一氧化碳变换催化剂的选用
一氧化碳变换催化剂的应用与发展(上)
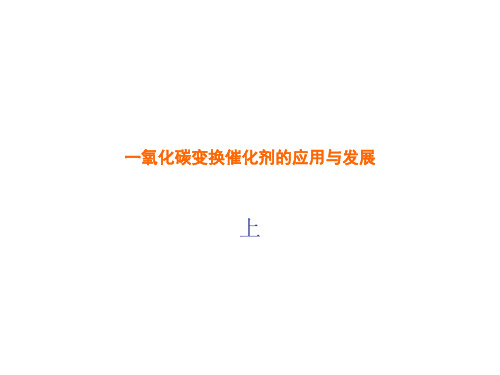
Page 8
LOGO
一氧化碳变换催化剂的应用与发展
1.2.4 Sod—Chemie公司
SOd.Chemie公司在其传统Fe—Cr型高温变换催化剂C12—3/G一3的基础
上加少量铜助剂,开发面成新一代产品C12—4/G.3C。C12-4/G一3C催化
剂在氧化态下的抗压碎强度为150 N,在还原态下为,能承受开车条件F的应力。 本体含硫量极低,可大大缩短开车时间。这种催化剂在汽/气比为0.4~0.5、 CO/C02大约为2的条件下基本无烃类生成。其适宜的入口温度可低至320℃, 有助于抑制Fe晶粒长大而引起的减活作用,
率,残留CO经甲烷化CO和C02含量均在10 mL/Nm3以下,勿需用复杂的铜洗 或氨洗工艺,简化流程,已成为典型制氨工艺。
艺。
Page 10
LOGO
万方
Page 9
LOGO
一氧化碳变换催化剂的应用与发展
2低温变换催化剂
美国制氨工业采用低温变换工艺始于1963年。我国在1965年将低温变 换工艺用于以煤为原料的中型氨厂,并把低温变换、氧化锌脱硫及甲烷化三 种工艺相结合。由于高温变换后出口气体中仍含有3%~4%的CO,铜系催化剂
在180~260℃可使CO进一步降至0.2%~O.4%,从而提高H2或NH3的产
铬,并且本体硫含量极低,能使F-T副产物的量减少到原来
生成量的10%以下。
Page 7
LOGO
一氧化碳变换催化剂的应用与发展
1.2.3 BASF巴斯夫公司
德国BASF公司在其经典催化剂K6.10基础上,开发了一种加铜的 Fe.Cr基高温变换催化剂K6—1l,此催化剂能在低H20/C下操作, 适宜的入口的温度为330℃,CO适宜的入口的浓度为I 1.5%(m01), 出口浓度为2.4%~2.8%(m01),在此条件下生成的C2~C4烃类 副产物的总量大约为3×10‾6。
浅谈变换催化剂和变换炉的选择

浅谈变换催化剂和变换炉的选择摘要:变换工艺根据所选用的催化剂是否耐硫,将变换工艺分为耐硫变换和非耐硫变换工艺。
变换反应的顺利进行主要取决于两方面的因素,催化剂和变换炉。
本文通过介绍不同类型变换催化剂和变换炉的发展、应用及优缺点,为广大化工同行在变换催化剂和变换炉的选择上提供帮助。
关键词:变换工艺;变换催化剂;变换炉1变换催化剂的选择通常使用的催化剂有高温变换催化剂、低温变换催化剂和宽温耐硫变换催化剂。
1.1高温变换催化剂高温变换催化剂其活性相是由Fe2O3部分还原得到的Fe3O4。
在实际应用过程中,高温烧结导致Fe3O4表面积下降,引起活性的急剧下降,造成纯Fe3O4的活性温区很窄,耐热性很差。
