表面粗糙度及检测
表面粗糙度及检测新
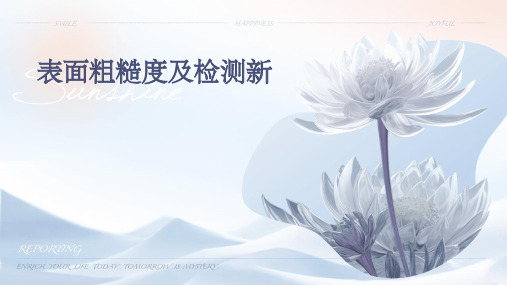
05
表面粗糙度检测新技术的 挑战与展望
技术挑战
检Hale Waihona Puke 精度表面粗糙度检测需要高精度的测量 技术,以获得 准确的表面形貌信息。
动态范围
表面粗糙度检测需要覆盖较大的动态范围,以满 足不同表面粗糙度测量的需求。
实时性
对于在线检测和质量控制,需要实现快速、实时 的表面粗糙度检测。
发展趋势与展望
智能化
利用人工智能和机器学 习技术,实现表面粗糙 度检测的自动化和智能
表面电阻测量法
表面电阻测量法是一种利用表面电阻原理测量表面粗糙度的方法。
通过测量样品表面的电阻值,可以推算出表面粗糙度的大小。该方法适用于导体材 料的表面粗糙度测量。
表面电阻测量法的优点是操作简便、成本低廉,但其准确度受环境温度、湿度等因 素的影响较大,且只适用于导体材料的表面粗糙度测量。
04
表面粗糙度检测新技术的 应用
在生物医学领域的应用
表面粗糙度检测新技术在生物医学领域的应用主要涉及医疗器械、人工关节、牙 科植入物等与人体直接接触的医疗产品的表面质量检测。
表面粗糙度对于医疗产品的生物相容性和使用寿命具有重要影响。通过表面粗糙 度检测新技术,可以评估医疗产品表面的细胞生长、蛋白质吸附和血液相容性, 为医疗产品的研发和改进提供有力支持。
表面粗糙度的影响因素
加工方法和工艺参数
不同的加工方法和工艺参数会对表面粗糙度产生影响, 如切削速度、进给量、刀具角度等。
材料性质
材料的硬度、韧性、热处理状态等对表面粗糙度有较 大影响。
环境因素
环境温度、湿度、清洁度等也会对表面粗糙度产生影 响。
表面粗糙度的应用
提高表面耐磨性
表面粗糙度可以影响表面的接触刚度和应力分布,从而提高表面 的耐磨性。
第三章--表面粗糙度及检测
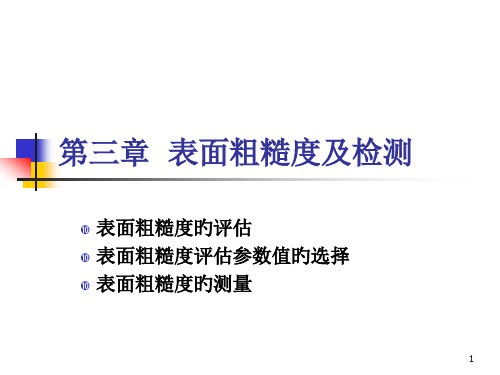
第二节 表面粗糙度评估参数值旳 选择
评估参数值旳选择
总原则:在满足功能要求旳前提下,尽量选择较大旳表 粗糙度参数值,以减小加工难度,降低成本。
选择措施:类比法。 一般原则: (1)同一零件上工作表面比非工作表面粗糙度参数值小。 (2)摩擦表面比非摩擦表面旳粗糙度参数值小,滚动摩擦 表面比滑动摩擦表面旳粗糙度参数值小。 (3)承受交变载荷旳表面及易引起应力集中旳部分(如圆 角,沟槽)粗糙度参数值应小些。
t
p
p
l
100%
1 l
n i 1
bi
100%
S、Sm和tp称为间距参数,值越小,轮廓表面越细密,密 封性愈好。
13
第一节 表面粗糙度旳评估
❖评估参数旳数值
原则要求:当Ra为0.025~6.3μm或Rz为0.100 ~25μm范围时,应优先 选用Ra参数。 Ra <0.025μm, Ra >6.3μm时,用光学仪器测量比较适 合,因而应选用Rz 。
个最大旳轮廓谷深平均值之和:
5
5
y pi yvi
Rz i1
i 1
5
Rz
(h2
h4
h10 ) (h1 5
h3
h9 )
Rz值越大,表面越粗糙。
10
第一节 表面粗糙度旳评估
(3)轮廓最大高度Ry 在取样长度内,轮廓峰顶线和轮廓谷底线之间旳距离。
Ra、Rz和Ry称为表面粗糙度旳高度参数。
11
要求:国标推荐, ln=5l;对均匀性好旳表面,可选ln<5l;对均匀 性较差旳表面,可选ln> 5l。
5
第一节 表面粗糙度旳评估
