材料改性实验答辩论文
聚苯醚的改性范文

聚苯醚的改性范文聚苯醚(Polyphenylene Ether,PPE)是一种具有优异绝缘性能、高温稳定性、机械强度和尺寸稳定性的高分子材料。
然而,聚苯醚在一些方面存在一些不足,例如低冲击强度、低耐磨性以及一些成型性能有待改善。
为了克服这些缺点,一些聚苯醚的改性方法被广泛研究和应用。
一、物理改性的方法:1.填充改性:向聚苯醚中添加填料,如玻璃纤维、石墨、炭黑等,来提高其力学性能,例如冲击强度和弯曲强度。
填料可以增加材料的强度和刚度,并提高低温性能,但可能会降低存储稳定性。
2.合金改性:将聚苯醚与其他高分子材料进行共混,以改善聚苯醚的成型性能和机械性能。
例如,聚苯醚可以与聚碳酸酯(PC)、聚苯硫醚(PPS)等共混,以获得更好的性能和热稳定性。
3.压缩改性:将液态单体通过压缩成型的方法渗透到聚苯醚的孔隙中,以提高其冲击强度和抗磨性。
这种方法可以改变聚苯醚的孔隙结构,并提供更好的力学性能。
二、化学改性的方法:1.接枝改性:通过在聚苯醚分子链上引入可接受配体的官能团,如氨基、羟基等,使聚苯醚与其他高分子材料或添加剂发生化学反应,从而改善聚苯醚的性能。
例如,将聚苯醚与聚苯乙烯形成接枝共聚物,以提高聚苯醚的力学性能和成型性能。
2.稳定剂改性:向聚苯醚中添加稳定剂,如抗氧剂、光稳定剂等,以提高聚苯醚的热稳定性和耐候性。
3.交联改性:通过引入交联剂,如过氧化物、有机硅化合物等,使聚苯醚发生交联反应,以提高其机械性能和热稳定性。
在聚苯醚的改性过程中,需要综合考虑材料性能的提升、成本的可接受性以及工艺的可行性。
这些改性方法可以单独应用,也可以结合使用,以获得最佳的性能和成本效益。
此外,随着科学技术的不断发展,新的改性方法也在不断涌现。
通过不断的研究和创新,聚苯醚的性能和应用领域将不断扩展和拓宽。
【自然辨证法论文-xxx-2016xxxx29-机械系】材料改性工艺的科学本质探索
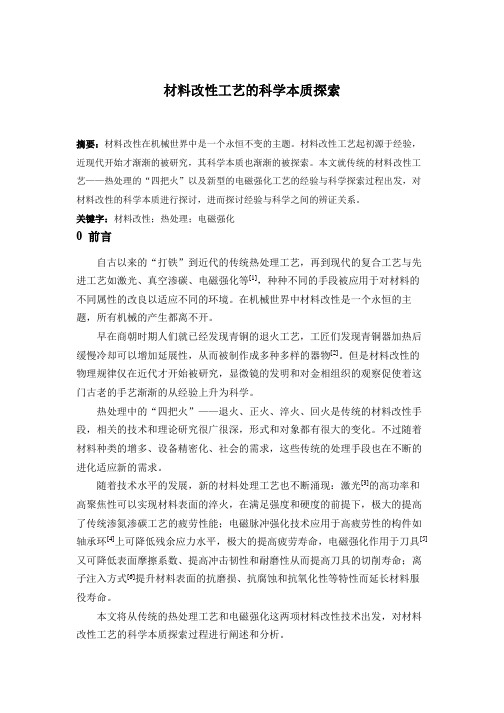
材料改性工艺的科学本质探索摘要:材料改性在机械世界中是一个永恒不变的主题。
材料改性工艺起初源于经验,近现代开始才渐渐的被研究,其科学本质也渐渐的被探索。
本文就传统的材料改性工艺——热处理的“四把火”以及新型的电磁强化工艺的经验与科学探索过程出发,对材料改性的科学本质进行探讨,进而探讨经验与科学之间的辨证关系。
关键字:材料改性;热处理;电磁强化0前言自古以来的“打铁”到近代的传统热处理工艺,再到现代的复合工艺与先进工艺如激光、真空渗碳、电磁强化等[1],种种不同的手段被应用于对材料的不同属性的改良以适应不同的环境。
在机械世界中材料改性是一个永恒的主题,所有机械的产生都离不开。
早在商朝时期人们就已经发现青铜的退火工艺,工匠们发现青铜器加热后缓慢冷却可以增加延展性,从而被制作成多种多样的器物[2]。
但是材料改性的物理规律仅在近代才开始被研究,显微镜的发明和对金相组织的观察促使着这门古老的手艺渐渐的从经验上升为科学。
热处理中的“四把火”——退火、正火、淬火、回火是传统的材料改性手段,相关的技术和理论研究很广很深,形式和对象都有很大的变化。
不过随着材料种类的增多、设备精密化、社会的需求,这些传统的处理手段也在不断的进化适应新的需求。