因此常加入结构助剂提高其耐热性,防止烧结引起的活性下降。
由于铁铬系高温变换催化剂中铬是剧毒物质,造成在生产、使用和处理过程中对人员和环境的污染及毒害,但工业化与应用业绩较少。
高温变换催化剂的粉化是它的一个主要问题。
催化剂的更换往往不是由于活性丧失,而是由于粉化造成过大的压差。
部分催化剂的粉化,引起气流不均匀,也将导致转化率下降。
蒸汽消耗较高,有最低水气比要求,要求变换入口水气比在1.4以上,变换后的水气比应大于0.8,导致过剩蒸汽冷凝量过多、能耗增加,不宜选用。
1.2低温变换催化剂低变催化剂的最大特点就是活性温度低,在200~260℃的范围内,变换反应就能迅速进行。
低变催化剂对硫化物极为敏感,由于生成铜盐而永久性中毒。
氯或氯离子也引起永久性中毒,这是由于催化剂发生结晶而引起的。
另外,原料气中的不饱和烃可能在催化剂表面析炭或结焦。
1.3宽温耐硫变换催化剂钴钼系耐硫宽温变换催化剂具有很高的低温活性,它比铁系高温变换催化剂起活温度低100~150℃,甚至在160℃就显示出优异的活性,与铜系低温变换催化剂相当,且其耐热性能与铁铬系高温变换催化剂相当,因此具有很宽的活性温区,几乎覆盖了铁系高温变换催化剂和铜系低温变换催化剂整个活性温区。
CO变换技术选择
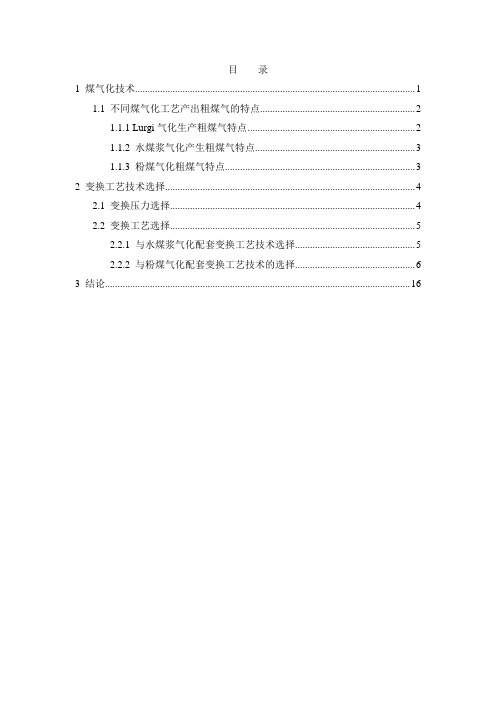
目录1 煤气化技术 (1)1.1 不同煤气化工艺产出粗煤气的特点 (2)1.1.1 Lurgi气化生产粗煤气特点 (2)1.1.2 水煤浆气化产生粗煤气特点 (3)1.1.3 粉煤气化粗煤气特点 (3)2 变换工艺技术选择 (4)2.1 变换压力选择 (4)2.2 变换工艺选择 (5)2.2.1 与水煤浆气化配套变换工艺技术选择 (5)2.2.2 与粉煤气化配套变换工艺技术的选择 (6)3 结论 (16)近年来以煤为原料生产合成氨、甲醇的煤化工技术得到大力发展,其中以加压水煤浆气化配套CO耐硫变换制备变换气的典型流程的应用尤为普遍。
在煤气化配套装置中,一氧化碳变换装置通过变换反应调节气化装置产出粗煤气的氢/碳,满足下游产品的需要,其工艺技术的选择,既要结合不同气化工艺产出的粗煤气的特点,也要考虑到后续装置及下游产品的要求。
各种气化工艺产出的粗煤气的组成相差较大,即便针对下游同一产品,与不同气化工艺配套的变换工艺技术也不尽相同。
变换工艺的选择,除了应适应粗煤气组成及满足产品要求以外,还应考虑安全及节能等问题。
安全方面,重点应避免变换炉的超温;节能方面,重点应减少蒸汽用量及有效利用余热。
根据目前大中型厂的变换工艺在整个净化工艺中的配置情况来看,变换使用的催化剂和热回收方式是关键,它决定了变换工艺的流程配置及工艺先进性。
1 煤气化技术煤气化技术的采用起始于18世纪末,现在已经开发了许多不同的技术。
