316卡套管腐蚀原因分析
1. 套管损坏原因

套管损坏的原因主要包括两方面的因素:地质因素和工程因素。
(1)地层的非均质性沉积的环境不同,油藏渗透性在层与层之间、层内平面都有较大的差别。
即使划分了层系,但同一层系内各小层渗透率仍相差很大,有的相差10倍,有的相差几十倍。
在注水开发过程中,油层的非均质性将直接导致注水开发的不均衡性,这是引发地层孔隙压力场不均匀分布的基本地质因素。
(a)(b)(2)地层(油层)倾角 陆相沉积的油田,一般储油构造多为背斜构造和向斜构造,由于背斜构造是受地层侧压应力为主的褶皱作用,一般在相同条件下,受岩体重力的水平分力的影响,地层倾角较大的构造轴部和陡翼部,比倾角较小的部位更容易出现套损。
图8-2 地层倾角影响图(3)岩石性质注水开发的泥砂岩油田,当油层中的泥岩及油层以上的页岩被注入水侵蚀后,不仅使其抗剪强度和摩擦系数大幅度降低,而且使套管受岩石膨胀力的挤压,同时当具有一定倾角的泥岩遇水呈塑性时,可将上覆岩层压力转移至套管,使套管受到损坏。
图8-3 岩性变化对套损的影响示意图(4)断层活动在沉积构造的油田中,地层沉降速度高的地区和油层断层本身所处的构造位置,均会促使断层活动,特别是注入水侵蚀后,更加剧对套管的破坏作用,造成成片套损区的发生。
套损深度与断层通过该井区的深度相同、断层活跃程度高的地区也恰好是现代地壳运动沉降速度较高的地区,而且是在油层构造的顶部和陡翼部。
图8-4 断层活动对套损的影响示意图(5)地震活动地震后,大量注入水通过断裂带或因固井胶结第二界面问题进入油顶泥岩、页岩,泥、页岩吸水后膨胀,又产生粘塑性,使岩体产生缓慢的水平运动,这种缓慢的蠕变速度超过10mm/a时,油水井套管将遭到破坏。
(6)地壳运动地球在不断地运转,地壳也在不停的缓慢运动中,其运动方向一般有两个:①水平运动(板块运动)②升降运动(地壳缓慢的升降运动产生的应力可以导致套管被拉伸损坏)(7)地面腐蚀地表地面腐蚀是不可忽视的套损原因之一。
化工厂316L输送管道失效原因分析

化工厂316L输送管道失效原因分析刘铭奇;董逢寅;董羲武【摘要】材质为316L不锈钢的半成品柴油输送管道在水平段底部出现快速腐蚀,9个月出现5次泄露.通过宏观分析、化学成分检测、力学性能测试、金相分析、腐蚀产物物相分析、腐蚀介质有害相分析、腐蚀产物分析等方法,对管道失效原因进行分析.结果表明:不锈钢管线腐蚀属于氧腐蚀及点蚀;氧化铁等腐蚀产物或杂质随介质在管线底部流动,对管线底部形成线状冲刷磨损,破坏了钝化膜的保护作用,造成管线底部率先腐蚀;腐蚀环境中Cl-极易破坏不锈钢表面的钝化膜,形成坑蚀,成为孔蚀延伸的活性中心.【期刊名称】《失效分析与预防》【年(卷),期】2018(013)006【总页数】5页(P373-377)【关键词】化工厂;316L;水平段底部;Cl-;氧腐蚀【作者】刘铭奇;董逢寅;董羲武【作者单位】国家石油装备产品质量监督检验中心, 山东东营257000;国家石油装备产品质量监督检验中心, 山东东营257000;国家石油装备产品质量监督检验中心, 山东东营257000【正文语种】中文【中图分类】TG1740 引言316L输送管广泛用于石油、化工、医疗、食品、轻工、机械仪表等工业输送管道以及机械结构部件等。
一条316L不锈钢输送管线在高温酸性条件下使用,从安装开始的9个月内共出现5次穿孔泄露。