随着技术水平的发展,新的材料处理工艺也不断涌现:激光[3]的高功率和高聚焦性可以实现材料表面的淬火,在满足强度和硬度的前提下,极大的提高了传统渗氮渗碳工艺的疲劳性能;电磁脉冲强化技术应用于高疲劳性的构件如轴承环[4]上可降低残余应力水平,极大的提高疲劳寿命,电磁强化作用于刀具[5]又可降低表面摩擦系数、提高冲击韧性和耐磨性从而提高刀具的切削寿命;离子注入方式[6]提升材料表面的抗磨损、抗腐蚀和抗氧化性等特性而延长材料服役寿命。
本文将从传统的热处理工艺和电磁强化这两项材料改性技术出发,对材料改性工艺的科学本质探索过程进行阐述和分析。
1. 传统热处理工艺——“四把火”[7]1.1 退火将组织偏离平衡状态的钢加热到适当的温度并保温一定时间,按照一定的规律以较慢的速度冷却(一般是炉冷),以获得接近平衡组织的热处理工艺叫做退火。
纳米毕业答辩碳酸钙填充改性PP配方设计之正交试验

表中一为水平1的实验结果总和,表中二为水平2的实验结果总合,表中三为水平3的实验 结果总和。数值一,二,三中较大的数值表示该因素的相应水平下实验结果有较高的值. 最后对各因素分别计算极差填入表中。极差大者表示该因素用量的波动对实验结果的影 响比较大, 极差小者表示该因素用量的波动对实验结果的影响比较小。
参数值
185
195
185
175
165
92
30
检讨是成功之母
3.9注射标准试样 采用注射成型机,选择适宜的成型加工条件(注射压力,温度,螺杆 转速等),将PP改性料制成标准试样。 注射成型的一般工艺过程如下: 合模→注射→保压→预塑(熔胶)→冷却→开模→顶出试样→顶退→ 合模 注塑机的工艺参数如下表3-11所示。
正交试验数据分析表
因素2 1(1) 2(2) 3(3) 1(1) 2(2) 3(3) 1(1) 2(2) 3(3) 实验后经计算数据 实验后经计算数据 实验后经计算数据 因素3 1(0.5) 2(1) 3(1.5) 2(1) 3(1.5) 1(0.5) 3(1.5) 1(0.5) 2(1) 实验后经计算数据 实验后经计算数据 实验后经计算数据 拉伸强度/Mpa 实验数据 实验数据 实验数据 实验数据 实验数据 实验数据 实验数据 实验数据 实验数据
非常感谢老师们四年以来对我的谆谆教导
2 配方设计
5.最终配比: 数值一,二,三中较大的数值表示该因素 在相应水平下实验结果具有较高的值.从而 确定出拉伸强度最优时的配比,同理可得 弯曲强度、冲击强度的最优时的配比。
非常感谢同学们四年以来对我的帮助与支持
3 实验部分
3.6填料表面预处理 填料表面预处理是实验的关键步骤,为了提高填料 与树脂的亲和能力,需要对填料进行表面预处理。 一般填料处理的方法有:(1)利用无机物或有机物 进行物料的表面涂层;(2)利用偶联剂进行表面处 理;(3)利用表面处理剂进行处理。 由于对填料进行单纯的涂覆或用偶联剂处理会存 在某些不足。故本次实验采用(1)和(2)两种方法 综合使用,对原料进行表面预处理。
材料类毕业论文答辩模板
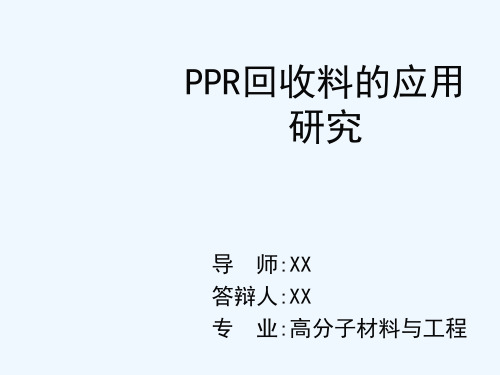
实验部分
实验过程
本实验属于研究型实验,需进行多组试验 ,用控制变量法来确定最佳配方。
1.按一定表2-3配比配料→制得母料→与 回收的PPR混合挤出发泡板材→对比确定 最佳板材→确定最佳配方及工艺参数。
通过对挤出发泡板材的高倍显微照片和密度等进行测定,发 现滑石粉用量为20g时,最为合适。
结果与讨论
4.机头温度的选择结果
图3-4不同机头温度下的PP发泡片材的高倍显微照片
