特种水泥之道路硅酸盐水泥的生产
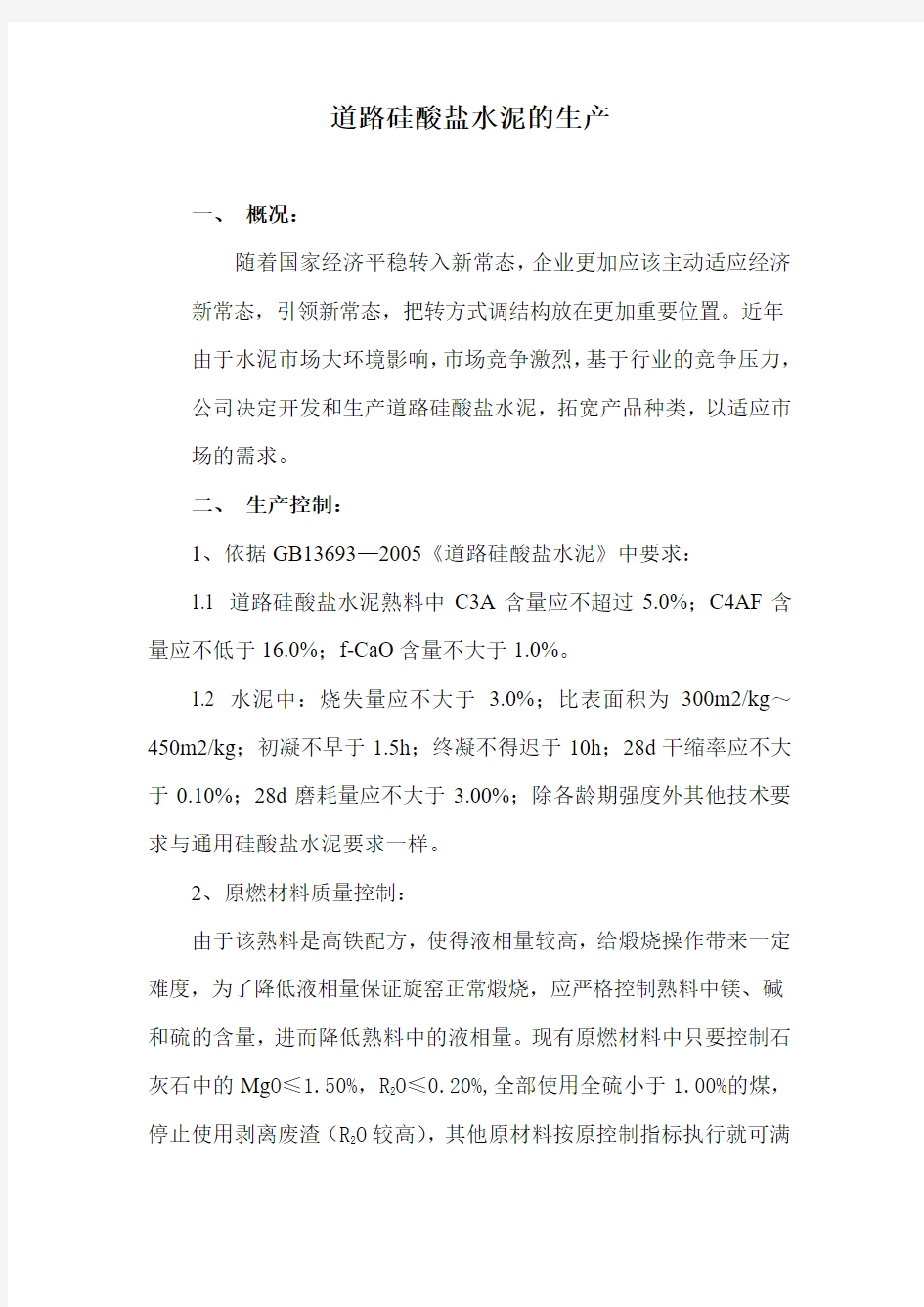

道路硅酸盐水泥的生产
一、概况:
随着国家经济平稳转入新常态,企业更加应该主动适应经济新常态,引领新常态,把转方式调结构放在更加重要位置。近年由于水泥市场大环境影响,市场竞争激烈,基于行业的竞争压力,公司决定开发和生产道路硅酸盐水泥,拓宽产品种类,以适应市场的需求。
二、生产控制:
1、依据GB13693—2005《道路硅酸盐水泥》中要求:
1.1 道路硅酸盐水泥熟料中C3A含量应不超过5.0%;C4AF含量应不低于16.0%;f-CaO含量不大于1.0%。
1.2 水泥中:烧失量应不大于 3.0%;比表面积为300m2/kg~450m2/kg;初凝不早于1.5h;终凝不得迟于10h;28d干缩率应不大于0.10%;28d磨耗量应不大于3.00%;除各龄期强度外其他技术要求与通用硅酸盐水泥要求一样。
2、原燃材料质量控制:
由于该熟料是高铁配方,使得液相量较高,给煅烧操作带来一定难度,为了降低液相量保证旋窑正常煅烧,应严格控制熟料中镁、碱和硫的含量,进而降低熟料中的液相量。现有原燃材料中只要控制石灰石中的Mg O≤1.50%,R2O≤0.20%,全部使用全硫小于1.00%的煤,停止使用剥离废渣(R2O较高),其他原材料按原控制指标执行就可满
足要求。
为保证生产一次成功,矿山要加强管理,确保进厂石灰石满足指标要求;技术质量部在监控好其他原材料的情况下,重点增加进厂石灰石取样频次,由原每班2次改为3次;生料制备部加强巡检,确保堆、取料机正常运行。
3、配料方案的确定:
3.1 设定熟料率值如下表:
3.2 配料方案如下:
3.3 生料、熟料化学分析如下:
4、生料质量控制
道路水泥熟料是高铁配料,转炉渣用量比较大(在10——20吨),用原剥离废渣库入转炉渣(皮带秤最大量程35吨)就能满足配料要求,其他调配库的原材料不变,生产道路水泥熟料之前生料制备部应将剥离废渣库誊空;执行道路水泥熟料配料方案时,技术质量部要密切关注出磨和入窑生料变化情况,随时与中控操作员沟通,入窑生料取样频次由1次/2小时改为1次/1小时,必要时可随时取瞬时样,确保出磨和入窑生料的稳定;
5、熟料质量控制:
道路水泥熟料由于低硅率,低铝率,液相量大,烧结范围窄,窑皮不好控制,烧成带末端容易长厚窑皮,所以就要求中控室和熟料制备部必须加强操作和巡检,稳定窑系统热工制度,严防结厚圈、堆雪
人,控制熟料结粒细小均齐,确保各项指标满足标准要求。
我公司通过研究实际试生产的熟料化学性能指标如下:
6、水泥生产质量控制:
6.1 水泥生产质量控制参数:
技术质量部通过多次小磨试验,确定52.5道路硅酸盐水泥生产控制指标如下:
6.2 用1#磨生产道路硅酸盐水泥,出磨水泥进5#库(5#库刚清空),
生产量800吨。
6.3 在没有用户需要的情况下,包装100吨,放至装车机二楼平
台处,技术质量部取样检验,并将样品送国家水泥质检中心做全套检验,检验结果如下:
所检测各项品质指标符合GB 13693-2005 52.5道路硅酸盐水泥标准。
三、结语:
我公司通过实验和试生产成功研制生产出优质的52.5道路硅酸盐水泥,增加了公司产品种类,在区域内提高了公司的竞争力,也在技术创新方面积累的更加丰富的经验。
广灵金隅水泥有限公司
特种水泥之道路硅酸盐水泥的生产
道路硅酸盐水泥的生产 一、概况: 随着国家经济平稳转入新常态,企业更加应该主动适应经济新常态,引领新常态,把转方式调结构放在更加重要位置。近年由于水泥市场大环境影响,市场竞争激烈,基于行业的竞争压力,公司决定开发和生产道路硅酸盐水泥,拓宽产品种类,以适应市场的需求。 二、生产控制: 1、依据GB13693—2005《道路硅酸盐水泥》中要求: 1.1 道路硅酸盐水泥熟料中C3A含量应不超过5.0%;C4AF含量应不低于16.0%;f-CaO含量不大于1.0%。 1.2 水泥中:烧失量应不大于 3.0%;比表面积为300m2/kg~450m2/kg;初凝不早于1.5h;终凝不得迟于10h;28d干缩率应不大于0.10%;28d磨耗量应不大于3.00%;除各龄期强度外其他技术要求与通用硅酸盐水泥要求一样。 2、原燃材料质量控制: 由于该熟料是高铁配方,使得液相量较高,给煅烧操作带来一定难度,为了降低液相量保证旋窑正常煅烧,应严格控制熟料中镁、碱和硫的含量,进而降低熟料中的液相量。现有原燃材料中只要控制石灰石中的Mg O≤1.50%,R2O≤0.20%,全部使用全硫小于1.00%的煤,停止使用剥离废渣(R2O较高),其他原材料按原控制指标执行就可满
足要求。 为保证生产一次成功,矿山要加强管理,确保进厂石灰石满足指标要求;技术质量部在监控好其他原材料的情况下,重点增加进厂石灰石取样频次,由原每班2次改为3次;生料制备部加强巡检,确保堆、取料机正常运行。
3、配料方案的确定: 3.1 设定熟料率值如下表: 3.2 配料方案如下: 3.3 生料、熟料化学分析如下: 4、生料质量控制 道路水泥熟料是高铁配料,转炉渣用量比较大(在10——20吨),用原剥离废渣库入转炉渣(皮带秤最大量程35吨)就能满足配料要求,其他调配库的原材料不变,生产道路水泥熟料之前生料制备部应将剥离废渣库誊空;执行道路水泥熟料配料方案时,技术质量部要密切关注出磨和入窑生料变化情况,随时与中控操作员沟通,入窑生料取样频次由1次/2小时改为1次/1小时,必要时可随时取瞬时样,确保出磨和入窑生料的稳定; 5、熟料质量控制: 道路水泥熟料由于低硅率,低铝率,液相量大,烧结范围窄,窑皮不好控制,烧成带末端容易长厚窑皮,所以就要求中控室和熟料制备部必须加强操作和巡检,稳定窑系统热工制度,严防结厚圈、堆雪
通用硅酸盐水泥的标准