输送介质为半成品柴油(0.15 MPa、260~270℃),输送速率为50~80 m/h。
腐蚀发生位置位于管线水平段底部,成间断性线性分布。
随着316L不锈钢管不断使用在各个领域中,必须寻找失效原因并提出改进建议,为后续该类型产品的故障判断与预防提供依据,以确保化工厂管道安全运行[1-3]。
1 试验过程与结果1.1 宏观观察和取样截取2段出现腐蚀的不锈钢管线进行实验室理化检验。
将第一段管段按安装方位的中间水平位置切割剖开进行观察,样品宏观形貌如图1所示,管线内表面中上部覆盖着一层棕褐色腐蚀产物,均匀分布于管体中上部,清除后管体特征为全面腐蚀加管线底部局部深度腐蚀穿孔。
管道腐蚀分析

管道防腐材料是抑制管道发生化学腐蚀和电化学腐蚀的一种材料,认识防腐材料前先来认识管道防腐必要性以及其意义。
一,钢质管道防腐蚀意义钢管腐蚀问题普遍存在于国民经济和国防建设的各个部门,既给国民经济带来了巨大的损失.也给生产和生活造成极大的困难。
钢管在自然条件下(大气,天然水体、土壤)或人为条件(酸、碱、盐及其它介质)下,每时每刻都在发生腐蚀.一种自发进行的无谓的消耗。
其根本原因钢质管道是因为处于热力学不稳定状态,在上述条件下它们就要恢复原来的相对稳定的状态.生成铁氧化物碳酸盐等.或转变为可溶性离子。
这一过程就是金属的腐蚀过程。
根据统计,我国钢铁年产量1.6亿吨.每年因腐蚀而损耗6千多万吨.差不多等于上海宝钢钢铁总厂的年产量。
腐蚀不仅是钢铁资源的浪费,还会因腐蚀使管道、设备使用寿命缩短更换新管道设备的造价费用远远超过金属材料本身的价格,生产成本因此而增大,降低了经济效益腐蚀造成的直接和间接经济损失是巨大的。
腐蚀产物形成垢层,影响传热和介质流速传热效率降低,能耗由此大大增加,我国每年因腐蚀造成的经济损失高达2800亿元,比每年风灾,水灾、地震火灾等自然灾害的总和还要多。
腐蚀造成各种事故和重大灾害。
由于钢质管道、设备的腐蚀,引起生产企业停工停产产品质量下降。
影响生活供、供气、供采暖蒸汽或热水,给人民生活带来很多困难。
埋地输油气、水等管道、管网的泄漏,企业炼油,化工、化纤、化肥、制药等管道、设备的跑、冒、滴漏.除损失大量有用的物质外又造成严重的环境污染,甚至引起火灾、爆炸、塌毁等灾难性事故。
鉴于金属腐蚀的普遍存在.为了防止或减缓金属腐蚀的发生.各种金属防腐技术和工艺应运而生。
金属防腐新工艺、新材料、新设备的推广应用.延长管道设备使用寿命,节省资金、保证安全生产。
我国石油化工、公共事业等行业.管道因腐蚀穿孔达2万次/年.其主要发生在钢管的接口处和管道自身的磕碰伤。
二:输油、输气钢质管道的腐蚀现状根据调查统计,在我国管道事故中,腐蚀造成的破坏约占3O%。
探讨套管损坏原因及修井作业技术
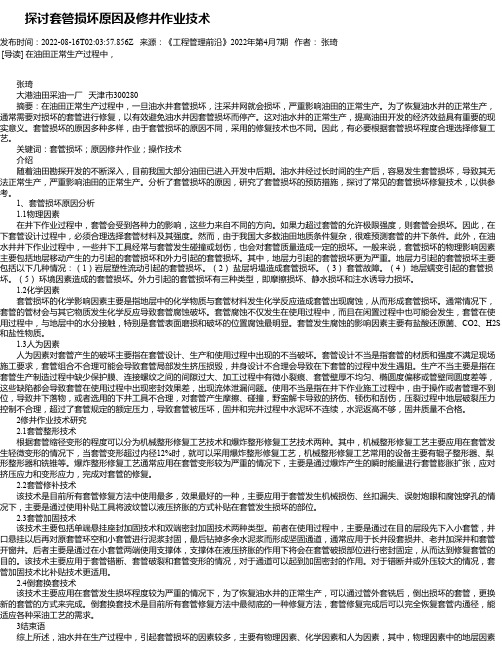
探讨套管损坏原因及修井作业技术发布时间:2022-08-16T02:03:57.856Z 来源:《工程管理前沿》2022年第4月7期作者:张琦[导读] 在油田正常生产过程中,张琦大港油田采油一厂天津市300280摘要:在油田正常生产过程中,一旦油水井套管损坏,注采井网就会损坏,严重影响油田的正常生产。
为了恢复油水井的正常生产,通常需要对损坏的套管进行修复,以有效避免油水井因套管损坏而停产。
这对油水井的正常生产,提高油田开发的经济效益具有重要的现实意义。