结果与讨论
经过对比分析可得出表3-6:
表3-6 实验参数汇总
经过对四组聚丙烯挤出发泡板材进行表面观察和密度测定,对比可 以发现密度机头温度为170℃时,板材发泡性相对理想。
将PPR分别与已选定最佳配方以质量配比 90/10均匀混合。在不同机头温度下,挤 出片材的高倍显微镜发泡照片再进行对比 。
实验部分
6.螺杆转速的确定
RM-200A转矩流变仪前三区温度分别为 :150℃、180℃、195℃,机头温度为 170℃。转速分别设定为:30 rpm、40 rpm、45rpm。
研究背景
PPR是由废旧的塑料水管回收而 得,其主要成分是PP。考虑到 发泡制品在建筑发面应用前景很 大,决定生产PPR发泡片材,用 作建筑模板的中心层。
实验部分 主要原料
实验部分 仪器设备
实验部分 工艺流程
制备发泡母料 增粘剂 + AC发泡剂 + 滑石粉 + ZnO → 双 螺杆挤出机 → 切粒 → 发泡母粒
所得片材冷却制成样条后在高倍显微镜下 照片进行对比。
实验部分
4.滑石粉用量的确定
材料改性实验答辩论文

浅析15号钢能否代替45号钢用作凸轮轴班级:姓名:学号:字数:摘要:凸轮轴是发动机的关键零件之一,要求凸轮轴具有相应的强度和硬度外,还应具有良好的抗擦性、抗接触疲劳能力和耐磨性。
还要有一定的抗弯强度和足够的韧性,能承受一定的抗扭转载荷,保证受力后无明显变形。
凸轮轴的材料选项主要取决于在发动机中的工作条件、使用工况,目前制造凸轮的材料、工艺种类较多,可分为钢和铸铁两大类。
根据凸轮轴的服役条件、受力和失效情况。
一般的凸轮轴选用渗碳钢和中碳钢。
关键字:45钢 15钢凸轮轴调质处理高频淬火表面渗碳低温回火一、45钢的简介45钢是中碳结构钢,冷热加工性能都不错,机械性能较好,且价格低、来源广,所以应用广泛。
它的最大弱点是淬透性低,截面尺寸大和要求比较高的工件不宜采用。
45钢主要成分为 Fe(铁元素),且含有以下少量元素:元素 C Si Mn Cr Ni Cu S P含量/%0.42~0.5%0.17~0.37%0.50~0.80%≤0.25%≤0.30%≤0.25%≤0.045%≤0.040%45钢的密度7.85g/cm3,弹性模量210GPa,泊松比0.269。
二、45钢用作凸轮轴的工艺1、45钢的调质处理45钢淬火温度在A3+(30~50)℃,在实际操作中,一般是取上限的,约为840~860℃。
偏高的淬火温度可以使工件加热速度加快,表面氧化减少,且能提高工效。
为使工件的奥氏体均匀化,就需要足够的保温时间,一般为1-2h。
如果实际装炉量大,就需适当延长保温时间。
不然,可能会出现因加热不均匀造成硬度不足的现象。
但保温时间过长,也会也出现晶粒粗大,氧化脱碳严重的弊病,影响淬火质量。
如装炉量大于工艺文件的规定,加热保温时间需延长1/5。
因为45钢淬透性低,故应采用冷却速度大的10%盐水溶液。
工件入水后,应该淬透,但不是冷透,如果工件在盐水中冷透,就有可能使工件开裂,这是因为当工件冷却到180℃左右时,奥氏体迅速转变为马氏体造成过大的组织应力所致。
材料科学中的材料表面改性研究
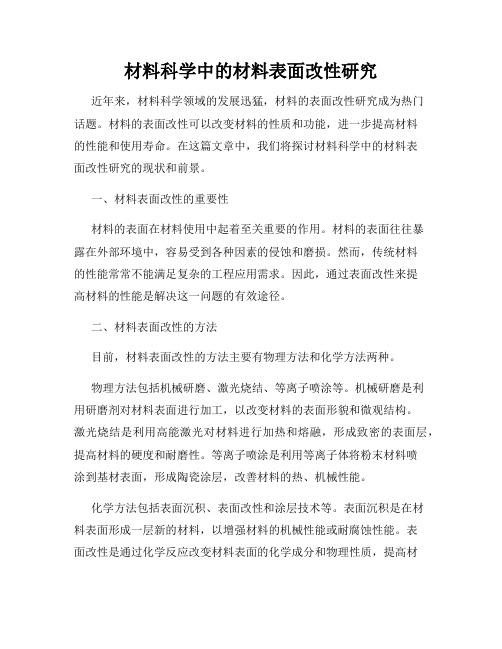
材料科学中的材料表面改性研究近年来,材料科学领域的发展迅猛,材料的表面改性研究成为热门话题。
材料的表面改性可以改变材料的性质和功能,进一步提高材料的性能和使用寿命。