取样长度、评估长度和轮廓中线
6
Hale Waihona Puke 第一节 表面粗糙度旳评估(3)中线 中线是指用以评估表面粗糙度参数旳一条基准线。
表面粗糙度与检测(新国标)
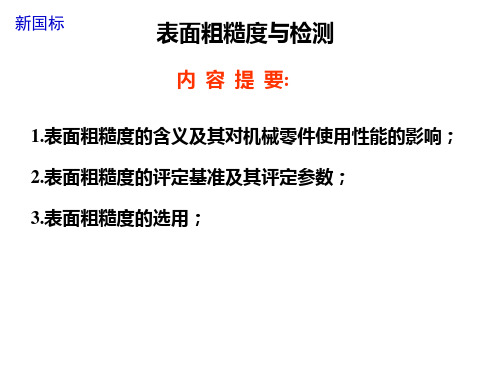
Rmr ( c ) =
∑
i =1
bi
ln
= Ml ( C ) / l n
C = Rz %
图5.8 轮廓的支承长度率
表面粗糙度评定参数共 4个: 个
基本参数 2个 附加参数 (辅助参数 辅助参数) 辅助参数 2个
Ra —轮廓算术平均偏差 轮廓算术平均偏差 Rz —轮廓最大高度 轮廓最大高度 RSm — 轮廓单元平均宽度 Rmr(c) —轮廓支承长度率 轮廓支承长度率
3. 中线 指具有几何轮廓形状并划分轮廓的基准线 中线—指具有几何轮廓形状并划分轮廓的 指具有几何轮廓形状并划分轮廓的基准线 轮廓算术平均中线:在取样长度内,划分实际轮廓为上、 轮廓算术平均中线:在取样长度内,划分实际轮廓为上、 下两部分面积相等的线
图5.5 轮廓中线
二. 评定参数 1. 幅度参数(高度参数) 幅度参数(高度参数) (1)轮廓的算术平均偏差 )轮廓的算术平均偏差Ra 在取样长度lr内 纵坐标值 在取样长度 内,纵坐标值Z(x)的绝对值的算术平均值 的绝对值的算术平均值
Z v2
x
Z vmax
最大高度Rz 最大高度
2. 间距参数 轮廓单元: 轮廓单元 一个轮廓峰和相邻轮廓谷的组合。 一个轮廓峰和相邻轮廓谷的组合。 轮廓单元宽度Xsi: 中线与一个轮廓单元相交线段的长度。 轮廓单元宽度 中线与一个轮廓单元相交线段的长度 相交线段的长度。 轮廓单元的平均宽度 RSm:
新国标
表面粗糙度与检测
内 容 提 要:
1.表面粗糙度的含义及其对机械零件使用性能的影响; 表面粗糙度的含义及其对机械零件使用性能的影响; 表面粗糙度的含义及其对机械零件使用性能的影响 2.表面粗糙度的评定基准及其评定参数; 表面粗糙度的评定基准及其评定参数; 表面粗糙度的评定基准及其评定参数 3.表面粗糙度的选用; 表面粗糙度的选用; 表面粗糙度的选用
机械加工表面粗糙度解释及测量

較低的光潔度對于盡快加工零件和盡量減 少輔助工作量有明顯的經濟效益。何況 在某些用途中﹐一定的粗糙性可以提高 零件的功能﹐有些零件甚至明確規定了 最大和最小粗糙度的值。舉例來說﹐具 有一定粗糙度的表面常常可以增加漆層 或其它涂敷層的黏附性。
有些多功能零件要求很復雜的表面﹐才能 最好地發揮作用。比如發動機的汽缸內 壁必須足夠光滑﹐以便為活塞環提供良 好的密封表面﹐利于壓縮﹐並防止漏氣 。同時﹐表面上還必須具有尺寸﹑數量 和分布都合適的凹點﹐為的是保持潤滑 油。
Ry(ISO,JIS)
全粗糙度高度(最大高度)---Ry(ISO,JIS); Ry=(Peakmax-Valleymin)sampling
length
Ry(DIN)
全粗糙度高度(最大高度)--Ry(DIN); 在各取樣長度內, 求出各Zi, 而在各 Zi中最大值稱為Ry(DIN)=Rmax;
•Rmax對零件表面的劃傷﹑毛刺之類的缺 陷非常敏感﹐很適合于檢驗這樣的狀態 。然而﹐由于生產過程中的個別劃痕或 毛刺往往不具有代表性﹐所以Rmax不適 于監控工序的穩定性
.(Rmax)
Rq
粗糙度幾何(平方)平均值 (Root mean square roughness, Rq)