套管损坏的原因多种多样,由于套管损坏的原因不同,采用的修复技术也不同。
因此,有必要根据套管损坏程度合理选择修复工艺。
关键词:套管损坏;原因修井作业;操作技术介绍随着油田勘探开发的不断深入,目前我国大部分油田已进入开发中后期。
油水井经过长时间的生产后,容易发生套管损坏,导致其无法正常生产,严重影响油田的正常生产。
分析了套管损坏的原因,研究了套管损坏的预防措施,探讨了常见的套管损坏修复技术,以供参考。
1、套管损坏原因分析1.1物理因素在井下作业过程中,套管会受到各种力的影响,这些力来自不同的方向。
如果力超过套管的允许极限强度,则套管会损坏。
因此,在下套管设计过程中,必须合理选择套管材料及其强度。
然而,由于我国大多数油田地质条件复杂,很难预测套管的井下条件。
此外,在油水井井下作业过程中,一些井下工具经常与套管发生碰撞或划伤,也会对套管质量造成一定的损坏。
一般来说,套管损坏的物理影响因素主要包括地层移动产生的力引起的套管损坏和外力引起的套管损坏。
其中,地层力引起的套管损坏更为严重。
地层力引起的套管损坏主要包括以下几种情况:(1)岩层塑性流动引起的套管损坏。
(2)盐层坍塌造成套管损坏。
(3)套管故障。
(4)地层蠕变引起的套管损坏。
(5)环境因素造成的套管损坏。
外力引起的套管损坏有三种类型,即摩擦损坏、静水损坏和注水诱导力损坏。
1.2化学因素套管损坏的化学影响因素主要是指地层中的化学物质与套管材料发生化学反应造成套管出现腐蚀,从而形成套管损坏。
管线腐蚀原因及处理
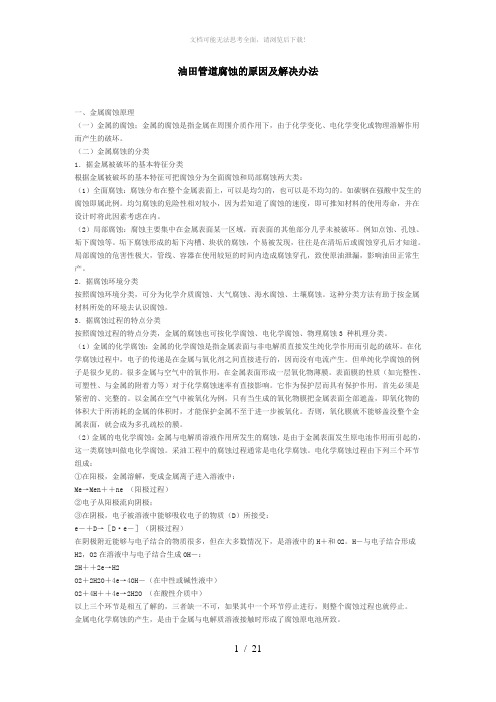
油田管道腐蚀的原因及解决办法一、金属腐蚀原理(一)金属的腐蚀;金属的腐蚀是指金属在周围介质作用下,由于化学变化、电化学变化或物理溶解作用而产生的破坏。
(二)金属腐蚀的分类1.据金属被破坏的基本特征分类根据金属被破坏的基本特征可把腐蚀分为全面腐蚀和局部腐蚀两大类:(1)全面腐蚀:腐蚀分布在整个金属表面上,可以是均匀的,也可以是不均匀的。
如碳钢在强酸中发生的腐蚀即属此例。
均匀腐蚀的危险性相对较小,因为若知道了腐蚀的速度,即可推知材料的使用寿命,并在设计时将此因素考虑在内。
(2)局部腐蚀:腐蚀主要集中在金属表面某一区域,而表面的其他部分几乎未被破坏。
例如点蚀、孔蚀、垢下腐蚀等。
垢下腐蚀形成的垢下沟槽、块状的腐蚀,个易被发现,往往是在清垢后或腐蚀穿孔后才知道。
局部腐蚀的危害性极大,管线、容器在使用较短的时间内造成腐蚀穿孔,致使原油泄漏,影响油田正常生产。
2.据腐蚀环境分类按照腐蚀环境分类,可分为化学介质腐蚀、大气腐蚀、海水腐蚀、土壤腐蚀。
这种分类方法有助于按金属材料所处的环境去认识腐蚀。
3.据腐蚀过程的特点分类按照腐蚀过程的特点分类,金属的腐蚀也可按化学腐蚀、电化学腐蚀、物理腐蚀3 种机理分类。
(1)金属的化学腐蚀:金属的化学腐蚀是指金属表面与非电解质直接发生纯化学作用而引起的破坏。
在化学腐蚀过程中,电子的传递是在金属与氧化剂之间直接进行的,因而没有电流产生。
但单纯化学腐蚀的例子是很少见的。
很多金属与空气中的氧作用,在金属表面形成一层氧化物薄膜。
表面膜的性质(如完整性、可塑性、与金属的附着力等)对于化学腐蚀速率有直接影响。
它作为保护层而具有保护作用,首先必须是紧密的、完整的。
