机床导轨的设计
导轨的选型及计算
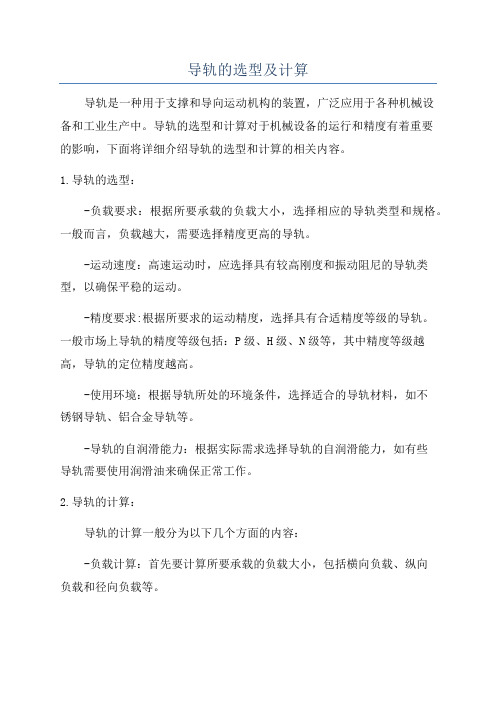
导轨的选型及计算导轨是一种用于支撑和导向运动机构的装置,广泛应用于各种机械设备和工业生产中。
导轨的选型和计算对于机械设备的运行和精度有着重要的影响,下面将详细介绍导轨的选型和计算的相关内容。
1.导轨的选型:-负载要求:根据所要承载的负载大小,选择相应的导轨类型和规格。
一般而言,负载越大,需要选择精度更高的导轨。
-运动速度:高速运动时,应选择具有较高刚度和振动阻尼的导轨类型,以确保平稳的运动。
-精度要求:根据所要求的运动精度,选择具有合适精度等级的导轨。
一般市场上导轨的精度等级包括:P级、H级、N级等,其中精度等级越高,导轨的定位精度越高。
-使用环境:根据导轨所处的环境条件,选择适合的导轨材料,如不锈钢导轨、铝合金导轨等。
-导轨的自润滑能力:根据实际需求选择导轨的自润滑能力,如有些导轨需要使用润滑油来确保正常工作。
2.导轨的计算:导轨的计算一般分为以下几个方面的内容:-负载计算:首先要计算所要承载的负载大小,包括横向负载、纵向负载和径向负载等。
-功率计算:根据负载计算出的数据,再根据所要求的运行速度,计算出导轨所需的功率。
-振动计算:根据负载和速度等参数,计算导轨运动时所产生的振动,并与实际需求进行对比,以确定导轨所需的振动阻尼能力。
-精度计算:根据所要求的运动精度,计算导轨的理论定位精度,并与导轨的精度等级进行比较。
如精度等级不够,需要重新选择导轨。
-刚度计算:根据负载和速度等参数,计算导轨的刚度,并与实际需求进行对比。
若刚度不够,也需要重新选择导轨。
-导轨的寿命计算:根据导轨的材料和工作环境等因素,计算导轨的使用寿命,并根据需求进行修正。
总之,导轨的选型和计算是机械设计的一个重要环节,它涉及到负载要求、运动速度、精度要求、使用环境等多个因素。
通过合理的选型和计算,可以确保导轨的适用性和可靠性,提高机械设备的运行精度和稳定性。
同时,需要注意参考相关的标准和规范,以确保导轨的质量和性能符合要求。
机床导轨宽度计算公式

机床导轨宽度计算公式在机床的设计和制造中,导轨是一个非常重要的部件,它直接影响着机床的精度和稳定性。
导轨的宽度是一个关键参数,它需要根据机床的使用要求和工件加工的特性来进行合理的计算和选择。
本文将介绍机床导轨宽度的计算公式及其影响因素。
机床导轨宽度的计算公式通常可以通过以下公式来进行计算:导轨宽度 = K × F × L。
其中,K为系数,F为工件的最大切削力,L为工件的加工长度。
在实际应用中,K的取值范围通常在1.2~1.5之间,具体取值需要根据机床的类型、加工工艺、工件材料等因素来综合考虑。
F是工件的最大切削力,它是影响导轨宽度的重要因素之一。
工件的最大切削力通常需要通过理论计算或者实验测量来获取,它受到工件材料、刀具类型、切削参数等因素的影响。
L是工件的加工长度,它也是影响导轨宽度的重要因素之一。
工件的加工长度越大,对导轨的要求就越高,因此在计算导轨宽度时需要充分考虑工件的加工长度。
除了上述的计算公式外,还需要考虑一些其他因素对导轨宽度的影响。
首先是机床的类型和规格,不同类型和规格的机床对导轨宽度的要求也有所不同。
例如,大型数控车床和加工中心对导轨宽度的要求通常会比普通车床和铣床要高。
其次是工件的加工精度要求,如果工件的加工精度要求很高,那么对导轨宽度的要求也会相应增加。
此外,还需要考虑机床的使用环境和工作条件,如温度、湿度、振动等因素都会对导轨宽度产生影响。
在实际应用中,导轨宽度的计算需要综合考虑上述因素,并进行合理的选择。