这些技术最重要的特征是氧化剂与煤颗粒接触的方式,它决定了给料方式、煤粒大小以及煤在气化炉中停留的时间。
根据氧化剂与煤颗粒相对流动的方式,气化炉一般分为3种类型:(1)逆流——移动床或固定床,如UGI、Lurgi;(2)并逆流——流化床或沸腾床,如温克勒、HTW、恩德炉和灰熔聚炉;(3)并流——气流床、喷流床、夹带床,如KT、Texaco、Shell、GSP炉。
UGI气化炉是最老的气化炉,这种气化技术国外早已淘汰,但在我国煤气化工艺中仍占主要地位。
一氧化碳变换反应温度
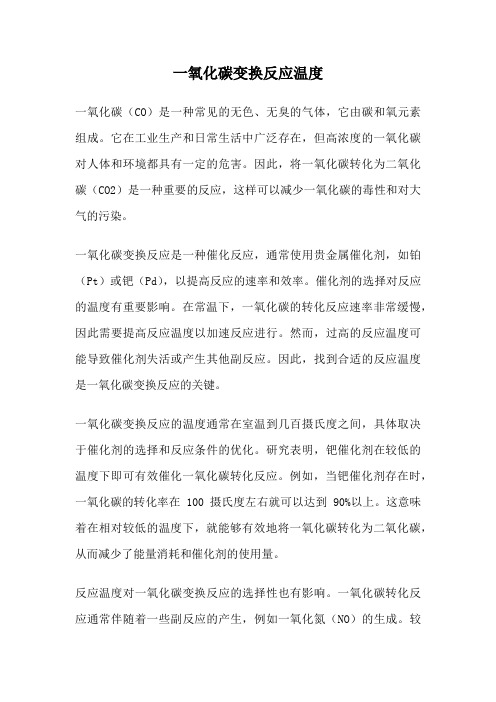
一氧化碳变换反应温度一氧化碳(CO)是一种常见的无色、无臭的气体,它由碳和氧元素组成。
它在工业生产和日常生活中广泛存在,但高浓度的一氧化碳对人体和环境都具有一定的危害。
因此,将一氧化碳转化为二氧化碳(CO2)是一种重要的反应,这样可以减少一氧化碳的毒性和对大气的污染。
一氧化碳变换反应是一种催化反应,通常使用贵金属催化剂,如铂(Pt)或钯(Pd),以提高反应的速率和效率。
催化剂的选择对反应的温度有重要影响。
在常温下,一氧化碳的转化反应速率非常缓慢,因此需要提高反应温度以加速反应进行。
然而,过高的反应温度可能导致催化剂失活或产生其他副反应。
因此,找到合适的反应温度是一氧化碳变换反应的关键。
一氧化碳变换反应的温度通常在室温到几百摄氏度之间,具体取决于催化剂的选择和反应条件的优化。
研究表明,钯催化剂在较低的温度下即可有效催化一氧化碳转化反应。
例如,当钯催化剂存在时,一氧化碳的转化率在100摄氏度左右就可以达到90%以上。
这意味着在相对较低的温度下,就能够有效地将一氧化碳转化为二氧化碳,从而减少了能量消耗和催化剂的使用量。
反应温度对一氧化碳变换反应的选择性也有影响。
一氧化碳转化反应通常伴随着一些副反应的产生,例如一氧化氮(NO)的生成。
较高的反应温度可能导致一氧化氮的生成增加,从而降低了一氧化碳的转化率。
因此,在优化反应温度时,不仅需要考虑反应速率,还需要考虑反应的选择性,以实现高效的一氧化碳转化。
反应温度还与反应系统的热力学平衡有关。
一氧化碳转化反应是一个可逆反应,根据Le Chatelier原理,在较高的温度下,反应平衡会偏向生成较少的产物,即一氧化碳。
因此,在选择反应温度时,需要在反应速率和产物选择性之间进行权衡,以获得最佳的反应效果。
一氧化碳变换反应的温度选择是一个复杂而关键的问题。
合适的反应温度能够提高反应速率和选择性,减少能量消耗和催化剂的使用量。
钯催化剂在较低的温度下已经显示出良好的催化性能,为一氧化碳变换反应的实际应用提供了新的可能性。
co变换反应原理与催化剂

co变换反应原理与催化剂
