过程控制系统设计说明
WinCC过程控制监控系统设计说明

第1章绪论1.1 设计要求1.1.1 设计题目和设计指标题目:基于WinCC软件的过程控制监控系统设计设计指标:1)下位机设备(S7-200)2)上位机组态软件(趋势图、报警界面、参数设定)1.1.2 设计功能1. 利用西门子S7-200可编程控制器实现液位PID控制系统,通过调节电动调节阀的开度,改变水箱的进水流量,从而使水箱内的液位维持于恒定值。
2. 在上位机编制工艺画面,能够显示系统的实时状态、通过对现场数据的采集处理,以动画显示、报警处理、流程控制、实时曲线、历史曲线和报表输出等多种方式,向用户提供检验液位PLC 控制系统的动态运行情况,显示SP(设定值)、PV(液位高度检测值)、OP(阀开度)、P(比例)、I(积分时间)、D(微分时间),并且在画面上能够实现手自动切换、历史数据查询、报表、报警信息、历史曲线等功能。
第2章下位机设计2.1PLC选型1、CPU 选择的型号是西门子的CPU-226,它是200系列中一款高档次的CPU,其主要应用于具有较高要求的控制系统中。
和其它型号的CPU相比,其具有更多的I/O点,更强的模块扩展能力,更快的运行速度和更强的内部集成的特殊功能。
主要特性如下:➢可携带7个模块➢集成24个输入、16个输入共40个数字量I/O点,最大可扩展至248路数字量I/O点或35路模拟量I/O点➢13K字节的程序和数据存储空间➢6个独立的30KHz的高速计数器,2路独立的20KHz高速脉冲输出,并具有PID控制器➢2个RS485通讯/编程接口,具有PPI通信协议、MPI通讯协议和自由方式通讯能力➢I/O端子排可很容易的整体拆卸2、模拟输入模块采用EM 231,其输入信号是4~20mA信号,本实验即要求输入量为该数,满足要求,因此选用该型号。
3、模拟量输出模块采用EM232。
2.2 系统框图及下位机硬件连接系统框图如2-2-1所示:图2-2-1系统框图下位机硬件连接如2-2-2所示:PC/PPI 通信电缆M LT1上水箱电动调节阀1液位变送器进水出水图2-2-2下位机硬件连接图第3章 WinCC组态设计3.1 变量设计变量名称地址数据类型存取P VW0 INT RWI VW1 INT RWD VW2 INT RW当前值VW5 INT RW给定值VW6 INT R1、打开PC Access SP2软件,建立PLC连接。
基于SCADA的过程控制系统设计与实现

基于SCADA的过程控制系统设计与实现一、引言SCADA(Supervisory Control and Data Acquisition)是指监控控制与数据采集系统,它可以将分散的数据进行集中处理,实现对远程设备的监控和控制。
在工业自动化领域中,SCADA系统已经广泛应用于过程控制系统的设计和实现中。
本文将介绍基于SCADA的过程控制系统的设计原理和实现方法。
二、SCADA系统的基本原理SCADA系统由监控主站和远程终端单元组成,其中监控主站负责数据采集、监视和控制,而远程终端单元则负责采集现场数据并将数据传输给监控主站。
SCADA系统通过使用现代通信技术,如以太网、无线通信等,实现了对远程设备的实时监测和控制。
三、过程控制系统的设计与实现1. 系统需求分析在设计过程控制系统之前,首先需要进行系统需求分析。
这包括确定系统的功能需求、性能需求和可靠性需求等,并对系统运行环境进行评估。
2. 系统架构设计基于SCADA的过程控制系统需要设计合适的系统架构。