一般来说,为了保证机床的加工精度和稳定性,导轨宽度通常会略大于计算得到的数值,以确保机床在使用过程中能够满足工件加工的要求。
总之,机床导轨宽度的计算是一个复杂的工程问题,需要综合考虑多个因素并进行合理的选择。
通过合理的计算和选择,可以保证机床在加工过程中具有良好的稳定性和加工精度,从而满足不同工件加工的要求。
希望本文所介绍的机床导轨宽度计算公式及其影响因素能够为相关工程技术人员在机床设计和制造中提供一定的参考和帮助。
关于数控外圆磨床砂轮架闭式静压导轨的设计研究

2020/12车辆工程与技术丨Vehicle engineering and technology146车时代AUTO TIME 在数控外圆磨床中,砂轮架静压导轨为重要零部件,未能得到合理设计将造成磨床各轴运动过程中金属直接接触,产生较大磨损,导致机床精度受到影响。
在磨床加工精度要求不断提高的背景下,还应加强静压导轨设计研究,以便使磨床运动性能得到改善。
1数控外圆磨床砂轮架静压导轨设计要求在数控外圆磨床中,静压导轨为床身导轨。
在动导轨沿着静压导轨运动过程中,能否保持较高直线精度将对机床工作精度产生直接影响。
作为滑动导轨,静压导轨之间存在静压油膜,将产生液体摩擦。
为砂轮架提供支撑力的同时,导轨设计还应保证磨损较小,能够保持运动均匀,体现良好油膜刚性和运动精度。
在磨床加工精度达到10-3m 的情况下,工作台运动速度较低,将在0.5-5mm/min 低速下运动不爬行,还应使低速爬行问题得到解决。
2数控外圆磨床砂轮架闭式静压导轨设计方法2.1设计思路传统卸荷静压导轨结构简单,受油膜不均等因素影响,将出现波纹、振纹。
设计开时导轨,利用动导轨自重和外部载荷施加作用力,只能提供一个方向油垫支承,同样会出现油膜不均等问题。
设计闭式静压导轨,能够使油腔和封油面在各个方向保持均匀对称分布,能够使结构运行的稳定性得到保证。
在结构运行的过程中,运动部件上将承受颠覆力矩。
增加压板使辅助导轨面得以形成,能够使主导轨各面接触良好。
在实际设计过程中,可以按照300mm/min 最大移动速度进行设计,最小运行速度则要达到10mm/min。
磨床磨削精度需要达到0.001mm,能够使纵截面保持0.004mm 一致性,因此需要使设计出的静压导轨达到较高刚度和进给精度。
采用双矩形导轨,完成上下方向导向块、进给方向导向块和静压导轨块的对称布置,并完成砂轮架体壳和毛细管节流器的布置,能够获得具有较强承载刚性的主支撑面。
结构组织较为简单,面磨损较小,在出现间隙超差情况时只需要调节油压,并且可以利用三个方向油腔实现上下浮起量和导向控制。
机械设计之导轨的结构布局设计
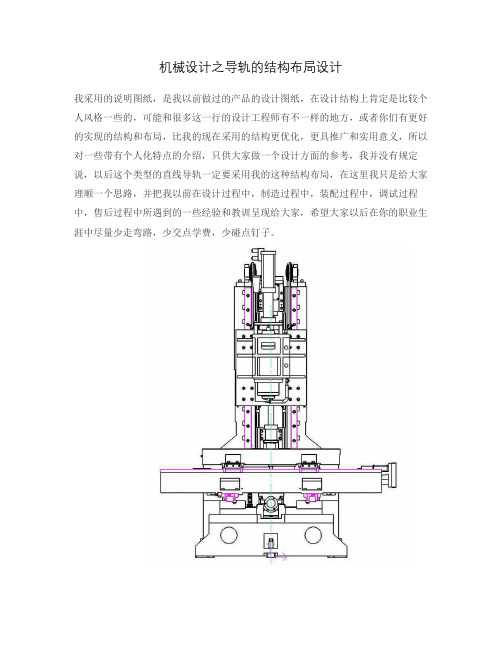
机械设计之导轨的结构布局设计我采用的说明图纸,是我以前做过的产品的设计图纸,在设计结构上肯定是比较个人风格一些的,可能和很多这一行的设计工程师有不一样的地方,或者你们有更好的实现的结构和布局,比我的现在采用的结构更优化,更具推广和实用意义,所以对一些带有个人化特点的介绍,只供大家做一个设计方面的参考,我并没有规定说,以后这个类型的直线导轨一定要采用我的这种结构布局,在这里我只是给大家理顺一个思路,并把我以前在设计过程中,制造过程中,装配过程中,调试过程中,售后过程中所遇到的一些经验和教训呈现给大家,希望大家以后在你的职业生涯中尽量少走弯路,少交点学费,少碰点钉子。
这是一台立式加工中心的光机图纸,其中紫色线条部分就该加工中心的X、Y、Z 三相直线导轨的布置位置,他们的功能就是实现该加工中心X、Y、Z三个方向的传动。