前言 本标准第、、条为强制性条款,其余为推荐性条款。 本标准参照欧洲水泥试行标准ENV 197-1:2000《通用波特兰水泥》修订。 本标准代替GB175-1999《硅酸盐水泥、普通硅酸盐水泥》、GB1344-1999《矿渣硅酸盐水泥、火山灰质硅酸盐水泥、粉煤灰硅酸盐水泥》、GB12958-1999《复合硅酸盐水泥》三个标准。与GB175-1999、GB1344-1999、GB12958-1999相比,主要变化如下: ——全文强制改为条文强制(本版前言); ——增加通用硅酸盐水泥的定义(本版第条); ——将各品种水泥的定义取消(原版GB175-1999、GB1344-1999、GB12958-1999第3章);——将组成与材料合并为一章,材料中增加了硅酸盐水泥熟料(原版GB175-1999、GB1344-1999、GB12958-1999第4章,本版第4章); ——普通硅酸盐水泥中“掺活性混合材料时,最大掺量不超过15%,其中允许用不超过水泥质量5%的窑灰或不超过水泥质量10%的非活性混合材料来代替”改为“活性混合材料掺加量为>5%,≤20%,其中允许用不超过水泥质量5%符合本标准第条的窑灰或不超过水泥质量8%符合本标准第条的非活性混合材料代替”。(原版GB175-1999中第条,本版第条); ——将矿渣硅酸盐水泥中矿渣掺加量由“20%~70%”改为“>20%,≤70%”(原版GB1344-1999中第条,本版第条、条); ——将火山灰质硅酸盐水泥中火山灰质混合材料掺量由“20%~50%”改为“>20%,≤40%”(原版GB1344-1999中第条,本版第条); ——将粉煤灰硅酸盐水泥中粉煤灰掺量由“20%~40%”改为“>20%,≤40%”(原版GB1344-1999中第条,本版第条); ——将复合硅酸盐水泥中混合材料总掺加量由“应大于15%,但不超过50%”改为“>20%,≤50%”(原版GB12958-1999中第3章,本版第条); ——材料中增加了粒化高炉矿渣粉(本版第、条); ——取消了粒化精铬铁渣、粒化增钙液态渣、粒化碳素铬铁渣、粒化高炉钛矿渣等混合材料以及符合附录A新开辟的混合材料,并将附录A取消(原版GB12958-1999中第条、第条和附录A) ——增加了M类混合石膏(原版GB175-1999、GB1344-1999和GB12958-1999中第3章,本版第条); ——助磨剂允许掺量由“不超过水泥质量的1%”改为“不超过水泥质量的%”(原版GB175-1999、GB1344-1999和GB12958-1999中第条,本版第条); ——普通水泥强度等级中取消和(原版GB175-1999中第5章,本版第5章); ——增加了氯离子含量的要求,即水泥中氯离子含量不大于%(本版第条); ——取消了细度指标要求,但要求在试验报告中给出结果(原版GB175-1999第条、GB1344-1999、GB12958-1999中第条,本版条); ——将复合硅酸盐水泥的强度等级改为和矿渣硅酸盐水泥、火山灰硅酸盐水泥、粉煤灰硅酸盐水泥一致(原版GB12958-1999中第条,本版第条) ——增加了水泥组分的试验方法(本版第条); ——强度试验方法中增加了“掺火山灰混合材料的普通硅酸盐水泥、粉煤灰硅酸盐水泥和复合硅酸盐水泥在进行胶砂强度检验时,其用水量按水灰比和胶砂流动度不小于180mm来确定。当流动度小于180mm时,须以的整倍数递增的方法将水灰比调整至胶砂流动度不小于180mm”(原版GB1344-1999第条,本版第条); ——将“水泥出厂编号按水泥厂年生产能力规定”改为“水泥出厂编号按单线年生产能力规定”(原版GB175-1999、GB1344-1999、GB12958-1999中第条,本版第条);
硅酸盐水泥生产工艺
硅酸盐水泥生产工艺 水泥生产工艺要点:两磨一煅烧 一、硅酸盐水泥生产方法分类 (一)按生料制备方法分
立窑生产工艺过程
硅酸盐水泥生产的原料 1.硅酸盐水泥的主要成分 硅酸三钙(3CaO·SiO2)、硅酸二钙(2CaO·SiO2)、铝酸三钙(3CaO·AI2O3)、 铁铝酸四钙(4CaO·AI2O3·Fe2O3) 其中:CaO 62~67%;SiO220~24%;AI2O34~7%;Fe2O32~6%。 2.硅酸盐水泥生产的主要原料 (1)石灰质原料: 以碳酸钙为主要成分的原料,是水泥熟料中CaO的主要来源。如石灰石、白垩、石灰质泥灰岩、贝壳等。一吨熟料约需1.4~1.5吨石灰质干原料,在生料中约占80%左右。 石灰质原料的质量要求 (2)粘土质原料: 含碱和碱土的铝硅酸盐,主要成分为SiO2,其次为AI2O3,少量Fe2O3,是水泥熟料中SiO2、AI2O3、Fe2O3的主要来源。粘土质原料主要有黄土、粘土、页岩、泥岩、粉砂岩及河泥等。一吨熟料约需0.3~0.4吨粘土质原料,在生料中约占11~17%。 粘土质原料的质量要求 223 (3)主要原料中的有害成分 ①MgO:影响水泥的安定性。水泥熟料中要求MgO<5%,原料中要求MgO<3%。 ②碱含量(K2O、Na2O):对正常生产和熟料质量有不利影响。水泥熟料中要求R2O<1.3%,原 料中要求R2O<4%。 ③P2O5:水泥熟料中含少量的P2O5对水泥的水化和硬化有益。当水泥熟料中P2O5含量在0.3%时, 效果最好,但超过1%时,熟料强度便显著下降。P2O5含量应限制。 ④TiO2:水泥熟料中含有适量的TiO2,对水泥的硬化过程有强化作用。当TiO2含量达0.5~1.0%, 强化作用最显著,超过3%时,水泥强度就要降低。如果含量继续增加,水泥就会溃裂。因此在石灰石原料中应控制TiO2<2.0%。 3. 硅酸盐水泥生产的辅助原料 (1)校正原料 ①铁质校正原料:补充生料中Fe2O3的不足,主要为硫铁矿渣和铅矿渣等。 ②硅质校正原料:补充生料中SiO2的不足,主要有硅藻土等。 ③铝质校正原料:补充生料中AI2O3的不足,主要有铝钒土、煤矸石、铁钒土等。