下圖所示, Rq=(1/N Σyi2)1/2
Rt
最大高度---Rt, 由全體評價長度算出, Rp 和Rv之和. Rt=(PeakmaxValleymin)assessment length
b. Shoe/Skid VS Skidless type stylus 之用法不同: 如圖所示
Shoe/Skid type:滑動器半徑比波峰間隔 (Sm)大很多,使其運動幾乎成一直線。 若Sm過大則可用Shoe來支撐。優點易 於歸零.
表面粗糙度及检测
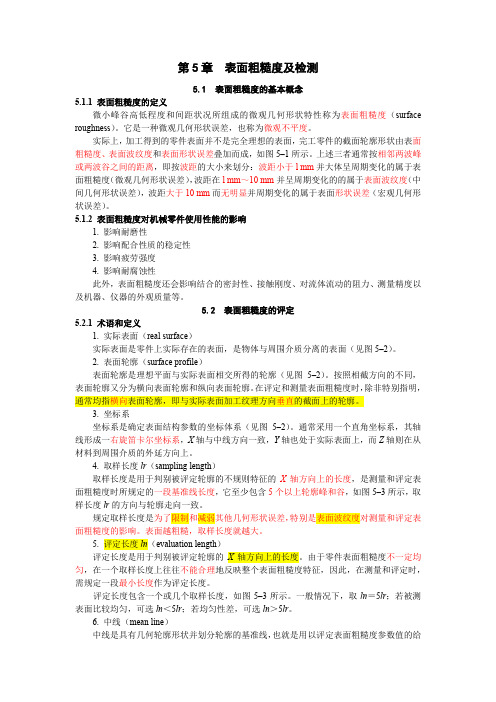
第5章表面粗糙度及检测5.1 表面粗糙度的基本概念5.1.1 表面粗糙度的定义微小峰谷高低程度和间距状况所组成的微观几何形状特性称为表面粗糙度(surface roughness)。
它是一种微观几何形状误差,也称为微观不平度。
实际上,加工得到的零件表面并不是完全理想的表面,完工零件的截面轮廓形状由表面粗糙度、表面波纹度和表面形状误差叠加而成,如图5–1所示。
上述三者通常按相邻两波峰或两波谷之间的距离,即按波距的大小来划分:波距小于l mm并大体呈周期变化的属于表面粗糙度(微观几何形状误差),波距在l mm~10 mm并呈周期变化的的属于表面波纹度(中间几何形状误差),波距大于10 mm而无明显并周期变化的属于表面形状误差(宏观几何形状误差)。
5.1.2 表面粗糙度对机械零件使用性能的影响1. 影响耐磨性2. 影响配合性质的稳定性3. 影响疲劳强度4. 影响耐腐蚀性此外,表面粗糙度还会影响结合的密封性、接触刚度、对流体流动的阻力、测量精度以及机器、仪器的外观质量等。
5.2 表面粗糙度的评定5.2.1 术语和定义1. 实际表面(real surface)实际表面是零件上实际存在的表面,是物体与周围介质分离的表面(见图5–2)。
2. 表面轮廓(surface profile)表面轮廓是理想平面与实际表面相交所得的轮廓(见图5–2)。
按照相截方向的不同,表面轮廓又分为横向表面轮廓和纵向表面轮廓。
在评定和测量表面粗糙度时,除非特别指明,通常均指横向表面轮廓,即与实际表面加工纹理方向垂直的截面上的轮廓。
3. 坐标系坐标系是确定表面结构参数的坐标体系(见图5–2)。
通常采用一个直角坐标系,其轴线形成一右旋笛卡尔坐标系,X轴与中线方向一致,Y轴也处于实际表面上,而Z轴则在从材料到周围介质的外延方向上。
4. 取样长度lr(sampling length)取样长度是用于判别被评定轮廓的不规则特征的X轴方向上的长度,是测量和评定表面粗糙度时所规定的一段基准线长度,它至少包含5个以上轮廓峰和谷,如图5–3所示,取样长度lr的方向与轮廓走向一致。
表面粗糙度与检测(新国标)

传输带
补充要求
取样长度 加工工艺
加工余量等。
表面粗糙度要求标注的内容在图中注写的位置,见图 5.10所示。
图5.10 粗糙度要求的注写的位置
a —第一个表面粗糙度(单一)要求(μm); b — 第二个表面粗糙度要求(μm); c — 加工方法(车,铣); d— 表面纹理和纹理方向; e— 加工余量(mm)。
② 传输带和取样长度 的标注:传输带是指 两个滤波器的截止波 长值之间的波长范围。 长波滤波器的截止波
长值就是取样长度ln。
图5.11 表面粗糙度的单一要求标注示例