其中X、Y两个方向是水平放置的,而Z向是垂直放置的,这个在直线导轨选型的时候,是需要和导轨供应商确认好放置方式的,你必须告诉供应商你的导轨是用于什么样的状态,是水平,还是垂直,或者是悬空等,供应商在给你做定型推荐的时候,他们也会根据你的使用情况来推荐给你最时候的直线导轨。
再上一张图纸,我们从侧面来看一下,这X、Y、Z三个方面的导轨布局是一个什么样的情况。
如果你是一个有相当经验的机械行业从业者,其实你是应该可以根据上面这两个图纸画出这个立式加工中心的大件图纸了,因为无论是改设备的结构,还是外形,这两张图纸都作了很好的呈现,尤其是一些细节也有了相对详细的描述。
以上给你参考的是一个光机装配图,在一些细节上的表述我会在接下来的图纸里给大家介绍。
我们今天抽取这个立式加工中心的底座来给大家介绍,下面还是要上图说话。
以上这张图就是一个底座的直线导轨装配图,紫色的部分就是导轨的装配状态,在设计的过程中,需要注意的是导轨的跨度的选取,即两条导轨之间的距离,这在某种程度上决定了机床加工的刚性和稳定性,也决定了机床精度的稳定性,同时我们还需要考虑一个关键点,那就是润滑油的聚集与回收,因为这种类型的机床,直线导轨和丝杆都是采用润滑站进行定时定点润滑的,所以润滑后的废油如何收集是一个需要考虑的关键点,如果不作这方面的考虑,那机床在正常使用时,润滑油会四处横流,弄脏一地,这也是体现设计能力和工业水准的地方。
制作导轨的机械加工流程

制作导轨的机械加工流程机床核心---直线导轨一、导轨的功能尽管导轨系统的形式是多种多样的,但工作性质都是相同的,机床工作部件在指定导轨系统上移动,尤如火车沿着铁轨在指定的方向上行驶。
主要体现如下三种基本功能:1、为承载体的运动导向;2、为承载体提供光滑的运动表面;3、把机床的切削所产生的力传到地基或床身上,减少产生的冲击对被动加工零件的影响。
沿导轨系统的运动,大多数为直线运动,也有少数为弧线运动。
直线导轨的很多技术可以直接应用弧形导轨。
支承和引导运动构件沿着一定轨迹运动的零件称为导轨副,也常简称为导轨。
运动部件的运动轨迹有直线、圆或曲线,滚动圆导轨可归人滚动推力轴承,曲线导轨在机械中极少应用。
导轨在机器中是个十分重要的部件,在机床中尤为重要。
机床的加工精度与导轨精度有直接的联系,小批量生产的精密机床,导轨的加工工作量占整个机床加工工作量的40%左右。
而且,导轨一旦损坏,维修十分困难。
按运动学原理,所谓导轨就是将运动构件约束到只有一个自由度的装置。
导轨副中设在支承构件上的导轨面为承导面,称为静导轨,它比较长;另一个导轨面设在运动构件上,称为动导轨,它比较短。
具有动导轨的运动构件常称为工作台、滑台、常用导轨面有平面和圆弧面。
圆弧导轨面构成圆柱形导轨;不同的平导轨面组合,构成矩形导轨面间的摩擦为滑动摩擦者称为滑动导轨,在导轨面间置人滚动元件,使摩擦转变为滚动摩擦者称为滚动导轨。
导轨有闭式和开式之分,闭式导轨可以承受倾覆力矩,而开式导轨则不能。
2015 年,我国出台《中国制造2025》,全面推进实施强国战略,这是我国实施制造强国战略的第一个十年的行动纲领,强调加快推动新一代技术信息与制造技术融合发展,把智能制造作为两化深度融合的主攻方向。
在智能制造里面,机床被誉为工业“母机”,特别是数控机床已日益成为装备制造业的主力加工设备,其数量的多少和技术的高低,不仅是一个地区装备制造业发展水平的重要标志,更是一个国家竞争力强弱的重要体现。
直线导轨滚珠丝杠的结构设计与精度提升
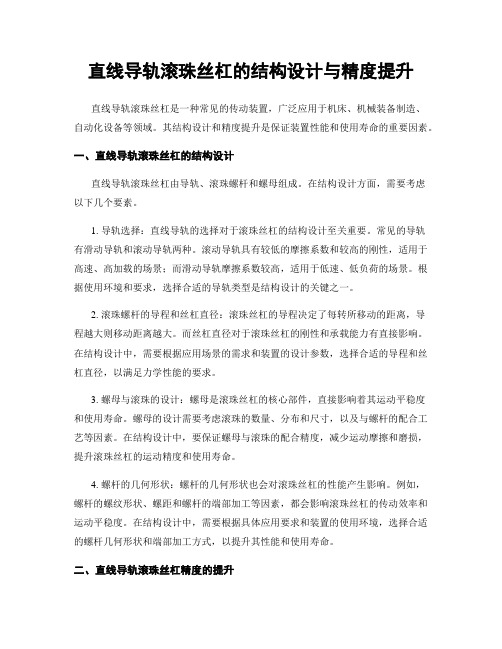
