在压痕形成后,轴承采用超声波方法,除掉部件上所有残留的污物或碎屑,然后,将其装入疲劳试验装置。
本次研究中所选择的试验模型列于表 1 中。
表1表示了不同的 48 组轴承试验,它们包括了来自 6 家顶级制造厂的、1228 个圆锥滚子轴承。
按照不同的操作条件,将上述不同的组别分成 5 大类:即厚润滑膜、薄润滑膜、有组装偏差的、负荷变化的和带碎屑的。
5测试组热处理λ率不对中(mrad )平均负荷区(deg)平均外圈温度 (ºC)D PW (mm)K 系数P/C 厚膜薄膜不对中不同负荷碎屑表1. 选用轴承的测试数据组123456789101112131415161718192021222324252627282930313233343536373839404142434445464748全淬透表面渗碳表面渗碳表面渗碳表面渗碳全淬透全淬透全淬透全淬透全淬透全淬透全淬透全淬透全淬透全淬透表面渗碳全淬透全淬透表面渗碳表面渗碳表面渗碳表面渗碳全淬透全淬透全淬透表面渗碳表面渗碳表面渗碳表面渗碳全淬透全淬透全淬透全淬透表面渗碳表面渗碳表面渗碳表面渗碳表面渗碳表面渗碳表面渗碳表面渗碳表面渗碳表面渗碳表面渗碳表面渗碳表面渗碳全淬透全淬透3.71.62.21.41.31.51.75.01.10.91.41.02.01.22.71.31.61.20.50.40.50.50.50.61.60.80.52.70.62.31.72.11.73.00.70.70.70.90.90.70.70.70.70.40.91.71.81.30.090.020.020.020.050.090.220.310.180.310.310.310.510.370.310.800.510.310.170.001.000.070.200.072.002.002.001.802.001.000.941.210.951.090.940.470.380.900.450.180.100.060.040.120.060.510.510.51135130135134142138145148155149140139135140133149128147146144150135149136135136153144146144147126152141175170140175165130130120120150135119148151485957615978464560434648465140464948798477919688768686477844484848438268678357898274668668785684612122122121206110957505752576270574562574710953120771206150475652534756503963636343439494949494946262621.51.31.31.31.31.51.41.51.41.51.81.51.11.41.51.41.11.51.41.41.61.31.41.31.51.11.11.11.81.61.11.11.11.61.71.71.71.71.71.31.31.31.31.31.31.11.11.10.410.460.460.460.420.410.390.410.450.410.440.410.440.380.410.410.440.410.400.380.370.420.410.420.410.390.390.400.400.390.420.450.440.400.390.200.160.390.200.620.360.210.150.410.210.390.390.3961.251.000.750.500.250.00铁姆肯公司样本方法铁姆肯公司先进专有方法DIN 281.1 DIN 281.4 图 2. 厚膜结果,可靠度达90%铁姆肯公司样本方法铁姆肯公司先进专有方法DIN 281.1 DIN 281.4 1.751.501.251.000.750.500.250.00图 3. 薄膜结果,可靠度达90%铁姆肯公司样本方法铁姆肯公司先进专有方法DIN 281.1 DIN 281.4 1.251.000.750.500.250.00L 15.91——预测值 / L 15.91——测试值图 4. 不对中结果,可靠度达 90%L 15.91——预测值 / L 15.91——测试值L 15.91——预测值 / L 15.91——测试值铁姆肯公司样本方法铁姆肯公司先进专有方法DIN 281.1 DIN 281.4 3.002.502.001.501.000.500.00L 15.91——预测值 / L 15.91——测试值7.006.005.004.003.002.001.000.00L 15.91——预测值 / L 15.91——测试值1.251.000.750.500.250.00加权总误差图 6. 碎屑压痕结果,可靠度达 90%图 7. 采用加权总误差的总体结果图 5. 不同负荷,可靠度达 90%结果讨论 厚膜和薄膜的结果显示:在预测方法和试验数据之间显示出相对好的一致性。