在这篇文章中,我们将探讨材料科学中的材料表面改性研究的现状和前景。
一、材料表面改性的重要性材料的表面在材料使用中起着至关重要的作用。
材料的表面往往暴露在外部环境中,容易受到各种因素的侵蚀和磨损。
然而,传统材料的性能常常不能满足复杂的工程应用需求。
因此,通过表面改性来提高材料的性能是解决这一问题的有效途径。
二、材料表面改性的方法目前,材料表面改性的方法主要有物理方法和化学方法两种。
物理方法包括机械研磨、激光烧结、等离子喷涂等。
机械研磨是利用研磨剂对材料表面进行加工,以改变材料的表面形貌和微观结构。
激光烧结是利用高能激光对材料进行加热和熔融,形成致密的表面层,提高材料的硬度和耐磨性。
等离子喷涂是利用等离子体将粉末材料喷涂到基材表面,形成陶瓷涂层,改善材料的热、机械性能。
化学方法包括表面沉积、表面改性和涂层技术等。
表面沉积是在材料表面形成一层新的材料,以增强材料的机械性能或耐腐蚀性能。
表面改性是通过化学反应改变材料表面的化学成分和物理性质,提高材料的功能。
涂层技术是在材料表面形成一层薄膜,以提高材料的抗腐蚀性、摩擦性和耐磨性。
三、材料表面改性的应用领域材料表面改性的研究在各个领域都有广泛的应用。
在航天领域,对于航天器的外壳材料,表面改性可以提高其抗氧化和隔热性能,从而提高航天器的使用寿命。
在医疗器械领域,通过表面改性可以改善材料的生物相容性和抗菌性能,降低医疗器械与人体组织之间的免疫反应,减少术后感染风险。
在能源领域,通过表面改性提高材料的吸附性能和催化活性,可以用于燃料电池、储能器件等新能源技术的研发。
在电子领域,表面改性可以提高材料的导电性和光电性能,用于光电器件、半导体设备等高新技术产业。
四、材料表面改性的挑战和前景材料表面改性的研究面临着一些挑战。
材料表面改性方法及其性能提升效果验证
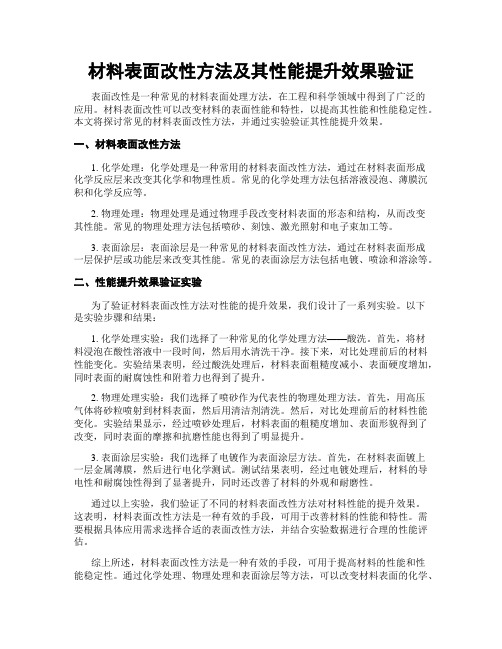
材料表面改性方法及其性能提升效果验证表面改性是一种常见的材料表面处理方法,在工程和科学领域中得到了广泛的应用。
材料表面改性可以改变材料的表面性能和特性,以提高其性能和性能稳定性。
本文将探讨常见的材料表面改性方法,并通过实验验证其性能提升效果。
一、材料表面改性方法1. 化学处理:化学处理是一种常用的材料表面改性方法,通过在材料表面形成化学反应层来改变其化学和物理性质。
常见的化学处理方法包括溶液浸泡、薄膜沉积和化学反应等。
2. 物理处理:物理处理是通过物理手段改变材料表面的形态和结构,从而改变其性能。
常见的物理处理方法包括喷砂、刻蚀、激光照射和电子束加工等。
3. 表面涂层:表面涂层是一种常见的材料表面改性方法,通过在材料表面形成一层保护层或功能层来改变其性能。
常见的表面涂层方法包括电镀、喷涂和溶涂等。
二、性能提升效果验证实验为了验证材料表面改性方法对性能的提升效果,我们设计了一系列实验。
以下是实验步骤和结果:1. 化学处理实验:我们选择了一种常见的化学处理方法——酸洗。
首先,将材料浸泡在酸性溶液中一段时间,然后用水清洗干净。
接下来,对比处理前后的材料性能变化。
实验结果表明,经过酸洗处理后,材料表面粗糙度减小、表面硬度增加,同时表面的耐腐蚀性和附着力也得到了提升。
2. 物理处理实验:我们选择了喷砂作为代表性的物理处理方法。
首先,用高压气体将砂粒喷射到材料表面,然后用清洁剂清洗。
然后,对比处理前后的材料性能变化。