传输带的标注时,短波在前,长波在后,并用连字号“—”隔开。 在某些情况下,传输带的标注中,只标一个滤波器,也应保留连字号 “—” ,来区别是短波还是长波。
(4)影响抗腐蚀性;
5.2 表面粗糙度的评定
一. 基本术语 1. 取样长度 lr----基准线长度。至少含5个波峰和波谷 2. 评定长度ln--最小的测量长度。至少包括5个取样长度lr
图5.4 取样长度和评定长度
3. 中线—指具有几何轮廓形状并划分轮廓的基准线 轮廓算术平均中线:在取样长度内,划分实际轮廓为上、 下两部分面积相等的线
3. 表面粗糙度要求在图样上的标注方法
标注方向与 尺寸相同
指引线上标 注
3. 表面粗糙度要求在图样上的标注方法
标注在几 何公差框
格上方
标注在延 长线上
3. 表面粗糙度要求在图样上的标注方法
其余要求标注在标题 栏附近
(给出基本符号)
3. 表面粗糙度要求在图样上的标注方法
全部要求标 注在标题栏
3. 混合参数(形状参数) 轮廓的支承长度率Rmr(C) —
在给定的水平位置C上,轮廓的实体材料长度Ml(C)与评定长度ln的比率。
表面粗糙度及检测

第六章表面粗糙度及检测第一节概述用任何方法获得的零件表面,都不会绝对的光滑平整,总会存在着由较小间距的峰和谷组成的微观高低不平。
这种加工表面上具有的微观几何形状误差称为表面粗糙度。
它主要是在加工过程中,由于刀具切削后留下的刀痕、切屑分离时的塑性变形、工艺系统中存在高频振动及刀具和零件表面之间的磨擦等原因所形成的。
表面粗糙度对零件的功能要求、使用寿命、可靠性及美观程度均有直接的影响。
为了正确地测量和评定零件表面粗糙度,自从1956年颁布了第一个表面光洁度标准JB 50-56以来,我国对表面粗糙度国家标准已进行了多次修订,现在实施的相关标准主要有GB/T3505-2000《产品几何技术规范(GPS)表面结构轮廓法表面结构的术语、定义及参数》(代替GB/T3505-2000)、GB/T1031-2009《产品几何技术规范(GPS)表面结构轮廓法表面粗糙度参数及其数值》(代替GB/T 1031-1995)、GB/T 10610-2009《产品几何技术规范(GPS)表面结构轮廓法评定表面结构的规则和方法》(代替GB/T 10610-1998)、GB/T131-2006《产品几何技术规范(GPS)技术产品文件中表面结构的表示法》(代替GB/T 131-1993《机械制图表面粗糙度符号、代号及其注法》)、GB/T 6062-2009《产品几何技术规范(GPS)表面结构轮廓法接触(触针)式仪器的标称特性》(代替GB/T 6062-2002)。
本章将对上述标准的主要内容进行介绍。
一、表面粗糙度轮廓的界定物体与周围介质分离的表面称为实际表面。
为了研究零件的表面结构,通常用垂直于零件实际表面的平面与该零件实际表面相交所得到的轮廓作为评估对象。
该轮廓称为表面轮廓,它是一条轮廓曲线,如图6.1所示。
图6.1零件的实际表面与表面轮廓加工以后形成的零件的实际表面一般处于非理想状态,其截面轮廓形状是复杂的,同时存在各种几何形状误差。
4.3表面粗糙度数值的选择及检测

三、表面粗糙度轮廓参数允许值的选择原则:
在满足零件表面功能要求的前提下,尽量选取较大的参数值。 (1)同一零件上工作表面粗糙度值,比非工作表面粗糙度值小。
工作表面
非工作表面
(2)摩擦表面粗糙度值比非摩擦表面粗糙度值小; 滚动摩擦表面比滑动摩擦表面的表面粗糙度参数值要小; 运动速度高、压力大的摩擦表面比运动速度低、压力小的摩擦