白色硅酸盐水泥标准
白色硅酸盐水泥标准 1 主题内容与适用范围 本标准规定了白色硅酸盐水泥的组成、技术要求、试验方法、检验规则、包装与标志、贮存与运输等。 本标准适用于白色和彩色灰浆、砂浆及混凝土用白色硅酸盐水泥。 2 引用标准 GB 176 水泥化学分析方法 GB 177 水泥胶砂强度检验方法 GB 1345 水泥细度检验方法(80μm筛筛析法) GB 1346 水泥标准稠度用水量、凝结时间、安定性检验方法 GB 5483 用于水泥中的石膏和硬石膏 GB 5950 建筑材料与非金属矿产品白度试验方法通则 GB 9774 水泥包装用袋 GSBA 67001 氯化镁粉末状物质白度实物标准 ZB Q12 001 掺入水泥中的回转窑窑灰 3 定义 由白色硅酸盐水泥熟料加入适量石膏,磨细制成的水硬性胶凝材料称为白色硅酸盐水泥(简称白水泥)。 磨制水泥时,允许加入不超过水泥重量5%的石灰石或窑灰作为外加物。 水泥粉磨时允许加入不损害水泥性能的助磨剂,加入量不得超过水泥重量的1%。 4 组分材料 4.1 白色硅酸盐水泥熟料 以适当成分的生料烧至部分熔融,所得以硅酸钙为主要成分,氧化铁含量少的熟料。 4.2 石膏 天然二水石膏应符合GB5483的规定。 4.3 石灰石 作为外加物的石灰石中的三氧化二铝含量不得超过2.5%。 4.4 窑灰 窑灰应符合ZBQ12001的规定,且白度不得低于70%。 5 技术要求 5.1 氧化镁熟料中氧化镁的含量不得超过4.5%。 5.2 三氧化硫水泥中三氧化硫的含量不得超过3.5%。 5.3 细度0.080mm方孔筛筛余不得超过10%。 5.4 凝结时间初凝不得早于45min,终凝不得迟于12h。 5.5 安定性用沸煮法检验必须合格。 5.6 强度各标号各龄期强度不得低于表1的数值。
公路工程水泥及水泥混凝土试验规程
公路工程水泥及水泥混凝土试验规程 T0501—2005水泥取样方法 1目的、适用范围和引用标准 本方法规定了水泥取样的工具、部位、数量及步骤等。 本方法适用于硅酸盐水泥、普通硅酸盐水泥、矿渣硅酸盐水泥、粉煤灰硅酸盐水泥、火山灰硅酸盐水泥、复合硅酸盐水泥、道路硅酸盐水泥及指定采用本方法的其它品种水泥。 引用标准: GB175-1999《硅酸盐水泥、普通硅酸盐水泥》 GB1344—1999《矿渣硅酸盐水泥、火山灰质硅酸盐水泥及粉煤灰硅酸盐水泥》 GB12958—1999《复合硅酸盐水泥》 GB13693—1992《道路硅酸盐水泥》 2仪器设备 ⑴袋装水泥取样器。 ⑵散装水泥取样器。 3取样步骤 3.1取样数量应符合各相应水泥标准的规定。 3.2分割样 3.2.1袋装水泥:毎1/10编号从一袋中取至少6kg。 3.2.2散装水泥:每1/10编号在5min内取至少6kg。 3.3袋装水泥取样器:随机选择20个以上不同的部位,将取样管插入水泥适当深度,用大拇指按住气孔,小心抽出取样管。将所取样品放入洁净、干燥、不易受污染的容器中。 3.4散装水泥取样器:通过转动取样内管控制开关,在适当位置插
入水泥—定深度,关闭后小心抽出。将所取样品放入洁净、干燥、不易受污染的容器中。 4样品制备 4.1样品缩分 样品缩分可采用二分器,一次或多次将样品缩分到标准要求的规定量。 4.2试验样及封存样 将每一编号所取水泥混合样通过0.9mm方孔筛,均分为试验样和封存样。 4.3分割样 每一编号所取10个分割样应分别通过0.9mm方孔筛,不得混杂。5样品的包装及贮存 5.1样品取得后应存放在密封的金属容器中,加封条。容器应洁净、干燥、防潮、密闭、不易破损、不及水泥发生反应。 5.2封存样应密封保管3个月。试验样及分割样亦应妥善保管。5.3在交货及验收时,水泥厂和用户共同取实物试样,封存样由买卖双方共同签封。以抽取实物试样的检验结果为验收依据时,水泥厂封存样保存期为40d;以同编号水泥的检验报告为验收依据时,水泥厂封存样保存期为3个月。 5.4存放样品的容器应至少在一处加盖清晰、不易擦掉的标有编号、取样时间、地点、人员的密封印,如只在一处标志应在器壁上。 5.5封存样应贮存于干燥、通风的环境中。 6取样单 样品取得后,均应由负责取样操作人员填写取样单. T0504—2005水泥比表面积测定方法(勃氏法) 1目的、适用范围和引用标准 本方法规定采用勃氏法进行水泥比表面积测定。
开题报告:年产500万吨粉煤灰硅酸盐水泥生产线的工艺设计
科技学院 毕业设计(论文)开题报告 题目年产500万吨粉煤灰硅酸盐水泥生产线的工艺设计学院冶金学院 专业班级无机非金属材料工程2011-01 学生姓名学号 20114 指导教师 2014 年 12 月 20 日
开题报告填写要求 1.开题报告作为毕业设计(论文)答辩委员会对学生答辩资格审查的依据材料之一。此报告应在指导教师指导下,由学生在毕业设计(论文)工作开始后2周内完成,经指导教师签署意见及系主任审查后生效。 2.开题报告内容必须用黑墨水笔工整书写或按教务处统一设计的电子文档标准格式(可从教务处网址上下载)打印,禁止打印在其它纸上后剪贴,完成后应及时交给指导教师签署意见。 3.学生查阅资料的参考文献理工类不得少于10篇,其它不少于12篇(不包括辞典、手册)。 4.“本课题的目的及意义,国内外研究现状分析”至少2000字,其余内容至少1000字。