实验结果显示,经过喷砂处理后,材料表面的粗糙度增加、表面形貌得到了改变,同时表面的摩擦和抗磨性能也得到了明显提升。
3. 表面涂层实验:我们选择了电镀作为表面涂层方法。
首先,在材料表面镀上一层金属薄膜,然后进行电化学测试。
测试结果表明,经过电镀处理后,材料的导电性和耐腐蚀性得到了显著提升,同时还改善了材料的外观和耐磨性。
通过以上实验,我们验证了不同的材料表面改性方法对材料性能的提升效果。
这表明,材料表面改性方法是一种有效的手段,可用于改善材料的性能和特性。
论文答辩决议(通用6篇)
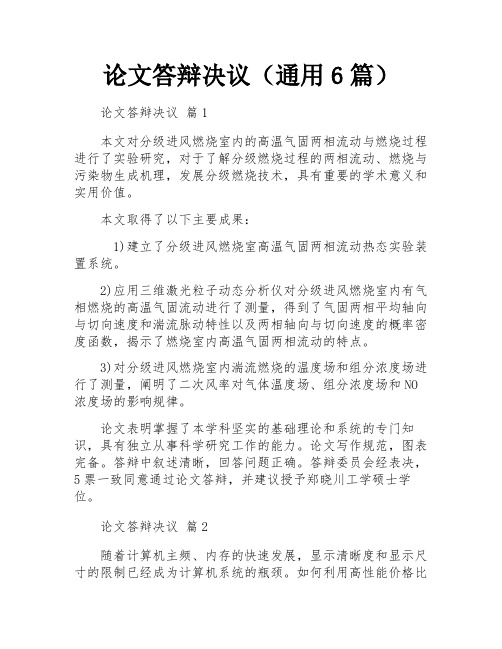
论文答辩决议(通用6篇)论文答辩决议篇1本文对分级进风燃烧室内的高温气固两相流动与燃烧过程进行了实验研究,对于了解分级燃烧过程的两相流动、燃烧与污染物生成机理,发展分级燃烧技术,具有重要的学术意义和实用价值。
本文取得了以下主要成果:1)建立了分级进风燃烧室高温气固两相流动热态实验装置系统。
2)应用三维激光粒子动态分析仪对分级进风燃烧室内有气相燃烧的高温气固流动进行了测量,得到了气固两相平均轴向与切向速度和湍流脉动特性以及两相轴向与切向速度的概率密度函数,揭示了燃烧室内高温气固两相流动的特点。
3)对分级进风燃烧室内湍流燃烧的温度场和组分浓度场进行了测量,阐明了二次风率对气体温度场、组分浓度场和NO 浓度场的影响规律。
论文表明掌握了本学科坚实的基础理论和系统的专门知识,具有独立从事科学研究工作的能力。
论文写作规范,图表完备。
答辩中叙述清晰,回答问题正确。
答辩委员会经表决,5票一致同意通过论文答辩,并建议授予郑晓川工学硕士学位。
论文答辩决议篇2随着计算机主频、内存的快速发展,显示清晰度和显示尺寸的限制已经成为计算机系统的瓶颈。
如何利用高性能价格比的机群实现超高分辨率的高清晰度大尺寸显示正在成为并行可视化方向一个重要的研究课题。
李颖敏同学的硕士论文以设计基于机群的拼贴显示系统提供方便的编程接口和编程环境为目的,其选题具有前瞻性,论文的工作有很好的应用前景。
(第一段:选题的意义)论文在分析调研国际目前研究动态的基础上应用“分布式共享显示内存”的新概念提出了一种并行程序环境下的拼贴显示接口,并以两种形式实现了该接口,简化了系统应用的编程实现。
提供了一些测试用的应用程序,为今后的研究工作提供了有参考价值的研究平台。
展示了基于机群作分布式显示的良好前景。
同时还利用该拼贴显示接口为一个地理图像信息系统实现了多屏显示应用,满足了该应用对高分辨率显示的需求。
(第二段:论文工作取得的成果或新见解)论文工作表明基础理论和专业知识都比较好,掌握了计算机系统结构领域分析问题、解决问题的基本方法和技能。
- 1、下载文档前请自行甄别文档内容的完整性,平台不提供额外的编辑、内容补充、找答案等附加服务。
- 2、"仅部分预览"的文档,不可在线预览部分如存在完整性等问题,可反馈申请退款(可完整预览的文档不适用该条件!)。
- 3、如文档侵犯您的权益,请联系客服反馈,我们会尽快为您处理(人工客服工作时间:9:00-18:30)。
浅析15号钢能否代替45号钢用作凸轮轴班级:姓名:学号:字数:摘要:凸轮轴是发动机的关键零件之一,要求凸轮轴具有相应的强度和硬度外,还应具有良好的抗擦性、抗接触疲劳能力和耐磨性。
还要有一定的抗弯强度和足够的韧性,能承受一定的抗扭转载荷,保证受力后无明显变形。