答案:
CO变换反应是一种重要的化学反应,主要涉及一氧化碳(CO)与水蒸气在催化剂的作用下反应生成氢气(H2)和二氧化碳(CO2)。
这一反应在化工生产中具有广泛的应用,特别是在合成氨和尿素的生产过程中。
反应的化学方程式为:
CO+H2O→H2+CO2
这个反应是可逆的,意味着在一定的条件下,二氧化碳和氢气也可以逆向反应生成一氧化碳和水。
同时,这个反应是放热的,即在反应过程中会释放出热量。
由于这个反应在较高温度下进行时速度较慢,因此需要使用催化剂来加快反应速度。
在实际应用中,使用的催化剂包括铁铬系、铜锌系和钴钼系等,这些催化剂能够显著提高反应速率,使得一氧化碳能够更有效地转化为氢气和二氧化碳。
CO变换反应在工业生产中的应用非常广泛,特别是在合成氨的生产过程中。
由于一氧化碳不是合成氨的直接原料,而且能够使氨合成催化剂中毒,因此在送往合成工序之前,必须将一氧化碳脱除。
通过CO变换反应,可以将大部分一氧化碳转化为二氧化碳和氢气,从而满足合成氨等化工过程的需求。
此外,CO变换反应还在冶金工业和化学工业中用于处理含有一氧化碳的废气,通过加水变换的方式,利用催化剂将一氧化碳转化为无害的二氧化碳,从而达到环保和处理污染的目的。
总的来说,CO变换反应原理及其使用的催化剂在化工生产和环境保护中扮演着重要的角色,通过这一反应,可以有效处理含有一氧化碳的废气,同时为化工过程提供必要的原料气体。
一氧化碳的变换.
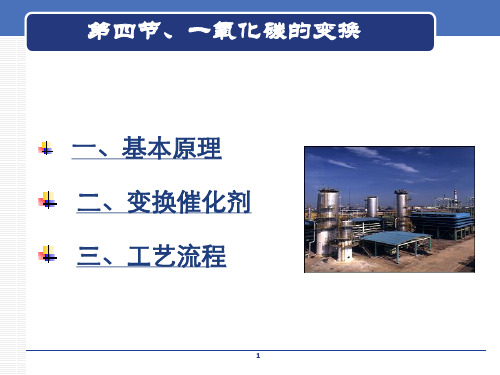
11
(二)、氧化锌法
❖氧化锌脱硫性能的好坏用硫容 量表示。所谓硫容就是每单位质 量氧化锌能脱除S的量。一些数 据如图所示。一些定性结论如下: 温度上升,硫容增加;空速增加, 硫容降低;汽气比上升,硫容下 降。
2、氧化锌脱硫剂:
100
ya,ya’ —分别为原料及变换气中一氧化碳的摩尔分率(干 基)
2
二、变换催化剂
❖ 1、中(高)变催化剂:
▪
以三氧化二铁为活性中心
▪ 铬、铜、锌、钴、钾等氧化物,可提高催化剂的活性
▪ 镁、铝等氧化物,可提高催化剂的耐热和耐毒性能。
❖ 目前常见的中(高)变换催化剂有:
▪ 铁铬系催化剂:以FeO3加Cr2O3为助催化剂。 ▪ 钴钼系催化剂:针对重油含S量高的耐高S变换催化剂。
K
0 p
pH2O
/
pH2S
10
❖ 一些条件下平衡S含量的计算值如下:
水蒸气含量/%
0.50 10 20
平衡硫含量/10-6 200℃ 0.000025 0.00055 0.005
300℃ 0.0008 0.018 0.16
400℃ 0.009 0.20 1.80
❖ 实际上天然气等原料中水蒸气含量很低,所以即使温度在400℃也可满足S含量 <0.1× 10-6的要求。 200℃含水20%时,S<0.005× 10-6,因此氧化锌也用在变 换工序作变换催化剂的保护剂。