一般来说,系统架构包括核心网络架构、系统软件架构和硬件架构等。
核心网络架构负责控制主站和远程终端单元之间的通信,系统软件架构负责数据采集和处理,而硬件架构则负责提供必要的硬件设备支持。
3. 数据采集与传输过程控制系统的设计和实现离不开数据采集和传输。
通过采集传感器和执行器的数据,可以实现对过程的监视和控制。
数据采集可以通过模拟量输入、数字量输入和通信接口等方式进行。
而数据传输则可以通过以太网、无线通信等手段实现。
4. 数据处理与控制SCADA系统的核心任务是对采集到的数据进行处理和控制。
数据处理包括数据存储、数据显示和数据分析等。
而数据控制则包括远程控制和命令下达等。
通过数据处理和控制,可以实现对过程的监控和调控。
5. 系统安全与可靠性保障过程控制系统设计和实现中要注意系统的安全和可靠性。
这包括对系统的保密性、完整性和可用性进行保护,以及对系统进行备份和恢复等措施的实施。
过程控制系统设计 PPT课件
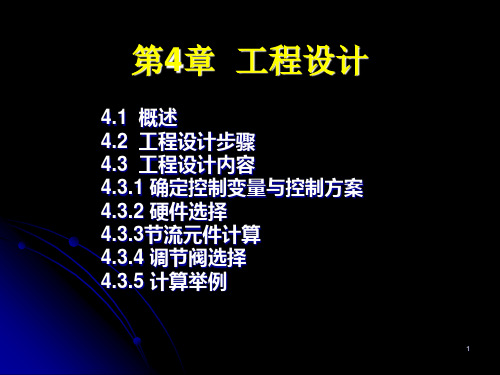
15
(一)确定控制变量与控制方案
2、操纵变量的选择 选择时考虑:
(1)工艺合理性 (2)被控对象的特性
操纵变量
q
干 扰
ƒ
对象
被控变量
y
(a)使被控对象控制通道的放大倍数较大,时 间常数较小,纯滞后越小越好;
(b)使被控对象干扰通道的放大倍数尽可能小, 时间常数越大越好
阻力越大,C值越小
CF
P
C的大小反映调节阀流量F的大小, 故习惯称为流通能力
C的定义:调节阀全开,阀两端压差为100Kpa,介质密度
为1g/cm3时,每小时流过调节阀的流量(m3/h)。
22
1、有关的系数 (1)阻塞流
当阀前压力一定,通过阀的流量随阀前后差压的增大而增 大,到达临界状态时,流量不随△P变化,为最大流量的流 动状况。 阻塞流的流量与差压的关系不遵循流量方程。
第4章 工程设计
4.1 概述 4.2 工程设计步骤 4.3 工程设计内容 4.3.1 确定控制变量与控制方案 4.3.2 硬件选择 4.3.3节流元件计算 4.3.4 调节阀选择 4.3.5 计算举例
1
4.1概述
4.1.1工程设计的定义
把生产过程自动化的各种控制方案,用设 计图纸资料和设计文件资料表达出来的全 部工作。
2
4.1.2自控工程设计的基本任务
从我国的实际情况出发,结合本厂的特点,确定 生产过程自动化水平。
根据工艺要求,确定各种检测参数。 主要控制参数的控制系统的设计。 工艺生产过程必要的信号报警和联锁保护设计。 控制室、仪表盘的设计。 仪表车间的设计。
3
4.1.3对工程设计人员的要求
生产过程模拟控制设计说明书

生产过程模拟控制设计说明书
一、总体控制方案
本控制方案全面实现了生产过程的模拟控制,该方案包括:本地控制器、运动控制、安全控制和PLC控制等。
1.1本地控制器
本地控制器负责处理生产设备的相关参数、故障信息和操作参数等,
并对生产系统实时的显示、控制、监测、显示和记录进行监控。
本地控制
器通过模块化的方式进行了设计,使得实现更加灵活、操作更加简单、稳
定性更好。
同时,该控制器能够满足客户对系统进行自定义设置,以更好
地服务客户的生产需求。
1.2运动控制
该方案为负责运动控制的部分,包括电子运动控制、模拟运动控制和
机械运动控制,电子运动控制使用PLC控制器实现,模拟运动控制使用数
字信号处理器实现,机械运动控制则使用伺服驱动器、步进驱动器等实现。
该控制方案能够实现对运动部件的实时监控、记录及报警等功能,以保证
运动部件的正常运行。