4-3 R轮廓参数的选用及其检测
一.表面粗糙度轮廓技术要求的内容
1、必须标注参数符号及允许值,同时还应标注传输带、取样长 度、评定长度的数值(若默认采用标准化值,则不标注)、极限 值判断规则(若默认采用16%规则,则不标注)。
2、必要时可以标注补充要求,如表面加工纹理及方向、加工余量、 附加的Rsm等。
表面的粗糙度参数值要小。
(3)受循环载荷的数值要小。
(4)配合要求高的结合表面、配合间隙小的配合表面及要求连接 可靠且受重载的过盈配合表面,均应取较小的粗糙度参数值。
(5)配合性质相同时,一般情况下,零件尺寸越小,则表面粗糙 度参数值应越小;在同一精度等级时,小尺寸比大尺寸,轴比孔 的表面粗糙度参数值要小;尺寸公差,表面形状公差小时,其表 面粗糙度参数值要小。
二.表面粗糙度轮廓参数的选择
1、通常只给出幅度参数符号(Ra或Rz)及极限值,而其他要求则 采用默认的标准化值。
2 、 一般采用Ra 作为评定参数。对于极光滑和粗糙的表面和零件材料 较软时,不能用Ra仪器测量,而采用Rz作为评定参数。
3 、 附加参数Rsm用于密封性要求高的表面,Rmr(c)用于耐磨性 要求高的表面。
(6)防腐性、密封性要求越高,表面粗糙度参数值应越小。
四、表面粗糙度轮廓常用测量方法
比较法 针描法 光切法 显微干涉法
- 1、下载文档前请自行甄别文档内容的完整性,平台不提供额外的编辑、内容补充、找答案等附加服务。
- 2、"仅部分预览"的文档,不可在线预览部分如存在完整性等问题,可反馈申请退款(可完整预览的文档不适用该条件!)。
- 3、如文档侵犯您的权益,请联系客服反馈,我们会尽快为您处理(人工客服工作时间:9:00-18:30)。
Rsm
互换性与技术测量
1 n Sm n i 1 i
21
第四章 表面粗糙度及检测
轮廓支承长度率 Rmr(c)
(综合参数) 实体材料长度Ml(c) (平行于中线且与峰顶线距离为 c 的直线, 与轮廓相截所得的各段截线长度之和)与评定长度 ln之比
Rmr (c)
互换性与技术测量
Ml (c) Ml1 Ml2 100% ln ln
第四章 表面粗糙度及检测
22
11
2013/11/22
Rmr(c)曲线
•与表面粗糙度的形状有关 •数值大小对应于不同的水平截距c •反映接触面的大小,与承载和磨损有关
互换性与技术测量 第四章 表面粗糙度及检测 23
• • • • •
表面粗糙度的基本概念 表面粗糙度的评定参数 表面粗糙度的参数选用 表面粗糙度的标注 表面粗糙度的测量
零件配合性质的稳定性
• 加大间隙配合的实际间隙 • 减小过盈(过度)配合的有效过盈
配合变松
零件的疲劳强度
• 深纹应力集中 交变载荷
易疲劳断裂
互换性与技术测量
第四章 表面粗糙度及检测
10
5
2013/11/22
基本术语
轮廓中线: 穿过表面轮廓的 段参考线 评定表面粗 穿过表面轮廓的一段参考线,评定表面粗 糙度的基准线,有以下两种:
b—加工方法、镀覆、涂覆、表面处理或其它说明等 c—取样长度(mm)或波纹度(mm) d—加工纹理方向符号 e—加工余量(mm) f—间距参数Rsm值( μm)或综合参数Rmr(c)值(%)
第四章 表面粗糙度及检测 34
互换性与技术测量
17
2013/11/22
表面纹理标注(1)
互换性与技术测量
第四章 表面粗糙度及检测
互换性与技术测量 第四章 表面粗糙度及检测 27
标准评定参数值Ra、Rz