以金属在空气中被氧化为例,只有当生成的氧化物膜把金属表面全部遮盖,即氧化物的体积大于所消耗的金属的体积时,才能保护金属不至于进一步被氧化。
否则,氧化膜就不能够盖没整个金属表面,就会成为多孔疏松的膜。
(2)金属的电化学腐蚀:金属与电解质溶液作用所发生的腐蚀,是由于金属表面发生原电池作用而引起的,这一类腐蚀叫做电化学腐蚀。
化工设备管道腐蚀原因及防腐措施浅析

化工设备管道腐蚀原因及防腐措施浅析在化工生产过程中,设备的腐蚀问题对于生产企业一直都是重点关注的领域。
在化工产品生产过程中会有大量的腐蚀性介质(气体或者液体)或化学物质出现在生产工艺流程中,这些腐蚀性气体长时间和设备发生接触后,设备的表面就会出现锈蚀、腐蚀的情况。
情况严重时还会对装置安全、人身健康造成重大威胁与危害,因此设备的防腐蚀管理对于保证企业的安全生产有着重大意义。
标签:化工;机械设备;腐蚀原因;应对措施一、化工设备常见的腐蚀原因设备材料原因在对于设备的腐蚀原因分析中,设备自身的结构和材料也是影响腐蚀情况的因素之一,具体如下:(1)设备材质选型使用不当设备材料使用不当通常是在安装或检修的过程中,维修安装人员没有选择合适的材料来进行替换或使用。
有的检修人员甚至使用锈迹、不耐腐蚀的材料对原材料部件进行替换,从而导致腐蚀的加剧。
另外检修人员对设备管道的安装维修要求标准太低,比如不锈钢的管道、安装的却是碳钢或者其他材质的紧固件,和设备本身的材料不一致,也会出现渗碳腐蚀的现象。
因此要选择适合的材料配件,避免因为材料的差异发生氧化还原反应,加快设备管道的腐蚀。
(2)材料备件管理混乱由于化工设备在生产装置中总会接触一些的腐蚀性气体。
不同的设备材料如果放置、保管、存储不当就会长期与空气中的腐蚀性气体接触,发生一系列的氧化还原反应,久而久之,腐蚀情况越来越严重。
因此对于设备零件、管道配件等材料需要妥善保管,避免此类情况发生。
(3)设计构造有缺陷对于设备而言,初期的结构设计对于整个设备的运行情况有着至关重要的作用。
结构设计影响着设备整体的承重能力和关键节点的使用耐久程度。
一旦出现结构设计不良,会导致设备出现故障和锈蚀的情况大幅增加。
1.2化工生产中的化学腐蚀由于化工生产的过程会有大量的腐蚀气体产生,如盐酸气体、氯化氢气体等。
这些气体和化学试剂都会和设备表面进行接触从而对金属表面产生腐蚀。
如果维护不当,长时间使用后会导致镀层的脱落,进而对设备本身造成腐蚀。
试论钻井工程对油井套管腐蚀损坏原因及预防措施

钻井液的pH值
钻井液的pH值是影响套管腐蚀 的重要因素之一。一般情况下, 酸性钻井液比碱性钻井液更容易
导致套管腐蚀。
钻井液中的微生物
某些微生物在钻井液中繁殖,可 能对套管造成腐蚀损害。
钻井过程中的物理化学因素对套管腐蚀的影响
压力与温度
钻井过程中,地层压力和钻井液的压力变化可能导致套管 内外产生压力差,从而加速套管腐蚀。同时,温度也是影 响套管腐蚀的重要因素之一。
套管材质
不同材质的套管对腐蚀的抵抗 力不同。
井液成分
井液中的酸、碱、盐等成分对 套管腐蚀有重要影响。
流速和冲刷
流速快、冲刷力强的区域更容 易导致套管腐蚀。
防腐措施
采取有效的防腐措施可以降低 套管的腐蚀速度。
01
钻井工程对油井套管腐蚀 损坏的影响
钻井液对套管腐蚀的影响
钻井液的化学性质
钻井液中通常含有多种化学成分 ,如无机盐、有机溶剂等,这些 成分可能对套管产生腐蚀作用。