1.3安全控制
安全控制方案采用三网安全体系,包括安全现场总线(SLC)、安全
总线系统(SBS)、以及安全驱动控制系统(SDCS)。
实现对安全模块的
连接、触发及记录,以保证系统的安全性。
1.4PLC控制
本控制方案采用工业控制器作为系统核心控制器。
《过程控制系统设计》PPT课件
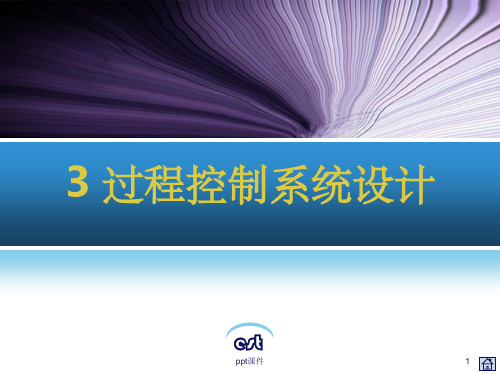
❖ 命题
▪ 确定所要求取的参数——流量、孔径、压差
❖ 从层流到紊流的分界线取决于
▪ 流量、流体的密度、粘度和管道内径
❖ 雷诺数Re
▪ Re〈2300 层流 ▪ Re〉4000 紊流
46微米厚的液晶层的流动。 当电场强度平缓增加时 •层流(右上) •弱的湍流(左下) •方格状对流(右下) 下侧两图混沌→湍流
ppt课件
14
3 过程控制系统设计
(2) 雷诺数Re(续)
ppt课件
8
3 过程控制系统设计
(3) 推断控制 当被控变量不能直接测量使用,利用辅助变 量的测量值来调节控制变量,使不可测的被控变 量保持在预期值。
ppt课件
9
3 过程控制系统设计
3.3 过程控制系统硬件选择
根据过程控制的输入输出变量以及控制要求,可
以选定系统硬件,包含:
保护
❖ 控制装置
装置
❖ 测量仪表、传感器 ❖ 执行机构
ppt课件
11
3 过程控制系统设计
3.3.2 测量仪表和传感器的选型原则
❖ 检测部件一般宜采用定型产品,设计过程控 制系统时,根据控制方案选择测量仪表和传 感器
❖ 选型原则:
▪ 可靠性 ▪ 实用性 ▪ 先进性
ppt课件
12
3 过程控制系统设计
3.4 流量计选择
3.4.1 流量计算有关的基本概念
(1) 流量Q 流体在单位时间内流过管道或设备某处横断面 的数量成为流量。
ε 可膨胀系数
a 节流装置开孔截面积
ρ1 流体流过节流装置前的密度
Δp 节流元件前后压力差
ppt课件
23
3 过程控制系统设计
工业过程控制系统设计与实现

工业过程控制系统设计与实现工业过程控制系统在现代工业生产中扮演着重要的角色,它是一种实现现代化自动化生产的关键技术之一。
随着科学技术的发展,工业过程控制系统逐渐成为工业企业中不可缺少的技术手段之一。
然而,工业过程控制系统设计与实现需要掌握一定的技术和知识,本文将就此进行探讨。
一、工业过程控制系统的概念工业过程控制系统是指将计算机技术与自动控制技术相结合,利用传感器、执行器、控制器等技术手段,对工业生产过程进行全面控制和管理的一种系统。
目的是提高企业生产效率、降低成本以及保证产品质量等。
二、工业过程控制系统的组成工业过程控制系统主要由以下几个部分组成:1、传感器:负责将实际物理量转换为电信号,并将其送至控制器。
2、控制器:负责根据对被控制对象的监测数据来进行计算和判断,并发出相应的控制信号,予以实现对被控对象的控制。
3、执行器:负责将控制信号转换为能够引起被控对象状态的控制动作,如通过振动、压力等方式对被控对象进行控制。
4、人机界面:通过人机交互界面,生产过程控制人员可以对整个过程进行实时监控和管理,以及根据生产需要进行各种数据分析、生产调度等操作。
三、工业过程控制系统的设计流程1、需求分析:在进行工业过程控制系统的设计之前,首先需要对所要控制的对象进行需求分析。
需要明确被控物体的控制需求及控制对象所需要完成的工作。
2、系统设计:在了解被控对象的需求后,需要进行系统设计,根据需求场景根据被控对象的运行状态、数据通信、数据处理、人机界面等方面进行设计。