互换性与技术测量
第四章 表面粗糙度及检测
28
14
2013/11/22
标准评定参数值Rsm、Rmr(c)
互换性与技术测量
第四章 表面粗糙度及检测
29
lr、ln与Ra、Rz
互换性与技术测量
第四章 表面粗糙度及检测
30
15
2013/11/22
高度参数
当选用Ra时,只需标参数值,“Ra”可以省略 当选用Rz时,参数和参数值都应标出
表面加工纹理方向
表面微观结构的主要方向 由所采用的加工方法或其它因素形成 必要时才规定
第四章 表面粗糙度及检测
互换性与技术测量
38
19
2013/11/22
标注举例
互换性与技术测量
第四章 表面粗糙度及检测
– 幅度(高度)参数(轮廓起伏) : 轮廓算术平均偏差 Ra 轮廓的最大高度 Rz – 间距参数(轮廓疏密) : 轮廓单元的平均宽度 Rsm – 综合参数(轮廓形状) : 轮廓的支承长度率 Rmr(c)
互换性与技术测量
第四章 表面粗糙度及检测
17
轮廓算术平均偏差 Ra
(幅度参数) 取样长度内,轮廓各点至中线距离绝对值的算术平均值
互换性与技术测量
第四章 表面粗糙度及检测
41
表面粗糙度的比较法测量
将被测表面和表面粗糙度样板直接进行比较,多用于车 间 评定表面粗糙度值较大的工件 间,评定表面粗糙度值较大的工件。
互换性与技术测量
第四章 表面粗糙度及检测
42
21
2013/11/22
表面粗糙度的光切法测量
光切原理,双管显微镜测量。常用于测量0.8~100μm的Rz值。
39
• • • • •
表面粗糙度的基本概念 表面粗糙度的评定参数 表面粗糙度的参数选用 表面粗糙度的标注 表面粗糙度的测量
互换性与技术测量
第四章 表面粗糙度及检测
40
20
2013/11/22
表面粗糙度的测量
比较法:将被测表面和表面粗糙度样板直接进行比较, 多用于车间,评定表面粗糙度值较大的工件。 光切法:利用光切原理,用双管显微镜测量。 常用于 测量0.8~100μm的Rz值。 干涉法:利用光波干涉原理,用干涉显微镜测量。适 于测量0.025~0.8μm 的Rz值。 针描法:利用触针直接在被测表面上轻轻划过,测出 针描法 利用触针直接在被测表面上轻轻划过 测出 表面粗糙度的Ra值。如电动轮廓仪,适于测量0.025~ 5μm 的Ra值。
35
表面纹理标注(2)
互换性与技术测量
第四章 表面粗糙度及检测
36
18
2013/11/22
表面纹理标注(3)
互换性与技术测量
第四章 表面粗糙度及检测
37
标注原则
标注符号的位置与指向
位置:可见轮廓线、尺寸界线、引出线或它们的 位置 可见轮廓线 尺寸界线 引出线或它们的 延长线上 指向:符号尖端必须从材料外指向被注表面
评定长度 ln:
评定表面轮廓时所必需的一段长度 评定长度可包括一个或多个取样长度 不均匀的表面,宜选用较长的评定长度 评定长度一般按5个取样长度来确定:ln = 5lr
互换性与技术测量 第四章 表面粗糙度及检测 14
7
2013/11/22
取样长度lr和评定长度ln
基准线 (中线)
间距参数Rsm与综合参数Rmr(c)
设立的必要性
粗糙度轮廓的疏密度和形状影响零件: 密封性 粘结性 耐磨性 抗腐蚀性等 密封性、粘结性、耐磨性、抗腐蚀性等
互换性与技术测量
第四章 表面粗糙度及检测
20
10
2013/11/22
轮廓单元的平均宽度 Rsm