凸轮轴的材料选项主要取决于在发动机中的工作条件、使用工况,目前制造凸轮的材料、工艺种类较多,可分为钢和铸铁两大类。
根据凸轮轴的服役条件、受力和失效情况。
一般的凸轮轴选用渗碳钢和中碳钢。
关键字:45钢 15钢凸轮轴调质处理高频淬火表面渗碳低温回火一、45钢的简介45钢是中碳结构钢,冷热加工性能都不错,机械性能较好,且价格低、来源广,所以应用广泛。
它的最大弱点是淬透性低,截面尺寸大和要求比较高的工件不宜采用。
45钢主要成分为 Fe(铁元素),且含有以下少量元素:元素 C Si Mn Cr Ni Cu S P含量/%0.42~0.5%0.17~0.37%0.50~0.80%≤0.25%≤0.30%≤0.25%≤0.045%≤0.040%45钢的密度7.85g/cm3,弹性模量210GPa,泊松比0.269。
二、45钢用作凸轮轴的工艺1、45钢的调质处理45钢淬火温度在A3+(30~50)℃,在实际操作中,一般是取上限的,约为840~860℃。
偏高的淬火温度可以使工件加热速度加快,表面氧化减少,且能提高工效。
为使工件的奥氏体均匀化,就需要足够的保温时间,一般为1-2h。
如果实际装炉量大,就需适当延长保温时间。
不然,可能会出现因加热不均匀造成硬度不足的现象。
但保温时间过长,也会也出现晶粒粗大,氧化脱碳严重的弊病,影响淬火质量。
如装炉量大于工艺文件的规定,加热保温时间需延长1/5。
因为45钢淬透性低,故应采用冷却速度大的10%盐水溶液。
工件入水后,应该淬透,但不是冷透,如果工件在盐水中冷透,就有可能使工件开裂,这是因为当工件冷却到180℃左右时,奥氏体迅速转变为马氏体造成过大的组织应力所致。
因此,当淬火工件快冷到该温度区域,就应采取缓冷的方法。
由于出水温度难以掌握,须凭经验操作,当水中的工件抖动停止,即可出水空冷(如能油冷更好)。
另外,工件入水宜动不宜静,应按照工件的几何形状,作规则运动。
静止的冷却介质加上静止的工件,导致硬度不均匀,应力不均匀而使工件变形大,甚至开裂45钢调质件淬火后的硬度应该达到HRC56~59,截面大的可能性低些,但不能低于HRC48,不然,就说明工件未得到完全淬火,组织中可能出现索氏体甚至铁素体组织,这种组织通过回火,仍然保留在基体中,达不到调质的目的。
45钢淬火后的高温回火,加热温度通常为560~600℃,硬度要求为HRC22~34。
因为调质的目的是得到综合机械性能,所以硬度范围比较宽。
关于回火保温时间,视硬度要求和工件大小而定,我认为,回火后的硬度取决于回火温度,与回火时间关系不大,但必须回透,一般工件回火保温时间总在一小时以上。
经过高温回火后的组织为回火索氏体。
2、45钢调质处理后表面高频淬火经感应加热淬火的零件比炉中加热淬火件的硬度高2~5HRC。
2.1 表面高频淬火的简介表面淬火的目的在于获得高硬度,高耐磨性的表面,而心部仍然保持原有的良好韧性,常用于机床主轴,齿轮,发动机的曲轴等。
表面淬火是将钢件的表面层淬透到一定的深度,而心部分仍保持未淬火状态的一种局部淬火的方法。
表面淬火时通过快速加热,使钢件表面很快到淬火的温度,在热量来不及穿到工件心部就立即冷却,实现局部淬火。
高频淬火是感应加热淬火的一种且多数用于工业金属零件表面淬火,是使工件表面产生一定的感应电流,迅速加热零件表面,然后迅速淬火的一种金属热处理方法。
感应加热设备,即对工件进行感应加热,以进行表面淬火的设备。