直线导轨滚珠丝杠的结构设计与精度提升直线导轨滚珠丝杠是一种常见的传动装置,广泛应用于机床、机械装备制造、自动化设备等领域。
其结构设计和精度提升是保证装置性能和使用寿命的重要因素。
一、直线导轨滚珠丝杠的结构设计直线导轨滚珠丝杠由导轨、滚珠螺杆和螺母组成。
在结构设计方面,需要考虑以下几个要素。
1. 导轨选择:直线导轨的选择对于滚珠丝杠的结构设计至关重要。
常见的导轨有滑动导轨和滚动导轨两种。
滚动导轨具有较低的摩擦系数和较高的刚性,适用于高速、高加载的场景;而滑动导轨摩擦系数较高,适用于低速、低负荷的场景。
根据使用环境和要求,选择合适的导轨类型是结构设计的关键之一。
2. 滚珠螺杆的导程和丝杠直径:滚珠丝杠的导程决定了每转所移动的距离,导程越大则移动距离越大。
而丝杠直径对于滚珠丝杠的刚性和承载能力有直接影响。
在结构设计中,需要根据应用场景的需求和装置的设计参数,选择合适的导程和丝杠直径,以满足力学性能的要求。
3. 螺母与滚珠的设计:螺母是滚珠丝杠的核心部件,直接影响着其运动平稳度和使用寿命。
螺母的设计需要考虑滚珠的数量、分布和尺寸,以及与螺杆的配合工艺等因素。
在结构设计中,要保证螺母与滚珠的配合精度,减少运动摩擦和磨损,提升滚珠丝杠的运动精度和使用寿命。
4. 螺杆的几何形状:螺杆的几何形状也会对滚珠丝杠的性能产生影响。
例如,螺杆的螺纹形状、螺距和螺杆的端部加工等因素,都会影响滚珠丝杠的传动效率和运动平稳度。
在结构设计中,需要根据具体应用要求和装置的使用环境,选择合适的螺杆几何形状和端部加工方式,以提升其性能和使用寿命。
二、直线导轨滚珠丝杠精度的提升直线导轨滚珠丝杠的精度是衡量其性能优劣的重要指标,涉及装置的定位精度、回程精度和稳定性等方面。
精度的提升可以通过以下几个途径实现。
1. 材料选择和热处理:滚珠丝杠的材料选择和热处理工艺对其精度有较大影响。
材料的选择需要考虑强度、硬度和耐磨性等因素,以适应高负荷和长时间使用的需求。
din 导轨 标准

din 导轨标准din导轨标准。
DIN导轨是一种标准化的机械零件,广泛应用于各种工业设备和机械装置中。
它具有高精度、高可靠性和高稳定性的特点,因此在工业生产中扮演着非常重要的角色。
本文将介绍DIN导轨的标准规范,包括其设计要求、安装要求和使用要求等方面的内容。
首先,DIN导轨的设计要求是非常严格的。
根据DIN标准,导轨的材料应选用高强度、高硬度和耐磨损的材料制成,以确保其在长时间使用中不会出现变形或磨损过快的情况。
此外,导轨的表面应经过精密加工,以保证其表面粗糙度和平整度符合标准要求。
同时,导轨的尺寸和公差也必须符合标准规定,以确保其与其他机械零件的配合精度。
其次,安装要求也是使用DIN导轨时需要重点关注的问题。
根据DIN标准,导轨的安装应在干净、平整的工作台面上进行,以确保其安装精度和稳定性。
在安装过程中,还需要使用专用的安装工具和夹具,以确保导轨与底座的配合精度和紧固稳固性。
此外,在安装完成后,还需要对导轨进行调试和检测,以确保其运行平稳、无卡滞和无噪音。
最后,使用要求是保证DIN导轨正常运行的关键。
根据DIN标准,导轨在使用过程中需要定期进行润滑和清洁,以确保其表面光洁和摩擦系数的稳定性。
同时,还需要对导轨进行定期的检测和维护,以确保其在使用过程中不会出现损坏或磨损过快的情况。
在使用过程中,还需要注意避免导轨受到外部冲击和振动,以确保其稳定性和可靠性。
总之,DIN导轨作为一种重要的机械零件,其标准规范对于保证其正常运行和使用具有非常重要的意义。
只有严格按照标准要求进行设计、安装和使用,才能确保DIN导轨具有高精度、高可靠性和高稳定性的特点,从而更好地为工业生产提供支持和保障。