提高其稳定性。 ❖ (2)低变催化剂的还原: ❖ CuO+H2=Cu+H2O △H0298=-86.7kJ/mol ❖ CuO+CO=Cu+CO2 △H0298=-127.7kJ/mol
甲醇原料气中一氧化碳的变换—变换工艺条件的选择
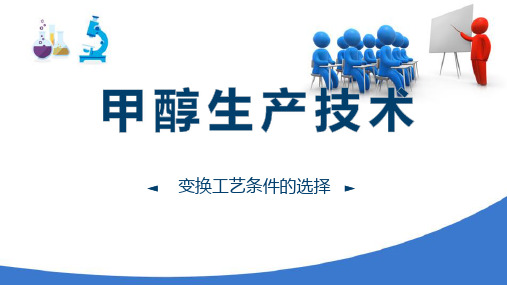
二、压力
压力对变换反应的平衡几乎没有影响,但加压可 提高反应速度和催化剂的生产能力,可采用较大的空 间速度,使设备紧凑,有利于过热蒸汽回收。由于干 原料气的物质的量小于干变换气物质的量,所以,先 压缩原料气进行加压变换的能耗,比常压变换后再压 缩变换气的能耗低15~30%,但加压变换需用压力较 高蒸汽,对设备材质要求高,所以一般小型合成氨厂 操作压力为0.8~1.2 MPa,中型厂为1.2~1.8MPa、 大型厂为3.0~8.0 MPa 。
✓ 如果进入中低变系统原料气中氧含量高,会引起催化剂活性组分与氧反 应,导致催化剂层的剧烈温升。同时,活性组分不同程度硫酸盐化造成 催化剂活性下降,所以各种变换催化剂入口气体中氧含量应小于0.5%。
三、汽气比
增加水蒸汽量,有利于提高CO的平衡变换率,降低CO残余含量, 加快反应速率,为此生产上均采用过量水蒸气。
• 过量水蒸汽的存在,抑制了析碳及甲烷化的副反应发生,保证了催化 剂活性组分Fe3O4的稳定而不被过渡还原,同时还起到载热体的作用, 使催化剂床层温升减小。所以,改变水蒸汽用量是调节床层温度的有 效手段。
五、出口气体中CO含量
✓ 小型氨厂中低变串联工艺指标是中变三段出口6%~8%,低变炉出口约 1.5%,以减轻原料气精制负荷;全低变工艺流程工艺指标是 一变炉出 口4%~7%,二变炉出口0.7%~1.5%,系统温度降低,出口一氧化碳 含量降低。总之,出口气体中一氧化碳含量应与后工序联合考虑。
六、入口气体中氧含量
变换工艺条件的选择
一、温度
变换反应存在最适宜温度
• 如果整个反应过程按最适宜温度曲线进行,则反应速率最大,在相同 的生产能力下所需催化剂用量最小,但实际生产完全按最适宜温度曲 线操作是不现实的。首先,反应开始时,最适宜温度很高,已超过了 中温变换催化剂允许使用的温度范围。其次,随着反应进行,要不断 移出反应热,使最适宜温度逐渐降低是极困难的。因此,变换过程的 操作温度应综合各方面因素来确定。
一氧化碳变换
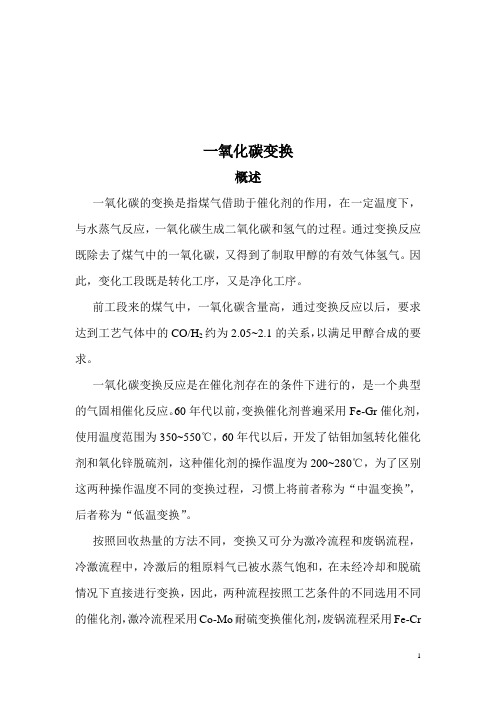
一氧化碳变换概述一氧化碳的变换是指煤气借助于催化剂的作用,在一定温度下,与水蒸气反应,一氧化碳生成二氧化碳和氢气的过程。