感应加热的原理:工件放到感应器内,感应器一般是输入中频或高频交流电 (1000~300000Hz或更高)的空心铜管。
产生交变磁场在工件中产生出同频率的感应电流,这种感应电流在工件的分布是不均匀的,在表面强,而在内部很弱,到心部接近于0,利用这个集肤效应,可使工件表面迅速加热,在几秒钟内表面温度上升到800~1000℃,而心部温度升高很小。
2.2 高频感应淬火硬化层深度感应加热淬火硬化层深度应根据零件的服役条件确定,表1列出了几种典型服役条件下的硬化层深度要求。
为了获得表层残余应力,一般要求过度层深度小于硬化层的1/4。
表1 典型服役条件下的零件表层硬化层深度要求失效原因工作条件硬化层深度及硬度值要求磨损互动磨损且负荷磨损较小以尺寸公差为限,一般1~2mm,硬度HRC55~63,可取上限负荷较大或承受冲击负荷一般在2.0~6.5mm之间,硬度HRC55~63,可取下限疲劳周期性弯曲或扭转负荷一般为2.0~12mm,中小型轴类可取半径的10%~20%,直径小于40mm的取下限;过渡层为硬化层的25%~30%凸轮轴在工作过程中承受一定的弯曲和扭转载荷外,主要是凸轮部分承受周期变化的挤压应力,其失效原因多为疲劳损伤。
根据凸轮轴的服役条件和表1可以判断45钢凸轮轴的硬化层在0.5~2.0mm之间。
2.3 高频感应加热电源的选择根据工件尺寸和要求的淬硬层深度选择合理的电流频率,以保证最佳的电效率。
感应加热频率的选择:根据热处理及加热深度的要求选择频率,频率越高加热的深度越浅。
高频(10KHZ以上)加热的深度为0.5~2.5mm,通过上面得知45钢凸轮轴的硬化层在0.5~2.0mm 之间,要想通过高频感应加热对45钢表面淬火,则应选择的电源频率为200~300kHz 。
2.4 高频感应加热淬火温度 当对45钢进行过调质处理后进行表面高频感应加热淬火时,一定要注意感应淬火的温度。
由于感应加热速度快,为使组织充分转变,淬火温度应比一般热处理的淬火温度高30~50℃,即达到830~870℃左右。
凸轮轴进行感应淬火硬化处理后,其奥氏体晶粒得到了细化,使表面硬度高,耐磨性以及疲劳性得到改善,另外具有变形小、效率高、节能、自动化和机械化操作程度高。
图1 45钢高频感应加热淬火 温度-硬度-组织分布 图2 45钢高频感应加热淬火后 的切应力分布 1-硬化层深度为1.5mm;2-硬化层深度为0.2mm;3-硬化层深度为3.0mm由于感应加热工艺是瞬间的高温、冷却过程,金属表面不仅会因迅速淬火而形成马氏体,而且在经过狭窄的淬硬区后还会得到感应淬火前的预处理基体组织。
高频感应淬火后有表层到芯部的组织:马氏体、马氏体+铁素体、珠光体+铁素体。
图3:感应加热表面淬火示意图3、45钢进行低温回火低温回火又称“消除应力回火”。
回火温度范围为150~250℃,回火后的组织为回火马氏体。
它是由过饱和的α相和与其共格的ε-Fe2.4C 组成,其形态仍保留淬火马氏体的片状或板条状。
使45钢具有高硬度和高耐磨性,但内应力和脆性降低。
经过回火后45钢凸轮轴的硬度一般为58~64HRC 。
三、15钢的分析1、15钢的简介15号钢优质碳素结构钢的S ,P 杂质含量比普通碳素结构钢要低些,一般在0.035%(质量分数)以下。
这类钢产量较大,用途较广,多轧制(或锻造)成圆、方、扁平产品,有的制成管材和丝材。
一般经正火或调质等热处理后使用,多用于机械或机器结构件。