工程实例三:采用缓蚀剂防护的套管防护
缓蚀剂防护是一种绿色、高效的防护方法。
缓蚀剂防护通过向油井中注入缓蚀剂,减缓或阻止套 管的腐蚀。该方法具有成本低、操作简便、环保等优 点。在实际应用中,需要根据油气田的实际情况选择 合适的缓蚀剂。
01
结论与展望
研究结论
套管材质的影响
不同材质的套管对腐蚀的敏感性不同。
摩擦与磨损
钻井过程中,钻头与套管壁之间的摩擦和磨损可能导致套 管表面损伤和腐蚀。
电化学腐蚀
在某些情况下,钻井液中的电解质可能引起电化学腐蚀, 导致套管损坏。
钻井过程中的微生物对套管腐蚀的影响
硫酸盐还原菌
这类微生物在缺氧条件下能将钻井液中的硫酸盐还原为硫化 氢,从而加速套管的腐蚀。
不锈钢腐蚀机理、发生原因和维护处理方法
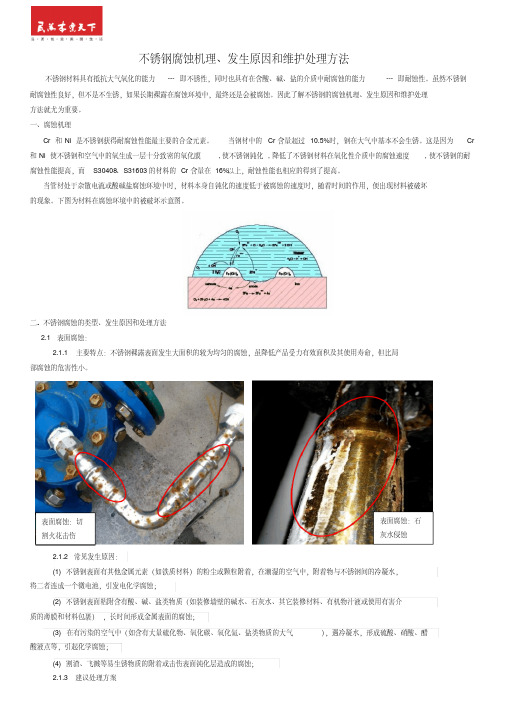
不锈钢腐蚀机理、发生原因和维护处理方法不锈钢材料具有抵抗大气氧化的能力---即不锈性,同时也具有在含酸、碱、盐的介质中耐腐蚀的能力---即耐蚀性。
虽然不锈钢耐腐蚀性良好,但不是不生锈,如果长期裸露在腐蚀环境中,最终还是会被腐蚀。
因此了解不锈钢的腐蚀机理、发生原因和维护处理方法就尤为重要。
一、腐蚀机理Cr 和Ni 是不锈钢获得耐腐蚀性能最主要的合金元素。
当钢材中的Cr 含量超过10.5%时,钢在大气中基本不会生锈。
这是因为Cr 和Ni 使不锈钢和空气中的氧生成一层十分致密的氧化膜,使不锈钢钝化,降低了不锈钢材料在氧化性介质中的腐蚀速度,使不锈钢的耐腐蚀性能提高,而S30408、S31603的材料的Cr 含量在16%以上,耐蚀性能也相应的得到了提高。
当管材处于杂散电流或酸碱盐腐蚀环境中时,材料本身自钝化的速度低于被腐蚀的速度时,随着时间的作用,便出现材料被破坏的现象。
下图为材料在腐蚀环境中的被破坏示意图。
二. 不锈钢腐蚀的类型、发生原因和处理方法2.1 表面腐蚀:2.1.1 主要特点:不锈钢裸露表面发生大面积的较为均匀的腐蚀,虽降低产品受力有效面积及其使用寿命,但比局部腐蚀的危害性小。
2.1.2 常见发生原因:(1) 不锈钢表面有其他金属元素(如铁质材料)的粉尘或颗粒附着,在潮湿的空气中,附着物与不锈钢间的冷凝水,将二者连成一个微电池,引发电化学腐蚀;(2) 不锈钢表面粘附含有酸、碱、盐类物质(如装修墙壁的碱水、石灰水、其它装修材料、有机物汁液或使用有害介质的薄膜和材料包裹),长时间形成金属表面的腐蚀;(3) 在有污染的空气中(如含有大量硫化物、氧化碳、氧化氮、盐类物质的大气),遇冷凝水,形成硫酸、硝酸、醋酸液点等,引起化学腐蚀;(4) 割渣、飞溅等易生锈物质的附着或击伤表面钝化层造成的腐蚀;2.1.3 建议处理方案表面腐蚀:切割火花击伤表面腐蚀:石灰水侵蚀(1) 保持不锈钢表面的洁净,如发现有污染物质和颜色暗淡现象发生,应及时进行清理;(2) 对出现轻度腐蚀的部位,先清除污锈,使用钝化膏溶液或喷雾涂抹,10秒后再用清水进行清洗,使不锈钢表面重新形成钝化膜。
- 1、下载文档前请自行甄别文档内容的完整性,平台不提供额外的编辑、内容补充、找答案等附加服务。
- 2、"仅部分预览"的文档,不可在线预览部分如存在完整性等问题,可反馈申请退款(可完整预览的文档不适用该条件!)。
- 3、如文档侵犯您的权益,请联系客服反馈,我们会尽快为您处理(人工客服工作时间:9:00-18:30)。
PRODUCTION TECHNOLOGY
Stainless steel tubing on oil and gas platforms is used in process instrumentation and sensing, as well as chemical inhi-bition, hydraulic lines, impulse lines and utility applications, over a wide range of temperature, flow and pressure condi-tions. Unfortunately, all over the globe, including the Gulf of Mexico (GOM), the North Sea, the China Sea and so on, cor-rosion of 316 stainless steel tubing has been observed.The two prevalent forms of localized corrosion are pitting corrosion, which is often readily recognizable, and crevice corro-sion, which can be more difficult to observe. The selection of in-adequate tubing alloy and suboptimal installation practices can lead to deterioration of tubing surfaces in a matter of months. Today’s minimally alloyed 316 stainless steel tubing, with close to 10.0% nickel, 2.0% molybdenum and 16.0% chromium, may experience corrosion more readily than the more gener-ously alloyed 316 tubing products produced decades ago.Contamination is another leading cause for surface degra-dation. Such contamination may be caused by iron particles from welding and grinding operations; surface deposits from handling, drilling and blasting; and from sulfur-rich diesel ex-haust. Periodic testing of seawater deluge systems, especially in combination with insufficient freshwater cleansing, may also leave undesirable chloride-laden deposits behind.