通过变换反应既除去了煤气中的一氧化碳,又得到了制取甲醇的有效气体氢气。
因此,变化工段既是转化工序,又是净化工序。
前工段来的煤气中,一氧化碳含量高,通过变换反应以后,要求达到工艺气体中的CO/H2约为2.05~2.1的关系,以满足甲醇合成的要求。
一氧化碳变换反应是在催化剂存在的条件下进行的,是一个典型的气固相催化反应。
60年代以前,变换催化剂普遍采用Fe-Gr催化剂,使用温度范围为350~550℃,60年代以后,开发了钴钼加氢转化催化剂和氧化锌脱硫剂,这种催化剂的操作温度为200~280℃,为了区别这两种操作温度不同的变换过程,习惯上将前者称为“中温变换”,后者称为“低温变换”。
按照回收热量的方法不同,变换又可分为激冷流程和废锅流程,冷激流程中,冷激后的粗原料气已被水蒸气饱和,在未经冷却和脱硫情况下直接进行变换,因此,两种流程按照工艺条件的不同选用不同的催化剂,激冷流程采用Co-Mo耐硫变换催化剂,废锅流程采用Fe-Cr变换催化剂。
第一节变换反应原理变换过程为含有C、H、O三种元素的CO和H2O共存的系统,在CO变换的催化反应过程中,除了主要反应CO+H2O=CO2+H2以外,在某种条件下会发生CO分解等其他副反应,分别如下:2CO=C+CO22CO+2H2=CH4+CO2CO+3H2=CH4+H2OCO2+4H2=CH4+2H2O这些副反应都消耗了原料气中的有效气体,生成有害的游离碳及无用的甲烷,避免副反应的最好方法就是使用选择性好的变换催化剂。
一、变换反应的热效应一氧化碳变换反应是一个放热反应,CO+H2O=CO2+H2+41kJ/gmol反应的热效应视H2O的状态而定,若为液态水,则是微吸热反应,若是水蒸气,则为放热反应。
变换反应的反应热随温度的升高而降低,具体反应热列表如下:表1 CO+H2O=CO2+H2的反应热温度℃25 200 250 300 350 400 450 500 550 △HkJ/gmol 41 39.8 39.5 39 38.5 38 37.6 37 36.6压力对变换反应的反应热影响较小,一般不做考虑。
- 1、下载文档前请自行甄别文档内容的完整性,平台不提供额外的编辑、内容补充、找答案等附加服务。
- 2、"仅部分预览"的文档,不可在线预览部分如存在完整性等问题,可反馈申请退款(可完整预览的文档不适用该条件!)。
- 3、如文档侵犯您的权益,请联系客服反馈,我们会尽快为您处理(人工客服工作时间:9:00-18:30)。
Page 2
LOGO
一氧化碳变换催化剂的选用
3.1 以煤为原料间歇制气铜液洗涤法净化 以煤为原料间歇制气制取的原料气半水煤气,虽经半水煤气脱硫但仍含有一定量
的硫;后续的铜洗净化一般要求CO含量1.2%左右较为经济。这些条件均适应