毕业设计(论文)开题报告 1.本课题的目的及意义,国内外研究现状分析 1.1本设计的目的和意义 据我国目前的电力系统来看,我国目前火力发电仍是占主要的地位,粉煤灰是其发展过程中不可避免的排放量大的工业废料。不仅是火力发电厂,各种依靠煤粉燃烧获得热源等的企业都是粉煤灰的主要产源。粉煤灰不仅需要占大量的土地来存放,而且对环境的污染也很大,因此对粉煤灰加以利用是解决当前问题的首选。 我国目前正处于高速发展阶段,各行各业的发展都离不开建筑,因此对水泥的需求仍处于上升阶段。虽然我国是水泥生产大国,但是由于水泥行业的高二氧化碳排放量以及粉尘、有害气体等的排放,致使水泥行业的发展受到了限制。要降低这些废气等的排放,就要减少水泥生产中熟料的使用。早在1990年,美国就提出了绿色混凝土的概念。绿色高性能混凝土的特征有:更多地节约熟料水泥,降低能耗与环境污染;更多地掺加工业废料为主的细掺料;更大的发挥混凝土的高性能优势,减少水泥与混凝土的用量[1]。粉煤灰在水泥熟料矿物水化产物氢氧化钙的激发下具有水化活性而形成一定的强度组分,能与水泥浆硬化体晶格坚固地结合起来,进而提高了混凝土的长龄期强度和混凝土的耐久性[2]。因此,用粉煤灰部分替代水泥熟料具有重要的意义。 但是,根据前人的研究,粉煤灰能与水泥水化产生的Ca(OH) 发生二次水 2 化反应在常温下反应过程非常缓慢,使水泥早期强度过低,造成其利用率一直很低[3]。按照GB1344-92规定,粉煤灰硅酸盐水泥中粉煤灰掺入量按重量百分比计为20%~40%,而目前我国大多水泥窑生产的粉煤灰水泥掺入量只有不到30%,且达不到应有的强度等级[4-5]。 究其根本原因,是因为粉煤灰的活性在前期并不理想,致使粉煤灰水泥没有具有应有的早期强度。因此想要提高粉煤灰的掺入量,提高粉煤灰水泥的性能,就应该从改善粉煤灰的活性着手。粉煤灰活性影响因素可分为:化学成分、晶体组成和玻璃相含量与结构[6]。万雪峰[7]等人对激发粉煤灰活性的措施物理法、物理化学法以及化学法做出了对比研究,认为化学法的活化程度高,且不限粉煤灰的掺入量,是一种可行的简单的方法。化学法主要是通过添加各种早强剂、诱导剂、激发剂等,使粉煤灰水泥的水化反应速度缩短,从而改善粉煤灰水泥的早期强度不足和初凝时间过长的缺陷,提高粉煤灰的掺入量[8-10]。物理法可以通过在研磨粉煤灰时填入助磨剂,改善粉煤灰的粒度,从而提高粉煤灰水泥的水化速度。焦晓飞[11]通过对粉煤灰掺入粒径的研究得到粉煤灰颗粒,粒度集中在10μm~20μm的粉煤灰活性最佳,水化速度最快,
硅酸盐水泥的生产原料、工艺流程参考模板
硅酸盐水泥生产的原料 聚煤网2014-05-23 15:12:12 浏览11 1.硅酸盐水泥的主要成分 硅酸三钙(3CaO?SiO2)、硅酸二钙(2CaO?SiO2)、铝酸三钙(3CaO?AI2O3)、铁铝酸四钙(4CaO?AI2O3?Fe2O3)其中:CaO 62~67%; SiO2 20~24%; AI2O3 4~7%; Fe2O3 2~6%。 2.硅酸盐水泥生产的主要原料 (1) 石灰质原料: 以碳酸钙为主要成分的原料,是水泥熟料中CaO的主要来源。如石灰石、白垩、石灰质泥灰岩、贝壳等。一吨熟料约需1.4~1.5吨石灰质干原料,在生料中约占80%左右。石灰质原料的质量要求 品位 CaO(%) MgO(%) R2O(%) SO3(%)燧石或石英(%) 一级品>48 <2.5 <1.0 <1.0 <4.0 二级品 45~48 <3.0 <1.0 <1.0 <4.0 (2)粘土质原料: 含碱和碱土的铝硅酸盐,主要成分为SiO2,其次为AI2O3,少量Fe2O3,是水泥熟料中SiO2、AI2O3、Fe2O3的主要来源。粘土质原料主要有黄土、粘土、页岩、泥岩、粉砂岩及河泥等。一吨熟料约需0.3~0.4吨粘土质原料,在生料中约占11~17%。粘土质原料的质量要求 品位硅酸率铁率 MgO(%) R2O(%) SO3(%)塑性指数 一级品 2.7~3.5 1.5~3.5 <3.0 <4.0 <2.0 >12 二级品 2.0~2.7或3.5~4.0 不限<3.0 <4.0 <2.0 >12 一般情况下SiO2含量60~67%,AI2O3含量14~18%。 (3)主要原料中的有害成分 ① MgO:影响水泥的安定性。水泥熟料中要求MgO<5%,原料中要求MgO<3%。 ②碱含量(K2O、Na2O):对正常生产和熟料质量有不利影响。水泥熟料中要求R2O<1.3%,原料中要求R2O<4%。 ③ P2O5:水泥熟料中含少量的P2O5对水泥的水化和硬化有益。当水泥熟料中P2O5含量在 0.3%时,效果最好,但超过1%时,熟料强度便显著下降。P2O5含量应限制。 ④ TiO2:水泥熟料中含有适量的TiO2,对水泥的硬化过程有强化作用。当TiO2含量达0.5~ 1.0%,强化作用最显著,超过3%时,水泥强度就要降低。如果含量继续增加,水泥就会溃裂。因此在石灰石原料中应控制TiO2< 2.0%。 3. 硅酸盐水泥生产的辅助原料 (1)校正原料
建筑材料复习-硅酸盐类水泥
学习指导 本章学习主要围绕着由水泥的生产到最终形成水泥石这一过程来进行的。在这一过程中主要讲述了水泥熟料的矿物组成和掺混合材的水化特性及反应对生成的水泥性质的影响,从而掌握通用水泥的特性,如何用通过水泥的技术性质来控制水泥的质量,水泥石的腐蚀及防腐。在掌握通用水泥的基础上了解其它品种的硅酸盐水泥。同时要求了解铝酸 盐类水泥。 一、解释名词 1.水硬性胶凝材料 2.硅酸盐类水泥 3.水泥的初凝和终凝 4.体积安定性 5.活 性混合材 6.火山灰性7.潜在水硬性8.标准稠度需水量9.水化热10.水泥的风化11.水泥的细度12.非活性混合材13.水泥的废品及不合格品14.水泥标号富余系数。 二、填空 1.通用水泥中,硅酸盐水泥代号为_、_,普通水泥代号为_,矿渣水泥代号为_,火山灰水泥代号为_,粉煤灰水泥代号为_。 2.硅酸盐水泥水泥熟料的矿物组成为_、_、_、_,简写为_、_、_、_。 3.变硅酸盐水泥的矿物组成可制得具有不同特性的水泥,提高_含量,可制得_,提高_和_,可制得快硬水泥,降低_和_的含量,提_的含量,可制得中、低热水泥;提高_含量降低_含量可制得道路水泥;降低_含量可制得白水泥。 