数控导轨磨床设计

摘要磨床可以加工各种表面,如内、外圆柱面和圆锥面、平面、渐开线齿廓面、螺旋面以及各种成形表面。
磨床可进行荒加工、粗加工、精加工和超精加工,可以进行各种高硬、超硬材料的加工,还可以刃磨刀具和进行切断等,工艺范围十分广泛。
磨床可以加工各种表面,如内、外圆柱面和圆锥面、平面、渐开线齿廓面、螺旋面以及各种成形表面。
磨床的种类很多,按其工作性质可分为:外围磨床、内圆磨床、平面磨床,工具磨床以及一些专用磨床。
如螺纹磨床、球面磨床、花键磨床、导轨磨床与无心磨床等。
导轨磨床就是一种按照工作性质划分出来的磨床。
本文主要是对导轨磨床进行设计与研究。
关键词:导轨磨床,磨床,磨床设计AbstractThe grinder can process a variety of surfaces, such as inner, outer cylindrical surface and a conical surface, plane, tooth profile of involute spiral surface and various surface, forming surface. The grinder can be hogging machining, rough machining, finish machining and ultra precision machining, can be a variety of high hard, superhard materials processing, can also be grinding tool and cutting process, a very wide range of.The grinder can process a variety of surfaces, such as inner, outer cylindrical surface and a conical surface, plane, tooth profile of involute spiral surface and various surface, forming surface. Grinder of many types, according to the nature of their work can be divided into: external grinder, internal grinder, surface grinder, grinding machine tools and some special grinding machine. Thread grinder, grinding machine, such as spherical spline grinding machine, grinder and centerless grinder. Rail grinding machine is a kind of according to the nature of the work out of the grinder.This paper is mainly about the design and research of guideway grinder.Key Words:Rail grinding machine, grinding machine, grinding machine design目录摘要 (I)Abstract (II)目录 (III)第1章绪论 (1)1.1 国内外研究现状 (1)1.2 磨床的现状及其发展趋势 (2)1.3论文研究的主要内容 (2)第2章数控龙门导轨磨床总体方案设计 (4)2.1 机床的设计要求 (4)2.2 设计方案 (4)2.2.1 机械部分设计 (4)2.2.2 数控系统选型 (5)2.3 本章小节 (6)第3章机床主轴箱的设计 (7)3.1 主轴箱的设计要求 (7)3.2主传动系统的设计 (7)3.2.1 主传动功率 (7)3.2.2 驱动源的选择 (8)3.2.3 转速图的拟定 (8)3.2.4传动轴的估算 (10)3.2.5齿轮模数的估算 (11)3.3主轴箱展开图的设计 (12)3.3.1设计的内容和步骤 (12)3.3.2 有关零部件结构和尺寸的确定 (12)3.3.3 各轴结构的设计 (15)3.3.4 主轴组件的刚度和刚度损失的计算 (16)3.4 零件的校核 (17)3.4.1齿轮强度校核 (17)3.4.2传动轴挠度的验算 (18)3.5 本章小节 (19)第4章主轴系统设计及计算 (26)4.1 主轴系统结构设计的原则 (26)4.2主轴部件精度 (26)4.3主轴部件结构 (27)4.4传动方案设计 (27)4.5主轴材料的选择 (28)4.6 主轴参数设计 (31)4.7 主轴组件的刚度计算 (33)4.7 主轴强度计算 (36)4.8 带传动设计 (38)4.9 联轴器设计 (38)4.10 伺服电动机的选择 (39)第5章周边磨头的动力参数进行设计计算 (41)5.1 砂轮架设计的基本要求 (41)5.2 主轴旋转精度及其提高措施 (41)5.3 主轴轴承系统的刚性 (41)5.4 砂轮架主轴初步设计 (41)5.5 主轴刚度校核 (42)5.6 动静压轴承 (43)5.7 传动装置设计 (44)第6章磨头垂直滑板滚珠丝杠副及其支撑方式设计 (50)6.1 对磨头垂直滑板滚珠丝杠副及其支撑方式的基本要求 (50)6.2 磨头垂直滑板滚珠丝杠副及其支撑方式系统的设计要求 (51)6.3滚珠丝杠的选择 (52)P (52)6.3.1 滚珠丝杠副的导程h6.3.2 滚珠丝杠副的载荷及选丝杠 (52)6.4同步齿形带的选择 (54)6.5伺服电机的选择 (54)6.6 滚珠丝杠副的安全使用 (55)6.6.1 润滑 (55)6.6.2 防尘 (56)6.6.3使用 (56)6.6.4 安装 (56)6.8 本章小节 (57)第7章床身、横梁导轨和工作台 (58)7.1 床身结构 (58)7.1.1 对床身结构的基本要求 (58)7.1.2 床身的结构 (59)7.2 导轨 (61)7.2.1 导轨的润滑与防护 (61)7.2.2 导轨的安装调整 (61)7.3 工作台 (62)7.4 本章小节 (62)第8章控制系统大体设计数控系统设计 (63)8.1 概述 (63)8.2 确定硬件电路总体方案 (63)8.3 接口,即I/O 输入/输出接口电路 (64)8.4 数控系统硬件框图 (64)8.4.1 主控制器CPU的选择 (64)8.4.2 程序存储器扩展 (65)8.4.3 数据存储器的扩展 (65)8.4.4 I/O口扩展电路设计 (65)8.4.5 键盘,显示接口电路 (68)8.4.6 8031与控制电机与电液阀8255A的联接其它辅助电路设计 (69)8.4.7 步进电机驱动电路 (69)参考文献 (71)致谢 (72)附录:第1章绪论1.1 国内外研究现状20世纪人类社会最伟大的科技成果是计算机的发明与应用,计算机及控制技术在机械制造设备中的应用是世纪内制造业发展的最重大的技术进步。