于铁铬中变催化剂和钴钼耐硫低变催化剂的使用,因此宣选用铁铬中变催化剂 (或耐硫型铁铬中变催化剂)串钴钼耐硫低变催化剂的中串低或中低低变换工艺: 或者放宽半水煤气脱硫要求,选用钴钼耐硫低变催化剂的全低变变换工艺,但应 选用改进型钴钼耐硫低变催化剂并采用保护剂,设备防腐和后系统变换气脱硫等 应予加强。
Page 3
LOGO
一氧化碳变换催化剂的选用
3,2 以煤为原料间歇制气联产甲醇铜液净化 由于联产甲醇,要求变换气CO%含量相应提高,当醇氨比较高时,变换气CO%
含量甚至被提高至大于6%:此时宜选用铁铬中变催化剂的中变工艺或者选用低
汽比铁铬中变催化剂串钴钼耐硫低变催化剂的中串低工艺。 3.3 以煤为原料间歇制气甲烷化法净化 由于后续甲烷化法净化,要求变换气CO%含量小于0.3% ,因此宜选用铁铬中 变催化剂(或耐硫型铁铬中变催化剂)串两段钴钼耐硫低变催化剂的中低低深度 变换工艺; 或者选用钴钼耐硫低变催化剂的全低变深度变换工艺。
Page 5
LOGO
一氧化碳变换催化剂的选用
3.5 以烃类(天然气、石脑油)为原料蒸汽转化制气甲烷化法净化 以烃类(天然气、石脑油)为原料蒸汽转化制气制取的原料气, 由于进 入蒸汽转化之前为保护蒸汽转化催化剂己进行了脱硫, 因此所制得的原 料气已基本不含硫: 另外节能型烃类蒸汽转化流程(水碳比小于2.75)
已广泛应用 后续甲烷化净化: 因此宜选用低水汽比铁铬中变催化剂(或
本体低硫铁铬中变催化剂)串铜锌低变催化剂的变换工艺
Page 6
LOGO
一氧化碳变换催化剂的选用
每种催化剂都有最适合它的工艺条件,每种工艺条件也有 最适合它的催化剂,本文将催化剂的性能和特点与工艺条件 的要求相结合,提出了变换催化荆的一般选用原则,给大家 一个直观了解,从而能更具体的熟悉变换工艺的本质。
Page 7
LOGO
一氧化碳变换催化剂的选用
本文
一氧化碳变换催化剂的选用
在合成氨和制氢工业中,一氧化碳变换的工艺条件主要取决于原料气的制气工艺 和少量一氧化碳的脱除方法 原料气的制气工艺主要有: 以煤为原料问歇制气工
艺、以煤或油为原料加压连续制气工艺、பைடு நூலகம்烃类(天然气、石脑油)为原料蒸汽转
化制气工艺等.。少量一氧化碱随脱除方法主要有:铜液洗涤法、甲烷化法、液 氮洗涤法等 有时变换的工艺条件主要决 定于制气 工艺; 有时决定于少量一化 碳的脱除方法。此外有些工厂联产甲醇也会对变换催化剂得当选用产生影响
Page 4
LOGO
一氧化碳变换催化剂的选用
3.4 以煤或油为原料加压连续制气液氮洗涤法净化 以煤或油为原料加压连续制气制取的原料气中含有较高的硫 和水蒸汽.后 续的液氮洗涤法净化常与低温甲醇洗脱碳相配 套, 而该法对硫等物质有良好的脱除效果:因 此直接选用 钴钼耐硫变换催化剂实现后工艺的要求。