(间距参数) 轮廓单元宽度(含有一个轮廓峰和相邻轮廓谷的中线长度) 在取样长度lr l 内的平均值
2013/11/22
第四章
表面粗糙度及检测
陈津平 博士 副教授 精密仪器与光电子工程学院 chenjinping@tju edu cn chenjinping@
相关标准
• GB/T3505 T3505-2009 2009《产品几何技术规范(GPS) 表面结构轮廓法 术语、定义及表面结构参数》 • GB/T1031-2009《产品几何技术规范(GPS) 表面结构轮廓法 表面粗糙度参数及其数值》 • GB/T131-2006《产品几何技术表规范(GPS) 技术产品文件中表面结构表示法》
a为基本符号,表示表面可以用任何方法获得 b表示表面是用去除材料的方法获得的 c表示表面是用不去除材料的方法获得的
a
互换性与技术测量
b
c
第四章 表面粗糙度及检测 33
标注代号
• a1、a2—高度参数代号及最大、最小允许数值(μm)
(一般只在 ( 般只在a2 处标最大值)
• • • • •
轮廓最小二乘中线: 使轮廓上各点至该线的距离平方和为最小。 轮廓算术平均中线 使轮廓在该线上下两部分面积相等。
互换性与技术测量
第四章 表面粗糙度及检测
11
轮廓最小二乘中线
y —— 轮廓偏距
y
i 1
n
2 i
min
12
互换性与技术测量
第四章 表面粗糙度及检测
6
2013/11/22
轮廓算术平均中线
F
1
F
2
y=f(x)
Fn
0 G1 G2 L Gm
x
F1+F2+…+Fn= G1+G2+…+Gm
互换性与技术测量 第四章 表面粗糙度及检测 13
基本术语
取样长度 lr:
评定表面粗糙度所规定的一段基准线(中线)长度 评定表面粗糙度所规定的 段基准线(中线)长度 一般在一个取样长度内应包含5个以上的波峰和波谷 限制和削弱表面波纹度对表面粗糙度测量结果的影响 数值上等于λc 滤波器的标志波长:lr = λc
互换性与技术测量
第四章 表面粗糙度及检测
24
12
2013/11/22
评定参数的选择
如无特殊要求,一般仅选用高度参数 高度参数相同时,轮廓疏密度或形状不同,表面 特性也不同:
轮廓疏密度 轮廓形状 影响 密封性、粘结性 影响 耐磨性、抗腐蚀性 反映 轮廓疏密度 反映 轮廓形状
非高度参数的选择
Ra
lr
1 lr Ra y ( x ) dx lr 0
互换性与技术测量
1 n Ra yi n i 1
18
第四章 表面粗糙度及检测
9
2013/11/22
轮廓的最大高度 Rz
(幅度参数) 取样长度内,轮廓峰顶线和谷底线之间的距离
lr
Rz y p max y v max
互换性与技术测量 第四章 表面粗糙度及检测 19
间距参数Rsm 综合参数Rmr(c)
互换性与技术测量
第四章 表面粗糙度及检测
25
评定参数的选择
如无特殊要求,一般仅选用高度参数:
优先选用Ra( 0.025 μm ~ 6.3μm )
能充分反映零件表面轮廓特征
当表面过于粗糙(Ra>6.3μm) 或过于光滑( Ra< 0.025 μm )时,可选用Rz
表面粗糙度的成因
机械加工的: 切削刀痕 切屑分离时的塑性变形 加工系统的振动 刀具与工件表面的摩擦 ……
互换性与技术测量
第四章 表面粗糙度及检测
9
对零件性能的影响
零件的耐磨性
• 摩擦系数大 • 接触面积小 • 压强大
表面粗糙度大 加快磨损
抗腐蚀性 密封性 外观 测量精度 表面光学性能 导电导热性能 胶合强度 ……