4.在硅酸盐水泥矿物组成中,水化放热量最大且最快,为_,其次_,_水化放热量最小,最慢的为_。对前期强度起决定性影响的为_。对后期强度提高有较大影响的为_。 5.石膏在硅酸盐水泥中起到_的作用,在矿渣水起到_和_的作用。 6.常用的活性混合材为_、_、_,活性混合材料的主要化学成分是_和_,这些活性成分能与引起水泥腐蚀的水化产物_反应,生成_和_而参与水泥凝结硬化。 7.在水泥矿物组成中反应速度最快的为_,其次为_,最慢的为_。 8.水泥矿物组成与水化反应后,生成的主要水化产物有_凝胶、_凝胶、_晶体、_晶体、_晶体,其中_约占70%,_约占20%。 9.在火山灰水泥生产加人石膏,生成钙矾石晶体,它不仅在水泥初期起到一定作用,而且会起_的作用。 10.水泥硬化过程中,_天强度增长幅度较大,_天强度增长率有所降低,_天强度增长率进一步下降。28天后强度_。 11.活性混合材的激发剂分为_和_两类。 12.掺混合材硅酸盐水泥的水化首先是_的水化,然后水化生成的_与_发生反应。故掺混合材硅酸盐水泥的水化进行了二次反应。 13.水泥熟料中掺有活性混合材可使水泥早期强度_,后期强度,水化热_,耐酸及耐水性。 14.硬化后水泥主要是由_、_、_、_等组成结构体。 15.引起水泥石腐蚀的内因主要是由于水化产物中含有_、_及水泥石的_所造成的。 16.水泥石腐蚀的类型主要有_、_、_、_。 17.防止水泥石腐蚀的措施主要有_、_、_三种方法。 18.硅酸盐水泥的细度用_表示,其他品种的通用水泥用_表示。
GB175~2007通用硅酸盐水泥标准
GB 175-2007 通用硅酸盐水泥 前言 本标准与欧洲水泥标准ENV197-1:2000《通用波特兰水泥》的一致性程度为非等效。本标准自实施之日起代替GB175-1999《硅酸盐水泥、普通硅酸盐水泥》、GB1344-1999《矿渣硅酸盐水泥、火山灰质硅酸盐水泥、粉煤灰硅酸盐水泥》、GB12958-1999《复合硅酸盐水泥》三个标准。 ——将火山灰质硅酸盐水泥中火山灰质混合材料掺量由“20%~50%”改为“>20%且≤40%”(原版GB1344-1999中第3.2条,本版第5.1条); ——将复合硅酸盐水泥中混合材料总掺加量由“应大于15%,但不超过50%”改为“>20%且≤50%”(原版GB12958-1999中第3章,本版第5.1条); ——取消了复合硅酸盐水泥中允许掺加粒化精炼铬铁渣、粒化增钙液态渣、粒化碳素铬铁渣、粒化高炉钛矿渣等混合材料以及符合附录A新开辟的混合材料,并将附录A取消(原版GB12958-1999中第4.2、4.3条和附录A); ——普通水泥强度等级中取消了32.5和32.5R(原版GB175-1999中第5章,本版第6章); ——增加了氯离子限量的要求,即水泥中氯离子含量不大于0.06%(本版第7.1条); ——增加了选择水泥组分试验方法的原则和定期校核要求(本版第8.1条); ——将“按0.50水灰比和胶砂流动度不小于180mm来确定用水量”的规定的适用水泥品种扩大为火山灰质硅酸盐水泥、粉煤灰硅酸盐水泥、复合硅酸盐水泥和掺火山灰质混合材料的普通硅酸盐水泥(原版GB1344-1999第7.5条,本版第8.5条);
——编号与取样中增加了年生产能力“200×104t以上”的级别,即:200×104t以上,不超过4000t为一个编号;将“120万吨以上,不超过1200吨为一个编号”改为“120×104t~200×104t,不超过2400t为一个编号”(原版GB175-1999、GB1344-1999、GB12958-1999中第8.1条,本版第9.1条); ——将“出厂水泥应保证出厂强度等级,其余技术要求应符合本标准有关要求”改为“经确认水泥各项技术指标及包装质量符合要求时方可出厂”(原版GB175-1999、GB1344-1999、GB12958-1999中第8.2条,本版第9.2条); ——增加了出厂检验项目(本版第9.3条); ——取消了废品判定(原版GB175-1999、GB1344-1999、GB12958-1999中第9.3条); ——检验报告中增加了“合同约定的其他技术要求”(原版GB175-1999、GB1344-1999、GB12958-1999中第8.4条,本版第9.5条); ——包装标志中将“且应不少于标志质量的98%”改为“且应不少于标志质量的99%”(原版GB175-1999、GB1344-1999、GB12958-1999中第9.1条,本版第10.1条); ——包装标志中将“火山灰质硅酸盐水泥、粉煤灰硅酸盐水泥和复合硅酸盐水泥包装袋的两侧印刷采用黑色”改为“火山灰质硅酸盐水泥、粉煤灰硅酸盐水泥和复合硅酸盐水泥包装袋的两侧印刷采用黑色或蓝色”(原版GB1344-1999、GB12958-1999中第9.2条,本版第10.2条)。 本标准由中国建筑材料工业协会提出。 本标准由全国水泥标准化技术委员会(SAC/TC184)归口。
硅酸盐水泥___论文
河南大学土木建筑学院课题:硅酸盐水泥