15号钢是一种低碳钢材料,它的延展性、可塑性都是比较好的,由于它的含碳量低(在0.12~0.18%之间),所以硬度比较低。
另外,由于15号钢的含2~3h 350 250150 温度/℃ 时间/h200~220℃ 油冷 水冷碳量低,对这样的材料制成的零件在进行热处理提高其硬度比较困难。
需要加热到1100℃以上,一般的钡盐浴炉是不能处理的,需要用高温硝酸盐浴炉来加热。
2、15钢的特性15号钢其塑性、韧性高,但强度、硬度较低,锻造、焊接和冷冲压性能良好,冷变形塑性高,但切削加工时不易得到光洁的表面。
用于制造受力不大、韧性要求高的零件和渗碳件,紧固件和冲模锻件以及不经热处理的低负荷零件。
3、15钢化学成分元素 C Si Mn Cr Ni Cu S P含量/%0.12~0.19%0.17~0.37%0.35~0.65%≤0.25%≤0.25%≤0.25%≤0.035%≤0.035%4、15钢的力学性能抗拉强度ζb (MPa):≥375;屈服强度ζs (MPa):≥225;伸长率δ5/(%):≥27;断面收缩率ψ/(%):≥55。
四、15钢用作凸轮轴的热处理工艺根据以上15号钢的性能分析,15号钢属于低碳钢,简单的热处理对其强度没有太大的改变,这样的情况下15号钢是无法用作凸轮轴的。
凸轮轴需要表面有较高的硬度,而且心部有较好的韧性。
如若15号钢用作凸轮轴的材料,那就必须经过特殊的热处理工艺,即最好先进行表面渗碳(或者碳氮共渗),渗碳深度视情况而定(一般1~3mm),然后进行淬火处理,如此,表面能够有比较高的硬度,内部又能基本保持原有的韧性。
1、15钢的渗碳处理1.1 钢的渗碳介绍钢的渗碳就是含碳量较低的钢制零件在渗碳介质中加热或者保温,使碳原子渗入表面,获得一定的表面含碳量,在淬火之后,含碳量高的表层硬度很高,而含碳量低的心部硬度低仍具有良好的韧性。
目的是使零件获得高的表面硬度、耐磨性以及高的接触疲劳强度和弯曲疲劳强度。
主要用于承受磨损、交变接触应力或者弯曲应力和冲击载荷的零件,如轴、齿轮、凸轮轴等,这些零件要求表面有很高的硬度而心部要有足够的强度和韧性。
渗碳法分为固体渗碳法、液体渗碳法和气体渗碳法三种。
另外还有真空渗碳法。
1.2 15钢的渗碳热处理工艺固体渗碳法就是把15钢放入固体渗碳剂(由木炭粉以及BaCO3和Na2CO3等促进剂组成)中然后放入渗碳容器里加热到900℃~930℃保温一定时间;液体渗碳是把15钢浸入以氰化钠(NaCN)为主(含NaCl、NaCO3和Na2CO3等添加剂)的熔融盐浴里,氰化钠分解所生成的C和N渗入15钢中;气体渗碳是把15钢放入通有CH4和CO的容器里加热使碳原子渗入工件表面。
我们经常提到的渗碳层深度是指淬火后的有效硬化层深度,国标GB9450—88上规定为从零件表面到维氏硬度值为550HV的距离,实际碳在零件中扩散达到的距离比这个要大得多。
渗碳层的深度可以达到几个毫米,其深度随渗碳时间的增加而增加,随渗碳温度的升高而加深,但是渗碳速度随时间的延长而减慢。
对不要渗碳的部位一般采用镀铜保护或者预留加工余量、渗碳后把该处切掉的方法进行防护。
1.3渗碳后的组织组织:若工件渗碳后缓慢冷却,从表面到心部的组织为珠光体+网状二次渗碳体、珠光体、珠光体+铁素体。
2、15钢渗碳后的热处理工艺渗碳后15钢必须进行淬火和低温回火处理以得到零件所需要的硬度(可达HRC55~65),注重高硬度时在150℃左右回火,而为了保持零件的尺寸精度,防止时效变形时在180~200℃左右回火。