PITTING AND CREVICE CORROSIONIn most cases, pitting corrosion of tubing can be readily rec-ognized. Individual shallow pits, and in later stages, deep and sometimes connected pits, can be observed by visual inspec-tion with the unaided eye, Fig. 1. Pitting corrosion starts when the chromium-rich passive oxide film on 316 tubing breaks down in a chloride-rich environment. Higher chloride concen-trations and elevated temperatures increase the likelihood for breakdown of this passive film. Once the passive film has been breached, an electrochemical cell becomes active. Iron goes into solution in the more anodic bottom of the pit, diffuses toward the top and oxidizes to iron oxide, or rust. The iron chloride solution concentration in a pit can increase as the pit gets deep-er. The consequence is accelerated pitting, perforation of tub-ing walls and leaks. Pitting can penetrate deep into the tubing walls, creating a situation where tubing could fail.Crevices are very difficult, or even impossible, to avoid in tubing installations. They exist between tubing and tube sup-ports, in tubing clamps, between adjacent tubing runs and underneath contamination and deposits that may have ac-cumulated on tubing surfaces. Tight crevices pose the great-est danger for crevice corrosion. General tubing corrosion in a
tight crevice causes the oxygen concentration in the fluid con-tained within a crevice to drop. A lower oxygen concentration increases the likelihood for breakdown of the passive surface oxide film, resulting in the formation of a shallow pit. Unlike in pitting corrosion described above, pit formation on tubing that is surrounded by a crevice will lead to an increase in Fe++ con-
centration in the fluid in the gap. Because of the strong interac-tion of Fe++ ions with OH- hydroxyl ions, the pH value drops.
Chloride ions will also diffuse into the gap, being attracted by Fe++ ions, resulting in an acidic ferric chloride solution that can
lead to accelerated corrosion of tubing within the crevice.Ideally, tubing should resist all forms of corrosion, including general, localized (pitting and crevice), galvanic, microbiological, chloride-induced stress corrosion cracking and sour gas cracking. The tubing should also have adequate mechanical properties es-pecially when fluid pressures are high. Erosion resistance comes into play when fluids contain potentially erosive particles. The environmental impact of the tubing should also be of concern: Aquatic life can be harmed by small concentrations of copper ions that can be readily released by copper-zinc alloys.An alloy’s resistance to localized tubing corrosion can be estimated by calculating from its chemical composition the alloy’s Pitting Resistance Equivalent Number (PREN). The most frequently used relationship is:
PREN = %Cr + 3.3·%Mo + 16·%N The higher the PREN value of an alloy, the higher its resis-tance to localized corrosion, i.e., the higher its Critical Pitting Temperature (CPT) and critical Crevice Corrosion Tempera-ture (CCT). These critical temperatures can be experimentally determined following common testing procedures such as ASTM G48 and ASTM G150.