硅酸盐水泥 胶凝材料是指在物理、化学作用下,从具有可塑性的浆体逐渐变成坚固石状体的过程,能将其他物料胶结为整体并具有一定机械强度的物质。因其具有原料丰富、生产成本低、耐久性好、适应性强、耐火性好等众多优点而广泛应用于工业、民用建筑、水利工程等建设之中,成为在国民经济及人民生活中不可缺少的重要材料。 胶凝材料一般可分为有机和无机两类。有机胶凝材料是指各种树脂和沥青等;无机胶凝材料又可分为水硬性和非水硬性。水硬性胶凝材料在拌水后技能在空气中硬化一,又能在水中硬化并具有强度,通常称为水泥,如硅酸盐水泥、铝酸盐水泥、硫酸盐水泥等;非水硬性胶凝材料是指不能在水中硬化,但能在空气中或其他条件下硬化,如石灰、石膏、镁质胶凝材料等等。 在众多的胶凝材料中,水泥占有尤为突出的,它是基本建设的主要原料之一,广泛应用于工业、农业、国防、交通、城市建设、水利及海洋开发等工程建设。水泥工业的发展对保证国家建设和提高生活水平具有十分重要的意义。水泥按其主要矿物组成可分为硅酸盐水泥、铝酸盐水泥、铁铝酸盐水泥、氟铝酸盐水泥、少熟料或无熟料水泥。水泥的主要技术特征是:水硬性(分为快硬和特快硬两类);水化热(分为中热和低热两类);抗硫酸盐性(分中抗硫酸盐腐蚀和高抗硫酸盐腐蚀);膨胀性(分为膨胀和自应力);耐高温性(铝酸盐水泥的耐高温性以水泥中氧化铝含量分级)。 在水泥诸多品种中,硅酸盐水泥是应用最广泛和研究最多的。在此从硅酸盐水泥的分类、生产、技术要求、性能及应用等方面对硅酸盐水泥进行简单的研究分析。 所谓硅酸盐水泥是指从黏土和石灰石为原料,经高温煅烧得到以硅酸盐钙为主要成分的熟料,加入0—5%的混合材料和适量石膏磨细制成的水硬性胶凝材料,国际上统称为波特兰水泥。 硅酸盐水泥的分类 硅酸盐水泥包括纯熟料硅酸盐水泥和掺混合材料硅酸盐水泥两类,我国按其混合材料的掺加情况,共分为如下五类:纯熟料硅酸盐水泥、普通硅酸盐水泥、矿渣硅酸盐水泥、火山灰质硅酸盐水泥粉煤灰硅酸盐水泥。 纯熟料硅酸盐水泥在硅酸盐水泥熟料中加入适量石膏,磨细而成的水泥,分425、525、625、725四个标号。其早期强度比其他几种硅酸盐水泥高5~10%,抗冻性和耐磨性较好,适用于配制高标号混凝土,用于较为重要的土木建筑工程。 普通硅酸盐水泥简称普通水泥。由硅酸盐水泥熟料掺加少量混合材料和适量石膏磨细而成。混合材料的加入量根据其具有的活性大小而定。普通水泥分为275、325、425、525、625和725六个标号,广泛用于制做各种砂浆和混凝土。 矿渣硅酸盐水泥简称矿渣水泥。由硅酸盐水泥熟料和粒化高炉矿渣,加
通用硅酸盐水泥规范标准
前言 本标准第7.1、7.3.1、7.3.2、7.3.3、8.4为强制性条款,其余为推荐性条款。 本标准与欧洲水泥标准ENV197-1:2000《通用波特兰水泥》的一致性程度为非等效。 本标准自实施之日起代替GB175-1999《硅酸盐水泥、普通硅酸盐水泥》、 GB1344-1999《矿渣硅酸盐水泥、火山灰质硅酸盐水泥、粉煤灰硅酸盐水泥》、 GB12958-1999《复合硅酸盐水泥》三个标准。 与GB175-1999、GB1344-1999、GB12958-1999相比,本标准主要变化如下:全文强制改为条文强制;增加了通用硅酸盐水泥的定义;将各品种水泥的定义取消(原版GB175-1999、GB1344-1999、GB12958-1999第3章;将组分与材料合并为一章(原版GB175-1999、GB1344-1999、GB12958-1999第4章,本版第5章);普通硅酸盐水泥中“掺活性混合材料时,最大掺量不超过15%,其中允许用不超过水泥质量5%的窑灰或不超过水泥质量10%的非活性混合材料来代替”改为“活性混合材料掺加量为>5%且≤20%,其中允许用不超过水泥质量8%且符合本标准第5.2.4条的非活性混合材料或不超过水泥质量5%且符合本标准第5.2.5条的窑灰代替”(原版GB175-1999中第3.2条,本版第5.1条); ——将矿渣硅酸盐水泥中矿渣掺加量由“20%~70%”改为“>20%且≤70%”,并分为A型和B型。A型矿渣掺量>20%且≤50%,代号P.S.A;B型矿渣掺量>50%且≤70%,代号P.S.B (原版GB1344-1999中第3.1条,本版第5.1条);
水泥胶砂流动度、道路硅酸盐水泥计算题
计算题: 1、某品种水泥,在进行胶砂流动度测定时,测得胶砂底面互相垂直的两个方向直径分别为193毫米和196毫米,试计算该水泥胶砂流动度。 解: 该水泥胶砂流动度为(193+196)÷2=194(毫米) 2、某道路硅酸盐水泥进行安定性试验,沸煮结束后,测量两试件煮后增加距离分别为0.5毫米和5.0毫米,判断该水泥安定性是否合格。 解: 因为两个试件煮后增加距离的差值为:5.0-0.5=4.5(毫米)>4.0毫米 所以应用同一样品立即重做一次试验。 3、某道路硅酸盐水泥,称取1.008克试样,经反复灼烧直至恒量后试料的质量为0.9842克,试计算该水泥的烧失量。 解: 该水泥的烧失量为(1.008-0.9842)×100÷1.008=2.36% 4、某道路硅酸盐水泥,称取0.5004克试样进行三氧化硫含量试验,最后反复灼烧至恒量后沉淀的质量为0.0425克,试计算该水泥中三氧化硫含量。 解: 该水泥中三氧化硫含量为0.0425×0.343×100÷0.5004=2.91% 5、某道路硅酸盐水泥进行比表面积试验,透气仪校准温度为23℃,巳知标准样品的比表面积、密度和试料层中的空隙率分别为3547cm2/g、3.16g/cm3和0.530,试验时的温度为26℃,标准样品试验时,压力计中液面降落测得的时间为120s,被测试样料层中的空隙率和密度分别为0.530和2.95 g/cm3, 被测试样在压力计中液面降落测得的时间分别为108s和109s,试计算该水泥的比表面为多少。 解: 该水泥试样第一次测得的比表面积为:3547×3.16×√108/2.95×√120=3600(cm2/g)该水泥试样第一次测得的比表面积为:3547×3.16×√109/2.95×√120=3620(cm2/g)该水泥试样的比表面积为:(3600+3620)÷2=3610(cm2/g) 6、某强度等级为42.5道路硅酸盐水泥样品,28天龄期胶砂强度检验的结果如下:抗折荷载分别为2.98kN、2.90 kN及2.50kN, 抗压荷载分别为73.6kN、75.2kN、72.9 kN、74.3 kN、63.1 kN及74.6kN,计算该水泥的抗压强度和抗折强度,并判断28天强度是否合格。 解: 抗折强度:R f1=1.5F f×L/b3=1.5×2.98×100/43=7.0(MPa) R f2=1.5F f×L/b3=1.5×2.90×100/43=6.8(MPa) R f3=1.5F f×L/b3=1.5×2.50×100/43=5.9 抗折强度平均值:(7.0+6.8+5.9)=6.6(MPa) 因:(6.6-5.9)÷6.6≈11%>10%,故R f3值应舍弃 抗折强度值为:(7.0+6.8)=6.9(MPa)