3、硬件选型:根据需求分析、系统设计的要求,为系统选择合适的硬件设备,包括传感器、控制器、执行器、数据采集卡等。
4、系统实现:根据硬件选型,开始对系统进行实现,包括软硬件的编程、算法的设计等。
5、调试测试:对设计实现的系统进行进行调试和测试,检测系统是否能够达到控制要求,是否能够正常运行。
6、系统维护:当系统正式推广到生产中时,需要进行后期的维护和更新。
生产过程模拟控制设计说明书

生产过程模拟控制设计说明书
一、简介
本模拟控制设计针对生产过程,采用模拟控制的思想,设计出一系列智能化的控制方案,以提升生产效率,改善产品质量,减少生产成本,确保生产安全。
二、技术特点
1.自控技术:采用标准的自控系统技术,实现自动启停及参数调节,确保过程控制的稳定性和精准度;
2.过程控制技术:采用成熟的过程控制技术,实现软件,硬件,制作方案的设计,同时拟定联锁系统,对过程参数做出良好的监控;
3.连接技术:采用标准的连接技术,建立稳定的控制系统,实现信号的高效传输,快速响应;
4.计算机技术:采用标准的计算机技术,实现信息的收集,处理,存储,分析,统计,方便相关人员对生产过程的监控和管理;
5.报警技术:采用标准的报警技术,全面实现对控制系统的监控,及时发现问题,并及时处理;
三、解决方案
1.自控:采用标准的PID控制系统,实现温度、压力、流量的自控;
2.过程控制:采用联锁系统,实现对过程参数的实时监控;
3.连接:采用标准的通信协议,实现设备间的数据交换;。
工业过程控制系统设计与优化

工业过程控制系统设计与优化工业生产中,过程控制系统设计与优化是至关重要的。
它不仅可以提高产品的质量和生产效率,还可以减少生产成本和安全事故的发生。
本文将从控制系统设计的基本理念和优化方法入手,为读者深入介绍工业生产中的过程控制系统设计与优化。
一、基本理念控制系统设计的基本任务是根据所需的生产过程,在系统中加入控制装置,使得整个生产过程可以稳定运行,并且达到预期的效果。
控制系统设计应当以实现生产过程的准确控制为前提,以提高生产效率、降低生产成本、保障生产安全为目标,针对生产过程的特点和要求进行综合考虑。
控制系统设计的核心是控制算法。
通过对生产过程进行观测和分析,采用合适的控制算法以最小化过程控制中的误差和变化,从而使生产达到更完美的效果。
设备的选择是控制系统设计的关键。
为了达到稳定的控制效果,设备必须具备稳定性、精度高、响应速度快、适用于不同的工作环境和工作状态等特点。
在实际设计过程中,应当结合生产需求和工作环境综合考虑,并根据需求选取合适的设备和器材。
二、控制系统优化方法控制系统优化的目标是提高生产效果和降低生产成本。
其核心任务是对控制算法进行细致分析和改进,使其更加准确和可靠。
同时,还要综合考虑生产过程的特点和要求,优化控制系统的各个组成部分,从而提高生产效率和降低生产成本。
(1)控制算法优化控制算法优化是控制系统优化的关键。
如果控制算法不够准确、灵活,那么就很难达到准确控制的目的。
因此,控制算法的优化应当是优化控制系统的首要任务。
控制算法的优化主要包括以下几个方面:①建立可靠的数学模型:建立准确、可靠的数学模型是优化控制算法的基础。
只有建立准确的数学模型,才能较为准确地预测生产过程中的变化。
②选择合适的控制算法:根据不同的生产过程要求,选择合适的控制算法。
比如,在一些要求精度较高的生产过程中,PID控制算法就可以起到较为良好的效果;而在一些需要更为复杂控制的生产过程中,可以考虑使用模糊、神经网络等现代控制算法。