硅酸盐水泥生产的主要原料
硅酸盐水泥生产的主要原料 (1)石灰质原料: 以碳酸钙为主要成分的原料,是水泥熟料中CaO的主要来源。如石灰石、白垩、石灰质泥灰岩、贝壳等。一吨熟料约需~吨石灰质干原料,在生料中约占80%左右。 石灰质原料的质量要求 品位 CaO(%) MgO(%) R2O(%) SO3(%)燧石或石英(%) 一级品>48 <<<< 二级品 45~48 <<<< (2)粘土质原料: 含碱和碱土的铝硅酸盐,主要成分为SiO2,其次为AI2O3,少量Fe2O3,是水泥熟料中SiO2、AI2O3、Fe2O3的主要来源。粘土质原料主要有黄土、粘土、页岩、泥岩、粉砂岩及河泥等。一吨熟料约需~吨粘土质原料,在生料中约占11~17%。 粘土质原料的质量要求 品位硅酸率铁率 MgO(%) R2O(%) SO3(%)塑性指数 一级品~~<<<>12 二级品~或~不限<<<>12 一般情况下SiO2含量60~67%,AI2O3含量14~18%。 (3)主要原料中的有害成分 ① MgO:影响水泥的安定性。水泥熟料中要求MgO<5%,原料中要求MgO<3%。 ②碱含量(K2O、Na2O):对正常生产和熟料质量有不利影响。水泥熟料中要求R2O<%,原料中要求R2O<4%。 ③ P2O5:水泥熟料中含少量的P2O5对水泥的水化和硬化有益。当水泥熟料中P2O5含量在%时,效果最好,但超过1%时,熟料强度便显着下降。P2O5含量应限制。 ④ TiO2:水泥熟料中含有适量的TiO2,对水泥的硬化过程有强化作用。当TiO2含量达~%,强化作用最显着,超过3%时,水泥强度就要降低。如果含量继续增加,水泥就会溃裂。因此在石灰石原料中应控制TiO2<%。 3. 硅酸盐水泥生产的辅助原料 (1)校正原料 ①铁质校正原料:补充生料中Fe2O3的不足,主要为硫铁矿渣和铅矿渣等。 ②硅质校正原料:补充生料中SiO2的不足,主要有硅藻土等。 ③铝质校正原料:补充生料中AI2O3的不足,主要有铝钒土、煤矸石、铁钒土等。 校正原料的质量要求 硅质原料硅率 SiO2(%) R2O(%) > 70~90 < 铁质原料 Fe2O3>40% 铝质原料 AI2O3>30% (2)缓凝剂:以天然石膏和磷石膏为主。掺加量3~5%。 4.工业废渣的利用 ①赤泥:烧结法生产氧化铝排出的赤色废渣,以CaO、SiO2为主。掺加石灰质原料可配制成生料。 ②电石渣:以CaO为主。可替代部分石灰石生产水泥。 ③煤矸石:以SiO2、AI2O3为主。可替代粘土生产水泥。 ④粉煤灰:以SiO2、AI2O3为主。可替代粘土配制生料,也可作混合材料。 ⑤石煤:以SiO2、AI2O3为主。可作不粘土质原料,也可作燃料。
《通用硅酸盐水泥》的标准
前言 本标准第6.1、6.3、8.3条为强制性条款,其余为推荐性条款。 本标准参照欧洲水泥试行标准ENV 197-1:2000《通用波特兰水泥》修订。 本标准代替GB175-1999《硅酸盐水泥、普通硅酸盐水泥》、GB1344-1999《矿渣硅酸盐水泥、火山灰质硅酸盐水泥、粉煤灰硅酸盐水泥》、GB12958-1999《复合硅酸盐水泥》三个标准。与GB175-1999、GB1344-1999、GB12958-1999相比,主要变化如下: ——全文强制改为条文强制(本版前言); ——增加通用硅酸盐水泥的定义(本版第3.1条); ——将各品种水泥的定义取消(原版GB175-1999、GB1344-1999、GB12958-1999第3章);——将组成与材料合并为一章,材料中增加了硅酸盐水泥熟料(原版GB175-1999、GB1344-1999、GB12958-1999第4章,本版第4章); ——普通硅酸盐水泥中“掺活性混合材料时,最大掺量不超过15%,其中允许用不超过水泥质量5%的窑灰或不超过水泥质量10%的非活性混合材料来代替”改为“活性混合材料掺加量为>5%,≤20%,其中允许用不超过水泥质量5%符合本标准第4.2.5条的窑灰或不超过水泥质量8%符合本标准第4.2.4条的非活性混合材料代替”。(原版GB175-1999中第3.2条,本版第4.1条); ——将矿渣硅酸盐水泥中矿渣掺加量由“20%~70%”改为“>20%,≤70%”(原版GB1344-1999中第3.1条,本版第3.4条、4.1条); ——将火山灰质硅酸盐水泥中火山灰质混合材料掺量由“20%~50%”改为“>20%,≤40%”(原版GB1344-1999中第3.2条,本版第4.1条); ——将粉煤灰硅酸盐水泥中粉煤灰掺量由“20%~40%”改为“>20%,≤40%”(原版GB1344-1999中第3.3条,本版第4.1条); ——将复合硅酸盐水泥中混合材料总掺加量由“应大于15%,但不超过50%”改为“>20%,≤50%”(原版GB12958-1999中第3章,本版第4.1条); ——材料中增加了粒化高炉矿渣粉(本版第4.2.2、4.2.3条); ——取消了粒化精铬铁渣、粒化增钙液态渣、粒化碳素铬铁渣、粒化高炉钛矿渣等混合材料以及符合附录A新开辟的混合材料,并将附录A取消(原版GB12958-1999中第4.2条、第4.3条和附录A) ——增加了M类混合石膏(原版GB175-1999、GB1344-1999和GB12958-1999中第3章,本版第4.2.2.1条); ——助磨剂允许掺量由“不超过水泥质量的1%”改为“不超过水泥质量的0.5%”(原版GB175-1999、GB1344-1999和GB12958-1999中第4.5条,本版第4.2.6条); ——普通水泥强度等级中取消32.5和32.5R(原版GB175-1999中第5章,本版第5章);——增加了氯离子含量的要求,即水泥中氯离子含量不大于0.06%(本版第6.1条);——取消了细度指标要求,但要求在试验报告中给出结果(原版GB175-1999第 6.5条、GB1344-1999、GB12958-1999中第6.3条,本版8.4条); ——将复合硅酸盐水泥的强度等级改为和矿渣硅酸盐水泥、火山灰硅酸盐水泥、粉煤灰硅酸盐水泥一致(原版GB12958-1999中第6.6条,本版第6.3.3条) ——增加了水泥组分的试验方法(本版第7.1条); ——强度试验方法中增加了“掺火山灰混合材料的普通硅酸盐水泥、粉煤灰硅酸盐水泥和复合硅酸盐水泥在进行胶砂强度检验时,其用水量按0.50水灰比和胶砂流动度不小于180mm 来确定。当流动度小于180mm时,须以0.01的整倍数递增的方法将水灰比调整至胶砂流动度不小于180mm”(原版GB1344-1999第7.5条,本版第7.5条); ——将“水泥出厂编号按水泥厂年生产能力规定”改为“水泥出厂编号按单线年生产能力规
硅酸盐水泥生产工艺流程168
硅酸盐水泥生产工艺流程 水泥生产原料及配料、硅酸盐水泥熟料的矿物组成、硅酸盐水泥生产工艺流程、硅酸盐水泥生产的原料水泥生产原料及配料: 生产硅酸盐水泥的主要原料为石灰原料和粘土质原料,有时还要根据燃料品质和水泥品种,掺加校正原料以补充某些成分的不足,还可以利用工业废渣作为水泥的原料或混合材料进行生产。 1、石灰石原料石灰质原料是指以碳酸钙为主要成分的石灰石、泥灰岩、白垩和贝壳等。石灰石是水泥生产的主要原料,每生产一吨熟料大约需要1.3吨石灰石,生料中80%以上是石灰石。 2、黏土质原料黏土质原料主要提供水泥熟料中的、、及少量的。天然黏土质原料有黄土、黏土、页岩、粉砂岩及河泥等。其中黄土和黏土用得最多。此外,还有粉煤灰、煤矸石等工业废渣。黏土质为细分散的沉积岩,由不同矿物组成,如高岭土、蒙脱石、水云母及其它水化铝硅酸盐。 3、校正原料当石灰质原料和黏土质原料配合所得生料成分不能满足配料方案要求时(有的含量不足,有的和含量不足)必须根据所缺少的组分,掺加相应的校正原料 (1)硅质校正原料含 80%以上 (2)铝质校正原料含 30%以上 (3)铁质校正原料含 50%以上 硅酸盐水泥熟料的矿物组成: 硅酸盐水泥熟料的矿物主要由硅酸三钙()、硅酸二钙()、铝酸三钙()和铁铝酸四钙()组成。硅酸盐水泥生产工艺流程: 1、破碎及预均化 (1)破碎水泥生产过程中,大部分原料要进行破碎,如石灰石、黏土、铁矿石及煤等。石灰石是生产水泥用量最大的原料,开采后的粒度较大,硬度较高,因此石灰石是生产水泥用量最大的原料,开采后的粒度较大,硬度较高,因此石灰石的破碎在水泥厂的物料破碎中占有比较重要的地位。 破碎过程要比粉磨过程经济而方便,合理选用破碎设备和和粉磨设备非常重要。在物料进入粉磨设备之前,尽可能将大块物料破碎至细小、均匀的粒度,以减轻粉磨设备的负荷,提高黂机的产量。物料破碎后,可减少在运输和贮存过程中不同粒度物料的分离现象,有得于制得成分均匀的生料,提高配料的准确性。 (2)原料预均化预均化技术就是在原料的存、取过程中,运用科学的堆取料技术,实现原料的初步均化,使原料堆场同时具备贮存与均化的功能。 原料预均化的基本原理就是在物料堆放时,由堆料机把进来的原料连续地按一定的方式堆成尽可能多的相互平行、上下重叠和相同厚度的料层。取料时,在垂直于料层的方向,尽可能同时切取所有料层,依次切取,直到取完,即“平铺直取”。
gb175-2007通用硅酸盐水泥标准
前言 本标准第、、、、为强制性条款,其余为推荐性条款。 本标准与欧洲水泥标准ENV197-1:2000 《通用波特兰水泥》的一致性程度为非等效。 本标准自实施之日起代替GB175-1999《硅酸盐水泥、普通硅酸盐水泥》、GB1344-1999《矿渣硅酸盐水泥、火山灰质硅酸盐水泥、粉煤灰硅酸盐水泥》、GB12958-1999《复合硅酸盐水 泥》三个标准。 与GB175-1999、GB1344-1999、GB12958-1999相比,本标准主要变化如下:全文强制改为条文强制;增加了通用硅酸盐水泥的定义;将各品种水泥的定义取消(原版GB175-1999、 GB1344-1999、GB12958-1999第3章;将组分与材料合并为一章(原版GB175-1999、GB1344-1999、GB12958-1999第4章,本版第5章);普通硅酸盐水泥中“掺活性混合材料时,最大掺量不超过15%,其中允许用不超过水泥质量5%的窑灰或不超过水泥质量10%的非活性混合材料来代替”改为“活性混合材料掺加量为>5%且≤20%,其中允许用不超过水泥质量8% 且符合本标准第条的非活性混合材料或不超过水泥质量5%且符合本标准第条的窑灰代替” (原版GB175-1999中第条, 本版第条); ——将矿渣硅酸盐水泥中矿渣掺加量由“ 20%~70%”改为“ >20%且≤70%”,并分为A 型和B 型。A 型矿渣掺量>20%且≤50%,代号;B 型矿渣掺量>50%且≤70%,代号(原版GB1344-1999中第条, 本版第条); ——将火山灰质硅酸盐水泥中火山灰质混合材料掺量由“ 20%~50%”改为“ >20%且≤40%”(原版GB1344-1999中第条,本版第条); ——将复合硅酸盐水泥中混合材料总掺加量由“应大于15%,但不超过50%”改为“ >20% 且≤50%”(原版GB12958-1999中第3章,本版第条); ——材料中增加了粒化高炉矿渣粉(本版第、条);